成品油船货油舱特涂净舱技术的研究与制备-国际船舶网
《原油油船货油舱保护涂层性能标准》介绍以及应对措施探讨

郭利雄 : 《 原 油 油 船 货 油 舱保 护涂 层 性 能 标 准 》介 绍 以及 应 对 措 施 探讨
表1 《货油舱 保 护涂层 性 能标 准 》实施 前后 重要 技术 指标 对 比
堑丝
涂层系统
l! 壅 堕堑 垦查
P S P C实 施 后 要 求
1 . 涂 层 系 统 的 设 计
《 原 油油船 货 油舱 保护 涂层 性能 标准 》介绍 以及应 对 措施 探讨
郭利 雄
( 广 船 国 际 兴 顺公 司 )
摘 要: 、 标准 适 用 范 围 、涂装 区域 、基 本 要 求 、检 验 内容 以及替 代 办 法 等方 面 详 细介 绍 了 《 原 油 油船 货 油舱保 护 涂 层 性 能标 准 》 , 以及 结 合压 载 舱 《 保 护 涂层 性 能 标 准 》实施 的经验 ,初 步探 讨 了 《 原 油 油船 货 油舱 保 护涂 层 性 能标 准 》实 施 的应 对
用 区 域
( 1 ) 作 为 最 低 限 度 ,下 列 区 域 须 按 照 《 货 油舱 保护 涂层 性能 标准 》得 到保 护 。 ① 舱 顶 板 及 全部 内部 结 构 ,包 括 与纵 向和 横 向 隔舱 壁 连 接 的 肘 板 。在 具 有 环 框 纵 梁 构 造 的舱 中 , 甲板 下 横 肋 须 涂 装 至 上 面板 之下 的第 一 防挠肘 板 。 ② 纵 向 和横 向隔 舱 壁涂 装 至 最 高 检 验 通 道 的 高 度 。最 高 检 验 通 道 及 其 支 撑 架 全 部 涂装 。 ③ 无 最 高检 验 通 道 的货舱 隔舱 壁 涂 层 延伸 至舱 中线高 度 的1 0 %,但 从 甲板 向 下延 伸无 需超 过3 m。 ④ 内平 底 和 全部 构 件 涂 装 至 内平 底 之
10000DWT成品油轮设计浅析

10000DWT成品油轮设计浅析10000DWT 成品油轮设计浅析摘要:本文对10000DWT 成品油轮的主尺度、性能等作了一些简要的介绍。
就该船的若干主要特点进行了讨论。
对于今后类似船型的设计有一定的参考价值。
关键字:10000DWT;成品油轮; 主尺度;前言10000DWT 成品油船为双底、单甲板、单壳、球首、双尾鳍尾机型油船,设双桨、双舵、柴油机推进,无限航区,装运成品油。
本船按法国船级社《BV钢质海船入级与建选规范》及其“修改通报”、《船舶与海上设施法定检验规则》(非国际航行船舶法定检验技术规则)进行设计。
本文就其总体设计做了一些简述,并对若干细节问题做了探讨,供以后设计类似的船型时参考。
概述船型介绍本船为钢质液货﹑单机单桨单舵油船。
船体采用双层底设计,双层底高度不大于1400mm满足MARPOL 组织对于油轮的相关规定。
船体设左右边舱,其宽度为1000mm,前后设隔离舱。
液货舱型式为整体重力式液货舱,具有带球首的前倾首柱与球尾。
本船为无限航区,经过特殊涂层的货油舱和污油舱可载运清洁与不清洁的石油产品以及原油。
船型介绍总长约为120.76m,垂线间长约为116.00m,设计吃水为6.50m,型宽为19.05m,型深为10.50m,设计吃水为6.50m,结构吃水为7.00m。
主机选用Mak9M32C 系列或者同等的主机类型,最大输出功率为4320kw,最大转速为600rpm.。
