甲醇催化剂
甲醇合成催化剂生产工艺

甲醇合成催化剂生产工艺甲醇合成催化剂分两期进行生产,甲醇合成催化剂每批生产周期(从物料加入到得到产品)为24小时,每批产品为500kg,一期年生产批数为2000批,总计为1000吨。
一期甲醇合成催化剂以电解铜、电解锌、碱式碳酸铜、碱式碳酸锌、碳酸氢钠、硝酸、氧化铝、石墨为原料,经备料、反应、过滤、烘干、焙烧、成型得到产品。
(1)备料①化铜先将电解铜和水加入5m3化铜罐中,再加入95%硝酸,化铜罐内设有冷却水盘管,用冷却水控制反应温度为60~70℃,铜和硝酸反应生成硝酸铜。
该工序涉及反应方程式如下:3Cu + 8HNO3 = 3Cu(NO3)2 + 2NO↑+4H2O②化锌先将电解锌和水加入5m3化锌罐中,再加入95%硝酸,化锌罐内设有冷却水盘管,用冷却水控制反应温度为60~70℃,锌和硝酸反应生成硝酸锌。
该工序涉及反应方程式如下:3Zn + 8HNO3 = 3Zn(NO3)2 + 2NO↑+4H2O将上述制备好的硝酸铜和硝酸锌溶液打入15m3混合液罐中进行混合,混合均匀后打入计量罐用作反应工序原料。
备料过程会有含氮氧化物废气产生,送二级低温水+二级尿素水溶液吸收系统处理。
(2)反应先向12m3反应罐加入一定量水,再夹套内通入蒸汽升温至60~65℃,开启搅拌器,然后加入碳酸氢钠。
保持罐内温度为60℃~65℃,将制备的硝酸铜、硝酸锌混合液经过计量后匀速加入反应罐中,硝酸铜、硝酸锌与碳酸氢钠发生反应生成碱式碳酸铜、碱式碳酸锌沉淀,碱式碳酸铜、碱式碳酸锌为难溶性物质,溶解度均小于0.01g/100g 水。
该工序涉及反应方程式如下:2Cu(NO3)2 + 4NaHCO3 = Cu2(OH)2CO3↓+4NaNO3 + H2O + 3CO2↑2Zn(NO3)2 + 4NaHCO3 = Zn2(OH)2CO3↓+4NaNO3 + H2O + 3CO2↑反应结束后,将称量好的碱式碳酸铜、碱式碳酸锌、氧化铝依次放入反应罐中,继续搅拌20~30分钟,然后静止沉降得到反应浆液。
二氧化碳制甲醇催化剂

二氧化碳制甲醇催化剂在我们这个万物互联的时代,大家可能都听说过二氧化碳。
没错,就是那种我们呼出来的,植物吸收的,听起来就像是个“坏小子”的东西。
可是,谁能想到,这位“坏小子”居然能摇身一变,变成美味的甲醇呢?是的,今天咱们就来聊聊二氧化碳如何转变为甲醇,以及背后的催化剂这些“隐形大英雄”。
咱们得明白,二氧化碳可不是个简单的家伙。
它虽然在大气中四处游荡,但要把它变成甲醇,就需要一些特别的帮手——催化剂。
这些催化剂就像厨房里的大厨,负责把原料变成美食。
不同的催化剂就像不同风格的大厨,有的擅长做川菜,有的专攻法餐。
而在二氧化碳转化的世界里,最常见的催化剂就是一些金属,比如铜、镍或者铑。
听起来是不是有点高大上?其实它们就在那儿静静地工作,为我们把二氧化碳变成甲醇。
说到催化剂,那可真是一门深奥的学问。
比如,铜催化剂就是个了不起的家伙,能够有效地把二氧化碳转化为甲醇,效率高得让人惊叹。
试想一下,二氧化碳和氢气在高温高压的环境下,经过这些催化剂的“调教”,瞬间就变得耳熟能详,成了我们生活中常用的甲醇,简直就是魔法啊!这种转化过程就像是把原本一文不值的废品,变成了人人争抢的宝贝,实在太有意思了。
大家可能不知道,甲醇不仅仅是酒精的“亲戚”。
它还是一个非常重要的化工原料,可以用来生产塑料、药品、燃料等,简直是个万金油。
更妙的是,甲醇的使用还能帮助我们减少对传统化石燃料的依赖,真是科技与环保的完美结合。
想象一下,我们都能喝上“绿色饮料”,把二氧化碳转化为有用的东西,岂不是美滋滋?催化剂的研究也不是一帆风顺。
科学家们常常要面对各种挑战,得不断寻找更高效、更环保的催化剂。
就像是打游戏一样,通关的路上总有各种Boss等着你。
有些催化剂在工作的时候,可能会出现“疲劳”,效率下降。
为了打破这个瓶颈,研究者们开始尝试各种新材料,甚至还有一些神奇的纳米材料,真是让人眼前一亮。
现在的科学研究,除了单纯的实验,还越来越注重数据分析。
很多时候,科学家们通过计算机模拟来预测催化剂的性能。
甲醇合成催化剂的进展

甲醇合成催化剂的进展摘要:本文综述了甲醇合成催化剂的现状,对各种催化剂的性能、特点进行了对比分析,介绍了甲醇合成催化剂的最新技术进展。
关键词:甲醇催化剂1前言甲醇是一种重要化工原料,可广泛用于医药、农药、染料、合成纤维、合成树脂和合成塑料等工业,更重要的是随着石油资源日益短缺,石油价格急剧攀升,甲醇做为可替代能源,大力发展甲醇燃料和甲醇制低碳烯烃及其产品的技术具有巨大的潜力和十分广阔的前景。
充分利用我国丰富的煤炭资源发展合成甲醇具有十分重要的意义。
合成甲醇催化剂是合成甲醇的关键技术之一,本文仅从合成甲醇催化剂的性能参数等方面介绍国内外甲醇催化剂的研究情况和进展[1]。
当代甲醇生产技术以海尔德-托普索(Haldor Topsoe)公司、Kvaerner工艺技术/Synetix公司(英国)、克虏伯-乌德公司、鲁齐油气化学(Lurgi)公司、Synetix公司的技术最为典型。
2甲醇催化剂的现状2.1 锌铬催化剂锌铬(ZnO/Cr2O3)催化剂是一种高压固体催化剂,由德国BASF公司于1923年首先开发研制成功。
锌铬催化剂的活性较低,为了获得较高的催化活性,操作温度必须在590 K~670 K。
为了获取较高的转化率,操作压力必须为25 MPa~35 MPa,故称为高压催化剂。
