5、浅谈四项常规无损检测在压力容器制造中的选用
浅谈无损检测技术在压力容器中的应用
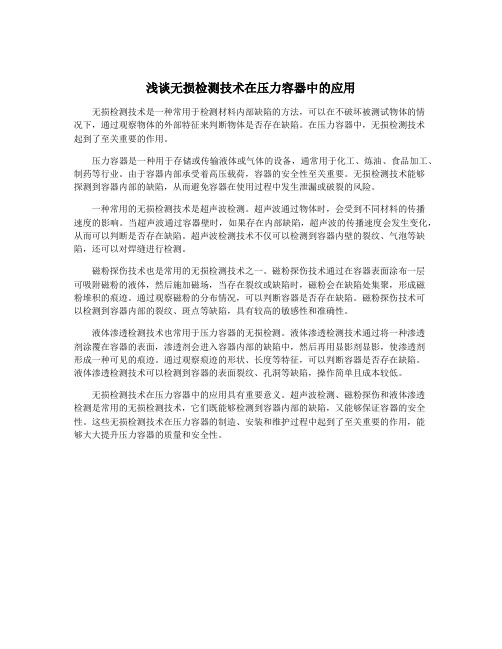
浅谈无损检测技术在压力容器中的应用无损检测技术是一种常用于检测材料内部缺陷的方法,可以在不破坏被测试物体的情况下,通过观察物体的外部特征来判断物体是否存在缺陷。
在压力容器中,无损检测技术起到了至关重要的作用。
压力容器是一种用于存储或传输液体或气体的设备,通常用于化工、炼油、食品加工、制药等行业。
由于容器内部承受着高压载荷,容器的安全性至关重要。
无损检测技术能够探测到容器内部的缺陷,从而避免容器在使用过程中发生泄漏或破裂的风险。
一种常用的无损检测技术是超声波检测。
超声波通过物体时,会受到不同材料的传播速度的影响。
当超声波通过容器壁时,如果存在内部缺陷,超声波的传播速度会发生变化,从而可以判断是否存在缺陷。
超声波检测技术不仅可以检测到容器内壁的裂纹、气泡等缺陷,还可以对焊缝进行检测。
磁粉探伤技术也是常用的无损检测技术之一。
磁粉探伤技术通过在容器表面涂布一层可吸附磁粉的液体,然后施加磁场,当存在裂纹或缺陷时,磁粉会在缺陷处集聚,形成磁粉堆积的痕迹。
通过观察磁粉的分布情况,可以判断容器是否存在缺陷。
磁粉探伤技术可以检测到容器内部的裂纹、斑点等缺陷,具有较高的敏感性和准确性。
液体渗透检测技术也常用于压力容器的无损检测。
液体渗透检测技术通过将一种渗透剂涂覆在容器的表面,渗透剂会进入容器内部的缺陷中,然后再用显影剂显影,使渗透剂形成一种可见的痕迹。
通过观察痕迹的形状、长度等特征,可以判断容器是否存在缺陷。
液体渗透检测技术可以检测到容器的表面裂纹、孔洞等缺陷,操作简单且成本较低。
无损检测技术在压力容器中的应用具有重要意义。
超声波检测、磁粉探伤和液体渗透检测是常用的无损检测技术,它们既能够检测到容器内部的缺陷,又能够保证容器的安全性。
这些无损检测技术在压力容器的制造、安装和维护过程中起到了至关重要的作用,能够大大提升压力容器的质量和安全性。
压力容器无损检测技术的选择及应用

压力容器无损检测技术的选择及应用压力容器通常用于储存或输送高压气体、液体或固体,在化工、制药、石油、天然气等行业广泛应用。
这些压力容器的工作环境极为恶劣,纯化度不高,加工精度不够,制造过程中存在缺陷,因此需要进行定期的无损检测以确保其安全可靠地运行。
本文将介绍常见的压力容器无损检测技术及其在工业生产中的应用。
1. X射线检测(RT)X射线检测是一种常见的无损检测技术,可以检测到容器壁内部的裂纹、腐蚀、孔洞等缺陷。
这种技术需要用到专业的电子设备和探测器,并且需要专业的技术人员操作。
2. 超声波检测(UT)超声波检测是利用超声波的声波反射原理来探测容器内部缺陷情况的一种技术。
该技术操作简单,成本低廉,能够检测到表层和深层的缺陷,具有较高的灵敏度和特异性。
磁粉检测是将可磁化物质撒在被测体表面,然后施加磁场,利用磁性颗粒的聚集来检测工件表面和近表面的缺陷,具有灵敏度高、能够检测到表层和近表面的缺陷等优点。
涡流检测是利用交流电磁场产生的涡流效应来对容器内部缺陷情况进行探测的一种技术。
该技术可以检测到容器内部的表层缺陷,对于薄壁容器的检测效果较好。
1. 化工行业化工行业是使用压力容器最多的行业之一。
在化学品生产和运输过程中,经常使用高压容器来储存化学反应产物或输送液体、气体,因此需要进行无损检测以确保容器的安全性。
2. 石油和天然气行业石油和天然气行业需要大量的储存和输送设备,包括储油罐、油气管道等。
这些设备工作在高压、高温和高腐蚀环境下,对设备的安全性和可靠性提出了更高的要求。
因此需要进行定期的无损检测来确保设备的安全可靠。
3. 医药行业在医药行业,压力容器主要用于制造药品和生物制品。
药品的制造和输送过程需要使用高压容器,通过无损检测可以确保药品的安全性。
总之,压力容器无损检测技术成为了很多工业领域中必不可少的检测手段,正是依托于这些科技创新,才能确保对危险场所的安全。
在未来的生产中,各行各业必将进一步发扬光大,促进可持续发展。
浅谈无损检测技术在压力容器检验的运用

浅谈无损检测技术在压力容器检验的运用前言目前,在我国许多领域,诸如造纸、冶金、石油、化工、医药等行业中都大量使用到了压力容器,表明压力容器有着极为广阔的应用范围。
压力容器属于特种设备的一类,其运行状况承受着各种恶劣的条件,包括高温、高压、易燃易爆、剧毒、强腐蚀性等,如果压力容器在使用过程中存在安全隐患,势必会影响设备的运行状况,严重时甚至会发生不可挽回的安全事故。
针对这一严峻的现状,如何做好压力容器的检验工作,对于保证各领域压力容器的使用安全而言有着极为重要的意义。
一、压力容器常用无损检测技术类别目前压力容器常用的检测方法主要包括射线检测、超声检测、磁粉检测和渗透检测,下面进行着重的介绍:(一)射线检测射线检测主要依靠的是x射线较强的穿透性能对压力容器内部缺陷进行的检测。
其主要原理是,x射线在穿透过程中,射线强度会受到不同程度的削弱,但是这种削弱是固定的,当穿透部位出现减弱程度变化时,在射线底片上会留下相应的投影图像[3]。
通过射线底片能够较为直观的看到缺陷部位的具体形状,从而对缺陷进行定量与定性分析。
非常适合检测对接焊缝中存在的缺陷,对体积型缺陷检出率很高。
射线检测的缺点是在检测过程中容易受到现场条件的制约无法进行大量、全面的检测,而且检验成本相对较为高昂,无法实现大规模普及。
(二)超声检测超声检测主要是依靠超声波对压力容器内部的缺陷进行检查。
一般来说,超声波的频率需要控制在0.5MHz至5MHz范围内,在这个频段内超声波的分辨力高,有利于区分相邻缺陷,且声速指向性也好。
超声检测的原理主要是超声波进入工件,在传导过程中遇到工件内部缺陷,其传播方向或特性会被改变,改变后的超声波被检测设备接收,通过分析其特性,判断是否存在缺陷。
超声检测的主要优势在于能够利用极强的穿透性提高裂纹等平面型缺陷的检出率,操作相对较为简单,灵敏度较高。
但是超声检测的缺点在于不能完全满足结构复杂、光洁度要求较低的零件检验,除此之外,对缺陷进行精确的定性,定量仍需作深入研究,缺陷的位置、形状对检测结果也会有一定影响。
刍议压力容器无损检测技术的选择及应用 压力容器无损检测方法