螺旋桨为4-5 叶,直径为3600mm,转速为167rpm,螺旋桨的材料为Ni-Al-Bronze 合金。
主发电机一共有三台,规格为 3 Set *550kw*1500rpm,采用三相交流400V,50HZ 制式.应急发电机的规格为1Set*99kw*1500rpm,采用三相交流,400V,50HZ 制式。
满载静深水,风力不超过蒲氏2 级时航速不小于13.8kn/h,续航力:以13.2kn/h 的服务航速时续航力不小于5000 海里。
288(87) 原油油船货油舱保护涂层性能标准(中文)
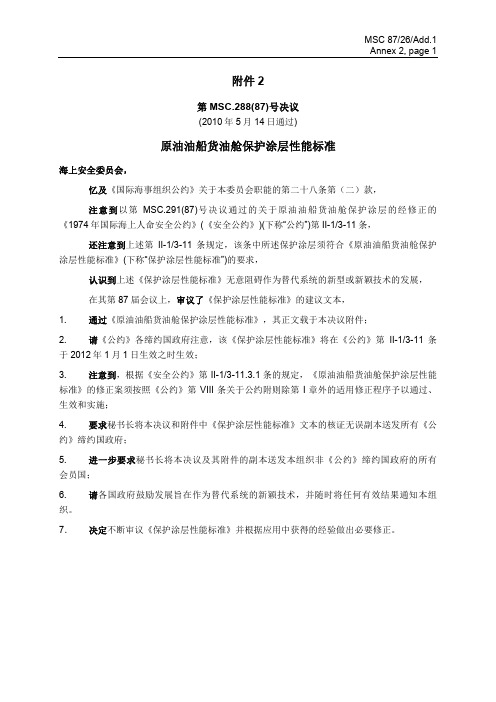
MSC 87/26/Add.1 Annex 2, page 7
特性
要求
.4 工作规范 须至少进行两道预涂和两道喷涂。在证明涂装的涂层能够满足标定总干膜厚 度要求时,可仅在焊缝区减少第二道预涂的范围,以避免不必要的涂层过 厚。任何第二道预涂范围的减少须详细地全部记录在涂层技术档案中。
预涂须采用刷涂或辊涂的方法。辊涂须仅用于排水孔、老鼠洞等部位。
MSC 87/26/Add.1 Annex 2, page 2
附件 原油油船货油舱保护涂层性能标准
1 目的
本标准规定了原油油船建造时货油舱内涂装的保护涂层最低标准的技术要求。
2 定义
下列定义适用于本标准: 2.1 原油油船为《73/78 年防污公约》附则 I 中界定的油船。 2.2 露点为空气中湿度饱和时的温度。 2.3 DFT 为干膜厚度。 2.4 灰尘为呈现在准备涂漆的表面上的、由于喷砂清理或其它表面处理工艺而产生的,或由 于环境作用而产生的松散颗粒性物质。 2.5 边缘打磨系指二次表面处理前对边缘的处理。 2.6 “良好”状况系指评估油船压载舱涂层的第 A.744 (18) 号决议界定的有少量点锈的状况。 2.7 硬涂层系指在固化过程中发生化学变化的涂层或可用于维护目的的非化学变化、在空气 中干燥的涂层。它可以是无机的也可以是有机的。 2.8 NDFT 为标定干膜厚度。90/10 原则系指所有测厚点的 90%测量结果须大于或等于标定 干膜厚度,其余 10%测量结果均须不小于 0.9×标定干膜厚度。 2.9 底漆系指车间底漆涂装后在船厂涂装的涂层系统的第一道涂层。 2.10 车间底漆系指加工前涂在钢板表面的底漆,通常在自动化车间喷涂(在涂层系统第一道 涂层之前)。 2.11 预涂系指对关键区域边缘、焊缝、不易喷涂区域等位置的预先涂刷,以保证良好的涂料 附着力和恰当的涂层厚度。 2.12 目标使用寿命为涂层系统设计寿命的目标值,以年计。 2.13 技术规格书为涂料生产商的产品规格书,包含与涂料及其涂装有关的详细技术性说明和 资料。
成品油船货油舱特涂研究
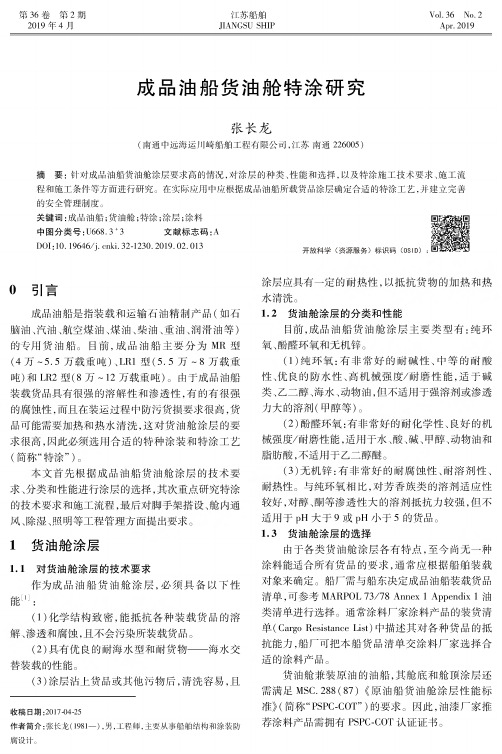
第36卷第2期2019年4月江苏船舶JIANGSU SHIPVol.36No.2Apr.2019成品油船货油舱特涂研究张长龙(南通中远海运川崎船舶工程有限公司,江苏南通226005)摘要:针对成品油船货油舱涂层要求高的情况,对涂层的种类、性能和选择,以及特涂施工技术要求、施工流程和施工条件等方面进行研究。
在实际应用中应根据成品油船所载货品涂层确定合适的特涂工艺,并建立完善的安全管理制度。
