电泳漆技术质量要求
阴极电泳
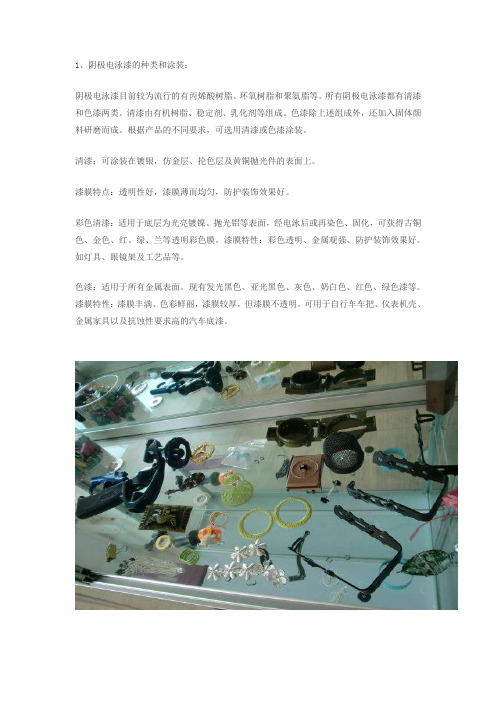
1、阴极电泳漆的种类和涂装:阴极电泳漆目前较为流行的有丙烯酸树脂、环氧树脂和聚氨脂等。
所有阴极电泳漆都有清漆和色漆两类。
清漆由有机树脂、稳定剂、乳化剂等组成。
色漆除上述组成外,还加入固体颜料研磨而成。
根据产品的不同要求,可选用清漆或色漆涂装。
清漆:可涂装在镀银,仿金层、抡色层及黄铜抛光件的表面上。
漆膜特点:透明性好,漆膜薄而均匀,防护装饰效果好。
彩色清漆:适用于底层为光亮镀镍、抛光铝等表面,经电泳后或再染色、固化,可获得古铜色、金色、红、绿、兰等透明彩色膜。
漆膜特性:彩色透明、金属观强、防护装饰效果好。
如灯具、眼镜架及工艺品等。
色漆:适用于所有金属表面。
现有发光黑色、亚光黑色、灰色、奶白色、红色、绿色漆等。
漆膜特性:漆膜丰满、色彩鲜丽,漆膜较厚,但漆膜不透明。
可用于自行车车把、仪表机壳、金属家具以及抗蚀性要求高的汽车底漆。
2、阴极电泳的涂装工艺:1)主要设备:电泳槽可用聚氯乙烯板制成。
分阳极室和阴极室,两室之间用渗析膜隔开。
电泳槽同时装有超滤设备和热交换器,工作时还需用泵循环搅拌。
电源为0-100V可调的直流电源,电流容量约30~50A。
另有烘箱或烘道(根据零件大小及量而定)。
2)电泳工艺参数:漆液组成:有机树脂、稳定剂、乳化剂等;PH:不同漆有不同的要求;导电率:(微西门子/厘米)1000±400施工电压:30~100V;漆液温度:25~32℃;电泳时间:0.5~2分钟;固化条件:120℃~170℃、30分钟。
3)工艺流程:(1)电泳清漆、基材前处理→镀金;镀银;镀仿金;镀彩色层或黄铜抛光→清洗→去离子水洗→阴极电泳清漆→去离子水洗→清洗→固化。
(2)彩色清漆:基村前处理→光亮镀镍或抛光铝等→清洗→去离子水洗→阴极电泳→去离子水洗→染色→清洗→固化。
(也有直接电泳成彩色清漆工艺)(3)色漆:基材前处理(包括磷化)→清洗→去离子洗→阴极电泳→去离子水洗→清洗→固化。
3、漆膜质量:1)漆膜硬度:4H~5H(中华牌铅笔)2)盐雾试验:漆膜厚度10μm时大于300小时。
电泳漆技术质量要求

1. 适用范围:本标准适用于钣金车身表面电泳涂层材料的检测。
2. 检验项目和技术指标见表一、表二。
序号检验项目单位指标 执行标准 1外观A 板 级8-10 QB8021 C 板8-10QB8021L 板 7-10 QB8021 H 板7-10 QB8021 2 膜厚 μm 20-30 GB/T1764 3 硬度 ≥ 2H GB/T6739 4 杯突 ≥ 6 GB/T9753 5 附着力 级 0-1 GB/T1720 6 柔韧性 mm 1 GB/T1731 7 冲击 cm 50 GB/T1732 8 光泽 (60°) 50-80 GB/T9754 9 耐水性 (40℃)h≥ 500 GB/T5209 10 耐盐雾 h ≥ 1000 ASTMB117 11 干燥时间 (工件温度) 175℃ min 25 GB/T1728 12泳透力cm ≥ 80%福特盒法文件名称 电泳漆技术质量要求 文件编号JB-2011-001发布部门 工艺技术部编制审核批准实施日期修订状态A1共2页表二:电泳漆原漆技术指标序号检验项目单位指标执行标准乳液色浆1 外观乳白色液体灰色粘稠液体,无结块目测2不挥发物(120±2)℃/1h%36±257±2GB/T67513 细度μm≤10 15 GB/T6753.14 PH值 6.3-6.9 酸度计5 电导率Μm/Cm 2000-2800 HC/T33366 MEQ酸mm01/100g 30-36 0.1mol/1NaOH滴定7 MEQ碱mm01/100g 55-65 0.1mol/1H2SO4滴定8 粘度(20℃)mP a·S≤100 GB/T27949 密度(20℃)g/ml 1.05-1.07 GB/T675010 溶剂含量(EB)% 0.5-1.5 气相色谱法。
Q JL J151005-2009吉利汽车车身用阴极电泳涂料标准

Q/JL浙江吉利控股集团有限公司企业标准Q/JL J151005-2009代替Q/JL J151005-2008 汽车车身用阴极电泳涂料标准2009-07-30发布2009-08-10实施 浙江吉利控股集团有限公司发 布前 言本标准是对Q/JL J151005-2008《汽车车身用阴极电泳涂料标准》的修订,与Q/JL J151005-2008相比,主要差异如下:——增加了试验方法中的测定方法:耐酸性、耐碱性和耐盐雾性能的测定;(见5.9、5.10和5.12条)——修改了膜厚单位:由mm改为μm;(见5.13.3条)——更改了膜厚的测定方法;(见表2中的第8项)——对标准的章、条进行了重新编排。
本标准由浙江吉利控股集团有限公司提出。
本标准由浙江吉利汽车研究院有限公司负责起草。
本标准起草人:李丽娜。
本标准2008年1月25日首次发布,于2009年7月30日第一次修订。
本标准所代替的历次版本发布情况:——Q/JL J151005-2008汽车车身用阴极电泳涂料标准1 范围本标准规定了汽车车身用阴极电泳涂料的技术要求、试验方法、检验规则、安全和卫生规定、包装、标志、运输和贮存。
