品质检验作业管理
质量检验管理制度(10篇)
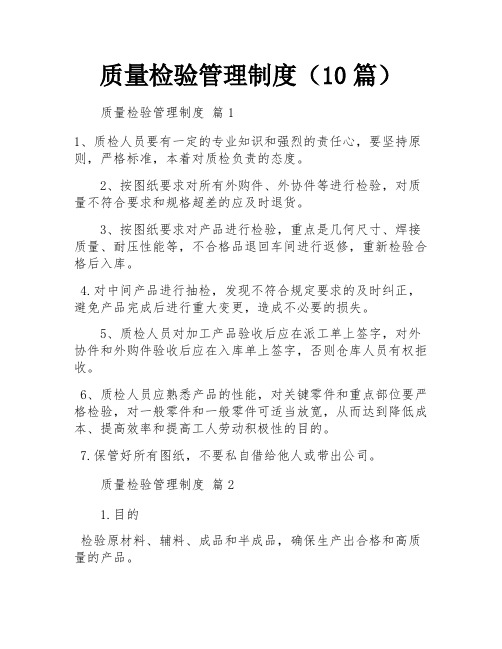
质量检验管理制度(10篇)质量检验管理制度篇11、质检人员要有一定的专业知识和强烈的责任心,要坚持原则,严格标准,本着对质检负责的态度。
2、按图纸要求对所有外购件、外协件等进行检验,对质量不符合要求和规格超差的应及时退货。
3、按图纸要求对产品进行检验,重点是几何尺寸、焊接质量、耐压性能等,不合格品退回车间进行返修,重新检验合格后入库。
4.对中间产品进行抽检,发现不符合规定要求的及时纠正,避免产品完成后进行重大变更,造成不必要的损失。
5、质检人员对加工产品验收后应在派工单上签字,对外协件和外购件验收后应在入库单上签字,否则仓库人员有权拒收。
6、质检人员应熟悉产品的性能,对关键零件和重点部位要严格检验,对一般零件和一般零件可适当放宽,从而达到降低成本、提高效率和提高工人劳动积极性的目的。
7.保管好所有图纸,不要私自借给他人或带出公司。
质量检验管理制度篇21.目的检验原材料、辅料、成品和半成品,确保生产出合格和高质量的产品。
监视和测量产品特性,验证产品要求得到满足,并确保顾客要求得到满足。
2.范围适用于生产所需的采购产品、过程产品和成品的监视和测量。
辅料的进货检验,半成品的过程检验,成品的出厂检验。
3.职责质量控制部是监视和测量产品特性的主要职能部门。
4.程序4.1质管科根据《检验标准》明确检测点.抽样方案.检测项目.检测方法.使用的检测设备等。
4.2进货验证4.2.1对生产购进物资仓库保管员核对,确认原材料品名,数量等无误.包装无损后,置于待检区,并通知检验员检验。
必要时,由化验室采样进行微生物和理化指标的检验。
4.2.2检验员根据《检验标准》进行全数或抽样验证,并填写《原料检验记录》:产品的过程检验由各工序的品管员负责,按照工艺标准对其检验和监控将检验合格的半成品交付下道工序,不合格品另行堆放。
a)检验合格。
仓库办理入库手续并做好标识。
b)检验不合格时,检验员在购进物资上加“不合格”标识,按《不合格品控制程序》进行处理。
品质部检验管理制度
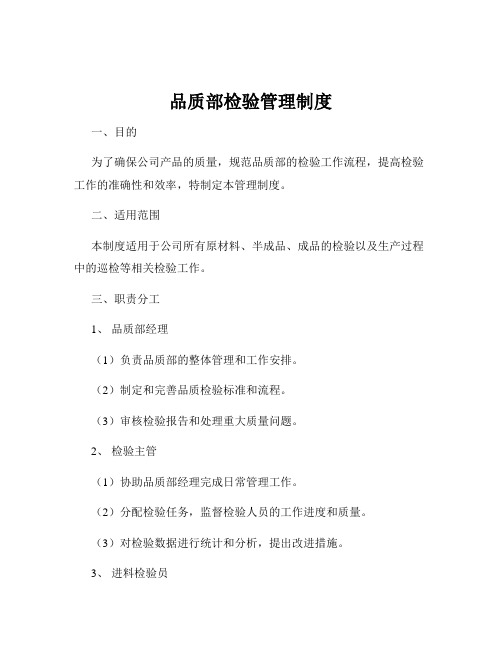
品质部检验管理制度一、目的为了确保公司产品的质量,规范品质部的检验工作流程,提高检验工作的准确性和效率,特制定本管理制度。
二、适用范围本制度适用于公司所有原材料、半成品、成品的检验以及生产过程中的巡检等相关检验工作。
三、职责分工1、品质部经理(1)负责品质部的整体管理和工作安排。
(2)制定和完善品质检验标准和流程。
(3)审核检验报告和处理重大质量问题。
2、检验主管(1)协助品质部经理完成日常管理工作。
(2)分配检验任务,监督检验人员的工作进度和质量。
(3)对检验数据进行统计和分析,提出改进措施。
3、进料检验员(1)负责原材料的检验工作,按照检验标准和抽样方案进行检验。
(2)填写进料检验报告,对不合格原材料进行标识和隔离。
4、过程检验员(1)负责生产过程中的巡检工作,及时发现和解决生产中的质量问题。
(2)对关键工序进行重点监控,确保生产过程符合质量要求。
5、成品检验员(1)负责成品的检验工作,按照检验标准进行全面检验。
(2)填写成品检验报告,对不合格成品进行标识和隔离。
四、检验标准和依据1、品质部应根据国家相关标准、行业标准、客户要求以及公司内部的技术文件,制定详细的检验标准和检验规范。
2、检验标准应明确检验项目、检验方法、检验频率、抽样方案、合格判定准则等内容。
3、检验人员应严格按照检验标准进行检验,不得随意更改检验方法和判定准则。
五、检验流程1、进料检验(1)供应商送货后,仓库管理员应及时通知进料检验员进行检验。
(2)进料检验员应在规定的时间内到达仓库,按照检验标准和抽样方案进行抽样检验。
(3)检验完成后,检验员应填写进料检验报告,注明检验结果和处理意见。
(4)对合格的原材料,仓库管理员办理入库手续;对不合格的原材料,检验员应进行标识和隔离,并及时通知采购部门与供应商协商处理。
2、过程检验(1)过程检验员应按照生产工艺流程和检验标准,对生产过程进行定期巡检。
(2)巡检过程中,检验员应重点关注关键工序和容易出现质量问题的环节,及时发现和解决质量问题。
企业品质管理流程制度模板——制程检验作业流程(附表单)

1.0 目的保证产品品质在制造过程得到有效控制,确保产品满足规定的要求,防止不合格品流通,减少生产返工及产品报废,特制定本流程。
2.0 适用范围适用于产品从原料投放、加工制作到完工出货全过程的检验和测量控制。
3.0 职责3.1品质部:负责制程品质的检验和制程品质管控,负责相关品质检验数据的记录和统计分析,负责品质责任认定和责任追究,负责品质改善监督和进度跟进。
3.2生产部:负责制程品质的首末件检验、报检、自检、互检、巡检及品质异常的反馈和处理。
3.3其它部门:负责协助品质部和生产部按本流程执行相关作业。
4.0 作业程序4.1 关键工序的识别在以下情况时,应对其作为关键或特殊工序予以识别和对待:4.1.1 工序的结果不能通过其后的检验和试验完全验证,或者加工后无法测量或需要实施破坏性实验才能得出结果;4.1.2 工序对最终产品的安全质量、主要性能有重大影响。
4.2 首件检验4.2.1各车间各工序依据生产排期计划、工艺流程、作业指导书、产品图纸、品质标准等进行首件检验。
4.2.2必须进行首件检验的工序:机加件(如挂具、挂钩、齿轮、轴承、研发样件)4.2.3上述工序出现以下情况时必须进行首件检验:开工生产时、更换工件、换料、换模、修模、设备维修、更换工装夹具、生产人员变更、加工方法变更及其它需要首检的情况。
4.2.4各工序/机台操作员根据生产排期计划及对应的加工工件的工艺流程、作业指导书、产品图纸、品质标准等进行首件生产,经自检合格后向品管送检。
4.2.5品管员接到报检后,依据工件的工艺流程、作业指导书、产品图纸、品质标准(标准品、限度样品或者图片)等完成首件检验并作好相关记录;若不合格则及时通知工序或机台操作员改善并重新制作首件;4.2.6工序或机台操作员再次制作的首件仍然不合格的,品管员应及时将首件检验结果通知班组组长或车间管理人员,车间管理人员在接到首件制作不合格的信息后须立即到场解决。
