潜在失效模式分析管理规定
潜在过程失效模式及后果分析(PFMEA)管理办法
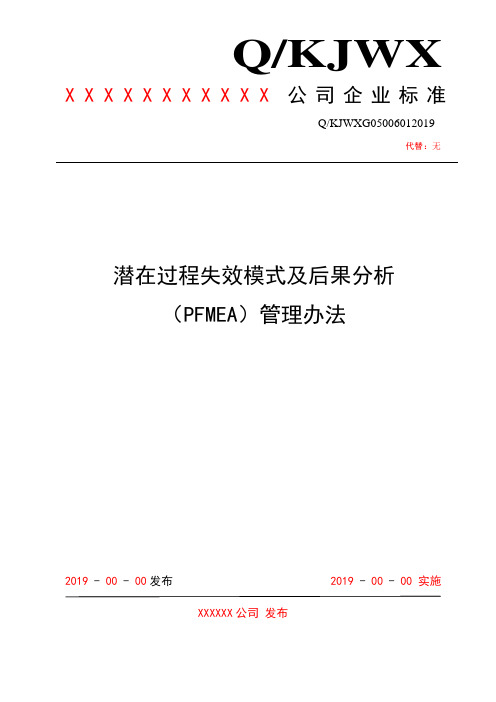
Q/KJWX X X X X X X X X X X X公司企业标准Q/KJWXG05006012019代替:无潜在过程失效模式及后果分析(PFMEA)管理办法2019 - 00 - 00发布2019 - 00 - 00 实施XXXXXX公司发布目次前言............................................................................. I II1 目的 (4)2 范围 (4)3 术语定义 (4)3.1 FMEA (4)3.2 PFMEA (4)3.3 顾客 (4)3.4 潜在失效模式 (4)3.5 严重度 (4)3.6 频度 (5)3.7 探测度 (5)4 职责 (5)4.1 工艺部 (5)4.2 试验部 (5)4.3 售后部 (5)4.4 品质保证部 (5)4.5 生产制造部 (5)4.6 标准化部 (5)5 工作流程 (5)5.1 PFMEA目的 (5)5.2 PFMEA制定原则 (6)5.3 PFMEA输入 (6)5.4 PFMEA格式编写要求 (6)5.5 PFMEA输出 (12)5.6 PFMEA小组 (13)5.7 PFMEA开始时机 (13)5.8 PFMEA完成时机 (13)5.9 PFMEA更新 (13)5.10 PFMEA分析步骤 (13)6 支持文件 (17)7 记录 (17)PFMEA小组成员清单 (18)潜在过程失效模式及后果分析表 (19)潜在过程失效模式及后果分析检查表 (20)潜在过程失效模式及后果分析失效链整理表 (21)潜在过程失效模式及后果分析编制清单 (22)文件更改状态记录 (23)前言本标准是根据XXXXXXXXXXXXXXXX公司发展要求而制定的,本标准按GB/T1.1-2009给出的编写规则进行起草。
本标准由XXXXXXXXXXXXXXXX公司工艺部提出。
本标准由XXXXXXXXXXXXXXXX公司标准化部归口管理。
潜在失效模式及后果分析管理程序
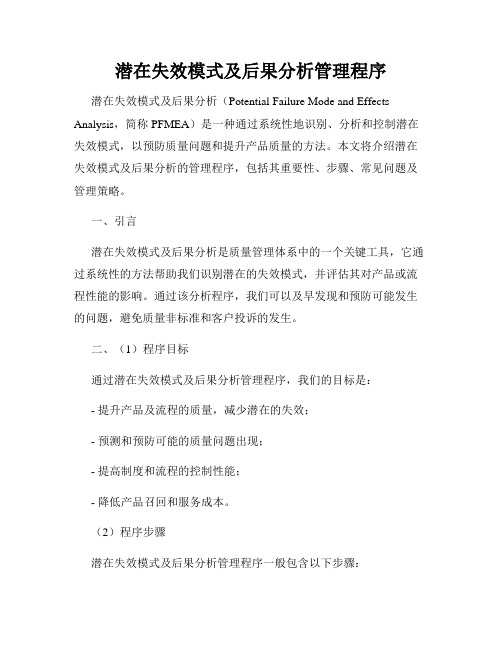
潜在失效模式及后果分析管理程序潜在失效模式及后果分析(Potential Failure Mode and Effects Analysis,简称PFMEA)是一种通过系统性地识别、分析和控制潜在失效模式,以预防质量问题和提升产品质量的方法。
本文将介绍潜在失效模式及后果分析的管理程序,包括其重要性、步骤、常见问题及管理策略。
一、引言潜在失效模式及后果分析是质量管理体系中的一个关键工具,它通过系统性的方法帮助我们识别潜在的失效模式,并评估其对产品或流程性能的影响。
通过该分析程序,我们可以及早发现和预防可能发生的问题,避免质量非标准和客户投诉的发生。
二、(1)程序目标通过潜在失效模式及后果分析管理程序,我们的目标是:- 提升产品及流程的质量,减少潜在的失效;- 预测和预防可能的质量问题出现;- 提高制度和流程的控制性能;- 降低产品召回和服务成本。
(2)程序步骤潜在失效模式及后果分析管理程序一般包含以下步骤:1. 确定分析对象:选择需要进行分析的产品或流程。
2. 制定团队:组建跨职能团队,包括设计师、工程师、生产经理及质量专家等。
3. 制定流程图:绘制分析对象的流程图,详细记录每个操作步骤。
4. 识别潜在失效模式:根据流程图,识别可能存在的失效模式,以及导致其发生的原因。
5. 评估失效后果:评估每种潜在失效模式对产品或流程性能的影响,确定其后果等级。
6. 制定预防控制措施:针对每种潜在失效模式,制定相应的预防控制措施,以降低失效发生的概率。
7. 实施控制措施:在生产或流程中实施预防控制措施。
8. 监控效果:对实施的控制措施进行监控,并评估其效果。
9. 持续改进:根据实施和监控结果,进行持续改进,提升产品或流程的质量和性能。
(3)常见问题及管理策略在潜在失效模式及后果分析管理过程中,常见的问题包括:- 遗漏潜在失效模式:由于团队成员的专业背景和经验不同,可能会遗漏一些潜在失效模式。
解决方案是广泛征求团队成员的意见,并进行多层次的复查。
潜在失效模式分析管理办法

1、目的:提供一种能被用于分析过程的工具,来帮助识别潜在失效模式,按优先次序区分潜在失效模式,明确一个行动计划去排除或减少潜在的失效模式发生的可能性,降低制造风险。