本标准适用于浙江吉利控股集团有限公司汽车车身用阴极电泳涂料。
2 规范性引用文件下列文件中的条款通过本标准的引用而成为本标准的条款。
凡是注日期的引用文件,其随后所有的修改单(不包括勘误的内容)或修订版均不适用于本标准,然而,鼓励根据本标准达成协议的各方研究是否可使用这些文件的最新版本。
凡是不注日期的引用文件,其最新版本适用于本标准。
GB/T 191-2008 包装储运图示标志GB/T 1723-1993 涂料粘度测定法GB/T 1724-1979(1989) 涂料细度测定法GB/T 1725-2007 色漆、清漆和塑料 不挥发物含量的测定GB/T 1731-1993 涂膜柔韧性测定法GB/T 1732-1993 漆膜耐冲击测定法GB/T 1733-1993 漆膜耐水性测定法GB/T 1747.2-2008 色漆和清漆 颜料含量的测定 第2部分:灰化法GB/T 1771-2007 色漆和清漆 耐中性盐雾性能的测定GB/T 1865-1997 色漆和清漆 人工气候老化和人工辐射暴露(滤过的氙弧辐射)GB/T 6680-2003 液体化工产品采样通则GB/T 6739-2006 色漆和清漆 铅笔法测定漆膜硬度GB/T 6750-2007 色漆和清漆 密度的测定 比重瓶法GB/T 6753.3-1986 涂料储存稳定性试验方法GB/T 8264-2008 涂装技术术语GB/T 9271-2008 色漆和清漆 标准试板GB/T 9286-1998 色漆和清漆 漆膜的划格试验GB/T 9753-2007 色漆和清漆 杯突试验GB/T 9754-2007 色漆和清漆 不含金属颜料的色漆漆膜的20°、60°和85°镜面光泽的测定 GB/T 13452.1-1992 色漆和清漆总铅含量的测定火焰原子吸收光谱法GB/T 13491-1992 涂料产品包装通则HG/T 3335-1977(1985) 电泳漆电导率测定法HG/T 3337-1977(1985) 电泳漆库仑效率测定法Q/JLY J711380-2008 电泳槽液溶剂含量测定方法3 术语和定义本标准采用GB/T 8264-2008的定义及以下定义。
电泳漆件检验标准

电泳漆件检验标准
应在标准光源对色灯箱CAC-600箱内,以目视方法进行。
进料检验记录砂眼、砂点(目视检测)外观不应有针孔、流漆、橘皮、皱纹等现象杂色流漆(聚油)
橘皮、皱纹针孔哑色(不折光)使用60º光泽度仪检测符合GB9754,光泽度60GS以上附着力(百格)测试用百格刀在试件表面划出方格,再用3M胶纸粘贴,然后用橡皮擦在胶纸上面来回摩擦数十次,使其完全密贴后,撕开胶纸,胶纸与试件表面成45°角迅速斜拉试件经百格测试,涂漆膜厚层不可有2格以上剥离为附着力合格。
铅笔硬度测试用H级硬度(4H、5H)之铅笔测试,以45º角用1mm/s速度500g力划过。
试件经铅笔划过,,擦拭干净后涂漆膜厚层不出现划痕为合格。
屈曲性冲击测试把试件放到冲击实验机工作台上做冲击试验试件经屈曲性测试,涂漆膜厚层不可有剥离:
正面冲击:500g重*500mm反面冲击:500g重*250mm进料检验记录膜厚测试用膜厚仪测量试件涂漆层膜厚膜厚一般要求:0.02~0.03mm,涂膜均一性。
酒精测试白色棉质软布(或脱脂棉)蘸来回擦拭50次烤漆表面无变化﹐或涂漆颜色无沾染到棉布(或脱脂棉)上为合格。
盐水喷雾测试用盐雾测试机(室温35º,氯化钠溶液5±1%的浓度,PH值6.5~7.2,喷雾的压力1.3~1.5c㎡)
测试时间为500小时,试件涂漆表面不能出现剥落、孔眼、起皱、锈斑、变色等为合格。
耐温测试60℃~70℃烘烤48小时无皱纹起泡、裂纹、脱皮、变色等状态出现。
耐水测试40℃水温置放超过500小时涂漆表面无明显变化为合格。
编制/日期:
审核/日期:
批准/日期:2。
电泳涂料槽液参数管理
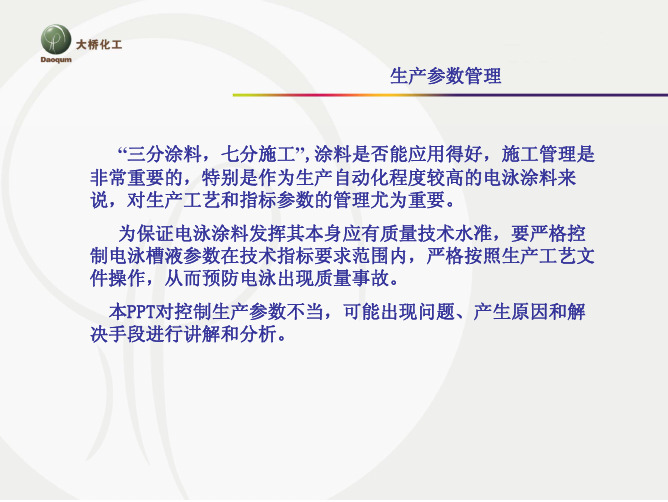
槽液灰份管理 槽液灰份表示固体份中颜料的重量比率 (%)。 槽液灰份高 1.漆膜平滑性降低。 2.漆膜光泽降低。 3.泳透力相对提高 4.UF透过量减少 5.电泳槽及后冲洗槽内更多沉 淀。 6.耐污染性提高。 槽液灰份低 1.相同工艺参数,膜厚降 低。 2.漆膜光泽较高。 3.泳透力降低。 4.遮盖力降低。 5.耐污染性提高。
槽液PH值管理 PH值偏高调整方法 1.补加添加剂A-01。(一次补加量不宜过大,分多次调整到位) 2.减少阳极液排放。 3. 检查阳极系统,阻止阳极液流失。 4. 检测纯水水质,保证泳前滴水电导< 50us/cm。 PH值偏低调整方法 1.停加添加剂A-01。 2.增加阳极液排放。 3. 检查阳极系统,阻止阳极液流失到电泳槽内。 4. 提高超滤液排放量 。
Hale Waihona Puke 电泳对整流器的要求 目的:将交流电源加以整流转换成直流电源。 1.电泳直流电源为0~400V电压可调。 2.电压脉冲幅度不能超过平均电压的5%, 3.在满负荷情况下电压脉冲功率<5% 4.整流器输出电压调节范围为从0V到额定电压。 5.稳定幅度:当输出电流在额定输出电流的10%~100%范围内, 输出电压为额定输出电压的50%~100%范围内,供压精度为1 %。 电流限幅耗度±5%。 7. 从0V达到额定直流电压值在5~59s内随意给定。 8.具有软启动,软停止功能,输出电压不突变。 9.可多段电压控制。
