改善报告案例
工厂改善案例分析报告范文

工厂改善案例分析报告范文一、案例背景本案例分析报告旨在通过具体工厂改善案例,探讨生产效率提升、成本控制、质量管理以及员工参与度提高等方面的实践与效果。
所选工厂为一家中型企业,主要生产电子产品配件,近年来面临激烈的市场竞争和成本压力。
二、改善前状况改善前,该工厂存在以下问题:1. 生产效率低下,设备老化,工艺流程不顺畅。
2. 成本控制不严格,原材料浪费严重。
3. 产品质量不稳定,客户投诉率高。
4. 员工参与度低,缺乏改进意识和动力。
三、改善目标1. 提升生产效率,减少设备故障率。
2. 严格控制成本,减少原材料浪费。
3. 提高产品质量,降低客户投诉率。
4. 增强员工参与度,培养改进文化。
四、改善措施1. 设备升级与维护:投资更新关键生产设备,并对现有设备进行定期维护,以减少故障率和提高生产效率。
2. 工艺流程优化:重新设计工艺流程,消除不必要的步骤,实现生产流程的简化和标准化。
3. 成本控制:实施精细化管理,对原材料采购、使用和库存进行严格监控,减少浪费。
4. 质量管理体系建设:建立全面的质量管理体系,从原材料检验到最终产品出厂,每个环节都有严格的质量控制。
5. 员工培训与激励:开展定期的员工培训,提高员工技能和质量意识。
同时,设立奖励机制,鼓励员工提出改进建议和参与改进活动。
五、改善过程1. 项目启动:成立专门的改善小组,明确改善目标和责任分工。
2. 现状分析:收集数据,分析生产效率、成本、质量等方面的问题。
3. 方案设计:根据分析结果,设计具体的改善措施和实施计划。
4. 方案实施:按照计划逐步实施改善措施,包括设备升级、工艺调整、培训等。
5. 监控与调整:在实施过程中,持续监控效果,并根据反馈进行调整优化。
六、改善效果1. 生产效率提升:通过设备升级和工艺优化,生产效率提高了20%。
2. 成本降低:原材料浪费减少,单位产品成本下降了15%。
3. 质量提升:客户投诉率下降了30%,产品一次合格率提高到98%。
改善案例报告
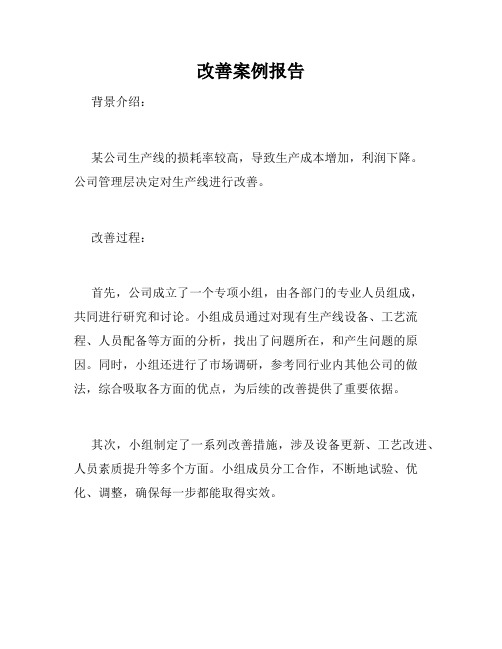
改善案例报告背景介绍:某公司生产线的损耗率较高,导致生产成本增加,利润下降。
公司管理层决定对生产线进行改善。
改善过程:首先,公司成立了一个专项小组,由各部门的专业人员组成,共同进行研究和讨论。
小组成员通过对现有生产线设备、工艺流程、人员配备等方面的分析,找出了问题所在,和产生问题的原因。
同时,小组还进行了市场调研,参考同行业内其他公司的做法,综合吸取各方面的优点,为后续的改善提供了重要依据。
其次,小组制定了一系列改善措施,涉及设备更新、工艺改进、人员素质提升等多个方面。
小组成员分工合作,不断地试验、优化、调整,确保每一步都能取得实效。
最后,在经过多次尝试后,公司成功地实施了一系列改善措施。
生产线的损耗率大幅下降,同时,产品的质量也有了明显的提升。
这一切,为公司的发展增添了助力。
改善结果:通过此次改善,不仅使公司得到了一次振奋,同时也发现了公司存在的不足和不良习惯。
公司经过不断的调整和完善,进一步提高了生产效率、降低了生产成本、改善了产品质量。
接着展开:从这次改善中,我们可以看到,一个企业想要成功,离不开不断地改进,不断地突破自我。
这需要有一个良好的团队合作,更需要领导的正确决策和坚定信念。
同时,对于一次成功的改善,我们也需要认真总结其成功的经验,在今后的发展中进一步提高业务技能和经验。
结论:改善不是一次性活动,而是一个企业需要持续关注的重点。
事实证明,在面对问题和挑战时,企业需要有高度的敏感性和反应力,只有不断地突破追求,才能在竞争中占据有利位置,实现可持续发展。
结果改善案例分析报告

结果改善案例分析报告近年来,随着企业竞争的加剧和市场环境的不断变化,越来越多的企业面临着业绩下滑、利润减少等问题。
为了应对这些挑战,企业需要不断寻求改善措施并推动其实施。
本文将以某公司为例,分析其改善案例并提出相应的建议。
某公司是一家制造业企业,主要生产汽车配件。
然而,最近几年,该公司面临着利润下降、产品质量问题、客户投诉增加等诸多挑战。
为了改善这些问题,公司制定了一系列的改善方案,并在一年的时间内进行了执行。
首先,针对利润下降的问题,公司进行了成本管理方面的改善。
通过对各个生产环节进行精细化的成本控制,公司降低了生产成本,提高了利润率。
例如,针对原材料采购成本,公司进行了供应商谈判并优化了供应链管理,降低了原材料采购成本;同时通过改善生产工艺和提高设备利用率,减少了设备折旧和生产周期,降低了生产成本。
其次,针对产品质量问题,公司进行了生产流程优化和质量控制方面的改善。
公司引入了先进的生产技术和质量管理方法,并对生产过程进行了全面的监控和管理。
通过合理安排生产流程、提高操作技能、加强设备维护等措施,公司成功降低了产品不良率。
此外,公司建立了完善的客户反馈机制,及时收集和处理客户投诉,并对相关问题进行深入分析和改进。
最后,为了应对客户投诉增加的问题,公司进行了客户关系管理方面的改善。
公司加强了与客户的沟通和合作,提高了产品的定制化能力和交货期可靠性。
此外,公司对销售团队进行了培训,加强了售前售后服务,提高了客户满意度。
通过以上一系列的改善措施,该公司取得了显著的效果。
利润率提高了10%,产品质量得到了显著改善,客户投诉量减少了20%。