关键词:成品油船;货油舱;特涂;涂层;涂料中图分类号:U668.3+6文献标志码:ADOI:15.19646/ki.32-1235.2219.22.519开放科学(资源服务)标识码(OSID)0引言成品油船是指装载和运输石油精制产品(如石脑油、汽油、舟油、煤油、柴油、重油、润滑油等)的专用货油船。
,成品油船主要MR型(4万〜5.3万载重吨)、LR1型(5.3万〜8万载重吨)和LR2型(8万〜12万载重吨)。
由于成品油船装载货品具有很强的溶解性和渗透性,有的有很强的性,而且在装运过程中货损要求很高,货品可能需要和,这对货油舱涂层的要求很高,选用合适的特种涂装和特涂工艺(简称“特涂”)。
根据成品油船货油舱涂层的技术要求、分类和性能进行涂层的选择,研究特涂的技术要求和施工流程,对、舱通风、除湿、照明等工程管理方面要求。
1货油舱涂层1.1对货油舱涂层的技术要求成品油船货油舱涂层,必须具备以下性能⑴:()能总种装载货品的溶、渗和,所装载货品。
(2)具有的耐海和耐货物——海水交替装载的性能。
(6)涂层沾上货品或其他污物后,清洗容易,且收稿日期:2297-04-25作者简介:张长龙(1961―),男,工程师,主要从事船舶结构和涂装防腐设计。
涂层应具有定的性,以货的和O1.1货油舱涂层的分类和性能,成品油船货油舱涂层主要类型有:纯环氧、和。
():有的性、中等的性、优良的性、高强度/耐磨性能,适于碱类、Z、海水、动物油,但不适用于强溶渗透力大的溶剂(甲醇等)。
成品油船货油舱特涂净舱技术的研究与制备-国际船舶网

成品油船货油舱特涂净舱技术的研究与制备陈涛(驻大连地区军事代表室,辽宁大连116021)摘要:通过研究成品油船货油舱特涂净舱技术,来掌握化学品船液货舱解决表面处理问题的办法和途径,以保证化学品船液货舱的涂装质量,为延长涂层的使用寿命创造条件,提高了在国内、国际造船市场上的竞争力。
关键词:净舱技术;表面处理;成品油船1引言根据化学品船货舱的表面处理技术要求及相关的表面处理标准,结合成品油轮液货舱净舱技术,通过对影响货舱涂装质量的表面清洁度、盐分及粗糙度等关键因素的研究,提出了解决表面处理问题的办法和途径。
提高了表面清洁度,降低了盐分,保证了粗糙度要求,从而满足表面处理的各项技术标准,解决了困扰船厂特涂施工多年的技术难题,净舱标准符合后续油漆配套(涂层)的要求,从而保证了化学品船货舱涂装质量,为延长涂层的使用寿命创造了条件。
主要研究内容如下:①特涂前钢材表面处理结构缺陷修理工艺的研究;②特涂用磨料的技术指标及选用;③钢材表面粗糙度、清洁度、盐分的检测技术。
为完成本研究,需解决如下关键技术:①液货舱表面盐分的控制;②钢材表面清洁度的控制。
2特涂前钢材表面处理结构缺陷修理工艺的研究特涂前钢材表面结构缺陷修理关系到特涂质量的好坏,它直接影响结构边缘、焊缝、边角等区域的涂层施工质量,经过多方面的技术讨论及论证,根据涂装配套以及船级社和油漆商的建议,对特涂前钢材表面结构缺陷修理进行了详细的规定,形成了标准文件(详见表1),有力地保证了特涂的施工质量。
表1缺陷处理要求表 1 缺陷处理要求3特涂用磨料的技术指标及选用化学品/成品油船货油舱的板材在流水线经过抛丸处理至Sa2.5级后,有的施工了车间底漆,有的并未施工车间底漆,暴露在大气环境下6~8个月,受海洋气候的影响,钢材表面含有较高的盐分,直接影响到液货舱涂层的施工质量。
为控制特涂前钢材表面的盐分,二次表面处理采用的磨料技术指标是影响特涂的关键。
