特种铸造之挤压铸造
挤压铸造
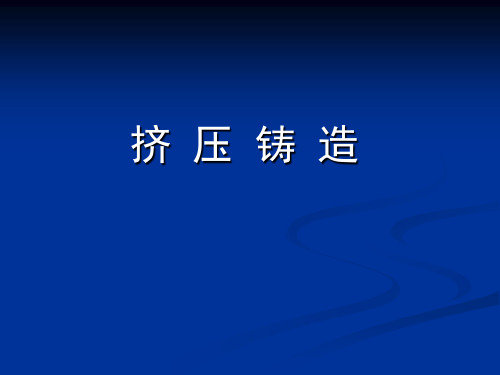
(4)便于实现机械化、自动化,可大大减轻工人的劳动强 度,改善铸造车间劳动条件。加之,挤压铸造通常没有浇冒 口,毛坯精化,铸件尺寸精度高,因而金属材料的利用率高, 可以减少切削加工量。所有这些,均有利于降低成本,提高 生产效率。与重力铸造相比,它可以提高铸件质量,减少废 品率。 (5)挤压铸造是通过压力传递进行补缩的,工艺的应用会 受到某些限制。对于薄壁零件和一些形状复杂的零件,因为 铸件冷凝速度快,有时来不及加压就凝固了,另外,直接式 挤压铸造通常无浇冒口系统,浇注的金属全部成形为铸件。 因此,铸件的高度是由浇入金属的量决定的。即其高度方向 的尺寸精度取决于定量浇注的精确程度。
二、挤压铸造技术发展概况
挤压铸造技术在30年代前就问世了,40至50年代中在 前苏联得到了推广应用,60年代末期有色金属挤压铸造在 日本得到了应用和发展。 我国挤压铸造技术的发展大体上可分为四个阶段。
第一阶段
50—60年代中末期为工艺探索阶段。50年代到60年代初 如武昌造船厂与华中科技大学协作的铜合金挤压铸造;杭 州前氧机厂,沈阳冶金机械专科学校等开展这方面的试验 研究工作;大连造船厂的高压阀体铸锻联合工艺等,都是 我国首批研究与试验生产的单位。
整体凹型
垂直分型凹型
水平分型凹型
复合分型凹型
带芯棒凹型
铸件收缩率:由于铸件凝固在封闭的金属型中受 高压作用进行,故铸件收缩较小,比常规数值小 一半。 加工余量:垂直合型挤压铸造时铸件加工面上的 加工余量可取较小,有色合金铸造时可选取 0.5~2mm,铸钢取3~5mm。
型腔表面粗糙度常取Ra6.3~0.8μm,铸造圆角半 径2~10mm,铸造斜度为1~3度。
适用范围
1、在材料种类方面适用性较广,可用于生产各种类型的 合金,如铝合金、锌合金、铜合金、灰铸铁、球墨铸铁、 碳钢、不锈钢等。 2、对于一些复杂且性能上有一定要求的零件,采用挤压 铸造合适。因为挤压铸造既能容易成形,又能保证产品性 能的要求。 3、在工件壁厚方面,一般来讲不能太薄,否则将给成形 带来困难。
挤压铸造文档
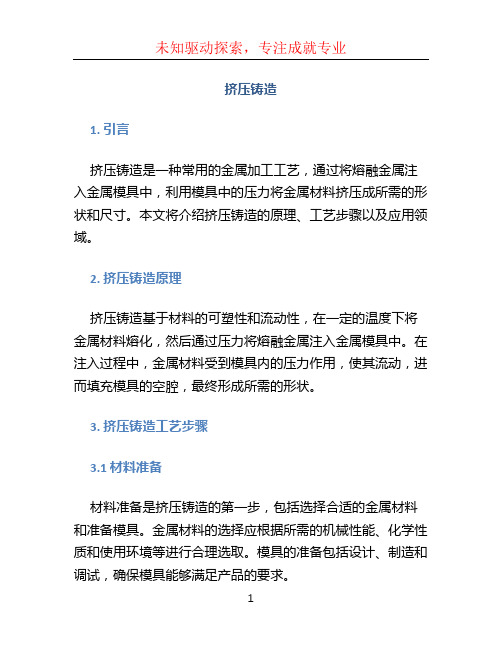
挤压铸造1. 引言挤压铸造是一种常用的金属加工工艺,通过将熔融金属注入金属模具中,利用模具中的压力将金属材料挤压成所需的形状和尺寸。
本文将介绍挤压铸造的原理、工艺步骤以及应用领域。
2. 挤压铸造原理挤压铸造基于材料的可塑性和流动性,在一定的温度下将金属材料熔化,然后通过压力将熔融金属注入金属模具中。
在注入过程中,金属材料受到模具内的压力作用,使其流动,进而填充模具的空腔,最终形成所需的形状。
3. 挤压铸造工艺步骤3.1 材料准备材料准备是挤压铸造的第一步,包括选择合适的金属材料和准备模具。
金属材料的选择应根据所需的机械性能、化学性质和使用环境等进行合理选取。
模具的准备包括设计、制造和调试,确保模具能够满足产品的要求。
3.2 加热与熔化将金属材料放入熔炉中进行加热,直到达到熔点,使其变为熔融状态。
在加热过程中,需要注意控制加热温度和时间,避免金属材料的过热或烧损。
3.3 挤压铸造将熔融金属通过挤压机的压力注入预热好的金属模具中。
在注入的过程中,可以通过控制挤压机的压力和速度来控制金属材料的流动性和填充性能。
在注入后,保持一定时间以保证金属材料充分冷却和凝固。
3.4 冷却与脱模经过一定时间的冷却后,金属材料逐渐凝固,然后可以进行脱模。
脱模可以通过拆卸模具或者采用其他合适的方法进行。
3.5 后处理在脱模后,需要对挤压铸造件进行后处理,包括切割、修整、清洁和检测等步骤。
通过后处理可以使挤压铸造件达到所需的尺寸、表面光洁度和质量要求。
4. 挤压铸造的应用领域挤压铸造广泛应用于各个行业,特别是在汽车、航空航天、电子和家电等领域。
以下是挤压铸造的一些常见应用: - 汽车行业:引擎零部件、车身结构件、车轮等。
- 航空航天行业:飞机结构件、发动机零部件等。
- 电子行业:散热器、电子外壳等。
- 家电行业:厨具、灯具等。
5. 结论挤压铸造是一种重要的金属加工工艺,具有高效、精密、经济的特点。
通过合理的工艺控制和材料选择,可以获得高质量的挤压铸造件。
挤压铸造
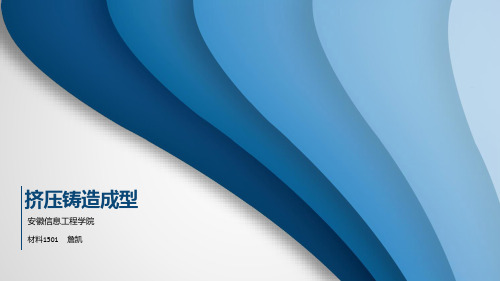
挤压铸造成型
