货油舱特涂施工工艺
油轮特涂工艺(Marine_line_America)中英文版
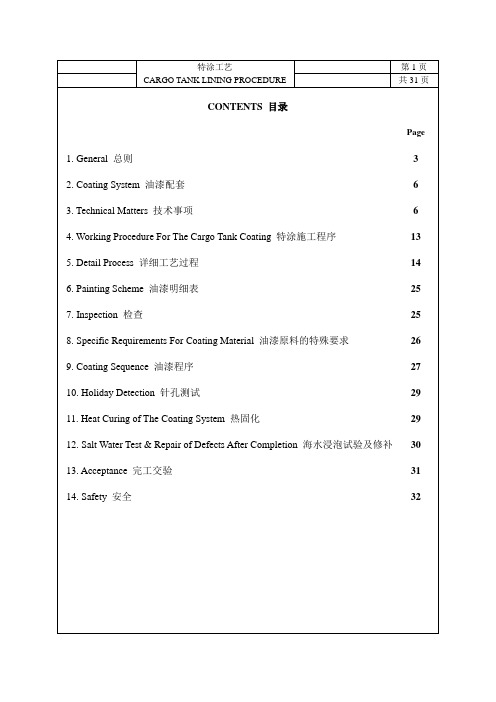
1.2 Tank coating shall be carried out after the completion of hot work in the tanks and adjacent areas and tank testing. 在舱内和舱体(六面体)周围火工作业结束及检查通过以后进行特涂施工。 1.3 Tank coating procedure shall be decided in accordance with the builder’s practice, paint manufacturer’s recommendation and owner’s final approval. 特涂工艺的制定要遵照施工方的惯例和涂料制造商的建议并经船东认可。 1.4 Surface preparation and coating shall be carried out after the erection and the completion of outfitting works. 表面预处理和油漆必须在上船台(或下坞)和舾装工作结束以后进行。 1.5 Any misapplied shop primer or other coating shall be completely removed during the secondary surface preparation. 任何误涂的车间底漆或其它油漆必须在二次除锈过程中清除。 1.6 This Coating Procedure shall together with the MarineLINE Application Procedure be the only valid documents for all parties involved in the tank coating operation. 本特涂工艺结合 Marine Line 施工工艺作为从事本特涂作业各方的唯一有效工艺文件。 1.7 The tank coating materials shall be stored, mixed, applied and cured in strict observance of the requirements and recommendations of the coating manufacturer, the MarineLINE Application Procedure, the Specification and this Coating Procedure. 本特涂油漆的贮存、 混合、 涂覆和固化必须严格遵守涂料制造商的要求和建议, 按照 MarineLINE 施工工艺、技术规格书和本特涂工艺进行。
船舶涂装工艺流程图
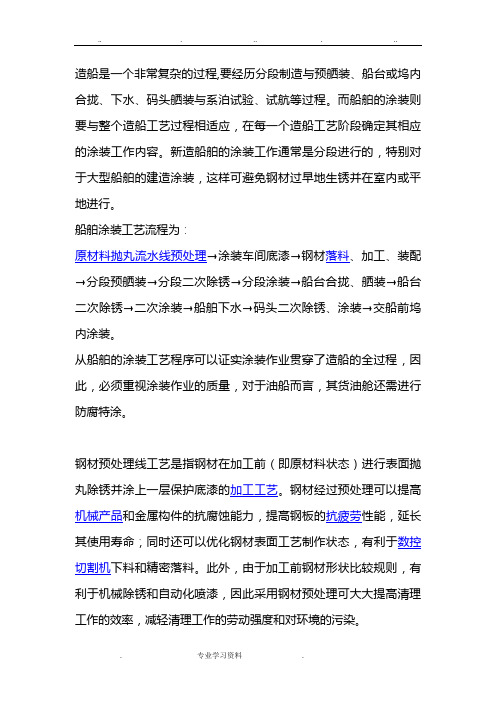
造船是一个非常复杂的过程,要经历分段制造与预舾装、船台或坞内合拢、下水、码头舾装与系泊试验、试航等过程。
而船舶的涂装则要与整个造船工艺过程相适应,在每一个造船工艺阶段确定其相应的涂装工作内容。
新造船舶的涂装工作通常是分段进行的,特别对于大型船舶的建造涂装,这样可避免钢材过早地生锈并在室内或平地进行。
