6高镍奥氏体球墨铸铁综述
关于高镍奥氏体球墨铸铁充满度的验证1C

铸造技术2009年第9期高镍奥氏体球墨铸铁饱和度和碳当量的验证程武超赵新武党波涛靳宝(西峡县内燃机进排气管有限责任公司河南西峡474500)摘要用不同的饱和度和碳当量的铁液浇注不同厚度的高镍奥氏体球墨铸铁试块,从金相组织、力学性能上对高镍奥氏体球墨铸铁的饱和度和碳当量进行了验证。
事实证明,饱和度A 超过4.9时,在不同的厚度上仍能得到球化率和力学性能合格的铸件。
当碳当量取较高值时,降低了铁液的液相线温度,熔炼温度随之下降,反过来又减少了高温熔炼带来的不利影响。
在不产生冷隔的前提下,为降低浇注温度创造了条件。
较高的碳当量有利于凝固过程的石墨化膨胀所产生的自补缩效果,可以减少缩松和缩孔缺陷。
关键词饱和度球化率力学性能缩松和缩孔中图分类号:TG143.5 文献标识码:A 文章编号:100-8365(2009)19-1097-05V erification of Austenite nodular cast ironSaturation and Carbon EquivalentCHENG Wu –chao, ZHAO Xin-wu, DANG Bo-tao, JIN Bao(Xixia Intake & Exhaust Manifold Co., Ltd, Xixia 474500 China)Abstract: Austenite nodular cast iron test block with different thickness were cast from different saturation and CE,and the saturation and CE were verified by microstructure and mechanical properties. It proves that qualified castings with different thickness in nodularity and mechanical properties are still obtained when the saturation (A) value exceeds 4.9. Adopting high value of CE can low the liquidus temperature of molten iron, which makes the melting temperature decrease, and it conversely reduces detrimental affect for high temperature melting. Under the precondition that no cold shut occurs, it creates conditions to decrease pouring temperature. Higher CE is helpful to improve the self-feeding ability of graphitizing expansion during solidification process, and to reduces casting defects, such as shrinkage and blowhole. Keywords: Saturation; Nodularity; Mechanical properties; shrinkage and blowhole 高镍奥氏体球墨铸铁是耐高温、耐腐蚀、抗氧化性能较好的铸铁材料。
典型增压器涡壳开裂失效案例分析

典型增压器涡壳开裂失效案例分析管奇贤董碧瑾杨亚宾蔺桂成(宁波吉利罗佑发动机零部件有限公司,宁波315336)摘要:涡轮增压器处在高温㊁高压和高速运转的复杂工作状态下,承受着较高的瞬态热负荷,对制造的材料㊁零部件的结构及加工技术等都有较高的要求㊂由于汽油机排气温度很高,随着不同工况的变化,涡壳通常在400~900ħ高温交变热负荷下工作[1],高温㊁快速㊁大范围的温变工况致使热应力引起的涡壳开裂成为增压器常见的失效现象㊂采用计算机辅助工程(C A E)分析计算㊁材料耐温分析㊁微观组织质量评价与台架试验边界等方法,对涡壳开裂问题进行探讨,增加在新产品开发及试制过程中处理及改善此类问题的经验,从而减少产品开发的成本,缩短开发周期,对提升发动机的可靠性及耐久性具有重要意义㊂关键词:涡轮增压器;开裂;D5S材料0前言涡轮增压技术可有效提高发动机升功率及燃油经济性,特别是有助于满足日益严格的车辆排放标准法规,从而成为了汽车技术的焦点㊂本文通过对某机型涡轮增压器涡壳开裂失效案例进行研究,对其失效机理开展分析,从而制定改进措施,并进行了效果验证㊂1涡轮增压器涡壳开裂失效现象涡轮增压器在发动机台架耐久试验过程中经常会发生涡壳开裂现象㊂在本案例中,发动机在完成400h 冷热冲击试验后,研究人员发现废气阀座附近存在贯穿裂纹,开裂情况见图1㊂研究人员通过对涡壳开裂部位断面的S E M分析,得出开裂主要原因为热应力㊂2增压器涡壳开裂失效原因分析引起汽油机涡轮增压器涡壳开裂失效的原因一般是各种因素的综合结果,但根据实际案例经验的积累,基本可分为以下4大类:(1)涡壳结构设计缺陷㊂由于安装空间和其他连接部件的限制,涡壳外形结构复杂而导致涡壳开裂[2]㊂主要表现为结构设计不合理,整体壁厚设计不均匀,局部倒角㊁圆角过小,过渡突兀等,可结合计算机辅助工程(C A E)仿真分析等手段进行分析㊂图1耐久试验后涡壳开裂(2)产品铸造㊁热处理问题㊂考量微观组织质量,主要表现为涡壳热处理不满足要求或者无热处理,无法目视的铸造缺陷(砂眼㊁气孔㊁缩松㊁缺肉等),金相组织㊁孔隙率等微观质量问题㊂(3)标定排温控制㊂涡壳在运行过程中的稳态最高排温超过了材料本身的许用限值导致开裂㊂(4)试验边界,台架悬置不合理(带来异常振动等)㊂排气系统未按照设计要求布置,未采用柔性悬挂,台架散热不佳或无散热等㊂772020 NO.6汽车与新动力All Rights Reserved.