合成氨工艺造气炉工作原理
化肥厂合成氨装置生产原理及工艺流 共78页
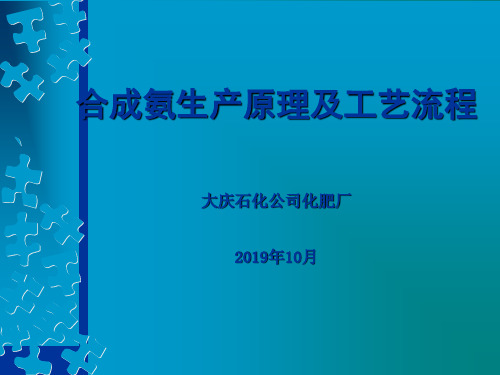
合成氨的生产方法因原料的不同主要有烃类蒸 汽转化法、重油部分氧化法、煤部分氧化法。作为 大型合成氨装置原料的烃类主要有天然气、油田伴 生气、重油和石脑油等。
合成氨的理论能耗约为22.3GJ/t·NH3,实际生 产要达到理论值是不可能的,现在合成氨生产最好 的能耗指标按天然气、渣油、煤原料分别为28.3 GJ/t·NH3、35.8 GJ/t·NH3和41.8 GJ/t·NH3。
氢源 正常生产时来自合成氨装置后部工序自产氢氮 气。也是最理想的氢源,它具有压力稳定、氢气浓 度适中、有害杂质少等优点。 开停工期间的氢源来自化工一厂。必须加入原 料气压缩机入口,配氢量少,脱硫效果不好,会造 成触媒中毒。配氢太多,由于氢气组份轻,容易造 成压缩机超速跳车,所以要求氢气压力必须稳定。
4.3 一段转化反应 在大型合成氨厂中,烃类蒸汽转化反应分两段进
行,即一段转化和二段转化。一段转化在外部供热的 管式转化炉内进行,二段转化在自热式的固定床层反 应炉中进行。
气态烃如天然气、油田伴生气等,其主要成分均 是甲烷,另外还含有少量其他低级烃,如乙烷等。因 此气态烃的蒸汽转化实际上主要就是甲烷的转化的反 应。
CO2气提 NH3气提 CO2气提
渣油,兰炼供,26万吨 天然气,长庆油田,3.5亿M3 渣油,总厂炼油厂供,26万吨
30
(30) 45
52
布朗流程
(52) 72
凯洛格流程
NH3气提 CO2气提
天然气,吐哈油田,3.5亿M3 天然气,大庆油田,4.6亿M3
30
52
渣油制氨谢尔流程 NH3气提 渣油,本厂或兰炼供,26万吨
合成氨生产原理及工艺流程
大庆石化公司化肥厂 2019年10月
1、合成氨概述与中石油合成氨企业状况
(工艺技术)合成氨工艺简介

合成氨工艺控制方案总结一合成氨工艺简介中小型氮肥厂是以煤为主要原料,采用固定层间歇气化法制造合成氨原料气。
从原料气的制备、净化到氨的合成,经过造气、脱硫、变换、碳化、压缩、精炼、合成等工段。
工艺流程简图如下所示:该装置主要的控制回路有:(1)洗涤塔液位;(2)洗涤气流量;(3)合成塔触媒温度;(4)中置锅炉液位;(5)中置锅炉压力;(6)冷凝塔液位;(7)分离器液位;(8)蒸发器液位。
其中触媒温度控制可采用全系数法自适应控制,其他回路采用PID控制。
二主要控制方案(一)造气工段控制工艺简介:固定床间歇气化法生产水煤气过程是以无烟煤为原料,周期循环操作,在每一循环时间里具体分为五个阶段;(1)吹风阶段约37s;(2)上吹阶段约39s;(3)下吹阶段约56s;(4)二上吹阶段约12s;(5)吹净阶段约6s.l、吹风阶段此阶段是为了提高炉温为制气作准备的。
这一阶段时间的长短决定炉温的高低,时间过长,炉温过高;时间过短,炉温偏低并且都影响发气量,炉温主要由这一阶段控制。
般工艺要求此阶段的操作时间约为整个循环周期的18%左右。
2、上吹加氮制气阶段在此阶段是将水蒸汽和空气同时加入。
空气的加入增加了气体中的氮气含量,是调节H2/N2的主要手段。
但是为了保证造气炉的安全该段时间最多不超过整个循环周期的26%。
3、上吹制气阶段该阶段与上吹加氯制气总时间为整个循环的32%,随着上吹制气的进行下部炉温逐渐下降,为了保证炉况和提高发气量,在此阶段蒸汽的流量最好能得以控制。
4、下吹制气阶段为了充分地利用炉顶部高温、提高发气量,下吹制气也是很重要的一个阶段。
这段时间约占整个循环的40%左右。
5、二次上吹阶段为了确保生产安全,造气炉再度进行吹风升温之前,须把下吹制气时留在炉底及下部管道中的半水煤气吹净以防不测,故进行第二次上映。
这段时间约占7%左右。
6、吹净阶段这段时间主要是回收上行煤气管线及设备内的半水煤气。
约占整个循环的3%。
煤化工合成氨工艺分析及节能优化对策
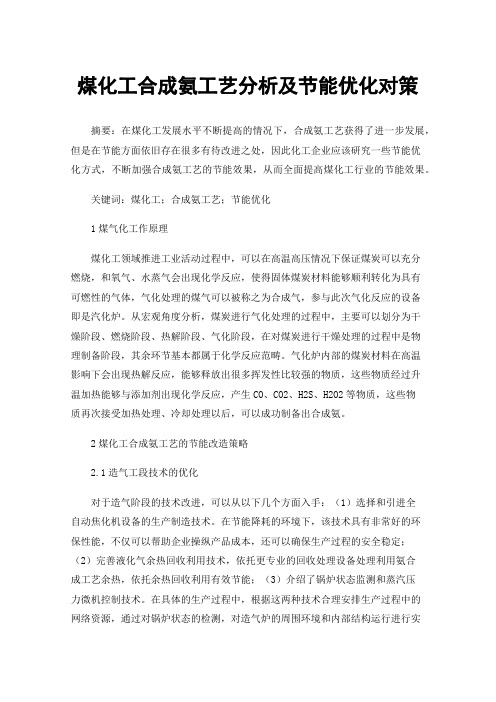
煤化工合成氨工艺分析及节能优化对策摘要:在煤化工发展水平不断提高的情况下,合成氨工艺获得了进一步发展,但是在节能方面依旧存在很多有待改进之处,因此化工企业应该研究一些节能优化方式,不断加强合成氨工艺的节能效果,从而全面提高煤化工行业的节能效果。
