旋挖钻钻孔灌注桩施工总结
工程桩基年度总结(3篇)

第1篇2022年,我国桩基工程取得了显著的进展,各类桩基施工技术不断革新,施工质量稳步提升。
在过去的一年里,我司在桩基工程领域也取得了丰硕的成果。
现将2022年度工程桩基工作总结如下:一、工作回顾1. 技术创新2022年,我司在桩基工程领域积极开展技术创新,引进了新型桩基施工设备和技术,如旋挖钻机、大直径钻孔灌注桩、高压旋喷桩等。
这些新技术的应用,有效提高了桩基施工效率和质量。
2. 项目管理在项目管理方面,我司严格执行国家相关规范和标准,确保工程安全、质量、进度和成本控制。
针对不同工程特点,制定科学合理的施工方案,确保项目顺利实施。
3. 人才培养为提高员工综合素质,我司加大了对人才培养的投入。
通过内部培训、外部交流等方式,提升员工的专业技能和团队协作能力。
4. 安全生产安全生产始终是我司工作的重中之重。
2022年,我司严格执行安全生产责任制,加强现场安全管理,确保了全年安全生产无事故。
二、主要成果1. 项目完成情况2022年,我司共承接了20个桩基工程项目,累计完成桩基工程量约10万米。
其中,重点工程有XX市XX区住宅项目、XX市XX区市政道路项目等。
2. 质量控制在质量控制方面,我司严格按照国家相关规范和标准进行施工,确保了工程质量。
全年共获得省级优质工程奖项2项,市级优质工程奖项5项。
3. 技术创新与应用2022年,我司在桩基工程领域成功应用了多项新技术,如旋挖钻机、大直径钻孔灌注桩等。
这些新技术的应用,提高了施工效率,降低了施工成本。
三、存在问题及改进措施1. 存在问题(1)部分工程进度滞后,影响了整体施工进度。
(2)施工现场管理有待加强,存在安全隐患。
(3)部分员工技术水平有待提高。
2. 改进措施(1)加强项目进度管理,优化施工方案,确保工程按期完成。
(2)强化现场安全管理,加大安全培训力度,提高员工安全意识。
(3)加大人才培养力度,提高员工综合素质,提升整体技术水平。
四、展望2023年,我司将继续加大技术创新力度,提高项目管理水平,努力提升工程质量和安全生产水平。
旋挖钻孔灌注桩经验总结报告
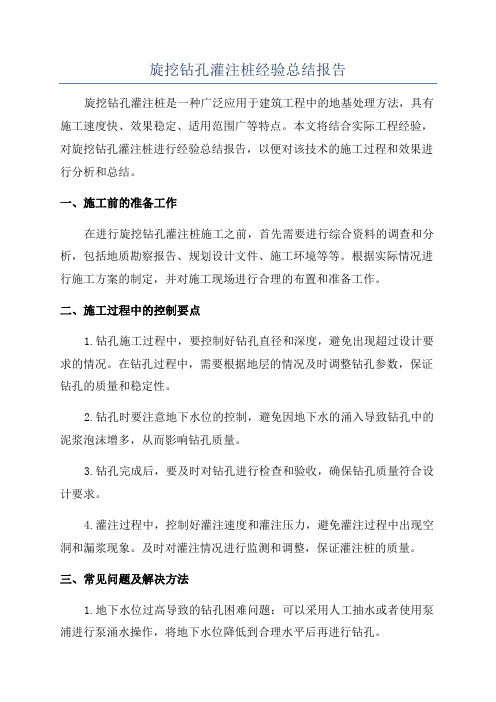
旋挖钻孔灌注桩经验总结报告旋挖钻孔灌注桩是一种广泛应用于建筑工程中的地基处理方法,具有施工速度快、效果稳定、适用范围广等特点。
本文将结合实际工程经验,对旋挖钻孔灌注桩进行经验总结报告,以便对该技术的施工过程和效果进行分析和总结。
一、施工前的准备工作在进行旋挖钻孔灌注桩施工之前,首先需要进行综合资料的调查和分析,包括地质勘察报告、规划设计文件、施工环境等等。
根据实际情况进行施工方案的制定,并对施工现场进行合理的布置和准备工作。
二、施工过程中的控制要点1.钻孔施工过程中,要控制好钻孔直径和深度,避免出现超过设计要求的情况。
在钻孔过程中,需要根据地层的情况及时调整钻孔参数,保证钻孔的质量和稳定性。
2.钻孔时要注意地下水位的控制,避免因地下水的涌入导致钻孔中的泥浆泡沫增多,从而影响钻孔质量。
3.钻孔完成后,要及时对钻孔进行检查和验收,确保钻孔质量符合设计要求。
4.灌注过程中,控制好灌注速度和灌注压力,避免灌注过程中出现空洞和漏浆现象。
及时对灌注情况进行监测和调整,保证灌注桩的质量。
三、常见问题及解决方法1.地下水位过高导致的钻孔困难问题:可以采用人工抽水或者使用泵浦进行泵涌水操作,将地下水位降低到合理水平后再进行钻孔。
2.钻孔出现地层不稳造成的灌注桩变形问题:可以采用加固杆进行辅助支撑,或者使用加固剂进行灌注桩加固,以增加灌注桩的稳定性。
3.灌注过程中出现漏浆现象的问题:可以通过调整灌注速度和灌注压力,以及合理选择灌注材料的方法来解决。
四、施工的注意事项1.施工人员要具备一定的技术水平和经验,了解各项施工参数和操作要点。
2.施工现场要严格按照设计要求和施工方案进行布置和准备。
3.施工设备要维护良好,保证正常运转。
4.施工过程中要做好安全措施,确保施工作业人员的人身安全。
五、经验总结通过多次的旋挖钻孔灌注桩施工实践,我们总结了以下经验:1.在施工前要做好充分的准备工作,包括综合资料的调查和分析、施工方案的制定等。
旋挖钻孔灌注桩施工要点
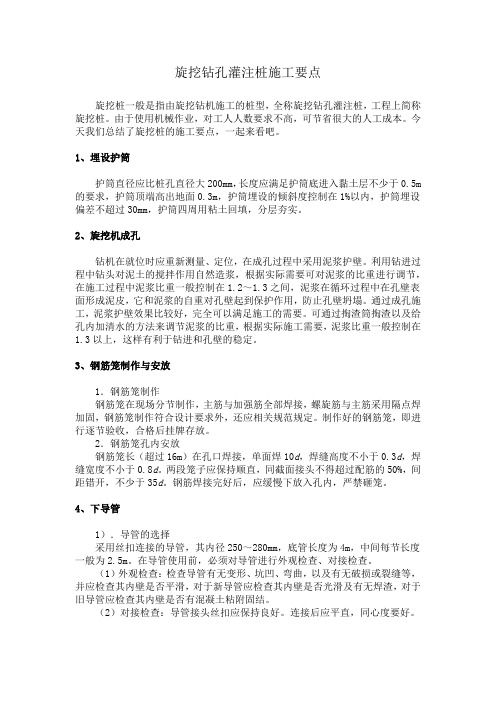
旋挖钻孔灌注桩施工要点旋挖桩一般是指由旋挖钻机施工的桩型,全称旋挖钻孔灌注桩,工程上简称旋挖桩。
由于使用机械作业,对工人人数要求不高,可节省很大的人工成本。
今天我们总结了旋挖桩的施工要点,一起来看吧。
1、埋设护筒护筒直径应比桩孔直径大200mm,长度应满足护筒底进入黏土层不少于0.5m 的要求,护筒顶端高出地面0.3m,护筒埋设的倾斜度控制在1%以内,护筒埋设偏差不超过30mm,护筒四周用粘土回填,分层夯实。
2、旋挖机成孔钻机在就位时应重新测量、定位,在成孔过程中采用泥浆护壁。
利用钻进过程中钻头对泥土的搅拌作用自然造浆,根据实际需要可对泥浆的比重进行调节,在施工过程中泥浆比重一般控制在1.2~1.3之间,泥浆在循环过程中在孔壁表面形成泥皮,它和泥浆的自重对孔壁起到保护作用,防止孔壁坍塌。
通过成孔施工,泥浆护壁效果比较好,完全可以满足施工的需要。
