快速反应程序
QRQC快速反应质量控制程序
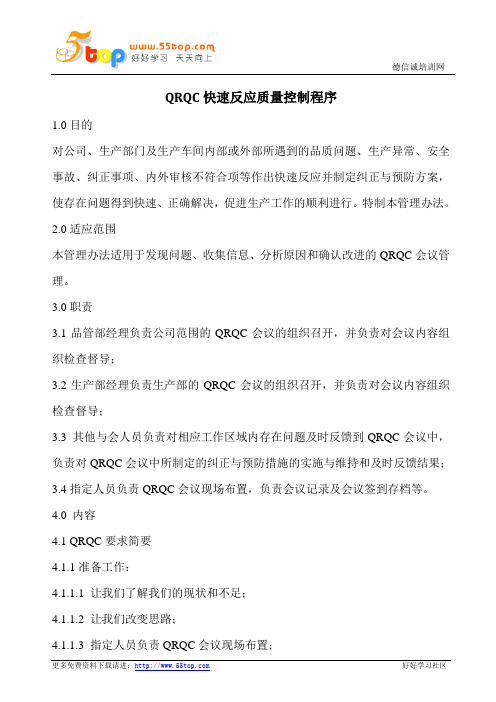
QRQC快速反应质量控制程序1.0目的对公司、生产部门及生产车间内部或外部所遇到的品质问题、生产异常、安全事故、纠正事项、内外审核不符合项等作出快速反应并制定纠正与预防方案,使存在问题得到快速、正确解决,促进生产工作的顺利进行。
特制本管理办法。
2.0适应范围本管理办法适用于发现问题、收集信息、分析原因和确认改进的QRQC会议管理。
3.0职责3.1品管部经理负责公司范围的QRQC会议的组织召开,并负责对会议内容组织检查督导;3.2生产部经理负责生产部的QRQC会议的组织召开,并负责对会议内容组织检查督导;3.3 其他与会人员负责对相应工作区域内存在问题及时反馈到QRQC会议中,负责对QRQC会议中所制定的纠正与预防措施的实施与维持和及时反馈结果;3.4指定人员负责QRQC会议现场布置,负责会议记录及会议签到存档等。
4.0 内容4.1 QRQC要求简要4.1.1准备工作:4.1.1.1 让我们了解我们的现状和不足;4.1.1.2 让我们改变思路;4.1.1.3 指定人员负责QRQC会议现场布置;4.1.1.4 指定人员负责收集当天需要审查的问题;4.1.1.5 将当天问题提前书写在QRQC现场记录板上;4.1.1.6会议前先在《会议培训签到表》上签到。
4.1.2会议时间:4.1.2.1公司QRQC会议,原则上每周五晚上19:00(特殊情况另行安排,以临时通知为准);4.1.2.2生产部QRQC会议,根据实际情况而定(凡发生重大品质事故时,必须及时召开)。
4.1.3会议地点:4.1.3.1公司QRQC会议:办公楼二楼会议室;4.1.3.2生产部QRQC会议:生产部作业现场。
4.1.4参加人员:4.1.4.1公司QRQC会议:副总经理、人事行政部经理、技术部经理、品管部经理、生产部经理、车间主管、班组长、质检员、工程师、技术员、代理或指定人员;必要时,通知营销部与采购部派人参加。
4.1.4.2生产部QRQC会议:生产经理、车间主管,班组长、质检员、工程师、技术员。
快速反应程序:解决质量问题的反应模式

(Example)
OPERATION:
STEP NO.
Standardized Operations Worksheet And Layout标准化操作工作表和布局
WORK ELEMENT
FROM:___________________________
QUANTITY PER SHIFT:______________
TO: _____________________________
SHIFT:________
ELEMENT TIME
HAND WORK MACHINE WALK
STANDARD INPROCESS STOCK
Q
QUALITY
CHECK
CUSTOMER CYCLE TIME:________________
•用目视管理方法建立统一的识别程序
• (Example) 用明亮色彩作为首选的识别方法
✓ ✓✓✓-
红色=废品 黄色=可疑品 绿色=合格品
废品
可疑品或待处 理品
标签内容
标签内容
IN THIS SECTION IN THIS SECTION
IS AT LOCAL
IS AT LOCAL
DISCRETION
DISCRETION
PLT001
红标签表示废品。
PLT002
黄色标签表示可疑产品或待 处理的材料,需要返工的材 料或需要进一步检查的材料
半成品或合格 品
标签内容 IN THIS SECTION
IS AT LOCAL DISCRETION
PLT003
绿色或其他颜色的标签表示产品是可 接受的 (红色和黄色除外). .
TOTAL
快速反应流程

修改码:B/0 1 目的建立快速反应流程,确保所有重大外部/内部问题尽快得到各职能部门的关注和沟通并快速反应,从而系统的分析解决问题,避免再发。
2 适用范围本流程适用于本公司及子(分)公司内生产、技术、质量、安全、采购、物流等相关部门进行快速反应解决问题。
3 定义3.1快速反应系统:--- 标准化的应对重大的内/外部质量问题的反应流程----通过例会加强沟通交流和知识分享----用可视化的方法展现重要问题3.2快速反应会议:生产例会,是一个沟通会议,不是问题解决会议。
3.3经验教训系统:主要指建立获取信息的流程,对所有操作流程的持续改进提供支持,利用成功经验,防止错误重复出现;经验教训适用于所有的岗位,因此组织中相关人员需参加。
3.4 高频客诉追踪:对于一年内再发或者高频客诉抱怨(12个月内多余24起)的,成立专项小组对应,快速记录清单使用红色色标标注。
(公司内部目标值:同类型缺陷相关原因产生的不良件数<2件每月)4 职责4.1 质量部:负责收集24小时内发生的重大问题,主导召开快速反应会议,并跟踪确认。
负责组织对发生问题(内外部问题、安全、交付)的产生与流出原因进行分析。
4.2 生产部:负责对发生问题(内外部问题、安全、交付)的产生与流出因分析及对策实施,负责解决模具、夹治具及生产条件问题,参与对已发生问题根本原因进行分析。
4.3物流部:负责汇报影响生产计划达成和交付问题的报警、跟踪确认。
4.4设备科:负责汇报因设备问题导致客户抱怨、内部重大不良或影响生产等问题,并负责改善确认。
4.5采购部:负责汇报由于采购件的短缺、批量质量问题导致影响交付问题的报警、跟踪确认。
4.6行政企划部:负责汇报安全、工伤问题,及原因调查整改确认。
修改码:B/0 5 程序5.1 快速反应5.1.1 会议前的准备活动为准备快速反应会议,质量部必须找出过去24小时发生的重大质量事故。
收集问题的要素包括问题描述,问题来源,发生日期,频次,原因分析,长短期措施及断点,措施验证结果,责任人。
快速反应会议管理程序
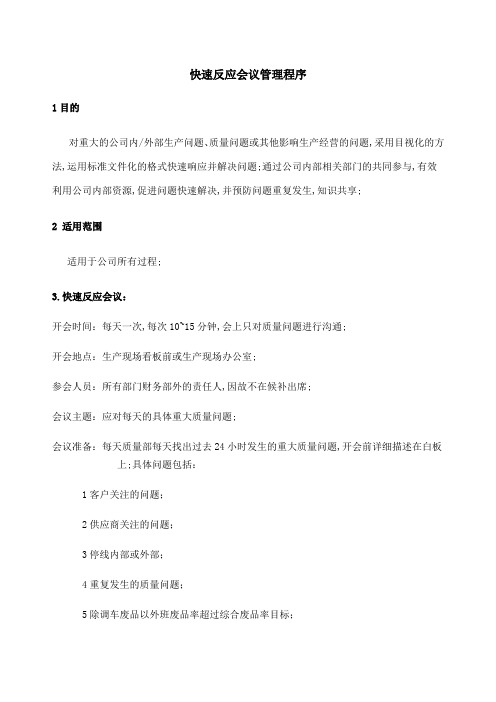
