第二章第6节 冲压模具设计——复合模和连续模
冲压模具结构连续模步骤

冲压模具结构连续模步骤冲压模具是一种用于形成和制造零件的模具,它是冲压工艺中重要的工具。
冲压模具结构与制造过程一般包括设计、制造、调试和加工等步骤。
下面是冲压模具结构连续模步骤的详细介绍。
第一步:产品设计冲压模具的结构设计是基于产品的设计要求来进行的。
首先需要确定产品的形状、尺寸、材料等,并根据产品的功能要求设计出合理的结构。
在设计过程中需要考虑到产品的成型性、加工性、精度要求等因素。
第二步:模具结构设计根据产品的设计要求,进行冲压模具的结构设计。
这个阶段需要考虑到模具的形状、结构、材料选择等因素。
通常包括上模、下模、顶针、导柱、导套、底座等组成部分。
同时,还需要设计出合理的排料、冷却系统以及模具的定位、固定等装置。
第三步:模具制造根据模具设计图纸开始进行冲压模具的制造。
这个过程通常包括材料的选择和采购、切割、加工、装配等步骤。
其中,切割和加工是制造模具的关键过程,需要使用精密的加工设备进行加工,如数控机床、线切割机等。
第四步:模具调试制造完成后,进行模具的调试工作。
首先需要进行模具的组装和调整,确保各个部分的精度和配合度。
然后,进行试模操作,调整冲程、料厚、排料等参数,检查模具是否正常工作,并对模具进行调整和修正,以满足产品制造的要求。
第五步:模具加工完成模具调试后,进行产品的批量加工。
这个阶段需要根据产品的要求进行操作,包括冲压、切割、冲孔、弯曲等工艺。
同时,需要进行模具的维护和保养,确保模具的使用寿命和稳定性。
以上是冲压模具结构连续模步骤的详细介绍,冲压模具的制造过程是一个复杂的工程,需要设计、制造、调试和加工等多个环节的协同作业。
只有确保每个环节都合理和精确,才能保证冲压模具的质量和性能。
第2章6-7节(冲裁工艺及冲裁模设计)
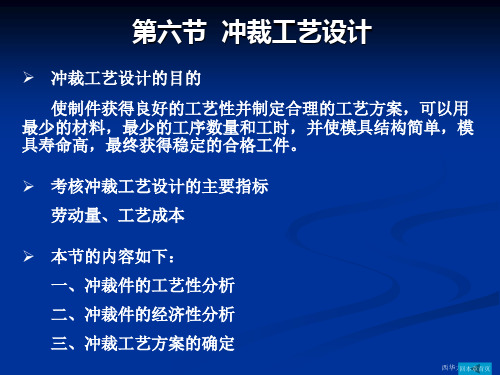
用途 薄件、平整要求高的零件、 薄件、平整要求高的零件、易分层的非金属件
西华大学 张晓洪
2、冲孔模 、
普通板坯冲孔模结构与落料模相似。 普通板坯冲孔模结构与落料模相似。 冲孔的多样性导致冲孔模有更多自己的特点。 冲孔的多样性导致冲孔模有更多自己的特点。
典型的冲孔模有: 典型的冲孔模有: (1)冲侧孔模 ) (2)单工序多凸模冲孔模 ) (3)导板式冲小孔模 )
西华大学 张晓洪
倒装复合模
冲制垫圈的复合冲裁模 适用条件 0.3mm以上低平直度要求件(刚性推件未压紧制件部分,卸 以上低平直度要求件(刚性推件未压紧制件部分, 以上低平直度要求件 料板也未压紧条料) 料板也未压紧条料) 特点 卸料板兼承料平面, 卸料板兼承料平面,冲前无法预压 凸凹模若直刃段长,则胀裂力大,须控制其最小壁厚 凸凹模若直刃段长,则胀裂力大, 条料废料部分: 条料废料部分:冲裁时有上下动作 改进 若上部改为弹性推件,则可加工 若上部改为弹性推件,则可加工0.3mm以下的冲件 以下的冲件
西华大学 张晓洪
… … …冲裁件的形状和尺寸 冲裁件的形状和尺寸
6、孔径不能太小; 、孔径不能太小; 自由凸模的最小尺寸 带护套凸模的最小尺寸 最小孔间距
西华大学 张晓洪
(二)冲裁件的尺寸精度和表面粗糙度要求
冲裁件的经济精度:一般不高于 冲裁件的经济精度:一般不高于IT11,冲孔比落料高一级 , 1、冲裁件外形与内孔尺寸公差表 、 2、冲裁件两孔孔心距公差表 、 3、冲裁件断面表面粗糙度表 、 4、冲裁件断面允许的毛刺高度表 、
第六节
冲裁工艺设计的目的
冲裁工艺设计
使制件获得良好的工艺性并制定合理的工艺方案, 使制件获得良好的工艺性并制定合理的工艺方案,可以用 最少的材料,最少的工序数量和工时,并使模具结构简单, 最少的材料,最少的工序数量和工时,并使模具结构简单,模 具寿命高,最终获得稳定的合格工件。 具寿命高,最终获得稳定的合格工件。 考核冲裁工艺设计的主要指标 劳动量、 劳动量、工艺成本 本节的内容如下: 本节的内容如下: 一、冲裁件的工艺性分析 二、冲裁件的经济性分析 三、冲裁工艺方案的确定
冲压模具的基本结构及工作原理

冲压模具的基本结构及工作原理冲裁模具的基本结构及工作原理一、冲裁模具按工序组合程度可分为:简单冲裁模、连续冲裁模、复合冲裁模。
(一)简单冲裁模即敞开模1、定义:它是指在一次冲裁中只完成冲孔或落料的一个工序。
2、简单冲裁模按其导向方式可分为:(1)无导向单工序模它的特点是结构简单,重量轻、尺寸较小、模具制造容易、成本低廉。
但冲模使用安装时麻烦,模具寿命低,冲栽件精度差,操作也不安全。
无导向简单冲模适用于精度要求不高、形状简单、批景小或试制的冲裁件。
(2)导板式简单冲裁模模精度高、寿命长、使用安装帧、操作安全,.但制造比较复杂。
一般适用于形状较简单、尺寸不大的工件。
(3)导柱式简单冲裁模由于这模具准确可靠,能保证冲裁间隙的均匀,冲裁的工件精度较高、模具使用寿命长而且在冲床上安装使用方便,因此导柱式冲裁模是应用最广泛的一种冲模,适合大批量生产。
