车间过程分层审核检查表(1)
分层审核检查表
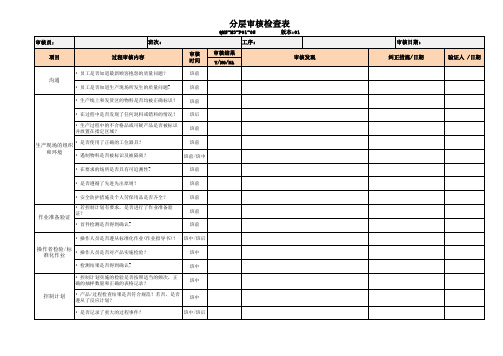
班中
• 返工完成后每个产品是否得到了确认?
班中
预防性维护活动 • 是否验证了设备的维护保养和点检的实施情况 班前
设备管理 • 设备修理后是否有记录,是否得到验证?
班前
审核结论:1.没有发现不符合项:Y 2.有需要改进项:NO ,并填写审核发现 3.审核条款不适用:NA
审核日期: 纠正措施/日期
验证人 /日期
班中 班中
• 是否记录了重大的过程事件?
班中/班后
审核日期: 纠正措施/日期
验证人 /日期
审核员: 项目
班次: 过程审核内容 • FTQ是否坚持执行“警戒控制线”?
分层审核检查表
QMS-M3-P01-05
版本:01
工序:
审核 时间
审核结果 Y/NO/NA
审核发现
班后
• 反映计划是否有效并被执行?
班后
班前
• 首件检测是否得到确认?
班前
• 操作人员是否遵从标准化作业(作业指导书)? 班中/班后
操作者检验/标 准化作业
•
操作人员是否对产品实施检验?
班中
• 检测结果是否得到确认?
班中
Байду номын сангаас控制计划
• 控制计划实施的检验是否按照适当的频次,正 确的抽样数量和正确的表格记录?
• 产品/过程检查结果是否符合规范?若否,是否 遵从了反应计划?
• 生产过程中的不合格品或可疑产品是否被标识 并放置在指定区域?
班前
生产现场的组织 • 是否使用了正确的工位器具?
和环境
• 遏制物料是否被标识及被隔离?
班前 班前/班中
• 在要求的场所是否具有可追溯性?
班前
• 是否遵循了先进先出原则?
分层审核检查表-模板
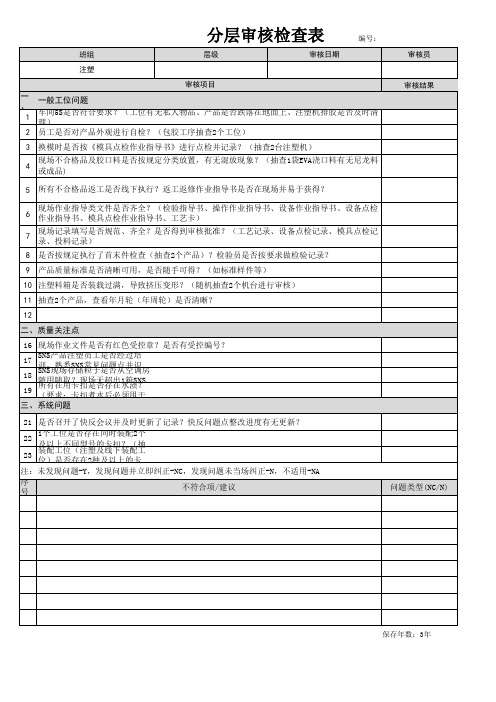
17 18 19
SNS产品注塑员工是否经过培 训SN,S现熟场悉存SN储S粒常子见是问否题从点空并调识房 随所用 有随 在取 用? 卡现 扣场 是无 否超 存出 在1水箱渍S?NS (要求:卡扣煮水后必须甩干
三、系统问题
21 是否召开了快反会议并及时更新了记录?快反问题点整改进度有无更新?
22 23
8 是否按规定执行了首末件检查(抽查2个产品)?检验员是否按要求做检验记录?
9 产品质量标准是否清晰可用,是否随手可得?(如标准样件等)
10 注塑料箱是否装载过满,导致挤压变形?(随机抽查2个机台进行审核)
11 抽查2个产品,查看年月轮(年周轮)是否清晰?
12
二、质量关注点
16 现场作业文件是否有红色受控章?是否有受控编号?
1个工位是否存在同时装配2个 及装以 配上 工不 位同 (型 注号 塑的 及卡 线扣 下? 装( 配抽 工 位)是否存在2种及以上的卡
注:未发现问题-Y,发现问题并立即纠正-NC,发现问题未当场纠正-N,不适用-NA
序 号
不符合项/建议
问题类型(NC/N)
保存年数:3年
审核员 审核结果
5 所有不合格品返工是否线下执行?返工返修作业指导书是否在现场并易于获得?
6
பைடு நூலகம்
现场作业指导类文件是否齐全?(检验指导书、操作作业指导书、设备作业指导书、设备点检 作业指导书、模具点检作业指导书、工艺卡)
7
现场记录填写是否规范、齐全?是否得到审核批准?(工艺记录、设备点检记录、模具点检记 录、投料记录)
分层审核检查表
编号:
班组
层级
审核日期
注塑
审核项目
一 、
1
分层审核用表模板

问题描述
改善计划
责任部门人签字 预计完成日期 实际完成日期
检查工位周围是否整洁有序,设备、工装模具、工作台及周边
5 地面进行了清洁,对废弃物进行了分类管理,并使用了正确的 工位器具。
6
检查工位周围是否有滞留的不明状态零件(无标识,无标 签,)
7
检查零件标签是否与实物一致,无错漏且标识填写完整
零件的周转、存储是否符合规定,不可超装、叠压、不良品分
8 类放置,料箱标识卡填写需完整且具有唯一性,不可有多余标 识卡,外箱不能有废旧标签;
设备运转是否有异常或故障情况,急停开关,双手开 14 关,光栅是否安全有效,各水流量、气流量压力值是否
在正常范围。 作业结束后设备、工装、物料是否放置在正确的位置 15
点焊工作站作业员是否正确有效的做自检画线检查,产品涂胶
16
是否清理干净
17 抽检确认设备使用参数是否符合标准,点焊焊点数量是否正确
18 检查凸焊数量核对表有无如实记录填写
9
首件是否及时送检并得到认可,并在首件检验合格后才进行批 量生产
10 检查记录表填写是否符合标准,巡检记录是否完整
11
检查操作者是否对正确的当前设备进行了点检(包括工装模具 、检具、设备、叉车、行车等)
12
检查设备(包括但不限于机床、运输设备、消防器材等)无明 显安全隐患。
13
检查操作者能够且能够简单口述设备点检的检查内容,及判定 标准。
序号 1
要素
周 班次
员工穿着符合要求(手套、工作衣、工作鞋等穿戴齐全)
2
作业指导书是否正确存放于现场,员工是否按照作业指导书要 求规范操作
3
员工是否充分理解与掌握了设备操作、设备点检、工艺参数点 检内容;并在生产开始前进行了点检与记录。
分层审核检查表
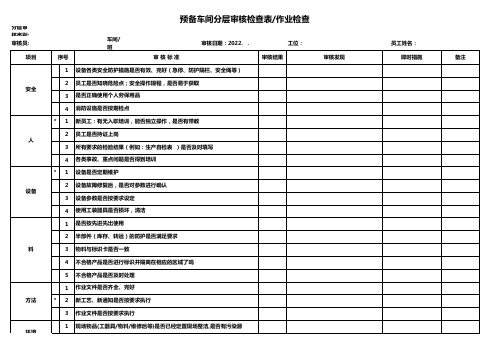
2 半部件(库存、转运)的防护是否满足要求
3 物料与标识卡是否一致
4 不合格产品是否进行标识并隔离在相应的区域了吗
5 不合格产品是否及时处理
1 作业文件是否齐全、完好
* 2 新工艺、新通知是否按要求执行
3 作业文件是否按要求执行
1 现场物品(工器具/物料/维修后等)是否已经定置现场整洁,是否有污染源
分层审 核类别: 审核员:
项目 安全
人
设备
料
方法 环境
预备车间分层审核检查表/作业检查
序号
车间/ 班
审核标准
审核日期:2022. .
