风电用树脂 文档
风电叶片环氧树脂
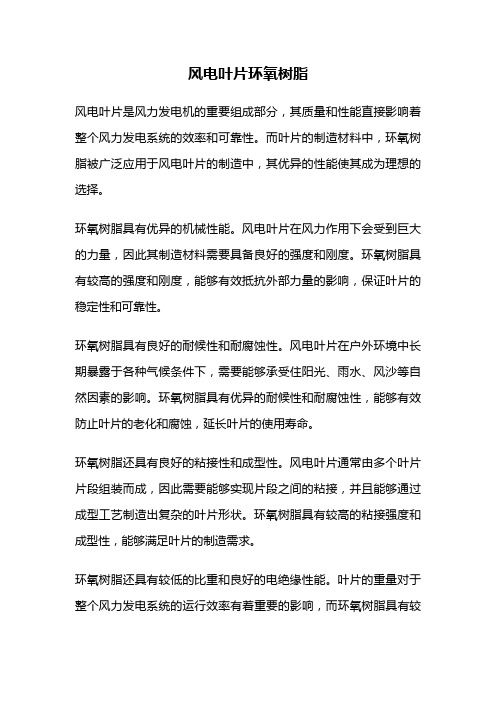
风电叶片环氧树脂风电叶片是风力发电机的重要组成部分,其质量和性能直接影响着整个风力发电系统的效率和可靠性。
而叶片的制造材料中,环氧树脂被广泛应用于风电叶片的制造中,其优异的性能使其成为理想的选择。
环氧树脂具有优异的机械性能。
风电叶片在风力作用下会受到巨大的力量,因此其制造材料需要具备良好的强度和刚度。
环氧树脂具有较高的强度和刚度,能够有效抵抗外部力量的影响,保证叶片的稳定性和可靠性。
环氧树脂具有良好的耐候性和耐腐蚀性。
风电叶片在户外环境中长期暴露于各种气候条件下,需要能够承受住阳光、雨水、风沙等自然因素的影响。
环氧树脂具有优异的耐候性和耐腐蚀性,能够有效防止叶片的老化和腐蚀,延长叶片的使用寿命。
环氧树脂还具有良好的粘接性和成型性。
风电叶片通常由多个叶片片段组装而成,因此需要能够实现片段之间的粘接,并且能够通过成型工艺制造出复杂的叶片形状。
环氧树脂具有较高的粘接强度和成型性,能够满足叶片的制造需求。
环氧树脂还具有较低的比重和良好的电绝缘性能。
叶片的重量对于整个风力发电系统的运行效率有着重要的影响,而环氧树脂具有较低的比重,能够有效减轻叶片的重量,提高系统的效率。
同时,环氧树脂具有良好的电绝缘性能,能够保证叶片在工作过程中的安全可靠性。
然而,风电叶片环氧树脂也存在一些问题。
首先,环氧树脂的制造过程需要高温硬化,对于能源消耗和环境污染有一定的影响。
其次,环氧树脂在长期使用中可能会出现老化和疲劳现象,需要进行定期维护和更换。
风电叶片环氧树脂在风力发电系统中起着重要的作用。
其优异的机械性能、耐候性和耐腐蚀性,以及良好的粘接性和成型性,使其成为理想的叶片制造材料。
然而,环氧树脂的制造和使用也存在一些问题,需要进一步研究和改进。
随着风力发电技术的不断发展,相信风电叶片环氧树脂将会迎来更加广阔的应用前景。
环氧树脂在风电上的应用

环氧树脂在风电上的应用嘿,朋友!想象一下这样一个场景:在广阔无垠的原野上,巨大的风力发电机像巨人一样矗立着,叶片在风中呼呼地转动。
你有没有想过,是什么让这些大家伙能够如此稳定、持久地工作呢?这其中,环氧树脂可发挥了大作用!咱先来说说这风力发电机的工作环境。
那可真是够“残酷”的!一会儿狂风呼啸,一会儿日晒雨淋,还有那温差变化,就跟小孩的脸似的,说变就变。
在这样恶劣的条件下,要保证发电机的各个部件牢固可靠,可不是一件容易的事儿。
这时候,环氧树脂就闪亮登场啦!它就像一个超级“黏合剂”,把各种关键部件紧紧地粘在一起。
比如说叶片,那可是直接承受风力的重要部分。
环氧树脂能够让叶片的结构更加稳固,不至于在狂风中“散了架”。
你可能会问,这环氧树脂到底有啥神奇的地方?其实啊,它就像是一个顽强的“卫士”。
具有出色的耐腐蚀性,不管是雨水的侵蚀,还是空气中的各种化学物质,它都能抵挡住,保护着内部的结构。
而且它的强度高,柔韧性也不错,就像一个能屈能伸的“硬汉”。
再看看那些维修工人,他们在对风力发电机进行维护的时候,可少不了和环氧树脂打交道。
他们小心翼翼地将环氧树脂涂抹在需要的地方,那认真的劲儿,仿佛在对待一件珍贵的宝贝。
一边干活还一边念叨着:“这环氧树脂可得涂好咯,要不然这大风一刮,可就出大问题啦!”还有那些研发人员,为了让环氧树脂在风电上发挥出更好的作用,那可是绞尽了脑汁。
不断地试验、改进,就像是在雕琢一件精美的艺术品。
你想想,如果没有环氧树脂,这风力发电机能这么稳稳当当地给我们发电吗?估计早就被这恶劣的环境折腾得“罢工”啦!所以说啊,环氧树脂在风电领域的应用那可真是至关重要。
它就像是幕后的英雄,默默守护着风力发电的正常运行,为我们的生活带来源源不断的清洁能源。
有了它,咱们才能享受着这清洁、便利的电力,让生活变得更加美好!。
风电叶片用真空导入环氧树脂的标准
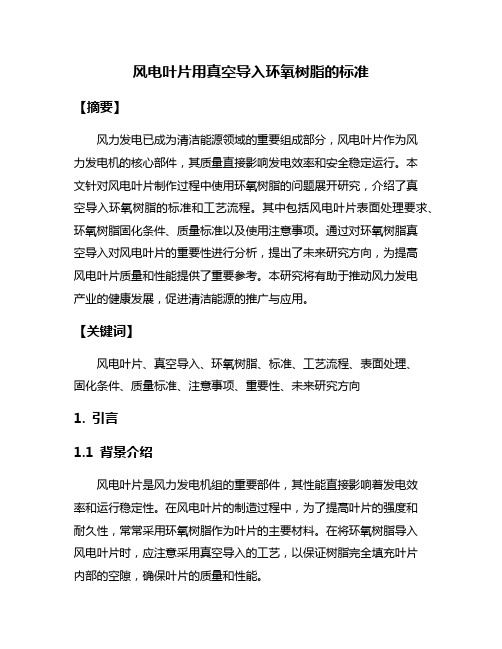
风电叶片用真空导入环氧树脂的标准【摘要】风力发电已成为清洁能源领域的重要组成部分,风电叶片作为风力发电机的核心部件,其质量直接影响发电效率和安全稳定运行。
本文针对风电叶片制作过程中使用环氧树脂的问题展开研究,介绍了真空导入环氧树脂的标准和工艺流程。
其中包括风电叶片表面处理要求、环氧树脂固化条件、质量标准以及使用注意事项。
通过对环氧树脂真空导入对风电叶片的重要性进行分析,提出了未来研究方向,为提高风电叶片质量和性能提供了重要参考。
本研究将有助于推动风力发电产业的健康发展,促进清洁能源的推广与应用。
