Ф4m×56m回转窑大齿圈裂纹的处理
回转窑轮带修复工艺方案

回转窑轮带修复工艺方案及具体步骤通过多日来对φ4.8×72m回转窑二档轮带的清缺,裂纹现象已基本清除到位,根据裂纹的实际现状,焊补施工具体步骤如下:1、焊补前的准备工作1.进一步检查确定裂纹是否清除干净,无裂纹气泡等,方法:目视+着色剂探伤。
检查结果需得到相关人员的认可,方能进行下一步施焊。
2.严格按轮带的焊补工艺要求,对焊条进行烘焙,烘焙温度200°保温。
3.轮带焊补区域需在焊前预热,方法:使用气割枪加热和加热带加热。
加热温度200°-220°2、施焊过程的操作及相关记录1.施焊严格按焊补工艺施焊,具体操作:①采用J506焊条打底(厚度约40mm),打底施焊逐层清理焊渣并敲击焊道释放应力,完成后检查焊补质量(肉眼检查焊道质量),质量合格进行下一步工作。
②在打底焊接完成后,采用CO2气体保护焊进行堆焊,先堆焊侧面再堆焊底面的原则逐层次严格进行焊道敲击和清渣,检查焊道质量。
若发现异常必须排除后才能进行继续施焊(必须使用砂轮打磨清除),确保最终焊接质量。
采用CO2气体保护焊施工过程中,每焊接50mm~100mm层次时,必须进行一次气割枪烘烤至暗红色去应力回火操作程序(温度550°),才能继续进行堆焊。
③堆焊封面结束后,首先进行气割枪烘烤去应力程序,再利用余热用碳弧气刨将轮带工作面多余焊层刨除后,立即使用加热带覆盖焊补区域进行加热保温(温度约为550°),保温6小时后,以每小时逐步缓冷得方式,将焊补区域温度降至能够打磨和超声波探伤及表面磁粉探伤。
3、修复时间安排1.采取每日8点至22点连续作业方式进行焊补,22点后至次日8点(焊补前)使用加热带进行保温(保温温度±200°)2.施工过程时间预计(1)焊补需时6天(2)保温去应力需时2天(3)探伤检查在加温去应力后进行。
回转窑轮带裂口焊修
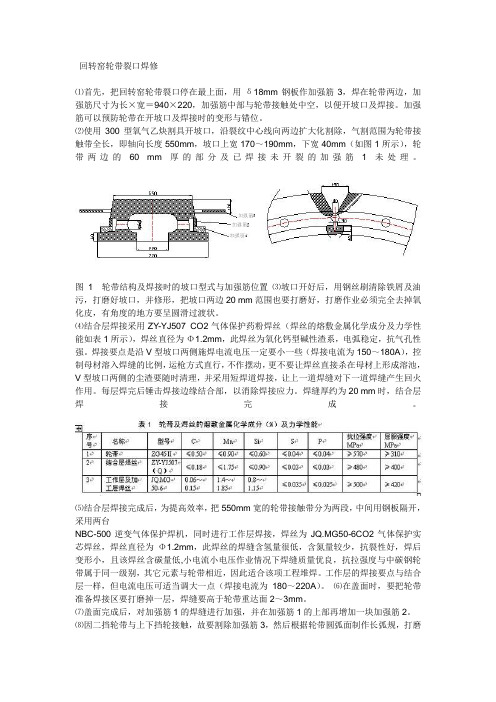
回转窑轮带裂口焊修⑴首先,把回转窑轮带裂口停在最上面,用δ18mm钢板作加强筋3,焊在轮带两边,加强筋尺寸为长×宽=940×220,加强筋中部与轮带接触处中空,以便开坡口及焊接。
加强筋可以预防轮带在开坡口及焊接时的变形与错位。
⑵使用300型氧气乙炔割具开坡口,沿裂纹中心线向两边扩大化割除,气割范围为轮带接触带全长,即轴向长度550mm,坡口上宽170~190mm,下宽40mm(如图1所示),轮带两边的60 mm厚的部分及已焊接未开裂的加强筋1未处理。
图1轮带结构及焊接时的坡口型式与加强筋位置⑶坡口开好后,用钢丝刷清除铁屑及油污,打磨好坡口,并修形,把坡口两边20 mm范围也要打磨好,打磨作业必须完全去掉氧化皮,有角度的地方要呈圆滑过渡状。
⑷结合层焊接采用ZY-YJ507 CO2气体保护药粉焊丝(焊丝的熔敷金属化学成分及力学性能如表1所示),焊丝直径为Φ1.2mm,此焊丝为氧化钙型碱性渣系,电弧稳定,抗气孔性强。
焊接要点是沿V型坡口两侧施焊电流电压一定要小一些(焊接电流为150~180A),控制母材溶入焊缝的比例,运枪方式直行,不作摆动,更不要让焊丝直接杀在母材上形成溶池,V型坡口两侧的尘渣要随时清理,并采用短焊道焊接,让上一道焊缝对下一道焊缝产生回火作用。
每层焊完后锤击焊接边缘结合部,以消除焊接应力。
焊缝厚约为20 mm时,结合层焊接完成。
⑸结合层焊接完成后,为提高效率,把550mm宽的轮带接触带分为两段,中间用钢板隔开,采用两台NBC-500逆变气体保护焊机,同时进行工作层焊接,焊丝为JQ.MG50-6CO2气体保护实芯焊丝,焊丝直径为Φ1.2mm,此焊丝的焊缝含氢量很低,含氮量较少,抗裂性好,焊后变形小,且该焊丝含碳量低,小电流小电压作业情况下焊缝质量优良,抗拉强度与中碳钢轮带属于同一级别,其它元素与轮带相近,因此适合该项工程堆焊。
工作层的焊接要点与结合层一样,但电流电压可适当调大一点(焊接电流为180~220A)。
回转窑筒体开裂怎么处理

如果回转窑筒体开裂应该如何处理?
