-液相烧结
材料的烧结----液相烧结

书山有路勤为径,学海无涯苦作舟
材料的烧结----液相烧结
液相烧结:凡是有液相参与的烧结过程称为液相烧结。
液相烧结的主要传质方式有:流动传质、溶解-沉淀传质等。
1、液相烧结的特点
液相烧结与固态烧结的共同之点是烧结的推动力都是表面能;烧结过程也是由颗粒重排、气孔填充和晶粒生长等阶段组成。
不同点是:由于流动传质速率比扩散快,因而液相烧结的致密化速率高,可使坯体在比固态烧结温度低得多的情况下获得致密的烧结体。
此外,液相烧结过程的速率与液相的数量、液相性质(粘度、表面张力等)、液相与固相的润湿情况、固相在液相中的溶解度等有密切的关系。
2、流动传质
粘性流动:在高温下依靠粘性液体流动而致密化是大多数硅酸盐材料烧结的主要传质过程。
在液相烧结时,由于高温下粘性液体(熔融体)出现牛顿型流动而产生的传质称为粘性流动传质(或粘性蠕变传质)。
粘性流动初期的传质动力学公式:
式中r 为颗粒半径;x 为颈部半径;η为液体粘度;γ为液-气表面张力,t 为烧结时间。
适合粘性流动传质全过程的烧结速率公式:
式中θ为相对密度。
塑性流动:当坯体中液相含量很少时,高温下流动传质不能看成是纯牛顿型流动,而是属于塑性流动类型。
也即只有作用力超过其屈服值(f)时,流动速率才与作用的剪切应力成正比。
此时传质动力学公式改变为:
式中η是作用力超过f 时液体的粘度;r 为颗粒原始半径。
3、溶解- 沉淀传质。
陶瓷工艺学第十四讲 烧结2

2 塑性流动
塑性流动:当坯体中液相含量很少时,高温下流动 传质不能看成是纯牛顿型流动,而是同于塑性流动 型。
max 1 exp(
2
fr
)
为了尽可能达到致密烧结,应选择最小的颗粒原始半 径r,液体粘度η和较大的液-气表面张力γ。
问题二:液相为什么加强了致密化过程?
➢增强颗粒重排:摩擦力便小 ➢增强物质输运:对于固相烧结,Dgb和晶界宽度 决定了物质输运的速率,而对于液相烧结,溶解 度DL和液相桥的宽度决定了物质输运的速率。
问题三:液相的来源 ➢添加剂 ➢添加剂与固相颗粒形成低共熔相(相图)
问题四:液相量
➢一般为5Vol%,较少可以达到10Vol%,一般不 可以充填满颗粒之间的空隙。而传统陶瓷可以达 到25~35%,基本上可以填满空隙,这个烧结就 类似于玻璃粉的烧结,直接玻璃化就可以了 (Vitrifiaction)。
在固态烧结中也存在塑性流动。在烧结早期,表面 张力较大,塑性流动可以靠位错的运动来实现;而 烧结后期,在低应力作用下靠空位自扩散而形成粘 性蠕变,高温下发生的蠕变是以位错的滑移或攀移 来完成的、塑性流动机理目前应用在热压烧结的动 力学过程是很成功的。
三、溶解-沉淀传质机理
1、溶解-沉淀传质概念
在有固液两相的烧结中,当固相在液相中有可溶性,这时烧 结传质过程就由部分固相溶解而在另一部分固相上沉积.直 至晶粒长大和获得致密的烧结体。
➢缺点:液相最后会在晶界上形成新相,劣化材料 性能,如高温力学性能;尺寸控制较难;开裂和 塌陷。
液态烧结特点
➢传质机理和液相量有关; ➢传质过程和液相的性质有关; ➢与固-液润湿性有关; ➢与固相在液相的溶解度有关。
《低温液相烧结法制备高性能p型(Bi,Sb)2Te3热电材料》

《低温液相烧结法制备高性能p型(Bi,Sb)2Te3热电材料》篇一一、引言热电材料作为新兴功能材料,其在热能与电能之间相互转换的独特性质,使其在能源领域具有广泛的应用前景。
其中,p型(Bi,Sb)2Te3热电材料因其优异的热电性能和相对较低的制造成本,受到了研究者的广泛关注。
本文将重点介绍一种低温液相烧结法制备高性能p型(Bi,Sb)2Te3热电材料的工艺流程和关键技术。
二、实验原理低温液相烧结法是利用液相反应与烧结相结合的方法,通过在较低的温度下实现材料的烧结与致密化。
在制备p型(Bi,Sb)2Te3热电材料的过程中,通过调整Bi、Sb的掺杂比例和烧结过程中的温度、压力等参数,实现对材料性能的优化。
三、实验过程1. 材料选择与准备:选用高纯度的Bi、Sb、Te原料,按照一定的比例混合后进行研磨,以获得均匀的混合粉末。
2. 低温液相烧结:将混合粉末置于低温环境中,通过液相反应使原料充分反应并形成(Bi,Sb)2Te3化合物。
随后进行烧结,使材料致密化。
3. 性能优化:通过调整Bi、Sb的掺杂比例和烧结过程中的温度、压力等参数,优化材料的性能。
四、实验结果与分析1. 实验结果:采用低温液相烧结法制备的p型(Bi,Sb)2Te3热电材料具有较高的电导率和赛贝克系数,以及较低的热导率。
此外,材料还具有较好的稳定性和重复性。
2. 结果分析:通过对实验结果的分析,发现Bi、Sb的掺杂比例对材料的性能具有显著影响。
适量的Bi、Sb掺杂可以提高材料的电导率和赛贝克系数,降低热导率。
此外,烧结过程中的温度、压力等参数也对材料的性能产生一定影响。