【关键词】风电叶片、真空导入、环氧树脂、标准、工艺流程、表面处理、固化条件、质量标准、注意事项、重要性、未来研究方向1. 引言1.1 背景介绍风电叶片是风力发电机组的重要部件,其性能直接影响着发电效率和运行稳定性。
在风电叶片的制造过程中,为了提高叶片的强度和耐久性,常常采用环氧树脂作为叶片的主要材料。
在将环氧树脂导入风电叶片时,应注意采用真空导入的工艺,以保证树脂完全填充叶片内部的空隙,确保叶片的质量和性能。
随着风力发电技术的不断发展,对风电叶片的要求也越来越高。
为了满足这一需求,研究人员不断探索新的制造工艺和材料,以提高风电叶片的性能和可靠性。
本文旨在探讨风电叶片制造中真空导入环氧树脂的标准,旨在为风力发电行业提供指导,并为未来的研究提供借鉴。
1.2 研究目的本文旨在探讨风电叶片用真空导入环氧树脂的标准,旨在为风电行业提供具体、可操作的指导,确保风电叶片的质量和安全性。
具体研究目的包括:1. 探讨真空导入环氧树脂的工艺流程,确定最佳操作方法;2. 分析风电叶片表面处理要求,确保环氧树脂的附着力和耐久性;3. 研究环氧树脂固化条件,找到最佳的固化参数;4. 制定真空导入环氧树脂的质量标准,为质量监控提供依据;5. 提出风电叶片使用中的注意事项,帮助企业在生产和维护过程中避免问题发生。
通过对以上研究目的的实现,本文旨在强调环氧树脂真空导入对风电叶片的重要性,并为未来研究提供指导方向。
风力发电机叶片用环氧乙烯基酯树脂
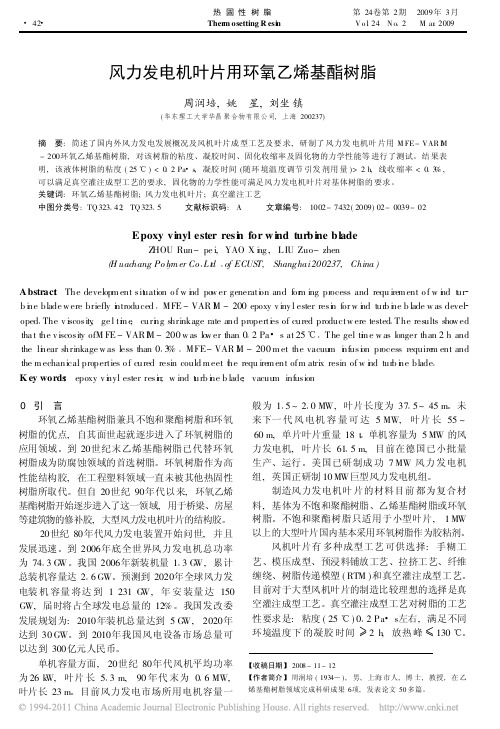
脂线收缩率的测定, 取一定量的树脂 ( 150~ 300 g) 加入 MEKP并搅匀后倒入长 1 000 mm, 30 mm的 半圆柱钢模具中, 待完全固化 (需放置 7~ 14 d) 后 测量其线收缩率。
1 1 1 原材料 主要原材料: 甲基丙烯酸、 E - 51环氧树脂和
苯乙烯均为市 售工业品; 扩链 剂富马酸双酯 为自 制; 阻聚剂对苯二酚、叔丁基对苯二酚和催化剂季 铵盐为市售工业品。 1 1 2 合成工艺
20世纪 80年代风力发电装置开始问世, 并且 发展迅速。到 2006年底全世界风力发电机总功率 为 74 3 GW。我国 2006年新装机量 1 3 GW, 累计 总装机容量达 2 6 GW。预测到 2020年全球风力发 电装 机 容量 将达 到 1 231 GW, 年 安 装量 达 150 GW, 届时将占全球发电总量的 12% 。我国发改委 发展规划为: 2010年装机总量达到 5 GW, 2020年 达到 30 GW。到 2010年我国风电设备市场总量可 以达到 300亿元人民币。
制造风力发电机叶 片的材料目前 都为复合材 料, 基体为不饱和聚酯树脂、乙烯基酯树脂或环氧 树脂。不饱和聚酯树脂只适用于小型叶片, 1 MW 以上的大型叶片国内基本采用环氧树脂作为胶粘剂。
环氧树脂体系在风力机中的应用、回收与更新

树脂成型工艺的要求 。 密封膜和脱模膜都是喷射在室温
品产生无光表面 。 该剂具有阻燃 、 无气味 、 快干 、 固化的特性 。 快 ‘ 芯 材 近来常州天晨新材料股份有限公司研制成 结构泡沫芯材 注 ,以乙烯基聚合物为
基础 , 具有芳香酞胺聚合网络修正的刚性交联结构 , 刚度 、 强度 、 抗疲劳性和抗冲击性都优 良 , 耐多种化学物质 , 几乎不吸水 , 隔音 、 隔热 可与多种纤维复合结构加工成芯材 叶片的结构泡沫芯材 、 夹芯复合材料 。 其性能达到国际先进水平 , 通过 了
国劳埃德认证 , 共 同供应欧洲市场 同时也使
德国
田 公司是欧洲领先的环氧树脂制造商 , 其产品有 普通环氧树脂 、 龙 特种环氧树脂 如 双酚
环氧 树脂 和各种活性稀释剂 。 ‘目前 公司提供的叶片用双组分环氧树脂有 两种浸渍 环氧树脂 , 一种层压环氧树脂 。 ‘ 乙烯基醋树脂 长度达 始湿强度 。 层压板里的 或 ℃ 含量 的粘度较低 室温 公司和 一 公 司 加工叶片的厚度 一巧 , 。 跟环氧树脂相 比它的优点有 ① 物料 如 叶
,
以 度 印 风力机叶 片的 复合 材料
“ 国 我 年
一
年的增长率约
’, 。 随着风力机 、 树脂生产实践和科技的发展 , 环氧复合材料除了
广泛用于加工叶片外 , 还加工叶片的模具和机舱罩 、 驱动轴 , 新近还出现了用 于修复叶片的 新趋势 , 等等 , 不一而足 — 真可谓不可或缺 、 用途广矣
环氧椰 旨 的物料则达
②固化性能较好 , 初
尤佳 。应该指出 , 湿强度对长条形复合材料制品
片、 结构件
很关键 。因为该制品必须经受住
℃ 的后固化工艺 要求快速提高到最大 ℃ 的高温环境里暴露 一 。该树脂能快
风电叶片用环氧树脂的研究

