半导体工厂大宗气体系统设计
半导体工厂大宗气体系统的设计

半导体工厂大宗气体系统的设计引言:半导体工厂(FAB)生产过程中需要使用大量的气体,这些气体在各个工序中起着至关重要的作用。
因此,设计一个高效可靠的大宗气体系统对于确保半导体工厂的正常运行和产品质量至关重要。
本文将重点探讨半导体工厂大宗气体系统的设计。
一、系统需求分析:在设计半导体工厂大宗气体系统之前,首先需要进行系统需求分析。
这包括对半导体生产工艺的了解,对所需气体种类和流量的确定,以及对系统的可靠性和安全性的考虑。
1.工艺要求:不同的半导体生产工艺所需的气体种类和流量可能会有所不同。
因此,需要先了解工艺要求,确定所需的气体类型,如氮气、氧气、氢气等,以及其流量。
2.流程和流量:在确定所需气体类型后,需要进行系统流程和流量的设计。
这包括确定气体的输送、净化、储存和分配的流程,并根据工艺要求确定每个阶段所需的气体流量。
3.可靠性和安全性:大宗气体系统设计需要考虑系统的可靠性和安全性。
可靠性包括系统的稳定性和可持续性,确保气体供应稳定并能满足生产需求。
安全性考虑包括气体的安全处理和泄漏的防范。
二、系统设计方案:在进行系统设计时,需要根据前面的需求分析,结合实际情况,提出一个合理的设计方案。
1.气体配送系统:气体配送系统用于将气体从供应源输送到工艺设备。
它包括气体输送管道、阀门和流量计等设备。
为了确保气体的流量和压力稳定,可以使用压力传感器和流量控制阀进行控制。
此外,还应根据需要设计合适的管网结构,确保气体分配均匀。
2.气体净化系统:气体净化系统用于去除气体中的杂质和污染物,以确保气体质量符合生产要求。
它包括过滤器、吸附剂和催化剂等设备。
根据不同的气体类型和污染物种类,选择适当的净化设备和方法。
3.气体储存系统:由于气体供应可能会有时间和流量的波动,因此需要设计一个气体储存系统,以弥补供应的不稳定性。
气体储存系统可以包括储气罐、压缩机和气体储存器等设备。
通过合理的容量和流量的设计,确保气体供应的持续和稳定。
厂务大宗气体及特殊气体系统知识

的选取主要在于其接头的尺寸及型式。
1/2”
2¼”
2.1.10其他:
(1)氩气:纯度99.999以上,每个钢瓶6立方公尺或7立方公尺,通常一瓶每组可使用2~3天。
(2)C型钢:制作支撑架用,有高低脚、双并、有孔等型式。
(3)电工管夹:将管材固定于C型钢上,最大可使用至5/8”之管子。
简单知识基本掌握
第一章气体概述
由于制程上的需要,在半导体工厂使用了许多种类的气体,一般我们皆依气体特性来区分,可分为一般气体()与特殊气体()两大类。
前者为使用量较大之气体,如N2、等,因用量较大,一般气体常以大宗气体称之。
后者为使用量较小之气体•一般指用量小,极少用量便会对人体造成生命威胁的气体,如4、3等
2.1.6调压阀:
•1.材质同管件
•2.材质: ,316L, 81…* N2O – .
•3.常用种类:
*高压/低压/一般压力
* 2P无表头/ 3P 4P单表头或双表头
* / /
•4.一般分高压与低压选取,但尚有高流量型式可供选取,另外可依表头()需求加以搭配。•(以为例)
*一般使用316L或316L等级/或
* ( )电子式压力表头
* ( )压力传送器
•2.使用于:盘面及管路上
•3.压力范围大致可分为:
*高压(0~3000 )
*低压(-30”0~30 )
(-30”0~160 )
• 4.常用电源: 24V , 4~20
2.1.8过滤器:
•1.功能:过滤气体中的微粒子( )
•2.过滤等级选择,即滤径尺寸( ) ,可分为:
(4)管束:分单立、双立、P型等型式,固定管子用。
(5)牙条:吊挂、固定型钢用。
半导体厂房净化空调系统设计与应用探析

半导体厂房净化空调系统设计与应用探析随着半导体产业的迅速发展,半导体厂房的净化空调系统设计和应用变得越来越重要。
半导体生产对空气质量和温度湿度要求非常严格,而且厂房内的设备和工艺对空调系统也提出了较高的要求。
设计一套稳定可靠的净化空调系统对半导体厂房的生产以及产品质量具有非常重要的意义。
一、半导体生产对空调系统的要求1. 温度湿度控制:半导体厂房内的生产设备对温度湿度要求非常严格,任何温度湿度的变化都会影响半导体产品的质量和稳定性。
净化空调系统必须能够确保厂房内的温度湿度在一定的范围内稳定。
2. 空气净化:半导体生产对空气质量的要求也非常高,空气中的微粒、尘埃、化学物质等都会对生产设备和产品造成影响。
净化空调系统必须能够对空气进行有效的净化处理。
3. 稳定性和可靠性:半导体生产对空调系统的稳定性和可靠性要求也非常高,任何运行问题都可能导致生产受到严重影响。
二、半导体厂房净化空调系统的设计要点1. 空气处理设备的选择:根据半导体生产对空气质量的要求,需要选择高效的空气处理设备,包括过滤器、换热器、除湿器、加湿器等。
这些设备需要能够高效地对空气进行处理,确保空气质量的要求。
2. 风管系统的设计:半导体厂房的风管系统设计需要考虑到空气的流动和分布,以及厂房内不同区域的温度湿度要求。
合理的风管设计可以确保空气在厂房内的均匀分布,同时保证不同区域的温度湿度稳定。
3. 控制系统的设计:净化空调系统需要有稳定可靠的控制系统,能够根据厂房内的温度湿度变化进行自动调节,并且能够及时响应生产设备的需求。
