表面光洁度与表面粗糙度对照表
表面粗糙度与表面光洁度级别对照表完整

表面粗糙度与表面光洁度级别对照表(可以直接使用,可编辑实用优秀文档,欢迎下载)表面粗糙度与表面光洁度级别对照表表面粗糙度与光洁度对照表•轮廓的平均算术偏差(R a):通过零件的表面轮廓作一中线m,将一定长度的轮廓分成两部分,使中线两侧轮廓线与中线之间所包含的面积相等,•不平度平均高度(Rz):就是在基本测量长度范围内,从平行于中线的任意线起,自被测轮廓上五个最高点至五个最低点的平均距离,•轮廓最大高度Ry:就是在取样长度内,轮廓峰顶线和轮廓谷底线之间的距离。
•轮廓的平均算术偏差(R a):通过零件的表面轮廓作一中线m,将一定长度的轮廓分成两部分,使中线两侧轮廓线与中线之间所包含的面积相等,•不平度平均高度(Rz):就是在基本测量长度范围内,从平行于中线的任意线起,自被测轮廓上五个最高点至五个最低点的平均距离,•轮廓最大高度Ry:就是在取样长度内,轮廓峰顶线和轮廓谷底线之间的距离。
表面粗糙在不同的加工方法中的参考应用详细资料表面粗糙度对照表一.表面粗糙度的符号注意:极限值表示参数的实测值中允许少于总数的16%的实测值超过规定值,高度参数常用Ra,在图中标注时常省略。
无max min则表示是上极限或下极限,如果有则表示最大值和最小值,单位为微米基本符号,表示可使用任何方法获得基本符号加一短划,表示表面用去除材料的方法获得表示用不去除材料方法获得(铸锻冲压等)表示所有表面具有相同的表面粗糙度要求二.表面粗糙度的代号1.d' =h/10;H=1.4h;h为字体高度a1、a2--粗糙度高度参数的允许值(mm);b加工方法、镀涂或其他表面处理;c取样长度(mm);d加工纹理方向符号;e加工余量(mm);f粗糙度间距参数值(mm)或轮廊支承长度率。
2.零件的加工表面的粗糙度要求由指定的加工方法获得,用文字标注在符号上边的横线,加工方法也可在图样的技术要求中说明3.加工纹理方向:= 纹理平行于标注符号的视图的投影面⊥纹理垂直于标注符号的视图的投影面x 纹理呈两相交的方向M 纹理呈多方向c 纹理呈近似同心圆R 纹理呈近似的放射状p 纹理无方向或凸起的细粒状4.加工余量:注在符号的左侧,标注时数值要加上括号,单位为毫米5.参数S Sm Tp l的标注,应标注在符号长边的横线下面,并且必须在参数值前注写参数的符号三。
(完整word版)光洁度与粗糙度Ra、Rz数值对照换算表

光洁度与粗糙度Ra、Rz数值对照换算表(单位:μm)另附:表面粗糙度国际标准表面粗糙度的表示法从量测仪器上,我们多可获得工件表面不规则状况的放大结果,而此一结果常被称为”表面轮廓图"(surface profile)。
当仪器的尖笔正沿着工件表面进行扫描时,其垂直方向的运动乃可被放大而被绘制下来,且在同时,我们亦可直接自仪器上读出在该处工件表面上的表面粗度算术平均值究竟为多少。
在1930年以前,这完全是要凭触觉来建立标准.检验时必须使用一系列具有不同粗度的试片,工厂人员在使用这些试片时,先用他的手指甲划过标准的试片表面,然后再划过他制造出来之工件的表面,当感觉这两个表面具有相同的粗度时,则工件表面便被认为足够光滑了。
在表面密封、滚珠轴承、齿轮、凸轮或轴颈等应用场合,表面光度对于设备的功能能否发挥影响很大,有人发现,设备的性能与对数的表面光度值成线性的变化关系。
也就是说,要使性能提高一倍时,平均的波峰到波谷的粗度值必须减低十倍。
于是乎,对表面粗糙度量化的要求也就产生了.图 1 表面轮廓包含了粗糙度曲线与波浪起伏的曲线表面轮廓断面曲线中,包含了粗糙度曲线与波浪起伏的曲线(图 1),一般说来波浪起伏的曲线是属于轮廓量测的范围,其值远大于表面粗糙度之值(有关轮廓量测请参阅第六章),但也有将表面轮廓断面两种曲线分开或合并考虑的作法,因此也就有了各种表面粗糙度之定义,如表 1。