风电叶片用环氧树脂的研究陈诚杜明兵孙富安何明阳陈群(江苏工业学院江苏省精细石油化工重点实验室,常州213164)摘要:以BPA环氧树脂、BPF环氧树脂为基体树脂,1,4-丁二醇二缩水甘油醚为稀释剂,配制出可用于风电叶片的复合型环氧树脂。
考察了不同的原料配比与力学性能的关系,并采用Statistica6·0统计软件对配方进行优化。
研究结果表明:当BPA树脂:稀释剂=13·5(质量比),BPA树脂:BPF树脂=1·6(质量比),树脂固化物冲击强度为88·00KJ·m-2,拉伸强度为68·52MPa,弯曲强度为88·20MPa,其性能接近进口树脂。
关键词:复合材料,环氧树脂,风电叶片,力学性能风力发电是重要的洁净能源,其开发利用受到世界各国越来越多的重视。
当今,风力发电向大功率、长叶片方向发展,更加凸显出叶片材料的重要性。
纤维增强环氧树脂复合材料和真空辅助浸渗技术以其效率高、成本低、质量好的优点,成为生产大型叶片时材料和工艺的主流方向。
真空辅助浸渗技术制备风力发电转子叶片的关键是优选浸渗用的基体树脂,特别要保证树脂的最佳黏度及其流动特殊性[1-2]。
目前国外用于真空辅助浸渗技术的树脂主要有Shell公司、3M公司、HEXION公司、荷兰DSM高等复合材料中心等企业的产品[3-6]。
国内风电叶片制造业的环氧树脂基本依靠进口,这在很大程度上制约了风电业在国内的发展。
本文选用BPA环氧树脂、BPF环氧树脂和活性稀释剂的混合物为基体树脂,以RIMH237为固化剂,在降低树脂黏度的同时保持较好的力学性能,研制出满足真空辅助浸渗工艺的风电叶片用复合型环氧树脂。
1实验部分1·1原料双酚A环氧树脂1460,环氧值0·52,蓝星材料无锡树脂厂;双酚F环氧树脂,自制,环氧值0·59;黏度,1100mPa·s;环氧稀释剂1,4-丁二醇二缩水甘油醚,自制,环氧值0·69。
国外风力发电用环氧树脂

· 19 ·综 述国外风力发电用环氧树脂(二)董永祺(建材情报所, 北京)摘 要本文简要介绍了国外风力发电用环氧树脂,即纤维/环氧树脂加工的产品:叶片、叶片胶衣、胶粘剂、风电机驱动轴和风电场高大、移动式风能测试塔。
介绍了采用的缘由、概况和实例。
关键词:风力发电 环氧树脂 复合材料 叶片 胶衣 胶粘剂1 叶片实例M11、M11.5牌环氧树脂(Hexcel Composites 公司研制)原用于加工预浸料,低温固化,低放热性(固化温度比原先的低)120℃、2~4 h 固化;或者80℃、4~6h 固化。
多层GF 、CF 增强该树脂层压板的固化性能好,而且层压板内因不同热膨胀系数导致的应力最小,不含敌草隆(diuron )[注],符合欧盟环保法规的要求。
([注]:也即:N-3.4-二氯苯基- N`- N`-二甲基脲) HexPly M9F 牌环氧树脂:用于低压模塑成型叶片,85~150℃固化,符合欧盟环保法规的要求。
Prime 20牌环氧树脂(SP 公司研制):低粘度、用于灌注工艺,固化后产品的机械性能好,约85℃固化,可加工SPRINT 预浸料。
SP 公司其他的环氧树脂适于加工预浸料。
叶片用得最广的Araldite 牌环氧树脂体系(绿色)可加工>40m 的叶片。
它是双组份(即:XD434环氧树脂[黄色]与XD4735标准固化剂[蓝色])的混合物。
二组份混合后呈绿色[1]。
美国Aeromax Corp 研制成静音(“stealth-acoustic”)1kw 风电机(安装于居民区),采用模压成型CF/环氧树脂叶片,即使叶轮高速运转时,CF/环氧树脂材料也能降低叶轮的旋转惯性,从而使叶轮平滑运行、轻声[3]。
又讯:英国Qinetiq 公司与NOI Scotland Ltd 合作研制成GF/树脂吸波叶片。
该GF/树脂具有吸收各类宽幅频率的雷达的特性。
又采用了军事的、气流控制、航海、气象监控等技术来干扰乱真(寄生)雷达信号。
风电环氧树脂

风电环氧树脂
风电环氧树脂是一种用于制造风力发电机叶片的特殊树脂。
它是由环氧树脂、填充剂、固化剂等材料混合而成的复合材料,具有优异的机械性能和耐久性。
在风力发电机叶片制造中,使用环氧树脂可以增强叶片的强度、刚度和耐久性,从而提高整个风力发电机的效率和寿命。
风电环氧树脂具有以下特点:
1.高强度:风电环氧树脂具有很高的强度和刚度,可以增强叶片的承载能力和抗风压能力,从而提高风力发电机的效率。
2.优良的耐久性:风力发电机经过长时间的使用和自然环境的影响,环氧树脂可以保持其优良的物理性能和化学性能,不易老化和开裂。
3.良好的成型性能:风电环氧树脂可以通过注塑、压模、层压等多种成型工艺进行加工,可以制造出各种形状和尺寸的叶片。
