防差错技术-第五节
防错技术与防错管理

做对的效益的三倍 ➢ 低错误率的保证—防错机制的建立
第三部分 防错技术开发
防错技法的理解与实现
防错案例
产品设计开发中的防错应用
36
互动
➢你的答案正确吗? 为什么出错了?
人为错误方式的分析
人为错误的种类 自以为是
敷衍、马虎 拖沓、松散
健忘 误解 判断(识别)失误 工作疏忽 故意
错误的场景 自认为了解 小事、不重要
无所谓 压力、精力不集中时 面对新的工作环境、自认为了解 环境、速度、经验主义 心不在焉、重复性工作 忽略标准或规则、情绪或利益
例1:在零件上预防缺陷 过程描述:用螺定紧固塑料外观件 问题:螺丝刀划伤塑料件表面
改进前:
解决方案:改变螺钉槽形状 关键改进措施:
改进后:
例2:在零件上预防缺陷 过程描述:轴的装配 问题:轴两端头装配错误
改进前:
不正确
正确
解决方案:轴的两端可互 换
关键改进措施:改变零件 的形状
改进后:
思考: 解决方案二:
案、拟达到的作用级别 步骤5 实施改善方案: 步骤6 确认防错效果:活动后必须查核能否按照目标获
得成果。 步骤7 维持防错:将防错方法规范化、标准化
分析问题的金字塔原理
问题
一级因素
二级 因素
原 因
解决问题的九个控制要素
5W
➢ Why ➢ What ➢ Where ➢ Who ➢ When
3H
➢ How ➢ How much ➢ How much cost
质量管理防差错技术,产能和过程控制

纯手工作业工序中的质量控制方法
• 在工厂中有部分的工序,没有工装夹具, 没有自动化设备,没有产品结构保证,而 是完全靠人来完成(比如,贴标签,装零 配)件),由于没有一定的质量保证措施, 此类工序很容易出错,无法保证重复性和 稳定性要求。 • 对于此类情况一般采用以下质量控制方法 • 1,细分作业内容,减少作业步骤,动作少 了自然出错的机会就少了。
全数检验方式的应用
• 1,比如焊接的制造方式本身就有一定的缺陷,无 法保证焊缝无泄漏,所以必须进行全数检验。 • 2,设备自动化程度很低,比如普通机床加工零件。 • 3,工序作业内容过于密集和交叉,生产节拍过快, 无细化,无防错,无验证能力,基本以纯手工作 业方式为主的工位,如装配干燥过滤器时作业步 骤较多,容易出错。按照114时焊工又要装配, 又要焊接,而且生产节拍过快。 装配炉胆端盖需 经常在同一个工装上切换作业,交叉作业时容易 出错。
自检和互检的理解
• 作为生产一线的员工他不是一个技术专家,也 不可能短时间内成为一名技术专家,它不可能完 全了解上道工序的作业要求,只能在他的能力范 围内查找不合格品。 • 如果你要把他培养成一名技术专家,什么问题都 靠他来发现,没有三五年是不可能的,这其中企 业是要付出很多的培训代价的。 • 所以企业不去做一些其它方面的改进,而是指望 一名专业能力很低的员工去控制不在自己能力范 围内的事情,太指望要培养它靠他来控制产品质 量,这样的想法是很愚蠢的。
三者关系
• 这三者是不能颠倒的,首先你必须要掌握与自 己工作相关联的技术,然后你才可以准备配备相 应的资源,制订相应的工作流程和标准化作业来 实现你的目的,最终制订制度来确保你所规定的 作业标准能有效的持续的执行下去。 • 就好比你都不知道这道菜是怎么烧出来的,你 当然不知道需要那些材料,烧成的步骤中的火温, 放的油盐酱醋的量,最后为了保证100个人烧这 道菜出来的味道都是一样的,就要制订标准化作 业规则制度来保证人人都按照你的要求执行。
防错技术培训教材 65页

判断型
通过对产品的检测和挑选,将不 合格品从合格品中挑选出来的检 测方法。
一般的质量控制所进行的 检验和测试
通过抽样方法取得检测数据,并 — 统计过程控制