控制系统也需要具有故障自检和报警功能,确保空调系统的稳定性和可靠性。
4. 节能技术的应用:净化空调系统的设计应用还需要考虑到节能技术的应用,通过合理的设计和设备选择,减少能耗,提高能源利用效率。
三、半导体厂房净化空调系统的应用探析1. 提高生产效率和产品质量:稳定可靠的净化空调系统可以提高半导体厂房的生产效率,同时保证产品的质量和稳定性。
半导体气体系统组成
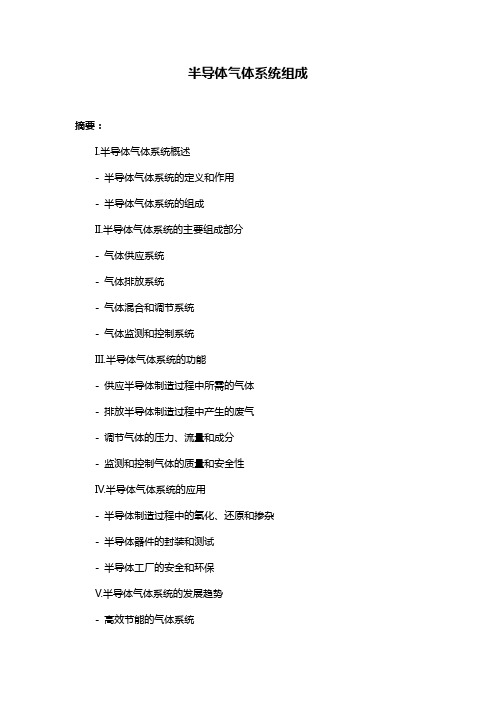
半导体气体系统组成摘要:I.半导体气体系统概述- 半导体气体系统的定义和作用- 半导体气体系统的组成II.半导体气体系统的主要组成部分- 气体供应系统- 气体排放系统- 气体混合和调节系统- 气体监测和控制系统III.半导体气体系统的功能- 供应半导体制造过程中所需的气体- 排放半导体制造过程中产生的废气- 调节气体的压力、流量和成分- 监测和控制气体的质量和安全性IV.半导体气体系统的应用- 半导体制造过程中的氧化、还原和掺杂- 半导体器件的封装和测试- 半导体工厂的安全和环保V.半导体气体系统的发展趋势- 高效节能的气体系统- 环保安全的气体排放技术- 智能化和自动化的气体监测和控制正文:半导体气体系统是半导体制造过程中的重要组成部分,它对半导体产品的性能、质量和生产效率有着重要的影响。
半导体气体系统主要由气体供应系统、气体排放系统、气体混合和调节系统以及气体监测和控制系统组成。
气体供应系统是半导体气体系统的核心部分,它负责向半导体制造过程供应各种气体,如氮气、氧气、氩气、氯气等。
气体供应系统通常由气瓶、压缩机、阀门、管道等组成,它们将气体从气瓶压缩后输送到半导体制造设备中。
气体排放系统是半导体气体系统的另一重要部分,它负责将半导体制造过程中产生的废气排放到大气中。
气体排放系统通常由排放管道、阀门、风机等组成,它们将废气从半导体制造设备中收集后排放到大气中。
气体混合和调节系统是半导体气体系统的重要组成部分,它负责将不同种类的气体按一定的比例混合,以满足半导体制造过程的要求。
气体混合和调节系统通常由混合器、调节阀、流量计等组成,它们可以精确地控制气体的压力、流量和成分。
气体监测和控制系统是半导体气体系统的安全保障,它负责监测和控制气体的质量和安全性。
气体监测和控制系统通常由传感器、控制器、报警器等组成,它们可以实时地监测气体的成分、压力、流量等参数,并及时地报警和调节,以保证半导体制造过程的安全和稳定。
半导体工厂(FAB)大宗气体系统的设计(精)

半导体工厂(FAB)大宗气体系统的设计(精)半导体工厂(FAB)大宗气体系统(Gas Yard)的设计1995年,美国半导体工业协会(SIA)在一份报告中预言:"中国将在10-15年内成为世界最大的半导体市场"。
随着中国经济的增长和信息产业的发展,进入21世纪的中国半导体产业市场仍将保持20%以上的高速增长态势,中国有望在下一个十年成为仅次于美国的全球第二大半导体市场。
而目前的发展态势也正印证了这一点。
作为半导体生产过程中必不可少的系统,高纯气体系统直接影响全厂生产的运行和产品的质量。
相比较而言,集成电路芯片制造厂由于工艺技术难度更高、生产过程更为复杂,因而所需的气体种类更多、品质要求更高、用量更大,也就更具代表性。
因此本文重点以集成电路芯片制造厂为背景来阐述。
集成电路芯片厂中所使用的气体按用量的大小可分为二种,用量较大的称为大宗气体(Bulk gas),用量较小的称为特种气体(Specialtygas)。
大宗气体有:氮气、氧气、氢气、氩气和氦气。
其中氮气在整个工厂中用量最大,依据不同的质量需求,又分为普通氮气和工艺氮气。
由于篇幅所限,本文仅涉及大宗气体系统的设计。
1 系统概述大宗气体系统由供气系统和输送管道系统组成,其中供气系统又可细分为气源、纯化和品质监测等几个部分。
通常在设计中将气源设置在独立于生产厂房(FAB)之外的气体站(Gas Yard),而气体的纯化则往往在生产厂房内专门的纯化间(Purifier Room)中进行,这样可以使高纯气体的管线尽可能的短,既保证了气体的品质,又节约了成本。
经纯化后的大宗气体由管道从气体纯化间输送至辅道生产层(SubFAB)或生产车间的架空地板下,在这里形成配管网络,最后由二次配管系统(Hook-up)送至各用户点。
图1给出了一个典型的大宗气体系统图。
2 供气系统的设计2.1 气体站2.1.1 首先必须根据工厂所需用气量的情况,选择最合理和经济的供气方式。
半导体气体系统组成

半导体气体系统组成(原创版)目录一、半导体气体的概述二、半导体气体系统的组成1.气体供应系统2.气体净化系统3.气体分配系统4.气体监测系统三、半导体气体的应用1.硅烷在半导体工业中的应用2.锗烷在电子工业中的应用3.磷烷在半导体工业中的应用四、全球半导体气体供应链的状况五、半导体式气体传感器的原理和应用六、我国半导体气体产业的发展正文一、半导体气体的概述半导体气体是指在半导体制造过程中所使用的各种气体,它们在半导体材料的生长、沉积、掺杂、刻蚀等工艺中发挥着重要作用。
常见的半导体气体有硅烷、锗烷、磷烷等。
二、半导体气体系统的组成半导体气体系统通常由四个部分组成,分别是气体供应系统、气体净化系统、气体分配系统和气体监测系统。
