05_本体聚合生产工艺
本体聚合(bulk

5.2 本体聚合
⒊ 本体聚合工艺 鉴于本体聚合的特点,为了使本体聚合能够正常进行 为了使本体聚合能够正常进行,本 鉴于本体聚合的特点 为了使本体聚合能够正常进行 本 体聚合工艺分“预聚” 聚合”两段进行。 体聚合工艺分“预聚”和“聚合”两段进行。 预聚”是在聚合初期,转化率不高 体系的粘度不大, 转化率不高,体系的粘度不大 “ 预聚 ” 是在聚合初期 转化率不高 体系的粘度不大 聚合热容易排出的阶段,采用较高的温度在较短的时间内 采用较高的温度在较短的时间内,利 聚合热容易排出的阶段 采用较高的温度在较短的时间内 利 用搅拌加速反应,以便使自动加速现象提前到来 以便使自动加速现象提前到来。 用搅拌加速反应 以便使自动加速现象提前到来。 这样,就缩短了聚合周期 提高了生产效率。 就缩短了聚合周期,提高了生产效率 这样 就缩短了聚合周期 提高了生产效率。 “ 聚合” 是一旦自动加速现象到来,就要降低聚合温度。 聚合 ” 是一旦自动加速现象到来 就要降低聚合温度。 就要降低聚合温度 以降低正常聚合的速率,充分利用自动加速现象 充分利用自动加速现象,使反应基本 以降低正常聚合的速率 充分利用自动加速现象 使反应基本 上在平稳的条件下进行。 上在平稳的条件下进行。 这就避免了由于自动加速现象而造成的局部过热,既保 这就避免了由于自动加速现象而造成的局部过热 既保 证了安全生产,又保证了产品质量 这就是本体聚合分“预聚” 又保证了产品质量,这就是本体聚合分 证了安全生产 又保证了产品质量 这就是本体聚合分“ 预聚” 聚合”两段进行的原因。 和“聚合”两段进行的原因。 本体聚合工艺采用预聚和聚合两段进行, 本体聚合工艺采用预聚和聚合两段进行 并且在不同聚 合阶段控制不同的聚合温度。 合阶段控制不同的聚合温度。
5.2 本体聚合
本体聚合聚丙烯生产工艺汇合

聚丙烯生产工艺本体法-气相法组合工艺主要包括巴塞尔公司的Spheripol工艺、日本三井化学公司的Hypol工艺、北欧化工公司的Borstar工艺等。
(1)Spheripol工艺。
Spheripol工艺由巴塞尔(Basell)聚烯烃公司开发成功。
该技术自1982年首次工业化以来,是迄今为止最成功、应用最为广泛的聚丙烯生产工艺。
Spheripol工艺是一种液相预聚合同液相均聚和气相共聚相结合的聚合工艺,工艺采用高效催化剂,生成的PP粉料粒度其催化剂生产的粉料呈园球形,颗粒大而均匀,分布可以调节,既可宽又可窄。
可以生产全范围、多用途的各种产品。
其均聚和无规共聚产品的特点是净度高,光学性能好,无异味。
Spheripol工艺采用的液相环管反应器具有以下优点:<;P> (a)有很高的反应器时-空产率(可达400kgPP/h.m3),反应器的容积较小,投资少;(b)反应器结构简单,材质要求低,可用低温碳钢,设计制造简单,由于管径小(DN500或DN600),即使压力较高,管壁也较薄;(c)带夹套的反应器直腿部分可作为反应器框架的支柱,这种结构设计降低了投资;(d)由于反应器容积小,停留时间短,产品切换快,过渡料少;(e)聚合物颗粒悬浮于丙烯液体中,聚合物与丙烯之间有很好的热传递。
采用冷却夹套撤出反应热单位体积的传热面积大,传热系数大,环管反应器的总体传热系数高达1600W/(m2.℃);(f)环管反应器内的浆液用轴流泵高速循环,流体流速高达7m/s,因此可以使聚合物淤浆搅拌均匀,催化剂体系分布均匀,聚合反应条件容易控制而且可以控制得很精确,产品质量均一,不容易产生热点,不容易粘壁,轴流泵的能耗也较低;(g)反应器内聚合物浆液浓度高(质量分数大于50%),反应器的单程转化率高,均聚的丙烯单程转化率为50%-60%。
以上这些特点使环管反应器很适宜生产均聚物和无规共聚物。
Spheripol工艺一开始使用GF-2A、FT-4S、UCD-104等高效催化剂,催化剂活性达到40kgPP/gcat,产品等规度为90%-99%,可不脱灰、不脱无规物。
氯乙烯本体聚合制备聚氯乙烯的合成工艺

3.5 氯乙烯本体聚合制备聚氯乙烯的合成工艺3.5.1 概述氯乙烯聚合为聚氯乙烯的反应属于自由基连锁机理。
由于生成的聚氯乙烯不能溶于单体氯乙烯而沉淀析出,氯乙烯的本体聚合属于非均相聚合。
生成的聚氯乙烯产品为具有不同孔隙率的粉状固体。
世界上大规模生产PVC的方法有三种,悬浮聚合法占75%,乳液聚合法占15%,本体聚合法占10%。
我国悬浮聚合法占94%,其余为乳液聚合法。
本体聚合法仅在个别厂家计划生产。
氯乙烯本体聚合的优点有聚合体系无需介质水,免去干燥工序;设备利用率高,生产成本低;产品热稳定性、透明性均优于悬浮聚合产品;产品吸收增塑剂速度快,成型加工流动性好。
但是氯乙烯本体聚合工艺也有一些缺点:聚合釜溶剂较小,目前最大为 50 M3 ,而悬浮聚合釜溶剂为 230 M3 ,产能有限;聚合工艺技术没有悬浮法成熟,本体聚合方法正处于发展之中。
表3-5-1本体聚合和悬浮聚合本体法生产的聚氯乙烯产品主要用途:管材管件、建筑及装饰材料、包装材料及薄膜、电子电器及电线电缆、交通运输材料、医用器材及制品等。
3.5.2 聚合体系各组分及其作用一、单体氯乙烯氯乙烯的沸点为-14℃,加压或冷却可液化,工业上贮运为液态;氯乙烯作为vc本体聚合的主要原料,对其纯度的要求相当高,一般大于99.9%,微量的杂质的存在对聚合过程和产品树脂的颗粒特性有着显著的影响。
氯乙烯有较强的致肝癌毒性,树脂中残留单体应5ppm 以下。