槽液搅拌管理 槽液搅拌过高 1. 击穿电压升高。 2.相同工艺参数,膜厚降低。 3.工件易脱落 槽液搅拌过低 1.击穿电压降低 2.槽内沉淀增多 3.工件水平面有沉淀 4.漆膜粗糙 5.泳透力降低 6.槽液表面漂浮物多
施工电压管理要求 阴极电泳涂装的电压主要取决于涂料的品种,操作时还应该综合考虑 极间距、极比、槽液温度等因素,以确定最佳电压范围。电压的高低对电 泳涂膜的质量影响很大。通常电泳时间是固定的,通过提高或降低电压来 调节涂膜厚度。极间电压越高,电场强度越强,电沉积量亦随之增加,工 件内表面及半封闭面的涂膜厚度增大。但电压过高,工件入槽瞬间的冲击 电流太大,涂膜沉积速度过快,易造成涂膜外观和性能变差。 电压高到超过电泳膜的击穿电压时,沉积涂膜被击穿,电解反应加 剧,电极表面产生大量气体,涂膜表面产生大量气泡。电泳电压过低,涂 料泳透力差,沉积速度慢,效率低,涂膜变薄。一般在保证涂膜外观质量 前提下,尽可能采用较高的电压进行阴极电泳涂装。电压控制在150~340 V 为宜。 线性升高电压既可获得较高的泳透力,又可限制峰值电流,防止涂膜 弊病的产生。
阴极电泳工艺及检验标准
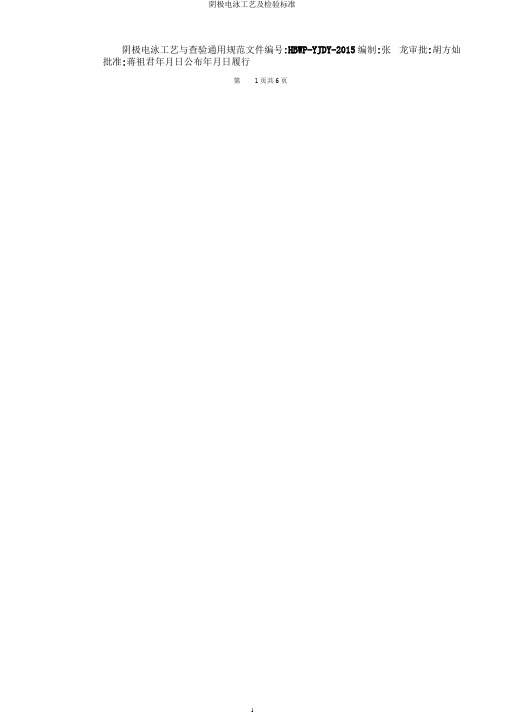
阴极电泳工艺与查验通用规范文件编号:HBWP-YJDY-2015编制:张龙审批:胡方灿批准:蒋祖君年月日公布年月日履行第1页共6页本标准规定了阴极电泳的工艺过程控制、质量控制及质量要求。
本标准合用于工程机械产品钢板厚度在4mm一下的薄板件(驾驶室、覆盖件、电控柜)以及无机加工面、加工孔的构造件的防备底涂层。
规范性引用文件以下文件中的条款经过本标准的引用而构成为本标准的条款。
凡是注日期的引用文件,其随后全部的改正单(不包含勘误的内容)或订正版均不合用于本标准,但是,鼓舞依据本标准完成协议的各方研究能否可使用这些文件的最新版本。
凡是不注日期的引用文件,其最新版本合用于本标准。
GB1720漆膜附着力测定法GB/T1730漆膜硬度检测法摆杆阻尼试验GB/T1731漆膜柔韧性测定法GB/T1732漆膜耐冲击测定法GB/T1771色漆和清漆耐中性盐雾性能的测定GB/T6739漆膜铅笔硬度测定法GB/T9286色漆和清漆漆膜的划格试验GB/T9753色漆和清漆杯突试验GB/T13312钢铁件涂装前除油程度查验方法(验油试纸法)HG/T3334电泳漆漆膜制备法HG/T3335电泳漆电导率测定法HG/T3336电泳漆泳透力测定法HG/T3337电泳漆库仑效率测定法HG/T3338电泳漆积淀积量测定法HG/T3339电泳漆泳透力测定法(钢管法)术语电泳涂装是带电荷的水溶性涂料粒子,在电场作用下,在相反电荷电极上堆积形成涂第2页共6页层的工艺。
有阴极电泳与阳极电泳之分。
泳透力泳透力是指电泳液在规定的电泳条件下(电压、时间、固体分和PH值),深入被屏电极点堆积的能力。
槽液固体分系指电泳槽液中成膜物质(树脂与颜料)的含量,一般以质量百分数表示。
工艺工艺流程图电泳工艺流程图前办理→电泳→超滤液洗1→超滤液洗2→去离子水洗1→去离子水洗2→烘干前办理工艺流程图预脱脂→脱脂→水洗→表调→磷化→水洗→去离子水洗工艺过程前办理工艺过程控制脱脂使用含有表面活性剂的碱性水基脱脂剂,采纳浸喷联合的方式,两次脱脂。
电泳漆性能测试标准

电泳漆问题处理、技术、测试参数:电泳漆性能对比1、外观,流平测试:同样时间、电流、固体份、温度、电泳对比漆膜厚、流平好的漆较好。
(外观)表面流平性大平面,无皱皮、波纹、电泳温度22-28度之间1、抗污染能力测试:同样的工作条件电泳的工件越多,处理的次数越少、漆越好。
槽液超滤能解决问题。
2、硬度测试:H笔划3、耐磨性测试:在纸上放一重量码,来回数次(结果)4、附着力(结合力) 测试:刚电泳湿膜,用带压力的水冲洗(0.01帕),无脱落、烤干后,在1*1mm划“#”格100个、再用胶纸撕、看掉不掉漆、不掉漆为结合力合格。
5、柔软性测试:烤干后折弯,看漆断不断。
6、电泳漆泳透力测试:用一根圆管,管内泳的越深、泳透力越好。
8、老化测试:水煮100度测老化30--1小时9、固体份(固含):用锡泊纸取漆称,烤180度40-60分钟,称固体份。
10、耐人工汗测试:香港标准:一、先把棉浸泡在5%乳酸水中湿透后包住工件,放在恒温箱,水温保持50度,48小时漆不软就可以了。
二、在密封箱内,5%乳酸加5%氯化钠加90%纯水。
水温保持50度,工件离水面1cm,工件存放时间多长人工汗就是多长。
11、电泳漆混合标准:取槽液,电货一件,加入另一种漆,电货对比有无区别一个礼拜或更长、电货看有无区别,是否有沉淀,分离,搅动有无好转电导率同样时间电压工件,固体份,色均匀度12、中性盐雾测试:(压铸合金件、化学镍、锌底)国标、中性盐雾、5%氯化钠、保持温度30度、喷雾量:20mI/H结果:60小时酸性测试:5%氯化钠PH调到3.0--3.2,温度55度,用冰醋酸调低。
13、丙铜测试;用丙铜浸湿棉来回擦100次不掉漆。
14、耐候性:(耐黄变)用气灯(QUV)200--500小时15、表面划伤:指甲用力划表面无划痕16、百格测试:在1*1mm工件面划“#”字格,然后用胶纸粘住用力瞬间拉开要不掉漆,(用指甲刮不掉漆)。