4.2.7首件经品管员检验合格后方可正式批量生产。
质量检验管理制度

质量检验管理制度质量检验工作是企业管理的重要组成部分,为搞好检验工作的管理,特编制如下检验管理制度。
一、检验的组织管理公司质检部是有限公司的质量管理部门,其职能是代表公司对原材料、工序半成品及成品进行检验和验收,检验人员独立行使检验权力,公司的中心试验室负责原材料的检验和相关产品性能指标的检测,工序检验员负责车间各个工序半成品的检测及质量控制,成品检验员负责成品的出厂检测及成品合格标示。
二、材料的进厂检验制度1、检验依据材料检验工作依据公司原材料检验规范进行,相关指标要符合公司的标准要求。
2、检验流程a.原材料进厂后由物资采购中心人员填写“原材料送检表”,书面通知中心试验室检验人员,检验人员依据原材料送检表去现场抽取样品。
b.被检物品必须有质量证明书,出厂检验报告或相关质量证明,方可取样检验。
c.检修人员如发现材料明显带有质量缺点可拒绝检修。
d.取回的产品(试样)依据相关试验请求进行检修和试验。
e.试验条件必须符合相关要求,试验方法应规范,以确保试验数据的准确性。
f.检验合格的产品,依据检验结果出具检测报告,物资采购中心依据检验合格报告办理相关入库手续。
g.不符合公司原材料检验标准,但质量缺陷对产品影响不大的材料,可做让步接收,让步接收的材料必须履行如下手续:①让步接收由检修员出具原材料检测报告,并由质检部、技术中心、生产管理部、物资采购中心主管及以上领导评审签字。
②原材料检测报告由中心试验室注明不符合项及指标,并记录试验编号。
XXX凭签字通过的原材料检测报告办理入库。
h.特殊情况因生产急需而无法检验时,可由试验室备案,主管副总批准后方可放行使用,放行材料必须是供货关系较长,质量较稳定的供应商,特殊放行的材料必须及时通知使用单位,做好试用工作,一经使用发现问题及时停止使用。
i.因结构尺寸或材料密度不符合公司相关要求的,应由中心试验室出具不合格材料、扣料通知单一式叁份报物资采购中心,留存一份由光电复合缆业务单元总监签述意见后转计量人员,计量人员在出具检斤单时,将其重量扣除,仓库多余数量应由材料核算人员以月为单位做涨库核销处理。
质量检验管理制度(7篇)
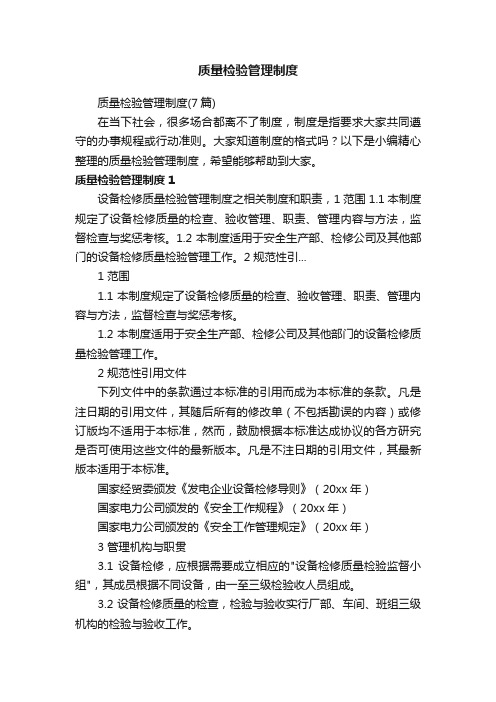
质量检验管理制度质量检验管理制度(7篇)在当下社会,很多场合都离不了制度,制度是指要求大家共同遵守的办事规程或行动准则。
大家知道制度的格式吗?以下是小编精心整理的质量检验管理制度,希望能够帮助到大家。
质量检验管理制度1设备检修质量检验管理制度之相关制度和职责,1范围1.1本制度规定了设备检修质量的检查、验收管理、职责、管理内容与方法,监督检查与奖惩考核。
1.2本制度适用于安全生产部、检修公司及其他部门的设备检修质量检验管理工作。
2规范性引...1 范围1.1 本制度规定了设备检修质量的检查、验收管理、职责、管理内容与方法,监督检查与奖惩考核。
1.2 本制度适用于安全生产部、检修公司及其他部门的设备检修质量检验管理工作。
2 规范性引用文件下列文件中的条款通过本标准的引用而成为本标准的条款。
凡是注日期的引用文件,其随后所有的修改单(不包括勘误的内容)或修订版均不适用于本标准,然而,鼓励根据本标准达成协议的各方研究是否可使用这些文件的最新版本。
凡是不注日期的引用文件,其最新版本适用于本标准。
国家经贸委颁发《发电企业设备检修导则》(20xx年)国家电力公司颁发的《安全工作规程》(20xx年)国家电力公司颁发的《安全工作管理规定》(20xx年)3 管理机构与职贯3.1 设备检修,应根据需要成立相应的"设备检修质量检验监督小组",其成员根据不同设备,由一至三级检验收人员组成。
3.2 设备检修质量的检查,检验与验收实行厂部、车间、班组三级机构的检验与验收工作。
3.3 设备质量检验三级机构:一级检验小组:由班(组)长、工程技术人员、工作负责人、现场值班人员组成;二级检验小组:由车间正、副主任、技术专责人及一级验收人员组成;三级验收小组:由生产副厂长、总工程师、安全生产部正、副经理、副总工程师、安全生产工程师、设备大修理监理人员、厂技术专责人、车间正、副主任、班(组)长组成。
3.4 厂部、车间、班组三级验收小组负责范围:一级(班组):辅助设备、工艺简单的工序、大坝中简单的异常处理之后;二级(车间):重要辅助设备、工艺较复杂的工序、大坝中的较大异常处理之后;三级(厂部)主要设备大小修,重要设备技术改造,大坝中的较大异常处理之后。
产品质量检验管理制度(三篇)
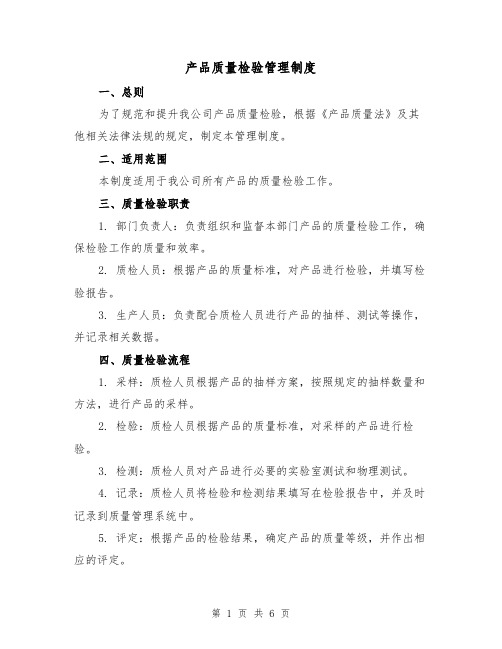
产品质量检验管理制度一、总则为了规范和提升我公司产品质量检验,根据《产品质量法》及其他相关法律法规的规定,制定本管理制度。
二、适用范围本制度适用于我公司所有产品的质量检验工作。
三、质量检验职责1. 部门负责人:负责组织和监督本部门产品的质量检验工作,确保检验工作的质量和效率。
2. 质检人员:根据产品的质量标准,对产品进行检验,并填写检验报告。
3. 生产人员:负责配合质检人员进行产品的抽样、测试等操作,并记录相关数据。
四、质量检验流程1. 采样:质检人员根据产品的抽样方案,按照规定的抽样数量和方法,进行产品的采样。
2. 检验:质检人员根据产品的质量标准,对采样的产品进行检验。
3. 检测:质检人员对产品进行必要的实验室测试和物理测试。
4. 记录:质检人员将检验和检测结果填写在检验报告中,并及时记录到质量管理系统中。
5. 评定:根据产品的检验结果,确定产品的质量等级,并作出相应的评定。
6. 处理:对不合格产品,按照公司《不合格品管理制度》进行处理。
五、产品质量标准1. 根据产品的性质和用途,确定相应的质量标准,包括外观、尺寸、性能等方面的要求。
2. 质检人员要熟悉产品的质量标准,并能正确使用相应的检验设备和工具。
3. 质检人员要及时了解产品质量标准的更新和变动情况,并及时调整检验方法和设备。
六、质量检验设备和工具1. 公司要配备适当的质量检验设备和工具,确保质量检验的准确性和可靠性。