1.气体供应系统:负责将各种半导体气体从储存装置输送到使用地点,通常包括气体瓶、阀门、压力调节器等。
2.气体净化系统:负责对半导体气体进行净化处理,去除其中的杂质和污染物,确保气体的纯度和质量。
常用的净化方法有吸附、过滤、冷凝等。
3.气体分配系统:负责将半导体气体按照工艺需求进行分配和切换,以满足不同工艺步骤的要求。
常用的分配方式有手动控制、自动控制等。
4.气体监测系统:负责对半导体气体的使用过程进行实时监测,确保气体的安全性和稳定性。
常用的监测方法有浓度监测、压力监测、温度监测等。
三、半导体气体的应用1.硅烷在半导体工业中的应用:硅烷主要用于制作高纯多晶硅、通过气相淀积制作二氧化硅薄膜、氮化硅薄膜、多晶硅隔离层、多晶硅欧姆接触层和异质或同质硅外延生长原料、以及离子注入源和激光介质等,还可用于制作太阳能电池、光导纤维和光电传感器等。
2.锗烷在电子工业中的应用:锗烷主要用于化学气相淀积,形成各种不同的硅锗合金用于电子元器件的制造。
3.磷烷在半导体工业中的应用:磷烷主要用于硅烷外延的掺杂剂。
四、全球半导体气体供应链的状况乌克兰局势引发了能源、黄金等大宗商品价格发生剧烈波动。
作为全球半导体特种气体主要供应地,乌克兰承载了全球近七成氖气产量,也是氩、氪、氙等多种半导体制造所需气体的重要产源地,美国超过 90% 的半导体级氖气来自乌克兰。
半导体工厂大宗气体工业纯化管道系统
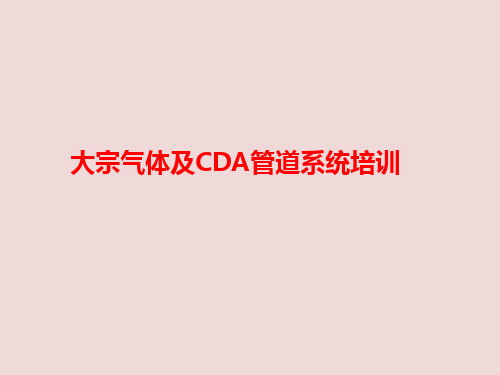
GGas
PGas
由于液晶面板厂制程上的需要,工厂会使用许多种类的气体。一般我们以气体的特性来区分。 可分为特殊气体和一般气体,前者使用量较小,如SiH4,NF3等;后者使用量较大,如N2等。因而使用量较大的气体 我们称之为“大宗气体”,即Bulk Gas。
1.大宗气体及CDA概述
➢ CDA气体:
CDA : Compressed/Clean dry air 干燥压缩空气
气体 过滤 系统
用来过滤气体 中的 Particle等 杂质
G-GAS在经过专业纯化器,纯化得到P-GAS.纯化间设置在4B栋东北角。 (除H2,H2纯化在大宗气站内完成)
G-GAS
2.大宗气体与CDA系统概述
相关的名词解释
➢ 桥架或地下沟渠:
气体管路的架装方式:生产厂房与气站之间均会设有安全区隔,管路输送系统从气站拉到生产厂房时,须经过 Tunnel (地下管沟) 或 Trench (地面 or 高架管桥) .
缩空气气管内部污染等),当洁净车间内大量使用压缩空气时,对其洁净度将有所影响。
2、化学品输送压力介质
P-GAS
3、制造惰性环境
4、参与反应
5、去除杂质
6、其他制程功能
2.大宗气体与CDA系统概述
2.大宗气体与CDA系统概述
将大气经过滤、压缩、冷却(液化) 、过滤、分馏、过滤、压缩、冷 却(液化)后,可分别取得 N2, O2,Ar 等气体,此过程称之为空 气分离技术。
2.大宗气体与CDA系统概述
相关的名词解释
➢ CQC 房间和 CQC 系统( Continuously Quality Control) 亦或称为气体监控系统 实时在线监测气体品质
GN2
半导体工厂(FAB)大宗气体系统的设计(精)
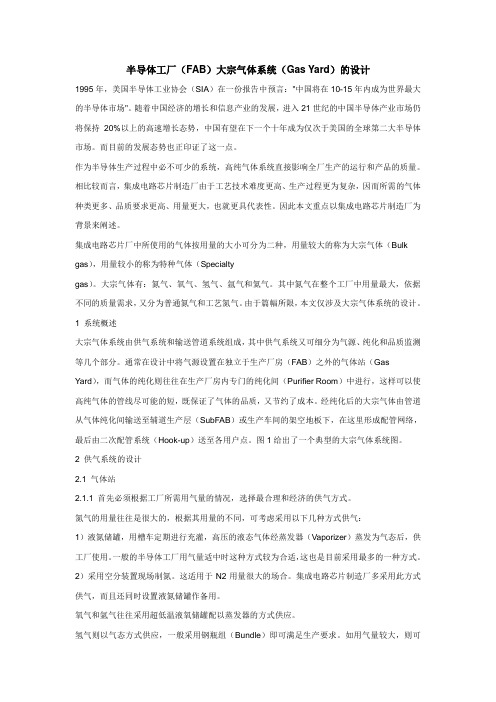
半导体工厂(FAB)大宗气体系统(Gas Yard)的设计1995年,美国半导体工业协会(SIA)在一份报告中预言:"中国将在10-15年内成为世界最大的半导体市场"。
随着中国经济的增长和信息产业的发展,进入21世纪的中国半导体产业市场仍将保持20%以上的高速增长态势,中国有望在下一个十年成为仅次于美国的全球第二大半导体市场。
而目前的发展态势也正印证了这一点。
作为半导体生产过程中必不可少的系统,高纯气体系统直接影响全厂生产的运行和产品的质量。
相比较而言,集成电路芯片制造厂由于工艺技术难度更高、生产过程更为复杂,因而所需的气体种类更多、品质要求更高、用量更大,也就更具代表性。
因此本文重点以集成电路芯片制造厂为背景来阐述。
集成电路芯片厂中所使用的气体按用量的大小可分为二种,用量较大的称为大宗气体(Bulk gas),用量较小的称为特种气体(Specialtygas)。
大宗气体有:氮气、氧气、氢气、氩气和氦气。
其中氮气在整个工厂中用量最大,依据不同的质量需求,又分为普通氮气和工艺氮气。
由于篇幅所限,本文仅涉及大宗气体系统的设计。
1 系统概述大宗气体系统由供气系统和输送管道系统组成,其中供气系统又可细分为气源、纯化和品质监测等几个部分。
通常在设计中将气源设置在独立于生产厂房(FAB)之外的气体站(Gas Yard),而气体的纯化则往往在生产厂房内专门的纯化间(Purifier Room)中进行,这样可以使高纯气体的管线尽可能的短,既保证了气体的品质,又节约了成本。
经纯化后的大宗气体由管道从气体纯化间输送至辅道生产层(SubFAB)或生产车间的架空地板下,在这里形成配管网络,最后由二次配管系统(Hook-up)送至各用户点。
图1给出了一个典型的大宗气体系统图。
2 供气系统的设计2.1 气体站2.1.1 首先必须根据工厂所需用气量的情况,选择最合理和经济的供气方式。
氮气的用量往往是很大的,根据其用量的不同,可考虑采用以下几种方式供气:1)液氮储罐,用槽车定期进行充灌,高压的液态气体经蒸发器(Vaporizer)蒸发为气态后,供工厂使用。