1 设备各类安全防护措施是否有效、完好(急停、防护隔栏、安全绳等)
2 员工是否知晓危险点;安全操作规程,是否易于获取
3 是否正确使用个人劳保用品
4 消防设施是否按期检点
工位: 审核结果
审核发现
员工姓名: 即时措施
备注
环境
2 锭子房内外部温度差是否符合标准要求
1 使用的计量器具是否齐全、完好、有标识、在有效期内
检测
2 员工是否会准确使用计量器具 3 皮带秤、小料称是否定期校验
4 在线测量设备、防误是否正常使用
变更
* 1 4M1E变更是否按要求执行
顾客要 求
内部 外部
* 1 新员工:有无入职培训,能否独立操作,是否有带教
2 员工是否持证上岗
3 所有要求的检验结果(例如:生产自检表 )是否及时填写
4 各类事故、重点问题是否得到培训
* 1 设备是否定期维护
2 设备故障修复后,是否对参数进行确认
3 设备参数是否按要求设定
4 使用工装器具是否损坏,清洁
1 是否按先进先出使用
分层审核检查表(科长)
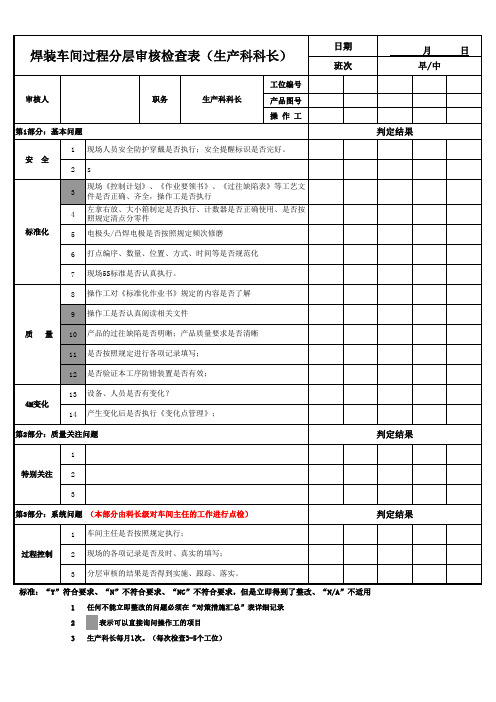
焊装车间过程分层审核检查表(生产科科长)
班次
月
日
早/中
审核人 第1部分:基本问题
职务
生产科科长
工位编号 产品图号 操作工
安全
1 现场人员安全防护穿戴是否执行;安全提醒标识是否完好。 2s
标准化
3
现场《控制计划》、《作业要领书》、《过往缺陷表》等工艺文 件是否正确、齐全,操作工是否执行
4
左拿右放、大小箱制定是否执行、计数器是否正确使用、是否按 照规定清点分零件
4M变化
13 设备、人员是否有变化? 14பைடு நூலகம்产生变化后是否执行《变化点管理》;
第2部分:质量关注问题
判定结果
1
特别关注 2
3
第3部分:系统问题 (本部分由科长级对车间主任的工作进行点检)
判定结果
1 车间主任是否按照规定执行;
过程控制 2 现场的各项记录是否及时、真实的填写;
3 分层审核的结果是否得到实施、跟踪、落实。
5 电极头/凸焊电极是否按照规定频次修磨
判定结果
6 打点编序、数量、位置、方式、时间等是否规范化
7 现场5S标准是否认真执行。
8 操作工对《标准化作业书》规定的内容是否了解
9 操作工是否认真阅读相关文件
质 量 10 产品的过往缺陷是否明晰;产品质量要求是否清晰
11 是否按照规定进行各项记录填写;
12 是否验证本工序防错装置是否有效;
标准:“Y”符合要求、“N”不符合要求、“NC”不符合要求,但是立即得到了整改、“N/A”不适用
1 任何不能立即整改的问题必须在“对策措施汇总”表详细记录
2
表示可以直接询问操作工的项目
3 生产科长每月1次。(每次检查3-5个工位)
过程分层审核检查表

1.8 检具、标准件是否标识清晰、完整,并在有效期内。
1.9 首件是否保留,并记录完整、正确。
1.10 交接班记录是否填写完整、清晰。
1.11 各检查记录和操作记录是否及时、准确、完整、清晰。
★●■▲ 2 个别工序重点关注问题
2.1 代加工产品有无锈蚀。
2.2 热处理温度参数是否符合工艺要求。
2.3 是否有SPC控制图,数据异常时是否有纠正行动。
`
1.2 员工劳防用品(工作服、工作鞋)穿戴是否整齐。
1.3 操作工是否有资格胜任岗位(上岗证、能力矩阵表).
