质量管理体系控制程序——制程检验管理程序
GBT19001-2016质量管理体系程序文件-014制程管理程序

版 次:03 修正码:1.0
深圳市铭鸿特科技有限公司 制程管理程序
文件编号:QP -014 页 次: 2 OF 2
要求,并作好日常维护、保养、维修、校验工作,具体按《量仪管理程序》规定执行。
详细书 面 报 告、 业务必须 妥善 协调沟通 客 户,合同变更后必须及时书面转达生产等
部 门 , 订单变更处理 具体按照《客 户服务管理程序》相关规定执行 。
4.14 防护标识:产品自材料到完工出货各环节,必须按照客户要求以及公司有关材质管理
要求规范准确标识产品材质、订单号、模件号等项目,并分区分类放置保管;
生产通知 单 》;
②复制记录表:业务《 ( 粗工 ) 生产通知单》内容分别复制粘贴于《 ( 备料 ) 自检记录
表》、《自 检记录 表》、《 产 品 检验记录 表》 对应栏次即形成以上三张记录表并
分别发放给仓库作下料自检记录、生产作生产自检记录、品检作产品质量检验记录。
4.11成品检验:产品生产完成后,品检根据图纸、订单要求、产品检验标准进行成品检验
现场产品必须区分合格品、不合格品、待工品、待检品等分类放置并标识记录 。
4.15 客户财产:客户提供图纸、代工产品必须明确标识、妥善保管。
4.16 记录保管:生产通知单、产品检验记录表、自主检查表、不合格品处理单等资料必须
予以受控保管,具体按《质量记录管理程序》执行。
4.17制程检验流程:
下单
生产
4.6 教育培训:对于新产品、新工艺、特殊重要产品、新上岗员工,必要时生产部、 品 质 部 应组织员 工 进 行 产 前培 训 ,确保生 产检验 人 员 明确 产 品工 艺 技 术 、 质 量交期 等要求并按正确要求 实 施作 业 。
质量管理五大核心工具APQP、PPAP、SPC、MSA、FMEA(精选)
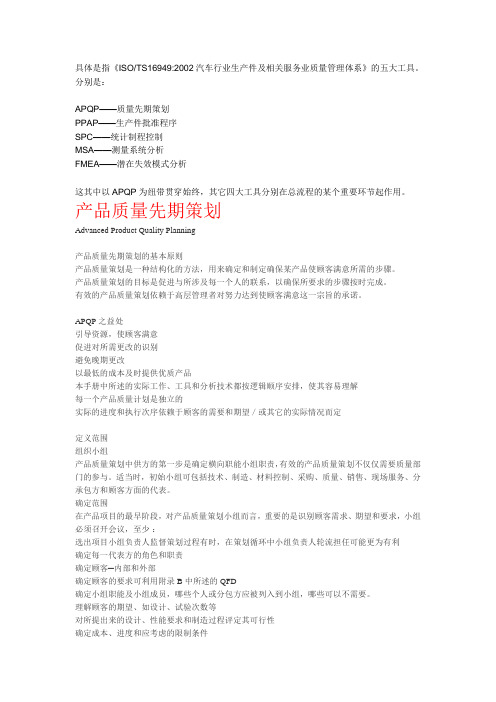
控制计划是控制零件和过程系统的书面描述,单独的控制计划包括三个独立的阶段:
样件:在样件制造过程中,对尺寸测量和材料与性能试验的描述。
试生产:在样件试制之后,全面生产之前所进行的尺寸测量和材料与性能试验的描述。
生产:在大批量生产中,将提供产品/过程特性,过程控制、试验和测量系统的综合文件。
问题的解决
第一阶段之输入
顾客的呼声
市场研究
保修记录和质量信息
小组经验
业务计划/营销策略
产品/过程基准数据
产品/过程设想
产品可靠性研究
顾客输入
第一阶段的输出作为第二阶段的输入
设计目标
可靠性和质量目标
初始材料清单
初始过程流程图
产品和过程特殊特性的初始清单
产品保证计划
管理者支持
顾客的呼声
“顾客的呼声”包括来自内部/外部顾客们的抱怨、建议、资料和信息。
确定范围
在产品项目的最早阶段,对产品质量策划小组而言,重要的是识别顾客需求、期望和要求,小组必须召开会议,至少:
选出项目小组负责人监督策划过程有时,在策划循环中小组负责人轮流担任可能更为有利
确定每一代表方的角色和职责
确定顾客─内部和外部
确定顾客的要求可利用附录B中所述的QFD
确定小组职能及小组成员,哪些个人或分包方应被列入到小组,哪些可以不需要。
APQP之益处
引导资源,使顾客满意
促进对所需更改的识别
避免晚期更改
以最低的成本及时提供优质产品
本手册中所述的实际工作、工具和分析技术都按逻辑顺序安排,使其容易理解
每一个产品质量计划是独立的
实际的进度和执行次序依赖于顾客的需要和期望/或其它的实际情况而定
HSF制程管制与检验管理程序
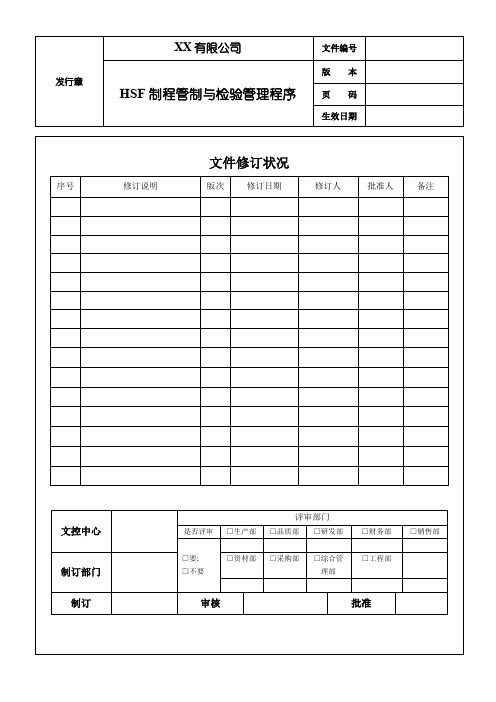
a、新产品每次导入时,由供应商提供有害物质测试报告。
b、每次检测之数据1年内保持有效。
c、供货商提供之有害物质测试报告,由品质部专人维护,在报告到期前一个月MAIL通知采购,由采购通知供应商提供更新有害物质测试报告。如在上一期报告到期日,但新报告还未提供者,则由我司直接送测,送测费用由供货商负担。
6.2.《HSF异常控制程序》
6.3.《HSF产品标识与追溯管理程序》
6.4《风险辨识和评价控制程序》
6.5.《HSF采购管理程序》
7.0.相关记录
7.1《产品批次流转卡》
7.2《质量状态标签》
7.3《生产日报表》
7.4.《首检记录》
7.5.《首件确认单》
7.6.《出货检验报告》
7.7《质量检验记录》
4.流程图:
无
5.程序内容:
5.1进料检验:
5.1.1.品质部进料检验员接到仓库开出的《采购收货报检单》后需核对以下信息:
