铸件质量提升方案
宁波市推进压铸行业规范提升实施方案(2021
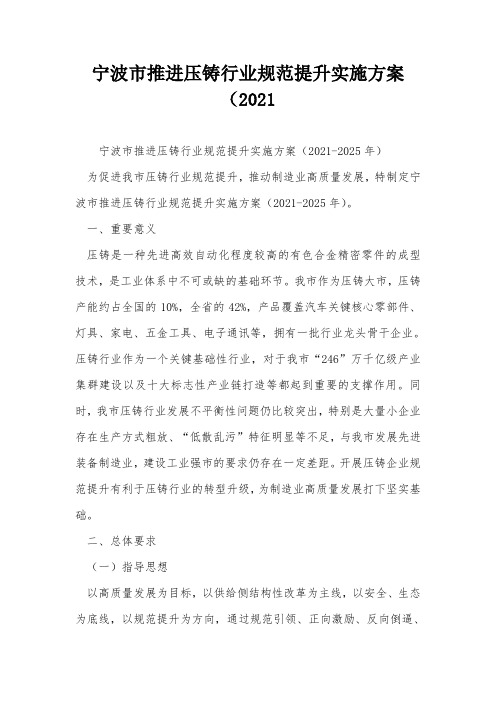
宁波市推进压铸行业规范提升实施方案(2021宁波市推进压铸行业规范提升实施方案(2021-2025年)为促进我市压铸行业规范提升,推动制造业高质量发展,特制定宁波市推进压铸行业规范提升实施方案(2021-2025年)。
一、重要意义压铸是一种先进高效自动化程度较高的有色合金精密零件的成型技术,是工业体系中不可或缺的基础环节。
我市作为压铸大市,压铸产能约占全国的10%,全省的42%,产品覆盖汽车关键核心零部件、灯具、家电、五金工具、电子通讯等,拥有一批行业龙头骨干企业。
压铸行业作为一个关键基础性行业,对于我市“246”万千亿级产业集群建设以及十大标志性产业链打造等都起到重要的支撑作用。
同时,我市压铸行业发展不平衡性问题仍比较突出,特别是大量小企业存在生产方式粗放、“低散乱污”特征明显等不足,与我市发展先进装备制造业,建设工业强市的要求仍存在一定差距。
开展压铸企业规范提升有利于压铸行业的转型升级,为制造业高质量发展打下坚实基础。
二、总体要求(一)指导思想以高质量发展为目标,以供给侧结构性改革为主线,以安全、生态为底线,以规范提升为方向,通过规范引领、正向激励、反向倒逼、集聚发展等方式,引导和促进我市压铸行业“固优势、补短板”,促进产业向规模化、高端化、集约化、绿色化方向发展,切实增强压铸行业对我市制造业的支撑作用。
(二)主要目标至2023年,完成压铸行业全面普查,建立市压铸行业动态监管数据库,制定发布压铸企业公告管理制度。
完成各类压铸相关企业规范提升500家,建设3个以上压铸产业园,星级绿色工厂达到150家。
至2025年,规范提升压铸相关企业800家,全市压铸行业发展不平衡问题得到有效缓解,“低散乱污”问题基本得到治理,企业入园率达到80%。
规模以上压铸企业星级绿色工厂基本实现全覆盖,单位产品排放、能耗等低于国家标准。
三、重点任务(一)严格源头把控。
鼓励企业做大做强,新(改、扩)建项目在符合空间规划、环保、安全要求的前提下,原则上应满足以下条件之一:压铸机、熔化炉等主体设备投资额在1000万元以上;投资后企业压铸设备总数5台或总吨位1000吨以上;新增用地项目亩均投资强度不少于300万/亩。
铸件质量提升实施方案
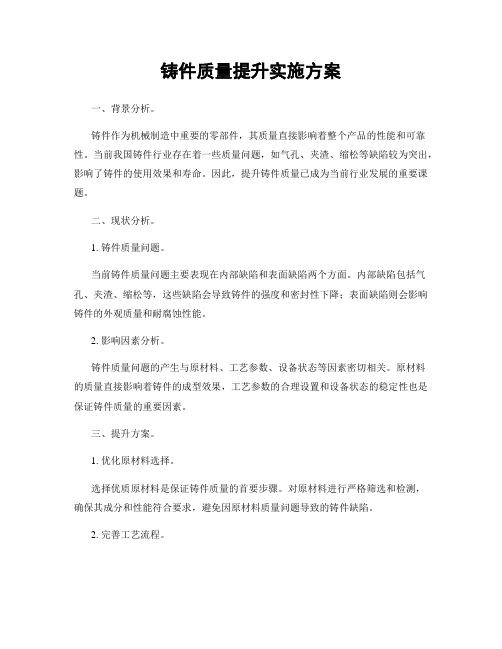
铸件质量提升实施方案一、背景分析。
铸件作为机械制造中重要的零部件,其质量直接影响着整个产品的性能和可靠性。
当前我国铸件行业存在着一些质量问题,如气孔、夹渣、缩松等缺陷较为突出,影响了铸件的使用效果和寿命。
因此,提升铸件质量已成为当前行业发展的重要课题。
二、现状分析。
1. 铸件质量问题。
当前铸件质量问题主要表现在内部缺陷和表面缺陷两个方面。
内部缺陷包括气孔、夹渣、缩松等,这些缺陷会导致铸件的强度和密封性下降;表面缺陷则会影响铸件的外观质量和耐腐蚀性能。
2. 影响因素分析。
铸件质量问题的产生与原材料、工艺参数、设备状态等因素密切相关。
原材料的质量直接影响着铸件的成型效果,工艺参数的合理设置和设备状态的稳定性也是保证铸件质量的重要因素。
三、提升方案。
1. 优化原材料选择。
选择优质原材料是保证铸件质量的首要步骤。
对原材料进行严格筛选和检测,确保其成分和性能符合要求,避免因原材料质量问题导致的铸件缺陷。
2. 完善工艺流程。
在铸造工艺中,合理设置浇注系统和浇注温度,采用适当的浇注速度和压力,避免气孔和夹渣等缺陷的产生。
同时,加强对熔炼和浇注过程的监控,确保工艺参数的稳定性。
3. 强化设备管理。
保证铸造设备的正常运行和维护,定期进行设备检修和保养,确保设备状态的稳定性和可靠性。
合理配置设备,提高生产效率,减少因设备故障导致的铸件质量问题。
四、实施措施。
1. 加强质量管理。
建立健全的质量管理体系,制定质量管理规范和标准,加强对生产过程的监控和检测,及时发现和解决质量问题。
2. 培训技术人员。
加强对生产技术人员的培训和教育,提高其对铸造工艺和设备操作的理解和掌握,增强其对质量控制的意识和能力。
3. 加强沟通协作。
生产、质检、技术等部门之间加强沟通和协作,形成合力,共同解决铸件质量问题,推动铸件质量的持续提升。
五、总结。
铸件质量的提升是一个系统工程,需要从原材料、工艺、设备、管理等多个方面综合考虑和实施。
只有通过全面的提升方案和实施措施,才能有效解决铸件质量问题,提高产品质量,增强市场竞争力。
2024年铸件项目发展计划
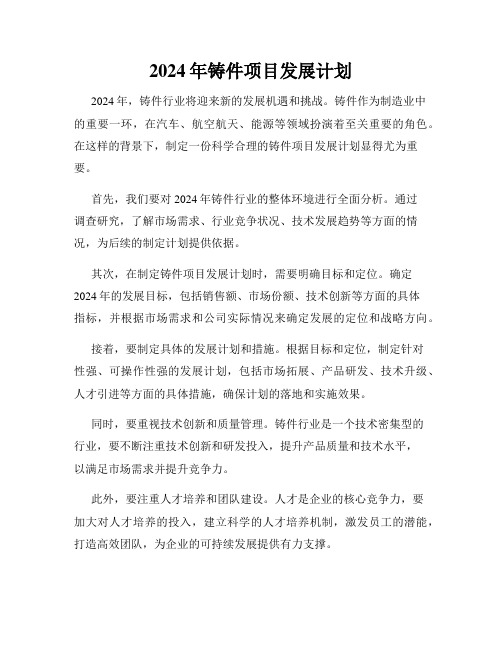
2024年铸件项目发展计划2024年,铸件行业将迎来新的发展机遇和挑战。
铸件作为制造业中的重要一环,在汽车、航空航天、能源等领域扮演着至关重要的角色。
在这样的背景下,制定一份科学合理的铸件项目发展计划显得尤为重要。
首先,我们要对2024年铸件行业的整体环境进行全面分析。
通过调查研究,了解市场需求、行业竞争状况、技术发展趋势等方面的情况,为后续的制定计划提供依据。
其次,在制定铸件项目发展计划时,需要明确目标和定位。
确定2024年的发展目标,包括销售额、市场份额、技术创新等方面的具体指标,并根据市场需求和公司实际情况来确定发展的定位和战略方向。
接着,要制定具体的发展计划和措施。
根据目标和定位,制定针对性强、可操作性强的发展计划,包括市场拓展、产品研发、技术升级、人才引进等方面的具体措施,确保计划的落地和实施效果。
同时,要重视技术创新和质量管理。
铸件行业是一个技术密集型的行业,要不断注重技术创新和研发投入,提升产品质量和技术水平,以满足市场需求并提升竞争力。
此外,要注重人才培养和团队建设。
人才是企业的核心竞争力,要加大对人才培养的投入,建立科学的人才培养机制,激发员工的潜能,打造高效团队,为企业的可持续发展提供有力支撑。
最后,要建立有效的监督和评估机制。
对于制定的发展计划和措施,要建立科学的监督和评估机制,及时发现问题并采取相应的调整措施,确保计划的顺利实施和达成预期目标。
综上所述,2024年铸件项目的发展计划需要全面分析市场环境、明确目标和定位、制定具体计划和措施、重视技术创新和质量管理、注重人才培养和团队建设,建立有效的监督和评估机制。
只有如此,铸件行业才能在新的一年中迎接更好的发展机遇,取得更大的成就。
铸造研发技术方案
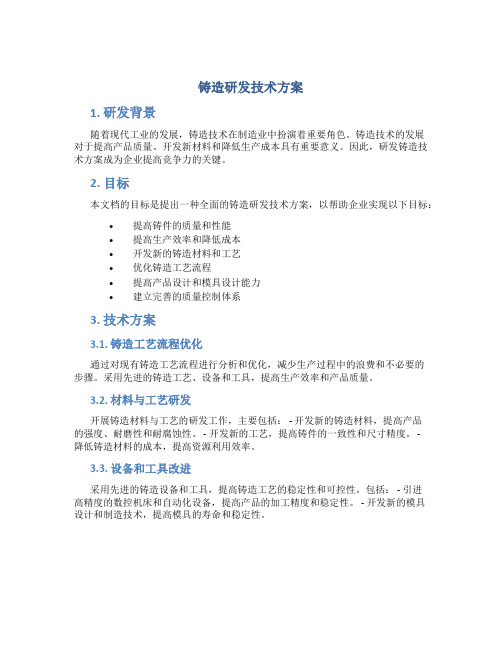