尽管各种表面粗糙度之定义有那么多,一般表面粗糙度之表示法只有下列三种:Ra(中心线平均粗糙度)、Rymax(最大高度粗糙度)、Rtm (十点平均粗糙度),现分述如下:图 2 中心线平均粗糙度之测量长度L1. Ra :中心线平均粗糙度若从加工面之粗糙曲线上,截取一段测量长度L(图 2) ,并以该长度内粗糙深之中心线为x轴,取中心线之垂直线为y轴,则粗糙曲线可用y = f(x)表之。
以中心线为基准将下方曲线反折.然后计算中心线上方经反折后之全部曲线所涵盖面积, 再以测量长度除之.所得数值以μm为单位,即为该加工面测量长度范围内之中心线平均粗糙度值,其数学定义为:中心线方向细分单位等间隔后取各分段点所对应之 hi 值,利用下式可得到 Ra的近似: (图 3)图 3 测量长度范围内之中心线平均粗糙度值Ra的近似中心线在表面具有曲度或形状误差时,则成曲线,粗糙度沿此曲线量取. 测量长度限于量具大小而无法涵盖整个机件表面,因此,一次量取求得之Ra 只是表面某部分的中心线平均粗糙度,故应在被测物表面多选几个不同的位置测量,将全部测得之Ra取其算术平均值则为表面的中心线平均粗糙度。
光洁度与粗糙度Ra、Rz数值对照换算表单位μm

光洁度与粗糙度Ra、Rz数值对照换算表(单位:μm)另附:表面粗糙度国际标准表面光洁度等级与表面粗糙度高度参数推荐转换表表面光洁度等级与表面粗糙度高度参数推荐转换表(一)表面光洁度(GB1031-68)级别代号 Ra Rz ▽ 1>40 ∽80 um> 160 ∽320 um▽ 2>20 ∽40 um> 80 ∽160 um▽ 3 >10 ∽20 um> 40 ∽80 um▽ 4>5 ∽10 um > 20 ∽40 um▽ 5>2.5 ∽5 um> 10 ∽20 um▽ 6>1.25 ∽2.5 um> 6.3 ∽10 um▽ 7>0.63 ∽1.25 um> 3.2 ∽6.3 um▽ 8>0.32 ∽0.63 um> 1.6∽3.2 um▽ 9>0.16 ∽0.32 um> 0.8 ∽1.6 um▽ 10>0.08 ∽0.16 um> 0.4 ∽0.8 um▽ 11>0.04 ∽0.08 um> 0.2 ∽0.4 um▽ 12>0.02 ∽0.04 um> 0.1 ∽0.2 u m▽ 13>0.01 ∽0.02 um> 0.05 ∽0.1 um▽ 14≤0.01 um≤0.05 um表面光洁度等级与表面粗糙度高度参数推荐转换表(二)表面粗糙度(GB1031-83)级别代号Ra RzⅠⅡⅢ▽1 50um 100um 80um 32 0um▽2 25um 50um 40um 1 60um▽3 12.5um 25um 20um 8 0um▽4 6.3um 12.5um 10um40um▽5 3.2um 6.3um 5um20um▽6 1.60um 3.2um 2.5um 1 0um▽7 0.80um 1.60um 1.25um 6.3 um▽8 0.40um 0.80um 0.63um 3.2 um▽ 9 0.20um 0.40um 0.32um 1.60um▽10 0.100um 0.20um 0.16um 0.80um▽11 0.050um 0.100um 0.08um 0.40um▽12 0.025um 0.050um 0.04um0.20um▽13 0.012um 0.025um 0.02um 0.100um▽14 0.012um 0.01um 0.050um轮廓算术平均偏差Ra ——在取样长度l内,轮廓偏距绝对值的算术平均值。
光洁度与粗糙度Ra_Rz数值对照换算表.