刍议压力容器无损检测技术的选择及应用压力容器无损检测方法摘要:随着工业生产制造技术不断进步与发展,人们对产品的质量和结构安全性、使用性和可靠性提出了更高要求。
鉴于无损检测技术具有不破坏试件、检测灵敏度高等优势,被广泛应用于压力容器质量安全及使用可靠检测中。
为了提升无损检测技术对压力容器的检验效果,本文初步分析了压力容器无损检测技术选用过程中应当注意的问题,以及压力容器制造及使用过程中采用的检测技术,使相关行业和企业使用到安全可靠的压力容器。
关键词:压力容器;无损检测技术;选择;制造;应用:TQ053 :A压力容器作为一种承载一定压力的密闭设备,其质量问题可能带来严重的人员伤亡及经济损失。
因此,检验是压力容器安全生产与应用的重要环节。
为了不破坏试件、保证检验结果科学可靠,无损检测技术被广泛应用于压力容器质检工作中。
无损检测技术是一种在不破坏试件前提下,用物理和化学手段、借助先进的技术和设备对试件内外表面的状态、性能、结构等指标进行检验,确保试件具有优良的使用性能,有效防止爆裂等危害性事故发生。
一、压力容器无损检测技术选用过程中应当注意的主要问题尽管无损检测技术具有一定的强大优势,可仍具有一定局限性,每一种检测技术都不是万能的。
比如,超声波及射线检测技术适用于承压设备的内部缺陷检测;渗透检测技术适用于非多孔性金属材料检测;磁粉检测技术适用于铁磁性材料制成的承压设备表面和近表面缺陷检测;等等。
因此,选择无损检测技术过程中应注意以下问题,尽量选择最合适的检测技术,才能在应用过程中充分发挥自身的有效性。
(一)确定无损检测技术实施时间压力容器质检过程中,检测人员应当根据检测目的,结合容器工况、制造工艺及材质等情况科学、合理地确定无损检测技术的实施时间。
由于每一种工件及每一道工序都有属于自己的最佳检测时间,不能颠倒检测循序与检测时间,否则起不到质检效果。
比如,锻件超声波探伤一般在锻造完成后,钻孔、精磨等工序加工前进行。
浅谈四项常规无损检测在压力容器制造中的选用
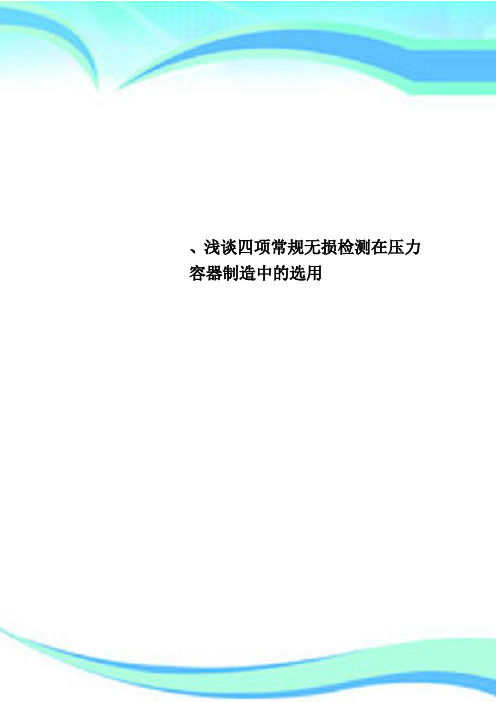
、浅谈四项常规无损检测在压力容器制造中的选用————————————————————————————————作者:————————————————————————————————日期:浅谈四项常规无损检测在压力容器制造中的选用童天海(安徽六方深冷股份合肥230088)摘要结合新版JB/T4730-2005《承压设备无损检测》,对压力容器产品制造过程中焊缝无损检测需要注意的几个方面进行总结,以引起同行们的注意。
关键词无损检测 UT超声检测 RT射线检测 PT渗透检测 MT磁粉检测1 前言压力容器是一种可能引起爆炸或中毒等危害性较大事故的特种设备,一旦发生爆炸或泄漏,往往并发火灾、中毒、污染环境等灾难性事故,所以压力容器比一般机械设备有更高的安全要求。
无损检测是压力容器安全管理的重要环节。
目的就是防止压力容器发生失效事故,特别是预防危害最严重的破裂事故发生。
因此,压力容器检验的实质就是失效的预测和预防。
现代无损检测的定义是:在不损坏试件的前提下,以物理或化学方法为手段,借助先进的技术和设备器材,对试件的内部及表面的结构,性质,状态进行检查和测试的方法。
2 对焊缝内部的无损检测射线探伤和超声波探伤是对焊缝内部进行无损检测的主要方法。
对于焊缝中的裂纹、未熔合等面状危害性缺陷,超声波比射线有更高的检出率。
随着现代科技快速发展,技术进步。
超声仪器数字化,探头品种类型增加,使得超声波检测工艺可以更加完善,检测技术更为成熟。
但众所周知:超声波探伤中人为因素对检测结果影响甚大;工艺性强;故此对超声波检测人员的素质要求高。
检测人员不仅要具备熟练的超声波探伤技术,还应了解有关的焊接基本知识;如焊接接头形式、坡口形式、焊接方法和可能产生的缺陷方向、性质等。
针对不同的检测对象制定相应的探伤工艺,选用合适的探伤方法,从而获得正确的检测结果。
2.1射线检测局限性2.1.1辐射影响,在检测场地附近,防护不当会对人体造成伤害。
2.1.2受穿透力等局限影响,对厚截面及厚度变化大的被检物检测效果不好。
浅谈压力容器设备无损检测技术的选用策略

浅谈压力容器设备无损检测技术的选用策略引言无损检测技术是在用压力容器产品安全控制中不可缺少的基础技术,随着压力容器的应用范围不断扩大,产品复杂程度增加和对安全性的严格要求,无损检测技术在在用压力容器产品安全控制中发挥着越来越重要的作用。
一、压力容器无损检测技术1、物质渗透检测技术压力容器的无损检测中,最常用的一种检测方法就是物质渗透检测,它具有适用范围广、可操作性强、检验结果精确、成本低廉等优势。
物质渗透检测法,就是将渗透液涂抹在待检测的容器表面,液体根据毛细管现象的原理,会渗入容器裂纹内部,当擦除容器表面的渗透液之后,使用和渗透液对应的显像物质可以让容器表面的裂纹显现出来。
这种检测方法具有很强的可靠性,但只能检测容器表面裂纹缺陷,对容器内部的缺陷无能为力。
2、物质辐射检测技术在工业生产领域,物质辐射检测也是一种常用的压力容器无损检测方法。
它主要依据被检测容器受损部位和正常部位吸收射线的类型差异而进行的,这种检测方法的优点是检测结果直观,能立体地展现容器缺陷,此外,这种检测方法不仅可以对缺陷进行定性,还可以定量,以此来评价掌握容器受损情况。
但是,物质辐射检测技术中使用的射線会危害人体,因此,在实际操作中应注意个体保护。
3、物质电磁检测技术物质电磁检测技术是依据压力容器材质的电磁特性进行的,依据该原理采用的方法主要有以下几种:(1)涡流检测。
主要适用于由导电材质制成的压力容器,通过电磁感应技术,发现容器表面存在的裂纹、腐蚀等。
(2)金属磁记忆检测。
这种方法检测结果精确程度高,尤其适用于对微小损伤的检测。
(3)漏磁检测。
在检测过程中首先磁化容器表面的铁磁物质,由于容器表面的损伤处会发生漏磁,根据这一原理可以发现容器表面的裂纹或者腐蚀状况。
漏磁检测技术与其他压力容器无损检验方法相比,具有自动程度高、检测结果精确的优势。
4、物质声学检测技术(1)声发射检测。
声发射检测是依据声音发射技术检测压力容器中存在的损伤,通过检测容器声发射信号确定其声发射源,根据容器内在损伤部位所特有的发声信号,确定容器损伤部位,这种检测方法与其他压力容器无损检测技术相比更简便,且成本更低廉,安全系数更高,检测结果的可靠性也有充分保障。
压力容器制造过程中无损检测的应用