综上,本文将重点围绕这4类导致涡壳开裂的典型原因进行分析论述㊂表1 D 5S 材料力学性能表项目性能要求化学成分/%CS iM nPST iM o N iM g C rɤ2.04.0~6.00.5~1.5ɤ0.05ɤ0.01--34~36-1.5~2.5石墨球化率ȡ90%,石墨球大小为6~8级基体奥氏体,少量碳化物机械性能抗拉强度ȡ370M P a ,延伸率ȡ10%,硬度130H B ~170H B2.1 涡壳介绍涡壳的流道曲面形状和外形结构复杂,影响涡壳开裂的因素较多,诸如流道设计结构㊁流道整体壁厚㊁涡轮外壳(W /G )凸台㊁涡壳材料等㊂本文所述增压器涡壳结构与排气歧管集成,材料采用高镍铸铁材料G G G -N i S i C r 35-5-2(以下简称D 5S )㊂安全使用温度约为920ħ,实际应用瞬态工况可以允许达到950ħ,持续时间一般应小于5s㊂材料的低热膨胀系数和稳定的金相组织有着较高重要性,它决定着涡壳在使用过程中的伸长㊁收缩和弯曲变形,材料具有较高的相变温度才能获得稳定的基体组织,以减小相变引起的热裂和变形[3]㊂该材料的力学性能见表1㊂2.2 热应力分析-校核涡壳结构设计2.2.1 裂纹原因分析在试验冷热过程中,由于受到材料热胀冷缩㊁壁厚不均㊁高温蠕变㊁振动及涡壳结构等因素的影响,会形成应力集中区,随着耐久试验的推进,应力集中区会产生裂纹㊂对于涡壳铸件来说,其壁厚一般为4~5m m ㊂均匀的壁厚将有利于涡壳的良好散热,也不容易产生热应力集中的情况㊂2.2.2 分析模型图通过模拟计算,评估涡壳热应力开裂风险并给出相应改进方案,分析流程按下文所述4点开展进行[4],并根据结果进行优化㊂(1)设定边界条件(基于有限元模型)㊂涡壳温度场负荷:气体换热系数和气体温度㊁环境热对流与辐射㊁模拟中间体冷却㊂涡壳热应力负荷:温度场㊁位移约束涡壳进气法兰[5];其中气体换热系数和气体温度通过计算流体力学(C F D )计算求得㊂(2)试验工况㊂模拟计算需加入台架试验的循环工况(冷热冲击),其示意图如图2所示㊂根据试验循环工况,排温最高出现在全速全负荷时候,模拟计算涡壳前废气排温怠速425ħ,额定功率点950ħ(实测数据)进行㊂图2 试验循环工况示意图(3)温度场分布㊂根据试验工况,得出各工况点下的涡壳温度场分布,可得出高温区域范围㊂涡壳温度场分布如图3所示㊂图3 涡壳温度场分布示意塑性应变分布:得出应变分布,业内考核通常采用等效塑性应变幅值(ΔP E E Q )来评价,涡壳内外部的考核标准根据实际有所差异,一般要求外部ΔP E E Q<0.1%㊂2.3 铸件微观组织质量对开裂的影响本试验采用高镍球墨铸铁(奥氏体镍抗球墨铸铁),高镍球铁一般含镍量为13%~36%㊂镍是强力的奥氏体稳定化学元素,可扩大奥氏体的存在区间,可以使基体在室温下获得稳定奥氏体组织[6-7]㊂高镍球铁具有优异的高温组织稳定性和抗氧化能力,下文从如78汽车与新动力All Rights Reserved.下几个微观组织方面进行论述㊂2.3.1碳化物金相组织中碳化物一般以粒状或网状分布较多,粒状要优于网状㊂如果碳化物呈网状分布的话,会降低材料的塑性㊂一旦出现了裂纹,则会大幅降低其抑制裂纹扩展的能力[8]㊂同时,铸件如果未采用热处理工艺,则其碳化物分布均匀性会相对较差㊂2.3.2显微缩松(孔隙率)一般而言,显微缩松越严重,说明铸造质量越差,其机械性能也就越差㊂根据涡壳具体部位的不同,对于孔隙率的评判标准也不大相同,关键放气阀座㊁涡壳舌口等功能部位要求严格,缩松目标为不大于2%,非功能区标准应控制在5%以下㊂2.3.3球化率球化率指标有着较高重要性,详见表2标准㊂在排气系统特别是在涡轮增压器涡壳的应用上建议为2级或者更高,即球化率大于90%㊂球化率级别越高,其机械性能越好,反之越差㊂另外,对石墨的大小也有要求,一般为6~7级㊂表2各类球铁应用温度值材料牌号基体组织应用温度/ħ铁素体球铁Q T420-15铁素体,珠光体含量ɤ5%,石墨球600~650高硅球铁-铁素体,珠光体含量ɤ5%,石墨球600~750硅钼球铁H i S i M oD C I铁素体,珠光体含量ɤ5%,石墨球650~820加钒硅钼球铁-铁素体,珠光体含量ɤ5%,石墨球ɤ850高镍球铁D5S㊁D4㊁D2奥氏体基体,石墨球化级别2~3级ɤ920 2.4标定排温控制对开裂的影响根据表2可知,D5S排温最高应不超过920ħ,可允许瞬时最高排温至950ħ㊂对于大负荷工况下的汽油机排温控制而言,通常的手段是采用加浓燃油喷射㊂因此在标定策略上必须以增压器涡壳材料耐温限值来约束标定的最高排温,以本研究的高镍球墨铸铁D5S为例,最高标定稳态排温必须限制在920ħ,此时过量空气系数λʈ0.79~0.80㊂2.5试验边界条件的控制对于试验边界条件的控制(台架布置的合理性),主要是通过散热及振动来关注㊂2.5.1振动加速度㊁振幅试验人员对台架耐久发动机排气系统振动加速度及振动幅值进行测试,在所有工况下的最大振动加速度最高可达12.5G,见图4㊂相比振动加速度,其振动幅值相对较小,其幅值为0.45m m,见图5㊂图4振动加速度图5振动幅值由此可以判断,过大的振动加速度将加剧涡壳开裂失效的风险㊂在可控范围内,加速度以及振幅均是越小越好[9]㊂2.5.2散热条件台架耐久试验不同于整车道路耐久试验,其全速全负荷工况恶劣,必须在排气侧加装额外的大功率散热风扇㊂综上分析,需要对此涡壳开裂案例进行整改,以达到规避风险的目标要求㊂3锁定本案例失效的主因根据上文可知,其热应力区域与本文故障增压器792020 NO.6汽车与新动力All Rights Reserved.涡壳开裂区域相吻合,热应力是其开裂的主要原因之一,详见图6塑性应变分布㊂图6 塑性应变分布D 5S 材料的耐温上限为920ħ,此故障件耐久试验并未对排温进行严格控制,详见图7㊂最高温度情况达到了950ħ,这是导致涡壳开裂的重要原因之一㊂图7 涡壳前废气排温曲线随着,研究人员对失效故障件切片进行微观组件检测,其孔隙率㊁碳化物含量偏高,可知微观质量缺陷为开裂主因之一,详见图8㊂显微缩松显示,碳化物含量偏高,且局部成网状分布,对机械性能产生影响,抑制裂纹扩展的能力大幅下降[8],详见图9㊂在试验室台架布置中,所有紧固支架㊁支撑点㊁散热风扇均已按照设计及试验要求安装,但是根据上述图8孔隙率以及显微缩松现象图9 100倍放大条件下的碳化物分布情况振动加速度的测量,振动加速度偏高㊂鉴于试验台架无法完全与整车布置一致,且台架悬置也已经按整车要求加装橡胶垫,因此振动加速度偏大不被纳入主因㊂失效故障增压器厂家设定的振动加速度标准为小于15G ,但针对非旋转部件(涡壳㊁中间壳等)的振动限值须根据实际项目应用情况测试,结果以满足使用要求㊁无共振为导向㊂4 改进措施及效果验证研究人员在偏薄区域增加壁厚,按5m m 的厚度考量,加大根部圆角,局部增设加强筋,优化涡壳三维(3D )造型,缓解热应力,详见图10㊂研究人员考虑优化微观结构,减少孔隙率㊁显微缩松,弱化碳化物㊂图11示出了改善后的结果,其已经满足功能区不大于2%,非功能区小于5%的目标要求㊂在失效案例整改的过程中,试验人员与铸造厂家交流了铸造工艺方面的几个要点:80汽车与新动力All Rights Reserved.图10优化前后3D 模型对比图11改善后的显微缩松分布示意图(1)炉料要求干净㊁无油污,杂质含量严格控制,浇冒口要抛丸处理;(2)严格控制开浇温度;(3)增加脱氧次数,提高抗氧化性[10];台架耐久排温监测,严格控制涡轮前废气温度,温度如达到920ħ会报警,温度如达到950ħ则会自动停机㊂通过上述整改措施,在后续的400h冷热冲击耐久试验中,开裂问题得到有效解决㊂5结论本文通过对涡轮增压汽油机涡壳台架耐久后开裂(贯穿裂纹)问题进行分析,围绕结构设计㊁涡壳材料㊁材料微观组织㊁排温㊁试验边界等方面开展详细的验证工作,最终开裂问题得到有效解决,从中得到如下结论㊂(1)涡壳结构的设计必须通过有限元分析研究,优化热应力集中部位结构,缓解热应力㊂(2)涡壳微观组织必须得到监控,根据不同材料制定相应的评价标准,同一批次保留样件,供后续分析㊁对比检测使用㊂(3)排温必须在涡壳材料许用温度限制以内,如采用果不能满足,则需要更换耐温更高的材料,如采用铸钢D I N1.4837材料㊂(4)台架振动带来的影响不可避免,尽可能通过结构优化及布置方式来减缓台架振动对排气侧的影响㊂参考文献[1]王泽华,许鹤皋,蒋兴国,等.