关键词:煤化工;合成氨工艺;节能优化1煤气化工作原理煤化工领域推进工业活动过程中,可以在高温高压情况下保证煤炭可以充分燃烧,和氧气、水蒸气会出现化学反应,使得固体煤炭材料能够顺利转化为具有可燃性的气体,气化处理的煤气可以被称之为合成气,参与此次气化反应的设备即是汽化炉。
从宏观角度分析,煤炭进行气化处理的过程中,主要可以划分为干燥阶段、燃烧阶段、热解阶段、气化阶段,在对煤炭进行干燥处理的过程中是物理制备阶段,其余环节基本都属于化学反应范畴。
气化炉内部的煤炭材料在高温影响下会出现热解反应,能够释放出很多挥发性比较强的物质,这些物质经过升温加热能够与添加剂出现化学反应,产生CO、CO2、H2S、H2O2等物质,这些物质再次接受加热处理、冷却处理以后,可以成功制备出合成氨。
2煤化工合成氨工艺的节能改造策略2.1造气工段技术的优化对于造气阶段的技术改进,可以从以下几个方面入手:(1)选择和引进全自动焦化机设备的生产制造技术。
在节能降耗的环境下,该技术具有非常好的环保性能,不仅可以帮助企业操纵产品成本,还可以确保生产过程的安全稳定;(2)完善液化气余热回收利用技术,依托更专业的回收处理设备处理利用氨合成工艺余热,依托余热回收利用有效节能;(3)介绍了锅炉状态监测和蒸汽压力微机控制技术。
在具体的生产过程中,根据这两种技术合理安排生产过程中的网络资源,通过对锅炉状态的检测,对造气炉的周围环境和内部结构运行进行实时检测。
如果在生产过程中发现问题,应及时解决预警信息,确保整个生产过程的安全稳定;(4)改进集中式高效气体洗涤器的应用。
在氨合成的具体过程中,可以采用集中高效气体洗涤器来缓解运行中的压力,特别是可以合理解决生产过程中产生的污水;(5)改进高炉余热回收利用技术。
国内典型合成氨装置工艺介绍

国内典型合成氨装置工艺介绍合成氨是一种广泛用于制备农药、化肥、涂料和塑料等化学产品的重要原料。
下面是国内典型合成氨装置工艺的介绍。
国内典型合成氨装置工艺通常采用哈伦-富特过程,该过程是通过在高温高压下将氮气与氢气经过一系列化学反应生成合成氨。
主要包括氮气副反应、合成气制备、催化反应和分离净化四个步骤。
下面将详细介绍每个步骤的过程。
首先,氮气副反应是将氮气通过精制空气中除去杂质,以得到高纯度的氮气。
在这一步骤中,氮气会通过压力摩尔筛进行脱氧和脱水处理,进而得到纯净的氮气。
接下来是合成气制备过程,合成气是指由氮气和氢气按照特定的比例混合而成的气体。
该步骤主要包括气体净化和合成气制备两个阶段。
在气体净化阶段,通过去除氢气中的杂质气体、液体和固体来提高氢气的纯度。
同时,还需要将氮气加热至合成气的反应温度。
在合成气制备阶段,首先将氮气和氢气按照一定的比例混合,然后进入合成气制备反应器。
由于合成气制备反应需要较高的温度和压力,通常使用催化剂来加速反应速率。
催化反应可以将氮气和氢气转化为合成气。
合成气中合成氨的产率取决于催化剂的性能和反应条件的控制。
催化反应结束后,合成气中会有一定的合成氨产生,但同时也会有未反应的氮气和氢气以及其他副产物存在。
因此,为了提高合成氨产率和纯度,需要进行分离净化处理。
分离净化过程分为两个部分,吸附分离和压缩分离。
吸附分离是通过将合成氨通入一种特殊的吸附剂中,吸附在表面上,从而分离出未反应的氮气和氢气,并将合成氨吸附在吸附剂上。
然后,通过改变压力或温度来释放出吸附在吸附剂上的合成氨。
压缩分离是通过改变气体的压力和温度,利用合成氨的气体性质与其他气体性质的差异,分离出纯净的合成氨。
以上就是国内典型合成氨装置工艺的介绍。
这个工艺通过一系列的化学反应和分离净化过程,可以高效地制备出高纯度的合成氨。
合成氨在农业和化工行业有着广泛的应用,对于促进经济发展和提高农产品的产量具有重要意义。
合成氨生产工艺介绍

1、合成氨生产工艺介绍1)造气工段造气实质上就是碳与氧气与蒸汽得反应,主要过程为吹风与制气。
具体分为吹风、上吹、下吹、二次上吹与空气吹净五个阶段。
原料煤间歇送入固定层煤气发生炉内,先鼓入空气,提高炉温,然后加入水蒸气与加氮空气进行制气。