可通过掏渣筒掏渣以及给孔内加清水的方法来调节泥浆的比重,根据实际施工需要,泥浆比重一般控制在1.3以上,这样有利于钻进和孔壁的稳定。
3、钢筋笼制作与安放1.钢筋笼制作钢筋笼在现场分节制作,主筋与加强筋全部焊接,螺旋筋与主筋采用隔点焊加固,钢筋笼制作符合设计要求外,还应相关规范规定。
制作好的钢筋笼,即进行逐节验收,合格后挂牌存放。
2.钢筋笼孔内安放钢筋笼长(超过16m)在孔口焊接,单面焊10d,焊缝高度不小于0.3d,焊缝宽度不小于0.8d。
两段笼子应保持顺直,同截面接头不得超过配筋的50%,间距错开,不少于35d。
钢筋焊接完好后,应缓慢下放入孔内,严禁砸笼。
4、下导管1).导管的选择采用丝扣连接的导管,其内径250~280mm,底管长度为4m,中间每节长度一般为2.5m。
在导管使用前,必须对导管进行外观检查、对接检查。
(1)外观检查:检查导管有无变形、坑凹、弯曲,以及有无破损或裂缝等,并应检查其内壁是否平滑,对于新导管应检查其内壁是否光滑及有无焊渣,对于旧导管应检查其内壁是否有混凝土粘附固结。
钻孔灌注桩首件施工监理总结(4篇)

钻孔灌注桩首件施工监理总结本项目钻孔灌注桩首件工程为s338互通主线桥12#-6钻孔灌注桩,施工时间为____年____月____日至____年____月____日。
该桩设计桩径ф____m,桩顶标高____m,桩底标高-____m,桩长____m,按设计要求为摩擦桩。
施工单位采用正循环成桩法进行施工。
按照指挥部作业指导书及监理组关于钻孔灌注桩监理细则的要求,开展本标段监理工作。
1、测量放样为保证桩位符合设计及规范要求,测量监理对施工单位测量工作进行复核,并要求在桩位四周设置____个护桩以确保中心位置的准确。
2、埋设护筒,备置泥浆池首先要求护筒坚实不漏水,且内径比钻头直径大20cm以上。
埋设时应以中心桩位及四周护桩为基准,确保护筒位置正确。
填埋护筒四周时要求施工单位将土夯实,开钻之前要求施工单位要配备好沉淀池和泥浆池,并测出护筒标高。
3、钻进在开钻之前监理要检查钻机的水平,钻杆的垂直度及钻头与桩位的对应情况,并对钻具长度,钻头直径进行复核,符合要求后同意开钻。
该地区上部土层主要为粘土、亚粘土,因此泥浆制备采取的是原孔造浆。
在钻进过程中监理主要采取巡视检查,要求施工单位做好钻孔记录。
并把开钻时间、终孔时间及标高,及时通知监理,尤其是地质发生变化时要通知监理到现场进行确认并捞取渣样以便判别。
并要求施工单位不得胡乱排弃泥浆,尤其不能排入河道污染环境。
4、终孔检查首先要求施工单位自检,合格后再通知监理,监理根据钻杆长度和转盘标高计算出孔底标高,符合设计要求方同意终孔。
一次终孔结束时以测绳测孔深,当测得沉淀厚度基本符合要求后方同意提钻。
5、下钢筋笼成孔之前进行钢筋笼检查,主要检查钢筋笼的尺寸、规格,钢筋数量和焊接质量,确认合格方允许使用。
下笼之前要求先下探孔器,探孔器顺畅到底才允许下笼。
否则要求施工单位采取措施。
下放钢筋笼监理全过程旁站,对每一节焊接进行检查,直至下完。
本桩钢筋笼下放顺利,未出现意外情况。
旋挖钻孔灌注桩首桩验收总结范本
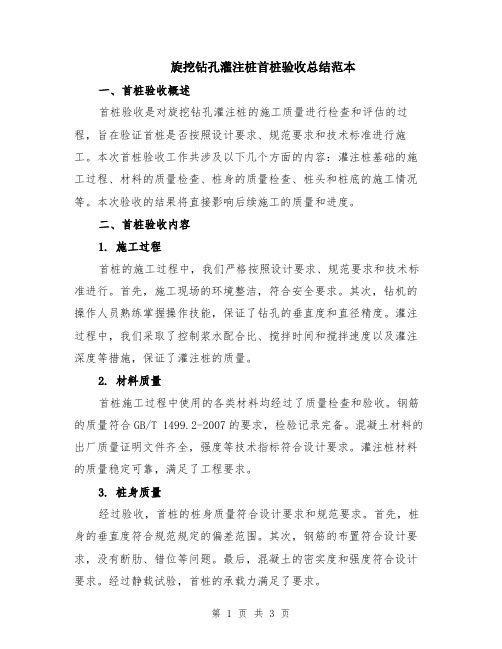
旋挖钻孔灌注桩首桩验收总结范本一、首桩验收概述首桩验收是对旋挖钻孔灌注桩的施工质量进行检查和评估的过程,旨在验证首桩是否按照设计要求、规范要求和技术标准进行施工。
本次首桩验收工作共涉及以下几个方面的内容:灌注桩基础的施工过程、材料的质量检查、桩身的质量检查、桩头和桩底的施工情况等。
本次验收的结果将直接影响后续施工的质量和进度。
二、首桩验收内容1. 施工过程首桩的施工过程中,我们严格按照设计要求、规范要求和技术标准进行。
首先,施工现场的环境整洁,符合安全要求。
其次,钻机的操作人员熟练掌握操作技能,保证了钻孔的垂直度和直径精度。
灌注过程中,我们采取了控制浆水配合比、搅拌时间和搅拌速度以及灌注深度等措施,保证了灌注桩的质量。
2. 材料质量首桩施工过程中使用的各类材料均经过了质量检查和验收。
钢筋的质量符合GB/T 1499.2-2007的要求,检验记录完备。
混凝土材料的出厂质量证明文件齐全,强度等技术指标符合设计要求。
灌注桩材料的质量稳定可靠,满足了工程要求。
3. 桩身质量经过验收,首桩的桩身质量符合设计要求和规范要求。
首先,桩身的垂直度符合规范规定的偏差范围。
其次,钢筋的布置符合设计要求,没有断肋、错位等问题。
最后,混凝土的密实度和强度符合设计要求。
经过静载试验,首桩的承载力满足了要求。
4. 桩头和桩底施工首桩的桩头和桩底的施工情况也进行了验收。
桩头的平整度、水平度和垂直度均符合规范要求。
桩底的平整度、强度和防水性能也符合要求。
经过专业测量和质量抽查,桩头和桩底的施工质量良好。
三、首桩验收结论根据我们对首桩的施工过程、材料质量、桩身质量和桩头、桩底施工的认真检查和评估,结论如下:1. 首桩的施工过程规范,符合设计要求和规范要求。
2. 使用的各类材料质量稳定可靠,符合技术标准。
3. 桩身质量良好,符合设计要求和规范要求。
4. 桩头和桩底施工质量良好,符合规范要求。
综上所述,首桩的施工质量较好,符合设计要求和规范要求。
旋挖钻钻孔灌注桩工艺性总结

1、每台钻机施工人员配备情况
序号
工种
1
机操手
2
电焊工
3
质检员
4
混凝土工
5
起重工