2、范围:适用于本公司PFMEA2.1新产品量产前2.2重要材料变更时2.3生产设备及工装新购及变更影响到过程更改时2.4工艺变更时3、定义:3.1 FMEA:失效模式与效应分析3.2 DFMEA:设计失效模式与效应分析3.3 PFMEA:过程失效模式与效应分析4、职责FMEA的编制与修改均由多方论证小组完成5、流程图流程图见下页:6、程序6.1说明6.1.1本公司无产品设计开发责任,所有产品均按客户的图纸/规范/相关标准书生产。
6.2 PFEMA的表格格式,参照FMEA手册。
6.3编制PFEMA资料的来源客户的DFEMA过程流程图(若无,则参考类似产品的过程流程图)本公司以往类似产品的PFMEA或经验本公司以往客户抱怨或客户退货资料本公司类似产品的不良率统计资料设备及工装运行不良之统计资料6.4RPN接收准则当RPN>130时,必须采取改进措施当S≥ 9且,必须采取措施6.5严重度数(S)之频度(O)、探测度(D)判定准则见附件。
6.8对策拟定执行与效果确认6.8.1 各相关部门针对多方论证小组识别出的潜在失效拟定相应对策并实施,确定责任人及完成期限,简述实际采取的措施及生效日期。
6.8.2多方论证小组对各部门采取的措施进行确认,重新计算纠正措施执行后的风险顺序数(严重度、频度和不可探测度)。
6.9 PFEMA之修改6.9.1多方论证小组在量产时应定期对相应产品的PFMA作修改,修改所需之资料见6.9.26.9.2FEMA修改时,可参考以下资料a. 该产品量产后之不良统计资料,这将涉及到(O)的改变b. 该产品交付顾客后的顾客抱怨及退货资料,这将涉及到(O)和(D)的改变c. 该产品量产之设备与工装之运行不良之统计,因设备及工装运行不良将影响到产品的不良,这将影响到(O)和(D)的改变d. 其它将影响RPN值改变的资料6.9.3PFMEA变化后,将影响控制计划、检查标准书及作业标准书的变化,所以多方论证小组将相应之控制计划、检查标准书和作业标准书进行修改,且按《文件控制程序》的规定执行。
DFMEA设计潜在失效模式和后果分析管理程序

版本修改条款1.目的通过分析、预测设计、设计中潜在的失效,研究失效的原因及其后果,并采取必要的预防措施,避免或减少这些潜在的失效,从而提高产品、过程的可靠性。
2.适用范围适用于公司产品设计DFMEA活动的控制。
3.职责3.1研发中心(PD)负责组织成立DFMEA(设计FMEA)小组,负责DFMEA活动的管理。
工程部(PE)负责组织成立PFMEA(过程FMEA)小组,负责PFMEA活动的管理。
3.2研发中心、工艺、品质、生产部、业务部等部门指定人员参加DFMEA小组与PFMEA小组。
必要时,由品质邀请供应商、客户参加。
3.3DFMEA小组负责制定《DFMEA潜在失效后果严重程度(S)评价标准》、《DFMEA潜在失效模式发生频度(O)评价标准》、《DFMEA潜在失效模式发现难度(D)评价标准》。
并负责准备《DFMEA和PFMEA的措施优先级(AP)》。
4.工作程序4.1设计FMEA的开发实施4.1.1DFMEA实施的时机4.1.1.1按APQP的计划进行DFMEA。
4.1.1.2DFMEA在设计之前开始。
DFMEA小组应在提交设计计划批准前就要收集资料,对以往的项目、样品试产时出现的问题、以及客户在检测样品时所反馈的信息进行分析。
4.1.1.3发生设计更改时,应复查DFMEA文件,其应体现最新的设计(或工艺设计水平)及改善,采取最新的相应措施。
4.1.2PFMEA实施前的准备工作4.1.2.1研发中心牵头成立DFMEA(设计FMEA)小组,研发中心(R&D)、品质、生产部、物料部采购等部门指定人员参加DFMEA小组,必要时,由品质邀请供应商、客户参加。
4.1.2.2在DFMEA活动实施前,DFMEA小组应制定出《DFMEA潜在失效后果严重度(S)评价标准》、《DFMEA潜在失效模式频度(O)评价标准》、《DFMEA潜在失效模式探测度(D)评价标准》。
a)DFMEA小组根据FMEA手册参考标准,确定出本公司的实际示例。
FMEA潜在失效模式分析管理程序

FMEA潜在失效模式分析管理程序FMEA潜在失效模式分析管理程序(IATF16949-2016)1.目的:确定潜在失效模式与评定其影响的严重程度。
确定关键特性与重要特性。
对潜在的过程缺陷进行排序。
帮助我们集中力量免除对过程的担心,防止问题的发生。
2.范围:适用于公司所有新产品、产品更改以及应用或环境有变化的沿用零件(包括:产品交付给客户后的抱怨(投诉)或退货的产品)。
3.定义:PFMEA:是英文Process Failure Mode and Effects Analysis 的缩写,即过程失效模式及后果分析,是一种表格化的系统方法,用来帮助我们思维,以确定失效模式及其影响,并通过周期性的FMEA分析,以此来获得产品品质的持续改进。