4.环保性:风电环氧树脂是一种绿色环保材料,不含有害物质,对环境没有污染。
目前,国内外许多企业都在积极研发和生产风电环氧树脂,以满足风力发电机叶片制造的需求。
未来,随着风力发电行业的不断发展和壮大,风电环氧树脂的市场前景将会越来越广阔。
- 1 -。
国外风力发电用环氧树脂_一_
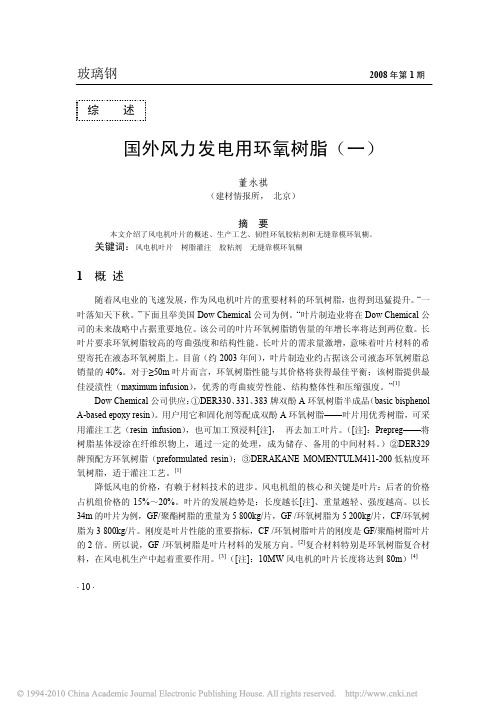
玻璃钢2008年第1期综 述国外风力发电用环氧树脂(一)董永祺(建材情报所,北京)摘要本文介绍了风电机叶片的概述、生产工艺、韧性环氧胶粘剂和无缝靠模环氧糊。
关键词:风电机叶片树脂灌注胶粘剂无缝靠模环氧糊1 概述随着风电业的飞速发展,作为风电机叶片的重要材料的环氧树脂,也得到迅猛提升。
“一叶落知天下秋。
”下面且举美国Dow Chemical公司为例。
“叶片制造业将在Dow Chemical公司的未来战略中占据重要地位。
该公司的叶片环氧树脂销售量的年增长率将达到两位数。
长叶片要求环氧树脂较高的弯曲强度和结构性能。
长叶片的需求量激增,意味着叶片材料的希望寄托在液态环氧树脂上。
目前(约2003年间),叶片制造业约占据该公司液态环氧树脂总销量的40%。
对于≥50m叶片而言,环氧树脂性能与其价格将获得最佳平衡;该树脂提供最佳浸渍性(maximum infusion),优秀的弯曲疲劳性能、结构整体性和压缩强度。
”[1]①、331、383牌双酚A环氧树脂半成品(basic bisphenolDow Chemical公司供应:DER330A-based epoxy resin)。
用户用它和固化剂等配成双酚A环氧树脂——叶片用优秀树脂,可采用灌注工艺(resin infusion),也可加工预浸料[注],再去加工叶片。
([注]:Prepreg——将②树脂基体浸涂在纤维织物上,通过一定的处理,成为储存、备用的中间材料。
)DER329③-200低粘度环牌预配方环氧树脂(preformulated resin);DERAKANE MOMENTULM411氧树脂,适于灌注工艺。
[1]降低风电的价格,有赖于材料技术的进步。
风电机组的核心和关键是叶片:后者的价格占机组价格的15%~20%。
叶片的发展趋势是:长度越长[注]、重量越轻、强度越高。
以长34m的叶片为例,GF/聚酯树脂的重量为5 800kg/片,GF /环氧树脂为5 200kg/片,CF/环氧树脂为3 800kg/片。
风电叶片材料(免费)
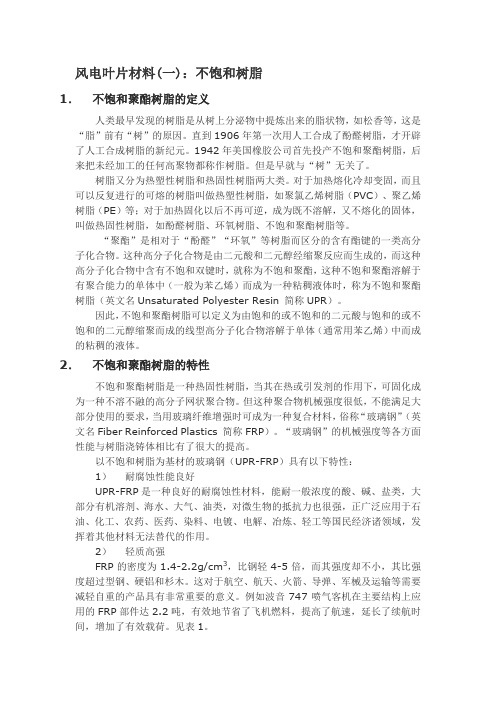
风电叶片材料(一):不饱和树脂1.不饱和聚酯树脂的定义人类最早发现的树脂是从树上分泌物中提炼出来的脂状物,如松香等,这是“脂”前有“树”的原因。
直到1906年第一次用人工合成了酚醛树脂,才开辟了人工合成树脂的新纪元。
1942年美国橡胶公司首先投产不饱和聚酯树脂,后来把未经加工的任何高聚物都称作树脂。
但是早就与“树”无关了。
树脂又分为热塑性树脂和热固性树脂两大类。
对于加热熔化冷却变固,而且可以反复进行的可熔的树脂叫做热塑性树脂,如聚氯乙烯树脂(PVC)、聚乙烯树脂(PE)等;对于加热固化以后不再可逆,成为既不溶解,又不熔化的固体,叫做热固性树脂,如酚醛树脂、环氧树脂、不饱和聚酯树脂等。
“聚酯”是相对于“酚醛”“环氧”等树脂而区分的含有酯键的一类高分子化合物。
这种高分子化合物是由二元酸和二元醇经缩聚反应而生成的,而这种高分子化合物中含有不饱和双键时,就称为不饱和聚酯,这种不饱和聚酯溶解于有聚合能力的单体中(一般为苯乙烯)而成为一种粘稠液体时,称为不饱和聚酯树脂(英文名Unsaturated Polyester Resin 简称UPR)。
因此,不饱和聚酯树脂可以定义为由饱和的或不饱和的二元酸与饱和的或不饱和的二元醇缩聚而成的线型高分子化合物溶解于单体(通常用苯乙烯)中而成的粘稠的液体。
2.不饱和聚酯树脂的特性不饱和聚酯树脂是一种热固性树脂,当其在热或引发剂的作用下,可固化成为一种不溶不融的高分子网状聚合物。
但这种聚合物机械强度很低,不能满足大部分使用的要求,当用玻璃纤维增强时可成为一种复合材料,俗称“玻璃钢”(英文名Fiber Reinforced Plastics 简称FRP)。
“玻璃钢”的机械强度等各方面性能与树脂浇铸体相比有了很大的提高。
以不饱和树脂为基材的玻璃钢(UPR-FRP)具有以下特性:1)耐腐蚀性能良好UPR-FRP是一种良好的耐腐蚀性材料,能耐一般浓度的酸、碱、盐类,大部分有机溶剂、海水、大气、油类,对微生物的抵抗力也很强,正广泛应用于石油、化工、农药、医药、染料、电镀、电解、冶炼、轻工等国民经济诸领域,发挥着其他材料无法替代的作用。
