加氢裂化柴油回炼技术探讨
催化柴油加氢裂化技术效益分析
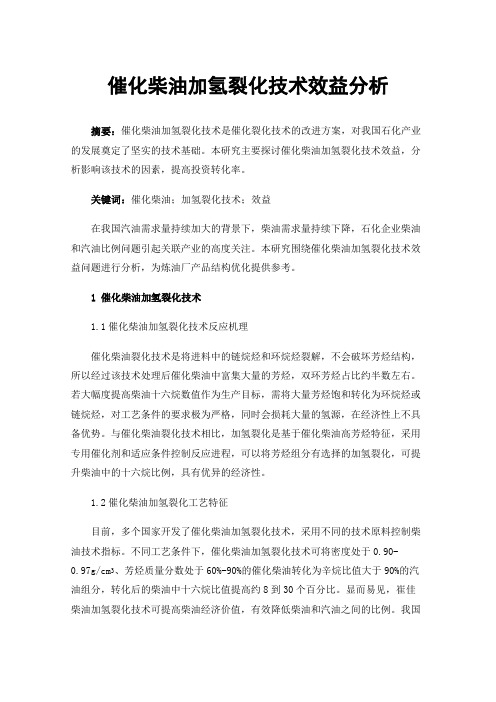
催化柴油加氢裂化技术效益分析摘要:催化柴油加氢裂化技术是催化裂化技术的改进方案,对我国石化产业的发展奠定了坚实的技术基础。
本研究主要探讨催化柴油加氢裂化技术效益,分析影响该技术的因素,提高投资转化率。
关键词:催化柴油;加氢裂化技术;效益在我国汽油需求量持续加大的背景下,柴油需求量持续下降,石化企业柴油和汽油比例问题引起关联产业的高度关注。
本研究围绕催化柴油加氢裂化技术效益问题进行分析,为炼油厂产品结构优化提供参考。
1 催化柴油加氢裂化技术1.1催化柴油加氢裂化技术反应机理催化柴油裂化技术是将进料中的链烷烃和环烷烃裂解,不会破坏芳烃结构,所以经过该技术处理后催化柴油中富集大量的芳烃,双环芳烃占比约半数左右。
若大幅度提高柴油十六烷数值作为生产目标,需将大量芳烃饱和转化为环烷烃或链烷烃,对工艺条件的要求极为严格,同时会损耗大量的氢源,在经济性上不具备优势。
与催化柴油裂化技术相比,加氢裂化是基于催化柴油高芳烃特征,采用专用催化剂和适应条件控制反应进程,可以将芳烃组分有选择的加氢裂化,可提升柴油中的十六烷比例,具有优异的经济性。
1.2催化柴油加氢裂化工艺特征目前,多个国家开发了催化柴油加氢裂化技术,采用不同的技术原料控制柴油技术指标。
不同工艺条件下,催化柴油加氢裂化技术可将密度处于0.90-0.97g/cm3、芳烃质量分数处于60%-90%的催化柴油转化为辛烷比值大于90%的汽油组分,转化后的柴油中十六烷比值提高约8到30个百分比。
显而易见,崔佳柴油加氢裂化技术可提高柴油经济价值,有效降低柴油和汽油之间的比例。
我国典型炼油厂加工中使用催化柴油加氢裂化技术可让全厂柴油与汽油比例下降10个百分比。
2 催化柴油加氢裂化技术效益分析催化柴油加氢裂化技术应用中,借助专用催化剂,有选择性的使用一次或部分循环生产技术,可控制化学反应温度、压力及工艺参数,可在一定程度上对柴油混合物进行调控。
应用催化柴油加氢裂化技术后可提升转化率技术水平,由于不同参数比获得的产量与产品性质存在差异,所以催化柴油加氢裂化技术效益需具体情况具体分析。
加氢裂化装置增产柴油问题探讨

衡和装置的具 体情 况 , 通过优 化操作条 件 , 调整
产 品结构 , 以达到 增产 优质 柴油 的 目的。
1 加 氢裂 化装 置增 产 柴油 的措 施
1 1 选 用 多产 柴油 的催 化剂 .
现有条件 , 依靠科技进 步挖 掘装置潜力 , 增产 车 用柴油 , 提高油品柴汽 比, 满足油品市场需求 , 是 我 国炼 油行 业 面临 的一项 非 常紧迫 的任务 。
此 , 2 年 来加 氢裂 化技 术在 我 国发展 很快 。我 近 0 国现有 加氢 裂化 工业装 置 2 0多套 , 总加 工 能力 已 达 1 t 6M/ a以上 。今 后 , 着 原油 重 质 化 、 随 劣质 化
加氢 裂 化 催 化 剂 品 种 很 多 。不 同 的 催 化 剂 适用 于 不 同 的 加 氢 裂 化 工 艺 ,满 足 加 工 不 同原 料油 、生 产 不 同 目的 产 品 的需 要 。根 据 目 的产 品不 同 ,加 氢 裂 化 催 化 剂 通 常 可 分 为 轻 油 型 、
调整 产 品切割 方案 和 优 化 装 置操 作 条 件 等 , 可 也 以大 幅度 提高 柴 油产 率 。此 外 , 可 以利 用 加 氢 还
很大 ,在 相 同 工 艺 条 件 下 加 工 相 同 原 料 油 时 ,
加氢 裂 化 不 仅 可 以加 工 高 硫 重 质 劣 质 原 料 生产 低硫 低芳 清 洁 柴油 , 而且 还 可 以通 过工 艺 流 程、 催化 剂和操 作 条 件 等 的优 化 选 择达 到 多产 柴 油 的 目的 。 比如 , 于 新 建 加 氢 裂 化 装 置 , 过 对 通 工艺 流程 优化 和 催化 剂 选 择 , 以生产 收率 高达 可
加 氢 裂 化 装 置 增 产 柴 油 问题 探 讨
加氢裂化装置掺炼催化柴油工业试验