所制得半水煤气进入洗涤塔进行除尘降温,最后送入半水煤气气柜。
造气工艺流程示意图2)脱硫工段煤中得硫在造气过程中大多以H2S得形式进入气相,它不仅会腐蚀工艺管道与设备,而且会使变换催化剂与合成催化剂中毒,因此脱硫工段得主要目得就就是利用DDS脱硫剂脱出气体中得硫。
气柜中得半水煤气经过静电除焦、罗茨风机增压冷却降温后进入半水煤气脱硫塔,脱除硫化氢后经过二次除焦、清洗降温送往压缩机一段入口。
脱硫液再生后循环使用。
脱硫工艺流程图3)变换工段变换工段得主要任务就是将半水煤气中得CO在催化剂得作用下与水蒸气发生放热反应,生成CO2与H2。
河南中科化工有限责任公司采用得就是中变串低变工艺流程。
经过两段压缩后得半水煤气进入饱与塔升温增湿,并补充蒸汽后,经水分离器、预腐蚀器、热交换器升温后进入中变炉回收热量并降温后,进入低变炉,反应后得工艺气体经回收热量与冷却降温后作为变换气送往压缩机三段入口。
变换工艺流程图4)变换气脱硫与脱碳经变换后,气体中得有机硫转化为H2S,需要进行二次脱硫,使气体中得硫含量在25mg/m3。
脱碳得主要任务就是将变换气中得CO2脱除,对气体进行净化,河南中科化工有限责任公司采用变压吸附脱碳工艺。
来自变换工段压力约为1、3MPa左右得变换气,进入水分离器,分离出来得水排到地沟。
变换气进入吸附塔进行吸附,吸附后送往精脱硫工段。
被吸附剂吸附得杂质与少量氢氮气在减压与抽真空得状态下,将从吸附塔下端释放出来,这部分气体称为解析气,解析气分两步减压脱附,其中压力较高得部分在顺放阶段经管道进入气柜回收,低于常压得解吸气经阻火器排入大气。
变换与脱硫工艺流程图5)碳化工段5、1、气体流程来自变换工段得变换气,依次由塔底进入碳化主塔、碳化付塔,变换气中得二氧化碳分别在主塔与付塔内与碳化液与浓氨水进行反应而被吸收。
合成氨工艺简介
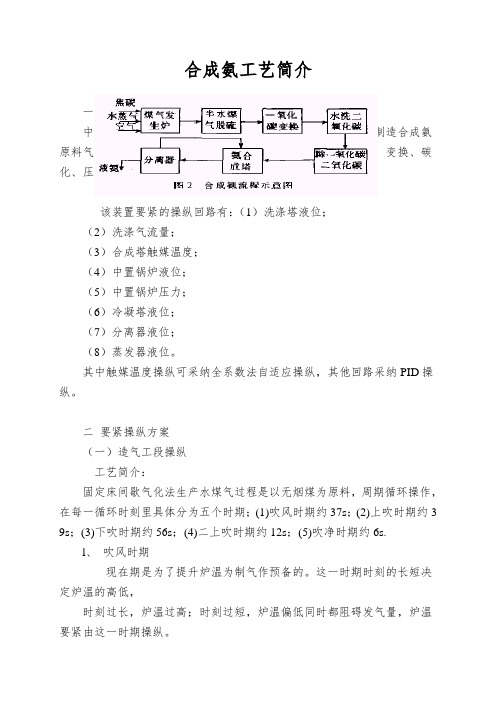
合成氨工艺简介一合成氨工艺简介中小型氮肥厂是以煤为要紧原料,采纳固定层间歇气化法制造合成氨原料气。
从原料气的制备、净化到氨的合成,通过造气、脱硫、变换、碳化、压缩、精炼、合成等工段。
工艺流程简图如下所示:该装置要紧的操纵回路有:(1)洗涤塔液位;(2)洗涤气流量;(3)合成塔触媒温度;(4)中置锅炉液位;(5)中置锅炉压力;(6)冷凝塔液位;(7)分离器液位;(8)蒸发器液位。
其中触媒温度操纵可采纳全系数法自适应操纵,其他回路采纳PID操纵。
二要紧操纵方案(一)造气工段操纵工艺简介:固定床间歇气化法生产水煤气过程是以无烟煤为原料,周期循环操作,在每一循环时刻里具体分为五个时期;(1)吹风时期约37s;(2)上吹时期约3 9s;(3)下吹时期约56s;(4)二上吹时期约12s;(5)吹净时期约6s.l、吹风时期现在期是为了提升炉温为制气作预备的。
这一时期时刻的长短决定炉温的高低,时刻过长,炉温过高;时刻过短,炉温偏低同时都阻碍发气量,炉温要紧由这一时期操纵。
般工艺要求现在期的操作时刻约为整个循环周期的18%左右。
2、上吹加氮制气时期在现在期是将水蒸汽和空气同时加入。
空气的加入增加了气体中的氮气含量,是调剂H2/N2的要紧手段。
然而为了保证造气炉的安全该段时刻最多不超过整个循环周期的26%。
3、上吹制气时期该时期与上吹加氯制气总时刻为整个循环的32%,随着上吹制气的进行下部炉温逐步下降,为了保证炉况和提升发气量,在现在期蒸汽的流量最好能得以操纵。
4、下吹制气时期为了充分地利用炉顶部高温、提升发气量,下吹制气也是专门重要的一个时期。
这段时刻约占整个循环的40%左右。
5、二次上吹时期为了确保生产安全,造气炉再度进行吹风升温之前,须把下吹制气时留在炉底及下部管道中的半水煤气吹净以防不测,故进行第二次上映。
这段时刻约占7%左右。
6、吹净时期这段时刻要紧是回收上行煤气管线及设备内的半水煤气。
约占整个循环的3%。
连续气化合成氨生产工艺介绍和原理培训教材

第一章设计基础资料一、装置能力1、总体说明本装置为HT-L粉煤气化炉气化装置,包括1500、1600、1700、1800单元:其中1500单元为磨煤及干燥装置,1600单元为煤加压及进煤装置,1700单元为气化及合成气洗涤装置,1800单元为渣及灰水处理装置。