五、结论本文采用低温液相烧结法制备了高性能p型(Bi,Sb)2Te3热电材料,通过对实验过程和结果的分析,得出以下结论:1. 低温液相烧结法可以实现p型(Bi,Sb)2Te3热电材料的低温制备和致密化,有效提高材料的性能。
2. Bi、Sb的掺杂比例对材料的性能具有显著影响,适量的掺杂可以提高材料的电导率和赛贝克系数,降低热导率。
液相烧结的特点

液相烧结的特点液相烧结是一种常见的陶瓷制备技术,通过添加适量的助熔剂将粉末与液相混合,然后在高温下进行加热处理,使其形成致密的块体。
液相烧结技术具有许多优点,如高度可控性、高效率、低成本等。
下面将详细介绍液相烧结的特点。
一、加速晶粒生长液相烧结过程中,添加的助熔剂能够溶解在晶界和颗粒表面处形成薄层,并且通过扩散和再结晶作用促进了晶粒生长。
此外,在液相存在的情况下,由于分子间距离缩小,晶体之间互相作用增强,从而使得颗粒更容易聚集并形成致密块体。
二、提高材料致密度液相烧结过程中,添加的助熔剂会在高温下部分蒸发或分解,从而产生气体压力并推动颗粒向更紧密排列。
此外,在高温下还会发生表面扩散和固态扩散等现象,使得颗粒之间的接触面积增大,从而进一步提高了材料的致密度。
三、改善材料性能液相烧结过程中,助熔剂的添加可以调节材料的组成和微结构,并且可以控制晶界和颗粒表面处的化学反应。
这些化学反应可以改变晶体中缺陷和杂质的分布状态,从而提高材料的力学性能、导电性能、磁性能等。
四、适用于多种陶瓷制备液相烧结技术适用于各种类型的陶瓷制备,包括氧化物陶瓷、非氧化物陶瓷、复合陶瓷等。
此外,液相烧结还可以与其他制备技术相结合使用,如溶胶-凝胶法、固态反应法等。
五、存在一定缺点虽然液相烧结技术具有许多优点,但也存在一定缺点。
首先,在高温下进行加工需要耗费大量能量,并且加工过程需要消耗大量助熔剂。
其次,在液相存在的情况下,晶体生长速度较快,容易形成颗粒不均匀的情况,从而影响材料的性能。
此外,液相烧结还存在一定的工艺难度,需要进行精确的温度控制和化学反应控制。
六、总结综上所述,液相烧结技术具有许多优点和一定的缺点。
在实际应用中需要根据具体情况选择合适的制备技术,并且进行必要的工艺优化和调整,以达到最佳的制备效果。
液相烧结

液相烧结粉末压坯仅通过固相烧结难以获得很高的密度,如果在烧结温度下,低熔组元熔化或形成低熔共晶物,那么由液相引起的物质迁移比固相扩散快,而且最终液相将填满烧结体内的孔隙,因此可获得密度高、性能好的烧结产品。
液相烧结的应用极为广泛,如制造各种烧结合金零件、电触头材料、硬质合金及金属陶瓷材料等。
液相烧结可得到具有多相组织的合金或复合材料,即由烧结过程中一直保持固相的难熔组分的颗粒和提供液相(一般体积占13%一35%)的粘结相所构成。
固相在液相中不溶解或溶解度很小时,称为互不溶系液相烧结,如假合金、氧化物—金属陶瓷材料。
另一类是固相在液相有一定溶解度,如Cu —Pb 、W —Cu —Ni 、WC —Co 、TiC —Ni 等,但烧结过程仍自始至终有液相存在。
特殊情况下,通过液相烧结也可获得单相合金,这时,液相量有限,又大量溶解于固相形成固溶体或化合物,因而烧结保温的后期液相消失,如Fe —Cu(Cu <8%)、Fe —Ni —A1、Ag —Ni 、Cu —Sn 等合金,称瞬时液相烧结。
一、液相烧结肋条件液相烧结能否顺利完成(致密化进行彻底),取决于同液相性质有关的三个基本条件。
1.润湿性液相对固相颗粒的表面润湿性好是液相烧结的重要条件之一,对致密化、合金组织与性能的影响极大。
润湿性由固相、液相的表面张力(比表面能)S γ、L γ以及两相的界面张力(界面能) SL γ所决定。
如图5—47所示:当液相润湿固相时,在接触点A 用杨氏方程表示平衡的热力学条件为cos S SL L γγγθ=+式中θ——湿润角或接触角。
完全润湿时,0θ=,cos S SL L γγγθ=+式变为S SL L γγγ=+;完全不润湿时,θ>90,则SL L S γγγ≥+。
图5—47表示介于前两者之间部分润湿的状态,0<θ<90。
液相烧结需满足的润湿条件就是润湿角θ<90;如果θ>90,烧结开始时液相即使生成,也会很快跑出烧结体外,称为渗出。
9-3液态烧结

2.塑性流动
当坯体中液相含量很少,高温下流动传质不能 看成是纯牛顿型流动,而是属于塑性流动型,只有 作用力超过屈服值(f)时,流动速度才与作用的剪 应力成正比,此时式(9.35)改为。
d 3 (1 )[1 dt 2r fr 1 ln( )] 1 2 (9.36 )
溶解沉淀传质的推动力仍是颗粒的表 面能。只是液相润湿固相,每个颗粒之间的 空腔都形成一系列的毛细管,表面张力以毛 细管力的方式使颗粒拉近,毛细管力数值为 △P=2γLV/r,其中r是毛细管半径。粉料粒度 在0.1-1µm时,如果其中充满液相,毛细管力 可达1.23-12.3Mpa,可见毛细管力所造成的烧 结推动力是很大的 。
在固态烧结中也存在塑性流动。选择较
小的r、,较大的可以促进烧结。在烧结早
期,表面张力较大,塑性流动可以靠位错的
运动来实现;而烧结后期,在低应力作用下