1.4 设备日常点检、维护保养是否完成,并记录。
1.5 现场产品状态标识/流转卡填写是否清晰、完整、正确。
1.6 可疑品、不合格品是否有效隔离,并标识。
1.7 工艺文件是否齐全、清晰、完成、有效。
2.4 磨加工机床参数、砂轮选择是否符合工艺要求。
2.5 自动检测装置是否有效。
2.6
探伤设备日常校验、磁悬液浓度检验关照度是否完成, 并记录
2.7 轴向游隙检测仪是否校验,并记录。
2.8 注脂设备是否校验,并记录。
2.9 清洗剂是否定期检验、更换,并记录。
2.10 清洗机滤网、滤芯是否定期检查、更换,并记录。
2.11
环境(温度、湿度、落尘量)是否满足要Fra bibliotek,并有监控 记录。
3 系统性问题
★●■3.1 看板是否更新
★●■3.2 员工对产品质量标准是否清楚。
★●■3.3 操作工是否理解各工序的关键特性。
★●■▲3.4 防错验证是否有效、是否有记录。
★●■3.5 班长/分厂长/生产经理等是否进行分层审核。
★●■3.6 生产中出现的设备问题和质量问题是否有很好的沟通。
分层审核过程审核查检表

仓库
刘工
2016/9/6
9月6日
任俊锋
OK
24
9月4日
182001无季度标签与品质PASS章
仓库
刘工
2016/9/6
9月6日
任俊锋
OK
25
9月4日
82038、电池盒、显示屏后盖、调节塞无季度标签
仓库
刘工
2016/9/6
9月6日
任俊锋
OK
26
9月4日
205产品区摆放94产品
仓库
刘工
2016/9/6
9月6日
31
9月6日
包材放置已检区,第二次
注塑
胡工
2016/9/7
9月7日
任俊锋
OK
32
9月6日
文件放置处未做标识,第二次
注塑
胡工
2016/9/7
9月7日
任俊锋
OK
33
9月6日
物料放置处杂乱,第二次
注塑
胡工
2016/9/7
9月7日
任俊锋
OK
34
9月6日
烤箱日点检表未做到位,对应日期未点检
注塑
胡工
2016/9/7
设备卡未及时点检与保养
组装
温工
2016/9/8
39
9月7日
生产无首件盒,无单独返工区域
组装
温工
2016/9/8
40
9月7日
现场看板无作业员上岗证,没有对应的人员技能矩陈图
组装
温工
2016/9/8
41
9月7日
不合格品未进行隔离
组装
温工
2016/9/8
42
9月7日
分层审核检查表
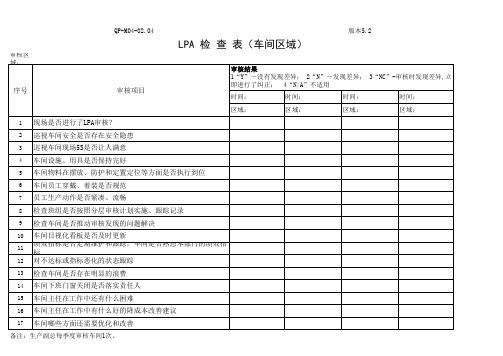
3 巡视车间现场5S是否让人满意
4 车间设施、用具是否保持完好
5 车间物料在摆放、防护和定置定位等方面是否执行到位
6 车间员工穿戴、着装是否规范
7 员工生产动作是否紧凑、流畅
8 检查班组是否按照分层审核计划实施、跟踪记录
9 检查车间是否推动审核发现的问题解决
10 车间目视化看板是否及时更新
11
绩效指标是否定期维护和跟踪,车间是否熟悉本部门的绩效指 标
QP-M04-02.04
版本5.2
审核区 域:
序号
审核项目
LPA 检 查 表(车间区域)
审核结果 1“Y”-没有发现差异; 2“N”-发现差异; 3“NC”-审核时发现差异,立 即进行了纠正; 4“N/A”不适用
时间:
时间:
时间:
时间:
区域:
区域:Βιβλιοθήκη 区域:区域:1 现场是否进行了LPA审核?
2 巡视车间安全是否存在安全隐患
12 对不达标或指标恶化的状态跟踪
13 检查车间是否存在明显的浪费
14 车间下班门窗关闭是否落实责任人
15 车间主任在工作中还有什么困难
16 车间主任在工作中有什么好的降成本改善建议
17 车间哪些方面还需要优化和改善
备注:生产副总每季度审核车间1次。
分层次审核检查表(适用于第二层、第三层)
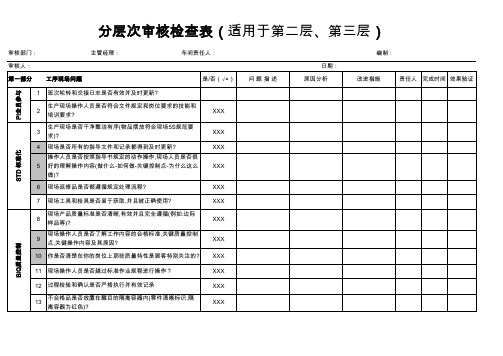
14
XXX
是否正确的零件放置在正确的容器内?
检查最少/最多周转量的符合性,零件是否遵循先进先出原
15 则?
XXX
是否每次设备启动和班次轮转的确认验证都被明确定义并
16
XXX
有效实施?
第二部分 工序质量关注(重点关注顾客反映以及内部审核过程中发现的 XXX
质量关注点)
1 岗位工序零件尺寸是否符合图纸要求
车间责任人:
审核人: LAYER
ED
NO.
XXX
Comments评论
XXX
XXX - 问题序号为灰色的部分需要直接询问现场操作
XXX 工 PI - 全员参与, STD - 标准化, BIQ - 质量控制,
XXX SLT - 现场物流, CI - 持续改进
日期:
编制:
第三部分 生产系统问题
XXX
PI
1 现场员工技能矩阵是否更新?
XXX
准化
STD标
2 车间是否有效实施分层审核?
XXX
3 工作现场5S是否符合标准要求?
XXX
4 过程控制计划是否及时更新并按照此计划进行控制?
XXX
诸次审核发现的问题所采取的纠正措施在现场是否有效实 XXX 5
施(问题报告编号: )
6 现场物料是否清晰标识,可疑品和不合格品是否隔离?
XXX
7 快速反映问题解决会议是否定期举行,所有记录是否更新?
XXX
BIQ质量控制
现场问题板上是否有足够的证据证据快速反应问题解决会
8 议按计划进行,并且所有发现的问题都有跟踪解决?
XXX
日期:
编制:
场物流
SLT现
CI持续改进
过程分层审核检查表

判定 N NG N/A
审核记录
8
作业环境适合生产要求(照明、抽风、空间等)
1
首检与样件一致,放置于首袋中,检验人员确认后生产人员放行
(2)产品质量/防错验证
2
防错样件,设施正常使用并在防错点检表中记录
设备零件无损伤,启动压力指数表正确无气液无泄漏,电器部件无铜丝外露,设
8
备外置部件固定安全可靠
特殊审核要求(具体内容参见生产线表格)
1
当班生产产品
工位
工位特殊要求
2
(6)所有层级必审项
3
4
5
6
7
8
9
不符合总数量
是否已制定行动计划
计划完成日期
备注:1、“Y”-没有发现差异;“N”-发现了差异;“NG”-发现了差异,审核期间立即进行了纠正;“N/A”不适用。 2、班组长者审核(1)至(3)部分;车间及以上管理人员审核(4)至(6)部分;
3
防错装置已验证并记录
4
不合格品/待确认品放置在相应的物料盒中并标识记录
5
生产现场岗位检查表有按照实际要求当班实施检查记录,并改善
6
产品样件,测试测量器具齐全,均在有效期内
(3)作业文件/作业?