锌铬催化剂的特点是: a)耐热性能好,能忍受温差在100℃以上的过热过程;b)对硫不敏感;c)机械强度高;d)使用寿命长、范围宽,操作控制容易;d)与铜基催化剂相比较, 其活性低、选择性低、精馏困难(产品中杂质复杂)。
由于在这类催化剂中Cr2O3的质量分数高达10%, 故成为铬的重要污染源之一。
铬对人体是有毒的, 目前该类催化剂已逐步被淘汰。
2.2 铜基催化剂铜基催化剂是一种低温低压甲醇合成催化剂,其主要组分为CuO/ZnO/Al2O3(Cu-Zn-Al),由英国 ICI公司和德国Lurgi公司先后研制成功。
低(中) 压法铜基催化剂的操作温度为210℃~300℃,压力为5MPa~10MPa,其特点是:a)活性好,单程转化率为7%~8%;b)选择性高,大于99%,其杂质只有微量的甲烷、二甲醚、甲酸甲酯,易得到高纯度的精甲醇;c)耐高温性差,对硫敏感。
甲醇重整催化剂和水汽变换催化剂

甲醇重整催化剂和水汽变换催化剂一、概述甲醇重整催化剂和水汽变换催化剂是化工领域中重要的催化剂之一,其在甲醇转化、氢气制备、清洁能源生产等方面发挥着重要作用。
本文将从催化剂的定义、分类、应用领域、发展趋势等方面进行综合介绍。
二、甲醇重整催化剂1. 定义甲醇重整催化剂是指在高温、高压条件下将甲醇与水蒸气催化转化为一氧化碳和氢气的催化剂,通常采用铜、锌、铬等金属氧化物作为活性组分。
2. 分类根据不同的反应机理和工艺条件,甲醇重整催化剂可分为氧气氧化重整催化剂、水蒸气重整催化剂、生物质重整催化剂等多种类型。
3. 应用领域甲醇重整催化剂广泛应用于氢气制备、甲醇汽车发动机、燃料电池等领域,是清洁能源生产的重要催化剂。
4. 发展趋势随着清洁能源技术的发展和产业需求的增加,甲醇重整催化剂的研发和应用将进一步拓展,新型高效、低成本的催化剂将成为未来的发展趋势。
三、水汽变换催化剂1. 定义水汽变换催化剂是指在一定温度和压力下,将水蒸气催化转化为氢气和氧气的催化剂,通常采用贵金属或氧化物作为活性组分。
2. 分类水汽变换催化剂可分为高温水汽变换催化剂和低温水汽变换催化剂两种,其中高温水汽变换催化剂主要用于工业氢气生产,低温水汽变换催化剂主要用于燃料电池、氢能储存等领域。
3. 应用领域水汽变换催化剂在清洁能源生产、化工工业、氢能技术等领域起着重要作用,是氢气制备和利用的重要催化剂。
4. 发展趋势随着燃料电池、氢能技术等领域的快速发展,水汽变换催化剂的需求将进一步增加,新型高效、稳定的催化剂将成为发展趋势。
四、结论甲醇重整催化剂和水汽变换催化剂是清洁能源生产、氢能技术等领域不可或缺的重要催化剂,在新型能源的发展和应用中发挥着重要作用。
随着清洁能源技术的不断进步和产业需求的增加,催化剂研发和应用将进一步加强,为推动清洁能源产业发展和应用提供重要支持。
甲醇重整催化剂和水汽变换催化剂将在未来的清洁能源领域中发挥着越来越重要的作用,加强研发和应用将成为行业发展的重要方向。
直接甲醇燃料电池催化剂性能测试

直接甲醇燃料电池催化剂性能测试直接甲醇燃料电池催化剂主要以Pt 系催化剂为主,再加以单壁碳纳米管为催化剂载体,催化剂有效分散,催化性能提高。
循环伏安法曲线正向扫描的峰电流密度可直接反映甲醇的氧化量及催化剂的电催化活性。
本实验主要针对直接甲醇燃料电池催化剂材料对甲醇氧化的的循环伏安曲线进行测试,了解直接甲醇燃料电池的工作原理及工作特性。
一、实验目的和要求:1.掌握用循环伏安法测定直接甲醇燃料电池催化性能的方法。
2.了解直接甲醇燃料电池的工作原理。
3.了解CHI 电化学工作站的设定方法。
二、测定原理:在电极上施加一个线性扫描电压,以恒定的变化速度扫描,当达到某设定的终止电位时,再反向回归至某一设定的起始电位,循环伏安法电位与时间的关系(见图a )。
若电极反应为O +e ⇔R ,反应前溶液中只含有反应粒子O ,且O 、R 在溶液均可溶,控制扫描起始电势从比体系标准平衡电势正得多的起始电势ϕi 处开始势作正向电扫描,电流响应曲线则如图b 所示。
当电极电势逐渐负移到ϕ平0附近时,O 开始在电极上还原,并有法拉第电流通过。
由于电势越来越负,电极表面反应物O 的浓度逐渐下降,因此向电极表面的流量和电流就增加。
当O 的表面浓度下降到近于零,电流也增加到最大值Ipc ,然后电流逐渐下降。
当电势达到ϕr 后,又改为反向扫描。
随着电极电势逐渐变正,电极附近可氧化的R 粒子的浓度较大,在电势接近并通过ϕ平0时,表面上的电化学平衡应当向着越来越有利于生成R的方向发展。
于是R开始被氧化,并且电流增大到峰值氧化电流Ipa,随后又由于R的显著消耗而引起电流衰降。
整个曲线称为“循环伏安曲线”。
三、仪器药品:电化学工作站一台玻碳工作电极一根Ag/AgCl参比电极一根铂丝电极一根高纯氮气Nafion 117溶液浓硫酸甲醇乙醇四、实验步骤:1. 取制备好的催化剂材料3.8mg分散到1mL乙醇中超声30min。
2. 取催化剂材料的乙醇分散液30μL滴涂到玻碳工作电极表面,静置15min干燥后,再其表面滴涂Nafion117溶液10μL,静置15min干燥,待用。
XNC-98系列合成甲醇催化剂使用说明书
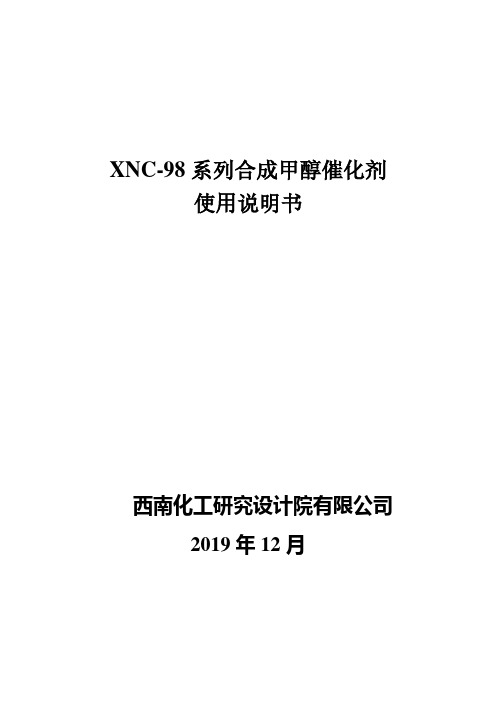
XNC-98系列合成甲醇催化剂使用说明书西南化工研究设计院有限公司2019年12月目次一.催化剂的主要物化特性 (2)二.催化剂的使用条件 (3)三.催化剂装填 (3)四.催化剂的升温、还原 (3)五.操作注意事项 (6)六.停车 (6)七.卸催化剂 (7)八.其他 (7)XNC-98系列合成甲醇催化剂使用说明书XNC-98系列催化剂是我公司研制和开发的一种高活性、高选择性的甲醇合成催化剂。