靠空位自扩散而形成粘性蠕变,高温下发生
的蠕变是以位错的滑移或攀移来完成的、塑 性流动机理目前应用在热压烧结的动力学过 程是很成功的。
三、溶解—沉淀传质 1、溶解-沉淀传质的条件 在有固-液两相的烧结中,当固相在液相 中有可溶性,这时烧结传质过程就由部分固 相溶解,而在另一部分固相上沉积.直至晶粒 长大和获得致密的烧结体。 研究表明发生溶解沉淀传质的条件有 : ①显著数量的液相, ②固相在液相内有显著的可溶性; ③液体润湿固相。
L 1 x ~t L
1+x的意义是该值约大于1,这是考虑在烧结进 行时,被包裹的小尺寸气孔减小,作为烧结推 动力的毛细管压力增大,所以略大于1。
颗粒重排对坯体致密度的影响取决于液相 的数量。 1).液相量少 如果液相数量不足,则液体既不能完 全包裹颗粒,也不能充填颗粒间的空隙,当 熔体从甲处流向乙处后,在乙处发生颗粒的 重排,同时在甲处产生空腔,这时能产生颗 粒的重排但不足以消除气孔。
-液相烧结(课堂PPT)
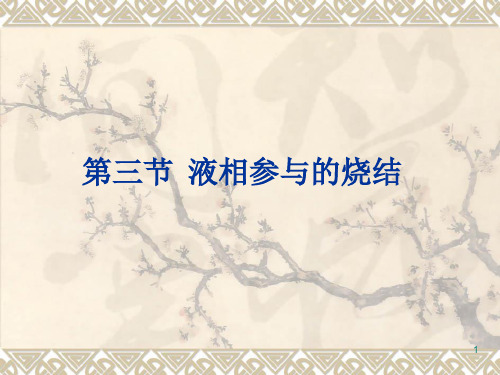
液相烧结的类型:据液相数量与性 质可分为两类三种情况:
表9-1 液相烧结类型
类 型
条件
Ⅰ
QLS >90° C=0
液相数量 烧结模型
0.01~0.5mol% 双球
传质方式
扩散
QLS <90° 少
Ⅱ
C>0
多
Kingery* LSW* *
溶解-沉淀
3
一. 流动传质:
1. 粘性流动: 机理(原因): 由于高温下粘性液体(熔融体)出现牛顿型流动而
第三节 液相参与的烧结
1
液相烧结:
❖ 凡有液相参加的烧结过程称为液相烧结。 ❖ 液相烧结与固相烧结的异同点: ❖ 相同点:烧结的推动力都是表面能,烧结过程
都是由颗粒重排、气孔充填和晶粒生长等阶段 组成
❖ 不同点:由于流动传质比扩散传质快,因而液 相烧结致密化速率高,可使坯体在比固态烧结 温度低得多的情况下获得致密的烧结体;影响 液相烧结的因素比固相烧结更为复杂,为定量 研究带来困难。
11
三. 不同烧结及传质机理比较
❖ 1. 固相烧结与液相烧结的异同点:
⑴ 相同点:
❖烧结的推动力都是表面能
❖烧结过程都包括颗粒接触、聚集、重排,气孔填充、 排出和晶粒生长等阶段
⑵ 不同点:
❖液相烧结比固相烧结传质速率高,因而液相烧结致 密化速率比固相烧结快,可以在更低的温度下使坯 体烧结成致密体
❖液相烧结的研究比固相烧结复杂。因为液相烧结速 率与液相量、η、γ、对固相润湿程度及固相在液 相中的溶解度等诸多因素有关。
❖ 3. 过程:颗粒重排和溶解-沉淀传质
8
❖ 颗粒重排:
颗粒在毛细管力作用下,通过粘性流动或在一 些颗粒间接触点上由于局部应力的作用而重新 排列,使堆积更致密。
第10章 液相烧结
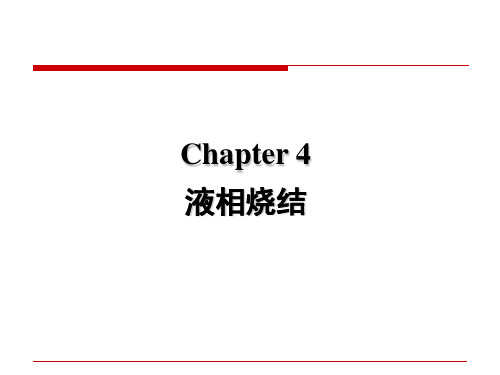
10.3烧结硬质合金的生产工艺
2.硬质合金生产
(5)最终烧结 WC~C0硬质合金的烧结是典型液相烧结过程。 液相主要来源于WC一C0的共晶液相。由WC一Co 平衡相图可知,于l320℃,WC与35%Co形成共 晶液相。当烧结温度高于1320℃时,WC—C0压 坯中就会形成一定体积分数的液相。
10.3烧结硬质合金的生产工艺
10.5超固相线烧结
10.6熔渗
要想成功地进行溶渗,必须注意以下几点: ①固态骨架与熔渗液体之间不得发生反应形成 化合物,或在熔渗完成之前堵塞孔道。 ②多孔性骨架中的孔洞必须是连通的,因为一 般熔渗不可能浸入到封闭孔隙中。 ③骨架材料在液态熔渗剂中的溶解度应为零或 尽可能低。 ④骨架材料的晶界与液相交汇处的两面角应当 小,但不能太小。
10.3烧结硬质合金的生产工艺
10.3烧结硬质合金的生产工艺
10.3烧结硬质合金的生产工艺
10.3烧结硬质合金的生产工艺
10.3烧结硬质合金的生产工艺
10.3烧结硬质合金的生产工艺
10.3烧结硬质合金的生产工艺
10.3烧结硬质合金的生产工艺
10.3烧结硬质合金的生产工艺
10.4具有可控孔隙度压坯的液相烧结
10.3烧结硬质合金的生产工艺
2.硬质合金生产
(5)最终烧结后续处理 为改进使用性能,精加工及研磨的硬质合金工 具表面往往要进行涂层处理。应用最多的是碳化钛 化学气相沉积法,它是以氢作为气体载体,用四氯 化钛与碳氢化合物蒸气进行沉积的。碳化钛涂层很 薄,约5um。涂层可增高刀刃的耐磨性,减小月 牙洼磨损及增强抗变形性,从而改进金属的切削率 和延长工具的使用寿命。除碳化钛外,还开发了碳 氮化钛、氮化钛及氧化铝涂层。涂层主要用于机卡 刀片。
按照烧结时是否出现液相,可将烧结分为两类固相烧结和液
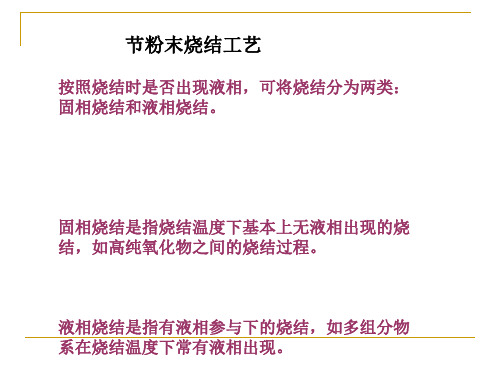
• 合金的收缩主要发生在液相出现之后。液相流动 引起WC颗粒重排与溶解和析出等过程使合金收缩 显著,并且导致WC颗粒长大。
• 保温时间愈长,WC晶粒愈粗并且愈不均匀。
• 烧结保温的后期,还发生WC的聚晶长大,它与通 过液相约重结晶长大不同,是发生在WC固架形成 之后的固相烧结长大。