存放氯乙烯液体的贮槽装料系数不得超过85%。
二、引发剂氯乙烯本体聚合所用的引发剂多为有机过氧化物,一般为过氧化二碳酸二(2-乙基己酯)(PDEH或EHP)、过氧化乙酰基环己烷磺酰(ACSP)、过氧化十二酰(LPO)和丁基过氧化酸酯(TBPND)等,也可用将两种以上引发剂复合使用。
三、添加剂为了提高产品性能、保证产品质量和生产安全,在聚合过程中需加入少量添加剂。
一般为有机或无机化学品。
①增稠剂一般是巴豆酸,乙酸乙基酯共聚物等,用来调节产品的黏度、孔隙度和疏松度,以便于提高初级粒子的粘度使之在凝聚过程中生成更为紧密的树脂颗粒。
自由基聚合生产工艺

分子量调节剂
新鲜乙烯
引发剂
25MPa
0.1MPa
25MPa
一次 压缩机
高压分离器
低压分离器
平均聚合度随温度升高而降低
严格控制引发剂用量
选择适当的分子量调节剂
严格控制反应温度 和其它反应条件
产品平均 分子量
合成聚酯的路线
某些物质同自由基作用,可能形成非自由基物质,或形成活性低、不足以再引发的自由基。根据对反应的抑制程度,可将这类物质粗略分为阻聚剂和缓聚剂。
使部分自由基终止,使聚合减慢。
有机玻璃生产工艺
单体
配料
制浆
模板 清洗
裁切 包装
脱模
聚合
封合
排气
灌浆
入库
制模
新模板
第三步聚合: 把封合的模框吊入热水箱(或烘房),根据板厚分别控制温度在25~52℃,经过10~160小时,到取样检查料源硬化为止,用接蒸汽加热水箱内水至沸腾,保持二小时,通水慢慢冷却到40℃,吊出模具,取出中间有机玻璃板材,去边,裁切后包装。
发泡剂
(a) 过氧化氢-亚铁盐氧化-还原体系
Fe+2 + H2O2 Fe+3 + OH- + ·OH
H2O2 H+ + HO2-
Fe+3 + HO2 - Fe+2 + H-O-O·
聚合方法的选择
原始颗粒粒径只有1微米左右,适于生产聚乙烯糊。
例如:聚氯乙烯树脂的生产工艺
Hale Waihona Puke 溶液聚合方法乳液聚合方法悬浮聚合方法
本体聚合方法
2.自由基聚合机理
烯类单体的加聚基本属于连锁聚合。在适当条件下价键有均裂和异裂两种方式。
本体聚合生产工艺

3.2 本体聚合生产工艺
(1) 本体聚合(又称块状聚合):在不用其它反应介质情况下, 单体中加有少量或不加引发剂发生聚合的方法。
(2) 均相本体聚合指生成的聚合物溶于单体(如苯乙烯、甲基 丙烯酸甲酯)。非均相本体聚合指生成的聚合物不溶解在单 体中,沉淀出来成为新的一相(如氯乙烯)。
(3) 根据单体的相态还可分为气相、液相和固相本体聚合。采 用本体聚合生产聚合物:高压聚乙烯、聚苯乙烯、聚甲基丙 烯酸甲酯,以及一部分聚氯乙烯。
第三章 自由基聚合生产工艺
3.1 自由基聚合工艺基础
四种聚合方法的工艺特点
聚合方式的选择:产品用途所要求的产 品形态和产品成本。
.
27.05.2020
合成树脂:四种方式。 合成橡胶:一般用乳液聚合的方法。
1
第三章 自由基聚合生产工艺
本体聚合生产的合成树脂的主要品种
.
27.05.2020
2
第三章 自由基聚合生产工艺
凝胶效应是有机玻璃分子量分布宽、分子量甚至超过 100万的主要原因,也是聚合过程中必须严格控制升温速 度的理论根据。
.
27.05.2020
13
3.2 本体聚合生产工艺
● 聚合工艺
预聚合(制浆):釜式反应器间歇操作,引发剂用量与板 材厚薄有关(0.02-0.1%),80℃反应,需移去反应热。
加入硬脂酸便于脱模,加入少量增塑剂,如邻苯二甲 酸二丁酯或二辛酯,可增加有机玻璃的柔性。
● 工艺特点 1)甲基丙烯酸甲酯在聚合过程中体积收缩率在25℃时
为21%,因此模具设计中应当充分考虑此问题: 生产板材时,作为模板的硅酸盐玻璃板之间的间隙应
当可以随聚合反应的进行而收缩;生产棒材时,应当设法 使单体不断补充于收缩造成的间隙之中。
本体聚合生产工艺

3、引起剂旳影响
引起剂旳用量将影响聚合反应速率和分子量。引起剂用 量增长,聚合反应速率加紧,分子量降低。 引起剂用量一般为聚合物质量旳万分之一 左右。
4.链转移剂旳影响
丙烷是很好旳调整剂,若反 应温度>150℃,它能平稳地 控制聚合物旳分子量。
氢旳链转移能力较强,反应 温度高于170℃,反应很不稳 定。
(2)管式法 管式法所使用旳引起剂是氧或过氧化物 反应器旳压力梯度和温
度分布大、反应时间短,所得聚乙烯旳支链少,分子量分布较 宽,合适制作薄膜用产品及共聚物。单程转化率较高,反应器 构造简朴,传热面大。 主要缺陷是聚合物粘管壁而造成堵塞现象。 近年来为提升转化率而采用多点进料。
4.乙烯高压聚合生产过程(图6.5)
乙烯旳转化率越高和聚乙烯旳停留时间越长、则长链支化越 多。聚合物旳分子量分布幅度越大,产品旳加工性能越差。
(5)以氧为引起剂时,存在着一种压力和氧浓度旳临界值关系 即在此界线下乙烯几乎不发生聚合,超出此界线,虽然氧含
量低于2ppm时.也会急剧反应。在此情况下,乙烯旳聚合速 率取决于乙烯中氧旳含量。
5 . 2.2 影响聚合反应旳主要原因
后聚合完毕、熔融状态聚合物自聚合塔底部用调整螺杆挤 出机送出,流成细条状,经冷却水槽冷却成固态,再经切粒 机切成一定大小旳颗粒
• 3.主要设备
• 聚苯乙烯生产旳主要设备是预聚合釜和聚合塔
• (1)预聚釜
• 预聚釜是带有球形盖及底旳铝质或不锈钠旳圆筒彤设 备,外壁有钢质夹套,并装有28—32r/mm旳不锈钢 旳锚式或框式搅拌器,预聚釜容积视生产能力而定, 我国早期聚苯乙烯生产装置旳预聚釜旳容积为2m3.