船舶涂装工艺流程为:原材料抛丸流水线预处理→涂装车间底漆→钢材落料、加工、装配→分段预舾装→分段二次除锈→分段涂装→船台合拢、舾装→船台二次除锈→二次涂装→船舶下水→码头二次除锈、涂装→交船前坞内涂装。
从船舶的涂装工艺程序可以证实涂装作业贯穿了造船的全过程,因此,必须重视涂装作业的质量,对于油船而言,其货油舱还需进行防腐特涂。
钢材预处理线工艺是指钢材在加工前(即原材料状态)进行表面抛丸除锈并涂上一层保护底漆的加工工艺。
钢材经过预处理可以提高机械产品和金属构件的抗腐蚀能力,提高钢板的抗疲劳性能,延长其使用寿命;同时还可以优化钢材表面工艺制作状态,有利于数控切割机下料和精密落料。
此外,由于加工前钢材形状比较规则,有利于机械除锈和自动化喷漆,因此采用钢材预处理可大大提高清理工作的效率,减轻清理工作的劳动强度和对环境的污染。
钢材预处理的重要性作用是1矫正变形;2.抛丸除锈;3.作底漆防腐船底、水线、船壳、上层建筑、压载水舱、饮用水/清水舱、货舱、耐热部位、锚链舱、甲板重防腐涂料:它的英文名称为healy-dudy coutury,指相对常规防腐涂料而言,能在相对苛刻腐蚀环境里应用,并具有能达到比常规防腐涂料更长保护期的一类防腐涂料。
①能在苛刻条件下使用,并具有长效防腐寿命,重防腐涂料在化工大气和海洋环境里,一般可使用10年或15年以上,即使在酸、碱、盐和溶剂介质里,并在一定温度条件下,也能使用5年以上。
②厚膜化是重防腐涂料的重要标志。
一般防腐涂料的涂层干膜厚度为100μm或150μm左右,而重防腐涂料干膜厚度则在200μm或300μm以上,还有500μm~1000μm,甚至高达2000μm。
化学品舱内部特种涂装施工工艺

一、主要内容与适用范围本工艺规定了化学品舱内部(含污油舱)特种涂装的施工工艺流程, 以及生产准备、现场勘查、搭设脚手架、安排施工设备、钢材表面的预处理、舱内温湿度的控制和测量、喷砂、清洁、喷漆、拆除脚手架、海水试验等施工要求。
二、引用标准A.ISO 8501-1:1988 涂装前钢材表面锈蚀等级和除锈等级。
B.GB7692-1987涂装作业安全规程,涂装前处理工艺安全。
C.CB/T3367-1992成品油轮货油舱涂装工艺技术条件。
D.CB/T3718-1995船舶涂装膜厚检测要求。
三、特涂工艺流程见随附“特涂工艺流程”图。
四、对工艺流程中关键步骤的说明1、准备工作1)明确该船的特涂区域以及相邻部位的钢结构和舾装件安装工作确已结束,并经船东代表和油漆代表检验合格(应有书面确认);2)确定喷砂的面积。
3)熟悉该船所涂油漆的技术性能、施工要求、估算油漆总用量。
4)根据喷砂面积及要求达到的标准等级,确定磨料的用量、硬度、含盐量、含水量等要求,与磨料厂商取得联系,每次购砂需要向厂商索取质检报告并抽查检测。
5)确定脚手架的用量(钢管、连接扣件、脚手板、铅丝及其它包扎物品等)。
根据要求的施工周期,制定初步的特涂施工计划。
6)根据计划安排喷砂枪、空压机、去湿机、吸砂机、喷漆泵、风机和加热器等设备和材料的需要量;提出电力、供水等的需求量。
7)确定搭架、喷砂、清洁、预涂装、喷漆等工人数。
8)开工前应召开各工种负责人和领班会议,明确安全、质量和环境保护等各项要求,确保工程顺利进行。
2、现场勘查1)了解舱内情况(舱容、面积、结构、钢板表面锈蚀状况), 并做好记录。
2)了解甲板情况, 布置设备放置的位置。
3)了解码头情况, 以及码头的吊运、动力源布置等情况。
3、搭设脚手架及安全检查1)脚手架搭设标准a. 脚手架应整体稳固,保障工作人员能够顺利到达任何施工表面,同时不妨碍涂装、通风和照明。