2. 检验设备和工具要定期进行校验和维护,确保其工作正常。
3. 严禁私自更改、调整或使用不合格的检验设备和工具。
七、质量检验记录和报告1. 检验人员要将检验结果及时记录在检验报告中,并签名确认。
2. 检验报告要包括产品的基本信息、检验结果、检验日期等内容。
3. 检验报告要保存密封,并按规定的时间进行存档。
4. 检验报告要可以追溯,可供相关部门和客户查阅。
八、质量检验结果评定1. 根据产品的质量标准和检验结果,对产品进行合格、不合格的评定。
某公司作业品质评估管理制度
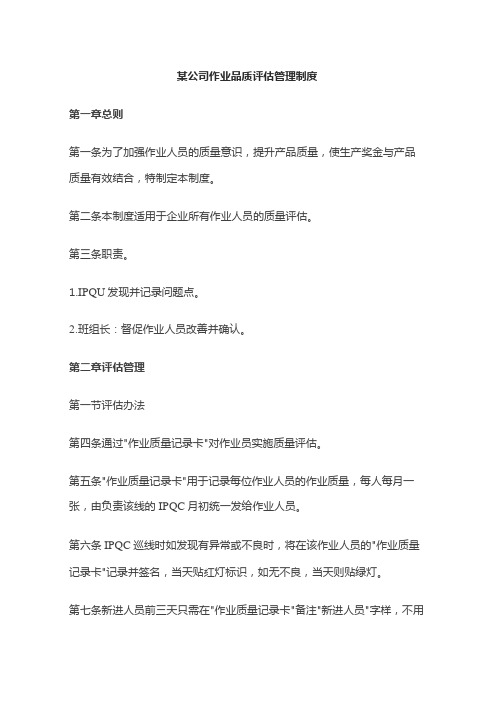
某公司作业品质评估管理制度第一章总则第一条为了加强作业人员的质量意识,提升产品质量,使生产奖金与产品质量有效结合,特制定本制度。
第二条本制度适用于企业所有作业人员的质量评估。
第三条职责。
1.IPQU发现并记录问题点。
2.班组长:督促作业人员改善并确认。
第二章评估管理第一节评估办法第四条通过"作业质量记录卡"对作业员实施质量评估。
第五条"作业质量记录卡"用于记录每位作业人员的作业质量,每人每月一张,由负责该线的IPQC月初统一发给作业人员。
第六条IPQC巡线时如发现有异常或不良时,将在该作业人员的"作业质量记录卡"记录并签名,当天贴红灯标识,如无不良,当天则贴绿灯。
第七条新进人员前三天只需在"作业质量记录卡"备注"新进人员"字样,不用贴灯。
第八条作业员有责任维护和保管好"作业质量记录卡",离职或晋升的作业员将该卡交还线上IPQC,如调动组别由作业员携带原卡到新岗位,否则该月不予考评。
第九条擅自涂改"作业质量记录卡"或更改"作业质量记录灯"(即红绿灯)者,除该月品质评估计O分外,另罚款30元。
第十条撕毁或丢失"作业质量记录卡"者,该月质量评估计0分,另罚款50元。
第十一条当红灯个数≤2时,班组长需及时督促作业员填写改善对策并签名;当红灯个数W3时,除以上纠正措施外,还需车间主任签字确认。
第十二条如因作业员作业不认真导致生产异常者,班组长及IPQC需协助作业员纠正作业,严重者可适当给予处分。
第十三条"作业质量记录卡"保存期限为3个月。
第二节质量因素考评办法第十四条此项作为评定生产奖金的系数,以1.0计满分。
第十五条由IPQC每月根据该月的"作业质量记录卡"红灯个数进行评分,经IPQC工程师核签后生效。
品检中的工序规范与作业指导

品检中的工序规范与作业指导在制造业中,品质检验是确保产品质量的关键环节。
为了保证产品的质量符合标准和客户的要求,制定适当的工序规范和作业指导显得尤为重要。
本文将探讨品质检验中的工序规范与作业指导的作用,并介绍如何制定和执行这些标准以确保产品质量的稳定性和可靠性。
工序规范是品质检验中的基础。
它定义了每个工序应该如何进行,以确保产品和生产过程的符合标准。
工序规范应该明确描述每个工序的目标、操作步骤、所需设备和工具、质量标准、验收标准以及记录和报告要求。
这些规范的目的是确保工序的标准化和一致性,从而最大程度地减少人为错误和质量缺陷的发生。
制定工序规范时,需要考虑产品的特性和客户的需求。
工序规范应该根据产品的设计和制造要求,确保每个工序都能满足相应的标准。
同时,工序规范应该参考行业标准和相关法规,以确保产品的合规性和安全性。
工序规范还应该考虑实际生产情况和设备的能力,以确保工序的可执行性和可控性。
作业指导是将工序规范转化为实际操作的指导文件。
作业指导应该详细描述每个工序的操作步骤、操作方法和注意事项,以确保操作人员能够正确地执行工序规范。
作业指导应该使用清晰简洁的语言,避免歧义和误读。
作业指导还应该包括相关的示意图和图片,以进一步提供对操作的理解。
制定作业指导时,需要密切与操作人员和工艺工程师的合作。
操作人员是直接执行工序的人员,他们对实际操作有着深入的了解和经验,他们的意见和建议对于改进工序规范和作业指导非常重要。
与此同时,工艺工程师应该负责制定作业指导,并确保其内容的准确性和可操作性。
实施工序规范和作业指导需要进行相关的培训和评估。
操作人员应该接受培训,确保他们了解工序规范和作业指导的内容,并能够正确地执行。
培训应该包括理论知识和实际操作的训练,以提高操作人员的技能和水平。
同时,还应该定期评估操作人员的执行情况,发现问题和改进的机会,并采取相应的措施进行纠正和改进。
品质检验中的工序规范和作业指导应该进行持续的监视和改进。
品质部管理制度
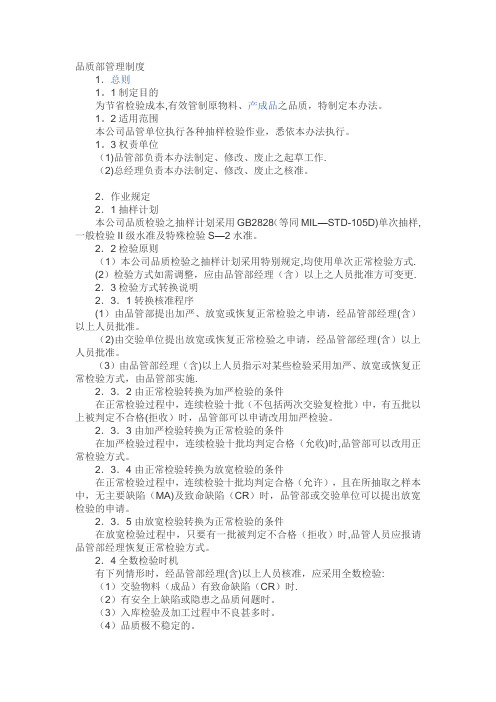
品质部管理制度1.总则1。
1制定目的为节省检验成本,有效管制原物料、产成品之品质,特制定本办法。
1。
2适用范围本公司品管单位执行各种抽样检验作业,悉依本办法执行。
1。
3权责单位(1)品管部负责本办法制定、修改、废止之起草工作.(2)总经理负责本办法制定、修改、废止之核准。
2.作业规定2.1抽样计划本公司品质检验之抽样计划采用GB2828(等同MIL—STD-105D)单次抽样,一般检验II级水准及特殊检验S—2水准。
2.2检验原则(1)本公司品质检验之抽样计划采用特别规定,均使用单次正常检验方式.(2)检验方式如需调整,应由品管部经理(含)以上之人员批准方可变更.2.3检验方式转换说明2.3.1转换核准程序(1)由品管部提出加严、放宽或恢复正常检验之申请,经品管部经理(含)以上人员批准。
(2)由交验单位提出放宽或恢复正常检验之申请,经品管部经理(含)以上人员批准。
(3)由品管部经理(含)以上人员指示对某些检验采用加严、放宽或恢复正常检验方式,由品管部实施.2.3.2由正常检验转换为加严检验的条件在正常检验过程中,连续检验十批(不包括两次交验复检批)中,有五批以上被判定不合格(拒收)时,品管部可以申请改用加严检验。
2.3.3由加严检验转换为正常检验的条件在加严检验过程中,连续检验十批均判定合格(允收)时,品管部可以改用正常检验方式。
2.3.4由正常检验转换为放宽检验的条件在正常检验过程中,连续检验十批均判定合格(允许),且在所抽取之样本中,无主要缺陷(MA)及致命缺陷(CR)时,品管部或交验单位可以提出放宽检验的申请。
2.3.5由放宽检验转换为正常检验的条件在放宽检验过程中,只要有一批被判定不合格(拒收)时,品管人员应报请品管部经理恢复正常检验方式。