4.权责:4.1APQP小组:负责初期产品生产过程潜在的失效模式及后果分析的作成和评审。
4.2生产部:负责统筹量产后FMEA的维护。
4.3各部门:参与产品生产过程潜在的失效模式及后果分析,并进行评审。
5.内容:5.1 制作PFMEA的三个假设:①PFMEA假设被定义的产品将符合设计意图;②假设投入生产的物料为合格品;③假设操作人员是经培训合格的。
5.2 PFMEA之使用时机:5.2.1 PFMEA为一活性的文件,它应该在APQP五个阶段中的第三个阶段(过程的设计和开发阶段)在制作过程流程图后,根据过程流程图作成。
5.2.2 PFMEA的制作:5.2.2.1讨论并填表:APQP小组成员对相应工序进行讨论,评估出现的几率、可查性、严重程度等项目。
根据评分结果拟定改善措施,负责人及实施日期。
填写相应的FMEA表格。
由指定的改善措施负责人组织,在规定的时间内实施具体的改善行动。
5.2.2.2 评估改善行动:根据计划,由APQP组长召集改善措施的评估会。
依据改善效果决定是否还需要进行下一轮FMEA。
5.2.2.2 FMEA制作流程:5.3 FMEA更改的时机:5.3.1 当生产过程发生更改后必须重新评定FMEA并更改。
潜在失效模式及后果分析流程规定

XXXX有限公司潜在失效模式及后果分析流程规定拟制:审核:批准:文件版本修改记录相关部门会签1.目的通过对产品在过程所采取的分析评估,消除存在或潜在的异常原因,提高产品的质量。
2.范围产品制造过程均适用此流程规定。
3.职责a、选定产品和工序并分析失效模式与效应,提出改善措施并追踪效果。
b、技术工程部、品质部、生产部、设备部、PFMEA小组人员及改善措施之执行。
c、由技术工程部主导,涉及部门积极参入的一系列活动。
4.定义1、严重度(S):潜在失效模式发生时对下一工序影响后果的严重程序的评监指标。
2、发生机率(O):实际上发生和造成失效模式之原因的机率。
3、难检度(D):失败将会延伸到下一个工站或客户的评价。
4、风险优先数(RPN):是指SXOXD二RPN,是用来评定事项处理的优先顺序。
5.内容:5.1PFMEA作业过程1、成立PFMEA小组:a、技术工程部召集成立PFMEA小组成员,以5-9人组成。
b、成员必须具备有权确定和执行任务的部门和个人。
2、PFMEA的立题选定:a、PFMEA小组应讨论出PFMEA的问题;b、研讨立题导入PFMEA的可行时机:1、产品变异时2、PPM值过高3、专案及客户要求;5.2PFMEA表格填写说明:1.PFMEA编号:记录PFMEA文件的编号,以便查询;2.确定项目名称:确定所分析的系统,子系统或零件的过程各程编号;3.责任部门确定:确定失效模式产生的部门和小组;4.确定权责人:填入负责准备PFMEA工作的责任人;5.确定项目:填入产品编号;6.记录制作日期:填入编制PFMEA原始稿的整理日期及最新修定的日期;7.填入PFMEA小组成员:将参加PFMEA小组的成员名单予以记录;8.确定工序:a、简单描述被分析的过程或工序,并尽可能简单地说明该工艺过程或工序的目的;b、如果工序过程包括许多具有不同失效模式,那么可以把这些工序作为独立的过程列出;9.确定失效模式:根据特定的工序,列出每一个不良现象;10.分析失效后果:应依据顾客或下一工序可能注意到的或经历的情况来描述失效的后果;11.评定严重性:依失效的后果评定严重度;12.失效起因分析/机理:针对每一个潜在的失效模式,在尽可能广的范围内,分析并列出每一个可以想到的失效起因;13.评审发生机率:依失效起因评定发生机率;14.过程控制方法描述:对尽可能阻止失效模式的发生或者探测发生的失效模式的控制的描述;评定难检度:评定在下一个或后续工艺前或零件离开制造或装配工位前,利用过程控制方法找出缺陷的可能性;16.计算风险优先数RPN: a、SXOXD=RPN b、通过RPN以体现及选择其需优先改善的失效模式;17.优先改善项目选定:当失效模式按RPN值排出先后顺序后,应首先对排列在最前面的事和最关键的项目采取纠正措施,在一般实距中不管RPN大小如何,当严重高时,就应予以特别注意,a:需改善,提出建议措施;b:不需改善,不予理会;18.建议措施责任确定:确定负责建议措施的组员和个人,以及预计完成日期;19.措施结果确认:当明确了纠正措施后,估算并记录纠正后的发生机率,严重度和难检度计算并记录纠正后的PRN值;20.