6
试验员
7
测量员
2、人员配置情况
每台钻机施工人员配备表
人数
备注
2
操作旋挖钻机
2
现场钢筋笼的焊接
2
现场质量检验
4
混凝土灌注
2
2
现场试验检测
4
现场测量放样
人员配置情况
序号 姓名 性别 出生年月
职务
学历
专业
专业年限
交川沟特大桥 旋挖钻施工钻孔桩工艺总结报告
一、试桩依据
(1)《新建铁路宝鸡至兰州客运专线(甘肃段)BLTJ-1标段施工招 标文件》、招标图纸及补遗(答疑)书等;
(2)《高速铁路桥涵工程施工技术指南》(铁建设[2010]241 号);
(3)《高速铁路桥涵工程施工质量验收标准》(TB 107522010);
(4)国家及相关部委颁布的法律、法规和铁道部颁布的现行设计规 范、施工规范、技术指南、验收标准及其它有关文件资料;
(5)施工现场实地勘察及周围地理环境情况; (6)《新建铁路宝鸡至兰州客运专线交川沟特大桥宝兰客专施桥 (特)20》; (7)《新建铁路宝鸡至兰州客运专线交川沟特大桥施桥参07》; (7)GB/T19001--2000质量标准体系、GB/T24001-1996环境管理体 系和GB/T28001-2001职业健康安全标准建立的质量、环境和职业健康管 理体系和《程序文件》; (8)《铁路混凝土工程施工质量验收标准》(TB 10424-2010); (9)《铁路混凝土工程钢筋机械连接技术暂行规定》 (铁建设 [2010]41号); (10)《铁路混凝土结构耐久性设计规范》(TB10005-2010); (11)《客运专线高性能混凝土暂行技术条件》 ; (12)《高速铁路工程测量规范》(TB 10601-2009); (13)《客运专线铁路工程质量安全监控要点手册》(铁道社); (14)《中华人民共和国安全生产法》; (15)《建设工程安全生产管理条例》; (16)《铁路桥涵工程施工安全技术规程》TB10303-2009;
旋挖钻孔灌注桩首桩验收总结范文
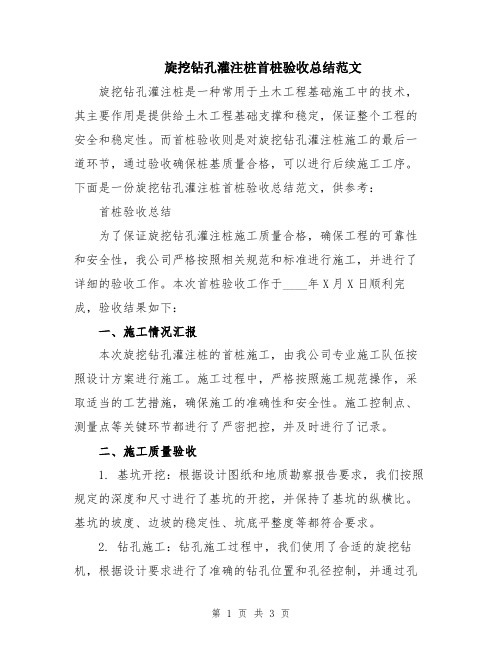
旋挖钻孔灌注桩首桩验收总结范文旋挖钻孔灌注桩是一种常用于土木工程基础施工中的技术,其主要作用是提供给土木工程基础支撑和稳定,保证整个工程的安全和稳定性。
而首桩验收则是对旋挖钻孔灌注桩施工的最后一道环节,通过验收确保桩基质量合格,可以进行后续施工工序。
下面是一份旋挖钻孔灌注桩首桩验收总结范文,供参考:首桩验收总结为了保证旋挖钻孔灌注桩施工质量合格,确保工程的可靠性和安全性,我公司严格按照相关规范和标准进行施工,并进行了详细的验收工作。
本次首桩验收工作于____年X月X日顺利完成,验收结果如下:一、施工情况汇报本次旋挖钻孔灌注桩的首桩施工,由我公司专业施工队伍按照设计方案进行施工。
施工过程中,严格按照施工规范操作,采取适当的工艺措施,确保施工的准确性和安全性。
施工控制点、测量点等关键环节都进行了严密把控,并及时进行了记录。
二、施工质量验收1. 基坑开挖:根据设计图纸和地质勘察报告要求,我们按照规定的深度和尺寸进行了基坑的开挖,并保持了基坑的纵横比。
基坑的坡度、边坡的稳定性、坑底平整度等都符合要求。
2. 钻孔施工:钻孔施工过程中,我们使用了合适的旋挖钻机,根据设计要求进行了准确的钻孔位置和孔径控制,并通过孔壁视觉检查,保证孔壁的垂直度和孔径的准确性。
在钻孔过程中,我们根据地层情况采取了适当的钻进速度和冲洗孔洞的措施,保证了孔壁的稳定性和钻孔进度的顺利进行。
3. 灌注桩施工:灌注桩施工过程中,我们严格按照设计要求,将混凝土按层灌入孔洞,并结合振捣措施,保证了混凝土的密实性和饱满度。
我们采用了合适的灌注速度和振捣频率,确保了桩身的质量和稳定性。
4. 桩身质量验收:桩身质量验收主要对灌注桩的外观质量和桩身强度进行检查。
通过外观检查,我们发现桩身表面平整光滑,没有明显的裂缝和砂浆剥离现象。
通过桩身取样,经送实验室检测,桩身的强度符合设计要求,满足设计要求。
三、验收结论经过对旋挖钻孔灌注桩首桩的详细检查和检测,确认施工质量符合设计要求和规范标准,验收合格。
旋挖钻孔灌注桩施工常见质量问题及控制措施
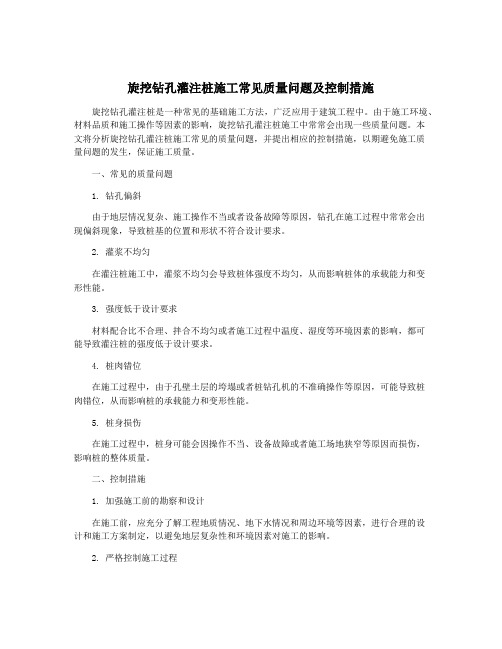
旋挖钻孔灌注桩施工常见质量问题及控制措施旋挖钻孔灌注桩是一种常见的基础施工方法,广泛应用于建筑工程中。
由于施工环境、材料品质和施工操作等因素的影响,旋挖钻孔灌注桩施工中常常会出现一些质量问题。
本文将分析旋挖钻孔灌注桩施工常见的质量问题,并提出相应的控制措施,以期避免施工质量问题的发生,保证施工质量。
一、常见的质量问题1. 钻孔偏斜由于地层情况复杂、施工操作不当或者设备故障等原因,钻孔在施工过程中常常会出现偏斜现象,导致桩基的位置和形状不符合设计要求。
2. 灌浆不均匀在灌注桩施工中,灌浆不均匀会导致桩体强度不均匀,从而影响桩体的承载能力和变形性能。
3. 强度低于设计要求材料配合比不合理、拌合不均匀或者施工过程中温度、湿度等环境因素的影响,都可能导致灌注桩的强度低于设计要求。
4. 桩肉错位在施工过程中,由于孔壁土层的垮塌或者桩钻孔机的不准确操作等原因,可能导致桩肉错位,从而影响桩的承载能力和变形性能。
5. 桩身损伤在施工过程中,桩身可能会因操作不当、设备故障或者施工场地狭窄等原因而损伤,影响桩的整体质量。