用于低温低压下由碳氧化物与氢合成甲醇。
可适用于各种类型的甲醇合成反应器。
具有低温活性高、热稳定性好的特点。
常用的操作温度为210~310℃,操作压力3.0~15.0MPa,空速5000~20000h-1(最佳空速8000~12000h-1)。
本催化剂可广泛适用于各种原料生产的合成气。
一.催化剂的主要物化特性1.催化剂主要物理性质外观:有黑色金属光泽的圆柱体外形尺寸(直径×高),mm:6×(4.5~5)堆密度,Kg/L:~1.25径向抗压碎强度,N/cm:≥2002.催化剂化学组成催化剂主要化学组成列于下表:3.催化剂的活性按本催化剂质量检验标准规定,在下述活性检验条件下:催化剂装量:4mL 粒度: 20目~40目反应压力: 5.00±0.05MPa 空速: 10000±300h-1反应温度:230±1℃、250±1℃气体组成:CO 12×10-2~15×10-2,CO2 3×10-2~8×10-2惰性气体 7×10-2~10×10-2,其余为H2。
催化剂活性为:230℃时,催化剂的时空收率≥1.50Kg/L∙h;250℃时,催化剂的时空收率≥2.0Kg/L∙h。
4.催化剂的使用寿命在正常条件下运转寿命为3年以上。
二.催化剂的使用条件XNC-98系列催化剂在下列条件范围内使用反应压力: 3.0~15.0MPa反应温度:还原好的催化剂在190℃就具有较好的活性,一般使用温度是200~300℃。
甲醇合成催化剂知识

甲醇合成催化剂知识d i4 X+ }1 z! j0 v1 铜基催化剂的催化原理 + W7 b1 C1 Y9 W4 M1 h)o9 F0 t8 j* c: D q, |6 O 目前,低压甲醇合成铜基催化剂主要组分是 CuO、ZnO和Al2O3,三组分在催化剂中的比例随着生产厂家的不同而不同。
一般来说, CuO的质量分数在40% ~80%, ZnO的质量分数在10% ~30%, Al2O3的质量分数在5% ~10%。
铜基催化剂在合成甲醇时, CuO、ZnO、Al2O3三组分的作用各不相同。
CO和H2在催化剂上的吸附性质与催化剂的活性有非常密切的关系。
在铜基催化剂表面对CO的吸附速率很高,而H2的吸附则比CO 慢得多。
ZnO是很好的氢化剂,可使H2被吸附和活化, 但对CO几乎没有化学吸附,因此可提高铜基催化剂的转化率。
纯铜对甲醇合成是没有活性的,H2和CO合成甲醇的反应是在一系列活性中心上进行的,而这种活性中心存在于被还原的Cu-CuO界面上。
在催化剂中加入少量 Al2O3的首要功能就是阻止一部分氧化铜还原。
当催化剂被还原后,开始进行反应时,合成气中的H2 和CO都是还原剂,有使氧化铜进一步还原的趋势。
这种过度的还原,使得活性中心存在的界面越来越小,催化剂活性也越来越低。
从合成的整个过程来看,随着还原表面向催化剂的内层深入,未还原的核心越来越小,作为被还原的Cu-CuO界面的核心表面积也越来越小,催化剂的活性降低,合成反应速率随之降低。
研究认为,Al2O3在催化剂中作为结构助剂起阻碍铜颗粒烧结的作用, CuO/ZnO/Al2O3催化剂的活性远高于双功能催化剂CuO/ZnO的活性。
q7 h- G8 n9 ]$ B5 m- Q: ?& ]/ D2 铜基催化剂助剂6 j8 } x5 L! ?0 V1 l1 K4 H$ Q! m% g\5 K8 e) C+ g5 A)E! ~ 铜基催化剂助剂的研究是甲醇合成催化剂研究的一个重要课题。
甲醇合成催化剂反应机理及应用1

甲醇合成催化剂的反应机理及应用新疆广汇新能源有限公司新疆哈密839000 杨林君摘要:本文介绍了甲醇合成反应的机理,合成催化剂的制备;对XNC-98催化剂的使用情况做了介绍。
关键词:甲醇合成催化剂甲醇是重要的有机化工原料,碳一化学的母体,广泛用于生产塑料、纤维、橡胶、染料、香料、医药和农药等,还是重要的有机溶剂。
甲醇在发达国家其产量仅次于乙烯、丙烯和苯,居第四位。
甲醇用作汽车发动机燃料,所谓甲醇汽油,今后随着石油不断开采资源日渐减少,直至枯竭,特别在我国少油多煤的资源下,甲醇用作汽车燃料将达亿吨/年以上,跃升化工产品的首位。
研究开发应用推广近代甲醇合成工艺与合成塔技术和建设大型化生产装置,成为我国甲醇工业大发展的必由之路[1]。
随着甲醇工业的发展,以低压法铜基催化剂为代表的甲醇合成技术得到了很大的发展。
国内近年来在合成催化剂的反应机理、性能及应用等方面研究不断深入,开发出具有世界先进水平的合成催化剂。
一甲醇合成反应的机理甲醇合成反应机理与活性中心的研究一直是甲醇合成反应过程的研究重点,其对高效催化剂的开发、实验现象本质特征的解释和反应结果的预测都具有重要意义。
一个合理的甲醇合成反应历程能够为反应条件的优化以及催化剂制备过程等催化体系的改进提供理论依据,为工业化生产提供理论支撑。
按合成甲醇直接碳源的不同,将机理划分为以下3种:CO与CO2共同作为直接碳源机理、CO作为直接碳源机理以及CO2作为直接碳源机理[2]。
1.1 CO直接作为碳源机理长期已来,在铜基催化剂上加氢合成甲醇的碳源问题都是研究者争论的焦点问题。
