三现五原则手法
三现五原则-最终版

要点二
详细描述
为了确保三现五原则的有效实施,企业应重视员工的培训 与参与。这可以通过开展定期培训、提供学习资源、鼓励 员工参与决策等方式实现。此外,企业应建立良好的激励 机制,表彰在原则实施过程中表现优秀的员工,以提高员 工的积极性和参与度。通过提高员工素质和参与度,企业 可以进一步推动三现五原则的落实,实现更好的发展成果 。
持续改进与优化的实施与效果
总结词
持续改进与优化是五原则的核心目标之一,它有助于组 织不断适应变化、提高竞争力和可持续发展。
详细描述
组织需要鼓励员工不断寻求改进和优化的机会,并为其 提供必要的资源和支持。这包括制定改进计划、设立改 进团队、引入创新技术和方法等。同时,组织还需要建 立有效的绩效评估体系,以衡量改进与优化的成果并持 续改进。持续改进与优化能够提高生产效率、降低成本 、增强创新能力、提升客户满意度和增强组织竞争力。
现状反思
定期对当前的工作情况进行反思和总结,找出可以改 进的地方。
现行措施调整
根据实际情况和反馈,及时调整现行措施,以实现持 续改进的目标。
04
五原则的实施与效果
管理层的决心和承诺的实施与效果
总结词
管理层对实施五原则的决心和承诺是至关重 要的,它决定了整个组织对五原则的重视程 度和执行力。
详细描述
VS
详细描述
随着企业内外部环境的变化,三现五原则 的实施方案也应不断调整和完善。企业应 定期评估原则的执行情况,总结经验教训 ,并根据实际情况调整实施方案。此外, 企业应关注行业动态和最佳实践,不断引 入新的理念和方法,以保持原则的先进性 和有效性。
原则五:员工培训与参与
要点一
总结词
员工培训与参与是三现五原则的重要支撑,需要提高员工 素质和参与度。
品质的三现五原则
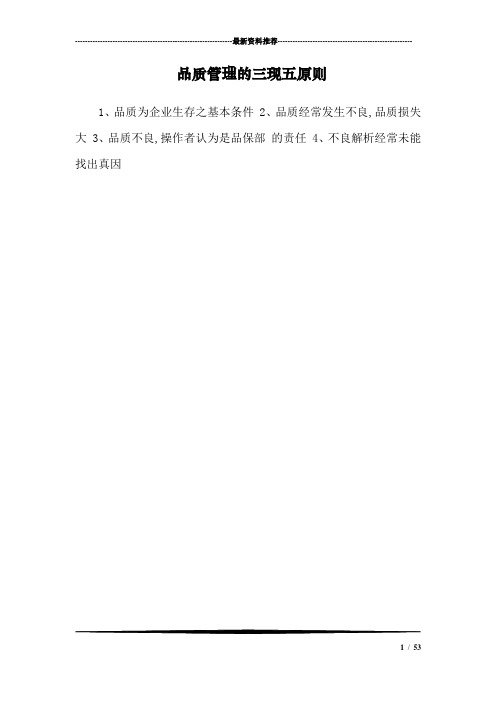
---------------------------------------------------------------最新资料推荐------------------------------------------------------品质管理的三现五原则1、品质为企业生存之基本条件2、品质经常发生不良,品质损失大3、品质不良,操作者认为是品保部的责任4、不良解析经常未能找出真因1/ 531、了解并运用三现五原则解析手法,真正改善重要品质问题2、解决问题→持续有效解决问题→不再是问题3、解决客诉品质问题挑战“零不良”---------------------------------------------------------------最新资料推荐------------------------------------------------------ 三、三现现物三现现状现场3/ 53现状把握确认项目1、机种、零件名称/号码 2、发生场所/环境/使用条件 3、发生的现象/问题 4、发生日期 