大宗硅烷供气系统设计
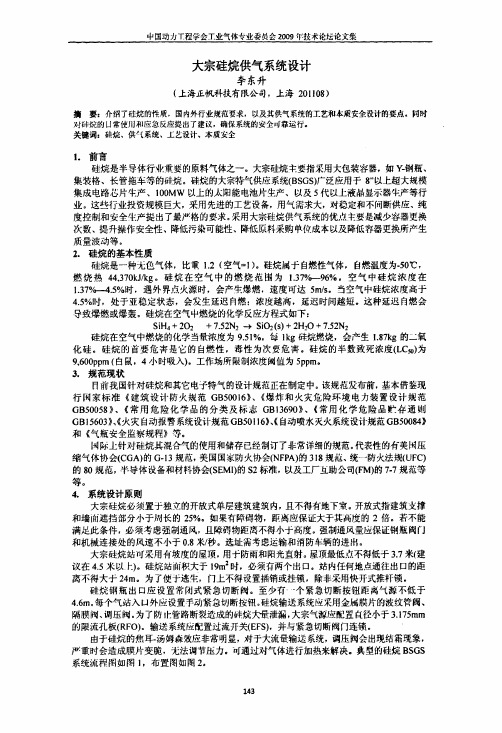
2.硅烷的基本性质
硅烷是一种无色气体,比蕈1.2(空气=1)。硅烷属于自燃性气体,自燃温度为.50℃, 燃烧热44,370kJ/kg。硅烷在空气中的燃烧范围为1.370/,--96%。空气中硅烷浓度在
1.37纠.5%时,遇外界点火源时,会产生爆燃,速度可达5m/s。当空气中硅烷浓度高于
硅烷在空气中燃烧的化学当量浓度为9.51%。每l埏硅烷燃烧,会产生1.87k的二氧
design:intrinsic safety
145
3.规范现状
目前我国针对硅烷和其它电子特气的设计规范正在制定中。该规范发布前,基本借鉴现 行嗣家标准《建筑设计防火规范GB50016》、《爆炸和火灾危险环境电力装置设计规范 GB50058》、《常用危险化学品的分类及标志GBl3690》、《常用化学危险品贮存通则 GBl5603))、《火灾自动报警系统设计规范GB50116》、《自动喷水灭火系统设计规范GB50084)) 和《气瓶安全监察规程》等。 阳际上针对硅烷其混合气的使用和储存已经制订了非常详细的规范。代表性的有美阿压 缩气体协会(CGA)的G.13规范,美国国家防火协会(NFPA)的318规范、统一防火法规(UFC) 的80规范,半导体设备和材料协会(SEMI)的S2标准,以及工厂互助公司(FM)的7.7规范等 等。 4.系统设计原则 大宗硅烷必须置于独立的开放式单层建筑建筑内,且不得有地下室。开放式指建筑支撑 和墙面遮挡部分小于蒯长的25%。如果有障碍物,足巨离应保证大于其高度的2倍。若不能 满足此条件,必须考虑强制通风,且障碍物距离不得小于高度。强制通风量应保证钢瓶阀门 和机械连接处的风速不小于O。8米/秒。选址需考虑运输和消防车辆的进出。 大宗硅烷站可采用有坡度的屋顶,用于防雨和阳光直射。屋顶最低点不得低于3.7米(建 议在4.5米以.卜:)。硅烷站确f积大于19m2时,必须有两个出口。站内任何地点通往出口的距 离不得大十24m。为了便于逃生,门上不得设置插销或挂锁,除非采用快开式推杆锁. 硅烷钢瓶出口应设置常闭式紧急切断阀。至少有~个紧急切断按钮距离气源不低于 4.6m。每个气站入【J外应设置手动紧急切断按钮。硅烷输送系统应采用金属膜片的波纹管阀、 隔膜阀、调压阀。为了防l}:管路断裂造成的硅烷大最泄漏,大宗气源应配置卣径小于3.175mm 的限流孔板(RFO)。输送系统应配置过流开关(EFS),并与紧急切断阀门连锁。 由于硅烷的焦耳.汤姆森效应非常明显,对于大流最输送系统,调压阀会出现结霜现象, 严蕈时会造成膜片变脆,无法调节压力。可通过对气体进行加热来解决。典型的硅烷BSGS 系统流程图如图l,布置罔如图2。
半导体工厂大宗气体系统的设计
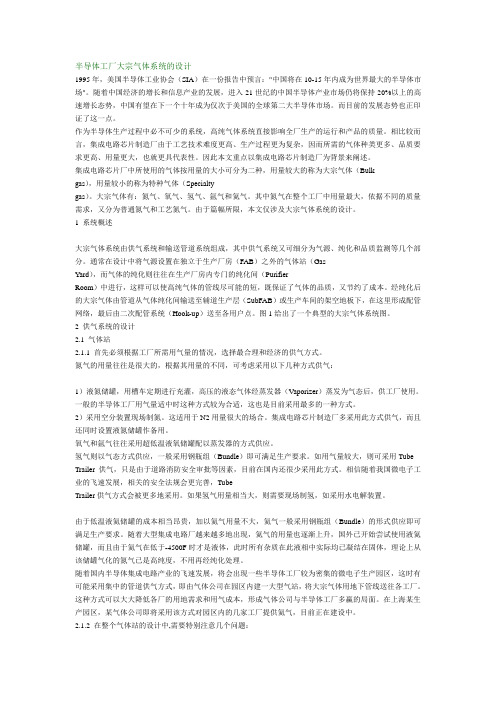
半导体工厂大宗气体系统的设计1995年,美国半导体工业协会(SIA)在一份报告中预言:"中国将在10-15年内成为世界最大的半导体市场"。
随着中国经济的增长和信息产业的发展,进入21世纪的中国半导体产业市场仍将保持20%以上的高速增长态势,中国有望在下一个十年成为仅次于美国的全球第二大半导体市场。
而目前的发展态势也正印证了这一点。
作为半导体生产过程中必不可少的系统,高纯气体系统直接影响全厂生产的运行和产品的质量。
相比较而言,集成电路芯片制造厂由于工艺技术难度更高、生产过程更为复杂,因而所需的气体种类更多、品质要求更高、用量更大,也就更具代表性。
因此本文重点以集成电路芯片制造厂为背景来阐述。
集成电路芯片厂中所使用的气体按用量的大小可分为二种,用量较大的称为大宗气体(Bulkgas),用量较小的称为特种气体(Specialtygas)。
大宗气体有:氮气、氧气、氢气、氩气和氦气。
其中氮气在整个工厂中用量最大,依据不同的质量需求,又分为普通氮气和工艺氮气。
由于篇幅所限,本文仅涉及大宗气体系统的设计。
1 系统概述大宗气体系统由供气系统和输送管道系统组成,其中供气系统又可细分为气源、纯化和品质监测等几个部分。
通常在设计中将气源设置在独立于生产厂房(FAB)之外的气体站(GasYard),而气体的纯化则往往在生产厂房内专门的纯化间(PurifierRoom)中进行,这样可以使高纯气体的管线尽可能的短,既保证了气体的品质,又节约了成本。
经纯化后的大宗气体由管道从气体纯化间输送至辅道生产层(SubFAB)或生产车间的架空地板下,在这里形成配管网络,最后由二次配管系统(Hook-up)送至各用户点。
图1给出了一个典型的大宗气体系统图。
2 供气系统的设计2.1 气体站2.1.1 首先必须根据工厂所需用气量的情况,选择最合理和经济的供气方式。
氮气的用量往往是很大的,根据其用量的不同,可考虑采用以下几种方式供气:1)液氮储罐,用槽车定期进行充灌,高压的液态气体经蒸发器(Vaporizer)蒸发为气态后,供工厂使用。
半导体代工厂的特气供应系统探讨
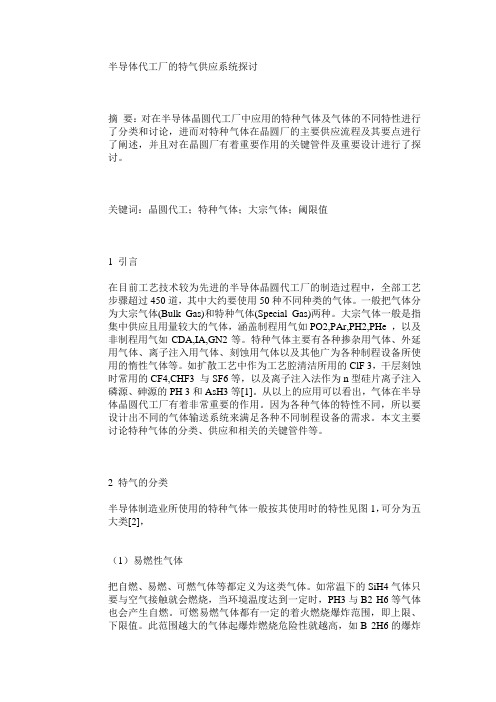
半导体代工厂的特气供应系统探讨摘要:对在半导体晶圆代工厂中应用的特种气体及气体的不同特性进行了分类和讨论,进而对特种气体在晶圆厂的主要供应流程及其要点进行了阐述,并且对在晶圆厂有着重要作用的关键管件及重要设计进行了探讨。