(二)连续冲裁模(连续模)1、连续冲裁模的定义:按一定的先后程序,在冲床的滑块的一次到和中,在模具的不同位置上,完成冲孔,落料导两个的上的冲后工序的冲裁模,又称及进模或跳步模。
2、连续冲裁模的定位原理可分为:导正销定位原理、侧刃定距原理(三)复合冲裁模1、复合冲裁模的定义:在部床滑块的一次行程中,在冲模的同一工位上同时完成内孔和外形两种的上工序的冲裁模。
2、复合冲裁模按结构可分为:正装式复合模、倒装式复合模二、我们请看看这三种模具的比较表导板式简单冲裁模上模部分主要由模柄、上模板、垫板、凸模固定板、凸模组成。
下模部分主要由下模板凹模、导尺、导板、回带式挡料销、托料板组成。
这种模具的特点是上模通过.凸模利用导板上的孔迸行导向,导板兼作卸料板。
工作时凸模始终不脱离导板.以保证模具导向精度。
因而,要求使用的压力机行程不大于导板厚度。
这种冲模的工作过程是:条料沿托料板、导尺从右向左送科,首次冲裁时使用临时挡料销定位,首次冲裁以后再往前送料,搭边越过活动挡料销后.再反向拉拽条料,使挡料销后端面抵住条料搭边进行定位,凸模下行实现冲裁。
冲压模具结构连续模步骤(设计标准)
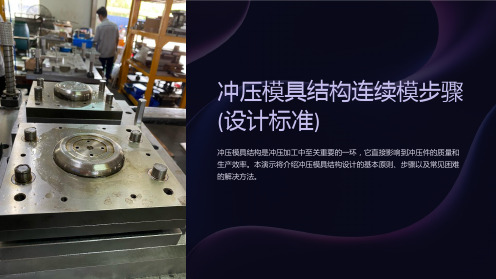
设计方案
2
的形状、材料和工艺要求。
根据需求,制定合适的模具结构设
计方案,并进行初步绘制。
3
详细设计
对模具进行详细设计,包括具体的
制造与组装
4
尺寸、部件,并进行组装和调试。
冲压模具结构设计的常见困难及解决 方法
复杂冲压件的结构 设计
对于复杂形状的冲压件, 需要深入分析,采用合 适的结构设计和加工工 艺。
高精度冲压设备
采用高精度的冲压设备,可 以提高冲压件的加工精度和 表面质量。
冲压模具结构设计的案例研究
案例1 案例2 案例3
汽车冲压件模具设计 电子产品外壳模具设计 家电冲压件模具设计
通过优化模具结构和工艺, 提高冲压零件的质量和效 率,降低成本。
采用连续模设计和模拟仿 真技术,提高电子产品外 壳的精度和一致性。
冲压模具结构设计的基本原则
• 合理布局:模具结构布局要科学合理、紧凑高效,便于加工和组装。 • 合理配合:各零部件之间的配合要合理,确保模具的稳定性和准确性。 • 合理分力:合理设计模具子零件的定位、卡紧以及支撑结构,使得在冲压过程中能承受合
理的力和压力。
冲压模具结构设计的步骤
1
需求分析
通过了解客户的需求,分析冲压件
通过优化模具结构和制造 工艺,提高家电冲压件的 生产效率和可靠性。
结论和总结
冲压模具结构设计是冲压加工中的关键环节,合理的模具结构设计可以提高冲压件的质量和生产 效率。随着技术的不断发展,冲压模具结构设计的前沿技术将不断涌现,为冲压加工带来更多的 可能性。
冲压模具结构连续模步骤 (设计标准)
冲压模具结构是冲压加工中至关重要的一环,它直接影响到冲压件的质量和 生产效率。本演示将介绍冲压模具结构设计的基本原则、步骤以及常见困难 的解决方法。
冲压模具结构连续模步骤

冲压模具结构连续模步骤1. 简介冲压模具是工业生产中常用的一种金属加工工具,用于将金属材料通过冲压工艺加工成所需形状的零件。
冲压模具结构是冲压工艺中关键的部分之一,决定了模具的加工效率和产品质量。
本文将介绍冲压模具结构的连续模步骤,以帮助读者了解冲压模具的制造过程。
2. 模具的基本结构在介绍冲压模具的连续模步骤之前,我们先来了解一下模具的基本结构。
冲压模具通常由上模座、上模、导向柱、下模、下模座和剪切系统等组成。
上模座和下模座用于支撑和固定模具,上模和下模分别安装在上模座和下模座上,导向柱起到模具定位和导向的作用。
剪切系统用于完成对金属材料的切割。
3. 冲压模具的连续模步骤冲压模具的连续模步骤是指通过一次冲压,连续完成多个工序的模具结构。
下面将逐步介绍连续模步骤的具体内容。
3.1 上模座安装首先,需要将上模座定位于冲床上,并进行固定。
上模座要能够承受冲压加工时的高压力,所以在安装时需要注意紧固螺栓的牢固程度。
3.2 上模安装安装上模之前,需要先将上模安装在上模座上。
上模是冲压模具的核心部分,其质量和结构直接影响到冲压加工的效果。
在安装上模时,需要确保上模与上模座的完全贴合,以避免后续工作中出现误差。
导向柱的作用是确保上模和下模的定位和导向准确无误。
在安装导向柱时,需要根据冲压模具的结构和尺寸,选择合适的导向柱进行安装。
导向柱要能够承受冲压时的高压力和冲击力。
3.4 下模安装下模与上模类似,同样也需要与模座完全贴合,并且安装正确的导向柱进行固定。
下模的安装位置要与上模相对应,以确保冲压加工时的准确性。
3.5 下模座安装下模座的安装位置要与上模座相对应,并且要能够稳固地支撑下模。
在安装下模座时,需要保证其与冲床底座的连接稳定,以避免冲压过程中的不稳定情况发生。
剪切系统是冲压模具中的重要部分,用于完成对金属材料的切割。
在连续模步骤中,剪切系统的安装位置一般位于下模座上。
剪切系统的设计和安装要确保切割的准确性和稳定性。
冲压模具结构基本概述

01.