通常液货舱磨料采用非金属磨料(即铜矿砂),完全能够满足特涂要求,其技术指标见表2。
7000DWT成品油船体建造工艺

70000DWT成品油船船体建造工艺一本船为单甲板、双底、单浆、单舵、尾机型的钢质成品油船,其主尺度如下:总长118.0m设计水线长113.0 m垂线间长110.0 m型宽17.6 m型深9.0 m设计吃水 6.6 m肋距尾—#90.6 m#9—146 0.7 m#146—艏0.6 m梁拱上甲板0.4 m首尾楼甲板0.3 m其他甲板0.2 m双层底高度 1.20 m货油舱内侧板与舷侧板间的垂直距离 1.0 m为了能更好更快、高质量的完成此船的建造任务,特制定此工艺方案。
二船体型线的放样1 根据设计院提供的图纸:型线图、基本结构图、横剖面图等主要图纸,进行样台的实尺放样,放样的精度:基线不直度±1mm,格子线对角线长度±2mm,总长或垂线间长±1mm,型深、型宽±1mm,型线各投影的吻合度≤2.5mm。
2 理论型线的绘制与光顺。
1)作各投影图的边界线。
在作中纵剖面的首尾轮廓线时,按图纸上规定的尺寸和首尾柱图上的要求,在格子线上刻点连线,只要连出的曲线光顺,即可以抛弃不在光顺曲线上的个别点子,不过总长、设计水线、垂线间长、尾轴中心线高度均不能变动。
2)绘制各图上的型线。
绘制型线时应注意各型线的光顺性、协调性,把在某图上修改的点的型值反映到另外两图上,看光顺否,进行反复的修改,直到光顺为止。
3)型线修正的原则。
型线放样的好坏主要体现在每根型线的光顺性,每对型值的一致性和每组型线间距的协调性。
型线修正的技术要求:一致性误差不大于2mm,设计水线以下各点的修正量应小于图纸上的比例尺寸为原则,本船为100mm,设计水线上各点的修正量可以放宽一些。
型线修正量应尽量保持原设计型线图的排水体积不变,主尺度不变、横中剖面上的甲板边线、尾部出口处螺旋桨叶尖与船体型线间的间隙、纵剖面首尾柱轮廓线等不变。
4)型线图的检验。
在横剖面图上作斜剖直线并与横剖线接近垂直相交,以斜剖面与中纵剖面相交为准,在纵剖线图或水线图上画出斜剖线的真实形状,若斜剖线很光顺说明船体型线符合技术要求,反之说明型线不协调,需要修正斜剖直线,并返画到投影图上对应处。
船舶涂装技术的发展-国际船舶网

船舶涂装技术的发展随着高效焊接技术的不断推广,造船生产设计的不断深入,区域法造船模式的不断完善,船舶建造的总工时不断下降,造船的周期也日益缩短。
但是在造船涂装领域内,除了钢材的预处理实现了自动化流水线生产以外,分段、船台、码头等阶段的除锈涂装作业,基本上还是处于半机械化的状态,劳动强度大、作业时间长。
据国内外有关资料统计,船舶涂装的工时根据不同的船型分别占造船总工时的10~20%,其中二次除锈的工作量又占整个涂装工作的50%以上。
船舶涂装贯穿于船舶建造的全过程,从钢材预处理、零件加工、管系制造、分段制造、预舾装、船台或船坞合拢,直到船舶下水、码头舾装、系泊试验、室内装璜等每一工艺阶段,均贯穿着不同要求的涂装工作,可见船舶涂装在造船工程中具有重要地位。
1 高效的船舶防锈底漆在严酷的海洋环境中,防锈是保护船舶的重要措施,防锈底漆是船舶涂料中最基本的品种,常用的有以下几类:醇酸、氯化橡胶、乙烯树脂、环氧、聚氨酯等。
氯化橡胶防锈底漆是最常用的品种,防锈性能良好,现多为厚浆型。
由于氯化橡胶的生产过程不符合环保的要求,国外已经限制氯化橡胶的生产,关闭了很多装备,势必会使氯化橡胶涂料用量下降。