当液相润湿固相时,在接触点A用杨氏 方程表示平衡的热力学条件为:
完全润湿时,θ=0o;完全不润湿时,θ>90o;部分润湿的状态, 0o<θ<90o
液相烧结需满足的润湿条件就是润湿角θ< ;如果θ>90,烧结开始 时液相即使生成,也会很快跑出烧结体外,称为渗出。发生渗出,烧结合金 中的低熔组分特大部分损失掉,使烧结致密化过程不能顺利完成。
WC—Co硬质合金的液相烧结
WC—Co硬质合金是液相烧结的典型例子: (1)Co对Wc完全润湿(θ→0); (2)WC在Co中部分溶解; (3)烧结温度超过Co的熔点,而液相在WC中不溶解,故保温阶段始终 存在液相。
工业合金含Co量为3%一25%(重 量),在过共晶相区。烧结温度随合金物 含量增高而降低,一般在1350~1480℃范 围内。
WC在Co中的溶解度随温度升高而增 大,在700~750℃,以Co为基的γ固溶体 中含Wc约1.5%(原子),1000℃时约4% (原子),共晶温度下约10%(原子)(~22 %重量)。Co在Wc中溶解度极低。
(1)预烧及升温阶段 为低于共晶温度的固相烧结。超过500℃之 后,在Co颗粒之间以及Co与Wc颗较之间开始发生烧结,压坯强度已有增 加;约1000℃时,Wc开始向Co中迅速扩散,并随温度继续升高而加快。
大,而两相的成分和比例都维持不变。
(4)保温完成后冷却 从液相中析出WC,液相数量减少,至共晶温 度时液相成分开始析出γ ,并同时结晶出共晶组织;低于共晶温度冷 却后,共晶中γ相不断析出二次WC晶体,有些附在原来的WC初晶颗粒上。 冷至室温后,合金组织应由原始末溶解的WC初晶和冷却过程中从液相或 γ相中析出的二次Wc晶体以及共晶(Wc十γ)所组成。
液相烧结的基本条件

液相烧结的基本条件一、液相烧结技术的原理液相烧结是一种常用的粉末冶金加工方法,通过加入适量的液相助熔剂,使粉末颗粒在高温下熔结成块状。
液相烧结的基本原理是:当热量作用于粉末堆体时,液相助熔剂在高温下熔化,填充在粉末颗粒之间,形成润湿层。
在润湿层的作用下,粉末颗粒之间发生了扩散和熔结,最终形成致密的块状产物。
二、液相烧结技术的应用液相烧结技术广泛应用于金属、陶瓷和复合材料等领域。
在金属材料方面,液相烧结可以用于制备高性能的工具钢、高速钢、不锈钢等。
在陶瓷材料方面,液相烧结可以制备高纯度的氧化铝、碳化硅、氮化硅等材料。
在复合材料方面,液相烧结可以用于制备金属基复合材料、陶瓷基复合材料等。
三、液相烧结技术的操作条件1. 温度:液相烧结的温度是影响烧结过程的重要参数。
温度过高会导致颗粒过度生长,烧结过程难以控制;温度过低则会影响烧结体的致密性。
不同材料的烧结温度有所差异,需要根据具体材料进行调控。
2. 压力:适当的压力可以促进粉末颗粒之间的扩散和熔结,提高烧结体的致密性。
压力过大可能导致烧结体变形或产生裂纹,压力过小则会影响烧结效果。
压力的选择应根据具体材料和烧结工艺进行调整。
3. 时间:烧结时间是影响烧结过程的重要因素。
时间过短会导致烧结体致密性不高,时间过长可能使烧结体结构粗化。
烧结时间的选择应综合考虑材料的烧结性能和工艺要求。
4. 液相助熔剂:液相助熔剂是液相烧结过程中的关键因素,它可以降低烧结温度,促进粉末颗粒的熔结。
常用的液相助熔剂有金属、氧化物、硼化物等。
液相助熔剂的选择应根据具体材料的烧结要求进行调整。
四、液相烧结技术的优缺点液相烧结技术具有以下优点:烧结体致密性高,性能稳定;可以制备复杂形状的零件;适用于高温材料和难熔材料。
然而,液相烧结技术也存在一些缺点:烧结过程中易产生气孔、裂纹等缺陷;烧结温度高,能耗较大;烧结过程中易产生气体污染。
总结液相烧结技术是一种重要的粉末冶金加工方法,具有广泛的应用前景。
3-6液相烧结教程
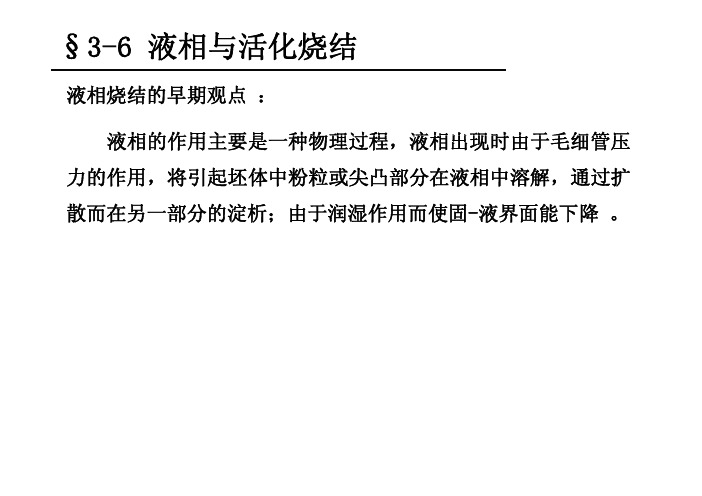
液相烧结的早期观点:液相的作用主要是一种物理过程,液相出现时由于毛细管压液相的作用主要是种物理过程液相出现时由于毛细管压力的作用,将引起坯体中粉粒或尖凸部分在液相中溶解,通过扩散而在另一部分的淀析;由于润湿作用而使固-液界面能下降。
Ref: 网络课件液相烧结的早期观点:液相的作用主要是一种物理过程,液相出现时由于毛细管压液相的作用主要是种物理过程液相出现时由于毛细管压力的作用,将引起坯体中粉粒或尖凸部分在液相中溶解,通过扩散而在另一部分的淀析;由于润湿作用而使固-液界面能下降。
¾近期的研究发现:近期的研究发现在绝大多数情况下,液相烧结都伴随着不同形式的化学反应。
这种化学反应的作用力远比毛细管压力大,其所引起的体系自由能的下降,也比表面(包括界面)自由能的下降要大几个数量级,的降也表括自的降大个数故有人将这类有反应作用的烧结称之为活化烧结(Activated sintering)。
§3-6 液相与活化烧结一、液相烧结中的物理作用过程前提条件:¾体系中必须具有一定的液相含量;体系中必须具有一定的液相含量¾固相物质在液相中必须具有明显的溶解度;¾液相必须能较好地润湿固相物质。