3.在挤压铸造工艺中应用人工神经网络 挤压铸造工艺参数的确定主要靠经验,而且这些参数很难确定,人 工神经网络是一个比较新的学科,在非线性系统、错误诊断、预测、 自适应控制等方面已取得了很大成功。但我国才刚刚起步,应加强 对人工神经网络预测挤压铸造工艺参数的研究。
挤压铸造成型
应用实例:
挤压铸造成型
7.铸型涂料 为了防止铸件黏焊铸型,使铸件能顺利地从型腔中取出,以降低铸件表
面粗糙度,提高铸型的寿命,减缓金属液在加压前的结壳速度,以利于金 属液在压力下充型,在挤压铸型的表面一般都必须喷涂涂料。在挤压铸造 中不能采用涂料层来控制铸件的凝固,因为施加在金属液上的高压将使涂 料层剥落,引起铸件产生夹杂缺陷,为此,采用50μm左右的薄层涂料。。
挤压铸造成型
适用范围:
1、在材料种类方面适用性较广,可用于生产各种类型的合金,如铝合 金、锌合金、铜合金、灰铸铁、球墨铸铁、碳钢、不锈钢等。
2、对于一些复杂且性能上有一定要求的零件,采用挤压铸造合适。 因为挤压铸造既能容易成形,又能保证产品性能的要求。
3、在工件壁厚方面,一般来讲不能太薄,否则将给成形带来困难。
挤压铸造成型
1.工艺原理及特点 (1)工艺原理 将一定量的液体金属(或半固态金属)浇入金属
型腔内,通过冲头以高压(50〜100MPa)作用于液体金属上, 使之充型、成形和结晶凝固,并产生一定塑性形变,从而获得优 质铸件。
(a)熔化
(b)充型
(c)挤压
(d)顶出铸件
挤压铸造成型
(2)工艺特点 适用的材料范围较宽,不仅是普通铸造合金,也适用于高性能的变形合金,
挤压铸造成型
安徽信息工程学院 材料1501 詹凯
目录
挤压铸造工艺简介
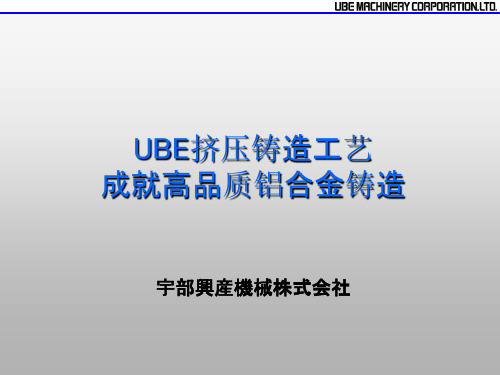
应力 [MPa]
200
180
160
σu=143MPa
140
120
100
80
σu=67MPa
60
普通压铸
40
挤压铸造
20
0
104
105
106
107
108
重复次数(Cycle) [次]
3.挤压铸造工艺的应用实例
3.挤压铸造工艺的应用实例
ABS valve body
压射单元的
YY
小型化
・压射行程
350T
800T
・油缸直径
X 3,250mm 4,100mm
XX
・熔杯直径
Y 2,600mm 3,400mm
・熔杯回倾角度
Z 2,000mm 3,700mm
1.挤压铸造工艺的概要
UBE压铸机的开发历史
昭和 35年
1960年
45年 1970年
55年 1980年
平成 2年 1990年
650
AC4CH挤压铸造 AZ91挤压铸造 600
AZ91普通铸造 550
AC4CH普通铸造
AC4CH熔点: 615℃ AZ91熔点: 595℃
热电偶
0
10
20
30
40
注汤后的时间经过 (sec)
熔杯内温 度测定
2.挤压铸造件的特征
2.挤压铸造品德特征
换挡片内部品质比较/A390合金(ADC14相当)
・射出速度:max. 10 m/s
1.挤压铸造工艺的概要
UBE挤压铸造机的出厂数量
Europe: 38 sets
挤压铸造原理及缺陷分析

挤压铸造原理及缺陷分析挤压铸造是一种将熔融金属挤压入模具中制造零件的方法。
其原理是通过一个称为挤压器的设备,在高温下应用高压将熔融金属挤压入永久性金属模具中,形成所需形状的零件。
这种工艺是高效率、高精度和高可靠性的制造方法之一。
挤压铸造的过程是将熔化的金属通过压力挤压入设计好的金属模具中。
在挤压过程中,金属将受到高度的压缩力,以使其具有所需的形状和结构。
这种挤压过程需要高度的技巧和专业知识,以确保零件的质量可靠。
挤压铸造的优点包括高精度、高品质、高效率、低成本、短周期、较少的加工量和高重复性。
另外,挤压铸造可用于制造一些常规铸造方法无法制造的零件。
挤压铸造过程中存在的缺陷包括:1. 内部气孔:在挤压过程中,熔化的金属流动性良好,但可能会导致在制造过程中产生气泡。
这些气泡会影响零件的质量和强度,甚至可能导致零件崩溃。
2. 金属受力不均:在挤压过程中,金属受到的压力和力量可能不均匀分布,这可能导致零件的某些区域强度低下。
3. 熔化的金属会受到冷却:在挤压过程中,金属会受到自然冷却。
这可能会降低材料的可加工性,并影响零件的准确度和质量。
4. 模具磨损:在整个挤压过程中,模具接触熔化的金属多次,并经受高压挤压力作用。
这可能导致模具表面磨损、裂纹或其它缺陷,进而影响零件质量。
5. 长时间的实验和制造周期:挤压铸造通常需要花费较长的时间来制造。
这可能导致生产周期较长,并且对公司的成本和效率产生不利影响。