铸造研发技术方案1. 研发背景随着现代工业的发展,铸造技术在制造业中扮演着重要角色。
铸造技术的发展对于提高产品质量、开发新材料和降低生产成本具有重要意义。
因此,研发铸造技术方案成为企业提高竞争力的关键。
2. 目标本文档的目标是提出一种全面的铸造研发技术方案,以帮助企业实现以下目标:•提高铸件的质量和性能•提高生产效率和降低成本•开发新的铸造材料和工艺•优化铸造工艺流程•提高产品设计和模具设计能力•建立完善的质量控制体系3. 技术方案3.1. 铸造工艺流程优化通过对现有铸造工艺流程进行分析和优化,减少生产过程中的浪费和不必要的步骤。
采用先进的铸造工艺、设备和工具,提高生产效率和产品质量。
3.2. 材料与工艺研发开展铸造材料与工艺的研发工作,主要包括: - 开发新的铸造材料,提高产品的强度、耐磨性和耐腐蚀性。
- 开发新的工艺,提高铸件的一致性和尺寸精度。
-降低铸造材料的成本,提高资源利用效率。
3.3. 设备和工具改进采用先进的铸造设备和工具,提高铸造工艺的稳定性和可控性。
包括: - 引进高精度的数控机床和自动化设备,提高产品的加工精度和稳定性。
- 开发新的模具设计和制造技术,提高模具的寿命和稳定性。
3.4. 产品设计与模具设计能力提升产品设计和模具设计能力,以满足市场对产品质量和性能的需求。
主要包括: - 建立产品设计团队,引进先进的设计软件和仿真工具,提高产品设计效率和准确性。
- 建立模具设计团队,提高模具设计和制造的精度和稳定性。
3.5. 质量控制体系建设建立完善的质量控制体系,确保产品质量的稳定性和可靠性。
主要包括: - 引进先进的质量检测设备和方法,提高产品质量的监控和控制能力。
- 建立严格的质量管理流程,确保产品在每个生产环节都符合质量标准。
- 建立质量培训和考核机制,提高员工对质量的意识和责任感。
4. 实施计划设计以下实施计划以达到研发目标:•第一年:进行铸造工艺流程优化和设备改进,建立产品设计和模具设计团队。
铸件质量提升措施

铸件质量提升措施引言铸件是一种常见的金属制造工艺,广泛应用于汽车、机械、航空航天等行业。
然而,由于铸造过程中存在多种因素的影响,铸件可能会出现一些质量问题,如气孔、缩松、夹杂等。
为了提高铸件的质量,我们需要采取一系列的措施来控制铸造过程中的各种因素,并确保铸件达到预期的质量要求。
1. 原材料选择铸件的质量很大程度上取决于所使用的原材料。
因此,在铸造之前,我们应该对原材料进行严格的选择和检测。
以下是一些原材料选择的注意事项:•熔点合适:选择与铸件材料相匹配的原材料,确保原材料的熔点不低于所需的铸造温度。
•成分稳定:要求原材料的成分稳定性好,以保证铸件的化学成分符合要求。
•清洁度高:原材料应具备较高的纯净度,减少夹杂物和杂质的存在。
2. 铸造工艺控制在铸造过程中,我们需要控制铸造工艺的各个环节,以确保铸件的质量。
以下是一些铸造工艺控制的措施:2.1 熔炼和炉温控制•采用合适的熔炼设备和工艺,确保熔炼过程中温度均匀,避免温度过高或过低造成的问题。
•控制炉温,避免铸件遭受过热或过冷的影响。
2.2 浇注系统设计•合理设计浇注系统,控制浇注速度和方向,以避免气孔和夹杂的产生。
•使用合适的浇口和冷却系统,以改善铸件的质量。
2.3 砂型制备和芯子制作•严格控制砂型的制备过程,确保砂型的密实性和表面质量。
•对芯子的制作要求严格,以减少夹杂和气孔的产生。
3. 检测和控制为了确保铸件的质量,我们还需要进行一系列的检测和控制措施。
以下是一些常见的检测和控制方法:3.1 X射线探伤利用X射线技术对铸件进行全面的探伤,以检测铸件中的夹杂、缺陷等问题。
3.2 磁粉检测利用磁粉检测技术对铸件进行表面和体内的缺陷检测,如裂纹、缩孔等。
3.3 声波检测利用声波检测技术对铸件进行内部的缺陷检测,如气孔、夹杂等。
3.4 压力测试在铸造过程中,进行合适的压力测试,以控制铸件的密实度。
4. 质量管理体系为了持续提高铸件的质量,建立和实施质量管理体系是非常重要的。
铸件质量控制计划

铸件质量控制计划
引言概述:
铸件是制造业中常见的一种零部件,其质量直接影响到产品的性能和可靠性。
因此,制定一套科学的铸件质量控制计划对于保证产品质量至关重要。
本文将从铸件质量控制计划的概念、目的、内容、实施步骤和效果等方面进行详细阐述。
一、铸件质量控制计划的概念
1.1 确定铸件质量控制计划的定义
1.2 铸件质量控制计划的重要性
1.3 铸件质量控制计划的制定原则
二、铸件质量控制计划的目的
2.1 提高铸件生产质量
2.2 降低生产成本
2.3 保证产品质量稳定性
三、铸件质量控制计划的内容
3.1 定义铸件的技术要求
3.2 制定合理的工艺流程
3.3 设定合理的质量检验标准
四、铸件质量控制计划的实施步骤
4.1 制定铸件生产计划
4.2 严格执行工艺流程
4.3 加强质量检验和控制
五、铸件质量控制计划的效果
5.1 提高产品质量
5.2 降低生产成本
5.3 提升企业竞争力
总结:铸件质量控制计划是保证产品质量的重要手段,只有制定科学合理的质量控制计划,才能有效提高产品质量、降低生产成本,提升企业竞争力。
企业在生产过程中应严格执行质量控制计划,不断改进和完善,以确保产品质量稳定性和持续改进。
铸造质量提升方案范文
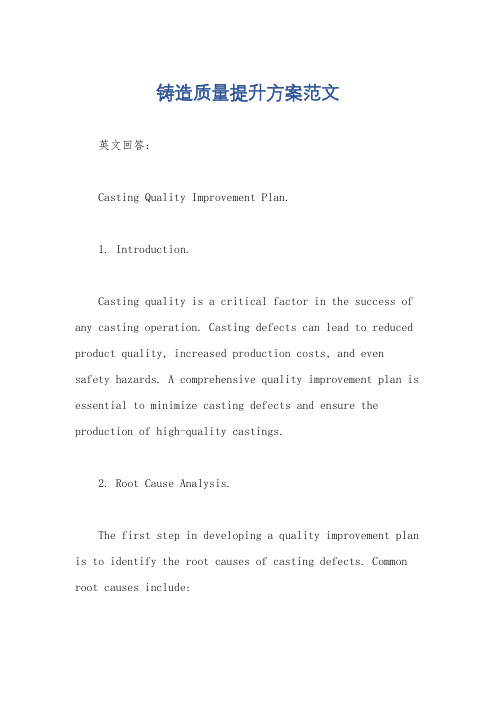
铸造质量提升方案范文英文回答:Casting Quality Improvement Plan.1. Introduction.Casting quality is a critical factor in the success of any casting operation. Casting defects can lead to reduced product quality, increased production costs, and even safety hazards. A comprehensive quality improvement plan is essential to minimize casting defects and ensure the production of high-quality castings.2. Root Cause Analysis.The first step in developing a quality improvement plan is to identify the