加氢裂化装置掺炼催化柴油工业试验1. 引言1.1 研究背景加氢裂化是一种通过加氢作用将高分子烃(如石脑油、重柴油等)裂解成较轻质油品的技术。
而掺炼催化柴油则是在催化剂的作用下,通过掺入适量的添加剂来提高柴油的氧化稳定性和清洁性。
结合这两种技术,可以制备出性能更优越的催化柴油产品,为工业和交通领域提供更环保、高效的能源选择。
本次工业试验旨在探索加氢裂化装置掺炼催化柴油的制备方法,评价其性能并展望其在工业应用中的前景。
1.2 研究目的研究目的是通过加氢裂化装置掺炼催化柴油工业试验,对掺炼催化柴油的制备方法进行探讨与优化,探究其制备技术及工艺条件对催化柴油质量的影响,提高催化柴油的质量和性能。
通过实验过程和实验结果分析,评价掺炼催化柴油的性能,并探讨其在工业应用中的展望,为促进我国柴油质量提升、石油资源有效利用以及环境保护做出贡献。
总结加氢裂化装置掺炼催化柴油工业试验的经验教训,指出未来研究方向,为进一步研究和开发更高效、更环保的催化柴油生产工艺提供参考,推动柴油质量不断提升,满足国内外对环保、高质量柴油的需求,促进我国石油化工行业的可持续发展。
2. 正文2.1 加氢裂化装置掺炼催化柴油的制备方法1. 原料准备:首先需要准备好加氢裂化装置所需的原料,包括重质原油、催化剂等。
2. 加氢裂化反应:将重质原油通过加氢裂化反应器进行加氢处理,将其中的硫、氮等杂质去除,同时将分子结构进行裂化,得到裂化油。
3. 催化柴油的制备:将裂化油经过一系列的脱氮、脱硫等处理后,与催化剂进行接触反应,得到催化柴油。
4. 分离提纯:对得到的催化柴油进行分离和提纯,去除其中的杂质和残留物,确保产品的质量。
5. 储存包装:最后将制备好的催化柴油进行储存和包装,确保其在使用过程中不受到污染或变质。
通过以上制备方法,可以得到高质量的掺炼催化柴油,满足工业生产的需求。
制备过程中需要严格控制各个环节的操作参数,确保产品的质量和稳定性。
2.2 实验过程加氢裂化装置掺炼催化柴油的制备方法是一个复杂的过程,需要经过多个步骤和严格控制条件。
加氢裂化柴油综合利用研究探索
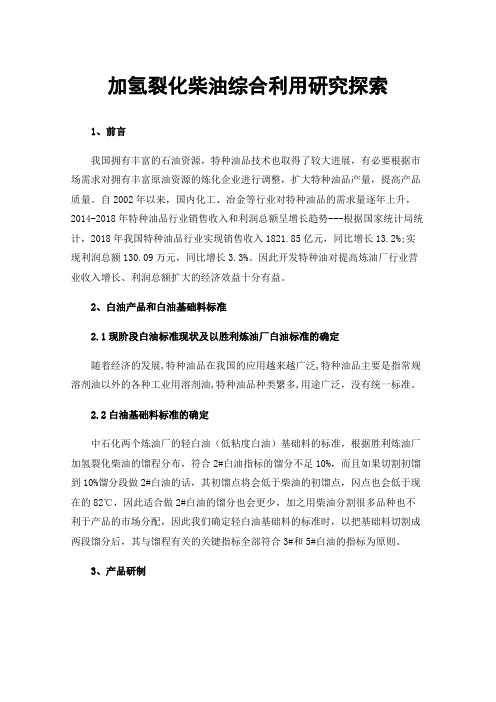
加氢裂化柴油综合利用研究探索1、前言我国拥有丰富的石油资源,特种油品技术也取得了较大进展,有必要根据市场需求对拥有丰富原油资源的炼化企业进行调整,扩大特种油品产量,提高产品质量。
自2002年以来,国内化工、冶金等行业对特种油品的需求量逐年上升,2014-2018年特种油品行业销售收入和利润总额呈增长趋势---根据国家统计局统计,2018年我国特种油品行业实现销售收入1821.85亿元,同比增长13.2%;实现利润总额130.09万元,同比增长3.3%。
因此开发特种油对提高炼油厂行业营业收入增长、利润总额扩大的经济效益十分有益。
2、白油产品和白油基础料标准2.1现阶段白油标准现状及以胜利炼油厂白油标准的确定随着经济的发展,特种油品在我国的应用越来越广泛,特种油品主要是指常规溶剂油以外的各种工业用溶剂油,特种油品种类繁多,用途广泛,没有统一标准。
2.2白油基础料标准的确定中石化两个炼油厂的轻白油(低粘度白油)基础料的标准,根据胜利炼油厂加氢裂化柴油的馏程分布,符合2#白油指标的馏分不足10%,而且如果切割初馏到10%馏分段做2#白油的话,其初馏点将会低于柴油的初馏点,闪点也会低于现在的82℃,因此适合做2#白油的馏分也会更少,加之用柴油分割很多品种也不利于产品的市场分配,因此我们确定轻白油基础料的标准时,以把基础料切割成两段馏分后,其与馏程有关的关键指标全部符合3#和5#白油的指标为原则。
3、产品研制白油基础料的指标的确定是以满足经过切割后的轻重馏分与馏程有关的指标分别满足3#和5#白油的指标要求为依据的。
其它主要是脱除芳烃使之达到白油指标即可实现生产3#和5#白油。
7#白油基础料及产品需单独进行馏分切割。
3.1白油基础料的研制选择有代表性的加氢裂化柴油进行实沸点切割以达到白油基础料的指标,对选择的加氢裂化柴油进行实沸点切割,>245℃的馏分符合指标要求。
白土精制主要是为了进一步脱出剩余酸渣,以确保有品质量的稳定性。
柴油加氢裂化装置航煤产品回炼分析

338/345 343/369 365/384
361
336/342 342/369 365/385
361.2
原料油
设计指标
回炼前
回炼期间
第一床层入口/出口
359/369
359/370
密度,g/cm3 十六烷值 N,μg/g S,μg/g
≯0.874 ≮33 ≯350 ≯2000
回炼前 平均加工量 t/h
13.48 296.25 70.52 380.25
3.17 3.27 13.31 17.46 84.88 62.17 193.75 2.25 380.25
比例% 3.55 77.91 18.55 100 0.83 0.86 3.50 4.59 22.32 16.35 50.91 0.59 100
1 装置生产操作指标分析
1.1 原料指标分析
表 1 回炼前后混合原料油性质对比
2017 年 3 月份惠州炼化二期项目投入运行后,进料改为直馏柴 油和催化柴油的混合油。回炼前,装置总处理量 380t/h,其中催 柴 70t/h,直馏柴油 310t/h。回炼期间,保持总处理量和催柴量不 变,随着航煤回炼量的提高,逐步降低直馏柴油量。回炼前后 混合原料油性质见表 1。从表 1 来看初馏点、10% 和 20% 馏出 温度降低,主要原因是回炼的产品航煤馏程范围在 150~220℃ 之间,拉低了馏出温度,但其余指标相差较小,可能与回炼比例 较小有关。 1.2 操作条件分析
稳定的操作温度区间 ,回炼期间原则上保证转化率不大于 35%,氢油比不低于 500。由表 2 可看出,回炼航煤后装置的工 艺参数变化不大,主要表现在:①回炼后精制反应器一床入口 温度降低约 2℃,主要原因是回炼部分航煤后,油品性质变好, 经过反应加热炉时,油品载热量下降,导致炉出口温度下降。 ②吨油氢耗和新氢量均比回炼前略低,主要因为回炼产品柴油 提高了总进料的品质,降低了反应苛刻度[3~4]。③精制床层和 裂化床层温升变化不大,主要是回炼量较少,且回炼的航煤硫 氮含量较新鲜原料更低,对床层温升贡献很小。
关于加氢裂化-加氢精制组合工艺技术的探讨_1