光洁度与粗糙度Ra、Rz数值对照换算表(单位:μm)
表面光洁度 表面 Ra 粗糙度 Rz 表面光洁度 表面 Ra 粗糙度 Rz
▽1 50 200 ▽8 0.40 3.2
▽2 25 100 ▽9 0.20 1.60
▽3 12.5 50 ▽10 0.100 0.80
▽4 6.3 25 ▽11 0.050 0.40
▽5 3.2 12.5 ▽12 0.025 0.20
▽6 1.60 6.3 ▽13 0.012 0.100
▽7 0.80 6.3 ▽14
0.050
另附:表面粗糙度国际标准
标准等 ห้องสมุดไป่ตู้代号
SPI(A1)
表面粗 糙度
Ra0.005
加工工具(方 法) 粗精钻 研研石 磨磨膏 砂砂抛 粒粒光 粒粒 度度
SPI(A2) Ra0.01
加工材料及硬度要求
S136 8407 DF-2 XW-10
54HRC 52HRC 58HRC 60HRC
光度描述
光洁度非常高,镜 面效果 光洁度较低,没有 砂纸纹
SPI(A3) Ra0.02 SPI(B1) Ra0.05 SPI(B2) Ra0.1 SPI(B3) Ra0.2
S136
300HB
718SUPREME 300HB
Ra0.4
Ra0.8
Ra1.6 Ra3.2 Ra6.3 Ra12.5 Ra25 Ra50
精加工:精车 \精刨\精 铣\磨\铰 \刮 精加工:精车 \精刨\精 铣\磨\铰 \刮
光洁度更低一级, 但没有砂纸纹
没有光亮度,有轻 微 3000#砂纸纹 没有光亮度,有轻 微 2000#砂纸纹 没有光亮度,有轻 微 1000#砂纸纹 不辨加工痕迹的方 向 微辨加工痕迹的方 向
表面粗糙度与光洁度对照表

参考资料1、外表粗糙度与光洁度对照表2、国内外表光洁度与粗糙度数值换算表3、外表粗糙度国际标准加工方法4、外表粗精度代号标注例如5、外表粗植度在图样上的注法6、外表粗糙在不同的抽工方法中的参考应用外表粗糙度与光洁度对照表中美表面粗糙度对照表中国旧标中国新标美国标美国标准(光洁准(粗糙准(微准(微英度)度)Ka氷)Ra J, Ra8.00320V 4 6.36.302505.002QQ v 5 3.2 4.001603.201252.50100V 6 1.6 2.00801.60631.2550▽70.8 1.00400.80 320.6325V 80.40.50200.4016・轮廓的平均算术偏差(RJ :通过零件的外表轮廓作一屮线m ,将一定长度的轮廓分成两局部,使屮线两侧轮廓线与屮线之间所包含的面积相等,・不平度平均高度(Rz):就是在根本测量长度范围内,从平行于中线的任意线起,自被测轮廓上五个最高点至五个最低点的平均距离,轮廓最大高度Ry:就是在取样长度内,轮廓峰顶线和轮廓谷底线Z间的距离。
表9-2表面租糙度高度参数匚值的代号标注示例2,表面粗糙度代号祈注GB/T 131— 1993规定了表面袒糙度的符号、代号及苴注法。
表両粗維度符号(、、)上注写所要求的表面特・轮廓的平均算术偏差(RJ :通过零件的外表轮廓作一中线m,将一定长度的轮廓分成两局部,使屮线两侧轮廓线与屮线之间所包含的面积相等,•不平度平均高度(Rz):就是在根本测量长度范围内,从平行于屮线的任意线起,自被测轮廓上五个最高点至五个最低点的平均距离,・轮廓最大高度Ry:就是在取样长度内,轮廓峰顶线和轮廓谷底线Z间的距离。
国例说明 图例 说明 代号中数字 的方向必须与尺 寸数字的方向一 致 对其中使用 爰劣的一种代 (符)号可以统 一标注32/V M8xl-6h蛭统的表面 粗糙度当零件所有 表面具有相同的 粗譴度时••且代 (符)号零件上连续 表面及重复宴素 (孔"用细实线相连 不连表—3表面組糙度在图样上的注法各倾斜卷面 代外表粗糙在不同的加工方法中的参考应用详细资料。
表面光洁度与粗糙度对照表