二、控制措施1. 加强施工前的勘察和设计在施工前,应充分了解工程地质情况、地下水情况和周边环境等因素,进行合理的设计和施工方案制定,以避免地层复杂性和环境因素对施工的影响。
2. 严格控制施工过程在施工过程中,应严格按照设计要求和施工方案进行操作,保证钻孔的垂直度和位置准确度,确保灌浆的均匀性和灌注桩的整体质量。
3. 合理选择材料和配合比在施工中应选择优质的水泥、骨料、砂等材料,并严格按照设计要求的配合比进行拌合,保证灌浆的强度和均匀性。
在施工过程中,应严格控制施工场地的温度、湿度等环境因素,避免影响材料的强度和灌浆的均匀性。
5. 强化施工监理和质量检测在施工过程中,应加强对施工的监理和质量检测,及时发现问题并进行整改,确保施工质量符合设计要求。
三、总结旋挖钻孔灌注桩是一种常见的基础工程施工方法,但在施工过程中常常会出现一些质量问题。
旋挖工程年度个人总结报告
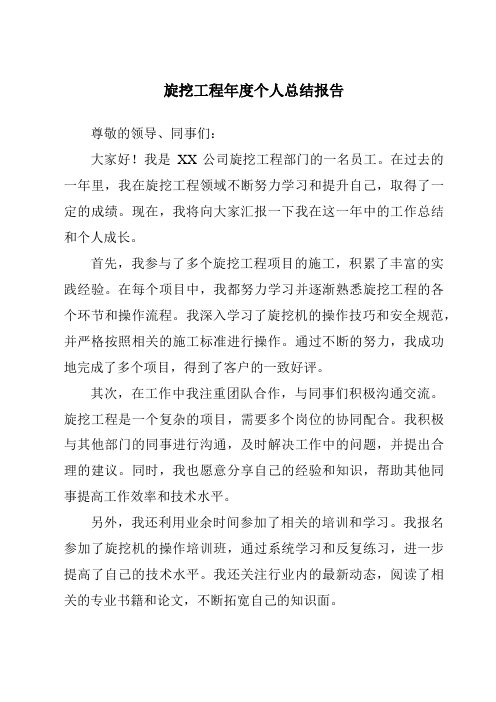
旋挖工程年度个人总结报告
尊敬的领导、同事们:
大家好!我是XX公司旋挖工程部门的一名员工。
在过去的一年里,我在旋挖工程领域不断努力学习和提升自己,取得了一定的成绩。
现在,我将向大家汇报一下我在这一年中的工作总结和个人成长。
首先,我参与了多个旋挖工程项目的施工,积累了丰富的实践经验。
在每个项目中,我都努力学习并逐渐熟悉旋挖工程的各个环节和操作流程。
我深入学习了旋挖机的操作技巧和安全规范,并严格按照相关的施工标准进行操作。
通过不断的努力,我成功地完成了多个项目,得到了客户的一致好评。
其次,在工作中我注重团队合作,与同事们积极沟通交流。
旋挖工程是一个复杂的项目,需要多个岗位的协同配合。
我积极与其他部门的同事进行沟通,及时解决工作中的问题,并提出合理的建议。
同时,我也愿意分享自己的经验和知识,帮助其他同事提高工作效率和技术水平。
另外,我还利用业余时间参加了相关的培训和学习。
我报名参加了旋挖机的操作培训班,通过系统学习和反复练习,进一步提高了自己的技术水平。
我还关注行业内的最新动态,阅读了相关的专业书籍和论文,不断拓宽自己的知识面。
在过去的一年中,我也遇到了一些困难和挑战。
有时候,工程进度紧迫,压力较大。
但是,我始终保持积极的态度,勇于面对困难,并通过与同事的协作和学习,解决了许多问题。
同时,我也不断反思和总结自己的不足之处,努力改进和提高。
最后,我感谢公司给予我这一年来的培养和信任。
我将继续努力学习,提升自己的专业技能,为公司的发展做出更大的贡献。
谢谢大家!。
桩基首件总结报告
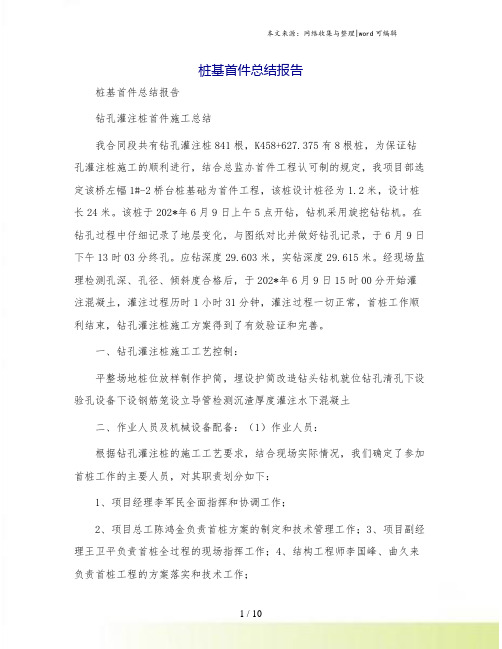
桩基首件总结报告桩基首件总结报告钻孔灌注桩首件施工总结我合同段共有钻孔灌注桩841根,K458+627.375有8根桩,为保证钻孔灌注桩施工的顺利进行,结合总监办首件工程认可制的规定,我项目部选定该桥左幅1#-2桥台桩基础为首件工程,该桩设计桩径为1.2米,设计桩长24米。
该桩于202*年6月9日上午5点开钻,钻机采用旋挖钻钻机。
在钻孔过程中仔细记录了地层变化,与图纸对比并做好钻孔记录,于6月9日下午13时03分终孔。
应钻深度29.603米,实钻深度29.615米。
经现场监理检测孔深、孔径、倾斜度合格后,于202*年6月9日15时00分开始灌注混凝土,灌注过程历时1小时31分钟,灌注过程一切正常,首桩工作顺利结束,钻孔灌注桩施工方案得到了有效验证和完善。
一、钻孔灌注桩施工工艺控制:平整场地桩位放样制作护筒,埋设护筒改造钻头钻机就位钻孔清孔下设验孔设备下设钢筋笼设立导管检测沉渣厚度灌注水下混凝土二、作业人员及机械设备配备:(1)作业人员:根据钻孔灌注桩的施工工艺要求,结合现场实际情况,我们确定了参加首桩工作的主要人员,对其职责划分如下:1、项目经理李军民全面指挥和协调工作;2、项目总工陈鸿金负责首桩方案的制定和技术管理工作;3、项目副经理王卫平负责首桩全过程的现场指挥工作;4、结构工程师李国峰、曲久来负责首桩工程的方案落实和技术工作;5、质检负责人张大鹏负责首桩全过程的质量检测工作;6、试验副主任齐志负责组织首桩全过程的试验检测工作;7、拌合站负责人张殿义负责砼的拌合工作;8、技术员南小辉、张春利、负责首桩全过程的施工放样及施工记录工作。
9、技术工人10人,普工15人。
灌注桩开工之前由质检部配合总工编制了详细的钻孔灌注桩作业指导书,具体指导灌注桩施工,作业指导书中含概了施工工艺、质量保证措施、安全保证措施以及文明施工等内容,并组织现场施工人员进行了系统的学习,确保了灌注桩的工程能够顺利进行。
(2)、机械设备配备施工的主要机械设备有SD-20多功能旋挖钻机1台,混凝土搅拌机HZS120型2套,混凝土罐车4台(8m3),汽车吊1辆(20t),电焊机4台,数控钢筋笼成型机1台,数控弯曲中心1台,龙门吊(10T)2台,钢筋切断机2台。
2024年旋挖钻孔灌注桩首桩验收总结
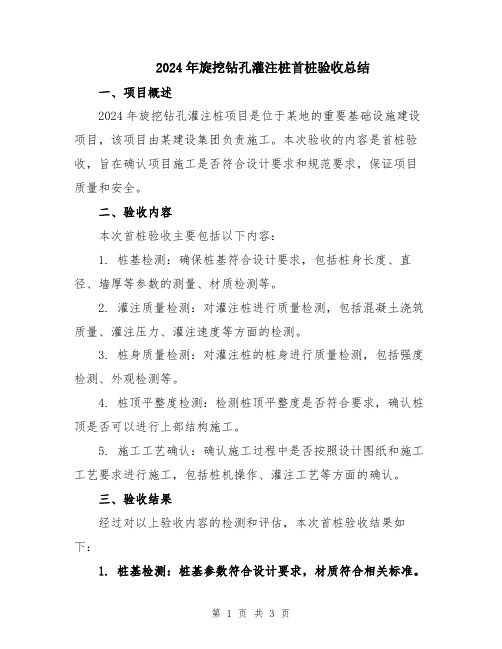
2024年旋挖钻孔灌注桩首桩验收总结一、项目概述2024年旋挖钻孔灌注桩项目是位于某地的重要基础设施建设项目,该项目由某建设集团负责施工。
本次验收的内容是首桩验收,旨在确认项目施工是否符合设计要求和规范要求,保证项目质量和安全。