17、膜厚:漆膜15—20us厚,5*5镍面流平好,190度不黄变。
电泳及喷塑质量标准技术协议

序号
检验项目
技术要求
试验方法
1
电泳外观
电泳后的表面应平整光滑,无明显的颗粒、疙瘩、陷穴、缩孔、针孔、水滴迹、斑痕、夹杂异物、挂流、不匀、粗糙、露底、剥落等缺陷。
目测检验
2
泳层厚度
15~25µm
3
泳层附着力
以1mm间距进行划100方格检验,划格力度深达底材,然后用3M胶布贴上,瞬间用力拉开,不得脱落20%
目测检验
3
塑膜附着力
用裁纸刀在涂层表面以1mm为间隔从垂直交叉方向切划下若干个方格,(注意刀片划割时应垂直于工件表面,且一定要切透到金属,(若涂层超过50微米则切线间距就为2mm),用透明胶带(25.4mm*50.8mm以上尺寸附着力度为10N/25mm),沿一切线方向贴在有方格的涂层上,(胶带不能起皱,用手指推紧胶带使其与涂层紧密接触),快速拉起胶带,观察工件表面变化,只能起线不能起面。(一个方格中20%面积被撕下为此方格被撕下,有方格被撕下为不合格品)
执行国际标准
注:喷塑件的抽样及检验判别按GB2828中一次抽样,Ⅱ级检查水平、AQL CR=0 ;A=0.65;B=2.5规定进行。
按技术要求中描述,进行检验。(CR类)
4
塑膜颗粒
漆膜表面不应有明显的颗粒,A类部件:1平方分米内Φ1.0mm的颗粒≤3颗,为合格;
B类部件:1平方分米内Φ1.0mm的颗粒≤5颗,为合格;
按技术要求,目测检验
1.A类部件:
2.B类部件:
6
残件及划伤
喷塑件有破裂、断柱、断扣、明显刮伤、碰伤
目测检验
硬度
2H铅笔
划格法测定
4
泳层耐蚀性
盐雾实验500小时无锈蚀。
铝合金型材电泳漆膜质量管理和常见缺陷分析
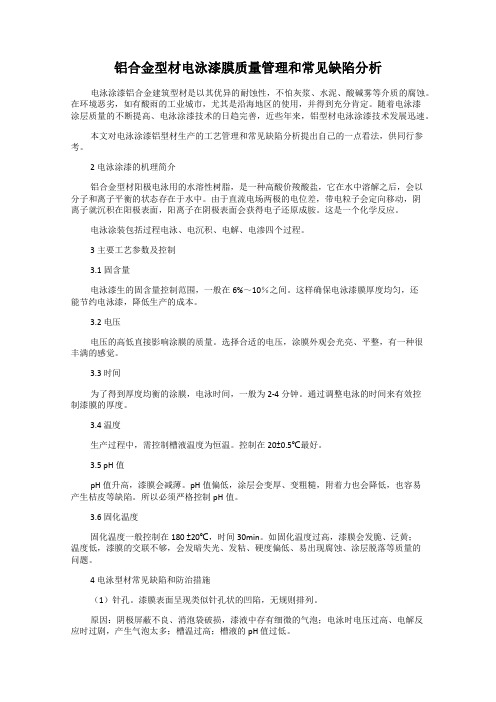
铝合金型材电泳漆膜质量管理和常见缺陷分析电泳涂漆铝合金建筑型材是以其优异的耐蚀性,不怕灰浆、水泥、酸碱雾等介质的腐蚀。
在环境恶劣,如有酸雨的工业城市,尤其是沿海地区的使用,并得到充分肯定。
随着电泳漆涂层质量的不断提高、电泳涂漆技术的日趋完善,近些年来,铝型材电泳涂漆技术发展迅速。
本文对电泳涂漆铝型材生产的工艺管理和常见缺陷分析提出自己的一点看法,供同行参考。
2电泳涂漆的机理简介铝合金型材阳极电泳用的水溶性树脂,是一种高酸价羧酸盐,它在水中溶解之后,会以分子和离子平衡的状态存在于水中。
由于直流电场两极的电位差,带电粒子会定向移动,阴离子就沉积在阳极表面,阳离子在阴极表面会获得电子还原成胺。
这是一个化学反应。
电泳涂装包括过程电泳、电沉积、电解、电渗四个过程。
3主要工艺参数及控制3.1固含量电泳漆生的固含量控制范围,一般在6%~10%之间。
这样确保电泳漆膜厚度均匀,还能节约电泳漆,降低生产的成本。
3.2 电压电压的高低直接影响涂膜的质量。
选择合适的电压,涂膜外观会光亮、平整,有一种很丰满的感觉。
3.3 时间为了得到厚度均衡的涂膜,电泳时间,一般为2-4分钟。
通过调整电泳的时间来有效控制漆膜的厚度。
3.4 温度生产过程中,需控制槽液温度为恒温。
控制在20±0.5℃最好。
3.5 pH值pH值升高,漆膜会减薄。
pH值偏低,涂层会变厚、变粗糙,附着力也会降低,也容易产生桔皮等缺陷。
所以必须严格控制pH值。
3.6 固化温度固化温度一般控制在180 ±20℃,时间30min。
如固化温度过高,漆膜会发脆、泛黄;温度低,漆膜的交联不够,会发暗失光、发粘、硬度偏低、易出现腐蚀、涂层脱落等质量的问题。
4 电泳型材常见缺陷和防治措施(1)针孔。
漆膜表面呈现类似针孔状的凹陷,无规则排列。
原因:阴极屏蔽不良、消泡袋破损,漆液中存有细微的气泡;电泳时电压过高、电解反应时过剧,产生气泡太多;槽温过高;槽液的pH 值过低。
电泳工艺条件对漆膜质量的影响

电泳工艺条件对漆膜质量的影响
一、电压
在电泳涂装中,电压高低对于不同电泳漆膜的影响比较大,若电压过高,电泳漆膜就会越厚,容易可以引起漆膜表面比较粗糙,烘干后易产生橘皮现象等;若电压过低,则容易导致引起电解氧化反应慢,漆膜薄不均匀,泳透力差。
因此,在电泳试涂装的过程中,可根据电泳漆种类和施工管理要求等方面问题进行分析,最终选择适合我们产品需求的施工电压。
二、电泳时间
电泳时间过短,容易导致漆膜过薄;反之,电泳膜厚度会随着电泳时间的延长而增加。
然而,当电泳漆膜达到一定厚度时,不仅膜厚会适量增加,而且会加剧副反应。
三、PH值
电泳漆的ph值会在一定程度上直接影响溶液的稳定性。
因此,一般要求在施工过程中,ph 值控制一般在5.6ー6.2之间(因涂料产品配方不同,控制有一定程度的变化)。
否则,如果ph 值过高,可能会导致工件表面光泽不均匀,漆液稳定性差,溶解性树脂会沉淀,漆膜表面粗糙,附着力降低; 如果ph 值过低,新沉积的漆膜会再次溶解,漆
膜会变薄,电泳后,冲洗会出现针孔现象。
四、电导率
进行电泳涂装之前,被涂布的制品需要预先处理,前处理处理不干净,会将杂质离子带入到电泳槽,电泳槽的电导率随之升高,这往往会导致电泳漆膜粗糙、不均匀和针孔弊病。
五、固体分和灰份