Herman 等研究了CO/H2体系在Cu/ZnO/Al2O3催化剂上的反应,认为反应的活性中心是Cu+,H2的解离吸附发生在ZnO上,并提出以下反应机理:CO+*(Cu2O)→CO*(Cu2O)H2+2*(ZnO)→2H*(ZnO)CO*(Cu2O)+H*(ZnO)→HCO*(Cu2O)+*(ZnO)H*(ZnO)+HCO*(Cu2O)→CH2O*(Cu2O)+*(ZnO)2H*(ZnO)+CH2O*(Cu2O)→CH3OH*(Cu2O)+2*(ZnO)CH3OH*(Cu2O)→CH3OH+*(Cu2O)式中:*指催化剂的活性吸附位。
甲醇合成催化剂失活及影响因素分析

甲醇合成催化剂失活及影响因素分析摘要:甲醇 (CHOH) 是一种结构最简单的一元醇,也被称为木醇,因为它最3初存在于干燥的蒸馏木材中。
甲醇是一种无色挥发性液体,有酒精气味。
它是一种重要的化工原料,广泛用于化学实验和化学领域。
用途广泛,不仅可作为萃取剂,还可作为化工原料及其加工产品,如甲醛、醋酸、农药等。
随着科学技术的发展,甲醇转化为烯烃生产技术不断发展,甲醇转化为高附加值产品的力度不断加大对甲醇的需求不断增长,甲醇合成领域的研究越来越受到研究关注。
催化剂是一类能够在化学反应过程中改变化学反应速率而不被自身消耗的物质,广泛应用于许多化学反应中。
催化剂作为甲醇合成中的一个非常重要的环节,与甲醇生产中的许多条件和性能指标密切相关,其种类、性能和活性对甲醇的合成起着重要的作用。
因此,有必要对催化剂活性进行系统的分析和研究。
关键词:甲醇合成;催化剂失活;影响因素引言甲醇制烯烃是以甲醇为原料,在催化剂的作用下,在流化床反应器中进行脱水和碳链重整的过程,实现MTO工艺优化的核心和关键是MTO催化剂,具有极高的比表面积、良好的水热稳定性、丰富的质子酸性和离子交换位,独特的八元环三维孔道体系更使得它拥有了极好的小分子择形催化性能。
甲醇制烯烃SAPO-34分子筛工业化应用过程中因反应物、反应过程及传质等问题,引起催化剂失活和磨损,导致催化剂需要再生和补充新的催化剂,增加了生产成本,必须进行再利用。
本文综述甲醇合成催化剂失活的影响因素,并对提高甲醇合成催化剂活性的措施进行总结,提出甲醇催化剂今后的发展方向。
1甲醇合成催化剂失活的影响因素1.1结蜡问题( 1) 在催化剂装填过程中,如果铁锈或油脂等杂质带入合成塔内,会降低催化剂的活性和选择性,促进石蜡的生成。
( 2) 铜基催化剂在使用过程中,随着使用时间的增加,特别是催化剂使用中后期,受催化剂选择性的限制,会生成一定量的石蜡。
同时,甲醇生产时难免会伴有少量甲酸及其他有机酸生成,这些酸类物质在 CO 的作用下腐蚀合成塔生成Fe( CO)5与 Ni( CO)4,加速石蜡的生成。
科莱恩甲醇合成催化剂

催化剂活化 MegaMax 800催化剂以氧化态形式进行装运且易于使用。更多详细 内容,请参考MegaMax 800的使用说明书。另外,催化剂业务始终 配备有技术专家的支持,以便对程序进行审查并协助装置开车,而 且我们可提供独立的氢分析仪以便对还原条件进行严格的控制。我 们的服务将帮助您尽可能降低停工时间并确保无故障启动。
CO + 2H2 ↔ CH3OH CO2 + 3H2 ↔ CH3OH + H2O
∆HR = -91 kJ/mol ∆HR = -49 kJ/mol
这两个甲醇合成反应都伴随着CO变换反应:
CO + H2O ↔ CO2 + H2
∆HR = -42 kJ/mol
如今,工业化规模的甲醇合成采用间接或直接的冷却方式,如在等 温或绝热反应器中进行。该低压工艺的主要优点是: • 降低投资和生产成本 • 操作可靠性高 • 工厂的规模上具有很大灵活性
因为其较高的稳定性,MegaMax 800可以在5年的寿命周期内保持 较高的活性,并且期望每立方米催化剂累计甲醇产量达45,000 吨 ( 图 4)。
碳效率 [%] 100
95
90 MegaMax® 800
85 基准
80 0
11250
22500
33750
45000
甲醇催化剂卸出方案

甲醇催化剂卸出方案甲醇催化剂是一种用于甲醇生产过程中的重要催化剂。
在甲醇生产过程中,甲醇催化剂的性能和使用寿命对甲醇的产量和质量有着直接影响。
因此,甲醇催化剂的卸出方案十分重要。
本文将从卸出原理、卸出步骤和卸出措施等方面详细讨论甲醇催化剂的卸出方案。
甲醇催化剂的卸出原理主要有机械挤压和溶剂法两种。
机械挤压法是将催化剂从反应器中挤压出来,常见的有高压水冲洗、高压氮气吹扫等方式。
溶剂法则是利用溶剂的溶解作用将催化剂溶解出来,常见的有酸洗、碱洗等方式。
甲醇催化剂的卸出步骤一般包括预处理、卸出和清洗三个环节。
预处理主要是为了降低催化剂与废料之间的附着力,一般包括降低反应温度、增加反应时间等措施。
卸出过程是将催化剂从反应器中物理或化学方式移出。
清洗环节则是将卸出的催化剂进行清洗,以去除附着在催化剂表面的杂质和反应物。
甲醇催化剂的卸出措施有很多,根据催化剂的特点和生产实际情况可以选择适合的卸出方式。
常用的方法有高压水冲洗、高压氮气吹扫、酸洗、碱洗等。
高压水冲洗是将高压水通过喷嘴喷射到催化剂上,通过高压水流的冲击力将催化剂从反应器中卸出。
高压氮气吹扫则是通过高压气流的冲击力将催化剂从反应器中吹出来。
酸洗和碱洗则是利用酸碱的溶解作用将催化剂溶解出来。
在进行甲醇催化剂的卸出过程中,还需要注意一些问题。
首先是卸出的环境和设备要具备一定的防腐蚀性,以保证卸出过程的安全性和稳定性。
其次是卸出过程中应该注意催化剂的回收利用,将卸出的催化剂进行处理和再生,以减少资源浪费和环境污染。
此外,卸出过程中还要根据生产需求和催化剂的状态进行合理的选择。