关键词:晶圆代工;特种气体;大宗气体;阈限值1 引言在目前工艺技术较为先进的半导体晶圆代工厂的制造过程中,全部工艺步骤超过450道,其中大约要使用50种不同种类的气体。
一般把气体分为大宗气体(Bulk Gas)和特种气体(Special Gas)两种。
大宗气体一般是指集中供应且用量较大的气体,涵盖制程用气如PO2,PAr,PH2,PHe ,以及非制程用气如CDA,IA,GN2等。
特种气体主要有各种掺杂用气体、外延用气体、离子注入用气体、刻蚀用气体以及其他广为各种制程设备所使用的惰性气体等。
如扩散工艺中作为工艺腔清洁所用的ClF 3,干层刻蚀时常用的CF4,CHF3 与SF6等,以及离子注入法作为n型硅片离子注入磷源、砷源的PH 3和AsH3等[1]。
从以上的应用可以看出,气体在半导体晶圆代工厂有着非常重要的作用。
因为各种气体的特性不同,所以要设计出不同的气体输送系统来满足各种不同制程设备的需求。
本文主要讨论特种气体的分类、供应和相关的关键管件等。
2 特气的分类半导体制造业所使用的特种气体一般按其使用时的特性见图1,可分为五大类[2],(1)易燃性气体把自燃、易燃、可燃气体等都定义为这类气体。
如常温下的SiH4气体只要与空气接触就会燃烧,当环境温度达到一定时,PH3与B2 H6等气体也会产生自燃。
可燃易燃气体都有一定的着火燃烧爆炸范围,即上限、下限值。
此范围越大的气体起爆炸燃烧危险性就越高,如B 2H6的爆炸上限为98%,爆炸下限为0.9%。
属于易燃气体有H 2,NH3,PH3,DCS,ClF3 等等。
(2)毒性气体(Toxic Gas):半导体制造行业中使用的气体很多都是对人体有害、有毒的。
大宗气体及特殊气体
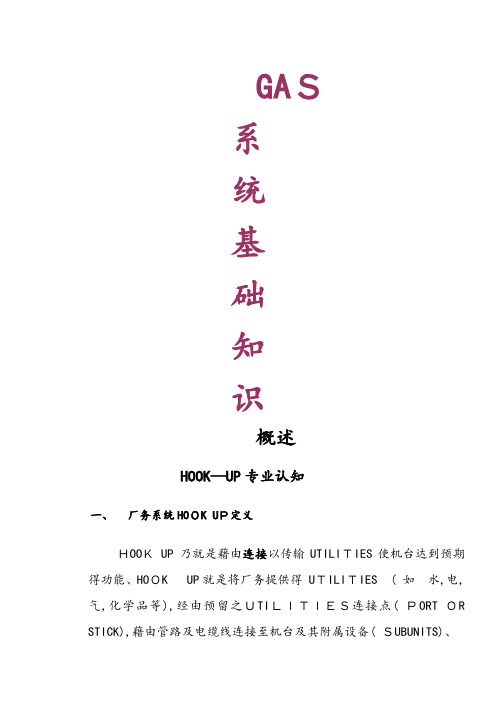
GAS系统基础知识概述HOOK—UP专业认知一、厂务系统HOOK UP定义HOOK UP 乃就是藉由连接以传输UTILITIES使机台达到预期得功能、HOOK UP就是将厂务提供得 UTILITIES ( 如水,电,气,化学品等),经由预留之UTILITIES连接点( PORT OR STICK),藉由管路及电缆线连接至机台及其附属设备( SUBUNITS)、机台使用这些 UTILITIES,达成其所被付予得制程需求并将机台使用后,所产生之可回收水或废弃物( 如废水,废气等),经由管路连接至系统预留接点,再传送到厂务回收系统或废水废气处理系统。
HOOK UP 项目主要包括∶CAD,MOVE IN ,CORE DRILL,SEISMIC ,VACUUM,GAS, CHEMICAL ,D、I ,PCW,CW,EXHAUST,ELECTRIC, DRAIN。
二、GAS HOOK-UP专业知识得基本认识在半导体厂,所谓气体管路得Hook—up(配管衔接)以Buck Gas(一般性气体如CDA、GN2、PN2、PO2、PHE、PAR、H2等)而言,自供气源之气体存贮槽出口点经主管线(Main Piping)至次主管线(Sub-Main Piping)之Take Off点称为一次配(SP1 Hook—up),自Take Off出口点至机台(Tool)或设备(Equipment)得入口点,谓之二次配(SP2 Hook-up)。
以SpecialtyGas(特殊性气体如:腐蚀性、毒性、易燃性、加热气体等之气体)而言其供气源为气柜(Gas Cabinet)。
自G/C出口点至VMB(Valve MainfoldBox、多功能阀箱)或VMP(Valve Mainfold Panel多功能阀盘)之一次测(Primary)入口点,称为一次配(SP1 Hook-up),由VMB或VMP Stick之二次侧(Secondary)出口点至机台入口点谓之二次配(SP2 Hook-up)。
半导体特种气体供应系统设计纲要
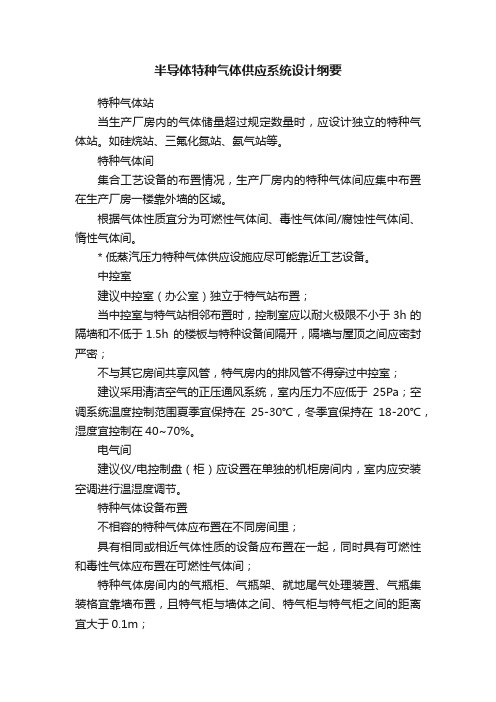
半导体特种气体供应系统设计纲要特种气体站当生产厂房内的气体储量超过规定数量时,应设计独立的特种气体站。
如硅烷站、三氟化氮站、氨气站等。
特种气体间集合工艺设备的布置情况,生产厂房内的特种气体间应集中布置在生产厂房一楼靠外墙的区域。
根据气体性质宜分为可燃性气体间、毒性气体间/腐蚀性气体间、惰性气体间。
* 低蒸汽压力特种气体供应设施应尽可能靠近工艺设备。
中控室建议中控室(办公室)独立于特气站布置;当中控室与特气站相邻布置时,控制室应以耐火极限不小于3h 的隔墙和不低于1.5h 的楼板与特种设备间隔开,隔墙与屋顶之间应密封严密;不与其它房间共享风管,特气房内的排风管不得穿过中控室;建议采用清洁空气的正压通风系统,室内压力不应低于25Pa;空调系统温度控制范围夏季宜保持在25-30℃,冬季宜保持在18-20℃,湿度宜控制在40~70%。
电气间建议仪/电控制盘(柜)应设置在单独的机柜房间内,室内应安装空调进行温湿度调节。
特种气体设备布置不相容的特种气体应布置在不同房间里;具有相同或相近气体性质的设备应布置在一起,同时具有可燃性和毒性气体应布置在可燃性气体间;特种气体房间内的气瓶柜、气瓶架、就地尾气处理装置、气瓶集装格宜靠墙布置,且特气柜与墙体之间、特气柜与特气柜之间的距离宜大于0.1m;毒性、腐蚀性气体的特种气体间应设置紧急洗眼器;特种气体间的中间通道净宽度不得小于2 米,布置应考虑维修与运转空间;安放地磅的坑内应有排水管道。