当电泳漆工作液的固体分含量太低时,容易导致漆膜的遮盖力不好,颜料易沉淀,涂料稳定性较差,涂膜品质下降;灰份过低,涂膜遮盖力下降;灰份过高,涂膜光泽度降低,涂膜厚度下降。
表面处理-电泳漆

电泳有阳极和阴极之分,一般看你用的是那种电泳漆?比较常用的是黑色阴极电泳漆!工艺好象都不一样?具体可也找卖漆的厂家!我就了解到这点了!如谁有详细资料还望能共享一下!!JB T10242-2001 阴极电泳涂装通用技术规范电泳涂装工艺流程:烫洗、预脱脂、脱脂、第一水洗、第二水洗、表面调整、皮膜化成、第三水洗、第四水洗、纯水洗、电泳涂装、UF1、UF2、UF3、纯水洗、干燥电泳漆施工工艺说明| [<<][>>]一、工艺路线上挂-电镀处理-自来水洗-自来水洗-纯水洗-纯水洗-纯水洗-纯水洗-电泳-第一道回收(用纯水)-第二道回收(用纯水)-纯水洗-纯水洗-自来水洗-进烘箱-下挂二、电脉漆操作条件1、电压:25V-60V2、时间:12-60秒3、槽液温:25℃-28℃三、电泳漆膜烘烤条件1、烤箱温度:130℃-160℃2、烤箱时间:20分-30分四、电泳漆配槽步骤(一)前期工作1、先用自来水将电泳槽稍微清洗,除去一产电泳槽时所产生的PVC及PP 碎屑。
2、再用水清洗,加入少许NaOH烧碱,以除去槽内表面之油污,清洗干净,倒去污水。
3、再用自来水彻底清洗2-3次,并开动过滤泵的检查各管路是否漏液。
检查电机正转还是反转。
4、再用纯水清洗两次、干净、开动搅拌机。
5、盖上盖子,等待开缸。
(二)配制有色电脉步骤(以配100升槽各色浆及漆比例)1、取调色漆0.5升或开一小桶内。
2、取1升色浆边搅拌边缓慢加入色浆,用电动搅拌机操作搅拌,搅拌充分30分钟。
3、将上述搅拌混合均匀之色浆移动至易一大塑料桶中。
4、取20升032#漆在大搅拌机搅拌下,加入上述之塑料桶中,充分搅拌1小时后,移入电泳槽。
5、重复1-4步骤。
6、将所配有色电泳漆全部混合液都在电泳槽后。
7、再将大搅拌机移至电泳槽中,充分搅拌电泳电泳漆半小时。
8、在强力搅拌下,缓慢加适应症纯水<要求电导率<5μs >加时要注意缓慢,间歇性。
9、性水位加至溢流槽位时,开支过滤泵循环。
电泳通用工艺参数及现场工艺控制卡样板
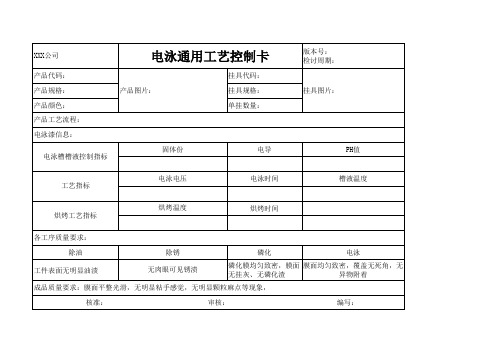
电泳通用工艺控制卡
产品代码: 产品规格: 产品颜色: 产品工艺流程: 电泳漆信息:
电泳槽槽液控制指标
产品图片: 固体份
挂具代码: 挂具规格: 单挂数量:
电导
版本号: 检讨周期: 挂具图片:
PH值
工艺指标
电泳电压
电泳时间
槽液温度
烘烤工艺指标
烘烤温度
烘烤时间
各工序质量要求:
除油
除锈
磷化
电泳
工件表面无明显油渍
28-30℃
30s-150s
50-150V
25-28℃
槽液参数最佳值
固体份%
PH值
16±2
6.2±0.5
10±2
4.5±0.5
电导值us/cm 1300±300 700±300
烘烤温度 170-200℃ 150-170℃
烘烤时间 30min 30min
灰分 0.12-0.20
——
Байду номын сангаас
槽液落差 5-10cm
工件离底部距 工件离极板距
离
离
工件与阳极的比例 阳极液的电导
10-20cm
>15cm
1:4-7
500us/cm上
以上各参数均为各类型电泳漆最佳操作参数,不同的生产条件、不同的工件、不同的客户要求可能存 在不同的操作值,具体以实际生产为准,以产品成膜效果为准。
无肉眼可见锈渍
磷化膜均匀致密,膜面 膜面均匀致密,覆盖无死角,无
无挂灰、无磷化渣
异物附着
成品质量要求:膜面平整光滑,无明显粘手感觉,无明显颗粒麻点等现象,
核准:
审核:
编写:
树脂类型 环氧
电泳漆膜附着力等级判定方法
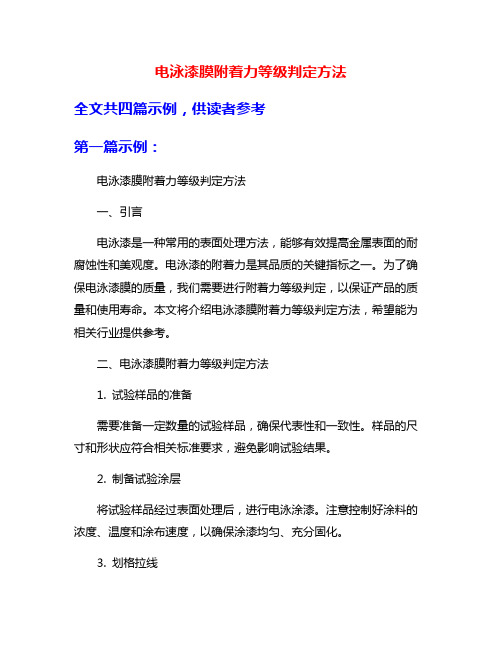
电泳漆膜附着力等级判定方法全文共四篇示例,供读者参考第一篇示例:电泳漆膜附着力等级判定方法一、引言电泳漆是一种常用的表面处理方法,能够有效提高金属表面的耐腐蚀性和美观度。
电泳漆的附着力是其品质的关键指标之一。
为了确保电泳漆膜的质量,我们需要进行附着力等级判定,以保证产品的质量和使用寿命。
本文将介绍电泳漆膜附着力等级判定方法,希望能为相关行业提供参考。
二、电泳漆膜附着力等级判定方法1. 试验样品的准备需要准备一定数量的试验样品,确保代表性和一致性。
样品的尺寸和形状应符合相关标准要求,避免影响试验结果。
2. 制备试验涂层将试验样品经过表面处理后,进行电泳涂漆。
注意控制好涂料的浓度、温度和涂布速度,以确保涂漆均匀、充分固化。
3. 划格拉线在试验样品的涂漆表面上划格拉线,确保拉力测试时拉力均匀分布。
4. 附着力测试使用专用设备对试验样品上的漆膜进行拉力测试,记录其破坏形式和拉力数值。
根据拉力数值和破坏形式,判定漆膜的附着力等级。
5. 附着力等级判定标准根据不同行业的标准要求,将电泳漆膜的附着力等级分为几个等级,如一级、二级、三级等。
根据试验结果进行等级判定,确保产品符合相关标准。
6. 结果分析和记录对试验结果进行分析,记录附着力等级判定结果、试验条件和样品信息。
如有异常结果,需及时调查原因,找出问题所在并进行改进。
三、附着力等级判定方法的重要性1. 保证产品质量电泳漆膜的附着力是保证产品质量的重要指标之一。