总之,甲醇催化剂的卸出方案对甲醇生产过程有着重要的影响。
通过选择合适的卸出方法和措施能够有效地提高催化剂的使用寿命和生产效率,降低生产成本和资源浪费。
因此,在实际生产中应根据催化剂的特点和生产需求采取适合的卸出方案,并注重进一步的研究和改进,以提高甲醇催化剂的卸出技术。
关于甲醇合成催化剂使用经验总结及问题分析
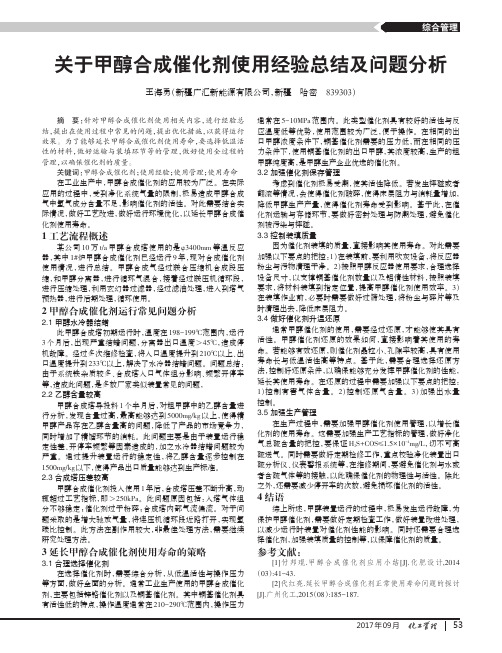
2017年09月关于甲醇合成催化剂使用经验总结及问题分析王海勇(新疆广汇新能源有限公司,新疆哈密839303)摘要:针对甲醇合成催化剂使用相关内容,进行经验总结,提出在使用过程中常见的问题,提出优化措施,以获得运行效果。
为了能够延长甲醇合成催化剂使用寿命,要选择低温活性的材料,做好运输与装填环节等的管理,做好使用全过程的管理,以确保催化剂的质量。
关键词:甲醇合成催化剂;使用经验;使用管理;使用寿命在工业生产中,甲醇合成催化剂的应用较为广泛。
在实际应用的过程中,受到净化系统气量的限制,极易造成甲醇合成气中氢气成分含量不足,影响催化剂的活性。
对此需要结合实际情况,做好工艺改进,做好运行环境优化,以延长甲醇合成催化剂使用寿命。
1工艺流程概述某公司10万t/a 甲醇合成塔使用的是φ3400mm 等温反应器,其中1#炉甲醇合成催化剂已经运行9年,现对合成催化剂使用情况,进行总结。
甲醇合成气经过联合压缩机合成段压缩,和甲醇分离器,进行循环气混合,接着经过联压机循环段,进行压缩处理,利用玄幻器过滤器,经过滤油处理,进入到塔气预热器,进行后期处理,循环使用。
2甲醇合成催化剂运行常见问题分析2.1甲醇水冷器结蜡此甲醇合成塔初期运行时,温度在198-199℃范围内,运行3个月后,出现严重结蜡问题,分离器出口温度>45℃,造成停机故障。
经过多次维修检查,将入口温度提升到210℃以上、出口温度提升到233℃以上,解决了水冷器结蜡问题。
问题总结:由于系统铁杂质较多、合成塔入口气体组分影响、频繁开停车等,造成此问题,是多数厂家类似装置常见的问题,2.2乙醇含量较高甲醇合成塔导投料1个半月后,对粗甲醇中的乙醇含量进行分析,发现含量过高,最高能够达到5000mg/kg 以上,使得精甲醇产品存在乙醇含量高的问题,降低了产品的市场竞争力,同时增加了精馏环节的消耗。
此问题主要是由于装置运行稳定性差、开停车频繁等因素造成的,加之水冷器结蜡问题较为严重。
甲醇合成催化剂钝化常见问题与应对方法

甲醇合成催化剂钝化常见问题与应对方法摘要:从低温甲醇洗净化后的新鲜气与换热后的反应器出口气体换热至60℃后,进入脱硫反应器中脱除气体中的微量硫,脱硫反应器出口气体中硫含量<0.01×10-6。
精脱硫后的气体与部分反应器出口气体换热,反应初期,气体升温至150℃后进入新鲜气加热器中,通过与蒸汽换热,加热至205℃。
反应后期,精脱硫后气体与部分反应器出口气体换热,直接升温至225℃,蒸汽加热器不使用。
循环气经压缩机加压后,进入循环气换热器与部分反应器出口气体,换热至225℃后与换热后的新鲜气混合,混合气进入甲醇合成反应器,甲醇合成气从反应器顶部进入,双反应器并联设计,气体自然分流进入到各反应器中。
关键词:甲醇合成催化剂;钝化;常见问题;应对方法1催化剂装填及运行情况合成塔选用管壳式合成塔,管内装填催化剂,壳程加热锅炉水,带走甲醇合成反应产生的热量,副产2.5MPa中压蒸汽。
其规格如下:Ø3600mm×15768mm;列管Ø44mm×2mm,H=7500mm,n=3990,F=3992m2。
反应器下部装填Ø16mm及Ø8mm氧化铝瓷球,瓷球在列管内高度为50~100mm合格;瓷球上部装催化剂,合成催化剂选用南化集团研究院C307型低压铜基甲醇催化剂,双塔共装填86.46m3。
最后装填Ø8mm氧化铝瓷球,高度约200mm。
2催化剂钝化原因甲醇合成催化剂寿命一般3~5a。
当弛放气气量占整个进气量的7%以上时,就直接影响正常生产,此时必须更换催化剂,催化剂更换前必须钝化卸剂。
钝化前应该编制钝化方案,严格按方案进行,配备熟悉操作人员进行操作。
如果钝化彻底,当维修人员打开底部卸料口时,催化剂就会自动流出,一般加上清理时间24h能完成卸剂工作,如催化剂出现架桥烧结处理起来会很慢。
所以甲醇合成停车更换催化剂前应充分钝化,以便顺利卸剂,进行新催化剂的装填缩短停车周期,最大限度减小装置停车时间。
甲醇重整制氢的催化剂
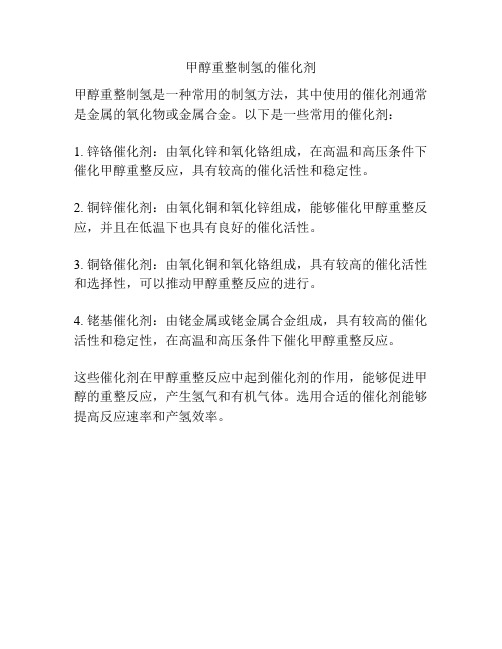
甲醇重整制氢的催化剂
甲醇重整制氢是一种常用的制氢方法,其中使用的催化剂通常是金属的氧化物或金属合金。
以下是一些常用的催化剂:
1. 锌铬催化剂:由氧化锌和氧化铬组成,在高温和高压条件下催化甲醇重整反应,具有较高的催化活性和稳定性。
2. 铜锌催化剂:由氧化铜和氧化锌组成,能够催化甲醇重整反应,并且在低温下也具有良好的催化活性。
3. 铜铬催化剂:由氧化铜和氧化铬组成,具有较高的催化活性和选择性,可以推动甲醇重整反应的进行。
4. 铑基催化剂:由铑金属或铑金属合金组成,具有较高的催化活性和稳定性,在高温和高压条件下催化甲醇重整反应。
这些催化剂在甲醇重整反应中起到催化剂的作用,能够促进甲醇的重整反应,产生氢气和有机气体。
选用合适的催化剂能够提高反应速率和产氢效率。
酸性环境中甲醇电氧化催化剂的研究进展

酸性环境中甲醇电氧化催化剂的研究进展摘要:甲醇不仅是重要的有机化工原料,还是性能优良的能源和车用原料。
