公差原则的应用
公差独立原则的应用场合
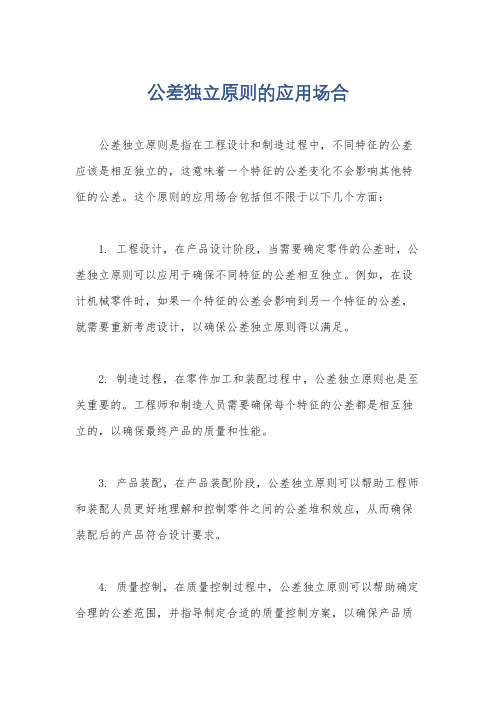
公差独立原则的应用场合
公差独立原则是指在工程设计和制造过程中,不同特征的公差应该是相互独立的,这意味着一个特征的公差变化不会影响其他特征的公差。
这个原则的应用场合包括但不限于以下几个方面:
1. 工程设计,在产品设计阶段,当需要确定零件的公差时,公差独立原则可以应用于确保不同特征的公差相互独立。
例如,在设计机械零件时,如果一个特征的公差会影响到另一个特征的公差,就需要重新考虑设计,以确保公差独立原则得以满足。
2. 制造过程,在零件加工和装配过程中,公差独立原则也是至关重要的。
工程师和制造人员需要确保每个特征的公差都是相互独立的,以确保最终产品的质量和性能。
3. 产品装配,在产品装配阶段,公差独立原则可以帮助工程师和装配人员更好地理解和控制零件之间的公差堆积效应,从而确保装配后的产品符合设计要求。
4. 质量控制,在质量控制过程中,公差独立原则可以帮助确定合理的公差范围,并指导制定合适的质量控制方案,以确保产品质
量稳定性和可靠性。
总之,公差独立原则的应用场合涵盖了工程设计、制造过程、
产品装配和质量控制等多个方面,对于确保产品质量和性能具有重
要意义。
在实际工程中,工程师和制造人员需要严格遵守这一原则,以确保产品能够满足设计要求并具有良好的可靠性和稳定性。
公差原则
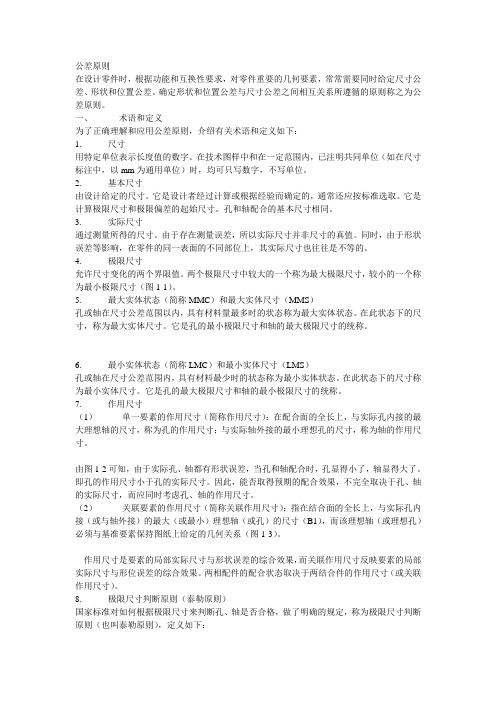
公差原则在设计零件时,根据功能和互换性要求,对零件重要的几何要素,常常需要同时给定尺寸公差、形状和位置公差。
确定形状和位置公差与尺寸公差之间相互关系所遵循的原则称之为公差原则。
一、术语和定义为了正确理解和应用公差原则,介绍有关术语和定义如下:1. 尺寸用特定单位表示长度值的数字。
在技术图样中和在一定范围内,已注明共同单位(如在尺寸标注中,以mm为通用单位)时,均可只写数字,不写单位。
2. 基本尺寸由设计给定的尺寸。
它是设计者经过计算或根据经验而确定的,通常还应按标准选取。
它是计算极限尺寸和极限偏差的起始尺寸。
孔和轴配合的基本尺寸相同。
3. 实际尺寸通过测量所得的尺寸。
由于存在测量误差,所以实际尺寸并非尺寸的真值。
同时,由于形状误差等影响,在零件的同一表面的不同部位上,其实际尺寸也往往是不等的。
4. 极限尺寸允许尺寸变化的两个界限值。
两个极限尺寸中较大的一个称为最大极限尺寸,较小的一个称为最小极限尺寸(图1-1)。
5. 最大实体状态(简称MMC)和最大实体尺寸(MMS)孔或轴在尺寸公差范围以内,具有材料量最多时的状态称为最大实体状态。
在此状态下的尺寸,称为最大实体尺寸。
它是孔的最小极限尺寸和轴的最大极限尺寸的统称。
6. 最小实体状态(简称LMC)和最小实体尺寸(LMS)孔或轴在尺寸公差范围内,具有材料最少时的状态称为最小实体状态。
在此状态下的尺寸称为最小实体尺寸。
它是孔的最大极限尺寸和轴的最小极限尺寸的统称。
7. 作用尺寸(1)单一要素的作用尺寸(简称作用尺寸):在配合面的全长上,与实际孔内接的最大理想轴的尺寸,称为孔的作用尺寸;与实际轴外接的最小理想孔的尺寸,称为轴的作用尺寸。
由图1-2可知,由于实际孔、轴都有形状误差,当孔和轴配合时,孔显得小了,轴显得大了。
即孔的作用尺寸小于孔的实际尺寸。
因此,能否取得预期的配合效果,不完全取决于孔、轴的实际尺寸,而应同时考虑孔、轴的作用尺寸。
(2)关联要素的作用尺寸(简称关联作用尺寸);指在结合面的全长上,与实际孔内接(或与轴外接)的最大(或最小)理想轴(或孔)的尺寸(B1),而该理想轴(或理想孔)必须与基准要素保持图纸上给定的几何关系(图1-3)。
公差原则在零件设计中的应用与分析
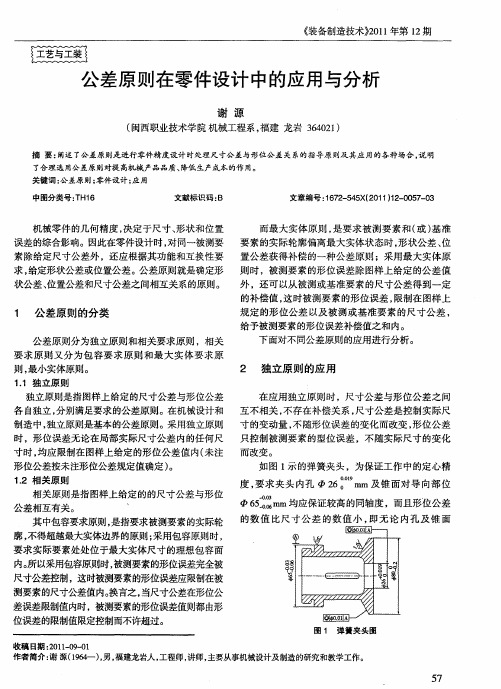
5 8
《 装备制造技术)o 1 ) l 年第 1 期 2 2 后达 到较高的配合性质要求 的零件 ,采用关联要 素 寸公差与形位公差综合的结果。 的包容原则 , 既可以保证两方面的要求, 又可以利用尺 寸公差对形位公差的补偿而便于制造。虽然有时实际 形位误差值超过设计值 , 但综合考虑其尺寸公差与形 位公差两者的相互作用 , 还是符合设计要求的。 如图 4 所示 的皮带轮与轴 的装配 ,以及机床 中
图 2 导 向零 件 图
3 m 圆柱部位处于最大实体尺寸时 , 3 m轴 5 m 5 m 线 与 M2 5螺纹 轴线垂 直度必 须 为零 ,当 3 m 2× 5 m 圆柱部位偏离最大实体尺寸时才允许两轴线间垂直度
未注形位公差视为独立原则 ,主要应用在零件 误差存在 , 最大为 0 1 m, 时虽然垂直度误差大 .6 0 m 这 对形位公差要求较低的场合 ,这些部位 的形位公差 于设计上的 0 1 m, . 但却能够保证设计上的要求 。 Om 可 以通过尺寸公差加 以控制 ,或者可以在加工工艺 当按 M 2 5 2 × 螺纹轴线 装配后将使 3 m 圆 5m 过程加 以控制 ,其数值按未注形位公差规定 的数值 柱部位轴线垂直度误差达到 0 1 m,垂直度误 .6 0 m
体原则。 如 图 5所示 ,可知当槽与螺钉 尺寸均处于最小
实体 尺寸时 ,定位槽 对导 向外 圆对 称度虽增 大至 0 6 m, . 但考虑尺寸公差和形 位公差 的综 合作用 的 2m