下垫脚
01.
上限位柱
01.
下限位柱
01.
外导柱
01.
取料槽
冲孔模的结构
下模部分 管位针 下模标准入子 内六角螺丝 定位销 内导套 码模槽 起吊螺丝
上垫板
冲孔模的结构
上模部分 扁线弹簧 内导柱 内六角螺丝 定位销 等高套筒 圆冲头 上夹板
冲孔模的工作过程
冲孔模的工作原理
冲孔模的工作过程根据冲床的运动时间顺序分为以下几个部分: 冲床滑块带动上模从开模状态时的最高点开始向下运动,此时上 下模未有接触. 当上打板接触到下模的冲件时,上打板停止运动,冲床滑块继续向下运动,上模脱料弹簧开始压缩,上打板受弹簧压力,压紧冲压件.经过一定的行程,装在上夹板上的冲子接触到冲件. 冲床滑块继续向下运动,在接近下死点(闭模状态)时,冲子完全进入下模孔内,完成冲孔. 冲孔废料从下模板到下垫板到下模座漏料孔落下. 在冲床经过下死点后,冲床滑块带动上模开始回升,此时,由于压力缓解,在上模脱料弹簧力的作用下,上打板把冲件从冲子上顶出,完成脱料.下模板的顶料销上顶,使冲件回位. 冲床滑块带动上模继续上行,回到开模状态时的最高点,完成一次冲压过程.
上模部分
闭模状态
开模状态
外导柱
外导柱
上模部分
内脱料
冲头
塞打
顶杆
内脱料
弹簧顶板
扁线弹簧
复合模的结构
复合模的工作过程 复合模的工作过程根据冲床的运动时间顺序分为以下几个部分: 1. 冲床滑块带动上模从开模状态时的最高点开始向下运动,此时下上模未有接触. 2. 当上脱料板接触到下模的冲件时上脱料板停止运动,冲床滑块继续向下运动,上模脱料弹簧开始压缩,上打板受弹簧压力,压紧冲件.经过一定的行程,上模板及装在上夹板上的冲子接 触到冲件. 3. 当上模板接触到冲件时,下模的脱料弹簧也开始压缩,下脱料板向下运动,下模板与上模板 发生剪切,模具开始落料. 4. 冲床滑块继续向下运动,在接近下死点(闭模状态)时,下模板完全进入上模板内,冲子完 全进入下模孔内,同时完成落料冲孔. 5. 落料的废边框被上模板压在下脱料板上,冲孔废料从下模板到下夹板到下模座漏料孔落下. 6. 在冲床经过下死点后,冲床滑块带动上模开始回升,此时,由于压力缓解,在上模脱料弹簧 力的作用下,上脱料板把冲件从冲子上顶出,完成脱料.下模板的顶料销上顶,使冲件回位. 下脱料板在下模脱料弹簧的作用下把废边框顶出高于下模面低于冲件的位置. 7. 冲床滑块带动上模继续上行,回到开模状态时的最高点,完成一次冲压过程.
冲压工艺与模具设计试题(简答)

冲压工艺与模具设计试题(简答)1、冲裁:是使板料沿封闭曲线相互分离的工序。
2、连续模:又称级进模,是在压力机一次行程中依一定顺序在同一模具的不同工位上完成两道以上工序的模具3、起皱:在拉深时凸缘变形区内的材料受到压应力的作用后,凸缘部分特别是凸缘外边部分的材料可能会失稳而沿切向形成高低不平的皱折,这种现象叫起皱。
4、复合模:在模具的一个工作位置上,同时完成两道或两道以上工序的模具称为复合模。
5、压力中心:冲裁力合力的作用点称为压力中心。
6、带料连续拉深:在一副模具上使用带料进行连续拉深,完成单工序生产需多副模具才能完成的拉深加工称为带料连续拉深。
1、弯曲的变形程度用什么来表示?为什么可用它来表示?弯曲极限变形程度受哪些因素的影响?答:弯曲的变形程度用弯曲系数k来表示,k= r/t。
r越小,t越大,k越小。
而板料外侧伸长率δ:δ=1/(2k+1); k越小,δ越大。
δ超过临界值,外侧发生开裂。
最小相对弯曲半径:会造成外侧开裂的相对弯曲半径(弯曲系数)r/t。
其影响因素:⑴材料塑性:材料塑性好,能承受的变形量大,最小弯曲半径可减小。
⑵材料的纤维方向:弯曲线与纤维方向垂直,最小弯曲半径可减小。
⑶弯曲角:弯曲角增大,最小弯曲半径可减小。
⑷板材表面质量:质量越好,最小弯曲半径可减小。
17.影响极限拉深系数的原因有哪些?答:(1)材料的组织与力学性能(2)板料的相对厚度t/D(3)摩擦与润滑条件(4)模具的几何参数除此之外还有拉深方法,拉深次数,拉深速度,拉深件形状等。
2、写出拉深变形时筒形件底部圆角处的应力、应变,可能产生的失效形式和预防措施。
答:底部圆角部分:径向拉应力σ1;切向拉应力σ3;厚向压应力σ2。
在拉、压应力作用下,径向产生拉应变,厚向产生压应变,底部圆角变薄。
此处,材料厚度最小,抗拉强度最低(加工硬化最小),两拉一压的应力状态,成为最薄弱部分,筒壁与凸模圆角相接处容易破裂,即开裂。
防止措施:①控制合理的变形程度;②选用合理的凸、凹模间隙及圆角半径;③采用中间退火,消除加工硬化;④合理润滑。
第二章 冲裁工艺及冲裁模设计

普通冲裁件的断面情况:
普通冲裁变形所得到的冲裁件端面常带有一定的锥度,并且 都有明显的区域特征,不同的是各区域的大小占整个断面的比例 不一样。 光亮带 产生于塑性变 圆角带
发生在弹性变形后 期和塑性变形初期, 由金属的弯曲和拉伸 而形成。其大小与材 质有关。
形阶段,断面主 要受剪应力和压 应力作用。断面 平整、光滑。通 常占整个区域的 1/2~1/3,与材质 有关。
第二章 冲裁工艺及冲裁模设计
普通冲裁原理