5、引擎号码---------------------------------------------------------------最新资料推荐------------------------------------------------------ 现状把握确认项目6、发生件数/严重性 7、行驶里程/耐久性 8、制造日期/批重性 9、出车日期/库存性 10、不良品品质确认5/ 53现状把握确认项目11、量产中品质水准确认 12、开发阶段品质水准比对 13、设计变更履历 14、其他异常履历 15、标准确认(图面、作业、控制计划、检验标准…)---------------------------------------------------------------最新资料推荐------------------------------------------------------ 四、五原则五原则7/ 531、把握现况现状把握目的针对问题,全盘调查事实掌握变异(机遇/非机遇原因) 归纳可疑方向---------------------------------------------------------------最新资料推荐------------------------------------------------------ 1、把握现况 - 5W2H–类型、种类、受影响的部分。
三现五原则
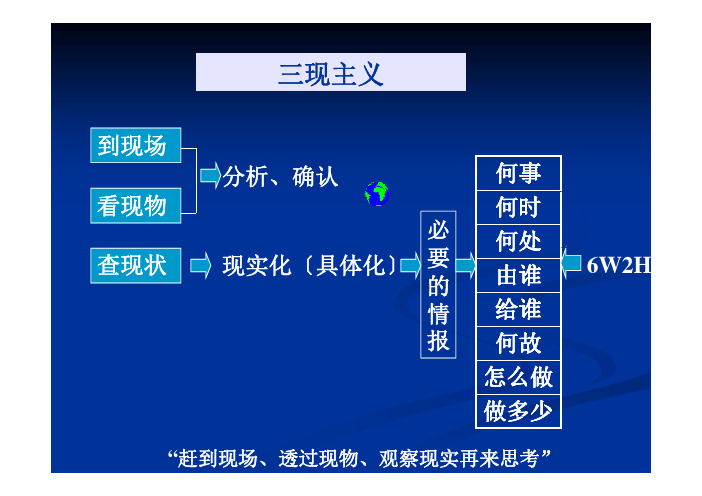
到 场 到现场 分析、确认 看现物 查现状 必 现实化〔具体化〕 要 的 情 报 何事 何时 何处 由谁 给谁 何故 怎么做 做多少
6W2H
“赶到现场、透过现物、观察现实再来思考”
三现五原则法: 三现五原则法 *三现:现场、现物、现状 *三现: 现场、现物、现状 发生状况 *五原则: *五原则 把握现状: 把握现状:时间、地点、现象、总生产量、不良 时间、地点、现象、总生产量、不良 数、不良率 不良率 。 查明原因: 制造不良原因:潜在因素、流出因素 制造不良要因 数据 不良简图 制造不良要因:数据、不良简图 对策追踪: 暂时对策 永久对策 永久 对策 确定所采措施 效果评估: 效果评估:改善后数据收集、左证成效 改善后数据收集、左证成效 回馈源流: 回馈源流 水平展开,引用于类似产品之设计开发 回馈源流:水平展开,引用于类似产品之设计开发 水平展开 引用于类似产品之设计开发 输入及制程规划之标准化
五原则表五个步骤
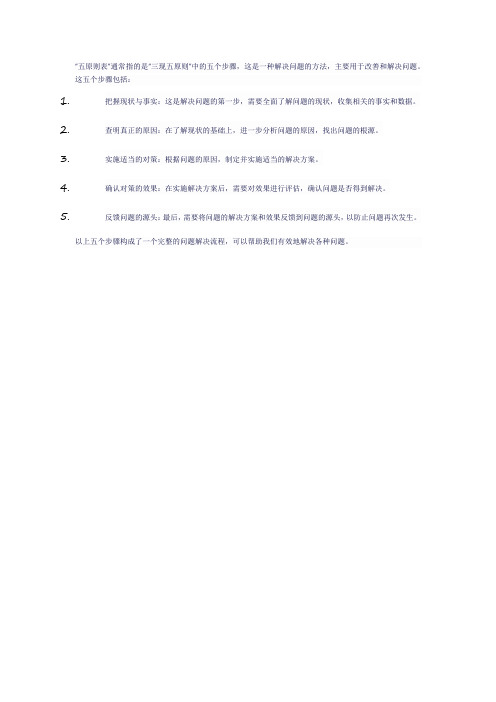
“五原则表”通常指的是“三现五原则”中的五个步骤,这是一种解决问题的方法,主要用于改善和解决问题。
这五个步骤包括:
1.把握现状与事实:这是解决问题的第一步,需要全面了解问题的现状,收集相关的事实和数据。
2.查明真正的原因:在了解现状的基础上,进一步分析问题的原因,找出问题的根源。
3.实施适当的对策:根据问题的原因,制定并实施适当的解决方案。
4.确认对策的效果:在实施解决方案后,需要对效果进行评估,确认问题是否得到解决。
