有关硅钼球铁的一些问题_李传拭
球墨铸铁常见缺陷的分析与对策
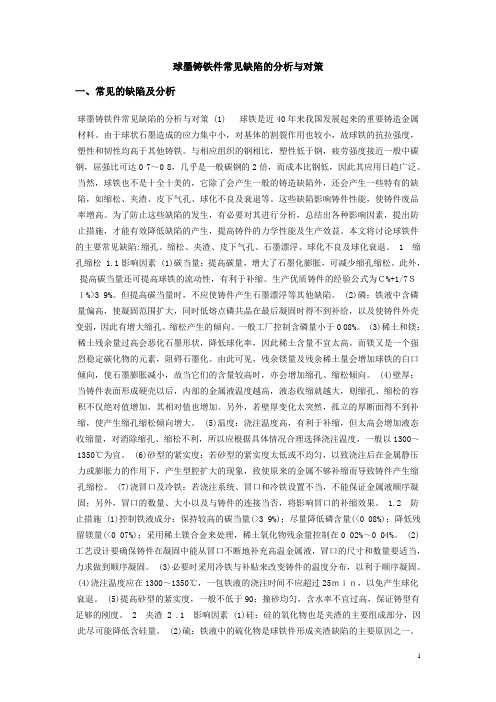
球墨铸铁件常见缺陷的分析与对策一、常见的缺陷及分析球墨铸铁件常见缺陷的分析与对策 (1) 球铁是近40年来我国发展起来的重要铸造金属材料。
由于球状石墨造成的应力集中小,对基体的割裂作用也较小,故球铁的抗拉强度,塑性和韧性均高于其他铸铁。
与相应组织的钢相比,塑性低于钢,疲劳强度接近一般中碳钢,屈强比可达0 7~0 8,几乎是一般碳钢的2倍,而成本比钢低,因此其应用日趋广泛。
当然,球铁也不是十全十美的,它除了会产生一般的铸造缺陷外,还会产生一些特有的缺陷,如缩松、夹渣、皮下气孔、球化不良及衰退等。
这些缺陷影响铸件性能,使铸件废品率增高。
为了防止这些缺陷的发生,有必要对其进行分析,总结出各种影响因素,提出防止措施,才能有效降低缺陷的产生,提高铸件的力学性能及生产效益。
本文将讨论球铁件的主要常见缺陷:缩孔、缩松、夹渣、皮下气孔、石墨漂浮、球化不良及球化衰退。
1 缩孔缩松 1.1影响因素 (1)碳当量:提高碳量,增大了石墨化膨胀,可减少缩孔缩松。
此外,提高碳当量还可提高球铁的流动性,有利于补缩。
生产优质铸件的经验公式为C%+1/7Si%>3 9%。
但提高碳当量时,不应使铸件产生石墨漂浮等其他缺陷。
(2)磷:铁液中含磷量偏高,使凝固范围扩大,同时低熔点磷共晶在最后凝固时得不到补给,以及使铸件外壳变弱,因此有增大缩孔、缩松产生的倾向。
一般工厂控制含磷量小于0 08%。
(3)稀土和镁:稀土残余量过高会恶化石墨形状,降低球化率,因此稀土含量不宜太高。
而镁又是一个强烈稳定碳化物的元素,阻碍石墨化。
由此可见,残余镁量及残余稀土量会增加球铁的白口倾向,使石墨膨胀减小,故当它们的含量较高时,亦会增加缩孔、缩松倾向。
(4)壁厚:当铸件表面形成硬壳以后,内部的金属液温度越高,液态收缩就越大,则缩孔、缩松的容积不仅绝对值增加,其相对值也增加。
另外,若壁厚变化太突然,孤立的厚断面得不到补缩,使产生缩孔缩松倾向增大。
球铁及其球化不良问题探讨分析
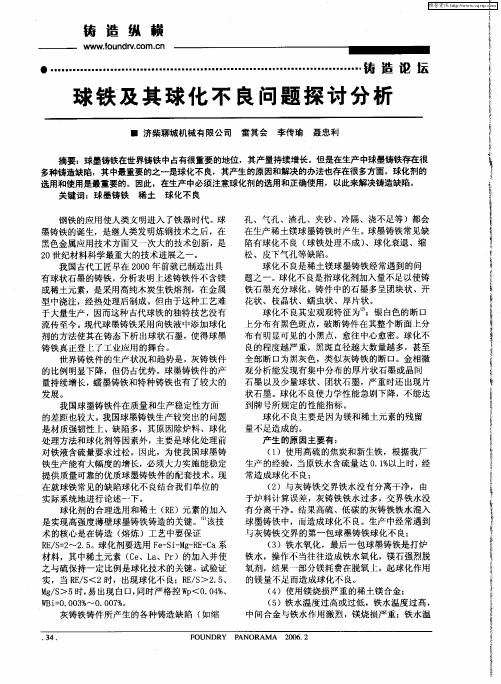
铸 造 纵 横
WWW. f o u n d r v . c o r r 1 . c n
・………………………………………………………………………” 铸 造 论
球 铁 及 其 球 化 不 良 问 题 探 讨 分 析
● 济柴聊城机械有限公司 雷其会 李传瑜 聂忠利 摘要:球墨铸铁在世界铸铁 中占有很重要的地位,其产量持续增长 。但是在生产 中 球墨铸铁存在很 多种铸造缺陷,其中最重要的之一是球化不良,其产生的原因和解决的办法也存在很多方面。球化剂的 选用和使用是最重要的。因此,在生产中必须注意球化剂的选用和正确使用,以此来解决铸造缺陷。 关键词:球墨铸铁 稀土 球化不良 钢铁的应用使人类文明进入了铁器时代 。 球 墨铸铁的诞生,是继人类发明炼钢技术之后 ,在 黑色金属应用技术方面又一次大的技术创新,是 2 O 世纪材料科学最重大的技术进展之一。 我 国古代 工 匠早在 2 0 0 0年 前 就 已制造 出具 有球状石墨的铸铁, 分析表明上述铸铁件不含镁 或稀 土元 素 ,是采 用 高纯木炭 生铁 熔 剂 ,在 金 属 型中浇注 ,经热处理后制成。但 由于这种工艺难 于大量生产,因而这种古代球铁的独特技艺没有 流传 至今 。现代球 墨铸 铁采 用 向铁液 中添 加球 化 剂的方法使其在铸态下析出球状石墨, 使得球 墨 铸 铁真 正登上 了工业应用 的舞 台 。 世 界铸铁 件 的生产 状况和 趋 势是 ,灰 铸铁 件 的 比例 明显 下 降,但 仍 占优 势 。球 墨铸铁 件 的产 量持续增长, 蠕墨铸铁和特种铸铁也有了较大的
参考 文献 : ( 1 )稀 土在 球墨 铸铁 中的应 用 中华铸造 网 ( 2 )王君卿等 铸造工艺 机械工业出版社
半 固 态 金 属 成 形 技 术 的研 究 及 应 用
有关Si-Mo球墨铸铁的一些问题

t o t h e h e a t . r e s i s t a n t n o d u l a r i r o n . A S i . Mn n o d u l a r i r o n h a s b e c o me c o mm o n l y u s e d c a s t a l l o y i n t h e
提 高S i 4 球铁的抗蠕变强度和断裂强度。碳和碳 当量 、锰 、磷 、硫等也对s i - M n 球铁 的性能有一定 的影响。为此 ,对于s i - M n  ̄ ,其碳 当量应略 大于常规球铁 ,锰含量一般 不超过 0 . 4 %~0 . 5 %, 磷含量应低于 0 . 0 5 %,硫含Байду номын сангаас控制在 0 . 0 1 O %~0 . 0 1 5 %。此外 ,还论述 了s i - M n 球铁在化学成分 和力学性 能要 求等方面的标准,以及熔炼、炉前处理 、铸件收缩缺 陷的预防、冷 隔及其预防、厚 壁铸件 中的碎块状石墨、铸件的热处理等生产工艺问题 。 关键词 :球 墨铸铁 ;石 墨化 ;铁素体;珠 光体 ; 固溶强化