风电环氧树脂工艺性能研究分析

树脂
时间
温度
并且,对于低黏度环氧树脂体系的最佳工艺窗口的最大黏度不同文献之间也存在 较大差异,从300mPa ·s ~ 800mPa·s不等。据。
5
5、风电环氧树脂工艺性能研究 本研究对DQ230E/DQ234H风电叶片用真空灌注环氧树脂体系的分析为例,用
两种不同的方法来研究风电环氧树脂的工艺性能。 第一种方法是:简单的黏度等高线判断方法; 第二种方法是:通过流变学的方法模拟环氧树脂黏度、灌注流速、灌注流动距离
越慢。由s=v×t可知,t=x时灌注树脂的流动距离s(T,x)的表达式为:
将 公式(1)、(6)代入公式(7)可得:
18
将公式(2)、(3)代入公式(8),我们就可以得出DQ230E/DQ234H灌注树脂的流动
公式(1)中参数a和b均为温度T的函数,参照双Arrhenius公式分别对a、T和b、T
进行拟合,找出拟合公式所对应的各参数如表2所示。
14
表2 a和b对T的拟合公式与参数值
拟合公式 m n R2
拟合公式 u v w R2
a(T)=m+n/T -20.55 7725.44 0.99392
b(T)=u/T+v×exp(w/T) -0.1765
2.4347×106 -5885.1571
0.99967
从表2中可以看出,使用以下公式进行模拟的调整R2数值均大于0.99,这说明拟 合公式拥有很高的匹配度。
15
将公式(2)、(3)代入公式(1),即可得到灌注树脂体系在等温条件下黏度随时间的 变化关系为:
16
人们常常使用达西定律来描述多孔介质中流体的流动性,该定律也同样适合用于 描述灌注环氧树脂体系在增强材料中的流动性,其表达式如下:
风电叶片用环氧树脂的固化动力学研究_贾智源

风电叶片用环氧树脂的固化动力学研究贾智源1,2赵俊山1邱桂杰1陈淳1薛忠民1付绍云2(1.中材科技风电叶片股份有限公司,北京102101;2.中国科学院理化技术研究所,北京100190)摘要通过差式扫描量热仪(DSC)进行非等温实验,研究了风电叶片生产用环氧树脂的固化过程,分析表明:该固化反应为多种反应共存的复杂反应,采用唯像法模型拟合确定其反应动力学方程为dαd t=1.141ˑ105exp-6655.87()T(1-α)0.897。
若树脂体系固化时处于恒温状态,则此反应动力学方程的解为α=1-1-1.175ˑ104t exp-6655.87() []T 9.7,明确了固化度与时间和温度之间的关系。
这一研究为风电叶片用环氧树脂的固化工艺优化提供了理论基础。
关键词差式扫描量热;环氧树脂;固化动力学当前国内大型风电叶片的生产中,主要采用适合于低成本、大制件制作的真空辅助树脂传递模塑工艺(VARTM)。
这一工艺多采用具有固化温度低、黏度小的环氧树脂作为基体材料闭模成型,具有成型效率高与环境污染小的优点[1]。
因而,近年来发展的比较迅速,广泛应用于航空航天、汽车以及风电等各个领域。
风电叶片作为大型复合材料制件,其生产周期和基本性能与树脂的固化过程紧密相关。
在树脂和固化剂体系确定的前提下,选取适当的固化工艺条件以缩短固化周期,并获得具有适用力学性能的复合材料的研究对获得低成本高质量的叶片产品显得尤为重要。
树脂的固化反应动力学可以确定树脂的反应速率与温度和固化程度之间的关系,是优化树脂固化工艺较为直接有效的方法[2]。
本文对风电叶片生产用环氧树脂的固化动力学进行了研究,以期确定最佳的固化工艺条件。
1实验1.1主要原材料MGS RIM135环氧树脂和MGS RIMH137固化剂,均为工业品,美国瀚森公司生产。
1.2测试方法和仪器采用美国TA公司的Q20型差式扫描量热仪以不同的升温速率1ħ/min、2ħ/min、4ħ/min、8ħ/min、16ħ/min分别对组成固定的树脂体系进行动态变温扫描。
风电叶片用双酚A型及双酚AF型环氧树脂复合材料性能研究

风电叶片用双酚A型及双酚A/F型环氧树脂复合材料性能研究*冯学斌1** ,周娟1,彭超义1, 2,曾竟成1, 2,唐先贺11 株洲时代新材料科技股份有限公司,湖南株洲4120072 国防科技大学航天与材料工程学院,湖南长沙410073摘要:对比研究风电叶片用双酚A型及双酚A/ F型两种环氧树脂材料体系。
对树脂体系力学性能、工艺性能进行考察,进一步通过真空灌注工艺制备玻璃纤维复合材料并测试。
结果表明,双酚A/ F型环氧树脂与双酚A型环氧树脂比较,材料具有更佳的冲击及疲劳性能。