1)确认供应商是否在《合格供应商名录》中,若不在合格供应商名录中的供应商送货,则及时将现况上报主管,并依照其指示做批退处理。
2)来料HSF标识及外箱标识(来料厂商名称、材料品名及规格、料号)是否清晰及符合我司要求;
文件修订状况
序号
修订说明
版次
修订日期
修订人
批准人
备注
文控中心
评审部门
是否评审
□生产部
□品质部
□研发部
□财务部
□销售部
□要;
□不要
制订部门
□资材部
□采购部
□综合管理部
□工程部
制订
审核
批准
1.目的:
为保证进入我司之所有原材料、辅助材料及出货成品均符合HSF(有害物质限制或消除)管理相关要求,以预防非环保品流入客户端,特制定本程序。
制程质量检验流程

制程质量检验流程一、导言制程质量检验是指在生产过程中通过对关键节点进行检验,以确保产品质量的有效控制过程。
通过制程质量检验,企业可以在生产过程中及时发现问题,并采取相应措施进行修正,以确保最终产品符合质量要求。
二、制程质量检验流程的重要性制程质量检验是实现质量管理的重要手段,它可以帮助企业提前发现问题,减少生产过程中的不良品率,提高产品质量和生产效率。
同时,制程质量检验还可以帮助企业节约成本,避免质量事故的发生,保护企业品牌形象。
三、制程质量检验流程的步骤1. 确定制程质量检验的关键节点制程质量检验需要确定生产过程中的关键节点,即需要进行检验的环节。
这些关键节点通常与产品的关键特征和工艺参数相关。
通过对关键节点进行检验,可以有效控制产品的制程质量。
2. 制定检验方法和标准根据产品的特点和质量要求,制定相应的检验方法和标准。
检验方法可以包括物理性能测试、化学成分分析、外观检查等。
标准可以是国家标准、行业标准或企业内部标准,确保检验结果的准确性和可靠性。
3. 编制检验计划根据制程质量检验的关键节点和检验方法,制定相应的检验计划。
检验计划包括检验时间、检验频率和样本数量等。
根据生产情况和风险评估,合理确定检验的频率和样本数量,以确保检验结果的代表性。
4. 进行制程质量检验按照检验计划进行制程质量的检验。
检验可以由质量管理部门的专业人员进行,也可以委托给第三方实验室或检验机构进行。
在检验过程中,要确保检验设备的准确性和精确度,严格按照检验方法和标准进行操作,记录检验结果和异常情况。
5. 分析检验结果收集和整理制程质量检验的结果,进行数据分析和处理。
通过对检验结果的分析,可以发现制程中存在的问题和潜在的风险,及时采取措施进行改进和修正。
同时,还可以找出制程的优势和改进的方向,为制程质量的持续改进提供参考和依据。
6. 采取纠正措施并改进制程根据分析的检验结果,采取相应的纠正措施进行改进。
纠正措施可以包括优化工艺参数、调整工作流程、更换检验设备等。
过程和产品检验控制程序

1.0目的对质量管理体系各个过程进行监测,对影响产品质量的过程进行监视测量,以明确满足顾客的要求;对产品特性进行监视和测量,以确保产品要求得到满足。
2.0适用范围适用对质量管理体系过程进行监视和测量,以及对生产所用的原材料和产品生产过程、和成品进行监视和测量。
3.0职责3.1管理者代表负责对质量管理体系过程进行监视和测量;3.2质检组负责对产品进行监视和测量,并负责督促操作员工在生产过程中对产品进行自检。
4.0程序4.1过程的监视和测量4.1.1管理者代表负责监视和测量公司的质量目标和各部门的质量目标的完成情况。
包括根据产品特点策划的各过程和子过程,特别是生产过程;4.1.2对与质量相关的各过程在适用时可以采取测量的方式,如工作质量的检查活动等;4.1.3在某些时候,对质量体系进行的内部审核、管理评审等系统性的活动,可以看作是对质量体系过程的监视和测量。
4.2产品的监视和测量4.2.1质检组负责编制《来料检验作业指导书》和《成品检验作业指导书》,明确检测点、检测频率、抽样方法、检测项目和方法、判别依据、使用的检测设备等。
4.2.2进货验证A.对进公司的物料,采购员先核对送货单,确认物料的品名、规格、数量等无误、包装无损坏后,先放置到指定的待检区,仓库保管员确认原材料的名称、规格、数量与送货单相符以及包装无损后,用《物料标识卡》作好标识;并由采购员填写《原料检验通知单》给质检组;B.质检组依据《来料检验作业指导书》进行抽检,并记录《来料检验报告单》,将检验结果反馈给业务部采购员;C.经验证合格的原材料,由采购员凭《来料检验报告单》向仓库保管员办理入库手续。
对检验不合格的,由质检组出示《来料检验报告单》,在《物料标识卡》检验状态栏里注明“不合格”字样作为标识,并按《不合格控制程序》的有关规定处理;D.紧急放行生产急需而来不及验证的原材料,在可追溯的前提下,由生产部门填写《紧急(例外)放行申请单》经质检组主管审核,报总经理批准后,方可进入生产车间使用。