汽车增压器涡轮壳材料研究[J].内燃机,1999(1):31-35.[2]蒋德明.高等内燃机原理[M].西安:西安交通大学出版社,1993.[3]王佳华.发动机排气歧管开裂失效分析[D].上海:同济大学机械与汽车工程学院,2009.[4]李红庆.杨万里,刘国庆,等.内燃机排气歧管热应力分析[J].内燃机工程,2005,26(5):81-84.[5]谷爱国.车用涡轮增压器涡壳流场分析[D].长春:吉林大学,2007.[6]金永锡,范仲嘉.高镍奥氏体球墨铸铁涡轮增压器壳体材质及工艺研究[J].铸造,2005,54(5):494-500.[7]陈平昌,黄志刚,肖理明,等.高镍奥氏体球墨铸铁高温性能研究[J].华中理工大学学报,1995,23(1):104-108.[8]球墨铸铁金相检验[S].G B/T9441-2009.[9]刑素芳,王现荣,王超,等.发动机排气系统振动分析[J].河北工业大学学报,2005,34(5):109-111.[10]中国机械工程学会.铸造手册(第1卷铸铁)[M].北京:机械工业出版社,1997.812020 NO.6汽车与新动力All Rights Reserved.。
高镍奥氏体球墨铸铁

高镍奥氏体球墨铸铁球墨铸铁是一种优良的工程材料,广泛应用于汽车、机械、建筑等领域。
它具有高强度、韧性、可加工性和耐腐蚀性等优点。
在球墨铸铁中,镍是一种非常重要的添加元素,它可以显著提高球墨铸铁的性能。
高镍奥氏体球墨铸铁就是一种应用广泛的高性能材料之一。
高镍奥氏体球墨铸铁是一种含有2-4%的镍的铁素体球墨铸铁。
它是通过将铁水中的硫化物转化为硫酸盐来进行净化的,从而使球墨铸铁具有更高的化学纯度。
镍的添加可以提高球墨铸铁的强度、韧性和耐腐蚀性。
此外,高镍奥氏体球墨铸铁还具有良好的耐磨性。
在高镍奥氏体球墨铸铁中,镍的添加量对性能有着重要的影响。
适当的镍含量可以平衡铁素体和奥氏体的比例,使得球墨铸铁具有较高的硬度和韧性。
过高的镍含量会使球墨铸铁变得脆性,而过低的镍含量则会影响球墨铸铁的耐腐蚀性和耐磨性。
除了镍的添加外,高镍奥氏体球墨铸铁还需要进行钙硅渗透处理。
这种处理可以在铁素体和奥氏体之间形成一定的界面,从而提高球墨铸铁的强度和韧性。
此外,球墨化处理也是高镍奥氏体球墨铸铁生产中不可或缺的一步。
球墨化处理可以使铁素体转化为球墨铁,并进一步提高球墨铸铁的性能。
高镍奥氏体球墨铸铁广泛用于机械工程、汽车工程和建筑工程等领域。
在机械工程中,它通常用于制造轴承、齿轮和其他高负荷部件。
在汽车工程中,高镍奥氏体球墨铸铁可用于制造曲轴、缸体和其他需要较高强度和耐磨性的部件。
在建筑工程中,它通常用于制造大型铸件,如桥墩和桥梁支架等。
总之,高镍奥氏体球墨铸铁是一种具有高强度、韧性和耐腐蚀性的优良材料。
它的性能取决于镍的含量、钙硅渗透和球墨化处理等工艺参数。
在未来,随着高性能材料需求的不断增加,高镍奥氏体球墨铸铁将会有更广泛的应用空间。
高镍奥氏体球墨铸铁支撑的材质及铸造工艺研究
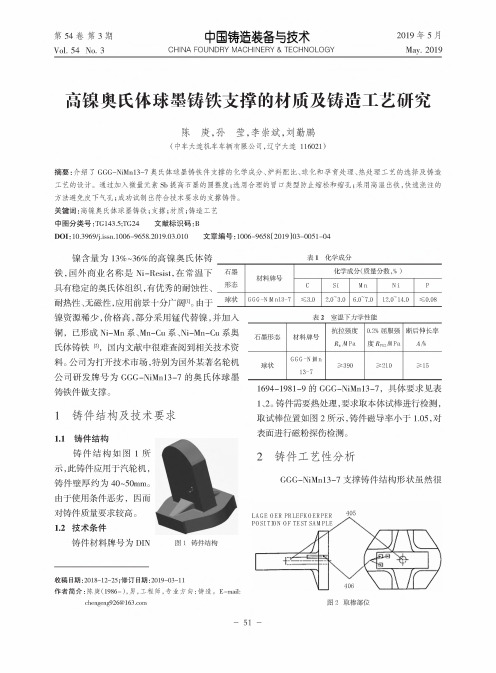
第57卷第3期中国铸造装备与技术Vol.54No.3CHINA FOUNDRY MACHINERY&TECHNOLOGY May.2019高鎳奥氏体球墨铸铁支撑的材质及铸造工艺研究陈庚,孙莹,李崇斌,刘勤鹏(中车大连机车车辆有限公司,辽宁大连116021)摘要:介绍了GGG-NiMn13-7奥氏体球墨铸铁件支撑的化学成分、炉料配比、球化和孕育处理、热处理工艺的选择及铸造工艺的设计。
通过加入微量元素Sb提高石墨的圆整度;选用合理的冒口类型防止缩松和缩孔;采用高温出铁,快速浇注的方法避免皮下气孔;成功试制出符合技术要求的支撑铸件。
关键词:高镰奥氏体球墨铸铁;支撑;材质;铸造工艺中图分类号:TG143.5;TG24文献标识码:BDOI:10.3969/j.issn.1006-9658.2019.03.010文章编号:1006-9658(2019)03-0051-04鎳含量为13%~36%的高鎳奥氏体铸_____铁,国外商业名称是Ni-Resist,在常温下石墨具有稳定的奥氏体组织,有优秀的耐蚀性、形态耐热性、无磁性,应用前景十分广阔[1]。
由于丄冬鎳资源稀少,价格高,部分采用b代替鎳,并加入铜,已形成Ni-Mn系、Mn-Cu系、Ni-Mn-Cu系奥氏体铸铁叫国内文献中很难查阅到相关技术资料。
公司为打开技术市,为国外名公司研发牌号为GGG-NiMn13-7的奥氏体球墨铸铁件。
1铸件结构及技术要求1.1铸件结构铸件结构如图1所示,此铸件应用于汽轮机,铸件壁厚约为40~50mm。
由于用件,对铸件量高。
1.2技术条件铸件材料牌号为DIN图1铸件结构收稿日期:2018-12-25;修订日期:2019-03-11作者简介:陈庚(1986-),6,工程8,专:方向:铸造。
E-mail: chengeng926@表1化学成分材料牌号化学成分(质量分数,%)C Si Mn Ni P GGG-N:Mn13-7!3.0 2.0>3.0 6.0>7.012.0>14.0!0.08表2室温下力学性能形料抗拉强度Pa0.2%屈服强度!p0.A Pa断后伸长率"/%球状GGG-NiMn13-7"390"210"15 1694-1981-9的GGG-NiMn13-7,具体要求见表1、2。
球墨铸铁简介介绍
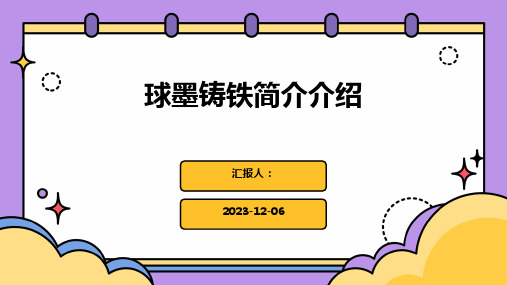
研究高效熔炼和浇注技术,缩短生产周期,降低能源消耗 和成本。例如,采用电炉熔炼、感应炉加热等先进技术, 提高熔炼效率和质量。
循环利用与废品再利用
加强废品回收和再利用,提高资源利用效率,降低生产成 本。例如,将废品进行破碎、熔炼后重新用于生产。
环保与可持续发展
减少污染排放
采取有效措施减少生产过程中的 废气、废水和固体废弃物的排放 ,降低对环境的影响。例如,采 用环保涂料和除尘设备等减少废
性质
具有高强度、高韧性、耐磨性等 优良性能,同时具有良好的可加 工性和耐腐蚀性。
球墨铸铁的历史与发展
历史
球墨铸铁最早由美国人发明,于19 世纪80年代问世。
发展
随着铸造技术的进步和新型材料的出 现,球墨铸铁的应用领域不断扩大。
球墨铸铁的生产过程
处理
对原材料进行质量 检验、合金化处理 、熔炼等步骤。
耐磨性
良好的耐磨性
球墨铸铁具有较好的耐磨性,能够在摩擦磨损条件下长期使 用。
磨损率低
球墨铸铁的磨损率较低,能够减少零件的磨损和更换频率。