关键词:环氧树脂;复合材料;风电叶片Study on the Properties of Bisphenol A and Bisphenol A/F Epoxy Resin Composites Used to Wind Turbine BladesFengxuebin1, Zhoujuan1, Pengchaoyi1, 2, Zengjingcheng1, 2, Tangxianhe11 Zhuzhou Times New Material Technology Co., Ltd., Hunan Zhuzhou, 4120072 College of Aerospace and Materials Engineering, National University of Defense Technology, Hunan Changsha410073Abstract: The two kinds of epoxy resins used to wind turbine blades, included Bisphenol A and Bisphenol A/F epoxy resins, were researched. The mechanical properties and process properties of the materials were compared, and the fibre reinforced epoxy resins composites prepared by the vacuum infusion process were tested. The results indicated that Bisphenol A/F epoxy resins have the higher impact and fatigue properties, compared with the Bisphenol A epoxy resins.Keywords: Epoxy Resin; Composites;Wind Turbine Blades引言:风力发电是一种广受各国高度关注的清洁、可再生能源,我国风电产业近年来以100%以上的速度迅猛发展,对风电设备有着巨大需求[1, 2]。
5mw和10mw风电叶片树脂材料用量

5mw和10mw风电叶片树脂材料用量
风力发电是一种清洁、可再生的能源形式,而风电叶片是风力发电机组中非常
重要的组成部分。
风电叶片的制造材料对于风力发电机组的性能和寿命具有重要影响。
在风电叶片的制造过程中,树脂材料是其中不可或缺的一部分。
5mw和10mw风电叶片的树脂材料用量是制造风电叶片时需要考虑的重要因素之一。
树脂材料主要用于制造风电叶片的外壳,它需要具有一定的强度、耐磨性和耐腐蚀性,以确保风电叶片在恶劣气候条件下能够正常工作。
对于5mw和10mw风电叶片的树脂材料用量,一般会根据具体的风电叶片设
计和制造工艺来确定。
一般来说,5mw风电叶片相对较小,树脂用量会相对较少;而10mw风电叶片相对较大,树脂用量会相应增加。
树脂用量的确定还受到叶片的形状、尺寸、材料特性以及生产工艺的影响。
在制造5mw和10mw风电叶片时,通常会根据叶片的设计要求和材料特性进
行树脂材料用量的计算。
树脂材料的用量需要考虑到叶片的整体结构和性能要求,以及树脂的特性和制造工艺的实际情况。
除了树脂材料的用量,还需要考虑到树脂的固化过程、成型工艺和后续的质量
检测等因素。
树脂材料的用量对于风电叶片的质量和性能有着重要的影响,合理的树脂用量可以提高风电叶片的耐久性和可靠性。
总的来说,5mw和10mw风电叶片的树脂材料用量是一个综合考量的过程,需要根据具体的叶片设计和制造工艺来确定。
合理的树脂用量可以提高风电叶片的性能和寿命,从而提高整个风力发电系统的效率和可靠性。
风电叶片用真空导入环氧树脂-最新国标
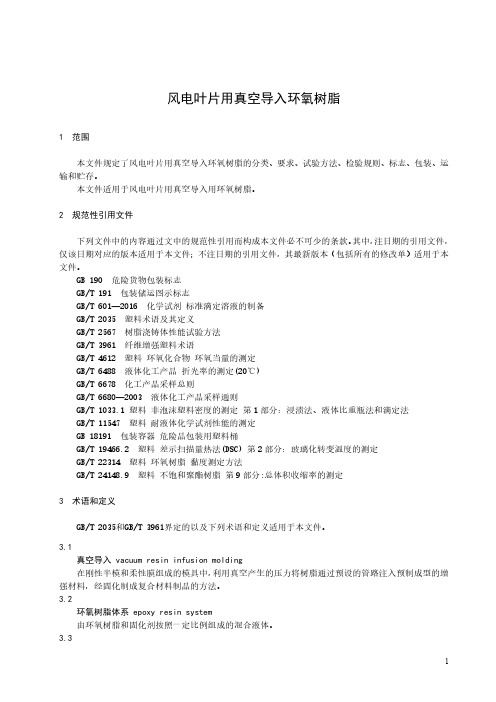
风电叶片用真空导入环氧树脂1范围本文件规定了风电叶片用真空导入环氧树脂的分类、要求、试验方法、检验规则、标志、包装、运输和贮存。
本文件适用于风电叶片用真空导入用环氧树脂。
2规范性引用文件下列文件中的内容通过文中的规范性引用而构成本文件必不可少的条款。
其中,注日期的引用文件,仅该日期对应的版本适用于本文件;不注日期的引用文件,其最新版本(包括所有的修改单)适用于本文件。