IATF16949:2016质量管理体系过程关系图
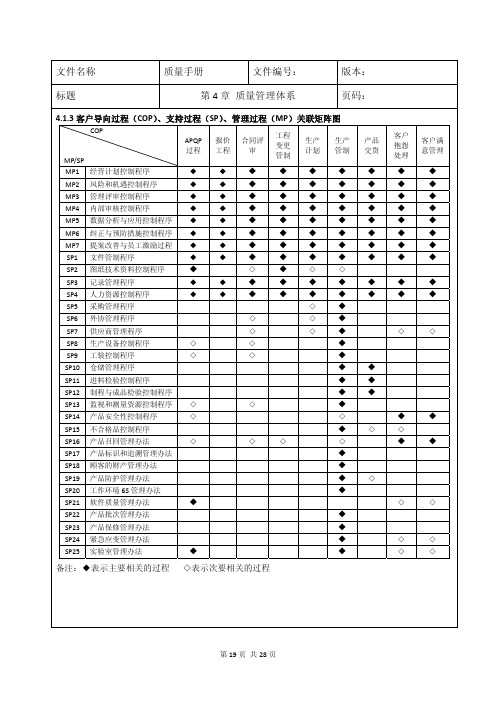
过程 类别
过程名称
总经 市场 销售 技术 开发 供应 理部部部部部
COP1 产品质量先期策划控制程序 ○
○●●○
COP 2 报价控制程序
○●
○
○
COP 3 合同评审控制程序
●
○○○
COP 4 工程变更控制程序
○
●●○
COP5 生产计划控制程序
○
○○○
COP 6 生产制程控制程序
○○○
COP 7 产品交货控制程序
●
○
COP 8 客户抱怨/退货控制程序
○●○○○○
COP 9 客户满意度控制程序
●●
MP1 经营计划控制程序
●○○○○○
MP2 风险和机遇控制程序
●○○○○○
MP3 内部审核程序
○○○○○○
MP4 管理评审程序
●○○○○○
MP5 分析评价及应用控制程序
○○○○○○
MP6 纠正与预防措施控制程序
○○○○○○
MP7 提案改善与员工激励程序
○○○○○○
SP1 文件控制程序
○○○○○○
SP2 图纸技术资料控制程序
●●○
SP3 记录控制程序
○○○○○○
SP4 人力资源控制程序
○○○○○○
SP5 采购控制程序
○○○○○●
SP6 外协控制程序
○○●
SP7 供应商控制程序
○○●
SP8 生产设备控制程序
○
○○○
SP9 工装控制程序
○○○
SP10 仓储管理程序
○○
●
SP11 进料检验控制程序
○○○
SP12 制程与成品检验控制程序
○○
体系制程产品内部审核管理程序

1目的本文件定义了内部审核及其他满足特定目的需要的内部审核的职责和流程,以确保内部审核得到有效的开展,从而提升系统运作的符合性和有效性,确保稳定受控的制程能力和产品的实物质量。
2适用范围本文件适用于000。
3参考文件4定义4.1审核:为获得审核证据并对其进行客观的评价,以确定满足审核准则的程度所进行的系统的、独立的并形成文件的过程。
4.2审核方案:针对特定时间段所策划,并具有特定目的的一组审核。
4.3审核准则:用作依据的一组方针、程序或要求。
4.4制程审核:对生产工序的质量能力进行评定,促使制造过程达到受控,并能在各种干扰因素的影响下仍然稳定受控。
4.5产品审核:以规定的频率,在生产及交付的适当阶段对产品进行审核,以验证符合所有规定的要求,例如:产品尺寸、功能、包装和标签等。
4.6重大产品质量问题:导致重大顾客投诉和/或产品因质量问题而批量退回/召回,包括强制性产品认证不通过和监督检查不通过。
5职责5.1总经理负责批准年度审核方案及年度审核总结报告。
5.2总办5.2.1编制和审核年度内审方案;5.2.2组织实施内部审核工作;5.2.3审核和提交内审报告;5.2.4负责组织对内部审核中发现的不符合项督导改善与效果验证;5.2.5负责本内部审核所有相关资料的归档;5.2.6负责内部审核员管理;5.2.7负责向推荐或指派合适的审核员参加级内部审核工作;5.3体系5.3.1负责制定级年度审核方案,组织实施,公布审核结果并就审核中发现的不合格项督导改善;5.3.2负责内部审核员的选择、评价及监督管理,协调并安排内部审核所需的资源;5.3.3视需要,协助各内部审核的实施;5.3.4视需要组织专项审核,并就审核中发现的严重问题酌情报告总经理;5.3.5负责撰写年度审核方案执行总结报告,并提交管理层评审;5.3.6负责内部审核所有相关资料的归档。
5.4受审核单位:负责配合审核方案的实施,并就发现的不合格项予以改善。
IPQC是制程检验

IPQC是制程检验,主要负责对生产线开始投产的第一个产品进行首件确认(外观,机构,电性),进行对生产人员进行QC就是质量控制,质量管理的意思IPQC就是对半成品的质量检验及管理AQC就是对成品的质量检验及管理IPQC就是品质检验和控制,IQC就是生产过程中对品质的跟踪,QA就是品质检验,也是对贴好PCB进行抽检我觉得你完全可以做好,因为那都是些很简单的东西,一学就会的!IPQC也就是制程过程的质量控制,也叫制程检验。
工作很筒单,也很单一,只需要看看产品,做做记录就可以了QC分四個階段:IQC(進料檢驗),IPQC(過程檢驗),FQC(最終檢驗)OQC(出貨檢驗IPQC是為了防止生產人員自檢的漏洞而設置的,所謂DUBLE CHECK,象產品流程一道防火牆,盡力將問題發現在萌芽階段QC的全称是QUALITY CONTROLLER(品质控制员),是负责检验产品,控制品质的人。
服装QC 顾名思义就是控制服装品质的人了。