二、验收内容本次首桩验收主要包括以下内容:1. 桩基检测:确保桩基符合设计要求,包括桩身长度、直径、墙厚等参数的测量、材质检测等。
2. 灌注质量检测:对灌注桩进行质量检测,包括混凝土浇筑质量、灌注压力、灌注速度等方面的检测。
3. 桩身质量检测:对灌注桩的桩身进行质量检测,包括强度检测、外观检测等。
4. 桩顶平整度检测:检测桩顶平整度是否符合要求,确认桩顶是否可以进行上部结构施工。
5. 施工工艺确认:确认施工过程中是否按照设计图纸和施工工艺要求进行施工,包括桩机操作、灌注工艺等方面的确认。
三、验收结果经过对以上验收内容的检测和评估,本次首桩验收结果如下:1. 桩基检测:桩基参数符合设计要求,材质符合相关标准。
2. 灌注质量检测:混凝土浇筑质量良好,灌注压力和速度符合规范要求。
3. 桩身质量检测:桩身强度符合设计要求,外观无明显缺陷。
4. 桩顶平整度检测:桩顶平整度符合要求,可以进行上部结构施工。
5. 施工工艺确认:施工过程中按照设计图纸和施工工艺要求进行施工,操作规范、流程清晰。
四、存在问题与建议经过本次首桩验收,发现以下问题:1. 某些测量工具的精度有待提高,对测量结果的准确性有一定影响。
2. 灌注过程中,灌注速度存在较大波动,需要进一步优化控制。
3. 某些桩身表面存在细微的裂缝和麻面现象,需要加强施工质量的把控和监督。
针对以上问题,提出如下建议:1. 提升测量工具的精度,使用更加准确的测量仪器进行桩基参数测量,以确保测量结果的准确性。
2. 在灌注过程中加强施工监督,稳定灌注压力和速度,避免造成灌注不均匀的情况。
3. 对施工工艺进行进一步优化,加强施工过程中的质量把控,避免出现桩身表面裂缝和麻面现象。
钻孔灌注桩首件总结报告

钻孔灌注桩首件总结报告中环快速路工业园区段工程八标段宏润建设集团有限公司中环快速路工业园区段工程标段八项目经理部编制人:审核人:编制日期:目录1 首件工程概况 ................................................ ................................................... .. (1)工程简介 ................................................ ................................................... ....................... 1 地质情况 ................................................ ................................................... ....................... 1 2 施工目标 ................................................ ................................................... . (1)质量目................................................... ........................ 1 安全目标 ................................................ ................................................... ........................ 1 环保目标 ................................................ ................................................... ....................... 1 首件目的 ................................................ ................................................... ....................... 1 3 编制依据 ................................................ ................................................... .................................. 2 4 施工准备 ................................................ ................................................... . (2)水、电及现场布置 ................................................ ................................................... ....... 2 技术准................................................... ....................... 