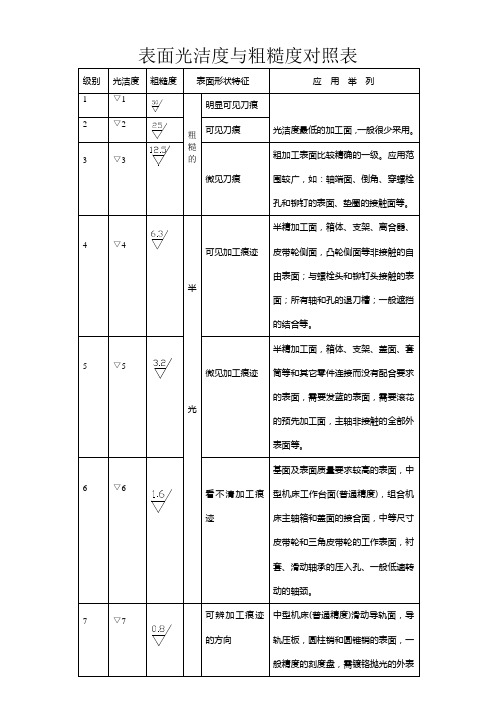
1
▽1
粗
糙
的
明显可见刀痕
光洁度最低的加工面,一般很少采用。
2
▽2
可见刀痕
3
▽3
微见刀痕
粗加工表面比较精确的一级。应用范围较广,如:轴端面、倒角、穿螺栓孔和铆钉的表面、垫圈的接触面等。
4
▽4
半
光
可见加工痕迹
半精加工面,箱体、支架、离合器、皮带轮侧面,凸轮侧面等非接触的自由表面;与螺栓头和铆钉头接触的表面;所有轴和孔的退刀槽;一般遮挡的结合等。
7
▽7
光
可辨加工痕迹的方向
中型机床(普通精度)滑动导轨面,导轨压板,圆柱销和圆锥销的表面,一般精度的刻度盘,需镀铬抛光的外表面,中速转动的轴颈,定位销压入孔。
8
▽8
微辨加工痕迹的方向
中型机床(提高精度)滑动导轨面,滑动轴承轴瓦的工作表面,夹具定位元件和转套的主要表面;曲轴和凸轮轴的工作轴颈;高速工作下的轴颈及衬套的工作面等。
基本符号上加一小圆,表示表面粗糙度是用不去除材料的方法获得,例如:铸、鍛、冲压变形、热轧、冷轧、粉末冶金等。
或者是用于保持原供应状况的表面(包括保持上道工序的状况)
表面粗糙度高度参数Ra值的标注
符号
意义
用任何方法获得的表面.Ra的最大允许值为3.2微米
用去除材料方法获得的表面.Ra的最大允许值为3.2微米
5
▽5
微见加工痕迹
半精加工面,箱体、支架、盖面、套筒等和其它零件连接而没有配合要求的表面,需要发蓝的表面,需要滚花的预先加工面,主轴非接触的全部外表面等。
6
▽6
看不清加工痕迹
基面及表面质量要求较高的表面,中型机床工作台面(普通精度),组合机床主轴箱和盖面的接合面,中等尺寸皮带轮和三角皮带轮的工作表面,衬套、滑动轴承的压入孔、一般低速转动的轴颈。
表面光洁度与表面粗糙度对照表

0.08~0.16
0.1
0.2
0.16
表面状况=暗光泽面
加工方法=超级加工
应用举例=工作时承受较大变应力作用的重要零件的表面。保证精确定心的锥体表面。液压传动用的孔表面。汽缸套的内表面,活塞销的外表面,仪器导轨面,阀的工作面。尺寸小于120mm的IT10~IT12级孔和轴用量规测量面等
▽11
0.004~0.08
1.25
表面状况=可辨加工痕迹的方向
加工方法=车、镗、拉、磨、立铣、刮3~10点/cm^2、滚压
应用举例=要求保证定心及配合特性的表面,如锥销与圆柱销的表面,与G级精度滚动轴承相配合的轴径和外壳孔,中速转动的轴径,直径超过80mm的E、D级滚动轴承配合的轴径及外壳孔,内、外花键的定心内径,外花键键侧及定心外径,过盈配合IT7级的孔(H7),间隙配合IT8~IT9级的孔(H8,H9),磨削的齿轮表面等
▽8
0.32~0.63
0.4
0.8
0.63
表面状况=微辨加工痕迹的方向
加工方法=铰、磨、镗、拉、刮3~10点/cm^2、滚压
应用举例=要求长期保持配合性质稳定的配合表面,IT7级的轴、孔配合表面,精度较高的齿轮表面,受变应力作用的重要零件,与直径小于80mm的E、D级轴承配合的轴径表面、与橡胶密封件接触的轴的表面,尺寸大于120mm的IT13~IT16级孔和轴用量规的测量表面
应用举例=一般非结合表面,如轴的端面、倒角、齿轮及皮带轮的侧面、键槽的非工作表面,减重孔眼表面
▽4
5~10
6.3
12.5
10
表面状况=可见加工痕迹
加工方法=车、镗、刨、钻、铣、锉、磨、粗铰、铣齿
应用举例=不重要零件的配合表面,如支柱、支架、外壳、衬套、轴、盖等的端面。紧固件的自由表面,紧固件通孔的表面,内、外花键的非定心表面,不作为计量基准的齿轮顶圈圆表面等
表面光洁度与表面粗糙度对照表

~
表面状况=不可辨加工痕迹的方向
加工方法=布轮磨、磨、研磨、超级加工