关于加氢裂化-加氢精制组合工艺技术的探讨发布时间:2022-07-15T06:14:23.813Z 来源:《科学与技术》2022年第5期3月作者:陈鹏[导读] 将馏分油当成是原料进行加氢生产,采用加氢裂化-加氢精制组合工艺可以达到优化产品结构的目标陈鹏中国石油抚顺石化公司石油二厂辽宁抚顺 113000摘要:将馏分油当成是原料进行加氢生产,采用加氢裂化-加氢精制组合工艺可以达到优化产品结构的目标。
基于此,对加氢裂化-加氢精制组合工艺展开了研究,结合项目实例从工艺装置、催化剂等方面对工艺应用过程进行了分析,可知产品中柴油和石脑油收率较高,且品质良好,因此采取的工艺具有一定推广价值。
关键词:加氢裂化;加氢精制;组合工艺引言:在蜡油轻质化加工方面,加氢裂化为主要工艺,能够生成高辛烷值和低氮硫量的汽油、柴油产品。
现阶段,国内主要采用单段串联工艺对蜡油进行加氢裂化,需要实现两个反应器串联,根据装填催化剂差异对装置操作条件进行调整,达到产品收率最大化目标。
而与加氢精制反应器组合,能够生产出优质柴油、石脑油等产品,为提高加氢工艺技术水平提供支持。
1加氢裂化-加氢精制组合工艺分析采用加氢裂化-加氢精制组合工艺,可以先将蜡油原料输入到加氢预处理反应器中。
经过催化剂床层的预处理后,能够将反应物流划分为两部分,一部分经过三相分离后生产气相物流,与轻循环油(LCO)混合后,进入加氢精制反应器,经过分离、分馏得到石脑油和柴油等产品。
在催化剂层中间布置气液分离器,分离得到的气相物流中含有氨、硫化氢,将导致LCO的加氢脱硫受到抑制。
对反应温度等参数进行调节,能够对加氢深度进行调控,使多环芳烃加氢饱和过程得到控制,有效提高汽油的辛烷值[1]。
剩余部分与新输入的氢气混合后进入预处理反应器,之后在加氢裂化反应器中进行分离、分馏,生成航煤产品、柴油等。
由于之前经过三相分离,可以减少氨分压对催化剂裂化活性的抑制作用,因此可以降低裂化装置操作难度。
关于催化裂化柴油加氢裂化工艺相关研究阐述

关于催化裂化柴油加氢裂化工艺相关研究阐述摘要:催化裂化柴油加氢裂化工艺是一种将柴油在加氢条件下进行裂化反应的技术,旨在提高柴油产率和质量。
本文对催化裂化柴油加氢裂化工艺的相关研究进行了综述。
介绍了催化裂化柴油加氢裂化工艺的意义。
随着能源需求的增长和环境保护的要求,传统的催化裂化工艺面临着一系列挑战,详细阐述了催化裂化柴油加氢裂化工艺的关键技术。
包括催化剂选择和制备、反应器设计和操作参数控制等。
这些关键技术对于提高工艺效率、降低能耗和改善产品质量具有重要意义。
关键词:催化裂化;裂化柴油加氢;加氢裂化工艺;相关研究一、引言催化裂化柴油加氢裂化工艺是一种重要的石油加工技术,旨在提高柴油产率和质量,以满足日益增长的能源需求和环境保护的要求。
然而,催化裂化柴油加氢裂化工艺仍然存在许多待解决的问题和挑战。
例如,如何选择合适的催化剂,如何优化反应条件,如何设计高效的反应器等。
本文旨在对催化裂化柴油加氢裂化工艺进行深入研究和阐述,通过分析相关文献,探讨该工艺的优势。
二、催化裂化柴油加氢裂化工艺存在的问题催化裂化柴油加氢裂化工艺是一种重要的石油加工技术,但在实际应用中存在一些问题。
催化剂失活,催化裂化柴油加氢裂化反应需要使用催化剂来促进反应,但由于原料中的杂质、硫化物和金属等物质的存在,催化剂容易受到污染和失活。
这会导致催化剂活性下降,减少反应效率和产品质量。
选择性和产物分布控制,催化裂化柴油加氢裂化反应产生的产物种类繁多,包括烷烃、烯烃、芳烃等。
如何实现对目标产物的高选择性和优化的产物分布仍然是一个挑战。
不同的催化剂和反应条件可能导致不同的产物分布,需要进行深入研究和优化。
能源消耗和环境影响,催化裂化柴油加氢裂化反应需要高温高压条件和大量的氢气供应。
这会带来较高的能源消耗和环境污染。
同时,催化剂的制备和再生过程也需要耗费大量的能源和资源。
反应器设计和操作优化,反应器的设计和操作参数的选择对反应效果和产品质量有重要影响。
加氢裂化装置掺炼催化柴油技术工业应用实践

加氢裂化装置掺炼催化柴油技术工业应用实践摘要:随着社会日益发展的需要和原油的日益劣质化、重质化,以及环境的污染,国家对干净、清洁的能源燃料越来越重视,而蜡油加氢裂化技术是原油深度加工生产清洁燃料的重要方式,所以在未来加氢裂化技术将会越来越普遍和推广。
本文就以美国UOP公司的Unicraking两段加氢裂化工艺技术为例进行实践论证。
关键词:加氢裂化;?催化柴油;?产品质量;1 装置概况为了适应全厂生产的灵活性,本装置设计为全循环和60%转化率两种工况。
设计加工来自国外的减压蜡油,经过加氢脱硫、加氢脱氮、加氢裂化等反应,生产优质的轻、重石脑油、航煤和柴油产品,加氢尾油作为催化裂化装置原料。
本装置反应的部分流程如下:图1 装置反应部分流程2?催化剂分布及原料性质2.1 催化剂分布本装置一段反应器共六个床层,其中第一床层到第四床层为加氢精制床层,催化剂型号分别为CT-30、KF-542、KG-5、HYT-8109、HYT-8119、KF-848 (再生) 、HYT-6219,第五床层和第六床层为加氢裂化床层,催化剂型号为HC-115LT (再生) ,反应器底部后精制剂型号为KF-851 (再生) 。
表1 原料油性质分析对比表2.2 原料性质及特点本装置自开工正常运转一段时间后,为了维持全厂物料平衡和实现效益最大化,开始在原料油中掺入催化柴油,并逐步增加至60 t/h。
如表1所示为在总进料量330 t/h不变的情况下,原料中未掺入以及掺入20 t/h、40 t/h及60 t/h数量催化柴油组成的滤后原料油的主要性质参数。
在整个掺炼观察期间,装置正常运行,各产品质量合格。
通过表1原料油性质分析对比表可以看出随着催化柴油掺炼比例的提高,混合原料油的密度逐渐增大,氮含量、硫含量所占比例都有相应的升高,这与催化柴油高硫、高氮性质特点相吻合,但由于本装置氮含量设计要求不大于867mg/kg,所以为保证本装置催化剂失活速率在正常范围内,建议在装置运行前期,当混合原料油中氮含量大于867mg/kg时,操作人员应密切关注原料油性质及反应器床层温度变化。
加氢裂化装置增产柴油问题探讨