1500单元设置三套磨煤机系统,正常运行二开一备,1600单元为粉煤输送,1700单元设置二台气化炉及合成气洗涤塔系统,1800单元为二级闪蒸及灰水处理。
2、装置能力本装置日消耗原料煤约1600吨,制备成5~90μm粒度的粉煤,在4.0MPa下气化为粗煤气,经洗涤,最终97417Nm3/h的煤气(干)送变换工段二、原料煤、氧气规格及化学品规格1、设计煤种原料煤规格煤质分析报告如下表所示,其中工业分析值和灰熔点元素分析值为推测值:2、氧气温度:34℃压力:5.0MPaG(在气化界区) 纯度:≥99.8%Ar:≤0.2%3、化学品(1)阳离子絮凝剂型号 BC-644或相当类型阳离子状态固体粉状(2)分散剂型号 WL-626或相当状态液态PH 2.0~3.0比重 1.15±0.05固含量≥30%三、公用工程条件1、高压锅炉给水悬浮物:≤5 mg/L 总硬度:≤2.0 μmol/L pH值(25℃)≥8.8~9.3 含油量:≤0.3 mg/L 含氧量:≤7 μg/L 含铁量:≤30 μg/L 含铜量:≤5 μg/L 含联氨:≤10~50 μg/L 二氧化硅:≤5 μg/L2、循环冷却水供水温度 34℃压力0.30Mpa(G),泵出口压力0.48Mpa(G)回水温度 42℃压力 0.20Mpa(G)污垢热阻 3.44×10-4m2.k/wPH值 7~8腐蚀余度 <0.125mm(碳钢)<0.005mm(不锈钢)3、脱盐水硬度≈0μmol/l电导率(25℃)≤0.3μS/cmSiO2 ≤20ppb温度 30~40℃4、蒸汽(1)9.8Mpa(G)高压蒸汽温度 535℃压力 8.83 MPa(G)(2)5.29Mpa(G) 次高压蒸汽温度 465℃压力 4.8 MPa(G)(3)2.5Mpa(G) 饱和蒸汽(4)1.27Mpa(G) 饱和蒸汽(5)0.5Mpa(G) 低压蒸汽5、仪表空气(含工厂空气,并由空分装置提供)温度≤40℃压力0.7Mpag(1)露点-40℃含油量<10mg/m3含尘量≤1mg/m3 (含尘粒径≤3微米)四、工厂空气温度40℃压力0.7MPa(G)含尘≤3μm含油≤10ppm(wt)五、高压氮气温度>40℃压力8.1MPaG纯度≥99.99%O2≤10ppm六、低压氮气温度40℃压力0.7MPaG纯度≥99.99%O2≤10ppm七、高压二氧化碳温度80℃压力8.12MPaG组成CO2≥98.5%八、电电源(1) 10kV供电电压 35kV/10kV (±10%)频率50Hz(±1%)相数三相三线,中性点不接地(2) 380V供电电压380/220V(±5%)频率50Hz(±1%)相数三相四线,中性点接地(3) 事故供电电压380/220(±5%)频率50Hz(±3%)相数三相九、燃料气开车燃料气来自煤化工一公司的半水煤气或合成甲烷气。
氨分解炉的工作原理
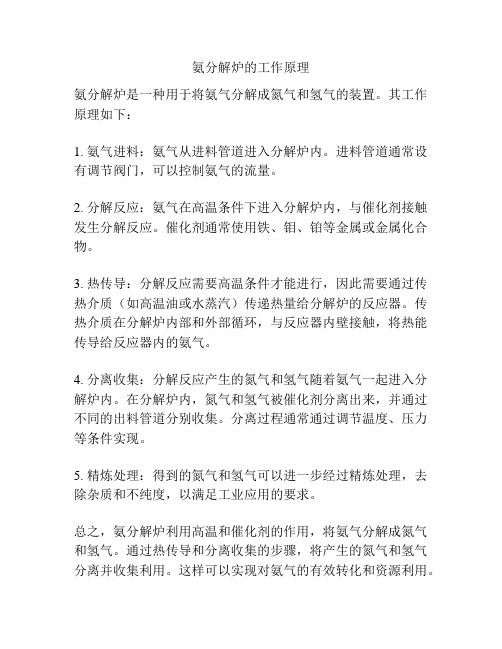
氨分解炉的工作原理
氨分解炉是一种用于将氨气分解成氮气和氢气的装置。
其工作原理如下:
1. 氨气进料:氨气从进料管道进入分解炉内。
进料管道通常设有调节阀门,可以控制氨气的流量。
2. 分解反应:氨气在高温条件下进入分解炉内,与催化剂接触发生分解反应。
催化剂通常使用铁、钼、铂等金属或金属化合物。
3. 热传导:分解反应需要高温条件才能进行,因此需要通过传热介质(如高温油或水蒸汽)传递热量给分解炉的反应器。
传热介质在分解炉内部和外部循环,与反应器内壁接触,将热能传导给反应器内的氨气。
4. 分离收集:分解反应产生的氮气和氢气随着氨气一起进入分解炉内。
在分解炉内,氮气和氢气被催化剂分离出来,并通过不同的出料管道分别收集。
分离过程通常通过调节温度、压力等条件实现。
5. 精炼处理:得到的氮气和氢气可以进一步经过精炼处理,去除杂质和不纯度,以满足工业应用的要求。
总之,氨分解炉利用高温和催化剂的作用,将氨气分解成氮气和氢气。
通过热传导和分离收集的步骤,将产生的氮气和氢气分离并收集利用。
这样可以实现对氨气的有效转化和资源利用。
化肥厂工艺反应原理简介.