信息型 利用此数据,来监控生产过程的 — 后一工序检查, 抽检
稳定性
— 自检
溯源型
对过程的作业条件进行检测和确 认,以保证在作业之前即满足高 品质生产所需的条件。
2、替代:
是进入更可靠的过程的一个变更;
方法:运用机器人技术或自动化技术(如插件机、自动螺丝机)
3、简单化:
将过程运行变的更简单化,也更准确;
方法:合并生产步骤,实施IE改善
4、检测:
如散热片组 装在线化
使错误在下一步操作前被发现,不流出不良品;
方法:使用电脑程序,在操作失误或不良时报警
5、减少:
是将错误的影响降到最低。 方法:采用保险丝进行过载保护。
• 它是利用传感器来探测质量、安全和生产率等特性的
电子装置或仪器。感应器可以高精度确定部件、工具或 夹具的存在和位置,并可探测破裂、损坏或磨损。
感应器
控制按钮
三、计数
• 在需要固定操作步骤或产品上要装上一定数量的零件
时,可应用此方法用一个计数器来计算操作步数或装入 的零件数,只有达到规定数量时才放行。
安全措施:建立技巧,工作标准化
8. 缺乏标准而产生的错误:有时由于缺乏指引或工作 标准时会发生错误。 例如,新工人不知道脚长、零件浮起等标准而导致 不良品的流出错误。
安全措施:工作标准化,工作指引。
9. 意外错误:当设备运行状况与预期不符时会发生错误。 例如:机器可能在生产时突然出现故障。
安全措施:预防保养,工作标准化
使用标示“①②~~”,提醒控
防错技术及其应用-PPT
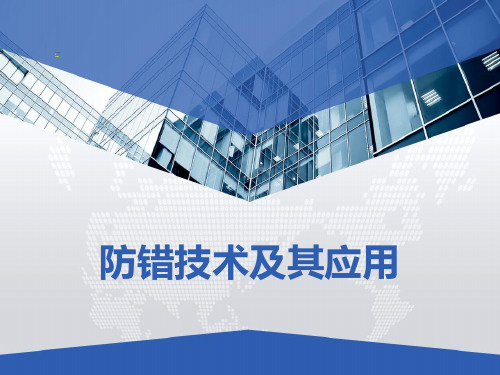
消除错误-缺陷的意义
零缺陷目标
– 减少各种错误-缺陷-损失 – 减少浪费(Muda) ——增加正向收获 – 降低废品率,减少返工 – 向消除质量检验迈进,降低检验成本
提高工作质量、强化效率 将操作人员的时间和精力解放出来,以从事更具有创造性和附加
价值的活动,从而使员工通过更多的参与获得成就感与满足感 增强安全性并适应环境保护的需要 降低质量风险、优化产品性能、提高顾客满意度,获取最大竞争
➢ 一般质检所进行的检验和测试均为判 断型检测
信息型
➢ 通过抽样方法取得检测数据,并利用 此数据,来监控生产过程的稳定性
➢ 统计过程控制(SPC)方法所进行的检 测即为信息型检测
Slide 35
防错思路4:检测法中的三种检测手段:
溯源型
➢ 对过程的作业条件进行检测和确认,以保证 在作业之前即满足高质量生产所需的条件
➢ 新产品开发设计过程的设计数据审查及测量 系统评估即为溯源型检测
自检
➢ 作业员完成作业,将产品投入下一工位前的 检查和验证作业的一部分,对每个产品百分 之百进行检验
➢ 良好作业习惯
互检
➢ 后道工序作业前对前道工序作业结果的正确 性的验证
➢ 防止出现因缺陷累积而造成大的损失 ➢ 利于建立作业人员的团队协作精神
Slide 32
防错思路3:简化
简化:
➢ 通过合并、削减等方法对作业流程进行简化 ➢ 流程越简单、出现操作失误的概率越低 ➢ 简化流程是较好的防错法之一,但流程简化并
并不能完全防止人为缺陷的产生 ➢ 崔西定律:
“崔西定律”是指:“任何工作的困难度与 其执行步骤的数目平方成正比:例如完成一件工 作有3 个执行步骤,则此工作的困难度是9,而 完成另一工作有5个执行步骤,则此工作的困难 度是25,所以必须要简化工作流程。”
防错法ppt课件

业过程方可成功。 (3)低成本。 (4)实时发现失误,实时反馈。
14
第二部分: 防错技术与工具
一、防错思路
防错思路
目标
削除 消除可能的失误
替代
用更可靠的过程代替目 前的过程以降低失误
简化 使作业更容易完成
检测
在缺陷流入下工序前对 其进行检测并剔除
认真做事可以把事情做对,用心做事才可以事情做好。 我们需要用心去实践精益制造!