压力容器制造过程中无损检测的应用压力容器是广泛应用于石化、化工、医药、汽车、食品等领域的一种基础设施,其主要功能是储存或运输高压气体、液体或蒸汽等物质。
由于压力容器的特殊性质,其在制造、使用和维护过程中需要保证安全可靠。
而无损检测技术则是目前最为成熟的检测方法之一,被广泛应用于压力容器的制造过程中。
无损检测技术是指不对被检测材料进行破坏或对其物理性质造成实质性损伤的情况下,通过各种物理、化学或者力学的手段去寻找被检测材料中的缺陷或物理指标。
常见的无损检测方法包括X射线检测、超声波检测、涡流检测、磁粉检测和红外热像检测等。
1.原材料检测压力容器制造的原材料通常采用高强度、耐腐蚀的材料,如铁、钢、镍等。
在原材料采购和入库过程中,需要对原材料的质量进行检测,确保所选材料符合国家或行业标准的规定。
无损检测技术可以通过扫描材料表面或内部,识别出其中是否存在缺陷、疵点或异物等问题,确保采购的原材料的质量稳定性。
2.焊接接头检测大多数压力容器采用焊接方式进行制造,焊接接头的质量对于整个容器的使用寿命和安全性至关重要。
在焊接接头中,易产生焊缝、毛刺、气孔等缺陷,而这些缺陷会降低焊接接头的强度和密封性。
无损检测技术可以通过对焊接接头的扫描和分析,及时发现并去除缺陷,保证焊接接头质量。
4.设备维修检测压力容器在使用过程中难免会受到磨损和损坏,需要及时进行维修或更换。
在设备维修过程中,对于设备的安全性能也需要重新检测确认。
无损检测技术可以在设备维修过程中对设备进行扫描和检测,及时发现设备存在的安全隐患并进行修补。
综上所述,无损检测技术的应用,为压力容器的制造、运输、使用提供了有效的保障。
它可以在制造过程中发现潜在的安全隐患,提前进行修复,保证制造质量和设备的安全性。
通过无损检测技术的不断优化和完善,压力容器的安全性和稳定性将得到很大提升。
四项常规无损检测在压力容器制造中的选用

机械化工科技风2016年12月下DOI:10.19392/ki.1671 -7341.201624086四项常规无损检测在压力容器制造中的选用林锐权中山市南方空气分离设备有限公司广东中山528400摘要:随着当前科学技术的不断发展和完善,国家综合国力的强大,我国在进行压力容器的无损检测过程中衍生出了几种有效的方式,分 别是射线探伤、超声波探伤、磁粉探伤以及渗透探伤四大类。
本文我们基于这四大类无损检测方法探究其在压力容器制造中的选择原理以及注 意事项。
关键词:常规无损检测;压力容器;焊缝压力容器的无损探伤对于保证社会的安定,人们生活的安居乐业 具有非常显著的意义。
压力容器一旦出现爆炸或者泄露等问题,不仅会 严重影响到企业的经济效益,同时也会使得人民的生活环境受到极大 的烕胁。
因此开展压力容器的无损检查是非常有必要的。
当前来看,无 损检测主要是通过物理或者化学上的方式,通过科学技术的辅助,X才压力容器的内部以及外部实现有效的检测,以判断压力容器的内外部是 否出现了裂缝等现象,能够在发现问题的情况下及时进行处理,确保压 力容器的质量。
―、焊缝内部的检测方式(一) 射线探伤当前在焊缝内部的探伤方式之一就是射线探伤,射线探伤主要是 通过X射线实现对压力容器内部裂缝的检测。
但是就目前的发展形式 和科学技术的进步来看,射线探伤的方式需要进行一定的改善和创新。
首先,射线探伤具有较强的辐射,对于操作人员以及周边的环境等都会 产生较大的影响,如果相关操作人员在穿着上没有进行全面系统的防 护,很容易造成不可磨灭的损伤。
其二,射线探伤对于一些压力容器规 格较小以及穿透性较好的材质比较容易探测,但是一旦压力容器厚度 过大或者其材质穿透性不高,那么射线探伤很容易在检测过程中出现 误检,或者将一些细小的裂缝遗漏,为后续压力容器投入使用造成了较 大的安全隐患。
也就是说射线探伤在进行压力容器内部检测过程中存 在一定的局限性。
第三,射线探伤能够有效的检测出压力容器内部的裂 缝等线状损伤,但是对于一些面积较大,与压力容器内表面相贴合的损 伤却不容易检测,会出现一定的误差。
压力容器无损检测方法的选择

压力容器无损检测方法的选择摘要:随着现代工业的发展,对产品的质量数量,结构安全性,使用可靠性,不断提高了要求,因为无损检测技术不会损坏试件,检测灵敏度高等优点,因此其应用越来越广泛。
本文简要介绍了压力容器的制造和使用过程使用射线照相测试,超声波测试,磁粉测试,穿透渗透测试,涡流测试,红外测试和磁存储器测试测试特性和选择原则。
关键词:压力容器;无损检测;方法引言无损检测技术具有无损检测片的优点,检测灵敏度高和其他功能,因此广泛用于压力容器的制造检查和带检查。
对于压力容器的检查,不同对的正确选择无损检测方法,并选择无损检测的质量利弊进行评估并将无损检测结果应用于安全整体状况评估。
因此,在制定检查计划时,相同无损检测方法的范围,技术特点,优点和局限性性能和非破坏性测试的时间安排,以正确控制测试比率例。
在这里,我们主要讨论使用中的压力容器的无损检测。
1、无损检测方法的特点和选择原则1.1非破坏性试验应与破坏性试验相结合。
无损检测的最大优点是在不损坏材料结构的基础上进行测试,设有综合测试机构无与伦比的优势。
无损检测技术具有局限性,不能全部替代破坏性的测试。
例如液体除无损检测外,LPG钢瓶还需要进行喷砂处理测试。
1.2选择无损检测的时机要恰当。
依据检测的目的进行压力设备的无损检测,结合设备工作条件,材料和制造工艺的特点,确实选择了无损检测的实施时间。
例如锻造声波探伤,通常在锻造和粗加工后布置加工后,在最终加工之前,例如钻孔,铣削,精磨等。
1.3正确选择无损检测的方法要适合。
通过各种检查,对压力设备进行无损检测量方法具有某些特性,不能应用于所有工件及所有缺陷应根据实际情况灵活调整选择最合适的无损检测方法。
例如钢铁分层缺陷不适合,因为其延伸方向平行于电路板超声检查应选择超声波检查。
1.4全面应用各种无损检测方法。
没有在无损检测中,任何无损检测方法都不是能够。
因此在无损检测中,尽可能使用多种检测方法来学习彼此的长处有关缺陷的信息,以便更清楚地了解实际情况。
浅谈压力容器制造过程中的检验

浅谈压力容器制造过程中的检验作者:任小玉靳艳涛赵培来源:《城市建设理论研究》2013年第04期摘要:文章概述压力容器制造过程检验的重要性,压力容器制造过程检验的目的,探讨检验的范围与项目。
关键词:压力容器;目的;范围;项目Abstract: The importance of the manufacturing process of pressure vessel inspection, pressure vessel manufacturing process for verification purposes, research scope and project inspection.Key words: pressure vessel; objective scope; project;中图分类号:TH49前言:据统计目前我国压力容器制造厂家1800余家,压力容器的用途十分广泛。
它是在石油化学工业、能源工业、科研和军工等国民经济的各个部门都起着重要作用的设备。
压力容器制造过程的检验基本与其制作工序基本一致,主要分为:原材料的检验、下料检验、组装检验、焊接检验、无损检测、热处理、压力试验检验及对制作过程中的质量验证的理化试验检验。
一、压力容器制造过程检验的目的:压力容器检验的基本目的就是防止压力容器失效事故,特别是危害最严重的破裂事故的发生,通过验证性检验和抽查等手段来保证压力容器产品的安全性能,在压力容器出厂或投入使用前就发现问题,从而杜绝因质量不符合规范标准要求而在使用时失效的可能性。
其内容包括外观检查、结构检查以及几何尺寸检查。
通过对压力容器制造过程的检验,压力容器检验员应对以下几个方面做出判断:1.压力容器的有关资料是否与实际相符;2.压力容器的制造质量如何;3.被检压力容器在后续检验工序中应该重点检验哪些方面。
二、压力容器制造过程检验的范围:一般压力容器的范围是指压力容器本体和安全附件一般包括:1、容器与外部管道连接2、壳体、封头(端盖)、膨胀节、设备法兰、球罐的球壳板、换热器的管板和换热管、M36以上(含M36)的设备主螺栓以及公称直径大于或者等于250mm的接管和管法兰。
无损检测在压力容器制造中的应用