2.4全数检验时机有下列情形时,经品管部经理(含)以上人员核准,应采用全数检验:(1)交验物料(成品)有致命缺陷(CR)时.(2)有安全上缺陷或隐患之品质问题时。
质量检验管理制度7篇

质量检验管理制度质量检验管理制度 7篇在学习、工作、生活中,很多场合都离不了制度,制度具有使我们知道,应该做什么,不应该做什么,惩恶扬善、维护公平的作用。
那么拟定制度真的很难吗?下面是小编收集整理的质量检验管理制度,供大家参考借鉴,希望可以帮助到有需要的朋友。
质量检验管理制度 11、质检人员要有一定的专业知识和较强的责任心,要坚持原则,严格标准,本着对质量负责的态度进行检验。
2、按图纸要求对所有外购件、外协件等进行检验,对质量不符合要求和规格超差的应及时退货。
3、按图纸要求对产品进行检验,重点是几何尺寸、焊接质量、耐压性能等,不合格品退回车间进行返修,重新检验合格后入库。
4、对中间产品进行抽检,发现不符合规定要求的要及时进行指正,避免产品完工后再做较大改动,造成不必要的损失。
5、质检人员对加工产品验收后应在派工单上签字,对外协件和外购件验收后应在入库单上签字,否则仓库人员有权拒收。
6、质检人员要熟悉产品的使用性能,对于重点部件和重点部位要严格检验,对于一般部件和一般部位可适当放宽,做到有的放矢,以达到降低成本,增加效益,提高工人的劳动积极性的目的。
7、妥善保管所有图纸,未经允许不准将图纸转借他人或私自带出公司。
质量检验管理制度 21---真理惟一可靠的标准就是永远自相符合质量检验部门安全职责1.企业在产品设计和工艺工装设计时,以及试制试验新产品的过程中,必须充分考虑可能出现的不安全因素,严格执行有关安全卫生的标准和规定;2.在检验产品质量时,应对其安全性能做出技术鉴定;3.参与有关安全技术方面的厂规、标准等的制订;4.协助有关部门提供安全技术信息和资料,审查和采纳安全技术方面的合理化建议;5.协同有关部门加强对职工的技术教育与考核,推广安全技术方面的先进经验;6.参加伤亡事故的分析调查,从技术方面提出意见或作出合理化分析,帮助确定事故原因和采取防范措施。
质量检验管理制度 31、目的未经检验或检验不合格的原辅材料及包装材料不投入使用,确保不合格的半成品不流入下道工序,防止不合格产品出厂。
品质检验作业流程规范

品质检验作业流程规范English.Quality Inspection Work Process Specification.1. Purpose.To establish a standardized work process for quality inspection activities to ensure the delivery of high-quality products and services.2. Scope.This specification applies to all personnel involved in the quality inspection process, including but not limited to:Quality inspectors.Production operators.Supervisors.Managers.3. Definitions.Quality inspection: The examination of a product or service to determine its conformance to requirements.Defect: Any non-conformance to requirements thataffects the function, appearance, or safety of a product or service.Inspection plan: A document that specifies the inspection criteria, methods, and frequency.Inspection report: A document that records the results of an inspection.4. Responsibilities.4.1 Quality Inspectors.Perform inspections in accordance with approved inspection plans.Identify and document defects.Report inspection results to the appropriate parties.Maintain and calibrate inspection equipment.4.2 Production Operators.Follow good manufacturing practices to minimize defects.Cooperate with quality inspectors during inspections.Take corrective action when defects are identified.4.3 Supervisors.Supervise the quality inspection process.Ensure that quality inspectors are adequately trained and equipped.Monitor inspection results and identify trends.Take corrective action to address quality issues.4.4 Managers.Establish and maintain the quality inspection system.Provide resources to support the quality inspection process.Review inspection results and make decisions on product or