冲裁间隙 冲裁模刃口尺寸的计算(重点) 冲裁件的排样(重点) 冲压工艺力(重点) 压力中心的计算(重点) 冲裁件的工艺性 冲裁模的基本形式及特点 冲裁模主要零、部件结构和设计(重点) 冷冲模的设计程序(重点)
2.1 普通冲裁的基本原理
冲模刃口尺寸、制造公差的大小主要取决于 冲裁件的形状和精度。
刃口尺寸的计算方法
冲模刃口 尺寸公差带 分析图
1. 凸、凹模分开加工时的刃口计算
δd+δp≤Zmax-Zmin 运用该方法必须使模具的制造公差与间隙满足 或 δp= 0.4(Zmax-Zmin) δd= 0.6(Zmax-Zmin)
根据刃口尺寸的计算原则,分开加工时凸、凹模刃口尺寸 的计算公式如下:
推件力Pd: Pd = KdP
冲压工艺力的计算:
(它是选取压力机吨位的主要依据,具体计算要考虑模具的结构型式) 采用刚性卸料自然漏料方式:Pz≥P+Pt = P +nKtP 采用刚性打料、弹性卸料的倒装结构方式:Pz≥P + Px = P + KxP 采用弹性卸料和弹性顶料方式:Pz≥P + Px + Pd = P + KxP + KdP 采用弹性卸料自然漏料方式:Pz≥P + Px + Pd = P + KxP + nKdP (选择压力机时,压力机的公称压力N必须大于或等于Px)
第二章 冲裁工艺及冲裁模
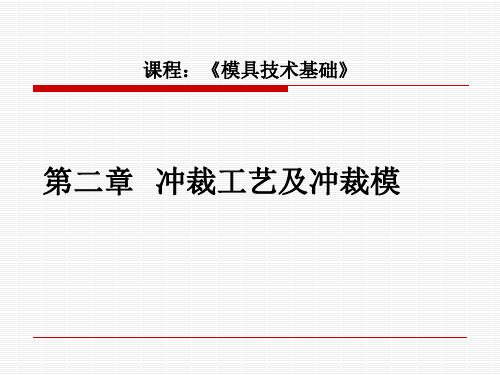
圆形凸模
第二章 冲裁工艺及冲裁模
非圆形凸模及其固定 冲小孔凸模及其导向结构
第二章 冲裁工艺及冲裁模
(4)凸模的长度 当采用固定卸料时(如图a):L=h1+h2+h3+h 当采用弹性卸料时(如图a):L=h1+h2+h4
2、凹模 定义:在冲压过程中,与凸模配合直接对冲制件进行分离或成形 的工作零件。
便于操作和实现生产自动化。 缺点:级进模轮廓尺寸较大,制造较复杂,成本较高。 适用:大批量生产小型冲压件。
第二章 冲裁工艺及冲裁模
第二章 冲裁工艺及冲裁模
第二章 冲裁工艺及冲裁模
第二章 冲裁工艺及冲裁模
第八节 冲裁模的部件和零件
第二章 冲裁工艺及冲裁模
一、工作零件 1、凸模 按整体结构分:整体式、护套式和镶拼式; 按截面形状分:圆形和非圆形; 按刃口形式分:平刃和斜刃。 凸模基本结构由两部分组成: 一是工作部分,用于成型冲件; 二是安装部分,用来使凸模正确固定在座上。 凸模的材料:形状简单寿命要求不高的凸模选用T8A、T10A等材料; 形状复杂且寿命要求较高凸模选用Cr12、Cr12MoV等制造 对于高寿命、高耐磨性的凸模选用硬质合金。 凸模的固定方法:
第二章 冲裁工艺及冲裁模
第四节 排样与搭边
一、排样 定义:排样指冲裁件在板料、条料或带料上的布置形式。 1、材料利用率 定义:在冲压生产中,材料利用率是指在一个进料距离内,冲裁件面积与板料
毛坯面积之比,用百分率表示。
A 100%
Bs
式中 ——材料利用率;
A——一个进料距离内冲裁件的实际面积,mm2; B——条料或带料宽度,mm; s——进料距离,mm。
第二章 冲裁工艺及冲裁模
冲压模具结构连续模步骤(设计标准)

处理能够得到较高强度和硬度的材料,广泛应用于EMI要求的cover和Bracket. 3. 特殊功能要求的不锈钢产品
a.外观件:光面,绒面,耐指纹 b.添加特殊的元素达到一些特殊的性能要求,如添加Ag增加抗菌性能等等。
H
D
L
A
C
L
W
WB
H
a a
Hale Waihona Puke (6)(7)D F
H
L
70°
R0.80 0.50
F
R0.80
R1.00
R0.30
R0.50
W R1.00
R0.30
a
(8)
(9)
滑块设计注意事項
a. 滑块垂直运动行程一般不得大于滑块厚度的一半﹔
b. 为確保滑块活动可靠﹐滑块顶部应布置适当数量的浮升销或弹簧﹔
c. 当滑块以共用形式加工时﹐应將两滑块绕模板中心旋转180度进行 加工﹐此时设计人员不需將图元旋转﹐调整工作由加工部门自行处 理﹔
3. 磷青铜片PBS(Phosphor Bronze Spring) 磷青铜是青铜(铜锌合金)添加脱氧剂(P)及其它微量元素如Fe组成
的,具有较强的延展性和耐疲劳性。 主要作用:电气开关,端子,EMI等弹片及导电材料,材料强度差于不锈钢, 一般表面需要电镀。 分类:根据金属元素的含量及加工工艺分,常用的牌号有C5102, C5191, C5212, C5210等。
6. 顶料销设计标准
一.选用原則 1.一般选用Φ8.0的LB型顶料销。若位置不夠时可选用
Φ6.0型的顶料销。 2.当所需顶料力很大,位置又夠时可选用Φ10.0的顶料
冲压模具设计-落料拉深复合模

摘要随着中国工业不断地开展,模具行业也显得越来越重要。
本文针对筒形零件的落料工艺性和拉深工艺性,确定用一幅复合模完成落料和拉深的工序过程。
介绍了筒形零件冷冲压成形过程,经过对筒形零件的批量生产、零件质量、零件构造以及使用要求的分析、研究,按照不降低使用性能为前提,将其确定为冲压件,用冲压方法完成零件的加工,且简要分析了坯料形状、尺寸,排样、裁板方案,拉深次数,冲压工序性质、数目和顺序确实定。
进展了工艺力、压力中心、模具工作局部尺寸及公差的计算,并设计出模具。