wh i l e s i l i c o n c o n t e n t i s i n c r e a s e d a s ma l 1 a mo u n t o f mo l y b d e n u m( p r e f e r a b l y 0 . 5 t o 1 . 0 % a l s o i S a d d e d
中硅钼耐热球墨铸铁模具寿命试验
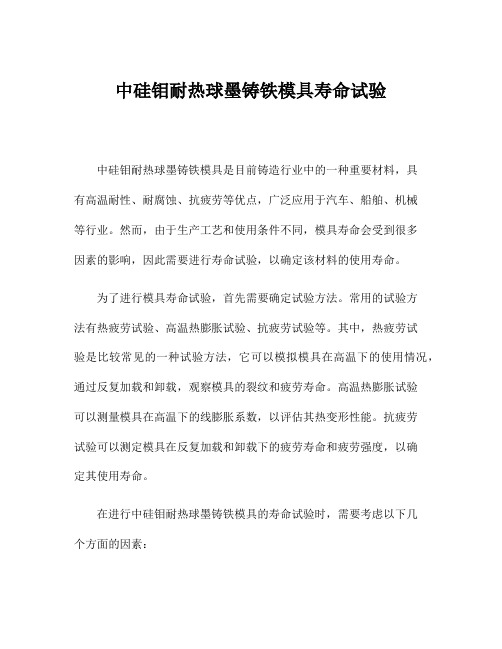
中硅钼耐热球墨铸铁模具寿命试验中硅钼耐热球墨铸铁模具是目前铸造行业中的一种重要材料,具有高温耐性、耐腐蚀、抗疲劳等优点,广泛应用于汽车、船舶、机械等行业。
然而,由于生产工艺和使用条件不同,模具寿命会受到很多因素的影响,因此需要进行寿命试验,以确定该材料的使用寿命。
为了进行模具寿命试验,首先需要确定试验方法。
常用的试验方法有热疲劳试验、高温热膨胀试验、抗疲劳试验等。
其中,热疲劳试验是比较常见的一种试验方法,它可以模拟模具在高温下的使用情况,通过反复加载和卸载,观察模具的裂纹和疲劳寿命。
高温热膨胀试验可以测量模具在高温下的线膨胀系数,以评估其热变形性能。
抗疲劳试验可以测定模具在反复加载和卸载下的疲劳寿命和疲劳强度,以确定其使用寿命。
在进行中硅钼耐热球墨铸铁模具的寿命试验时,需要考虑以下几个方面的因素:1.试验温度:中硅钼耐热球墨铸铁在高温下的性能比较优秀,但是其性能也会随着温度的升高而下降。
因此,试验应该在能够满足使用条件的温度范围内进行,一般在1000℃-1200℃之间。
2.试验载荷:试验载荷是对模具的一种负载,也是对模具寿命试验的重要参数之一。
载荷过大容易导致模具疲劳损伤,载荷过小又难以模拟实际使用情况。
因此,试验载荷应该根据模具的实际使用情况和经验选定。
3.试验次数:不同的模具寿命试验需要进行不同的试验次数。
一般来说,在试验过程中需要不断观察模具的状态,如果发现模具有裂纹或明显的疲劳现象,需要立即停止试验。
试验次数应该足够大,以确定模具的寿命。
4.试验样本:试验样本的制备和选择也是模具寿命试验的一个重要环节。
通常情况下,试验样本的制备需要考虑试验温度和试验载荷,并根据实际情况和经验制备。
选择试验样本需要考虑模具的整体结构和使用情况。
通过上述因素的综合考虑,进行中硅钼耐热球墨铸铁模具寿命试验,可以得到比较准确的结果,以评估该材料的使用寿命。
但是需要注意的是,试验结果只能作为参考,具体的使用情况还需要考虑其他因素的影响。
球铁常见缺陷及特征
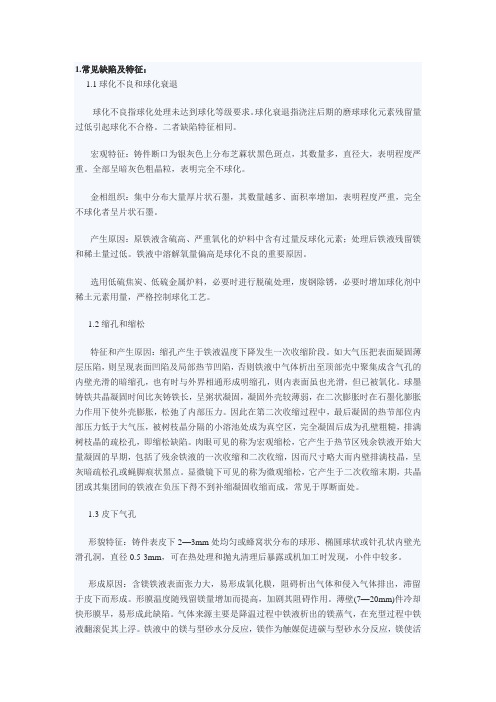
1.常见缺陷及特征:1.1球化不良和球化衰退球化不良指球化处理未达到球化等级要求。
球化衰退指浇注后期的磨球球化元素残留量过低引起球化不合格。
二者缺陷特征相同。
宏观特征:铸件断口为银灰色上分布芝蔴状黑色斑点,其数量多,直径大,表明程度严重。
全部呈暗灰色粗晶粒,表明完全不球化。
金相组织:集中分布大量厚片状石墨,其数量越多、面积率增加,表明程度严重,完全不球化者呈片状石墨。
产生原因:原铁液含硫高、严重氧化的炉料中含有过量反球化元素;处理后铁液残留镁和稀土量过低。
铁液中溶解氧量偏高是球化不良的重要原因。
选用低硫焦炭、低硫金属炉料,必要时进行脱硫处理,废钢除锈,必要时增加球化剂中稀土元素用量,严格控制球化工艺。
1.2缩孔和缩松特征和产生原因:缩孔产生于铁液温度下降发生一次收缩阶段。
如大气压把表面疑固薄层压陷,则呈现表面凹陷及局部热节凹陷,否则铁液中气体析出至顶部壳中聚集成含气孔的内壁光滑的暗缩孔,也有时与外界相通形成明缩孔,则内表面虽也光滑,但已被氧化。
球墨铸铁共晶凝固时间比灰铸铁长,呈粥状凝固,凝固外壳较薄弱,在二次膨胀时在石墨化膨胀力作用下使外壳膨胀,松弛了内部压力。
因此在第二次收缩过程中,最后凝固的热节部位内部压力低于大气压,被树枝晶分隔的小溶池处成为真空区,完全凝固后成为孔壁粗糙,排满树枝晶的疏松孔,即缩松缺陷。
肉眼可见的称为宏观缩松,它产生于热节区残余铁液开始大量凝固的早期,包括了残余铁液的一次收缩和二次收缩,因而尺寸略大而内壁排满枝晶,呈灰暗疏松孔或蝇脚痕状黑点。
显微镜下可见的称为微观缩松,它产生于二次收缩末期,共晶团或其集团间的铁液在负压下得不到补缩凝固收缩而成,常见于厚断面处。
1.3皮下气孔形貌特征:铸件表皮下2—3mm处均匀或蜂窝状分布的球形、椭圆球状或针孔状内壁光滑孔洞,直径0.5-3mm,可在热处理和抛丸清理后暴露或机加工时发现,小件中较多。
形成原因:含镁铁液表面张力大,易形成氧化膜,阻碍析出气体和侵入气体排出,滞留于皮下而形成。
球墨铸铁生产的难点与要点
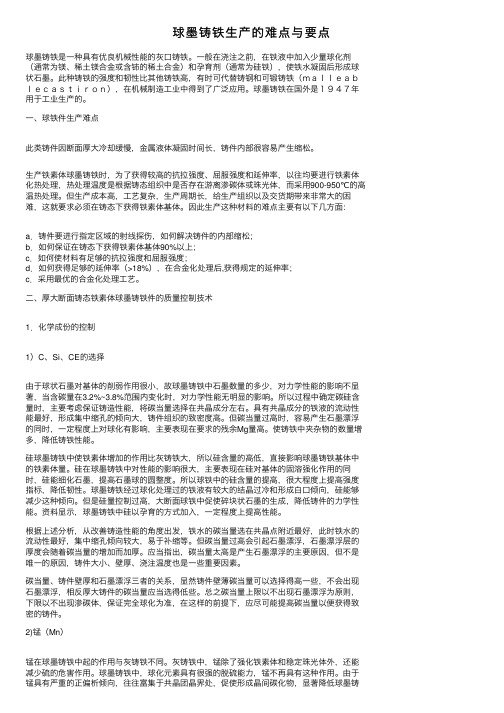
球墨铸铁⽣产的难点与要点球墨铸铁是⼀种具有优良机械性能的灰⼝铸铁。
⼀般在浇注之前,在铁液中加⼊少量球化剂(通常为镁、稀⼟镁合⾦或含铈的稀⼟合⾦)和孕育剂(通常为硅铁),使铁⽔凝固后形成球状⽯墨。