这些改善不仅为公司带来了经济效益,也增强了公司在市场中的竞争力。
基于以上分析,针对该公司的改善案例,我们提出以下建议:首先,公司应继续注重成本管理,寻找降低成本的机会,并进一步提高利润率。
其次,公司应持续改进生产流程和质量控制,加强员工培训和设备维护,进一步提升产品质量。
化工企业改善案例报告范文

化工企业改善案例报告范文1. 简介本报告旨在介绍化工企业改善案例,探讨如何通过改进管理和工艺流程来提高企业的效益和竞争力。
本案例以某化工企业为例,通过引入先进的生产技术和管理理念,取得了显著的改善效果。
2. 基本情况该化工企业是一家中型企业,主要从事某种化学原料的生产和销售。
由于市场竞争的加剧,企业利润逐年下降并面临被淘汰的危险。
为了解决这个问题,企业决定进行全面的改善。
3. 改善方案3.1 引入先进的生产技术企业决定引进一套先进的生产设备,该设备具有高效率、低能耗的特点。
通过对生产设备进行改造和升级,生产效率得到了显著提高。
与此同时,企业还加大了对员工培训的力度,提高了员工的技术水平,使其能够更好地操作和维护新设备。
3.2 优化供应链管理传统的供应链管理方式效率低下,存在很多浪费和瓶颈。
为了提高供应链管理的效率,企业决定引入先进的ERP系统,实现供应链的透明化和自动化。
通过ERP系统,企业能够更好地控制原材料的采购和库存,减少了库存的积压和过剩,降低了原材料的损耗和浪费。
3.3 推行精益生产企业决定推行精益生产的理念,通过持续改进和消除浪费来提高生产效率。
为此,企业组织了一支专门的改善团队,负责进行现场改进和员工培训。
通过对生产流程的详细分析和改善,企业成功地减少了生产周期和生产成本,提高了产品的质量和交付能力。
3.4 加强质量管理质量是化工企业的核心竞争力之一,为了提高产品质量,企业决定引入全面质量管理体系,采取有效的措施控制和改进产品质量。
企业的质量管理部门定期对生产过程进行检查和监控,对不合格产品进行追溯和处理,确保产品符合国家和行业的相关标准。
4. 改善效果经过一段时间的努力,企业取得了显著的改善效果:- 生产效率提高了30%,生产成本降低了20%;- 产品质量得到了显著的提升,不合格率下降了50%;- 储备物料的积压量减少了50%,库存周转率提高了30%;- 员工的工作积极性和满意度得到了提高,员工流失率下降了20%。
案例:改善A3报告
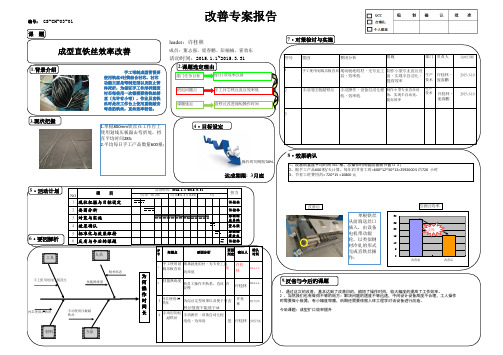
编号:GS-CH-03-01leader :许桂林成员:董志强、庞春鹏、彭楠楠、霍效东活动时间:2015.1.1~2015.3.31NO 1234改善比1071075改善前286改善后16现场就地取材,无专业工具效率低许桂林3为保证定型效果以及便于弯制否铁丝强度不能低于4#4手动操作,设备自动化程度低,效率低是许桂林衬芯使用4#铁丝2015/1/6手动用压板敲铁丝2015/1/61月第3周~2月第4周3月标准化与效果维持彭楠楠霍效东效果确认董志强活动时间:2015.1.1~2015.3.311月第一周~2周反省与今后的课题许桂林担当项 目要因分析许桂林对策与实施彭楠楠庞春鹏现状把握与目标设定许桂林改善专案报告51015202530改善前改善后成型直铁丝效率改善7‧对策检讨与实施6‧要因解析1.背景介绍4‧目标设定课題3.现状把握8‧效果确认5‧活动计划达成期限: 3月底2.课题选定理由人员工具材料精神状态方法手动使用压板敲铁丝衬芯使用4#铁丝技能熟练度为何操作时间长部门任务目标每月1项效率改善班组问题点手工衬芯铁丝直丝效率低课题选定直铁丝改进缩短操作时间许桂林2014-1-6否新员工操作不熟悉,直丝较慢技能熟练度22014-1-6许桂林是手工使用划线压板直丝1确认时间确认人要因判定要因分析问题点序号手工使用划线压板直丝9.反省与今后的课题1、通过这次的改善,基本达到了改善目的,缩短了操作时间,较大幅度的提高了工作效率。
2 、当然我们也有做得不够的地方:解决问题的速度不够迅速,中间设计设备高度不合理,工人操作时需要做小板凳,有小幅度弯腰,后期还需要依据人体工程学对该设备进行改造。
今后课题:成型扩口效率提升改善后43%改善后效率1.单根800mm 铁丝在工作台上使用划线压板敲击弯折处,捋直平均时间28S ;2.平均每日手工产品数量600根;操作时间缩短30%32015-3-10生产技术制作小型专业直丝设备,实现半自动化,提高效率手动操作,设备自动化程低,效率低手动用压板敲铁丝22015-3-10许桂林、庞春鹏生产技术制作小型专业直丝设备,实现半自动化,提高效率现场就地取材,无专业工具,效率低手工使用划线压板直丝1完成日期负责人部门措施要因分析要因序号1、改善后直丝平均时间16S/根,总操作时间较改善前节省12 S ;2、据手工产品600 根/天计算,每年约节省工时=600*12*30*12=2592000 S 约720 小时3、节省工时费用约= 720*15 =10800 元手工弯制成型管需要使用铁丝+衬簧组合衬芯,衬芯功能主要是弯制定型以及防止管体死折,为保证手工件形状精度衬芯每使用一次都需要将铁丝捋直(允许有小弯),作业员直铁丝时是在工作台上使用重物敲击弯曲的铁丝,直丝效率较低。
8D报告案例
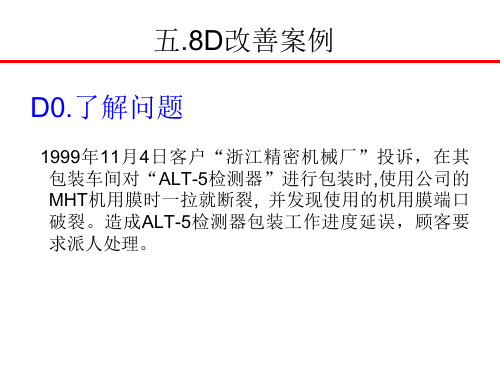
–1. 文件标准化,修改搬运、贮存作业标准书. –2. 对库管课员工进行标准的培训宣贯.