偏转量 ,仍然不超过设计上允许 的偏转量 04 m, . m 2 这样利用尺寸公差对形位公差进行补偿 ,以扩大形 位公差值 , 方便了制造。 像机器上 的法兰和箱体端盖上 的螺孑 ,往往主 L 要是达到螺栓的互换性装配 ,而对配合性 质并不要
尺寸标准公差

尺寸标准公差尺寸标准公差是指在工程设计和制造过程中,为了保证零件尺寸的精度和质量,对尺寸公差进行规定和控制的一种技术要求。
尺寸标准公差的合理选择和应用,对于提高产品的质量、降低成本、提高生产效率具有重要意义。
本文将就尺寸标准公差的概念、作用、选择原则和应用进行详细介绍。
一、尺寸标准公差的概念。
尺寸标准公差是指在设计图纸上规定的尺寸公差,用来限制零件尺寸的变化范围。
在实际生产中,由于加工误差、测量误差和材料性能的不均匀性等因素的影响,零件的尺寸很难完全符合设计要求。
因此,必须在设计图纸上规定一定的尺寸公差,以保证零件在加工和装配过程中的质量要求。
二、尺寸标准公差的作用。
1. 保证零件的互换性。
在一定的尺寸公差范围内,不同厂家生产的零件可以互相替换使用,提高了零部件的通用性和标准化水平。
2. 控制零件的加工精度。
尺寸标准公差的设置可以指导加工工艺和工艺装备的选择,保证零件的加工精度和表面质量。
3. 降低生产成本。
合理的尺寸标准公差可以减少对加工精度的要求,降低了加工难度和成本。
4. 提高产品质量。
通过尺寸标准公差的控制,可以减少零件的尺寸变化范围,提高了产品的质量稳定性和可靠性。
三、尺寸标准公差的选择原则。
1. 根据零件的功能和使用要求确定。
对于需要密封、传动、定位等功能的零件,应选择较小的尺寸公差;对于外形尺寸较大、结构简单的零件,可以适当放宽尺寸公差。
2. 考虑加工工艺和设备能力。
在选择尺寸标准公差时,必须考虑到加工设备的精度和加工工艺的可行性,避免因尺寸公差过小而导致加工难度和成本的增加。
3. 综合考虑经济性和可靠性。
在确定尺寸标准公差时,必须综合考虑产品的使用要求、生产成本和市场竞争力,寻求经济效益和产品质量的最佳平衡点。
四、尺寸标准公差的应用。
1. 在设计图纸上明确规定。
设计人员在绘制零件图纸时,必须根据零件的功能和使用要求,合理选择和规定尺寸标准公差,确保零件的质量和可靠性。
2. 在加工过程中严格控制。
公差原则应用及答疑
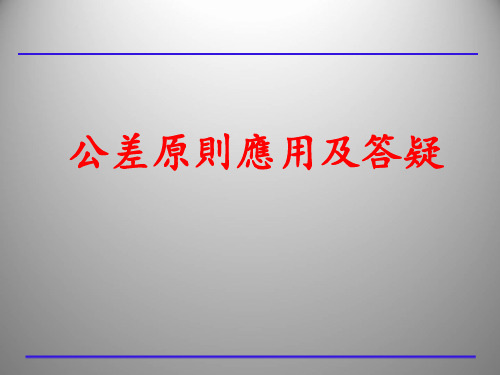
一、術語及其意義
6.實效尺寸
最大實體實效尺寸(MMVS) 最大實體實效狀態下 的體外作用尺寸,稱為最大實體實效尺寸。
單一要素:DMV、dMV 關聯要素:D′MV、d′MV
最小實體實效尺寸(LMVS) 最小實體實效狀態下 的體內作用尺寸,稱為最小實體實效尺寸。
單一要素:DLV、dLV 關聯要素:D′LV、d′LV。
可逆要求
一、術語及其意義
1.局部實際尺寸(Da,da)
指在實際要素的任意正截面上,兩對應點之間測得的距 離。
一、術語及其意義
2.作用尺寸
體外作用尺寸 指在被測要素的給定長度上,與實際內 表面(孔)體外相接的最大理想面,或與實際外表面(軸) 體外相接的最小理想面的直徑或寬度。
單一要素體外作用尺寸
一、術語及其意義
單一要素 在尺寸公差帶後 加注 E
用於被測要 素時
用於基準要 素時
在形位公差框格第二格 公差值後加 M
在形位公差框格相應的 基準要素後加 M
一、術語及其意義
4.實體尺寸
最大實體尺寸(MMS) 實際要素在最大實體狀態下 的極限尺寸,稱為最大實體尺寸。
孔和軸的最大實體尺寸分別用 DM、dM表示。
DM
= Dmin;dM = dmax。
最小實體尺寸(LMS) 實際要素在最小實體狀態下
的極限尺寸,稱為最小實體尺寸。
孔和軸的最小實體尺寸分別用DL、 dL 表示。 DL = Dmax;dL= dmin。
對一批零件而言,每個零件都不一定相同,但每個 零件的體外或體內作用尺寸只有一個。
對於被測實際軸,dfe≥dfi; 對於被測實際孔,Dfe≤Dfi。
一、術語及其意義
3.實體狀態
最大實體狀態(MMC) 實際要素在給定長度上處處 位於極限尺寸之內,並具有材料量最多時的狀態,稱 為最大實體狀態。
公差原则中相关要求的分析及应用

( ) 一 学习型 图书馆是主动、 协作式的馆 员继续教 育模式
所 谓学 习型 图书馆 , 指 能够 敏 锐地 观 察到 图书 馆 内外 环 境 的 是
各种变 化 , 通过 制度化 和有 组织 的形式 捕获 信 息 , 理 和使 用各 种知 管 识和技 术 , 并对 各种 变化及 时作 出调整 , 得图 书馆 作为 一个 整 体 系 使
L —
I _ _
理越过舞 f 鞋
蚓
体垃 )
坪搬曲
f 盛 奄 协4 他 ’
艘 b
)
() 2 当轴 的局部 实际 尺 寸处 于最 大 实体 尺 寸与 最 小实 体 尺寸 之
间, d 即 =I9 8时 ; 1. 对 于图 1 实 际 尺寸 没 有 充满 最 大 实体 尺 寸 形 成 的 整 个边 界 区 ,
引 言 公 差原则 …是用 来处 理 尺 寸 公差 与形 位 公差 之 间 关 系 的方 法 。
一
、
≤ D ; D =D
~
外 表面 ( ) ≤d = 一 十t d d = d ) 轴 d d 且 = ~ d = 。
4 含义 不 同” 、 () 1 当轴 的局部实 际 尺寸处 处 为最 大实 体 尺 寸 , d d 即 . =Io 2
d l I2 —Io 1 = o 1 见 示意 图 b 。 =, f o 2 . l I . ( )