51
8
三、制造过程常见失误
制造过程不同,其失误种类也千差万別,但 大致可归为以下几类:
01、漏掉某个作业步骤 02、作业失误 03、工件设置失误 04、缺件 05、用错部品
06、工件加工错误 07、误操作 08、调整失误 09、设备参数设置不当 10、工装夹具准备不当
9
四、制造过程常见失误分类
失误原因
48
四、几类常见防错装置
4、检查表
检查表可以防止人为疏漏,如出货检查表, 包装检查表,5S检查表等,示意如下:
5S检查表
NO
项目
状况
1
2
3
4 i
49
学习感言(一)
50
学习感言(二)
导入【丰田式管理】的公司,失败的比 成功的多。
失败者遇瓶颈,并未探究真正的原因去 改善或执行者并未真正投入。
只是找个理由「丰田式模式」并不适合 我们而放弃。
40
三、防错法应用案例
1、照相机快门防错装置
(1) 在相机快门上加装一机构, 如拍摄者在拍摄一 次后如忘记过卷, 则无法按下快门, 只有过卷后, 快门方可按下。这属于检测型防错。
防错的五类方法和五大原则

防错的五类方法和五大原则--- 教你防错技术防错的五类方法和五大原则一教你防错技术一、有5种类型的错误防止方法:--- 失效-安全装置(Fail-safe devices)--- 传感器放大(Magnification of senses)--- 冗余(Redundancy)--- 倒计数(Countdown)--- 特殊检验、控制装置(Special checking and control devices)1.失效-安全装置(Fail-safe devices)互锁顺序(InterlookingSeqUences):保证在前一个操作顺利完成前,下一个操作不能开始;预警与中断(Alarm and cutoff):将在过程中出现法场情况时被激活;全部完成信号(All-clear signals):将在全部补救措施完成后被激活;防傻型工件夹紧装置(FOOIPrOOf):保证工作的一部分只能被固定在一个位置;限位机械装置(LinIiting mechanisms):用来保证工具不能超过某一位置或数量。
2.传感器放大(Magnification of senses)用来增强人的视觉、听觉、嗅觉、触觉、味觉和肌肉力量,如:光学放大、多重视觉和听觉信号、监控危险过程的遥控以及用图片代替文字等等。
3.冗余(Redundancy):用作保证质量的附加措施。
多重确认码(Multiple-identify CodeS):例如防止产品混淆的条码和彩色码;冗余措施和批准(Redundant actions and approvals):需要两个人独立工作;审核评审和检查程序(Audit review and checking procedure):保证计划被跟踪;验证设计(DeSign for verification):利用特殊设计如:观察孔,来确定产品或过程是否在令人满意的执行;复合测试台(Multiple test StatiOnS):可检查很多特征,如出现在高速生产线上的特征。
防差错管理PPT课件
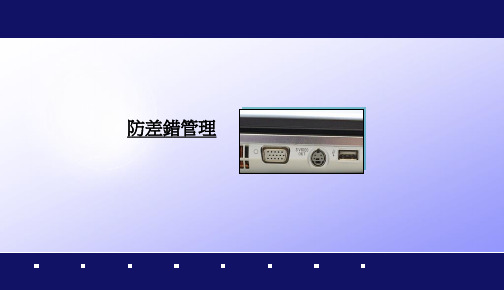
方法七:
每個人輪流分粥,但是分粥的人要最後一個領粥。
在這一制度下,七隻碗裏的粥每次都 是一樣多,就像用科學儀器量過一樣。 每個主持分粥的人都意識到,如果七 隻碗裏的粥不相同,他確定無疑將享 用那份最少的。
一個好的制度能造就好人,
因為好的制度,會湧現出一批不斷 進取、奮發向上的人。
相反,不好的制度造就的是壞 人,只能讓許多的人變得好吃懶
導演:徐景达 (1934.10—1987.2)
别名阿达
分享一下 您的觀後感!
對人性的假設
人性善
人性惡
人性有善有惡
其它
仁愛
法制
權變
下屬是愛你好,還是怕你好?
达摩克利斯之剑
小故事:
8歲的飛錦是一個孩子王,時常在學校領導一些孩子做“壞 事”,而父母隨時被叫去開家長會,很是苦惱。
方法四:
大家選舉一個信得過的人主持分粥。
他就有意識的為 自己和溜鬚拍馬 的人多分。
方法五:
民主選舉一個分粥委員會和監督委員會,形成民主監督和制約機制。
由於監督委員會經 常提出各種議案, 分粥委員會又據理 力爭,等分粥完畢 時,粥早就涼了。
方法六:
對於分粥,每人都有一票否決權。
最後恐怕誰也不會喝上粥。
嚴管重罰
新加坡的鞭刑
頑症,需猛藥
2、POKA-YOKE的觀點
首先弄清楚産生差錯的根本原因,然後針對原因采取對策。前面我們已討論過,
傳統方法可以防止産生差錯的人為原因中的一部分,而因為人為疏忽、忘記 等原因所造成的差錯無法靠培訓和懲罰來消除。日本豐田
汽車公司的工程師SHIGEO SHINGO 通過長期研究,建立了一套新的防錯模式—
一次就做對!