加氢裂化装置增产柴油问题探讨作者:程猛来源:《中国化工贸易·上旬刊》2019年第12期摘要:近年来,随着我国汽柴油供应的市场变化,加氢裂化装置增产柴油的问题开始进入实质的探索阶段。
本文就加氢裂化装置工艺进行阐述,并对加氢裂化装置增产柴油的策略从催化剂、切割方案、馏分设计三个层面予以分析,将为我国加氢裂化装置的优化提供一定的参考。
关键词:加氢裂化装置;柴油;增产加氢裂化装置技术应用开始于上世纪50年代,经历60多年发展,该项技术已基本趋于成熟,其技术应用下的产品生产能力和结构基本可以满足经济社会发展对石油化工行业的要求。
当前,我国汽柴油价格的供需关系对炼化企业产生不小的影响。
汽油供过于求,而柴油供不应求。
这就要求对加氢裂化生产工艺进行改造,使其产品结构实现可控,并以此为策略来应对成品油市场的价格变动。
以增产为目标的加氢裂化装置优化,应有利于柴油产品的产品及品质的上升,从而最大限度地确保石油炼化企业的生产效益。
1 加氢裂化装置工艺分析加氢裂化装置是“油、化、纤”结合的核心,可以生产优质航煤、柴油和润滑油基础油原料,以及重整原料和乙烯原料等化工原料。
该装置属于临氢的催化工艺技术,由反应、分馏、脱硫三大工艺模块组成。
装置采取串联生产工艺流程,运行时首先将原料油进行加热,而后将其输送到反应器中,并在反应器中实现加氢反应,在反应后将其在输送到分馏塔中,在分馏塔中完成分馏处理,而后便可得到相应的汽柴油初级产品。
而后在装置工艺内再次完成对汽柴油初级产品的净化、脱硫作业,使汽柴油产品能够达到国家相关质量标准。
在增产实践中,可对工艺的流程进行适当改造,优化装置的运行参数,并对不同性能的催化剂的用量进行调控,进而实现加氢裂化装置柴油增产提质的目标。
2 加氢裂化装置增产柴油的策略2.1 合理选择增产催化剂在加氢裂化装置增产柴油的工艺研发中,可选用的催化剂种类较为多样,在相同的工艺条件下不同的催化剂类型其作用下的柴油的产出率也会有所不同。
加氢裂化装置掺炼催化裂化柴油研究

加氢裂化装置掺炼催化裂化柴油研究摘要:文章以加氢裂化装置掺炼催化裂化柴油为研究对象,首先对加氢裂化装置概况进行了阐述分析,随后分析研究了加氢裂化装置进行FCC柴油掺炼催化产品,最后运用加氢裂化装置掺炼FCC柴油应注意的问题以供参考。
关键词:加氢裂化装置;催化裂化柴油;掺炼前言:FCC柴油具有杂质含量高、密度较大、储存安全性差等特点,并且直接用作车用能源产生的污染气体较多,随着人们的环保意识不断增强,国家对车用柴油产品质量要求不断提升,需要进一步加强对FCC柴油的处理,有效改善并提升FCC柴油的品质,降低柴油用作能源带来的污染,从而有效满足我国对车用柴油质量品质的要求。
一、加氢裂化装置概况该加氢裂化装置为2.0Mt/a 高压加氢裂化装置,由中国石化工程建设公司参与设计,并于2007年成功投料开车。
该装置主要由四部分组成,分别是反应部分、分馏部分、吸收稳定部分及脱硫部分组成,其中反应部分采用的是目前国内外已经应用较为成熟的炉前混氢流程,操作更加简便,传热效率更加高效,流程也得到了良好的优化。
分馏部分通过设置硫化氢汽提塔,并采用分馏塔进料,常压塔与加热炉出柴油的方案,在分馏塔中,还设置了两个中段回流,从而使得热量得到了较好的回收,有利于整体装置能耗降低。
吸收稳定部分在吸收方案选择上,采用的是重石脑油作为吸收剂的方案,从而使得干气中的液化气得到很好的回收,有效避免了轻石脑油与液化气出现更大的损失;最后对于脱硫部分来说,在脱硫剂选择上,选择的是N-甲基二乙醇胺,进行低分气与液化气的脱硫方案。
主要产品为石脑油、航煤、柴油及用作制乙烯原料的尾油。
该装置所得产品众多,并且分向不同的去向,例如所得的柴油更加清洁,十六烷值高,倾点低,造成污染更小;所得的尾油作为乙烯原料,烷烃含量高,芳烃指数值较低;所得的重石脑油作为催化重整原料,芳烃潜含量较高。
在2010年,该装置转入了第二生产周期,结合实际生产需求,该装置采用了RN—32V 制催化剂和 RHC—3 裂化催化剂,上述两种催化剂由中国石化石油化工科学研究院研发,对尾油质量提升上具有较为积极的影响意义。
加氢裂化装置提高石脑油收率