应用举例=工作时受变应力作用的重要零件的表面。保证零件的疲劳强度、防腐性和耐久性,并在工作时不破坏配合性质的表面,如轴径表面、要求气密的表面和支承表面,圆锥定心表面等。IT5、IT6级配合表面、高精度齿轮的表面,与G级滚动轴承配合的轴径表面,尺寸大于315mm的IT7~IT9级级孔和轴用量规级尺寸大于120~315mm的IT10~IT12级孔和轴用量规的测量表面等
表面光洁度与表面粗糙度对照表
光洁度(旧标)
粗糙度
级别
Ra(μm)
Ra(μm)
方案1
方案2
方案3
▽1
40~80
50
100
80
▽2
20~40
25
50
40
表面状况=明显可见的刀痕
加工方法=粗车、镗、刨、钻
应用举例=粗加工后的表面,焊接前的焊缝、粗钻孔壁等
▽ 3
10~20
25
20
表面状况=可见刀痕
加工方法=粗车、刨、铣、钻
▽5
~5
5
表面状况=微见加工痕迹
加工方法=车、镗、刨、铣、刮1~2点/cm^2、拉、磨、 锉、滚压、铣齿
应用举例=和其他零件连接不形成配合的表面,如箱体、外壳、端盖等零件的端面。要求有定心及配合特性的固定支承面如定心的轴间,键和键槽的工作表面。不重要的紧固螺纹的表面。需要滚花或氧化处理的表面
▽6
~
表面状况=看不清加工痕迹
▽8
~
表面状况=微辨加工痕迹的方向
加工方法=铰、磨、镗、拉、刮3~10点/cm^2、滚压
应用举例=要求长期保持配合性质稳定的配合表面,IT7级的轴、孔配合表面,精度较高的齿轮表面,受变应力作用的重要零件,与直径小于80mm的E、D级轴承配合的轴径表面、与橡胶密封件接触的轴的表面,尺寸大于120mm的IT13~IT16级孔和轴用量规的测量表面
表面光洁度与表面粗糙度对照表
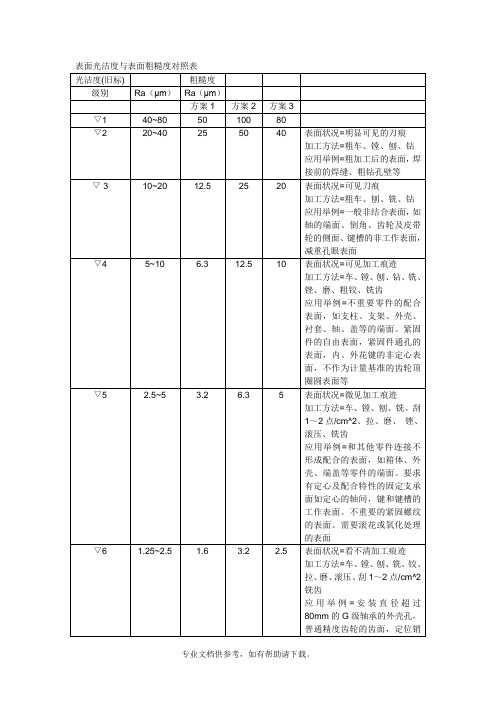
专业文档供参考,如有帮助请下载。
孔,V 型带轮的表面,外径定
心的内花键外径,轴承盖的定
中心凸肩表面
▽7
0.63~1.25 0.8
1.6
1.25 表面状况=可辨加工痕迹的方
向
加工方法=车、镗、拉、磨、立
铣、刮 3~10 点/cm^2、滚压
应用举例=要求保证定心及配
合特性的表面,如锥销与圆柱
销的表面,与 G 级精度滚动轴
面
▽9
0.16~0.32 0.2
0.4
0.32 表面状况=不可辨加工痕迹的
方向
加工方法=布轮磨、磨、研磨、
超级加工
应用举例=工作时受变应力作
用的重要零件的表面。保证零
件的疲劳强度、防腐性和耐久
性,并在工作时不破坏配合性
质的表面,如轴径表面、要求
气密的表面和支承表面,圆锥
定心表面等。IT5、IT6 级配合
专业文档供参考,如有帮助请下载。
表面、高精度齿轮的表面,与
G 级滚动轴承配合的轴径表
面,尺寸大于 315mm 的 IT7~
IT9 级级孔和轴用量规级尺寸
大于 120~315mm 的 IT10~
IT12 级孔和轴用量规的测量表
面等
▽10
0.08~0.16 0.1
0.2
0.16 表面状况=暗光泽面
加工方法=超级加工
应用举例=工作时承受较大变
应力作用的重要零件的表面。
保证精确定心的锥体表面。液
压传动用的孔表面。汽缸套的
内表面,活塞销的外表面,仪
器导轨面,阀的工作面。尺寸
小于 120mm 的 IT10~IT12 级
孔和轴用量规测量面等
▽11
光洁度与粗糙度Ra、Rz数值对照换算表

光洁度与粗糙度Ra、Rz数值对照换算表(单位:μm)另附:表面粗糙度国际标准表面粗糙度的表示法从量测仪器上,我们多可获得工件表面不规则状况的放大结果,而此一结果常被称为"表面轮廓图"(surfac e profil e)。
当仪器的尖笔正沿着工件表面进行扫描时,其垂直方向的运动乃可被放大而被绘制下来,且在同时,我们亦可直接自仪器上读出在该处工件表面上的表面粗度算术平均值究竟为多少。
在1930年以前,这完全是要凭触觉来建立标准。
检验时必须使用一系列具有不同粗度的试片,工厂人员在使用这些试片时,先用他的手指甲划过标准的试片表面,然后再划过他制造出来之工件的表面,当感觉这两个表面具有相同的粗度时,则工件表面便被认为足够光滑了。