快速反应会议管理程序1目的对重大的公司内/外部生产问题、质量问题或其他影响生产经营的问题,采用目视化的方法,运用标准文件化的格式快速响应并解决问题;通过公司内部相关部门的共同参与,有效利用公司内部资源,促进问题快速解决,并预防问题重复发生,知识共享;2 适用范围适用于公司所有过程;3.快速反应会议:开会时间:每天一次,每次10~15分钟,会上只对质量问题进行沟通;开会地点:生产现场看板前或生产现场办公室;参会人员:所有部门财务部外的责任人,因故不在候补出席;会议主题:应对每天的具体重大质量问题;会议准备:每天质量部每天找出过去24小时发生的重大质量问题,开会前详细描述在白板上;具体问题包括:1客户关注的问题;2供应商关注的问题;3停线内部或外部;4重复发生的质量问题;5除调车废品以外班废品率超过综合废品率目标;6验证岗位中发现的问题;7分层审核中发现的问题;8其它内部质量问题;会议内容:1会议主席协调各方意见,确定新问题的责任人和关闭日期;2旧问题负责人提交相关报告,报告具体进度,紧抓问题退出标准,由与会人员确认关闭;3会议主席根据当天情况,标明具体问题和日Q图的状态;会后工作:问题负责人运用8D等方法、相关工具解决问题,总结形成报告;其他定期工作:快速反应跟踪表应记录所有产生的问题;每月汇总公布问题发生数趋势图;4职责公司生产部长:负责组织和主持快速反应会议,跨部门指定解决问题的责任人;质量部:是快速反应会议的归口管理部门,负责收集和反馈公司内/外部问题,并跟踪问题解决进展;其他部门:负责参加并积极响应快速反应会议;问题责任人:负责按照规定的时间完成问题解决并符合推出标准;协调跨部门问题解决小组在会议外完成相应审核;更新快速反应看板上退出标准及状态栏;向快速反应会议报告问题各阶段的进展;5工作程序6相关文件7相关表单编制/日期:审核人:审核/日期:批准/日期:。
学校135快速反应处置流程
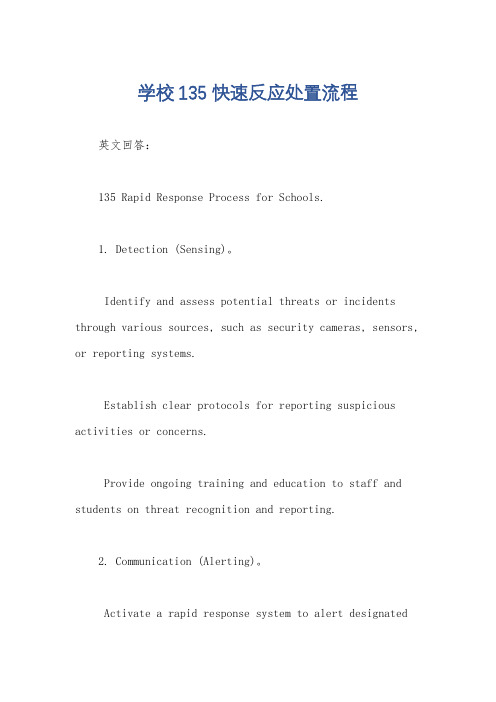
学校135快速反应处置流程英文回答:135 Rapid Response Process for Schools.1. Detection (Sensing)。
Identify and assess potential threats or incidents through various sources, such as security cameras, sensors, or reporting systems.Establish clear protocols for reporting suspicious activities or concerns.Provide ongoing training and education to staff and students on threat recognition and reporting.2. Communication (Alerting)。
Activate a rapid response system to alert designatedpersonnel, including school administration, security, and law enforcement.Ensure multiple communication channels are available for efficient and redundant alerting.Establish standardized messaging and protocols for notifying stakeholders of an incident.3. Response (Action)。
Deploy trained security personnel to assess the situation and contain the threat.Coordinate with law enforcement and other emergency responders as needed.Implement emergency response plans and procedures to protect students and staff.Provide medical assistance or other first aid support as required.4. Evaluation (Assessment)。
快速反应程序

1 目的使用标准化的反应流程来应对重大的内/外部质量问题,使所有的问题都得到彻底的解决,降低质量问题再次发生的次数。
提高处理质量问题的效率,保证生产顺利进行和产品的准时交付2 术语2.1 快速反应:通过每日例会加强沟通和管理,采用目视管理方法展示重要信息,使应对重大的内、外部质量问题的反应标准化。
2.2 问题解决:一个系统化的用来识别、分析和消除现状和现行标准或期望之间的差距,并预防根本原因再次发生的过程。
2.3 经验总结:利用成功经验,防止问题重复出现。
3 职责:3.1 生产副总负责快速反应会议,每天召开快速反应会,并担任快速反应会议主持人。
如因故不在应提前指定候补代理人主持。
3.2 质量部负责汇总过去24小时内发生及收到的重大质量问题,并在快速反应会议前将问题写在快速反应看板上;每天更新《快速反应跟踪板》和《日质量Q图》。
3.3 制造部负责收集与汇报生产停线问题;3.4 研发部负责收集与汇报重大新品和工艺验证问题;3.5 设备部负责收集与汇报重大设备责任事故问题;3.6 工伤安全事故发生部门负责收集与汇报重大安全事故问题;3.7 问题责任人负责采用8D等方法、运用相应质量工具解决问题。
原则上问题责任人(或问题出现/发现工序主管)为每个问题的总负责人,确保能按时完成所有退出标准所要求的项目,将问题解决,并在每次指定的汇报时间,向领导层汇报问题解决的状态。
收集问题解决的所有资料,并提交到质量部存档。
3.8各负责部门负责总结其相应经验教训活动。
4 工作内容4.1 快速反应会议4.1.1 开会时间:必须每工作日进行一次,时间为每天早上8:00~8:30,每次15~30分钟,会上只对质量问题进行沟通。
4.1.2开会地点:生产现场看板前或生产现场办公室。
4.1.3参会人员:所有部门(财务部除外)的第一责任人,因故不在由候补代理人出席。
参加会议人员应在《日质量会议签到表》上签到。
4.1.4会议主题:应对每天具体的重要质量问题。
QSB快速反应流程