五.8D改善案例
D8.恭贺小组
• 成效计算:以每卷成本50元计,改善前自99年5-1月统计 破损200卷,损失金额10,000元;改善后虽成本投入增加 1元,同样可减少损失9,800元.
五.8D改善案例
D5.长期对策
5.1决定采用长期对策
– 1.修改搬运、贮存作业方法,将原来搬运和堆放高度3层改 为2层,减少重力。 – 2.改变包装方法,每卷产品用托盘运装。 – 3.包装箱内部增加泡沫,以减少碰撞冲力。
五.8D改善案例 5.2验证长期对策(小批量验证)
小组采用同一规格20μMHT机用膜产品按照三 项措施各100卷进行小批量验证
5
25
0
0
A BC DE F GH
五.8D改善案例
4.3 确定根本原因并识别可能的方案
• 通过小组因果分析,验证统计确定产品堆放高度过高 、包装方式不合理是导致产品端口受损根本原因。
• 识别可能的解决方案。
– 修改搬运、贮存作业方法,将原来搬运 和堆放高度3层改为 2层,减少重力。
– 改变包装方法,每卷产品用托盘运装。 – 包装箱内部增加泡沫,以减少碰撞冲力。 – ……。
•经确认后,没有不良品再流出的可能,不会再扩大损 失。
五.8D改善案例
D4. 原因分析
•识别可能原因(因果图) • 选择最有可能的原因(矩阵图) • 确定是否是根本原因 • 识别可能方案
五.8D改善案例
4.1 因果分析
环
法
库房湿度大
精益改善案例提案改善报告

精益改善案例提案改善报告一、背景我们所处的公司是一家生产化妆品的企业,由于市场竞争激烈和内部管理不足等多种原因,导致生产效率低下,产品质量不稳定,在市场上的竞争力较弱。
为此,我们决定通过精益管理的方法来对生产过程进行改善,提高生产效率和产品质量,以增强企业的市场竞争力。
二、问题定义通过对企业生产过程的分析,我们发现以下问题:1. 生产过程中存在大量浪费,如原料浪费、等待时间浪费、生产线下停机时间浪费等,导致生产效率低下;2. 生产线某些工站出现了制造不良品的情况,存在质量问题;3. 生产过程中缺乏可视化管理,员工难以及时发现和解决问题。
三、改善方案针对上述问题,我们提出以下改善方案:1. 实施6S管理6S管理是指整理、整顿、清洁、清点、标准化和维护的管理方法,通过对现场进行整理、清理、标识等操作,去除生产过程中的浪费,提高生产效率。
同时,开展6S培训,增强员工的职业素养和安全意识,营造整洁有序的工作环境,提高工作效率和生产质量。
2. 引入可视化管理针对生产过程中缺乏可视化管理的问题,我们将引入可视化管理技术,将生产过程中的各项数据实时呈现在生产线上方的显示屏上,让员工随时了解生产状况,更好地发现和解决问题。
3. 实施质量管理和问题解决在生产过程中,存在不良品生成的情况,我们将加强质量管理,对生产过程中的各项质量参数进行监控和检测,及时发现和解决问题。
同时,我们将建立定期例会和工作汇报机制,及时解决员工工作中遇到的问题,为员工提供更好的工作支持。
四、实施计划通过培训,将6S管理理念传递至员工,开展整理、整顿、清洁等活动,打造整洁有序的生产环境,提高生产效率和产品质量。
引入并实施可视化管理系统,打造实时监控的全新生产模式,加强员工生产意识和工作效率,实现生产流程信息和数据的可视化和透明化。
五、效果预期通过精益管理的方法,我们期望实现以下效果:1. 生产效率提高:通过实施6S管理和改善流程,去除浪费,提高生产效率,降低生产成本。
工厂改善报告汇总
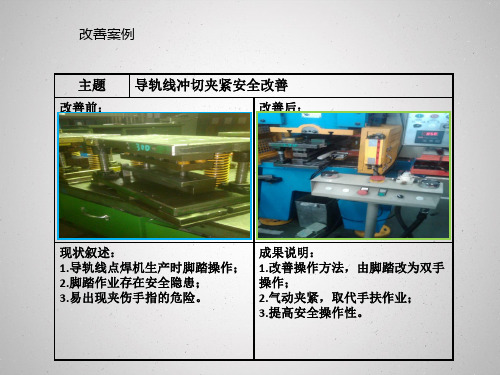
改善前 无
改善后
改善前问题点
改善后优点
因机床无水泵,加工过程中刀件易损坏, 在机床上安装循环水泵,安装冷却水管,对刀具进行冷却;机
严重影响刀具寿命,及加工效率,使刀 具寿命缩短,百分之六十左右,大约每
器 员设工计对A此过dd程给Y予中o设存ur计在T和一ex安定t 装缺道陷具,,需使要正额常外损加耗装下冷降却,水降泵低,了我生公产司
改善前 无
改善后
改善前问题点
改善后优点
由于空气湿度较大,空气机系统设备运 时形成水份过多,在过滤器中及储气罐 内积储,平均两至三小时放水一次也难 保证空气水分滤净,从而保证不了涂装 喷漆用气。
改善后:
从 棉节的省造A成人dd员喷Y漆及o质劳ur量动T缺强ex陷度t 。方面考虑,保证了涂装喷漆用气质量,
方案:修改设备程序,删除程序多余步骤,减少不必要的等待