按照我的理解,QC跟INSPECTOR(验货员)是两个不同的概念,QC的重点是在控(CONTROL),目的是使公司得到品质良好的产品;而INSPECTOR只是通过INSPECT(检验),而判断一批货是否合格品(PASS OR FAIL),目的是避免公司收到不合格的产品。
不过现在多数人都是把QC和INSPECTOR混为一谈的,我们在这里也都叫QC吧。
有些公司对每款服装只在出货前进行一次尾期检验(FINAL INSPECTION);有些至少要查一次中期(INTER INSPECTION INSPECTION)和一次尾(FINAL);有些甚至要在服装生产的全过程进行品质控制,进行多次的早期检验(EARLY INSPECTION)或在线检验(IN-LINE INSPECTION),以尽可能早地发现问题解决问题。
CLInetLabIQC(以下简称IQC)是CLInet在多年开发维护EQA(实验室间质量评价)系统后,成功开发的一套完善的实验室内部的质量评价、质量控制的软件。
制程质量控制程序
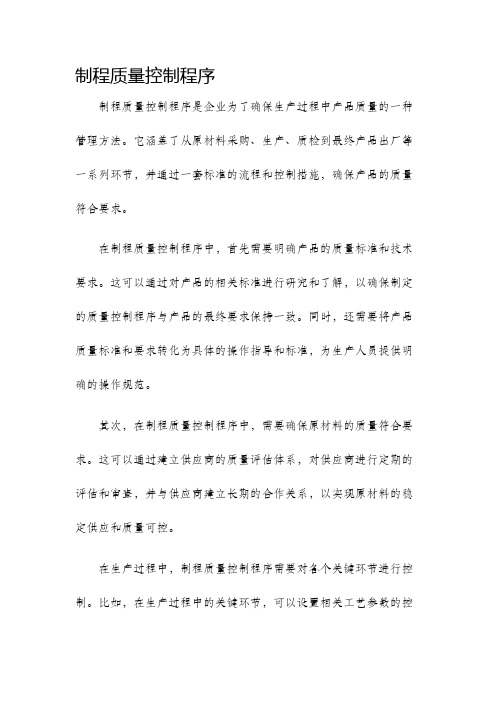
制程质量控制程序制程质量控制程序是企业为了确保生产过程中产品质量的一种管理方法。
它涵盖了从原材料采购、生产、质检到最终产品出厂等一系列环节,并通过一套标准的流程和控制措施,确保产品的质量符合要求。
在制程质量控制程序中,首先需要明确产品的质量标准和技术要求。
这可以通过对产品的相关标准进行研究和了解,以确保制定的质量控制程序与产品的最终要求保持一致。
同时,还需要将产品质量标准和要求转化为具体的操作指导和标准,为生产人员提供明确的操作规范。
其次,在制程质量控制程序中,需要确保原材料的质量符合要求。
这可以通过建立供应商的质量评估体系,对供应商进行定期的评估和审查,并与供应商建立长期的合作关系,以实现原材料的稳定供应和质量可控。
在生产过程中,制程质量控制程序需要对各个关键环节进行控制。
比如,在生产过程中的关键环节,可以设置相关工艺参数的控制范围,并对生产设备进行定期的维护和保养,以确保设备的运行状态稳定可靠。
同时,还可以通过设置工艺流程和生产作业指导书等方式,对生产人员进行培训和指导,确保生产过程中的操作规范和质量要求得到满足。
制程质量控制程序还需要进行定期的质量检验和测试。
通过对关键工艺环节的质量检验和控制,可以及时发现和纠正生产过程中的质量问题。
这可以通过使用各种质量检测工具和设备,如流程控制图、检验工具、专用设备等,来完成。
同时,在建立质量档案的基础上,可以对质量问题进行追踪和分析,并采取相应的措施进行改进。
制程质量控制程序还需要建立一套完善的质量管理体系。
这可以通过制定相关的质量管理制度和规程,明确各级质量管理人员的职责和权益,以确保质量管理的有效运行。
同时,还需要建立一套质量管理的绩效评估和改进机制,对各个关键环节进行监控和考核,推动质量管理工作的持续改进。
质量管理体系文件:持续改进控制程序
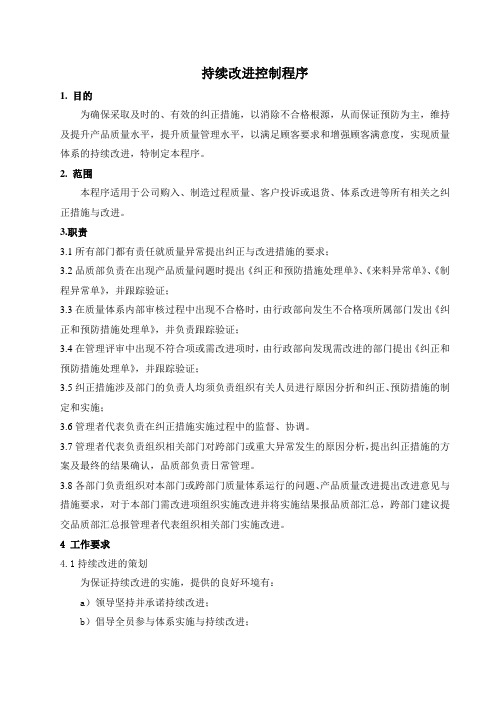
持续改进控制程序1. 目的为确保采取及时的、有效的纠正措施,以消除不合格根源,从而保证预防为主,维持及提升产品质量水平,提升质量管理水平,以满足顾客要求和增强顾客满意度,实现质量体系的持续改进,特制定本程序。
2. 范围本程序适用于公司购入、制造过程质量、客户投诉或退货、体系改进等所有相关之纠正措施与改进。
3.职责3.1所有部门都有责任就质量异常提出纠正与改进措施的要求;3.2品质部负责在出现产品质量问题时提出《纠正和预防措施处理单》、《来料异常单》、《制程异常单》,并跟踪验证;3.3在质量体系内部审核过程中出现不合格时,由行政部向发生不合格项所属部门发出《纠正和预防措施处理单》,并负责跟踪验证;3.4在管理评审中出现不符合项或需改进项时,由行政部向发现需改进的部门提出《纠正和预防措施处理单》,并跟踪验证;3.5纠正措施涉及部门的负责人均须负责组织有关人员进行原因分折和纠正、预防措施的制定和实施;3.6管理者代表负责在纠正措施实施过程中的监督、协调。
3.7管理者代表负责组织相关部门对跨部门或重大异常发生的原因分析,提出纠正措施的方案及最终的结果确认,品质部负责日常管理。
3.8各部门负责组织对本部门或跨部门质量体系运行的问题、产品质量改进提出改进意见与措施要求,对于本部门需改进项组织实施改进并将实施结果报品质部汇总,跨部门建议提交品质部汇总报管理者代表组织相关部门实施改进。
4 工作要求4.1持续改进的策划为保证持续改进的实施,提供的良好环境有:a)领导坚持并承诺持续改进;b)倡导全员参与体系实施与持续改进;c)鼓励持续改进和创新工作;d)为员工提供培训和必要的资源,保证改进和创新工作。