中 图 分 类 号 :T 4 H9 文 献 标 识 码 :B 文 章 编 号 :1 0 — 16 ( 0 0 3( ) 0 7 一 1 0 9 9 6 2 1 )0 5C 一 09 O 正 确选 择 无损 检 测 ( D )方 法 ,提 高 对压 力 容 照方 式 主 要 根据 产 品或 工 件 的 结 构和 几何 尺 寸 来 确 定 , N T 器焊缝无损检测 ( T ND )的可 靠性 。我们知道 ,无损检 其 目的 是 为 了保证 焊 缝 的 抽 检 率 和保 障 检 测 的 准 确性 。 测 是 指 在 不 损 坏 和破 坏 材 料 或 工 件 本 业使 用 目的 和 价 值 ( )暗 室 处 理 质量 的提 高 。 有 人 说 ,射 线 检 测 起 始 于 4 的情 况 下 ,对其 内 、外 部 质 量 进 行 检 测和 评 定 的 一 种 检 暗 室 ,又 终 止于 暗 室 。这 主 要是 强调 底 片 质 量 的好 坏 贯 测 方 法 。而 压 力 容 器无 损 检 测 是 在 容 器应 力分 析 和 材 料 穿 于 检 测 的每 一 过 程 ,且 最 终还 是 要 靠 观 察 评 定底 片的 性能评价的前提 下,确定焊缝中是否存在缺 陷,以及缺 结 果 来 判 断焊 缝 质量 的 优 劣 。 我 们现 在 采 用 的 是胶 片手 陷 当量 、缺 陷性 质和 危 害 程 度 ,以 保证 压 力容 器安 全 运 工 处 理 ,整 个暗 室 处 理 过 程 分 为 显影 、停 显 、定影 、水 行 的 一 种 手 段 。 无损 检 测 的 可 靠 性 依赖 于 缺 陷的 检 出率 洗 、干 燥五 个步 骤 。暗 室 处 理 不 当 ,会 带 来 各 种各 样 的 和 对 检 出 缺 陷定 笥 、定 量 结 果 的 正 确程 度 两 方 面 。而 四 伪 缺 陷 ,直 接 影 响检 测 结 果 的 可 靠性 。在 暗 室 处理 中 , 大 常规 无 损 检测 方 法各 有其 优 缺 点 :射 线检 测 ( RT)和 曾经 底 片 发黄 。我 们 分 析 原 因 ,主 要 有 以 下 几 点 :①胶 超 声 波检 测 ( UI )主 要是 检 查 焊缝 内部 的 缺 陷 。射 线 检 片 本 身 质量 差 ; ②定 影 液 严 重氧 化 失 效 ;③水 洗时 间不 测 对 于 气 孔 、夹 渣 、未 焊 透 等 体 积 型缺 陷 比较 敏 感 ,但 够 等 。 经仔 细 分 析 ,定 影 液 温 度 高 ,长 期 没换 ,氧 化 失 对 裂 纹 、未 熔 合 等 面 状 缺 陷 并 不 敏 感 ,且 检 查 操 作 比较 效 极 有 可能 。重 新 配 制 定 影 液 ,再 进 行 暗 室处 理 ,则 底 麻 烦 ,并 受 到擦 伤 设 备 能 力 和射 线检 测 方 向的 限 制 ;而 片 黄 色 消 失 ,验 证 了推 论 是 正确 的 。又 如 ,中 间有 段 时 超 声 波 检测 对 于 裂 纹 、未 熔 合 等 面 型缺 陷 比较 敏 感 ,而 间没使用停影液 ,底片上有蛙机状条纹 ,经分析观察 , 对 体 积 型缺 陷的 检 出率 相 对 比较 低 ,且 检 出结 果 取 决 于 发 现 是 显 影 液 的 碱和 定影 液 中 的酸 相 互 作 用 产 生 CO , 探 伤 人 员的 熟练 程 度 和 探 伤 仪 器 的精 确 灵敏 度 。磁 粉检 在 定影 时 气泡 沿 胶 片 表 面 上 升 ,至 此 胶 片 定影 不 均 匀 造 测 ( T)和渗 透 检 测 ( M PT)主 要 适 用于 表 面 裂 纹 的检 成 的 ,找到 了原 因 ,此 后 暗 室处 理 时 经 过停 显 、并 在 处 查 ,磁 粉检 测 主 要 适 用 于 铁 磁性 材 料 的 表 面 和 近表 面缺 理过程 中不断抖动底片 ,消除了这一不 良现象。 ()底 5 陷 的 检测 ,但 无 法 检 测 有 色 金 属和 奥 氏体 不 锈 钢 等 非铁 片的正 确评定和检测结果的处理 。正确理解各种标准 , 磁 性物 质 ;而 渗 透 检 测 不 仪 适用 于 铁 磁 性 材 料 ,而 且适 合 理评 定底 片 ,对 保 证 产 品 的 质量 和 降 低 制造 成 本 起 着 用 于 有 色金 属 材 料 表 面 开 口缺 陷 的检 测 ,尤 其 对针 孔和 积极重要的作用 ,在平时底 片评定中 ,应尽量先 了解产 疏松类缺 陷的检测更合适 ,但不能判断缺陷的取向和 内 品的结构 、坡 口型式、焊接方法 、材质、透 照方式等评 片信息 ,估计材料焊接可能产生的缺陷情 况,再运用有 部尺寸 ,只能检出表面开口缺陷。 二 、无损检测 ( T ND )质控 系统 工作 质量的提高依 关标准 ,获取底片上的所有信息 ,综合评定 。记得有一 赖 于 整 个 检 测 过 程 各 工 序 的 质 量 把 关 。 ( )依 据 有 关 次在评片 中,我发现底片焊缝热影响区有一类似裂纹的 1 规 程 、标 准 ,正 确 制 定 出检 测 工艺 ,尽 量 做 到 缺 陷不 漏 “ 陷 ” ,仔 细 观 察 其 两端 ,发 现 既 无发 展 趋 势 的 尖锐 缺 检 。压 力容 器 一 般 按 GB10 钢 制 压 力 容 器 》制 造 、检 分 叉 ,且 黑 度 也 较 均 匀 。为 安 全 起 见 ,我 先 用 超 声 波 复 5 验 和 验 收 ,并 受 《 力 容 器 安 全 技 术 监 察 规 程 》 的 监 验 ,发 现 无 缺 陷 反 射波 ,后 又 在 工 件 原位 置适 当改 变射 压 督 ,所 以 在 编 制 检 测 工 艺时 ,就 应 考 虑 采 用哪 种 检 测 方 线机检测角度 ( 防止射线干涉现象产生伪缺陷 )重新拍 缺陷”。再一分析 ,可能是 法 探伤 ,探伤比例是多少等 。如压力容器壁厚 小于或等 了一张底片 ,发现 并无此 “ 于3 rm的碳素钢 ,其A类及B 8 a 类焊缝 ,主要采 用射线检 装胶片或暗室处理 显影前 由于轻微划痕所造成的。对于 测 ( RT)。 又 如 压 力 容 器 封 头 拼 缝 应 在 冲压 成 型 之 后 局 部 检 测 评 定 不 合格 的 底 片 ,发 放返 修 通 知 单 时 还应 考 进 行 l0 0 %的射 线 检测 ,检 测 的 合 格级 别 应 与 简体 的 要 求 虑 由于 透 照 方 式 不 同 引起 的 缺 陷 影像 的偏 移 ,以便 正 确 致 ;若在冲压前检测 ,因过渡段在冲压过程 中变形较 确定返修部位。局部检测返修部位焊缝除进行复拍外 , 大 ,易 引起一些微小缺 陷的扩展 ,产生超标缺 陷,所以 还 要 按 标 准 规 定 对 该 条 焊 缝 增 拍 ,产 品 检 测 结 果 合 格 冲 压 成 型 后 应 对过 渡 段 进 行 一 定 比 例 的检 测 抽 查 ,合 格 后 , Ⅱ级 以 上 检测 人 员应 对 检 测 结果 及 时 出具 报告 、存 级 别仍 与 简 体 要 求 一致 。鉴 于 此 ,在执 行 压 力容 器 无 档 。 三 、无 损检测 ( D )作 为一种先进的综合性应用 N T 损检测) B T 7 0 -0 5 )J / 43 - 20 标准时,封头拼缝按纵缝 ( A 缝 )K 要 求 。 当用 周 向X 线 机曝 光 时 ,其 一 条拼 缝 至 科学技术 ,在 生产上发挥其 巨大作用 。众所周知 ,国外 值 射 少得内透三次 ,此时工作效率较高 ,且检测质量可靠。 将 NDT朱之 为现 代 工业 的 基础 。随 着改 革 开放 的 不断 深 j ()射线 检 测 的 实施 时 间和 局部 检 测 时 的检 测部 位 。压 入 ,国 内NDT 越来 越 受 到人 们 的关 注 与 重视 。有 人 预 2 也 力 容 器 的 焊缝 应 在 规 定 的 形 状 尺 寸和 外观 质量 检 查 合 格 计 ,无 损 检测 要 经 历无 损 探 伤 、 无损 检 测 、和 无损 评 价 后 ,才 能 进行 射 线 检 测 ;有 裂 纹 倾 向 的材 料 ,应 在 焊接 三 个 阶 段 。 目前 我 国在 检 测 仪 器设 备 和 尖 端技 术上 与国 完 成 2 小 时后 ,方 能 进 行 了 射 线检 测 。局 部 检 测 时 ,首 际先 进 水平 相 比还 有一 定差 距 ( T F 技术 在 厚板检 测 4 如 O D 选 每 一 相 交 的焊 缝 部 位 ,其 次 选 开孔 附 近 焊 缝 部 位 、支 领 域 的 普 及应 用 ) 。在 检 测技 术 标 准 上 ,有 关部 门 已结 座 垫 板 等 覆 盖焊 缝 部 位 和 最 后 组焊 部 位 。 因为 这 些 部位 合我国实际情 况与 国际先进工作者标准接轨。我 国的无 都 是 应 力 比较 集 中 ,焊 接 条 件 恶 劣且 易产 生 危 险 性 缺 陷 损 检 测 技 术也 正 在 向微 型 化 、数 字 化 、智 能化 和 自动 化 的 部 位 。 ( )射 击线 检 测 ( 3 RT)透 照方 式 、工 艺 参数 的 方 向发展 。 作者单位 :河南油田油建公 司 等的正确选择和灵活运用。射线检测 ( RT)中焊缝的透
压力容器何时进行无损检测以及无损检测方法的选择