化肥厂生产装置工艺反应原理简介化肥厂技术科2008-12-15第一章合成氨装置工艺原理1、合成氨工艺反应机理化肥厂合成氨装置工艺采用烃类蒸汽转化法。
整套工艺共有七个主反应,按照工艺流程顺序分别为钴钼加氢反应、氧化锌脱硫反应、转化反应(包括一段转化和二段转化反应)、变换反应(包括高温变换和低温变换反应)、脱碳反应、甲烷化反应、合成氨反应。
合成氨装置的原料为油田伴生气、空气和水蒸气,这三种原料经过上述七个主反应最后生成产品氨。
注: ①第三步转化反应分为一段和二段转化反应的原因是:如果要求在一段转化反应就使原料气中的甲烷完全转化为氢气、一氧化碳和二氧化碳,则必须要加大水碳比或者提高温度。
前一种方法必将导致耗用过多的水蒸气,而后一种方法对于采用外加热方式的一段反应炉来说对设备材质的要求也会更高。
因此在自热式的二段转化炉内通过气体自身燃烧放热,只需要在炉内做一层耐火衬里就能既解决高温对设备材料的要求又能增加反应温度,可使原料气中的甲烷完全转化,同时二段转化工段在加入空气助燃的同时又加入了合成氨反应所需的氮气。
②第四步变换反应分为高温变换和低温变换反应的原因是:采用Fe3O4催化剂的高变反应只能使96-98%的一氧化碳转化为二氧化碳,要想使一氧化碳含量降低到0.2-0.5%的指标范围内,只有在单质铜催化剂存在下的低温变换反应才能达到,如果在高温变换反应中应用单质铜催化剂,由于单质铜催化剂较昂贵会增加催化剂的使用成本,而且由于单质铜催化剂的作用温度低将导致废热的利用价值降低。
2、工艺流程简述油田伴生气加压至4.05MPa,经预热升温到371℃在脱硫工序脱硫后与水蒸汽混合,进入一段转化炉进行转化制H2反应,一段转化炉出来的转化气进入二段转化炉,在此引入空气,转化气在二段炉内燃烧掉一部分H2,放出热量以供进一步转化,同时获得N2。
二段转化气经余热回收后,进入变换系统,气体中的CO与水蒸汽反应,生成CO2和H2,从变换系统出来的气体经脱碳、甲烷化后为合成氨提供纯净的氢氮混合气,氢氮混合气经压缩至14.0MPa,送入合成塔进行合成氨反应。
中小型合成氨厂的流程与原理

合成氨厂学习总结在领导的帮助下,再学习了解了氨原料气的生产后,继续来到了合成氨厂学习。
在这里,谢谢帮助我的部领导、各分厂领导以及教会我许许多多知识的师傅们。
谢谢你们。
在学习过程中,我了解了氨合成系统的生产流程,了解了各种生产设备,掌握了初步的操作知识,同时也让我了解了氨合成的原理和初步的生氨合成产模型。
我想这些对我以后的工作中一定有很重要的帮助。
在学习掌握知识过程中,有很多设备和工艺使我的感触很深,但印象最深的应该是热交换器。
看到热交换器的时候,我想起了我第一个学习的地方煤气发生炉长达一分钟的吹风放空时间。
我觉得如果能让半水煤气与吹风空气换热,这样不但回收了热量,减少了煤气发生炉的吹风时间,也减少了放空时间,而且可以把多余的吹风时间用在制气上增加生产能力。
除此之外还可以减少了冷却水的使用,降低环境的污染。
具体措施是:在煤气发生炉上气道上使用换热器,使高温的半水煤气与吹风气换热。
降低半水煤气的出口温度,提高吹风气温度。
但得煤气发生炉吹风气和其他煤气发生炉的上气道出口半水煤气换热(吹风和制气有时间差)。
如1#的上气道出口的半水煤气与2#的吹风气换热。
学习人:魏启泽学习时间:2007年11月8日~2008年3月1日第一部分合成氨生产系统1.1 合成氨系统造气生产的半水煤气中除了含有合成氨所需的H2、N2外,还有大量的H2S、CO、CO2。
这些气体不但不是合成氨有效气体,而且对设备、管道有腐蚀作用,对催化剂有毒作用和能污染铜液。
所以进入合成塔前一定要将其脱出。
于是利用半脱岗位的脱硫塔脱除H2S,变化岗位的变换炉将CO转换成CO2,脱碳岗位脱除CO2、粗甲、铜洗脱除净化脱除不完全的H2S、CO、CO2。
在动力方面,除了半脱的脱硫塔和一段总管所需的动力是煤气风机提供外,其它各个工序的动力由压缩机提供。
压缩机是合成氨系统的动力核心。
1.2 煤气风机和半脱造气生产的半水煤气经过气柜的混合稳定,再经电捕焦油器分离出部分焦油后,一部分被罗茨风机加压送往新系统作为复肥系统的燃料气,另一部分被一次煤气风机送到净化的半脱岗位的脱硫塔脱除大量的H2S。
合成氨工艺及反应原理简介

合成氨工艺及反应原理简介合成氨工艺采用烃类蒸汽转化法。
天然气经加压至4.05MPa,经预热升温在脱硫工序脱硫后,与水蒸汽混合,进入一段转化炉进行转化制H2,随后进入二段转化炉,在此引入空气,转化气在炉内燃烧放出热量,供进一步转化,同时获得N2。
工艺气经余热回收后,进入变换系统,将CO变为CO2,随后经脱碳、甲烷化反应除去CO和CO2,分离出的CO2送往尿素工艺。
工艺气进入分子筛系统除去少量水份,为合成氨提供纯净的氢氮混合气。
氢氮混合气经压缩至14MPa,送入合成塔进行合成氨的循环反应,少量惰性气体经过普里森系统分离进行回收利用。
产品氨送往尿素工艺和氨罐保存。