加氢裂化装置提高石脑油收率【摘要】石脑油是炼油中的重要产品,其收率的提高对炼油行业具有重要意义。
加氢裂化装置是一种有效的工艺,可以提高石脑油的收率。
该装置通过加氢作用,将重质石脑油转化为更轻质的产品,从而提高了收率。
加氢裂化装置在石脑油生产中得到广泛应用,具有高效、环保等优势。
随着技术的不断发展,加氢裂化装置的工艺也在不断改进,其应用前景十分广阔。
加氢裂化装置是提高石脑油收率的有效途径,对于石脑油生产具有重要意义。
【关键词】关键词:石脑油、加氢裂化装置、收率提高、工作原理、影响、应用、优势、发展趋势、有效途径、应用前景1. 引言1.1 石脑油的重要性石脑油是一种重要的石油炼制产品,主要用于生产合成橡胶、塑料、合成纤维等化工产品,具有广泛的应用领域。
石脑油中的芳烃含量较高,有良好的溶解性和稳定性,是制造化工产品的重要原料之一。
石脑油还可以作为柴油的添加剂,提高柴油的燃烧效率和清洁度。
由于石脑油的重要性,其供应稳定性和质量品质对整个化工产业链至关重要。
在当前能源结构转型的背景下,石脑油将继续扮演重要的角色。
随着汽车行业的快速发展,对石油产品的需求也在不断增加,因此石脑油的生产和供应将成为未来能源市场的重要议题。
提高石脑油的收率不仅可以满足市场需求,还可以降低生产成本,提高化工产品的竞争力。
研究和应用加氢裂化装置来提高石脑油收率具有重要意义,对推动化工产业的发展具有积极的影响。
1.2 石脑油收率的提高意义提高石脑油收率的意义在于能够提高石脑油的产量和质量,从而满足市场需求,增加生产效益。
石脑油是一种重要的石油副产品,广泛用于石化工业、化肥生产、合成树脂制造等领域。
提高石脑油收率可以有效降低生产成本,提高利润。
石脑油是一种重要的能源资源,提高其收率也有利于节约能源资源、保护环境。
提高石脑油收率还可以减少石油资源的浪费,延长石油资源的利用寿命,有利于国家能源安全。
随着全球能源需求的不断增长和石油资源的逐渐枯竭,提高石脑油收率成为了当前石油工业发展的重要课题。
加氢裂化装置掺炼催化柴油工业试验

加氢裂化装置掺炼催化柴油工业试验一、引言近年来,全球能源需求不断增长,石油资源的开采程度也越来越高,而传统的炼油工艺已经无法满足现代社会的能源需求。
加氢裂化技术逐渐成为炼油行业的研发热点之一。
加氢裂化技术能够将重负荷石油馏分转化为高质量的清洁燃料,其中催化柴油是加氢裂化技术的重要产品之一。
本文将对加氢裂化装置掺炼催化柴油工业试验进行研究,以期为炼油行业的技术进步提供一定的参考。
加氢裂化装置掺炼催化柴油工业试验是指在加氢裂化装置的基础上,对不同的催化柴油生产工艺进行试验和研究。
催化柴油是一种高质量的柴油产品,它具有较高的抗氧化性能和低凝固点,可以有效降低柴油发动机的排放和提高燃烧效率。
通过对加氢裂化装置掺炼催化柴油工业试验的研究,可以优化生产工艺,提高产品质量,降低生产成本,从而增强炼油企业的竞争力。
三、试验内容和方法1.试验内容本次加氢裂化装置掺炼催化柴油工业试验主要包括以下内容:(1) 对不同的催化剂进行筛选和评估,找出最适合催化柴油生产的催化剂;(2) 对不同的加氢裂化工艺条件进行试验,包括温度、压力、氢气流量等参数的优化;(3) 通过改变裂化装置操作条件,比较不同的烃裂化效果和燃料品质;(4) 分析改变不同的工艺条件对产品质量的影响,包括产品密度、凝固点、芳烃含量等。
2.试验方法四、试验设计为了保证试验的科学性和可靠性,本次试验将采用一定的设计方案:(1) 设定不同的实验组和对照组,分别采用不同种类的催化剂和工艺条件进行试验;(2) 在每种催化剂和工艺条件下,进行多次试验,得到可靠的试验数据;(3) 通过对比试验数据,找出最适合催化柴油生产的催化剂和工艺条件;(4) 对试验数据进行统计学分析,确保试验结果的可靠性和科学性。
五、预期效果本次加氢裂化装置掺炼催化柴油工业试验预期将取得以下效果:(1) 找出最适合催化柴油生产的催化剂和工艺条件,为炼油企业提供技术支持和决策参考;(2) 优化加氢裂化装置的操作条件,提高炼油产品的质量,降低生产成本;(3) 为炼油行业的技术进步和产业升级提供一定的参考和支持,增强企业的竞争力。
加氢裂化装置掺炼催化柴油工业试验

加氢裂化装置掺炼催化柴油工业试验加氢裂化装置掺炼催化柴油这一工业试验是为了提高柴油的品质和性能,以满足不断增长的能源需求和环境保护的要求。
本文将介绍该工业试验的背景、目的、原理、操作流程和实验结果等方面。
一、背景随着全球能源消耗的不断增加,传统石油资源的供应面临了严峻的挑战。
环境污染问题也日益严重,传统柴油的高排放成为了重要的环境问题。
为了解决这些问题,人们开始探索新能源和清洁燃料的替代方案,其中催化柴油成为了一种较为理想的选择。
二、目的本工业试验的目的是通过加氢裂化装置对传统柴油进行掺炼和催化处理,使柴油的品质和性能得到提升,同时降低其排放量,以满足环境保护的要求。
三、原理加氢裂化装置是一种液体石油加工装置,利用高温和催化剂的作用将长链烃分子裂解成短链烃分子,从而提高燃料的辛烷值和低温流动性。
在这一工业试验中,传统柴油与催化剂一起进入加氢裂化装置,经过一系列的化学反应,形成催化柴油。
四、操作流程1. 加载传统柴油和催化剂:按照一定比例将传统柴油和催化剂装入加氢裂化装置中;2. 加热:通过加热装置对加氢裂化装置进行加热,使反应温度达到所需的范围;3. 压力控制:通过调节进气和出气的阀门,控制加氢裂化装置内的压力;4. 反应:在适宜的温度、压力和催化剂的存在下,传统柴油和催化剂发生一系列的化学反应,形成催化柴油;5. 分离:将反应后的产物进行分离,得到催化柴油和其他副产品;6. 净化:通过一系列的净化步骤,除去催化柴油中的杂质和残留催化剂;7. 检测:对催化柴油进行品质和性能的检测,包括辛烷值、芳烃含量、燃烧性能等。
五、实验结果经过加氢裂化装置掺炼催化柴油工业试验,传统柴油的品质和性能得到了显著提升。
催化柴油的辛烷值提高了,低温流动性也得到了改善,从而降低了车辆的启动难度。
催化柴油的芳烃含量也得到了降低,燃烧更加充分,排放产物的多环芳烃含量也得到了降低。
柴油催化加氢裂化机理及反应动力学的研究