service acceptance.5. Procedures.5.1 Inspection Planning.Develop inspection plans based on product or service requirements and risk assessment.Specify the inspection criteria, methods, and frequency.Review and approve inspection plans.5.2 Inspection Execution.Perform inspections in accordance with approved inspection plans.Use appropriate inspection methods and equipment.Identify and document defects.Record inspection results on inspection reports.5.3 Inspection Reporting.Report inspection results to the appropriate parties, including production, engineering, and management.Identify trends and recommend corrective action.Maintain inspection records for future reference.5.4 Corrective Action.Investigate defects and determine root causes.Implement corrective action to prevent defects from recurring.Monitor the effectiveness of corrective actions.6. Quality Records.Maintain inspection plans, inspection reports, and corrective action records.Store quality records securely for future reference.7. Training.Provide quality inspectors with adequate training on inspection methods, equipment, and documentation.Refresher training shall be provided on a regular basis.8. Continuous Improvement.Regularly review the quality inspection process to identify opportunities for improvement.Implement improvements to enhance efficiency and effectiveness.Monitor the impact of improvements on product orservice quality.中文回答:质量检验作业流程规范。
产品检验管理制度 产品质量检验管理制度三篇

产品检验管理制度产品质量检验管理制度三篇产品检验管理制度产品质量检验管理制度11目的为了加强产品出厂质量检验,确保产品质量,维护消费者利益,提高企业信誉,特制定本制度。
2内容2.1化验室负责产品检验工作,独立行使检验职权,对产品逐批逐次进行检验,严把质量关,禁止不合格产品或产品不经检验出厂。
2.2化验人员根据GB/T27588、GB2757标准,进行产品出厂质量检险。
检验项目为感官、标签、净含量、酒精度、总酸、总酯、总糖、干浸出物、甲醇,达不到标准要求的判定为不合格产品,不准出厂。
2.3出厂检验时,同一班次、同品种、同一次投料的产品规定为一个生产批,对每批产品严格按抽样规则进行抽样,经出厂检验合格后开据合格检验报告方可出厂。
2.4出厂检验指标如有一项不符合规定要求,不准出厂,应重新自同批产品中抽取两倍数量样品进行复验,以复验结果为准,若仍存在不合格,则判定该批产品为不合格。
2.5检验包装物是否完好无损,不得有脏污和破损现象,如有上述现象则按不合格拒绝出厂。
3相关文件及记录《标准汇编》《销售档案》《出厂检验记录》产品检验管理制度产品质量检验管理制度2第一条为加强我厂产品质量保证工作,明确质量检验工作任务、范围、职责,特制定本制度,产品质量检验规章制度本制度在本厂范围内实施,品保部负责监督执行。
第二条本规定包含:产品质量检验制度、计量管理制度、各种标志的用处和定义、不合格品管理制度、钢材质量检验制度、外协件质量检验制度、能源计量管理等规定。
第二章:质量检验制度第三条品保部的基本职责:1、负责原材料外购、外协件、毛坯、半成品,直至成品出厂整个生产过程的质量检验工作。
2、执行不合格产品不出厂的原则,保证出厂产品符合规定的标准和技术要求,负责签发产品出厂质量检验合格证。
3、负责各种仪器,量具校验及管理。
4、负责客户之埋怨,分析处理。
5、负责统计技术之运用及各类检验报告整理。
6、员工品质教育之规划与训练。
7、各种检验标准之制定。
品质检验作业流程图

专业
一、IQC 作业流程:
1.1 正常进料检验流程:
1.2 物料紧急放行作业流程:
MRB:全称是Material Review Board, 中文意思是材料审查会议。
它是针对所有检验工作站发现产品异样状态暂时不能确定是否为缺陷的一种处理办法。
这里的工作站包括进料检验,过程检验,出货检验以及客户退回的产品。
根据不确定缺陷发现的位置,MRB会议可由不同的人召集。
补充:1.在材料待检前应标示好待检标示;
专业WORD.
2.在材料检验后需待一段时间后才有结果时,应「Hold」标示;
3.材料检验结果出来后应及时贴上相应标示并要求仓库分区摆放。
二、IPQC作业流程:
NG
OK
OK
OK
专业WORD.
专业WORD.