当班的作业文件、警示牌都已经受控,返修作业指导书、临时文件有责任人签字
批 准:
1
并在有效期内
2
员工实际操作符合作业文件标准要求,并按要求自检、检验
3
设备保养与质量检查表按实际检查记录、异常问题及时上报记录
工位符合工艺设计要求标准,特殊产品工位人员按照要求佩戴静电手环、静电鞋
分层审核检查表样表

车间: 钢化预处理 生产线名称: 项目 序号 人员 资格 培训 1 2 3 4 标准 化 5 6 7 8 不合 格品 控制 9 10 11 12 13 14 质量 控制 点 15 16 17 18 19 20 1 内部 问题 关注 2 吸盘真空度在运行过程中漏气导致产品不合格; 班次: 日期: 检查人: 审核: 结果 内 容 第一部分:各生产线日常管理项目 员工是否有资格胜任其岗位,培训员工是否有相应的培训教师指导和监督其工作。(人 员上岗资格、培训情况) 新项目、新的作业指导书及更新的文件是否对员工进行培训,是否有培训记录? 各项记录是否填写,且真实、完整、规范?(车间首检、点检、不合格品记录、SPC) 是否进行了首件、末件检验并保留现场? 生产过程是否遵循了控制计划的各项要求?工艺参数设定是否符合规定? 产品的质量要求是否明确、是否能够获得且易于遵守?(缺陷样片和标准样片、质量要求) 现场标识是否规范?(物料、产品) 防错装置是否经过防错验证检查,且处于良好的工作状态? 不合格品是否被正确标识并放置在不合格区域或者红色料架上? 出现不合格品,是否及时记录并采取措施? 返工返修品是否有正确标识并存放在指定区域?返修后是否经检验、标识流入下道工序? 第二部分:本生产线重点关注项目和质量控制点 吸盘真空度是否达到参数设置要求。 磨轮质量是否达到要求,磨边质量是否符合要求;是否有斜边、烧焦、亮斑存在; 是否对孔径尺寸、钻孔质量进行确认。 针对边部磨边质量、亮斑等是否进行了整车检验; 切割样片的编号(包括本厂编号、零件号)与跟踪单要求是否一致; 尺寸检验是否符合要求; 。。。。。。
REV01(0804)
1 顾客投诉产品磨边不良; 外部 投诉 2
备注
班组长每班审核一次,车间主任每天抽查一个班次进行审核,厂长每周抽查一个班次进 行审核,各班组审核报表及时放置在各车间的相应栏目内;原工艺监督只需跟踪快速反 应中的问题关闭实施情况。
分层过程审核检查表
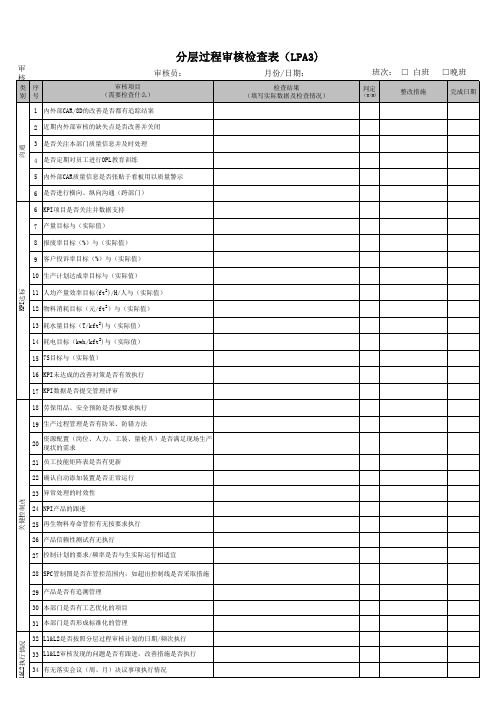
29 产品是否有追溯管理 30 本部门是否有工艺优化的项目 31 本部门是否形成标准化的管理 32 L1&L2是否按照分层过程审核计划的日期/频次执行 33 L1&L2审核发现的问题是否有跟进,改善措施是否执行 34 有无落实会议(周、月)决议事项执行情况
班次: □ 白班
判定
(Y/N)
整改措施
□晚班
L1&L2执行情况
审 核
类序 别号
分层过程审核检查表(LPA3)
审核员:
月份/日期:
审核项目况)
1 内外部CAR/8D的改善是否都有追踪结案
2 近期内外部审核的缺失点是否改善并关闭
3 是否关注本部门质量信息并及时处理
沟通
4 是否定期对员工进行OPL教育训练
5 内外部CAR质量信息是否张贴于看板用以质量警示
6 是否进行横向、纵向沟通(跨部门)
6 KPI项目是否关注并数据支持
7 产量目标与(实际值)
8 报废率目标(%)与(实际值)
9 客户投诉率目标(%)与(实际值)
10 生产计划达成率目标与(实际值)
KPI达标
11 人均产量效率目标(ft2)/H/人与(实际值)
20
资源配置(岗位、人力、工装、量检具)是否满足现场生产 现状的需求
21 员工技能矩阵表是否有更新
22 确认自动添加装置是否正常运行
23 异常处理的时效性
关健控制点
24 NPI产品的跟进
25 再生物料寿命管控有无按要求执行
26 产品信赖性测试有无执行
27 控制计划的要求/频率是否与生实际运行相适宜
28 SPC管制图是否在管控范围内,如超出控制线是否采取措施
12 物料消耗目标(元/ft2)与(实际值)
LPA生产车间分层审核检查表
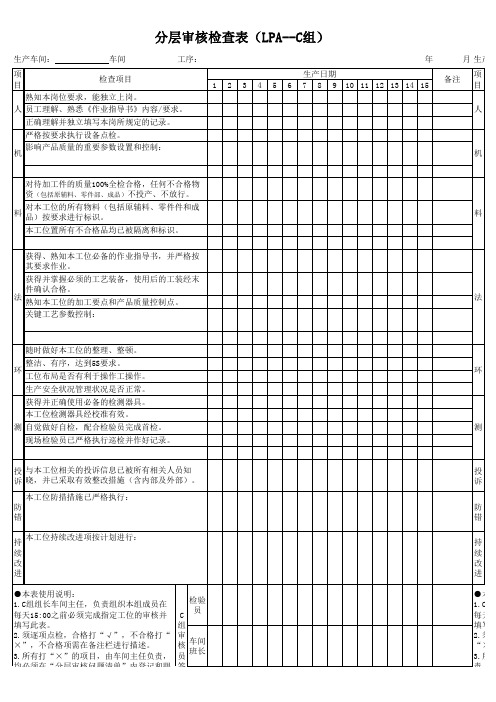
审 核 员
车间 班长
责,均必须在“分层审核问题清单”内登 签
记和跟踪。
字
4.本表由车间主任负责回收,并提交总经
办归档保存。
“×”,不合格项需在备注栏进行描述。 3.所有打“×”的项目,由车间主任负 责,均必须在“分层审核问题清单”内登 记和跟踪。 4.本表由车间主任负责回收,并提交总经 办归档保存。
审 核 员
车间 班长
均必须在“分层审核问题清单”内登记和跟 签
踪。
字
4.本表由车间主任负责回收,并提交总经办
归档保存。
环
测
投 诉
防 错
持 续 改 进
●本表 1.C组组 每天15 填写此 2.须逐 “×” 3.所有 责,均 记和跟 4.本表 办归档
×”,不合格项需在备注栏进行描述。
核
3.所有打“×”的项目,由车间主任负责, 员
备注
项 目
人
机
对待加工件的质量100%全检合格,任何不合格物 资(包括原辅料、零件部、成品)不投产、不放行。
对本工位的所有物料(包括原辅料、零件件和成
料 品)按要求进行标识。
料
本工位置所有不合格品均已被隔离和标识。
获得、熟知本工位必备的作业指导书,并严格按 其要求作业。
获得并掌握必须的工艺装备,使用后的工装经末
投 与本工位相关的投诉信息已被所有相关人员知 诉 晓,并已采取有效整改措施(含内部及外部)。