一
一 - I
一 ・…
…
一
一
i
一 一…一
一
理想边界 ( 晟太实体边界)
理甚边羿 r 太空体实教边徉) 最
一
星盘瘩 盛
土
照 俘 蕊 埘 t 蔓 ,
1
第六节公差原则与实例分析

第六节公差原则与实例分析公差原则是指在产品设计与制造中,为了保证产品的质量和相互替换的可行性,针对不同的零部件和工艺要求制定适当的公差范围。
公差原则是实现产品交货质量的保证,同时也是确保产品生产制造的可行性的基础。
以下将通过实例分析来说明公差原则的具体应用。
首先,我们以一家汽车制造公司的生产线为例。
在汽车制造过程中,涉及到各种零部件的加工与安装,每个零部件都有其特定的公差范围。
例如,在车轮与车轴的安装过程中,需要考虑车轮与车轴的匹配度,确保安装后的车轮能够正常转动且不会出现偏差。
为此,汽车制造公司需要制定车轮与车轴的公差范围,例如车轮直径与车轴直径之间的公差为±0.1mm,以保证车轮能够在安装后的车轴上正常运转。
其次,我们以手机制造公司的生产线为例。
在手机制造过程中,涉及到各种零部件的加工与组装,如屏幕、电池、摄像头等。
每个零部件都有其特定的公差范围。
例如,在手机屏幕的制造过程中,需要考虑屏幕的大小、厚度以及显示效果等因素。
为此,手机制造公司需要制定屏幕尺寸与厚度的公差范围,以确保不同批次的屏幕能够正常安装在手机上,并且显示效果一致。
此外,公差原则还可应用于其他领域,如家电制造、航空航天、机械制造等。
在家电制造中,例如电视机的组装过程中需要考虑屏幕的尺寸、显示效果、音质等因素,为此需要制定相应的公差范围。
在航空航天领域中,飞机的液压系统需要涉及到各种油管的连接与安装,为了确保油管的密封性和可靠性,需要制定油管的公差范围。
在机械制造中,例如机器零件的加工与组装过程中需要考虑零件的尺寸、配合度等因素,制定适当的公差范围确保零件的互换性和装配的可行性。
综上所述,公差原则在产品设计与制造过程中起到了至关重要的作用。
通过合理制定公差范围,可以保证产品质量,提高产品的可替换性和互换性。
不同的产品领域和行业在应用公差原则时需要考虑不同的因素和要求,制定相应的公差范围。
通过实例分析,我们可以看到公差原则的具体应用,为产品交付的质量提供了保证。
《公差原则》标准的分析及应用-最小实体要求和可逆要求

《航 天 标 准 化 》 在 2006 年 第 4 期 [ 1] 和 2007 年第 3 期 [2] 上 分 别 介 绍 了 公 差 原 则 中 的 独 立 原 则、包容要求和最大要求。本文应用工程中的 示例阐述了公差原则中其余的最小实体要求和 可逆要求的概念、图样标注方法及其在工程中
对 于 内 表 面 ( 孔 ) : Dfi≤DLV=DL+t=Dmax+t, 且 Da≥DM=Dmin;
+0 .25
!8 0 !0.4 + A
!8.65 ( DLV)
6 A
f=t=!0.4 6
2.1.2 最小实体要求应用于被测要素的含义 最小实体要求应用于被测要素时, 图样上标
注的形位公差值是被测要素处于最小实体状态下 给出的公差值, 并且用最小实体实效边界控制该 要素的实际尺寸和形位误差。即被测要素的体内 作用尺寸不得超越其最小实体实效尺寸, 实际尺 寸不得超出其极限尺寸。当实际尺寸偏离最小实 体尺寸的条件下, 允许被测要素的尺寸公差补偿 其形位公差, 其补偿关系可用下例说明。
b) 基准要素的实际尺寸不得超出其极限尺 寸的范围。 2.3 最小实体要求的应用
最小实体要求主要应用于以下两种情况。 a) 在产品零件设计中, 为了保证实际壁厚 大于最小极限值的强度要求 ( 如图 1 和图 2 示 例) , 不能采用独立原则, 因其允许的位置公差 值是不变的, 它不能充分利用尺寸公差, 带来最 佳的经济效益; 也不能采用最大实体要求来实现 同时保证被测要素所要求的位置公差和最小壁 厚; 而只有采用最小实体要求, 方可达到壁厚的 设计要求。 b) 为了控制零件表面至中心要素的最大距 离等功能要求, 如图 3 所示, 应用最小实体要求 来限制转盘槽的侧面至理想中心平面的最大 距离。
形位公差,公差原则与应用
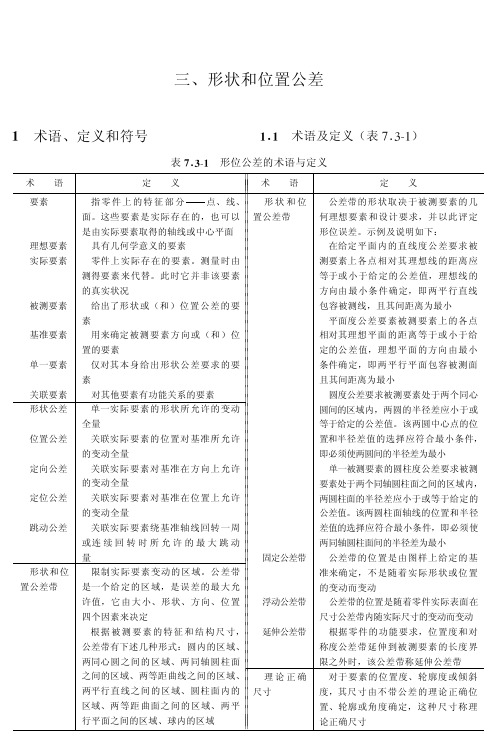
最大实体 状态
最大实体 尺寸
最小实体 状态
最小实体 尺寸
最大实体 实效状态
理想基准要素的简称,它是确定要 最 大 实 体 素间几何系的依据,分别称为基准点, 实效尺寸 基准直线( 轴 线 ) 和 基 准 平 面 (中 心 平面)
作为单一基准使用的单个要素
作为单一基准使用的一组要素
最小实体 实效状态
测量被测实际要素上具有代表性的 参数(即特征 参 数 ) 来 表 示 形 位 误 差 值
被测实际要素绕基准轴线回转过程 中,沿 给 定 方 向 测 量 其 对 某 参 考 点、 或线的 变 动 量。 变 动 量 是 指 指 示 器 最 大与最小读数之差
检测被测实际要素是否超过实效边 界,以判断合格与否
三、形状和位置公差
%+*
表!"#!# 被测要素、基准要素的标注及其他附加符号(摘自 "#/$%%&’—%(())
项目
符号
项目
符号
项目
符号
直接 被测要素的标注
用字母
理论正确尺寸
*+
包容要求
可逆要求 延伸公差带
基准要素的标注
最大实体要求
自由状态 (非刚性零件)条件
!!!!!!!!!!!!!!!!!!!!!!!!!!!!!!!!!!!!!!!!