确定核准:由技术工程部经理及品质部经理核准;由相关单位将有效的措施纳入正式文件;XXXX有限公司管理文件(三级文件)文件编号JS-WI-019题目:潜在失效模式及后果分析流程规定版本号A/0页数5/115.3操作步骤及作业内容步骤作业内容负责单位技术工程部召集成立PFMEA小组技术工程部成员,以5-9人组成讨论出PFMEA的问题,以及导入PFMEA小组PFMEA的可行时机根据特定的工序,列出每一个不PFMEA小组良现象依失效的后果评定严重度PFMEA小组依失效起因评定发生机率PFMEA小组评定在下一个或后续工艺前或零件离开制造或装配工位前,利用PFMEA小组过程控制方法找出缺陷的可能性SXOXD=RPN 通过RPN技术工程部以体现及选择其需优先改善的失效模式;当RPN值排出先后顺序后,对在PFMEA小组最前面的事和最关键的项目采取纠正措施,当严重高时,要特别注意,需改善时,提出建议措施PFMEA小组确定负责建议措施的组员和个人,以及预计完成日期当明确了纠正措施后,估算并记录纠正后的发生机率,严重度和PFMEA小组难检度计算并记录纠正后的PRN值。
过程潜在失效模式及后果分析(PFMEA)管理规定

过程潜在失效模式及后果分析(PFMEA)管理规定编号:SDFK/A2.GS0035-2016编制:刘滨日期:2017年1月1日审核:李瑞芳日期:2017年1月1日批准:杜孝权日期:2017年 1月1 日山东福宽生物工程有限公司1、目的1.1根据过程失效模式,分析出潜在失效原因,研究该项失效模式对下工序和最终用户会产生什么影响。
1.2失效分析用于找出零件、组件或系统的潜在弱点,以便技术、制造、质量等部门采取可行对策,降低产品的失效风险,最大限度地保证产品能满足客户的要求和期望。
2、适用范围本程序适用于公司新产品进入批量生产前阶段,以及工艺改进阶段。
3、职责3.1供应链管理部门工艺人员、研发工程师/系统工程师、质量部工程师、售后工程师及供应链管理部门经理共同组成过程潜在失效模式及后果分析小组;3.2研发工程师和系统中心工程师给供应链管理部门工艺人员提供工艺过程潜在失效模式分析的技术支持;3.3销售与市场部售后人员应及时将现场故障情况及客户反馈反映给质量部门及供应链管理部门,协助其进行产品工艺过程潜在失效模式分析;3.4供应链管理部门车间应协助工艺人员和质量工程师完成改进措施。
4、过程控制及流程4.1过程失效模式的定义过程失效模式是一种按小组进行工作的严格的预防性分析技术,在失效分析中,首先要明确产品的失效是什么,否则产品的数据分析和可靠度评估结果将不一样。
一般而言,失效是指:4.1.1在规定条件下(环境、操作、时间),被分析对象不能完成既定功能。
4.1.2在规定条件下,产品参数值不能维持在规定的上下限之间。
4.1.3产品在工作范围内,导致零组件的破裂、断裂、卡死、损坏等现象。
4.2过程失效模式分析的内容4.2.1过程功能:根据附件表格,依次填入要被分析的过程或工序。
尽可能简单地说明该工艺过程或工序的目的,当过程包含不同失效模式工序,可将这些工序作为独立的过程分析其失效模式。
4.2.2潜在失效模式:潜在失效模式是指过程可能不符合过程要求或设计意图。
PFMEA管理规定

PFMEA管理规定1.目的通过建立预先的失效模式及后果分析,对生产工艺流程进行策划和评估,并采取措施降低失效风险以支持生产过程开发,从而确定产品的工艺特性,建立充足的加工能力。
2.范围适用于本公司生产加工过程流程图中定义的工序。
3.职责3.1产品质量策划小组负责确定PFMEA分析工序,指定各过程工作小组责任人;3.2各过程工作小组责任人负责组织成立核心小组和组织工作的开展。
4.定义4.1PFMEA是过程潜在失效模式及后果分析(Process Failure Mode and Effects Analysis)的英文简称,是由负责制造/装配的工程师/小组主要采用的一种分析技术,用以最大限度地保证各种潜在的失效模式及其相关的起因/机理已得到充分的考虑和论述4.2DFMEA是设计潜在失效模式及后果分析(Design Failure Mode and Effects Analysis)的英文简称,DFMEA在一个设计概念形成之时或之前开始,并且在产品开发各阶段中,当设计有变化或得到其他信息时及时不断地修改,并在图样加工完成之前结束。
4.3潜在的失效模式:是指过程可能发生的不满足过程要求或设计意图的形式或问题点,是对某具体工序不符合要求的描述。
它可能是引起下一道工序的潜在失效模式,也可能是上一道工序失效模式的后果。
4.4潜在失效后果:是指失效模式对顾客的影响,站在顾客的角度描述失效的后果,这里的顾客可以是下道工序或是最终使用者。
4.5严重度(S):是对一个已假定失效模式的最严重影响的评价等级。
它是单个FMEA范围内的一个比较级别。
要减少严重度识别等级,只能通过对零件的设计变更,或对过程重新设计,否则,严重度不会发生变化。
严重度分1(无影响)-10(后果严重)级。
4.6频度(O):是指具体失效起因发生的可能性。
