自动车床凸轮设计教程
常见问题解决和自动车床之凸轮设计

常见问题解决和自动车床之凸轮设计自动、半自动车床车工安全操作规程1、必须遵守普通车工安全操作规程。
2、气动卡盘所需的空气压力,不能低于规定值。
3、装工件时,必须放正,气门夹紧后再开车。
4、卸工件时,等卡盘停稳后,再取下工件。
5、机床各走刀限位装置的螺钉必须拧紧,并经常检查防止松动。
夹具和刀具须安装牢靠。
6、加工时,不得用手去触动自动换位装置或用手去摸机床附件和工件。
7、装卡盘时要检查卡爪,卡盘有无缺陷。
不符合安全要求严禁使用。
8、自动车床禁止使用锉刀、刮刀、砂布打光工件。
9、加工时,必须将防护挡板挡好。
发生故障、调整限位挡块、换刀、上料、卸工件、清理铁屑都应停车。
10、机床运转时不得无人照看,多机管理时(自动车床),应逐台机床巡回查看。
自动车床学习一、攻牙不稳定的七大原因我们在自动车床在加工时经常会遇到因为攻牙而出现的一些问题,就平时所遇到的攻牙不稳定七大原因来谈一下解决方法:1、挡攻牙梢磨损或弹簧松弛无力。
应检查挡攻牙梢有没磨损导致受力不均,再就是检查弹簧是不是调太松或换新的弹簧。
2、攻牙皮带调整不够紧或皮带损坏导致打滑。
攻牙三角皮带太松可调整机器后面的调节螺丝调整到合适状态或换新皮带。
3、攻牙小皮带太松可将固定攻牙机的四个小螺丝松掉再将攻牙机往下压,然后上紧四个螺丝。
4、离合器之刹车电豉不良,可换刹车片或更换攻牙机。
5、微动开关坏掉,更换新的微动开关。
(怎么更换微动开关待续)6、凸轮停止开关位置不对。
如果启动太慢也会导致攻牙的不稳定。
7、材料变形或夹头内残渣过多。
应该多检查材料及多清理夹头。
二、外圆粗糙度不良解决办法在我们生产中经常会碰到外圆粗糙、尺寸不稳定的情况,一般是什么原因造成的呢?这就要从机器和操作方面来说了,先说下机器方面的问题吧!1、夹头调整过松或开闭爪太松或破损,夹头过松时夹头夹不紧材料,会导致材料后退有刀痕;另开闭爪太松或破损时也会导致夹头夹不紧或开闭爪单边受力,应换掉开闭爪或多检查夹头松紧。
凸轮设计步骤
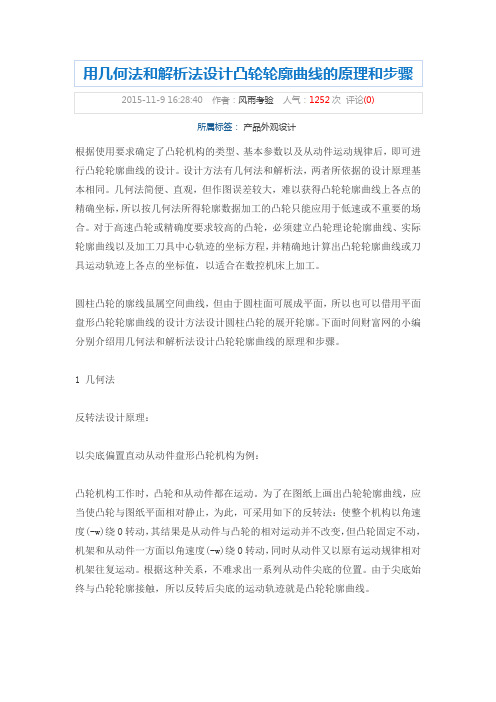
所属标签:产品外观设计根据使用要求确定了凸轮机构的类型、基本参数以及从动件运动规律后,即可进行凸轮轮廓曲线的设计。
设计方法有几何法和解析法,两者所依据的设计原理基本相同。
几何法简便、直观,但作图误差较大,难以获得凸轮轮廓曲线上各点的精确坐标,所以按几何法所得轮廓数据加工的凸轮只能应用于低速或不重要的场合。
对于高速凸轮或精确度要求较高的凸轮,必须建立凸轮理论轮廓曲线、实际轮廓曲线以及加工刀具中心轨迹的坐标方程,并精确地计算出凸轮轮廓曲线或刀具运动轨迹上各点的坐标值,以适合在数控机床上加工。
圆柱凸轮的廓线虽属空间曲线,但由于圆柱面可展成平面,所以也可以借用平面盘形凸轮轮廓曲线的设计方法设计圆柱凸轮的展开轮廓。
下面时间财富网的小编分别介绍用几何法和解析法设计凸轮轮廓曲线的原理和步骤。
1 几何法反转法设计原理:以尖底偏置直动从动件盘形凸轮机构为例:凸轮机构工作时,凸轮和从动件都在运动。
为了在图纸上画出凸轮轮廓曲线,应当使凸轮与图纸平面相对静止,为此,可采用如下的反转法:使整个机构以角速度(-w)绕O转动,其结果是从动件与凸轮的相对运动并不改变,但凸轮固定不动,机架和从动件一方面以角速度(-w)绕O转动,同时从动件又以原有运动规律相对机架往复运动。
根据这种关系,不难求出一系列从动件尖底的位置。
由于尖底始终与凸轮轮廓接触,所以反转后尖底的运动轨迹就是凸轮轮廓曲线。
1). 直动从动件盘形凸轮机构尖底偏置直动从动件盘形凸轮机构:已知从动件位移线图,凸轮以等角速w顺时针回转,其基圆半径为r0,从动件导路偏距为e,要求绘出此凸轮的轮廓曲线。
运用反转法绘制尖底直动从动件盘形凸轮机构凸轮轮廓曲线的方法和步骤如下:1) 以r0为半径作基圆,以e为半径作偏距圆,点K为从动件导路线与偏距圆的切点,导路线与基圆的交点B0(C0)便是从动件尖底的初始位置。
2) 将位移线图s-f的推程运动角和回程运动角分别作若干等分(图中各为四等分)。
自动车床凸轮设计详解
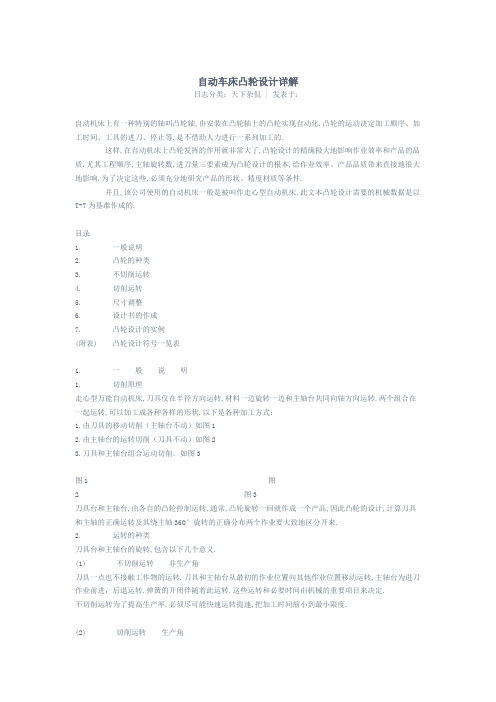
自动车床凸轮设计详解日志分类:天下杂侃 | 发表于:自动机床上有一种特别的轴叫凸轮轴,由安装在凸轮轴上的凸轮实现自动化.凸轮的运动决定加工顺序、加工时间、工具的进刀、停止等,是不借助人力进行一系列加工的.这样,在自动机床上凸轮发挥的作用就非常大了,凸轮设计的精确极大地影响作业效率和产品的品质.尤其工程顺序,主轴旋转数,进刀量三要素成为凸轮设计的根本,给作业效率、产品品质带来直接地很大地影响.为了决定这些,必须充分地研究产品的形状、精度材质等条件.并且,该公司使用的自动机床一般是被叫作走心型自动机床.此文本凸轮设计需要的机械数据是以T-7为基准作成的.目录1. 一般说明2. 凸轮的种类3. 不切削运转4. 切削运转5. 尺寸调整6. 设计书的作成7. 凸轮设计的实例(附表) 凸轮设计符号一览表1. 一般说明1. 切削原理走心型万能自动机床,刀具仅在半径方向运转,材料一边旋转一边和主轴台共同向轴方向运转.两个组合在一起运转,可以加工成各种各样的形状.以下是各种加工方式:1.由刀具的移动切削(主轴台不动)如图12.由主轴台的运转切削(刀具不动)如图23.刀具和主轴台组合运动切削。