产生的物理效应:1.润滑效应——液相对固粒的润滑作用,使粉粒之间的摩擦减小,便于粉粒作相对运动,可使成型时留下的内应力下降,粉粒堆集度也有所改善。
2.毛细管压力与粉粒的初次重排当液相能很好润湿固相时,粉粒间的大多数空隙都将被液相填充,形成毛细管状液膜。
直径为0.1-1微米的毛细管在可在般陶瓷粉粒间产生110Mpa左右的压强,如此大的压可在一般陶瓷粉粒间产生1-10Mpa强加上液相的润滑作用,使胚体成型后粉粒重新排布,达到更紧密的空间堆积。
这被称为烧结过程中的初次重排。
5.熟化与外形适应(Ripening with shape accommodation)——奥氏熟化(Ostwald Ripening)d ti)奥氏熟化(O t ld Ri i)在可传质媒介中的颗粒大现象在可传质媒介中的颗粒长大现象。
液相烧结

三、液相烧结过程和机构
液相烧结的动力是液相表面张力和固—液界面张力 。
1、烧结过程
液相烧结过程可划分为三个界线不十分明显的阶段:
(1)液相流动与颗粒重排阶段
固相烧结时,不可能发生颗粒的相对移动,但 在有液相存在时,颗粒在液相内近似悬浮状态。受 液相表面张力的推动发生位移,因而液相对固相颗 粒润湿和有足够的液相存在是颗粒移动的重要前提。 颗粒间孔隙中液相所形成的毛细管力以及液相本身 的粘性流动,使颗粒调整位置、重新分布以达到最
紧密的排布,在这阶段,烧结体密度迅速增大。
(2)固相溶解和再析出阶段 固相颗粒表面的原子逐 渐溶解于液相,溶解度随温度和颗粒的形状、大小 而变。液相对于小颗粒有较大的饱和溶解度,小颗 粒先溶解,颗粒表面的棱角和凸起部位(具有较大曲 率)也优先溶解,因此,小颗粒趋向减小,颗粒表面 趋向平整光滑。相反,大颗粒的饱和溶解度较低, 使液相中一部分过饱和的原子在大颗粒表面沉析出
相界面,只产生固相
颗粒问的烧结。实际
上,只有液相与固相
的界面张力 SL愈小,
也就是液相润湿固相
愈好时,二面角才愈 小,才愈容易烧结。
温度与时间 升高温度或延长液—固接触时间均能减
润
小 角 ,但时间的作用是有限的。
湿
铜中添加镍能改善对许多金属或化合物
性 影
表面活性物质 的润湿性 ; 表低面 活L,性只元有素减的小作用SL才并能不使表润现湿为性降改善
液相烧结
1045562117 沈祥
一、定义与分类
液相烧结
指在烧结过程中出现 少量液相的烧结过程
瞬时液相烧结
长时间大量液相出现的烧结
二、液相烧结的影响因素
基本因素
润湿性
液相烧结助剂

液相烧结助剂在金属陶瓷材料的制备过程中,液相烧结助剂扮演着至关重要的角色。
液相烧结助剂作为促进金属陶瓷颗粒间结合的重要组成部分,可以有效降低烧结温度、促进烧结过程中的相转变、改善材料的性能等。
本文将从液相烧结助剂的定义、种类、作用机理等方面展开讨论,以期深入探究液相烧结助剂在金属陶瓷材料制备中的重要作用。
液相烧结助剂是指在金属陶瓷材料的制备过程中,添加的一种能够促进粉体颗粒结合的物质。
液相烧结助剂通常为氧化物、碱金属化合物、硼酸盐等物质,其添加可以有效降低烧结温度,提高烧结密度,并有利于晶界扩散和相转变。
在实际生产中,液相烧结助剂的种类和用量需根据具体材料的性质和要求而定,合理的添加可以有效改善材料的性能。
液相烧结助剂的种类多种多样,常用的有氧化铝、氧化锌、氧化镁、氧化铍、氧化钇等。
这些液相烧结助剂具有不同的特性和作用机制,可以分为玻璃相烧结助剂、氧化物烧结助剂、盐类烧结助剂等几类。
玻璃相烧结助剂主要是玻璃形成的液相,其添加可以在晶体颗粒间形成液相,促进烧结反应的进行。
氧化物烧结助剂则是一种以氧化物为主要成分的液相烧结助剂,其主要作用是在烧结过程中形成氧化物间的液相,从而促进颗粒间的结合。
盐类烧结助剂是指将一定量的金属盐或碳酸盐等添加到材料中,通过在烧结过程中分解产生气体,促进颗粒间的结合。
这些液相烧结助剂可以根据实际需求进行选择和调整,以获得最佳的烧结效果。
液相烧结助剂的作用机理主要包括两部分,一是通过形成液相,在颗粒间起到粘结作用,促进颗粒间的结合;二是通过促进烧结过程中的相转变,改善材料的结晶结构和性能。
在烧结过程中,液相烧结助剂可以在晶界扩散过程中起到助剂作用,降低晶界扩散的能垒,加速晶界扩散速率,从而促进颗粒间的结合。
此外,液相烧结助剂还可以改善材料的性能,例如提高材料的抗弯强度、硬度、热稳定性等,使其在实际应用中更加稳定和可靠。
因此,液相烧结助剂在金属陶瓷材料的制备中扮演着至关重要的角色,其选择和使用对材料的最终性能有着重要影响。
液相烧结影响因素
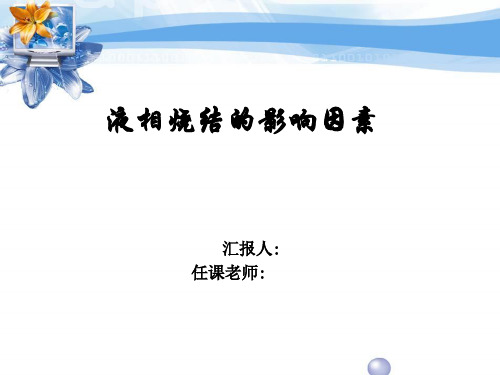
• 对于冷切速度快慢的优劣,应根据具体的情况的不同进行选择: (1)冷却速度过快,基体中的合金化元素越容易达到饱和,因此得到的 烧结强度越高,但在液相的凝固温度下,容易形成孔隙,因此,过快的 冷却速度是有害的。 (2)冷却速度可以控制杂质的析出。由于杂质可以降低界面能,因此将 优先在界面处偏析,从而造成制品的脆性,因此快速冷却是有好处的。