三、FQC 作业流程:
OK
NG
OK
四、OQC作业流程:
专业WORD.。
IPQC作业(管理)规范

IPQC作业规范1、目的:为确保制程上质量能符合客户要求,在制造过程中及时预警及改善,对产品质量进行有效的管控,以证明制造过程中一切符合生产条件, 使整个制程能防患于未然。
2、范围:适应于本公司所有产品的制程到制成过程中对人、机、物、法、环各环节影响到产品质量的管制。
3、权责:3.1 品质部:对生产全过程进行巡回检验,于不良发生之初期,能预先提出警示,以便导正缺点,减少不良率;对重大不良问题发生时,发出《纠正/预防措施报告》,追踪并验证改善措施的有效性。
3.2 工程部:负责不良品之失败原因分析,并提出有效对策及重整作业方式;对提出特采申请之项目或产品,提出分析及意见。
3.3 生产部:于制程巡回检验过程中发现有缺失时能了解并立即改善,以预防再发生;对重大问题发生时,对纠正措施导入产品,并对批量不良产品实施重工处理。
4、定义:4.1 IPQC(In-Process Quality Control):制程品质控制4.2 BOM(Bill of Material):材料清单4.3 ROHS(Restiction of Hazardous Substances):有害物质限用5、作业内容:5.1 产前检验:5.1.1. 产品上线前生产时,IPQC需确认有无新发行的BOM表、作业指导书、工程变更通知单等相关文件。
5.1.2. 材料上线前,IPQC必须依BOM、工程变更通知单核对材料领用清单,并将检验结果记录于IPQC检验报表内。
5.1.3. 产品上线开拉前,IPQC监督生产人员对仪器、工具设备进行静电检测。
5.2. 首件检验:5.2.1. 当每班开线、产品换线、材料更换、生产工艺更改和生产设备更换时,IPQC均要进行首件检验;同时参照《IPQC检验规范》作业。
5.2.2. 生产部生产的第一台产品,由拉长或测试员检查,并填写《首件检验报告》,检测合格后,交于工程PE/IE确认,确认结果合格再交给IPQC做首件确认。
质量检验管理制度(五篇)

质量检验管理制度一、总则1、目的为严格执行公司产品质量标准,加强产品质量管理,严格落实国家产品质量的有关规定和要求,确保公司产品生产的质量安全稳定,特制定本制度。
2、责任公司产品质量检验工作由公司品管部门负全责,生产部、技术部门协助配合。
并由品管部门负责最终给产品张贴质量合格标识,负责向顾客提供有关产品的质量证明文件。
凡因产品质量问题出现的客户退货、产品召回、纠纷等问题时,均由检验人员按规定承担全部责任。
3、质量检验主要环节质量检验主要环节分为。
原材料检验(依据相关购买合同条款进行检验)、产品生产过程检验和产品出厂检验三个方面。
4、检验方法直观检查与仪器检查相结合、抽检和普检相结合。
5、检验人员权限检验人员对产品质量拥有一票否决权,凡被检验认定为不合jg-001格的产品(或原材料),不得进行生产和销售。
6、检验记录每次检验都要有检验记录,并由相关人员签字后进行存档保管,产品原始检验记录至少保存二年以上。
二、原材进厂检验1、时机原材料入厂办理入库前,由采购部门通知品管部门对来料进行检验,未经过品管部门检验或检验不合格的来料不得办理入库手续。
2、查验内容主要检查产品合格证书是否齐全,查验产品外包装是否破损,是否受潮,雨淋。
3、质量抽检依据公司标准和与供应商签订的相关合同标准,对不同批次产品进行抽检,如两项以上指标不合格,则判定为不合格品,并通知采购部门进行退货处理。
合格品填写来《来料产品质量检验单》签字后交付采购部门办理入库手续。
三、生产过程检验1、生产过程检验原则(1)原材料批次更换时必须取样检验。
jg-001(2)原纸、纱线换卷时必须取样检验(3)生产线因故障停机,再开机后生产产品必须取样检验。
(4)每卷纸下线后必须取样检验。
(5)每卷纸生产过程中必须有3-____次取样检验。
2、主要检验内容(1)生产过程取样检验主要检测“定量(克重)、抗张力、撕裂度,耐破度”四项批标。
(2)产品下线及每卷纸生产中间应按照公司产品规定的检测内容,进行不少于____个项目的内容检验(详见《产品标准检测表》)3、产品质量判定。
品质检测管理制度

品质检测管理制度一、引言品质检测管理是企业运营中至关重要的一环,通过有效的品质检测管理制度可以确保产品和服务的质量符合客户的需求和期望,提升企业的竞争力。
本文将介绍一套完善的品质检测管理制度,帮助企业建立和实施高效可行的品质检测管理体系。
二、管理目标1. 提供高品质产品和服务:品质检测管理的首要目标是确保生产线上的产品符合国际标准和客户的要求,经过严格检测后才能投放市场。
在提供高品质产品的基础上,还需要提供专业、周到、高效的售后服务,以满足客户的需求和期望。
2. 持续改进:品质检测管理制度需要定期评估和改进,以适应市场和客户的需求变化。
通过收集和分析检测数据,确定潜在问题和改进机会,并采取相应措施进行持续改进,不断提升产品和服务的品质。
三、质量控制流程1. 产品开发阶段:在产品设计和开发阶段,需要制定明确的质量标准和检测要求,确保产品能够满足设计和市场要求。
通过设计验证、样品检测和试制品评估等环节,对产品进行全面的质量控制,确保产品能够满足客户的期望。
2. 原材料采购与质量控制:在原材料采购阶段,需要建立供应商评估机制,筛选出优质的供应商,并制定明确的原材料质量标准和检测要求。
在收货时进行严格的质量检验,确保原材料符合标准,不影响产品质量和安全。
3. 在线检测与过程控制:在生产线上,需要建立有效的在线检测机制和过程控制措施,监控生产过程中的关键参数,及时发现并纠正潜在问题,确保产品质量稳定可靠。
通过合理规划检测频次和检测项目,提高工作效率,降低不良率。
4. 产品出货检验:在产品出货前,通过全面检验确保产品符合质量标准和客户需求。
对各项指标进行测试和评估,包括尺寸、外观、性能等多个方面,确保产品质量稳定,达到客户的期望和要求。
5. 售后服务与投诉处理:品质检测管理制度还需要涵盖售后服务和投诉处理方面的内容。
确保及时响应客户的问题和投诉,并制定相应的处理措施,以满足客户的需求并提升客户满意度。
四、质量管理人员培训为了有效实施品质检测管理制度,需要培训和提升质量管理人员的专业技能和知识水平。
品质检验质量管理

抽样检验的基本概念
1、抽样检验的概念 1) 所谓抽样检验是指从交验的一批产品(批量为