压力容器何时进行无损检测以及无损检测方法的选择为了确保压力容器的安全质量,从压力容器使用的原材料开始都要通过无损检测来进行质量控制。
压力容器使用的原材料包括金属板材、管材、棒材、锻件和铸件等,需根据这些材料制造工艺和几何形状采用不同的无损检测技术。
1.1 压力容器用金属板材的无损检测压力容器用金属板材一般包括钢板、不锈钢板、双相钢板、铝及铝合金板材、钛及钛合金板材等,主要用于压力容器筒体和封头的制造。
所有的压力容器制造规范或标准均规定,处于剧毒、腐蚀、高压等较苛刻工作条件下的压力容器,其金属板材必须逐张进行超声检测。
此超声检测所用的探头为单晶或双晶直探头,主要用于检测金属板材在冶炼和轧制过程中产生的分层、白点和裂纹等缺陷。
大面积的钢板检测(包括边区检测和面积检测)一般都用充水耦合探头进行。
1.2 压力容器用管材的无损检测1 P% M3 u* e9 @: s" 压力容器用管材包括无缝钢管、焊接钢管、铜及铜合金管、铝及铝合金管、钛及钛合金管等,# F9 l: o- v# Y5 z三维网技术论坛主要用于换热器的制造。
7 n$ h* f4 M7 ]7 X无缝钢管采用液浸法或接触法超声波检测,主要检测纵向缺陷。
液浸法检测使用线聚焦或点聚1 l1 x. b, k, A7 a# E焦探头,接触法检测使用与钢管表面吻合良好的斜探头或聚焦斜探头。
; Z& C2 T0 Q" b2 w5 q: 所有类型的金属管材都可用涡流检测法探测其表面和近表面缺陷。
铁磁性钢管一般用外穿过式5 y6 A9 R& g1 |. {6 ?三维,cad,机械,技术,汽车,catia,pro/e,ug,inventor,solidedge,solidworks,caxa,时空,镇江线圈或放置式线圈检测;对于非铁磁性材料,管材口径较小时一般用外穿过式线圈检测。
三维网技术论坛7 Y& e0 l# P- ^. O2 a$ j; P1.3 压力容器用钢锻件的无损检测0 o5 r' I0 e3 V三维|cad|机械|汽车|技术|catia|pro/e|ug|inventor|solidedge|solidworks|caxa压力容器用钢锻件主要包括接管、法兰、凸元、管板和圆筒等。
在用压力容器的无损检测

在用压力容器的无损检测在用压力容器检验的重点是压力容器在运行过程中受介质、压力和温度等因素影响而产生的腐蚀、冲蚀、应力腐蚀开裂、疲劳开裂及材料劣化等缺陷,因此除宏观检查外需采用多种无损检测方法。
(一)表面检测表面检测的部位为压力容器的对接焊缝、角焊缝、焊疤部位和高强螺栓等。
铁磁性材料一般采用磁粉法检测,非铁磁性材料采用渗透法检测。
(二)超声检测超声检测法主要用于检测对接焊缝内部埋藏缺陷和压力容器焊缝内表面裂纹。
超声法也用于压力容器锻件和高压螺栓可能出现裂纹的检测。
由于超声波探伤仪体积小、重量轻,便于携带和操作,而且与射线相比对人无伤害,因此在在用压力容器检验中得到广泛使用。
(三)射线检测x射线检测方法主要在现场用于板厚较小的压力容器对接焊缝内部埋藏缺陷的检测,对于人不能进入的压力容器以及不能采用超声检测的多层包扎压力容器和球形压力容器通常采用lr-192或Se-75等同位素开展Y射线照相。
另外,射线检测也常用于在用压力容器检验中对超声检测发现缺陷的复验,以进一步确定这些缺陷的性质,为缺陷返修提供依据。
(四)涡流检测对于在用压力容器,涡流检测主要用于换热器换热管的腐蚀状态检测和焊缝表面裂纹检测。
(五)磁记忆检测磁记忆检测方法用于发现压力容器存在的高应力集中部位,这些部位容易产生应力腐蚀开裂和疲劳损伤,在高温设备上还容易产生蠕变损伤。
通常采用磁记忆检测仪器对压力容器焊缝开展快速扫查,以发现焊缝上存在的应力峰值部位,然后对这些部位开展表面磁粉检测、内部超声检测、硬度测试或金相分析,以发现可能存在的表面裂纹、内部裂纹或材料微观损伤。
(六)红外检测许多高温压力容器内部有一层珍珠岩等保温材料,以使压力容器壳体的温度低于材料的允许使用温度,如果内部保温层出现裂纹或部分脱落,则会使压力容器壳体超温运行而导致热损伤。
采用常规红外熟成像技术可以很容易发现压力容器壳体的局部超温现象。
压力容器上的高应力集中部位在经大量疲劳载荷后,如出现早期疲劳损伤,会出现热斑迹图象。
压力容器无损检测技术的选择及应用

压力容器无损检测技术的选择及应用【摘要】压力容器无损检测技术的选择及应用对于确保压力容器在运行过程中的安全性至关重要。
本文从引言、常见的无损检测技术和结论三个方面展开讨论。
在文章探讨了压力容器无损检测技术的重要性以及目前的发展现状。
在分别介绍了常见的无损检测技术包括超声波检测技术、磁粉检测技术、涡流检测技术以及磁记忆检测技术,并阐述了它们在压力容器中的应用。
在强调了在选择无损检测技术时需要根据具体情况进行选择,并强调了无损检测技术在压力容器安全运行中的重要性。
文章呼吁持续关注无损检测技术的发展,以确保压力容器的安全性和稳定性。
【关键词】压力容器、无损检测技术、超声波检测、磁粉检测、涡流检测、磁记忆检测、安全运行、发展现状、重要性、实际情况。
1. 引言1.1 压力容器无损检测技术的重要性压力容器无损检测技术的重要性在现代工业生产中至关重要。
压力容器作为承载和传递压力的设备,在工业生产中扮演着至关重要的角色。
由于长期使用或者制造过程中的瑕疵可能会导致压力容器的损坏,这会给生产过程带来严重的安全隐患。
为了及时发现和解决压力容器的潜在问题,无损检测技术成为必不可少的手段。
通过无损检测技术,可以在不破坏压力容器的情况下,对其进行全面、准确的检测,及时发现裂纹、腐蚀等缺陷。
采用无损检测技术可以大大提高工作效率,避免因检测过程中对压力容器造成损害,同时也能减少生产停工时间和维修成本。
更重要的是,通过无损检测技术可以确保压力容器的安全运行,减少事故发生的概率,保障人员和设备的安全。
压力容器无损检测技术的重要性不言而喻。
只有不断完善和应用先进的无损检测技术,才能更好地保障压力容器在工业生产中的安全运行,实现高效、可持续的生产。
1.2 压力容器无损检测技术发展现状压力容器无损检测技术的发展现状主要体现在以下几个方面:首先是技术的不断更新迭代。
随着科学技术的不断进步,新的无损检测技术不断涌现,如基于人工智能的智能无损检测技术、激光检测技术等,使得检测精度和效率得到了显著提升。
压力容器无损检测技术的合理选择与应用分析