QSB快速反应流程快速反应流程(QSB,Quick Service Bulletin)是一种用于迅速处理问题和将解决方案迅速传达给相关人员的流程。
它旨在确保问题能够得到及时解决,以最小程度地对组织的正常运营造成干扰。
以下是一个包含超过1200字的QSB的标准流程:第一步:问题识别(Identification)快速反应流程的第一步是识别问题。
这可以通过多种方式进行,例如通过客户反馈、内部质量监控和检查、日常操作的异常情况等等。
一旦问题被发现,相关人员应该立即报告给负责的团队或部门。
第二步:问题分析(Analysis)第三步:解决方案开发(Solution Development)一旦问题的根本原因得到确认,团队需要制定相应的解决方案。
这通常涉及到制定一系列具体的步骤和行动计划,以修复问题并防止类似问题的再次发生。
解决方案应该是可操作和具体的,以便相关人员能够迅速理解并采取相应行动。
第四步:解决方案验证(Solution Validation)在制定解决方案之后,团队需要进行验证,以确保问题解决方案的有效性。
这可能包括验证方案的实施、测试解决方案的可行性,并确保它真正解决了问题。
如果验证过程中发现问题或需要进行进一步的调整,团队将返回前面的步骤进行修正。
第五步:解决方案发布(Solution Release)在解决方案被验证通过之后,团队需要将其传达给相关人员。
这可能包含编制发布公告、更新相关文件或培训相关人员。
目标是确保解决方案被传达给那些需要知道并实施它的人员。
第六步:问题解决(Problem Resolution)解决方案发布之后,团队需要跟踪问题是否得到解决。
这可以通过定期的监控和检查来实现。
如果发现问题仍未解决或出现新的问题,团队需要立即采取行动进行纠正。
第七步:总结和反馈(Summary and Feedback)在问题解决之后,团队应该进行总结和反馈。
这包括评估问题解决的效果、提取教训和经验,并在需要的情况下更新标准操作程序和其他相关文件。
美军应急装备采办的做法和启示

军现代战争在战争形态、作战样式、武器装备等方面都发生了很大的变化,信息化装备越来越多,装备的技术含量越来越高,装备、物资消耗越来越快,传统机械化战争时代所采用的战时采办程序已不能适应现代高技术战争的战场需要,迫切需要一种快速应急反应程序来实现战场军事装备的快速补给。
美军结合近几场战争的实践,在应急装备采办的组织机构、法规制度、采办程序和合同管理等方面,积累了大量经验,建立起一套应急装备采办程序,较好地满足了战争的需要。
1.美军应急装备采办程序应急装备采办程序是指国家在应对紧急状况的准备阶段或是紧急状态期间(包括战争、突发自然灾害以及其他紧急状况)进行装备采办活动或采办事项办理的先后顺序。
应急装备采办由于其“应急”特点,美军在应急装备采办的组织机构、法规制度、采办程序和合同管理等方面,积累了大量经验,建立起一套应急装备采办程序,较好地满足了战争的需要。
本文结合美军应急装备采办程序的主要内容、实施途径等方面谈几点对我军装备采办的启示。
美军应急装备采办的做法和启示■ 贺 鸣因此主要适用于金额相对较低的二、三类武器装备,而金额较高的一类(如航母、坦克、飞机等),通常采用常规的装备采办程序。
目前美军应急装备采办主要采用以下三种采办程序。
1.1快速反应程序快速反应程序(RRP)是海湾战争开始之前,由美空军提出的,主要针对战场上的紧急装备需求,通过减少管理层次、简化采办程序,加速成熟技术转化为作战能力。
该采办程序的实施分为三个阶段:第一阶段由作战部门提出装备需求,编写作战任务需求书提交空军参谋长批准;第二阶段由“快速反应评估委员会”、空军装备司令部以及“快速反应程序委员会”等机构对项目进行评审,并起草项目管理指令;第三个阶段为项目执行官发布项目管理指令,开始实施采办计划。
一般来讲,快速反应程序从提交《作战任务需求书》到发布计划管理指令不到16天,整个采办周期一般不超过半年。
项目经费由空军各司令部根据项目紧急程度从国会已经划拨的采办经费中提取。
现场急救的程序和原则
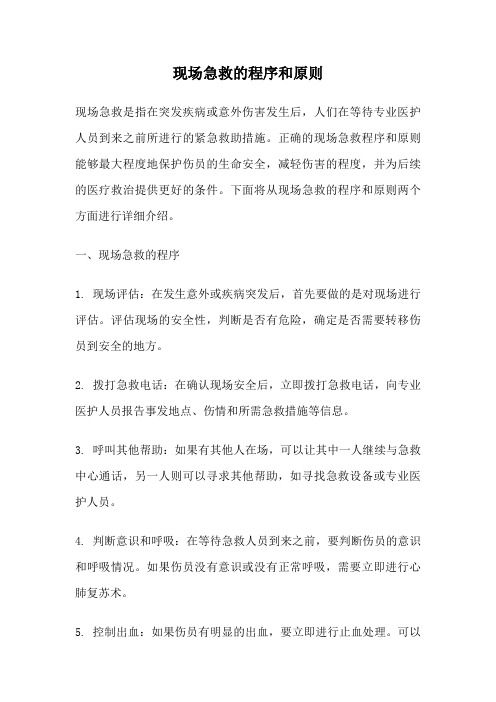
现场急救的程序和原则现场急救是指在突发疾病或意外伤害发生后,人们在等待专业医护人员到来之前所进行的紧急救助措施。
正确的现场急救程序和原则能够最大程度地保护伤员的生命安全,减轻伤害的程度,并为后续的医疗救治提供更好的条件。
下面将从现场急救的程序和原则两个方面进行详细介绍。
一、现场急救的程序1. 现场评估:在发生意外或疾病突发后,首先要做的是对现场进行评估。
评估现场的安全性,判断是否有危险,确定是否需要转移伤员到安全的地方。
2. 拨打急救电话:在确认现场安全后,立即拨打急救电话,向专业医护人员报告事发地点、伤情和所需急救措施等信息。
3. 呼叫其他帮助:如果有其他人在场,可以让其中一人继续与急救中心通话,另一人则可以寻求其他帮助,如寻找急救设备或专业医护人员。
4. 判断意识和呼吸:在等待急救人员到来之前,要判断伤员的意识和呼吸情况。
如果伤员没有意识或没有正常呼吸,需要立即进行心肺复苏术。
5. 控制出血:如果伤员有明显的出血,要立即进行止血处理。
可以使用纱布等物品进行直接压迫,控制出血并尽量减少伤害。
6. 固定骨折:如果伤员有骨折,要尽量保持伤员的身体稳定,避免进一步移动,可以使用固定带或木板等物品进行固定。
7. 保持体温:在急救过程中,要注意保持伤员的体温。
可以使用毯子等物品进行保暖,避免伤员受寒造成进一步损伤。
8. 安抚伤员:急救过程中,要保持冷静并安抚伤员的情绪。
积极与伤员交流,给予必要的心理支持,以减轻其焦虑和恐惧。
二、现场急救的原则1. 保护自己:在进行现场急救时,要时刻注意自身安全,避免受到伤害。
只有保护好自己,才能更好地救助他人。
2. 快速反应:在突发状况下,时间非常宝贵,要迅速做出反应并采取紧急措施。
尽量缩短救援时间,为伤员争取更多的生存机会。
3. 优先救治重症:在现场急救中,要优先救治重症伤员。
根据伤势的严重程度,给予及时有效的急救措施,避免病情恶化。
4. 不移动伤员:除非伤员所处的环境非常危险,否则应尽量避免移动伤员。
学校135快速反应处置流程