本工位防措措施已严格执行: 防 错
持 本工位持续改进项按计划进行: 续 改 进
●本表使用说明: 1.C组组长车间主任,负责组织本组成员在 每天15:00之前必须完成指定工位的审核并
检验 C员
填写此表。
组
分层审核检查表-机加工

2
设备工装
2.1 观察设备标识/生产状态标识/生产产品标识是否齐全,没有缺少;
2.2 机台是否有异常停机履历表,并按照要求进行填写及更新;
2.3 检查设备点检表是否按照要求填写,并随机抽取点检项目要求操作员口述点检操作,是否清晰了解;
问题简述
2.4 产品加工结束,要求暂停加工,检查机加工工装是否存在松动以及损坏;
审核结果 Y N C NG
1.2 观察员工作业手法,是否存在违规操作,导致的可能人身侵害;
1.3 设备上下料区域是否有明确的区域划分,并保持整体清爽;
1.4 对应工位是否具有5S检查标准,并能按照5S标准进行区域清洁和物品摆放整齐;
1.5 员工是否正确的穿戴了劳保用品,防噪耳塞以做安全防护;
1.6
待(已)生产物料放置于正确的容器或区域,加以标识产品名称/数量/批次,并保持整齐及无其他风险 (如跌落);
3.6 过程质量是否进行了过程巡检,巡检的结果是符合的,或者不符合被跟踪处理;
4
其他事项
4.1
工序是否建立物料检查标准,检查待生产物料,是否存在上工序明显缺陷流出,如未去隔皮,同时询问员工 是否会做检查;
4.2 观察员工作业,是否存在未经批准的返工返修动作,如对产品进行打磨;
4.3 观察员工作业,气枪清洁动作时长是否足以完全清洁加工底座铝屑;
2.5 产品加工结束,要求暂停加工,检查设备刀具寿命控制与工艺要求一致,且未超出管控寿命;
2.6 其他设备参数与工艺要求保持一致且未超出管控要求,如切削液浓度/主轴转速/进给倍率等;
2.7 工位是否具有设备维护作业指导书及维护作业记录,相关记录填写完整;
3
过程监控
生产工位是否具有相对应的标准作业指导书/质量作业标准,且文件是受控下发的,随机抽取要求项目询 3.1 问操作员是否理解;
分层审核检查表(一)
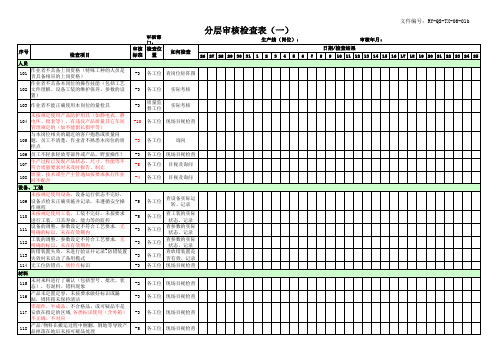
132
样件未进行管理,无台账,标识不清晰,超 过有效期
133
标样件不能在作业现场得到正确使用(包括 目视图片),未进行样件验证
134
出现不良时未填写制程异常情况报告且在10 分钟内通知巡检
135
半成品、成品未经检验流入下工序,检验记 录不认真、未记或不标识
136
生产过程中错装、漏装,下工序发现上工序 不良品
126
返工/返修未按作业指导书进行,返工/返修 后的产品或零件无合适的标识和确认
127
生产首件提交后检验不合格,成品抽检不合 格
128
首件提交不合格再次调整工艺参数后提交仍 不合格,首检未通过开始批量生产
129
未按要求执行了首末件检验,未做好相关记 录
130 首末件品未按规定标识、放置
131
未按工艺要求的频率、抽样数进行检验并记 录
-5
各工位
查工装的实际 状态、记录
111
设备的调整、参数设定不符合工艺要求,无 明确的标识,未在有效期内
-3
各工位
查参数的实际 状态、记录
112
工装的调整、参数设定不符合工艺要求,无 明确的标识,未在有效期内
-3
各工位
查参数的实际 状态、记录
113
防错装置失效,未进行验证并记录?防错装置 失效时未启动了备用模式
-5 各工位 目视及询问
108
质量、技术或生产主管通知按要求执行作业 时不配合
-4 各工位 目视及询问
设备、工装
未按规定使用设备,设备运行状态不完好, 109 设备点检未正确实施并记录,未遵循安全操
作规程
-5
各工位
查设备实际运 转、记录
110
分层审核检查表 生产
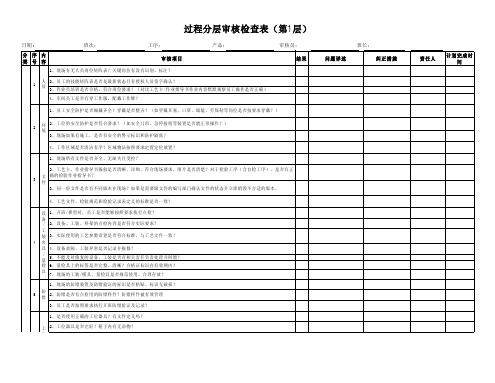
一 、 工 位 问 题
7
材 3 、 自 制 件 是否有标识( 流转 卡)? 填 写 是否正确? 料 4 、 来料包 装是否无 破损 、符合要求? 5 、 线边库存被 有 效管理了吗 ?标识是否 清晰 , 产 品 是否有防护 6 、 多余 物 料 是否按 照 要求 登 记并执行 退库 处 理 ? 记录 是否 完 整? 1 、正 在使用 的 测量 装置( 量具 、 检 具 )是否是 检验 指导书 或 控 制计划中 指 定 的 测量 装置? 2 、是否正确 执行 了首 、 末 件及 过程 检验 ? 不 符合 项 是否按 照 反应计划 正确 处 理 ? 3 、 首 件 是否保 留 在 现场?且按 照 要求 进 行 标识? 4 、对 于需 要 进 行 外 观 检 查 的 产 品 ,有无 明 确的 目视化 的 可接收 标 准 ? 5 、员工是否能 依据外 观标 准 作 出了 正确的 判断 ?正确识别 OK 与 NOK 件 过 程 6 、现场 张贴 不 合格 品处 置 流程吗 ? 控 制 7 、 不 合格 品记录 是否 完 整 清晰 ? 8 、 检验 后 不 合格 品 是否 及时 被 隔离 以 防 止混 用 ? 9 、 看板信息 是否 及时 更 新且有 效 ? 10 、 当 班 生产过程 是否有 变 化 点 ? 变更信息 是否有 效 传递 ?(人员、 材料 、工装、工艺、 测量 等 变 化 ) 11 、 零 件 是否 粘贴 正确标识? 12 、 生产 节拍 是否 平衡 ? 1 、现场是否有 受控 的 换 模 指导书?