5.反馈问题的源头:最后,需要将问题的解决方案和效果反馈到问题的源头,以防止问题再次发生。
以上五个步骤构成了一个完整的问题解决流程,可以帮助我们有效地解决各种问题。
三现原则是指什么

三现原则是指什么
三现原则是现场、现物、现实。
现场是解决问题要到问题发生的场所去,把现场看作问题发生的根源、管理水平提升的基石。
现实是依据事实和数据找出问题的根源。
生产管理中的五原则:
1、发生状况(现象、申诉内容、发生次数),把握事实(对零部件确认结果、原因分析、现正生产该部件品质状况)。
2、查明原因(发生途径、问题再现试验,5个WHY的分析)。
3、适当的对策(对策内容、效果预测)。
4、确认效果(确认对策的实绩效果)。
5、对源头的反馈(要落实到体系、组织标准化的内容)。
5WHY解决问题的三现五原则

三现五原则
1.现场:不良品发生的原地,环境因素。
2.现物:实际不良品。
3.现状:不良发生的状况,包括实际状况 五原则
1.把握现状:零件的品质状态,确认结果,要因分析。
2.查明原因:再现试验,原因分析。
3.适当对策:对策内容,效果预测。
45.回馈更正:体制改善,反应修正。
如何做有效的分析与报告
问题解决之五大原则
1.1 发生状况:现场、现物、现状、日期、数量、LOT NO。
1.2 把握现状:基准值与实测的差异,再现试验,要因分析。
现在生产品质状况。
发生对象与相关原材料、中间制品。
1.3 原因的查明:分析主要要因。
再现性原因的确认。
1.4 适当的额对策:暂时或者永久性的对策内容,日期、LOT NO.在库品处理,已出库品处理。
1.5 确认对策的效果:比较对策前后都额差异。
1.6 回馈。
三现五原则over[1]1
![三现五原则over[1]1](https://img.taocdn.com/s3/m/698f88d076eeaeaad1f33070.png)
对策:首末件检查→全检
10.要因:焊接后H方向尺寸NG
对策:焊接治具H方向调整
质量培训专用教材
16
核准
对策单位 复核
承办
1.发生状况 机种
零件编号
零件名称
发生时间
发生地点
数量
不良现象/抱怨内容
反应单位
生产日期
责任单位
临时措施:
3.问题点五层分析
问题 ①
WHY ②
发 生 源
WHY ③
WHY ④
流 出 面
实例:不良现象:踩剎车时BrakePedal有上、下作动感觉
1
2
3
4
5
為什
目視檢查時
麼之 Drum 內徑黑 未檢查
五層 皮產生
Drum 內徑
分析
尺寸 NG
無檢查基準 鑄造時 Drum 加熱變形 模具與 Drum 間隙過大
溫度過高加熱不 無溫度控制
均勻(500℃↑ ) (180℃~200℃)
模具磨損
無標準規定
分析方法: 1.制造面:分析4M的变化点→真因对策。 2.流出面: a.分析制造中的流程→作业环境、作业检验工程标准; b.分析检验的流出面:检验标准、限度样品、自动检测、 防呆装置。
质量培训专用教材
13
十、解析对策应五层分析内容连贯