3 试验工作 ................................................ ................................................... ....................... 3 5 施工部署 ................................................ ................................................... . (3)人员配置 ................................................ ................................................... ........................ 3 材料配置 ................................................ ................................................... ....................... 4 施工设备配置 ................................................ ................................................... ............... 4 施工安排 ................................................ ................................................... ....................... 4 施工现场管理体系网 (4)6 首件施工过程 ................................................ ................................................... .......................... 5 7 首件工程中存在的不足 ................................................ ................................................... .......... 7 8 下步施工注意事项和需要进一步改进的地方 ................................................ ......................... 8 9 综合评价及总结 ................................................ ................................................... . (8)为了保证工程质量优质,质量目标明确,减少盲目施工,施工前确定标准的施工工艺,施工工艺通过首件施工确定。
桩基旋挖钻首件工程总结

K180+580放牧通道0#-0桩基首件施工总结为了使桥梁钻孔灌注桩的施工能够达到设计和规范要求, 我项目部于 2012年5月25日~2012 年5月26日对K180+580放牧通道0#-0桩进行了桩基础首件施工, 并在施工中对试验桩各个工序进行了控制和检测, 其结果符合设计和规范要求, 现将钻孔灌注桩试验桩总结报告如下: 一、施工机械人员的配备梁板预制对本桥的施工有重要的作用, 做好本分项工程是本桥的一个关键环节, 我项目部由项目领导统一安排, 具体如下:施工总负责: 张丛明技术总负责: 陈中略现场负责人: 周超技术员: 冯伟、陈彪质检工程师: 钟康保试验员: 黎瑞波现场专职安全员: 朱熙施工班组长: 王登荣本工程钻孔灌注桩钢筋笼采用在钢筋加工场加工, 钢筋笼成型后用平板车运输至现场后吊车下笼;混凝土采用集中拌和。
K180+580放牧通道0#-0桩实际投入的主要设备: 旋挖钻钻机1台, JS1500拌合机1台, X400型电焊机4台, 25T吊车1台, 日立60挖掘机1台, 徕卡全站仪1台, DS3水准仪1台、8m3混凝土运输车4台。
实际投入的人员有42人, 其中技术管理人员7人, 机械操作人员及驾驶人员12名, 熟练工9人、钢筋工14人。
二、施工过程1.准备工作:根据设计图纸提供的桩号坐标于2012年5月25日采用全站仪进行测量放样, 定出各个桩位并打上木桩, 再钉上小铁钉并作明显标志防止施工中破坏;在距桩中心约2m处安全地带设置十字形护桩, 用混凝土埋护, 防止移动, 便于校核。
在钻机就位后用水准仪测定护筒标高, 并计算出设计孔深以便在施工中用校验好的测绳控制钻孔深度。
根据当地地质情况, 护筒用6mm的钢板制作, 其内径为1.4m, 高度3m。
为增加刚度防止变形, 在护筒上、下端口和中部外侧各焊一道加劲肋。
其底部埋置在地表下2.7m中, 护筒顶高出原地面0.3m。
护筒埋设采用挖埋法, 开挖所要埋护筒的土层后, 将护筒放入其中。
2024年旋挖钻孔灌注桩首桩验收总结(3篇)

2024年旋挖钻孔灌注桩首桩验收总结刚刚进行的____年旋挖钻孔灌注桩首桩验收工作是一次非常成功的经验,旋挖钻孔灌注桩作为一种新兴的桥梁基础施工技术,正在逐渐被广泛应用于各类桥梁建设项目中。