同时具体分析了模具的主要零部件〔如凸凹模、卸料装置、拉深凸模、垫板、凸模固定板等〕的设计与制造,冲压设备的选用,凸凹模间隙调整和编制一个重要零件的加工工艺过程。
列出了模具所需零件的详细清单,并给出了合理的装配图。
通过充分利用现代模具制造技术对传统机械零件进展构造改良、优化设计、优化工艺方法能大幅度提高生产效率,这种方法对类似产品具有一定的借鉴作用。
关键词:复合模;拉深;落料;目录目录 (I)前言第一章课程设计任务书 (2)第二章模具构造设计 (2)2.1 读产品图:分析其冲压工艺性 (2)2.2 分析计算确定工艺方案 (3)2.2.1 计算毛坯尺寸 (3)2.2.2 计算拉深次数 (3)2.2.3 确定工艺方案 (3)2.3 主要工艺参数的计算 (4)2.3.1 确定排样、裁板方案 (4)2.3.2 确定拉深工序尺寸 (5)2.3.3 计算工艺力,选设备 (5)2.4 模具构造设计 (6)2.4.1 模具构造型式选择 (6)2.4.1 模具工作局部尺寸计算 (7)第三章模具标准件选择及闭合高度计算 (8)3.1 标准模架的选择 (13)3.2 模具的实际闭合高度计算 (8)3.3 压力中心确实定 (8)第四章模具零件的构造设计 (9)4.1 落料凹模设计 (14)4.2 拉深凸模设计 (15)4.3 凸凹模设计 (15)4.4 弹性卸料板设计 (10)4.5 顶料板设计 (11)4.6 模柄设计 (12)4.7 导柱、导套设计 (12)4.8 打料块设计 (12)4.9 上模座设计 (12)0 下模座设计 (12)第五章模具装配图 (18)结语 (15)参考文献 (16)一.课程设计〔论文〕的主要内容及根本要求内容:落料、拉深复合模设计;产品工件图见附图;生产批量:大批量要求:目录、设计任务书、产品图及设计说明书、装配图及零件图。
2。2-冲压模具
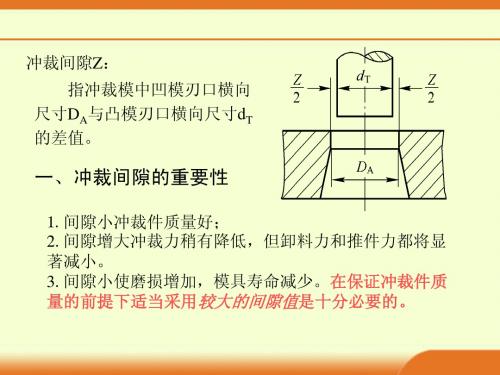
3、典型的冲裁模结构及特点:
1)、单工序冲裁模:指在压力机的一次工作行程中只 完成一个基本冲裁工序的模具。 ①固定导板式落料模: 是将凸模与导板用H7/h6的间隙配合,导板与导 料板、凹模、下模座联接在一起,既对凸模导向,又 起固定卸料作用。回程时凸模不能离开导板。
第二章 冲裁工艺与冲裁模设计
1-上模座 2-凸模 3-卸料板 4-导料板 5-凹模 6-下模座 7-定位板
第二章 冲裁工艺与冲裁模设计
第二章 冲裁工艺与冲裁模设计
落料凸、凹模尺寸 a) 落料凹模尺寸 b) 落料凸模尺寸
2.4.3冲裁力和压力中心的计算
一、冲裁力的计算
冲裁力:冲裁过程中凸模对板料施加的压力。
用普通平刃口模具冲裁时,冲裁力F一般按下式计算:
F=1.3L·t·τ(N)
注: F——冲裁力; L——冲裁件周长; t——材料厚度; τ——材料抗剪强度; b
无导向单工序落料模
1-模柄 2-上模座 3-导套 4-导柱 5下模座图2-57 滑动导向模架
第二章 冲裁工艺与冲裁模设计
1-模柄 2-止动销 3-上模座 4、8-内六角螺钉 5-凸模 6-垫板 7-凸模固定板 9-导板 10-导料板 11-承料板 12-螺钉 13-凹模 14-圆柱销 15-下模座 16-固定挡料销 17-止动销 18-限位销 19-弹簧 20-始用挡料销
DA Dmax x0
A (36 0.5 0.62)0 0.025 mm 35.690 0.025 mm
DT D A Z min t (35.69 0.04 ) 0 0.016 mm 35.65 0 0.016 mm
0
校核:0.016 + 0.025 = 0.04 > 0.02(不能满足间隙公差条件) 因此,只有缩小,提高制造精度,才能保证间隙在合理范围内, 由此可取: T ≤ 0.4Z max Z min =0.4×0.02=0.008mm A ≤ 0.6Z Z =0.6×0.02=0.012mm max min
冲压模具设计

4、材料利用率:工件总面积/条料面积
η=nA/bl×100%
n-工件个数 A-工件面积 b、l-条料宽和长
三、模具压力中心确定
1、对称形状工件:压力中心位于图形几
何中心。
第 二 章
2、复杂形状工件: ①将凸模轮廓线分解成若干基线段—直 线、圆弧、曲线段; ②计算各线段重心的座标值xi、yi
冲 (圆弧、曲线段重心座标值查表);
知
4、应用面广,广泛用于国民经济各个领
识
域。 三、冲压分类:
1、分离工序
2、变形工序
§1-2冲压基本工序
一、分离工序:
第
切断、冲裁(落料、冲孔)、切
一
边、切口等。
章 二、变形工序:
冲 压
弯曲、拉深、翻边、起伏、胀 形、缩口、扩口、整形 等。
基
本
知
识
§1-3金属冲压变形规律
一、冲压变形的应力应变状态:
第 二
凹模磨损后: 尺寸变大-A尺寸 尺寸变小-B尺寸
凸模磨损后: 尺寸变小-A尺寸 尺寸变大-B尺寸
章
尺寸不变-C尺寸
尺寸不变-C尺寸
冲 裁
⑴落料件:确定凹模尺寸:
(A-Δ) A凹=(A-xΔ)+ δ凹
(B+Δ) B凹=(B+xΔ)- δ凹
(C±Δ) C凹=C±δ凹/2
第
凸模尺寸按凹模尺寸配制,保正双
裁
③根据各线段重心的座标值,求整个图