总之,虽然挤压铸造具有创新性、可靠性和高效性等优点,但同时也存在一些缺陷,需要在制造过程中得到控制和解决。
特种铸造简介
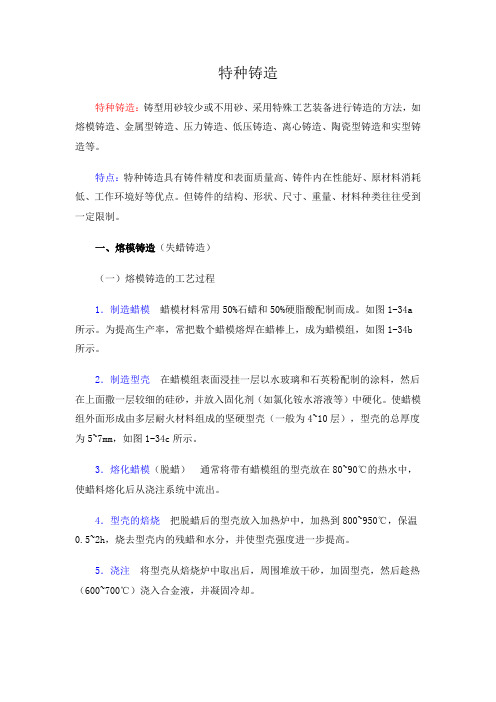
特种铸造特种铸造:铸型用砂较少或不用砂、采用特殊工艺装备进行铸造的方法,如熔模铸造、金属型铸造、压力铸造、低压铸造、离心铸造、陶瓷型铸造和实型铸造等。
特点:特种铸造具有铸件精度和表面质量高、铸件内在性能好、原材料消耗低、工作环境好等优点。
但铸件的结构、形状、尺寸、重量、材料种类往往受到一定限制。
一、熔模铸造(失蜡铸造)(一)熔模铸造的工艺过程1.制造蜡模蜡模材料常用50%石蜡和50%硬脂酸配制而成。
如图1-34a 所示。
为提高生产率,常把数个蜡模熔焊在蜡棒上,成为蜡模组,如图1-34b 所示。
2.制造型壳在蜡模组表面浸挂一层以水玻璃和石英粉配制的涂料,然后在上面撒一层较细的硅砂,并放入固化剂(如氯化铵水溶液等)中硬化。
使蜡模组外面形成由多层耐火材料组成的坚硬型壳(一般为4~10层),型壳的总厚度为5~7mm,如图1-34c所示。
3.熔化蜡模(脱蜡)通常将带有蜡模组的型壳放在80~90℃的热水中,使蜡料熔化后从浇注系统中流出。
4.型壳的焙烧把脱蜡后的型壳放入加热炉中,加热到800~950℃,保温0.5~2h,烧去型壳内的残蜡和水分,并使型壳强度进一步提高。
5.浇注将型壳从焙烧炉中取出后,周围堆放干砂,加固型壳,然后趁热(600~700℃)浇入合金液,并凝固冷却。
6.脱壳和清理用人工或机械方法去掉型壳、切除浇冒口,清理后即得铸件。
(二)熔摸铸造铸件的结构工艺性熔摸铸造铸件的结构,除应满足一般铸造工艺的要求外,还具有其特殊性:1.铸孔不能太小和太深否则涂料和砂粒很难进入腊模的空洞内,只有采用陶瓷芯或石英玻璃管芯,工艺复杂,清理困难。
一般铸孔应大于2mm.。
2.铸件壁厚不可太薄一般为2~8mm。
3.铸件的壁厚应尽量均匀熔摸铸造工艺一般不用冷铁,少用冒口,多用直浇口直接补缩,故不能有分散的热节。
(三)熔模铸造的特点和应用熔模铸造的特点是:(1)铸件精度高、表面质量好,是少、无切削加工工艺的重要方法之一,其尺寸精度可达IT11~IT14,表面粗糙度为Ra12.5~1.6μm。
压力铸造、挤压铸造及气压铸造成形技术
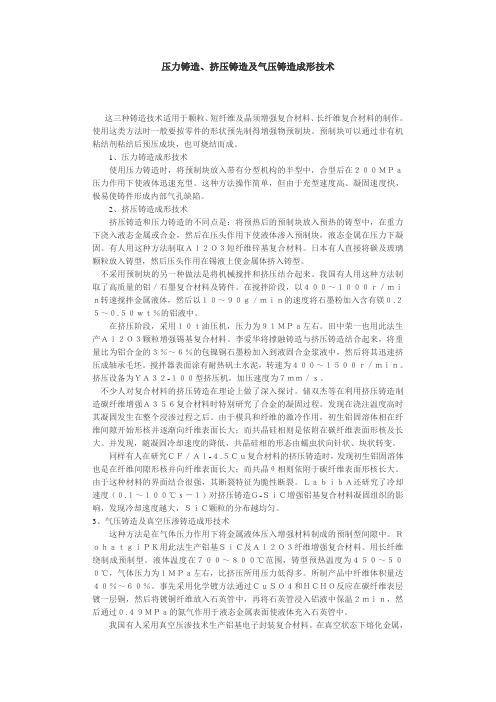
压力铸造、挤压铸造及气压铸造成形技术这三种铸造技术适用于颗粒、短纤维及晶须增强复合材料、长纤维复合材料的制作。
使用这类方法时一般要按零件的形状预先制得增强物预制块。
预制块可以通过非有机粘结剂粘结后预压成块,也可烧结而成。
1、压力铸造成形技术使用压力铸造时,将预制块放入带有分型机构的半型中,合型后在200MPa压力作用下使液体迅速充型。
这种方法操作简单,但由于充型速度高、凝固速度快,极易使铸件形成内部气孔缺陷。
2、挤压铸造成形技术挤压铸造和压力铸造的不同点是:将预热后的预制块放入预热的铸型中,在重力下浇入液态金属或合金,然后在压头作用下使液体渗入预制块,液态金属在压力下凝固。
有人用这种方法制取Al2O3短纤维锌基复合材料。
日本有人直接将碳及玻璃颗粒放入铸型,然后压头作用在锡液上使金属体挤入铸型。
不采用预制块的另一种做法是将机械搅拌和挤压结合起来。
我国有人用这种方法制取了高质量的铝/石墨复合材料及铸件。
在搅拌阶段,以400~1000r/min转速搅拌金属液体,然后以10~90g/min的速度将石墨粉加入含有镁0.25~0.50wt%的铝液中。
在挤压阶段,采用10t油压机,压力为91MPa左右。
田中荣一也用此法生产Al2O3颗粒增强锡基复合材料。
李爱华将撑融铸造与挤压铸造结合起来,将重量比为铝合金的3%~6%的包镍铜石墨粉加入到液固合金浆液中,然后将其迅速挤压成轴承毛坯。
搅拌器表面涂有耐热矾土水泥,转速为400~1500r/min。
挤压设备为YA32-100型挤压机,加压速度为7mm/s。
不少人对复合材料的挤压铸造在理论上做了深入探讨。
储双杰等在利用挤压铸造制造碳纤维增强A356复合材料时特别研究了合金的凝固过程。
发现在浇注温度高时其凝固发生在整个浸渗过程之后。
由于模具和纤维的激冷作用,初生铝固溶体相在纤维间隙开始形核并逐渐向纤维表面长大;而共晶硅相则是依附在碳纤维表面形核及长大。
并发现,随凝固冷却速度的降低,共晶硅相的形态由蠕虫状向针状、块状转变。
特种铸造之压力铸造

真空压铸镁合金
真空压铸铝件
4.1 铸造在压力下成形特征