N)中,随机抽取一个样本(由n个单位产品组 成)进行检验,从而对批产品质量作出批断的 过程。抽样检验示意如图4-1所示。 2) 抽样检验的目的是“通过样本推断总体”,而其 期望则在于“用尽量少的样本量来尽可能准确地 判定总体(批)的质量”。而欲达到这一目的和 期望,传统的“百分比抽样”是不科学的、不合 理的,通过多少年来的理论研究和实践证明只 有采用“统计抽样检验”才能保证科学、合理地 实现这一目的和期望。
确认 3、制程品质异常的跟踪、确认及处理 4、特采案件的确认与跟踪处理 5、原材料、半成品和成品的检验判定及审核
确认 6、原材料或成品不合格项联络与改善后的检
定作业
16
7、各项检验报表的审核确认 8、托外加工成品检验及记录 9、品质检验人员的工作安排与调度 10、品检人员的工作安排与调度 11、制程检验及记录 12、托外加工物品制程检验及记录 13、供应商的辅导 14、客户品质抱怨之处理 15、上级交办事项之执行及回报
20
品管课机能: 1、供应商提供样品的审查与确认 2、各项统计资料的收集、整理、分析,针
对不符合项提出改善要求,对改善成效 的审查与确认 3、重要不合格的判定及跟踪处理 4、成品出货的确认放行 5、检验标准的制定和检验作业指导书的拟 定与审核 6、检验测量和试验中仪器及治具的规划
21
7、 月品质检讨会议的联系及会议决定事项的 记录及跟踪处理
22
16、新产品试制过程中的样品确认 17、成品退货的检定与分析提报 18、样板的标识与管理 19、质量会议资料的整理与提报 20、质量会议的收集、传迅与处理 21、检测设备的管理,计量仪器有效性的监察 22、成品各项功能试验 23、新产品新规格之品质验证 24、新模具之品质检验 25、商检样品确认 26、上级交办事项之执行及回报
IPQC作业管理规范

5.1.3IPQC首件确认无误后,即签核首件品一份。与《首件确认表》一起交生产单位挂于
XXX汽车传动轴有限公司
文件编号
WI-QC-006
文件名称
IPQC作业指导书
页码
2/2
版本
A/0
`机台旁;同时做好首件检测报告。
5.2巡回检查
5.2.1生产单位接到首件板后开始正常批量生产,IPQC则对所有机台进行巡回检查.
5.3.2检验结果合格,则在该批料件的标识卡上签“OK及姓名”。否则,以红色不合格品标识卡标识。不合格品按《不合格品管理程序》处理。
5.3.3巡检、转序检查前,必须先找到相应的图纸、检验规范、作业指导书等相关资料作为参考依据。
5.3.4外发加工产品时,检验依4.3.1—4.3.3执行。
5.3.5、预防措施报告》。
7.4《纠正、预防措施报告》
5.4报表填写
5.4.1IPQC根据检验结果填写《IPQC巡检报告》交主管审核后存档。
5.4.2每个月IPQC要填写《IPQC检验统计表》,交品质主管作为统计技术参考资料。
6.参考文件:
6.1《不合格品管理程序》
6.2《抽样计划规范》
7.表单记录:
7.1《首件确认表》
7.2《IPQC巡检报告》
7.3《IPQC检验统计表》
5.2.2每2H由IPQC负责抽检一次,每次每台机抽2PCS进行尺寸、功能等方面检查,取10PCS进行外观检查。并将检验结果记录于《IPQC巡检报告》中。尺寸判定标准为AC:0,RE:1,外观判定标准为主要缺陷和严重缺陷AC:0,RE:1,轻微缺陷AC:1,RE:2。巡查中发现的不合格品应做好标识并隔离。
- 1、下载文档前请自行甄别文档内容的完整性,平台不提供额外的编辑、内容补充、找答案等附加服务。
- 2、"仅部分预览"的文档,不可在线预览部分如存在完整性等问题,可反馈申请退款(可完整预览的文档不适用该条件!)。
- 3、如文档侵犯您的权益,请联系客服反馈,我们会尽快为您处理(人工客服工作时间:9:00-18:30)。
品质检验作业管理一、来料检验管理(IQC)1、什么是来料检验:对采购的原材料,辅料,外购件,外协件及配套件等入库前的接收检验。
2、来料检验的种类:(1)、首批样品检验的范围:①、供应商首次交货。
②、供应商的产品在设计上,结构上有重大改变。
③、供应商的产品在工艺上有重大改变。
(2)、成批的来料检验方法:①、分类检验法:以质量特性的重要性和缺陷严重度分成三类:。
A类:严格实施全项检查。
B类:对必要的质量特性进行全检或抽检。
C类:可作少量项目的抽样。
②、抽样检验法:对大批量来料,以双方约定的检验水平抽样方案,实行抽样检验。
3、来料检验作业要领:(1)、来料作业流(见品管部的来料检验作业流程图)(2)、作业要领:①、核对单据:来料时,仓库应依“采购订购单”和供应商“送货单”核对品名,规格,数量,包装,无误后将来料置于待验区。
②、发出检验通知:。
由仓库填材料检验通知单”给IQC。
IQC及灯杯组接到通知时先抽样检查后才安排检验。
③、检验并贴标示:对于合格物料,检验员应贴上绿色标签,不合格品贴上红色标签。
④、特采:依特采,流程进行作业。
⑤、拒收与不合格品处理:。
拒收:贴不合格标签后随检验报告送仓库处理。
不合格品处理:贴上标签后送回仓库,依不合格品处理流程进行作业。
二、制程检验管理(IPQC)1、制程检验目的:制程检验目的是防止在制程中出现大批不合格品,流入下道工序,维持生产过程处于正常的受控状态。
(1)、制程检验种类:①、首件检验:首件是指生产刚开始的第一个工件,如加工过程中换人,换料,换机台,停电,故障排除,工装/模具调整后加工的第一个工件。
②、首件检验方法:一般采“三方三检制”先由操作员自捡、再由班组长检、最后由QC员专检。
③、首件检验原则:。
首件专检合格后,应打上记号,并做好记录。
无论在任何状况下,首件不合格,不准生产。
(2)、巡回检验重点:①、什么是巡回检验:是QC员在生产现场制造工序及其产品和生产条件进行巡回的监督检验。
②、巡回检验重点:检验重点是工序质量控制点,检验结果应标示在控制图上。
③、巡回检验要求:。
应依检验指导书的频率进行检验,并做好记录。
应主动帮助操作员建立“品质第一”的品质意识,分析质量原因提高操作技术。
应严格把关,发现问题时,应与班组长共同找出原因才恢复正常生产,同时必须对上次巡检后到本次巡检前所有的加工件进行复检,以保证设有不合格品流入下道工序。
(3)、生产部操作员工检验:①、操作员应严格按工艺,指导书进行作业及自检,互检。