每层高度一般1.9m左右, 每个舱要搭几层则由该船的总高度来确定。
货油舱特涂工艺th
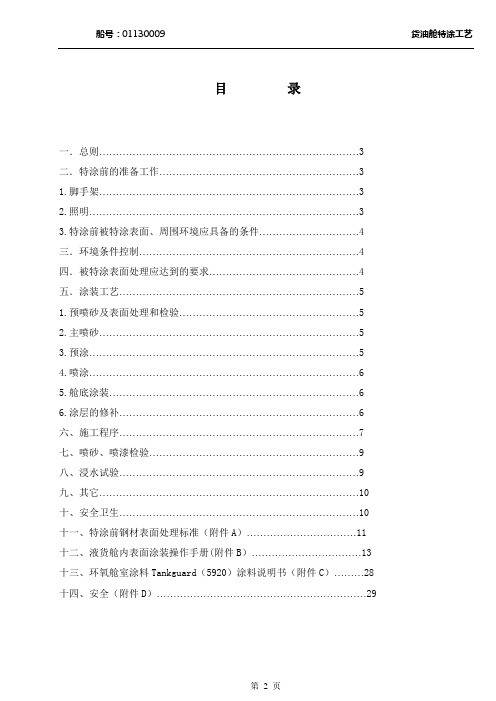
目录一.总则 (3)二.特涂前的准备工作 (3)1.脚手架 (3)2.照明 (3)3.特涂前被特涂表面、周围环境应具备的条件 (4)三.环境条件控制 (4)四.被特涂表面处理应达到的要求 (4)五.涂装工艺 (5)1.预喷砂及表面处理和检验 (5)2.主喷砂 (5)3.预涂 (5)4.喷涂 (6)5.舱底涂装 (6)6.涂层的修补 (6)六、施工程序 (7)七、喷砂、喷漆检验 (9)八、浸水试验 (9)九、其它 (10)十、安全卫生 (10)十一、特涂前钢材表面处理标准(附件A) (11)十二、液货舱内表面涂装操作手册(附件B) (13)十三、环氧舱室涂料Tankguard(5920)涂料说明书(附件C) (28)十四、安全(附件D) (29)一、总则1.本工艺规程中提到的货油舱包括污油水舱。
2.本工艺规程编制依据:广船国际兴顺公司与International paint company有限公司(以下简称IP)签订的《特涂技术协议》、《液货舱内表面涂装操作手册》;货油舱特涂检验标准及产品说明书;3.本工艺规程适用范围:特涂施工范围:NO.1P/S货油舱、NO.2P/S货油舱、NO.3P/S货油舱、NO.4 P/S货油舱、NO.5 P/S货油舱、NO.6P/S货油舱、Residual tank共13个特涂舱。
#主甲板集油槽?#货油管内外?#舱内的不锈钢如何处理?4.本工艺规程中规定的技术要求不能随意改变。
如果需要变动,船厂代表需与船方代表、IP代表共同协商,三方达成协议后方可改动。
6.本工艺规程中没有规定的事项应由船厂代表与船东代表、IP代表共同协商确定。
二、特涂前的准备工作1.脚手架1.1 脚手架吊板应为网状结构式以利于通风及清洁,在搭设脚手架时必须将所有管子的管口及架板的管子端口封堵,防止砂尘污染涂层表面1.2脚手架的任何部位距离被涂装表面的最小距离约300mm左右,行走通道的脚手板宽度应在630mm以上,使施工人员容易而安全地接近所要涂装的表面。
船舶涂装通用工艺
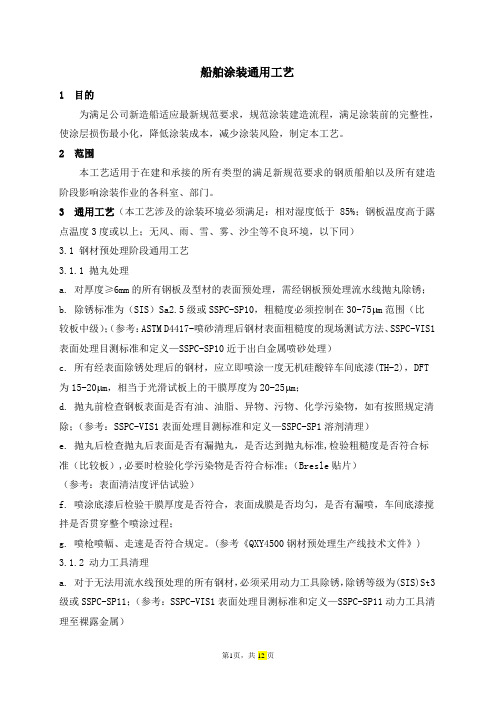
船舶涂装通用工艺1目的为满足公司新造船适应最新规范要求,规范涂装建造流程,满足涂装前的完整性,使涂层损伤最小化,降低涂装成本,减少涂装风险,制定本工艺。
2 范围本工艺适用于在建和承接的所有类型的满足新规范要求的钢质船舶以及所有建造阶段影响涂装作业的各科室、部门。
3 通用工艺(本工艺涉及的涂装环境必须满足:相对湿度低于85%;钢板温度高于露点温度3度或以上;无风、雨、雪、雾、沙尘等不良环境,以下同)3.1 钢材预处理阶段通用工艺3.1.1 抛丸处理a. 对厚度≥6mm的所有钢板及型材的表面预处理,需经钢板预处理流水线抛丸除锈;b. 除锈标准为(SIS)Sa2.5级或SSPC-SP10,粗糙度必须控制在30-75μm范围(比较板中级);(参考:ASTM D4417-喷砂清理后钢材表面粗糙度的现场测试方法、SSPC-VIS1表面处理目测标准和定义—SSPC-SP10近于出白金属喷砂处理)c.所有经表面除锈处理后的钢材,应立即喷涂一度无机硅酸锌车间底漆(TH-2),DFT 为15-20μm,相当于光滑试板上的干膜厚度为20-25μm;d. 抛丸前检查钢板表面是否有油、油脂、异物、污物、化学污染物,如有按照规定清除;(参考:SSPC-VIS1表面处理目测标准和定义—SSPC-SP1溶剂清理)e.抛丸后检查抛丸后表面是否有漏抛丸,是否达到抛丸标准,检验粗糙度是否符合标准(比较板),必要时检验化学污染物是否符合标准;(Bresle贴片)(参考:表面清洁度评估试验)f. 喷涂底漆后检验干膜厚度是否符合,表面成膜是否均匀,是否有漏喷,车间底漆搅拌是否贯穿整个喷涂过程;g.喷枪喷幅、走速是否符合规定。