0.99 10 =0.90 0.99 50 =0.60 0.99 100 =0.37 0.99 200 =0.13 0.99 300 =0.05 1n =1
在防差错应用中以下不属于防错原则的是

防错原则一、例题【标准答案】在防差错应用中,以下不属于防错原则的是()。
A 削减、合并、调整或简化(ECRS)B 全员参与C 追求完美D 效率优先标准答案:D二、防错技术基本原则1.轻松原则对于难辨、难拿、难动等作业,可以用不同颜色区分使容易辨认,难拿的上把手,难动的用搬运工具。
2.简单原则需要高度技能、直觉和容易发生人为失误的作业,可以用工装或机械化使新进人员不容易出错。
3.安全原则有不安全或不安全因素时,加以改善使其不会有危险。
马虎作业或勉强作业有危险时,设法安装无法马虎或无法勉强作业的装置。
4. 自动化原则依赖眼睛、耳朵等器官进行作业时,容易出错,可以制作工装或使之自动化,减少用人的感官来判断作业过程。
企业的防错技术在很大程度上属于工程技术部门,防错的重点也应该放在控制变化的动态上,下面13个原则通常是工程技术部门实施防错技术的基本准则:①消除潜在隐患,降低风险;②降低危险因素的成分、数值;③层层设障,多重预防;④自动防控装置⑤屏障危险能量:⑥间隔有效距离;⑦控制时间因素;⑧抓住薄弱环节;⑨放大安全系数;⑩关注个体化;⑪识别替代人员;⑫应急预备方案;⑬禁止和警告提示。
三、防错思路消除:应用防错技术,通过产品及制造过程的重新设计,消除可能的错误。
替代:运用机器人技术或自动化技术,更可靠的过程替代目前的过程,以降低可能的失误。
简化:合并生产步骤,实施工业工程改善,位作业过程更容易完成。
检测:使用电脑软件,在操作失误时予以警告,在缺陷流入下道工序前对其进行剔除。
减少:采用类似保险丝进行过载保护,将失误影响降至最低,四、防错技术十大原理断根原理:将会造成错误的原因从根本上排除掉,使绝不发生错误。
保险原理:藉用两个以上的动作必需共同或依序执行才能完成工作。
自动原理:以各种光学、电学、力学、机构学、化学等原理来限制某些动作的执行或哪执行,以避免错误发生。
相符原理:藉用检核是否符合的动作,来防止错误的发生。
16-防差错技术

防差错技术目录•防错法概述–认识错误与缺陷的关系–产生失误的一般类型及原因–防错法的作用–防差错的基本原则和思路–防差错的基本方法–防差错的应用范围防错法概述•认识错误与缺陷的关系缺陷错误z 所有的缺陷均由错误产生;z 不是所有的错误都产生缺陷。
思考:什么情况下的错误不会产生缺陷?人为差错•操作者实际完成的职能与该工作所要求完成的职能之间的偏差。
表现为–未执行分配给他的职能–错误地执行了分配给他的职能–执行了未赋予的分外职能–按错误的程序或错误的时间执行了职能–执行职能不全面错误有各种不同的类别•几乎所有的缺陷都由人的错误而产生,人至少有十种错误–遗忘–误解产生的错误–识别的错误–新手错误–故意的错误–疏忽的错误–迟钝的错误–缺少标准的错误–意外的错误–蓄意的错误错误产生的基本原因–过程的遗忘:遗漏一个或多个过程步骤–过程的操作没有按标准工作程序实施–处理错误的工件–操作错误–对现行产品使用了不正确的工具或设备–遗漏部件–装配时安装了错误的部件–无SOP或指示不明,不清楚怎样操作–机器设备的设置、调整带来的错误–损害的刀具或不良的工装夹具等带来的错误什么是防错法?•定义:不管谁去做,不管做法如何,也不管做多少数量,结果是一样的,不会发生偏差。
简单的说,就是不管愚笨的还是心不在焉的人去做,都可以防止他做错的方法。
•为什么要防错?–质量和过程的稳定是精益生产的基本。