如图3图1 图2 图3刀具台和主轴台,由各自的凸轮控制运转,通常,凸轮旋转一回就作成一个产品,因此凸轮的设计,计算刀具和主轴的正确运转及其绕主轴360°旋转的正确分布两个作业要大致地区分开来.2. 运转的种类刀具台和主轴台的旋转,包含以下几个意义.(1) 不切削运转非生产角刀具一点也不接触工作物的运转.刀具和主轴台从最初的作业位置向其他作业位置移动运转,主轴台为进刀作业前进,后退运转.弹簧的开闭伴随着此运转.这些运转和必要时间由机械的重要项目来决定.不切削运转为了提高生产率,必须尽可能快速运转提速,把加工时间缩小到最小限度.(2) 切削运转生产角是由一个或两个以上的刀具进行加工的运转.这跟工作物的材质,精加工精度,切削面粗糙度,使用刀具的材质等有直接联系.3. 主轴台的运转HS凸轮主轴台的前进是从板凸轮主轴推动进行,后退由一根弹簧进行.对于主轴台的运转,凸轮的设计可以从1∶1到1∶3的任意值来设定.为了减少不切削运转的时间,选择1∶1更好,但是短的产品和要求特别高精度的部品则选定1∶2或者1∶3.高级精密的设计根据产品选1∶2的多.该公司通常使用1∶2.4. 刀具台的运转(1) 刀番号标准刀具台有5个如图4称为1号刀具台,..5号刀具台.(2) 天平刀架1号刀具台和2号刀具台安装在摆动杆上.此刀具的运转是凸轮运转高度的1/3,构造方面也比其他刀具台好,所以主要用于精度较高的重要部分的精加工切削.并且凸轮的上升有使2号刀具台前进切入,同时使1号刀具台后退的作用.凸轮的下降有与其相反的效果.因此除了主轴台以及1号刀具台的其他所有的刀具台随凸轮上升而前进,(随凸轮)下降而后退.但是,只有1号刀具台与此相反,1号刀具台前进凸轮下降,1号刀具台后退凸轮上升.这是在凸轮设计中必须要注意的事项.(3) VT刀架刀具台3,4,5号刀具台能够由各自的凸轮单独前进、后退运转.这些VT刀架刀具台主要用于粗加工,倒角,突切等作业,必要的话也可以用于精加工切削.3号刀具台的杆比为1∶1(刀具和凸轮的运转相同),4,5号刀具台则变成1∶2(刀具的运转是凸轮运转的1/2),根据情况调整杆比稍微变更也是可以的.附件的杆比,除了特别的部品外一般为1∶1.主轴台HS 1:1~1:3天平刀架NO。
自动车床凸轮CAD设计
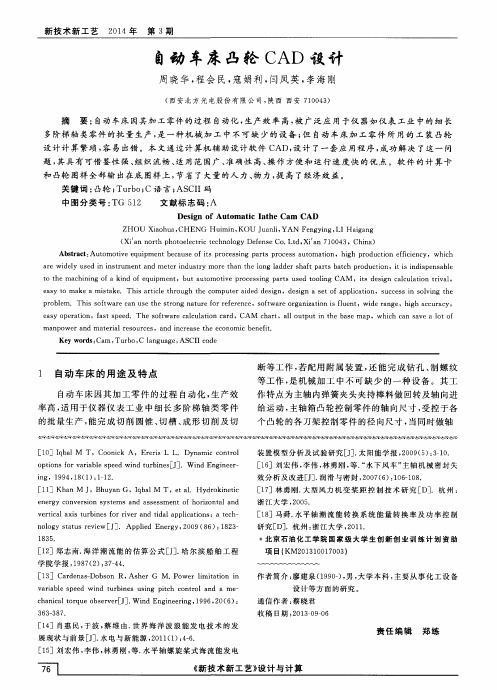
自动 车 床 凸 轮 C AD 设 计
周 晓华 , 程会 民, 寇娟利 , 闫凤 英 , 李海 刚
( 西 安北 方 光 电股 份 有 限公 司 , 陕西 西安 7 1 0 0 4 3 )
摘 要 : 自动车床 因其加 工 零件 的过程 自动 化 , 生产效 率 高 , 被 广 泛应 用于仪 器如 仪 表 工业 中的 细长 多阶梯 轴 类零件 的批 量 生产 , 是 一种 机械 加 工 中不 可缺 少的设 备 ; 但 自动 车 床加 工零 件 所 用 的 工装 凸轮 设 计计 算繁 琐 , 容 易 出错 。本文 通过计 算机 辅助 设计软 件 C AD, 设 计 了一套 应 用程 序 , 成功 解决 了这 一 问 题, 其 具有 可借鉴 性 强 、 组 织流 畅 、 适 用范 围广 、 准确性 高、 操作 方便 和 运行 速 度 快 的优 点 。软 件 的计 算 卡 和 凸轮 图样 全部 输 出在底 图样上 , 节 省 了大量 的人 力、 物力, 提 高 了经济效 益 。
凸轮设计方法

平面凸轮机构基本尺寸的确定
凸轮基圆半径的确定 一、基圆半径对压力角的影响
ds/d e PD OP e tan s0 s BD r02 e 2 s
增大基圆半径,可使凸轮机构的压力角减小; 增大基圆半径会使凸轮机构的整体尺寸增大 在压力角不超过许用值的原则下,应尽可能采用 较小的基圆半径。
从动件尖底的运 动轨迹就是凸轮 的廓线
偏置直动尖顶从动件
s
e
120° 90 ° 90 ° 60 °
偏置直动尖顶从动件
s
e 120 ° 90 ° 90 ° 60 °
偏置直动尖顶从动件
s
1
2 3
4 5
6
7
8 9
e
1 2 3 9 8
4
6
7
5
偏置直动尖顶从动件
s
120 ° 90 ° 90 ° ° 60
• 偏置直动尖顶从动件盘形凸轮 • 偏置直动滚子从动件盘形凸轮 • 对心直动平底从动件
摆动从动件盘形凸轮
凸轮廓线设计的基本原理——反转法 为了便于绘出凸轮轮廓 曲线, 应使工作中转动着的 凸轮与不动的图纸间保持相 对静止。 如果给整个凸轮机构加 上一个与凸轮转动角度ω数 值相等、 方向相反的“-ω” 角速度, 则凸轮处于相对静 止状态。
从动件的基本运动规律
从动件位移s对凸轮转角的函数
s
关系s( )称为从动件运动规律
ds s d
d 2s s d 2
s
s
s( ) — 类速度 s( ) — 类加速度
0
ds ds d v s dt d dt d 2 s d 2 s d 2 2 a 2 ( ) s 2 dt d dt
自动车床凸轮设计详细教程..