时 和,间由,A原增dd来加Y的停o4止u0r秒时T的/e件x缓t提冲升,到减31小.5设秒备/件震,动整,体使提设升备效动率作2更1.2加5%柔,
提升后月生产能力可达10000多套,满足交付要求,并去掉手 动安装线;改善后能源节省:两台设备总功率为3千瓦,每年 可节省电费5000多元; 改善后人工节省:按每年12万套计算,可节省工时3400小时, 节省80000多元;
开A泵漆管阀门A1,B泵B2漆管,控制人员去换漆,日可节约60 分钟。
改善案例-〔 YFC组D立i机a效gr率a提m升〕
改善前 无
改善后 无
改善前问题点
改善后优点
YFC脚踏板月订单10000套,现双班四人 生产每天360套,月生产能力只能达到 8000套,无法满足交付需求,为满足交
付需求,需要增加手工线进行生产,手 工线每班3人,人员工时浪费较大;
超实用精益改善案例(某集团改善报告)

xxx精密机械有限公司
改善前生产现场
改善后生产现场
工具摆放不整齐,没有标示,经常用 工具时需要到处寻找工具浪费时间
工具摆放整齐、标示清楚明了, 员工不需要再寻找工具。
xxx精密机械有限公司
改善后标准工作表及负荷表
标准工作表
质量检验
起亚机
安全预防
+
哈斯 机
+
哈斯 机
+ +
品 检
+
半品
半品数量
3
北
接拍时间/U秒
1 下料
卧铣
15
5
1 下料
卧铣
10
3
2 飞底面
立铣
35
15
2 飞底面
立铣
30
15
3 铣长度
哈斯机
15
60
3 铣长度
哈斯机
10
64
4 铣内腔
起亚机
15
270
4 铣内腔
起亚机
10
110
5 铣外宽
哈斯机
15
80
5 铣外宽及沉孔 哈斯机
15
80
6 反面沉孔
佳铁
15
18
7 自检
60
6 自检
60
8 研磨去毛刺 振动研磨
120
周期时间/u秒
289
46302011生产线员工技能表
一级:(能培训员工,并且使他们能达到二级水平)
二级:(单独熟练操作)
三级:(能操作但不熟练)
产品
工序 下料
姓名
夏世强
飞面
46302011AG
铣长度 与粗加 工内腔
内腔精 加工
亲子关系改善一个成功案例报告
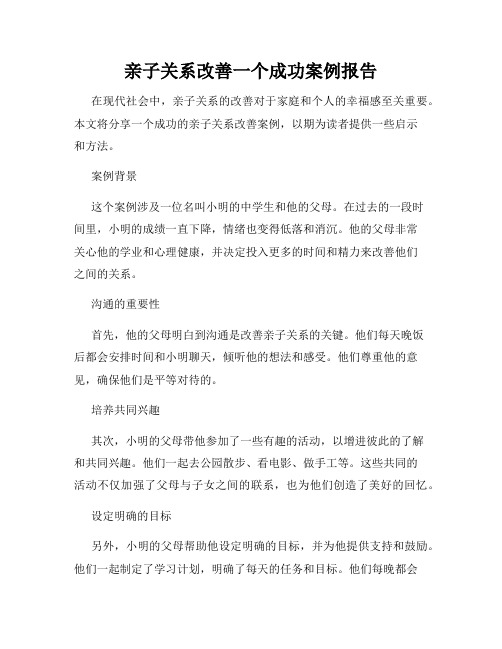
亲子关系改善一个成功案例报告在现代社会中,亲子关系的改善对于家庭和个人的幸福感至关重要。
本文将分享一个成功的亲子关系改善案例,以期为读者提供一些启示和方法。
案例背景这个案例涉及一位名叫小明的中学生和他的父母。
在过去的一段时间里,小明的成绩一直下降,情绪也变得低落和消沉。
他的父母非常关心他的学业和心理健康,并决定投入更多的时间和精力来改善他们之间的关系。
沟通的重要性首先,他的父母明白到沟通是改善亲子关系的关键。
他们每天晚饭后都会安排时间和小明聊天,倾听他的想法和感受。
他们尊重他的意见,确保他们是平等对待的。
培养共同兴趣其次,小明的父母带他参加了一些有趣的活动,以增进彼此的了解和共同兴趣。
他们一起去公园散步、看电影、做手工等。
这些共同的活动不仅加强了父母与子女之间的联系,也为他们创造了美好的回忆。
设定明确的目标另外,小明的父母帮助他设定明确的目标,并为他提供支持和鼓励。
他们一起制定了学习计划,明确了每天的任务和目标。
他们每晚都会检查他的作业,并为他提供帮助和指导。
这种积极的参与让小明感受到他们对他的关心和支持。
尊重个体差异同时,小明的父母鼓励他发展自己的兴趣和才能,尊重他的个体差异。
他们帮助他发现自己的激情,并鼓励他积极参与相关活动。
这种支持和认可让小明增强了自信心,逐渐找回了学习的动力。
建立良好的家庭环境最后,小明的父母努力营造了一个温馨和谐的家庭环境。
他们经常进行家庭聚会,增进亲子之间的情感联系。
此外,他们也注重家庭成员之间的尊重和理解,家庭成员可以坦诚地表达自己的想法和感受,这有助于促进彼此间的和谐共处。
案例结果经过一段时间的努力和改善,小明的成绩得到了明显的提升。
他的情绪也变得积极向上,与父母之间的关系更加紧密。
他们之间的沟通变得更加顺畅,彼此之间的理解和尊重也得到了加强。
小明的自信心得到了提升,他也更加愿意参与学习和家庭活动。
结论通过这个案例,我们可以得出一些改善亲子关系的启示。
首先,沟通是建立良好关系的基础,父母应该倾听和理解孩子的想法和感受。
改善案例报告模板
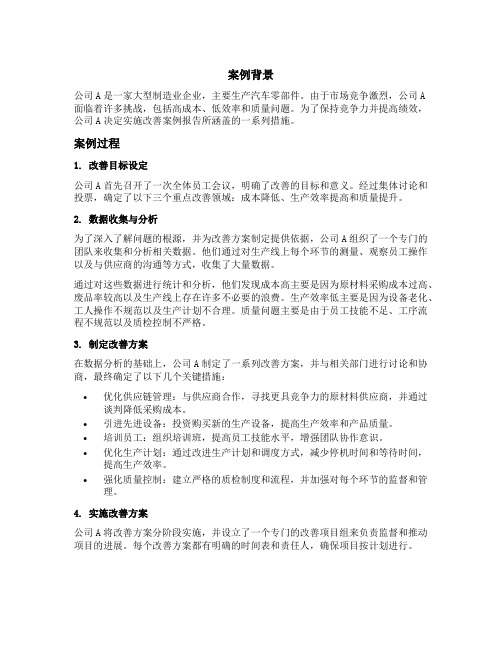