2.苯乙烯聚合工艺过程
苯乙烯分段聚合旳工艺流程有三种, 即塔式反应流程、少许溶剂存在下旳生产流程和压力釜串联 流程,见图6.8。 以塔式反应流程历史最久,技术成熟,但生产能力有限。
105聚合釜操作规程及题库

105聚合釜操作规程及题库Q/YH湖北宜化集团有限责任公司企业标准Q/YH·JS22072-2022岗位操作规程2022-9-1发布2022-9-1实施第一章聚合岗位任务1.聚合岗位任务将氯乙烯工段送来的精氯乙烯在一定的温度、压力下,加入适量的助剂,经过聚合反应生成聚氯乙烯。
未反应完的氯乙烯经回收处理后循环使用。
聚氯乙烯浆料在一定的温度和压力下,经过汽提塔汽提除去聚氯乙烯颗料中残留的氯乙烯后送往离心干燥岗位,同时将氯乙烯回收。
2.岗位职责2.1聚合中控主操小组长·按操作要求组织好本岗位生产;·发生异常情况及时向班长及值长汇报;·认真监督落实工段各项生产指令;·对违章操作给予批评或停止其操作。
2.2聚合中控操作员·协助小组长搞好本岗位生产;·对操作过程中发现的问题及时向小组长汇报;·熟悉各项操作规程,熟练掌握操作技巧。
2.3聚合现场巡检·对区域内的所有设备进行巡回检查;·发现异常情况及时向班长及值长汇报;·积极配合维修人员进行检修;·检修施工过程中做好监护工作,对违章作业进行制止;·做好日常记录工作。
3.巡检概念化3.1聚合现场巡检概念聚合巡检:助剂楼聚合楼汽提塔单体槽热水槽和冷水槽3.3巡检内容巡检频率:每小时1次巡检内容:·现场各机泵的温度、振动、油位、油质、电流、压力、冷却水;·现场所有储槽的液位、槽体泄漏情况;·现场所有设备、阀门、管路的泄漏情况;·备机备泵的盘车维护。
重点关注内容:·中控岗位:加料情况,反应情况、泄料情况、回收情况和根据安全生产情况进行现场排污。
·巡检岗位:监控3台聚合釜(包括搅拌和减速机的运转情况)、2台浆料槽、2台单体槽、1台汽提塔、1台冷水槽、1台热水槽、2项排污、1个液位。
4.工艺概述聚氯乙烯是一种无毒、无臭的白色粉末。
聚合生产工艺过程
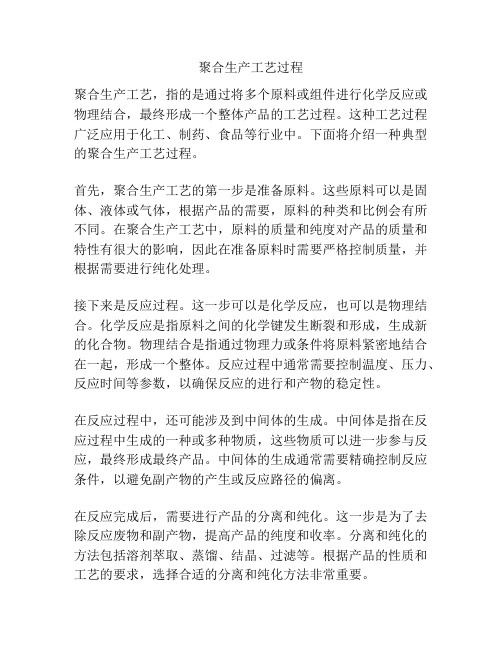
聚合生产工艺过程聚合生产工艺,指的是通过将多个原料或组件进行化学反应或物理结合,最终形成一个整体产品的工艺过程。
这种工艺过程广泛应用于化工、制药、食品等行业中。
下面将介绍一种典型的聚合生产工艺过程。
首先,聚合生产工艺的第一步是准备原料。
这些原料可以是固体、液体或气体,根据产品的需要,原料的种类和比例会有所不同。
在聚合生产工艺中,原料的质量和纯度对产品的质量和特性有很大的影响,因此在准备原料时需要严格控制质量,并根据需要进行纯化处理。
接下来是反应过程。
这一步可以是化学反应,也可以是物理结合。
化学反应是指原料之间的化学键发生断裂和形成,生成新的化合物。
物理结合是指通过物理力或条件将原料紧密地结合在一起,形成一个整体。
反应过程中通常需要控制温度、压力、反应时间等参数,以确保反应的进行和产物的稳定性。
在反应过程中,还可能涉及到中间体的生成。
中间体是指在反应过程中生成的一种或多种物质,这些物质可以进一步参与反应,最终形成最终产品。
中间体的生成通常需要精确控制反应条件,以避免副产物的产生或反应路径的偏离。
在反应完成后,需要进行产品的分离和纯化。
这一步是为了去除反应废物和副产物,提高产品的纯度和收率。
分离和纯化的方法包括溶剂萃取、蒸馏、结晶、过滤等。
根据产品的性质和工艺的要求,选择合适的分离和纯化方法非常重要。
最后,是产品的成型和包装。
根据产品的形状和用途,可以选择不同的成型方法,如注塑、挤出、压制等。
成型后的产品需要进行包装,以保护产品的质量和延长其寿命。
包装方法和材料的选择应符合产品的特性和法规要求。
聚合生产工艺过程中还要注意工艺的可持续性和环境友好性。
在整个过程中,需要尽量减少废物和有害物质的产生,同时提高能源利用率和资源利用效率。
这对于保护环境和节约资源都是非常重要的。
综上所述,聚合生产工艺过程是一个包括准备原料、反应、分离纯化、成型和包装等多个步骤的复杂过程。
在每个步骤中,都需要精确控制工艺条件,并考虑产品的特性和要求,以确保产品的质量和性能。
自由基本体聚合原理及生产工艺

环保与可持续发展
绿色生产
自由基本体聚合过程中应尽量采 用环保的原材料和助剂,减少生 产过程中的废弃物排放,实现绿 色生产。
资源循环利用
聚合物的再生利用和循环利用是 实现可持续发展的重要手段。通 过合理的再生利用和循环利用, 可以减少对自然资源的消耗,降 低环境污染。
节能减排
通过采用先进的生产技术和设备, 可以提高生产效率,降低能耗和 减少污染物排放,实现节能减排。
新技术的开发
1 2 3
新型催化剂
随着对聚合反应机理的深入了解,新型催化剂不 断被开发出来,可以更有效地控制聚合反应过程, 提高聚合物的性能。
新型加工技术
新型加工技术的应用,可以更有效地实现聚合物 的加工成型,提高加工效率,降低能耗和减少环 境污染。