(参考《QXY4500钢材预处理生产线技术文件》)3.1.2 动力工具清理a.对于无法用流水线预处理的所有钢材,必须采用动力工具除锈,除锈等级为(SIS)St3 级或SSPC-SP11;(参考:SSPC-VIS1表面处理目测标准和定义—SSPC-SP11动力工具清理至裸露金属)b. 动力工具处理前检查钢板表面是否有油、油脂、异物、污物、化学污染物,如有按照规定清除;(参考:SSPC-VIS1表面处理目测标准和定义—SSPC-SP1溶剂清理)c.动力工具处理后检查待涂表面是否达到动力工具处理标准,必要时检验化学污染物是否符合标准;(Bresle贴片)d.动力工具处理后的钢材,应立即喷涂一度无机硅酸锌车间底漆(TH-2),DFT为15-20μm,相当于光滑试板上的干膜厚度为20-25μm;e. 喷涂底漆后检验干膜厚度是否符合,表面成膜是否均匀,是否有漏喷,车间底漆搅拌是否贯穿整个喷涂过程。
船舶特涂工艺

1.7 The tank coating materials shall be stored, mixed, applied and cured in strict observance of the requirements and recommendations of the coating manufacturer, the MarineLINE Application Procedure, the Specification and this Coating Procedure. 本特涂油漆的贮存、混合、涂覆和固化必须严格遵守涂料制造商的要求和建议,按照 MarineLINE 施工工艺、技术规格书和本特涂工艺进行。
27
10. Holiday Detection 针孔测试
29
11. Heat Curing of The Coating System 热固化
29
12. Salt Water Test & Repair of Defects After Completion 海水浸泡试验及修补 30
13. Acceptance 完工交验
1.11 Standard safety precautions employed in tank coating operations and local laws relating to all aspects of the work to be performed inside the tanks and their environments, shall be strictly observed and followed. 在舱内及其周围场所施工时,严格遵守特涂作业的安全规范和相关的法律法规。
1.12 Dust and solvents released during tank coating operations are both noxious and explosive. Consequently, proper ventilation must be provided to the tanks during all operations to keep the “Low Explosion Limit” (LEL) below 10%. 特涂施工中产生的粉尘和挥发的溶剂是有害和致爆的,因此,在所有施工过程中必须提供恰当 的通风,保持低于“最低爆炸极限”10%。