此种铸铁的强度和韧性⽐其他铸铁⾼,有时可代替铸钢和可锻铸铁(malleablecastiron),在机械制造⼯业中得到了⼴泛应⽤。
球墨铸铁在国外是1947年⽤于⼯业⽣产的。
⼀、球铁件⽣产难点此类铸件因断⾯厚⼤冷却缓慢,⾦属液体凝固时间长,铸件内部很容易产⽣缩松。
⽣产铁素体球墨铸铁时,为了获得较⾼的抗拉强度、屈服强度和延伸率,以往均要进⾏铁素体化热处理,热处理温度是根据铸态组织中是否存在游离渗碳体或珠光体,⽽采⽤900-950℃的⾼温热处理。
但⽣产成本⾼,⼯艺复杂,⽣产周期长,给⽣产组织以及交货期带来⾮常⼤的困难,这就要求必须在铸态下获得铁素体基体。
因此⽣产这种材料的难点主要有以下⼏⽅⾯:a.铸件要进⾏指定区域的射线探伤,如何解决铸件的内部缩松;b.如何保证在铸态下获得铁素体基体90%以上;c.如何使材料有⾜够的抗拉强度和屈服强度;d.如何获得⾜够的延伸率(>18%),在合⾦化处理后,获得规定的延伸率;c.采⽤最优的合⾦化处理⼯艺。
⼆、厚⼤断⾯铸态铁素体球墨铸铁件的质量控制技术1.化学成份的控制1)C、Si、CE的选择由于球状⽯墨对基体的削弱作⽤很⼩,故球墨铸铁中⽯墨数量的多少,对⼒学性能的影响不显著,当含碳量在3.2%~3.8%范围内变化时,对⼒学性能⽆明显的影响。
所以过程中确定碳硅含量时,主要考虑保证铸造性能,将碳当量选择在共晶成分左右。
具有共晶成分的铁液的流动性能最好,形成集中缩孔的倾向⼤,铸件组织的致密度⾼。
但碳当量过⾼时,容易产⽣⽯墨漂浮的同时,⼀定程度上对球化有影响,主要表现在要求的残余Mg量⾼。
使铸铁中夹杂物的数量增多,降低铸铁性能。
硅球墨铸铁中使铁素体增加的作⽤⽐灰铸铁⼤,所以硅含量的⾼低,直接影响球墨铸铁基体中的铁素体量。
【热坛讨论】关于球墨铸铁的一次与二次夹杂物问题的讨论
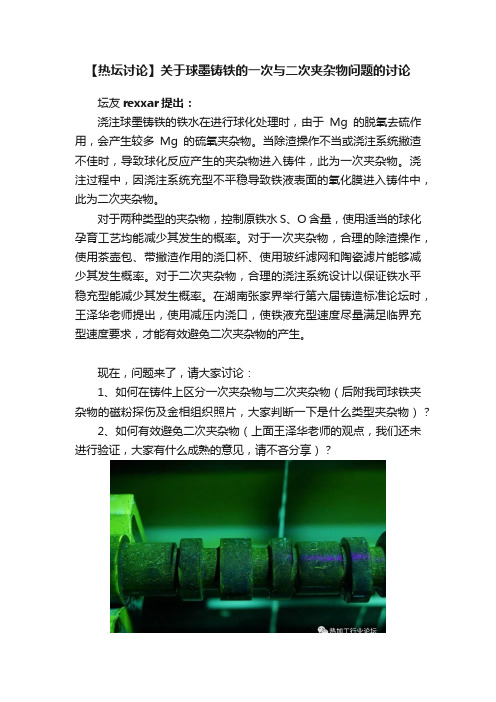
【热坛讨论】关于球墨铸铁的一次与二次夹杂物问题的讨论坛友rexxar提出:浇注球墨铸铁的铁水在进行球化处理时,由于Mg的脱氧去硫作用,会产生较多Mg的硫氧夹杂物。
当除渣操作不当或浇注系统撇渣不佳时,导致球化反应产生的夹杂物进入铸件,此为一次夹杂物。
浇注过程中,因浇注系统充型不平稳导致铁液表面的氧化膜进入铸件中,此为二次夹杂物。
对于两种类型的夹杂物,控制原铁水S、O含量,使用适当的球化孕育工艺均能减少其发生的概率。
对于一次夹杂物,合理的除渣操作,使用茶壶包、带撇渣作用的浇口杯、使用玻纤滤网和陶瓷滤片能够减少其发生概率。
对于二次夹杂物,合理的浇注系统设计以保证铁水平稳充型能减少其发生概率。
在湖南张家界举行第六届铸造标准论坛时,王泽华老师提出,使用减压内浇口,使铁液充型速度尽量满足临界充型速度要求,才能有效避免二次夹杂物的产生。
现在,问题来了,请大家讨论:1、如何在铸件上区分一次夹杂物与二次夹杂物(后附我司球铁夹杂物的磁粉探伤及金相组织照片,大家判断一下是什么类型夹杂物)?2、如何有效避免二次夹杂物(上面王泽华老师的观点,我们还未进行验证,大家有什么成熟的意见,请不吝分享)?附:工艺示意图,壳型背丸侧浇PS:我们曾经对这种缺陷进行过微区分析,结果表明:夹杂物中主要含Mg、O、Si元素,部分区域含S元素。
另有一些存在片状石墨的部位含Ca、Al等孕育剂特有的成分。
这与Karsay博士在《球墨铸铁浇口和冒口》一书中提出的夹杂物是硅酸镁(MgO·SiO2)的观点基本一致(Page83)。
我的疑问是:如何区别一次夹杂物与二次夹杂物?最好能够从形态特征上进行区分,以便采取相应的措施。
【以下摘录部分坛友的交流讨论回复】坛友zhjsdlc74:我认为王教授的观点是正确的,与John Camplell 的观点一样,尽量避免浇注紊流,减少bifilm缺陷。
虽然我没有做这方面的实践。
坛友chp0186:正如楼主所说:因除渣操作不当或浇注系统撇渣不佳导致球化反应产生的夹杂物进入铸件,此为一次渣。
有关硅钼球铁的一些问题-李传拭
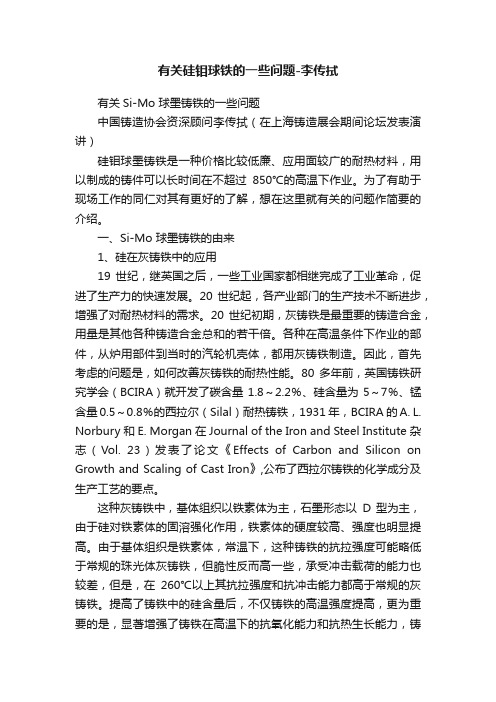
有关硅钼球铁的一些问题-李传拭有关Si-Mo 球墨铸铁的一些问题中国铸造协会资深顾问李传拭(在上海铸造展会期间论坛发表演讲)硅钼球墨铸铁是一种价格比较低廉、应用面较广的耐热材料,用以制成的铸件可以长时间在不超过850℃的高温下作业。
为了有助于现场工作的同仁对其有更好的了解,想在这里就有关的问题作简要的介绍。
一、Si-Mo 球墨铸铁的由来1、硅在灰铸铁中的应用19 世纪,继英国之后,一些工业国家都相继完成了工业革命,促进了生产力的快速发展。
20 世纪起,各产业部门的生产技术不断进步,增强了对耐热材料的需求。
20 世纪初期,灰铸铁是最重要的铸造合金,用量是其他各种铸造合金总和的若干倍。
各种在高温条件下作业的部件,从炉用部件到当时的汽轮机壳体,都用灰铸铁制造。
因此,首先考虑的问题是,如何改善灰铸铁的耐热性能。