意义:五层分析是一个形容词,代表追根究底的意思,其目 的在寻找真正的原因,并不是一次要作五次为什么分 析,可以比五次少,也可以比五次多。
担当 期限
效果确认
判定
7.效果确认(收集改善后一段时间的数据判断改善的效果) 确认者
单责 位任 主单 管位 核接 准单 后后 回应 复立 品即 保采 部取 ;临 品时 保措 部施 将消 稽除 核顾 对客 策/ 的下 实工 施程 状的 况抱 和怨 实; 施对 的策 效报 果告 。原
8D手法+5W分析法
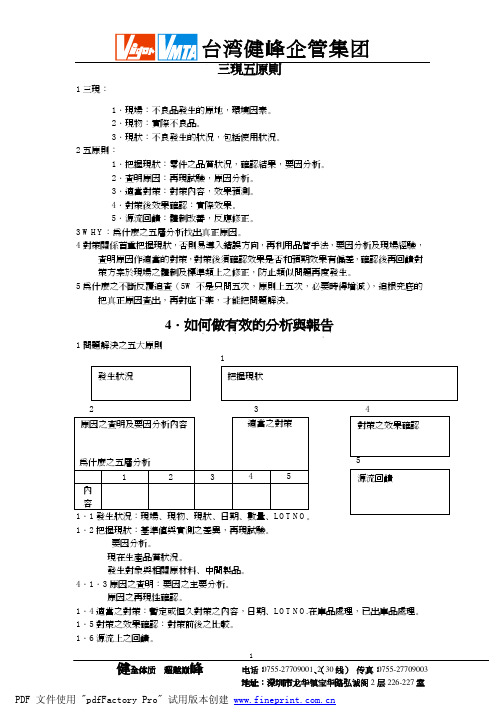
是否適合生產能力
2 . 設 備 、 工 具
是否適合工程能力 加油是否適切 檢查是否充分 是否因故障而停止 是否有精度不夠的 是否發出異常聲音來 配置是否適當 數量上是否有過分不足的情形
有否整理整頓
數量有否差異 等級有否差異 品牌是否有差異 3 是否有異材的混入 . 庫存量是否適當 原 是否有所浪費 料 處理是否良好 未成品是否被放置不管 配置是否良好 品質水準是否良好
作業標準的內容是否良好 作業標準是否予以改訂 該方法是否能安全去做 4 是否是能造出優良製品的方法 . 是否是能增進能率的方法 方 順序是否適正 法 程式是否良好 溫度、濕度是否適當 照明、通風是否適當 與前後工程的銜接是否良好
Ⅲ.現場的三大缺點
人員是否勉強
技能是否勉強
1 . 有 否 勉 強
方法是否勉強 時間是否勉強 設備是否勉強 工具是否勉強 資材是否勉強 生產量是否勉強 庫存量是否勉強
台湾健峰企管集团
三現五原則
1 三現:
1.現場:不良品發生的原地,環境因素。 2.現物:實際不良品。 3.現狀:不良發生的狀況,包括使用狀況。 2 五原則: 1.把握現狀:零件之品質狀況,確認結果,要因分析。 2.查明原因:再現試驗,原因分析。 3.適當對策:對策內容,效果預測。 4.對策後效果確認:實際效果。 5.源流回饋:體制改善,反應修正。 3 WHY:為什麼之五層分析找出真正原因。 4 對策關係首重把握現狀,否則易導入錯誤方向,再利用品管手法,要因分析及現場經驗, 查明原因作適當的對策,對策後須確認效果是否和預期效果有偏差,確認後再回饋對 策方案於現場之體制及標準類上之修正,防止類似問題再度發生。 5 為什麼之不斷反覆追查(5W 不是只問五次,原則上五次,必要時得增減),追根究底的 把真正原因查出,再對症下藥,才能把問題解決。
解决问题的五原则
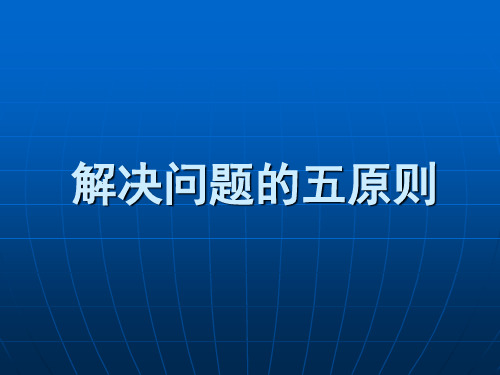
写好五原则表的关键:运用五原则手法分析、解决问题
五原则表的表达要求
要用简单、具体、准确的表述语言填写事实,不要 使用抽象性、否定性(确实、正确、避免、不要、 可能等)的语言。 要求插入示意图、照片、路线图、表格等,这样, 在传递过程时,就可以使你表达的意思和阅读的人 理解内容的一致。 ①.尽量使用短句写 ②.用小学六年的孩子能理解的话写
解决问题的五原则
五原则的定义
“五原则”是指从“三现主义”出发,分五个步骤解决问题
充分把握事实 查明的真正原因 实施切实的对策 确认对策的有效性 反馈到问题的源头