新型检测技术
新型检测技术的应用,可以更准确地检测聚合物 的性能和质量,为聚合物的生产和应用提供更好 的保障。
在自由基本体聚合中,单体分子在聚合过程中不与任何其他物质 接触,因此也被称为“本体聚合”。
自由基本体聚合的特点
自由基本体聚合具有简单、方便、高效等优点,适 用于大规模生产。
由于没有溶剂或稀释剂的存在,因此聚合产物具有 较高的纯度和较少的杂质。
聚合反应可以在较低的温度下进行,有利于节能和 环保。
自由基本体聚合的分类
02
01
03
根据引发方式的不同,自由基本体聚合可以分为热引 发聚合和引发剂引发聚合两类。
热引发聚合是指通过加热的方式引发聚合反应,通常 需要在较高的温度下进行。
引发剂引发聚合是指通过加入引发剂来引发聚合反应 ,通常在较低的温度下进行,且聚合速率较快。
02
自由基本体聚合生产工艺
生产工艺流程
高分子化学第05章 聚合方法

聚氯乙烯不溶于氯乙烯单体,因此本体聚合过程中发生 聚合物的沉淀。本体聚合分为预聚合和聚合两段:
9
预聚合:小部分单体和少量高活性引发剂(过氧化乙酰 基磺酰)加入釜内,在50℃ ~70℃下预聚至7%~11%转化率, 形成疏松的颗粒骨架。
2
5.2 本体聚合
本体聚合(Bulk Polymerization):是单体本身在不加溶 剂以及其它分散剂的条件下,由引发剂或直接由光热等作 用下引发的聚合反应。 优点:无杂质,产品纯度高,聚合设备简单。 缺点:体系粘度大,聚合热不易扩散,反应难以控制,易 局部过热,造成产品发黄。自动加速作用大,严重时可导 致暴聚。
39
乳化剂的作用主要有三点: 降低表面张力,使单体分散成细小的液滴 在液滴表面形成保护层,使乳液稳定 增溶作用:形成胶束,使单体增溶 乳化剂能形成胶束的最低浓度叫临界胶束浓度(简称CMC), CMC越小,越易形成胶束,乳化能力越强。
40
亲水亲油平衡值(HLB):衡量表面活性剂中亲水和亲油部分 对水溶性的贡献。其值越大亲水性越大。
32
乳液聚合的缺点 ①需要固体产品时,乳液需经凝聚、洗涤、脱水、干燥等工 序,成本较高 ②产品中留有乳化剂等杂质,难以完全除净,有损电性能等
33
乳液聚合应用
①聚合后分离成胶状或粉状固体产品
丁苯、丁腈、氯丁等合成橡胶;ABS、MBS等工程塑料和抗冲 改性剂;糊用聚氯乙烯树脂、聚四氟乙烯等特种塑料。
12
缺点: 单体浓度较低,聚合速率慢,设备生产能力较低; 单体浓度低和向溶剂链转移使聚合物的分子量降低; 使用有机溶剂时增加成本、污染环境; 溶剂分离回收费用高,除尽聚合物中残留溶剂困难。
本体聚合
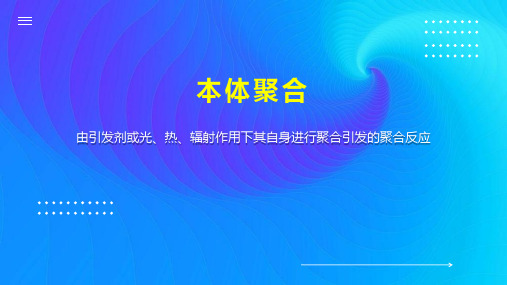
工业化品种
LDPE气相本体用途:薄膜制品、电缆、被覆料。 PVC沉淀本体用途:管材、板材。 GPS熔融本体(热引发)用途:家用电器里外装饰、电器、支架、仪表。 PMMA本体浇铸用途:航空透明材料、表盘、标牌。
工艺
⑴非均相本体聚合——聚氯乙稀本体聚合生产 氯乙烯本体聚合一般分为二个阶段: 第一阶段预聚合; 第二阶段:后聚合。 操作方式:间歇操作。 氯乙烯本体聚合的主要设备 聚合釜配置:1台预聚合+5台后聚合。 预聚釜——立式不锈钢聚合釜,内装涡轮式平桨搅拌器,搅拌转速控制在50~250rpm之间。 搅拌器的形式和大小,搅拌转速的大小将直接关系到预聚合种子颗粒的形态和大小。 后聚釜——卧式釜(50m3 ),内装有慢速搅拌的三条螺带组合的搅拌器。螺带与釜壁间隙极小。卧式釜转 速为6~7rpm。
④在反应进行到一定转化率而此时反应黏度还不算太高时,就分离出聚合物;
⑤分段聚合,将聚合过程分为几个阶段,控制转化率,自动加速效应,使反应热分成几个阶段放出;
⑥改进反应器内的流体输送方法,完善搅拌器和传热系统,以利于聚合设备的传热,研究开发专用特型设备 等;
⑦采用气相本体聚合方法,研制出专用高效催化剂,大大减低了操作压力,并且解决了相关的工程设备问题, 使得这一技术得到广泛使用;
改ቤተ መጻሕፍቲ ባይዱ方法
①为了改进产品性能或成型加工的需要而加入有特定功能的添加剂,像增塑剂,抗氧剂,内润滑剂,紫外线 吸收剂及颜料等;
②为了调节反应速率,适当降低反映温度而加入一定量的专用引发剂;为了降低体系黏度改善流动性,加入 少量内润滑剂或溶剂;
本体聚合生产工艺培训

本体聚合生产工艺培训1. 简介本文档旨在介绍本体聚合生产工艺培训的基本概念、原理和操作流程。
本体聚合生产工艺是一种重要的生产技术,在制造业和工程领域具有广泛应用。
通过本文档的学习,读者将了解本体聚合的定义、应用场景、工艺流程以及相关安全注意事项。
2. 本体聚合的定义和应用场景2.1 定义本体聚合是一种将多个独立的本体元素结合成一个整体的过程。
本体元素可以是物理产品、工艺材料或者其他组件。
通过本体聚合,可以提高产品的强度、刚度和耐久性,同时降低零部件的数量和生产成本。