80 多年前,英国铸铁研究学会(BCIRA)就开发了碳含量1.8~2.2%、硅含量为5~7%、锰含量0.5~0.8%的西拉尔(Silal)耐热铸铁,1931 年,BCIRA 的A. L. Norbury 和E. Morgan在Journal of the Iron and Steel Institute 杂志(Vol. 23)发表了论文《Effects of Carbon and Silicon on Growth and Scaling of Cast Iron》,公布了西拉尔铸铁的化学成分及生产工艺的要点。
这种灰铸铁中,基体组织以铁素体为主,石墨形态以D 型为主,由于硅对铁素体的固溶强化作用,铁素体的硬度较高、强度也明显提高。
由于基体组织是铁素体,常温下,这种铸铁的抗拉强度可能略低于常规的珠光体灰铸铁,但脆性反而高一些,承受冲击载荷的能力也较差,但是,在260℃以上其抗拉强度和抗冲击能力都高于常规的灰铸铁。
提高了铸铁中的硅含量后,不仅铸铁的高温强度提高,更为重要的是,显著增强了铸铁在高温下的抗氧化能力和抗热生长能力,铸件可以在850℃、甚至900℃的高温下作业。
【坛友分享】球铁件七种常见缺陷原因分析

【坛友分享】球铁件七种常见缺陷原因分析热加工行业论坛热加工行业论坛昨天1、石墨球异化石墨球异化出现不规则石墨,如团块状、蝌蚪状、蠕虫状、角状或其他非圆球状。
这是由于球状石墨沿辐射方向生长时,局部晶体生长模式和生长速率偏离正常生长规律所致。
铸件中残余球化元素量超出应有范围时,如残余镁太高,超过了保持石墨球化所需的最低量时,也会影响石墨结晶条件,就容易产生蝌蚪壮石墨。
而残余稀土较多时,高碳当量铁水易产生碎块石墨,碎块石墨的集中区域一般称做“灰斑”。
而蠕虫状石墨的出现则是由于球化元素残余量不足或者含有超限的钛和铝。
2、石墨漂浮过共晶成分的厚壁球铁件中,在浇注位置顶部,常常出现一个石墨密集区域,即“始末漂浮”现象,这是由于石墨与铁水密度不同,过共晶铁水直接析出的石墨受到浮力作用向上所致。
石墨漂浮程度与碳当量、球化元素的种类及残留量、铸件凝固时间、浇注温度等因素有关系。
镁能使球铁的共晶含碳量提高,碳当量相同的铁水,提高其残余镁量就能减少石墨漂浮,残留稀土量过高,有助于爆裂状石墨的升成。
3、反白口一般铸铁件的白口组织容易出现在冷却较快的表层、尖角、披缝等处,反白口缺陷则相反,碳化物相出现在铸件中等断面心部、热节等部位。
球化元素残余量过多时,有促进反白口缺陷产生的作用,稀土元素强于镁,它们一般都能增加球铁组织形成时的过冷度。
4、皮下针孔皮下针孔内主要含有氢,也有少量一氧化碳和氮。
残余镁量过高时,也同时加强了从湿型中吸收氢的倾向,因而产生皮下针孔的几率增加。
另外,球化铁水停留时间长也能增加针孔的数量。
5、缩孔缩松缩孔常出现在铸件最后凝固部位(热节处、冒口颈与铸件连接处、内角或内浇口与铸件连接处),是隐蔽于铸件内部或与外表连通的孔洞。
缩松,宏观的出现在热节处,细微的收缩孔洞,大多是孔洞内部互相连通。
与球化元素有关的是,要控制残余镁和稀土不能过高,这对减少宏观和微观缩松都有明显效果,缩松倾向几乎与球化元素成正比。
6、黑渣它一般发生在铸件的上部(浇注位置),主要分为块状、绳索状和细碎黑渣。
球墨铸铁件常见缺陷及工艺措施

攀枝花学院Panzhihua University本科毕业设计(论文)文献综述院(系):材料工程学校专业:材料成型及控制工程班级: 2010级材料成型及控制工程2班学生姓名:范家栋学号: 2010111020112013年12月4日文献综述:球墨铸铁件常见缺陷及工艺措施摘要:本文对球墨铸铁件生产中常见的缩孔、缩松、夹渣、、皮下气孔、球化衰退与球化不良缺陷及影响因素进行了详细分析, 并根据实际情况提出了一些有效的工艺措施措施。
关键词:球墨铸铁缺陷工艺措施球墨铸铁是20世纪五十年代发展起来的一种高强度铸铁材料,具有良好的强度和韧性, 其机械性能与铸钢件相当, 在耐热性、耐蚀性及耐磨性上优于传统的片状石墨铸铁, 而且在经济上球墨铸铁件生产成本低于铸钢件,因此高强度球墨铸铁件在结构件上有取代铸钢的趋势。
当然,球墨铸铁因其自身特性常产生一些常见缺陷外的特有缺陷。
这些缺陷影响铸件性能, 使铸件废品率增高。
为了防止这些缺陷的发生, 有必要对其进行分析, 总结出各种影响因素, 提出防止措施, 才能有效降低缺陷的产生, 提高铸件的力学性能及生产效益。
本文将讨论球铁件的主要常见缺陷: 缩孔、缩松、夹渣、皮下气孔、石墨漂浮、球化不良及球化衰退。
1 缩孔缩松1.1 产生原因缩孔的形状不规则,孔壁粗糙。
防止缩孔产生的条件是合金在恒温或很小的温度范围内结晶。
铸件壁逐层凝固的方式进行凝固。
液态合金填满铸型后。
因铸型吸热,靠近型腔表面的金属很快就降到凝固温度,凝固成一层外壳,温度下降,合金逐层凝固,凝固层加厚,内部的剩余液体,由于液体收缩和补充凝固层的凝固收缩,体积缩减,液面下降,铸件内部出现空隙,直到内部完全凝固,在铸件上部形成缩孔。
已经形成缩孔的铸件的铸件继续冷却到室温时,因固态收缩,铸件的外形轮廓尺寸略有缩小,如缩孔的形成过程分为4个阶段见图1.缩松为当合金结晶温度范围较宽时,在铸件表面结壳后,内部有一个较宽的液、固两相共存的凝固区域。
高硅钼球墨铸铁的研发