• 如右图所示
•
由于添加剂的颗粒大小控制着添加剂颗粒的原来位置所形成 的孔隙的大小,因此,应该选用具有小而均匀的颗粒尺寸的 添加剂。
对于液相烧结会产生膨胀的系统,使用小颗粒和提高加热速 度可以使得膨胀量最小,达到最好的致密化。
3.粉末内部的孔隙
• 在液相烧结过程中,液相将首先进入固体颗 粒内部的孔隙,从而减小了颗粒之间液相的 数量。由于颗粒内部孔隙的体积小于颗粒之 间孔隙的体积,因此颗粒内部孔隙中液体的 毛细作用要比颗粒之间孔隙中液体的毛细作 用大得多。因此,不同材料或相同材料不同 状态下,粉末孔隙的多少以及他们的分布影 响材料的烧结。
二.粉末的特性
1.颗粒的形状
• 颗粒的形状在压坯的成形阶段和在液相烧结的颗粒重新排列阶段 具有重要作用。
• 压坯成形阶段 颗粒不均匀 颗粒间摩擦力增大 生坯的密度减小 烧结的密
度降低。 • 重新排列阶段
颗粒的形状变化 排布期间毛细管力的变化。 通常,球形对毛细 管力的作用比较敏感。 形状复杂导致颗粒重排阻力增加,故球形颗粒有利于颗粒重排。 不规则形状的颗粒粉末比使用球形的颗粒粉末所得到的烧结显微组 织的不均匀性要大得多,从而造成制品性能的降低。 • 在液相烧结的后期阶段,由于溶解-再析出作用,颗粒形状将变化,
液相烧结传质机理塑性流动传质

c exp[ ] kT kT
3
G f
在颈部表面的过剩空位浓度为
c'c0 c 3 exp 1 c0 c0
冶金学院硅一般烧结温度下, 于是 c
3 1 c0 kT
c c0 kT
3
从式可见,在一定温度下空位浓度差是与表面张力成比例的, 因此由扩散机理进行的烧结过程,其推动力也是表面张力。
由于空位扩散既可以沿颗粒表面或界面进行,也可能通过颗 粒内部进行,并在颗粒表面或颗粒间界上消失。为了区别, 通常分别称为表面扩散,界面扩散和体积扩散。有时在晶体 内部缺陷处也可能出现空位,这时则可以通过质点向缺陷处 扩散,而该空位迁移到界面上消失,此称为从缺陷开始的扩 散。 冶金学院硅酸盐教研室
G f n0 C0 exp( ) N kT
冶金学院硅酸盐教研室
第二节 固相烧结传质原理
倘若质点(原子或离子)的直径为δ ,并近似地令空位体积 为δ 3,则在颈部区域每形成一个空位时,毛细孔引力所做 的功△W=γ δ 3/ρ 。故在颈部表面形成一个空位所需的能 量应为△Gf=-γ δ 3/ρ ,相应的空位浓度为
第一节
基本概念
与烧结有关的一些概念 A.烧结与烧成(firing): 烧成:包括多种物理和化学变化。例如脱水、坯体内气体 分解、多相反应和熔融、溶解、烧结等。而烧结仅仅指粉 料经加热而致密化的简单物理过程,烧结仅仅是烧成过程 的一个重要部分。 B.烧结和熔融(Melt): 烧结是在远低于固态物质的熔融温度进行的。烧结和熔融 这两个过程都是由原子热振动而引起的,但熔融时全部组 元都为液相,而烧结时至少有一组元是处于固态。 冶金学院硅酸盐教研室
第一节
基本概念
C.烧结与固相反应: 两个过程均在低于材料熔点或熔融温度之下进行的。并且 在过程的自始自终都至少有一相是固态。两个过程不同之 处是固相反应必须至少有两组元A和B参加,并发生化学反 应,最后生成化合物AB。AB结构与性能不同于A和B。而 烧结可以只有单组元,或者两组元参加,但两组元并不发 生化学反应。仅仅是在表面能驱动下,由粉体变成致密体。 从结晶化学观点看,烧结体除可见的收缩外,微观晶相组 成并未变化,仅仅是晶相显微组织上排列致密和结晶程度 更完善。但在实际生产中,纯的烧结是很难见到的。 冶金学院硅酸盐教研室
液相烧结机制

液相烧结机制一、液相烧结的定义及其分类定义:凡有液相参加的烧结过程称为液相烧结。
由于粉末中总含有少量杂质,因而大多数材料在烧结中都会或多或少地出现液相,即使在没有杂质的纯固相系统中,高温下还会出现“接触"熔融现象因而纯粹的固态烧结实际上不易实现,在无机材料制造过程中,液相烧结的应用范围很广泛,如长石质瓷,水泥熟料、高温材料(如氮化物,碳化物等都采用液相烧结原理。
液相烧结与固态烧结的共同之点是烧结的推动力都是表面能,烧结过程也是由颗粒重排、气孔充填和晶粒生长等阶段组成。
不同点是由于流动传质速率比扩散传质快,因而液相烧结致密化速率高,可使坯体在比固相烧结温度低得多的情况下获得致密的烧结体,此外液相烧:结过程的速率与液相数量.液相性质(粘度和表面张力等)液相与固相润湿情况,固相在液相中的溶解度等等有密切的关系,因此影响液相烧结的因素比固相烧结更为复杂,为定量研究带来困难。
分类:1.瞬时液相烧结(transient liquid phase sintering) 在烧结中、初期存在液相,后期液相消失的烧结过程特点:烧结中初期为液相烧结,后期为固相烧结。
液相数量取决于成分(低熔点组分的含量)、升温速度、粉末颗粒的粒度。