②、当生产中出现不合格品时,应立即与合格品分离,将不合格品放在指定地点,并立即报告班组长。
(4)、制程检验不合格处理:①、当不合格发生时,应通知班组长进行返工。
②、对于返工产品应由QC员复检,才可进入下道工序。
③、无法返工或返工部分不合格者,应通知品管部经理,车间主管进行分析处理,恢复正常后才能继续生产。
④、不合格品应予以隔离并贴标识,以防错用、误用。
三、最终检验管理(FQC):1、什么是最终检验:最终检验是企业验证产品是否符合标准的最后机会,所以是企业对质量保证的重要内容。
2、最终检验要求:(1)、应严格按检验标准进行禁止任何不合格品包装。
(2)、客户有特殊要求时,应依要求进行检验,必要时,向客户提供有关质量记录。
3、最终检验方式:最终检验可以全检或抽检方式进行,具体可视产品特点及工序而定。
4、最终检查作业要领:(1)、产品包装前检查:依成品离开生产线时,所进行的质量检验,大部分是在进行包装的生产作业。
(2)、包装品质检验控制点的设置:①、首件产品确认。
②、包装内容核对。
③、包装材料,如卡纸,说明书,吊牌、贴纸、不干胶、海棉、内盒、彩盒、外盒、吸塑盒、纸箱……检验。
④、包装过程中的不确定因素,如配套方式,附件放置……。
(3)、包装、过程的巡检:产品外观、尺寸、结构、功能、放置、印字……检验。
(4)、包装品质检验的巡检记录。
(5)、品质异常的反馈与处理,应及时报告,同时跟进改善结果,直到完全合格为止。
5、成品入库检验:(1)、核对入库产品(规格、型号、数量、品名)与入库单,是否相符。
(2)、检验准备:依产品检验规范实施。
(3)、检验实施:全捡/抽检。
(4)、允收处理:合格品盖品质PASS章/贴合格标签/填写检验报告表。
(5)、拒收处理:贴不合格标签/填写检验报告表/生产部返工。
(6)、生产部返工应进行复检,合格依允收方式处理,不合格品依不合格品处理流程作业。
四、出货检验管理(OQC):(1)、QC员负责到指定区域实施抽检/全检。
(2)、QC员依检验作业指导书进行检验,验后填写检验报告。
(3)、检验后处理:合格品才能出货,不合格品依不合格品处理流程作业。
五、不合格品管理:1、什么是不合格品:不合格品又称不良品,依不合格程度可分为:废品,次品,留用品,返工(修)品。
2、不合格品产生的原因:3、不合格的标识:(1)、标识物的选择:①、标识牌:如待验牌、暂收牌、合格牌、不合格牌、待处理牌、送货牌、查验牌、返工牌、返修牌、报废牌……主要用于大量货物或成批的产品标识。
②、标签或卡片:使用时,将判别结果注明在标签或卡片上,证明物料(产品)的品名,规格,颜色、材质、供应商、工单号、日期、数量……等内容。
③、色标:有园形的或方形的,大约0.5cm~2cm大小的有色贴纸,可直接贴在货物/产品的不良部位。
也可贴在产品的外包装上。
(2)、标识物的颜色:①、绿色:代表受检产品合格,一般贴在货物/产品的右下角,易于看见的地方。
②、黄色:代表受检产品品质有争议,暂时无法确定,一般贴在货物/产品的右上角易于看见的地方。
③、红色:代表受检产品不合格,一般贴在货物/产品的左上角易于看见的地方。
(3)、标识物的应用:①、来料不合格的标识:来料经IQC检验后不合格,应马上做标识,挂上待处理的标识,报请部门主管裁定处理,并按最后的审批意见,改挂相应的标识,如暂收,挑选,退货等。
②、制程中不合格品的标识:不合格品箱:员工自检,互检,QC专检的不合格品,员工应自动的放入不合格品箱,待该单完成或下班组长清点数量时,贴上不合格品的“标签”并搬到不合品区整齐放置。
暂时无法确认的品质问题,QC可在该批货品/产品外包装或容器上挂“待处理”标识牌,并放置在指定地点,等待处理。
③、库存不合格品标识:QC定期对库存物品进行品质评定,对不合格品外包装上挂上不合格标识牌或帖上不合格标签,对暂时无法处理的不合格品可挂上“待处理”标识,等待处理结果。
4、不合格品的隔离:(1)、不合格品区域规划:①、不合格的物品/产品没有品管部的书面处理通知,任何部门或任何人都不得擅自处理或使用。
②、不合格品的处理必须在品管部的监督下进行。
报废:由有关单位在QC监督下送到指定地点进行处理。
返工:责成有关部门进行返工,具体包括:返工,返修,挑选。
让步收货:QC接受通知时取消所有标识,改成合格标识。
其他不合格的处理规定:均由QC按处理通知,协助相关单位进行处理。
5、不合格品的处理:(1)、让步收货(ADD):也称“特殊”接受,又称“偏差接受”当该批货品被特许进厂后,IQC应该在该批货上作“特采”标识,同时将信息传达给使用部门,让相关部门做对应行动。
(2)、挑选收货:对来料基本合格,但其中存在有不定数量的合格品时,在入库前或使用前,由工厂组织人力剔除不良品,然后才入库或投入生产,称之为“来料挑选”如果未经挑选投入生产边选边做,称之为“挑选收货”。
(3)、返工与返修:是指对不合格品重新加工和修理,使之达到合格的要求;QC应做如下控制:①、QC应说明返工,返修之品质要求及重点。
②、把握返工品在制程上品质检验与试验方法。
③、记录返工品品名,规格、数量。
④、对返工品进行复检验收。
(4)、退货:不论被退货是自制还是外购,退货前应考虑:①、该批料可否有其他方式被接受,如挑选返工。
②、所退的货是否组成产品的重要部份,若被采用,对产品的功能(性能)是否造成严重影响。
③、若退货,是否会造成停工待料,若强行使用是否会造成重大的品质隐患。
(5)、报废:进行报废前应考虑:①、若进行报废,工厂是否会造成重大经济损失。
②、是整体报废,还是部份报废,产品组件是否可拆下移作他用。
③、批量进行报废时,应注意报废批中,是否能挑选出见收品。
6、不合格品记录:(1)、不合格品记录方法:①、检验记录:如IQC来料检验报告,IPQC巡检报表,产品检验表等。
②、品质评审与处理记录:如IQC退货报告,品质鉴定单,不合格品报告表,特采申请表,物料/产品报废申请表等。
③、品质改善报告:如品质纠正与预防措施,品质异常处理单。
④、品质分析记录:如月度品质状况分析报告。
(2)、不合格品的记录内容:①、不合格品的名称,规格,颜色、编号。
②、不合格品的订单号,生产日期,生产车间。
③、不合格品的比率。
④、不合格品的缺点描述(缺点项目及缺点数)。
⑤、相关部门的评审结论。
⑥、不合格品的处置意见及实施状况总结。
对不合格品纠正及预防措施与效果验证结果。