成品油船与特涂解析

1、使涂层化学结构致密,能抵御各种装载对象的溶解、 渗透和腐蚀; 2、有优良的耐海水性和耐货物--海水交替装载的性能, 使涂层具有耐热水清洗和耐油品加热的特性。 3、涂层沾上货物或其他污物后,清洗容易,并且涂层应 具有一定的耐热性,以抵抗货物的加热和热水清洗。
船舶涂装技术 6/86
船舶涂装技术 2/86
01:16
成品油船与特涂
一、特殊的装载对象
成品油船的装载对象大致有以下品种。
1、石油精制品 1.1)白色制品 1.2)黑色制品 1.3)润滑油 汽油、煤油、柴油等。 重油、红灯油等。 各类润滑油、机油等。
船舶涂装技术 3/86
01:16
成品油船与特涂
2、石油化学制品: 脂肪烃化合物、芳烃化合物 。 3、化学合成制品: 有机化合物、苛性化合物、酸性化合物。 4、其他油脂类: 动物油、植物油。 5、其他: 蜜糖、果汁、葡萄
三、特殊的施工条件 1、必须在船上作整体涂装 2、必须进行温度和露点的管理 环境露点:是指该环境的温度和相对湿度的条件下,环境温 度若下降到物体表面刚刚开始发生结露时的温度,这一温度既 该环境条件下的露点。
船舶涂装技术 7/86
01:16
成品油船与特涂
四、特殊的表面处理 1、结构性处理
成品油船与特涂
船舶的特殊涂装,通常是指成品油船的货油舱的涂装。
在船舶涂装工艺中,成品油船的特殊涂装技术是船舶涂装的尖 端工艺。
船舶涂装技术 1/86
01:16
成品油船与特涂
成品油船涂装的特殊性
油船:
从广义上讲是指散装运输各种油类的船。除了运输石油 外,装运石油的成品油,各种动植物油,液态的天然气 和石油气等。但是,通常所称的油船,多数是指运输原 油的船。 而装运成品油的船,称为成品油船。
成品油船货油舱特涂净舱技术的研究与制备-国际船舶网

成品油船货油舱特涂净舱技术的研究与制备陈涛(驻大连地区军事代表室,辽宁大连116021)摘要:通过研究成品油船货油舱特涂净舱技术,来掌握化学品船液货舱解决表面处理问题的办法和途径,以保证化学品船液货舱的涂装质量,为延长涂层的使用寿命创造条件,提高了在国内、国际造船市场上的竞争力。
关键词:净舱技术;表面处理;成品油船1引言根据化学品船货舱的表面处理技术要求及相关的表面处理标准,结合成品油轮液货舱净舱技术,通过对影响货舱涂装质量的表面清洁度、盐分及粗糙度等关键因素的研究,提出了解决表面处理问题的办法和途径。
提高了表面清洁度,降低了盐分,保证了粗糙度要求,从而满足表面处理的各项技术标准,解决了困扰船厂特涂施工多年的技术难题,净舱标准符合后续油漆配套(涂层)的要求,从而保证了化学品船货舱涂装质量,为延长涂层的使用寿命创造了条件。
主要研究内容如下:①特涂前钢材表面处理结构缺陷修理工艺的研究;②特涂用磨料的技术指标及选用;③钢材表面粗糙度、清洁度、盐分的检测技术。
为完成本研究,需解决如下关键技术:①液货舱表面盐分的控制;②钢材表面清洁度的控制。
2特涂前钢材表面处理结构缺陷修理工艺的研究特涂前钢材表面结构缺陷修理关系到特涂质量的好坏,它直接影响结构边缘、焊缝、边角等区域的涂层施工质量,经过多方面的技术讨论及论证,根据涂装配套以及船级社和油漆商的建议,对特涂前钢材表面结构缺陷修理进行了详细的规定,形成了标准文件(详见表1),有力地保证了特涂的施工质量。