案例背景公司A是一家大型制造业企业,主要生产汽车零部件。
由于市场竞争激烈,公司A面临着许多挑战,包括高成本、低效率和质量问题。
为了保持竞争力并提高绩效,公司A决定实施改善案例报告所涵盖的一系列措施。
案例过程1. 改善目标设定公司A首先召开了一次全体员工会议,明确了改善的目标和意义。
经过集体讨论和投票,确定了以下三个重点改善领域:成本降低、生产效率提高和质量提升。
2. 数据收集与分析为了深入了解问题的根源,并为改善方案制定提供依据,公司A组织了一个专门的团队来收集和分析相关数据。
他们通过对生产线上每个环节的测量、观察员工操作以及与供应商的沟通等方式,收集了大量数据。
通过对这些数据进行统计和分析,他们发现成本高主要是因为原材料采购成本过高、废品率较高以及生产线上存在许多不必要的浪费。
生产效率低主要是因为设备老化、工人操作不规范以及生产计划不合理。
质量问题主要是由于员工技能不足、工序流程不规范以及质检控制不严格。
3. 制定改善方案在数据分析的基础上,公司A制定了一系列改善方案,并与相关部门进行讨论和协商,最终确定了以下几个关键措施:•优化供应链管理:与供应商合作,寻找更具竞争力的原材料供应商,并通过谈判降低采购成本。
•引进先进设备:投资购买新的生产设备,提高生产效率和产品质量。
•培训员工:组织培训班,提高员工技能水平,增强团队协作意识。
•优化生产计划:通过改进生产计划和调度方式,减少停机时间和等待时间,提高生产效率。
•强化质量控制:建立严格的质检制度和流程,并加强对每个环节的监督和管理。
4. 实施改善方案公司A将改善方案分阶段实施,并设立了一个专门的改善项目组来负责监督和推动项目的进展。
每个改善方案都有明确的时间表和责任人,确保项目按计划进行。
在实施过程中,公司A积极与员工沟通,征求他们的意见和建议,并鼓励他们参与到改善项目中。
同时,公司A还定期组织培训和交流活动,提高员工对改善方案的理解和支持。
5. 改善效果评估在改善方案全部实施完毕后,公司A对各项指标进行了评估。
改善提案报告(案例)

改善前改善后作者感悟:十多年前,公司十多名员工。
公司发展到现在,在华东、华中、华南三个工厂就有近千名员工!国家在发达,公司在发展,做为公司的一员,我们更要不断地改善和进步。
只有这样,我们的成本才会越做越低,品质越做越好;只有这样,我们才能得到客户的信任,真正留住客户;只有这样,我们才能提升自己的“附加值”,实现人生价值。
精益从心开始,改善从我做起。
让我们团结一心,找到解决问题的最佳方法,持续改善吧!刚开始,一次性只能过2筒纤维,因为我们公司静电刷产品品种较多,客户也多,每个客户每种产品要求纤维硬度不一样,所以需要过胶的纤维种类、数量也多,每天加班很晚才过500克纤维,而且过出来的纤维在筒上行程很窄,不久又要换筒。
效率远远满足不了生产的需要,我们急需改善。
第一次改善:更换了一个电机,做了几个皮带轮,连了3根长轴出来,这样一次性可过10筒纤维,效率比以前提高了5倍。
同时,收纤维机的凸轮也换了,纤维筒缠的又多又好用。
第二次改善:在原来的基础上增加了6筒,一次性过16筒纤维,效率从240克/小时,提高到500克/小时。
以前,每天加班赶不上生产需要,现在每天工作8小时就够用,而且还有库存,效率明显提高一半。
案例背景:自2004年使用过胶机以来,已经改善了很多,这是公司降低成本的一个重要环节。
当时,由于买不到进口的1K碳素纤维,我们就从别的供应商处,找了些很散的纤维回来试用。
开始,手工绕线还能做出产品,但有部分碳素纤维,是在钩织机上面编好,才能做出成品。
比如京瓷2FM0409B4、2FV04140A,富士施乐105CE20460、105CE20470等,由于碳素纤维比较脆,在钩织时“U”型易断,且碎毛特别多,根本无法生产。
改善过程:1、收线机(缠线机)第一事业部(越南)改善历程作者:日期:。
经营改善案例报告
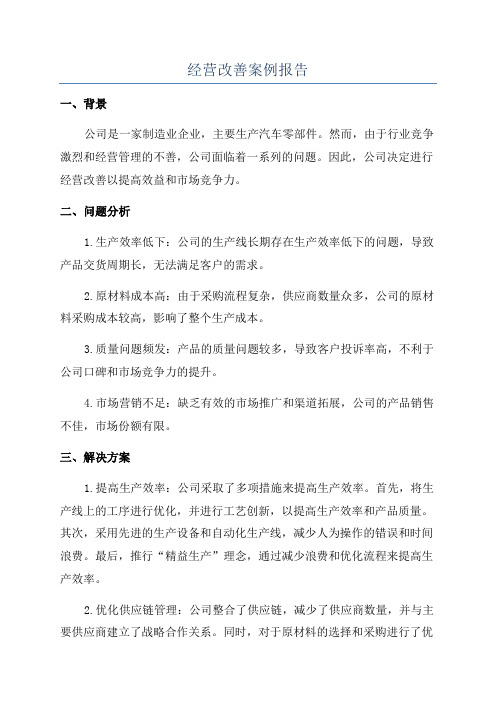
经营改善案例报告一、背景公司是一家制造业企业,主要生产汽车零部件。
然而,由于行业竞争激烈和经营管理的不善,公司面临着一系列的问题。
因此,公司决定进行经营改善以提高效益和市场竞争力。
二、问题分析1.生产效率低下:公司的生产线长期存在生产效率低下的问题,导致产品交货周期长,无法满足客户的需求。