1
五 个 步 骤
2
3 4 5
三现主义
不但适用于制 造现场,也适 用于广泛的其 它工作。
亲自接触实物
亲自到现场
(现物)
总是以事 实为基础 而行动
异常对应难以预测的现象: 临时调休 突发的产品质量问题 突发的设备故障 到货材料、零件异常 停电、地震、洪灾、台风等
工厂是避免不了变化 点的,问题是对变化 点有没有制定正确的 对应方法
三、充分把握事实—2
<要因变化点的确定>
4M变化点
人 变化点的具体事例
(批次追踪及变化点调查)
对预测的变化点,没有进行 正确的管控时也会发生问题
③.用小学六年之前学过的汉字写
④.尽量不要使用专业性很强的文字和西洋文字 (英 、日文)写
五原则表填写要领
01.标题
发生状况 现状把握
02.发生状况
1-1 不良品确认 结果
合适 的 对 策
1-2 批次跟踪 变化点调查
1-3 原因分析
查 明的原 因
检查对 策 的效 果
2-1.查明的原因 发生机理 再现试验
品质管理的三现五原则 ppt课件
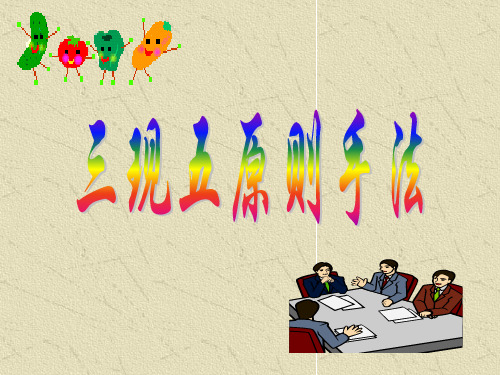
2-A 查明原因(WHY WHY 分析)
2-B 查明原因(发生的途径、问题再现试验WHY WHY分析)
3 采取)适当的对策 (对策内容、效果预测PPA) 4确认(对策)效果(效果实绩) 5对(问题)源头的反馈(需落实到体制、组织的内容)
品质管理的三现五原则
右腕受伤
1- A 发生状况(现象、申诉内容、发生次数、5W1H处置内容)
笨,没有学问无颜见爹娘 ……” • “太阳当空照,花儿对我笑,小鸟说早早早……”
4
1、了解并运用三现五原则解析 手法,真正改善重要品质问 题
2、解决问题→持续有效解决问 题→不再是问题
3、解决客诉品质问题挑战“零不良”
品质管理的三现五原则
现物
三现
现状
现场
品质管理的三现五原则
1、机种、零件名称/号码 2、发生场所/环境/使用条件 3、发生的现象/问题 4、发生日期 5、引擎号码
记入要领
1-B 对事实的把握(对零部件的确认结果、原因分析、现在正在生产的该零部件的品质状况)
1、在确认事故发生时,也发现了
同样汽缸倒下来的情况,作业
人
设备
人员每一次都是同样地用手把 它扶起来(还了解到一般9个 里会倒1个)
疲劳
注意 不够
没有反馈 不知道方法
作业标准不完善
2、在事故发生时,作业人员的健
汽缸倒下来这 一情况未反馈
与特性要因图(鱼刺图),利用系统的、有条理的Q&A(提 问和回答)方法,抓住找出真正的原因 2-A 查明原因( WHY WHY 分析)
1
2
3
4
5
内
检验: 为何会检测不出来。
品质管理的三现五原则
意义:为什么之五层分析是一个形容 词,代表追根究底的意思,其目 的在寻求真正的原因,并不是一 次要作五次为什么分析,可以比 五次少,也可以比五次多,只要 能寻求出真正的原因。
质量管理三现五原则

2-B 查明原因(发生的途径、问题再现试验WHY WHY分析)