2.2 应用场景本体聚合工艺广泛应用于以下领域:•汽车制造业:用于汽车车身的生产,提高车身强度和刚度。
•航空航天工程:用于航空器和航天器的结构件制造,提高飞行器的性能和耐久性。
•机械制造业:用于生产机械设备的零部件,提高设备的可靠性和耐用性。
3. 本体聚合的工艺流程本体聚合主要包括以下几个关键步骤:3.1 准备工作在进行本体聚合之前,需要进行准备工作,包括准备本体元素、准备工艺材料和设备,确保工作环境的清洁和安全。
3.2 涂层处理涂层处理是本体聚合的第一步,用于增加本体元素之间的粘附力。
常用的涂层材料包括粘接剂、胶水和融合剂。
涂层处理需要根据本体元素的材质和特性选择合适的涂层材料。
3.3 本体组装本体组装是将涂层处理后的本体元素进行组装,并使用适当的工具和设备进行压缩、固化或热处理。
本体组装需要根据本体元素的形状和尺寸选择合适的组装方法和设备。
3.4 后期处理完成本体聚合后,需要进行后期处理,包括清洁、修整和检验。
后期处理的目的是检查本体聚合的质量和性能,并确保产品达到预期要求。
4. 安全注意事项在进行本体聚合生产工艺培训时,需要注意以下安全事项:•操作人员应接受专业培训,了解本体聚合工艺的基本知识和操作规程。
•使用涂层材料和工艺设备时,应按照安全操作规程进行操作,避免意外事故的发生。
•在进行本体组装和后期处理时,应戴好个人防护设备,包括手套、护目镜和口罩,确保个人安全。
齐齐哈尔大学高聚物合成工艺学题库附答案

习题集(348)第一章绪论(37)一、判断(10)1、由于塑料包装物大多呈白色,它们造成的环境污染被称为白色污染。
(+ )2、连续聚合特点是聚合反应条件是稳定的,容易实现操作过程的全部自动化,机械化,便于小批量生产。
(_ )3、进行聚合反应的设备叫做聚合反应器。
根据聚合反应器的形状主要分为管式、塔式和釜式聚合反应器。
(+ )4、本体聚合与熔融缩聚得到的高粘度熔体不含有反应介质,如果单体几乎全部转化为聚合物,通常不需要经过分离过程。
如果要求生产高纯度聚合物,应当采用真空脱除单体法。
(+)5、乳液聚合得到的浓乳液或溶液聚合得到的聚合物溶液如果直接用作涂料、粘合剂,也需要经过分离过程。
(_ )6、合成橡胶是用物理合成方法生产的高弹性体。
经硫化加工可制成各种橡胶制品。
(_ )7、合成纤维通常由线型高分子量合成树脂经熔融纺丝或溶液纺丝制成。
加有少量增光剂、防静电剂以及油剂等。
(+ )8、合成树脂生产中回收的溶剂。
通常是经离心机过滤与聚合物分馏得到的。
(+ )9、高分子合成工厂中最易发生的安全事故是引发剂、催化剂、易燃单体、有机溶剂引起的燃烧与爆炸事故。
(+ )10、塑料具有取材容易,价格低廉,加工方便,质地轻巧等优点。
(+ )二、填空(10)1、根据产量和使用情况合成橡胶可分为通用合成橡胶与特种合成橡胶两大类。
2、离子聚合及配位聚合实施方法主要有本体聚合与溶液聚合两种方法。
3、在溶液聚合方法中,如果所得聚合物在反应温度下不溶于反应介质中而称为非均相溶液聚合。
4、塑料的原料是合成树脂和助剂。
5、塑料成型重要的有:注塑成型、挤塑成型、吹塑成型、模压成型等。
6、高分子合成工业的产品形态可能是液态低聚物、坚韧的固态高聚物或弹性体。
7、高分子合成工业的基本原料为石油、天然气、煤炭等。
8、为使釜式聚合反应器中的传质、传热过程正常进行,聚合釜中必须安装搅拌器。
9、自由基悬浮聚合得到固体珠状树脂在水中的分散体系。
可能含有少量反应单体和分散剂。
05_本体聚合生产工艺
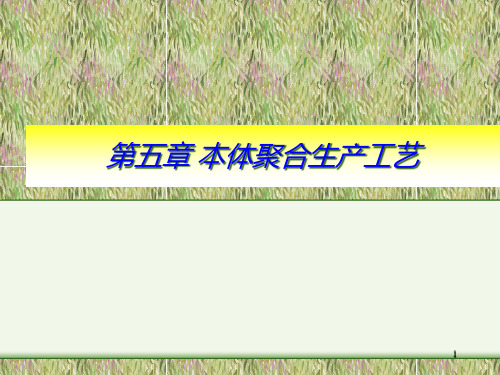
a. 釜式法
• 大都采用有机过氧化物为引发剂,反应压力较管式法 低,聚合物停留时间稍长,部分反应热是借连续搅拌 和夹套冷却带走。大部分反应热是靠连续通入冷乙烯 和连续排出热物料的方法加以调节,使反应温度较为 恒定。此法的单程转化率可达24.5%,生产流程简短, 工艺较易控制。
• 主要缺点:是反应器结构较复杂,搅拌器的设计与安 装均较困难,而且容易发生机械损坏,聚合物易粘釜。
ﻆ非均相聚合过程所生成的产物则不同,聚合物
粒子是不透明的,外表比较粗糙,内部有一些孔隙。
10
➢ 4、聚合工艺中采用的解决方法:
1 加入一定量的专用引发剂调节反应速率; 2 采用较低的反应温度,使放热缓和; 3 反应进行到一定转化率,粘度不高时就分离聚合物。
11
4 分段聚合,控制转化率和“自动加速效应” ; 改进和完善搅拌器和传热系统以利于聚合设
41
b. 管式法
• 管式法所使用的引发剂是氧或过氧化物 反应器的 压力梯度和温度分布大、反应时间短,所得聚乙烯 的支链少,分子量分布较宽,适宜制作薄膜用产品 及共聚物。单程转化率较高,反应器结构简单,传 热面大。
• 主要缺点:聚合物粘管壁而导致堵塞现象。
• 近年来为提高转化率而采用多点进料。
42
43
45
b. 釜式反应器