柴油催化加氢裂化机理及反应动力学的研究随着车辆排放标准的不断提高,发动机的燃烧效率和排放性能愈发受到关注,同时,汽车行业也在致力于解决环境污染问题。
柴油催化加氢裂化技术因其可以有效降低柴油排放中的污染物而备受关注。
本文将就柴油催化加氢裂化的机理及反应动力学进行阐述和探讨。
一、柴油催化加氢裂化机理柴油催化加氢裂化是一种通过对柴油分子进行加氢变性来降低其点火时期弱性和改善燃烧性能的技术。
该技术的核心在于利用催化剂使柴油分子中的碳链得到断裂和加氢反应。
在催化剂的作用下,高碳重分子可裂解为低碳重分子,且其中的不饱和链会被氢气加氢,形成一些烷基化合物。
柴油催化加氢裂化的催化剂分为两类:常见的为黄金催化剂和铁基催化剂。
黄金催化剂在现代柴油机中被广泛应用,尤其是在催化氧化还原(CO和NOx)的领域。
而铁基催化剂则使用在含硫柴油的处理过程中。
柴油催化加氢裂化的整个催化反应流程大致可分为5个步骤:环烷烃的吸附、裂解过渡态的形成、大分子烃的裂解、氢的遍历和脱附。
其中,环烷烃的吸附是整个反应过程的开始,高效的吸附和催化剂活性以及对各种反应性质的选择,是决定整个反应性能的关键因素。
二、柴油催化加氢裂化反应动力学柴油催化加氢裂化反应动力学是研究反应速率和反应机理的科学领域。
柴油催化加氢裂化反应反应速率主要受催化剂性能和反应条件(温度、压力等)的影响。
反应条件:实验结果表明,催化加氢裂化反应中,反应温度是影响柴油分子裂解和加氢反应的主要因素之一。
当反应温度从200℃增加到400℃时,反应速率也大大增加。
然而,当反应温度超过400℃时,反应速率反而降低。
因此,反应温度不同于其他催化反应,具有“温度优化区”的特点。
催化剂性能:柴油催化加氢裂化反应的催化剂主要是均质氢化催化剂和金属催化剂。
这两种催化剂在催化裂解反应中的作用机理是不同的。
在均质氢化反应过程中,反应动力学在反应物和催化剂之间产生的化学吸附物表面上发生。
这种表面吸附和反应动力学是由化学反应动力学决定的。
探析加氢裂化装置掺炼劣质催化裂化柴油技术的运用
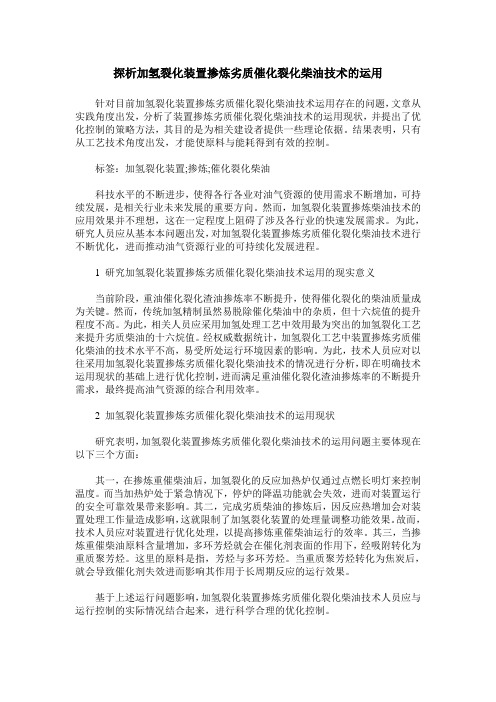
探析加氢裂化装置掺炼劣质催化裂化柴油技术的运用针对目前加氢裂化装置掺炼劣质催化裂化柴油技术运用存在的问题,文章从实践角度出发,分析了装置掺炼劣质催化裂化柴油技术的运用现状,并提出了优化控制的策略方法,其目的是为相关建设者提供一些理论依据。
结果表明,只有从工艺技术角度出发,才能使原料与能耗得到有效的控制。
标签:加氢裂化装置;掺炼;催化裂化柴油科技水平的不断进步,使得各行各业对油气资源的使用需求不断增加,可持续发展,是相关行业未来发展的重要方向。
然而,加氢裂化装置掺炼柴油技术的应用效果并不理想,这在一定程度上阻碍了涉及各行业的快速发展需求。
为此,研究人员应从基本本问题出发,对加氢裂化装置掺炼劣质催化裂化柴油技术进行不断优化,进而推动油气资源行业的可持续化发展进程。
1 研究加氢裂化装置掺炼劣质催化裂化柴油技术运用的现实意义当前阶段,重油催化裂化渣油掺炼率不断提升,使得催化裂化的柴油质量成为关键。
然而,传统加氢精制虽然易脱除催化柴油中的杂质,但十六烷值的提升程度不高。
为此,相关人员应采用加氢处理工艺中效用最为突出的加氢裂化工艺来提升劣质柴油的十六烷值。
经权威数据统计,加氢裂化工艺中装置掺炼劣质催化柴油的技术水平不高,易受所处运行环境因素的影响。
为此,技术人员应对以往采用加氢裂化装置掺炼劣质催化裂化柴油技术的情况进行分析,即在明确技术运用现状的基础上进行优化控制,进而满足重油催化裂化渣油掺炼率的不断提升需求,最终提高油气资源的综合利用效率。
2 加氢裂化装置掺炼劣质催化裂化柴油技术的运用现状研究表明,加氢裂化装置掺炼劣质催化裂化柴油技术的运用问题主要体现在以下三个方面:其一,在掺炼重催柴油后,加氢裂化的反应加热炉仅通过点燃长明灯来控制温度。
而当加热炉处于紧急情况下,停炉的降温功能就会失效,进而对装置运行的安全可靠效果带来影响。
其二,完成劣质柴油的掺炼后,因反应热增加会对装置处理工作量造成影响,这就限制了加氢裂化装置的处理量调整功能效果。
加氢裂化装置掺炼催化柴油工业试验

加氢裂化装置掺炼催化柴油工业试验加氢裂化装置掺炼催化柴油工业试验是一种新型的炼油技术,旨在提高柴油的质量和减少环境污染。
该工艺将加氢处理和催化裂化技术相结合,通过对原油进行一系列的加氢和裂化反应,实现原油中的低品位组分转化为高质量的柴油产品。
这种工艺的主要过程包括进料预处理、加氢裂化反应、催化柴油分离和再生等环节。
进料预处理是指将原油中的杂质和重质组分进行处理,以保证后续反应过程的顺利进行。
加氢裂化反应是核心步骤,通过加氢作用和高温裂化作用,将原油中的硫、氮和重质组分进行转化和降解,从而提高柴油的质量。
催化柴油分离是指将反应后的油品进行分离和精制,得到高质量的柴油产品。
再生是将废催化剂进行处理和再利用,减少资源浪费和环境污染。
该工艺的主要优点有以下几个方面。
可以有效降低柴油中的硫和氮含量,减少柴油的环境污染。
可以提高柴油的凝点和氧化安定性,增加柴油的存储稳定性和使用寿命。
该工艺还可以提高柴油的燃烧性能和动力性能,减少发动机的磨损和故障。
该工艺还存在一些问题和挑战。
加氢裂化装置的建设和运行成本较高,需要大量的投资和能源消耗。
反应过程中产生的废催化剂和废水需要进行处理和处理,增加了环境保护的难度。
加氢裂化装置的操作和维护技术要求较高,需要专业的技术人员进行管理。
为了解决这些问题,需要进一步研究和开发新的炼油技术和装置。
可以探索新型的催化剂和反应条件,以降低装置的运行成本和能源消耗。
还应加强对废催化剂和废水处理技术的研究和开发,以解决环境保护的问题。
还应加强对操作和维护技术的培训和管理,提高装置的运行效率和安全性。
加氢裂化装置掺炼催化柴油工业试验是一种新型的炼油技术,可以提高柴油的质量和减少环境污染。
该工艺还存在一些问题和挑战,需要进一步研究和开发。
通过不断的努力,相信这种新型工艺将对炼油行业的发展和环境保护产生积极的影响。
加氢裂化工艺的进展和发展趋势