在表面密封、滚珠轴承、齿轮、凸轮或轴颈等应用场合,表面光度对于设备的功能能否发挥影响很大,有人发现,设备的性能与对数的表面光度值成线性的变化关系。
也就是说,要使性能提高一倍时,平均的波峰到波谷的粗度值必须减低十倍。
于是乎,对表面粗糙度量化的要求也就产生了。
图 1 表面轮廓包含了粗糙度曲线与波浪起伏的曲线表面轮廓断面曲线中,包含了粗糙度曲线与波浪起伏的曲线(图 1),一般说来波浪起伏的曲线是属于轮廓量测的范围,其值远大于表面粗糙度之值(有关轮廓量测请参阅第六章),但也有将表面轮廓断面两种曲线分开或合并考虑的作法,因此也就有了各种表面粗糙度之定义,如表 1.尽管各种表面粗糙度之定义有那么多,一般表面粗糙度之表示法只有下列三种:Ra(中心线平均粗糙度)、Rymax(最大高度粗糙度)、Rtm (十点平均粗糙度),现分述如下:图 2 中心线平均粗糙度之测量长度L1. Ra :中心线平均粗糙度若从加工面之粗糙曲线上,截取一段测量长度L(图 2) ,并以该长度内粗糙深之中心线为x轴,取中心线之垂直线为y轴,则粗糙曲线可用y = f(x)表之。
表面光洁度与表面粗糙度对照表

表面光洁度与表面粗糙度对照表
Ra:轮廓算术平均偏差值
*.方案1的Ra与旧国标各等级的平均值相近,能保证产品质量,建议用于重要表面.
**.方案2的Ra比旧国标的各等级上限大25%,其经济性较好,建议用于不太重要的表面.
***.方案3的Ra与旧国标各等级上限一致,当提高产品的制造精度有困难,而降低又不能保证功能时采用.
****Ra为0.1μm时,其符号如下,余类推.
冲压模具、检具、夹具的估算报价是分析他的工艺要求,构思其结构,用料.加工和他的难度,一般的按平时的报,(模具价格=材料费+设计费+加工费与利润+增值税+试模费+包装运输费
各项比例通常为:
材料费:材料及标准件占模具总费用的15%-30%;
加工费与利润:30%-50%;
设计费:模具总费用的10%-15%;
试模:大中型模具可控制在3%以内,小型精密模具控制在5%以内; 包装运输费:可按实际计算或按3%计);有难度的加个保险系数,。
表面光洁度与表面粗糙度对照表

表面光洁度与表面粗糙度对照表表面光洁度与表面粗糙度对照表光洁度级别(旧标)粗糙度Ra(μm)1)表面状况、2)加工方法和3)应用举例▽140~80▽220~401)明显可见的刀痕2)粗车、镗、刨、钻3)粗加工后的表面,2焊接前的焊缝、粗钻孔壁等。
▽ 310~201)可见刀痕2)粗车、刨、铣、钻3)一般非结合表面,如轴的端面、倒角、齿轮及皮带轮的侧面、键槽的非工作表面,减重孔眼表面▽45~101)可见加工痕迹2)车、镗、刨、钻、铣、锉、磨、粗铰、铣齿3)不重要零件的配合表面,如支柱、支架、外壳、衬套、轴、盖等的端面。
紧固件的自由表面,紧固件通孔的表面,内、外花键的非定心表面,不作为计量基准的齿轮顶圈圆表面等▽5 2.5~51)微见加工痕迹2)车、镗、刨、铣、刮1~2点/cm^2、拉、磨、锉、滚压、铣齿3)和其他零件连接不形成配合的表面,如箱体、外壳、端盖等零件的端面。
要求有定心及配合特性的固定支承面如定心的轴间,键和键槽的工作表面。
不重要的紧固螺纹的表面。
需要滚花或氧化处理的表面▽6 