过程分层审核检查表(第 1 层)
日期 : 分 序 内 类 号 容 班 次: 工序: 审核项目
1 、现场有无人员岗位矩阵表?关键岗位有没有识别、标注? 1 人 2 、员工的技能矩阵表是否是最新状态且有授权人员签字确认? 员 3 、作业员培训是否合格,符合岗位要求?(对比工艺卡 / 作业指导书作业内容默默观察员工操作是否正确) 4 、车间员工是否有穿工作服,配戴工作牌? 1 、员工安全防护是否佩戴齐全?穿戴是否整齐?(如穿戴耳塞、口罩、眼镜、劳保鞋等岗位是否按要求穿戴?) 环 2 、工位的安全防护是否符合要求?(如安全门帘、急停按钮等装置是否能正 常 操作?) 境 3 、现场如 果 有 施 工,是否有安全的 警示 标识 和 防护 隔离 ? 4 、工作 区域 是否 清洁 有 序 ? 区域物品 按 照 要求 定 置 定 位 放 置? 1 、现场 所 有 文件 是否齐全、无 缺失 且 受控 ? 2 、工艺卡、作业指导书 描叙 是否 清晰 、 详细 、符合现场要求, 图片 是否 清楚 ?对 于检验 工 序 ( 含自检 工 序 ),是否有正 文 确的 检验 作业指导书? 件 3 、 同一份文件 是否有 不同版本在 现场?如 果 是 需 要 跟文件 的 编写部 门确认 文件 的状态 并立即销毁不 合 适 的 版本。 4 、工艺 文件 、 检验规范和检验记录 表 定义 的标 准 是否 一致 ? 设 备 / 工 装 夹 具 / 量 检 具 1 、 开班 / 换型时 ,员工是否能 够 按 照 要求 执行点检 ? 2 、 设备 、工装、 样架 的 点检 内容是否符合 实际 要求? 3 、 实际使用 的工艺 参数设 置是否符合标 准 , 与 工艺 文件一致 ? 4 、 设备故障 、工装 异常 是否 记录并报修 ? 5 、 不 能 及时修复 的 设备 、工装是否有 相 关 责任负责处 理 并 回馈 ? 6 、 量 检 具上 的标签是否 完 整、 清晰 ?合格 证 标识 在 有 效期 内? 7 、现场的工装 / 模具 、 量 检 具 是否 规范使用 ,合 理存 放 ? 1 、现场的防 错 装置 及 防 错 验 证 的标识是否 粘贴 、标识无 破损 ? 5 防 2 、防 错 是否有 点检用 的防 错 样件 ?防 错 样件 被 有 效管理 错 3 、员工是否按 照 要求 执行开班 防 错 验 证 及记录 ? 1 、是否 使用 正确的工位 器具 ?有 文件定义 吗 ? 工 2 、工位 器具 是否 完好 ? 箱子 内有无 杂 物 ? 位
车间分层审核检查表
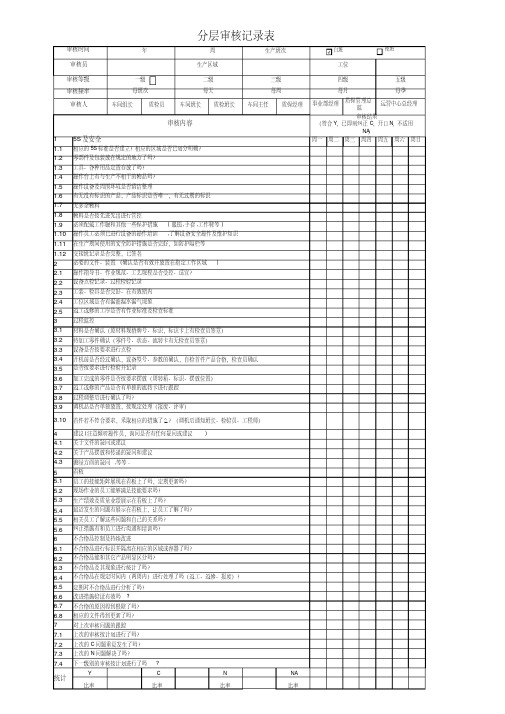
年周车间组长质检员车间班长质检班长车间主任质保经理1周一周二周三周四周五周六周日1.11.21.31.41.51.61.71.81.91.101.111.1222.12.22.32.42.533.13.23.33.43.53.63.73.83.93.1044.14.24.355.15.25.35.45.55.666.16.26.36.46.56.66.76.877.17.27.37.4Y C N NA 比率比率比率比率下一级别的审核按计划进行了吗?统计不合格的原因得到根除了吗?相应的文件得到更新了吗?对上次审核问题的跟踪上次的审核按计划进行了吗?上次的C 问题重复发生了吗?上次的N 问题解决了吗?不合格品进行标识并隔离在相应的区域或容器了吗?不合格品能和其它产品明显区分吗?不合格品及其现象进行统计了吗?不合格品在规定时间内(两周内)进行处理了吗(返工、返修、报废)?定期对不合格品进行分析了吗?改进措施验证有效吗?现场作业的员工能够满足技能要求吗?生产绩效及质量业绩展示在看板上了吗?最近发生的问题有展示在看板上,让员工了解了吗?相关员工了解这些问题和自己的关系吗?纠正措施有和员工进行沟通和培训吗?不合格品控制及持续改进建议(注意倾听操作员,询问是否有任何疑问或建议)关于文件的疑问或建议关于产品摆放和传递的疑问和建议测量方面的疑问,等等.看板员工的技能矩阵展现在看板上了吗,定期更新吗?是否按要求进行检验并记录加工完成的零件是否按要求摆放(周转箱、标识、摆放位置)返工返修的产品是否有单独的流转卡进行跟踪过程调整后进行确认了吗?调机品是否单独放置,按规定处理(报废、评审)首件若不符合要求,采取相应的措施了么?(调机后通知班长、检验员、工程师)返工返修的工序是否有作业标准及检查标准过程监控材料是否确认(原材料规格牌号、标识,标识卡上有检查员签章)待加工零件确认(零件号、状态、流转卡有无检查员签章)设备是否按要求进行点检开机前是否经过确认,设备型号、参数的确认,自检首件产品合格,检查员确认交接班记录是否完整,已签名必要的文件、装置(确认是否有效并放置在指定工作区域)操作指导书、作业规范、工艺规程是否受控、适宜?设备点检记录、过程检验记录工装、检具是否完好、在有效期内工位区域是否有漏油漏水漏气现象有无没有标识的产品,产品标识是否唯一,有无过期的标识无多余物料物料是否按先进先出进行管控必须配戴工作服和其他一些保护措施( 眼镜,手套,工作鞋等)操作员工必须已进行设备的操作培训,了解设备安全操作及维护知识在生产期间使用的安全防护措施是否完好,如防护隔栏等5S 及安全相应的5S 标准是否建立?相应的区域是否已划分明确?零部件及包装放在规定的地方了吗?工具、各种用品定置存放了吗?操作台上有与生产不相干的物品吗?操作设备及周围环境是否清洁整理审核人事业部经理质保管理总监运营中心总经理审核内容审核结果(符合Y ,已即刻纠正C ,开口N ,不适用NA )审核频率每班次每天每周每月每季审核等级一级二级三级四级五级分层审核记录表审核时间生产班次审核员生产区域工位夜班白班。