耐腐蚀性
良好的耐腐蚀性
球墨铸铁具有较好的耐腐蚀性,能够抵抗常见的化学腐蚀。
在腐蚀环境下长期使用
球墨铸铁可以在腐蚀环境下长期使用,适用于各种恶劣环境。
03
球墨铸铁的应用领域
后处理工艺与设备
后处理工艺
包括热处理、切割、打磨等工序,以进一步提高产品 的力学性能和外观质量。
后处理设备
包括热处理炉、切割机、磨床等设备,其中热处理炉 需具备温度控制精度高、炉内温度均匀等特点。
05
球墨铸铁的未来发展趋势 与挑战
新材料与新工艺的研究与应用
01
高镍奥氏体球墨铸铁阀杆螺母及其制造方法[发明专利]
![高镍奥氏体球墨铸铁阀杆螺母及其制造方法[发明专利]](https://img.taocdn.com/s3/m/49531db6f01dc281e43af077.png)
专利名称:高镍奥氏体球墨铸铁阀杆螺母及其制造方法专利类型:发明专利
发明人:项楠
申请号:CN200810019438.9
申请日:20080107
公开号:CN101481769A
公开日:
20090715
专利内容由知识产权出版社提供
摘要:一种选用D-2型高镍奥氏体球墨铸铁制造的阀杆螺母以及其制作方法,所选用材料成分为碳≤3.0%、硅1.5-3.0%、锰0.7-1.25%、铬1.75-2.75,镍18-22%、磷≤0.08%,机械性能为抗拉强度≥400MPa,屈服强度≥207MPa,延伸率≥8%,硬度139-202HB,其组织为奥压体基体上分布球状的石墨,并含有少量碳化物,选定材料后,制作方法分为:1.造型制芯,2.熔炼,3.球化处理,4.孕育处理,5.炉前检测,6.浇注,7.炉后检测,8.清理和粗加工,9.机床精细切削加工等共9个步骤。
本发明的有益之处在于所选用的阀杆螺母材料具有良好的耐蚀性、耐高温、抗氧化性,同时有良好的低热膨胀性和低温冲击韧性,完全符合阀杆螺母的各种恶劣工作环境。
申请人:项楠
地址:224400 江苏省阜宁县阜城工业区
国籍:CN
更多信息请下载全文后查看。
奥氏体球墨铸铁
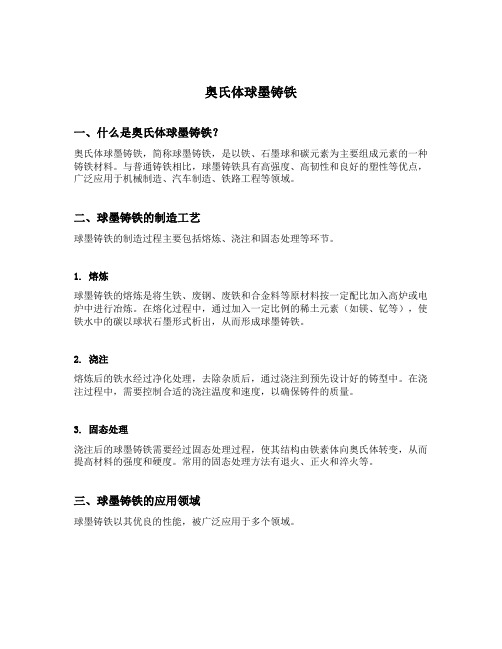
奥氏体球墨铸铁一、什么是奥氏体球墨铸铁?奥氏体球墨铸铁,简称球墨铸铁,是以铁、石墨球和碳元素为主要组成元素的一种铸铁材料。
与普通铸铁相比,球墨铸铁具有高强度、高韧性和良好的塑性等优点,广泛应用于机械制造、汽车制造、铁路工程等领域。
二、球墨铸铁的制造工艺球墨铸铁的制造过程主要包括熔炼、浇注和固态处理等环节。
1. 熔炼球墨铸铁的熔炼是将生铁、废钢、废铁和合金料等原材料按一定配比加入高炉或电炉中进行冶炼。
在熔化过程中,通过加入一定比例的稀土元素(如镁、钇等),使铁水中的碳以球状石墨形式析出,从而形成球墨铸铁。
2. 浇注熔炼后的铁水经过净化处理,去除杂质后,通过浇注到预先设计好的铸型中。
在浇注过程中,需要控制合适的浇注温度和速度,以确保铸件的质量。
3. 固态处理浇注后的球墨铸铁需要经过固态处理过程,使其结构由铁素体向奥氏体转变,从而提高材料的强度和硬度。
常用的固态处理方法有退火、正火和淬火等。
三、球墨铸铁的应用领域球墨铸铁以其优良的性能,被广泛应用于多个领域。
1. 机械制造领域球墨铸铁的高强度和耐磨性使其成为机械制造中不可或缺的材料。
它可以用于制造各种机械零件,如发动机缸体、汽车曲轴箱、工程机械零件等。
2. 汽车制造领域球墨铸铁在汽车制造中扮演着重要的角色。
它可以用于制造汽车发动机缸体、曲轴箱、制动系统零件等。
球墨铸铁的高强度和耐磨性使汽车零件能够承受高温、高压和高速的工作条件。
3. 铁路工程领域球墨铸铁可以用于制造铁路车辆的车轮、车轴和悬挂系统等重要零件。
它的高强度和耐磨性使铁路车辆能够在重负荷和恶劣工况下安全稳定地运行。
4. 其他领域除了上述领域,球墨铸铁还广泛应用于矿山设备、农业机械、建筑工程等领域。
它的优良性能和可靠性使其成为工业生产中的重要材料。
四、球墨铸铁的发展前景随着工业技术的不断进步和需求的增加,球墨铸铁的应用前景非常广阔。
首先,随着汽车工业的快速发展,球墨铸铁在汽车制造中的需求将继续增加。
高镍奥氏体蠕铁组织性能的研究 毕业论文
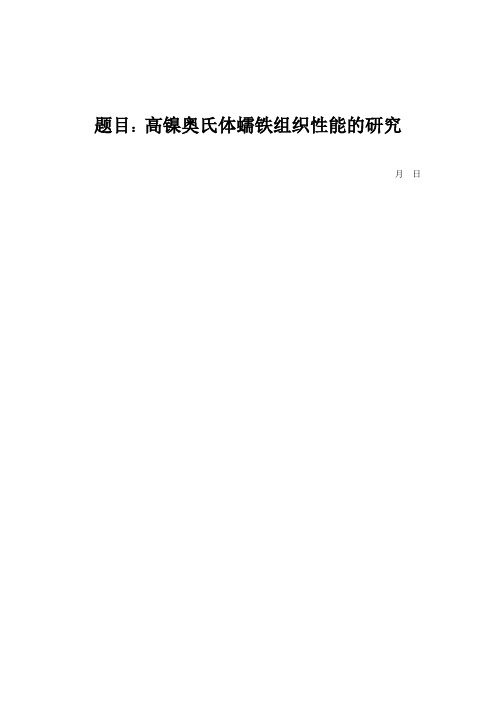
题目:高镍奥氏体蠕铁组织性能的研究月日高镍奥氏体蠕铁组织性能的研究摘要本文通过高镍蠕铁成分的设计,以及碳当量的合理配比,采用力学性能、金相分析和热膨胀系数实验,确定高镍蠕铁的合理成分并研究不同成分的蠕化剂配比对普通蠕铁的影响。
实验研究表明:高镍蠕铁进行蠕化处理时,蠕化剂采用Ni-Mg-Ti合金蠕化剂;采用坑内冲入法(Tundish),加入比例为 1.1%左右;能够得到很好地蠕虫状石墨;高镍蠕铁基体为奥氏体,具有良好的高温性能;普通蠕墨铸铁的延展性δ为7.14%、热膨胀系数为14.32×10-6℃-1、抗拉强度σb为378MPa;高镍蠕铁的延展性δ为14.4%、热膨胀系数为4.62×10-6℃-1、抗拉强度σb为334MPa。
关键词:高镍奥氏体蠕墨铸铁;组织;力学性能The research of High nickel austenitic vermicular cast ironAbstractIn this paper the design of Vermicular graphite cast iron components of th e high nickel, and a reasonable ratio of carbon equivalent, mechanical propertie s, metallographic analysis and the coefficient of thermal expansion experiments; determine the reasonable elements of vermicular graphite cast iron of high nic kel. Also studied the different components vermicular zing ratio of ordinary ver micular graphite cast iron.Experimental studies have shown that:vermicular graphite cast iron of high nickel creep treatment,the Vermicular zing Ni-Mg-Ti alloy Vermicular zing,and we can adopt tundish adding method with the addition about 1.1 per in weight,which spheroidal graphite with perfect vermicular graphite can be acquired;Vermicular graphite