合成氨工艺的5个过程:1、天然气脱硫:R-SH+H2=RH+H2S H2S+ZnO=H2O(汽)+ZnS2、转化CH4+H20(汽)=CO+3H2 CH4+2H2O(汽)=CO2+4H2 (H2+ 1/2 O2=H2O)3、变换:CO+H2O(汽)=CO2+H24、脱碳:1)K2CO3+CO2+H2O⇔2KHCO32KHCO3⇔K2CO3+CO2+H2O2)甲烷化:CO+3H2=CH4+H2O CO2+4H2=CH4+2H2O5、N2+3H2=2NH31 脱硫系统工艺流程及原理1.1流程天然气进入界区后分为两路:一路作原料气,另一路作燃料气。
原料天然气进入原料气压缩机吸入罐116-F,除去携带的液体,经过原料气压缩机102-J被压缩到4.05MPa(G),经过原料气预热盘管预热到399℃,接着原料气与来自合成气压缩机103-J一段的富氢气混合。
经过Co-Mo加氢器101-D把有机硫转换成H2S,将3 ml/m3的有机硫转化为无机硫,原料气中总硫为30~90ml/m3左右,经氧化锌脱硫槽脱硫至总硫小于0.5mg/m3。
随后进入氧化锌脱硫槽,天然气中的硫化物被ZnO所吸附,制得合格原料气。
ZnO脱硫槽共二个,可以串联或并联操作,一般串联操作。
阀门及管线的配置可以使任何一个脱硫槽停止使用而另一个继续运转。
合成氨工艺简介

合成氨工艺简介煤气化法是我国合成氨的主要制气方法,也是未来更替天然气和石油资源所必将采用的制气方法。
即利用无烟煤、蒸汽和空气在碳发生炉内生产合成氨所需要的气体,俗称半水煤气。
在已制得的半水煤气中,除了含有按合成工艺所需要的氮气和氢气外,还含有许多杂质和有害气体。
由于这些杂质和有害气体很容易使合成触媒中毒而降低触媒效能。
为保护触媒,延长其使用寿命,保证合成氨生产的正常进行,半水煤气中的杂质和有害气体必须在合成之前得以及时清除,这就需要对混合气体进行净化处理,并且要求连续性作业,以达到化学反应稳定进行,从而构成了合成氨工艺流程错综复杂和连续性强的生产特点。
一合成氨的生产方法简介氨的合成,必须制备合成氨的氢、氮原料气。
氮可取之于空气或将空气液化分离而制得,氮气或使空气通过燃料层汽化将产生CO或CO2转化为原料气。
氢气一般常用含有烃类的各种燃料制取,亦通过焦碳,无烟煤,重油等为原料与水作用的方法制取。
由于我国煤储量丰富,所以以煤为原料制氨在我国工业生产中广泛使用。
合成氨的过程一般可分为四个步骤:1.造气:即制备出含有氮一定比例的原料气。
2.净化:任何制气方法所得的粗原料气,除含有氢和氮外,还含有硫化氢、有机硫、一氧化碳、二氧化碳和少量氧,这些物质对氨合成催化剂均有害,需进行脱除,直至百万分之几的数量级为止。
在间歇式煤气炉制气流程中,脱硫置于变换之前,以保护变换催化剂的活性。
3.精炼:原料气的最终精炼包括清除微量一氧化碳、二氧化碳、氧、甲烷和过量氮,以确保氨合成催化剂活性和氨合成过程的经济运行。
4.合成:将合格的氢氮混合气体压缩到高压,在催化剂作用下合成氨气。
二合成氨反应的基本原理1. 造气:合成氨的原料——氢氮可以用下列两种方法取得(1)以焦碳与空气、水蒸气作用(2)将空气分离制取氮,由焦炉气分离制氢采用煤焦固定床间歇式汽化法。
反应方程如下:C+H2O=CO +H2 (1)CO+O2=CO2 (2)2.脱硫:无论以固体煤作原料还是以天然气、石油为原料制备氢氮原料气都含有一定成分的硫元素,无机硫主要含有硫化氢;有机硫主要含有二硫化碳、硫化氧碳等等。
合成氨工艺流程原理

合成氨工艺流程原理合成氨是一种重要的化工原料,广泛用于制造化肥、合成纤维和其他化学产品。
合成氨工艺流程是通过将氮气和氢气在特定条件下进行高效反应合成氨气。
以下是合成氨工艺流程原理的详细介绍。
合成氨的工艺流程主要包括催化剂选择、氮气净化、氢气净化、氨合成反应、气体分离和氨精制等步骤。
催化剂选择是合成氨工艺中的关键一步。
目前常用的合成氨催化剂是铁钼催化剂,它采用钾铝硅合金促进催化剂的活性,并能减少催化剂的脱活作用。
催化剂的选择和活性对于合成氨工艺的效率和生产能力有着重要的影响。
氮气净化是为了去除氮气中的杂质和水分。
通常通过压缩、冷冻和吸附等方法进行净化,确保氮气纯度达到合成氨反应的要求。
氢气净化是为了除去氢气中的杂质和水分。
常用的方法是通过活性炭、吸附剂和催化剂等材料吸附和催化处理氢气,以保证氢气的纯度和质量。
氨合成反应是合成氨工艺流程中的关键步骤。
氮气和氢气按照一定的摩尔比例在催化剂的作用下,经过高温高压条件下的合成反应生成氨气。
该反应是一个放热反应,反应温度通常在350-450摄氏度,反应压力在150-250兆帕范围内。
气体分离是将反应产生的氨气与未反应的氮气和氢气进行分离。
这一步骤通过升温、降压和吸附等方法对气体进行处理,使氨气从其他气体中分离出来。
氨精制是为了提高氨气的纯度和质量。
氨气经过冷却、压缩和精馏等处理,去除残余水分和杂质,最终得到纯净的合成氨。
总结起来,合成氨工艺流程是通过选择催化剂、净化氮气和氢气、氨合成反应、气体分离和氨精制等步骤来实现合成氨的生产。