root causes of casting defects. Common root causes include:Inadequate melt quality.Inaccurate mold design.Improper gating and risering.Insufficient solidification time.Poor heat treatment.3. Process Control.Once the root causes of casting defects have been identified, process controls can be implemented to eliminate or mitigate these causes. Process controls may include:Melt testing and refining.Mold design optimization.Gating and risering simulation.Solidification modeling.Heat treatment optimization.4. Quality Monitoring.Regular quality monitoring is essential to ensure that casting defects are detected early and corrective action can be taken. Quality monitoring techniques may include:Visual inspection.Radiographic testing.Ultrasonic testing.Magnetic particle testing.Destructive testing.5. Continuous Improvement.A quality improvement plan should be a continuous process. Regular data analysis and feedback from customers can identify areas for further improvement. By continuously improving processes and techniques, foundries can consistently produce high-quality castings.中文回答:铸造质量提升方案。
铸件质量控制计划
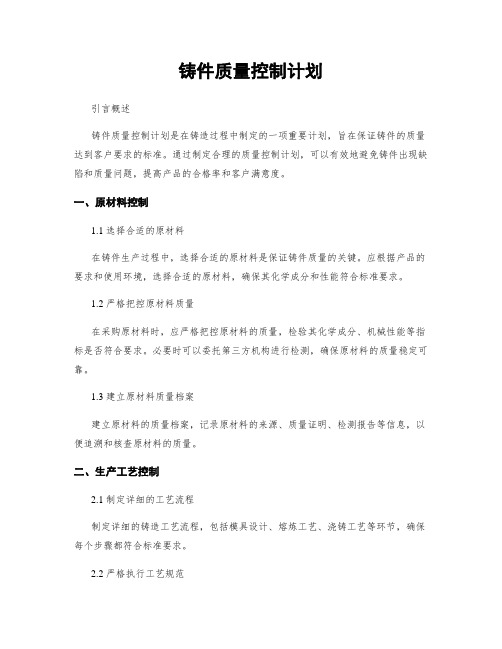
铸件质量控制计划引言概述铸件质量控制计划是在铸造过程中制定的一项重要计划,旨在保证铸件的质量达到客户要求的标准。
通过制定合理的质量控制计划,可以有效地避免铸件出现缺陷和质量问题,提高产品的合格率和客户满意度。
一、原材料控制1.1 选择合适的原材料在铸件生产过程中,选择合适的原材料是保证铸件质量的关键。
应根据产品的要求和使用环境,选择合适的原材料,确保其化学成分和性能符合标准要求。
1.2 严格把控原材料质量在采购原材料时,应严格把控原材料的质量,检验其化学成分、机械性能等指标是否符合要求。
必要时可以委托第三方机构进行检测,确保原材料的质量稳定可靠。
1.3 建立原材料质量档案建立原材料的质量档案,记录原材料的来源、质量证明、检测报告等信息,以便追溯和核查原材料的质量。
二、生产工艺控制2.1 制定详细的工艺流程制定详细的铸造工艺流程,包括模具设计、熔炼工艺、浇铸工艺等环节,确保每个步骤都符合标准要求。
2.2 严格执行工艺规范在生产过程中,严格执行工艺规范,确保每道工序按照要求进行,避免出现疏漏和错误。
2.3 加强过程监控加强生产过程的监控,及时发现和处理问题,确保生产过程的稳定性和可控性。
三、设备保养和维护3.1 定期检查设备状态定期检查铸造设备的状态,确保设备运行正常,避免因设备故障导致的质量问题。
3.2 建立设备维护计划建立设备维护计划,定期进行设备维护和保养,保证设备的正常运行和使用寿命。
3.3 培训维护人员对设备维护人员进行培训,提高其维护技能和意识,确保设备维护工作的有效进行。
四、质量检验和控制4.1 制定质量检验标准制定铸件的质量检验标准,包括外观质量、尺寸精度、化学成分、机械性能等指标,确保检验的全面和准确。
4.2 建立质量检验流程建立质量检验流程,明确检验的步骤和责任人,确保每个环节都得到有效执行。
4.3 强化质量问题处理对于发现的质量问题,要及时进行处理和整改,分析问题原因,并采取有效措施避免问题再次发生。
铸件质量控制计划
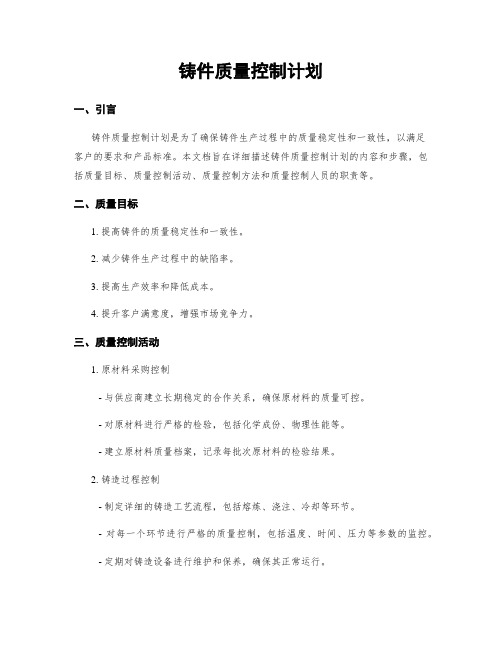
铸件质量控制计划一、引言铸件质量控制计划是为了确保铸件生产过程中的质量稳定性和一致性,以满足客户的要求和产品标准。
本文档旨在详细描述铸件质量控制计划的内容和步骤,包括质量目标、质量控制活动、质量控制方法和质量控制人员的职责等。
二、质量目标1. 提高铸件的质量稳定性和一致性。
2. 减少铸件生产过程中的缺陷率。
3. 提高生产效率和降低成本。
4. 提升客户满意度,增强市场竞争力。
三、质量控制活动1. 原材料采购控制- 与供应商建立长期稳定的合作关系,确保原材料的质量可控。
- 对原材料进行严格的检验,包括化学成份、物理性能等。
- 建立原材料质量档案,记录每批次原材料的检验结果。
2. 铸造过程控制- 制定详细的铸造工艺流程,包括熔炼、浇注、冷却等环节。
- 对每一个环节进行严格的质量控制,包括温度、时间、压力等参数的监控。
- 定期对铸造设备进行维护和保养,确保其正常运行。
3. 检验和测试控制- 制定详细的检验和测试方案,包括外观检查、尺寸测量、力学性能测试等。
- 对每批次铸件进行全面的检验和测试,确保其符合产品标准和客户要求。
- 建立检验和测试记录,保留至少五年的时间。
4. 缺陷分析和改进控制- 对铸件生产过程中的缺陷进行分析,找出根本原因。
- 制定改进措施,防止类似缺陷再次发生。
- 定期评估改进效果,对改进措施进行调整和优化。
四、质量控制方法1. 统计过程控制(SPC)- 通过采集和分析数据,监控铸件生产过程中的关键参数,及时发现和纠正异常。
- 利用控制图和过程能力指数等工具,评估铸件生产过程的稳定性和能力。
2. 全面质量管理(TQM)- 引入全面质量管理理念,将质量控制融入到整个铸件生产过程中。