3 采取)适当的对策 (对策内容、效果预测PPA) 4确认(对策)效果(效果实绩) 5对(问题)源头的反馈(需落实到体制、组织的内容)
15、案例
右腕受伤
1- A 发生状况(现象、申诉内容、发生次数、5W1H处置内容)
1、发生场所:汽缸压铸NO.2生产线。 2、 发生状况:请参照右手腕受伤素描图
检验: 为何会检测不出来。
10、五层分析
意义:为什么之五层分析是一个形容 词,代表追根究底的意思,其目 的在寻求真正的原因,并不是一 次要作五次为什么分析,可以比 五次少,也可以比五次多,只要 能寻求出真正的原因。
10、五层分析
实例说明: 不良现象:踩刹车时有上、下作动感觉。
1
2
3
4
5
目视检查
为什 Drum内 未检查
3、五层分析是三现五原则单之中 心思想及布局。
11、要因 对策案例练习
1.要因:人为疏忽 对策:教育训练加强
2.要因:XX治具磨损 对策:更换新治具
3.要因:遗漏焊接 对策:后工程实施全检以确保
4.要因:半成品因台车太小不慎流入后工程 对策:台车修改加大
5.要因:修护车辆,等待时间长 对策:等待时间提供杂志阅读
1、把握现况 - 5W2H
WHERE 何地 – 记入问题发生的场所。 WHY 为什么 – 具体的内容 HOW 怎么样 – 问题是怎样发生的 HOW MANY 什么程度 – 问题发生量,
程度。
1、把握现况的填写方法
1、问题点的概要(信息的收集、整 理)。例:针对部品或工程。
2、问题再现试验的结果 3、现行品(现在生产)的品质状况 4、发生的对象范围
解决问题的五原则
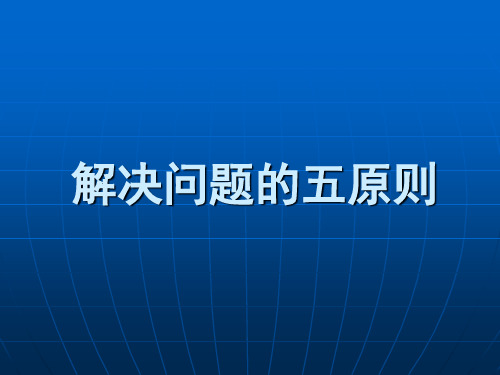
发
临时调休
点有没有制定正确的
的 变 化 点
突发的产品质量问题 突发的设备故障 到货材料、零件异常 停电、地震、洪灾、台风等
对应方法
三、充分把握事实—2 (批次追踪及变化点调查)
<要因变化点的确定>
对预测的变化点,没有进行 正确的管控时也会发生问题
4、发生数量:明确不良数量、不良率 车架/发动机号、购买日期、行驶里程(如果是市场发生时)
从反馈 部门得 到正确 的信息
5、发生现象:在什么情况下发生的? ●外观、装配问题可简单描述 ●动态问题要详尽描述:离合器手柄作动不顺畅!详尽:哪种角度还是全角度?
6、处理情况 发生问题的车(机)型及零件的处理内容 ●怎样处置:换装、挑选、调整、返修等
变化点 固定、反复的作业
通常这个能持续的话就 不会发生问题
可
非固定、非定期的作业
预
机种准备
测
夹具、刀具、设备、模具维修
由于有这样的事情出现导 致问题发生时就被定义 为要因变化点(见下页)
的
工艺变化、加工方法变更
变
零件更换
化
避免不了变化
突
异常对应难以预测的现象: 点的,问题是对变化
2日
3日
100
100
100
100
300
问题对象批次
4日
5日
100
/
100
100
变人
化 设备
☆设备变更了
点 方法 基于4M进行变化点的调查
材料
<批次追踪及变化点调查结果>
1)问题批次是×月×日~ ×月×日生产的××台
2)对象批次的变化点是什么?