cast iron substrate, high-nickel austenite, has a good high temperature performance;Normal vermicular cast iron ductile δ is 7.14%, the ductility of δ thermal expansion coefficient is 14.32 x 10-6℃-1, tensile strength σb for 378 MPa;High nickel vermic ular graphite cast iron, ductile δ is 14.4%, the thermal expansion coefficient of 4.62 × 10-6 ℃-1, tensile strength the σb as 334MPa.Key words: High nickel austenitic vermicular cast iron; Microstructure; Mechanical properties目录1 绪论 (1)1.1前言 (1)1.2蠕墨铸铁以及高镍铸铁的发展历史及应用 (3)1.3我国研究现状 (4)1.4国外研究现状 (5)1.5蠕墨铸铁与高镍铸铁的组织、性能特点及应用 (6)1.5.1组织特点 (6)1.5.2性能特点 (6)1.5.3性能特点及应用 (7)1.6高镍蠕铁化学成分的分析及影响因素 (8)1.6.1高镍蠕铁化学成分的分析和确定 (8)1.6.2石墨形态的影响 (10)1.6.3共晶团的影响 (10)1.6.4基体组织的影响 (10)1.6.5合金化元素Cu和Mo的影响 (10)1.7课题研究的目的意义及主要研究内容 (11)1.7.1课题研究的目的意义 (11)1.7.2课题研究的主要内容 (11)2 实验条件和方法 (12)2.1实验材料 (12)2.2材料成分 (12)2.2.1成分配比 (12)2.2.2蠕化剂选取 (13)2.2.3制备方法 (14)2.3实验工艺 (14)2.4造型 (14)2.4.1圆棒试样 (14)2.4.2试样的制备 (15)2.5实验设备 (15)2.6实验方法 (16)2.6.1力学性能实验 (16)2.6.2金相组织及SEM-EDX分析 (16)3 实验结果及分析 (17)3.1镁基(不含Re)蠕化剂成分优化实验 (17)3.2 高镍奥氏体蠕铁金相组织分析 (19)3.3普通蠕铁与高镍奥氏体蠕铁力学性能 (21)3.4 普通蠕墨铸铁与高镍蠕铁热膨胀系数的测定 (22)4 结论 (23)参考文献 (24)1 绪论1.1前言国际形式的变化和世界兵器技术的发展,对陆军激动兵器的激战术性能提出了越来越高的要求。
球墨铸铁简介及用途

球墨铸铁简介及应用球墨铸铁是通过球化和孕育处理得到球状石墨,有效地提高了铸铁的机械性能,特别是提高了塑性和韧性,从而得到比碳钢还高的强度。
球墨铸铁是20世纪五十年代发展起来的一种高强度铸铁材料,其综合性能接近于钢,正是基于其优异的性能,已成功地用于铸造一些受力复杂,强度、韧性、耐磨性要求较高的零件。
球墨铸铁已迅速发展为仅次于灰铸铁的、应用十分广泛的铸铁材料。
所谓“以铁代钢”,主要指球墨铸铁。
简介生铁是含碳量大于2%的铁碳合金,工业生铁含碳量一般在2.5%--4%,并含C、SI、Mn、S、P等元素,是用铁矿石经高炉冶炼的产品。
根据生铁里碳存在形态的不同,又可分为炼钢生铁、铸造生铁和球墨铸铁等几种。
吉龙模具钢材析出的石墨呈球形的铸铁。
球状石墨对金属基体的割裂作用比片状石墨小,使铸铁的强度达到基体组织强度的70~90%,抗拉强度可达120kgf/mm2,并且具有良好的韧性。
球墨铸铁除铁外的化学成分通常为:含碳量3.6~3.8%,含硅量2.0~3.0%,含锰、磷、硫总量不超过1.5%和适量的稀土、镁等球化剂。
成分表目前市面上球墨铸铁光谱标准样品成分如下:国内历史在河南巩县铁生沟西汉中、晚期的冶铁遗址中出土的铁䦆,经过金相检验,具有放射状的球状石墨,球墨铸铁球化率相当于现代标准一级水平。
而现代的球墨铸铁则是迟至1947年才在国外研制成功的。
我国古代的铸铁,在一个相当长的时期里含硅量都偏低,也就是说,在约2000年前的西汉时期,我国铁器中的球状石墨,就已由低硅的生铁铸件经柔化退火的方法得到。
这是我国古代铸铁技术的重大成就,也是世界冶金史上的奇迹。
球墨铸铁以其优良的性能,在使用中有时可以代替昂贵的铸钢和锻钢,在机械制造工业中得到广泛应用。
国际冶金行业过去一直认为球墨铸铁是英国人于1947年发明的。
西方某些学者甚至声称,没有现代科技手段,发明球墨铸铁是不可想象的。
1981年,我国球铁专家采用现代科学手段,对出土的513件古汉魏铁器进行研究,通过大量的数据断定汉代我国就出现了球状石墨铸铁。
高镍球墨铸铁牌号

高镍球墨铸铁牌号
高镍球墨铸铁是一种高性能铸铁材料,具有优异的机械性能和耐
蚀性能。
在工业领域,它被广泛应用于制造耐磨、耐腐蚀和高强度要
求的零件。
下面,我将详细介绍几种常见的高镍球墨铸铁牌号。
1. GGG40.3
GGG40.3是一种高镍球墨铸铁牌号,主要由铸铁、球墨和适量的镍组成。
它具有优异的强度和韧性,适用于制造承受高载荷和冲击力的
零件,如汽车发动机零部件、风力发电机零件等。
2. GGG50
GGG50是另一种常见的高镍球墨铸铁牌号,其镍含量相对较高。
它具有较高的耐蚀性和耐磨性,适用于在强酸、强碱环境下工作的场合。
GGG50常用于制造化工设备、海洋设备和石油钻采设备等。
3. GGG60
GGG60是一种高强度高镍球墨铸铁牌号。
它具有很高的屈服强度和抗拉强度,适用于制造高负荷和高压力工作的零件,如机械传动零部件、卡车传动轴等。
4. GGG70
GGG70是镍含量较高的高镍球墨铸铁牌号。
它具有优异的耐蚀性和高温性能,可以在高温下工作。
GGG70常用于制造冶金设备、高温熔炼设备和高温热交换设备等。
除了以上几种常见的高镍球墨铸铁牌号,还有许多其他不同牌号的材料可以根据具体使用要求进行选择。
高镍球墨铸铁的性能可通过合适的热处理来提升,如铸态调质、热处理等方法。
总之,高镍球墨铸铁是一种具有优异性能的铸铁材料,广泛应用于工业领域。
凭借其高强度、高韧性和耐蚀性能,它被用于制造各种重要的零件和设备,为许多行业提供了可靠的解决方案。
铸态高镍奥氏体球墨铸铁稳定化生产

铸态高镍奥氏体球墨铸铁稳定化生产
史明;徐德立;田雨;熊云龙;陈瑞
【期刊名称】《铸造》
【年(卷),期】2018(067)001
【摘要】分析了一些主要元素对高镍奥氏体球铁组织和性能的影响,确定了合理的内控化学成分.球化处理采用冲入法,镍镁合金球化剂用量为铁液重量的
0.7%~0.9%,球化后高镍奥氏体球铁Mg残留量为0.07%~0.09%.采用硅铁和硅钡孕育剂炉前孕育,孕育剂用量为铁液量的1.0%~1.5%.采用以上工艺方法生产的铸态高镍奥氏体球铁力学性能合格率明显提高.