–所有的人都会犯错误–机器并不是不犯错误错误预防——目标•问题发现得越晚,所需的补救费用就会越多:问发得越晚所需的补救费用就会越多如果在这儿发现过失设计进行加工OP1OP2OP3OP4客户﹩10,000在这儿被发现,﹩100﹩1,000﹩10就要花费:﹩1产品质量控制点的四级水准•水准D:无检查项目•水准C:检验出不良•水准B:不流出不良品•水准A:不产生不良品不同质量保证战略的对比防错法的具体表现•即使有人为疏忽也不会发生错误——不需要注意力;•外行人来做也不会出错——不需要经验与直觉;•不管是谁或在何时工作都不会出差错——不需要专门知识和高超的技能防错法的作用•在作业过程中,作业者不时会因疏漏或遗忘而发生作业失误,由此所致的品质缺陷所占的比例很大,如果能够用防错法防止此类失误的发生,则品质水平和作业效率必会大幅提高。
李淑英-防差错技术培训教材
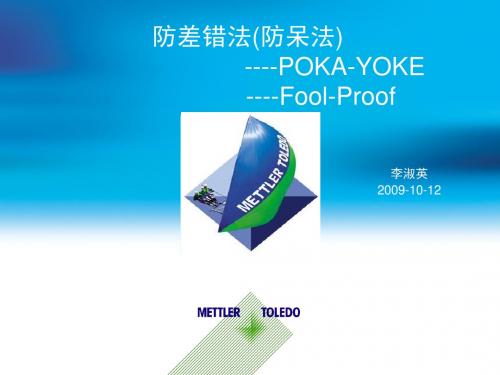
采用不同状 两个开关同时按下 才能开动机器 10
Internal usage only
目录
目的 意义 功用
应用范围
基本原则 基本原理 应用原理
11
Internal usage only
基本原则
使作业的动作轻松 使作业不要技能与直觉 使作业不会有危险 使作业不依赖感官
31
Internal usage only
目录
目的 意义 功用 应用范围 基本原则
基本原理
应用原理 案例分享
32
Internal usage only
改善案例分享
有形设计防差错
33
Internal usage only
改善案例分享
有形设计防差错
34
Internal usage only
28
Internal usage only
应用原理 –层别原理
以线条之粗细或形状加以区别
-例:所得税之申报单将申报人必需填与之数据范围记载在粗线框内。 -例:回函条请沿虚线之位置撕下。
以不同之颜色来代表不同之意义或工作之内容
-例:公文卷宗红色:代表紧急文件白色:代表正常文件黄色:代表机密文 件 -例:在生产在线将不良品挂上“红色”之标贴;将重修品挂上“黄色”之标
改善案例分享
改善前
AB两个机种类似,两个测试程序容易混
B有盖子
追加识别的探针,
A无盖子
改善后
- 追加识别的探针,A产品没有盖子
,探针是自然状态,B产品有盖子 ,探针是压缩状态
35
Internal usage only
改善案例分享
防错法知识培训
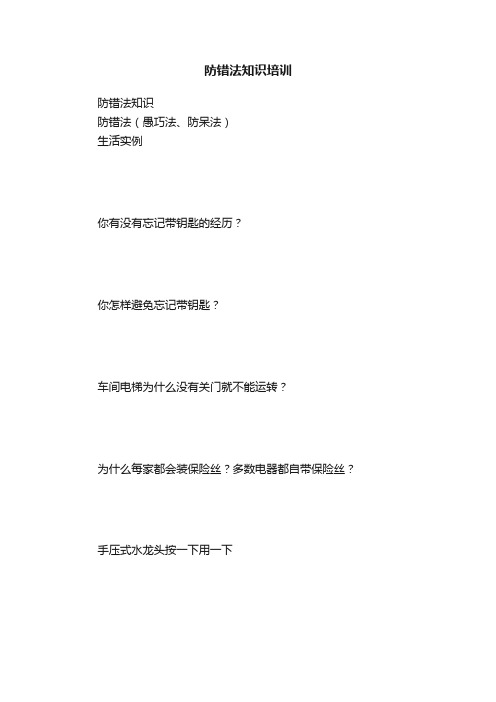
防错法知识培训防错法知识防错法(愚巧法、防呆法)生活实例你有没有忘记带钥匙的经历?你怎样避免忘记带钥匙?车间电梯为什么没有关门就不能运转?为什么每家都会装保险丝?多数电器都自带保险丝?手压式水龙头按一下用一下声控灯第一节防错法的概述及作用防错法日文称POKA-YOKE,又称愚巧法、防呆法。
意即在过程失误发生之前即加以防止。
是一种在作业过程中采用自动作用、报警、标识、分类等手段,使作业人员不特别注意也不会失误的方法。
在作业过程中,作业者不时会因疏漏或遗忘而发生作业失误,由此所致的质量缺陷所占的比例很大,如果能够用防错法防止此类失误的发生,则质量水平和作业效率必会大幅提高。
最明显的作用有以下3点:1、防错法意味着“第一次把事情做好”因为防错法采用一系列方法和工具防止失误的发生,某结果即为第一次即将事情做好。
2、提升产品质量,减少由于检查而导致的浪费防错法意味着“第一次即把事情做好”,直接结果就是产品质量的提高,与靠检查来保证质量相比,防错法是从预防角度出发所采取的预防措施。