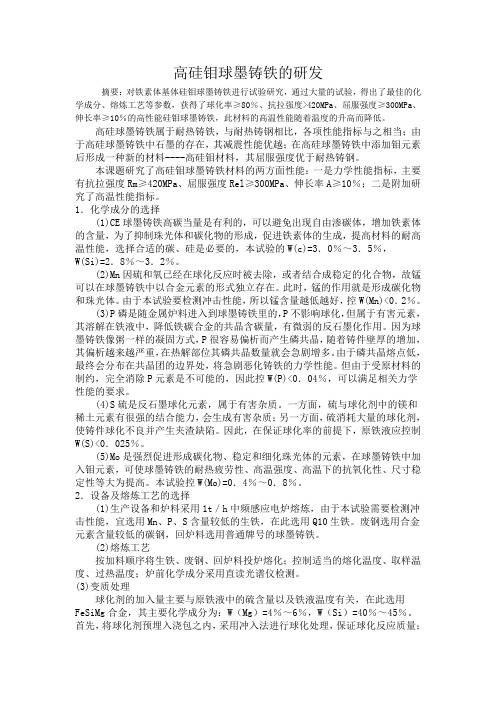
高硅钼球墨铸铁的研发摘要:对铁素体基体硅钼球墨铸铁进行试验研究,通过大量的试验,得出了最佳的化学成分、熔炼工艺等参数,获得了球化率≥80%、抗拉强度>420MPa、屈服强度≥300MPa、伸长率≥10%的高性能硅钼球墨铸铁,此材料的高温性能随着温度的升高而降低。
高硅球墨铸铁属于耐热铸铁,与耐热铸钢相比,各项性能指标与之相当;由于高硅球墨铸铁中石墨的存在,其减震性能优越;在高硅球墨铸铁中添加钼元素后形成一种新的材料----高硅钼材料,其屈服强度优于耐热铸钢。
本课题研究了高硅钼球墨铸铁材料的两方面性能:一是力学性能指标,主要有抗拉强度Rm≥420MPa、屈服强度Rel≥300MPa、伸长率A≥10%;二是附加研究了高温性能指标。
1.化学成分的选择(1)CE球墨铸铁高碳当量是有利的,可以避免出现自由渗碳体,增加铁素体的含量,为了抑制珠光体和碳化物的形成,促进铁素体的生成,提高材料的耐高温性能,选择合适的碳、硅是必要的,本试验的W(c)=3.0%~3.5%,W(Si)=2.8%~3.2%。
(2)Mn因硫和氧已经在球化反应时被去除,或者结合成稳定的化合物,故锰可以在球墨铸铁中以合金元素的形式独立存在。
此时,锰的作用就是形成碳化物和珠光体。
由于本试验要检测冲击性能,所以锰含量越低越好,控W(Mn)<0.2%。
(3)P磷是随金属炉料进入到球墨铸铁里的,P不影响球化,但属于有害元素,其溶解在铁液中,降低铁碳合金的共晶含碳量,有微弱的反石墨化作用。
因为球墨铸铁像粥一样的凝固方式,P很容易偏析而产生磷共晶,随着铸件壁厚的增加,其偏析越来越严重,在热解部位其磷共晶数量就会急剧增多。
由于磷共晶熔点低,最终会分布在共晶团的边界处,将急剧恶化铸铁的力学性能。
但由于受原材料的制约,完全消除P元素是不可能的,因此控W(P)<0.04%,可以满足相关力学性能的要求。
(4)S硫是反石墨球化元素,属于有害杂质。
一方面,硫与球化剂中的镁和稀土元素有很强的结合能力,会生成有害杂质;另一方面,硫消耗大量的球化剂,使铸件球化不良并产生夹渣缺陷。
有关硅钼球铁的一些问题_李传拭

有关Si-Mo 球墨铸铁的一些问题中国铸造协会资深顾问传拭(在铸造展会期间论坛发表演讲)硅钼球墨铸铁是一种价格比较低廉、应用面较广的耐热材料,用以制成的铸件可以长时间在不超过850℃的高温下作业。
为了有助于现场工作的对其有更好的了解,想在这里就有关的问题作简要的介绍。
一、Si-Mo 球墨铸铁的由来1、硅在灰铸铁中的应用19 世纪,继英国之后,一些工业国家都相继完成了工业革命,促进了生产力的快速发展。
20 世纪起,各产业部门的生产技术不断进步,增强了对耐热材料的需求。
20 世纪初期,灰铸铁是最重要的铸造合金,用量是其他各种铸造合金总和的若干倍。
各种在高温条件下作业的部件,从炉用部件到当时的汽轮机壳体,都用灰铸铁制造。
因此,首先考虑的问题是,如何改善灰铸铁的耐热性能。
80 多年前,英国铸铁研究学会(BCIRA)就开发了碳含量1.8~2.2%、硅含量为5~7%、锰含量0.5~0.8%的西拉尔(Silal)耐热铸铁,1931 年,BCIRA 的A. L. Norbury 和E. Morgan在Journal of the Iron and Steel Institute 杂志(Vol. 23)发表了论文《Effects of Carbon and Silicon on Growth and Scaling of Cast Iron》,公布了西拉尔铸铁的化学成分及生产工艺的要点。
这种灰铸铁中,基体组织以铁素体为主,石墨形态以D 型为主,由于硅对铁素体的固溶强化作用,铁素体的硬度较高、强度也明显提高。
由于基体组织是铁素体,常温下,这种铸铁的抗拉强度可能略低于常规的珠光体灰铸铁,但脆性反而高一些,承受冲击载荷的能力也较差,但是,在260℃以上其抗拉强度和抗冲击能力都高于常规的灰铸铁。
提高了铸铁中的硅含量后,不仅铸铁的高温强度提高,更为重要的是,显著增强了铸铁在高温下的抗氧化能力和抗热生长能力,铸件可以在850℃、甚至900℃的高温下作业。
硅铁中硅含量的快速测定
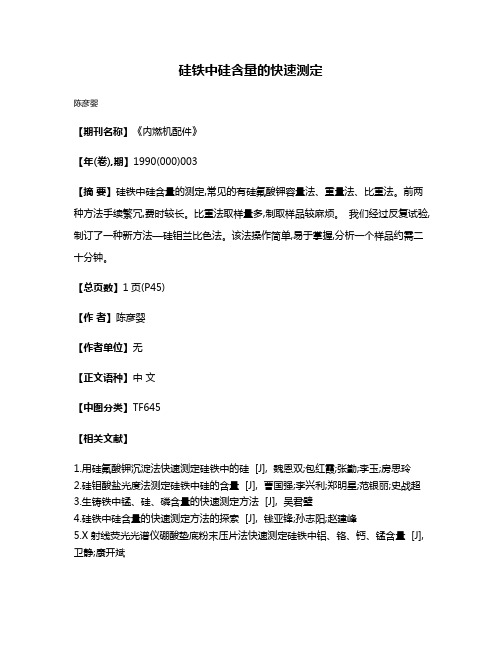
硅铁中硅含量的快速测定
陈彦婴
【期刊名称】《内燃机配件》
【年(卷),期】1990(000)003
【摘要】硅铁中硅含量的测定,常见的有硅氟酸钾容量法、重量法、比重法。
前两种方法手续繁冗,费时较长。
比重法取样量多,制取样品较麻烦。
我们经过反复试验,制订了一种新方法—硅钼兰比色法。
该法操作简单,易于掌握,分析一个样品约需二十分钟。
【总页数】1页(P45)
【作者】陈彦婴
【作者单位】无
【正文语种】中文
【中图分类】TF645
【相关文献】
1.用硅氟酸钾沉淀法快速测定硅铁中的硅 [J], 魏恩双;包红霞;张勤;李玉;房思玲
2.硅钼酸盐光度法测定硅铁中硅的含量 [J], 曹国强;李兴利;郑明星;范银丽;史战超
3.生铸铁中锰、硅、磷含量的快速测定方法 [J], 吴君璧