自动车床主要靠凸轮来控制加工过程,能否设计出一套好的凸轮,是体现自动车床师傅的技术高低的一个标准。
凸轮设计计算的资料不多,在此,我将一些基本的凸轮计算方法送给大家。
凸轮是由一组或多组螺旋线组成的,这是一种端面螺旋线,又称阿基米德螺线。
其形成的主要原理是:由A点作等速旋转运动,同时又使A点沿半径作等速移动,形成了一条复合运动轨迹的端面螺线。
这就是等速凸轮的曲线。
凸轮的计算有几个专用名称:1、上升曲线——凸轮上升的起点到最高点的弧线称为上升曲线2、下降曲线——凸轮下降的最高点到最低点的弧线称为下降曲线3、升角——从凸轮的上升起点到最高点的角度,即上升曲线的角度。
我们定个代号为φ。
4、降角——从凸轮的最高点到最低点的角度,即下降曲线的角度。
代号为φ1。
5、升距——凸轮上升曲线的最大半径与最小半径之差。
我们给定代号为h,单位是毫米。
6、降距——凸轮下降曲线的最大半径与最小半径之差。
代号为h1。
7、导程——即凸轮的曲线导程,就是假定凸轮曲线的升角(或降角)为360°时凸轮的升距(或降距)。
代号为L,单位是毫米。
8、常数——是凸轮计算的一个常数,它是通过计算得来的。
代号为K。
凸轮的升角与降角是给定的数值,根据加工零件尺寸计算得来的。
凸轮的常数等于凸轮的升距除以凸轮的升角,即K=h/φ。
由此得h=Kφ。
凸轮的导程等于360°乘以常数,即L=360°K。
由此得L=360°h/φ。
举个例子:一个凸轮曲线的升距为10毫米,升角为180°,求凸轮的曲线导程。
(见下图) 解:L=360°h/φ=360°×10÷180°=20毫米升角(或降角)是360°的凸轮,其升距(或降距)即等于导程。
这只是一般的凸轮基本计算方法,比较简单,而自动车床上的凸轮,有些比较简单,有些则比较复杂。
在实际运用中,许多人只是靠经验来设计,用手工制作,不需要计算,而要用机床加工凸轮,特别是用数控机床加工凸轮,却是需要先计算出凸轮的导程,才能进行电脑程序设计。
设计凸轮机构的步骤

设计凸轮机构的步骤1.引言1.1 概述概述部分的内容如下:引言部分是文章的开端,旨在向读者介绍关于设计凸轮机构步骤的基本概念和重要性。
设计凸轮机构是指在机械传动中用于转化运动的一种重要装置,广泛应用于各种机械设备中,如发动机、制造机械、自动化机械等。
凸轮机构的设计直接关系到机械传动的性能和效率,因此在机械设计中具有重要的地位。
本文将介绍设计凸轮机构的具体步骤,帮助读者了解如何更好地应用凸轮机构设计各类机械装置。
首先,我们将介绍凸轮机构的基本原理和功能,为后续内容的理解奠定基础。
然后,我们将详细讲解设计凸轮机构的步骤,包括凸轮曲线的选择、凸轮的参数计算、凸轮机构的布局设计等内容。
在每个步骤中,我们都将提供详细的方法和注意事项,帮助读者更好地理解和掌握凸轮机构的设计过程。
通过本文的学习,读者将能够系统地掌握设计凸轮机构的方法和技巧,提高机械设备的传动效率和性能。
同时,文章还将展望未来凸轮机构设计领域的发展趋势,激发读者的思考和创新意识。
在下文中,我们将详细介绍凸轮机构的设计步骤,希望读者能够通过本文的学习,对凸轮机构的设计有更深入和全面的了解。
1.2 文章结构文章结构部分的内容可以包括以下内容:在设计凸轮机构之前,了解凸轮机构的基本概念及其作用是非常重要的。
凸轮机构可以将圆周运动转化为直线或间歇运动,广泛应用于各个领域的机械设计中。
本文将介绍设计凸轮机构的步骤,以帮助读者了解如何有效地进行设计过程。
文章主要分为三个部分:引言、正文和结论。
引言部分将首先概述凸轮机构的作用和重要性。
凸轮机构作为一种重要的机械传动装置,在现代机械设计中起着不可替代的作用。
随后,将介绍本文的结构和内容安排,以帮助读者快速了解文章的组织结构和各个部分的内容。
正文部分将详细介绍设计凸轮机构的步骤。
首先,步骤一将介绍凸轮机构的设计前准备工作,包括确定凸轮的基本参数、选择凸轮的类型和形状等。
然后,步骤二将详细讲解凸轮机构的设计过程,包括凸轮的轮廓设计、凸轮与从动件的配合设计等。
机械原理课程设计凸轮机构设计说明书

全面探究凸轮机构设计原理及方法凸轮机构是一种常用的机械传动装置,通过凸轮和摆杆的配合组成,具有可逆性、可编程性和高精度的特点。
本文将从设计原理、设计方法和优化策略三个方面探究凸轮机构设计的要点。
一、设计原理