压力容器无损检测技术的合理选择与应用分析压力容器是工业中常见的重要设备之一,在各行各业中都有广泛的应用。
它们通常被用于存储或运输各种液体、气体或危险废物等。
然而,在使用过程中,由于压力容器受到内部和外部的压力影响,会出现腐蚀、裂纹、变形等问题,会给生产带来很大的危害。
因此,对压力容器实施无损检测非常重要。
无损检测是利用物理学、化学技术等对物体进行测试,检测其疵点、缺陷等隐蔽缺陷,从而实现对物体无破坏的检测。
在压力容器的无损检测中,可以采用多种技术,包括超声波、射线检测、渗透探伤等。
合理的选择无损检测技术可以有效地提高检测准确率,降低维修成本,避免生产事故的发生。
评估无损检测技术的适用性和优缺点通常基于以下几个方面:1.技术优劣评估不同的无损检测技术针对不同的缺陷有其优缺点。
例如,超声波检测可以发现内部缺陷,较适合于检测腐蚀、裂纹等问题,但其无法发现表面缺陷;切换检测可以检测出较大的裂纹,是检测较深的缺陷的较好选择;渗透探伤适合于表面缺陷的检测。
因此,在选择无损检测技术时,需考虑具体问题的性质,确定合适的检测技术。
2.现场使用的方便程度有些无损检测技术的操作比较复杂,参考书籍和资料都比较丰富。
有些无损检测技术的操作比较容易掌握。
这就决定了整体的现场使用的方便程度,应该在实际应用中加以考虑。
3.成本和效益针对不同类型和大小的压力容器,选择不同的无损检测技术需要耗费不同的成本。
随着技术的全面运用,现在无损检测的成本已经大大降低,这些技术的优点也得到了明显的提高。
在检测之前我们应该考虑好成本和效益,选择最合适的方案来进行。
4.其他可能的风险在选择无损检测技术时,需要考虑可能的风险,如辐射风险和电磁辐射风险等。
要认真评估固有风险,并确保对实际操作进行安全评估和规划。
在实际应用中,无损检测技术需要根据实际情况进行现场操作。
不管是哪种无损检测技术,都需要根据情况进行不同的方案。
操作人员需要具备一定的专业知识和训练,以保证检测结果的准确性和可靠性。
浅析压力容器制造中的四项常规无损检测技术

2018年06月浅析压力容器制造中的四项常规无损检测技术郭志伟(浙江巨化装备制造有限公司,浙江衢州324004)摘要:近年来,现代工业发展迅速,压力容器的应用与发展也越来越快,压力容器的安全问题也越加受到社会重视。
而在保障压力容器的安全上无损检测技术的运用至关重要。
本文简单介绍压力容器制造中的四项常规无损检测技术。
关键词:压力容器;无损检测;射线检测在压力容器的制造过程中,企业对于压力容器的质量保障有一套完善的质保体系,其中有着各项检验工序,如:焊接工艺评定、焊接试件的理化检验、外观检验、无损检测、耐压试验等。
其中无损检测是非常重要的一环。
在压力容器制造过程中无损检测的对象主要是焊接接头,执行的检测标准NB/T47013-2015。
1无损检测方法概述无损检测能够在不破坏被检工件的前提下,检测出工件内的缺陷。
四种常规无损检测技术:射线检测、超声检测、磁粉检测、渗透检测。
1.1射线检测射线在穿透工件过程中与物质发生作用,使穿透工件的射线强度减弱,减弱程度与物质的衰减系数和射线穿透的物质厚度有关。
当工件中存在缺陷时,构成缺陷的物质不同于工件基本物质,其衰减系数也不同,因此穿过工件缺陷部位和完好基体后的射线强度也会不同,从而使放在工件后面胶片的感光程度不同。
胶片经处理后,这种感光程度差异会在底片上呈现出不同黑度的影像,依据底片上的影像可以判别工件中缺陷,并对缺陷准确定性、定量。
优点:底片上能显示缺陷的直观图像,并可以长期保存;能够准确的对缺陷的定性、定量、定位;对诸如气孔、夹渣等体积型缺陷检出率高。
缺点:对裂纹、末熔合等面积型缺陷的检出率受透照角度影响;射线检测的成本较高,检测速度较慢;射线对人体危害较大,检测时必须采取安全防护措施。
1.2超声检测超声检测通过检测仪器激发探头发射超声波进入工件,超声波在工件缺陷处或工件表面发生反射现象,探头接收到反射波转换成电信号,电信号经过仪器的信号处理后显示出来,通过分析反射声波的波幅和位置等信息,判别缺陷的存在,并对缺陷定位。
压力容器无损检测技术的选择及应用浅析
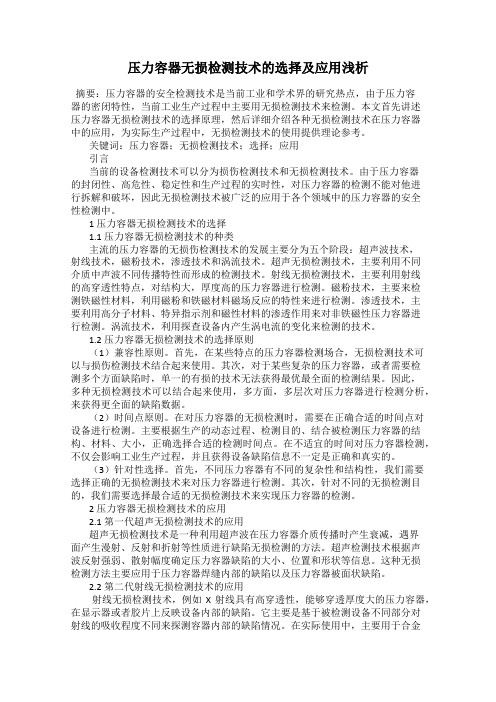
压力容器无损检测技术的选择及应用浅析摘要:压力容器的安全检测技术是当前工业和学术界的研究热点,由于压力容器的密闭特性,当前工业生产过程中主要用无损检测技术来检测。
本文首先讲述压力容器无损检测技术的选择原理,然后详细介绍各种无损检测技术在压力容器中的应用,为实际生产过程中,无损检测技术的使用提供理论参考。
关键词:压力容器;无损检测技术;选择;应用引言当前的设备检测技术可以分为损伤检测技术和无损检测技术。
由于压力容器的封闭性、高危性、稳定性和生产过程的实时性,对压力容器的检测不能对他进行拆解和破坏,因此无损检测技术被广泛的应用于各个领域中的压力容器的安全性检测中。
1 压力容器无损检测技术的选择1.1 压力容器无损检测技术的种类主流的压力容器的无损伤检测技术的发展主要分为五个阶段:超声波技术,射线技术,磁粉技术,渗透技术和涡流技术。
超声无损检测技术,主要利用不同介质中声波不同传播特性而形成的检测技术。
射线无损检测技术,主要利用射线的高穿透性特点,对结构大,厚度高的压力容器进行检测。
磁粉技术,主要来检测铁磁性材料,利用磁粉和铁磁材料磁场反应的特性来进行检测。
渗透技术,主要利用高分子材料、特异指示剂和磁性材料的渗透作用来对非铁磁性压力容器进行检测。
涡流技术,利用探查设备内产生涡电流的变化来检测的技术。
1.2 压力容器无损检测技术的选择原则(1)兼容性原则。
首先,在某些特点的压力容器检测场合,无损检测技术可以与损伤检测技术结合起来使用。
其次,对于某些复杂的压力容器,或者需要检测多个方面缺陷时,单一的有损的技术无法获得最优最全面的检测结果。
因此,多种无损检测技术可以结合起来使用,多方面,多层次对压力容器进行检测分析,来获得更全面的缺陷数据。
(2)时间点原则。
在对压力容器的无损检测时,需要在正确合适的时间点对设备进行检测。
主要根据生产的动态过程、检测目的、结合被检测压力容器的结构、材料、大小,正确选择合适的检测时间点。
压力容器无损检测技术的选择及应用
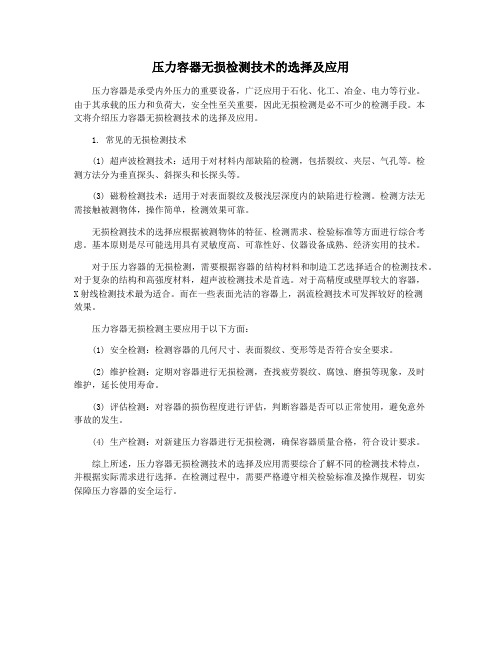
压力容器无损检测技术的选择及应用压力容器是承受内外压力的重要设备,广泛应用于石化、化工、冶金、电力等行业。
由于其承载的压力和负荷大,安全性至关重要,因此无损检测是必不可少的检测手段。
本文将介绍压力容器无损检测技术的选择及应用。
1. 常见的无损检测技术(1) 超声波检测技术:适用于对材料内部缺陷的检测,包括裂纹、夹层、气孔等。
检测方法分为垂直探头、斜探头和长探头等。
(3) 磁粉检测技术:适用于对表面裂纹及极浅层深度内的缺陷进行检测。
检测方法无需接触被测物体,操作简单,检测效果可靠。
无损检测技术的选择应根据被测物体的特征、检测需求、检验标准等方面进行综合考虑。
基本原则是尽可能选用具有灵敏度高、可靠性好、仪器设备成熟、经济实用的技术。
对于压力容器的无损检测,需要根据容器的结构材料和制造工艺选择适合的检测技术。
对于复杂的结构和高强度材料,超声波检测技术是首选。
对于高精度或壁厚较大的容器,X射线检测技术最为适合。
而在一些表面光洁的容器上,涡流检测技术可发挥较好的检测效果。
压力容器无损检测主要应用于以下方面:(1) 安全检测:检测容器的几何尺寸、表面裂纹、变形等是否符合安全要求。
(2) 维护检测:定期对容器进行无损检测,查找疲劳裂纹、腐蚀、磨损等现象,及时维护,延长使用寿命。
(3) 评估检测:对容器的损伤程度进行评估,判断容器是否可以正常使用,避免意外事故的发生。
(4) 生产检测:对新建压力容器进行无损检测,确保容器质量合格,符合设计要求。
综上所述,压力容器无损检测技术的选择及应用需要综合了解不同的检测技术特点,并根据实际需求进行选择。
在检测过程中,需要严格遵守相关检验标准及操作规程,切实保障压力容器的安全运行。
浅谈压力容器无损检测技术的选择