回转窑在长时间的使用过程中,会出现筒体开裂的情况,为了能够尽快的处理这个问题,我们首先应该分析筒体开裂的原因是什么,根据原因来进行处理。
回转窑筒体开裂的原因:
1、窑体振动;
2、红窑烧损,窑筒体强度削弱;
3、某挡轮顶力太大;
4、钢板沉陷不均,造成窑体弯曲;
5、钢板薄;
6、基础沉陷不均,造成窑体弯曲;
7、筒体表面超过400℃报警温度,钢板蠕变降低强度。
通过长期经验总结回转窑筒体出现开裂可以归纳为上面的七种情况,我们根据每种情况进行下面的处理:
回转窑筒体开裂的处理方法:
1、修复窑体,加固筒体;
2、正确调整托轮,减轻负荷;
3、用探伤仪检查内部缺陷,及缺陷部位的周围。
4、用铆钉铆住,以防扩展;
5、选择合适的钢板厚度;
6、调整托轮底座位置;
7、采取措施,降低窑筒体温度。
回转窑筒体裂纹的原因分析及预防措施

回转窑筒体裂纹的原因分析及防范措施焦作坚固水泥有限公司王占光邮编454002一、引言随着窑外分解技术的成熟,水泥大型装备的不断研发和机械制造业的提升,为水泥单线生产能力的扩大提供了条件,日产10000吨的熟料生产线在我国已投运多年,日产5000吨的熟料生产线已成为生产主力。
但由于设计、制造、安装、维护、配料等方面的原因,很多回转窑在投运不长的时间内,便出现了筒体裂纹,特别是回转窑过渡带的筒体裂纹,给生产企业造成了不小的损失,为此,笔者根据自己的经验,分析了回转窑筒体产生裂纹的主要原因,提出了针对预防裂纹的具体措施,望能对水泥设备管理者起到借鉴作用。
二、回转窑易产生裂纹的部位及形式回转窑裂纹的部位及形式较多。
裂纹的部位多发生在轮带、大齿圈两侧的焊缝处以及其它筒体焊缝的两侧,当前裂纹最多的发生在回转窑过渡带筒体上,且一旦开裂,修复的经济性、可靠性较差,即不具备修复性,必须更换筒体。
裂纹的形式也有多种,但归纳起来有三种,即纵向裂纹、环向裂纹以及不规则裂纹。
纵向裂纹多发生在轮带下筒体的垫板及挡块和筒体的焊缝处;环向裂纹多发生在轮带两侧的过度筒体的焊缝处,以及回转窑过渡带的筒体焊缝处,还有大齿圈下筒体与弹簧板的焊缝处。
不规则裂纹多发生在回转窑的喂料、出料的筒体开口处,目前该类窑型因已淘汰而不多见,故在下文中不再赘述。
三、回转窑筒体产生裂纹的原因分析回转窑是多点支撑、重载低速的热工设备,受力复杂,引起裂纹的因素较多,涉及设计、制造、安装、检修维护、管理诸多方面。
现就产生裂纹的主要原因进行分析。
3.1纵向裂纹形成的原因纵向裂纹多发生在轮带下筒体与垫板或挡块的焊缝处,一般由外及里且沿轴向延伸形成纵向裂纹,甚至开裂。
究其原因主要由四个方面造成。
首先是设计时筒体板材厚度选择较薄,我们知道回转窑要求横刚纵柔,若板材厚度不足,就难以保证其横向刚度,所以筒体在自重和托轮支撑反力的产生的交变应力和脉冲应力的作用下,易使材料产生疲劳,达到一定条件后,裂纹便会在该处比较薄弱的焊缝热影响区形成,即筒体与挡块或垫板焊缝处形成,并在径向上由外向内发展、在轴向上左右延伸,形成纵向裂纹。
回转窑托轮表面裂纹修复方案

回转窑托轮表面裂纹修复方案可以采用以下步骤:
1. 检测:首先使用探伤仪对托轮表面进行检测,找出裂纹的位置、长度和深度。
同时,对裂纹周边进行打磨处理,确保表面干净、平整,为后续修复做好准备。
2. 选择修复材料:根据托轮的材质和工况条件,选择具有良好耐磨、耐热、抗腐蚀性能的修复材料,如“MSFH”功能梯度冶金粉末复合材料。
3. 预处理:对受损部位进行预处理,如去除残留的旧涂层、氧化皮和焊渣等,以提高修复材料与基体的粘结力。
4. 熔敷层的结构设计:根据工件的材质、工况条件和技术要求,设计结合层、过渡层和工作层的厚度。
5. 修复工艺:采用焊接或热喷涂等方法,将修复材料涂敷到托轮表面,并控制熔敷过程中的温度、速度和压力等参数,以确保涂层的质量和性能。
6. 固化与加工:修复材料熔敷后,进行适当的热处理和冷却,使其达到预期的硬度和强度。
然后对修复部位进行加工,如打磨、抛光等,以满足托轮的使用要求。
7. 检验与验收:对修复后的托轮进行检验,检查修复部位的表面质量、尺寸和性能是否满足要求。
如有必要,可以进行二次修复或调整。
8. 后期维护与保养:在托轮修复后,要加强监测其使用过程中的磨损和裂纹情况,及时采取措施进行调整和修复。
同时,遵守相关操作规程,确保托轮的正常运行。
回转窑筒体开裂的修复

回转窑筒体开裂的修复王宗璞【摘要】回转窑是水泥厂的关键设备,筒体又是回转窑的关键部件,筒体开裂的原因很复杂,且受多方面因素影响.文章通过分析筒体开裂原因,制定和实施修复方案,并采取一定的措施,确保修复后的筒体焊缝质量,防止裂纹扩展,保证回转窑的正常运行.【期刊名称】《水泥技术》【年(卷),期】2016(000)004【总页数】2页(P72-73)【关键词】筒体;开裂;修复【作者】王宗璞【作者单位】博爱金隅水泥有限公司,河南焦作454461【正文语种】中文【中图分类】TQ172.622.29我公司2 500t/d熟料水泥生产线于2006年2月投产,回转窑年实际产能均在设计生产能力的110%~115%。
2013年年终大修停产冷窑后,发现在窑长度居中(距窑头窑尾约30 000mm处)的烧成带与过渡带交汇区2号轮带处,筒体加厚段往窑尾方向轴向排列有三道环向裂缝和若干道磨蚀沟。
我公司分析了原因,制定了修复方案并实施,经过两年多的运转证实,修复方案合理可行,措施得当,保证了回转窑的正常运转。
1.1 开裂及磨蚀区域我公司回转窑规格为ϕ4m×60m,筒体钢板材质为Q235-B,钢板厚度为22~60mm,其开裂及磨蚀区域如图1、图2所示。