凸轮机构的设计原理是在摆杆与凸轮配合时,摆杆可以沿凸轮轮廓实现规定的运动规律,如直线运动、往返运动和旋转运动等。
凸轮可以根据运动轨迹、运动频率和运动速度等要求,通过凸轮轮廓的设计来完成。
凸轮轮廓的设计包括了初步设计、动力学分析、运动规划等步骤。
二、设计方法
凸轮机构的设计方法包括手工绘图及设计软件辅助。
手工绘图是传统的凸轮轮廓设计方法,适用于简单的凸轮机构,如往复式转动机构、转动转动机构等;而对于复杂的凸轮机构,可以利用计算机辅助设计软件,如ProEngineer、CATIA、AutoCAD等,进行三维建模、运动模拟和优化设计。
此外,对于凸轮机构的设计还需要考虑到强度计算、可靠性分析等相关问题。
三、优化策略
凸轮机构的设计优化策略主要包括凸轮轮廓的形状优化、摆杆的长度优化和机构传动效率的优化等。
凸轮轮廓的形状优化通常是通过
Cycloid、Involute、Bezier等曲线的拟合来实现;摆杆的长度优化可以通过数学模型来建立,利用遗传算法、粒子群算法等优化算法进行
求解;传动效率的优化可以通过轮廓优化、材料优化、润滑优化等途
径来进行。
凸轮机构的设计是机械工业中非常重要的一环,它涉及到运动学、动力学、力学等多个学科的知识,需要学习者在多方面进行深入研究
和实践。
通过对凸轮机构的深入探究,我们可以更好地理解机械原理
的精髓,提高机械设计的水平和能力。
凸轮程序的设计

凸轮程序的设计凸轮程序的设计1. 引言凸轮是一种机械元件,可以将旋转运动转化为直线或曲线运动。
在工程设计和机械加工中,凸轮被广泛用于控制机械装置的动作,如运动轨迹、速度和加速度等。
本文将介绍凸轮程序的设计方法和步骤。
2. 凸轮程序的基本要素凸轮程序的设计需要考虑以下几个基本要素:- 凸轮形状:凸轮的形状决定了运动轨迹和运动方式。
常见的凸轮形状有圆形、椭圆形、心形、凹形等。
- 凸轮半径:凸轮的半径决定了运动的范围和速度。
较大的凸轮半径可以实现更大范围的运动,而较小的凸轮半径则可以实现更快的速度。
- 凸轮周期:凸轮周期是指凸轮完成一次完整运动所需的时间。
凸轮周期可以通过调整凸轮的旋转速度来实现。
- 凸轮角度:凸轮角度是指凸轮当前的旋转角度。
凸轮角度可以用来控制机械装置的状态和动作。
3. 凸轮程序的设计步骤设计凸轮程序的一般步骤如下:3.1 确定凸轮的形状和尺寸根据实际需求和机械装置的要求,确定凸轮的形状和尺寸。
可以使用计算机辅助设计(CAD)工具来绘制凸轮的轮廓,并进行必要的修正和优化。
3.2 确定凸轮的运动轨迹根据机械装置的要求和设计需求,确定凸轮的运动轨迹。
可以根据凸轮的形状和运动方式,计算出凸轮在不同角度下的坐标值。
3.3 编写凸轮控制程序根据凸轮的形状、尺寸和运动轨迹,编写凸轮控制程序。
可以使用编程语言(如C++、Python等)来实现凸轮控制程序。
程序可以包括凸轮的旋转控制、角度计算和坐标计算等功能。
3.4 调试和优化凸轮程序在实际使用中,可能需要对凸轮程序进行调试和优化。
可以通过实际测试和仿真验证凸轮程序的准确性和性能,并根据实际情况进行必要的调整和优化。
4. 示例下面是一个简单的凸轮程序示例,使用Python编写:python凸轮程序示例import math凸轮半径R = 10凸轮周期T = 2计算凸轮角度和坐标def calculate_cam_position(angle):x = R math.cos(math.radians(angle))y = R math.sin(math.radians(angle))return x, y主程序def mn():for angle in range(0, 360, 10):x, y = calculate_cam_position(angle)pri。
自动车床凸轮CAD设计
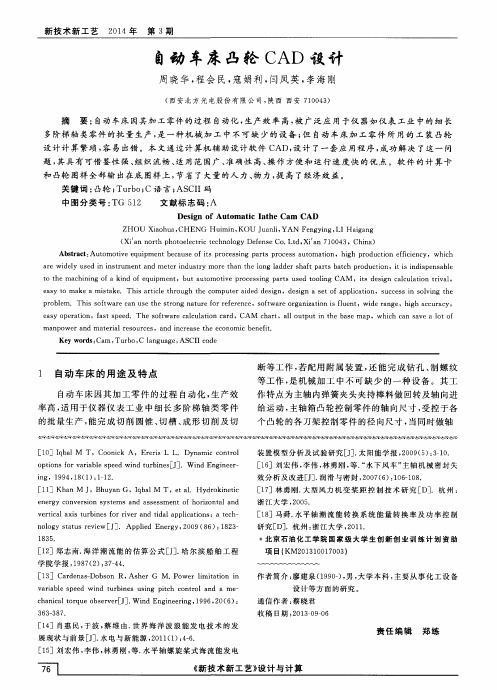
, 1 1 8 ]马 舜 . 水 平 轴 潮 流 能 转 换 系 统 能 量 转 换 率 及 功 率 控 制
n o l o g y s t a t u s r e v i e wI , J ] .Ap p l i e d E n e r g y , 2 0 0 9 ( 8 6 ) : 1 8 2 3 —
1 8 35 .
研究[ D ] .杭 州 : 浙江大学 , 2 0 1 1 .