加氢裂化工艺的进展和发展趋势加氢裂化是一种高级催化裂化技术,目前是炼油工业中非常重要的一个领域。
该技术可以将石油原料转化为高附加值和高品位的产品,例如高辛烷值汽油、轻质石蜡和烯烃等。
因此,加氢裂化工艺已经成为国内炼油企业的重点发展领域,并且目前在炼油领域中占有重要的地位。
本文将详细介绍加氢裂化工艺的进展和发展趋势。
一、加氢裂化工艺简介1. 工艺概述加氢裂化是指在催化剂的作用下,将高分子烃加氢和裂化,从而在得到较短的碳链烃的同时,也可以得到高质量的燃料组分。
加氢裂化工艺的主要原理是在适当的反应温度和压力下使用高活性的催化剂,将高分子烃裂解并加氢,以得到轻质高辛烷值汽油、烯烃和轻烷烃等产品。
2. 工艺优点(1)可以根据实际需要生产不同种类和质量的产品,例如高辛烷值汽油、轻质石蜡、烯烃和轻烷烃等。
(2)具有较高的反应选择性,并能使裂解产品达到质优、量多和产率高等优点。
(3)原料适应性强,可以使用各种类型的原油、与烃和重烷烃作为催化反应的原料。
(4)反应温度适宜,可以在相对低的温度和压力条件下进行反应,不仅能减少能耗,而且能降低裂化催化剂的脆化率。
二、加氢裂化工艺的进展1. 催化剂的选择加氢裂化的催化剂选择是该工艺的一个重要方面,催化剂的性能和优劣直接影响到反应的效果和产物质量。
国内外的加氢裂化研究表明,采用酸性和金属修饰剂的催化剂体系具有较高的反应活性和稳定性。
2. 反应设备的改进反应设备的改进是加氢裂化工艺的另一个关键方面。
现代加氢裂化装置采用独具特色的工艺设计和新型反应器,能够充分利用催化剂的作用,提高反应效率,同时还可以对反应物的质和量进行精确控制。
例如在重油加氢裂化反应中,采用反应器的催化层分段温度控制,能够使反应过程中物料的质和量能够更好地得到控制。
三、加氢裂化工艺的发展趋势1. 用于生产替代能源传统石油资源已经进入生命周期的后期,且具有一定的环境污染,因此研究替代能源已经成为全球研究的热点问题。
加氢裂化装置掺炼催化柴油工业试验

加氢裂化装置掺炼催化柴油工业试验
加氢裂化技术是现代炼油工业中的一项关键技术,它能够加工含有较高硫、氮、钢等
重金属组分的重质油类,将其转化成为高质量的项目,特别是催化柴油的加氢裂化技术更
是一个重要的方向。
本文主要介绍一个加氢裂化装置掺炼催化柴油工业试验的流程和实验
结果。
工业试验采用了一个高效的加氢裂化反应器,通过一系列反应过程,将重质油类中的
含硫、氮、钢等重金属组分降低,在此同时将其转化为催化柴油。
具体实验过程如下:
首先将催化剂(波尔布特N854催化剂)和氢气分别注入反应器。
然后将重质油类和轻质石蜡同时送入反应器,该流程采用了连续进料方式。
反应器内部的加氢裂化反应在一定
的温度和压力下进行。
反应过程中催化剂能够促进反应的进行,并使反应得到更好的控制。
随着反应的进行,重质油类中的含硫、氮等重金属组分逐步被吸附和处理,最终反应所产
出的催化柴油可以达到高质量的要求。
实验结果表明,通过加氢裂化技术处理后的催化柴油具有更高的氢化度和清洁度。
在
反应器温度为390℃,压力为4.0 MPa的环境中,得到了催化柴油的收率为92.4%。
经过化验分析,催化柴油的氢化度为77.8%,硫含量为0.003%,氮含量为0.03%,钢含量为0.16 ppm。
这表明,该加氢裂化装置掺炼催化柴油工业试验是一项成功的尝试。
蜡油加氢裂化装置掺炼加氢精制柴油的探讨

馏程 ħ ? 初馏点 5% 0% 1 0% 2 0% 5 0% 6 3 0 2 3 3 4 3 4 9 3 6 6 4 0 0 4 2 1 4 5 7 4 7 5 5 2 1 2 9 9 3 3 0 3 4 6 3 6 3 3 9 9 4 1 1 4 5 6 4 7 5 5 2 2 3 3 4 3 4 8 3 5 9 2 6 8 2 1 1 1 7 8
0% 9 5% 9 终馏点
2 0 1 7 0 5 1 6;修改稿收到日期 : 2 0 1 7 0 7 1 6。 收稿日期 : 方友 , 从事加氢裂化工艺管理工作 。 作者简介 : 方友 , : 。 E m a i l f a n o u@c n o o c . c o m . c n 通讯联系人 : g y
1 5] 精制柴油的可行性及其经济效益 [ 。
裂化反应床层 。 蜡 油 加 氢 裂 化 装 置 掺 炼 加 氢 精 制 柴油前以 减 二 线 蜡 油 、 减三线蜡油和焦化蜡油为 原料 , 实际原料加工质量比为 5 掺炼后 0ʒ2 5ʒ2 5, 维持设计的 3 种 蜡 油 间 的 比 例 不 变 。 蜡 油 转 化 率 并尽量维持稳定 。 控制在 8 7%ʃ0 . 5% , 1 1 原料油性质 表 1 为掺炼加氢 精 制 柴 油 前 后 混 合 原 料 油 的 性质对比 。 掺炼前后原料性质基本保持稳定 , 加氢
第1 1期
方 友, 等. 蜡油加氢裂化装置掺炼加氢精制柴油的探讨
5 7
精制柴油硫 、 氮 含 量 很 低, 掺 炼 量 又 较 少, 不影响 氮 含 量, 混 合 进 料 的 硫、 氮含量主 混合进料的 硫 、 要受蜡油进料硫 、 氮含量的变化影响( 主要是原油 。 虽然 加 氢 精 制 柴 油 馏 程 较 轻 , 但因 品种的变化 ) 为掺炼量少 , 并未影 响 混 合 原 料 的 馏 程 , 而且混合 没有出现 原料高压 进 料 泵 的 运 行 也 未 受 到 影 响 , 振动增大的问题 。 通过掺炼硫 、 氮 含 量 很 低 的 加 氢 精 制 柴 油, 有 效降低了 装 置 混 合 进 料 的 硫 含 量 和 密 度 , 硫质量
加氢裂化装置在压减柴油中的作用分析