1.2 开裂磨蚀情况(1)2号轮带处的轮带下筒体钢板(厚度80mm)与过渡段筒体钢板(厚度60mm)焊缝环向开裂,从内壁向外延伸,沿圆周方向长度1 460~1 500mm,厚度方向局部已裂透至筒体外表面,裂缝宽1~1.5mm(图3)。
焊缝向窑尾方向200mm(正好是一块耐火砖长度)处环向开裂,从内壁向外延伸,沿圆周方向长度600~650mm,局部已裂透至筒体外表面,裂缝宽0.5~1.2mm (图4)。
焊缝向窑尾方向约400mm(正好是两块耐火砖长度)处环向开裂,从内壁向外延伸,沿圆周方向长度1 300mm左右,局部已裂透至筒体外表面,裂缝宽1~1.5mm(图5)。
(2)焊缝向窑尾方向约600mm轴向排列3道间隔200mm(正好是一块耐火砖长度)磨蚀沟,宽15~18mm,深3mm左右(图6)。
回转窑筒体裂纹修复方案研讨
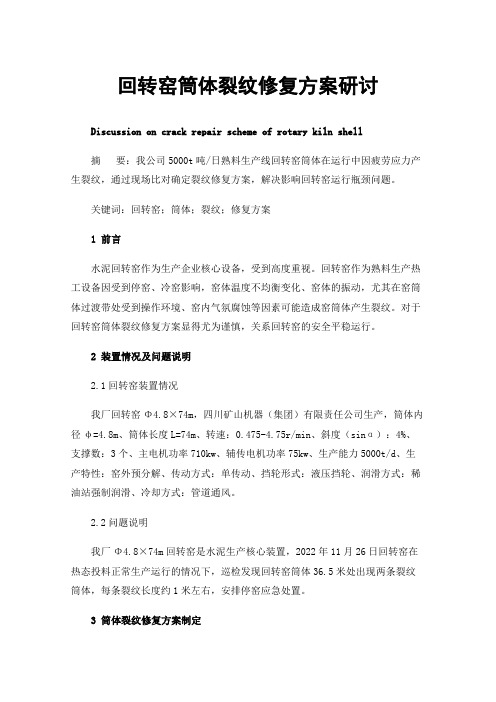
回转窑筒体裂纹修复方案研讨Discussion on crack repair scheme of rotary kiln shell摘要:我公司5000t吨/日熟料生产线回转窑筒体在运行中因疲劳应力产生裂纹,通过现场比对确定裂纹修复方案,解决影响回转窑运行瓶颈问题。
关键词:回转窑;筒体;裂纹;修复方案1 前言水泥回转窑作为生产企业核心设备,受到高度重视。
回转窑作为熟料生产热工设备因受到停窑、冷窑影响,窑体温度不均衡变化、窑体的振动,尤其在窑筒体过渡带处受到操作环境、窑内气氛腐蚀等因素可能造成窑筒体产生裂纹。
对于回转窑筒体裂纹修复方案显得尤为谨慎,关系回转窑的安全平稳运行。
2 装置情况及问题说明2.1回转窑装置情况我厂回转窑Φ4.8×74m,四川矿山机器(集团)有限责任公司生产,筒体内径φ=4.8m、筒体长度L=74m、转速:0.475-4.75r/min、斜度(sinα):4%、支撑数:3个、主电机功率710kw、辅传电机功率75kw、生产能力5000t/d、生产特性:窑外预分解、传动方式:单传动、挡轮形式:液压挡轮、润滑方式:稀油站强制润滑、冷却方式:管道通风。
2.2问题说明我厂Φ4.8×74m回转窑是水泥生产核心装置,2022年11月26日回转窑在热态投料正常生产运行的情况下,巡检发现回转窑筒体36.5米处出现两条裂纹筒体,每条裂纹长度约1米左右,安排停窑应急处置。
3 筒体裂纹修复方案制定查找设备采购与服务合同,回转窑筒体36.5米筒体壁厚28mm。
我厂确定方案筒体修补方案是先从筒体外部对裂纹补焊、然后进入回转窑内挖砖、内部裂纹补焊。
具体修复方案如下:3.1修复前准备情况3.1.1根据裂纹长度下料制作“U”形加强拉筋3~4件,用Q235B δ30钢板割制(如图1),在立腿部位开坡口。
(图1)(图2)3.1.2根据裂纹长度下料制作筒体加强板4~6件,长度为500 mm,宽度为200 mm,两端制成圆弧,另在加强板中心位置开一直径为6 mm的孔,此孔为通气孔,排出焊接产生的气体以及今后运行过程中加强板与筒体微动产生的杂质等,用Q235B δ20钢板卷制(如图2),在与筒体贴合部位开焊接坡口。
回转窑筒体裂纹及腐蚀的处理与预防

中图分类号:TQ 72.622.26 文献标识码:B 文章编号: 008-0473(20 8)03-0073-03 DOI编码: 0. 6008/ki. 008-0473.20 8.03.0回转窑筒体裂纹及腐蚀的处理与预防朱攀勇1 付金强1 高先梨2 余明江2 王盛凯21. 中国葛洲坝集团水泥有限公司,湖北 武汉 430073;2. 葛洲坝宜城水泥有限公司,湖北 宜城 441400摘 要 2018年大检修期间,停窑拆除耐火砖,硅莫砖部位筒体吸潮“冒汗”现象严重,窑筒体形成栅格状有大量的腐蚀层,37.8 m处挡砖圈阶梯靠窑头侧有20~30 mm宽的环向凹槽,欲更换的34.7~37.5 m处宽2.8 m 筒体冷却后在短时间内由3道裂纹增至数十条对称裂纹。
为了防止更换窑砖与筒体后再次发生腐蚀、产生裂纹,通过筒体探伤、测厚、腐蚀层及筒体检测等对回转窑筒体裂纹及腐蚀机理进行研究分析,得出结论:应力与腐蚀是筒体裂纹产生的主要原因。
腐蚀主要原因是高温氧化、硫化腐蚀、氯化腐蚀。
针对裂纹与腐蚀采取有效的处理方法,并提出防范措施。
关键词 回转窑 筒体 裂纹 腐蚀 处理 预防0 引言2017年2月3日,我公司回转窑(Φ4.8 m×74 m)筒体在开机过程中发现34.2m处回转窑60~28 m过渡带附近出现一条500 mm长环向裂纹,随后立即对该处筒体进行了探伤检测,结果显示在该裂纹环向共有三道长短不一的裂纹。
考虑窑筒体加工制造需要较长时间,为了保证生产,采用了应急处理方案,堆焊裂纹,在筒体发生裂纹的周向加焊了20块δ=40 mm的筋板。
2018年1月原裂纹加强筋板边缘(靠窑尾方向)处又出现三段环向裂纹,止料停窑后约24 h,回转窑按要求冷却至常温,该处又出现数十道长从100 mm至1 200 mm不等的环向裂纹,于是按照检修计划更换了该处2.8 m长筒体。
拆除耐火砖,硅莫砖部位筒体吸潮“冒汗”现象严重,窑筒体形成栅格状有大量的腐蚀层,对腐蚀层与筒体进行了化验检测,对窑筒体整体进行了测厚与探伤,化验结果显示腐蚀层Cl-含量达到3.73%,磷化物含量高达5.95%,硫化物浓度达0.18%,筒体最薄区段为37.8~47.8 m段δ=28 mm的10 m长窑筒体,且37.8 m处挡砖圈阶梯靠窑头侧有20~30 mm宽的环向凹槽,最薄厚度达到14 mm。
石灰回转窑筒体断裂的原因及处理方式

石灰回转窑筒体断裂的原因及处理石灰回转窑是活性石灰厂关键设备之一。
由于体积庞大,加上又处于冷热交替、高温作业环境下,因而筒体断裂及焊缝开裂事故时有发生。