这个流程工艺是在高温高压和特定条件下进行的,需要精确控制反应条件和催化剂的选择,以提高氨的产率和纯度。
合成氨工艺的发展对于提高化肥生产效率、减少能源消耗和环境污染具有重要意义。
液氨分解气化炉设备工艺原理

液氨分解气化炉设备工艺原理液氨分解气化炉是一种常用的气化设备,主要是将液态氨加热分解成氢气和氮气。
液氨分解气化炉的工艺原理主要涉及到炉内反应、传热、传质等多个方面。
液氨分解气化炉的工艺流程液氨分解气化炉的工艺流程包括氨的加料、加热、分解反应、产气、冷却等多个步骤。
1.液氨的加料先将液氨输送至炉站。
液氨经过氨泵加压,输送至炉内装有预热器和加热器的氨加热系统。
2.液氨的加热在氨加热系统中,液氨被加热至设定的分解温度。
加热器中的传热介质是热油或高温水蒸汽。
当液氨在加热器中加热过程中,同时充分与传热介质进行热交换,使液氨温度逐渐升高。
液氨加热至分解温度后,进入分解反应室。
3.分解反应当液氨进入分解反应室中,其分子开始分解成氢气和氮气。
反应初期,分解的氢气和氮气按反应公式反应生成,但随着反应的进行,氢气会在炉内继续反应,进一步生成一氧化碳和甲烷等不良物质。
因此,在反应末期,要注入少量的氧气,使CO化为CO2,减少污染物的排放。
4.产气处理分解出的氢气和氮气再经过冷却、吸附、干燥等工艺处理,最终产生高纯度的氢气和氮气。
液氨分解气化炉的工艺原理液氨分解气化炉的工艺原理主要涉及到炉内反应、传热、传质等多个方面。
1.炉内反应液氨分解气化炉利用高温下液氨分子的分解反应产生氢气和氮气。
反应公式为:NH3 → 1.5H2 + 0.5N2在反应过程中,要控制反应温度和反应时间,以保证氢气和氮气的产生率、氢气和氮气的纯度等符合工艺要求。
同时,要注意控制物料流量和反应气体的流动速度。
2.传热液氨分解气化炉中的氨加热系统采用高温传热油或水蒸汽作为传热介质,通过传热管将热量传到液氨中,使其逐渐加热至分解温度。
高温介质和液氨之间的传热,主要是通过对流和导热的方式进行,而液氨分解反应的放热过程则主要是通过辐射传热进行。
为提高传热效率,可以采用多级加热的方式进行加热,同时加热器的结构设计也需要考虑防结垢和结焦问题。
3.传质液氨分解气化炉中的传质主要是指氨和氢气、氮气等气体之间的传递。
合成氨工艺原理

合成氨工艺原理合成氨是一种重要的化工产品,广泛应用于化肥、医药、塑料等领域。
合成氨工艺是通过氮气和氢气在催化剂的作用下进行反应,生成氨气的过程。
本文将从催化剂选择、反应条件、反应原理等方面介绍合成氨工艺的原理。
首先,催化剂的选择对合成氨工艺至关重要。
常用的催化剂包括铁、铑、钼等金属,它们能够促进氮气和氢气的反应,提高反应速率和产物选择性。
其中,铁是最常用的催化剂,它能够在较低的温度和压力下催化氮气和氢气的反应,降低能耗,提高生产效率。
其次,合成氨反应的条件对反应效果有着重要影响。
合成氨的反应是一个放热反应,通常在较高的温度(400-500°C)和压力(100-300atm)下进行。
高温能够提高反应速率,而高压则有利于提高氨气的产率。
此外,还需要适量的催化剂和适当的反应时间来保证反应的充分进行。
合成氨的反应原理主要是氮气和氢气在催化剂的作用下发生氮氢键的断裂和形成,生成氨气。
氮气分子中的三根共价键在催化剂的作用下被分解成氮原子,并与氢气中的氢原子结合形成氨气。
这一过程是一个放热反应,放出大量的热能,因此需要采取相应的措施来控制反应温度,防止过热。
合成氨工艺的原理虽然看似简单,但其中涉及的化学反应、热力学和动力学等知识都需要深入研究和理解。
只有充分了解合成氨工艺的原理,才能够更好地指导工业生产实践,提高合成氨生产的效率和质量。
总之,合成氨工艺的原理涉及到催化剂选择、反应条件和反应原理等多个方面。
只有在这些方面做到科学合理的安排和控制,才能够保证合成氨工艺的顺利进行,从而获得高效率和高产量的合成氨产品。
希望本文的介绍能够对合成氨工艺的理解有所帮助,同时也希望相关领域的研究者能够在此基础上做出更深入的研究和探索。
焦炉尾气生产合成氨的原理

经过提氢后的富甲烷气送回焦化厂作为 燃烧气。
三、空分制氮工艺原理及过程简介
1、空分制氮工艺原理 N2在自然界中分布很广,是空气的主要 成分,主要以单质分子氮的形式存在于大 气之中。在干燥空气中,N2的体积占空气 的78.03%。因此,空气是制取氮气的最大 原料库,它取之不尽,用之不竭。 工业用氮气的制取总是以空气为原料, 将其中的O2和N2分离而获得,其方法主要 有:
基础培训专题
焦炉尾气生产合成氨的原理及过程
二0一二年五月
概述
焦炭生产过程中副产的大量焦炉尾气,而焦 炉煤气中含有丰富的氢气,H2体积分数约55%, 目前焦炉煤气主要用作工业和民用燃料,宝贵 的氢气资源未得到更好地利用,随着资源充分 利用的循环经济需要,焦炉煤气尤其是其中H2 的提取和利用成为焦炉煤气综合利用的发展方 向。
强
2、变压吸附提氢工艺流程简图
TSA 变温吸附 PSA-1 一级提氢 PSA-2 二级提氢
脱氧脱水装置
氢气去联合压缩机
焦炉气压缩机
富甲烷气去焦化 气柜 原料气 焦炉气预处理鼓风机