通过附着力等级判定,能够及时发现漆膜附着力不足的问题,确保产品的质量和使用寿命。
2. 提高生产效率附着力等级判定方法可以帮助企业及时了解生产过程中的问题,指导生产工艺的改进,提高生产效率和产品质量。
3. 降低生产成本通过附着力等级判定,可以避免产品出现漆膜剥落等质量问题,减少产品召回和维修成本,降低生产成本。
四、结语电泳漆膜的附着力等级判定方法是保证产品质量和生产效率的重要手段。
通过严格执行附着力等级判定标准,能够有效提高产品质量,降低生产成本,保障企业的可持续发展。
电泳漆漆膜厚度标准
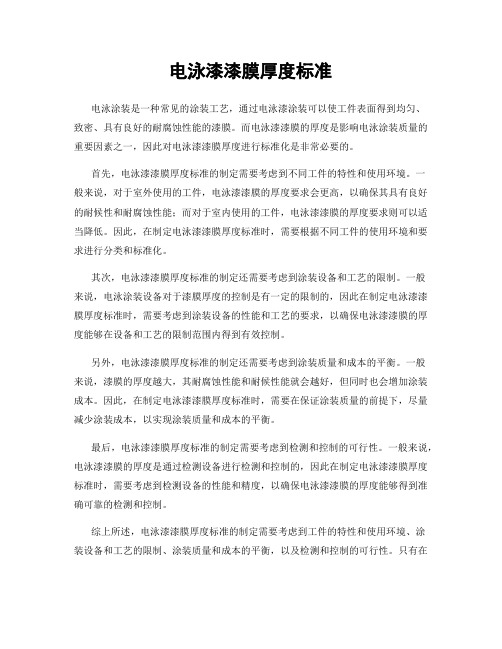
电泳漆漆膜厚度标准电泳涂装是一种常见的涂装工艺,通过电泳漆涂装可以使工件表面得到均匀、致密、具有良好的耐腐蚀性能的漆膜。
而电泳漆漆膜的厚度是影响电泳涂装质量的重要因素之一,因此对电泳漆漆膜厚度进行标准化是非常必要的。
首先,电泳漆漆膜厚度标准的制定需要考虑到不同工件的特性和使用环境。
一般来说,对于室外使用的工件,电泳漆漆膜的厚度要求会更高,以确保其具有良好的耐候性和耐腐蚀性能;而对于室内使用的工件,电泳漆漆膜的厚度要求则可以适当降低。
因此,在制定电泳漆漆膜厚度标准时,需要根据不同工件的使用环境和要求进行分类和标准化。
其次,电泳漆漆膜厚度标准的制定还需要考虑到涂装设备和工艺的限制。
一般来说,电泳涂装设备对于漆膜厚度的控制是有一定的限制的,因此在制定电泳漆漆膜厚度标准时,需要考虑到涂装设备的性能和工艺的要求,以确保电泳漆漆膜的厚度能够在设备和工艺的限制范围内得到有效控制。
另外,电泳漆漆膜厚度标准的制定还需要考虑到涂装质量和成本的平衡。
一般来说,漆膜的厚度越大,其耐腐蚀性能和耐候性能就会越好,但同时也会增加涂装成本。
因此,在制定电泳漆漆膜厚度标准时,需要在保证涂装质量的前提下,尽量减少涂装成本,以实现涂装质量和成本的平衡。
最后,电泳漆漆膜厚度标准的制定需要考虑到检测和控制的可行性。
一般来说,电泳漆漆膜的厚度是通过检测设备进行检测和控制的,因此在制定电泳漆漆膜厚度标准时,需要考虑到检测设备的性能和精度,以确保电泳漆漆膜的厚度能够得到准确可靠的检测和控制。
综上所述,电泳漆漆膜厚度标准的制定需要考虑到工件的特性和使用环境、涂装设备和工艺的限制、涂装质量和成本的平衡,以及检测和控制的可行性。
只有在考虑到这些因素的基础上,制定的电泳漆漆膜厚度标准才能够真正满足涂装质量和成本的要求,从而推动电泳涂装工艺的发展和应用。
汽车零部件油漆涂层技术规范
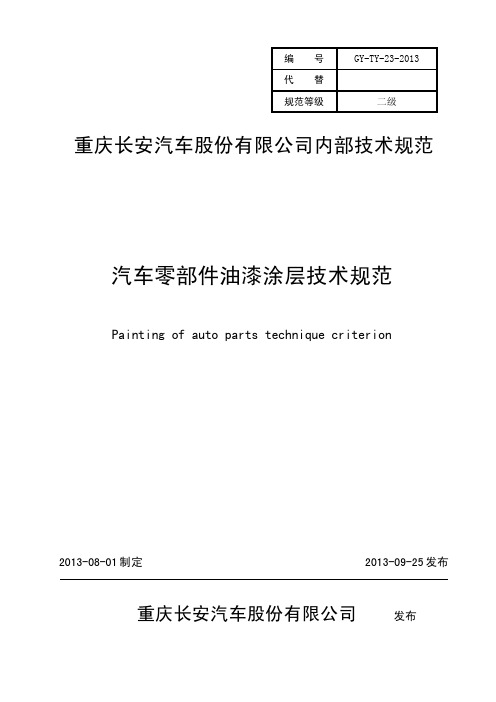
240h
备胎升降器 钢板弹簧
较 电泳漆≥20μm 恶 或喷塑≥40μm 劣 喷漆≥40μm
240h 144h
480h 240h
注: (1) (2) (3)
(4)
高防腐要求适用于市场定位和质量水平高的汽车,如:高级轿车、中高级 SUV、豪华商用车等。 转向节等铸铁件防腐技术难度大,防腐指标有所降低;铝车轮等安全件应提升其防腐指标。 电泳漆烘干温度≥160℃,喷塑烘干温度≥180℃,不耐温零件不适用,只能采用浸漆或喷漆。 喷塑一般采用静电粉末喷涂,受“静电屏蔽”影响,内腔件、复杂件不适用。 工作时,不被砂石撞击的零件,不进行抗石击试验;工作时,不接触水、机油、汽油的零件, 不进行耐水、耐机油、耐汽油试验。
7
6.2 涂覆工艺 6.2.1 油漆涂料应在保质期内,喷涂前调整涂液粘度是关键,应采用粘度计监测并记录。 6.2.2 采用电泳涂覆时,应监测电导率、电压、固体份、灰份、细度、库仑效率、泳透力等 工艺参数,并记录。 6.2.3 采用电泳涂覆时,必须配置超滤、过滤设备,槽液应搅拌均匀,不允许有结块、沉 淀等现象。 6.2.4 采用电泳涂覆时,必须配置纯水设备,配电泳漆槽以及电泳后的水洗(喷淋或浸洗), 必须采用干净的纯水。 6.2.5 采用喷塑时,应采用静电粉末喷涂,需控制装挂方式、喷涂时间、喷涂电压、喷粉 量、粉末导电率、粉末粒度、粉末和空气混合物的速度梯度等。 6.3 烘烤工艺 6.3.1 烘烤设备应具备预加热段、烘烤保温段、吹风冷却装置等。 6.3.2 烘烤温度和时间应严格控制,其直接影响着涂层的外观和附着力。 6.4 标准化作业 6.4.1 供应商应具备规范的半自动或自动涂覆生产线,2015 年 7 月 1 日起必须采用自动生 产线,作业安全规程符合 GB 6514 的规定。 6.4.2 油漆涂料应贮存在专用的库房,配备有防火等设备,库房的温度和湿度应满足要求。 6.4.3 除油、酸洗、抛丸、涂覆、烘烤等关键工序,应编制作业指导书,并做好操作记录。 6.4.4 除油、酸洗、抛丸、涂覆、烘烤等关重设备,应定期检修,并做好检修记录。 6.4.5 应具备规范的试验室,配备涂液分析仪器、涂层测厚仪、附着力测量仪、盐雾试验 箱等试验设备,试验之后做好相关记录。 6.4.6 鼓励供应商开展 ISO9001 质量体系认证。 6.5 环保控制 6.5.1 油漆涂层涂覆供应商应具备规范的废水、废气处理设施,不允许乱排放。 6.5.2 供应商应按 HJ/T 293 规定清洁涂覆生产,鼓励开展清洁生产审核,2015 年 7 月 1 日起必须具备该项要求。 6.6 涂覆供应商评价体系