4.硅铁中硅含量的快速测定方法的探索 [J], 钱亚锋;孙志阳;赵建峰
5.X射线荧光光谱仪硼酸垫底粉末压片法快速测定硅铁中铝、铬、钙、锰含量 [J], 卫静;康开斌
因版权原因,仅展示原文概要,查看原文内容请购买。
球墨铸铁件缺陷产生的原因与预防措施(3)

球墨铸铁件缺陷产生的原因与预防措施(3)球墨铸铁件缺陷产生的原因与预防措施(5)必要情况下,可以加入钼等反石墨化元素,提高碳在铁液中的溶解度,从而减少石墨析出。
4 皮下气孔4. 1 影响因素(1)碳当量:适当增加含硅量有助于皮下气孔的减少。
同时,在硅量保持不变的情况下,随着含碳量的增加,球铁中皮下气孔的个数呈现出单峰曲线,且峰值点总保持在共晶点左右,因此,最好将碳硅含量选择得高一些,以使球铁的碳当量稍大于共晶点。
(2)硫:硫高会引起皮下气孔等缺陷,这是因为产生H2S气体而形成。
当含硫量超过0.094%时就会产生皮下气孔,含硫量越高,情况越严重。
(3)稀土:铁液中加入稀土元素能脱氧、脱硫,提高铁液表面张力,因此有利于防止产生皮下气孔。
但稀土含量太高,会增加铁液中氧化物的含量,使气泡外来核心增加,皮下气孔率增加。
残余稀土量应控制在0.043%以下。
(4)镁:过高的镁将会加剧铁液的吸氢倾向,大量的镁气泡和氧化物进入型腔,增加气泡的外来核心;此外镁蒸汽直接与砂型中的水分作用,产生MgO烟气及氢气,也会产生皮下气孔。
试验表明,残镁量大于0.05%后便易出现皮下气孔,残镁越高越严重。
因此在保证球化基础上,尽量降低残留镁量。
(5)铝:铁液中的铝是铸件产生氢气孔的主要原因。
据报道,当湿型铸造球墨铸铁的残留铝量为0.030%~0.050%时,将产生皮下气孔。
e.r.kaczmarek等人研究认为,铁液与铸型中的水反应生成FeO与H2,由于铝的脱氧作用,又生成Al2O3,其即为气泡生成的核心而又能吸附一定的气体,增加了球铁产生皮下气孔的倾向。
但是在减少渣中的`FeO成分时,镁的存在使得铝显得多余,故铝的敏感含量是有一定范围的。
(6)壁厚:皮下气孔还有“壁厚效应”特征,即气孔的产生在一定壁厚范围内,实际上这与铸件的凝固速度有关。
铸件壁厚大时,其凝固结皮时间推迟,有利于气泡逸出。
因此,一般来说壁厚小于6mm或大于25mm时不易产生皮下气孔。
球墨铸铁常见缺陷及防止措施
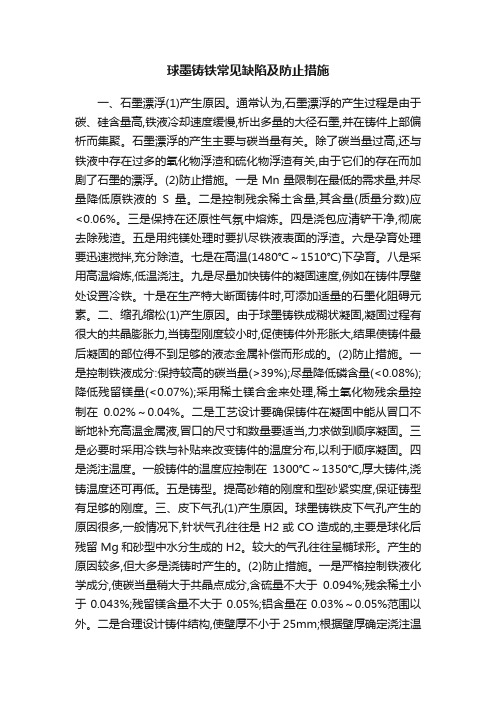
球墨铸铁常见缺陷及防止措施一、石墨漂浮(1)产生原因。
通常认为,石墨漂浮的产生过程是由于碳、硅含量高,铁液冷却速度缓慢,析出多量的大径石墨,并在铸件上部偏析而集聚。
石墨漂浮的产生主要与碳当量有关。
除了碳当量过高,还与铁液中存在过多的氧化物浮渣和硫化物浮渣有关,由于它们的存在而加剧了石墨的漂浮。
(2)防止措施。
一是Mn量限制在最低的需求量,并尽量降低原铁液的S量。
二是控制残余稀土含量,其含量(质量分数)应<0.06%。
三是保持在还原性气氛中熔炼。
四是浇包应清铲干净,彻底去除残渣。
五是用纯镁处理时要扒尽铁液表面的浮渣。
六是孕育处理要迅速搅拌,充分除渣。
七是在高温(1480℃~1510℃)下孕育。
八是采用高温熔炼,低温浇注。
九是尽量加快铸件的凝固速度,例如在铸件厚壁处设置冷铁。
十是在生产特大断面铸件时,可添加适量的石墨化阻碍元素。
二、缩孔缩松(1)产生原因。
由于球墨铸铁成糊状凝固,凝固过程有很大的共晶膨胀力,当铸型刚度较小时,促使铸件外形胀大,结果使铸件最后凝固的部位得不到足够的液态金属补偿而形成的。
(2)防止措施。
一是控制铁液成分:保持较高的碳当量(>39%);尽量降低磷含量(<0.08%);降低残留镁量(<0.07%);采用稀土镁合金来处理,稀土氧化物残余量控制在0.02%~0.04%。
二是工艺设计要确保铸件在凝固中能从冒口不断地补充高温金属液,冒口的尺寸和数量要适当,力求做到顺序凝固。
三是必要时采用冷铁与补贴来改变铸件的温度分布,以利于顺序凝固。
四是浇注温度。
一般铸件的温度应控制在1300℃~1350℃,厚大铸件,浇铸温度还可再低。
五是铸型。
提高砂箱的刚度和型砂紧实度,保证铸型有足够的刚度。
三、皮下气孔(1)产生原因。
球墨铸铁皮下气孔产生的原因很多,一般情况下,针状气孔往往是H2或CO造成的,主要是球化后残留Mg和砂型中水分生成的H2。
较大的气孔往往呈椭球形。
产生的原因较多,但大多是浇铸时产生的。
铬、钒对中硅钼球铁组织和力学性能的影响

铬、钒对中硅钼球铁组织和力学性能的影响
钱坤才;高顺;范建华
【期刊名称】《铸造》
【年(卷),期】2014(063)012
【摘要】研究了合金元素铬、钒对中硅钼球铁组织性能的影响.Cr能显著增加中硅钼球铁的珠光体和碳化物含量,加入0.60%左右的Cr后,强度比普通中硅钼提高了50 MPa,但伸长率下降了约50%.弥散分布的V碳化物作为结晶核心,起到固溶强化、第二相强化作用,不仅提高了强度,还有利于伸长率的提高,加入0.5%左右V的中硅钼球墨铸铁强度比普通中硅钼球墨铸铁和硅钼铬球墨铸铁提高10%~15%,伸长率略有增加,获得了高强度、高韧性的良好结合.