或连 续 回 转 时 所 允 许 的 最 大 跳 动
量
固定公差带
限制实际要素变动的区域。公差带
是一个 给 定 的 区 域, 是 误 差 的 最 大 允
许值,它由大小、形 状、方向、位 置 浮动公差带
四个因素来决定
根 据 被 测 要 素 的 特 征 和 结 构 尺 寸, 延伸公差带
三种公差原则 -回复

三种公差原则-回复三种公差原则是工程建设和制造业中的关键概念,用于确保产品和结构的质量和精度达到特定的要求。
公差是指允许产品或结构尺寸、形状等特性的变化范围。
下面将一步一步回答中括号内的主题,详细介绍三种公差原则。
一、什么是公差?公差是在工程或制造过程中,为了满足产品和结构的设计要求而允许的尺寸、形状等特性的变化范围。
公差的存在可以弥补制造误差和材料特性的不确定性,使产品和结构的尺寸能够在设计要求的允许范围内进行波动。
二、为什么需要公差?工程建设和制造过程中,难免会出现制造误差或材料特性的不确定性。
如果没有公差的存在,任何微小的误差或波动都会导致产品或结构无法满足设计要求。
而公差的引入能够确保产品和结构在实际加工过程中能够实现设计要求,达到预期的质量和精度。
三、公差的种类公差可以根据其作用和适用范围分为三种类型:基本偏差、限制偏差和配合偏差。
1. 基本偏差基本偏差是一组与公差带上、下限无关的数值。
它是设计者根据产品或结构的功能和使用要求而决定的,通常由制造精度、材料特性和使用环境等因素决定。
基本偏差是用来定义尺寸偏差的起点,在制造或测量过程中,通过将基本偏差与公差带上、下限相加或相减,可以得到具体的尺寸公差。
2. 限制偏差限制偏差是指与产品或结构的功能和装配要求密切相关的公差。
它是根据产品或结构的使用要求和装配要求而决定的。
限制偏差规定了可接受的最大偏差值或范围,确保在装配和使用过程中,产品和结构的性能和功能不受影响。
3. 配合偏差配合偏差是指两个或多个相互连接的零件之间所允许的尺寸差异。
它是为了实现特定的配合要求而设定的。
配合偏差规定了两个或多个部件之间的尺寸工差,确保装配过程中的相互配合和运动要求得到满足。
四、公差原则的应用公差原则在工程建设和制造过程中的应用非常重要,能够保证产品和结构的质量和精度。
1. 公差原则的一致性公差原则要求在整个制造过程中,从零件设计、加工到装配,各个环节的公差都要一致和相互协调。
公差的十分之一原则
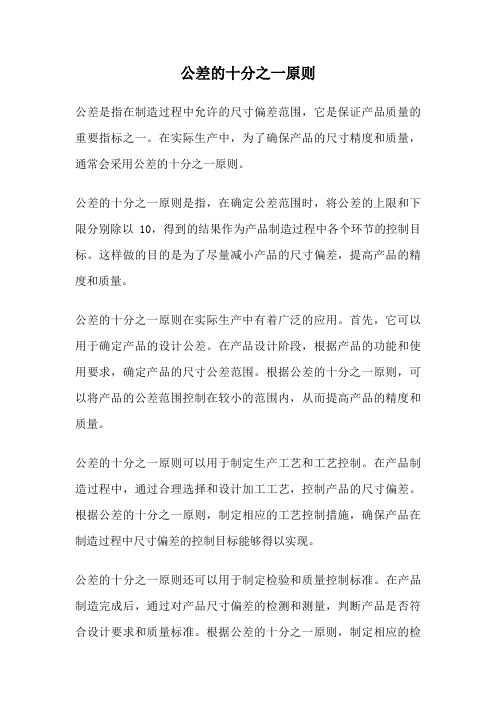
公差的十分之一原则公差是指在制造过程中允许的尺寸偏差范围,它是保证产品质量的重要指标之一。
在实际生产中,为了确保产品的尺寸精度和质量,通常会采用公差的十分之一原则。
公差的十分之一原则是指,在确定公差范围时,将公差的上限和下限分别除以10,得到的结果作为产品制造过程中各个环节的控制目标。
这样做的目的是为了尽量减小产品的尺寸偏差,提高产品的精度和质量。
公差的十分之一原则在实际生产中有着广泛的应用。
首先,它可以用于确定产品的设计公差。
在产品设计阶段,根据产品的功能和使用要求,确定产品的尺寸公差范围。
根据公差的十分之一原则,可以将产品的公差范围控制在较小的范围内,从而提高产品的精度和质量。
公差的十分之一原则可以用于制定生产工艺和工艺控制。
在产品制造过程中,通过合理选择和设计加工工艺,控制产品的尺寸偏差。
根据公差的十分之一原则,制定相应的工艺控制措施,确保产品在制造过程中尺寸偏差的控制目标能够得以实现。
公差的十分之一原则还可以用于制定检验和质量控制标准。
在产品制造完成后,通过对产品尺寸偏差的检测和测量,判断产品是否符合设计要求和质量标准。
根据公差的十分之一原则,制定相应的检验标准和质量控制措施,确保产品的尺寸精度和质量。
公差的十分之一原则的应用可以有效地提高产品的质量和精度。
通过合理地控制产品的尺寸偏差,可以减小产品的尺寸误差,提高产品的相互替换性和可靠性。
同时,公差的十分之一原则也可以提高生产过程的稳定性和一致性,减少因尺寸偏差引起的不良品和废品的产生,降低生产成本。
公差的十分之一原则是制造过程中重要的质量控制原则之一。
它通过合理地控制产品的尺寸偏差,提高产品的精度和质量。
在实际生产中,应用公差的十分之一原则可以有效地提高产品的质量稳定性和一致性,降低生产成本,提高企业的竞争力。
因此,在产品设计和制造过程中,应充分考虑公差的十分之一原则,以确保产品的质量和精度。
公差原则及其应用

我国形位公差国家标准 (GB T 42491996 和 GB T 16671- 1996) 中明确规定了 处理尺寸公差和形位公差的公差原则, 并把 公差原则分为独立原则和相关要求, 相关要 求又分为包容要求、最大实体要求、最小实体 要求。 这些公差原则都是反映某种设计要求 提出的, 对于不同的功能要求采用不同的公 差原则。 1 独立原则
第 19 卷 第4期
标 准 化 报 道 R EPO R T IN G O F STANDA RD IZA T ION
·机械标准化·
V o l. 19 N o. 4 1998
公差原则及其应用
赵妙霞 陈洪根
(甘肃工业大学 兰州 730050)
摘 要 对 GB T 4249- 1996《公差原则》的图样标注、应用范围、检验等学习体会予以交流。 关键词 公差原则 国标 包容要求 最大实体要求 最小实体要求
41
4. 2. 1 最小实体要求应用于基准要素时, 基 准要素应遵守相应的边界。 若基准要素的实 际轮廓偏离相应的边界, 即其体内作用尺寸 偏离相应的边界尺寸, 则允许基准要素在一 定范围内浮动, 其浮动范围等于基准要素的
体内作用尺寸与相应边界尺寸之差。 4. 2. 基准要素本身采用最小实体要求时, 则相应的边界为最小实体实效边界。此时, 基 准代号应直接标注在形成该最小实体实效边 界的形位公差框格下面。 如图 8 所示。
图 1 为独立原则标注常见示例。
图 1 独立原则标注
1. 1 含义 给出的尺寸公差、形位公差彼此无关, 要
分别满足要求。 1. 2 识别
标注中无特殊记号或说明。 1. 3 职能 (见图 1)
对设计人员来说, 则要满足:
收稿日期: 1998- 05- 21 38
汽车零部件设计中公差原则的应用与分析
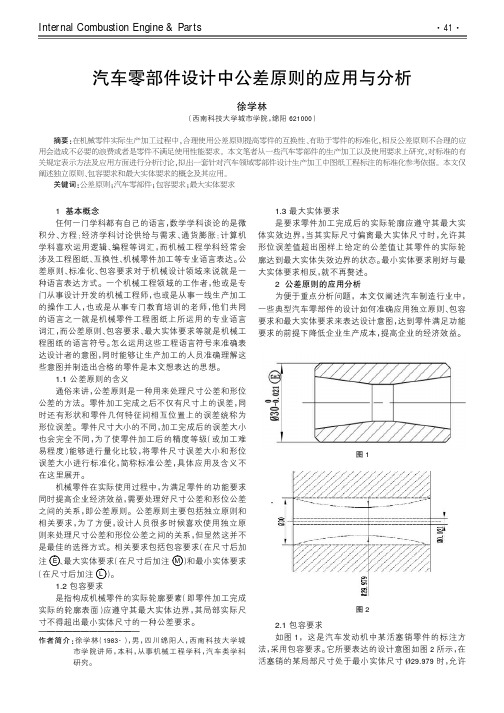
Internal Combustion Engine &Parts1基本概念任何一门学科都有自己的语言,数学学科谈论的是微积分、方程;经济学科讨论供给与需求、通货膨胀;计算机学科喜欢运用逻辑、编程等词汇,而机械工程学科经常会涉及工程图纸、互换性、机械零件加工等专业语言表达。
公差原则、标准化、包容要求对于机械设计领域来说就是一种语言表达方式。
一个机械工程领域的工作者,他或是专门从事设计开发的机械工程师,也或是从事一线生产加工的操作工人,也或是从事专门教育培训的老师,他们共同的语言之一就是机械零件工程图纸上所运用的专业语言词汇,而公差原则、包容要求、最大实体要求等就是机械工程图纸的语言符号。
怎么运用这些工程语言符号来准确表达设计者的意图,同时能够让生产加工的人员准确理解这些意图并制造出合格的零件是本文想表达的思想。
1.1公差原则的含义通俗来讲,公差原则是一种用来处理尺寸公差和形位公差的方法。
零件加工完成之后不仅有尺寸上的误差,同时还有形状和零件几何特征间相互位置上的误差统称为形位误差。
零件尺寸大小的不同,加工完成后的误差大小也会完全不同,为了使零件加工后的精度等级(或加工难易程度)能够进行量化比较,将零件尺寸误差大小和形位误差大小进行标准化,简称标准公差,具体应用及含义不在这里展开。
机械零件在实际使用过程中,为满足零件的功能要求同时提高企业经济效益,需要处理好尺寸公差和形位公差之间的关系,即公差原则。
公差原则主要包括独立原则和相关要求,为了方便,设计人员很多时候喜欢使用独立原则来处理尺寸公差和形位公差之间的关系,但显然这并不是最佳的选择方式。
相关要求包括包容要求(在尺寸后加注最大实体要求(在尺寸后加注和最小实体要求(在尺寸后加注。
1.2包容是指构成机械零件的实际轮廓要素(即零件加工完成实际的轮廓表面)应遵守其最大实体边界,其局部实际尺寸不得超出最小实体尺寸的一种公差要求。
1.3最大实体要求是要求零件加工完成后的实际轮廓应遵守其最大实体实效边界,当其实际尺寸偏离最大实体尺寸时,允许其形位误差值超出图样上给定的公差值让其零件的实际轮廓达到最大实体失效边界的状态。
公差相关原则包括-概述说明以及解释
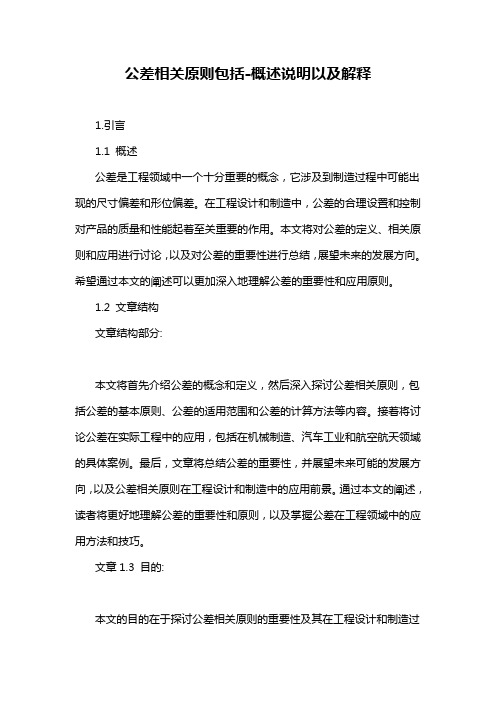
公差相关原则包括-概述说明以及解释1.引言1.1 概述公差是工程领域中一个十分重要的概念,它涉及到制造过程中可能出现的尺寸偏差和形位偏差。
在工程设计和制造中,公差的合理设置和控制对产品的质量和性能起着至关重要的作用。
本文将对公差的定义、相关原则和应用进行讨论,以及对公差的重要性进行总结,展望未来的发展方向。
希望通过本文的阐述可以更加深入地理解公差的重要性和应用原则。