特种气体输送系统不相容气体瓶严禁放置于同一气瓶柜或气瓶架中;气瓶柜闭门时应保持不低于100Pa负压,其排风换气次数不得低于300次/小时;气瓶柜的负压应持续监控;可燃与自燃性气瓶柜应设置水喷淋系统,但是ClF3气瓶柜不应设置水喷淋系统。
吹扫和排气系统特种气体系统吹扫氮气的设置,应符合下列要求:自燃、可燃、毒性、腐蚀性特种气体系统的吹扫氮气应与独立的氮气源连接,不得与公用氮气或工艺氮气系统相连;不相容性特种气体系统的吹扫氮气不得共用同一氮气源;吹扫氮气管线必须设置止回阀。
半导体工厂大宗气体系统的设计

半导体工厂大宗气体系统的设计随着半导体行业的迅猛发展,半导体工厂的大宗气体系统的设计变得尤为重要。
大宗气体在半导体制造过程中扮演着重要角色,包括制造环境的控制、材料的处理和设备的冷却等。
一个合理设计的大宗气体系统可以有效地提高生产效率、降低运营成本并确保产品质量。
本文将讨论半导体工厂大宗气体系统的设计。
首先,大宗气体系统的设计应该从工厂的需求出发。
在设计过程中,需要综合考虑各种气体使用量、工艺需求和设备容量等因素。
根据不同的工艺需求,选择合适的气体类别和纯度,并确定所需的气体流量和压力。
其次,大宗气体系统的设计应该注重安全性。
考虑到大宗气体的危险性,设计中应采取适当的安全措施,包括气体泄漏检测系统、报警系统、紧急切断装置等。
此外,应设计合理的气体管道布局,确保气体的流动畅通,并避免气体混合和火灾等安全风险。
第三,大宗气体系统的设计应充分考虑节能和环保。
在选择气体供应方式时,应优先考虑以废气回收和再利用为主,减少对环境的影响。
同时,设计中应采用高效的气体输送系统,减少能量损耗。
与此同时,应考虑系统的可持续性发展,确保气体供应的持久稳定。
第四,大宗气体系统的设计还应考虑维护和管理。
在设计过程中,应充分考虑系统的易维护性,包括易操作、易清洁和易维修,以减少工厂的停机时间和维护成本。
此外,应考虑建立一个完善的管理系统,包括对气体的监测、记录和管理,以确保系统的稳定运行和合规性。
最后,大宗气体系统的设计还需要与其他设备和系统进行整合。
半导体工厂是一个复杂的生产系统,各个系统之间需要紧密协调和配合。
在设计大宗气体系统时,应与供电系统、制冷系统、废物处理系统等其他系统进行协调和整合,确保整个工厂的高效运行。
综上所述,半导体工厂大宗气体系统的设计应综合考虑工厂需求、安全性、节能环保、维护管理和整体一体化等因素。
一个合理设计的大宗气体系统可以提高工厂的生产效率、降低生产成本并确保产品质量。
在设计过程中,需要与相关部门和专业人士进行合作,确保设计的科学性和实用性。
大宗气体及特殊气体
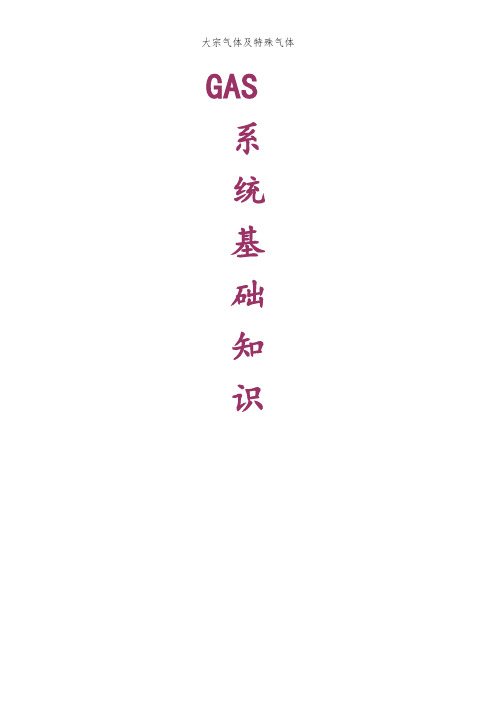
GAS 系统基础知识概述HOOK-UP专业认知一、厂务系统HOOK UP定义HOOK UP 乃就是藉由连接以传输UTILITIES使机台达到预期的功能。
HOOK UP就是将厂务提供的 UTILITIES ( 如水,电,气,化学品等),经由预留之UTILITIES连接点( PORT OR STICK),藉由管路及电缆线连接至机台及其附属设备( SUBUNITS)。
机台使用这些 UTILITIES,达成其所被付予的制程需求并将机台使用后,所产生之可回收水或废弃物( 如废水,废气等),经由管路连接至系统预留接点,再传送到厂务回收系统或废水废气处理系统。
HOOK UP 项目主要包括∶CAD,MOVE IN ,CORE DRILL,SEISMIC ,VACUUM,GAS, CHEMICAL ,D、I ,PCW,CW,EXHAUST,ELECTRIC, DRAIN、二、GAS HOOK-UP专业知识的基本认识在半导体厂,所谓气体管路的Hook-up(配管衔接)以Buck Gas(一般性气体如CDA、GN2、PN2、PO2、PHE、PAR、H2等)而言,自供气源之气体存贮槽出口点经主管线(Main Piping)至次主管线(Sub-Main Piping)之Take Off点称为一次配(SP1 Hook-up),自Take Off出口点至机台(Tool)或设备(Equipment)的入口点,谓之二次配(SP2 Hook-up)。
以Specialty Gas(特殊性气体如:腐蚀性、毒性、易燃性、加热气体等之气体)而言其供气源为气柜(Gas Cabinet)。
自G/C出口点至VMB(Valve Mainfold Box、多功能阀箱)或VMP(Valve Mainfold Panel多功能阀盘)之一次测(Primary)入口点,称为一次配(SP1 Hook-up),由VMB或VMP Stick之二次侧(Secondary)出口点至机台入口点谓之二次配(SP2 Hook-up)。
- 1、下载文档前请自行甄别文档内容的完整性,平台不提供额外的编辑、内容补充、找答案等附加服务。
- 2、"仅部分预览"的文档,不可在线预览部分如存在完整性等问题,可反馈申请退款(可完整预览的文档不适用该条件!)。