而检查不能防止缺陷的产生,检查发现的缺陷只能去纠正。
这是一种浪费,防错法消除了这种浪费。
3 消除返工及其引起的浪费:防错法会提升产品质量,消除缺陷,这会导致返工次数的削减,由于返工所致的时间和资源浪费便得以消除。
失误与缺陷失误是由于作业者疏忽等原因造成的。
而缺陷是失误所产生的结果,比如由于作业者疏漏而产生装螺丝作业失误,而导致配件袋漏装一颗螺丝的缺陷。
缺陷与失误举例如下表:产生失误的一般原因产生失误的基本原因有以下九个1、忘记即忘记了作业或检查步骤,比如忘记在打吊树装八字夹之前先装上介子。
2、对过程/作业不熟悉。
由于不熟悉作业过程或步骤,产生失误就很难避免,如让一个刚经过培训的新手去打夹工序,产生失误的概率比熟手肯定大得多。
3、识别错误。
识别错误是对工作指令或程序判断或理解错误所致。
如包装过程中使用了同大小而不同PO的纸箱。
4、缺乏工作经验。
防差错(PPT 39页)

34
如何找出可以做防错的项目
1.刀 具 磨 损 2. 换 模 与 设 定 刀 具 3. 零 件 尺 寸 变 化 很
大 4. 多 工 序 的 过 程 5. 不 常 用 的 过 程
6. 未 按 标 准 进 行 的 过 程
7. 生 产 对 称 性 零 件 8. 快 速 重 复 的 作 业 9. 大 量 生 产 10. 会 影 响 产 品 质 量
小组成员 寻 找、 选 定 实 施 防 错 技 巧 的 区 域 实 施 防 错 措 施 ,消 除 错 误 和 产 生
不合格品的原因
37
防差错措施执行工作表
小 组 成 员: 过 程: 1、 缺 陷 原 因 说 明:
日 期:
2、 不 合 格 率:
产 品:
3、 缺 陷 在 何 处 发 现:
4、 不 合 格 率 在 何 处 发 生:
5
缺 陷-- 差 错 间 的 关 系
差错---过程 缺陷---产品
6
缺陷
• 车辆装上错误的选 项配备
• 冷凝水漏
• 异音或部件松动
• 门因撞到东西而损 坏
差错
• 错误的选项配备
被排入 组装线的 序列料架
• 组装时水管的束 紧器位置不对
• 磨损的组装工具 造成成型时夹具安 装不正确
• 在最后组装线门 未关
14
.基本理念
决不允许哪怕一点点缺陷产品出现,要想成为
世界级的企业,不仅在观念上,而且必须在实 际上达到“0”缺陷 生产现场是一个复杂的环境,每一天的每一件 事都可能出错,差错导致缺陷,缺陷导致顾客 不满和资源浪费 我们不可能消除差错,但是必须及时发现和立 即纠正,防止差错形成缺陷
防错技术-培训资料ppt课件.ppt

设备名称
设备编号
防错装置名称
1 三柱壳1#、2#、3#、4#、5#生产线 saet中频淬火机
2
三柱壳2#、3#、4#、5#生产线
外径检测机
2.4钟形壳线防错清单
C738-06/07/08/12/15 C571-07/08/14/15
涡流防错装置 外径检测机
防错编号 ZPFC-01 ZPFC-02 ZPFC-03 ZPFC-04 ZPFC-05 ZPFC-06 ZPFC-07
1) 将质量融入过程。 2 )所有无意识差错和不良均可避免。 3) 从现在开始立即停止将事做错。 4 )不要去想理由,而要考虑如何将事做对,要找理由总是有的,但防错是首要的 考虑,它是做对事的技术保证。 5) 60%的成功可能性就足够了,立即实施你的对策。 6 )只有共同努力,才能消灭不良,做到差错为0。置身其内,才能调动积极性, 贯彻其中,才能形成责任性。 7 )头脑风暴法及其重要。 8 )善用5-WHY和因果图,可找到差错的真正原因。
错误的根源是什么?