1.2 文章结构文章结构部分:本文将首先介绍公差的概念和定义,然后深入探讨公差相关原则,包括公差的基本原则、公差的适用范围和公差的计算方法等内容。
接着将讨论公差在实际工程中的应用,包括在机械制造、汽车工业和航空航天领域的具体案例。
最后,文章将总结公差的重要性,并展望未来可能的发展方向,以及公差相关原则在工程设计和制造中的应用前景。
通过本文的阐述,读者将更好地理解公差的重要性和原则,以及掌握公差在工程领域中的应用方法和技巧。
文章1.3 目的:本文的目的在于探讨公差相关原则的重要性及其在工程设计和制造过程中的应用。
通过对公差的定义、相关原则和应用进行深入分析和探讨,旨在帮助读者更好地理解公差的概念和作用,以及如何在实际工程中正确应用公差相关原则,确保产品的质量和性能。
同时,本文也旨在引起更多工程师和制造商对公差问题的重视,促进相关领域的研究和发展,为未来工程设计和制造提供更好的指导和支持。
2.正文2.1 公差的定义公差是指在工程制图和产品制造中允许的尺寸偏差范围。
在实际生产中,由于材料、设备和工艺等因素的影响,制造出来的零部件很难完全与设计尺寸完全一致,因此需要对尺寸偏差进行控制和管理。
公差的设置能够保证产品的可靠性和可制造性,确保产品的功能和性能要求得到满足。
公差通常分为上限公差和下限公差。
上限公差指的是在设计尺寸上方允许的最大尺寸偏差,而下限公差指的是在设计尺寸下方允许的最小尺寸偏差。
通过设定合理的公差范围,可以确保产品在生产中能够达到规定的功能和质量要求,同时也能够在一定程度上控制制造成本。
公差原则中最大实体要求的分析及应用
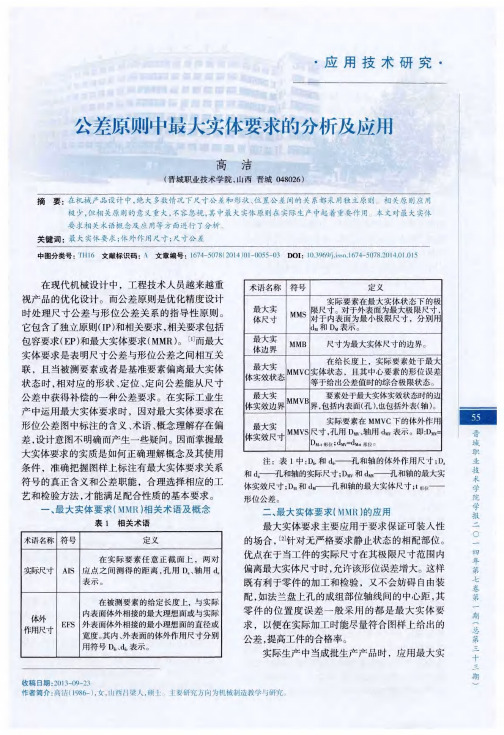
最大实体要求给出形位公差值时 ,在公差框 格 内形 位公 差值 后 面加 注符 号 “ M” , [ 4 ] 应 用 于基 准 要 素时 ,在 相应 公 差框 格 中的基 准字 母后 加 注 符
号“ M” 。如 图 l ( a ) 所示 。
偿值 0 . 0 1 5 =  ̄3 0 一 2 9 . 9 8 5 再加上给定的公差值 q b O . 0 1 5 , 即为 0 . 0 3 ; 当轴的实际尺寸 d 处处等于最 小实体尺寸 d ( 2 9 . 9 7 9 ) 时, 轴线直线度误差的最 大允许补偿值为形状公差 t ( 0 . 0 1 5 ) 与尺寸公差 T ( 0 . 0 2 1 ) 值之和 , 即 0 . 0 3 6 。如图 l ( c ) 所示 。 图1 ( d ) 为图 1 ( c ) 轴线直线度误差允许值 t 随 轴的实际尺寸 d 变化规律的动态公差图。 3 . 轴的实际尺寸应在最小极限( 2 9 . 9 7 9 ) 与最 大 极 限尺寸 ( q b 3 0 ) 之间, 即q b 2 9 . 9 7 9 ≤d ≤ 3 0 。
3 0 1 5
.
0 2】
d 凸
幽
3 0
( c )最 小 实 体 状 态
( d )动 态 公 差 图
图 1 最大实体要 求应 用于被测要素
内表 面 : D ≥D M v = D , . o — t
D一 ≥ D ≥ D
2 . 当被测要素轴的实际尺寸偏离最大实体尺
别为 1 8 - m 0 . 0 叫 1 , 6 轴的轴线和 2 5 ∞ 轴的轴线 。 从 图纸 标注中可得出 ,零件 中的基准要素本身是采用了
公 差 原则 中的独 立 原则 ,即 图样 中给 出的尺 寸 公
英制形位公差应用指南介绍3(公差原则部分)
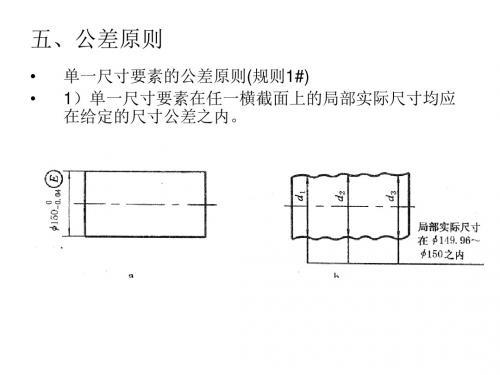
规则2a#(仅用于位置度公差)
如果适用,可以对给定公差、基准要素或 两者同时在图样上规定RFS。
关于RFS的解释
在RFS基础上给出几何公差时,规定的公差与 被测要素的实际尺寸无关。该公差被限定在给 定值之内,与该要素的实际尺寸无关。
同样,在RFS基础上的基准要素意味着必须以 轴线或中心平面定心,而与基准要素的实际尺 寸无关。
• 规则1#的应用 • 通止规概念和检测应用
• 通规是测量尺寸要素MMC尺寸和MMC理想形 状。通规就是尺寸要素MMC的理想几何形状。
• 止规可测量尺寸要素的LMC尺寸。LMC尺寸要 作两点法测量。
•
规则1#失效 在下列情况下规则1#失效。 ----直线度应用在尺寸要素上。 ----一个说明应用在尺寸要素上。
• 螺纹
对于螺纹的方向或位置公差以及作为基准要 素都是指由螺纹中径轴线。如果不是指中径而 是其它特定的螺纹要素(如小径或大径)必须在 公差框格之下或基准要素符号之下或基准要素 符号附近予以明确。
•
齿轮和花键 除螺纹要素外,对齿轮、花键的方向 或位置公差以及作为基准要素,都必须明 确指出是用于齿轮、花键的哪个特定要素 (如大径、节径或小径),且必须在公差框 格之下或在基准要素符号之下进行规定。
• 关于MMC下的零公差(0 )解释 • 当位置或方向公差应用在MMC下的零公差(0 ) 时,该公差完全依赖于被测要素的实际尺寸。如 果要素处于MMC极限尺寸下,此时不允许有位 置或方向公差,而且,在这种情况下,它必须是 处C时,允许公差等于这个偏离量。 当形状处于LMC时,此时总的允许位置或方向偏 差为最大。
五、公差原则
• • 单一尺寸要素的公差原则(规则1#) 1)单一尺寸要素在任一横截面上的局部实际尺寸均应 在给定的尺寸公差之内。
公差原则,很详细
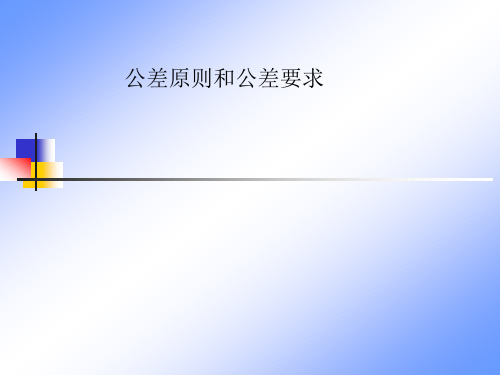
2.最小实体状态(LMC) 和最小实体尺寸(LMS) LMC— 是指实际要素在给定长度上处处位于尺寸公差带内, 并具有实体最小(即材料最少,重量最轻)的状态。 LMS —是指在LMC下的尺寸。 对孔 DL= Dmax 对轴 dL= dmin 3.体外作用尺寸(EFS)见P95 图4.50 EFS 是 指 被 — 测要素在给定长度 上,与实际内表面 (孔)体外相接的 最大理想面或与实 际外表面(轴)体 外相接的最小理想 面的直径或宽度。 孔 Dfe= Da-f形位
0.4 0.3 0.1 -0.3 -0.2 Ø19.7 Da/mm
ø20(dMMS) Ø 20.1(dMMVS)
最大实体要求应用实例(二)
如图所示,被测轴应满足下列要求: 实际尺寸在ø 11.95mm~ø 12mm之内; 实际轮廓不得超出关联最大实体实效边界,即关联体外作用尺寸不大 于关联最大实体实效尺寸dMMVS=dMMS+t=12+0.04=12.04mm 当被测轴处在最小实体状态时,其轴线对A基准轴线的同轴度误差允 许达到最大值,即等于图样给出的同轴度公差( ø0.04 )与轴的尺 寸公差(0.05)之和( ø0.09 )。 0
图样标注见 P103 图4.54
(a)
(b)
若可逆要求用于MMR时(如 — Φ 0.1
(c)
(d) M R
) 其动态公
差带图如图4.54(d)。
MMR为零形公差时,其标注和动态公差带图 见P104 图4.55。
应用:最大实体要求用于只要求可装配性的要素。 检测:最大实体要求一般用功能量规来检验。
具 有 理 想 形 状 且 BS 为
具有理想形状 且 BS 为LMS的
具 有 理 想 形 状 且 BS 为
公差原则的应用

公差原则的应用Chapter 1: Introduction- Background information about the tolerance principle- Explanation of the importance of the tolerance principle in manufacturing and engineering- Purpose and objectives of the paper- Overview of the structure of the paperChapter 2: Understanding the Tolerance Principle- Definition of the tolerance principle- Types of tolerances- The importance of tolerances in manufacturing and engineering - Limitations and challenges of using tolerancesChapter 3: Application of the Tolerance Principle- Importance of considering the tolerance principle during the design phase- How to determine the appropriate tolerances for different applications- Effects of varying tolerance values on the performance and cost