【总页数】4页(P62-65)
【作者】史明;徐德立;田雨;熊云龙;陈瑞
【作者单位】沈阳铸造研究所有限公司,辽宁沈阳110022;沈阳铸造研究所有限公司,辽宁沈阳110022;沈阳铸造研究所有限公司,辽宁沈阳110022;沈阳铸造研究所有限公司,辽宁沈阳110022;沈阳铸造研究所有限公司,辽宁沈阳110022
【正文语种】中文
【中图分类】TG143.5
【相关文献】
1.高镍奥氏体球墨铸铁显微缩松与碳化物的研究 [J], 程凤军;罗广思;潘安霞
2.高镍奥氏体球墨铸铁件缺陷分析及对策 [J], 赵新武
3.高镍奥氏体球墨铸铁支撑的材质及铸造工艺研究 [J], 陈庚;孙莹;李崇斌;刘勤鹏
4.铸态高镍球墨铸铁排气歧管的生产工艺 [J], 徐军霞;奚霞
5.D-5S高镍奥氏体球墨铸铁抗高温氧化性能研究 [J], 魏家强;程文;周宏伟;相永宇因版权原因,仅展示原文概要,查看原文内容请购买。
高Ni奥氏体球墨铸铁的生产
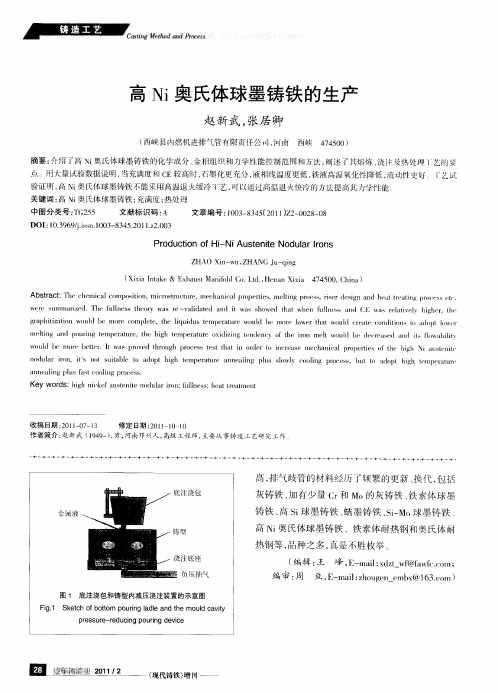
—
1; l
编审: 周
亘 ,- alzogn e x 6 【l) E m i hue mb @1 3 )1 : I
日
壁塑
现 铸 代 铁增
|
l
高 N 奥氏体球墨铸铁因其优异的抗热冲击性 、 i
抗 热蠕 变性 、 蚀性 、 温抗 氧化性 以及低 的热 膨胀 耐 高
表 1 奥 氏体铸铁化学成分( 一般工程用牌号 ) (rd sfr o ga e o mmo n ie r g s g s c ne gn e i u a e ) n
达 , 液流 动 性差 , 铁 补缩 困难 , 易产 生缩松 、 极 缩孔 缺 陷 。 资料 介绍 不 能大 于 44 , 笔者 经过 大量 有 .圳 但 1 试验( 见表 3认 为 , 观点有 待商榷 。 ) 此
12 CEa . l
传 统 的充 满 度 ( 称饱 和度 ) 论 l 为 : N 又 理 l 】 认 高 i
%( %) ( ) %
Tab 1 Che ial o p io fa sent a ti s . m c m ost nso u t i c s r c i e on
性和低 温冲击韧性 , 在国内外 被广泛用于制造海水 泵 、 增压器壳体 、 阀、 排气管 、 门座等耐热 、 气 耐蚀 的 零部件 。奥 氏体球墨铸铁具有原子紧密堆积的面心 立方晶格结构 , 在常温下具有稳定的奥 氏体组织 , 因 而 比普通球墨铸铁和硅钼球墨铸铁热 化学稳定性
魄 霞街堪 6 ¥ e 抟
__._
I
Cj
同
N 奥氏体球墨铸铁 的生产 i
赵新武 , 张居 卿
西峡 440 ) 75 0
( 西峡县 内燃机进排气管有限责任公 , 南 河
6高镍奥氏体球墨铸铁综述
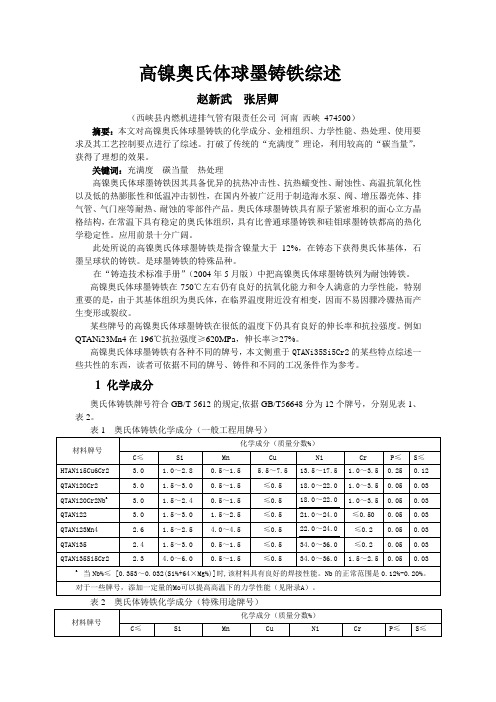
高镍奥氏体球墨铸铁综述赵新武张居卿(西峡县内燃机进排气管有限责任公司河南西峡474500)摘要:本文对高镍奥氏体球墨铸铁的化学成分、金相组织、力学性能、热处理、使用要求及其工艺控制要点进行了综述。
打破了传统的“充满度”理论,利用较高的“碳当量”,获得了理想的效果。
关键词:充满度碳当量热处理高镍奥氏体球墨铸铁因其具备优异的抗热冲击性、抗热蠕变性、耐蚀性、高温抗氧化性以及低的热膨胀性和低温冲击韧性,在国内外被广泛用于制造海水泵、阀、增压器壳体、排气管、气门座等耐热、耐蚀的零部件产品。
奥氏体球墨铸铁具有原子紧密堆积的面心立方晶格结构,在常温下具有稳定的奥氏体组织,具有比普通球墨铸铁和硅钼球墨铸铁都高的热化学稳定性。
应用前景十分广阔。
此处所说的高镍奥氏体球墨铸铁是指含镍量大于12%,在铸态下获得奥氏体基体,石墨呈球状的铸铁。
是球墨铸铁的特殊品种。
在“铸造技术标准手册”(2004年5月版)中把高镍奥氏体球墨铸铁列为耐蚀铸铁。
高镍奥氏体球墨铸铁在750℃左右仍有良好的抗氧化能力和令人满意的力学性能,特别重要的是,由于其基体组织为奥氏体,在临界温度附近没有相变,因而不易因骤冷骤热而产生变形或裂纹。
某些牌号的高镍奥氏体球墨铸铁在很低的温度下仍具有良好的伸长率和抗拉强度。
例如QTANi23Mn4在-196℃抗拉强度≥620MPa,伸长率≥27%。
高镍奥氏体球墨铸铁有各种不同的牌号,本文侧重于QTANi35Si5Cr2的某些特点综述一些共性的东西,读者可依据不同的牌号、铸件和不同的工况条件作为参考。
1 化学成分奥氏体铸铁牌号符合GB/T 5612的规定,依据GB/T56648分为12个牌号,分别见表1、表2。
表1 奥氏体铸铁化学成分(一般工程用牌号)表2 奥氏体铸铁化学成分(特殊用途牌号)注: QTANi35Si5Cr2牌:ASTM A439-83 C≤2.3. DIN1694-1981 C≤2.0。
ISO 2892:2007 C≤2.0。
奥氏体球墨铸铁标准

奥氏体球墨铸铁标准
奥氏体球墨铸铁的标准包括:
1. 化学成分:碳、硅、锰、硫、磷的含量应符合GB/T 13808的规定。
2. 力学性能:屈服强度基体材料不小于350MPa,硬度(布氏)为
140-260HB。
3. 基体组织:基体组织要有足够数量的基体α-石墨和铁素体。
如球
墨铸铁是非金属夹杂物数量较少、球铁中非金属材料数量较大,可以
看成具有多相组织的合金。
石墨球数不少于95%。
4. 铁素体和珠光体的含量:铁素体和珠光体的总量不大于5%。
此外,还有冲击试验、弯曲试验、拉伸试验、硬度试验、弯曲疲劳试
验等性能要求。
铸造厂家需通过技术经济指标、生产质量保证体系、球墨铸铁管的生
产能力、技术装备水平、生产经验等条件进行选择,也可以参考相关
行业标准。
奥氏体球墨铸铁是一种高级球墨铸铁,其综合性能优于普
通球墨铸铁。
特殊性能铸铁

5特殊性能铸铁5.1耐磨铸铁耐磨铸铁分为减摩铸铁和抗磨铸铁。
前者在有润滑、受粘着条件下工作,例如机床导轨、发动机缸套、活塞环、轴承等;后者在干摩擦的磨料磨损条件下工作,例如轧辊、磨球等。
5.1.1减摩铸铁减摩铸铁通常是在软基体上嵌有坚硬的强化相。
控制铸铁的化学成分和冷却速度获得细片状珠光体根本上能满足这种要求。
铸件的耐磨性随珠光体数量的增加而提高,细片状珠光体耐磨性比粗片状好;粒状珠光体的耐磨性不如片状珠光体。
故减摩铸铁希望得到片状珠光体。
托氏体和马氏体基体铸铁耐磨性更好。
球墨铸铁耐磨性比片状石墨铸铁好,但球墨铸铁吸振性差,铸造性能不如灰铸铁。
因此,减摩铸铁常用灰铸铁。
在灰铸铁的根底上,参加适量的Cu,Mo,Mn等元素,可以强化基体增加珠光体含量,有利于提高耐磨性;参加少量P形成磷共晶,参加V,Ti等碳化物形成元素形成稳定的,高硬度C,N化物质点,起支撑骨架作用,能显著提高耐磨性。
在灰铸铁根底上参加质量分数0.4%-0.7%的P形成高磷铸铁,由于高硬度的磷共晶细小而断续的分布,提高提高铸铁的耐磨性。
用高磷铸铁作机床床身,其耐磨性比孕育铸铁HT250提高一倍。