方法/作业因 –规定不明/没说/没教 –过程冗长/步骤繁琐 –要技巧/靠感觉 –要小心/要集中精神 –时间紧迫/工作量大/ 劳动强度太强 –…
物料/材料因 –品种/数量太多 –形状类似 –质量不良…
设备/工装因 –操作困难 –精度劣化/基准偏移 –安全威胁…
环境因 –高温/高湿/噪声 –混乱/拥挤 –昏暗/难识…
总成装配线 总成装配线 总成装配线 总成装配线 总成装配线
设备编号
防错装置名称
钢球直径大小防错装置
钢球数量红外线检测
C579-
OP20防止无卡簧或多卡簧报警装置
01/02/03/11 OP30压装固定节拉脱报警装置
培训及学习资料_防错技术.pptx
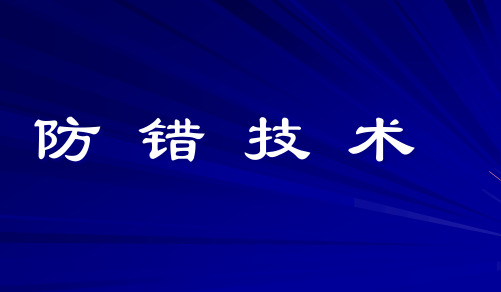
防错技术的装置或方法核心
例三:送往喷漆车间的小批量零部件根据每 批产品上所贴的号码确定喷漆的颜色,但是 有时工人会选错油漆,造成整批部件返工。
防错技术的装置或方法核心
例四:金属面板的制作工艺要求将一个长方 形的金属板伸入冲压机中,但是有时候工人 会把金属板伸入的方向弄颠倒。
防错技术的装置或方法核心
工作中的人为差错不仅仅意味着时间、金钱 的损失,还可能给员工带来危险和伤害,甚 至导致企业经营的失败……
99.9%的正确率意味着……
每个月有一小时的饮用水受到污染。 每天有两班飞机在首都机场降落时发生事故。 每天有50个新生儿从医生手中滑落在地上。 每周发生500起外科手术事故。 每小时有16,000封信被错误的投递。 每小时发生22,000次银行转帐错误。 每人每年心脏停跳32,000次……
防错技术的定义
“防错技术”的定义里蕴含着两方面的意义。
首先,必须能够发现潜在的问题;
其次,就是要消除特定产品缺陷产生的根源, 这又被称为“防错技术的装置或方法核心”。
发现潜在问题的方法
新卿重夫为发现潜在问题所采取的方法:
100%检验!
自检 后继检验
成功实施自检与后继检验的要求
1、明确检验目标 2、及时的反馈与行动 3、关心并支持员工 4、明确与自动化检验的关系 5、正确处理100%检验与周期延长的矛盾 6、强化自主管理(Jidoka)
思考…
相对于100%检验,传统抽样检验及统计 过程控制(SPC)的缺点有哪些…. 提示: 1、对抽样的依赖性 2、延时性 3、实用性 4、抽样检验的受制因素,如批量、生产稳定性、 某些产品特性检验对于机器、人的感觉的依
思考
1、自检与后继检验有哪些优点和缺陷? 2、为什么新卿重夫强调每天工作后专业检验技
- 1、下载文档前请自行甄别文档内容的完整性,平台不提供额外的编辑、内容补充、找答案等附加服务。
- 2、"仅部分预览"的文档,不可在线预览部分如存在完整性等问题,可反馈申请退款(可完整预览的文档不适用该条件!)。
- 3、如文档侵犯您的权益,请联系客服反馈,我们会尽快为您处理(人工客服工作时间:9:00-18:30)。
18
7
第五节 防错技术实施方法
第四步:评估选择可行方案
防错装置的选择标准 可靠 耐用 易维护 杜绝重犯 不影响操作 设计精巧 易用好使 便宜(500元以下)
8
第五节 防错技术实施方法
第五步:实施方案
尽可能快地实施防错方案。不要苛求防错方案可 以100%的解决问题,如果有50%的有效性就值得 尝试。 在实施中要注意: 得到所有相关人员的承诺。鼓励大家说出自己的 疑问,澄清相关问题,不要盲从。一旦取得共识, 大家就要全力以赴,达成目标。 自始至终使用相同的人员、零件、设备和程序, 以便减少差异,方便查找故障原因,尽量使方案 能够完全消除缺陷;
防差错技术(POKA-YOKE)应用
1
第五节 防错技术实施方法
2
第五节 防错技术实施方法
第一步:识别现有和潜在缺陷
用FEMA (潜在失效模式及后果分析) 的方法对过 程进行分析; 找出可能发生错误的地方; SPC数据; 客户投诉; 日常生产问题; 观察.