加氢裂化装置在压减柴油中的作用分析摘要:柴油作为基础燃料,被大量应用于工业快速发展时期的生产和运输,在国民经济增长过程中发挥了重要的作用。
然而,受国内油品消费市场变化的影响,柴油市场消费量已达峰值,中国成品油市场消费柴汽比逐步降低,由2015年的1.52降至2021年的1.05,预计2025年前后柴汽比将下降到0.98左右。
柴油需求逐渐降低,汽油、芳烃、乙烯等化工品需求不断增长,压减柴油产量成为炼油厂的主要经营策略之一,炼油厂从燃料型向燃料-化工型转变已成共识。
关键词:加氢裂化装置;压减柴油;作用;引言1966年我国第一台加氢裂化装置在大庆石油化工总厂投产,1979年,茂名、金陵、上海、扬子石化相继引进了美国联合石油公司的4套大型加氢裂化装置并于1980年先后投产。
随着服役时间的延长,越来越多的加氢裂化装置老化,而由于加氢裂化装置本身的高温高压临氢环境,一旦发生失效,后果非常严重,而装置的老化也会导致失效风险的增加。
1加氢裂化加氢裂化技术主要指通过脱蜡加氢将油品原料油中主要烃类物质分子含量减少10%以上的裂化工艺,包括专用馏分油脱蜡加氢裂化、渣馏分油脱蜡加氢裂化和专用馏分油脱蜡加氢裂化脱蜡。
2压减柴油策略2.1增产非柴油产品加氢裂化装置非柴油产品主要包括轻石脑油、重石脑油、喷气燃料和尾油,以下基于增产轻石脑油、增产重石脑油和增产喷气燃料3种生产方案,从原料配比及性质、关键工艺参数、产品收率、产品性质4个方面进行对比和分析。
2.2充分利用催化裂化处理能力,减产柴油在优化调整装置工艺参数的基础上,充分利用催化裂化能力大的优势,将柴油转化为汽油、液化气和丙烯酸酯,达到产品结构调整的目的。
首先,根据柴油的消耗量,油渣加氢装置可以停止柴油(柴油每月产量可从5kts减少到6kts),油渣加氢装置的柴油与重油一起进入催化裂化装置;其次,根据柴油池的协调条件,调节柴油燃料的终点,以降低的压力,将柴油组件压入减压塔,同时将减压塔顶部的油和柴油燃料的第一线插入燃油(每月可压减柴油9~10kt);三是做好焦化装置操作的优化);三是优化炼焦装置的工作,降低柴油的炼焦终点,部分柴油炼焦成焦油(柴油的炼焦终点由350°C降低至330°C,柴油月产量可由6吨降低至7吨),净化后进入催化裂化装置。
- 1、下载文档前请自行甄别文档内容的完整性,平台不提供额外的编辑、内容补充、找答案等附加服务。
- 2、"仅部分预览"的文档,不可在线预览部分如存在完整性等问题,可反馈申请退款(可完整预览的文档不适用该条件!)。
- 3、如文档侵犯您的权益,请联系客服反馈,我们会尽快为您处理(人工客服工作时间:9:00-18:30)。
龙源期刊网
加氢裂化柴油回炼技术探讨
作者:臧晖
来源:《科学大众》2019年第12期
摘; ;要:文章在分析加氢裂化柴油回炼技术的基础上,进行了小型回炼实验。
实验结果表明,通过对比加氢柴油、加氢蜡油的单独反应情况,在运用混合原料进行实验后,低价值产物产率会下降,总液体收率会有所增加。
分别选择了两种工况进行工业生产验证,实践证明该技术路线是可行的。
关键词:加氢裂化柴油;加氢;回炼技术
加氢裂化工艺技术对原料油适应性强,具有可大量生产优质中间馏分油产品、液体产品收率高并且灵活调整产品结构等优点,是炼油企业提高柴汽比的最有效的重油加工技术和清洁生产技术。
因此,加氢裂化及加氢精制工艺和技术越来越受到世界各大石油公司的重视,加氢装置的建设和技术的开发得以更快地发展。
近年来,我国加氢裂化及加氢精制技术的开发和应用得到快速发展,在低利润、高竞争性的炼油行业中,如何提高产品收率成为工艺流程研究的重点,这就需要应用新技术进行柴油的回炼,可使炼油企业在减少投入和操作成本的情况下,改善产品结构,提高目的产品收率。
1; ; 加氢回炼技术原理
一般情况下,催化柴油的转化有两种方式,一种是催化裂化,另一种是加氢裂化。
无论是采用哪种技术,其技术开发点都是以催化柴油组成特点为基础的。
其技术路线可分为4种:第一种是加氢精制。
要么直接加工催化柴油,要么在直馏柴油中加入10%左右的催化柴油,这样就可有效增加十六烷值单元。
第二种是加氢改质。
主要就是指运用加氢裂化剂、加氢精制剂,实现烯烃、芳烃等的饱和加氢,以此达到增加十六烷值单元的目的。
比如催化柴油深度加强处理技术、提高催化柴油十六烷值的加氢改质工艺技术就是以此为原理的。
第三种是利用加氢装置掺入部分催化柴油,并进行回炼,主要就是实现柴油的深度转化。
第四种是加氢-催化裂化组合技术,即在加氢装置的基础上,进行柴油加氢或蜡油加氢,然后将其与精制蜡油进行混合,作为装置原料,接下来利用加氢装置进行催化柴油的转化。
在具体选择中,企业必须要根据实际生产流程、柴油质量升级要求、柴油组成等,选择性价比较高的技术路线。
另外,还需注意加氢柴油黏度低、沸点低,正有利于加氢柴油、高黏度新鲜原料的混合原料黏度。
比如对比常压渣油、加氢柴油的密度和蒸馏曲线,并利用软件模拟混合不同比例加氢柴油,且基准温度为180 ℃,210 ℃的原料黏度。
可以明显地发现在混合加氢柴油后,混合原料黏度会下降,且随着温度的降低,其黏度下降数值越大。
这主要就是因为混合原料运动黏度可以改变原料油的性质,使其能经受住高温的催化。