表1缺陷处理要求表 1 缺陷处理要求3特涂用磨料的技术指标及选用化学品/成品油船货油舱的板材在流水线经过抛丸处理至Sa2.5级后,有的施工了车间底漆,有的并未施工车间底漆,暴露在大气环境下6~8个月,受海洋气候的影响,钢材表面含有较高的盐分,直接影响到液货舱涂层的施工质量。
为控制特涂前钢材表面的盐分,二次表面处理采用的磨料技术指标是影响特涂的关键。
通常液货舱磨料采用非金属磨料(即铜矿砂),完全能够满足特涂要求,其技术指标见表2。
- 1、下载文档前请自行甄别文档内容的完整性,平台不提供额外的编辑、内容补充、找答案等附加服务。
- 2、"仅部分预览"的文档,不可在线预览部分如存在完整性等问题,可反馈申请退款(可完整预览的文档不适用该条件!)。
- 3、如文档侵犯您的权益,请联系客服反馈,我们会尽快为您处理(人工客服工作时间:9:00-18:30)。
Tank Coating Seminar Working Procedure
Jiang Ming
25-04-2008
货油舱施工工艺简介
喷砂前 货油舱上部涂层的检验 脚手架的拆除
货油舱施工工艺简介
货油舱底部涂层的施工及检验 舱底漆膜及甲板管道开口涂层的修补 不锈钢 海水试验 附件 -安全及钢材预处理资料 附件 – 涂料产品说明书
通风及湿度控制(喷砂及油漆施工中)
相对湿度与返锈比率
错误的方法
脚手架/台
脚手架/台
脚手架的搭设应能保证施工人员能安全地到达 任何一个作业面。特别注意脚手架、脚手板不 要接触舱壁表面。脚手架与舱壁之间的距离应 为30 – 60 厘米。脚手架与舱底之间仅限于点接 触。 槽型舱壁必须搭设工作平台,以便施工人员能 安全地到达各个凹面进行表面处理、涂装及检 验工作。 所有脚手架应能做到易于清洁。 喷砂前脚手架钢管两端应用塞子封堵。
货油舱涂料的施工
应按有关涂料配套及产品说明书的要求,将涂料直接喷涂在喷过砂 的舱壁表面。 所有焊缝、型材背面、自由边、过水孔、过焊孔等必须做预涂。预 涂须在两道统喷之间进行。 涂层不能超厚。每道涂层包括预涂都须经过式玛涂料现场服务工程 师的检验,认可后方可进行下道涂料的施工。 配套中每道涂层必须是完整的,并无漆雾、无垂流、无流挂、无漏 涂。上述缺陷必须在涂料的复涂间隔期内、下道涂料施工前处理完 毕。处理此类缺陷所产生的粉尘须用吸尘器清除干净。 配套中每道涂层的复涂间隔时间应严格按照最新产品说明书中的要 求。
喷砂
所有铁锈、氧化皮、杂物及水溶性盐必须彻底去除,以 符合ISO SA2.5级。这也包括完全去除车间底漆。所有 过水孔、过焊孔、减轻孔、舱口内側及型材背面须特别 留意。 舱底脚手架支撑点也须列入喷砂程序。 完成每一个喷砂工序后,应进行清理及喷砂标准检查。 喷砂后的表面粗糙度及表面灰尘吸附状况也须列入检查 范围。 如喷砂质量符合要求,应用硬毛刷、真空吸尘作最后清 洁。 清除脚手架上及舱内设备上残留的磨料。
油漆粘度相对温度变化趋势
viscosity (dPas)
25 20 15 10
5 0
0
Viscosity versus temperature
Series1
10
20
30
40
t (degrees C)
稀释剂需求相对温度变化趋势
% thinner (v)
12 10
8 6 4 2 0
0
temperature/thinner
脚手架/台
采用真空吸尘 将砂粒清除干净! 如果脚手架上有砂粒或灰尘,在喷 漆过程中会被带到钢板表面,这将 会导致今后油漆脱落!!