*北 京 石 油 化 工 学 院 国 家 级 大 学 生 创 新 创 业 训 练 计 划 资 助 项 目( K M2 0 1 3 1 0 0 1 7 0 0 3 )
, 1 1 2 ]郑 志 南 . 海洋潮 流能 的估 算公式 [ J ] . 哈 尔 滨 船 舶 工 程
符, 在 显示 器 上显 示 信 息 , 读写磁盘, 主 机 向打 印机
、 - 石 写 \ I 石 、
, 1 1 0 ]I q b a l M T,C o o n i c k A,E r e r i s L L .D y n a mi c c o n t r o l o p t i o n s f o r v a r i a b l e s p e e d w i n d t u r b i n e s E J ] .Wi n d E n g i n e e r —
凸轮设计步骤
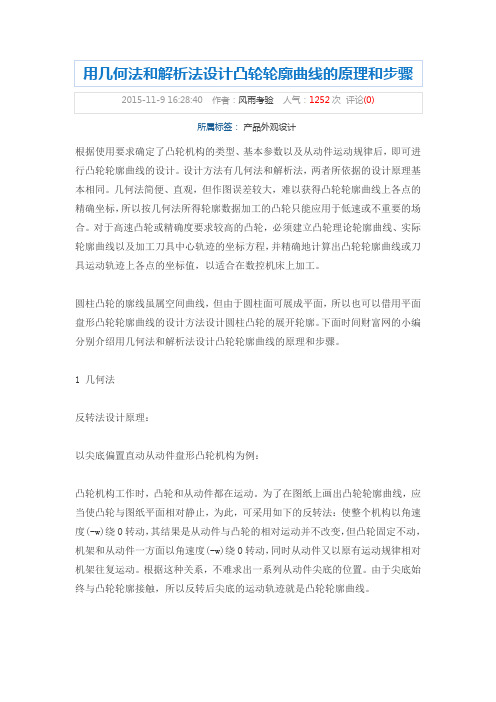
所属标签:产品外观设计根据使用要求确定了凸轮机构的类型、基本参数以及从动件运动规律后,即可进行凸轮轮廓曲线的设计。
设计方法有几何法和解析法,两者所依据的设计原理基本相同。
几何法简便、直观,但作图误差较大,难以获得凸轮轮廓曲线上各点的精确坐标,所以按几何法所得轮廓数据加工的凸轮只能应用于低速或不重要的场合。
对于高速凸轮或精确度要求较高的凸轮,必须建立凸轮理论轮廓曲线、实际轮廓曲线以及加工刀具中心轨迹的坐标方程,并精确地计算出凸轮轮廓曲线或刀具运动轨迹上各点的坐标值,以适合在数控机床上加工。
圆柱凸轮的廓线虽属空间曲线,但由于圆柱面可展成平面,所以也可以借用平面盘形凸轮轮廓曲线的设计方法设计圆柱凸轮的展开轮廓。
下面时间财富网的小编分别介绍用几何法和解析法设计凸轮轮廓曲线的原理和步骤。
1 几何法反转法设计原理:以尖底偏置直动从动件盘形凸轮机构为例:凸轮机构工作时,凸轮和从动件都在运动。
为了在图纸上画出凸轮轮廓曲线,应当使凸轮与图纸平面相对静止,为此,可采用如下的反转法:使整个机构以角速度(-w)绕O转动,其结果是从动件与凸轮的相对运动并不改变,但凸轮固定不动,机架和从动件一方面以角速度(-w)绕O转动,同时从动件又以原有运动规律相对机架往复运动。
根据这种关系,不难求出一系列从动件尖底的位置。
由于尖底始终与凸轮轮廓接触,所以反转后尖底的运动轨迹就是凸轮轮廓曲线。
1). 直动从动件盘形凸轮机构尖底偏置直动从动件盘形凸轮机构:已知从动件位移线图,凸轮以等角速w顺时针回转,其基圆半径为r0,从动件导路偏距为e,要求绘出此凸轮的轮廓曲线。
运用反转法绘制尖底直动从动件盘形凸轮机构凸轮轮廓曲线的方法和步骤如下:1) 以r0为半径作基圆,以e为半径作偏距圆,点K为从动件导路线与偏距圆的切点,导路线与基圆的交点B0(C0)便是从动件尖底的初始位置。
2) 将位移线图s-f的推程运动角和回程运动角分别作若干等分(图中各为四等分)。
凸轮轮廓设计PPT课件

9’
设计:潘存云
③确定反转后,从动件尖顶在各等份点的位置;
④将各尖顶点连接成一条光滑曲线。 第4页/共31页
(右)偏置直动尖顶从动件盘形凸轮绘制过程
第5页/共31页
(右)偏置直动滚子从动件盘形凸轮绘制过程
第6页/共31页
4)摆动尖顶推杆盘形凸轮机构
已知凸轮的基圆半径r0,角速度ω,摆杆长度l以及摆
由图可知: s0=(r02-e2)1/2
x= (s0+s)sinδ+ ecosδ y= (s0+s)cosδ- esinδ
(1)
实际轮廓线-为理论轮廓的等距线。
曲线任意点切线与法线斜率互为负倒数:
tgθ= -dx/dy =(dx/dδ)/(- dy/dδ) =sinθ/cosθ 第11页/共31页
对(1)式求导,得:
提问:在设计一对心凸轮机构设计时,当出现α≥[α]
的情况,在不改变运动规律的前提下,可采取哪些措 施来进行改进?
tgα=(ds/dδ-e)/[(r02-e2)1/2+s] 1)加大基圆半径r0 , r0↑ →α↓ 2)将对心改为偏置, e↑ →α↓
3)采用平底从动件, α=0
确定上述极值r0min不方便,工程上常根据诺模图
若不满足此条件时:
增大r0 减小rr
第25页/共31页
4.平底尺寸l 的确定 作图法确定: l=2lmax+(5~7)mm
ω
1’ 2’
3’
B’7
B’6
B’5
φ4
A4
φ6
φ5
A5
5)直动推杆圆柱凸轮机构
思路:将圆柱外表面展开,得一长度为2πR的平面移 动凸轮机构,其移动速度为V=ωR,以-V反向移动 平面凸轮,相对运动不变,滚子反向移动后其中心点 的轨迹即为理论轮廓,其内外包络线为实际轮廓。
自动车床凸轮设计教程

1.自动车床主要靠凸轮来控制加工过程,能否设计出一套好的凸轮,是体现自动车床师傅的技术高低的一个标准。
凸轮设计计算的资料不多,在此,我将一些基本的凸轮计算方法送给大家。
凸轮是由一组或多组螺旋线组成的,这是一种端面螺旋线,又称阿基米德螺线。
其形成的主要原理是:由A点作等速旋转运动,同时又使A点沿半径作等速移动,形成了一条复合运动轨迹的端面螺线。
这就是等速凸轮的曲线。
凸轮的计算有几个专用名称:1、上升曲线——凸轮上升的起点到最高点的弧线称为上升曲线2、下降曲线——凸轮下降的最高点到最低点的弧线称为下降曲线3、升角——从凸轮的上升起点到最高点的角度,即上升曲线的角度。
我们定个代号为φ。
4、降角——从凸轮的最高点到最低点的角度,即下降曲线的角度。