公司确定并选择改进机会,采取必要措施,以满足顾客要求和增强顾客满意,主要包括以下三个方面的内容:a)改进产品和服务,以满足要求并应对未来的需求和期望,赢得顾客的信任并为顾客创造价值,助力公司持续成功;b)纠正、预防或减少不利影响;以问题为导向,针对质量管理体系及其过程运行中发现的问题,通过采取纠正和必要的纠正措施或预防措施消除、减少、防止问题的发生或不利影响。
质量管理体系文件:检验控制程序

检验控制程序1 目的通过对来料、生产过程及成品各环节实施必要的检验与验证活动,获取产品特性符合性信息,对产品质量全面分析及改进,使产品质量不断提升,最终使客户满意。
本程序特规定来料检验、过程检验、成品检验、紧急放行等环节的要求与程序。
2 范围本程序适用于公司所有产品的监视和测量过程。
3 职责3.1品质部负责编制检验规范、流程等检验文件;实施对各阶段产品的检验或验证,放行产品;并负责记录、统计、保存检测数据,以及物资检验状态的标识;负责不合格品的标识、隔离、控制与管理。
3.2物管部负责接收采购的物资,到货后及时向检验员报检。
需验证尺寸、功能特性的物资,相关部门应提供产品图样、技术规范或技术协议要求等验收依据。
3.3营销中心负责接收顾客财产,验收后及时向检验员报检。
需验证尺寸、功能特性的物资,需对接顾客提供检验依据。
3.4 技术部负责指导、分析、处理产品过程中出现的技术问题;3.5制造部负责制造过程中各工序的自检和互检以及合格后按程序提交检验。
4 工作程序4.1来料检验来料检验是指对进货物资做品质确认和查核,判断其质量是否符合技术要求,并严格控制不合格品流程。
4.1.1 来料检验方法a)外观检测:一般用目视进行验证;b)尺寸检测:一般用卡尺、千分尺、三坐标等量具验证;c)结构检测:一般用拉力器、扭力器、硬度计验证;d)特性检测: 如电气的、物理的、机械的特性,一般采用检测仪器和特定方法来验证。
4.1.2来料检验方式a)全检:适用于检验过程简单、数量少、价值高、检验不会对产品破坏、关键的性能要求高的、不良品对后道工序造成严重后果的或者指定进行全检的物料。
b)抽检:适用于质量较稳定,批量太大、检验成本昂贵、检验会对产品会造成破坏的、非关键件的物料。
c)免检:供应商送货连续十批次完全合格收货的可以考虑免检。
适用于数控系统、光栅尺、线轨等产品。
4.1.3来料检验的流程a)采购员提前通知物管部来料情况以及明细,物资到厂后,应立即通知物管部一起进行来料核对,确认来料的名称、规格、型号、数量、外观等,无误后,物管部将物料置于待检区或做好待检标识,与采购部做好交接,填写入库单连同有关质量证明文件或质量记录,向品质部报检。
IATF16949质量管理体系流程全图(品质保证流程图)

TZQP-PG-004 产品鉴别与追溯管理程序
TZQP-PG-003 采购产品品质管理程序TZQP-CG-001 采购管理程序
TZQP-PG-003 采购产品品质管理程序TZQP-PG-012 品质异常处理程序TZQP-SJ-006 模治具管理程序TZQP-GL-004 6S 管理程序TZQP-ZZ-001 制程管制程序TZQP-PG-009 检验与测试管理程序TZQP-GL-013 资料分析与持续改进管理程序TZQP-PG-013 纠正与预防措施管理程序TZQP-PG-010 信赖性试验管理程序
TZQP-SG-003 紧急应变管理程序
TZQP-GL-013 资料分析与持续改进管理程序
TZQP-GL-011 客户财产控制程序
TZQP-SJ-004工程变更管理程序
TZQP-PG-008 统计技术管理程序
TZQP-GL-005 员工激励与满意度调查管理程TZQP-SJ-001合理化管理程序TZQP-GL-001 记录管理程序TZQP-SG-001 交货管理程序TZQP-PG-014 客户抱怨管理程序TZQP-PG-011不合格品管理程序
TZQP-PG-005 量测系统分析管理程序TZQP-GL-006 训练管理程序TZQP-GL-010 经营计划管理程序TZQP-GL-012 内部质量审核管理程序TZQP-GL-007 产品审核管理程序
TZQP-YY-002 服务管理程序TZQP-SG-002搬运储存包装管理程序TZQP-PG-007 实验室管理程序
TZQP-PG-006 检验、测量与测试设备管理程序
TZQP-PG-004 产品鉴别与追溯性管理程序
TZQP-PG-001 品质会议管理程序。
质量管理控制程序