石灰回转窑筒体断裂通常有以下几种情况:①处于轮带下的筒体,发生程度不同的“颈缩”现象,持续运转就容易造成筒体断裂(裂纹或裂断)。
②在冷却机与石灰回转窑下料口交接处的筒体,回转窑容易发生筒体断裂事故。
石灰回转窑筒体断裂时,通常有多种形态:①裂纹沿筒体截面圆周长分布,并伴有筒体弯曲现象。
②裂纹一旦超出窑圆周长1/3以上,就有可能产生筒体断裂事故。
1.原因分析造成石灰回转窑筒体断裂的原因是多方面的,归纳起来有以下几点:(1)整体强度低,投入正常生产后,引起筒体断裂比如,多筒冷却机石灰回转窑,在冷却筒与窑下料口交接处筒体圆周上均布着若干个多筒冷却机下料孔,使实有铁板长度仅为圆周长的1/2左右,整体强度明显下降,故此处极易断裂。
(2)高温状态下材质疲劳,引起筒体断裂石灰回转窑筒体要长期承受交变载荷作用和冷热变化,因回转窑生产原因及非生产原因停窑时,都有可能使筒体断面产生径向变形。
对窑的热工标定表明,筒体表面温度常常高达300℃以上。
在这种高温工作环境下,尤其是冷热交替,极易导致筒体钢板材质疲劳,刚度下降,进而断裂。
(3)不适当的维修导致了筒体断裂石灰回转窑筒体出现裂纹后,必然进行抢修。
但在抢修过程中,如果焊工焊接技术不过关,或焊接填充金属选择不当,所焊回转窑部位容易再次开裂,并延伸扩大,导致筒体断裂事故的发生。
(4)石灰回转窑筒体在加工制造、运输、安装等过程中不经心形成了沟痕,导致了微细裂纹,荷重后微细裂纹扩展开来,发展到筒体断裂。
或者筒体在制作过程中残留下了焊接应力,甚至焊缝内有气孔、砂眼等缺陷,在交变应力和高温作用下,缺陷形成裂纹,焊缝成为裂缝,导致筒体断裂。
2.处理方法(1)断裂筒体的抢修对于断裂情况不十分严重的石灰回转窑筒体,可采用焊接的方法加以抢修。
结合实例谈回转窑轮带裂纹处理方法
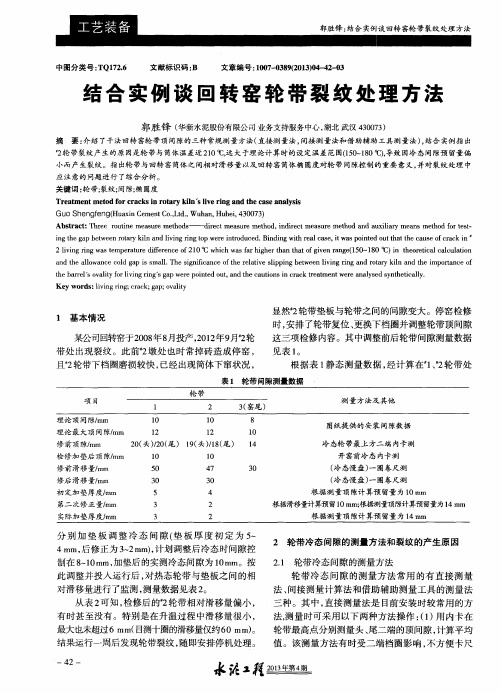
应 注 意 的 问题 进 行 了综 合 分 析 。
关键词 : 轮 带; 裂纹; 间隙; 椭 圆度
Tr e a t me n t me t o d f o r c r a c k s i n r o t a r y k i l n S l i v e r i n g a n d t h e c a s e r i n g w a s t e mp e r a t u r e d i f f e r e n c e o f 2 1 0 o C w h i c h w a s f a r h i g h e r t h a n t h a t o f g i v e n r a n g e ( 1 5 0 - 1 8 0 o c ) i n t h e o r e t i c a l c a l c u l a t i o n
中图分类 号 : T Q1 7 2 . 6
文献标识码 : B
文章 编号 : 1 0 0 7 — 0 3 8 9 ( 2 0 1 3 ) 0 4 — 4 2 — 0 3
结 合 实 例 谈 回 转 窑 轮 带 裂 纹 处 理 方 法
郭胜 锋 ( 华新水泥股份有限公司业务支持服 务中心, 湖北武汉4 3 0 0 7 3 )
表 1 轮带间隙测量数据
奎 篙
这三项检修 内容 。其 中调整前后轮带间隙测量数据 见表 1 。 根据表 1 静态测量数据 , 经计算在 1 、 2 轮带处
分 别 加 垫 板 调 整 冷 态 间 隙( 垫板 厚 度 初 定 为 5 ~ 4 m m, 后修正为 3 ~ 2 m m ) , 计划调整后冷态时间隙控 制在 8 ~ 1 0 m l T l , 加 垫后 的实 测冷 态 间隙 为 1 0 mm。按 此调整并投入运行后 , 对热态轮带与垫板之 间的相 对 滑移 量进 行 了监测 , 测量 数 据见表 2 。 从表 2 可知 , 检修后的 2 轮带相对滑移量偏小 , 有 时甚至没有 。特别是在升温过程中滑移量很小 , 最大也未超过6 mm ( 目 测十圈的滑移量仅约6 0 mm ) 。 结 果运 行一 周后 发现 轮带 裂纹 , 随 即安 排停机 处 理 。
回转窑大齿圈维修要点

回转窑设备运转维护更换大齿圈的方法和技巧回转窑设备运转到一定时间的时候,有些部件会有不同程度的磨损,对于日后如何维护和更换回转窑这种大型设备上的部件,回转窑生产厂家泰达集团是非常有经验的,本篇,就由泰达集团回转窑科研小组详细解答一下回转窑设备更换大齿圈的一些方法和技巧。
对于一些直径4m以上、运转时间较长的窑,会发现回转窑设备大齿轮、小齿轮的齿顶宽的磨损都超过1/3,齿顶间隙已达20mm,回转窑窑体振动严重。
此时,更换大齿圈是一个办法,只要非工作面的齿面及弹衡板完好,通过将大齿圈翻面,并更换小齿轮,不但同样可以使回转窑窑正常运行很长时间,而且节约很大一笔维修费用。
回转窑设备更换大齿圈的具体步骤和要求如下。
确定回转窑大齿圈及弹簧板是否可用。
在回转窑大齿圈最下方固定百分表,让窑慢转,选择齿圈上的8个点测量大齿圈的径向与端向跳动量,以判断大齿圈是否变形。
并侧量大齿圈上两个相邻孔距离,间接反映螺栓孔磨损量,以确定弹黄板是否可用。
拆卸回转窑大齿圈。
在回转窑大齿圈的一个半圆转到正上方时,拆除小齿轮轴,使大齿圈与原传动脱离,作好标记后拆下螺栓。
然后用卷扬机转动窑体,取下另一半大齿圈。
如果回转窑拆下第一个半圆后即刻翻面为最好,但由于螺桂很难整体取出,只好将大齿圈放置到地上。
同时回转窑要预防弹簧板在大齿圈的拆装过程中挤压和变形。
安装回转窑大齿圈。
清理油污并打磨齿上毛刺和凸合后,用吊车把大齿圈安在筒体的上半部。
用螺栓与弹黄板连接,焊接方钢、调节螺栓等找正工具。
转动窑后安装另一半,紧固对口螺栓。
共用六块方钢分别焊接在大齿圈的立筋位置。
回转窑设备大齿圈投正。