频度的可能性分级数字是一个比较的含义,不是绝对值。
频度1意味极少发生,频度10意味经常发生。
4.7探测度(D):是对产品或者过程如何探测失效起因或者失效模式起因的一种评估。
潜在失效模式分析管理规定
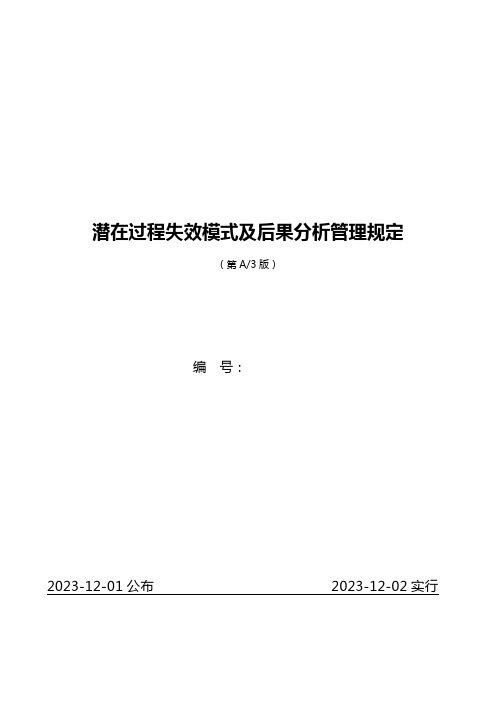
潜在过程失效模式及后果分析管理规定(第A/3版)编号:2023-12-01公布2023-12-02实行1.目旳用以规范PFMEA编制与管理。
2.合用范围合用于我司汽车零件PFMEA文献编制与管理。
3.职责3.1 技术部负责组织项目组,项目组可由技术部、质量部、生产部、采购部、销售部等有关人员构成。
如有必要,供应商和顾客代表也可参与。
3.2 项目组负责PFMEA编制,并将其应用于生产过程中。
3.3 生产部门负责执行PFMEA中已定义旳防止或改善措施。
4.定义4.1 PFMEA:是Process Failure Model and Effect Analysis旳简称,中文翻译为”潜在过程失效模式及后果分析”,用以评价产品和过程中潜在失效管理,透过改善措施减少失效旳频度或提高可侦测性来防止量产时所也许发生旳产品及过程异常。
4.2 失效:零件在规定条件下不能完毕其规定旳功能,或参数不能保持在规定范围内,或操作者失误,导致产品功能失效,及因应环境力变化导致功能丧失。
4.3 严重度(S):失效状况旳等级,数字愈大,导致旳损伤愈严重。
4.4 频度(O):失效模式旳发生频率,数字愈小,表达发生率越低。
4.5 探测度(D):失效模式旳可被侦测度,数字愈小,表达不合格愈轻易被发现。
4.6 风险系数(RPN):即严重度(S)*频度(O)*探测度(D)。
4.6.1 S=5时,即意味着减少性能并持续衰退;O=5时,即意味着大概有0.05%旳发生也许性;D=5时,即意味着可在流到下道工序或装运前检出;顾客指定期需依顾客规定实行,未指定期,当RPN值≥125,即需采用措施,并列入高风险项目清单,于换阶、例行、临时评审时检讨措施有效性。
4.6.2 特殊状况如S、O、D其中之一不小于或等于9时,必须识别为高风险项目,列入高风险项目清单中,并制定对应旳防错措施以减少顾客风险,于换阶、例行、临时评审时讨论措施有效性。
5作业流程:5.1研讨各过程失效模式→评估严重度→评估现行控制频度→评估现行措施探测度→计算风险系数→识别改善项目→采用改善措施→重新计算风险系数→结案→列入经验教训数据库。
FMEA第五版教材的潜在失效模式分析风险评估与管理

FMEA第五版教材的潜在失效模式分析风险评估与管理随着技术和工业的不断发展,风险评估与管理在各个领域中扮演着重要的角色。
为了更好地应对潜在的失效模式,FMEA(Failure Mode and Effects Analysis,潜在失效模式与影响分析)被广泛应用于各种工业和生产领域。
本文将以FMEA第五版教材为基础,探讨潜在失效模式分析风险评估与管理的相关概念和方法。
一、潜在失效模式分析的介绍潜在失效模式分析是一种通过系统性的方法识别、分析和评估潜在的失效模式、确定其风险等级,并采取相应的措施进行管理和改进的工具。
通过对潜在失效模式及其后果进行准确的评估,可以有效降低产品质量问题的风险,提高生产效率和产品可靠性。
二、潜在失效模式分析的方法论1. 识别失效模式:通过对产品、系统或过程进行全面的分析,确定可能出现的失效模式。
这些失效模式可以是因环境、材料、工艺或人为因素引起的。
2. 评估失效后果:对每个失效模式进行后果评估,包括对人身安全、设备损坏、生产过程中断等方面的评估。
评估结果可以用来确定失效模式的风险等级。
3. 确定风险等级:根据失效模式的后果评估以及可能性、严重性和侦测性等因素,对失效模式进行风险等级的划分。
常用的评估方法包括风险矩阵法和风险优先级数法。
4. 制定改进和控制措施:根据风险等级的高低,确定相应的改进和控制措施。
对高风险失效模式,应采取更严格的控制和改进措施,以保证产品的质量和可靠性。
5. 实施和追踪措施:将制定的措施纳入生产和管理体系中,确保其正确执行。
同时,需要建立追踪和更新机制,对措施的有效性进行监控和评估。
三、FMEA第五版教材的要点FMEA第五版教材是对传统FMEA方法的一次重要更新。
它引入了一些新的概念和工具,以更好地适应现代生产环境的需求。
以下是FMEA第五版教材的一些重要要点:1. 引入风险优先级数:风险优先级数是评估失效模式风险等级的常用指标。
它是通过将可能性、严重性和侦测性等评估因素综合考虑,给出一个综合的风险等级指数。
FMEA潜在失效模式及后果分析管理程序

FMEA潜在失效模式及后果分析管理程序FMEA(Failure Mode and Effects Analysis)是一种系统性的方法,用于识别和评估产品或过程的潜在失效模式及其可能引起的后果。