但是在此机器上装斜和维护铸型比较麻烦,生产效率较 前两种冷压室压铸机低。
4.1.2 压铸时金属流的特征
压力铸造过程的主要特征就是金属在高压作用下的高速填充型腔。 因此欲掌握压铸件成型实质,主要就应了解压力铸造时金属充型过程中 的所受压力变化,充型时金属的流动形态,以便采取合适的技术措施, 充分运用压铸时金属充型特殊现象的有利方面,避免和克服此现象可能 带来的负面影响,高效地制造出质量符合要求的压铸件。
的致密度。此一增大的压力值一直保持到型内铸件完全凝固。
最终的压力值可为50~500MPa。
2、压铸时金属填充型腔的形态——理论假设
A 弗洛梅尔(Frommer)理论
Frommer 1932
1 当金属流经浇口进入型腔后,仍 保持浇口的断面直向型腔远端的对面型 壁射去;
2 待到达对面型壁厚,在此处的型 腔中聚积,消失了冲击力后,沿型壁在 整个型腔断面上反向移动。型腔中的空 气和随金属六进入型腔的空气依靠金属 液充型时的压力挤出型外: 如果浇口横截面积较小(浇口截面积 f/型腔截面积F>(1/3~1/4))反向流动平 稳,金属液以小的旋转涡流形式移动; 如果浇口截面积较大(f/F<1/3),则 液流速度高,返回流回呈现为强烈的涡 状紊流。
在后续进入型腔金属的补充 下,沿型腔整个断面向正对 浇口的另一端型腔填充,直 至充满型腔。
挤压铸造原理及缺陷分析
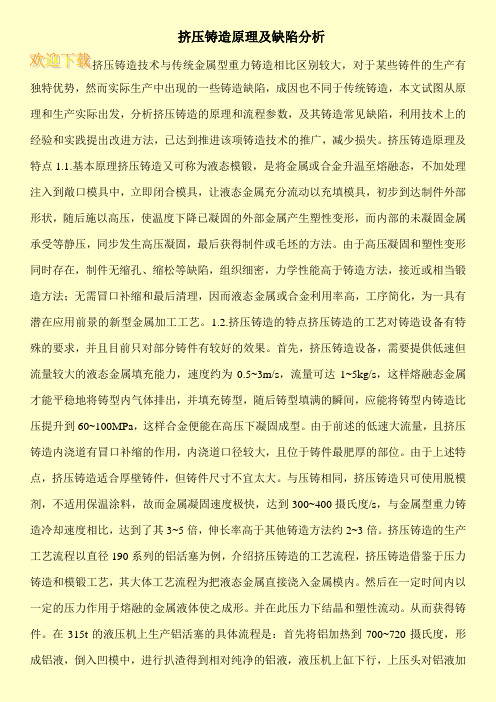
挤压铸造原理及缺陷分析挤压铸造技术与传统金属型重力铸造相比区别较大,对于某些铸件的生产有独特优势,然而实际生产中出现的一些铸造缺陷,成因也不同于传统铸造,本文试图从原理和生产实际出发,分析挤压铸造的原理和流程参数,及其铸造常见缺陷,利用技术上的经验和实践提出改进方法,已达到推进该项铸造技术的推广,减少损失。
挤压铸造原理及特点1.1.基本原理挤压铸造又可称为液态模锻,是将金属或合金升温至熔融态,不加处理注入到敞口模具中,立即闭合模具,让液态金属充分流动以充填模具,初步到达制件外部形状,随后施以高压,使温度下降已凝固的外部金属产生塑性变形,而内部的未凝固金属承受等静压,同步发生高压凝固,最后获得制件或毛坯的方法。
由于高压凝固和塑性变形同时存在,制件无缩孔、缩松等缺陷,组织细密,力学性能高于铸造方法,接近或相当锻造方法;无需冒口补缩和最后清理,因而液态金属或合金利用率高,工序简化,为一具有潜在应用前景的新型金属加工工艺。
1.2.挤压铸造的特点挤压铸造的工艺对铸造设备有特殊的要求,并且目前只对部分铸件有较好的效果。
首先,挤压铸造设备,需要提供低速但流量较大的液态金属填充能力,速度约为0.5~3m/s,流量可达1~5kg/s,这样熔融态金属才能平稳地将铸型内气体排出,并填充铸型,随后铸型填满的瞬间,应能将铸型内铸造比压提升到60~100MPa,这样合金便能在高压下凝固成型。
由于前述的低速大流量,且挤压铸造内浇道有冒口补缩的作用,内浇道口径较大,且位于铸件最肥厚的部位。
由于上述特点,挤压铸造适合厚壁铸件,但铸件尺寸不宜太大。
与压铸相同,挤压铸造只可使用脱模剂,不适用保温涂料,故而金属凝固速度极快,达到300~400摄氏度/s,与金属型重力铸造冷却速度相比,达到了其3~5倍,伸长率高于其他铸造方法约2~3倍。
挤压铸造的生产工艺流程以直径190系列的铝活塞为例,介绍挤压铸造的工艺流程,挤压铸造借鉴于压力铸造和模锻工艺,其大体工艺流程为把液态金属直接浇入金属模内。
挤压铸造工艺原理、特点、分类

第9章挤压铸造概述挤压铸造,简称挤铸,也称“液态模锻”或“液锻”。
其原理是对进入挤压铸型型腔内的液态(或半固态)金属施加较高的机械压力,使其成形和凝固,从而获得铸件或铸锭的一种工艺方法。
此工艺是一种介于模锻与压铸之间,实施铸锻结合的工艺。
其与模锻不同,置于模具(铸型)中的不是固态坯料,而是液态(或半固态)金属;与普通压铸不同,其液态金属是自下而上缓慢、平稳充型的,并保持在高压力下凝固。
从工艺方法方面,挤压铸造主要分两大类:①直接挤压铸造,简称直接挤铸,包括直接冲头挤铸、柱塞挤铸等,即液态金属在压力推动下充填由冲头与凹型组成的型腔中,且挤压冲头直接挤压在铸件上(见图9-1)。
②间接挤压铸造,简称间接挤铸,包括上压式和下顶式间接挤铸等,即液态金属在压力推动下,充填已闭合锁型的型腔中,挤压压冲头通过内浇道将压力传递到铸件上(见图9-2)。
图9-1典型直接挤压铸造工艺程序示意图a)铸型准备b)浇注c)合挤压压d)开型,取出铸件按挤压铸型的分(合)型方向的不同,挤压铸造也可分为立式挤铸(水平分型,如图9-1所示)和卧式挤铸(垂直分型,如图9-2所示)两大类。