学校135快速反应处置流程学校面对各类突发事件时,快速反应和有效处置是确保师生安全和学校正常运转的关键。
本文将详细探讨学校在应对突发事件过程中的“135快速反应处置流程”,旨在确保事件处理及时、有序,最大限度减少可能的影响和损失。
1. 一级响应:快速警报与启动1分钟内:现场目击者或发现事件的工作人员迅速触发应急报警系统,通知安保部门和学校领导团队。
3分钟内:安保部门接到报警后立即派遣现场应急小组赶赴现场,同时启动应急预案,准备全面应对可能出现的情况。
5分钟内:学校领导团队和相关职能部门主要负责人集结于指定的应急指挥中心,启动应急响应和协调工作。
2. 三级响应:事件调查与初步控制一旦现场处于控制之下,学校将进行详细的事件调查和初步控制措施:15分钟内:安保部门负责人和指挥中心主任组织现场调查团队,获取事件详细信息和现场状况,评估事件严重性和影响范围。
30分钟内:针对事件类型,学校启动相应的应对程序,确保现场安全和人员疏散;通知相关职能部门参与事件处置,如医务人员、后勤服务等。
45分钟内:学校公共关系团队和媒体联络人员介入,准备好应对媒体关注和外界询问,及时发布事故情况通报,保持信息透明度和公信力。
3. 五级响应:全面恢复与后续处理在事件得到初步控制后,学校将全面进行恢复工作和后续处理:1小时内:安保部门和指挥中心与相关部门共同制定完善的后续处置计划,包括伤员救治、场地清理、安全检查等。
2小时内:学校启动全员复工或复课计划,确保学生和教职员工正常安全的恢复学习和工作环境。
学校135快速反应处置流程不仅仅是一套操作流程,更是学校安全管理体系的重要组成部分。
通过快速的警报与启动、详细的事件调查与初步控制,以及全面的恢复与后续处理,学校能够在面对突发事件时迅速响应,保障师生安全和正常教学秩序。
在未来的工作中,学校将持续完善和优化该处置流程,提高应对突发事件的能力和水平,确保学校安全稳定的运行。
4. 三级响应:事件调查与初步控制在事件初步控制后,学校将进行详细的事件调查和进一步的控制措施:15分钟内:安保部门领导和指挥中心主任召集现场调查小组,收集事件详细信息和现场状况,评估事件的严重性和潜在影响。
急诊快速反应小组制度及流程

急诊快速反应小组制度及流程英文回答:Rapid Response Team (RRT) System and Protocol.Introduction.The Rapid Response Team (RRT) is a multidisciplinary team of healthcare professionals who are trained to respond quickly to deteriorating patients and implement early intervention to prevent further clinical deterioration or cardiac arrest. The RRT system is designed to improve patient outcomes by providing timely and appropriate interventions in time-critical situations.Components of the RRT.The RRT typically consists of the following members:Physician (e.g., intensivist, emergency physician,hospitalist)。
Nurse (e.g., critical care nurse, charge nurse)。
Respiratory therapist.Pharmacist (optional)。
Activation Criteria.The RRT should be activated when there is concern about a patient's clinical status, such as:Altered mental status.Acute shortness of breath.Hypotension or hypotension.Severe pain.Suspected sepsis.Procedure.1. Activation: The RRT is activated by a healthcare professional who is concerned about a patient's condition. The activation is typically made through a designated phone number or pager system.2. Assessment: Upon arrival, the RRT team assesses the patient's vital signs, clinical status, and medical history. The team then develops an immediate plan of action.3. Interventions: The RRT initiates appropriate interventions based on the patient's condition, such as:Administering oxygen.Starting intravenous fluids.Administering medications.Conducting blood tests or imaging studies.Providing respiratory support.4. Consultation: If necessary, the RRT may consult with other specialists, such as an intensivist or cardiologist, to determine the best course of action.5. Transfer: If the patient requires more intensive care, the