FMEA可以帮助组织预防或最小化潜在失效对产品质量、安全性和可靠性的影响。
下面是一个FMEA潜在失效模式及后果分析管理程序的示例,确保在组织中有效实施FMEA。
一、引言该程序旨在确保组织对产品或过程进行系统性的失效模式及后果分析(FMEA),以评估潜在失效的风险,并采取适当的预防措施。
二、定义1. FMEA:Failure Mode and Effects Analysis,是一种识别和评估潜在失效模式及其可能引起的后果的方法。
2.潜在失效模式:指在产品或过程中可能发生的具体失效模式。
3.后果:指潜在失效模式发生后产生的影响。
三、程序内容1.确定FMEA的范围和目标:明确进行FMEA的产品或过程范围,以及FMEA的目标是为了什么。
例如,产品的质量改进、安全性提升、故障率降低等。
2.组建FMEA团队:确保组建具有相关领域知识和技能的跨部门团队。
团队成员应包括产品设计、工艺工程、质量控制等相关专业人士。
3.制定FMEA计划:制定详细的FMEA计划,包括时间表、任务分配和所需资源等。
4.进行FMEA分析:a.识别潜在失效模式:收集和分析产品或过程中可能出现的失效情况。
b.评估失效后果:针对每个潜在失效模式,评估其可能引起的后果,包括质量、安全、可靠性和法规符合性等方面。
c.确定风险优先级:通过综合评估潜在失效模式的严重性、发生概率和探测能力,确定每个潜在失效的风险优先级。
d.制定预防措施:针对高风险优先级的潜在失效模式,制定相应的预防措施,以减少或消除潜在失效的风险。
e.实施预防措施:组织相关部门或人员实施制定的预防措施,并跟踪措施的有效性。
f.更新FMEA文档:在FMEA过程中产生的所有数据和分析结果都应及时记录和更新FMEA文档。
潜在失效模式及后果分析管理程序
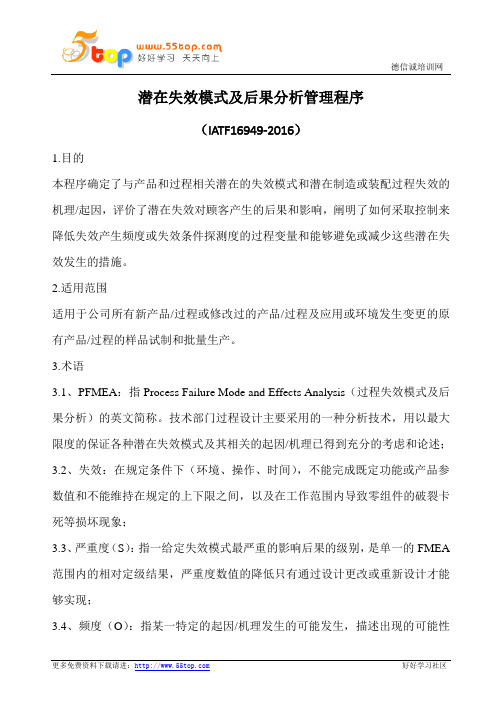
潜在失效模式及后果分析管理程序(IATF16949-2016)1.目的本程序确定了与产品和过程相关潜在的失效模式和潜在制造或装配过程失效的机理/起因,评价了潜在失效对顾客产生的后果和影响,阐明了如何采取控制来降低失效产生频度或失效条件探测度的过程变量和能够避免或减少这些潜在失效发生的措施。
2.适用范围适用于公司所有新产品/过程或修改过的产品/过程及应用或环境发生变更的原有产品/过程的样品试制和批量生产。
3.术语3.1、PFMEA:指Process Failure Mode and Effects Analysis(过程失效模式及后果分析)的英文简称。
技术部门过程设计主要采用的一种分析技术,用以最大限度的保证各种潜在失效模式及其相关的起因/机理已得到充分的考虑和论述;3.2、失效:在规定条件下(环境、操作、时间),不能完成既定功能或产品参数值和不能维持在规定的上下限之间,以及在工作范围内导致零组件的破裂卡死等损坏现象;3.3、严重度(S):指一给定失效模式最严重的影响后果的级别,是单一的FMEA 范围内的相对定级结果,严重度数值的降低只有通过设计更改或重新设计才能够实现;3.4、频度(O):指某一特定的起因/机理发生的可能发生,描述出现的可能性的级别数具有相对意义,但不是绝对的;3.5、不易探测度(D):指在零部件离开制造工序或装配之前,利用第二种现行过程控制方法找出失效起因/机理过程缺陷或后序发生的失效模式的可能性的评价指标;或者用第三种过程控制方法找出后序发生的失效模式的可能性的评价指标;3.6、风险优先数(RPN):指严重度数(S)和频度数(O)及不易探测度数(D)三项数字之乘积。
3.7、顾客:一般是指“最终使用者”,但也可以是随后或下游的制造或装配工序,维修工序或政府法规;4.职责4.1、技术部负责过程失效模式及后果分析(PFMEA)的制定与管理。
5.依据标准5.1、本程序依据IA TF16949:2016质量管理体系中标准条款8.1、8.1.1、8.1.2、8.3、8.3.1、8.3.1.1、8.3.2.3、8.3.3、8.3.3.1、8.3.3.2、8.3.3.3、8.3.4、8.3.4.1、8.3.4.2、8.3.4.3、8.3.4.4、8.3.6、8.3.6.1编制。
设备潜在失效模式及后果分析管理规定

设备潜在失效模式及后果分析(FMEA)管理规定一、目的生产科、设备管理及使用部门、精益办通过对设备故障失效分析及故障产生的后果分析,使设备在出现故障前、后对设备各种可能产生的风险进行评价、分析,以便在现有的技术基础上事前确定改善措施,提前预防来消除这些风险或把风险降低在可接受的水平内。
二、FMEA的实施1、由生产科组织设备FMEA分析小组。