随着石油资源的不断开采和利用,以煤、天然气制甲醇的工艺路线越来越显示出重要性。
国家能源集团宁夏煤业有限公司煤制油装置年产100万t·a-1的甲醇合成单元以煤为原料,在催化剂存在下,用一氧化碳和氢气(俗称合成气)加压加温来制造甲醇。
关键词:燃料电池;甲醇电催化反应;催化剂;酸性环境引言甲醇合成催化剂是该甲醇生产技术路线的关键技术。
Cu-Zn-Al催化剂由于具有良好的低温活性与高温稳定性而成为目前研究最多的合成甲醇催化剂体系。
其中,Cu为主要活性组分,ZnO的加入可以与CuO产生协同效应,提高催化剂活性。
Al2O3作为载体,可以提高催化剂的比表面积和铜的分散度,防止反应过程中因铜晶粒烧结导致催化剂失活,提高催化剂的稳定性。
还有研究表明在Cu-Zn-Al体系催化剂中加入适量MgO,更利于铜晶粒的分散,可以进一步提高催化剂的热稳定性。
1甲醇氧化反应机理对酸性环境中甲醇氧化机理的研究表明甲醇氧化存在双反应路径,包括直接路径(非CO路径)和间接路径(CO路径)。
在CO路径中,甲醇会首先脱氢生成CO,然后被进一步氧化成CO2,而在非CO路径中,甲醇则直接氧化生成CO2。
早期MatthewNeurock运用第一性原理密度泛函理论计算分析甲醇电催化的反应机制。
他认为对于Pt(111),主要是CO路径占主导地位,当电位小于0.6VNHE时,CO会覆盖活性位点并且难以被氧化;而当电位高于0.6VNHE时,水会氧化生成OH;当电位略高于0.66VNHE时,CO会被氧化。
此外他还认为不同的反应路径中,中间体的活化对应所需的Pt活性位点数量不一,如对于非CO路径而言,中间体的活化仅需1~2个Pt原子,而CO路径则需要较大的表面集合和阶梯状活性位点。
根据DFT,具体的反应路径取决于甲醇脱氢是由C-H键还是O-H键的断裂开始的。
甲醇合成催化剂

CATALYST HANDLING 2231-00-T2-M1 (8)Rev: 00 MKH02/09/09IJM 02/09/09 HAC 02/09/09 MG 03/09/09 ORIGINAL ISSUERev. No.Made byDATEChecked byDATEApproved byDATEAuthorised byDATEDetails第八部分- 催化剂处理CATALYST HANDLING 2231-00-T2-M1 (8)Rev: 0CONTENTS8.0催化剂处理38.1催化剂处理38.2催化剂装载38.2.1筛选38.2.2取样48.2.3合成气净化槽48.2.4甲醇反应器58.3催化剂卸载88.3.1合成气净化槽88.3.2甲醇反应器88.3.3甲醇反应器催化剂氧化88.4催化剂保护11CATALYST HANDLING 2231-00-T2-M1 (8)Rev: 08.0 催化剂处理8.1 催化剂处理通常,催化剂要供应到金属槽或IBCs(中型散装容器)中。
催化剂应该储存在干燥建筑,然而,在环境不允许的情况下,要放置在木制托盘上,并严密覆盖以保持干燥。
在装载之前,密封盖要一直盖在槽上。
开放槽在检测和抽样检验完毕后,要重新密封。
要尽可能谨慎地处理催化剂。
减少对槽的重复处理,不能滚动槽,为此要提供适当的设备。
催化剂颗粒不能落在以下段落指定的距离之外。
清空槽时,轻微倾斜可限制排放流量。
需要进入催化剂容器内时,可使用木板。
8.2 催化剂装载根据正常操作下催化剂的物理性质和流动模式,不同的装载技术用于装置中的每个催化剂。
例如,易碎的催化剂要求轻柔的装载方法,而坚硬的催化剂通常可以采用漏斗装载。
在装载前,由调试工程师检验容器,并将在现场检测工艺目标是否贯彻到物理设备上。
热电阻组件通常是比较活跃的部分,不合格的安装会降低运行质量。
对于手孔中的催化剂滞留装置,需检测需检测催化剂排放喷嘴和人行通道。
甲醇催化剂在还原和使用中的注意事项
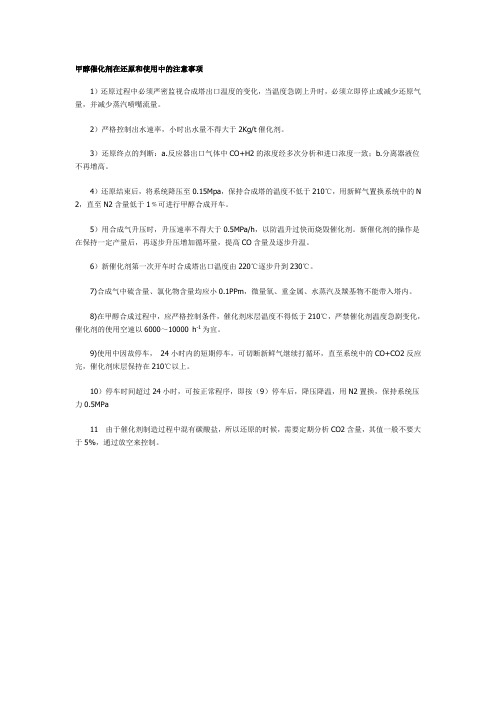
甲醇催化剂在还原和使用中的注意事项
1)还原过程中必须严密监视合成塔出口温度的变化,当温度急剧上升时,必须立即停止或减少还原气量,并减少蒸汽喷嘴流量。
2)严格控制出水速率,小时出水量不得大于2Kg/t催化剂。
3)还原终点的判断:a.反应器出口气体中CO+H2的浓度经多次分析和进口浓度一致;b.分离器液位不再增高。
4)还原结束后,将系统降压至0.15Mpa,保持合成塔的温度不低于210℃,用新鲜气置换系统中的N 2,直至N2含量低于1﹪可进行甲醇合成开车。
5)用合成气升压时,升压速率不得大于0.5MPa/h,以防温升过快而烧毁催化剂。
新催化剂的操作是在保持一定产量后,再逐步升压增加循环量,提高CO含量及逐步升温。
6)新催化剂第一次开车时合成塔出口温度由220℃逐步升到230℃。
7)合成气中硫含量、氯化物含量均应小0.1PPm,微量氧、重金属、水蒸汽及羰基物不能带入塔内。
8)在甲醇合成过程中,应严格控制条件,催化剂床层温度不得低于210℃,严禁催化剂温度急剧变化,催化剂的使用空速以6000~10000 h-1为宜。
9)使用中因故停车,24小时内的短期停车,可切断新鲜气继续打循环,直至系统中的CO+CO2反应完,催化剂床层保持在210℃以上。
10)停车时间超过24小时,可按正常程序,即按(9)停车后,降压降温,用N2置换,保持系统压力0.5MPa
11 由于催化剂制造过程中混有碳酸盐,所以还原的时候,需要定期分析CO2含量,其值一般不要大于5%,通过放空来控制。
甲醇无火焰制热催化剂