但不论是何种类型,为创造良好的排气条件,挤压冲头对液态金属的挤压力,大都是垂直方向(由上向下或自下而上)施加的。
图9- 2典型间接挤压铸造(下顶式)工艺程序示意图a)铸型准备后浇注 b)合型,挤压料筒摆正e)挤压头和挤压料筒上升 d)挤压头上升挤压挤压铸造的工艺过程一般分为下列步骤(见图9-1,图9-2)。
(1)铸型准备包括对铸型、挤压料简及挤压冲头的清理和喷涂,并将其回复到准备位置上。
(2)浇注将液态(或半固态)金属注入凹型或料筒中。
(3)合型合型并锁型,将料筒、冲头进入待挤压位置。
(4)挤压用挤压冲头将液态(半固态)金属推人型腔,并继续保压直至其完全凝固。
(5)开型推出铸件。
挤压铸造一般在专用挤压铸造机(简称挤铸机)上进行。
但国内外也不少是选普通液压机代用,后者设备投资少,也可行,但生产效率低并会影响产品质量。
挤压铸造铝合金
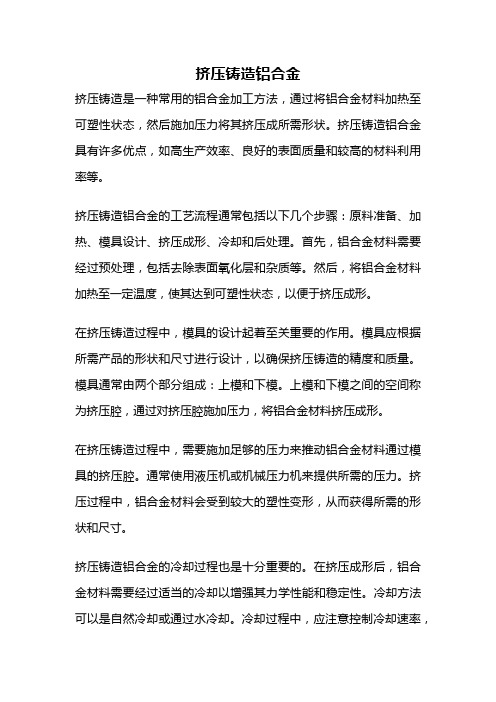
挤压铸造铝合金挤压铸造是一种常用的铝合金加工方法,通过将铝合金材料加热至可塑性状态,然后施加压力将其挤压成所需形状。
挤压铸造铝合金具有许多优点,如高生产效率、良好的表面质量和较高的材料利用率等。
挤压铸造铝合金的工艺流程通常包括以下几个步骤:原料准备、加热、模具设计、挤压成形、冷却和后处理。
首先,铝合金材料需要经过预处理,包括去除表面氧化层和杂质等。
然后,将铝合金材料加热至一定温度,使其达到可塑性状态,以便于挤压成形。
在挤压铸造过程中,模具的设计起着至关重要的作用。
模具应根据所需产品的形状和尺寸进行设计,以确保挤压铸造的精度和质量。
模具通常由两个部分组成:上模和下模。
上模和下模之间的空间称为挤压腔,通过对挤压腔施加压力,将铝合金材料挤压成形。
在挤压铸造过程中,需要施加足够的压力来推动铝合金材料通过模具的挤压腔。
通常使用液压机或机械压力机来提供所需的压力。
挤压过程中,铝合金材料会受到较大的塑性变形,从而获得所需的形状和尺寸。
挤压铸造铝合金的冷却过程也是十分重要的。
在挤压成形后,铝合金材料需要经过适当的冷却以增强其力学性能和稳定性。
冷却方法可以是自然冷却或通过水冷却。
冷却过程中,应注意控制冷却速率,以避免产生内部应力和变形。
挤压铸造铝合金的后处理包括修整、表面处理和热处理等。
修整是指对挤压成形后的产品进行切割、修整、冲孔等加工,以获得所需的尺寸和形状。
表面处理可以包括喷涂、阳极氧化、电泳涂装等,以提高产品的表面质量和耐腐蚀性能。
热处理可以通过固溶处理和时效处理等方法,提高铝合金材料的强度和硬度。
挤压铸造铝合金具有许多优点。
首先,挤压铸造是一种高效率的加工方法,可以大批量生产具有相同形状和尺寸的铝合金制品。
其次,挤压铸造的产品表面质量较好,可以减少后续加工工序。
同时,挤压铸造铝合金还具有较高的材料利用率,能够最大限度地减少材料浪费。
然而,挤压铸造铝合金也存在一些局限性。
首先,挤压铸造铝合金的产品形状较为简单,不适合复杂形状和细小尺寸的产品。
特种铸造之压力铸造
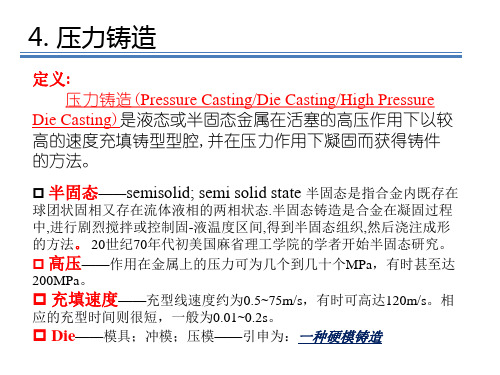
徐州科比特开发生产的管道型轴流通风机, 叶轮采用铝合金压力铸造
压铸是最先进的金属成型方法之一,是实现少切屑,无切屑的有效 途径,应用很广,发展很快。目前压铸合金不再局限于有色金属的锌、 铝、镁和铜,而且也逐渐扩大用来压铸铸铁和铸钢件。压力铸造法适用 于大批量生产的铸件,生产效率高,生产过程容易实现机械化和自动化。 压铸件也不再局限于汽车工业和仪表工业,逐步扩大到其它各个工 业部门,如农业机械、机床工业、电子工业、国防工业、计算 机、医疗 器械、钟表、照相机和日用五金等几十个行业。在压铸技术方面又出现 了真空压铸、加氧压铸、精速密压铸以及可溶型芯的应用等新工艺。
在活塞端面前可能会形成液流 的波峰,它也会把空气裹入金属液, 在铸件中形成气孔。
C 活塞移动速度适当
随着活塞的移动,在活塞端面 前形成充满压室整个断面的液面 抬高短,随着活塞的继续前进, 一次增加抬高段的程度,把压室 内空气向左挤,进入型腔,通过 排气通道进入大气。
瑞士已有技术实现活塞移动的等加速压射系统,可获得理 想压室全断面的充满过程。