本次验收总结从设计准备、施工组织、质量控制和安全管理等方面进行了详细分析,总结了验收工作中存在的问题和亮点,并提出了一些建议和改进措施。
设计准备方面,本次验收首先重点关注了工程图纸的合理性和施工方案的可行性。
经过设计师和施工单位的多次沟通和讨论,最终确定了合适的设计方案。
然后,我们对施工单位进行了详细的考察和评估,确保施工单位具备必要的技术和资质。
此外,在设计准备阶段还注重对施工材料的选择和采购,确保施工材料的质量符合标准要求。
施工组织方面,我们注重了对施工队伍的培训和管理。
由于旋挖钻孔灌注桩属于一种较为新颖的施工技术,施工队伍中的工人们对其不够熟悉,因此在施工前,我们组织了一次专题培训,对施工工艺和注意事项进行了详细讲解。
此外,在施工过程中,我们提前准备了足够的施工设备,确保施工进度和质量的稳定。
质量控制方面,我们注重了每个施工环节的监控和记录。
首先,我们要求施工单位在施工前对工地进行详细勘测,确保施工的准确性和可行性。
其次,我们要求施工单位在施工过程中严格按照设计方案和标准要求进行施工,对施工过程中的关键环节进行了严格监控。
最后,我们对施工结束后的桩身进行了全面检测,确保桩身的强度和稳定性。
安全管理方面,我们注重了现场安全和工人的安全教育。
在施工现场,我们设置了安全警示标志,落实了安全管理责任,定期组织安全检查,确保施工现场的安全和有序。
同时,我们要求施工单位对工人进行了安全教育和培训,提高了工人们的安全意识和操作技能。
在本次验收中,我们取得了很多亮点和成功经验。
首先,施工单位严格按照设计方案和施工要求进行了施工,保证了桩身的质量和安全。
其次,我们注重了施工过程中的质量监控和记录,确保了施工质量的稳定。
最后,我们组织了安全教育和培训,确保施工现场的安全和工人的安全。
旋挖钻孔灌注桩首桩验收总结样本(2篇)
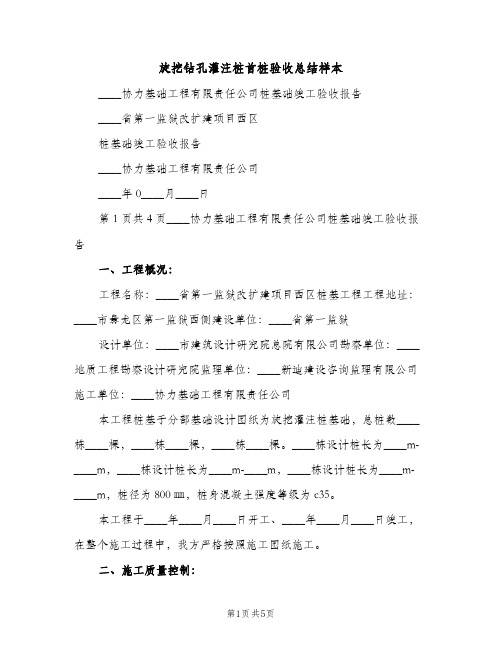
旋挖钻孔灌注桩首桩验收总结样本____协力基础工程有限责任公司桩基础竣工验收报告____省第一监狱改扩建项目西区桩基础竣工验收报告____协力基础工程有限责任公司____年0____月____日第1页共4页____协力基础工程有限责任公司桩基础竣工验收报告一、工程概况:工程名称:____省第一监狱改扩建项目西区桩基工程工程地址:____市盘龙区第一监狱西侧建设单位:____省第一监狱设计单位:____市建筑设计研究院总院有限公司勘察单位:____地质工程勘察设计研究院监理单位:____新迪建设咨询监理有限公司施工单位:____协力基础工程有限责任公司本工程桩基子分部基础设计图纸为旋挖灌注桩基础,总桩数____栋____棵,____栋____棵,____栋____棵。
____栋设计桩长为____m-____m,____栋设计桩长为____m-____m,____栋设计桩长为____m-____m,桩径为800㎜,桩身混凝土强度等级为c35。
本工程于____年____月____日开工、____年____月____日竣工,在整个施工过程中,我方严格按照施工图纸施工。
二、施工质量控制:1、本工程所有材料进场时,由项目部取样员及监理单位见证员按规范规定对现场的材料进行见证取样送检,并及时上报出厂合格证及检验报告。
2、进场时,按建设单位提供的各主要控制点逐一引测到场地周围(不受施工影响且不受破坏的建筑物、地面等部位)。
并加以妥善保护,经建设单位代表及监理代表复核验收合格后,再对桩位施放。
在施工过程中再次对每个桩位逐根进行复核。
第2页共4页____协力基础工程有限责任公司桩基础竣工验收报告3、桩孔成孔以后,我方立即认真自检每段工序,自检合格后通知现场甲方、监理进行检复查,凡建设、监理单位指出不合格的工序我方立即整改,经整改检查合格才进行下一道工序施工。
4、在浇筑混凝土之前,并安排专人对每棵桩芯在砼浇捣前清理孔底虚土杂物,以便影响桩的质量。
旋挖灌注桩试桩总结

旋挖灌注桩试桩总结一、引言旋挖灌注桩是一种常用的地基处理方法,通过旋转挖掘机进行钻孔,并在孔内注入混凝土形成桩体,具有承载能力强、施工速度快等优点。
为了确保施工质量,通常需要进行试桩来验证设计参数和施工工艺,本文将对旋挖灌注桩试桩的实施过程和结果进行总结。
二、试桩前的准备工作1.设计参数的确定:根据工程的要求和地质条件,确定试桩的孔径、桩长、桩间距等参数。
2.试桩方案的制定:根据设计参数,制定试桩的施工方案,包括施工工艺、设备选型等。
3.施工材料的准备:准备好所需的混凝土、钢筋等施工材料,并进行质量检验。
三、试桩的实施过程1.孔洞的钻掘:根据设计要求,使用旋挖钻机进行孔洞的钻掘,控制钻孔的位置、方向和倾斜度。
2.孔洞清理:将钻孔中的杂物清理干净,确保孔洞内壁光滑,便于混凝土的浇注。
3.钢筋的布置:根据设计要求,在孔洞中布置钢筋,确保钢筋的位置准确,并与孔壁之间有一定的间隙。
4.混凝土的浇注:使用混凝土搅拌站将混凝土输送至孔洞中,同时使用振捣器进行振捣,以确保混凝土的密实性。
5.桩顶处理:在混凝土浇注完成后,对桩顶进行修整,使其符合设计要求。
四、试桩结果分析1.桩身质量:通过对试桩的观测和检测,可以评估桩身的质量,包括桩长、桩径、桩身的垂直度等。
2.桩端承载力:通过对试桩的静载试验或动力触探试验,可以评估桩端的承载力,判断桩身的质量是否满足设计要求。