1.25~2.51)看不清加工痕迹2)车、镗、刨、铣、铰、拉、磨、滚压、刮1~2点/cm^2铣齿3)安装直径超过80mm的G级轴承的外壳孔,普通精度齿轮的齿面,定位销孔,V型带轮的表面,外径定心的内花键外径,轴承盖的定中心凸肩表面▽70.63~1.251)可辨加工痕迹的方向2)车、镗、拉、磨、立铣、刮3~10点/cm^2、滚压3)要求保证定心及配合特性的表面,如锥销与圆柱销的表面,与G级精度滚动轴承相配合的轴径和外壳孔,中速转动的轴径,直径超过80mm的E、D级滚动轴承配合的轴径及外壳孔,内、外花键的定心内径,外花键键侧及定心外径,过盈配合IT7级的孔(H7),间隙配合IT8~IT9级的孔(H8,H9),磨削的齿轮表面等▽80.32~0.631)微辨加工痕迹的方向2)铰、磨、镗、拉、刮3~10点/cm^2、滚压3)要求长期保持配合性质稳定的配合表面,IT7级的轴、孔配合表面,精度较高的齿轮表面,受变应力作用的重要零件,与直径小于80mm的E、D级轴承配合的轴径表面、与橡胶密封件接触的轴的表面,尺寸大于120mm的IT13~IT16级孔和轴用量规的测量表面▽90.16~0.321)不可辨加工痕迹的方向2)布轮磨、磨、研磨、超级加工3)工作时受变应力作用的重要零件的表面。
光洁度与粗糙度Ra Rz数值对照换算表
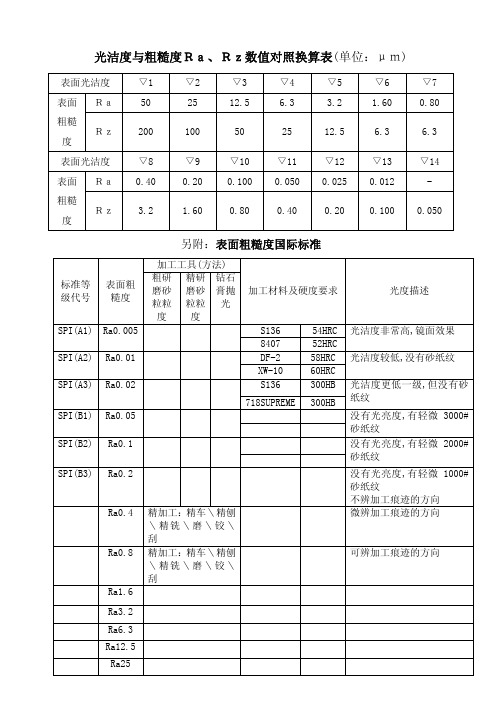
表面粗糙度的表示法
从量测仪器上,我们多可获得工件表面不规则状况的放大结果,而此一结果 常被称为"表面轮廓图 "(surface profile)。当仪器的尖笔正沿着工件表面 进行扫描时,其垂直方向的运动乃可被放大而被绘 制下来,且在同时,我们亦 可直接自仪器上读出在该处工件表面上的表面粗度算术平均值究竟为多少。 在 1930 年以前,这完全是要凭触觉来建立标准。检验时必须使用一系列 具有不同粗度的试片,工厂人员 在使用这些试片时,先用他的手指甲划过标准 的试片表面,然后再划过他制造出来之工件的表面,当感觉 这两个表面具有相 同的粗度时,则工件表面便被认为足够光滑了。在表面密封、滚珠轴承、齿 轮、凸轮 或轴颈等应用场合,表面光度对于设备的功能能否发挥影响很大,有 人发现,设备的性能与对数的表面光 度值成线性的变化关系。 也就是说,要使 性能提高一倍时,平均的波峰到波谷的粗度值必须减低十倍。于是乎,对表面 粗糙度量化 的要求也就产生了。
▽11 0.050
▽12 0.025
▽13 0.012
▽14 -
0.80
0.40
0.20 0.100 0.050
另附:表面粗糙度国际标准
标准等 表面粗 级代号 糙度
SPI(A1) Ra0.005 SPI(A2) Ra0.01 SPI(A3) Ra0.02
SPI(B1) Ra0.05
加工工具(方法) 粗研 精研 钻石 磨砂 磨砂 膏抛 粒粒 粒粒 光 度度
图 5 Rtm :十点平均粗糙度
3. Rtm :十点平均粗糙度(图 5) 由表面曲线上截取基准长度 L 做为测量长度,求出第三高波峰与第三深波谷 ,分别画出二条并行线,两并 行线间距即为十点平均粗糙度值 Rz 其值以 μm 为 单位,并在数值后加上小写字母 z 以区别另两种粗糙 度。 三种粗糙度数值间之关系约为:4 Ra ? Rymax ? Rtm
- 1、下载文档前请自行甄别文档内容的完整性,平台不提供额外的编辑、内容补充、找答案等附加服务。
- 2、"仅部分预览"的文档,不可在线预览部分如存在完整性等问题,可反馈申请退款(可完整预览的文档不适用该条件!)。
- 3、如文档侵犯您的权益,请联系客服反馈,我们会尽快为您处理(人工客服工作时间:9:00-18:30)。
2.5~5
3.2
6.3
5
表面状况=微见加工痕迹
加工方法=车、镗、刨、铣、刮1~2点/cm^2、拉、磨、锉、滚压、铣齿
应用举例=和其他零件连接不形成配合的表面,如箱体、外壳、端盖等零件的端面。要求有定心及配合特性的固定支承面如定心的轴间,键和键槽的工作表面。不重要的紧固螺纹的表面。需要滚花或氧化处理的表面
0.05
0.1
0.08
▽12
0.02~0.04
0.025
0.05
0.04
▽13
0.01~0.02
0.012
0.025
0.02
▽14
<0.01
0.006
0.012
0.01
Ra:轮廓算术平均偏差值
*.方案1的Ra与旧国标各等级的平均值相近,能保证产品质量,建议用于重要表面.