调节找正工具至受力状态。
使回转窑大齿圈处于基本正确位置,转动窑体,用百分表测量齿圈的径向和端向跳动量。
此时,一般将齿根作为找正基准,并用电焊将齿圈及弹簧板耳点焊在一起准各俊孔。
在松开找正工具后。
进行第二次侧量确认,如有较大的变化,将焊点脱开后再重新找正。
回转窑设备镗孔。
回转窑轮带修复方案

设备隐患防范治理案例之—回转窑轮带焊接修复方案一、概况截止到2014年2月底,股份公司共有112台窑,随着设备运行时间的延长,枞阳、铜陵等公司回转窑相继出现了轮带开裂的重大隐患,严重影响窑系统的稳定运行。
为做好窑轮带开裂问题处理,缩短设备维修时间,降低运行成本,铜陵海螺公司采取了对裂纹焊接的方式进行了现场修复,目前使用效果较好,现对处理方案进行了整理,供各公司参考。
轮带开裂部位轮带开裂部位二、处理方案1、在轮带工作表面及侧面开裂处分别用厚度为δ=50mm 钢板进行加固,加固后逐段进行处理,防止一次性将裂纹打坡口后造成轮带断裂。
轮带工作面筋板加固轮带侧面筋板加固2、将轮带窑尾侧裂纹处用气割按厚度开U型坡口,坡口宽度大约400-500mm左右,深度到裂纹终端为止,开好坡口后用磨光机进行打磨清理,直至露出金属本色。
对U型坡口打磨过后露出金属本色3、首先用KM1酸性焊丝(含药芯)从坡口开始进行堆焊,每焊一层,对焊层上焊渣进行清除,检查焊层有无夹渣和气孔,同时对堆焊层表面进行打磨,露出金属光泽后继续堆焊。
堆焊至150mm高时,用黄色焊丝进行堆焊。
每焊一层,对堆焊层上焊渣进行清除,检查焊层有无夹渣和气孔。
每堆焊1层,对结合处进行打磨,露出金属光泽为止。
继续堆焊,堆焊至离顶部2-3层时,在堆焊层均匀撒处理药粉,再进行堆焊,直至堆焊到顶部。
(注:堆焊时,下部每堆焊5层时,在堆焊层表面均匀撒一次KM-1#金属粉;中部每堆焊5层时,在堆焊层表面均匀撒一次KM-2#金属粉;上部每堆焊8层时,在堆焊层表面均匀撒一次KM-3#金属粉)堆焊所使用的焊丝对堆焊层进行清理对堆焊层进行打磨处理完成的堆焊层5、对剩余一侧的裂纹按照以上方式进行坡口处理,在处理时对新熔敷堆焊部分清理30-40mm重合区,并依次进行打磨、堆焊和弧度修复处理。
6、两侧堆焊全部结束后,再次对熔敷表面进行整体修复,确保加工面弧度与原轮带弧度一致,误差控制在-0.30mm以内。
国转窑轮带裂纹修复工艺方案分析
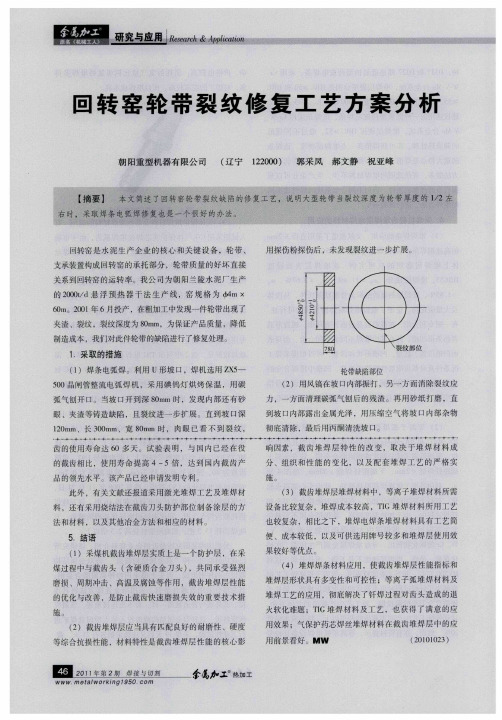
响因素 ,截齿堆 焊 层特 性 的改 变 ,取决 于堆 焊 材料 成 分 、组织 和性 能 的变化 ,以及 配套 堆焊 工艺 的严 格 实 施。 ( )截齿堆焊层堆焊材料中 ,等离子堆焊 材料所需 3 设备 比较复杂 ,堆焊成本较 高,TG堆焊材料 所用 工艺 I 也较复杂 ,相 比之 下,堆焊 电焊条堆焊 材料具有工 艺简 便 、成本较低 ,以及可供选用牌号较多 和堆焊层使用效
磨损 、周期 冲击 、高温及腐蚀等作用 ,截 齿堆焊层性 能
的优化与改善,是 防止截齿快速磨损失效 的重要技术 措
施。
( )截齿堆 焊层应 当具有匹配 良好的耐磨性 、硬 度 2 等综 合抗损性能 ,材料特性是截齿堆焊层性 能的核心影
用效果 ;气保 护药芯焊丝堆焊材料在截齿 堆焊层 中的应 用前景看好。MW (0 00 3 2 1 12 )
大 及温 度突变 ,极 易产生 裂纹 ,达不 到补 焊质量 的要 求。
表 1 Z 30 7 G 1 —5 O的化 学 成 分 及 力 学 性 能
化学 成 分 C S Mn S i ( 质量 分数 % ) .0O 6 .00 0 .4O 3 . 50 3 . .5 0 5 . 00 9 . 400 . 00 3 .O O 2 O 0
,
为了保证根部焊道热影 响区 的补焊 质量 ,使焊缝金 属与母材 的强度 、韧性与补焊层更好地结 合 ,底部用镍 基焊条打底 。该焊 条具有 良好 的抗 裂性 能 和工艺性 能。 选用 A 0 5 7奥氏体不锈 钢焊条作 为过 渡层材料 ,此 焊条 具有 良好 的抗裂和抗氧化性能 ,可交直流 两用 ,有 良好 的操作工艺性能。 为 了保证轮带 的使用性 能,焊接 材料宜选择等 强或
回转窑筒体裂纹的处理

#" 多年, 因此安全系数要大些。
修复后的窑筒体自开始运转至今,状况一直良 好; 稳 定 运 转 熟 料 最 高 达 ’ !"" 4562 从 而 保 证 了 生 产的顺利进行。
. /01012 . 345#1#$$!%$"%&&2
!!!!!!!!!!!!!!!!!!!!!!!!!!!!!!!!!!!!!!!!!!!!!! !广告 !
!""# !" $ #
%$" !"" %!4 % %.$# ".&"
9:;<=>? @(*67A %
烧成带筒体厚度均在 !" // 以上。而该窑烧成带筒 体选用 %2 // 厚 8# 钢,加上长时间运行中的氧化 腐蚀等原因, 实 测 筒 体 厚 度 仅 为 %1.2 //, 较薄、 强 度小。烧成带筒体厚度 "! 计算公式如下:
!," - , 保温 ’," - 。选用 (#)! && 的 .,"% 酸性焊
条, 其焊 缝 金 属 塑 性 、 韧性、 抗裂性均较好, 且其焊 接工艺特点是电弧稳定、 飞溅小、 脱渣容易、 熔深适 中。焊接电流为 ’"" /’!" 0。 焊接时必须严格保证焊接质量,除净焊渣; 每 焊一层应用小锤对焊缝隙表面进行锤击, 以消除焊 接残余应力。填充焊接结束时要严格保证焊接处平 缓圆滑过渡, 焊缝饱满, 均匀整齐, 保证焊缝隙金属 与母材金属完全融合, 再用砂轮机对筒体表面突出 的焊肉进行打磨修理, 使表面平滑。 裂纹修复后, 对焊缝进行超声波仪检验, 不能
+
" (%)*+,-.