GB190危险货物包装标志GB/T191包装储运图示标志GB/T601—2016化学试剂标准滴定溶液的制备GB/T2035塑料术语及其定义GB/T2567树脂浇铸体性能试验方法GB/T3961纤维增强塑料术语GB/T4612塑料环氧化合物环氧当量的测定GB/T6488液体化工产品折光率的测定(20℃)GB/T6678化工产品采样总则GB/T6680—2003液体化工产品采样通则GB/T1033.1塑料非泡沫塑料密度的测定第1部分:浸渍法、液体比重瓶法和滴定法GB/T11547塑料耐液体化学试剂性能的测定GB18191包装容器危险品包装用塑料桶GB/T19466.2塑料差示扫描量热法(DSC)第2部分:玻璃化转变温度的测定GB/T22314塑料环氧树脂黏度测定方法GB/T24148.9塑料不饱和聚酯树脂第9部分:总体积收缩率的测定3术语和定义GB/T2035和GB/T3961界定的以及下列术语和定义适用于本文件。
3.1真空导入vacuum resin infusion molding在刚性半模和柔性膜组成的模具中,利用真空产生的压力将树脂通过预设的管路注入预制成型的增强材料,经固化制成复合材料制品的方法。
3.2环氧树脂体系epoxy resin system由环氧树脂和固化剂按照一定比例组成的混合液体。
3.3初始混合黏度initial mixed viscosity环氧树脂和固化剂按照一定比例在一定温度下持续混合一定时间测得的黏度。
3.4适用期applicable time环氧树脂和固化剂按照一定比例混合,35℃下混合黏度达到1000mPa.s时的时间。
- 1、下载文档前请自行甄别文档内容的完整性,平台不提供额外的编辑、内容补充、找答案等附加服务。
- 2、"仅部分预览"的文档,不可在线预览部分如存在完整性等问题,可反馈申请退款(可完整预览的文档不适用该条件!)。
- 3、如文档侵犯您的权益,请联系客服反馈,我们会尽快为您处理(人工客服工作时间:9:00-18:30)。
一、国内外风电叶片的主要生产企业:
外资企业主要以维斯塔斯、GE、艾尔姆(LM)、哥美飒(GAMESA)为代表。
丹麦LM Glasfiber A/S是一个世界上领头的风力机叶片制造商,并且是唯一以全球基础运营的供应商。
LM公司活跃在所有主要的风能市场上,在全球8个国家建有生产厂,具有在亚洲(印度有两个厂,中国有两个厂)、北美洲和欧洲可扩展的生产能力。
LM公司在乌鲁木齐、天津和秦皇岛建立了艾尔姆玻璃纤维制造品有限公司,全球目前运行的风力机,每3台风力机就有一台配装该公司的叶片。
其生产的目前世界上最大的风电叶片长61.5米,采用了玻纤/碳纤维混杂复合材料结构,在横梁和翼缘等要求较高的部位使用碳纤维作为增强材料,单片叶片质量达17.7 t。
国内企业以中航惠腾、中复连众、中材科技为代表。
国内企业的市场份额占到70%,这其中,大部分都是三家巨头的份额。
叶片的发展历程
二、国内风电叶片企业用树脂的现状
我国兆瓦级玻璃钢风电叶片技术大都是从德国和荷兰引进,叶片的叶形设计、结构设计、铺层设计、材料设计、模具技术到叶片制造是一个系统工程,对纤维和树脂有特定要求,并经过德国船级社GL认证。
国内叶片技术市场上,主要是德国Aerodyn技术和荷兰CTC技术。
无论是那一国的叶片技术,都经历了
将近十年的风场考验,并通过GL论证。
德国、丹麦、西班牙、挪威等国成功的叶片制造技术也相应带动了一批玻璃钢原材料企业。
目前进入我国风电市场的环氧、不饱和聚酯树脂企业有亨斯迈、汉森、长濑、DOW、巴斯夫、亚什兰、DSM、DIC和昭和等。
国内目前的环氧树脂用于风电叶片还存在一些问题,企业对风电叶片所需环氧树脂研究不足,短期内还无法完成技术攻关。
因此,当前叶片厂商生产所需的环氧树脂,绝大部分都是进口。
三、叶片用树脂的性能要求及其改进方法
风机叶片要承受强风载荷、砂粒冲刷、紫外线照射、大气氧化与腐蚀等外界因素的作用。
为了提高复合材料叶片的承载能力、耐腐蚀和耐冲刷等性能,必须对树脂基体系统进行精心设计和改进。
性能优异的专用风能环氧树脂代可以改善玻璃纤维/树脂界面的粘结性能,从而提高叶片的承载能力,扩大玻璃纤维在大型叶片中的应用范围。
同时,为了提高复合材料叶片在恶劣工作环境中长期使用性能,还需要开发耐紫外线辐射的新型环氧树脂系统。
GL风力机认证要求风力机叶片设计寿命在3000h/a全载荷下为20年。
作为一个对比,以20rpm的速度运行20年相当于一辆轿车行驶总里程35万公里(以平均轮胎的尺寸计算),这样也远远超过目前轿车的寿命要求。
此外,风力机叶片白天黑夜运转,有时是在极其恶劣的气候环境下(-40~50℃和7000T变化/年)。
所以叶片的可靠性是该产业重要的参数,这并不令人感到惊讶。
具体的性能要求如下:
1)风力机叶片韧性改善
疲劳试验后,复合材料层合板典型的破坏有微裂纹,甚至纤维剥离,如图所示,该图显示了手工层合板试样疲劳试验后的情况。
这些缺陷可以使用增韧技术有效解决。
塑料基体的增韧已是一个有几十年之久的难题。