RRT may transfer the patient to the ICU or another appropriate unit.6. Debriefing: After the patient is stabilized, the RRT team debriefs to discuss the case and identify areas for improvement.Benefits of the RRT System.The RRT system has been shown to improve patient outcomes by:Reducing the incidence of cardiac arrest.Improving survival rates.Shortening hospital stays.Reducing healthcare costs.Conclusion.The RRT system is an essential component of modern healthcare. It provides a structured and efficient way to respond to deteriorating patients and implement early intervention. The RRT system has been shown to improve patient outcomes and reduce healthcare costs.中文回答:急诊快速反应小组制度及流程。
快速反应程序
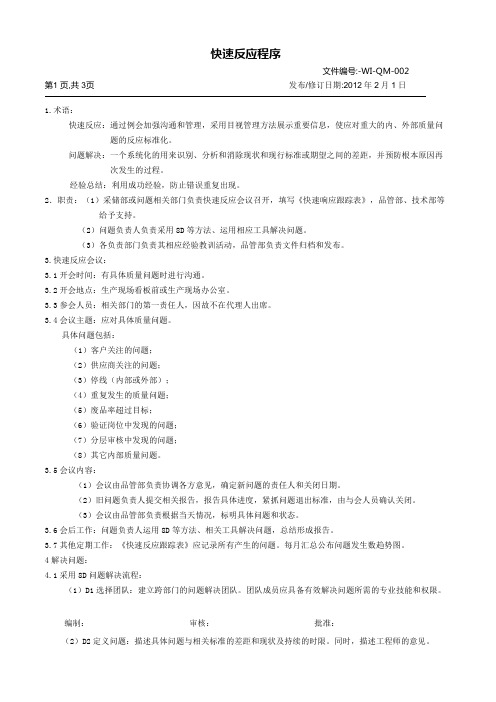
第1 页,共3页发布/修订日期:2012年2月1 日1.术语:快速反应:通过例会加强沟通和管理,采用目视管理方法展示重要信息,使应对重大的内、外部质量问题的反应标准化。
问题解决:一个系统化的用来识别、分析和消除现状和现行标准或期望之间的差距,并预防根本原因再次发生的过程。
经验总结:利用成功经验,防止错误重复出现。
2.职责:(1)采储部或问题相关部门负责快速反应会议召开,填写《快速响应跟踪表》,品管部、技术部等给予支持。
(2)问题负责人负责采用8D等方法、运用相应工具解决问题。
(3)各负责部门负责其相应经验教训活动,品管部负责文件归档和发布。
3.快速反应会议:3.1开会时间:有具体质量问题时进行沟通。
3.2开会地点:生产现场看板前或生产现场办公室。
3.3参会人员:相关部门的第一责任人,因故不在代理人出席。
3.4会议主题:应对具体质量问题。
具体问题包括:(1)客户关注的问题;(2)供应商关注的问题;(3)停线(内部或外部);(4)重复发生的质量问题;(5)废品率超过目标;(6)验证岗位中发现的问题;(7)分层审核中发现的问题;(8)其它内部质量问题。
3.5会议内容:(1)会议由品管部负责协调各方意见,确定新问题的责任人和关闭日期。
(2)旧问题负责人提交相关报告,报告具体进度,紧抓问题退出标准,由与会人员确认关闭。
(3)会议由品管部负责根据当天情况,标明具体问题和状态。
3.6会后工作:问题负责人运用8D等方法、相关工具解决问题,总结形成报告。
3.7其他定期工作:《快速反应跟踪表》应记录所有产生的问题。
每月汇总公布问题发生数趋势图。
4解决问题:4.1采用8D问题解决流程:(1)D1选择团队:建立跨部门的问题解决团队。
团队成员应具备有效解决问题所需的专业技能和权限。
编制:审核:批准:(2)D2定义问题:描述具体问题与相关标准的差距和现状及持续的时限。
同时,描述工程师的意见。
(3)D3遏制:制定临时措施以防止问题在客户端发生。
解决消费者投诉和纠纷的快速反应计划与程序
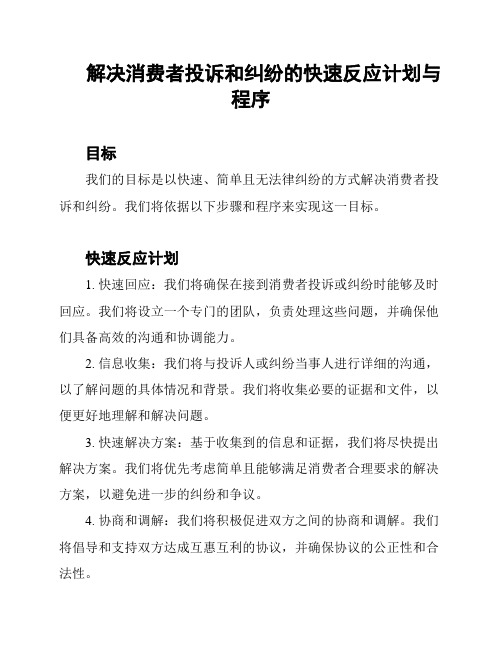
解决消费者投诉和纠纷的快速反应计划与程序目标我们的目标是以快速、简单且无法律纠纷的方式解决消费者投诉和纠纷。
我们将依据以下步骤和程序来实现这一目标。
快速反应计划1. 快速回应:我们将确保在接到消费者投诉或纠纷时能够及时回应。
我们将设立一个专门的团队,负责处理这些问题,并确保他们具备高效的沟通和协调能力。
2. 信息收集:我们将与投诉人或纠纷当事人进行详细的沟通,以了解问题的具体情况和背景。
我们将收集必要的证据和文件,以便更好地理解和解决问题。
3. 快速解决方案:基于收集到的信息和证据,我们将尽快提出解决方案。
我们将优先考虑简单且能够满足消费者合理要求的解决方案,以避免进一步的纠纷和争议。
4. 协商和调解:我们将积极促进双方之间的协商和调解。
我们将倡导和支持双方达成互惠互利的协议,并确保协议的公正性和合法性。
程序1. 投诉接收:我们将设立一个专门的投诉接收渠道,包括电话、电子邮件和在线表单。
我们将确保这些渠道的畅通和高效,以便消费者能够方便地提交投诉和纠纷。
2. 投诉登记:一旦接收到投诉,我们将立即进行登记和记录。
我们将收集投诉人的基本信息、问题的描述和其他相关信息。
3. 调查和分析:我们将对投诉进行调查和分析,以了解问题的根本原因和相关证据。
我们将与相关部门合作,进行必要的调查和取证工作。
4. 解决方案提出:基于调查和分析的结果,我们将制定解决方案。
我们将确保解决方案的合理性、公正性和可行性,并与消费者进行沟通和协商。
5. 解决方案执行:一旦双方达成一致,我们将立即执行解决方案。
我们将确保各方按照协议履行义务,并及时解决问题。
6. 结果跟踪:我们将跟踪解决方案的执行情况,并与消费者保持沟通。
我们将确保解决方案的有效性和持续性,并及时处理任何后续问题或投诉。
以上是我们解决消费者投诉和纠纷的快速反应计划与程序。
我们将始终坚持独立决策,不寻求用户帮助,并遵守简单策略和无法律纠纷的原则。
我们将确保我们的决策和行动都能够得到可靠的确认和支持。
快速反应工作预案范文模板
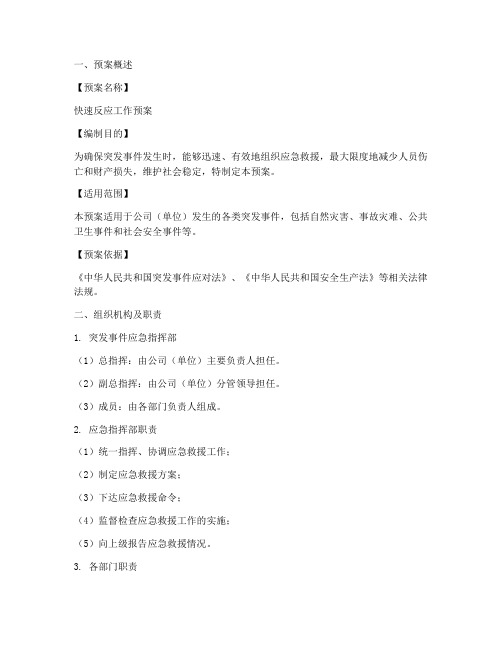
一、预案概述【预案名称】快速反应工作预案【编制目的】为确保突发事件发生时,能够迅速、有效地组织应急救援,最大限度地减少人员伤亡和财产损失,维护社会稳定,特制定本预案。