- 建立质量管理体系,包括质量政策、质量目标、质量手册等。
- 实施质量培训,提高员工的质量意识和技能。
3. 5S管理- 实施5S管理,即整理、整顿、清扫、清洁、素质。
- 维护铸件生产现场的整洁和有序,提高工作效率和质量稳定性。
铸造qc年度工作计划
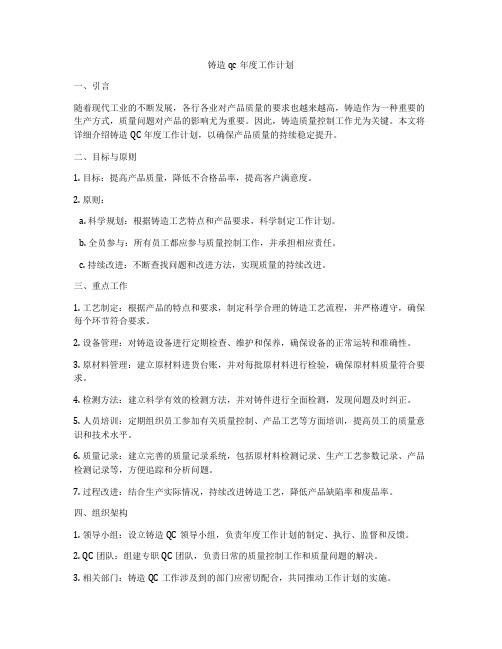
铸造qc年度工作计划一、引言随着现代工业的不断发展,各行各业对产品质量的要求也越来越高,铸造作为一种重要的生产方式,质量问题对产品的影响尤为重要。
因此,铸造质量控制工作尤为关键。
本文将详细介绍铸造QC年度工作计划,以确保产品质量的持续稳定提升。
二、目标与原则1. 目标:提高产品质量,降低不合格品率,提高客户满意度。
2. 原则:a. 科学规划:根据铸造工艺特点和产品要求,科学制定工作计划。
b. 全员参与:所有员工都应参与质量控制工作,并承担相应责任。
c. 持续改进:不断查找问题和改进方法,实现质量的持续改进。
三、重点工作1. 工艺制定:根据产品的特点和要求,制定科学合理的铸造工艺流程,并严格遵守,确保每个环节符合要求。
2. 设备管理:对铸造设备进行定期检查、维护和保养,确保设备的正常运转和准确性。
3. 原材料管理:建立原材料进货台账,并对每批原材料进行检验,确保原材料质量符合要求。
4. 检测方法:建立科学有效的检测方法,并对铸件进行全面检测,发现问题及时纠正。
5. 人员培训:定期组织员工参加有关质量控制、产品工艺等方面培训,提高员工的质量意识和技术水平。
6. 质量记录:建立完善的质量记录系统,包括原材料检测记录、生产工艺参数记录、产品检测记录等,方便追踪和分析问题。
7. 过程改进:结合生产实际情况,持续改进铸造工艺,降低产品缺陷率和废品率。
四、组织架构1. 领导小组:设立铸造QC领导小组,负责年度工作计划的制定、执行、监督和反馈。
2. QC团队:组建专职QC团队,负责日常的质量控制工作和质量问题的解决。
3. 相关部门:铸造QC工作涉及到的部门应密切配合,共同推动工作计划的实施。
五、实施计划1. 明确责任:明确各部门的职责和责任,并建立绩效考核机制,激励员工积极参与质量控制工作。
2. 定期会议:定期召开铸造QC会议,分享工作经验、问题分析和改进方案。
3. 工作检查:定期对各部门的工作进行检查,发现问题及时提出解决方案,确保工作计划的顺利实施。
潍坊市人民政府办公室印发《关于加快铸造企业转型升级推动实现高质量发展的实施方案》的通知

潍坊市人民政府办公室印发《关于加快铸造企业转型升级推动实现高质量发展的实施方案》的通知文章属性•【制定机关】潍坊市人民政府办公室•【公布日期】2020.03.09•【字号】潍政办字〔2020〕23号•【施行日期】2020.04.01•【效力等级】地方规范性文件•【时效性】失效•【主题分类】企业经营机制转换正文潍坊市人民政府办公室印发《关于加快铸造企业转型升级推动实现高质量发展的实施方案》的通知各县市区人民政府,市属各开发区管委会,市政府各部门、单位,各重点企业,各人民团体:《关于加快铸造企业转型升级推动实现高质量发展的实施方案》已经市政府第五十三次常务会议研究通过,现印发给你们,请结合实际认真组织实施。
潍坊市人民政府办公室2020年3月9日关于加快铸造企业转型升级推动实现高质量发展的实施方案为加快实现全市铸造企业转型升级和高质量发展,根据国家、省有关规定和《关于印发潍坊市铸造行业转型升级实施意见的通知》(潍政办字〔2019〕25号)、《关于印发2019-2020年冬春季大气污染综合治理攻坚方案的通知》(潍环委发〔2019〕10号)要求,结合我市实际,制定如下实施方案。
一、基本原则(一)绿色环保。
依法落实企业环境保护主体责任,坚持清洁生产,在铸造生产各个环节,积极采用环保节能装备,节约用能、节约用水、节约用材,降低污染排放,确保废气、废水稳定达标排放,固体废弃物安全处置。
(二)共建共享。
通过建立铸造共享工厂、共享平台,培育一批铸造模具生产服务企业、短流程铸造熔炼企业、铸造喷涂企业、铸造用砂服务企业、检测实验中心,提高熔炼、制模、喷涂、铸造废砂处理、检测专业化水平,做到资源信息共享,实现铸造行业低碳共享发展。
(三)转型升级。
坚持以先进技术改造传统行业,积极推广应用铸造新技术、新设备、新工艺,提高铸造工艺、技术和装备水平,淘汰“高污染、高消耗、低效率”的落后工艺装备,推进智能化铸造,提高铸造企业发展的质量水平、效益水平。
铸件质量提升方案范文

铸件质量提升方案范文英文回答:Improving the quality of castings is crucial for ensuring the overall performance and reliability of the final products. Here, I will present a comprehensive plan to enhance the quality of castings.Firstly, it is essential to optimize the casting process. This involves carefully selecting the appropriate materials, designing the mold, and controlling the casting parameters. For example, in a foundry, we can use advanced simulation software to analyze the flow of molten metal and identify potential defects, such as shrinkage or porosity. By making adjustments to the mold design and process parameters, we can minimize these defects and improve the quality of the castings.Secondly, implementing strict quality control measures is vital. This includes conducting thorough inspections ateach stage of the casting