在很早时期,使用增塑剂改善材料的脆性,虽然它能降低材料的机械和化学强度。
而且,增塑剂不是固定在树脂基体中,间久了会迁移,这必然改变材料的性能。
对于风力机叶片而言,由于其较长使用寿命要求在二十年内材料性能不改变,这种方法可能并不合适。
除增塑剂之外,也可通过松驰树脂网状结构达到在基体主链中增塑的效果。
然而,即使增塑是建立在基体里,不利的影响仍然存在。
松弛的网状结构明显地降低了玻璃化转变温度(Tg)。
真正的增韧是在橡胶材料如端羧基丁腈液体橡胶(CTBN)的出现才得以实现,这种增韧剂在保持Tg不变的同时改善脆裂性能。
不过,CTBN确实提高了环氧树脂基体的粘度,至少对灌注技术而言,它似乎形成了一些障碍。
后来在纳米核壳橡胶增韧上的努力解决了这个多余的粘度增加,但因为预分散颗粒,粘度仍然是一个问题。
新的增韧技术是以一种嵌段共聚物为基础。
它仅仅在固化的环氧树脂中形成第二相。
这种橡胶第二相使固化体系在裂纹发生前能吸收更多能量。
达到这种效果的关键是控制第二相的颗粒大小、多分散性和界面强度。
仅仅在固化体系中形成第二相是不够的,因为第二相的尺寸、形状以及和基体之间的相互作用也很重要。
一个嵌段是“憎环氧”,即不能与环氧基体混合,而其他嵌段是“亲环氧”,也就是很容易与环氧基体混合。
当这种嵌段共聚物加入系统,憎环氧嵌段自己崩塌形成第二相(就像油在水中一样),而亲环氧嵌段包围着憎环氧嵌段,使之稳定地悬浮在基体中。
这种自组装过程的优点在于需要较少的材料就可达到所需的韧性。
改性的和未改性的试样拥有相同的刚度,改性或增韧系统已提高了延伸率,应力/应变曲线下方的面积增加了。
根据定义,应力应变曲线下方的面积就是韧性。
第二增韧相能阻止微裂纹的传播。
图片显示了在第二相中裂纹是如何被终止的。
这种形变能够吸收裂纹的能量。
当增韧作用在第二相发生时,Tg保持不变。
下图展示两种不同的性能:断裂韧
性和玻璃化转变温度。
结果显示,嵌段共聚物能够在不改变玻璃化转变温度下改善断裂韧性。
但这如何转换成抗疲劳数据呢?为了解答这个问题,Dow公司以常规疲劳试验方案对嵌段共聚物增韧进行了测试。
这个研究显示了在风能上应用嵌段共聚物增韧技术,复合材料抗疲劳性能显著提高。
Dow公司使用的嵌段共聚物增韧技术是基于一种完全混合、低粘度材料,它最适合用于风能应用中最常见的树脂灌注成型工艺(RIM)。
由于材料完全溶解在液态基体中,这样就没有传统颗粒增韧所带来的过滤效应。
第二相在固化和提供增韧作用时才会分离,即材料灌注后。
这是一个非常显著的改善,包含了风力机叶片制造中另一个重要的需求:提高生产率。
2)提高生产率
面对风力发电不断增长的需求,制造商正提高生产率来增加产量。
根据推算,在2020年,每三分钟生产一片新叶片才可以满足需求。
这样大的产量只有优化制造周期和最大效率才可能实现。
可靠性和生产率这两项指标将降低每kWh电能的成本,而这正是风电产业和其他能源产业竞争所需要的。
简单地说,就是要缩短周期,同时保持高质量来延长复合材料叶片的寿命。
当前市场需求是基于工艺要求,如较低的放热量,较长的使用时限以及快速固化反应。
针对这种情况,Dow公司开发了新的AIRSTONE灌注线,它提供了可调整的使用时限,以适用于现今和将来灌注超大型叶片的最高要求。
但是,这
就增加了对一种相对潜伏性环氧系统的需求,它将显示在灌注期间粘度并无明显增加。
这种需求似乎与快速固化反应相抵触,相对于快速灌注,快速固化最终可以更多地缩短周期。
Dow公司设法在不同温度下优化反应速率,以便在较高温度下的固化速度超过传统的灌注系统。
最终,如果固化反应较好,叶片就能够得到更好的固化均匀度。
不考虑自加热的作用,更快地在叶片的所有部分达到玻璃化转变温度,将缩短固化时间。
最后,超过90℃的玻璃转变温度将可能取决于固化条件。
以这种方式,Dow公司在风电产业提高生产率的要求上已经做出了很大的贡献。
采用基于环氧树脂和固化剂的巴斯夫Baxxodur双组分系统可显著提高大型风机叶片的生产能力。
为确保叶片模具被完全且快速地填充,巴斯夫系统初始反应速度较慢,然后通过加热提高固化速度,以便更快地脱模,开始生产下一个叶片。
由此风机叶片的生产周期可缩短达30%,提高了生产效率。
不仅如此,与传统产品相比,这些新系统的加工温度范围更宽,因此工艺也更加灵活。
3)粘接性能
涂料解决方案具有高耐候性(抗紫外)、灵活性和耐摩擦等特点。
该系统由凝胶涂层、底漆、特殊边缘保护产品和外涂层组成。
通过完善的服务与培训、灵活的应用方法(滚刷/喷涂),涂料解决方案可帮助客户降低生产过程的成本。
通过使用高性能的双组分聚氨酯,这些产品不含任何溶剂,并为全球可再生能源做出重要贡献。