2.原材料成本高:由于采购流程复杂,供应商数量众多,公司的原材料采购成本较高,影响了整个生产成本。
3.质量问题频发:产品的质量问题较多,导致客户投诉率高,不利于公司口碑和市场竞争力的提升。
4.市场营销不足:缺乏有效的市场推广和渠道拓展,公司的产品销售不佳,市场份额有限。
三、解决方案1.提高生产效率:公司采取了多项措施来提高生产效率。
首先,将生产线上的工序进行优化,并进行工艺创新,以提高生产效率和产品质量。
其次,采用先进的生产设备和自动化生产线,减少人为操作的错误和时间浪费。
最后,推行“精益生产”理念,通过减少浪费和优化流程来提高生产效率。
2.优化供应链管理:公司整合了供应链,减少了供应商数量,并与主要供应商建立了战略合作关系。
同时,对于原材料的选择和采购进行了优化,降低了采购成本。
此外,建立了供应链信息系统,实现了供应链的可视化管理。
3.加强质量控制:公司加强了对产品质量的控制,建立了严格的质量管理体系。
通过提高工艺标准和设备维护,加强员工培训和验收工作,提高了产品的质量水平。
同时,建立了客户投诉反馈机制,及时处理客户投诉,并进行品质改进。
4.加大市场推广力度:公司加大了市场推广和渠道拓展的力度。
与一些汽车厂商建立了合作关系,拓展了产品的销售渠道。
同时,进行了品牌宣传和广告推广,提升了品牌知名度和市场形象。
四、实施效果1.生产效率提升:经过生产效率优化和工艺创新,公司的生产效率得到了显著提升。
产品交货周期大幅缩短,客户满意度提高。
2.采购成本降低:通过整合供应链和优化原材料采购流程,公司的采购成本得到了明显的降低。
现实中的8D改善报告案例

现实中的8D改善报告案例(出租屋被水淹了)案例:以下通过一件发生在我们身边的平常小事,来说明8D报告(纠正/预防措施)的写法。
事由:出租屋内,一日早晨,小王正在水龙边洗脸准备上班,刚洗完脸,突然家中打来电话,于是把脸帕一挂就去屋内接电话,接完电话就去上班。
下午下班回家时发现家中全部被水淹了。
铺在地上的草席和被子全都漂在水中。
D1-成立改善小组:马上叫上住在隔壁的几个同事,组成事故处理小组。
小组成员:张三、李四、王五。
D2(第二步):问题描述王五家中被水淹,家中所有摆放在地上的物品都浸在水中(不良率100%)。
如:草席、被子和书本等。
D3(第三步)-暂时围堵行动(即应急对策或叫临时对策)1、马上与小组成员一起把家中的水设法排放出去。
负责人:张三2、立即把浸在水中的物品捞起并摊开到阳台去凉干。
负责人:李四D4(第四步)---根本原因分析:1、早晨洗完脸时,接听家中突然打来的电话,然后忘记关水,造成水淹小屋。
2、下水道出口太小,而且都采用网格式的盖子盖住。
昨天洗菜洗出来的小片烂蔬菜叶梗在网格上,致使下水道出水很慢,长时间积累后,大量未及时排放出去的水把小屋淹了。
分析人:王五审核:王五妻子D5(第五步)---制订永久对策(即长期对策)1、把下水道出口上的网格式盖子去掉,以便加大出水口,不会造成被水淹的情况。
责任人:王五预计完成时间:2007-10-12D6(第六步)---实施/确认PCA1、经过王五实际操作,把下水道出口加大后,小片蔬菜叶不会再梗在出水口处,堵住废水往外流。
并且即使把水龙头打开到最大,水仍能及时地从下水道出水口完全地流出去。
现确认此永久对策有效,并已经执行。
验证人:王五D7(第七步)---防止再发生(即采取预防措施)1、早晨上班出门前一定要检验水龙头是否关闭。
2、以后洗蔬菜时一定要把烂蔬菜叶丢到垃圾筐里,并且要把地面清理干净。
3、早晨洗脸时不能带电话在身上。
在洗脸过程中,就算电话铃响起也不能接。
现场改善案例集范文
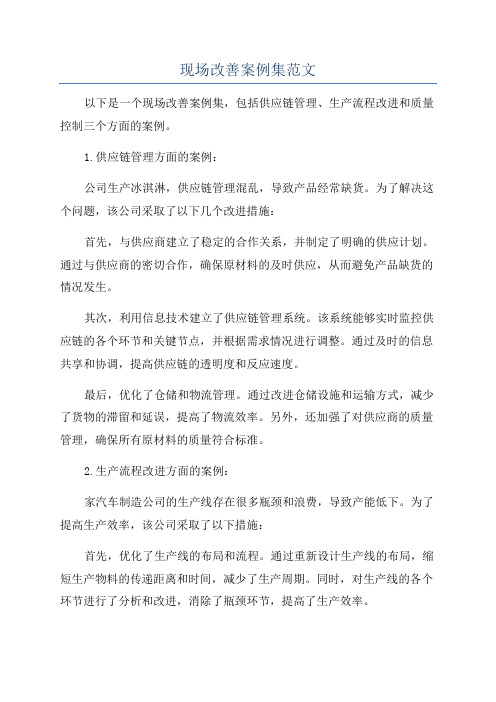
现场改善案例集范文以下是一个现场改善案例集,包括供应链管理、生产流程改进和质量控制三个方面的案例。
1.供应链管理方面的案例:公司生产冰淇淋,供应链管理混乱,导致产品经常缺货。
为了解决这个问题,该公司采取了以下几个改进措施:首先,与供应商建立了稳定的合作关系,并制定了明确的供应计划。
通过与供应商的密切合作,确保原材料的及时供应,从而避免产品缺货的情况发生。
其次,利用信息技术建立了供应链管理系统。
该系统能够实时监控供应链的各个环节和关键节点,并根据需求情况进行调整。
通过及时的信息共享和协调,提高供应链的透明度和反应速度。
最后,优化了仓储和物流管理。