3
第五节 防错技术实施方法
第二步: 缺陷分析
5
第五节 防错技术实施方法
第三步:提出防错方案
“脑力风暴”是一种可以激发小组成员产生大量的 有创意点子的方法。 “Brain Storm”原则: 发掘集体智慧 追求数量 严禁批评 ……
6
第五节 防错技术实施方法
第四步:评估选择可行方案
对方案进行成本/ 效益分析,评审行动方案,选 择最优方案,在此基础上提出实施计划。 投资 收益 回报周期 后期维护成本 实施时间 风险 然后确定工序上的更改,选择合适的防错装置, 制定责任及时间表,分配所需的资源。
17
第五节 防错技术实施方法
防错技术发展方向
更多通用、方便、廉价的防错装置的出现; 防错技术更广泛的应用,不仅仅局限于生产制造 和安全,例如在人们的日常生活中会用到越来越 多的具有防错功能的产品; 成熟的防错工具和规范的出现; 随着科技产品的成本不断降低,传感器、视觉识 别等部件或系统在防错装置中被更多地采用。
14
第五节 防错技术实施方法
防错技术推广(3)
制定培训方案,对员工进行防错理论和应 用的培训和教育。首先要根据防错的一般 理论和方法,结合自己的生产工艺条件和 已有的防错案例编写适合的防错培训教材。
15
第五节 防错技术实施方法
防错技术推广(4)
所有的操作工人、工程人员和管理人员都 要经过防错概念和应用方面的培训。培训 的目的是,通过个人和团队的实践,将防错 与日常工作相联系。
找出缺陷发生的源头,用“QC7七工具”和“5Why” 方法找出根本原因: 涉及到生产中的哪些要素? 失误属于何种类型? 失误会造成什么缺陷? 找出失误和缺陷之间的联系。
4
第五节 防错技术实施方法
5 Why
案例:设备停机
第一个为什么:为什么停机了? ( 机器过载,保险烧了) 第二个为什么:为什么会过载? (轴承润滑不够) 第三个为什么:为什么润滑不够?(机油泵没抽上足够的油) 第四个为什么:为什么油泵抽油不够?(泵体轴磨损) 第五个为什么:为什么泵体轴磨损?(金属屑被吸入泵中) 第六个为什么:为什么金属屑被吸入泵中?(吸油泵没第五步:实施方案
在实施中要注意: 检查方案实施过程中是否满足周期时间的要求, 生产成本是否增加,有没有新的问题出现等。 根据顾客的反馈来决定缺陷是否已经消除。 用“恶心的试验”来验证防误措施。 “恶心的试验”就是故意制造一些错误以试验 防错措施是否有效,可以缩短调试时间,对所采 取的措施及时得到反馈。
11
第五节 防错技术实施方法
第七步:标准化和推广
对防错过程进行评审,,前面的过程和结果进行 总结、归档并补充数据库,探讨方案能否复制、 推广于其它类似设备和生产厂。 特别要强调的是改进工作的标准化,它包括: 为新的系统/装置建立文档、图纸; 更新现有文档,清理无用的文档; 重新评估现有的工作程序(包括操作、维护、检 查等)并进行必要的修定; 对相关人员进行培训;
12
第五节 防错技术实施方法
防错技术推广(1) 首先,需要成立一个由高层管理人员组成的 指挥小组,显示管理高层对项目的支持和承 诺,并保证能够取得所需的资源。
13
第五节 防错技术实施方法
防错技术推广(2) 其次,需要成立一个质量实施小组,由质量 人员和生产线上的各小组长组成,负责制定 防错装置的实际引入计划和具体实施步骤, 并将防错与“零缺陷”的战略目标相结合。
16
第五节 防错技术实施方法
防错技术推广(5)
通过示范项目引入防错体系。首先在各个生产线 上实施示范项目。目的是通过层次化的方式引入 防错的原则。下一个阶段就是对示范项目进行正 式评审,对其中的方法和效果进行总结和评估,然 后再进行全面实施。实施的长期目标是将防错过 程融入到日常工作中,培养整个企业的防错意识, 形成“零缺陷”文化。
10
第五节 防错技术实施方法
第六步:监控运行和评估
收集数据并与实施前相比较: 操作工是距生产线最近的人,最适合观察记录工 作。 工业工程师进行实地评测 质量工程师跟踪产品质量的变化。 不要急于结束改进小组的工作,改进小组还要定 时召开会议,将收集数据与实施前相比较,检查 缺陷是否已经消除并没有新的问题产生。