浅谈压力容器无损检测技术的选择摘要:随着时代的发展、科学技术的进步.对产品的安全状况和产品质量以及使用的性能都提出了越来越高的要求,由于无损检测技术自身的优越性,在压力容器产品制造和使用中得到广泛应用。
关键词:压力容器;无损检测;应用一、无损检测的特点.1.1无损检测主要是指在不对检测构件造成任何损伤的前提下,运用声、光、电、磁等特性,且借助先进的技术和设备器材,对检测构件的内部以及表面的结构性质状态等进行检查和测试,从而查明构建表面和内部的实际状况。
1.2现阶段常用的无损检测方法包括射线检测法、超声波检测法、磁粉检测法、渗透检测法、涡流检测法以及声发射法等,其中射线检测法和超声波检测法是应用最为广泛的无损检测法。
射线检测法主要工作原理是利用X射线或者Y射线穿透被检测构件使胶片感光,如果检测构件内存在缺陷,该部位的射线衰减情况与正常区域会有明显的差异,作用于感光胶片各处的射线能量也会相应地表现出明显的强弱差异,所以通过底片就可以直接判断被检测构件存在缺陷的具体部位。
1.3超声波检测法主要是通过声波的反射透射以及散射作用,对被检测构件进行几何特性测量缺陷检测以及力学性能变化检测等。
射线检测法可以获得缺陷的直观图像,定性准确,并且对长度宽度尺寸的定量也比较准确,射线检测结果能够进行现场记录,便于长期保存。
此外,射线检测法还具有较强的重复性,对一些体积状缺陷或者一些与照射方向平行的缺陷有非常明显的检测效果。
1.4超声波检测法适用于金属非金属和复合材料等多种制件的无损检测,穿透能力强,对缺陷的定位准确,并且还可以对厚度较大的试件内部的缺陷进行检测。
此外,超声波检测法操作简单成本低检测速度快,对人体以及环境不会造成危害。
射线检测与超声波检测的性能比较如表1所示:表1射线检测与超声波检测的性能比较二、无损检测技术检验压力容器前的准备工作.(1)现场勘察,找出所有可能出现的噪声源,如电磁干扰、振动、摩擦和流体流动等。
- 1、下载文档前请自行甄别文档内容的完整性,平台不提供额外的编辑、内容补充、找答案等附加服务。
- 2、"仅部分预览"的文档,不可在线预览部分如存在完整性等问题,可反馈申请退款(可完整预览的文档不适用该条件!)。
- 3、如文档侵犯您的权益,请联系客服反馈,我们会尽快为您处理(人工客服工作时间:9:00-18:30)。
5、浅谈四项常规无损检测在压力容器制造中的选用浅谈四项常规无损检测在压力容器制造中的选用童天海(安徽六方深冷股份合肥230088)摘要结合新版JB/T4730-2005《承压设备无损检测》,对压力容器产品制造过程中焊缝无损检测需要注意的几个方面进行总结,以引起同行们的注意。
关键词无损检测 UT超声检测 RT射线检测 PT渗透检测 MT磁粉检测1 前言压力容器是一种可能引起爆炸或中毒等危害性较大事故的特种设备,一旦发生爆炸或泄漏,往往并发火灾、中毒、污染环境等灾难性事故,所以压力容器比一般机械设备有更高的安全要求。
无损检测是压力容器安全管理的重要环节。
目的就是防止压力容器发生失效事故,特别是预防危害最严重的破裂事故发生。
因此,压力容器检验的实质就是失效的预测和预防。
现代无损检测的定义是:在不损坏试件的前提下,以物理或化学方法为手段,借助先进的技术和设备器材,2.1.3面状缺陷受方向影响检出率低。
2.1.4不能提供缺陷的深度信息。
2.1.5需接近被检物体的两面。
2.1.6检测周期长,结果反馈慢。
设备较超声笨重,成本高。
X射线与γ射线的一般特性:X射线和γ射线一样,是一种高能电磁辐射,有较强的穿透能力,且只有通过与物质相互作用,才能使物质间接地产生电离效应。
X射线和γ射线的不同之处在于: = 1 \* GB3 ①其能量低于γ射线; = 2 \* GB3 ②产生的机制不同,γ射线由放射性核素自发衰变释放出,而X射线通常是由高速电子轰击金属钯产生的。
且X射线电磁波,具有光波的一切特性(如反射、折射、干涉等),波长极短(0.001nm到1nm)2.2超声检测局限性:2.2.1由于操作者操作误差导致检测结果的差异。
2.2.2对操作者的主观因素(能力、经验、状态)要求很高。
2.2.3定性困难。
2.2.4无直接见证记录(有些自动化扫查装置可作永久性记录)。
2.2.5对小的(但有可能超标的缺陷)不连续性重复检测结果的可能性小。
2.2.6对粗糙、形状不规则、小而薄及不均质的零件难以检查。
2.2.7需使用耦合剂使波能量在换能器和被检工件之间有效传播。
超声波的一般特性:超声波是机械波(光和X射线是电磁波)。
超声波基本上具有与可闻声波相同的性质。
它们能在固态、液态或气态的弹性介质中传播。
但不能在真空中传播。
在很多方面,一束超声波类似一束光。
向光束一样,超声波可以从表面被反射;当其穿过两种声速不同物质的边界时可被折射(实施横波检测基理);在边缘处或在障碍物周围可被衍射(裂纹测高;端点衍射法基理)。
常规超声波检测不存在对人体的危害,它能提供缺陷的深度信息和检出射线照相容易疏漏的垂直于射线入射方向的面积型缺陷。
能即时出结果;与射线检测互补。
焊缝内部质量一般用射线来检测。
但对于厚壁容器或焊缝中的裂纹、未熔合等危险性缺陷,超声检测方法优于射线检测。
JB 4730 修订版对母材厚度为8~300mm 的全焊透熔化焊对接焊缝的超声检测进行了明确规定。
并指出应检测到整条焊缝、熔合线和热影响区。
而过去人们认为,对焊缝的超声检测只是检测焊缝。
3 对焊缝表面及近表面的无损检测磁粉探伤和渗透探伤是对焊缝表面及近表面进行无损检测的主要方法。
对于焊缝表面中的气孔、裂纹等危害性缺陷,磁粉比渗透有更高的检出缺陷灵敏度。
随着现代科技快速发展,技术进步。
磁粉探伤机类型增加,使得磁粉检测工艺可以更加完善,检测技术更为成熟。
但众所周知:磁粉探伤只针对铁磁性材料且非荧光性磁粉对工作人员的视力也有较高要求;故此对磁粉波检测人员的素质要求高。
而渗透检测适用于非多孔性材料,它适用范围广,但检测灵敏度较低对焊缝表面质量要求也很高。
所以检测人员不仅要具备熟练的表面检测探伤技术,还应了解有关的焊缝材料材质、表面检验及可能产生缺陷的情况;如焊缝表面尽量打磨光亮及管座式C、D类焊缝圆滑过渡等。
针对不同的检测对象制定相应的探伤工艺,选用合适的探伤方法,从而获得正确的检测结果。
3.1磁粉检测的局限性3.1.1.不能检测非铁磁性材料;3.1.2不能检测较深的缺陷,只适用于检测表面及近表面缺陷;3.1.3. 对检测环境光照对比度有要求;3.1.4.用直接通电法和触头法时,易产生电弧烧伤工件;3.1.5.对被检测物体表面光洁度有一定要求;3.1.6. 与工件表面几乎平行的分层不易发现。