of a product- Case studies of how the tolerance principle has been successfully applied in different industriesChapter 4: Benefits of Applying the Tolerance Principle- Improved product quality and performance- Reduced production costs and waste- Increased efficiency and productivity- Enhanced customer satisfaction and brand reputationChapter 5: Future of the Tolerance Principle- Trends and innovations in the use of tolerance principles- Challenges and opportunities for further research and development- Implications for the future of manufacturing and engineering Chapter 6: Conclusion- Summary of the key points discussed in the paper- Implications for practitioners and researchers- Recommendations for future work- Final thoughts and conclusion.Chapter 1: IntroductionThe tolerance principle plays a crucial role in manufacturing and engineering processes by specifying the acceptable deviation from the intended design or specification. The principle is applied to ensure that the final product meets the required quality standards, is cost-effective, and complies with safety regulations. This paper aims to discuss the tolerance principle in detail, providing an overview of its application, limitations, and benefits.The objectives of this paper are to:1. Explain the definition of the tolerance principle and show its importance in manufacturing and engineering.2. Analyze the limitations associated with tolerances and how they can affect the quality of the final product.3. Demonstrate how the tolerance principle can be applied in various situations to enhance the quality and performance of products.Chapter 2: Understanding the Tolerance PrincipleThe tolerance principle refers to the acceptable level of deviation or variation from the intended design or specification. There are two types of tolerances: dimensional and geometric. Dimensional tolerance relates to the size and shape of an object, while geometric tolerance refers to the orientation, profile, and location of features on a given part. Tolerances are necessary to ensure that mechanical parts and systems function as intended, and that products meet their performance, safety, and regulatory requirements.However, tolerances have limitations. One of the limitations is that they increase production costs, especially when the required tolerances are very tight. Moreover, it can be challenging to determine the correct tolerances, especially when incorporating significant variations that may have a significant effect on the product's performance. Additionally, applying extremely tight tolerances may be unnecessary, leading to increased production costs with no significant benefit to product performance.Chapter 3: Application of the Tolerance PrincipleThe tolerance principle is a fundamental aspect of design and manufacturing, and its application has practical benefits. In the design phase, the use of tolerance analysis assists in determining the appropriate tolerances to be used for each component. This helps in finding a balance between the requirements for quality, cost, and performance. Additionally, proper application of the tolerance principle ensures that parts are manufactured within acceptable limits, improving their functionality.The selection of tolerances is a significant factor in determining the performance of a product. A high tolerance variation may lead to poor fitting between parts, while a small tolerance may make the parts too costly. However, using the appropriate tolerances will lead to improved performance and, thus, better customer satisfaction.This principle affects the performance, quality, and cost of products during manufacturing. The management of part production and assembly through the tolerance principle reduces rework and ensures the components' correct