process, from raw material inspection to final product testing. For instance, we can use non-destructive testing techniques like X-ray or ultrasonic testing to detect any internal defects that may compromise the integrity of the castings. By identifying and removing defective castings early on, we can prevent them from reaching the customers and ensure only high-quality products are delivered.Furthermore, investing in employee training and skill development is crucial. By providing comprehensive training programs, we can equip our workers with the necessary knowledge and skills to perform their tasks effectively. Additionally, fostering a culture of continuous improvement and encouraging open communication within the team can also contribute to enhancing the quality of castings. For instance, conducting regular meetings to discuss any issues or challenges faced during the casting process can lead to valuable insights and innovative solutions.Lastly, establishing strong partnerships with suppliers is essential. By collaborating closely with materialsuppliers, we can ensure the consistent quality of raw materials used in the casting process. Additionally, maintaining open and transparent communication with customers can help us understand their specificrequirements and expectations, enabling us to tailor our casting process accordingly.In conclusion, improving the quality of castingsrequires a comprehensive approach that involves optimizing the casting process, implementing strict quality control measures, investing in employee training, and establishing strong partnerships. By adopting these strategies, we can enhance the overall quality and reliability of our castings, resulting in satisfied customers and increased competitiveness in the market.中文回答:提升铸件质量对于确保最终产品的综合性能和可靠性至关重要。
铸造质量与检验

铸造质量与检验铸造是一种重要的制造工艺,广泛应用于汽车、机械、航空航天等行业。
铸造质量的好坏直接影响到制品的性能和使用寿命。
为了确保铸件的质量,铸造过程中需要进行严格的检验。
本文将探讨铸造质量与检验的相关内容。
一、铸造质量的影响因素铸造质量受到多个因素的影响,包括:1.原材料的质量:铸造过程中使用的原材料包括金属、砂型、熔剂等,它们的质量直接决定了铸造品的质量。
2.铸造工艺的控制:铸造工艺包括砂型制备、熔炼、浇注、冷却等环节,每个环节都需要控制参数,以确保铸件的完整性和性能。
3.铸型设计:铸型的设计需要考虑到铸件的形状、尺寸、壁厚等因素,合理的铸型设计能够降低铸件的缺陷率。
4.设备状态和操作技术:铸造设备的状态和操作技术直接影响到铸件的质量,如炉温控制、浇注速度控制等。
二、铸造质量的检验方法为了确保铸件的质量,需要采用适当的检验方法,主要包括以下几种:1.视觉检验:视觉检验是最常用的一种检验方法,通过目视观察铸件的外观,检查是否有裂纹、气孔、夹杂物等表面缺陷。
2.尺寸检验:尺寸检验主要是对铸件的几何尺寸进行测量,以检查是否符合设计要求。
3.金相检验:金相检验是通过显微镜观察铸件的金相组织结构,以了解铸件的显微组织情况和组织均匀性。
4.硬度检验:硬度检验是通过硬度计对铸件的硬度进行测量,以表示铸件的抗拉强度和耐磨性。
5.化学成分分析:化学成分分析是通过对铸件材料进行化学成分测定,以验证其材料的成分是否符合标准要求。
6.无损检测:无损检测是利用超声波、射线等非破坏性的方法对铸件进行检测,以发现内部缺陷、裂纹等问题。
三、铸造质量控制与提升为了确保铸造质量,需要进行严格的质量控制与提升措施。
1.制定质量控制计划:在铸造过程中,制定详细的质量控制计划,明确每个环节的控制要点和控制方法。
2.培训操作人员:确保操作人员具备良好的专业知识和技能,能够正确地操作铸造设备和工艺,并严格遵守操作规程。
3.强化设备维护:定期检查和维护铸造设备,确保其正常运行,减少设备故障对铸件质量的影响。
铸造质量年度工作计划
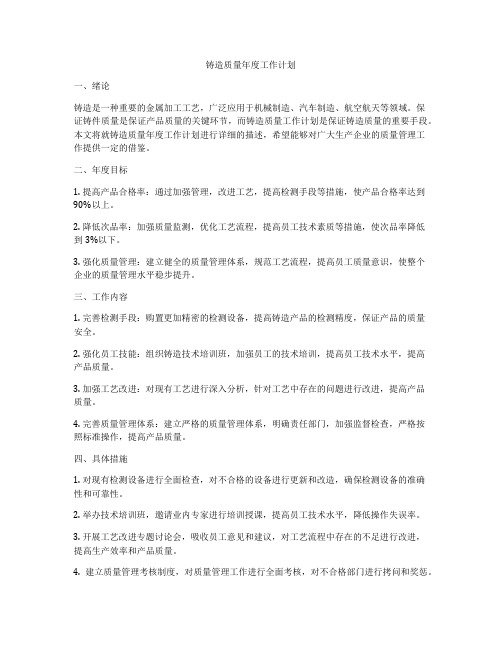