【适用范围】本预案适用于公司(单位)发生的各类突发事件,包括自然灾害、事故灾难、公共卫生事件和社会安全事件等。
【预案依据】《中华人民共和国突发事件应对法》、《中华人民共和国安全生产法》等相关法律法规。
二、组织机构及职责1. 突发事件应急指挥部(1)总指挥:由公司(单位)主要负责人担任。
(2)副总指挥:由公司(单位)分管领导担任。
(3)成员:由各部门负责人组成。
2. 应急指挥部职责(1)统一指挥、协调应急救援工作;(2)制定应急救援方案;(3)下达应急救援命令;(4)监督检查应急救援工作的实施;(5)向上级报告应急救援情况。
3. 各部门职责(1)综合部:负责收集、整理、上报突发事件相关信息,协调各部门开展应急救援工作;(2)安全环保部:负责现场安全监管,组织应急救援队伍;(3)人力资源部:负责组织人员疏散、安置;(4)财务部:负责应急救援资金保障;(5)其他部门:按照职责分工,协助应急指挥部开展应急救援工作。
三、应急响应程序1. 信息报告(1)突发事件发生后,事发单位应立即向应急指挥部报告;(2)应急指挥部接到报告后,应立即核实情况,并向上级报告;(3)上级接到报告后,应按照相关规定进行处理。
2. 应急响应(1)应急指挥部根据突发事件性质、影响范围和严重程度,启动相应级别的应急响应;(2)应急指挥部下达应急救援命令,各部门按照职责分工,开展应急救援工作;(3)应急救援过程中,如遇特殊情况,应急指挥部应调整应急救援方案。
3. 应急结束(1)突发事件得到有效控制,影响消除,应急指挥部决定结束应急响应;(2)各部门按照职责分工,恢复正常工作。
四、应急处置措施1. 自然灾害(1)地震、洪水、台风等自然灾害发生后,迅速组织人员疏散、转移;(2)采取有效措施,防止次生灾害发生;(3)及时开展救援工作,保障受灾群众基本生活。
快速反应控制程序

6.1《快速反应会议签到表》
6.2《快速反应问题清单》
6.3《质量Q图》
7.相关文件
通用-质量系统基础《GM-BIQS(Built-In Quality Supplybase)供应商制造质量》
8ቤተ መጻሕፍቲ ባይዱ附件
8.1工作流程图
4.3各生产部门的管理层人员(副主管或以上人员)必须参加协调会议开展情况。
4.4品管部领班负责更新每日快速反应跟踪板的相关信息,并作好相关改善记录。
5.工作流程描述
5.1为准备快速反应会议,每天开班时(大约上午8:30分),保持既定的会议时间(大约10
分钟),品管部必须收集过去24小时发生的重大质量事故,同时需要在《快速反应签到表》
本程序适用于公司的所有工序。
3.术语与定义
重大质量事故:当注塑当日制程平均不良在5%以上,电镀、喷涂制程平均不良在15%以上,或客户投诉以及环境物质不合格时,均定义为重大质量事故。
4.职责权限
4.1 品管部负责召开会议,生产部、工程部等部门根据责任归属进行改善问题。
4.2品管部负责收集每日会议的重大质量问题点,该会议最少每天一次。
的问题,写明其负责人的联系方式)。 如果需要汇报供应商的问题,则须在开会之前通知
供应商参加。
5.3 快速反应看板现场需张贴《质量Q图》,并确认前一天/班别的质量状况,并根据实际质量
状况实施更新。
5.4快速反应中的每个问题都必须有一个问题解决报告,如8D(PDCA)或类似的报告/纠正预
防措施报告(CAR),会后由品管负责人进行跟进并记录在《快速反应跟踪看板》中。由品
管部每月根据《快速反应问题清单》汇总所有改善报告并归档,将有代表性的个案加入公
IATF16949快速反应控制程序(含表格)

快速反应控制程序(ISO9001-2015/IATF16949-2016)1.0目的为了开展日常改善活动,确保产品质量,提高处理质量问题的效率,保证生产顺利进行和产品的准时交付。
2.0范围本程序适用于公司内外部质量问题的处理。
3.0职责任务和职责部门R=负责;S=支持;GM PM QA GD PD FD SD I=信息;O=如果有必要收集和汇总并确认何种问题要上快S R S S 速响应看板组织召开快速响应会议并跟踪措施R R R 的实施检查3.1品管部质量人员QE负责客户的外观件标准,并将标准及时传达各分厂;3.2PM负责执行客户外观件标准,并细化到相应对应的《产品检验规范》中;4.0术语和定义4.1快速反应:通过每日例会加强沟通和管理,采用目视管理方法展示重要信息,使应对重大的内、外部质量问题的反应标准化。
4.2问题解决:一个系统化的用来识别、分析和消除现状和现行标准或期望之间的差距,并预防根本原因再次发生的过程。
4.3经验总结:利用成功经验,防止错误重复出现。
4.1各客户外观件检验标准:5.工作程序5.1开会时间:每天8:30分,每次10~15分钟,会上只对质量和生产问题进行沟通。
5.2开会地点:快速响应看板前(质量)和生产办公室(生产部门)。
5.3参会人员:质量部经理、质量工程师、生产班组长、模具维修人员,工艺人员,设备维修人员。
5.4会议主题:应对每天人、机、料、法、环等各方面发生的问题。
5.5会议准备:质量部每天找出过去24小时发生的重大质量问题,其他部门上报人、机、料、法等发生的问题,具体问题包括:(1)客户关注的问题;(2)供应商关注的问题;(3)停线(内部或外部);(4)重复发生的质量问题;(5)除调试废品以外废品率超过综合废品率目标;(6)验证岗位中发现的问题;(7)分层审核中发现的问题;(8)其它内部质量问题。
5.6会议内容:(1)会议主持人协调各方意见,确定新问题的责任人和关闭日期。
快速反应会
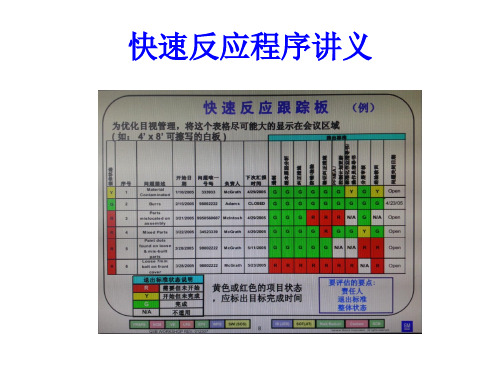
为准备快速反应会议,每天开班时,质量部必须 找出过去24小时发生的重大质量事故,包括:
•外部问题:
-客户关注的问题(PRR’s,客户抱怨,客户电话等) -分供方关注的问题
•内部问题:
-验证岗位*发现的问题 -过程分层审核*中发现的问题 -停线问题 -其他的内部质量问题(码头审核, 产品遏制行动等)
•一次下线合格率数据(FTQ,First Time Quality)
问题解决
什么是“问题”?
所谓问题,就是当前状态和客户满意之间的差距
问题解决
问题是持续改善的种子! 问题是积极的机会!
没有任何问题则意味着有些错误已经发生!