提高瞬时液相烧结过程中的液相数量可采用提高低熔点组分含量升温速度快,高熔点组分颗(与液相接触面积小,减小扩散面积)。
3 熔浸(infiltration) 多孔骨架的固相烧结和低熔点金属渗入骨架后的液相烧结过程前期为固相烧结,后期为液相烧结。
4.超固相线液相烧结:液相在粉末颗粒内形成,是一种在微区范围内较普通液相烧结更为均匀的烧结过程。
二、液相烧结技术的优缺点优点:1)加快烧结速度:a 液相的形成加快了原子迁移速度。
b 在无外压的情况下,毛细管力的作用加快坯体的收缩c 液相的存在降低颗粒间的摩擦有利于颗粒重排列。
2) 晶粒尺寸可以通过调节液相烧结工艺参数加以控制,便于优化显微结构和性能 3) 可制得全致密的P/M材料或制品,延伸率高。
液相烧结所应该满足的条件
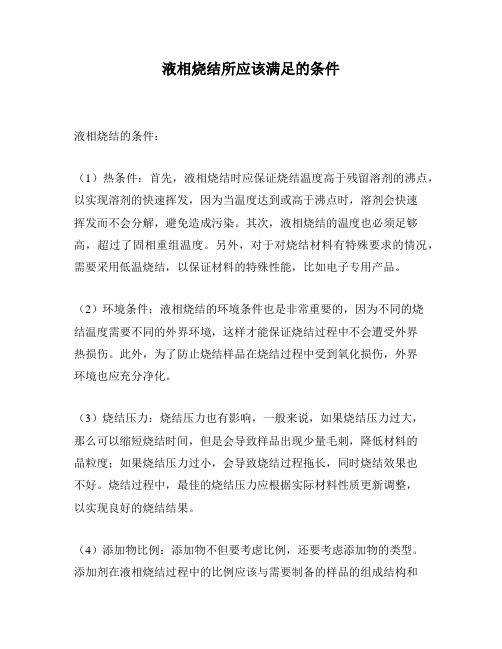
液相烧结所应该满足的条件
液相烧结的条件:
(1)热条件:首先,液相烧结时应保证烧结温度高于残留溶剂的沸点,以实现溶剂的快速挥发,因为当温度达到或高于沸点时,溶剂会快速
挥发而不会分解,避免造成污染。
其次,液相烧结的温度也必须足够高,超过了固相重组温度。
另外,对于对烧结材料有特殊要求的情况,需要采用低温烧结,以保证材料的特殊性能,比如电子专用产品。
(2)环境条件:液相烧结的环境条件也是非常重要的,因为不同的烧
结温度需要不同的外界环境,这样才能保证烧结过程中不会遭受外界
热损伤。
此外,为了防止烧结样品在烧结过程中受到氧化损伤,外界
环境也应充分净化。
(3)烧结压力:烧结压力也有影响,一般来说,如果烧结压力过大,
那么可以缩短烧结时间,但是会导致样品出现少量毛刺,降低材料的
晶粒度;如果烧结压力过小,会导致烧结过程拖长,同时烧结效果也
不好。
烧结过程中,最佳的烧结压力应根据实际材料性质更新调整,
以实现良好的烧结结果。
(4)添加物比例:添加物不但要考虑比例,还要考虑添加物的类型。
添加剂在液相烧结过程中的比例应该与需要制备的样品的组成结构和
应用特性有关,同时,添加量恰当也无小事,太多太少都会影响到样品的特性和性能。
(5)烧结时间:烧结的温度虽然有了把握,但是要把握烧结时间也是必要的,烧结时间太长容易失控,烧结时间太短又达不到最佳烧结效果。
此外,烧结时间还与温度息息相关,烧结时间随着温度的上升而减少,因此,应根据特定材料的性质,更新调整温度,以实现最佳的烧结效果。
- 1、下载文档前请自行甄别文档内容的完整性,平台不提供额外的编辑、内容补充、找答案等附加服务。
- 2、"仅部分预览"的文档,不可在线预览部分如存在完整性等问题,可反馈申请退款(可完整预览的文档不适用该条件!)。
- 3、如文档侵犯您的权益,请联系客服反馈,我们会尽快为您处理(人工客服工作时间:9:00-18:30)。
液相烧结的早期观点:
液相的作用主要是一种物理过程,液相出现时由于毛细管压液相的作用主要是种物理过程液相出现时由于毛细管压力的作用,将引起坯体中粉粒或尖凸部分在液相中溶解,通过扩散而在另一部分的淀析;由于润湿作用而使固-液界面能下降。
Ref: 网络课件
液相烧结的早期观点:
液相的作用主要是一种物理过程,液相出现时由于毛细管压
液相的作用主要是种物理过程液相出现时由于毛细管压力的作用,将引起坯体中粉粒或尖凸部分在液相中溶解,通过扩散而在另一部分的淀析;由于润湿作用而使固-液界面能下降。
¾近期的研究发现:
近期的研究发现
在绝大多数情况下,液相烧结都伴随着不同形式的化学反应。
这种化学反应的作用力远比毛细管压力大,其所引起的体系自由能的下降,也比表面(包括界面)自由能的下降要大几个数量级,的降也表括自的降大个数
故有人将这类有反应作用的烧结称之为活化烧结(Activated sintering)。
§3-6 液相与活化烧结
一、液相烧结中的物理作用过程
前提条件:
¾体系中必须具有一定的液相含量;
体系中必须具有一定的液相含量
¾固相物质在液相中必须具有明显的溶解度;
¾液相必须能较好地润湿固相物质。
产生的物理效应:
1.润滑效应——液相对固粒的润滑作用,使粉粒之间的摩擦减小,便于粉粒作相对运动,可使成型时留下的内应力下降,粉粒堆集度也有所改善。
2.毛细管压力与粉粒的初次重排
当液相能很好润湿固相时,粉粒间的大多数空隙都将被
液相填充,形成毛细管状液膜。
直径为0.1-1微米的毛细管在
可在般陶瓷粉粒间产生110Mpa左右的压强,如此大的压可在一般陶瓷粉粒间产生1-10Mpa
强加上液相的润滑作用,使胚体成型后粉粒重新排布,达到
更紧密的空间堆积。
这被称为烧结过程中的初次重排。
5.熟化与外形适应(Ripening with shape accommodation)——奥氏熟化(Ostwald Ripening)
d ti)奥氏熟化(O t ld Ri i)
在可传质媒介中的颗粒大现象
在可传质媒介中的颗粒长大现象。
气相传质:蒸发-凝结引起的大粒变大,小粒消失过程;
液相传质:溶入-析出引起的粗粒变粗,细粒变细或消失的过程;