处京癥建一建殺工程韦限公司质量管理投制程為QB / C J Y/QES 2005-0 91.目的为了对施工生产活动的全过程进行质量监控,预防不合格的成品、半成品流入下道工序或交付用户使用,保证工程质量满足规定要求,并使管理体系运行中出现的不符合项和施工过程中出现的不合格过程及不合格品得到有效地纠正和预防,特制定本程序。
2.适用范围本程序适用于公司承建的匸程项L1的施工质量管理控制工作.3.职责3.1公司总工程师负责领导组织贯彻执行国家、行业、地方的技术标准、规范、工艺标准;督促、指导分管机构履行和落实质量职责,开展各项质量管理、监督、指导活动;组织领导参与工程质量创优评比活动;并组织有关职能部门和机构对重大质量事故的调查处理,制定质量整改措施和处理方案,并监督、指导实施.3.2公司质量管理部负责编制并实施本程序。
质量管理部、技术发展部、丄程管理部负责对工程的施工质量控制情况进行监督、检查和考核。
3.3项訂管理公司、专业分公司质量部门负责对下属工程的施工质量控制情况进行监督、检查和考核.3o 4项訂经理部经理负责组织实施本项忖的质量管理工作;项LI经理部生产、技术、质量负责人对参施单位的工程质量进行检查、预控,并完成文件规定的各种检查验收记录.并应针对本部门(单位)出现的不合格项、不合格过程及不合格品,采取有效的纠正和预防措施.4.工作程序工作流程图:定年度质量LI标、质量保证措施,下发公司《年度质量管理U标和措施》。
4. 1 o 2项目管理公司、专业分公司根据公司当年施工生产任务和公司总体质量目标的要求,及公司下发的《年度质量管理口标和措施》,制定年度质量tJ 标、质量保证措施,并报公司质量管理部审批。
4.1o 3项□经理部为确保工程质量LI标,依据国家工程质量验收规范、北京市工程质量验收规范、《北京市建筑结构长城杯工程评审管理办法》、《北京市建筑长城杯工程评审管理办法》、《建筑工程施工质量验收统一标准》,制定质量保证措施、质量奖罚管理办法。
制程检验作业管理办法(4篇)

制程检验作业管理办法第一章总则第一条为规范和管理制程检验作业,提高制程检验的效率和质量,制定本办法。
第二条本办法适用于所有需要进行制程检验的生产和加工工序。
第三条制程检验作业是指在生产和加工过程中,对每个工序进行定期、抽样或全检,以判断该工序的合格性和相应控制措施的有效性的检验活动。
第四条制程检验的目的是确保每个工序的产品符合质量要求,并能够及时发现和纠正生产和加工过程中的不良问题。
第五条制程检验作业应依照规定的程序、标准和方案进行,确保检验结果的准确性和可靠性。
第六条制程检验作业应由专门的检验人员执行,确保其技术水平和素质要求。
第二章制程检验作业的组织与管理第七条制程检验作业应由生产或加工工序的质量管理部门负责组织和管理。
第八条质量管理部门应根据产品生产和加工工序的特点,制定相应的制程检验计划,并定期进行评估和调整。
第九条制程检验计划应包括以下内容:(一)工序的检验项目、方法和标准;(二)检验频次和抽样方案;(三)检验人员的培训和考核计划;(四)不合格品的处理程序和措施。
第十条质量管理部门应确保制程检验作业的实施符合质量管理体系的要求,并进行相应的记录和报告。
第十一条质量管理部门应与生产或加工工序的相关责任部门建立良好的沟通与协调机制,及时处理制程检验中的问题和反馈意见。
第十二条质量管理部门应定期进行制程检验的绩效评估,不断改进检验方法和流程,提高制程检验的效率和质量。
第三章制程检验作业的流程和方法第十三条制程检验应采用科学、合理的方法,确保检验结果的真实性和准确性。
第十四条制程检验的流程一般包括以下几个环节:(一)工序准备:对即将进行检验的工序进行准备工作,包括准备检验设备和工具,获取检验所需的样品和数据等。
(二)工序执行:按照检验计划和标准对工序进行检验,对样品进行抽样、检测、记录和分析。
(三)结果判定:根据检验结果和标准,判断工序的合格性,并进行相应的记录和处理。
(四)问题处理:对不合格的产品或工序,进行问题分析、控制和改进措施的制定,并记录和追踪其整改情况。
ISO-9001 质量管理体系-SPC控制程序

XX X X X X X有限责任公司企业标准XXXXXSPC控制程序XXXXX有限责任公司发布XXXXX前言根据质量、环境、职业健康安全管理体系要求,结合公司标准体系管理要求,制定本标准。
本标准由XXXXX有限责任公司技术质量部提出。
本标准由XXXXX有限责任公司技术质量部归口。
本标准由XXXXX有限责任公司技术质量部起草。
本标准主要起草人:XXX本标准审核人:XXX本标准批准人:XXX本标准于2016年8月首次发布。
XXXXXXSPC控制程序1 范围1.1 主要用于对过程的控制,使控制过程处于“受控”状态。