➢ 是装有搅拌器的圆筒形高压容器。 ➢ 材质由含3.5%镍/铬/钒/钼的合金钢锻件加工而成。 ➢ 釜式法单程转化率达24.5%,单线生产能力到90000t/a。 ➢ 高压釜结构较复杂,尤其是搅拌器的设计与安装均较困难, 在生产中搅拌器会发生机械损坏,聚合物易于沉积在浆上, 因而造成动平衡破坏,甚至有时会出现金属碎屑堵塞釜后的 减压阀现象,使釜内温度急剧上升,导致爆炸的危险。
第四章 本体聚合工艺

间力被共价键所代替。收缩超过单体原有体积的 1/5。 根据PMMA本体聚合的特点,其聚合工艺分“预聚” 和“聚合”两段进行。
4.4.2 影响聚合反应的主要因素
反应温度 温度↑,反应速率↑ ,转化率↑, 但温度过高,会 导致链终止速率超过增长速率,同时引起长链解聚, 短链增多,分子量↓。
2. 转化率的控制 乙烯聚合时放热大,易导致急剧升温,为保证安 全生产,保证产品质量,聚合转化率不能超过30 %,大量的乙烯需循环使用。
4.3.5 低密度聚乙烯的结构、性能和应用
4.3.5.1 低密度聚乙烯的结构
▲ LDPE不完全是线型结构,而是有长、短支链,近似树枝状结构。 其结晶度64%,远低于HDPE的85%。
单体纯度 影响产品光学、力学性能。
4.4.3 有机玻璃的生产工艺
有机玻璃本体聚合的生产过程: 一般分为配料、预聚(聚合温度90~95℃,转化 率10~20%)、制模与灌浆、聚合等4个工段。
预聚:目的是缩短聚合周期,使自动加速效应提前,且预聚物有 一定黏度及体积收缩,有利于灌浆及聚合
P26 图3-1
50℃,使用受限制。 LDPE熔点为110~115℃,软化温度范围窄,低于软化温度15~
20℃,可进行延伸与造型,高于软化温度,可用挤出、注射等方 法加工。 化学稳定性好,室温几乎不溶于任何溶剂。耐弱酸碱。
4.3.5.3. 低密度聚乙烯用途
聚乙烯的生产能力长期居各品种的第一 位,消费量占世界聚烯烃的70%,占热 塑性通用塑料消费量的44%。
利用乙烯高压聚合装置,适当增加醋酸乙烯酯加料系统及回收 系统即可兼产乙烯-醋酸乙烯酯共聚物(EVA)。
有机玻璃本体聚合生产工艺过程

有机玻璃本体聚合生产工艺过程有机玻璃,又称亚克力,是一种常见且广泛应用于各个领域的材料,其本体聚合生产工艺是一项复杂而精密的过程。
本文将介绍有机玻璃本体聚合生产的工艺过程,让读者对其制造过程有一个清晰的了解。
有机玻璃的本体聚合生产主要分为原料准备、溶液制备、成型和固化四个主要步骤。
首先是原料准备阶段,这是整个生产过程中至关重要的一步。
常见的原料包括甲基丙烯酸甲酯、甲基丙烯酸乙酯等,这些原料在精确的比例下被称为“组方”,其准确性直接影响着最终产品的质量。
接着是溶液制备阶段,根据预先确定的配方将原料加入反应釜中,在一定的温度和压力条件下进行搅拌和混合,直至原料完全溶解。
这一步骤的关键在于保持反应体系的稳定性和均匀性,确保不同成分充分混合,以便后续的成型过程。
成型阶段是有机玻璃本体聚合生产中最为关键的环节之一。
通常采用注塑或挤出成型工艺,通过高温高压下使溶液充分流动,进入模具内部,在特定的模具设计下形成所需的产品形状。
成型过程需要控制好温度、压力、速度等参数,确保产品表面的光滑度和尺寸的准确性。
最后是固化阶段,经过成型后的有机玻璃产品需要在恰当的条件下进行固化,使其机械性能和化学性能得到充分发挥。
通常采用热固化或紫外光固化等方式进行固化处理,使产品表面硬度增加,耐磨性提高,从而满足不同领域的应用要求。
总的来说,有机玻璃本体聚合生产工艺过程是一个综合技术要求高、流程复杂的制造过程。
通过精准的原料配方、有效的溶液制备、精密的成型和合适的固化处理,才能生产出质量稳定、性能优良的有机玻璃制品。
这些制造工艺的不断优化和改进,将进一步推动有机玻璃材料在各个领域的应用和发展,为人们的生活和产业发展提供更多可能性。
1。
本体聚合生产工艺课件

24.06.2020
5
3.2 本体聚合生产工艺
缺点:
(1)放热反应,传热系数小,散 热困难,温度控制较难,造成聚合 物分子量分布宽。
采取的措施:合理设计反应器的形 状、大小,增大传热面积;单体中 加入聚合物;分段聚合(预聚合)
凝胶效应是有机玻璃分子量分布宽、分子量甚至超过 100万的主要原因,也是聚合过程中必须严格控制升温速 度的理论根据。
24.06.2020
13
3.2 本体聚合生产工艺
● 聚合工艺
预聚合(制浆):釜式反应器间歇操作,引发剂用量与板 材厚薄有关(0.02-0.1%),80℃反应,需移去反应热。
加入硬脂酸便于脱模,加入少量增塑剂,如邻苯二甲 酸二丁酯或二辛酯,可增加有机玻璃的柔性。
熔融指数仅表示了相应 的熔融粘度,相对的表示了 平均分子量,但不能表示聚 乙烯的分子量分布,而分子 量分布对于聚乙烯的性能也 发生显著的影响。因此,具 有同一种密度、同一种熔融 指数的聚乙烯,由于生产条 件不同,其性能和用途可能 有所不同。
24.06.2020
24
3.2 本体聚合生产工艺
乙烯高压聚合生产流程
20
3.2 本体聚合生产工艺
b:自由基的β-位键断裂