电泳漆漆膜厚度测试标准
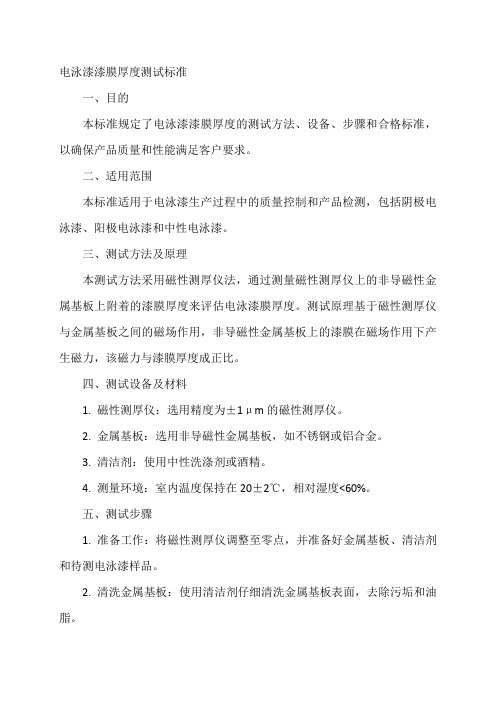
电泳漆漆膜厚度测试标准一、目的本标准规定了电泳漆漆膜厚度的测试方法、设备、步骤和合格标准,以确保产品质量和性能满足客户要求。
二、适用范围本标准适用于电泳漆生产过程中的质量控制和产品检测,包括阴极电泳漆、阳极电泳漆和中性电泳漆。
三、测试方法及原理本测试方法采用磁性测厚仪法,通过测量磁性测厚仪上的非导磁性金属基板上附着的漆膜厚度来评估电泳漆膜厚度。
测试原理基于磁性测厚仪与金属基板之间的磁场作用,非导磁性金属基板上的漆膜在磁场作用下产生磁力,该磁力与漆膜厚度成正比。
四、测试设备及材料1. 磁性测厚仪:选用精度为±1μm的磁性测厚仪。
2. 金属基板:选用非导磁性金属基板,如不锈钢或铝合金。
3. 清洁剂:使用中性洗涤剂或酒精。
4. 测量环境:室内温度保持在20±2℃,相对湿度<60%。
五、测试步骤1. 准备工作:将磁性测厚仪调整至零点,并准备好金属基板、清洁剂和待测电泳漆样品。
2. 清洗金属基板:使用清洁剂仔细清洗金属基板表面,去除污垢和油脂。
3. 涂抹电泳漆:将适量电泳漆涂抹在金属基板表面,确保涂抹均匀,无气泡和杂质。
4. 干燥:将涂抹好电泳漆的金属基板放置在干燥环境中,待其干燥。
一般干燥时间为10-15分钟。
5. 测量:将干燥好的金属基板放置在磁性测厚仪上,调整测厚仪至合适位置,读取漆膜厚度值。
每个样品至少测量三次,取平均值作为最终结果。
6. 结果记录:记录每个样品的漆膜厚度值,并进行分析和比较。
六、合格标准根据客户要求和产品标准,制定相应的合格标准。
以下是一般情况下的合格标准示例:1. 漆膜厚度应在规定范围内,如未规定范围则需根据产品特性和客户要求确定。
2. 漆膜厚度均匀,偏差不得超过规定范围。
3. 不得出现气泡、杂质等缺陷。
4. 符合相关环保法规要求。
七、注意事项1. 测试过程中要保持环境清洁,避免灰尘和杂物影响测量结果。
2. 每次测量前需将测厚仪调整至零点,确保测量准确性。
电泳漆膜附着力等级判定方法

电泳漆膜附着力等级判定方法全文共四篇示例,供读者参考第一篇示例:电泳漆膜附着力是指电泳漆膜与基材之间的粘附力,是评价涂层质量的重要指标之一。
附着力的好坏直接影响涂层的耐腐蚀性、耐磨性和耐候性等性能,因此对电泳漆膜附着力的判定至关重要。
为了准确判定电泳漆膜附着力,需要依据一定的标准和方法进行评定。
以下将介绍一种常用的电泳漆膜附着力等级判定方法。
一、工具和材料准备1. 电泳漆膜样品2. 附着力测试仪3. 刀片4. 砂纸5. 确保工具和材料的干净和合适性二、测试步骤1. 准备样品:从已干燥的电泳漆膜样品中选取符合要求的试验片。
确保电泳漆膜表面平整、无氧化和杂质。
如果有必要,可以使用砂纸轻轻打磨表面以确保表面平整。
2. 剥离测试:将刀片平放在电泳漆膜样品表面并用力沿着一定方向剥离涂层。
观察电泳漆膜与基材之间的剥离情况,判断附着力等级。
3. 评定等级:根据剥离测试的结果,将电泳漆膜附着力分为以下等级:(1)等级0:电泳漆膜与基材完全剥离。
(2)等级1:电泳漆膜与基材局部剥离。
(3)等级2:电泳漆膜与基材出现破损但未剥离。
(4)等级3:电泳漆膜与基材无明显破损或剥离。
4. 记录结果:对每个样品的测试结果进行记录,包括试验片编号、试验员信息、测试日期和附着力等级。
三、注意事项1. 在进行剥离测试时要注意操作技巧,以免损坏涂层或基材。
2. 确保测试环境干燥和安静,避免外界干扰。
3. 根据需要可以对不同方向、不同位置的样品进行多次测试,以获得更准确的结果。
4. 根据测试结果及时进行分析和处理,对于附着力等级较低的样品要及时调整涂装工艺以提高附着力。
通过以上的方法,可以对电泳漆膜的附着力进行准确判定,为涂装过程的质量控制提供参考依据。
在实际生产中,厂家可以根据自身情况对测试方法进行适当调整和改进,以满足产品质量要求。
希望以上内容对您有所帮助,谢谢!第二篇示例:电泳漆膜附着力是评定电泳漆膜在基材表面附着牢固程度的重要指标之一,对于确保电泳漆膜的质量和性能起着至关重要的作用。
电泳漆液成分及工艺条件对膜层的影响

电泳漆液成分及工艺条件对膜层的影响一、固体分含量固体分含量过低时,电解作剧烈,漆膜薄,气泡多,易产生针孔;过高时则膜层比较粗糙,易起桔皮。
因此稳定固体分含量是保证电泳质量的一个关键,对于EC-3000金色电泳漆来说,每电泳15一20M2的零件需补充1L浓缩液。
二、溶剂电泳漆液刚配制时,其溶剂含量稍高。
但随着漆液使用时间的延长和超滤的使用,溶剂不断挥发和滤出,其含量会逐渐下降,影响漆膜质量。
严重时,漆膜会在烘烤前脱落。
因此,应及时添加调整,一般每滤出100L超滤渗透液,应补充1.2L溶剂。
三、电压极间电压升高,电场作用加强,漆液中带电粒子泳动,沉积速度加快,使泳透力提高,膜层增厚。
电泳操作时,应根据零件形状与大小,槽液温度高低,所需膜的厚薄,选择最佳电压。
当电泳漆槽刚配制时,其溶剂含量及导电度均高,则电压应适当降低。
四、PH值由于阳极采用隔膜控制,电泳漆液的PH值较为稳定,当超滤液排出太多或隔膜液漏出进入电泳漆液时,使电泳漆液PH值发生变化,可用有机酸调整。
PH值过低时,漆膜再溶解增加,膜层变薄,且对设备腐蚀严重。