水泥回转窑轮带结构裂纹在线修复技术
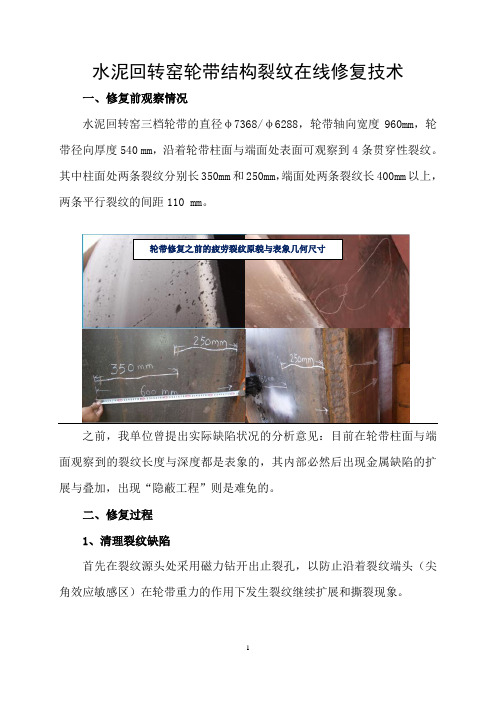
水泥回转窑轮带结构裂纹在线修复技术一、修复前观察情况水泥回转窑三档轮带的直径φ7368/φ6288,轮带轴向宽度960mm,轮带径向厚度540 mm,沿着轮带柱面与端面处表面可观察到4条贯穿性裂纹。
其中柱面处两条裂纹分别长350mm和250mm,端面处两条裂纹长400mm以上,两条平行裂纹的间距110 mm。
轮带修复之前的疲劳裂纹原貌与表象几何尺寸之前,我单位曾提出实际缺陷状况的分析意见:目前在轮带柱面与端面观察到的裂纹长度与深度都是表象的,其内部必然后出现金属缺陷的扩展与叠加,出现“隐蔽工程”则是难免的。
二、修复过程1、清理裂纹缺陷首先在裂纹源头处采用磁力钻开出止裂孔,以防止沿着裂纹端头(尖角效应敏感区)在轮带重力的作用下发生裂纹继续扩展和撕裂现象。
之后,采用碳弧气刨的方法清理裂纹缺陷。
打开金属缺陷处,则发现在轮带柱面表层下40-50mm 的位置存在着空洞缺陷和沿径向层状撕裂金属,为首先发生宏观的金属疲劳破坏的部位。
这是因为轮带大型铸钢件内部难免存在着铸造缺陷(气孔、夹渣等),同时轮带与托轮接触表面之下40--50 mm ,区域,恰好也是动荷载条件下因支反力所致交变应力集中处,从而成为轮带发生疲劳破坏(金属组织不断地发生塑性变形和冷作硬化,逐渐发生脆化,初始期的形态为显微裂纹)的源头。
在长期服役过程中,所产生的疲劳裂纹必然会逐步扩展,最终导致沿着轮带的径向与轴向方向,出现宏观裂纹的后果。
可见,水泥窑的轮带或者托轮若出现了表面金属缺陷与脱落时,则表明其构件内部金属已经发生了疲劳破坏现象,需要及时给予修补。
非常忌讳因为忙于完成生产任务而贻误了及早“治疗”的时机,“带病作业”会加速已形成的显微裂纹的扩展,最终造成疲劳断裂,加剧了设备的损坏,得不偿失。
轮带柱面表层下40-50mm 的位置疲劳破坏金属缺陷的起始区疲劳裂纹 铸造空穴缺陷层状金属缺陷 用磁力钻钻止裂孔疲劳破坏将导致表面金属缺陷与脱落现象为了避免轮带结构在打开缺陷的“手术”中,因窑体自重而沿着裂纹处发生彻底断裂,从而发生轮带构件的径向错位(若破坏了同心度,则水泥窑旋转时轮带会产生径向跳动,影响设备正常运行),我们随时做出了正确的应力分析,尤其是判断应力的走向与分布,以此来制定具体的清除金属缺陷工艺流程。
回转窑胴体开裂焊接处理方案
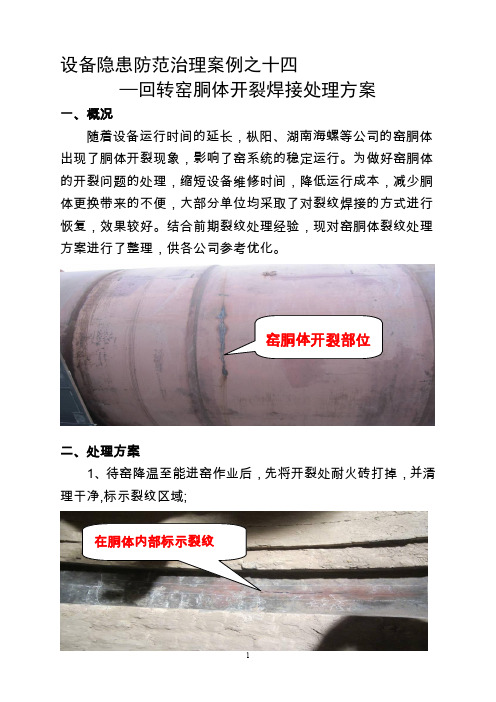
设备隐患防范治理案例之十四—回转窑胴体开裂焊接处理方案一、概况随着设备运行时间的延长,枞阳、湖南海螺等公司的窑胴体出现了胴体开裂现象,影响了窑系统的稳定运行。
为做好窑胴体的开裂问题的处理,缩短设备维修时间,降低运行成本,减少胴体更换带来的不便,大部分单位均采取了对裂纹焊接的方式进行恢复,效果较好。
结合前期裂纹处理经验,现对窑胴体裂纹处理方案进行了整理,供各公司参考优化。
窑胴体开裂部位二、处理方案1、待窑降温至能进窑作业后,先将开裂处耐火砖打掉,并清理干净,标示裂纹区域;在胴体内部标示裂纹2、对裂纹延生区打磨、探伤,根据探伤情况确定裂纹的实际长度和端部位置,在裂纹两侧终端用磁力钻钻止裂孔,止裂孔大小根据裂缝大小确定;确定裂纹长度和端部3、在胴体外部的裂纹位置,环向搭操作平台及防雨棚;4、用碳弧气刨将内部开裂处打V形坡口,坡口深度根据开裂处筒体厚度而定,坡口用角向磨光机打磨处理;用碳弧气刨开V型坡口V型坡口清理再次确认裂纹位置和止裂孔的大小及位置是否合理5、开裂处的V形坡口沟槽经打磨后,用J507焊条进行焊接。
焊接前将焊条放在350℃烘箱干燥处理,不得低于2小时,且将焊接位置进行预热处理后,避免在焊接过程中出现气孔,堆焊至筒体内壁相平。
焊接前对焊接位置进行预热处理内部打底堆焊内部堆焊,每根焊条焊完必须经打磨处理后,方可施焊第二根焊条焊接结束后将焊缝打磨平整6、待内部焊接完毕后,启动辅传将筒体开裂处转至上部,按照在内部焊接的方式对外部进行焊接。
外部开“V”型坡口焊接前加热处理外部堆焊焊接完毕后探伤检查用超声波对焊缝进行全面探伤其它部位探伤检查7、裂缝全部焊接完成后,用钢板制作加强筋在筒体外侧沿开裂处环向均布焊接,钢板长度方向两边满焊,钢板轴向方向不焊接。
胴体外部焊接加强筋8、焊接后,再次用割枪加热焊缝至150℃以上,后用保温棉覆盖保温5小时以上,内部耐火砖砌筑,系统检查,准备开机。
窑胴体开裂的原因有:⑴、胴体长期运行疲劳受力,发生开裂;⑵、胴体被腐蚀,胴体变薄,强度不够;⑶、使用过程中,一些细小的开裂未及时发现,导致胴体开裂迅速扩大。
Φ4 m×56 m回转窑大齿圈裂纹的处理

Φ4 m×56 m回转窑大齿圈裂纹的处理
廖炳坤;李德清;王福华
【期刊名称】《新世纪水泥导报》
【年(卷),期】2009(015)006
【摘要】@@ 1 存在问题rn广西鱼峰水泥股份有限公司1号线Φ4 m×56 m回转窑于2002年1月投产使用,到2005年7月开始发现大齿圈腹板出现多处裂纹,其中弹簧板支撑销轴孔部位有三处相当严重.经仔细检查发现大齿圈在铸造时就存在多处铸造缺陷(裂纹),经补焊处理后加工出厂,造成部件内应力没有完全消除,导致在使用过程中继续出现裂纹,并不断扩散恶化.