烧结后期:体内孤立气孔,通过空格点扩散而引起的大孔长大,小孔缩小或消失的过程(此时气孔被当作颗粒)。
固态脉络的形成
§3-6 液相与活化烧结
6.固态脉络(Solid Skeleton)的形成液相烧结实验的典型收缩曲线
粉粒重排由于液相的润滑作用毛细管压的拉紧作用¾粉粒重排,由于液相的润滑作用,毛细管压的拉紧作用,使粉粒间的配位数提高,使坯体中的气孔大量消失,收缩率显著增加,故线收缩率特别大。
液相烧结实验的典型收缩曲线由于受压接触平滑作用,收缩比较缓慢,其线收缩率与烧
6.固态脉络(Solid Skeleton)的形成
固态脉络的形成
液相烧结实验的典型收缩曲线
¾致密化过程已接近饱和,收缩率几乎不随烧结时间而变。
这一阶段被解释为是由于在烧结体中形成了固态脉络。
即在此时期固态晶粒相互接触支撑,形成了彼此联续的骨架。
在此时期固态晶粒相互接触支撑形成了彼此联续的骨架
考虑化学反应时的性液相烧结
二、考虑化学反应时的活性液相烧结1.固溶体的形成
体系的组分为C 0
T Ts ,L出现
平衡时:
陶瓷瓷料添加剂
液相的成分为C L
成分为C β的固相将不断析出。
形成固溶体的液相烧结图料
存在于B相和β相之间的浓度
梯度即为这种溶入析出过程的主
要推动力,直到粉粒B全部溶入
并转化为β析出为止。
这时体系
才达到化学平衡状态。
在上图中A相+B相全部材料转化为β+L或β相时,其自由能下降的典型值为100~1000焦耳/摩尔;
而已知由于颗粒长大而引起的表面能或界面能的下降,而已知由于颗粒长大而引起的表面能或界面能的下降一般为1~10焦耳/摩尔。
由此可见化学势下降推动力应起到主导作用。
2.粒界渗蚀、粉粒纠裂与二次重排
在液相润滑和毛细管压的作用之下,细小粉粒之间可能相对在液相润滑和毛细管压的作用之下细小粉粒之间可能相对运动,以缓和残存的机械应力或填充坯体孔隙,这一过程即称之为粉粒的二次重排。
3.定向粒长
被富镍相液膜分隔的一对钨球
所
(上)和微探针线扫描所得的
镍成分分布(下)
这一过程也可作为一种溶入-析出机理来描述,其推动力即为化学势差,它存在于纯钨和析出的镍-钨固溶合金之间。
它存在于纯钨和析出的镍钨固溶合金之间
在BaTiO 3-SrTiO 3系球状粉粒的烧结过程中,也观察到这种定向粒长的情况由于Ba +2+2具有更大的扩散能力这种定向粒长的情况,由于Ba 比Sr 具有更大的扩散能力,故在烧结过程中BaTiO 3球不断缩小,形成了(Ba,Sr)TiO 3固溶体,并向SrTiO 3粒处凝结,这类固溶瓷的烧结化过程,都比单一成分烧结时要快得多,这就是由于烧结过程中出现了化单成分烧结时要快得多,这就是由于烧结过程中出现了化学势差推动的活化作用。
不过值得提醒的是在B TiO S TiO 系的活化烧结中不过,值得提醒的是,在BaTiO 3-SrTiO 3系的活化烧结中,决定粒长方向的主要因素在于扩散系数的不同,在此体系中并没有观察到相应的液相。
因为BaTiO 3和SrTiO 3两者之间是互为无限固溶的连续固溶体烧结温度仍在固相线之下这也说明无限固溶的连续固溶体,烧结温度仍在固相线之下,这也说明活化烧结并非必须存在液相。
4.常规粒长与粒形适应
尽管体系有液相存在,但在烧结坯体中进行的化学反应,仍属于固相和液相之间的非均相反应,均匀一致的固溶体的形成需要相当长的时间,几小时、几十小时,乃至于更长,要看相应的烧结温度和具体的扩散系数而定。
所以,当均一的固溶体尚未形成,液相还没有消失的时候,晶粒长大与粒形适应的过程早已开始。
总体来说,在烧结中期促使渗蚀解裂、二次重排的化学
势能下降,乃是烧结的主要推动力。
故这时坯体收缩得特
β
别快,但到了后期相已形成并已接近均匀化,化学势之下
降已逐步减弱或趋于消失,而表面及界面能的下降逐渐上
升为主要因素,烧结的推动力变得很小,致密化过程也就
变慢了。
变慢了
5.活化液相烧结与致密化过程
活性液相烧结可概括为三种基本机理,即粒界的蚀
活性液相烧结可概括为三种基本机理即粒界的蚀裂与二次重排,定向粒长,常规粒长和粒形适应。
这三种机理的推动力并不完全一样,但都和溶入-析出过程有关。
同时,这三种机理都与瓷体的致密化过程密切相关。
定向粒长和重排致密示意图常规粒长与外形适应致密图
§3-6 液相与活化烧结
参照液相烧结收缩率曲线,
可作如下考虑:在烧结前期,进
可作如下考虑:在烧结前期进
入恒温阶段之前,液相出现,绝
大部分粉粒受到润湿与一次重排,
大部分粉粒受到润湿与一次重排
出现最大的收缩率;到了中期,
主要靠渗蚀解裂与二次重排,这
主要靠渗蚀解裂与二次重排这
时收缩率还不算小,到了后期则
以常规粒长和适应熟化机理为主,
以常规粒长和适应熟化机理为主
收缩将越来越小乃至于接近饱和。
致密化的全过程是多种机理的共同作用或交替重叠的。
主要是两种推动力:其一是活性的溶入与析出,但必须要求
有化学势差的存在;第二是重排与常规粒长。
它的界面能下有化学势差的存在第二是重排与常规粒长它的界面能下
降为推动力,但必须有结构间隙和足够界面存在。