目前国外有些公司在开发水相法生产氯化橡胶,待该技术成熟后,氯化橡胶涂料的使用也许会出现转机。
乙烯系防锈底漆通常是指以氯乙烯与醋酸乙烯共聚物(氯醋树脂)为基料的防锈涂料,氯醋树脂的生产采用水相法,涂料的防锈性能良好,但存在固含量低,涂装道数多的缺点。
BASF公司水相法生产的LaroflexMP乙烯树脂(氯乙烯与乙烯异丁基醚共聚物,氯醚树脂),克服了以往乙烯系漆的缺点,同时符合环保要求。
环氧防锈底漆是用量最大的综合性能最好的品种,也是各大公司大量研发的品种,主要向快干、厚膜、无溶剂型发展。
(1)低表面处理底漆为了减少二次除锈的工作量,目前各涂料厂商纷纷开发对表面处理要求低的防锈底漆,通常的防锈底漆要求表面处理达到SIS(或ISO)标准的Sa2.5级或Sa3级(少数只要求Sa2级),而低表面处理底漆只要求除去表面疏松的铁锈、油脂与垃圾即可,而附着较牢的锈则可不必除去,这将大大降低除锈作业的工作强度,缩短工作周期。
化学品船特涂工艺技术

化学品船特涂工艺技术张彬【摘要】主要通过介绍化学品船液货舱对特涂的要求、涂料的分类及其性能,从而对特涂的施工工艺、表面处理及设备提出了一定的要求。
【期刊名称】《江苏船舶》【年(卷),期】2011(000)005【总页数】2页(P43-44)【关键词】化学品船;液货舱;涂料;漆膜;涂装【作者】张彬【作者单位】扬州市地方海事局,江苏扬州225002【正文语种】中文【中图分类】U671化学品船主要用于散装运输任何液体化学品货船。
在装卸化学品时,会有部分残液留在货舱表面,如果没有合适的材料来防止液货附着、渗透或与表面材料作适度的化学反应等,不仅会污染货品,更给洗舱、清舱带来困难。
不锈钢材料虽然可以较好地满足上述要求,但建造成本高,施工工艺要求高。
多数化学品船采用特涂工艺防腐。
实船建造表明,目前的特涂材料能满足不同货品的装运要求,并具有较好的施工性能。
(1)保护船体结构免受化学品、压载水的侵蚀。
(2)对货品种类适应性广。
(3)不污染货品,不受先前运载货的污染。
(4)清舱容易,表面光滑耐久,对气候施工条件不苛刻。
(5)价格合理。
少数货品如苛性钠、植物油、糖浆可不用涂层的低碳钢来承存,但是,多数化学品船采用不锈钢或涂层的低碳钢,并且少数货品仍对不锈钢有腐蚀。
环氧树脂类涂料漆膜附着力好,坚韧,耐磨,耐盐水、石油制品、淡水、原油、化学溶剂、碱和稀酸等侵蚀,适于碱类、乙二醇、海水、动植物油,不适用于醇类货物。
需要注意的是,这类漆易吸收载运货物,并被芳香烃等类货物所软化,如苯、甲苯、脂类、酮类。
环氧树脂类涂料用于淡水舱、溶剂舱、化学品舱、成品油舱、动植物油舱,当气温低于10℃、相对湿度高时不宜施工。
表面喷砂处理需达到瑞典防锈标准SA2.5级。
无机硅酸锌类涂料漆膜坚韧,耐磨,耐热,耐石油制品、淡水、原油、溶剂,适用于芳烃等类酮类、醇类货物。
其易维修更新、价格便宜,较其他涂料适用范围更广,但不耐强酸、碱、脂肪酸及某些胺类,不得用于含锌的油舱。
- 1、下载文档前请自行甄别文档内容的完整性,平台不提供额外的编辑、内容补充、找答案等附加服务。
- 2、"仅部分预览"的文档,不可在线预览部分如存在完整性等问题,可反馈申请退款(可完整预览的文档不适用该条件!)。
- 3、如文档侵犯您的权益,请联系客服反馈,我们会尽快为您处理(人工客服工作时间:9:00-18:30)。