五、电导率电导率是控制电泳漆膜层质量的关键指标之一。
新配溶液时电导率可能较高,因此需要通地超滤排出渗液以降低电导率。
电导率过高,则膜厚易产生桔皮和表面粗糙等现象。
电导率过低,则容易产生针孔和麻点。
因此当电导率的高低不同时需要采用不同的电压和槽液温度,以便获得良好的膜层。
电导率较高时,可采用较低的电压和温度;反之则要相应提高电压和温度。
六、温度电泳漆液的温度一般控制在26度左右。
温度过低,必需使用较高的电压以达到电泳的目的;温度过高,则加剧溶剂的挥发,不利于电导率的稳定和控制。
七、电泳时间电泳时间的长短会影响漆膜外观及膜层的厚薄。
当电泳时间过长时,膜厚色深,透明性变差。
电泳时间过短,则膜层不完整。
因此需要根据漆液的电导率,固体分含量等因素的变化,在确定溶液温度和电压的前提下,选择最佳的电泳时间,以确保膜层的质量。
电泳常见质量问题之针孔及麻点

针孔:使用电泳设备对工件进行电泳时,工件上的电泳涂膜在烘干后产生针尖状的小凹坑或小孔,称为针,它与缩孔(陷穴)的区别是孔径小,中心无异物,且四周无漆膜堆积凸起。
由漆膜再溶解而引起的针孔,称为再溶解针孔;由于电泳设备在电泳过程中产生的气体、湿膜脱泡不良而产生的针孔,称为气体针孔;沿被涂物带电入槽的斜线形成的气体针孔称为带电人槽阶梯式针孔,一般出现在被涂物的下部。
①电泳电压过高,电解反应过剧,产生气泡过多,或升压速度过快。
适当降低电压。
②混入电泳漆中的杂质(油、润滑脂等)粘附在漆膜上。
除去电泳漆中的油脂等杂质。
③助溶剂含量偏低。
添加助溶剂。
④槽液温度过低或搅拌不充分,脱泡不良。
控制好槽液温度。
⑤涂料的pH过低及溶剂过剩使漆膜极化能力变低,抵抗杂质能力变弱。
提高涂料的pH并将漆膜厚度控制在必要的范围内。
⑥槽液杂质离子过高,电解反应剧烈,被涂物表面产生的气体多。
超滤除去杂质离子。
阴极电泳的缩孔产生原因还有前处理不良和涂料质量低劣(采取相应之法消除),这两种原因及第⑥项原因产生的缩孔或凹陷,一般可见底材。
⑦固体分过低。
提高固体分。
⑧电泳涂装后清洗不彻底或不及时,使漆膜再溶解。
磷化膜孔隙率高,易含气泡。
工件带电人槽时链速过慢;若链速太慢,不宜选用带电入槽的工艺,改用人槽后通电。
被涂物人槽端处液面流速低,有泡沫堆积;可使液面流速大于0.2m/s,以消除泡沫。
麻点:①电泳液中存在较粗大的机械杂质;检查电泳槽过滤装置。
②车间空气中含有的尘埃等漂浮物飘落到放在滴干区的工件上;搞好车间环境卫生,防止灰尘飘浮。
③烘炉内存在灰尘等杂物;清洁烤炉。
电泳漆膜出现陷穴(缩孔)怎么办由外界造成被涂物表面、磷化膜或电泳湿膜上附有尘埃、油分等,或在漆膜中混有与电泳涂料不相溶的异物,它们成为陷穴中心,并造成烘干初期的流展能力不均衡而产生火山口状的凹坑,直径通常为0.5-3.0mm,不露底的称为陷穴、凹坑,露底的称为缩孔。
产生原因:(1)槽液中混入异物(油分、灰分),油漂浮在电泳槽液表面或乳化在槽液中。
- 1、下载文档前请自行甄别文档内容的完整性,平台不提供额外的编辑、内容补充、找答案等附加服务。
- 2、"仅部分预览"的文档,不可在线预览部分如存在完整性等问题,可反馈申请退款(可完整预览的文档不适用该条件!)。
- 3、如文档侵犯您的权益,请联系客服反馈,我们会尽快为您处理(人工客服工作时间:9:00-18:30)。
1. 适用范围:本标准适用于钣金车身表面电泳涂层材料的检测。
2. 检验项目和技术指标见表一、表二。
序号
检验项目
单位
指标 执行标准 1
外观
A 板 级
8-10 QB8021 C 板
8-10
QB8021
L 板 7-10 QB8021 H 板
7-10 QB8021 2 膜厚 μm 20-30 GB/T1764 3 硬度 ≥ 2H GB/T6739 4 杯突 ≥ 6 GB/T9753 5 附着力 级 0-1 GB/T1720 6 柔韧性 mm 1 GB/T1731 7 冲击 cm 50 GB/T1732 8 光泽 (60°) 50-80 GB/T9754 9 耐水性 (40℃)h
≥ 500 GB/T5209 10 耐盐雾 h ≥ 1000 ASTMB117 11 干燥时间 (工件温度) 175℃ min 25 GB/T1728 12
泳透力
cm ≥ 80%
福特盒法
文件名称 电泳漆技术质量要求 文件编号
JB-2011-001
发布部门 工艺技术部
编制
审核
批准
实施日期
修订状态
A1
共2页
表二:电泳漆原漆技术指标
序号检验项目单位
指标
执行标准乳液色浆
1 外观乳白色液体灰色粘稠液体,
无结块
目测
2
不挥发物
(120±2)℃/1h
%36±257±2GB/T6751
3 细度μm≤10 15 GB/T6753.1
4 PH值 6.3-6.9 酸度计
5 电导率Μm/Cm 2000-2800 HC/T3336
6 MEQ酸mm01/100g 30-36 0.1mol/1NaOH滴定
7 MEQ碱mm01/100g 55-65 0.1mol/1H2SO4滴定
8 粘度(20℃)mP a·S≤100 GB/T2794
9 密度(20℃)g/ml 1.05-1.07 GB/T6750
10 溶剂含量(EB)% 0.5-1.5 气相色谱法。