**.方案2的Ra比旧国标的各等级上限大25%,其经济性较好,建议用于不太重要的表面.
▽10
0.08~0.16
0.1
0.2
0.16
表面状况=暗光泽面
加工方法=超级加工
应用举例=工作时承受较大变应力作用的重要零件的表面。保证精确定心的锥体表面。液压传动用的孔表面。汽缸套的内表面,活塞销的外表面,仪器导轨面,阀的工作面。尺寸小于120mm的IT10~IT12级孔和轴用量规测量面等
▽11
0.004~0.08
▽8
0.32~0.63
0.4
0.8
0.63
表面状况=微辨加工痕迹的方向
加工方法=铰、磨、镗、拉、刮3~10点/cm^2、滚压
应用举例=要求长期保持配合性质稳定的配合表面,IT7级的轴、孔配合表面,精度较高的齿轮表面,受变应力作用的重要零件,与直径小于80mm的E、D级轴承配合的轴径表面、与橡胶密封件接触的轴的表面,尺寸大于120mm的IT13~IT16级孔和轴用量规的测量表面
6.3......250 ......N9..............0.1 ...... 4 ....... N3
3.2......125 ......N8..............0.05 ..... 2 ....... N2
1.6......63 .......N7..............0.025 .... 1 ....... N1
***.方案3的Ra与旧国标各等级上限一致,当提高产品的制造精度有困难,而降低又不能保证功能时采用.
****Ra为0.1μm时,其符号如下,余类推.
粗糙度数值Ra .... .粗糙度等级数....粗糙度数值Ra ....粗糙度等级数
μm(微米).μin(微英寸)..... ......μm(微米).μin(微英寸)
50 ...... 2000 .....N12 ............0.8 ...... 32 ...... N6
25 ...... 1000 .....N11.............0.4 ...... 16 ...... N5
12.5.....500 ......N10.............0.2 .....6
3.2
2.5
表面状况=看不清加工痕迹
加工方法=车、镗、刨、铣、铰、拉、磨、滚压、刮1~2点/cm^2铣齿
应用举例=安装直径超过80mm的G级轴承的外壳孔,普通精度齿轮的齿面,定位销孔,V型带轮的表面,外径定心的内花键外径,轴承盖的定中心凸肩表面
▽7
0.63~1.25
0.8
1.6
应用举例=一般非结合表面,如轴的端面、倒角、齿轮及皮带轮的侧面、键槽的非工作表面,减重孔眼表面
▽4
5~10
6.3
12.5
10
表面状况=可见加工痕迹
加工方法=车、镗、刨、钻、铣、锉、磨、粗铰、铣齿
应用举例=不重要零件的配合表面,如支柱、支架、外壳、衬套、轴、盖等的端面。紧固件的自由表面,紧固件通孔的表面,内、外花键的非定心表面,不作为计量基准的齿轮顶圈圆表面等
表面光洁度与表面粗糙度对照表
光洁度(旧标)
粗糙度
级别
Ra(μm)
Ra(μm)
方案1
方案2
方案3
▽1
40~80
50
100
80
▽2
20~40
25
50
40
表面状况=明显可见的刀痕
加工方法=粗车、镗、刨、钻
应用举例=粗加工后的表面,焊接前的焊缝、粗钻孔壁等
▽3
10~20
12.5
25
20
表面状况=可见刀痕
加工方法=粗车、刨、铣、钻
1.25
表面状况=可辨加工痕迹的方向
加工方法=车、镗、拉、磨、立铣、刮3~10点/cm^2、滚压
应用举例=要求保证定心及配合特性的表面,如锥销与圆柱销的表面,与G级精度滚动轴承相配合的轴径和外壳孔,中速转动的轴径,直径超过80mm的E、D级滚动轴承配合的轴径及外壳孔,内、外花键的定心内径,外花键键侧及定心外径,过盈配合IT7级的孔(H7),间隙配合IT8~IT9级的孔(H8,H9),磨削的齿轮表面等
▽9
0.16~0.32
0.2
0.4
0.32
表面状况=不可辨加工痕迹的方向
加工方法=布轮磨、磨、研磨、超级加工
应用举例=工作时受变应力作用的重要零件的表面。保证零件的疲劳强度、防腐性和耐久性,并在工作时不破坏配合性质的表面,如轴径表面、要求气密的表面和支承表面,圆锥定心表面等。IT5、IT6级配合表面、高精度齿轮的表面,与G级滚动轴承配合的轴径表面,尺寸大于315mm的IT7~IT9级级孔和轴用量规级尺寸大于120~315mm的IT10~IT12级孔和轴用量规的测量表面等