【总页数】4页(P1250-1253)
【作者】钱坤才;高顺;范建华
【作者单位】南车戚墅堰机车车辆工艺研究所有限公司,江苏常州213011;南车戚
墅堰机车车辆工艺研究所有限公司,江苏常州213011;南车戚墅堰机车车辆工艺研
究所有限公司,江苏常州213011
【正文语种】中文
【中图分类】TG143.5
【相关文献】
1.直读光谱法测定球铁中硅锰磷铬镍钼钒钛 [J], 梁启华
2.退火温度对冷硬低铬钼球铁轧辊组织和硬度的影响 [J], 严奕义;翟启杰
3.形变参数对中碳铬镍钼钒钢奥氏体晶粒的影响 [J], 马柏生;李友荣
4.形变参数对中碳铬镍钼钒钢奥氏体晶粒的影响 [J], 马柏生;李友荣;魏元春
5.中碳铬镍钼钒钢晶粒长大倾向及对力学性能的影响 [J], 张耀文;马培雄
因版权原因,仅展示原文概要,查看原文内容请购买。
高硅钼球铁的应用研究
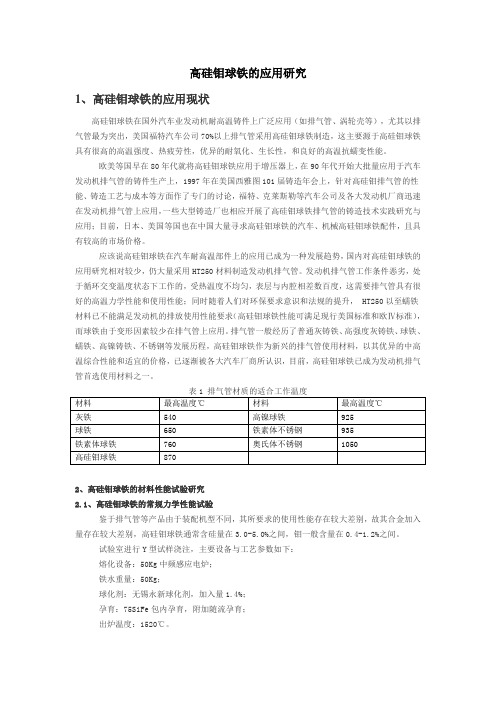
高硅钼球铁的应用研究1、高硅钼球铁的应用现状高硅钼球铁在国外汽车业发动机耐高温铸件上广泛应用(如排气管、涡轮壳等),尤其以排气管最为突出,美国福特汽车公司70%以上排气管采用高硅钼球铁制造,这主要源于高硅钼球铁具有很高的高温强度、热疲劳性,优异的耐氧化、生长性,和良好的高温抗蠕变性能。
欧美等国早在80年代就将高硅钼球铁应用于增压器上,在90年代开始大批量应用于汽车发动机排气管的铸件生产上,1997年在美国西雅图101届铸造年会上,针对高硅钼排气管的性能、铸造工艺与成本等方面作了专门的讨论,福特、克莱斯勒等汽车公司及各大发动机厂商迅速在发动机排气管上应用,一些大型铸造厂也相应开展了高硅钼球铁排气管的铸造技术实践研究与应用;目前,日本、美国等国也在中国大量寻求高硅钼球铁的汽车、机械高硅钼球铁配件,且具有较高的市场价格。
应该说高硅钼球铁在汽车耐高温部件上的应用已成为一种发展趋势,国内对高硅钼球铁的应用研究相对较少,仍大量采用HT250材料制造发动机排气管。
发动机排气管工作条件恶劣,处于循环交变温度状态下工作的,受热温度不均匀,表层与内腔相差数百度,这需要排气管具有很好的高温力学性能和使用性能;同时随着人们对环保要求意识和法规的提升, HT250以至蠕铁材料已不能满足发动机的排放使用性能要求(高硅钼球铁性能可满足现行美国标准和欧Ⅳ标准),而球铁由于变形因素较少在排气管上应用。
排气管一般经历了普通灰铸铁、高强度灰铸铁、球铁、蠕铁、高镍铸铁、不锈钢等发展历程,高硅钼球铁作为新兴的排气管使用材料,以其优异的中高温综合性能和适宜的价格,已逐渐被各大汽车厂商所认识,目前,高硅钼球铁已成为发动机排气管首选使用材料之一。
2、高硅钼球铁的材料性能试验研究2.1、高硅钼球铁的常规力学性能试验鉴于排气管等产品由于装配机型不同,其所要求的使用性能存在较大差别,故其合金加入量存在较大差别,高硅钼球铁通常含硅量在3.0-5.0%之间,钼一般含量在0.4-1.2%之间。
- 1、下载文档前请自行甄别文档内容的完整性,平台不提供额外的编辑、内容补充、找答案等附加服务。
- 2、"仅部分预览"的文档,不可在线预览部分如存在完整性等问题,可反馈申请退款(可完整预览的文档不适用该条件!)。
- 3、如文档侵犯您的权益,请联系客服反馈,我们会尽快为您处理(人工客服工作时间:9:00-18:30)。
有关Si-Mo 球墨铸铁的一些问题中国铸造协会资深顾问传拭(在铸造展会期间论坛发表演讲)硅钼球墨铸铁是一种价格比较低廉、应用面较广的耐热材料,用以制成的铸件可以长时间在不超过850℃的高温下作业。
为了有助于现场工作的对其有更好的了解,想在这里就有关的问题作简要的介绍。
一、Si-Mo 球墨铸铁的由来1、硅在灰铸铁中的应用19 世纪,继英国之后,一些工业国家都相继完成了工业革命,促进了生产力的快速发展。
20 世纪起,各产业部门的生产技术不断进步,增强了对耐热材料的需求。
20 世纪初期,灰铸铁是最重要的铸造合金,用量是其他各种铸造合金总和的若干倍。
各种在高温条件下作业的部件,从炉用部件到当时的汽轮机壳体,都用灰铸铁制造。
因此,首先考虑的问题是,如何改善灰铸铁的耐热性能。
80 多年前,英国铸铁研究学会(BCIRA)就开发了碳含量1.8~2.2%、硅含量为5~7%、锰含量0.5~0.8%的西拉尔(Silal)耐热铸铁,1931 年,BCIRA 的A. L. Norbury 和E. Morgan在Journal of the Iron and Steel Institute 杂志(Vol. 23)发表了论文《Effects of Carbon and Silicon on Growth and Scaling of Cast Iron》,公布了西拉尔铸铁的化学成分及生产工艺的要点。
这种灰铸铁中,基体组织以铁素体为主,石墨形态以D 型为主,由于硅对铁素体的固溶强化作用,铁素体的硬度较高、强度也明显提高。
由于基体组织是铁素体,常温下,这种铸铁的抗拉强度可能略低于常规的珠光体灰铸铁,但脆性反而高一些,承受冲击载荷的能力也较差,但是,在260℃以上其抗拉强度和抗冲击能力都高于常规的灰铸铁。
提高了铸铁中的硅含量后,不仅铸铁的高温强度提高,更为重要的是,显著增强了铸铁在高温下的抗氧化能力和抗热生长能力,铸件可以在850℃、甚至900℃的高温下作业。
不久以后,为了改善西拉尔铸铁的常温力学性能,将硅含量修订为4~6%。
这样的成分,一直沿用至今。
早期,西拉尔铸铁是世界知名的耐热铸铁。
2、由西拉尔铸铁到Si-Mo 球墨铸铁20 世纪40 年代,球墨铸铁问世,为铸铁的发展开创一个新的纪元。
随着球墨铸铁的推广应用,50 年代就有人研究将西拉尔铸铁的经验用于球墨铸铁。
将球墨铸铁中的硅含量提高到4~6%,铸铁的抗氧化能力、抗热生长能力都显著改善,60 年代,一些工业国家就已在生产中应用。
硅含量5~6%的球墨铸铁抗氧化能力很好,但是,硅含量超过5%以后,铁素体有一部分会转变为脆性相Fe3Si,使韧性大幅度下降,出于兼顾二者的折衷考虑,耐热球墨铸铁的硅含量一般都不超过5%。
提高了硅含量的球墨铸铁中,加入0.6~2.0%的钼,可以提高常温下的强度和韧性,高温力学性能的改善尤为明显,钼含量从0.2%逐步增加到2.5%,铸铁的蠕变性能也逐步改善。
但是,从价值工程的观点看来,最相宜的加入量为0.5~1.0%。
从20 世纪70 年代起,Si-Mo 球墨铸铁就是一种常用的耐热铸造合金,其用途很广。
早期的燃机,燃烧效率不高,排出的废气温度约在500℃左右,排气歧管一般都用灰铸铁制造。
随着技术的进步,燃机排气温度逐渐提高,排气歧管的材质也随之不断改进。
80 年代以后,档次较高的燃机排气温度超过了800℃,所用的排气歧管和涡轮增压器,灰铸铁、蠕墨铸铁、硅铸铁等材质都不能适应要求。
于是,Si-Mo 球墨铸铁大行其道,广泛用于世界各国的汽车行业,其需求量猛增。
90 年代以后,一些汽车发动机的排气温度超过了900℃,Si-Mo 球墨铸铁不能胜任了,开始用高镍奥氏体球墨铸铁。