通过改进仓储设施和运输方式,减少了货物的滞留和延误,提高了物流效率。
另外,还加强了对供应商的质量管理,确保所有原材料的质量符合标准。
2.生产流程改进方面的案例:家汽车制造公司的生产线存在很多瓶颈和浪费,导致产能低下。
为了提高生产效率,该公司采取了以下措施:首先,优化了生产线的布局和流程。
通过重新设计生产线的布局,缩短生产物料的传递距离和时间,减少了生产周期。
同时,对生产线的各个环节进行了分析和改进,消除了瓶颈环节,提高了生产效率。
其次,引入了自动化设备和机器人技术。
通过引入自动化设备和机器人技术,减少了人工操作的时间和错误率,提高了生产线的生产能力和质量稳定性。
另外,还利用数据分析和预测技术,实现了产能的动态管理和优化。
最后,加强了员工培训和团队合作。
通过加强员工的培训和技能提升,提高了员工的生产能力和质量意识。
同时,注重团队合作和沟通,促进了生产线各个环节的协同和高效运转。
3.质量控制方面的案例:家电子产品公司的产品经常出现质量问题,影响了公司的声誉和销售。
为了改善产品质量,该公司采取了以下几种措施:首先,加强了原材料的质量管理。
与供应商建立了长期合作关系,并对原材料进行严格的质量检验和筛选。
通过提高原材料的质量,有效降低了产品的良品率。
其次,建立了完善的质量管理体系。
8d报告改善的案例

8d报告改善的案例近年来,随着企业管理水平的不断提升,8D报告(8 Disciplines Report)作为一种问题解决工具,被广泛应用于各行各业。
它以8个有序的步骤,系统地解决和改善问题,被许多企业认为是提升产品质量和管理效率的必备工具。
本文将通过一个实际案例,来展示8D报告在企业中的改善效果。
案例背景是某汽车制造企业的一个生产线出现了频繁的零部件故障问题。
故障导致生产效率下降,产品质量不稳定,给企业造成了巨大的损失。
为了解决这个问题,企业决定运用8D报告方法进行改善。
第一步:组建小组根据8D报告的要求,首先是组建一个由不同岗位代表组成的小组,以确保问题的全面性和多角度思考。
该小组由研发、生产、品质和技术等部门的代表组成,具备了解决问题所需要的知识和经验。
第二步:问题描述小组成员通过调查和观察,对故障问题进行了详细描述。
他们分析发现,故障主要发生在某特定型号的传感器上,故障频率逐渐增加并影响到整个生产线的稳定性。
第三步:立即控制为了避免故障继续扩大,小组采取了紧急措施,包括更换故障传感器、调整工艺参数以及加强产品质量检测。
通过这些措施,故障在一段时间内得到了一定的控制。
第四步:问题原因分析小组成员进行了深入的问题原因分析。
他们发现,由于生产线中使用的传感器来自多个供应商,供应商质量控制不一致导致了部分传感器质量不稳定。
此外,生产过程中的振动和温度变化也会对传感器的寿命和稳定性产生影响。
第五步:制定纠正措施根据问题原因分析的结果,小组制定了纠正和预防措施。
他们与供应商沟通并落实了强化质量控制的要求,采取了合适的设备和工艺参数以减少对传感器的损害,并优化了产品检测流程以确保产品出厂质量的稳定。
第六步:验证纠正措施效果通过对纠正措施的实施,小组对生产线进行了一段时间的观察,并收集相关数据进行分析。
结果显示,故障率明显下降,生产线稳定性得到有效提升。
这证明了所采取的纠正措施是有效的。
第七步:预防措施为了防止类似故障再次发生,小组总结前期经验和教训,制定了一系列预防措施。
改善案例报告
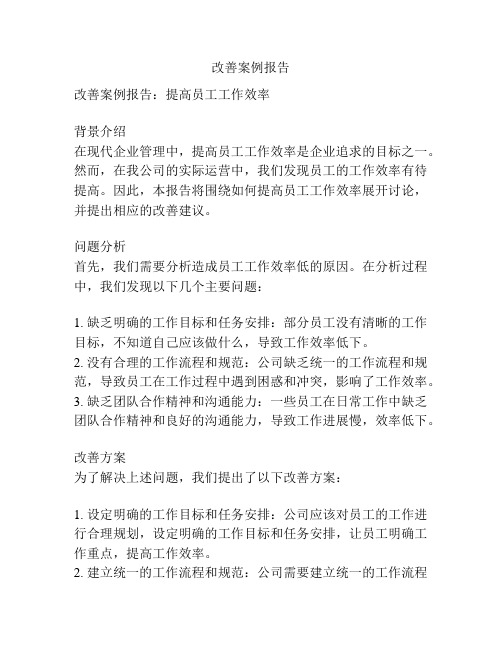
改善案例报告改善案例报告:提高员工工作效率背景介绍在现代企业管理中,提高员工工作效率是企业追求的目标之一。
然而,在我公司的实际运营中,我们发现员工的工作效率有待提高。
因此,本报告将围绕如何提高员工工作效率展开讨论,并提出相应的改善建议。
问题分析首先,我们需要分析造成员工工作效率低的原因。
在分析过程中,我们发现以下几个主要问题:1. 缺乏明确的工作目标和任务安排:部分员工没有清晰的工作目标,不知道自己应该做什么,导致工作效率低下。
2. 没有合理的工作流程和规范:公司缺乏统一的工作流程和规范,导致员工在工作过程中遇到困惑和冲突,影响了工作效率。
3. 缺乏团队合作精神和沟通能力:一些员工在日常工作中缺乏团队合作精神和良好的沟通能力,导致工作进展慢,效率低下。