杂质
钢板
脚手架/台
发生在1998年某压载舱内木制脚手架由于承受了太大的外力而导致断裂
喷砂
喷砂标准为ISO 8501-01。喷漆前最终验收最低标准ISO Sa2.5级。 喷砂后的表面粗糙度(Rz)须符合产品说明书的要求。 喷砂所用矿质磨料应为出厂原装磨料,并不得循环使用。 本程序所指的矿质磨料包括有棱角的铜矿砂、钢丸、金刚砂、硅酸 铝、熔渣及熔渣混合物等等,应能有效地清除钢材表面的锈、锈层 、旧涂层及车间底漆。 符合本程序要求的其它矿质磨料也可使用,但它必须干净、颗粒完 整、坚硬,并不含任何杂质、油脂、有毒物、漆皮、有机物及水溶 性盐。 袋装或散装的磨料,其含水量不得超过0.5%(重量比)。 磨料的水溶性盐的电导率不得超过250 µS/cm (micron Siemens per centimeter)
喷砂前的钢结构表面处理
通风及湿度控制(喷砂及油漆施工中)
承包商须提供足够的通风、加热及除湿设备,以确保在工程的各个 阶段如喷砂、喷漆及固化时,舱内能始终保持如下状态:
通风及湿度控制(喷砂及油漆施工中)
舱内始终保持无结露状态。 钢板温度不得低于产品说明书所规定的最低温度,并必须高于露点 温度3度。 在喷砂及涂装过程中,舱内的相对湿度必须低于80%。(如低于 50%,则喷过砂的表面不易返锈。 在最后一道油漆的施工及固化过程以及修补油漆过程中,舱内须按 产品说明书的要求继续保持良好通风及无结露状态。通风管道须布 置合理以求取得最佳效果,舱内应稍呈正压状态。 在舱口及甲板开口处应设置遮雨棚,以防止雨水、尘埃及其它杂物 进入舱内。 在低温条件下施工时,可通过舱外铺设保温层的方法,使舱内保持 所需的温度(最低固化所需温度见产品说明书)。保温层的铺设与 否取决于舱外温度、除湿机及加热机的数量和功率。
Series1
10
20
30
40
t=(degrees C)
第一度油漆的施工
货油舱涂料的施工
为什么要做预涂?
货油舱涂料的施工
在油漆喷涂时在一些死角或R 孔及自由边等处没法喷到,为达到油漆的膜后 要求在喷漆前或喷漆后需要进行预涂施工
预涂施工部位:
1. 内表面及R 孔 2. 自由边
3. 电焊逢 4. 喷漆时无法喷到的部位
喷砂前的钢结构表面处理
所有锐边要打磨至半径最少为3 毫米的圆角。 清除所有飞溅和焊渣。 所有切割边缘的溶渣须清除干净。 喷砂前任何电焊咬口、气孔须重焊。 所有毛刺应在喷砂前用打磨机磨掉。 开始喷砂之前,舱内及周边相邻部位的烧焊和火工工程必 须完全结束。 所有电焊接地片、接地支架须切除并打磨光顺。 焊缝的突出部分须打磨光顺。 残留在表面的油迹及污物必须清除干净
温湿度控制
除湿机
通风原理示意图
抽风
舱室开口处 进气
AIR
净化舱室空气环境
盐份测试
钢板表面盐份过高
引起油漆表面产生水泡
货油舱涂料的施工
应按有关涂料配套及产品说明书的要求,将涂料直接喷 涂在喷过砂的舱壁表面。 所有焊缝、型材背面、自由边、过水孔、过焊孔等必须 做预涂。预涂须在两道统喷之间进行。 涂层不能超厚。每道涂层包括预涂都须经过式玛涂料现 场服务工程师的检验,认可后方可进行下道涂料的施工 。 配套中每道涂层必须是完整的,并无漆雾、无垂流、无 流挂、无漏涂。上述缺陷必须在涂料的复涂间隔期内、 下道涂料施工前处理完毕。处理此类缺陷所产生的粉尘 须用吸尘器清除干净。