【总页数】2页(P68-69)
【作者】廖炳坤;李德清;王福华
【作者单位】广西鱼峰水泥股份有限公司,545008;广西鱼峰水泥股份有限公司,545008;广西鱼峰水泥股份有限公司,545008
【正文语种】中文
【中图分类】TP172.8;TP29
【相关文献】
1.回转窑大齿圈振动的处理 [J], 徐英民;马力;单绍仁;宋卫华;桑波磊
2.回转窑大齿圈齿面的修复 [J], 邓荣娟
3.回转窑大齿圈装置弹簧板连接的修复 [J], 王虎;任国
4.回转窑大齿圈及小齿轮轴密封改造 [J], 王学忠; 李宝树; 尚亚宁; 杨小强
5.回转窑传动大齿圈振动分析及处理方法 [J], 李少康
因版权原因,仅展示原文概要,查看原文内容请购买。
回转窑筒体裂纹的处理
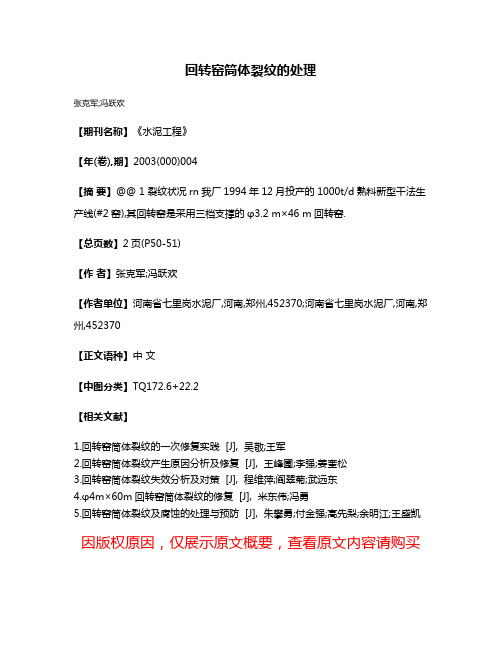
回转窑筒体裂纹的处理
张克军;冯跃欢
【期刊名称】《水泥工程》
【年(卷),期】2003(000)004
【摘要】@@ 1裂纹状况rn我厂1994年12月投产的1000t/d熟料新型干法生产线(#2窑),其回转窑是采用三档支撑的φ3.2 m×46 m回转窑.
【总页数】2页(P50-51)
【作者】张克军;冯跃欢
【作者单位】河南省七里岗水泥厂,河南,郑州,452370;河南省七里岗水泥厂,河南,郑州,452370
【正文语种】中文
【中图分类】TQ172.6+22.2
【相关文献】
1.回转窑筒体裂纹的一次修复实践 [J], 吴敬;王军
2.回转窑筒体裂纹产生原因分析及修复 [J], 王峰圃;李强;姜奎松
3.回转窑筒体裂纹失效分析及对策 [J], 程维萍;阎翠菊;武远东
4.φ4m×60m回转窑筒体裂纹的修复 [J], 米东伟;冯勇
5.回转窑筒体裂纹及腐蚀的处理与预防 [J], 朱攀勇;付金强;高先梨;余明江;王盛凯因版权原因,仅展示原文概要,查看原文内容请购买。
回转窑筒体开裂的修复

回转窑筒体开裂的修复
王宗璞
【期刊名称】《中国水泥》
【年(卷),期】2016(000)007
【摘要】博爱金隅水泥有限公司2 500t/d熟料水泥生产线2006年2月份投产,回转窑的年实际产能均在设计生产能力的110%~115%。
2013年年终大修停产冷窑后,发现在窑长度的居中(距窑头窑尾约30 000mm处)的烧成带与过渡带交汇区2号轮带处筒体加厚段往窑尾向轴向排列有三道环向裂缝和若干道磨蚀沟。
1大窑筒体裂缝及磨蚀情况1.1开裂及磨蚀区域我公司回转窑筒体为φ4m×60m,材质为Q235-B,钢板厚度为22~60mm,其开裂及磨蚀区域见图1、图2。
【总页数】2页(P89-90)
【作者】王宗璞
【作者单位】博爱金隅水泥有限公司,河南焦作454461
【正文语种】中文
【中图分类】TQ172.622.24
【相关文献】
1.回转窑筒体局部变形挖补修复
2.回转窑筒体开裂质量事故分析与修复
3.回转窑筒体开裂原因分析
4.回转窑筒体开裂的修复
5.回转窑筒体开裂的影响因素探讨及性能分析
因版权原因,仅展示原文概要,查看原文内容请购买。
- 1、下载文档前请自行甄别文档内容的完整性,平台不提供额外的编辑、内容补充、找答案等附加服务。
- 2、"仅部分预览"的文档,不可在线预览部分如存在完整性等问题,可反馈申请退款(可完整预览的文档不适用该条件!)。
- 3、如文档侵犯您的权益,请联系客服反馈,我们会尽快为您处理(人工客服工作时间:9:00-18:30)。
3处 理步骤
a
直观 图
A^ - 剖面围
( )停 窑 、冷 窑 ,大齿 圈 裂 纹 打磨 处 理 ,钻 1
止裂孔 。
加 固后使 用 至今 快两年 时间 ,原大 齿 圈裂纹 未见严
重恶化扩散 ,设备运转平稳 , 明处理效果较好 , 说 同时节 省 了更 换 新大齿 圈所需 的 巨额 费用及 较长 的
更换 时 间 。
( 收稿 日期 :20 — 2 1 0 9 0 — 9)
69
( )安装 大齿 圈罩壳 。 9
1存 在 问题
广 西鱼峰水 泥股 份有 限公 司 l 号线 4m×5 6m 回转 窑于20 年 1 02 月投 产使 用 ,到20 年7 开始 发 05 月 现大齿 圈腹板 出现 多处裂 纹 ,其 中弹 簧板支 撑销轴 孔部位 有三处 相 当严 重 。经仔 细检查 发现大 齿 圈在 铸造 时就存 在多处 铸造缺 陷 ( 纹 ),经补 焊处 理 裂
第一次4o M, 0 N 第二次8o l, 0 N l 第三次1 0 M,以 V 0 2 N 便在拧紧丝杆后焊接各连接板 ,最终拆除各丝杆后 在连接板内预留一定的预应力 。 ( 在焊接连接板 ( 9 件 ) ,两侧采用 5) 共 6 时 连续焊接 ,焊接长度约10m 5 m,高度约1 m。为 5m
( 2)拆 除 窑 中大 齿 圈 罩 壳 ,测 量 大 齿 圈 径 向、轴 向跳 动情况 和传动 大 小齿 轮 啮合顶 隙及侧 隙
( 圆周均分测量 8 个点 )。
( 3)传 动 大齿 圈 腹板 工 艺 孔 ( 4 )内孔 打 2孔
磨 ,轴套 (4 ) 2件 外径与孔相配加工后与孔焊接 。
l20k, 间 ;二 次风 温一 般在 1 0 0 g之 l 0℃ 左 右 ,最 0
状 不受 控 ,煤 粉燃烧 速 度慢 ,火 焰 长 ,烧 成带 热力
高1 5 0℃ ;回转窑尾部易结厚窑皮 ,从大齿圈 0 至 窑尾 ,简 体 温 度 有 时仅 10 ℃ ,常 常 造 成 窑 尾 0 漏料 ,被迫减产 ,烧成带末端易结后 圈 ,伴 随着 大 球 ,造 成 熟 料 破 碎 机 口堵 塞 多 次 ,被 迫停 窑 处 理 ,熟料产量徘徊在2 0 d 0/ 7 t 左右 。
提 高 回 转 窑 产 质 量 的 措 施
成忠 贤 江西锦 溪水 泥有限公 司 (3 3 3 330 )
1存在 的 问题
2 原 因分析