代号为φ1。
5、升距——凸轮上升曲线的最大半径与最小半径之差。
我们给定代号为h,单位是毫米。
6、降距——凸轮下降曲线的最大半径与最小半径之差。
代号为h1。
7、导程——即凸轮的曲线导程,就是假定凸轮曲线的升角(或降角)为360°时凸轮的升距(或降距)。
代号为L,单位是毫米。
8、常数——是凸轮计算的一个常数,它是通过计算得来的。
代号为K。
凸轮的升角与降角是给定的数值,根据加工零件尺寸计算得来的。
凸轮的常数等于凸轮的升距除以凸轮的升角,即K=h/φ。
由此得h=Kφ。
凸轮的导程等于360°乘以常数,即L=360°K。
由此得L=360°h/φ。
举个例子:一个凸轮曲线的升距为10毫米,升角为180°,求凸轮的曲线导程。
(见下图) 解:L=360°h/φ=360°×10÷180°=20毫米升角(或降角)是360°的凸轮,其升距(或降距)即等于导程。
这只是一般的凸轮基本计算方法,比较简单,而自动车床上的凸轮,有些比较简单,有些则比较复杂。
在实际运用中,许多人只是靠经验来设计,用手工制作,不需要计算,而要用机床加工凸轮,特别是用数控机床加工凸轮,却是需要先计算出凸轮的导程,才能进行电脑程序设计。
凸轮机构及其设计PPT课件
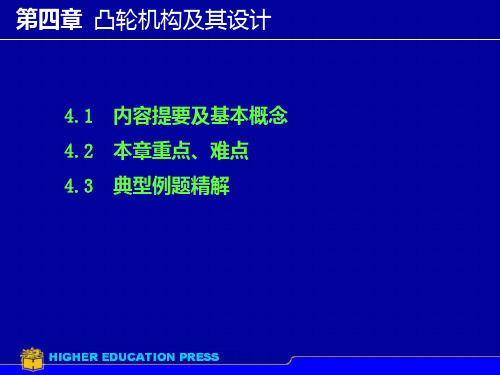
产生非常大的惯性力。 柔性冲击——由于加速度发生有限值的突变,导致从动件产生有限值的惯性
力突变而产生有限的冲击。
压力角、许用压力角 ——从动件在高副接触点所受的法向力与从动件该 点的速度方向所夹锐角α 。压力角过大时,会使机 构的传力性能恶化。工程上规定其临界值为许用压 力角[α]。不同的机器的许用压力角要求不同,凸轮 机构设计时要求 α ≤ [α]。
2) 摆动从动件的压力角
如下图所示, ω1和ω2同向,P点是瞬心点,过 P作垂直于AB延长线得D。由ΔBDP得
tanα =BD/PD
(2)
由ΔADP得
BD =AD-AB= APcos(ψ0 +ψ)-l
P
PD= APsin(ψ0 +ψ)
n
由瞬心性质有 AP ω2 =OP ω1 = (AP-a) ω1
解得
s=h[1-φ/Φ’ +sin(2πφ/Φ’)/2π] v=hω[cos(2πφ/Φ’)-1]/Φ’ a=-2πhω2 sin(2πφ/Φ’)/Φ’2
特点:无冲击,适于高速凸轮。
s
Φ v a
.
h φ
Φ’
φ
φ
21
改进型运动规律
单一基本运动规律不能满足工程要求时,
分别取一、二、五次项,就得到相应幂次的运动规律。
基本边界条件
凸轮转过推程运动角Φ ——从动件上升h 凸轮转过回程运动角Φ’——从动件下降h
将不同的边界条件代入以上方程组,可.求得待定系数Cபைடு நூலகம் 。
16
1) 一次多项式(等速运动)运动规律 边界条件
在推程起始点: φ =0, s=0 在推程终止点: φ =δ0 ,s=h 代入得:C0=0, C1=h/Φ
凸轮设计步骤
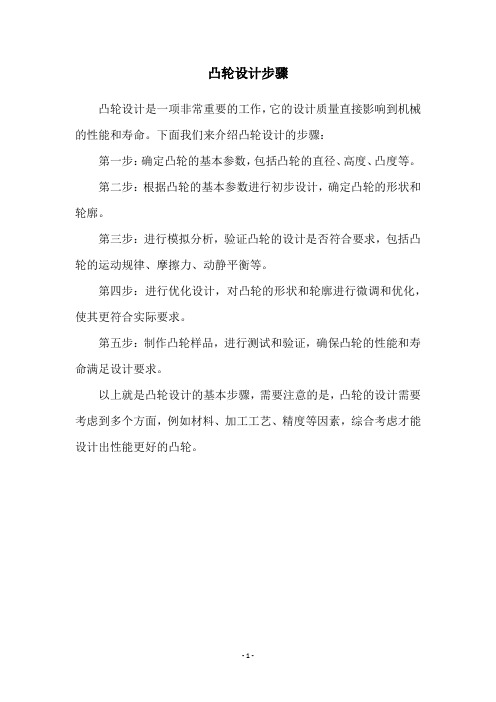
凸轮设计步骤
凸轮设计是一项非常重要的工作,它的设计质量直接影响到机械的性能和寿命。
下面我们来介绍凸轮设计的步骤:
第一步:确定凸轮的基本参数,包括凸轮的直径、高度、凸度等。
第二步:根据凸轮的基本参数进行初步设计,确定凸轮的形状和轮廓。
第三步:进行模拟分析,验证凸轮的设计是否符合要求,包括凸轮的运动规律、摩擦力、动静平衡等。
第四步:进行优化设计,对凸轮的形状和轮廓进行微调和优化,使其更符合实际要求。
第五步:制作凸轮样品,进行测试和验证,确保凸轮的性能和寿命满足设计要求。
以上就是凸轮设计的基本步骤,需要注意的是,凸轮的设计需要考虑到多个方面,例如材料、加工工艺、精度等因素,综合考虑才能设计出性能更好的凸轮。
- 1 -。
图解法设计凸轮轮廓曲线法设计凸轮轮廓曲线
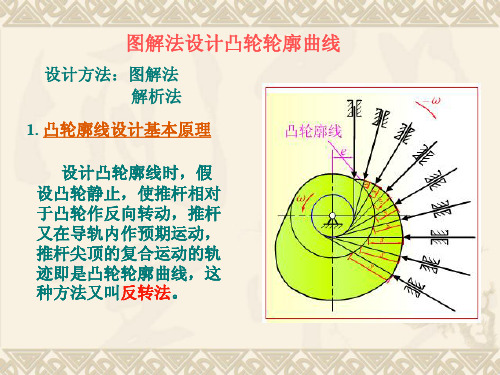
设计方法:图解法 解析法 1. 凸轮廓线设计基本原理 设计凸轮廓线时,假 设凸轮静止,使推杆相对 于凸轮作反向转动,推杆 又在导轨内作预期运动, 推杆尖顶的复合运动的轨 迹即是凸轮轮廓曲线,这 种方法又叫反转法 种方法又叫 反转法。 。
2. 图解法设计凸轮轮廓曲线
1)偏置直动尖顶推杆盘形凸轮机构
5)摆动尖顶推杆盘形凸轮机构 已知:基圆半径r ,凸轮逆时针 0 转动w,推杆的运动规律 j=j(d),LOA、LAB
A B
确定基圆 A点所在圆、AB初始位置 确定基圆、 将A点所在圆瓜分
O
自基圆向外量取等分点角位移 确定推程、远休、回程、近休廓线
3)对心直动滚子推杆盘形凸轮机构
以滚子中心为尖顶,按尖顶推杆设计凸轮廓线 按尖顶推杆设计凸轮廓线, 得到理论廓线。 以理论廓线上的各点为圆心,滚子半径为半径 滚子半径为径, 画一系列滚子圆,这些滚子圆的包络线即为 这些滚子圆的包络线即为实 际廓线。 注意:基圆半径是理论廓线上的最小向径。
4)对心直动平底推杆盘形凸轮机构 以平底中心A为尖顶,按尖顶推杆 设计凸轮廓线,得到理论廓线。 以理论廓线上的各点为平底中心, 画一系列平底,这些平底的包络线 即为实际廓线。
已知:基圆半径r ,凸轮逆时针转动w,推 0 杆的运动规律s=s(d),偏距为e,推杆在 凸轮回转中心右侧。
作偏距圆、基圆、推杆的初始位置 将偏距圆瓜分 将推程运动角等分,作偏距圆的切线 从基圆向外量推杆的位移,得推程廓线