在高磷铸铁的根底上参加质量分数0.6%-0.8%的Cu和0.1%-0.5%的Ti,形成磷铜钛铸铁。
Cu在铸铁凝固时能促进石墨化并使石墨均匀分布,在共析转变时促进珠光体形成并使之细化。
少量Ti使石墨细化,并形成高硬度TiC。
因此磷铜钛铸铁耐磨性超过高磷铸铁和镍铬铸铁,是用于精细机床的一种重要构造材料。
利用我国钒钛资源参加一定量稀土硅铁,处理得到高强度稀土钒钛铸铁,其中ωv=0.18%-0.35%,ωTi=0.05%-0.15%。
钒钛是强碳化合物形成元素,能形成高硬度强化相质点,并能显著细化片状石墨和珠光体基体。
其耐磨性高于磷铜钛铸铁,比孕育铸铁HT300高约2倍。
近年来迅速开展了廉价的硼耐磨铸铁,其中ωB=0.02%-0.2%,形成珠光体基体加石墨加硼化物的铸铁组织。
球铁的金相组织
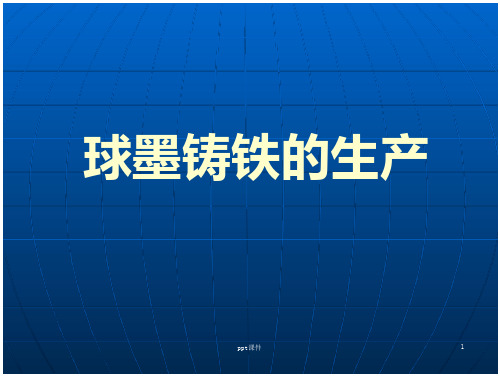
球墨铸铁的生产过程包含以下几个环节:熔炼合格的铁液,球化处理,孕育处理,炉前检查,浇注铸件,清理及热处理,铸件质量检查。在上述各个环节中,熔炼优质铁液和进行有效的球化—孕育处理是生产的关键。
1. 化学成分的选定
选择适当化学成分是保证铸铁获得良好的组织状态和高性能的基本条件,化学成分的选择既要有利于石墨的球化和获得满意的基体,以期获得所要求的性能,又要使铸铁有较好的铸造性能。
生产铸态珠光体球铁要遵循以下原则:
严格控制炉料(生铁与废钢),避免含有强烈形成碳化物元素如Cr、V、Mo、Te等,含锰量取下限,以防止铸态下形成游离渗碳体。适量孕育,一方面防止形成碳化物,另一方面还要防止因强化孕育导致出现大量的铁素体。根据铸件壁厚的性能要求,添加稳定珠光体,但又不形成碳化物的元素如Cu、Ni、Sn等,其中,添加铜的效果显著,成本较低(与添加镍相比),而且也无副作用(与添加锡相比)。在生产高强度珠光体球墨铸铁(抗拉强度要求超过700MPa)时,应采用纯净炉料、严格控制形成碳化物元素、干扰元素以及P、S等有害杂质元素的含量,必要时,还应添加适量的铜和钼。
1.4.3 铁素体-珠光体球墨铸铁
生产牌号QT500-7这种铁素体和珠光体混合基体的球铁时,可参考铁素体、珠光体球铁生产所必须遵循的原则。采用热处理生产铁素体-珠光体球铁时,参考生产退火铁素体球铁 所要求的化学成分,此时,可不必添加铜,只是在石墨化退火第二阶段,缩短保温时间,令其中的部分珠光体转变成铁素体,其余部分则保留下 来,组成混合基体。视所要求的铁素体与珠光体的相对含量,决定缩短 第二阶段的保温时间,要求的铁素体越多,则要缩短的保温时间就越短。采用铸态生产铁素体-珠光体球铁时,参考生产铸态铁素体球铁要遵循的原则。在此基础上,通过控制添加铜的数量,以获得铁素体与珠光体的混合基体,随加铜量的增多,珠光体量增加。
- 1、下载文档前请自行甄别文档内容的完整性,平台不提供额外的编辑、内容补充、找答案等附加服务。
- 2、"仅部分预览"的文档,不可在线预览部分如存在完整性等问题,可反馈申请退款(可完整预览的文档不适用该条件!)。
- 3、如文档侵犯您的权益,请联系客服反馈,我们会尽快为您处理(人工客服工作时间:9:00-18:30)。
高镍奥氏体球墨铸铁综述赵新武张居卿(西峡县内燃机进排气管有限责任公司河南西峡474500)摘要:本文对高镍奥氏体球墨铸铁的化学成分、金相组织、力学性能、热处理、使用要求及其工艺控制要点进行了综述。
打破了传统的“充满度”理论,利用较高的“碳当量”,获得了理想的效果。
关键词:充满度碳当量热处理高镍奥氏体球墨铸铁因其具备优异的抗热冲击性、抗热蠕变性、耐蚀性、高温抗氧化性以及低的热膨胀性和低温冲击韧性,在国内外被广泛用于制造海水泵、阀、增压器壳体、排气管、气门座等耐热、耐蚀的零部件产品。
奥氏体球墨铸铁具有原子紧密堆积的面心立方晶格结构,在常温下具有稳定的奥氏体组织,具有比普通球墨铸铁和硅钼球墨铸铁都高的热化学稳定性。
应用前景十分广阔。
此处所说的高镍奥氏体球墨铸铁是指含镍量大于12%,在铸态下获得奥氏体基体,石墨呈球状的铸铁。
是球墨铸铁的特殊品种。
在“铸造技术标准手册”(2004年5月版)中把高镍奥氏体球墨铸铁列为耐蚀铸铁。
高镍奥氏体球墨铸铁在750℃左右仍有良好的抗氧化能力和令人满意的力学性能,特别重要的是,由于其基体组织为奥氏体,在临界温度附近没有相变,因而不易因骤冷骤热而产生变形或裂纹。
某些牌号的高镍奥氏体球墨铸铁在很低的温度下仍具有良好的伸长率和抗拉强度。
例如QTANi23Mn4在-196℃抗拉强度≥620MPa,伸长率≥27%。
高镍奥氏体球墨铸铁有各种不同的牌号,本文侧重于QTANi35Si5Cr2的某些特点综述一些共性的东西,读者可依据不同的牌号、铸件和不同的工况条件作为参考。
1 化学成分奥氏体铸铁牌号符合GB/T 5612的规定,依据GB/T56648分为12个牌号,分别见表1、表2。
表1 奥氏体铸铁化学成分(一般工程用牌号)表2 奥氏体铸铁化学成分(特殊用途牌号)注: QTANi35Si5Cr2牌:ASTM A439-83 C≤2.3. DIN1694-1981 C≤2.0。
ISO 2892:2007 C≤2.0。
意大利标准C≤2.4。
QTANi35Si5Cr2为依据ISO 2892:2007编制的国家标准牌号(未发布)。
1.1 充满度理论⑶传统的充满度理论认为:高镍奥氏体球铁中的碳、硅、镍含量必须满足饱和度公式:A ≥TC%+0.2Si%+0.06Ni%。
式中A称为饱和度,当铁液中的碳、硅、镍大于某一极限值(饱和度A)时则石墨形态就呈碎块状分布;奥氏体枝晶发达,铁液流动性差,补缩困难,极易产生缩松、缩孔缺陷。
有资料介绍A不能大于4.4⑴⑵。
这一理论禁区能不能突破?我们经过大量的试验,打破了充满度理论的禁区(见表3)。
生产中实测化学成分表31.2 碳当量按照公式CE=C%+0.33(Si%)+0.047(Ni%)-0.0055(Si%)(Ni%)。
CE计算结果见表2。
按照公式CE=15.7826-0.0096575T1T1的计算结果见表2。
从计算结果可以看出,1~4次试验饱和度在4.95~5.15范围内波动,CE在4.35 ~4.44范围内波动。
T1在1174℃~1192℃范围内波动。
5~8次试验饱和度在5.27~5.31范围内波动,CE在4.49~4.62范围内波动。
T1在1156℃~1170℃范围内波动。
在保证化学成分的前提下饱和度相差0.36,CE量相差0.27,温度相差36度。
当然T1是推算结果。
在实际生产中由于采用了较高的碳当量,铁液的流动性提高了,并且熔炼温度从最初的1680℃下调到1620℃。
在生产涡轮壳产品时甚至出炉温度在1575℃,浇注温度低于1500℃,残留镁量≤0.09%(质量分数)的情况下,同样生产出了金相组织和力学性能合格的铸件。
1.3 关于饱和度的验证阶梯形试块见图1。