. 江西锦溪水泥有限公司新型干法生产线 ( 主机 21 煤风 机选 型偏 大 规格 见表 1 )于20 年 9 0 5 月投 产 ,l月达标 。但 2 0 0 06 煤风机设计风量为 280 320m/,送煤罗 0 ~ 0 。 h 年7 以前 ,窑系统运行状况不太理想。喷煤管拢 茨 风机 实 际 风量 4l6m/。 由于煤风 量过 大 ,煤 月 1 3 h 风 出口速度高 ,内外风调节作用几乎失效 ,火焰形 焰 罩磨 损 很 快 ;熟 料 立升 重 偏 低 ,一般 在 110~ 0
后加工出厂,造成部件内应力没有完全消除,导致
在使 用过程 中继续 出现裂纹 ,并 不断扩 散恶化 。
2处理 方案
方案 1 :更 换新 的大 齿 圈 。费用 高 ,周 期 长 , 而生 产不允许长 时 间停机 。 方案2 :大齿 圈裂 纹 焊接 加 固 。直 接 把 大齿 圈
裂纹处打磨后焊接加固,技术难度大,焊接变形难 以控 制 ,风 险大。 方案3 :大 齿 圈裂 纹处 理 加 固 。大 齿 圈 裂纹 打
4m 5 x 6m回转窑大齿圈裂纹的处理
廖炳坤 李德清 王福华 广西鱼峰水泥股份有限公 司 (40 8 5 50 )
() 7 连接板 (6 ) 9件 与加 固板焊接。 ( 8)拆 除 各 丝杆 与 支 座 ,再 次 测量 大 齿 圈径 向 、轴 向跳动情况和传动大小齿轮啮合 顶隙及侧 隙,检查核对前后各数据有无变化。
见 图l 。
b剖 面 图
图1大齿 圈裂纹处理加固
( 4)安 装加 固板 ( 8 圈 ( 4 )等拧紧 。 2套
1 大 齿 圈 ;2 加 固板 ;3 轴 套 ;4 垫 圈 ;5 连接 螺 一 - - - 一
母 ;6 连接螺栓 ;7 连接板. - -
表 1主 机 规 格 表
强度偏低 ,从而造成升重偏低 ;二次风温不高 ,由 于 煤 风 出 口速 度高 ,外 风起 不 到包裹 作用 ,煤 粉 冲 刷拢焰罩,造成拢焰罩很快磨损。
22煤 的不 正常 燃烧 .
设备名称
规格性能
公司采用北方烟煤 ( ) 表2 与本地无烟煤搭配 使用 ,各 1 ,人窑煤粉控制指标见表3 / 3 。对无烟煤 而 言 ,细 度 ≤8 %,控 制 指 标偏 粗 ,在 烧 成 带是 来
( 3)大齿 圈腹 板 工 艺孔 ( 4 )内孑 与轴 套 2孔 L
加热、烘干 ,预热 ̄20o并保温约1 。 J C 15 h 渣。 () 4 各加固板之间用丝杆 ( 4 , 8 ) M 2 共4件 拉 5 效果 紧,要求用扭力板手拧紧 ( 力矩约1 0 N ,各丝 0 M) 2 我公 司 1 号线 O4m×5 6m回转 窑大齿 圈裂纹 于 杆拉力要均匀, 并对称拧紧,分三次逐渐加大扭力 , 20 年3 0 7 月处理加 固过程 中各数据测量变化不大 ,
2 0 年 第6 09 期
N0 6 2 0 . 0 9
新世 纪水 泥导 报
Ce e tGuie f w o h m n d orNe Ep c 驺 之谈
中图分类号 :T 7 . 22 Q126 . 2 6
文献标识码 :B
文章 编号 :10 —4 32 0 )60 6 —2 0 80 7 (0 90 —0 90
( 5)沿连接板 拉力 方 向在加 固板 上焊接 调 4 处理技 术要 求 整各加 固板间拉力的丝杆支座 ( 6 ),用丝杆 9件 ( )大 齿 圈 的轴 向 跳动 允许 偏 差 为 15Im, 1 .T l ( 4) M 2 拧紧,要求用扭力板手拧紧。 径 向跳 动允许 偏差为 O 5ml . r。 7 l ( 6)再 次测 量 大 齿 圈径 向 、轴 向跳 动情 况 和 ( )大 小 齿 轮 的 齿 顶 间 隙 应 在 82 2 .5mm 传动大小齿轮啮合顶隙及侧隙 ,检查核对前后各数 9 51T . I 范围内;侧隙应在 1 2I 2 TI I . l 21 m 9 T m~ . m 范围 7 据 有无变 化 ,若变 化较大 则需要进 行相应 调整 。 内。
不及充分燃烧的 ,粗颗粒无烟煤被带到窑尾继续燃 烧 ,导致尾 温 偏高 ,同时煤 粉粗 ,造 成人 窑物 料温 度 高 ,也促 进 液相 过早 出现 。上 半年 雨季 ,煤 粉水 分 有 时达25 . %,也影 响 了煤粉 的正 常燃烧 。 23烟 室7. 热 器 出口未安装 气体 分析仪 _ tC预
2 0 年 第6 09 期
N 6 o. 2 0 09
新 世 纪水 泥导报
Cemen i orNe Ep c tGudef w o h 鼯 之该
中 图 分类 号 :T 128 T 2 P 7 .; P 9
文 献标 识 码 :B
文 章 编 号 : 10 —4 32 0 )60 6 -2 0 80 7(0 90 —0 80
分 解炉 T F型 中5 0 D 0 6
篦冷机 T 一 14 篦床面积 6.r ( C 16 , 1 2 净面积 ) 2n
高温风机 W6 2 0 O 3 . ,风量 4000 — ×3N . 1 F 5 6 / 0mh
I : }
}
.
主
_
减小变形 ,采用对称交替焊接 ,即焊好一面后 ,再 (4 ) 2 件 外径间隙配合后焊接 ,要求沿连接板拉力 转到对称面焊接 ,从中间往两侧施焊 ,焊角高度上 方 向左 右两 侧段 焊 ,焊 缝 高度 约 1 0mm,上下 方 向 下4 。左右 ,不宜上下不均或焊脚过高 ,以免应力 5 不焊接 。因大齿圈材质为3CN 3 o 5 riM ,轴套材质为 集 中产 生不 良后 果 。焊接 速度 要 均匀 ,避 免过快 或 Q 3 一 ,故采用56 25A 0 焊条焊接,并且焊条必须事先 过 慢 ,不 得 有 裂 纹 或 夹 渣 ,做 到 边 焊 接 边 敲 打 清
为 了节省 投 资 ,烟 室及 C预热 器 出 口没有 安装 气体分析仪 ,窑炉用风量全靠经验。投产初期 ,三
回转窑 4mx 0m,转速 0 9 —3 6 /i , 6 . 6 . r n 主电机 3 5 3 9r a 1 k 预热器
C :2 47 0;C : 1 66 0 C : 1 6 8 0 l 一 0 2 - 0 ; 3 - 0 ; C : 1 68 0 4 一 0 ; : 1 70 0 - 0