3、变压吸附提氢工艺流程简述
来自焦炉气柜压力约3KPa、温度30℃的焦 炉气经焦炉气预处理压缩机加压至35KPa、 80℃,进入固定管板间接水冷器冷却至40℃, 进入TSA变温吸附粗脱装置,在粗脱塔内,分 别除去焦油、硫化物、苯、奈等杂质。然后经 焦炉气压缩机加压至1.7MPa,冷却及除油水 后进入PSA-1(一级提氢)工序,
在装置的吸附塔中,吸附剂选择吸附的条 件下一次性除去甲烷等大部分杂质,获得 纯度大于83%的粗氢气,排出送入PSA-2 (二级提氢)工序,在装置的吸附塔中, 吸附剂选择吸附的条件下下一次性除去除 氢气外的大部分杂质,获得纯度大于 99.99%的氢气。
合成氨工艺原理

合成氨工艺原理
合成氨是一种重要的化工原料,广泛用于制备化肥、塑料、纤维素等产品。
合成氨的工艺原理主要包括两个步骤:氮气催化还原和氢气催化氧化。
氮气催化还原是指将氮气转化为氨气的化学反应。
该反应在催化剂的存在下进行,常用的催化剂有铁、钨等金属或金属合金。
氮气和氢气首先通过压缩机进行压缩,然后以适当的比例进入反应器中。
在反应器内,氮气分子被催化剂吸附并激活,形成活性吸附态。
氢气分子也被吸附到催化剂表面,并与氮气分子进行反应,生成氨气。
反应完成后,氨气被分离出来,纯度达到要求后可以作为成品使用。
氢气催化氧化是指将氢气转化为水的反应过程。
这一步骤是为了去除反应残留的氢气,同时防止反应产物中的氢气杂质。
在氮气催化还原后,残留的氢气与氧气一起进入氢气催化氧化反应器。
催化剂通常是铁氧化物或铝氧化物等,它们可以催化氢气和氧气反应生成水。
反应完成后,反应器中的氢气和水蒸气一同进入冷凝器,通过冷却和分离,分离出纯净的水。
以上就是合成氨的工艺原理,通过氮气催化还原和氢气催化氧化,在合适的条件下,可以高效地制备出纯度高的氨气。
这个工艺过程在化工工业中被广泛应用,为各行各业提供了重要的原料。
合成氨的生产方法及原理

合成氨的生产方法及原理
嘿,你知道合成氨是咋回事不?这可是个超级重要的化工过程呢!合成氨的生产方法主要是哈伯法。
先把氮气和氢气按一定比例混合,然后在高温高压和催化剂的作用下,让它们发生反应生成氨。
这就好比一场激烈的化学反应大战,氮气和氢气就是勇敢的战士,催化剂就是神奇的魔法棒,让它们快速结合在一起。
生产步骤呢,首先要制备纯净的氮气和氢气。
氮气可以从空气中分离得到,氢气可以通过水煤气反应或者其他方法制取。
然后把它们压缩到合适的压力,送入合成塔。
在合成塔里,催化剂发挥着关键作用,加速反应的进行。
这一步可得小心操作,要是出了岔子,那可就麻烦啦!比如压力控制不好,或者催化剂失效,那可就糟糕透了。
合成氨的过程安全性和稳定性那是相当重要啊!毕竟这涉及到高温高压的环境,稍有不慎就可能引发危险。
所以工厂里都有严格的安全措施,各种监测设备时刻盯着反应过程。
这就像给化学反应加上了一把安全锁,让它稳稳地进行。
那合成氨有啥用呢?应用场景可多啦!农业上,氨可以用来生产化肥,让庄稼长得壮壮的。
没有合成氨,咱们的粮食产量能有这么高吗?工业上,氨还可以用来制造其他化学品。
这就像一个万能的小助手,在各个领域都
能发挥大作用。
实际案例也不少呢!比如某个化肥厂,通过合成氨生产出了高质量的化肥,农民们用了这些化肥,庄稼丰收了,那叫一个高兴啊!这效果,简直杠杠的。
合成氨就是这么厉害,它为我们的生活带来了巨大的改变。
它就像一个默默奉献的英雄,虽然不那么起眼,但却不可或缺。
所以啊,咱们得重视合成氨的生产,让它更好地为我们服务。
- 1、下载文档前请自行甄别文档内容的完整性,平台不提供额外的编辑、内容补充、找答案等附加服务。
- 2、"仅部分预览"的文档,不可在线预览部分如存在完整性等问题,可反馈申请退款(可完整预览的文档不适用该条件!)。
- 3、如文档侵犯您的权益,请联系客服反馈,我们会尽快为您处理(人工客服工作时间:9:00-18:30)。
合成氨工艺造气炉工作原理
合成氨工艺的造气炉主要包括催化剂床、还原气发生器、燃烧器、加热器和废气烟气处理装置等组成部分。
其工作原理如下:
1. 还原气发生器产生还原气体,通常使用煤、重油、天然气等作为原料,经过加热燃烧反应,产生含有大量CO和H2的混
合气体。
这一步骤的目的是为了提供合成氨所需的还原剂。
2. 合成气中的CO和H2进入催化剂床。
催化剂床通常使用铁
系或镍系催化剂,并在高温和高压条件下进行反应。
CO和
H2经过一系列催化反应,生成含有高浓度氨气的合成气。
3. 合成气进一步通过换热器进行冷却,以控制反应温度,并减少不需要的副产物。
4. 在燃烧器中,还原气体与空气进行混合燃烧,产生高温高压的燃烧气,用于提供炉内所需的热量。
5. 加热器通过将炉内产生的高温烟气与进料气体进行换热,提高工艺热效率。
6. 废气烟气处理装置用于净化炉内产生的废气和烟气,通常通过脱硫、脱氢、除尘等工艺进行气体处理,以降低对环境的污染。
通过以上工艺步骤,合成氨工艺的造气炉可以将原料转化为合成氨的高纯度气体,用于后续的合成氨生产。