<要点> 问题的发生总是 由变化点引起
品质管理的三现五原则

5、变化点分析不清楚
疑 问 点:以前为何不会发生不良,现在才发生? 一定是哪里有变更,变化点在哪里? 思 考:不良隐藏於变化点中。
分析方法:4M1D里寻找真因 人[Man]:人员有否更换,有否依标准作业、人员之 士气等。 机[Machine]:机器设备、镆、治、检、工具有否调 整、变更等。 料[Material]:材料有否改变、前工程流入件不良事 等。 方法[Method]: 标准有否规定?标准是否明确? 设计[Design]: 是否设计变更等。
疑 问 点:常发生的直觉判断 ~ 焊接强度不足对策:焊道加长2mm.正确吗? ~ 模温不足变形对策:模温提高10℃.没问题吗? 思 考:加长2mm、提高10℃如何得到的?
直觉+经验≠事实
100个直觉或经验不如1个数据
分析方法:科学的根据=实验数据 ~ 有实验的数据才能决定新的标准。 ~ 要去试验出焊道加长2mm及模温提高10℃是作 业最好的条件。
9、制造面、流出面未检讨
疑 问 点:1.为何会流出?为何会制造出?为何设备检不出? 2.流出面之解析对策经常被疏忽。 思 考:顾客所反应之问题必定制造面、流出面共同发生, 仅对策制造或流出面并未能彻底解决问题。 分析方法:1.制造面→分析4M之变化点→真因对策。 2.流出面→a.分析制程中之流程→作业环境、作 业检验工程标准。 b.分析检验之流出→出货检验标准、 限度样品、自动检测、防呆装置。 检验: 为何会检测不出来。
发生问题 零件号 零件名称
提出部门
日期 批准 审核 编制
日期
编制部门
批准 审核 编制
1-A 发生状况(现象、申诉内容、发生次数、5W2H处置内容)
1-B 把握事实(对零部件的确认结果、原因分析、现在正在生产的零件的品质状况)
三现五原则--最终版
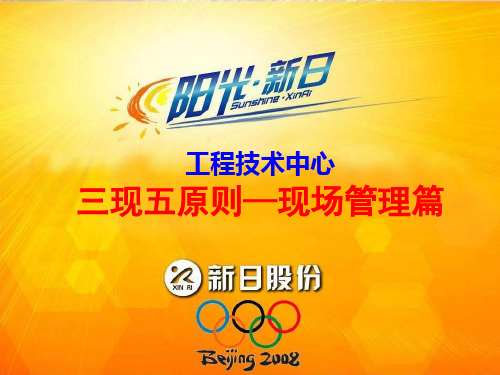
只有在 针对 才能通过观察、分析把握到 。在 我们即将讲到的“五原则”中,三现是其根本基础,离开三现,一切都 会沦为空谈。
现场
现物
现实
质 量 ● 创 新 ●● 创 新 ● 服 务
学习目的
1、了解并运用五原则解析 手法,真正改善重要品质问 题 2、把问题追溯到源头,从根本上解决问题 3、治理流程 4、制定、改善标准 5、重视“再现”,避免主观臆断或片面错断
质 量 ● 创 新 ● 服 务
WHERE 何地 – 记入问题发生的场所。 WHY 为什么 – 具体的内容 HOW 怎么样 – 问题是怎样发生的 HOW MANY 什么程度 – 问题发生量, 程度。
质 量 ● 创 新 ● 服 务
4M分析
5W分析法
查明原因
特性要因图 再现试验 NG再现 OK再现 不良再现 不良原因 (制造面)
解析对策必须手遵守三现主义
质 量 ● 创 新 ● 服 务
9、制造面、流出面未检讨
疑 问 点:1.为何会流出?为何会制造出?为何设备检不出? 2.流出面之解析对策经常被疏忽。 思 考:顾客所反应之问题必定制造面、流出面共同发生, 仅对策制造或流出面并未能彻底解决问题。
分析方法:1.制造面→分析4M之变化点→真因对策。 2.流出面→a.分析制程中之流程→作业环境、作 业检验工程标准。 b.分析检验之流出→出货检验标准、 限度样品、自动检测、防呆装置。 检验: 为何会检测不出来。
质 量 ● 创 新 ● 服 务
6、无回馈标准
疑问点:如何保证以后不会再发?或这样对策就不会再发吗? 欠缺了什么。 思 考:1.作业者不知道、不清楚、则不良问题仍然会再发生, 所以让作业者明白如何才能做良品是非常重要的。 2.
标准回馈 明确 作业者知道 如何去做 作业者正确 的去做