2)对心直动尖顶推杆盘形凸轮机构
对心直动尖顶推杆盘形凸轮机构推杆在反转过 程中始终通过凸轮的回转中心。
- 1、下载文档前请自行甄别文档内容的完整性,平台不提供额外的编辑、内容补充、找答案等附加服务。
- 2、"仅部分预览"的文档,不可在线预览部分如存在完整性等问题,可反馈申请退款(可完整预览的文档不适用该条件!)。
- 3、如文档侵犯您的权益,请联系客服反馈,我们会尽快为您处理(人工客服工作时间:9:00-18:30)。
1.自动车床主要靠凸轮来控制加工过程,能否设计出一套好的凸轮,是体现自动车床师傅的技术高低的一个标准。
凸轮设计计算的资料不多,在此,我将一些基本的凸轮计算方法送给大家。
凸轮是由一组或多组螺旋线组成的,这是一种端面螺旋线,又称阿基米德螺线。
其形成的主要原理是:由A点作等速旋转运动,同时又使A点沿半径作等速移动,形成了一条复合运动轨迹的端面螺线。
这就是等速凸轮的曲线。
凸轮的计算有几个专用名称:1、上升曲线——凸轮上升的起点到最高点的弧线称为上升曲线2、下降曲线——凸轮下降的最高点到最低点的弧线称为下降曲线3、升角——从凸轮的上升起点到最高点的角度,即上升曲线的角度。
我们定个代号为φ。
4、降角——从凸轮的最高点到最低点的角度,即下降曲线的角度。
代号为φ1。
5、升距——凸轮上升曲线的最大半径与最小半径之差。
我们给定代号为h,单位是毫米。
6、降距——凸轮下降曲线的最大半径与最小半径之差。
代号为h1。
7、导程——即凸轮的曲线导程,就是假定凸轮曲线的升角(或降角)为360°时凸轮的升距(或降距)。
代号为L,单位是毫米。
8、常数——是凸轮计算的一个常数,它是通过计算得来的。
代号为K。
凸轮的升角与降角是给定的数值,根据加工零件尺寸计算得来的。
凸轮的常数等于凸轮的升距除以凸轮的升角,即K=h/φ。
由此得h=Kφ。
凸轮的导程等于360°乘以常数,即L=360°K。
由此得L=360°h/φ。
举个例子:..一个凸轮曲线的升距为10毫米,升角为180°,求凸轮的曲线导程。
(见下图) 解:L=360°h/φ=360°×10÷180°=20毫米升角(或降角)是360°的凸轮,其升距(或降距)即等于导程。
这只是一般的凸轮基本计算方法,比较简单,而自动车床上的凸轮,有些比较简单,有些则比较复杂。
在实际运用中,许多人只是靠经验来设计,用手工制作,不需要计算,而要用机床加工凸轮,特别是用数控机床加工凸轮,却是需要先计算出凸轮的导程,才能进行电脑程序设计。
要设计凸轮有几点在开始前就要了解的.在我们拿到产品图纸的时候,看好材料,根据材料大小和材质将这款产品的主轴转速先计算出来.计算主轴转速公式是[切削速度乘1000]除以材料直径.切削速度是根据材质得来的,在购买材料时供应商提供.单位是米/分钟.材料硬度越大,切削速度就越小,切的太快的话热量太大会导致材料变形, 所以切削速度已知的.切削速度乘1000就是把米/分钟换算成毫米/分钟,在除以材料直径就是主轴每分钟的转速了.材料直径是每转的长度,切削速度是刀尖每分钟可以移动的距离.主轴转速求出来了,就要将一个产品需要多少转可以做出来,这个转的圈数求出来.主轴转速除以每个产品需要的圈数就是生产效率.[单位.个/分钟]..每款不同的产品,我们看到图纸的时候就先要将它的加工工艺给确定下来.加工工艺其实就是加工方法,走芯机5把刀具怎么安排,怎么加工,哪把刀具先做,按顺序将它安排,这样就是确定加工工艺.确定加工工艺的时候有几点应该注意的地方.一. 2把相邻的刀具最好不安排在一前一后顺序加工,应该错开刀具安排,这样就容易避免刀具相撞.二. 确定一条基准线,一般以切断刀的靠近中心架夹头的那个面为基准.其余的4把刀具在靠近基准面时留有一点距离.后面会有例子.三. 尽量不要安排2把刀同时加工,以免互相干扰,出现不稳定情况.当然也有些例外的,比如2把倒角一起加工有时候是可以的.四. 合理的安排刀具,在刀具够用的时候倒角可以用成型刀最好.区分好行程和空行程的步骤.行程就是刀具在加工的时候;空行程则是刀具在未加工的时候.我们在这开始讲空行程的角度计算方法:1. 凸轮开关夹,夹头弹开的时候的角度是10度,夹紧角度是15度.2. 根据算得的生产效率来确定凸轮上升下降的空行程所要乘的比例系数.当生产效率小于或者等于3的时候,凸轮上升角度比例系数是1比1,也就是..凸轮每上升1毫米,角度为1度.凸轮下降角度比例系数是1比0.7,也就是凸轮每下降1毫米,角度为0.7度.当生产效率小于等于8大于3的时候,凸轮上升角度比例系数是1比1.5,也就是凸轮每上升1毫米,角度为1.5度.凸轮下降角度比例系数是1比1,也就是凸轮每下降1毫米,角度为1度.当生产效率小于等于14大于8的时候,凸轮上升角度比例系数是1比2,也就是凸轮每上升1毫米,角度为2度.凸轮下降角度比例系数是1比1.3,也就是凸轮每下降1毫米,角度为1.3度.当生产效率大于14的时候,凸轮上升角度比例系数是1比2.5,也就是凸轮每上升1毫米,角度为2.5度.凸轮下降角度比例系数是1比1.7,也就是凸轮每下降1毫米,角度为1.7度.生产效率实际指的就是凸轮轴每分钟转的圈数,而不是产品每分钟做的个数,因为产品简单的时候我们设计的时候甚至可以每圈做2,3个产品,可能更多...空行程说清楚了也就是这两个要点.凸轮空行程的凸轮上升下降角度可以根据第2点全计算出来.由于纵切自动车床一般都具有五个刀架和附件装置,因此它的加工工艺围比较广,许多复杂的轴类零件也可以用这种机床一次加工完成。