2000 年代早期,高档汽车发动机的排气温度又越过了950℃,排气歧管和涡轮增压器不得不改用铁素体耐热钢。
2005 年以后,为了进一步提高燃油的燃烧效率,排气温度超过了1000℃,又要改用高镍奥氏体不锈钢。
在燃机燃烧效率不断提高的条件下,Si-Mo 球墨铸铁在汽车行业的应用是有所减少了,而且还有继续减少的趋向。
但是,在柴油机方面的应用仍然很多,而且,其他方面对耐热铸件的需求量也非常可观,Si-Mo 球墨铸铁仍然是一种重要的铸造合金。
二、Si-Mo 球墨铸铁的化学成分及其对力学性能的影响Si-Mo 球墨铸铁中的主要合金元素是硅,钼是为改善铸铁而加入的辅助合金元素,在硅、钼含量确定之后,对碳、锰、磷、硫等元素的含量也应该予以严格的控制。
1、硅在Si-Mo 球墨铸铁中,硅是重要的组分,其在球墨铸铁中的作用是多方面的,主要是提高抗氧化能力和降低热生长率,同时还可以使铁素体固溶强化。
其负面作用是,硅含量太高时导致铸铁脆化。
(1)促进石墨化、抑制渗碳体的析出在铸铁中,硅固溶于奥氏体中的溶解度约为2%,在铁素体中的溶解度可高达18.5%。
铸铁中,硅是促进石墨化作用最强的合金元素,其促进石墨化的能力大致是镍的3 倍、铜的5 倍。
无论在液态铸铁或固态铸铁中,铁与硅结合的能力比与碳结合的能力强。
增加铸铁中的硅含量,可以使铁-碳平衡图中铁-石墨系的共晶转变温度略有提高,铁-渗碳体系的共晶转变温度明显降低,从而使二者之间的间隔显著扩大。
对二者的共析转变温度也有类似的影响。
液态铸铁中含有硅,就会使碳的溶解度降低。
铁液中硅的含量愈高,能溶解的碳量相应地愈低,就会有更多的碳脱溶析出。
铁液为过共晶成分时,硅含量高,凝固过程中,有更多的碳以初生石墨的形态析出,直到剩余的铁液达到共晶成分后发生共晶转变。
铁液为亚共晶成分时,凝固过程中,硅富集于初生奥氏体中。
共晶转变时,硅富集于早期结晶的共晶奥氏体中,抑制碳与铁化合成渗碳体,增强碳在奥氏体中的扩散速度,促使碳以共晶石墨的形态析出。
共析转变时,固溶于奥氏体中的硅,仍然抑制碳与铁形成渗碳体,增强碳在奥氏体中的扩散速度,促使碳以共析石墨的形态析出,硅含量为4%左右的铸铁,基体组织大体上全是铁素体。
在加入了钼,而且用于制造薄壁铸件的条件下,组织中就可能含有少量的珠光体和碳化物。
Si-Mo 球墨铸铁中,硅含量较高,因而,薄壁铸件中形成碳化物的倾向较低,这对于制造排气歧管之类的薄壁铸件是很适宜的。
(2)提高铸铁的抗氧化能力一般说来,耐热铸件的作业条件是,在高温下、长时间与氧化性气体(主要是O2 、H2O、CO2)接触。
在这种条件下,铁基铸件的表面层会被氧化。
高温气体介质中有时还含有硫化物,硫对铁的作用也属于氧化反应。
耐热铸件应具有在高温下抗氧化的能力,也就是高温下的化学稳定性。
铁在高温下的氧化从表面开始,先形成一层薄氧化膜,然后逐渐增厚。
由于铸铁件的基本成分是铁,其氧化过程实际上是铁被氧化的过程。
在570℃以上的高温下,铁基铸件表面的氧化膜为三层结构。
层(贴近金属本体)为FeO,中间层为Fe3O4,外层为Fe2O3。
氧化过程中,氧原子以扩散的方式通过氧化膜进入铁中,使铁氧化,铸铁中的铁原子则向氧化膜方面扩散。
铁逐层被氧化成FeO,FeO 逐层被氧化成Fe3O4 ,Fe3O4 又逐层被氧化成Fe2O3。
结果是各氧化层不断增厚,金属本体逐渐减薄(见图1)。
铸铁的氧化过程中,在金属本体逐渐减薄的同时,由于氧化膜的密度小于铁,铸件的体积却反而会增加。
铸件外表面产生的氧化皮,是可能剥落的。
如果铸件的部氧化,则产生的氧化皮不可能剥落,结果是导致铸件的体积增大,这就是因氧化而致的热生长。
图1 铁基铸件表面氧化的示意图要提高铸铁的抗氧化能力,必须使其中含有能形成致密氧化膜的合金元素,而且这种氧化膜还应与金属本体结合紧密,从而抑制外界的氧原子通过氧化膜向铸件部扩散、以及铁原子向氧化膜扩散。
如果铸铁中含有加入铝、硅、铬等元素,形成的氧化膜的成分和结构都有变化,可以增强铸铁的抗氧化能力。
铬、铝含量高时,铸件的表面上形成致密的Cr2O3 或Al2O3 氧化膜,有良好的保护作用。
铬、铝含量不很高时,铸件的表面上形成FeO·Cr2O3、FeO·Al2O3 等尖晶石型氧化物,能与铁结合牢固,也有一定的保护作用。
硅含量较高的铸铁中,氧化膜的主要组成成分是铁橄榄石(Fe2SiO4),致密程度大为改善,能抑制外界的氧原子通过表面进入铸铁部。
就提高铸铁的抗氧化能力而言,硅是很强的抗氧化元素,其作用能力大约是铬的3 倍。
几种常用合金元素对铁氧化速率的影响见图2。
图2 常用合金元素对铁氧化速度的影响(3)减少铸件的热生长铸铁件热生长的定义是:铸件长时间暴露于高温下,或在反复加热、冷却作用下所产生的永久性体积增大。
热生长不仅使铸铁的强度降低,还可能损坏与之接触的其他部件。
铸铁发生热生长的原因,可以简要地归纳为以下三个方面。
1)高温下珠光体中的渗碳体分解、析出石墨所致的体积膨胀球墨铸铁中的珠光体在540℃以下比较稳定。
超过540℃以后,其中的渗碳体就会逐渐分解,碳以石墨的形态析出,通过扩散方式沉积在石墨球上。
650℃以上,石墨化的速度提高。
在700℃以上,石墨化在短时间就可以完成。
石墨化的结果就导致铸铁的体积膨胀。
基体组织全部为珠光体的球墨铸铁件,因石墨化而致的体积生长,按计算,大约是1%。
由于铸件部存在疏松和其他细小的孔隙,实际铸件因石墨化而致的生长低于此值。
有研究报告称:珠光体组织的球墨铸铁件,在高温下长时间保持,因石墨化而致的体积生长约在0.25~0.5%之间。
完全铁素体基体的球墨铸铁件,在820℃以下保持,实际上不可能因石墨化而产生体积增长。
Si-Mo 球墨铸铁中,硅含量提高到4%左右,不仅基体组织基本上是铁素体,珠光体很少,而且可以使铁-石墨系的共析转变温度A c1提高到870℃以上。
因此,在作业温度不超过850℃的条件下,不必担心铸件因石墨化而产生热生长的问题。
2)相变所致的体积膨胀铸件作业过程中,即使是铁素体基体的球墨铸铁,如果所处的温度不断通过铸铁共析转变温度围,铸铁周期性地发生铁素体→奥氏体、奥氏体→铁素体的相变。
加热到基体组织为奥氏体时,少量石墨溶入奥氏体,留下一些微小的孔隙。
冷却时,奥氏体中的碳又以石墨的形态析出,但不会析出在原来留下的孔隙中,从而造成石墨化膨胀。
长时间反复经历这种转变,铁就会有可观的体积膨胀,导致很坏的后果。
因此,常规的铁素体球墨铸铁的作业温度,一般都不能高于共析转变温度(约在760℃左右)。
提高铸铁中的硅含量,可以使其共析转变温度提高,铸铁作业的温度也可相应地提高,参见表1。
表1 硅含量对共析转变温度的影响3)铸铁部氧化所致的体积膨胀前面已经提到,铸铁件的部氧化是导致热生长的主要原因之一,而铸铁组织中石墨的形态和数量又是影响铸件部氧化的重要因素。
灰铸铁的显微组织中,石墨呈分散的片状,实际上是相互连接的团簇体,而且还有触及铸件表面的石墨片。