成品油船货油舱特涂净舱技术的研究与制备
陈涛
(驻大连地区军事代表室,辽宁大连116021)
摘要:通过研究成品油船货油舱特涂净舱技术,来掌握化学品船液货舱解决表面处理问题的办法和途径,以保证化学品船液货舱的涂装质量,为延长涂层的使用寿命创造条件,提高了在国内、国际造船市场上的竞争力。
关键词:净舱技术;表面处理;成品油船
1引言
根据化学品船货舱的表面处理技术要求及相关的表面处理标准,结合成品油轮液货舱净舱技术,通过对影响货舱涂装质量的表面清洁度、盐分及粗糙度等关键因素的研究,提出了解决表面处理问题的办法和途径。
提高了表面清洁度,降低了盐分,保证了粗糙度要求,从而满足表面处理的各项技术标准,解决了困扰船厂特涂施工多年的技术难题,净舱标准符合后续油漆配套(涂层)的要求,从而保证了化学品船货舱涂装质量,为延长涂层的使用寿命创造了条件。
主要研究内容如下:①特涂前钢材表面处理结构缺陷修理工艺的研究;②特涂用磨料的技术指标及选用;③钢材表面粗糙度、清洁度、盐分的检测技术。
为完成本研究,需解决如下关键技术:①液货舱表面盐分的控制;②钢材表面清洁度的控制。
2特涂前钢材表面处理结构缺陷修理工艺的研究
特涂前钢材表面结构缺陷修理关系到特涂质量的好坏,它直接影响结构边缘、焊缝、边角等区域的涂层施工质量,经过多方面的技术讨论及论证,根据涂装配套以及船级社和油漆商的建议,对特涂前钢材表面结构缺陷修理进行了详细的规定,形成了标准文件(详见表1),有力地保证了特涂的施工质量。
表1缺陷处理要求
表 1 缺陷处理要求
3特涂用磨料的技术指标及选用
化学品/成品油船货油舱的板材在流水线经过抛丸处理至Sa2.5级后,有的施工了车间底漆,有的并未施工车间底漆,暴露在大气环境下6~8个月,受海洋气候的影响,钢材表面含有较高的盐分,直接影响到液货舱涂层的施工质量。
为控制特涂前钢材表面的盐分,二次表面处理采用的磨料技术指标是影响特涂的关键。
通常液货舱磨料采用非金属磨料(即铜矿砂),完全能够满足特涂要求,其技术指标见表2。
表2非金属磨料技术指标
表 2 非金属磨料技术指标
但是,随着当今造船技术的发展,在缩短造船周期、提高船舶性能的同时,造船的环保意识已经越来越受到重视,涂装工作也越来越倾向于保护环境,用钢砂代替铜矿砂进行特涂船只液货舱的涂装施工是大势所趋。
下面对钢砂及铜矿砂的优缺点进行分析,确定钢砂特涂的可行性,见表3。
表3钢砂特涂与铜矿砂特涂的优缺点分析
表 3 钢砂特涂与铜矿砂特涂的优缺点分析
综合分析表明,采用钢砂进行表面处理,其质量好、污染小、综合成本低。
但是如采用钢砂进行特涂施工,还必须对特涂设备进行系统分析,解决配套问题。
经了解,钢砂特涂的设备有韩国产的和上海事必达研制生产的,其各自性能及优缺点见表4。
表4钢砂特涂设备优缺点分析
表4钢砂特涂设备优缺点分析
综上所述,认为购买钢丸喷砂系统用于船上特涂喷砂作业,无论在环保上还是在喷砂效率、喷砂后的表面质量上都远好于铜矿砂,而且长远考虑,钢砂由于可重复使用,远期成本远低于铜矿砂,而且大大节省仓库和运输成本,因此经与油漆公司技术部门共同研究,决定开始进行技术工艺革新,将非金属磨料(铜矿砂)改为金属磨料(钢砂)。
最终选用的钢砂规格为G25、G40,并配以适当的钢丸等,其各项理化指标均满足相关的行业标准。
从实船应用来看,此项工艺革新效果很理想,在国内属首例应用。
4钢材表面粗糙度、清洁度、盐分检测技术