热压室压铸机(简称热空压铸机)压室浸在保温溶化坩埚的液态 金属中,压射部件不直接与机座连接,而是装在坩埚上面。这种压铸 机的优点是生产工序简单,效率 高;金属消耗少,工艺稳定。但压 室,压射冲头长期浸在液体金属中,影响使用寿命。并易增加合金的 含铁量。热压室压铸机目前大多用于压铸锌合金等低熔点合金 铸件, 但也有用于压铸小型铝、镁合金压铸件。
A 活塞式热压室压铸机
喷嘴左端和压铸型上的直浇道口相接, 坩埚和压室(压力容器)一般都用铸铁铸 成一体,在坩埚外面用燃气或电阻丝加热。 压铸时,活塞式热压室压铸机上的活塞上 提,金属液从坩埚流入压室,活塞下压, 把压室内金属液经鹅颈、喷嘴压入铸型。
挤压铸造工艺优势与应用简介
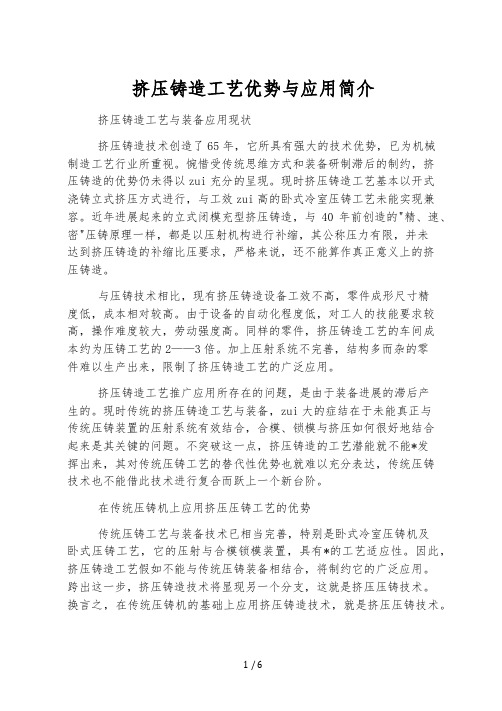
挤压铸造工艺优势与应用简介挤压铸造工艺与装备应用现状挤压铸造技术创造了65年,它所具有强大的技术优势,已为机械制造工艺行业所重视。
惋惜受传统思维方式和装备研制滞后的制约,挤压铸造的优势仍未得以zui充分的呈现。
现时挤压铸造工艺基本以开式浇铸立式挤压方式进行,与工效zui高的卧式冷室压铸工艺未能实现兼容。
近年进展起来的立式闭模充型挤压铸造,与40年前创造的"精、速、密"压铸原理一样,都是以压射机构进行补缩,其公称压力有限,并未达到挤压铸造的补缩比压要求,严格来说,还不能算作真正意义上的挤压铸造。
与压铸技术相比,现有挤压铸造设备工效不高,零件成形尺寸精度低,成本相对较高。
由于设备的自动化程度低,对工人的技能要求较高,操作难度较大,劳动强度高。
同样的零件,挤压铸造工艺的车间成本约为压铸工艺的2——3倍。
加上压射系统不完善,结构多而杂的零件难以生产出来,限制了挤压铸造工艺的广泛应用。
挤压铸造工艺推广应用所存在的问题,是由于装备进展的滞后产生的。
现时传统的挤压铸造工艺与装备,zui大的症结在于未能真正与传统压铸装置的压射系统有效结合,合模、锁模与挤压如何很好地结合起来是其关键的问题。
不突破这一点,挤压铸造的工艺潜能就不能*发挥出来,其对传统压铸工艺的替代性优势也就难以充分表达,传统压铸技术也不能借此技术进行复合而跃上一个新台阶。
在传统压铸机上应用挤压压铸工艺的优势传统压铸工艺与装备技术已相当完善,特别是卧式冷室压铸机及卧式压铸工艺,它的压射与合模锁模装置,具有*的工艺适应性。
因此,挤压铸造工艺假如不能与传统压铸装备相结合,将制约它的广泛应用。
跨出这一步,挤压铸造技术将显现另一个分支,这就是挤压压铸技术。
换言之,在传统压铸机的基础上应用挤压铸造技术,就是挤压压铸技术。
依据挤压压铸自身工艺的特点,对传统压铸机进行相应的完善改造,这套设备就是一台全新的挤压压铸机了。
正确而全面认得压铸工艺与传统压铸机的功能把握挤压铸造工艺的原理,在传统压铸机上地简单应用挤压压铸工艺并不是件难事,关键的是突破传统观念。
机械制造基础 第1章-03特种铸造
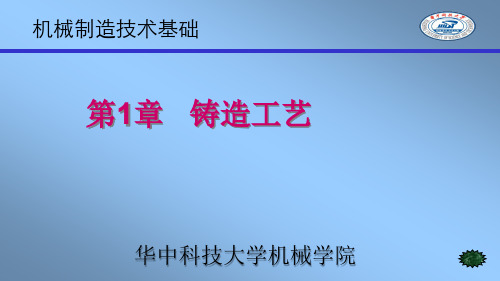
离心铸造主要用于大批生产铸铁管、气缸套、铜套、双金属 轴承、无缝钢来自毛坯、造纸机滚筒、细薄成形铸件等。
§1-3 特种铸造 五、熔模铸造
1.熔模铸造的工艺过程 将液态金属浇入由蜡模熔失后形成的中空型壳中,从而获得精密 铸件的方法,称为熔模铸造或失蜡铸造。
§1-3 特种铸造 二、压力铸造
将液态金属高速压人铸型,使其在压力下结晶而获得铸件的方法 1. 压力铸造工艺过程
压型必须用合金工具钢来制造,并要进行严格的热处理。压型工 作时应保持120~280度的工作温度,并定期喷刷涂料。
§1-3 特种铸造 2.压力铸造的特点及应用范围
(1)生产率高,生产过程易于机械化和自动化。
低熔点合金铸件。
三、挤压铸造
挤压铸造也称“液态模锻”,是对进入 挤压模内的液态金属施加较高的机械压 力,使其凝固成为铸件的铸造方法。
1. 挤压铸造的工艺过程
挤压铸造
挤压铸造与压力铸造的主要区别是:
挤压铸造 压力铸造
充型速度(m/s ) 凝固过程
0.1~0.4 15~100
压力下结晶并产生 塑性变形
② 原材料价贵,铸件成本高。
主要用来生产形状复杂、精度要求较高或难以切削加工的小型 合金铸件。在航空、船舶、汽车、机床、仪表、刀具和兵器等行 业得到了广泛应用。
§1-3 特种铸造 六、消失模铸造
用泡沫塑料模样造 型后,不取出模样、 直接浇注,使模样气 化消失而形成铸件的 方法,称为消失模铸 造。
1. 负压消失模铸 造工艺过程
机械制造技术基础
第1章 铸造工艺
华中科技大学机械学院
机械制造技术基础
第1章 铸造工艺
挤压铸造特点及应用

挤压铸造特点及应用挤压铸造是一种能够将金属材料通过压力挤压成型的铸造工艺。