图1 阶梯状试块为了验证在不同厚度、不同饱和度、不同碳当量、不同温度下的球化效果和力学性能,我们制作了阶梯形试块。
试验在生产高镍产品时进行。
试块厚度6mm 、12mm 、24mm 、36mm 。
试块的球化处理工艺与产品相同(原铁液碳高,硅低。
包底用75硅铁覆盖,硅锶孕育剂二次孕育)。
出炉温度1620℃,包头浇注温度1530℃,包尾浇注温度1460℃。
饱和度5.19。
碳当量4.46。
推算出液相线温度T 11172℃。
包头、包尾各浇一箱。
随流孕育。
冷却后分别对6mm 、12mm 、24mm 、36mm 的部位解剖后检测球化率。
任取5个视场取其平均值。
见表3。
不同壁厚的球化率表 32 金相组织2.1 不同壁厚下的球化率从表3 包头、包尾的球化率来看,随着试块厚度的增加,球化率有所下降,从图2的图片可以看到36mm 处已有团絮状石墨出现。
但笔者认为这不是充满度过高造成的。
这种现象符合球墨铸铁的凝固规律。
球化处理一旦结束,球化衰退已经开始了,随着时间的推移非球状石墨会越来越多。
从表中可以看出球化率随着厚度的增加而逐渐下降。
也可以说当残留镁量相同时,越厚的地方,凝固时间越长;球化率就越低。
由于包头的残留镁量高,浇注温度也高,凝固缓慢。
包尾的残留镁量低,浇注温度也低,凝固较块。
使得包头包尾的球化率在规定的时间内都在要求的范围。
以上分析可以这样认为,残留镁量、浇注温度、凝固时间、球化率都建立了一一对应的关系。
包头 6mm 壁厚 球化率94%包头 36mm 壁厚 球化率84%包尾 6mm 壁厚 球化率92% 包尾 36mm 壁厚 球化率82%图2 同一包铁水浇铸的试块2.2 不同标准规定的球化率图3 国外某公司的奥氏体球墨铸铁金相厚壁处石墨形态图3是某国外的标准规定合格的金相组织,从图片中明显的可以看出厚壁处的碎块状石墨,4mm 厚的管壁距表层0.3mm 处的衰退石墨和脱碳层。
图4 西排公司生产的奥氏体球墨铸铁金相依据我们的生产经验在制定《奥氏体铸铁件》的国家标准中规定,奥氏体铸铁件的球化率≥4级。
并把ISO 标准中碳≥2.0%修改为≥2.3%就是基于我们对“充满度”和“碳当量”的认识。
2.3 国标规定的金相组织奥氏体球墨铸铁的金相组织:奥氏体+少量晶界碳化物+球状石墨。
球化级别不低于4级,石墨大小5~7级。
如有特殊要求,球化级别由供需双方商定。
在国外的诸多标准中仅对化学成分和力学性能作了明确的规定,但未对奥氏体球墨铸铁的金相组织作出具体的规定。
3 力学性能力学性能见表4表4奥氏体铸铁的力学性能(一般工程用牌号)表4 奥氏体铸铁的力学性能(特殊用途牌号)从表4可以看出,奥氏体球墨铸铁的抗拉强度较低,它适合于耐热、耐蚀、对磁性有要求的场合,适合于做结构件,而不适合于做较强的承载件。
需要指出的是,通过高温退火快速冷却,可使基体组织得到固溶强化,力学性能仍有提升的空间。
4 熔炼工艺高镍奥氏体铸件的镍含量在12 ~36%,基体组织为奥氏体。
耐热、耐蚀性能类似于奥氏体不锈钢。
铸造性能则类似于普通球墨铸铁。
属于糊状凝固,缩松倾向大。
4.1 熔炼熔炼大都采用无芯中频电炉。
炉料一般由低硫生铁、无锈废钢、镍、高碳铬铁、75硅铁、高碳锰铁和回炉料构成。
炉料中要特别注意微量元素的影响。
应特别注意避免混入铅和铝。
原铁水中含0.003%的铅,显微组织中就可能出现魏氏石墨,使力学性能明显降低。
铝则可能使铸件中出现针孔缺陷。
炉料一定要干净纯洁,避免有害元素的混入。
例如Pb、Ti、As等。
使用南非的高纯生铁,质量一直很稳定,我们曾试图使用国产的Q10生铁,在冒口处发现有片状石墨。
后在使用南非生铁生产时也发现有片状石墨。
见图9。
经过分析认为电炉熔炼蠕铁材质后接着熔炼高镍材质,混入了微量元素(如Ti),高镍材质不含稀土元素,无法抵消微量有害元素的影响,估计微量有害元素的干扰是产生片状石墨的原因。
后把熔炼顺序改为生产普通球铁后再生产高镍球墨铸铁,并加强炉料的管理。
这一现象得到了消除。
增碳剂一定用速溶增碳剂在低温加入。
镍有极强的吸气性,为防止铁液吸气,镍板在熔炼后期加入,铁液要覆盖熔炼。
铬铁等合金最好在光谱测量原铁水成分后调整成分时加入。
Q10生铁球化率86%(有片墨) 南非生铁球化率90%(有片墨)图9 不同生铁均有片状石墨奥氏体球墨铸铁熔炼过程中吸气倾向大于一般球墨铸铁,炉料中回炉料多时吸气倾向更大,因此,有锈、有油污或潮湿的炉料只能投入没有铁液的热炉中,不可在有铁液时投入。
此外,应特别注意不能使用带红色铁锈的炉料,因其中含氢氧化铁,其稳定性很强,在320℃以下不易分解,氢不易形成水分析出而蒸发。
炉料中的磷含量必须在0.05%以下,含磷量高,就可能在晶界上析出磷共晶,从而造成晶界腐蚀,导致铸件渗漏、破裂。
石墨熔入镍含量高的铁液比较缓慢,因而不宜用石墨处理。
为使生铁锭和回炉料中的石墨能充分溶于铁液中,这两种炉料应放在首批料中,早期装炉。
如在后期外加这类含石墨的炉料,则加入后至少应在过热条件保温10分钟。
熔炼过程中,应避免太高的过热温度和过长的保温时间,回炉料也不宜多次反复使用,这些因素都会导致铸铁的过冷度增大,使组织中碳化物含量增多。
如果生产中铸件产生气孔的问题严重,应考虑采用吹氩除气工艺。
4.2 球化处理奥氏体球墨铸铁应采用不含稀士的球化剂。
在相同的条件下进行球化处理,奥氏体球墨铸铁中镁的收得率可能比一般球墨铸铁高20%~30%,而且在此后转运和浇注过程中镁的衰减也较慢。
为改善组织中的石墨形态并提高拉伸试验时试样的伸长率,奥氏体球墨铸铁中的残留镁量应略高于一般球墨铸铁,有时可高达0.10%。
当然,残留镁量高于0.06%时,铸件中易于出现渣孔。
如果采用较低的浇注温度,而且孕育处理得当,也可以在残留镁较低(0.04%~0.05%)的情况下得到良好的石墨组织。
4.3 孕育处理奥氏体球墨铸铁孕育处理后,孕育效果的衰退比一般球墨铸铁快。
因此,应注意做好孕育处理并安排好孕育后的转运和浇注作业。
特别是含铬的奥氏体球墨铸铁,孕育不好,铸件很容易产生缩孔、缩松缺陷,而且加工性能也会恶化。
为得到良好的孕育效果,要注意以下几点:在熔炼的后期加入铬铁;最后加入锰铁和硅铁;炉前孕育处理用75%的硅铁细粒,加入的硅量约为0.5%;浇注时用硅锶孕育剂进行随流孕育,加入量为0.2%左右,孕育剂的粒度为20~40目,切忌用200目以下的细粉。
4.4浇注铁液中加入大量的镍,会使液相线温度提高。
因此,奥氏体球墨铸铁的浇注温度要比一般球墨铸铁高。
要留意残留镁量、浇注温度和浇注速率三者之间的关系。
残留镁量高时,宜采用较高的浇注温度和较高的浇注速率。
如残留镁量较高而浇注温度较低,则铸件中易形成浮渣缺陷。
以提高浇注温度来防止浮渣缺陷,可能导致收缩缺陷。
5 铸件冒口的设置奥氏体球墨铸铁中的镍含量高,会使碳在奥氏体中的固溶度降低。
因此,虽然奥氏体球墨铸铁中的碳含量较低,但在凝固过程中析出的石墨量与一般球墨铸铁凝固过程中析出的石墨量却相差不多。