成品油船、化学品船特涂的技术要求:钢材表面粗糙度为30~75μm,清洁度为1级,盐分指标不大于50mg/m2。
经确认的检测程序分别采用国际标准:ISO8501-1《钢材在涂装油漆及和油漆有关产品前的预处理——表面清洁度的目视评定》、ISO8502-3《钢材在涂装油漆及和油漆有关产品前的预处理——表面清洁度评估试验第3部分:油漆涂装前的钢材表面的灰尘评定(压敏粘贴带法)》、ISO8503-2《钢材在涂装油漆及和油漆有关产品前的预处理——喷射清理过的钢材表面粗糙特征》、ISO8502-9《喷射清理过的钢材表面可溶性盐的测定》。
4.1表面粗糙度
为满足液货舱表面粗糙度的要求,必须在一次表面处理时加以控制,否则难以保证最终特涂表面粗糙度的要求。
虽然油漆商认为粗糙度略高于标准值(30~75μm)可以接受,但粗糙度高容易造成车间底漆消耗过大和清洁度不能满足要求。
通过试验,用于一次表面处理的抛丸磨料钢丸规格为1.0~1.2mm,
并添加5%~10%的棱角砂是较好的配比,但有的油漆商更希望是70%的丸料与30%的砂料的组合。
另外,降低钢板表面粗糙度的同时也能减少表面颗粒镶嵌物,从而提高表面清洁度。
粗糙度除了取决于磨料的类型、规格和配比以外,喷枪角度、出口压力和喷砂工的操作技能也是不可忽视的因素。
本公司普遍采用钢砂进行分段二次表面处理,钢砂、钢丸和钢丝段的比例为7∶2∶1(或8∶1∶1)。
通过试验,钢砂规格用G25(1.0mm)取代G18(1.2mm)可以有效地降低钢板表面粗糙度。
4.2盐分
为了保证特涂的涂装质量及相应的涂层寿命,经过对纯环氧涂层与不同钢材表面盐分状态的施工试验研究,水溶性盐超标的部位大多集中在分段的底部,也就是践踏比较多的区域。
另外,一次与二次表面处理间隔期超过3个月也是其中的原因之一。
因此,制定了《分段施工阶段清洁管理办法》。
同时,在安排生产计划时,从批量划分、出图计划、分段预舾装和分段涂装等主要节点都作出合理的衔接和细致的安排,总的目标:从钢板预处理到分段二次表面处理的时间控制在3个月以内。
虽然经过控制,但经检测,一般钢材均超过要求的盐分,以No.5P货油舱为例,采用ISO8502-9的检验方法及程序,对喷砂前钢材表面进行盐分检测,盐分平均为89.97mg/m2,超过要求的盐分。
为了解决这一技术难题,经过反复研究试验,在特涂施工过程中采取了以下相应措施:①采取整舱预喷砂的方式,把预喷砂是为了暴露结构缺陷这单一目的增加为大大降低原始钢板表面氯化物的含量;②改变预喷砂后的整舱水洗方式,尽可能除去钢板表面的盐分。
通过对预喷砂和水洗方式的改变,钢材表面氯化物含量完全控制到了
48mg/m2以下。
4.3清洁度
借助真空泵除尘是提高清洁度的主要手段。
通常出现不达标的情况是除尘不彻底所致。
因此,让施工者掌握操作要领,并采取加强过程检查的措施是必要的。
同时,通过改进现有的吸尘器,并购进世界上先进的真空吸尘设备,涂装前钢材表面清洁度的控制完全满足涂装要求。
5结语
通过净舱技术要求及标准的研究,收集、整理了大量关于化学品/成品油船液货舱表面处理的相关国际标准等资料,并转化为企业标准,掌握了化学品/成品油船液货舱表面处理技术,解决了困扰船厂特涂施工多年的技术难题,为延长涂层的使用寿命创造了条件。
在净舱技术要求研究上,还存在如下问题需进一步完善:①盐分控制要求形成文件;②继续跟踪国际涂装标准的变化。