相比于传统的铸造工艺,挤压铸造具有以下特点。
首先,挤压铸造具有高效性能。
挤压铸造的工艺能够在短时间内将金属材料形成所需的结构和形状,生产效率高,并且具有高度的一致性和重复性。
其次,挤压铸造的产品具有优良的机械性能。
挤压过程中,金属材料通过挤压力产生的高压力和高温度,能够使金属内部的结晶粒细化,并且使得材料中的夹杂物和气孔等缺陷得到排除,从而提高了产品的强度、硬度和韧性等机械性能。
再次,挤压铸造可以生产大尺寸和复杂结构的产品。
挤压铸造工艺能够按照模具的形状要求将金属材料挤压成形,因此可以生产出形状复杂、壁厚薄的产品,包括管道、棒材、异型材等。
同时,挤压铸造还具有较高的尺寸精度和表面质量,能够满足高要求的工程需求。
最后,挤压铸造还具有节约能源和环保的优点。
挤压铸造过程中,在减少熔化能耗的同时,还能够最大限度地减少材料的损耗和废弃物的产生,从而降低了资源的浪费和对环境的污染。
挤压铸造在工业生产中有着广泛的应用。
首先,在汽车工业中,挤压铸造被应用于生产汽车零部件,如车身结构件、发动机零部件、悬挂系统等。
挤压铸造能够生产出质量优良、精度高的零部件,提高汽车整体性能。
其次,在航空航天工业中,挤压铸造被广泛应用于生产航空发动机叶片、飞机结构件等关键零部件。
挤压铸造能够保证零部件的高强度和高温性能,提高航空器的安全性和可靠性。
此外,挤压铸造还被应用于制造机械设备的零部件和工具。
比如挤压铸造能够生产出高强度、耐磨损的传动轴、齿轮、螺纹和各种模具等工具件,提高机械设备的使用寿命和性能。
另外,挤压铸造还被广泛应用于建筑、电子、电力等领域。
比如在建筑领域,挤压铸造可以生产出抗震、防火性能优良的铝合金门窗、墙板等建筑材料。
在电子领域,挤压铸造可以生产出散热性能好的铝合金外壳、散热片等电子器件。
在电力领域,挤压铸造可以生产出高导热、高强度的铜导线、铝合金散热器等电力设备。
简述挤压铸造的原理及应用
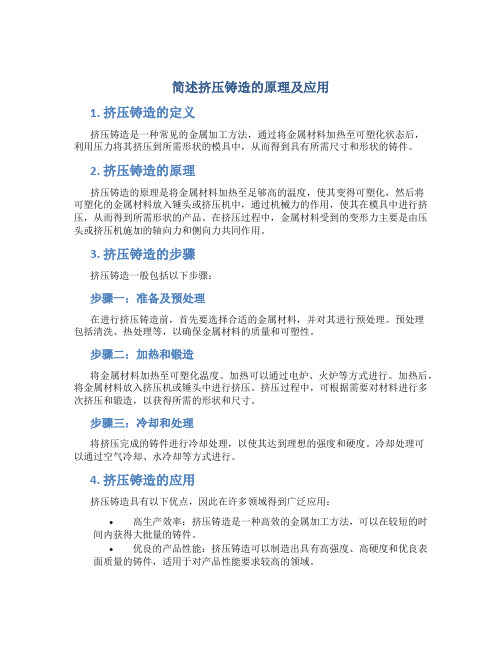
简述挤压铸造的原理及应用1. 挤压铸造的定义挤压铸造是一种常见的金属加工方法,通过将金属材料加热至可塑化状态后,利用压力将其挤压到所需形状的模具中,从而得到具有所需尺寸和形状的铸件。
2. 挤压铸造的原理挤压铸造的原理是将金属材料加热至足够高的温度,使其变得可塑化,然后将可塑化的金属材料放入锤头或挤压机中,通过机械力的作用,使其在模具中进行挤压,从而得到所需形状的产品。
在挤压过程中,金属材料受到的变形力主要是由压头或挤压机施加的轴向力和侧向力共同作用。
3. 挤压铸造的步骤挤压铸造一般包括以下步骤:步骤一:准备及预处理在进行挤压铸造前,首先要选择合适的金属材料,并对其进行预处理。
预处理包括清洗、热处理等,以确保金属材料的质量和可塑性。
步骤二:加热和锻造将金属材料加热至可塑化温度。
加热可以通过电炉、火炉等方式进行。
加热后,将金属材料放入挤压机或锤头中进行挤压。
挤压过程中,可根据需要对材料进行多次挤压和锻造,以获得所需的形状和尺寸。
步骤三:冷却和处理将挤压完成的铸件进行冷却处理,以使其达到理想的强度和硬度。
冷却处理可以通过空气冷却、水冷却等方式进行。
4. 挤压铸造的应用挤压铸造具有以下优点,因此在许多领域得到广泛应用:•高生产效率:挤压铸造是一种高效的金属加工方法,可以在较短的时间内获得大批量的铸件。
•优良的产品性能:挤压铸造可以制造出具有高强度、高硬度和优良表面质量的铸件,适用于对产品性能要求较高的领域。
•节约材料:挤压铸造可以实现材料的节约,因为挤压过程中材料的利用率较高,可以有效减少材料浪费。
•可复杂加工:挤压铸造可以制造出复杂形状的产品,适用于一些形状特殊、难以通过其他加工方式获得的产品。
挤压铸造在许多领域都有广泛的应用,包括汽车工业、航空航天工业、机械制造业等。
例如,在汽车工业中,挤压铸造可以用于制造车身结构件、发动机零部件等。
在航空航天工业中,挤压铸造可以用于制造飞机零部件、导弹零部件等。
5. 总结挤压铸造是一种常见的金属加工方法,通过将金属材料加热、挤压和锻造,可以获得具有所需形状和尺寸的铸件。
挤压铸造原理及缺陷分析

挤压铸造原理及缺陷分析集团企业公司编码:(LL3698-KKI1269-TM2483-LUI12689-ITT289-挤压铸造原理及缺陷分析挤压铸造技术与传统金属型重力铸造相比区别较大,对于某些铸件的生产有独特优势,然而实际生产中出现的一些铸造缺陷,成因也不同于传统铸造,本文试图从原理和生产实际出发,分析挤压铸造的原理和流程参数,及其铸造常见缺陷,利用技术上的经验和实践提出改进方法,已达到推进该项铸造技术的推广,减少损失。