- 3、如文档侵犯您的权益,请联系客服反馈,我们会尽快为您处理(人工客服工作时间:9:00-18:30)。
半导体工厂大宗气体系统的设计搞要本文对集成电路芯片厂中的大宗气体系统的设计过程作了概括性的描述,对当前气体设计技术及其发展方向作了探讨,同时结合自己对多个FAB厂房的设计经验提出了设计中值得注意的问题和解决方案。
This paper introduces a general design process for Bulk Gas System in gas design technology and its development directionare also on the author抯 experience in FABdesign,several potential problems in design and relevant solutions are issued.1995年,美国半导体工业协会(SIA)在一份报告中预言:"中国将在10-15年内成为世界最大的半导体市场"。
随着中国经济的增长和信息产业的发展,进入21世纪的中国半导体产业市场仍将保持20%以上的高速增长态势,中国有望在下一个十年成为仅次于美国的全球第二大半导体市场。
而目前的发展态势也正印证了这一点。
作为半导体生产过程中必不可少的系统,高纯气体系统直接影响全厂生产的运行和产品的质量。
相比较而言,集成电路芯片制造厂由于工艺技术难度更高、生产过程更为复杂,因而所需的气体种类更多、品质要求更高、用量更大,也就更具代表性。
因此本文重点以集成电路芯片制造厂为背景来阐述。
集成电路芯片厂中所使用的气体按用量的大小可分为二种,用量较大的称为大宗气体(Bulkgas),用量较小的称为特种气体(Specialtygas)。
大宗气体有:氮气、氧气、氢气、氩气和氦气。
其中氮气在整个工厂中用量最大,依据不同的质量需求,又分为普通氮气和工艺氮气。
由于篇幅所限,本文仅涉及大宗气体系统的设计。
1 系统概述大宗气体系统由供气系统和输送管道系统组成,其中供气系统又可细分为气源、纯化和品质监测等几个部分。
通常在设计中将气源设置在独立于生产厂房(FAB)之外的气体站(GasYard),而气体的纯化则往往在生产厂房内专门的纯化间(PurifierRoom)中进行,这样可以使高纯气体的管线尽可能的短,既保证了气体的品质,又节约了成本。
经纯化后的大宗气体由管道从气体纯化间输送至辅道生产层(SubFAB)或生产车间的架空地板下,在这里形成配管网络,最后由二次配管系统(Hook-up)送至各用户点。
图1给出了一个典型的大宗气体系统图。
2 供气系统的设计气体站2.1.1 首先必须根据工厂所需用气量的情况,选择最合理和经济的供气方式。
氮气的用量往往是很大的,根据其用量的不同,可考虑采用以下几种方式供气:1)液氮储罐,用槽车定期进行充灌,高压的液态气体经蒸发器(Vaporizer)蒸发为气态后,供工厂使用。
一般的半导体工厂用气量适中时这种方式较为合适,这也是目前采用最多的一种方式。
2)采用空分装置现场制氮。
这适用于N2用量很大的场合。
集成电路芯片制造厂多采用此方式供气,而且还同时设置液氮储罐作备用。
氧气和氩气往往采用超低温液氧储罐配以蒸发器的方式供应。
氢气则以气态方式供应,一般采用钢瓶组(Bundle)即可满足生产要求。
如用气量较大,则可采用TubeTrailer供气,只是由于道路消防安全审批等因素,目前在国内还很少采用此方式。
相信随着我国微电子工业的飞速发展,相关的安全法规会更完善,TubeTrailer供气方式会被更多地采用。
如果氢气用量相当大,则需要现场制氢,如采用水电解装置。
由于低温液氦储罐的成本相当昂贵,加以氦气用量不大,氦气一般采用钢瓶组(Bundle)的形式供应即可满足生产要求。
随着大型集成电路厂越来越多地出现,氦气的用量也逐渐上升,国外已开始尝试使用液氦储罐,而且由于氦气在低于-4500F时才是液体,此时所有杂质在此液相中实际均已凝结在固体,理论上从该储罐气化的氮气已是高纯度,不用再经纯化处理。
随着国内半导体集成电路产业的飞速发展,将会出现一些半导体工厂较为密集的微电子生产园区,这时有可能采用集中的管道供气方式,即由气体公司在园区内建一大型气站,将大宗气体用地下管线送往各工厂。
这种方式可以大大降低各厂的用地需求和用气成本,形成气体公司与半导体工厂多赢的局面。
在上海某生产园区,某气体公司即将采用该方式对园区内的几家工厂提供氦气,目前正在建设中。
2.1.2 在整个气体站的设计中,需要特别注意几个问题:首先,供氢系统和供氧系统的安全性问题是必须予以高度重视的,如气体站的平面布置必须符合相关安全规范。
其次,在设计供气压力时不仅要参照最终用户点的压力需求,而且必须考虑纯化器、过滤器以及配管系统的压力降。
另外,随着集成电路工艺的提升,对工艺氧气中的氮杂质含量要求也提高了。
值得注意的是,该杂质目前尚无法通过气体纯化器有效去除,必须在空分装置中增加专门的超低温精馏过程处理,这不可避免导致成本的上升,当然由此法制取的氧气纯度已足够高,不需要经纯化即可直接用于工艺设备。
另一折衷的方法是,目前200mm芯片生产工艺中,只有部分工艺设备对氧中氮的含量要求甚高,如果这些设备的用氧量不大,则可以考虑外购高纯氧气钢瓶专门对这些设备供气。