fitting and functionality, reducing waste and contributing to enhanced efficiency and productivity. Furthermore, the application of tolerances ensures that products comply with regulatory safety requirements, reducing the risk of accidents caused by product failure.In conclusion, the tolerance principle plays a crucial role in the manufacturing and engineering industries, ensuring product safety, compliance, and quality. Selecting appropriate and reasonable tolerances during the design phase of product development leads to improved performance and reduced production costs.Overall, understanding and properly applying the tolerance principle is essential to ensure the success of manufacturing and engineering processes.Chapter 4: Limitations of the Tolerance PrincipleAs mentioned earlier, the tolerance principle has limitations that can affect the quality, cost, and performance of products. Some ofthe limitations include:1. Cost of production: Tight tolerances increase the cost of production since they require higher precision machinery, inspection instruments, and specialized personnel. Moreover, the cost of reworking parts that fail to meet the required tolerances can also lead to additional expenses.2. Tolerance stack-up: When a product has different components, their tolerances can add up, leading to significant variations in the final product. This means that setting tight tolerances for each component can lead to an excessive accumulation of tolerances in the final product, resulting in poor quality, improper fit, and functionality issues.3. Assembly issues: The use of tight tolerances can make assembly difficult, especially for complex parts. For instance, a slight deviation in the part's geometry may cause it to interfere with mating parts, requiring additional work and inspection. This can result in additional cost and unnecessary delays.4. Lack of standardization: The tolerance principle lacks a universal standard for different industries and applications. This means that tolerances for similar parts or products can differ depending on the manufacturer or industry, leading to confusion and uncertainty.5. Over-specification: Using extremely tight tolerances can be unnecessary and may even lead to suboptimal performance. For instance, in an industrial application where tight tolerances are notrequired, using them may lead to unnecessary expenses and reduced efficiency.Chapter 5: Practical Application of the Tolerance PrincipleThe application of the tolerance principle is critical in manufacturing and engineering processes. Correct application leads to improved performance, better reliability, cost optimization, and increased efficiency. The following are practical applications of the tolerance principle:1. Design phase analysis: The proper selection of tolerances is essential in the design phase since the targeted application will determine the tolerance levels necessary for each part. In the design phase, tolerance analysis software can be used to predict the impact of different tolerance levels on the final product's performance.2. Quality control: The use of automated inspection systems and measurement instruments improves the accuracy of quality control, reducing the risk of non-conformance. By ensuring that parts meet the required tolerances, they can be easily fitted and assembled with other components, reducing the risk of improper assembly.3. Assembly alignment: The use of specialized gauging equipment and fixtures during assembly can help reduce assembly issues that may arise from tight tolerances. The correct alignment of mating parts ensures that they fit correctly, leading to improved functionality and reliability.4. Part selection: The selection of the appropriate part manufacturers is crucial since they can determine