形压力中心
Xc=L1X1+L2X2+…+LnXn/L1+L2+…+Ln Yc=L1Y1+L2Y2+…+LnYn/L1+L2+…+Ln
【汽车工艺】冲压模具结构

冲
裁
第 二 章
工 艺 与 模
具
设
计
8.2 复合冲裁模
复合模(多工序冲裁模) 定义:冲床一次行程中,在模具同一位置上能完成几个不同冲裁工序的 模具。 结构特点:一副模具有一个凸凹模。 分类:①正(顺)装式复合模
8.5.2导正销 导正销主要用在连续模中,对条料进行精确定位,以保证制件外形与内孔相互位置的正确。
作用:可以消除步距的误差,起精确定位的作用。 注意:当导正销较长时,应适当减少与凸模的精加工长度。 8.5.3侧刃 1、侧刃实质是一个裁切边料凸模。 2、工作原理: (侧刃 的长度等于一个步距) 3、在模具结构中,可根据制件的结构和材料的价值,采用单侧刃或双侧刃。 (1) 单侧刃一般用于步数少、材料较硬或厚度较大的级进模中; (2) 双侧刃用于步数较多、材料较薄的级进模中。 4、与侧刃相配的侧刃孔(又称侧刃凹模)按侧刃凸模实际尺寸加单面间隙配制。 8.5.4定位板和定位钉 (单个毛坯的定位装置 ) 注意:1、转角处应用工艺孔过渡;
冲
裁
第 二 章
工 艺 与 模
具
设
计
8.5 定位零件的结构
定位零件包含:1、挡料零件(如挡料销、导正销、侧刃等) 2、导料零件(如导料销、导料板、侧压板) 3、块料定位零件(如定位销、定位板)。
8.5.1挡料销 (挡料销材料为T7,硬度为HRC50-55 ) 作用:是控制板料的送进距离 分类:(1)固定挡料销 (2)活动挡料销 ①回带式活动挡料销 ②隐蔽式活动挡料销 ③临时挡料销
2、 尽量减少定位板与毛坯的接触面积。
பைடு நூலகம்
第二章第6节冲压模具设计——复合模和连续模
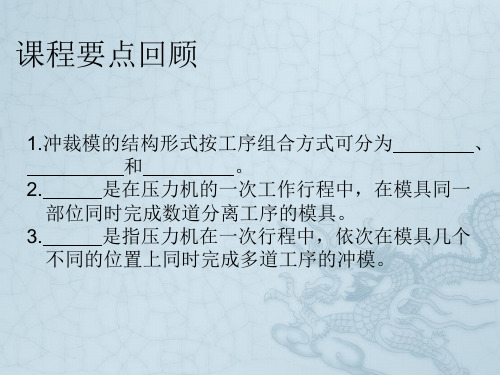
2
2.连续模的排样设计
2.1 连续模设计步骤
连续模设计与普通冲模有很大的不同,要求也要高的多。
2.8 载体设计
载体:多工位冲压时条料上连接工序件,并使工序 件在模具上稳定送进的部分材料。载体与工序件之 间的连接段称为搭接头。
载体的形式:单侧载体、双侧载体、中间载体、无 载体和边料载体。
单侧载体
双侧载体
中间载体
无载体
边料载体
工序排样过程
带局部成形时的工序排样
2.9连续模结构设计
课程要点回顾
1.冲裁模的结构形式按工序组合方式可分为
、
和
。
2.
是在压力机的一次工作行程中,在模具同一
部位同时完成数道分离工序的模具。
3.
是指压力机在一次行程中,依次在模具几个
不同的位置上同时完成多道工序的冲模。
课程要点回顾
1.冲裁模的结构形式按工序组合方式可分为 单工序 模 、 复合模 和 连续模 。
4.5模架
若采用中间导柱模架,则导柱对称分布, 受力平衡,滑动平稳,拔模方便,但只能一个方 向送料。若采用对焦导柱模架,则受力平衡,滑 动平稳,可纵向或横向送料。若采用后侧导柱模 架,则可三方向送料,操作者视线不被阻挡,结 构比较紧凑,但模具受力不平衡,滑动不平稳。
本设计决定采用中间导柱模架。
4.6计算模具刃口尺寸
在倒装复合模中,如果在上模内采用弹性装置, 也可保证冲件有较高的平直度。所以,倒装模比正 装模应用更广泛。
冲压模具设计:复合模结构、模板作用,终于全掌握了

冲压模具设计:复合模结构、模板作用,终于全掌握了前面我们谈到关于如何快速、精准的进行模具设计,以及模具设计外挂是如何快速画图。
这篇文章带大家一起来详细探讨模具结构。
要想自己做设计,首先得知道模具的类型、各模具类型中的作用,每块模板的用途、结构合理性等等。
前文中提到模具种类的划分我们在学习、了解的时候,不用分得这么详细,只需要通过模具的成型工艺可以进行如下划分:冲孔模、复合模模、折弯模、连续模这几种来进行了解就行。
在工程模(单冲模)设计工艺中,下料、冲孔一般都是放在最前面的工艺,因此,如果工程模中有下料冲孔基本都会放在工艺排样的最前面。
而复合模的工艺就包含(如下料、冲孔、打凸、拉伸)等。
因为其导柱倒装所以也称为倒装模;而有时因其只是在冲压过后工序件为产品的外形(不冲孔、打凸等)别的工序,只有下外形,故也称为下料模,有时也称冲孔、下料模或剪口模。
我们首先从复合模结构开始了解,上图为复合模基本标准结构类型。
因为复合模的主要作用是下料,冲裁后产品料就是后工序的展开外形,一般为了节约工步,节省成本,会在此工序中加入如,冲孔、打凸、拉伸、抽牙等。
认识一套模具,需要从结构入手,得先知道为什么需要这样,原理是什么?不这样做有什么样的后果或是问题?先来看下模具中每块模板的作用以及材料的选择:•上模座:用于固定上下模导正,方便模具固定到压力机上,俗称:架模。
材质优先选用A3料;或是用S50C料以节约成本。
•空板(加高板):顾名思义主要作用增加高度,在中间挖出一个让位孔,留出弹簧行程与打板活动间隙。
材料优先选择A3料,空板较厚,有时也可用上垫块(脚)替换。
•打板:打板也有叫上承板的。
主要作用是将弹簧箱的弹力传递给打杆。
材质为45#,有时也会热处理至45º。
•上垫板:防止冲头将模座打出凹槽,影响模具冲裁精度。