铸造质量年度工作计划一、绪论铸造是一种重要的金属加工工艺,广泛应用于机械制造、汽车制造、航空航天等领域。
保证铸件质量是保证产品质量的关键环节,而铸造质量工作计划是保证铸造质量的重要手段。
本文将就铸造质量年度工作计划进行详细的描述,希望能够对广大生产企业的质量管理工作提供一定的借鉴。
二、年度目标1. 提高产品合格率:通过加强管理,改进工艺,提高检测手段等措施,使产品合格率达到90%以上。
2. 降低次品率:加强质量监测,优化工艺流程,提高员工技术素质等措施,使次品率降低到3%以下。
3. 强化质量管理:建立健全的质量管理体系,规范工艺流程,提高员工质量意识,使整个企业的质量管理水平稳步提升。
三、工作内容1. 完善检测手段:购置更加精密的检测设备,提高铸造产品的检测精度,保证产品的质量安全。
2. 强化员工技能:组织铸造技术培训班,加强员工的技术培训,提高员工技术水平,提高产品质量。
3. 加强工艺改进:对现有工艺进行深入分析,针对工艺中存在的问题进行改进,提高产品质量。
4. 完善质量管理体系:建立严格的质量管理体系,明确责任部门,加强监督检查,严格按照标准操作,提高产品质量。
四、具体措施1. 对现有检测设备进行全面检查,对不合格的设备进行更新和改造,确保检测设备的准确性和可靠性。
2. 举办技术培训班,邀请业内专家进行培训授课,提高员工技术水平,降低操作失误率。
3. 开展工艺改进专题讨论会,吸收员工意见和建议,对工艺流程中存在的不足进行改进,提高生产效率和产品质量。
4. 建立质量管理考核制度,对质量管理工作进行全面考核,对不合格部门进行拷问和奖惩。
5. 加强对原材料的管控,严格按照标准要求采购原材料,确保原材料质量符合要求。
五、保障措施1. 对整个年度工作计划进行详细分解,制定具体的任务目标和完成时间,确保工作计划的有效实施。
2. 加强对每个环节的质量监督,建立检查记录,对发现的问题及时处理,确保产品质量符合标准。
铸造加工质量月活动方案
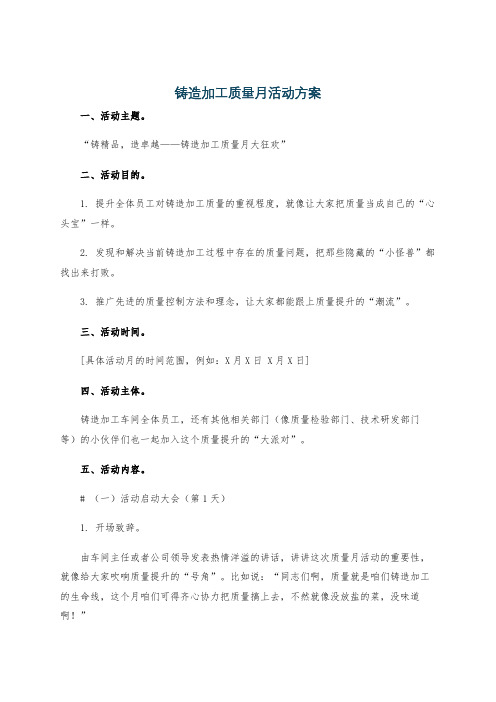
铸造加工质量月活动方案一、活动主题。
“铸精品,造卓越——铸造加工质量月大狂欢”二、活动目的。
1. 提升全体员工对铸造加工质量的重视程度,就像让大家把质量当成自己的“心头宝”一样。
2. 发现和解决当前铸造加工过程中存在的质量问题,把那些隐藏的“小怪兽”都找出来打败。
3. 推广先进的质量控制方法和理念,让大家都能跟上质量提升的“潮流”。
三、活动时间。
[具体活动月的时间范围,例如:X月X日 X月X日]四、活动主体。
铸造加工车间全体员工,还有其他相关部门(像质量检验部门、技术研发部门等)的小伙伴们也一起加入这个质量提升的“大派对”。
五、活动内容。
# (一)活动启动大会(第1天)1. 开场致辞。
由车间主任或者公司领导发表热情洋溢的讲话,讲讲这次质量月活动的重要性,就像给大家吹响质量提升的“号角”。
比如说:“同志们啊,质量就是咱们铸造加工的生命线,这个月咱们可得齐心协力把质量搞上去,不然就像没放盐的菜,没味道啊!”2. 质量月活动计划介绍。
详细介绍活动的计划安排,包括各种比赛、培训、检查等活动内容,让大家心里都有个底,就像给大家发一张“活动寻宝图”。
3. 团队宣誓。
全体参与人员分成小组,每个小组的组长带领组员进行质量宣誓,比如:“我们承诺,在质量月里,认真对待每一个铸造加工环节,不放过任何一个质量瑕疵,为打造优质产品而努力!”喊出大家对质量的决心。
# (二)质量培训讲座(第2 3天)1. 内部专家讲座。
邀请公司内部经验丰富的老师傅或者技术骨干,给大家讲讲铸造加工中的质量要点,从原材料的选择到最后的成品检验,就像老师傅传授独门秘籍一样。
老师傅可以结合自己多年的实战经验,讲一些有趣的案例,像“曾经有一次,就是因为一个小小的砂眼,差点让一整批产品都报废了,大家可不能小瞧这些小问题啊!”2. 外部专家视频讲座。
如果有条件的话,找一些行业内知名的外部专家录制的视频讲座播放给大家看,让大家学习外面先进的质量理念和技术,就像打开一扇通往质量新世界的大门。
铸件质量控制计划
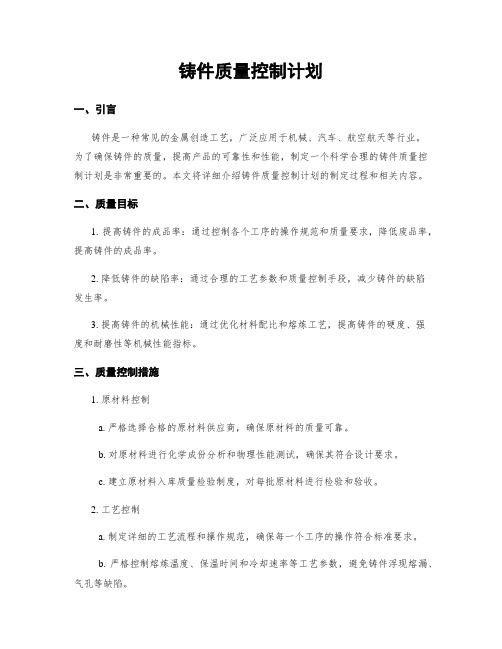
铸件质量控制计划一、引言铸件是一种常见的金属创造工艺,广泛应用于机械、汽车、航空航天等行业。
为了确保铸件的质量,提高产品的可靠性和性能,制定一个科学合理的铸件质量控制计划是非常重要的。
本文将详细介绍铸件质量控制计划的制定过程和相关内容。
二、质量目标1. 提高铸件的成品率:通过控制各个工序的操作规范和质量要求,降低废品率,提高铸件的成品率。
2. 降低铸件的缺陷率:通过合理的工艺参数和质量控制手段,减少铸件的缺陷发生率。
3. 提高铸件的机械性能:通过优化材料配比和熔炼工艺,提高铸件的硬度、强度和耐磨性等机械性能指标。
三、质量控制措施1. 原材料控制a. 严格选择合格的原材料供应商,确保原材料的质量可靠。
b. 对原材料进行化学成份分析和物理性能测试,确保其符合设计要求。
c. 建立原材料入库质量检验制度,对每批原材料进行检验和验收。
2. 工艺控制a. 制定详细的工艺流程和操作规范,确保每一个工序的操作符合标准要求。
b. 严格控制熔炼温度、保温时间和冷却速率等工艺参数,避免铸件浮现熔漏、气孔等缺陷。
c. 对熔炼炉和铸造设备进行定期维护和检修,确保设备的正常运行和工艺的稳定性。
d. 建立铸件尺寸检验制度,对每一个工序的铸件进行尺寸检验,确保产品尺寸的精度和一致性。
3. 检验控制a. 建立完善的铸件检验标准和方法,包括外观检验、尺寸检验、力学性能测试等。
b. 配备先进的检测设备和仪器,确保检验结果的准确性和可靠性。
c. 对不合格的铸件进行追溯和处理,找出问题原因并采取相应的纠正措施。
四、质量记录和分析1. 建立质量记录档案,包括原材料检验记录、工艺参数记录、铸件检验记录等,以便追溯和分析。
2. 定期对质量数据进行统计和分析,找出存在的问题和改进的方向。
3. 建立质量改进措施和纠正预防措施,确保质量问题得到及时解决和防止再次发生。
五、质量培训1. 对员工进行相关的质量培训,提高其对质量控制的认识和操作技能。
2. 定期组织质量知识培训和技术交流会议,促进质量管理的持续改进和提升。
球墨铸铁提高球化率的工艺实用方案
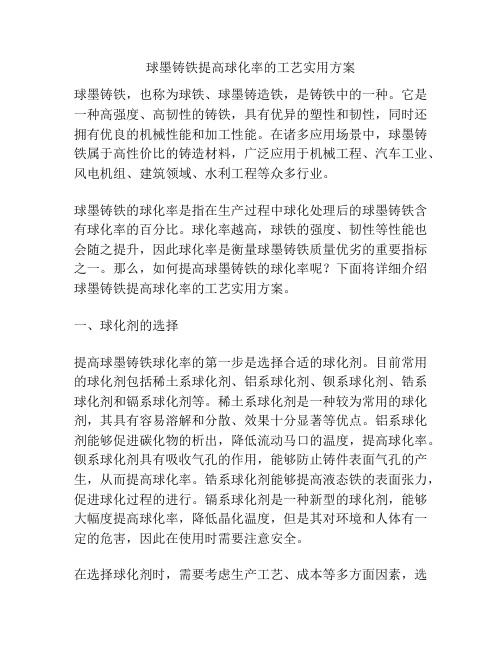
球墨铸铁提高球化率的工艺实用方案球墨铸铁,也称为球铁、球墨铸造铁,是铸铁中的一种。
它是一种高强度、高韧性的铸铁,具有优异的塑性和韧性,同时还拥有优良的机械性能和加工性能。