the quality of parts produced and the tolerances used. The manufacturer's quality assurance system, equipment used, and experience can all affect the tolerances produced.5. Standardization: The adoption of standardization across different industries and applications is critical in reducing confusion and uncertainty surrounding the tolerance principle. Industries should agree on standard tolerance limits for different parts and products, ensuring that the final product meets the intended specifications.ConclusionIn conclusion, the tolerance principle plays a crucial role in engineering and manufacturing industries. The principle is essential in ensuring that products meet the required safety, reliability, and performance standards. While tolerances have limitations, their application can lead to significant improvements in quality, efficiency, and cost reduction.The selection of appropriate tolerances and the use of advanced equipment and software in the design and production phases can go a long way in reducing assembly issues and production costs. Standardization ensures that products conform to the intended specifications, reducing confusion and uncertainty.Overall, the tolerance principle plays a critical role in ensuring the success of engineering and manufacturing processes, and its proper application is essential to achieving the desired outcome.。
- 1、下载文档前请自行甄别文档内容的完整性,平台不提供额外的编辑、内容补充、找答案等附加服务。
- 2、"仅部分预览"的文档,不可在线预览部分如存在完整性等问题,可反馈申请退款(可完整预览的文档不适用该条件!)。
- 3、如文档侵犯您的权益,请联系客服反馈,我们会尽快为您处理(人工客服工作时间:9:00-18:30)。
20(dM)
20 19.99
0 0.01
最大实体边界
19.98
19.97
0.02
0.03
轴线直线度 最大实体要求
0.1 M
直线度/mm
13
/ 50
0.4
0.3 0.2 0.1
20(dM)
19.7(dL)
0.3 0.2 0.1
0
实际尺寸/mm
20(dM)
20.1(dMV)
几何规范
公差设计与检测 互换性与技术测量
D45•公差原则应用
公差原则
尺寸公差与几何公差相互关系的原则 保证孔、轴配合性质
公差原则 独立原则 包容要求Ⓔ 最大实体要求Ⓜ 相关要求 最小实体要求Ⓛ 可逆最小实体要求ⓁⓇ
2
/ 61
保证可装配性、批量 生产的互换性
可逆最大实体要求ⓂⓇ
保证抗磨损性、零件 强度、最小壁厚、最 小边距、加工余量等
0.1
20.1(dMV)
轴线直线度 最大实体要求 包容要求
14
/ 50
19.97(dL)
0 M
最大实体边界 最大实体实效边界
20(dM)
0.03
轴线直线度 最大实体要求
15
/ 50
中心平面平面度 最大实体要求
16
/ 50
17
/ 50
方向公差 应用公差原则
方向公差 最大实体要求
18
45
/ 50
车身应用
46
/ 50
车身应用
47
/ 50
车身应用
48
/ 50
车身应用
49
/ 50
50
/ 50
尺寸 最大实体要求
41
/ 50
Ø10.5
Xmax Xmin
= 20 – 9.9/2 – 9.7/2 = 10.2 mm = 20 – 10.1/2 – 10.5/2 = 9.7 mm = 20 – 10.1/2 – (10.1 – 9.7/2) = 9.7 mm
尺寸 最大实体要求
42
/ 50
Ø10.5
Ø10.3
Xmax Xmin
= 20 – 9.9/2 – 9.7/2 = 10.2 mm = 20 –10.3/2 – 10.5/2 = 9.6 mm = 20 – (10.1 – 9.9/2) – (10.1 – 9.7/2) = 9.6 mm
43
/ 50
汽车零件实例
车身应用
44
/ 50
车身应用
/ 50
非圆尺寸要素位置度 最大实体要求
27
/ 50
复合位置度 最大实体要求
28
/ 50
保证最小壁厚 最小实体要求
29
/ 50
保证最小壁厚 最小实体要求
30
/ 50
保证键槽中心 最小实体要求
31
/ 50
基准应用 最大实体要求
32
/ 50
基准应用 最大实体要求
33
/ 50
基准应用 最大实体要求
/ 50
轴线平行度 最大实体要求
19
/ 50
轴线平行度 最大实体要求
20
/ 50
轴线垂直度 最大实体要求
21
/ 50
轴线垂直度 最大实体要求
22
/ 50
轴线垂直度 最大实体要求
23
/ 50
24
/ 50
位置公差 应用公差原则
位置公差 最大实体要求
25
/ 50
轴线位置度 最大实体要求
26
独立原则 Ⓘ
ISO 缺省公差原则:
3
/ 50
独立原则
ASME 缺省公差原则(Rule #1):
包容要求
ASME 第二公差原则(Rule #2):
独立原则 Ⓘ
相关要求 Ⓔ Ⓜ Ⓛ Ⓡ
只能够用于约束尺寸要素:
孔、轴 凸台、槽 内、外螺纹 内、外圆柱 …
4
/ 50
只能够用于的几何公差项目:
9
/ 50
10
/ 50
形状公差 应用公差原则
轴线直线度 包容要求
11
/ 50
轴线直线度 包容要求
直线度/mm 0.03
12
பைடு நூலகம்
/ 50
0.02
0.01 0
19.97(dL) 20(dM)
实际尺寸/mm
19.97(dL)
动态公差示意图
0.03
公差补偿示意计算
被测要素 实际尺寸 允许的 直线度误差
直线度、平面度 平行度、垂直度、倾斜度 同轴度、对称度、位置度
包容要求Ⓔ
常用于保证孔、轴的配合性质 用在孔轴的尺寸和形状相互作用、相互影响的情况下
5
/ 50
包容要求Ⓔ
6
/ 50
常用于需要保证最小间隙时。如在热力机械中的零件或在高速运转中的零 件,遇热易膨胀,为了避免在工作中卡死,需要保证最小间隙 常用于需要保证最大过盈时。如薄壁套筒零件,需采用过盈配合或过渡配 合,又不允许过盈量太大,装配时容易开裂 可以用光滑极限量规来检测,通规体现最大实体边界,止规控制最小实体 尺寸
34
/ 50
基准应用 最大实体要求
35
/ 50
基准应用 最大实体要求
36
/ 50
基准应用 最大实体要求
37
/ 50
基准应用 最大实体要求
38
/ 50
基准应用 最大实体要求
39
/ 50
尺寸 最大实体要求
40
/ 50
Ø7.4
Ø17.8
Xmax Xmin
= 30 – 5.8/2 – 15.8/2 = 19.2 mm = 30 – 17.8/2 – 7.4/2 = 17.4 mm = 30 – (16.8 – 15.8/2) – (6.6 – 5.8/2) = 17.4 mm
最大实体要求Ⓜ
用在特征的尺寸和位置相互作用,相互影响的情况下 可以用功能量规来检测,通规体现最大实体边界,止规控制 最小实体尺寸
7
/ 50
最大实体要求Ⓜ
在保证零件可装配性要求时,降低了加工难度,同时降低了 检验的成本
8
/ 50
最小实体要求Ⓛ
用在特征的尺寸和位置相互作用,相互影响的情况下 使用于保证孔边厚度和轴的强度的场合,配合孔对导向 销起到定位作用,如装配时需要导向的零件