通常用CR12料,一般都需要热处理,而热处理后的HRC为52º~56º。
•上夹板:主要作用夹冲头、过弹簧等。
- 1、下载文档前请自行甄别文档内容的完整性,平台不提供额外的编辑、内容补充、找答案等附加服务。
- 2、"仅部分预览"的文档,不可在线预览部分如存在完整性等问题,可反馈申请退款(可完整预览的文档不适用该条件!)。
- 3、如文档侵犯您的权益,请联系客服反馈,我们会尽快为您处理(人工客服工作时间:9:00-18:30)。
二、垫片冲压工艺方案的确定
完成此工件需要冲孔、落料两道工序。其 加工方案分为3种,见表2.1。
表2.1 工艺方案
序 号
工艺方案
结构特点
单工序模生产: 模具结构简单,但需要两道工序、两套 落料→冲孔( 模具才能完成零件的加工,生产效率低,难 1 或冲孔→落料) 以满足零件大批量生产的需求。且两道工序 中的定位误差,将导致中心孔的位置精度难 以保证。
(1)工序排样的内容
①在冲切刃口设计的基础上,将各工序内容进行优化组合 形成一系列工序组,对工序排序,确定工位数和每一工位 的加工工序。 ②确定载体形式与坯料定位方式。 ③设计导正孔直径,确定导正销数量。 ④绘制工序排样图(图7-21)。 (2)工序排样类型
①落料型工序排样; ②切边型工序排样; ③混合型工序排样
1
1.何谓冲压模具,其优点如何
何谓连续冲模具: 连续冲压模具是指数个工程都结合在同一模具内,将材 料穿入模内透过每一送距的冲压,能够完整的将五金制品 冲压成型。在各型的冲压模具中,连续冲压模具因具有着 高生产效率的产能,故最适合于大量生产之用,且连续冲压 模具应用范围极广,适用于各种五金零件制品。
2
根据本零件的设计要求以及各方案的特点, 决定采用第2种方案比较合理。
三、工艺计算
3.1排样方案的确定 零件外形为圆形 ,可以采用单排、交叉双排或 多排;考虑到零件为中等批量生产,如果采用交 叉双排或多排,则模具尺寸和结构就会相应增大, 从而增加模具生产成本,所以本设计决定采用单 排结构。如图所示。
同一副模具完成两道不同的工序,大大 减小了模具规模,降低了模具成本,提高生 复合模生产: 产效率,也难以提高压力机等设备的使用效 落料-冲孔复合 率;操作简单、方便,适合大批量生产;能 可靠保证中心孔的位置精度。 连续模生产: 冲孔-落料连续 3 同一副模具不同工位完成两道不同的工 序,生产效率高,模具规模相对第二种方案 要大一些,模具成本要高;两道工位之间的 定位要求非常高;否则无法保证中心空的位 置精度。
比较项目 单工序模 连续模 一般IT11级以下 高 复合模 较高,IT9以下 较高
工件形位公差 较低 冲压生产率 低
自动化
较易(多工位车 床上自动化)
容易(单件全自 动化)
严格 较安全 简单件比复合模 制造难度低 较差,用于形状 简单、尺寸不大 精度要求不高型 件的大批量生产
难(单件半自动 化)
不严 较差 复杂件比连续模 制造难度低 较差,用于形状 简单、尺寸不大 精度要求较高型 件的大批量生产
一、工艺方案分析
1.垫片冲压工艺分析 2.产品尺寸精度、粗糙度、断面质量分析
四、模具结构的确定
4.1模具的形式 4.2定位装置
二、垫片冲压工艺方案的确定
三、工艺计算
3.1排样方案的确定 3.2搭边值的确定 3.3条料宽度的确定 3.4材料利用率 3.5计算冲压力 3.6计算模具压力中心 4.7模具工作零件的设计计算 4.8其他零件的设计
工艺设计时必须得到试制或小批量生产的技术数据或工 序样件,必要时还可以使用简易模具或手工进行工艺验证, 以获得较为准确的零件展开形状及尺寸、工序性质、工序数 量、工序顺序以及工序件(半成品)尺寸等。而这些都是多工 位冲压条料排样设计的重要依据,而连续模排样设计是连续 模结构设计的关键。排样之后便可进行凸模、凹模、凸模固 定板、垫板、卸料装置,导料、定距等零部件的结构设计。 最后绘制模具总装配图和零件图,并提出使用维护的说明。
(2)工序排样类型
(2)工序排样类型
混合型工序排样
单侧载体
单侧、双侧载体尺寸
具体尺寸见图销;3-侧刃挡块;4-导正销
2.6 工序排样原则与要点
1.级进冲裁工序排样 2.级进弯曲工序排样 3.级进拉深工序排样 4.含有局部成形时连续模的工序排样
4.4导向零件 导向零件有许多种,如用导板导向,则在 模具上安装不便而且阻挡操作者视线,所以不 采用;若用滚珠式导柱导套进行导向,虽然导 向精度高、寿命长,但结构比较复杂,所以也 不采用;针对本次加工的产品的精度要求不高, 采用滑动式导柱导套极限导向即可。而且模具 在压力机上的安装比较简单,操作又方便,还 可降低成本。
复合模的命名
正装复合模基本结构
倒装复合模基本结构
正装复合模:凸凹模在上模
倒装复合模:凸凹模在下模
正、倒装的命名:凸凹模
正装复合模
复合模结构的完善
卸料机构 推件机构
顶件机构
倒装复合模
复合模结构的完善
倒装复合模
推件机构
卸料机构
3.复合模特点
复合模的特点: [优]结构紧凑,生产率高,制件精度高,特别 是制件孔对外形的位置度容易保证。 [缺]模具结构复杂,对模具零件精度的要求较 高,对模具的装配精度要求也较高。 适用场合: 生产批量大、精度要求高的冲裁件。