在诸多应用场景中,球墨铸铁属于高性价比的铸造材料,广泛应用于机械工程、汽车工业、风电机组、建筑领域、水利工程等众多行业。
球墨铸铁的球化率是指在生产过程中球化处理后的球墨铸铁含有球化率的百分比。
球化率越高,球铁的强度、韧性等性能也会随之提升,因此球化率是衡量球墨铸铁质量优劣的重要指标之一。
那么,如何提高球墨铸铁的球化率呢?下面将详细介绍球墨铸铁提高球化率的工艺实用方案。
一、球化剂的选择提高球墨铸铁球化率的第一步是选择合适的球化剂。
目前常用的球化剂包括稀土系球化剂、铝系球化剂、钡系球化剂、锆系球化剂和镉系球化剂等。
稀土系球化剂是一种较为常用的球化剂,其具有容易溶解和分散、效果十分显著等优点。
铝系球化剂能够促进碳化物的析出,降低流动马口的温度,提高球化率。
钡系球化剂具有吸收气孔的作用,能够防止铸件表面气孔的产生,从而提高球化率。
锆系球化剂能够提高液态铁的表面张力,促进球化过程的进行。
镉系球化剂是一种新型的球化剂,能够大幅度提高球化率,降低晶化温度,但是其对环境和人体有一定的危害,因此在使用时需要注意安全。
在选择球化剂时,需要考虑生产工艺、成本等多方面因素,选择最优的球化剂。
同时,为了避免球化剂的混杂和影响,需要注意球化剂的储存和使用。
二、铁液的浇注温度和冷却速率铁液的浇注温度和冷却速率对球墨铸铁的球化率有着明显影响。
在浇注时,铁液的温度太低会导致球化剂未能完全分解,球化率低;而温度太高则会使球化剂的反应速度变慢,同样影响球化率。
因此,在生产过程中需要合理选择铁液的浇注温度,通常情况下铁液的温度控制在1450-1550℃之间。
除了温度,冷却速率也会影响球墨铸铁的球化率。
快速冷却能够降低球化剂的化学反应速率,从而影响球化率。
因此,在铸造过程中需要控制冷却速率,确保铁液冷却均匀。
铸件质量控制计划
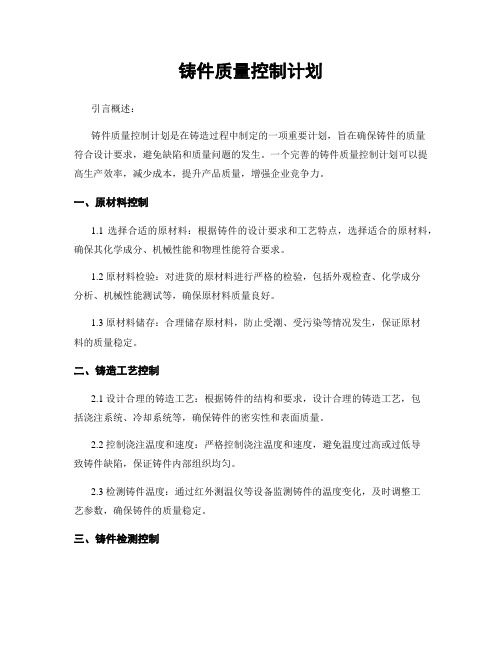
铸件质量控制计划引言概述:铸件质量控制计划是在铸造过程中制定的一项重要计划,旨在确保铸件的质量符合设计要求,避免缺陷和质量问题的发生。
一个完善的铸件质量控制计划可以提高生产效率,减少成本,提升产品质量,增强企业竞争力。
一、原材料控制1.1 选择合适的原材料:根据铸件的设计要求和工艺特点,选择适合的原材料,确保其化学成分、机械性能和物理性能符合要求。
1.2 原材料检验:对进货的原材料进行严格的检验,包括外观检查、化学成分分析、机械性能测试等,确保原材料质量良好。
1.3 原材料储存:合理储存原材料,防止受潮、受污染等情况发生,保证原材料的质量稳定。
二、铸造工艺控制2.1 设计合理的铸造工艺:根据铸件的结构和要求,设计合理的铸造工艺,包括浇注系统、冷却系统等,确保铸件的密实性和表面质量。
2.2 控制浇注温度和速度:严格控制浇注温度和速度,避免温度过高或过低导致铸件缺陷,保证铸件内部组织均匀。
2.3 检测铸件温度:通过红外测温仪等设备监测铸件的温度变化,及时调整工艺参数,确保铸件的质量稳定。
三、铸件检测控制3.1 X射线探伤:对铸件进行X射线探伤,检测铸件内部是否存在气孔、夹杂等缺陷,及时发现并进行修补。
3.2 超声波探伤:利用超声波技术对铸件进行探伤,检测铸件的内部结构是否均匀,确保铸件的质量可靠。
3.3 磁粉探伤:采用磁粉探伤技术对铸件进行检测,发现铸件表面是否存在裂纹、夹杂等缺陷,及时处理。
四、表面处理控制4.1 砂型表面处理:对砂型进行喷涂、涂覆等表面处理,保证砂型表面光滑、坚固,避免对铸件表面造成损伤。
4.2 清理铸件表面:清理铸件表面的氧化皮、砂粒等杂质,确保铸件表面光洁,提高铸件的外观质量。
4.3 表面涂层处理:根据需要对铸件进行表面涂层处理,如喷漆、镀层等,提高铸件的耐腐蚀性和美观度。
五、质量记录与追溯5.1 记录生产数据:对每一批次生产的铸件进行详细记录,包括原材料检验报告、生产工艺参数、检测结果等,便于追溯质量问题。
如何提升精密铸件质量
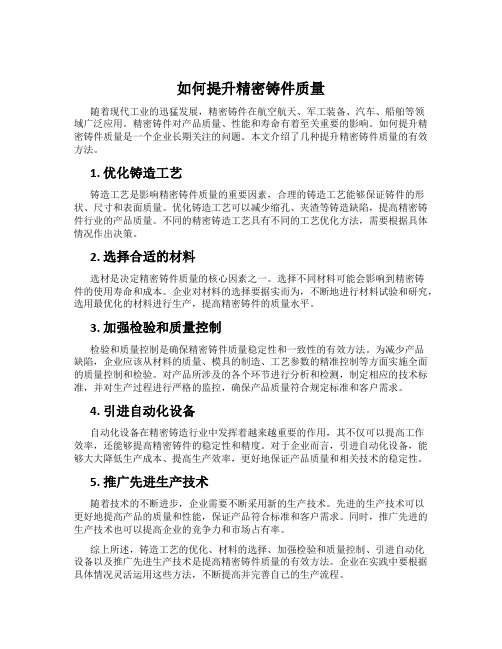
如何提升精密铸件质量随着现代工业的迅猛发展,精密铸件在航空航天、军工装备、汽车、船舶等领域广泛应用。
精密铸件对产品质量、性能和寿命有着至关重要的影响。
如何提升精密铸件质量是一个企业长期关注的问题。
本文介绍了几种提升精密铸件质量的有效方法。
1. 优化铸造工艺铸造工艺是影响精密铸件质量的重要因素,合理的铸造工艺能够保证铸件的形状、尺寸和表面质量。
优化铸造工艺可以减少缩孔、夹渣等铸造缺陷,提高精密铸件行业的产品质量。
不同的精密铸造工艺具有不同的工艺优化方法,需要根据具体情况作出决策。
2. 选择合适的材料选材是决定精密铸件质量的核心因素之一。
选择不同材料可能会影响到精密铸件的使用寿命和成本。
企业对材料的选择要据实而为,不断地进行材料试验和研究,选用最优化的材料进行生产,提高精密铸件的质量水平。
3. 加强检验和质量控制检验和质量控制是确保精密铸件质量稳定性和一致性的有效方法。
为减少产品缺陷,企业应该从材料的质量、模具的制造、工艺参数的精准控制等方面实施全面的质量控制和检验。
对产品所涉及的各个环节进行分析和检测,制定相应的技术标准,并对生产过程进行严格的监控,确保产品质量符合规定标准和客户需求。
4. 引进自动化设备自动化设备在精密铸造行业中发挥着越来越重要的作用,其不仅可以提高工作效率,还能够提高精密铸件的稳定性和精度。
对于企业而言,引进自动化设备,能够大大降低生产成本、提高生产效率,更好地保证产品质量和相关技术的稳定性。
5. 推广先进生产技术随着技术的不断进步,企业需要不断采用新的生产技术。
先进的生产技术可以更好地提高产品的质量和性能,保证产品符合标准和客户需求。
同时,推广先进的生产技术也可以提高企业的竞争力和市场占有率。
综上所述,铸造工艺的优化、材料的选择、加强检验和质量控制、引进自动化设备以及推广先进生产技术是提高精密铸件质量的有效方法。
企业在实践中要根据具体情况灵活运用这些方法,不断提高并完善自己的生产流程。
铸件质量提升方案范文
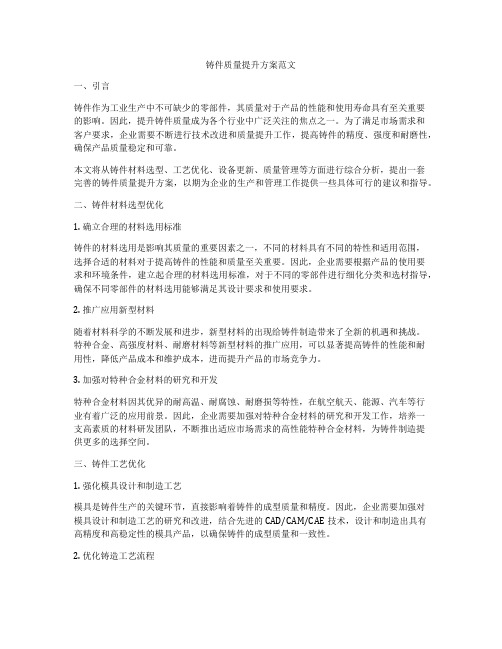
铸件质量提升方案范文一、引言铸件作为工业生产中不可缺少的零部件,其质量对于产品的性能和使用寿命具有至关重要的影响。
因此,提升铸件质量成为各个行业中广泛关注的焦点之一。
为了满足市场需求和客户要求,企业需要不断进行技术改进和质量提升工作,提高铸件的精度、强度和耐磨性,确保产品质量稳定和可靠。