磁粉检测的特性:是缺陷处漏磁场与磁粉的磁相互作用,即铁磁性材料或工件磁化后,探伤机在表面和近表面如有不连续性存在,则在不连续性处磁力线离开工件和进人工件表面发生局部畸变产生磁极,并形成可检测的漏磁场,它吸附施加在工件表面的磁粉,形成在合适光照下目视可见的磁痕,从而显示出不连续性的位置、形状和大小。
3.2渗透检测的局限性3.2.1.不能检测多孔性材料;3.2.2.不能检测较深的缺陷,只适用于检测表面开口缺陷;3.2.3. 渗透剂有毒且易燃易爆;3.2.4. 检测程序繁琐,速度慢,试剂成本较高;3.2.5. 对被检测物体表面光洁度有一定要求;3.2.6. 灵敏度低于磁粉检测,对于埋藏缺陷或闭合性表面缺陷无法测出渗透检测特性:是利用液体的毛细管作用,将渗透液渗入固体材料表面开口缺陷处。
再通过显像剂将渗入的渗透液析出到表面显示缺陷的存在。
4 制造检验中四项常规无损检测是相辅相成的现在无损检测探伤中超声检测与射线检测是对产品质量把关不可忽视的一个重要环节,但焊缝表面检测也至关重要,所以在制造生产过程中对无损检测的工艺选取就显得尤为重要了。
实际工作中因考虑多方因素选取最适合的探伤方法。
1、例我公司在2010年制造一台甲醇合成反应器外壳,本台设备是台多层产品,筒体及封头选用的材料都是15CrMo。
因为设计产品的时候是5月份,天气正热,所以图纸设计未考虑到特殊材料焊前要加热焊后要保温冷却这一重要的环节,造成了本台产品后期检验中出现很多缺陷问题,以下仅对无损检测方法选用:A.本台产品钢板15CrMo因为板厚200mm,由于钢板厚度过大一种检测手段无法保证产品检测准确性,为了确保后期检测结果准确,结合JB/T4730-2005,UT与RT检测互相结合且根据规定采用焊后24小时进行检测,因板厚超出Co60最大透照范围,故采用两次焊接分开探伤:①首先由焊工在外焊至140mm的厚度(因我公司Co60机子并非新机子,透照厚度为140mm 左右),进行RT探伤对外层焊缝的焊接质量进行检测同时进行UT可记录探伤⑴因为RT检测需要时间较长,先UT检测先检测出结果,在UT探伤机上只能反映出2处较大长度的缺陷⑵再用Co60(钴)进过4个小时的拍片,经过暗室处理,底片出来后发现有很多细小黑,反而UT检出的两处缺陷在射线底片上反映不太明显,不太明显的不规则灰雾度。
⑶经过焊工返修细小黑丝全部是由于焊接前未加热及焊后未保温冷却从而引起的冷裂纹,而超声做出的两处缺陷是清根不干净造成的夹渣。
从射线底片和超声记录进行对比,射线对体积形式的缺陷检测敏感度比超声更高,而对于夹渣、气孔等面积形式的缺陷超声检测比射线更灵敏。
B.本台产品封头与人孔接管对接焊缝,检测工艺根据JB/T4730-2005标准规定采用超声检测和磁粉检测对接管角焊缝内外表面进行检验且满足焊后24小时在实际操作中由于公司为了提高生产效率焊后未保温冷却24小时,焊后一段时间就进行检测,当时检测结果未出现有表面裂纹等缺陷显示,因为是产品最后环节,所以由焊工检查员等交验完毕后整体进行热处理,后进行水压试验,试压结果发现接管表面出现延伸裂纹,产生裂纹的原因很多但在无损检测环节没有发现缺陷的原因只有探伤作业人员的素质水平和未按要求在施焊后24小时候再进行无损检测。
2、例我公司在2012年制造一台水冷却器,因换热管材质20,属于铁磁性材料,设计及检测工艺则要求换热管与管板焊接接头采用磁粉检测检测方法。
在实际探伤过程中,因为换热管直径很小,管板上的焊接接头相当多,造成焊后表面清理相当困难,为了提高生产效率,经制造方、设计部门及容器使用单位一致决定,将MT改成PT检测。
渗透检测相对于磁粉检测表面要求的光洁度等不高,且产生缺陷对比度很清晰,用渗透检测检测出,少量的气孔和很小的表面裂纹,经打磨完成后,进行管程水压试验,再慢慢的提压过程中发现焊缝有渗水,为了找出缺陷,又进行一遍PT检测,但检测结果未发现问题。
最后采用MT检测,发现管板与换热管最外层有裂纹产生。
分析可能是表面有油渍等造成了闭口形的缺陷,是PT检测的灵敏度降低,MT检测缺陷灵敏度高于PT,但是对焊缝检测环境要求太高,而后多次产品出现同样的PT缺陷未检出,发现铁磁性材料优先采用MT检测。
在各种焊缝检测过程中,由于环境及其材质等影响,为了使检测结果能更全面对产品负责,无损检测人员应该在工作实践中总结经验,并采用多种探伤方法全面控制产品质量。
5 制造检验中错判的缺陷及可能产生的原因现场无损检测探伤中现场环境及仪器错误显示、人员操作不当等都可能产生伪缺陷。
以下举几个在实际工作发现的供同行参考。
5.1在射线探伤中,条形缺陷和未融合、未焊透等不容易区分,例我公司生产的低温罐,外筒体对接终接焊缝(焊缝结构如下图),材质都为Q245R,因为焊接方式是采用在外侧单面焊接内表面加垫板防止烧穿等,公司一直采用100%RT射线检测一次性周向曝光为了提高效率,连续一半的底片上出现焊缝一边有断断续续的缺陷显示。
图1焊缝结构图5.1.1底片显示,因板厚为24mm,Ⅱ级合格,若按条形缺陷评判,单个缺陷长度测量不超过3mm,由JB/T4730.2-2005标准≤T/3且≤20mm,且不超过6L相邻间距条形缺陷累计长度不超过T(T为板厚,L为其中最大缺陷长度),因此不需要返修处理。
5.1.2对于无法准确判定是否属于危害性较大的缺陷,我们探伤人员和责任工程师经过商议,返修最多缺陷的一张片子,现场发现底部垫板与筒体处因为小量的错边,底部空隙不紧密,造成中间有大量的未熔合和夹渣。
5.1.3场观察发现,垫板焊缝底片中,若类似不规则但在焊缝边缘附近且在一直线上,再根据现场观察是否有错边现象,也可根据焊工的施焊电流和焊速等多方面判断上述缺陷定性为未熔合。
5.2在厚板及厚管环缝超声波探伤时,常发现检测背面3—8mm深度范围内的熔合线附近有不同长度连续的超标反射回波,有时甚至在焊缝长度都会有此反射波,以我单位60mm的厚管节为例,其焊缝结构如图。
使用这叫K2的探头和数字式增益型探伤仪,其回波指示位置见表,且波幅均在DAC曲线Ⅱ区,甚至会超过Ⅲ区。
对于这样的反射波,最基本的判断就是未熔合或是母材缺陷,当在探测对立面用手沾点水放在焊缝处,波形就会有明显变化。
图2超声波探伤回波位置表1 回波位置回波编号声程指示水平指示深度指示1 107.0 92.6 53.52 104.0 89.2 51.53 103.5 89.2 51.5经过现场砂轮打磨检测对立面焊缝,波幅会逐渐降至甚至消失。