•定义:
–一个系统化的用来识别、分析和消除现状与现行标准或期望之间的 差距,并预防根本原因再次发生的过程。
问题解决的基本原则
•抛开先入为主的想法。 •避免对没有数据支持的问题做出反应。 •将问题分解。 •直接观察问题的发生现象和原因点(Point of Cause),而不是通过 二手信息。 •适当延迟根本原因分析直至已彻底弄清楚究竟发生了什么。 •标准是什么?与应该发生的情况相比,实际究竟发生了什么? •建立原因/结果间的关系。 •不停地问“为什么?”直到你通过根本原因分析可以预防问题的 再次发生时。
快速反应程序关键步骤
• 质量部收集过去24小时内发生的重大质量事件
• 通过每日快速反应会议指定每个问题的负责人。会后责 任人应通过问题解决流程来纠正问题和预防问题的再次 发生。 • 责任人应完成所有的退出项目。沟通汇报解决问题的过 程。快速反应跟踪表显示所有退出项目状态是绿色,表 示问题解决完成。 • 通过快速反应跟踪板跟踪问题。要求责任人应定期在快 速反应会议上更新状态。
快速反应总结
快速反应控制程序(含表格)

快速反应控制程序(ISO9001-2015/IATF16949-2016)1.0目的通过每日例会加强沟通管理;使用标准化的反应流程来应对重大的内外部质量问题;提供系统的问题解决方法,提高质量水平和客户满意度2.0适用范围本程序适用于公司内外部质量问题的处理。
3.0术语3.1快速反应:通过每日例会加强沟通和管理,采用目视管理方法展示重要信息,对重大内、外部质量问题的反应标准化。
3.2问题解决:一个系统化用来识别、分析和消除现状和现行标准或期望之间的差距,并预防根本原因再次发生的过程。
3.3交接班信息传递:确保所有班次之间有开放的沟通渠道。
3.4经验总结:利用成功经验,防止错误重复出现。
4.0职责4.1生产管理部:4.1.1负责快速反应会议的支持召开,及时更新快反问题进展状态的更新;4.1.2负责指定快反问题解决责任人;4.1.3负责制定专人维护跟新快速反应展板的更新;4.1.4负责快速反应问题阶段跟踪及关闭条件的确认;4.1.5负责快反问题的完成后内部传递;4.1.6负责内、外部质量问题遏制措施跟踪;4.2质量管理部:4.2.1负责收集内、外部质量问题的并传递给生产制造部;4.2.2负责责任问题的措施制定、实施、跟踪、汇报;4.2.3负责相关部门质量工具的指导及应用;4.3技术部:4.3.1负责责任问题的措施制定、实施、跟踪、汇报;4.3.2负责问题解决过程中的技术支持;4.3.3负责问题关闭后PFMEA的更新管理;4.4作业部:4.4.1负责内、外部质量问题遏制措施的执行;4.4.2负责责任问题的措施制定、实施、跟踪、汇报;4.4.3负责制造问题解决过程中措施的执行及跟踪;4.5物流部门4.5.1协助物流过程中紧急遏制措施实施;4.5.2参与相关责任部门根本原因分析、负责物流过程中纠正措施落实并进行效果验证;4.6相关部门:4.6.1负责责任问题的措施制定、实施、跟踪、汇报;4.6.2涉及责任问题的协助及参入;4.7总经理/副总经理4.7.1不定期参加快速反应会议;4.7.2负责批准纠正/改进措施所必需的资源配置;4.7.3定期对快速反应会议予以跟踪,在分层审核时进行跟踪;5.0工作流程:5.1开会时间:每天早上9:00开始,每次时间10~20分钟的站立会;5.2开会地点:快反会议室(作业一部一楼会议室);5.3参会人员:生产管理部、作业部、质量管理部、物流部等部门部长及问题责任汇报人员;5.4会议主持人:第一责任人第二责任人第三责任人生产管理部副总生产管理部长质量管理部长5.5快反会议流程5.5.1会议类型:生产例会/早会及快速反应会5.5.2生产例会:5.5.2.1跟踪生产过程中的生产、安全问题,利用生产例会展板指定责任部门/责任人进行问题解决;5.5.2.2问题责任人部门/人按照要求汇报问题的解决情况;5.5.2.3在生产例会上未能按照要求解决的问题,由生产管理部将问题升级至快速反应展板,按照快反问题解决流程执行。
- 1、下载文档前请自行甄别文档内容的完整性,平台不提供额外的编辑、内容补充、找答案等附加服务。
- 2、"仅部分预览"的文档,不可在线预览部分如存在完整性等问题,可反馈申请退款(可完整预览的文档不适用该条件!)。
- 3、如文档侵犯您的权益,请联系客服反馈,我们会尽快为您处理(人工客服工作时间:9:00-18:30)。
5工作流程
流程
召开快速反应会议(注1)
岗位
各分厂厂长 生产部部长 各分厂厂长 质量保证部部长 技术工程部部长 机动技安部部长 质量副总经理 各分厂厂长 质量保证部部长 技术工程部部长 产品研发部部长 整改小组组长
相关文件
每日快速反应会议签到表 会议纪要
日常快速反应会议流程 (注2)
Q图
Hale Waihona Puke 内、外部质量问题快速反应 流程 (注3)
5.2.5出现内部质量问题时,各分厂值班长在问题发生 后2小时内,在分厂Q图上挂黄色标识。出现外部质 量问题时,质量保证部接到信息2小时内,在公司Q 图上挂红色标识。无质量问题时由各分厂值班长、质 量保证部在分厂、公司Q图上挂绿色标识,以证明过 去24小时内无质量问题,悬挂时间不得超过上午9点。 5.3 内、外部质量问题快速反应流程 5.3.1 内、外部质量问题整改的组织跟踪及验证 出现内、外部质量问题时,各类主管人员按下列要求 任命质量问题整改小组组长,组长组织质量问题整改 小组开展工作。
组长工 作任务 组织召 开问题 解决会 议,对 问题完 成情况 进行跟 踪。
验证 各分厂厂长 组织相关人 员对完成情 况进行验证。 质量保证部 组织对完成 情况进行验 证。
供方 质量问题
新产品 质量问题
外部、内 部重大质 量问题 (批量的、 跨部门的 质量问题)
5.4内部、外部质量问题解决分析会 5.4.1整改小组组长组织召开问题解决会议,组织分析产生问题的 根本原因,落实质量问题解决责任人,对质量问题进行遏制,明 确工作任务,组长对纠正措施的执行情况进行跟踪,必须保证所 有的问题被关闭和退出标准中的各个项目都能按期完成。 5.4.2外部质量问题必须在24小时内制定并执行临时措施,找出出 现问题的点 (分界点),查清所有可疑产品的地点、数量,明确遏制负责人, 对所有可疑产品进行遏制。在问题没有得到解决之前,质量保证 部要确定特别控制方案(例如100%检验)。对于顾客的其他回复 要求,整改小组组长要在24小时内给予初始回复,对未能达成一 致事宜可确定再次沟通时间与形式。若质量问题整改报告需提交 给顾客,整改小组组长要在24小时内将问题解决报告传递至顾客 (如顾客有指定报告格式按顾客要求提交,若顾客没有指定按公 司报告格式提交)。
参加成员 值班长、班组长、相关 操作者、技术工程部工 艺员 质保部供应商管理员、 技术工程部工艺员、产 品研发部相关人员 值班长、质保部部长或 相关人员、技术工程部 部长或工艺员、产品研 发部部长或相关人员 公司领导、质量保证部 部长/副部长/相关人员、 技术工程部部长/工艺员、 产品研发部部长/相关人 员、各分厂厂长、值班 长、相关操作者