在纵切单轴自动车床上可以进行下列一些工作:车圆柱面、车倒角、车锥面、沉割加工、切断、车圆弧、打中心孔、钻孔、绞孔、镗孔、功外螺纹、冲方孔等等其他工作。
前面我们讲完了空行程的计算方法,这里讲行程的计算方法.凸轮设计里面除了行程剩下的全是空行程.在这也可以反过来用.行程里面刀具加工的方法很多:1. 左车外径2. 右车外径3. 成型刀倒角,圆弧,插槽等等4. 切断(1) 平面切断(2) 圆弧切断(3) 斜面切断(4) 切断面往里面凹进去,也可以是产品后面打中心孔5. 打中心孔(钩刀钩平底孔)6. 根据凸轮和刀具配合移动走倒角,或者走圆弧7. 沉割刀具清理外径根部圆角或者批锋8. 钻孔9. 功牙,套牙..10 冲方孔(孔是正多边型的)自动车床,以其无可替代的加工手段的优势,正在为越来越多的厂家所青睐。
而自动车床使用的凸轮的设计,则成为使用此类机床的厂家所必须要掌握的一门技术。
自动车床凸轮的设计,即编写凸轮调整卡,对于不了解其本来面貌的人来讲,神秘、深奥;当对它有了稍微粗浅了解的人,又会觉得不过如此而已,稍学即会。
其实,此项技术和其他任何门类的技术一样,“会易精难”。
依据机床说明书的提示来编写完成的凸轮设计调整卡,不一定是好的设计作品。
一个优秀的设计作品,包括以下容:一,合理的工步编排。
二,合理的设定走刀量。
三,能得出较高的生产率。
..此外,还应在制造凸轮、调整机床时易于操作。
也可以这样说,要想作出一件比较优秀的设计作品,前提是能够深刻体味各个设计步骤的实质性的意义。
只有这样才能做到,你的设计作品与机床说明书中提示的方法相比较,不只是形似,而是神似,甚至比其更优秀。
考核一个设计作品的优劣,最重要的标准是其最后得出的生产率的高低;生产率的高低,取决于工作角度总和的大小;而工作角度总和的大小,则取决于工步编排得是否合理。
由此看来,合理的编排工步,在整个设计过程中,具有着相当重要的作用。
要想做好工步编排,一是要有相当时间的工作经验的积累;二是要有丰富的想象力,这一点尤其重要。
一、生产率的计算方法与作用作为投资人,都希望在尽可能短的时间,得到尽可能高的效益;作为生产过程的组织者,都希望机床能生产数量和品种都尽可能多的产品,以缓解交货期代来的时间压力;作为操作工,都希望机床能够优质高产,以获得较高的收入。
所以说,希望优质高产是所有与机床有关联的人的共同愿望。
..那麽,现在就分析一下下面的这个公式,就可以知道机床的生产率究竟是怎样形成的了。
N 不难看出,这是一个多元一次分式方程式。
在这一公式里,A=————————函括了整个设计过程的全部计算容。
Σn工÷Σa工×360°式中:A=生产率单位=件/分N=主轴转数单位=转/分n工=某切削工步工作时的主轴转数α工=某切削工步工作时占用的角度∑:希腊字母。
表示在计算过程中某项数值的累计总和。
首先,介绍几个在设计中使用的专用名词:工步——生产过程中每一个动作称做一个工步。
切削时主轴转数——完成某一切削工步时主轴转过的圈数。
工作角度——完成某一切削工步时所占用的角度。
在“车”加工中,无论使用的是哪种类型车床,在切削前都要先确定:①主轴转数。
..②每次进刀多少毫米(进刀深度)。
③走刀时的速度(走刀量)。
这就是平常所说的“切削三要素”。
自动车加工时的主轴转数,是由被加工材料的种类和直径决定的。
例:切削直径10毫米A3棒料时(此钢种属低碳钢),根据说明书中切削速度表给出的数值,是60m/分。
即:60×1000/(10×3.1416)≈1910(转)据此,就可确定机床最接近此数值的主轴转数。
准确的选择主轴转数,是保持零件加工时工艺尺寸稳定的关键,这一点往往容易被忽略。
如果主轴转数过快,直接影响刀具的使用寿命;而主轴转数过慢,又会因切削速度不够而造成加工的零件工艺尺寸不稳定、光洁度不高等等缺陷。
其他类型的车床,在加工零件时,一般是一次加工一个零件,每个部位可能会分若干次进刀,当尺寸发生变化时可随时采取措施。
自动车床就不同了,它一经启动,零件就会不断产出。
主轴转数设定的准确与否,直接影响的就是、生产效率。
也可以这样讲,当我们确定了所要生产的产品,也就同时确定了主轴转数。
..综上所述,我们在进行凸轮设计时,可以把主轴转数N当作一个常量来设定;无疑,(Σn工/Σα工)×360°是一个变量。
N设:(Σn工/Σα工)×360°=W。
公式则可成为为: A= ——W根据数学的计算法则,A的值与W的值成反比。
只有W的值尽可能的小,A的值才能尽可能的大。
那么,怎样才能使W即(Σn工/Σα工)×360°的值尽可能的小呢?二、设计公式的分析与使用在一篇凸轮设计调整卡中,工步编排得是否完美,直接影响着(Σn工÷Σα工)×360°值的大小。
也就是说,(Σn工÷Σα工)×360°的值,是编排完工步后计算的结果。
前面提到,作好工步编排,既需要相应的工作经验,更需要丰富的想象力。
这一点,充分体显在凸轮设计开始前,对每把刀所要加工的部位的设定上。
合理的使用每一把刀,是使一件设计作品尽可能完..美的前提。
本文后面有几篇例,都是经工作实践检验证明是较为成功的作品,读者可作为设计时的参考。
下面只从计算的角度分析一下:怎样才能使(Σn工÷Σα工)×360°的值尽可能的小。
Σn工公式:Σn工÷Σα工×360° = W 即:—————×360° = WΣα工公式中①Σn工——累计切削工步主轴转数的总和。