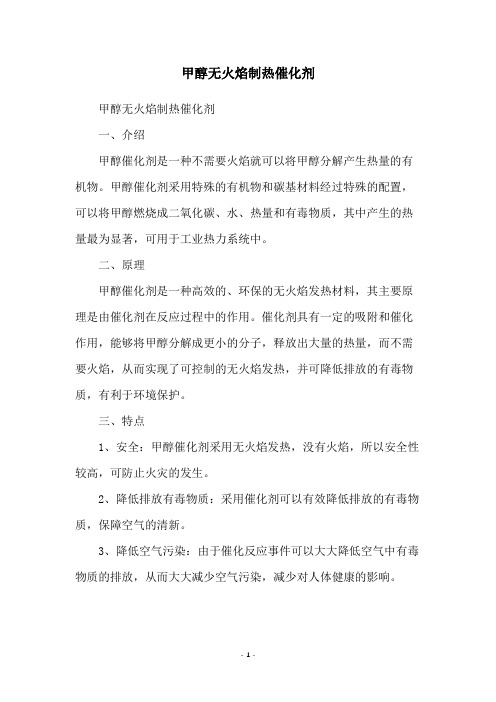
甲醇无火焰制热催化剂
甲醇无火焰制热催化剂
一、介绍
甲醇催化剂是一种不需要火焰就可以将甲醇分解产生热量的有机物。
甲醇催化剂采用特殊的有机物和碳基材料经过特殊的配置,可以将甲醇燃烧成二氧化碳、水、热量和有毒物质,其中产生的热量最为显著,可用于工业热力系统中。
二、原理
甲醇催化剂是一种高效的、环保的无火焰发热材料,其主要原理是由催化剂在反应过程中的作用。
催化剂具有一定的吸附和催化作用,能够将甲醇分解成更小的分子,释放出大量的热量,而不需要火焰,从而实现了可控制的无火焰发热,并可降低排放的有毒物质,有利于环境保护。
三、特点
1、安全:甲醇催化剂采用无火焰发热,没有火焰,所以安全性较高,可防止火灾的发生。
2、降低排放有毒物质:采用催化剂可以有效降低排放的有毒物质,保障空气的清新。
3、降低空气污染:由于催化反应事件可以大大降低空气中有毒物质的排放,从而大大减少空气污染,减少对人体健康的影响。
- 1 -。
- 1、下载文档前请自行甄别文档内容的完整性,平台不提供额外的编辑、内容补充、找答案等附加服务。
- 2、"仅部分预览"的文档,不可在线预览部分如存在完整性等问题,可反馈申请退款(可完整预览的文档不适用该条件!)。
- 3、如文档侵犯您的权益,请联系客服反馈,我们会尽快为您处理(人工客服工作时间:9:00-18:30)。
合成甲醇催化剂
摘要:法合成甲醇催化剂现在使用较多的是Cuo.Zno—A120,为主要组成的铜基催化剂,同时还有LC308型甲醇催化剂的锌—铬系催化剂等。
催化剂是甲醇生产中一个重点控制对象,催化剂使用的好与坏直接决定着装置的运行质量和经济效益,本文对甲醇催化剂进行了介绍,,对生产中如何使用好催化剂的问题展开论述。
关键词: 甲醇; 催化剂; 寿命; 改进
甲醇是重要的有机化学品和基础化工原料, 在新能源战略中具有举足轻重的作用。
现在我国富煤、贫油、少气,且资源分布极其不均衡, 据资料统计, 2007 年, 我国煤炭探明储量为1. 08万亿吨, 约占世界探明储量的12. 6% , 居世界第三位, 产量和消费量分别为21. 9亿吨和21. 4亿吨, 分别占世界总量的35. 7% 和36. 9% , 均居世界第一位, 原油和天然资源所占世界比例仅为1. 4% 和1. 2% 。
煤炭的清浩化工利用己确定为我国新能源战略, 以煤炭出发经合成气生产甲醇、醇醚燃料、燃料电池燃料或以甲醇为原料进一步生产烯烃、醋酸和二甲醚等基础有机化学品被公认是技术可靠、工业化应用成熟的非石油路线生产有机化学品的先进工艺技术。
作为有机产品合成的源头产业链, 甲醇工业在近几年得到了迅猛发展。
据中国石化工业协会数据,2007年, 我国共有甲醇生产企业177 家,2008年底我国甲醇产能达到了28 510 kt,国内能够于2010年年底前投产的甲醇在建项目共有25 个。
CO加氢合成甲醇是应用广泛的甲醇合成方法,无论是早期的高温高压法合成技术还是近几年发展起来的低温低压法技术, 催化剂一直是甲醇合成工艺的关键技术。
(1)铜基催化剂
德国BASE公司于1923年首先开发成功了锌铬(ZnO/Cr20,)催化剂,其操作温度590 K 一670 K,操作压力25 MPa一35 MPa,被称为高压催化剂。
1966年以前,世界上几乎所有的甲醇合成厂家都使用该类催化剂。
我国于1954年开始建立甲醇工业,当时也使用锌铬催化剂。
目前,锌铬催化剂已逐渐被淘汰。
从20世纪50年代开始,很多国家着手进行低压甲醇催化剂的研究工作。
1966年以后,由英国ICI公司和Lurgi公司先后研制成功了铜基催化剂。
铜基催化剂是一种低压催化剂,主要组分为CuO/ZnO/A1203,操作温度为500 K~530 K,压力却只有5 MPa一10 MPa,比传统的合成温度低很多,对甲醇合成反应平衡有利。
目前,甲醇合成催化剂总的发展趋势是由高压向低、中压发展,而低、中压流程所用的催化剂都是铜基催化剂。
铜基催化剂系列品种较多,有铜锌铬系(Cuo/ZnO/Cr203)、铜锌铝系(CuO/ZnO/A1203)、铜锌硅系(CuO/ZnO/Si203)、铜锌锆系(CuO/ZnO/ZrO)等。
目前,有使用经验的
型号包括国产的C301、C302、C303和NC501,英国的ICl5l—l或ICl51-3,前苏联的CHM.1或CHM-3,丹麦托布索的MK-101,德国巴斯夫的$3-86和13本三菱的M-5等。
这些铜基催化剂同原高压法使用的zn—Cr催化剂相比,具有活性温度低、选择性好、使用温度低的特点,通常工作温度为220℃一300℃、压力为5.0 MPa一10.0 MPa。
但是,铜基催化剂的耐高温性和抗毒性均不如zn·cr甲醇催化剂。
低压法合成甲醇催化剂主要是CuO-ZnO—A120,为主要组成的催化剂,其三部分的作用各不相同。
在合成甲醇时,一氧化碳在铜催化剂表面的吸附率相当高,氢的吸附率则比一氧化碳小得多;ZnO是很好的氢化剂,使氢吸附和活化,因此提高了铜基催化剂的转化率。
实验证实,纯铜对甲醇合成是没有活性的。
催化理论认为,氢和一氧化碳合成甲醇的反应是在一系列活性中心上进行的,这种活性中心存在于被还原的Cu —CuO界面上。
在催化剂中加入少量的AI:0,,其首要功能就是阻止一部分氧化铜还原。
当催化剂被还原后的初期,合成气中的氢和一氧化碳成为还原剂,有使氧化铜进一步还原的趋势。