内、外部质量问题解决分析 会 (注4)
问题解决报告 (8D报告或A3提案)
问题退出标准 (注5)
整改小组组长 质量保证部部长 质量保证部工艺员
遏制工作表 快速反应表/板
注1 召开快速反应会议 1.1 快速反应会是一个问题沟通会议,不是问题解决 会议。快速反应会分为各分厂内部快速反应会、公司 级快速反应会。各分厂内部快速反应会每天早8:00召 开,公司级快速反应会生产部每日下午4:30分组织 召开。快速反应会议利用10-20分钟时间在生产现场/ 生产现场会议室/公司快速反应室召开,会议内容由主 管部门形成会议纪要,以OA或书面的形式发放到各 责任部门/责任人。总经理、质量副总经理可随时参加 公司级快速反应会议。
快速反应程序
王静娟 2009年5月11日
快速反应程序
1 目的 使用科学、有效的方法,及时解决出现的内/外部质量问题,通过例会加强交流, 用可视化的方法展现重要问题,使各种质量问题得到迅速、有效的解决。 2 范围 本程序适用于公司内、外部重大质量问题的解决。 3 术语和定义 3.1 外部问题 3.1.1 客户关注的问题(顾客信息反馈、电话等) 3.1.2 供应商的质量问题 3.2内部问题 3.2.1 生产过程控制中发现的问题 3.2.2 过程分层审核中发现的问题 3.2.3 造成停线的问题 3.2.4 其他的内部质量问题 3.2.5 一次交验合格率数据(FTQ) 3.2.6 检验工序发现的质量问题 3.2.7 各种作业指导书在编制、执行以及后续审核中发现的问题 3.2.8 SPC发现问题
质量保证部部长、副 部长 技术工程部部长 机动技安部部长 副部长 各分厂厂长 采购中心主任
副部长 部长助理 部长指定人员 副部长指定人员 分厂值班长 副主任 相关业务员
生产部分配 工作任务, 指定专人对 问题完成情 况进行跟踪、 验证
5.2日常快速反应会议流程 5.2.1会议汇报顺序:质量问题——安全生产问题——生产过程中 存在的问题——设备问题等。 5.2.2质量问题是对过去24小内发生的质量问题进行回顾。各分厂 快速反应会由值班长汇报生产现场质量等方面的情况;公司级快 速反应会由各分厂厂长汇报本单位生产线不合格品统计情况、生 产过程中存在的内部质量问题;质量保证部部长汇报生产现场质 量情况,包括出现的内部重大质量问题、外部质量问题。各类其 他问题由各分厂主管人员、公司主管部门人员 进行汇报。 5.2.3如有质量问题发生时,对质量问题进行详细描述,如产品名 称、不合格描述、不合格数量、不合格比例等。 5.2.4参加快速反应会议人员要在“每日快速反应会议签到表”签 到,会议由会议组织者指派专人做好会议纪要并下发到相关单位。
5.4.3从发生公司内部、外部质量问题至问题关闭期间,整改组长 要在每天快速反应会议上汇报整改进展情况。整改小组组长按纠 正措施的时间节点更新整体状态。 5.5问题退出标准 5.5.1 遏制,对不合格产品可能存在的场所(外部、内部)进行遏 制,填写“遏制工作表”,详见《生产过程不合格品控制程序》; 5.5.2质量问题必须在48小时内分析出问题可能存在的原因。在原 因分析的过程中要采用5个为什么的方法,当一个原因被发现时, 不停地问为什么,直到找到真正的根本原因,整个分析的思路要 从“为什么生产过程中没有防止缺陷;为什么质量控制过程中没 有控制住缺陷;为什么先期质量策划过程中没有预测出缺陷的产 生”。对所分析出的原因,要确定是普通原因还是特殊原因,要 在原因分析中注明,要首先针对普通原因采取措施,要针对最后 一个why确定纠正措施,明确责任人、完成时间。
4 权责 4.1 各分厂厂长每天早上组织召开分厂内部快速反应 会议,对分厂内过去24小时的质量问题进行回顾。 4.2 生产部每天下午4:30组织召开公司级快速反应会。 4.3 内部重大质量问题(批量的、跨部门的质量问 题)、外部发生时,质量保证部部长/质量副总经理组 织召开快速反应会,质量副总经理任命质量问题整改 小组组长,组长组织召开质量问题解决会议。 4.4 质量保证部、技术工程部、产品研发部、机动技 安部等配合各分厂解决生产现场发生的质量问题。
5.5.7 要将出现的质量问题纳入分层审核。 5.5.8 要将出现的质量问题纳入到经验教训数据库。 5.6退出标准状态说明: R(红色)需要但未开始 Y(黄色)开始但未完成 G(绿色)完成 N/A(无色)不适用 5.7每一项退出标准要分别确定负责人及完成时间,各负责人在规 定的时间内,将整改证据提交给整改小组组长,整改小组组长根 据完成情况更新退出标准状态及总体状态。 5.8整改状态为G(绿色)时,整改小组组长向质量保证部提出关 闭申请,质量保证部验证合格后在提交的报告封面签字,该问题 即为关闭,从关闭日期起一个月后,快速反应跟踪表中的相关内 容才能去除。 5.9整改小组组长在所有问题关闭后,要将此次质量问题所涉及到 所有整改报告和检测数据提交质量保证部,质量保证部纳入到经 验教训数据库中,具体详见《经验教训总结程序》。
6 相关/支持性文件 《内、处部质量问题处理程序》 《QSB质量体系基础》 《经验教训程序》 7 质量记录 Q图 每日快速反应会议签到表 会议纪要 问题解决报告(8D报告或A3提案) 快速反应跟踪表/板 遏制工作表
快速反应会职责及参加人员如下:
分类 各分 厂快 速反 应会 公司 级快 速反 应会
主持人 各分厂 厂长
替代人 员 副厂长 值班长
必须参加部门/人 副厂长、值班长、技 安员、班长 需要时操作者参加
替代人员
备注 分厂厂长分 配工作任务, 指定专人对 问题完成情 况进行跟踪、 验证
生产部 部长
部长 助理 值班长
质量问题 内部 质量问题
会议组织 各分厂厂长组织快速 反应会,任命整改小 组组长,分配工作任 务。 质量保证部部长组织 快速反应会,任命整 改小组组长,分配工 作任务 产品研发部部长组织 快速反应会,任命整 改小组组长,分配工 作任务 质量保证部部长或质 量副总经理组织快速 反应会,任命整改小 组组长,分配工作任 务。
5.5.3 纠正措施,针对根本原因采取纠正措施。 5.5.4质量问题必须在15天内制定出纠正和预防措施, 纠正和预防措施要针对问题产生的每一个原因制定, 所制定的措施要能防止问题的再发生,应多采用防错 的方法,使之彻底解决。 5.5.5对采取的纠正措施进行验证,包括以下四个方面 进行验证:根本原因,临时措施,长期措施,问题的 预防。验证已实施的措施是否将问题彻底消除(短期 措施,长期措施,及其它类似的流程),并且不会产 生其它的问题。 5.5.6 必须针对所发生的质量问题对FMEA进行评审, 如FMEA没有此问题的分析,必须重新进行分析,对 因FMEA的更新引起控制计划更新的,必须更新控制 计划、操作指导书,以预防问题重复发生。