挤压铸造原理及特点1.1.基本原理挤压铸造又可称为液态模锻,是将金属或合金升温至熔融态,不加处理注入到敞口模具中,立即闭合模具,让液态金属充分流动以充填模具,初步到达制件外部形状,随后施以高压,使温度下降已凝固的外部金属产生塑性变形,而内部的未凝固金属承受等静压,同步发生高压凝固,最后获得制件或毛坯的方法。
由于高压凝固和塑性变形同时存在,制件无缩孔、缩松等缺陷,组织细密,力学性能高于铸造方法,接近或相当锻造方法;无需冒口补缩和最后清理,因而液态金属或合金利用率高,工序简化,为一具有潜在应用前景的新型金属加工工艺。
1.2.挤压铸造的特点挤压铸造的工艺对铸造设备有特殊的要求,并且目前只对部分铸件有较好的效果。
首先,挤压铸造设备,需要提供低速但流量较大的液态金属填充能力,速度约为0.5~3m/s,流量可达1~5kg/s,这样熔融态金属才能平稳地将铸型内气体排出,并填充铸型,随后铸型填满的瞬间(50ms~150ms),应能将铸型内铸造比压提升到60~100MPa,这样合金便能在高压下凝固成型。
由于前述的低速大流量,且挤压铸造内浇道有冒口补缩的作用,内浇道口径较大,且位于铸件最肥厚的部位。
由于上述特点,挤压铸造适合厚壁铸件(10~50mm),但铸件尺寸不宜太大(小于200mm)。
与压铸相同,挤压铸造只可使用脱模剂,不适用保温涂料,故而金属凝固速度极快,达到300~400摄氏度/s,与金属型重力铸造冷却速度相比,达到了其3~5倍,伸长率高于其他铸造方法约2~3倍。
- 1、下载文档前请自行甄别文档内容的完整性,平台不提供额外的编辑、内容补充、找答案等附加服务。
- 2、"仅部分预览"的文档,不可在线预览部分如存在完整性等问题,可反馈申请退款(可完整预览的文档不适用该条件!)。
- 3、如文档侵犯您的权益,请联系客服反馈,我们会尽快为您处理(人工客服工作时间:9:00-18:30)。
1.凹型的结构(耐热模具钢) 整体凹型 垂直分型凹型 水平分型凹型 复合分型凹型 带芯棒凹型
S4-1 铸型垂直合型挤压铸造
2.冲头加压的工艺参数
1)压力 铸件壁厚越薄,施加压力需越大。 铸钢件压力大于有色金属件。 半固态时压力应大于液态合金。 2)浇筑后开始加压的时间:不超过15s 3)冲头的下压速度(金属液流速<0.8m/s) 过快:金属液产生涡流,卷气。 过慢:金属液过早凝固,挤压不能继续进行,不能成形。 4)保压时间 持续到铸件完全凝固时为止。 壁厚越厚,时间越长
垂直分型
水平分型
S4-2 旋转合型挤压铸造
用于生产大型薄壁件:机翼
S4-2 旋转合型挤压铸造
一 旋转合型挤压铸造的成形特点
1.充型过程平稳,不易卷气。 2.适用于生产大型薄壁件。 断面由大变小—阻力较小;散热慢
3.利于排气,排渣,避免夹渣、 气孔的缺陷。 4.利于补缩,获得致密铸件。
S4-2 旋转合型挤压铸造
第四章 挤 压 铸 造
定义:是指在两个半型分开的情况下,浇注金属液而后两个半型 合拢,将金属液挤压充填整个型腔,使之凝固成形的铸造方法, 又称液态金属冲压。(区别于压力铸造) 工艺流程是:喷涂料、浇合金、合模、加压、保压、泄压,分模、 毛坯脱模、复位。
与压力铸造的区别:施压部位同时作为型腔。
S4-1 铸型垂直合型挤压铸造
合型后不封闭的优缺点: 优点:
1)铸件内部气孔、缩松等缺陷少,组织致密,晶粒细小。 2)铸件尺寸精度高。
3)出现裂纹的倾向小。
4)应用合金种类范围广。 5)无浇冒口系统,金属液损失少,出品率高。
6)生产率高,易实现机械化。
缺点:
液压机成本高,不宜铸造复杂件
S4-1 铸型垂直合型挤压铸造
一 垂直合型挤压铸造的工艺特点
S4-1 铸型垂直合型挤压铸造
3.冲铸型的工作温度 预热的作用:避免挤压前,金属液在凹型中冷却过快 —形成硬壳—挤压破碎—卷入铸件 4.金属液的浇注温度—偏低为佳 5.金属液的定量 过少:浇不足 过多:尺寸偏差 造成浪费 6.铸型的润滑
涂料(同压力铸造)
S4-1 铸型垂直合型挤压铸造
二、挤压铸造用设备
旋转合型挤压铸造机
S4-2 旋转合型挤压铸造
二 旋转合型挤压铸造的工艺特点 1.干砂芯预热:110℃
2.铸型预热:金属型、转轴、侧板、
3.热节处设置冷铁,加强补缩。 4.合理的液面上升速度。 过慢:薄壁处浇不足 过快:出现波纹、裹气、冲刷砂芯
本 章 重 点
1.垂直挤压铸造冲头加压的工艺参数的控制 2.旋转挤压铸造的成形特点