本文将从铸件材料选型、工艺优化、设备更新、质量管理等方面进行综合分析,提出一套完善的铸件质量提升方案,以期为企业的生产和管理工作提供一些具体可行的建议和指导。
二、铸件材料选型优化1. 确立合理的材料选用标准铸件的材料选用是影响其质量的重要因素之一,不同的材料具有不同的特性和适用范围,选择合适的材料对于提高铸件的性能和质量至关重要。
因此,企业需要根据产品的使用要求和环境条件,建立起合理的材料选用标准,对于不同的零部件进行细化分类和选材指导,确保不同零部件的材料选用能够满足其设计要求和使用要求。
2. 推广应用新型材料随着材料科学的不断发展和进步,新型材料的出现给铸件制造带来了全新的机遇和挑战。
特种合金、高强度材料、耐磨材料等新型材料的推广应用,可以显著提高铸件的性能和耐用性,降低产品成本和维护成本,进而提升产品的市场竞争力。
3. 加强对特种合金材料的研究和开发特种合金材料因其优异的耐高温、耐腐蚀、耐磨损等特性,在航空航天、能源、汽车等行业有着广泛的应用前景。
因此,企业需要加强对特种合金材料的研究和开发工作,培养一支高素质的材料研发团队,不断推出适应市场需求的高性能特种合金材料,为铸件制造提供更多的选择空间。
三、铸件工艺优化1. 强化模具设计和制造工艺模具是铸件生产的关键环节,直接影响着铸件的成型质量和精度。
因此,企业需要加强对模具设计和制造工艺的研究和改进,结合先进的CAD/CAM/CAE技术,设计和制造出具有高精度和高稳定性的模具产品,以确保铸件的成型质量和一致性。
2. 优化铸造工艺流程铸造工艺是影响铸件质量的主要因素之一,企业需要结合产品的特点和要求,对铸造工艺进行全面分析和优化,不断寻求提高工艺效率和铸件质量的有效途径。
- 1、下载文档前请自行甄别文档内容的完整性,平台不提供额外的编辑、内容补充、找答案等附加服务。
- 2、"仅部分预览"的文档,不可在线预览部分如存在完整性等问题,可反馈申请退款(可完整预览的文档不适用该条件!)。
- 3、如文档侵犯您的权益,请联系客服反馈,我们会尽快为您处理(人工客服工作时间:9:00-18:30)。
关于进一步提升铸件产品质量的实施方案为进一步提升公司铸件产品的质量水平,为公司确定的“产品质量与国际知名企业接轨”的目标提供优质的毛坯产品保障,根据高层领导对铸件产品质量的具体要求,针对供应商当前生产工艺和产品质量实际,制订本提升方案。
一、指导思想
以全力保障“与国际知名企业接轨”的质量要求为目标,以高层领导的相关要求为指导,从强化质量意识、改进技术工艺、加大成本投入、规范流程管理入手,将产品质量控制点前移,切实把好每道工序质量关,全面提升铸件产品的质量水平。
为公司“树立企业形象,打造一流品牌,拓展业务市场”提供全力支持与保障。
二、组织领导
为切实加强对铸件产品质量提升工作的组织、落实与领导,公司成立“铸件产品质量提升工作领导小组”。
总经理任组长,质量技术总监、生产总监任副组长,*********为成员。
下设领导小组办公室,生产部长兼任办公室主任,负责相关工作的组织、衔接、协调与落实。
三、具体实施
(一)宣传发动阶段(*年*月*日至*月*日)
该阶段目标:改变以往对产品质量只求过得去,不求高标准和安于现状的错误思想观念,进一步强化质量意识,激发进取精神。
1、召开中层以上管理人员专题会议,传达贯彻有关精神,提高认识,统一思想,研究部署具体方案。
2、召开全体员工大会,传达高层领导关于“产品质量要与国际知名企业接轨”的相关要求;学习公司《关于进一步提升铸件产品质量的实施方案》,明确工作目标和具体要求。
3、班前会反复强调、灌输质量意识和理念。
4、悬挂横幅、标语,营造浓厚氛围。
(二)持续改进阶段(*年*月*日至*年*月*日)
该阶段目标:改变以往着力于后工序处理质量缺陷以及重成本、轻质量的做法,将质量控制点前移,加强对造型、浇铸等前工序的质量控制,适当增加成本投入,促使铸件产品质量提升达到预期目标。
质量提升分两步走:第一步(*年*月*日至*年*月*日):进一步加强和规范模具制作、日常保管、维护、维修以及现场使用的管理;对造型工艺加以改进,增加浇道管、型腔涂料、铬铁矿砂用量等生产成本投入;对氧割、碳弧气刨、打磨等后工序进行优
化调整,增加抛丸次数及提高控制标准,使铸件外观质量提升初见成效。
第二步(*年*月*日至*月*日):加强对炉前冶炼的质量控制和改进浇铸工艺,以优良的钢水品质确保铸件产品的内在质量,由此促使铸件产品质量整体迈上一个更高的档次,基本达到客户对铸件产品的质量要求。
(三)巩固深化阶段(*年*月*日至*月*日)
该阶段目标:对改进阶段积累的经验进行梳理和总结,将已经成熟的工艺及流程形成管理文件和相对固定模式,把这次质量提升成果转化为日常化、制度化工作。
1、工艺改进方面:各类技术优化、工艺流程、指标参数等记录资料的整理和汇总。
2、管理流程方面:质量要点控制、问题发现、问题解决、信息传达、跟踪处理等方面的管理措施和经验总结。
四、几点要求
(一)公司各部门、各车间负责人要认真领会高层领导对提升铸件产品质量的有关指示精神,破除安于现状、不思进取的守旧思想,并积极引导所属员工澄清模糊认识,增强质量意识。
统一思想,积极参与,攻坚克难,确保铸件产品质量提升工作顺利进行。
(二)各工序和岗位人员,务必认真履行岗位工作职责,在实施质量提升过程中,主动发现问题,积极采取措施,全程详细记录,不断总结经验,确保铸件产品质量提升工作取得实效。
(三)各部门、车间负责人要随时跟踪检查,将各工序反映的问题及时进行处理或向相关人员反馈,加强部门与部门之间、车间与车间之间,工序与工序之间的协同、衔接与配合。
不得对员工反映的问题置之不顾,或消极对待。
(四)公司全体员工要全员参与、全力投入到本次铸件产品质量提升工作中来,不得有抵触思想和情绪,不得以任何理由搪塞、推诿安排的工作事项。
五、奖罚措施
为确保本次质量提升工作顺利开展、取得实效。
公司安排专项资金*元,用于质量提升工作经费和奖励资金。
其中,*元用于领导小组的工作经费及成员的工作绩效奖励;另外*元作为对相关生产人员在质量提升工作中表现积极、贡献突出的奖励资金。
但是,对于在质量提升工作中,不服从安排、不服从管理、消极怠工、延误进度,或因个人行为造成不良后果和影响的,将依据公司《人力资源管理办法》中的有关奖惩规定视情给予相应处罚。
附:《铸件产品质量提升工作领导小组成员具体分工表》
铸件产品质量提升工作领导小组成员
具体分工表
铸件产品质量提升控制节点、检查标准及责任人明晰表
编制:张建新审核:批准:。