• 复合模设计案例分析
1.复合模的基本结构
复合模:在压力机的一 个工作行程内,在模 具的同一个部位同时 完成数道冲压工序的 模具。
2.复合模分类
分类 正装式(顺装式)复合模:落料凹模装在下模座
倒装式复合模:落料凹模装在上模座 举例: 复合模结构主要特点 ----凸凹模: 既是落料凸模又是冲孔凹模
第二章第5节 冲压模具设计
——复合模具和连续模具 本节主要内容: 一.复合模 复合模工艺特点 复合模具设计实例讲解 二.连续模具 连续模工艺特点 连续模具设计实例讲解
课程要点回顾
1.冲裁模的结构形式按工序组合方式可分为 、 和 。 2. 是在压力机的一次工作行程中,在模具同一 部位同时完成数道分离工序的模具。 3. 是指压力机在一次行程中,依次在模具几个 不同的位置上同时完成多道工序的冲模。
对材料的要求 不严 生产安全性 较差
模具难易程度 较易,价格低 通用性好,适用 中、小批量生产 和大型件的大量 生产
应用
6.冲孔落料复合模设计案例
一、设计内容 零件名称:双扇挡片 材 料: 20钢 材料厚度:1 mm 毛刺要求:孔及轮廓边 缘无毛刺 尺寸精度要求:IT12级 二、生产类型 中批量生产
正装复合模特点: 凸凹模在上,落料凹模在下; 冲件和废料均从下模的上表面取出,需二次清理, 既不安全也不方便; 板料是在压紧的状态下分离,冲出的冲件平直度较高。 正装复合模适用场合: 适于冲裁工件平直度要求较高或冲裁时易弯曲的 大而薄的工件。
倒装复合模特点:
凸凹模在下,落料凹模在上; 冲件从上模推下,冲孔废料直接从压力机台面漏下, 卸料可靠,操作方便。 采用刚性推件的倒装式复合模,板料不是在压紧的状 态下冲裁,因而平直度不高。 倒装复合模适用场合: 适于冲裁较硬的或厚度大于0.3mm的板料。
4.3卸料装置
4.4导向零件
4.5模架
4.6计算模具刃口尺寸
一、工艺方案分析及确定
1.垫片冲压工艺分析 由图可知,产品为圆片落料、圆片冲孔。 产品形状结构简单对称,无狭槽、尖角; 孔与孔之间、孔与零件边缘之间的最小距 离满足c>1.5t。
2.产品尺寸精度、粗糙度、断面质量分析 (1)尺寸精度 任务书对冲件的尺寸精度要求为IT12级,查参考文献知,普通冲裁 时对于该冲件的精度要求为IT12~IT11级,所以尺寸精度满足要求。 (2)冲裁件断面质量 因为一般用普通冲裁方式冲1mm 的金属板料时,其断面粗糙度Ra 可达12.5~3.2,毛刺允许高度为0.05~0.1mm;本产品在断面粗 糙度上没有太严格的要求,单要求孔及轮廓边缘无毛刺,所以只要 模具精度达到一定要求,在冲裁后加修整工序,冲裁件断面的质量 就可以保证。 (3)产品材料分析 对于冲压件材料一般要求的力学性能是强度低,塑性高,表面质量 和厚度公差符合国家标准。本设计的产品材料为20钢,属优质碳素 结构钢,其力学性能是强度、硬度低而塑性较好,非常适合冲裁加 工。另外产品对于厚度与表面质量没有严格要求,所以尽量采用国 家标准的板材,其冲裁出的产品表面质量和厚度公差就可以保证 经上述分析,产品的材料性能符合冷冲压加工要求。 (4)生产批量 产品批量为中等批量,适合采用冲压加工的方法,最好采用复合模 或连续模。
3.2搭边值的确定
3.3条料宽度的确定
3.4材料利用率
3.5计算冲压力
3.6计算模具压力中心
由于该零件完全对称于相互垂直的两条多层 次线,所以模具的压力中心在几何图形的中 心。
四、模具结构的确定
4.1模具的形式 复合模又可分为正装式和倒装式。
经分析,此工件无较高的平直度要求,工 件精度要求也较低,所以从操作方便、模具制 造简单等方面考虑,决定采用倒装式复合模。
4.正装和倒装复合模的比较:
结构的比较:凸凹模位置不同,废料和冲 件取出方式不同。 生产率的比较:倒装模比正装模生产率高; 安全性的比较:倒装模比正装模安全可靠。 在倒装复合模中,如果在上模内采用弹性装置, 也可保证冲件有较高的平直度。所以,倒装模比正 装模应用更广泛。
5.复合模与其它模的比较:
2.8 载体设计
载体:多工位冲压时条料上连接工序件,并使工序 件在模具上稳定送进的部分材料。载体与工序件之 间的连接段称为搭接头。
载体的形式:单侧载体、双侧载体、中间载体、无 载体和边料载体。
单侧载体
双侧载体
中间载体
无载体
边料载体
4.2定位装置 采用伸缩式挡料销定位,安装在橡胶垫和活动 卸料板之间。工作时可随凹模下行而压入孔内, 工作很方便。 4.3卸料装置
(1)条料的卸除 采用弹性卸料板。因为是倒装式复合模,所以卸料 板安装在下模。 (2)工件的卸除 采用打料装置将工件从落料凹模中推下,落在模具 工作表面上。 (3)冲孔废料的卸除 下模座上采用漏料孔排出。冲孔废料在下模的凸凹 模内积聚到一定数量,便从下模座的漏料孔中排出。
课程要点回顾
1.冲裁模的结构形式按工序组合方式可分为 单工序 模 、 复合模 和 连续模 。 2. 复合模 是在压力机的一次工作行程中,在模具同 一部位同时完成数道分离工序的模具。 3. 连续模 是指压力机在一次行程中,依次在模具几 个不同的位置上同时完成多道工序的冲模。