改善方案为了解决上述问题,我们提出了以下改善方案:1. 设定明确的工作目标和任务安排:公司应该对员工的工作进行合理规划,设定明确的工作目标和任务安排,让员工明确工作重点,提高工作效率。
2. 建立统一的工作流程和规范:公司需要建立统一的工作流程和规范,对员工进行培训和指导,让员工了解工作流程和规范,避免工作冲突和误解,提高工作效率。
3. 提升团队合作精神和沟通能力:公司可以组织团队合作培训和沟通技巧培训,提升员工的团队合作精神和沟通能力,加强团队凝聚力,提高工作效率。
实施计划为了保证改善方案的顺利实施,我们需要制定详细的实施计划:1. 设定明确的工作目标和任务安排:在每个新项目开始之前,制定明确的工作目标和任务安排,并与员工进行沟通和确认。
2. 建立统一的工作流程和规范:制定公司内部工作流程和规范手册,对新员工进行培训,并定期进行审核和更新。
3. 提升团队合作精神和沟通能力:针对缺乏团队合作和沟通能力的员工,开展相关培训课程,并建立常规的沟通机制,促进员工之间的交流和合作。
预期效果通过以上的改善方案和实施计划,我们预期可以达到以下效果:1. 提高员工的工作效率,完成工作任务的速度更快、更准确。
五金行业公司专案改善报告案例样板

五金行业公司专案改善报告案例样板一、概述五金行业公司作为一个具有悠久历史的产业,近年来面临着市场竞争加剧、产品同质化严重等问题。
为了应对这些挑战,本公司制定了一项专案改善计划,旨在提高公司的竞争力和产品质量,提升客户满意度,实现可持续发展。
二、问题分析1.市场竞争加剧:随着五金行业市场的日渐饱和,公司面临着更加激烈的市场竞争,需要提升产品质量和服务水平,增强市场竞争力。
2.产品同质化严重:市场上五金产品同质化现象普遍,产品差异化不强,导致公司难以实现产品的溢价销售。
3.客户投诉率较高:公司产品在使用过程中出现故障和质量问题的投诉率较高,客户满意度有待提高。
三、改善目标1.提高产品质量:通过制定更严格的产品质量控制标准和质检流程,减少产品出现故障和质量问题的概率,提高产品质量水平。
2.提升市场竞争力:加大研发投入,提升产品创新能力,凸显差异化优势,提高市场份额。
3.降低客户投诉率:通过改进服务流程,提高售后服务的质量和效率,降低客户投诉率,提高客户满意度。
四、改善措施1.优化研发流程:加大对研发团队的培训和技术支持,加快产品研发周期,提升产品创新能力。
2.引进先进设备:投资购买先进的生产设备,提高生产效率和产品质量。
3.强化质量控制:建立严格的质检标准和流程,从原材料采购到成品出货全程监控,确保产品质量合格。
4.完善售后服务:增加售后服务人员数量,提高售后服务的及时性和质量,减少客户投诉。
5.加大宣传力度:增加宣传推广的投入,提高公司品牌知名度和市场竞争力。
五、改善效果评估1.产品质量:通过质量数据统计和客户反馈,评估产品质量是否有所提升。
2.市场竞争力:通过市场调研和销售额增长情况,评估市场竞争力是否得到提升。
3.客户满意度:通过客户满意度调查和客户投诉情况,评估客户满意度是否有所提高。
六、改善计划执行1.制定详细的改善计划,并明确责任人和执行时间节点。
2.建立监督机制,定期跟进改善计划的执行情况。
- 1、下载文档前请自行甄别文档内容的完整性,平台不提供额外的编辑、内容补充、找答案等附加服务。
- 2、"仅部分预览"的文档,不可在线预览部分如存在完整性等问题,可反馈申请退款(可完整预览的文档不适用该条件!)。
- 3、如文档侵犯您的权益,请联系客服反馈,我们会尽快为您处理(人工客服工作时间:9:00-18:30)。
改善案例-NS LED灯板不良改善一、成立改善小组
小组成员
二、选题
三、现状调查
从2011年1月到6月LED灯板不良持续上升,总不良数达到897件;到2011年6月份不良率达到1.31%,占总不良率的31%。
以下为897个不良品中,选取100个不良品进行测量分析的结果,主要不良现象为:R1损坏与LED断路。
(%)
四、设定目标
1、设定目标值:NS LED灯板不良率从6月的1.31%,6个月内下降至0.5%以下。
2、可行性分析:
LED灯板也作为PCB板的一种,可以把不良率控制在与其他PCB同一个水平线。
其他PCB不良在0.5%左右,LED灯板因为元器件比较少,并且LED的本身寿命比较长,不良率可以比其他PCB更低。
根据其他同行业不良率统计结果,同比情况下不良
率也是可以控制在0.5%以下。
五、分析原因
六、要因确认
末端要因分析表
要因收集表。