分层审核检查表可编辑全文
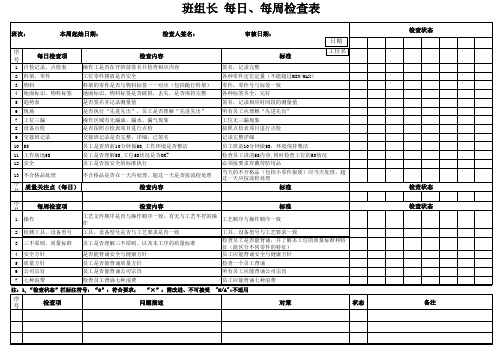
班次:
本周起始日期:
检查人签名:
序 号
每日检查项
1 自检记录、点检表
2 料架、零件
3 物料
4 地面标识、物料标签
5 趋势表
6 现场
7 工位三漏
8 设备点检
9 交接班记录
10 5S
11 工作场地5S
12 安全
检查内容
操作工是否在开班前签名并检查相应内容 工位零件摆放是否安全 料架的零件是否与物料标签一一对应(包括随行料架) 地面标识、物料标签是否破损,丢失,是否保持完整 是否签名并记录测量值 是否执行“先进先出”,员工是否理解“先进先出” 操作区域有无漏油、漏水、漏气现象 是否按照点检表项目进行点检 交接班记录是否完整、详细,已签名 员工是否班前10分钟做5S,工作环境是否整洁 员工是否理解5S,工位5S状况是否OK? 员工是否按安全的标准执行
13 不合格品处理
不合格品是否在一天内处理,超过一天是否按流程处理
序 号
质量关注点(每日)
检查内容
审核日期: 标准
日期 工位名
签名,记录完整 各种零件定位定量(不能超过MIN/MAX) 零件,零件号与标签一致 各种标签齐全,完好 签名,记录相应时间段的测量值 所有员工应理解“先进先出” 工位无三漏现象 按照点检表项目进行点检 记录完整详细 员工班前10分钟做5S,环境保持整洁 检查员工讲清5S内容,同时检查工位的5S情况 必须按要求穿戴劳防用品 当天的不合格品(包括小零件报废)应当天处理,超 过一天应按流程处理
备注Biblioteka 5 质量方针员工是否能背诵质量方针
检查一个员工背诵
6 公司宗旨
员工是否能背诵公司宗旨
所有员工应能背诵公司宗旨
过程分层审核-制造过程(一级)

生产车间(生产线):
审 审核员:班组长/技术员/车间主任 核
类别
序 号
检查项目
检查范围
如何检查
审核结果
周周周周周周 一二三四五六
作业者是否具备本岗位的操作技能(包括工艺文件 1 理解、设备工装的维护保养、参数的设置等)?特 抽查
殊工种的人员是否具备相应的上岗资格
6
本工位是否有与工位生产产品不相关或状态不明的 物料?
100%检查 100%检查
现场目视检查 现场目视检查
7
塑胶粒子是否按标准烘烤,烘烤的温度和时间是否 有记录确认?
100%检查
现场目视检查
8
本工位使用的模具/工装、设备是否与作业文件要求 一致?
100%检查
现场目视检查
设备运行状态是否完好,设备点检是否正确实施并
100%检查 现场目视检查
环境
20
现场环境是否符合6S要求?工位附近是否有与工作 无关的零件、工装等其它物品?
/安
全
21
工位照明是否正常,并满足强度要求,以便于操作 工进行外观目视自检?
100%检查 100%检查
现场目视检查 现场目视检查
注: 审核
执行审核员:
车间负责人:
审核问题记录
现场已整改问题
第 2 页,共 2 页
查上岗证、培训记 录、员工技能矩阵 图等;实际考核
审核问题记录
人员 2 操作员工是否知道如何使用紧急停机按钮?戴劳保防护用品( 眼镜、手套 、工作鞋、防护服、耳塞、防护面罩等)?
100%检查
现场目视检查
4 材料在生产区域是否定置摆放?
100%检查 现场目视检查
焊接车间过程分层审核检查表
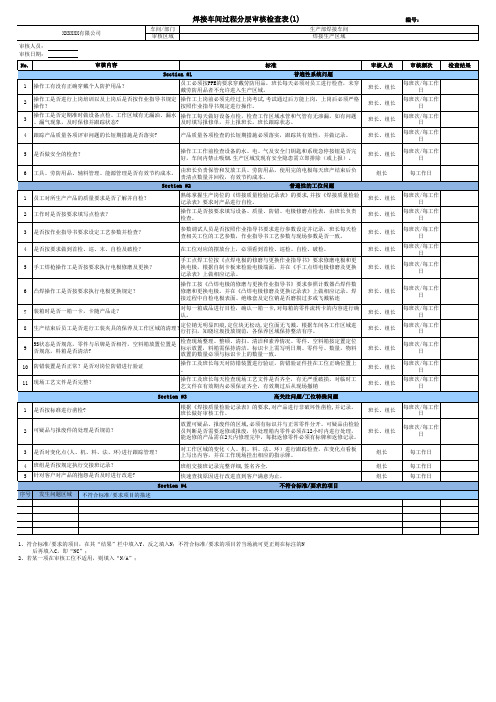
2
操作工是否进行上岗培训以及上岗后是否按作业指导书规定 操作工上岗前必须先经过上岗考试,考试通过后方能上岗,上岗后必须严格
操作?
按照作业指导书规定进行操作。
3
操作工是否定期准时做设备点检、工作区域有无漏油、漏水 操作工每天做好设备点检,检查工作区域水管和气管有无渗漏,如有问题
、漏气现象,及时保修并跟踪状态?
每班次/每工作 日
每班次/每工作 日
班长、组长
每班次/每工作 日
班长、组长 班长、组长
每班次/每工作 日
每班次/每工作 日
班长、组长
每班次/每工作 日
班长、组长
每班次/每工作 日
组长
组长 组长
每工作日
每工作日 每工作日
检查结果
1、符合标准/要求的项目,在其“结果”栏中填入Y,反之填入N;不符合标准/要求的项目若当场就可更正则在标注的N 后再填入C,即“NC”;
2 工作时是否按要求填写点检表?