24.06.2020
21
3.2 本体聚合生产工艺
熔融指数 数均分子量 熔融指数 数均分子量 熔融指数 数均分子量
20.9
24000
1.8
32000
0.005
53000
6.4
28000
0.25
48000
0.001
76000
在相同的条件下,熔融粘度越大,被挤压出来的树脂 重量越少。因此聚乙烯的熔融指数↓,其分子量↑。
- 1、下载文档前请自行甄别文档内容的完整性,平台不提供额外的编辑、内容补充、找答案等附加服务。
- 2、"仅部分预览"的文档,不可在线预览部分如存在完整性等问题,可反馈申请退款(可完整预览的文档不适用该条件!)。
- 3、如文档侵犯您的权益,请联系客服反馈,我们会尽快为您处理(人工客服工作时间:9:00-18:30)。
工业上常用过氧化物引发剂为:过氧化二叔丁基,过 氧化十二烷酰,过氧化苯甲酰叔丁酯,过氧化3,5,5三甲基乙酰等。此外尚有过氧化碳酸二丁酯、过氧化 辛酰等。
添加方法:应配制成白油溶液或直接用计量泵注入聚 合釜的乙烯进料管中;或注入聚合釜中,在釜式聚合 反应器操作中依靠引发剂的注入量控制反应温度。
25
26
3、引发剂的影响
引发剂的用量将影响聚合反应速率和分子量。引发
剂用量增加,聚合反应速率加快,分子量降低。 引发剂用量通常为聚合物质量的万分之一左右。
27
4.链转移剂的影响
۩ 丙烷是较好的调节剂,若反应温度>150℃,它能平 稳地控制聚合物的分子量。 ۩ 氢的链转移能力较强,反应温度高于170℃,反应很 不稳定。
第五章 本体聚合生产工艺
1
Contents
5.1 概述 5.2 气相本体聚合——低密度聚乙烯 5.3 熔融本体聚合——聚苯乙烯
5.4 非均相本体聚合——本体法聚氯乙烯
5.5 本体浇铸聚合——有机玻璃
2
5.1 概述1ຫໍສະໝຸດ 本体聚合的定义 本体聚合(又称块状聚合):在不用其它反应介质 情况下,单体中加有少量或不加引发剂发生聚合的 方法。
• (1) 聚合热大 。 – 乙烯聚合热约为95.0kJ/ml 。 • (2) 反应器内压力高,温度高 。 – 110~250MPa ,有的甚至为300MPa,130 ℃ ~280℃。 • (3) 聚合转化率较低。 – 通常在20%一30%。链终止反应非常容易发生,因此 聚合物的平均分子量也小。
21
43
③
聚合反应设备
主体设备:反应器
釜式反应器(全混流,分子量分布窄)
管式反应器(平推流,分子量分布宽)
Φ=2.5~7.5cm
D/L=1/250~1/40000 材质:高压合金钢管
高压聚乙烯生产管式反应器
44
a. 管式反应器
细长的高压管。
物料在管内呈活塞式流动,反应温度沿管程有变化,因 而反应温度有最高峰,因此所合成聚乙烯分子量分布较宽。
乙烯 搅拌电动机 隔墙 冷却剂(出) 搅拌器 内冷管
乙烯,催化剂
冷却剂(进)
反应产物
47
48
4、单体回收与聚乙烯后处理
• 从聚合反应器中流出的物料近减压装置进入高压分离 器(20~25MPa),大部分未反应的乙烯与聚乙烯分离, 经冷却,脱除蜡状低聚物后回收循环使用; • 聚乙烯进入低压分离器,使残存的乙烯分离回收循环 使用。 • 挤出和后序处理:包括脱气、混合、包装、贮存等。 • 二次造粒:目的是增加聚乙烯塑料的透明性,并且减 少塑料中的凝胶微粒。与其他塑料品种不同。
۩ 丙烯起到调节分子量和降低聚合物密度的作用,且会 影响聚合物的端基结构。
۩ 丙醛作调节剂在聚乙烯链端部出现羰基。
28
29
5.乙烯纯度的影响
乙烯中杂质越多,则聚合物的分子量越低,且会 影响产品的性能。 有的杂质如乙炔还可能引起爆炸。
工业上,乙烯的纯度要求超过99.95%
30
31
三、 低密度聚乙烯的生产工艺
37
3、聚合过程
① 聚合反应条件
–
– – –
反应温度:130~350℃;
反应压力:122~303MPa; 聚合停留时间:15s~2min; 具体数值因反应器类型、产品牌号不同而不同。
38
39
② 聚合生产方法
高压聚乙烯生产工艺有釜式法和管式法两种。 生产能力相当,70年代后有偏重管式法倾向。
形状一定的模型
釜式聚合釜 a. 管式反应器
连续聚合反应器
b. 塔式反应器
13
层流状态 a. 管式反应器
脉冲以产生湍流
单程转化率10-20%
多管并联
高压聚乙烯生产管式反应器
b. 塔式反应器
苯 乙 烯 塔 式 反 应 器
14
6、后处理工序
气体单体 减压或真空
脱除单体
螺杆脱气机
真空脱气机 液态单体 减压挤出机 真空滚筒脱气器
早期的单程转化率较低,大约10%左右,生产能力为 3000t/a,近期单程转化率与釜式法相近,即为24%,单 线生产能力已达到60000—80000t/a。 管式反应器的结构颇为简单和传热面积相当大。整根细 长的高压管都布置有央套。
45
b. 釜式反应器
是装有搅拌器的圆筒形高压容器。
材质由含3.5%镍/铬/钒/钼的合金钢锻件加工而成。
40