气体纯化与过滤2.2.1气体的品质要求随着集成电路技术的不断发展,设计线宽不断微缩,这对气体品质的要求也越来越严格,目前对大宗气体的纯度要求往往达到ppb级,表1给出了某200mm芯片生产工艺线对大宗气体的品质要求。
因此,必须用不锈钢管道将大宗气体从气体站送至生产厂房的纯化室(purifierRoom)进行纯化,气体经纯化器除去其中的杂质,再经过滤器除去其中的颗粒(Particle)。
出于安全考虑,一般将氢气纯化室设计为单独一室,并有防爆、泄爆要求。
2.2.2 纯化器目前国内采用的气体纯化器都是进口的,主要的生产厂家有SAES、Taiyo、Toyo、JPC、ATTO等。
纯化器根据其作用原理的不同可以对不同的气体进行纯化。
我将目前市场上纯化器的情况作了整理,见表2。
一般说来,N2、O2纯化器较多采用触媒吸附式,Ar、H2纯化器则以Getter 效果最佳,H2纯化器也多采用触媒吸附结合Getter式。
在设计中要注意的是,不同气体纯化器需要不同的公用工程与之相配套。
例如,触媒吸附式N2纯化器需要高纯氢气供再生之用;触媒吸附式纯化器需要冷却水。
因此,相关的公用工程管线必须在气体纯化间内留有接口。
2.2.3 过滤器半导体生产工艺过程不仅对气体纯度要求十分严格,而且对气体中的颗粒含量也有极高的要求,目前在集成电路芯片生产中,对大宗气体颗粒度的要求通常为:大于μm的颗粒含量为零。
而去除颗粒则需采用气体过滤器。
一般的,经纯化的气体需经过两个串联的过滤器即可达到工艺要求,为方便滤芯更换,往往并联设置两组过滤器组,参见图1。
气体的品质监测大宗气体在经纯化及过滤后应对其进行品质监测,观察其纯度与颗粒度的指标是否已高于实际的工艺要求。
目前着重对气体中的氧含量、水含量和颗粒度进行在线连续监测,而对CO、CO2及THC杂质采用间歇监测,测试结果连同其他测试参数(诸如压力、流量等)都会被送往控制室中的SCADA(SupervisoryControl and Date Acquisition)系统。
供气系统的可靠性问题由于微电子行业的投入与产出都是非常的大,任何供气中断都会带来巨大的经济损失,尤其对大型集成电路芯片生产厂而言。
因此在设计中必须充分考虑气体供应系统运行的安全可靠性。
若采用现场制气方式,往往还需要设置该种气体的储蓄供气系统作备用。
1)每一种气体的纯化器都需要有一台作备用。
2)氧气若采用现场制气方式,虽然可以不经纯化而直接供工艺设备使用,但仍应该设置一台纯化器作备用。
当然,以上这些措施必须会导致气体成本的急剧上升,虽然与供气中断造成的损失相比要小的多,但这必须要与业主讨论确定。
而且,每个项目都有其特殊性,不必强求一步到位,可以考虑在不同的建设阶段逐步实施。
另外,若有条件采用集中管道供气方式,还需要考察气体供应商的系统设计情况,是否有对供气中断、管路污染等突发事故的预防措施、应急措施和恢复手段。
有必要提请业主注意在该种经济便利的供气方式背后潜在的风险。
3 大宗气体输送管道系统的设计经纯化后的大宗气体由气体纯化间送至辅助生产层(SubFAB)或生产车间(FAB)的架空地板下,在这里形成配管网络,再由二次配管系统(Hook-up)送至各用户点。
以我的设计经验,在设计中要着重考虑以下几个方面。
配管系统的整体架构目前,较为常见的架构有树枝型(图2)和环型(图3)两种。
其中又数树枝型最为常用,其架构清晰,且与其它系统的配管架构相似,利于整体空间规划。
环型则能较好地保持用气点压力的稳定,但投资较高。
因此在设计中应根据用气点的分布情况及用气压力要求综合考虑。
例如,笔者在某200mm集成电路芯片生产厂的设计中,大宗气体配管系统均采用树枝型架构。
由于该FAB厂房很大,管线较长,而工艺氮气用气点较多,有一些用气点对压力要求也较高,因此对工艺氮气管路系统特别采用了树枝型与环型相结合的方式(图4),环型主管主要保证用气点的压力稳定,其管径可小于树枝型主管的管径,从而降低成本。
配管系统的灵活性设计微电子行业的发展非常迅速,经常会发生工艺设备更新、挪位和新增等状况。
即使在整个工厂的建设中,最终的工艺设备分布也会与设计时相去甚远。
这种行业的特殊性要求设计必须充分考虑其灵活性(Flexibility),能满足未来的扩展需求。
配管系统的基本设计原则是在主管(Main)上按一定间距设置支管端(Branch),再在每个支管上按一定间距设置分支管(BranchTake-off)供二次配管使用。
另外,主管的管径不必随流量的递减而采取渐缩设计。
无庸讳言,这种配管系统的确具有充分的灵活性,但由于超高纯气体管路的管件和阀件价格昂贵,该系统的成本之高也是显而易见的。
通常,集成电路芯片厂的建设往往会分成若干个阶段,一方面可以缓解一次性投资的巨大资金压力,另一方面也可以根据市场状况作出相应的调整决策。
在新厂建设的第一阶段,设计产量往往不是很高,用气点也不是很多,尤其是氢、氩、氧、氦的用气点就更少。
因此必须考虑如何来简化该配管系统以降低成本。
下面以图5为例,对一些典型的工况作分析:工况一:支管I中,用气点a与b均在该支管的最远端,因此无法作简化。
即使c与d处目前暂无用气点,但还是应该设置分支管和阀门,以备将来之用。
工况二:支管II中,用气点e和f的远端没有其它的用气点,则支管线可以分别在e点和f点后结束。
注意,支管的终端阀必须带排气口,以供管线延伸使用。