操作工是否按要求填写设备、质量、防错、电极修磨点检表,由班长负责 检查。
3 是否按作业指导书要求设定工艺参数并检查?
参数调试人员是否按照作业指导书要求进行参数设定并记录,班长每天检 查相关工位的工艺参数,作业指导书工艺参数与现场参数是否一致。
4 是否按要求做到首检、巡、末、自检及破检?
及时填写报修单,并上报班长,班长跟踪状态。
4 跟踪产品质量各项评审问题的长短期措施是否落实?
产品质量各项检查的长短期措施必须落实,跟踪其有效性,并做记录。
5 是否做安全的检查?
操作工工作前检查设备的水、电、气及安全门钥匙和系统急停按钮是否完 好,车间内禁止吸烟.生产区域发现有安全隐患需立即排除(或上报)。
- 1、下载文档前请自行甄别文档内容的完整性,平台不提供额外的编辑、内容补充、找答案等附加服务。
- 2、"仅部分预览"的文档,不可在线预览部分如存在完整性等问题,可反馈申请退款(可完整预览的文档不适用该条件!)。
- 3、如文档侵犯您的权益,请联系客服反馈,我们会尽快为您处理(人工客服工作时间:9:00-18:30)。
每班次/每工作 日
12 凸焊操作工是否按要求执行电极更换规定?
每班次/每工作 日
13 装箱时是否一箱一卡,卡随产品走?
对每一箱成品进行目检,确认一箱一卡,对每箱的零件流转卡的内容进行确 每班次/每工作 认。 日
定位销无明显凹痕,定位块无松动,定位面无飞溅。根据车间各工作区域进 14 生产结束后员工是否进行工装夹具的保养及工作区域的清理? 行打扫,知晓垃圾投放规范,各保养区域保持整洁有序。 检查现场整理、整顿、清扫、清洁和素养情况。零件、空料箱按定置定位 5S状态是否规范,零件与吊牌是否相符,空料箱放置位置是 标示放置,料箱需保持清洁。标识卡上需写明日期、零件号、数量,物料 否规范,料箱是否清洁? 放置的数量必须与标识卡上的数量一致。 操作工及班长每天对防错装置进行验证,防错验证件挂在工位正确位置上 。
3
每班次/每工作 日
4
跟踪产品质量各项评审问题的长短期措施是否落实?
产品质量各项检查的长短期措施必须落实,跟踪其有效性,并做记录。
每班次/每工作 日
5
是否做安全的检查?
操作工工作前检查设备的水、电、气和系统急停按钮是否完好,车间内禁 止吸烟.生产区域发现有安全隐患需立即排除(或上报)。
每班次/每工作 日
每班次/每工作 日
15
每班次/每工作 日
16 防错装置是否正常?是否对岗位防错进行验证
每班次/每工作 日
17 现场工艺文件是否完整?
操作工及班长每天检查现场工艺文件是否齐全,有无严重破损,对临时工 艺文件在有效期内必须保证齐全,有效期过后从现场撤销
每班次/每工作 日
18 是否按标准进行凿检?
根据《焊接质量检验记录表》的要求,对产品进行非破坏性凿检,并记录。 班长做好审核工作。
8
工作时是否按要求填写点检表?
操作工是否按要求填写设备、质量、防错、电极修磨点检表,由班长负责 检查。
每班次/每工作 日
9
是否按作业指导书要求设定工艺参数并检查?
参数调试人员是否按照作业指导书要求进行参数设定并记录,班长每天检 查相关工位的工艺参数,作业指导书工艺参数与现场参数是否一致。
每班次/每工作 日
制造部过程分层审核检查表
No. 1 审核内容 操作工有没有正确穿戴个人防护用品? 标准 员工必须按安全的要求穿戴劳防用品,班长每天必须对员工进行检查,未 穿戴劳防用品者不允许进入生产区域。 审核频次 每班次/每工作 日 1号 2号 3号 4号 5号 6号 7号 8号 9号 10号 11号 12号 13号 14号 15号 16号
每班次/每工作 日
19 可疑品与报废件的处理是否规范?
放置可疑品、报废件的区域,必须有标识并与正常零件分开。可疑品由检验 每班次/每工作 员判断是否需要返修或报废,待处理箱内零件必须在12小时内进行处理, 日 能返修的产品需在2天内修理完毕,每批返修零件必须有标牌和返修记录。 对工作区域的变化(人、机、料、法、环)进行跟踪检查,在变化点看板 上写出内容,并在工作现场挂出相应的指示牌。
每工作日 不符合标准/要求项目的描述
1、符合标准/要求的项目,在其“结果”栏中填入Y,反之填入N;不符合标准/要求的项目若当场就可更正则在标注的N 后再填入C,即“NC”; 2、若某一项在审核工位不适用,则填入“N/A”;
20 是否对变化点(人、机、料、法、环)进行跟踪管理?
每工作日
21 班组是否按规定执行交接班记录?
班组交接班记录完整详细,签名齐全.
每工作日
22 针对客户对产品的抱怨是否及时进行改进?
快速查找原因进行改进直到客户满意为止。
每工作日
23 S11拖曳臂生产时是否跟踪? 序号 发生问题区域
按时抽查,入库前检查,针对问题开班前教育员工,检查员工是否自查
10 是否按要求做到首检、巡、末、自检?
在工位对应的摆放台上,必须看到首检、巡检、自检。
每班次/每工作 日
11 悬挂点焊操作工是否按要求执行电极修磨及更换?
悬挂点焊工位按《作业指导书》要求修磨电极和更换电极。并在《电极修 磨及更换记录表》上做相应记录。 操作工按《凸焊电极的修磨与更换作业指导书》要求参照计数器凸焊件数 修磨和更换电极。并在《凸焊电极修磨及更换记录表》上做相应记录。焊 接过程中自检电极表面、绝缘套及定位销是否磨损过多或飞溅粘连
6
工具、劳防用品、辅料管理、能源管理是否有效节约成本。 由班长负责保管和发放工具、劳防用品,使用完的电极每天班产结束后负 责清点数量并回收,有效节约成本。
每工作日
7
员工对ቤተ መጻሕፍቲ ባይዱ生产产品的质量要求是否了解并自检?
熟练掌握生产岗位的《焊接质量检验记录表》的要求,并按《焊接质量检验 每班次/每工作 记录表》要求对产品进行自检。 日
2
操作工是否进行上岗培训以及上岗后是否按作业指导书规定 操作工上岗前必须先经过上岗考试,考试通过后方能上岗,上岗后必须严格 每班次/每工作 操作? 按照作业指导书规定进行操作。 日 操作工是否定期准时做设备点检、工作区域有无漏油、漏水 操作工每天做好设备点检,检查工作区域水管和气管有无渗漏,如有问题 、漏气现象,及时保修并跟踪状态? 及时填写报修单,并上报班长,班长跟踪状态。