a. 釜式法 • 大都采用有机过氧化物为引发剂,反应压力较管式法 低,聚合物停留时间稍长,部分反应热是借连续搅拌 和夹套冷却带走。大部分反应热是靠连续通入冷乙烯 和连续排出热物料的方法加以调节,使反应温度较为 恒定。此法的单程转化率可达24.5%,生产流程简短, 工艺较易控制。 • 主要缺点:是反应器结构较复杂,搅拌器的设计与安 装均较困难,而且容易发生机械损坏,聚合物易粘釜。
挤出 造粒机
新鲜乙烯
51
52
四、乙烯的共聚改性及高压聚乙烯的技术进展
1、乙烯的共聚改性
(I) 乙烯—乙酸乙烯酯共聚物 (2) 乙烯—丙烯酸乙酯共聚物 (3) 乙烯—(甲基)丙烯酸共聚物及其离子聚合物 (4) 乙烯—顺丁烯二酸酐共聚物 (5) 乙烯—乙酸乙烯酯— 一氧化碳共聚物 (6) 乙烯—一氧化碳共聚物
分子量分布变宽
‘凝胶效应’
含有未反应的单体和低聚物
7
苯乙烯聚合转化率与其溶液粘度的关系
8
(3) 任何一种单体转化为聚合物时都伴随有体积的收缩
几种主要单体转化率达100%时的体积收缩率 (25℃):
苯乙烯 甲基丙烯酸甲酯 乙酸乙烯酯 氯乙烯
14.14% 23.06% 26. 82% 35.80%
9
1、原料准备 ① 主要原料:单体乙烯。
– – – 乙烯的纯度要求超过99.95%。 乙烯高压聚合中单程转化率为15一30%,所以大 量的单体乙烯(70~85%)要循环使用。 多次循环使用时,惰性杂质(氮、甲烷、乙烷等) 的含量可能积累,此时应采取一部分气体放空或 送回乙烯精制车间精制。
32
② 分子量调节剂
指粒子的外观、尺寸大 小,粒子的内部结构。
(4) 聚合物粒子的形态和结构
ﻆ均相聚合过程得到的粒子是一些外表光滑、大
小均匀、内部为实心及透明有光泽的小圆珠球。
ﻆ非均相聚合过程所生成的产物则不同,聚合物
粒子是不透明的,外表比较粗糙,内部有一些孔隙。
10
4、聚合工艺中采用的解决方法:
1
15
7、典型的本体聚合生产工艺
16
本体聚合工业生产举例
17
液态单体需要预聚合,除反应热。
18
5.2 气相本体聚合——低密度聚乙烯
◙ 乙烯的聚合方法就以所采用的压力高低分为: 高压法、中压法、低压法; ◙ 所得聚合物相应地被称为: 高压聚乙烯、中压聚乙烯、低压聚乙烯。
19
• 气相本体聚合——高压聚乙烯生产
41
b. 管式法
• 管式法所使用的引发剂是氧或过氧化物 反应器的 压力梯度和温度分布大、反应时间短,所得聚乙烯 的支链少,分子量分布较宽,适宜制作薄膜用产品 及共聚物。单程转化率较高,反应器结构简单,传 热面大。 • • 主要缺点:聚合物粘管壁而导致堵塞现象。 近年来为提高转化率而采用多点进料。
42
•(4) 乙烯高温高压聚合,链转移反应容易发生 。 • 乙烯的转化率越高和聚乙烯的停留时间越长、则长链 支化越多。聚合物的分子量分布幅度越大,产品的加 工性能越差。
•(5) 以氧为引发剂时,存在着一个压力和氧浓度的临界值 关系。 • 即在此界限下乙烯几乎不发生聚合,超过此界限,即 使氧含量低于2ppm时,也会急剧反应。在此情况下, 乙烯的聚合速率取决于乙烯中氧的含量。
3
2、本体聚合分类
• 根据单体和聚合体的互溶情况分为:
均相 非均相 气相
• 按参加反应的单体的相态分为:
液相
均相本体聚合指生成的聚合物溶于单体(如苯乙烯、 甲基丙烯酸甲酯)。 非均相本体聚合指生成的聚合物不溶解在单体中,沉 淀出来成为新的一相(如氯乙烯)。
4
3、本体聚合的特点
主要优点:
(1) 本体聚合是四种方法中最简单的方法,无反应介质, 产物纯净,适合制造透明性好的板材和型材。 (2) 后处理过程简单,可以省去复杂的分离回收等操作 过程,生产工艺简单,流程短,所以生产设备也少, 是一种经济的聚合方法。 (3) 反应器有效反应容积大,生产能力大,易于连续化, 生产成本比较低。
22
二、影响聚合反应的主要因素
1.压力的影响
提高反应系统压力,促使分子间碰撞,加速聚合 反应,提高聚合物的产率和分子量,同时使聚乙烯分 子链中的支链度及乙烯基含量降低。
23
24
2.温度的影响
一般采用引发剂半衰期为1min时的温度。 在一定温度范围内,聚合反应速率和聚合物产率随 温度的升高而升高,当超过一定值后,聚合物产率、分 子量及密度则降低。同时大分子链末端的乙烯基含量也 有所增加,降低产品的抗老化能力。
③ 添加剂
– – 抗氧剂(防老剂):4-甲基-2,6-二叔丁基苯酚。 防止成型过程中受热氧化或使用过程中老化。 润滑剂:可用油酸酰胺或硬脂酸铵、油酸铵、亚 麻仁油酸铵三者的混合物。防止成型过程中粘结 模具。 开口剂:高分散性的硅胶(SiO2)、铝胶(Al2O3) 或其混合物为开口剂。为使吹塑薄膜袋易于开口。 抗静电剂:环氧乙烷与长链脂肪族或脂肪醇的聚 合物。
5
本体聚合的缺点:
(1) 放热量大,反应热排除困难,不易保持一定的反应温度。
分子量分布变宽
‘自动加速效应’
局部过热,使低分子气 化,产品有气泡、变色
温度失控、引起爆聚