因为过程的问题是根源,需要对过程进行定时检查,以达到尽早找出问题,减少浪费之目的。
采用适当的统计技术,确保产品质量得到有效控制。
1.2 适用于产品质量形成的各个有关过程。
2 规范性引用文件下列文件中的条款通过本标准的引用而成为本标准的条款。
凡是注日期的引用文件,其随后所有的修改单(不包括勘误的内容)或修订版均不适用于本标准,然而,鼓励根据本标准达成协议的各方研究是否可使用这些文件的最新版本。
凡是不注日期的引用文件,其最新版本适用于本标准。
无3 术语3.1 SPC:全称为 Statistical Process Control(统计过程控制)是应用统计技术,分析过程中的质量特性,从而控制过程变异。
4 管理职责4.1 技术质量部负责统计技术的运用与管理以及产品质量统计数据的分析﹑整理与公布。
4.2 生产部负责纠正预防措施的制定与执行。
5 标准内容- 1 -- 2 -5.10.1 计量型控制图:其特点是可以连续读取这些数据,如长度、重量等。
5.10.2 计数型控制图:其特点是不可连续读取这些数据,只可读取整数,如不合格个数、缺点数等。
5.11 常用控制图5.11.1 单值-移动极差(X-MR)控制图。
5.11.2 P-Chart 不良率(计数型)控制图。
5.12 控制图的应用5.12.1 客户无特殊要求时,对特殊特性作控制图。
制程检验作业管理办法(4篇)
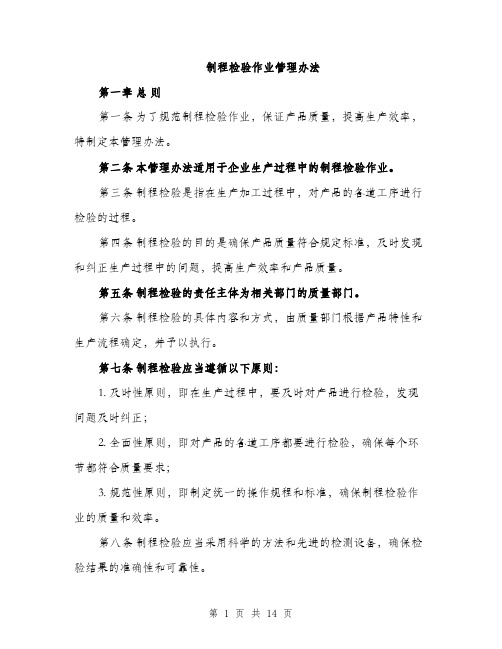
制程检验作业管理办法第一章总则第一条为了规范制程检验作业,保证产品质量,提高生产效率,特制定本管理办法。
第二条本管理办法适用于企业生产过程中的制程检验作业。
第三条制程检验是指在生产加工过程中,对产品的各道工序进行检验的过程。
第四条制程检验的目的是确保产品质量符合规定标准,及时发现和纠正生产过程中的问题,提高生产效率和产品质量。
第五条制程检验的责任主体为相关部门的质量部门。
第六条制程检验的具体内容和方式,由质量部门根据产品特性和生产流程确定,并予以执行。
第七条制程检验应当遵循以下原则:1. 及时性原则,即在生产过程中,要及时对产品进行检验,发现问题及时纠正;2. 全面性原则,即对产品的各道工序都要进行检验,确保每个环节都符合质量要求;3. 规范性原则,即制定统一的操作规程和标准,确保制程检验作业的质量和效率。
第八条制程检验应当采用科学的方法和先进的检测设备,确保检验结果的准确性和可靠性。
第九条制程检验结果应当记录,并及时反馈给相关部门,以便做出相应的调整和改进。
第十条制程检验作业过程中发现的问题,应当及时报告,并采取对应措施进行处理。
第二章制程检验作业流程第一节检验准备第十一条在进行制程检验作业之前,需要对相关设备和仪器进行校验和调试,确保其正常运行。
第十二条制程检验前,相关人员应当进行培训,了解检验标准和要求,熟悉操作流程。
第十三条制程检验前,应当准备好检验样品和检验记录表,确保检验的顺利进行。
第二节制程检验第十四条制程检验应当按照规定的检验方法和标准进行,确保结果的准确性和可靠性。
第十五条制程检验应当在生产过程中进行,及时发现和纠正问题,确保产品质量符合要求。
第十六条制程检验过程中发现的问题,应当及时进行记录,并通知相关部门进行处理。
第三节检验结果处理第十七条制程检验结果应当及时反馈给产品质量管理部门。
第十八条制程检验结果不合格的,应当进行追溯,找出原因,并采取相应的纠正措施。
第十九条制程检验结果合格的,应当及时进行记录和归档,并通知相关部门。
- 1、下载文档前请自行甄别文档内容的完整性,平台不提供额外的编辑、内容补充、找答案等附加服务。
- 2、"仅部分预览"的文档,不可在线预览部分如存在完整性等问题,可反馈申请退款(可完整预览的文档不适用该条件!)。
- 3、如文档侵犯您的权益,请联系客服反馈,我们会尽快为您处理(人工客服工作时间:9:00-18:30)。
确保生产过程产品品质能够满足规定的要求,及时发现制程产品的不合格或潜在的不合格,通过对检验记录进行统计分析,持续改进,不断提高产品品质。
2.0范围
本程序适用于本公司制程管制、生产条件的检验确认、作业方法的稽核。
3.0定义
3.1首件确认:指在生产前对其生产工艺及材料进行品质和一致性确认,避免在量产时造成批量性的不良。
3.2自检作业:指作业员按照作业指导书要求对该工序产品品质进行检查。
3.3互检作业:指后工序作业员对前工序产品的品质进行检查。
4.0权责
4.1品质部:负责产品实现全过程的检验控制,对制程中的品质异常提出处理意见,控制不良率。
开据《品质异常纠正措施单》追踪查核品质异常时其部门拟定的纠正措施,跟催及验证改善措施的有效性;负责不良品的原因分析,并提出有效对策及返工作业程序。