设备管理人员、使用部门人员、精益生产人员共同组成设备FMEA分析小组。
设备FMEA分析管理架构组长:黄建栋制品科烧结科机加工科设备组机加工1 机加工2 机加工3唐环贵李雷李捷孟彦青钟永首王曙光龚晓峰刘保苗辉、张景元王宏青张发晶刘波朱贵春2、设备维修部门制定设备FMEA分析计划,选择分析设备,建立设备FMEA分析台账。
3、设备维修部门收集设备资料。
(设备图纸资料、设备操作说明书、设备维护保养说明书、维修记录等)4、生产科组织专业维修技术人员对设备进行FMEA分析,把出现的潜在失效模式、产生的原因、预防措施、检测方法进行对S、O、D、RPN评分,并制定出相应的维修措施。
5、设备维修部门制作FMEA分析表进行动态管理。
6、结合TPM活动或融入TPM中,也可独立执行。
7、设备维修部门输出结果,确定维修策略。
8、生产科总结、完善、更新,FMEA是始终反应最新水平及最近的相关措施,包括开始生产以后发生的。
三、设备FMEA分析量化指标,是对故障的严重度S、故障发生的频度O、检测时的探测度D进行评估,确定设备存在的故障风险指标RPN,制定维修策略。
RPN=S*O*D 最大RPN=10*5*4=200 最小RPN=1*0.5*1=0.5S 严重度系数:故障严重度分析(1-10)O频度系数:故障发生频率分类(0.5-5)5、编制/日期: 审核/日期:批准/日期:。
潜在失效模式后果分析FMEA控制程序

潜在失效模式后果分析FMEA控制程序潜在失效模式后果分析(Failure Mode and Effects Analysis, FMEA)是一种系统化的方法,用于评估和控制潜在失效模式及其对系统、产品或过程的影响。
以下是FMEA控制程序的一般步骤和相关考虑事项。
1.确定分析的范围和目标:明确需要进行FMEA的系统、产品或过程范围,以及分析的目标,如识别潜在失效模式、评估后果等。
2.组建FMEA团队:成立由跨职能团队组成的FMEA团队,包括设计、制造、质量等相关部门和人员。
在团队成员中确定一个负责人。
3.识别潜在失效模式:对系统、产品或过程进行全面的分析,识别可能出现的潜在失效模式,并列出所有潜在失效模式。
4.评估失效后果:对每个潜在失效模式进行评估,考虑其对系统、产品或过程的影响。
评估标准可以包括安全性、可靠性、维修性、可用性和环境影响等方面。
5.确定失效频率:评估每个潜在失效模式发生的频率或概率。
这可以通过历史数据、经验知识和专家判断等方法来获得。
6.确定探测能力:评估当前探测或检测系统对失效模式的能力,以及探测到失效模式后能否及时采取相应控制措施。
7.计算风险优先级数(RPN):根据失效模式的后果、发生频率和探测能力来计算风险优先级数。
通常使用一个简单的公式:RPN=后果×频率×探测。
8.制定控制措施:对具有较高风险优先级数的失效模式,制定并实施相应的控制措施,以减少或消除潜在风险。
9.重新评估和追踪:定期重新评估已采取控制措施的失效模式,追踪其效果并及时调整控制程序。
10.修订和更新:根据实施控制措施的效果和经验教训,以及新的信息和要求,修订和更新FMEA控制程序。
在FMEA控制程序中1.缺陷的严重程度:评估失效模式对系统、产品或过程的影响程度,包括安全性、可靠性等方面。
2.失效发生的频率:评估失效模式发生的概率或频率,以便更准确地评估潜在风险。
3.探测控制能力:评估当前的探测系统、检测方法或控制措施是否能够及时发现和控制失效模式。
潜在失效模式及后果分析FMEA控制程序
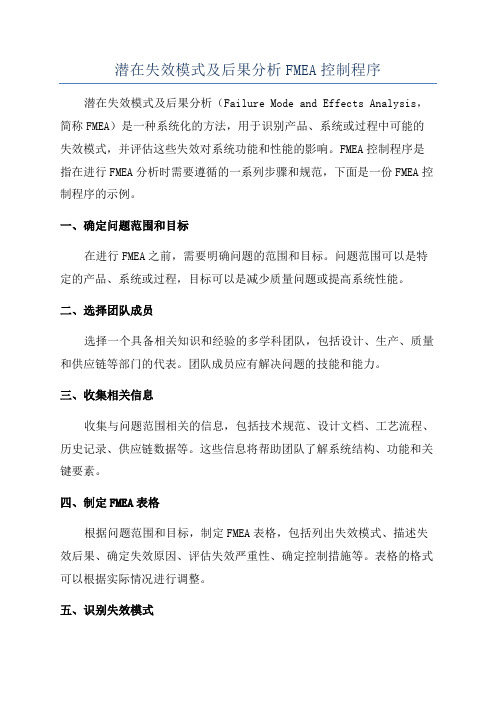
潜在失效模式及后果分析FMEA控制程序潜在失效模式及后果分析(Failure Mode and Effects Analysis,简称FMEA)是一种系统化的方法,用于识别产品、系统或过程中可能的失效模式,并评估这些失效对系统功能和性能的影响。
FMEA控制程序是指在进行FMEA分析时需要遵循的一系列步骤和规范,下面是一份FMEA控制程序的示例。
一、确定问题范围和目标在进行FMEA之前,需要明确问题的范围和目标。
问题范围可以是特定的产品、系统或过程,目标可以是减少质量问题或提高系统性能。
二、选择团队成员选择一个具备相关知识和经验的多学科团队,包括设计、生产、质量和供应链等部门的代表。
团队成员应有解决问题的技能和能力。
三、收集相关信息收集与问题范围相关的信息,包括技术规范、设计文档、工艺流程、历史记录、供应链数据等。
这些信息将帮助团队了解系统结构、功能和关键要素。
四、制定FMEA表格根据问题范围和目标,制定FMEA表格,包括列出失效模式、描述失效后果、确定失效原因、评估失效严重性、确定控制措施等。