这种过度的还原,使得活性中心存在的界面越来越小,催化剂活性则越来越低。
从整个合成过程来看,随着还原表面向催化剂的内层深入,未还原的核心越来越小,作为Cu—CuO 界面的核心表面积也越来越小,合成反应速率随之降低,直到反应热不能补充气体所带走的热量时,催化剂就失去了继续使用的价值。
但原料气中某些组分与催化剂发生作用,使其组成结构发生变化,导致催化剂活性降低甚至失去活性。
由氧及含氧化合物引起的中毒,可以通过重新还原使催化剂恢复活性,这叫暂时性中毒。
由S、CI及一些重金属或碱金属、羰基铁、润滑油等物质引起的中毒,使催化剂原有的性质和结构彻底发生改变,催化活性不能再恢复,称为永久性中毒。
S、cl与催化剂中的Cu作用生成无活性物质CuS和CuCI:;而油受热析出炭,堵塞催化剂的活性中心,从而引起催化剂活性下降。
由于铜基催化剂的第二大弱点是耐热性较差,因此,一方面应当提高合成气中的二氧化碳含量,因为它与氢气合成甲醇时会生成1个摩尔的水,有利于避免局吝捧过热;另一方面,应尽量控制合成气中的氧含量,否则合成气中所含的少量氧会进人催化剂床层,使还原好的金属迅速氧化,放出大量的热。
因此,控制合成气中的氧含量,避免催化剂过热,对于延长催化剂的寿命是非常必要的。
(2)LC308型甲醇催化剂
西北化工研究院于20世纪90年代开展了以铜-锌- 铝为基础的甲醇催化剂的研究, 通过对催化剂组成、前驱体制备技术、物相结构、沉淀剂、加料方式及制备条件等因素的研究, 从催化剂小试、中试到工厂模拟侧线试验等逐级放大试验, 相继开发出LC210 型联醇催化剂和LC308 型甲醇催化剂。
LC308型甲醇催化剂性能:黑色圆柱体, 规格5mm * ( 4~ 5) mm, 侧压强度180 N•cm- 1, 堆积密度( 1. 38~ 1. 40) kg•L- 1, 比表面积> 60 m2 •g-。
在原有催
化剂研究基础上, 对甲醇催化剂的制备工艺进行了优化改进: ( 1) 研究了锌铝尖晶石对催化剂的影响, 通过不断完善载体制备工艺, 制备出更合适的锌铝尖晶石载体; ( 2) 通过改进铜锌共沉淀母液制备工艺条件, 采用性能较佳的沉淀剂, 选择适宜的沉淀温度、pH、热煮时间和老化温度等条件,使活性组分铜锌之间的协同作用增强; ( 3) 采用分步法共沉淀催化剂制备工艺, 提高了活性组分的分散度, 改善了催化剂孔结构和有效比表面积等物化指标, 使催化剂活性有较大幅度提高; ( 4) 研究助剂对催化剂的影响, 实验表明, 添加结构助剂或活性助剂, 可以在一定程度上提高催化剂活性和选择性, 延长催化剂使用寿命。
改进型LC308型甲醇催化剂和国内外新型甲醇催化剂性能相当, 达到了国内先进水平。
我国新能源战略为甲醇工业的发展提供了发展机遇, 加强催化剂技术的研究, 开发适合大型化和节能型甲醇装置的新型催化剂, 为甲醇工业的发展提供强有力的技术支撑。
采用新制备工艺生产的新型LC308型甲醇催化剂比早期开发的甲醇催化剂活性和稳定性都有大的提高, 可应用于大型甲醇生产装置。
(3)实际运行中催化剂需改进方面
①合成塔前需有保护床或其他气体净化设备无论是保护床、过滤器,还是内装脱除催化剂的分离器、净化器,其目的都是为了保证将进入催化剂床层的气体进行有害介质的脱除和分离,以利于吸收微量的毒物,并且在工况波动时能起到缓冲和吸收毒物的效果,把容易造成催化剂中毒或降低催化剂活性的介质阻挡在合成塔前,禁止这些物质进入合成塔内部而逐渐损害催化剂。
②装置建成后的系统净化装置建成进行试开车时,需进行系统吹扫和清理等试开车工作,使管道内的铁锈和焊渣等毒物清理干净,以免进行生产时这些毒物杂质会随着气体进入到催化剂床层,进而损害催化剂活性,造成催化剂活性降低及产品质量下降,并避免对系统运行产生不利影响。
③系统运行时的气体净化整个系统运行时,对于系统的气体质量,要做好监控,精心操作,把气体的成分指标控制好,尤其要在气体成分超标时,按照紧急预案进行放空处理,防止不合格的气体、严禁有毒介质进入催化剂床层。
④严禁工况大幅度波动运行中的工况调整要引起重视,运行初期需控制好CO 含量,严禁CO 含量高,否则会使催化剂局部过热而降低使用寿命; 控制好温度、温差、压力、压差和空速等指标,温度和压力的升降速率要按照指标进行,温度和压力超标会使催化剂寿命和活性降低、甚至粉化; 精心控制整个系统的操作,减少开停车次数,每次开停车温度和压力等工况会大幅波动,对催化剂的损伤严重; 严禁入塔气带液,防止入塔甲醇含量超标,严
禁甲醇液体带入催化剂床层。
⑤系统停车时做好保护在系统进行停车时要做好催化剂的保护工作,按照规定的降温和降压速率降低到指标后,进行系统置换,停车后定期取样分析,对催化剂进行氮气惰性气的正压保护。
严禁催化剂表面有反应气体存在,要保证气体循环反应完毕、置换彻底,不留死角,与其他系统可靠隔离,严禁反应气体进入合成塔,以免使催化剂报废。
(4)结语
甲醇催化剂的使用与国外催化剂相比有差距,说明还有很大开发潜力及提升空间,在今后的实际项目建设及运行中,需不断总结经验、汲取教训、共同提高。
参考文献:
[1]王桂茹.催化剂与催化作用[M].大连: 大连理工大学出版社, 2004.
[2]刘方斌.我们拿什么来抗衡中东甲醇[N].中国化工报,2010 - 06 - 23.
[3] 董松. 甲醇生产、市场及竞争力分析[ J]. 上海化工,2010, 35( 6): 6.
[4]高俊文. 联醇催化剂和合成甲醇催化剂的研制[ J]. 化肥设计, 2005, 43( 4): 2.。