4.2生产部:首件的制作,负责对生产过程进行自检,针对生产过程中的品质异常,制定并执行纠正措施,对不合格品返工进行具体指导作业。
4.3责任单位:对《品质异常纠正措施单》中所提出的问题或缺失,提出改善和预防对策。
5.0内容
5.1制程控制流程图见(附件一):
5.2首件确认时机:新产品生产、产品间断性生产、换料、换人、机器故障、更换机台。
5.3首件品生产:生产部门在生产前4小时完成首件生产并认真对首件成品进行自检,确认OK后,再将首件确认品交IPQC进行品质确认。
5.4首件确认
5.4.1 IPQC在确认时应依据:BOM清单及工程图纸/工程样板/安规、EMC清单/客户邮件等相关资料进行确认,IPQC需在2小时内完成首件确认,并将确认结果记录于《首件检查表》,再交生产组长及品质组长确认,由品质部主管核准。
5.4.2确认项目:材料/加工工艺/尺寸/外观/特性/包装等方面进行品质确认及一致性检查,及时发现问题,避免在量产时造成批量性的不良。
5.4.3首件成品经IPQC确认不合格,需退回生产部,要求重新制作首件品,经确认合格后方可批量生产,首件确认不合格品依《不合格品控制程序》执行。
5.5.1自检:作业员在作业时依《产品工序作业指导书》对该工序产品品质自主检查,发现不良应及时标识隔离,以防止不合格品流入下一工序,同时通知现场领班进行改善。
若无法确定应及时通知现场IPQC确认。
5.5.2互检:则是后工序作业员在检查本工序产品品质同时,还要对上工序半制品或成品进行品质确认,若发现不良应及时标识隔离,同时要把问题点通知上工序作业员,问题较严重或不良较多还应及时通知现场管理人员和IPQC。
5.6巡检
5.6.1检验依据
IPQC依据《QA检验作业指导书》、《工序作业指导书》、工程样板、各段巡检报表项目等对各工序进行巡回抽检及品质判定,巡检时还包括对作业员的作业方法/品质状况/状态标识/设备运行状况/机器设备点检记录/作业指导书等项目进行确认,巡检结果记录于各段巡检报表上,以便追溯和统计分析。
5.6.2制程巡检频率
IPQC在巡检时,品质记录频率为2小时记录一次,(注释:2小时并不表示该工序巡检后非要等2小时再巡检此工序,只表示在这两小时中巡检发现的问题点记录于这时间段),巡检时还应考虑该产品品质稳定状况及此产品不良履历和客户投诉的问题点,再合理安排巡检力度,重要工序/新人上岗/换物料/工序品质不稳定等情形应重点跟踪。
5.7巡检异常反馈
制程异常反馈规则如下:
a)同一工艺不良连续出现2台;
b)同一结构不良连续出现2台;
c)同一电性不良连续出现2台;
d)单项不良占4%以上;
e)总不良影响制程生产效率超过5%;
IPQC应填写《品质异常纠正措施单》交品质部组长确认,主管核准。
最后将异常单给责任单位进行原因分析和制定改善及处理对策,IPQC负责追踪不良现象的处理及对策有效性的追踪。
已生产出的不良品IPQC应即时标识隔离,放入指定的红色不良品框或指定地方以便识别。
同时需把问题点反馈给现场FQC,以便FQC在全检时重点跟进。
5.8制程异常的追踪确认
针对在巡检中所发现的不良品或不良批次,IPQC除标识隔离外,还需对不良品的流向及处理方式进行追踪确认,对责任单位回复的《品质异常纠正措施》进行确认,(确认原因分析是否正确,改善对策制定是否合理等),若回复不符要求则退回责任单位重新分析,责任单位在改善过程中IPQC应进行全程跟踪验证。
5.9巡检发现之不合格品或不合格批处理
对已判不合格产品或批次,IPQC应及时标识隔离,生产单位对已返工之不良品或不良批次必须重新上线重流生产,如确实无法维修的不合格品,参照《不合格品的控制程序》执行。
5.10制程中发现原材料不良的处理方式
制程中生产部门发现材料不良情形,应及时通知现场IPQC确认,此时IPQC需对已做好的半制品或成品进行标识隔离,并及时通知IQC对此款材料的库存进行品质再确认,经确认在库材料不良,需标识隔离,同时品质部需及时开出《品质异常纠正措施单》知会相关单位和通知供应商改善。
5.11 FQC检验(最终检验)
5.11.1全检中发现不良品应及时标识隔离,并将检验结果记录于《FQC检验日报表》。
5.11.2全检作业中发现不良率超出相关文件规定时,FQC应及时通知IPQC现场确认,同时IPQC需发出《品质异常联络单》给生产单位。
必要时IPQC需将此不良信息反馈给OQC,以便OQC在出货检验时重点跟进。
6.0相关文件
《不合格品控制程序》
7.0相关表单
IPQC制程巡查记录表
IPQC首检验记录表
品质异常联络单
FQC检验日报表
附件一:制程控制流程图。