表格的格式可以根据实际情况进行调整。
五、识别失效模式团队成员按照经验和知识识别可能的失效模式。
失效模式可以是产品功能缺陷、系统故障、质量不符合要求等。
团队成员可以使用头脑风暴、故障模式与影响分析(FMEA)会议等方法来识别失效模式。
六、描述失效后果对于每个失效模式,团队成员应详细描述其潜在的后果。
后果可以包括安全风险、功能损失、效率下降、成本增加等。
描述后果时,可以使用图表、图像、文字说明等形式。
七、确定失效原因团队成员需要分析和确定导致每个失效模式的原因。
原因可能包括设计缺陷、生产工艺问题、供应链质量问题等。
团队成员可以使用因果图、5W1H法(即What、Why、When、Where、Who、How)等方法确定失效原因。
八、评估失效严重性对于每个失效模式,团队成员需要评估其对系统功能和性能的严重性。
评估可以基于潜在的后果、出现的频率、影响的程度等。
- 1、下载文档前请自行甄别文档内容的完整性,平台不提供额外的编辑、内容补充、找答案等附加服务。
- 2、"仅部分预览"的文档,不可在线预览部分如存在完整性等问题,可反馈申请退款(可完整预览的文档不适用该条件!)。
- 3、如文档侵犯您的权益,请联系客服反馈,我们会尽快为您处理(人工客服工作时间:9:00-18:30)。
潜在失效模式分析管理规定
潜在过程失效模式和后果分析管理规定
(版本A/3)
号码:
汇编:
批准:批准:
2016年12月1日发布2016年12月2日实施
1.目的
规范全氟甲烷烃的制备和管理。
2.适用范围
适用于公司汽车零部件PFMEA文件的编制和管理。
3.责任
3.1技术部负责组建项目组,可由技术部、质量部、生产部、采购部、销售部等相关人员组成。
如有必要,供应商和客户的代表也可以参加。
3.2项目团队负责制备PFMEA并将其应用于生产过程。
3.3生产部负责实施PFMEA中规定的预防或改进措施。
4.定义
4.1工艺失效模式和影响分析:工艺失效模式和影响分析的简称,中文翻译为“潜在工艺失效模式和后果分析”,用于评估产品和工艺中的潜在失效管理,并通过降低失效频率或通过改进措施提高可检测性来防止大规模生产过程中可能出现的产品和工艺异常。
在规定的范围内,或者操作者的错误,产品功能失效,并且由于环境力的变化而失去功能。
4.3严重性(S):故障条件的数量越多,损坏越
严重。
4.4频率(O):故障模式数量越少,发生率越低。
4.5可检测性(d):故障模式的可检测性,数量越少,越容易发现不合格。
4.6风险因素(RPN):即严重程度(S)*频率(O)*检测程度(D)。
4.6.1当s = 5时,意味着性能将下降并继续下降;当0 = 5时,意味着有大约0.05%的可能性发生。
D=5,这意味着它可以在流向下一工序之前或装运之前被检测到;客户指定应根据客户要求进行。
如无指定,当RPN值≥125时采取措施,并纳入高风险项目清单,措施的有效性在换级、常规和临时评审时进行评审。
4.6.2如果S、O和D中的一个大于或等于9,则必须将其识别为高风险项目并列入高风险项目清单,并制定相应的防错措施以降低客户风险。
措施的有效性应在等级变更、例行和临时审查期间进行讨论。
4.2故障:零件不能完成其规定的功能或参数不能在规定的条件下保持5工作流程:
5.1讨论每个过程的故障模式?评估严重性?评估当前控制频率?评估当前措施的检测程度?米
计算风险因素?确定改进项目?采取改进措施?重新计算风险因素?关门了吗?包括在经验教训数据库中。
5.1.1当改进措施未能有效地将风险系数降至125以下时,应重新考虑该计划,直至合格。
5.1.2每次FMEA评价前,应参考类似产品的经验教训数据库的数据,识别失效模式和风险因素。
5.1.3项目负责人每两周召开一次小组成员会议,审查FMEA的适宜性,立即重新审查难以实施或失败的故障模式的内容,及时做出变更,
并对具有相似或可能相同问题的产品进行每次变更的并行开发,以审查或提出预防措施。
5.2 S、o、d评估标准:
5.2.1严重程度评估标准:(A/1版)影响标准:产品影响严重程度客户影响严重程度标准:过程影响严重程度制造/组装影响缺陷/可能导致故障影响车辆安全运行的异常/不符合法规;未提前满足影响车辆安全运行的安全警告和/或监管要求/不符合规定;存在预报警主要功能故障(车辆不可操作,不影响车辆安全)主要功能故障(车辆可操作,但降低了车辆的操作性能)次要功能故障(车辆可操作,但舒适性和便利性不能操作)次要功能故障(车辆可操作,但舒适性和便利性降低)外观或可听噪声,车辆可操作,大多数客户注意到的缺陷(> 75%)用户讨厌外观或声音噪音,车辆是可操作的,大多数客户注意到的缺陷(> 50%)外观或声音噪音,车辆是可操作的,客户注意到的缺陷(。