3.桩身围护效果:通过对试桩的孔隙水压力的观测,可以评估灌注桩的围护效果,判断桩身的密实性和抗渗性能。
五、问题及解决方案在试桩过程中,可能会遇到一些问题,如孔洞塌方、混凝土浇注不均匀等,需要及时采取措施进行解决,确保试桩的顺利进行。
六、优缺点分析旋挖灌注桩试桩的优点包括施工速度快、承载能力强等;缺点包括施工设备较大、对土质要求高等。
七、结论通过旋挖灌注桩试桩的实施和结果分析,可以评估设计参数和施工工艺的合理性,为后续施工提供参考和改进的依据。
八、参考文献[1] XX. 旋挖灌注桩试桩技术研究[D]. XX大学,20XX.[2] XX. 旋挖灌注桩施工手册[M]. XX出版社,20XX.(注:本文仅供参考,具体内容和结构可根据实际情况进行调整)。
旋挖钻钻孔灌注桩施工总结

旋挖钻钻孔灌注桩施工总结我项目桩基施工主要采用旋挖钻机施工,旋挖钻机施工是钻孔灌注桩施工中一种较先进的施工方法,该施工方法的主要特点是施工效率高.旋挖钻机因其具有程控速度快,移动灵活方便,产生废浆少,低噪音,环境污染小、适应地层较广泛等特点,在桥梁桩基施工中得到广泛应用,适用于工期要求紧的工程项目,在特大桥施工发挥着重要作用。
一、工程概况我项目基础大多采用钻孔桩基础,桩基直径多为1。
25m,少量1.5 m,根据不同跨度和地质条件,单个承台的桩基数量多采用6根,部分采用8根。
桩长为8m~18m, 比较适用旋挖钻机施工。
二、施工流程1、旋挖钻成孔桩基施工工艺旋挖钻成孔桩基施工工艺详见以下“旋挖钻施工工艺流程图”:2、旋挖钻成孔施工步骤(1)桩位放样合理布置施工场地,先平整场地、清除杂物、换除软土、夯打密实。
在进行场地整平后,组织有资格的测量放样人员,将所有桩位放出,钉好十字保护桩,做好测量复核。
(2)埋设钢护筒桩基定位后,根据桩定位点拉十字线钉放四个控制桩,以四个控制桩为基准埋设钢护筒,为了保护孔口防止坍塌,形成孔内水头和定位导向,护筒的埋设是旋挖作业中的关键。
护筒选用5㎜~10mm厚钢板卷制而成,护筒内径为设计桩径+20~+40cm,高度2.0m,护筒埋设时顶端高出地面0.3m。
上部开设2个吊装孔,护筒埋设时,由人工、机械配合完成,主要利用钻机旋挖斗将其静力压入土中,其顶端应高出地面20cm,并保持水平,埋设深度1。
8 m,护筒中心竖直线应与桩中心线重合,平面位置允许偏差为10cm,倾斜度的偏差不大于1%。
(3)钻机定位在桩位复核正确,护筒埋设符合要求,护筒、地坪标高已测定后钻机就位;钻机定位要准确、水平、垂直、稳固,钻机导杆中心线、回旋盘中心线、护筒中心线应保持在同一直线。
旋挖钻机就位后,利用自动控制系统调整其垂直度,钻机安放定位时,要机座平整,机塔垂直,转盘(钻头)中心与护筒十字线中心对正后,进行钻孔。
2024年旋挖钻孔灌注桩首桩验收总结(二篇)
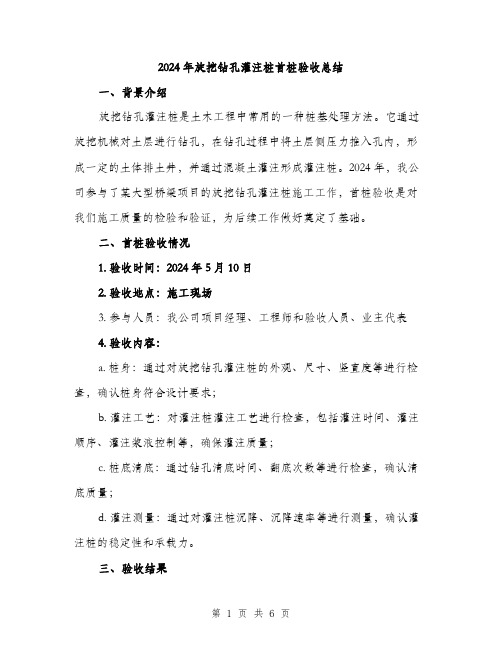
2024年旋挖钻孔灌注桩首桩验收总结一、背景介绍旋挖钻孔灌注桩是土木工程中常用的一种桩基处理方法。
它通过旋挖机械对土层进行钻孔,在钻孔过程中将土层侧压力推入孔内,形成一定的土体排土井,并通过混凝土灌注形成灌注桩。
2024年,我公司参与了某大型桥梁项目的旋挖钻孔灌注桩施工工作,首桩验收是对我们施工质量的检验和验证,为后续工作做好奠定了基础。
二、首桩验收情况1. 验收时间:2024年5月10日2. 验收地点:施工现场3. 参与人员:我公司项目经理、工程师和验收人员、业主代表4. 验收内容:a. 桩身:通过对旋挖钻孔灌注桩的外观、尺寸、竖直度等进行检查,确认桩身符合设计要求;b. 灌注工艺:对灌注桩灌注工艺进行检查,包括灌注时间、灌注顺序、灌注浆液控制等,确保灌注质量;c. 桩底清底:通过钻孔清底时间、翻底次数等进行检查,确认清底质量;d. 灌注测量:通过对灌注桩沉降、沉降速率等进行测量,确认灌注桩的稳定性和承载力。
三、验收结果经过全面的检查和测试,首桩验收结果如下:1. 桩身:桩身外观光滑,尺寸精确,没有明显的裂缝和变形现象。
竖直度在设计要求的允许范围内,满足施工要求。
2. 灌注工艺:灌注桩的灌注工艺符合设计要求,灌注时间控制得当,浆液质量稳定,没有出现泥浆回流和漏浆现象。
3. 桩底清底:桩底清底时间合理,翻底次数充分,确保了桩底的平整和清理彻底。
4. 灌注测量:灌注桩的沉降量较小,沉降速率平稳,表明桩的稳定性和承载力良好。
四、问题及解决措施在首桩验收过程中,我们也发现了一些问题,但及时采取了解决措施,确保了工程的顺利进行。
1. 桩身尺寸偏差较大:造成尺寸偏差的原因是施工人员在钻孔过程中没有严格按照设计要求控制钻孔直径。
解决措施是加强施工人员的培训和质量监督,确保钻孔的准确性和一致性。
2. 灌注时间不足:造成灌注时间不足的原因是施工人员对于灌注工艺掌握不足。
解决措施是增加施工人员的技术培训和指导,确保灌注时间的准确掌握。
旋挖钻孔灌注桩首桩验收总结

旋挖钻孔灌注桩首桩验收总结一、引言旋挖钻孔灌注桩是一种在土体中,通过旋转钻杆驱动钻头进行钻孔,然后注入水泥浆或混凝土的桩基施工方法。
其作为深基坑工程中常用的桩基类型之一,具有施工便捷、质量可控等优点。
本文将对旋挖钻孔灌注桩首桩验收进行总结与分析。
二、验收目的首桩验收是对旋挖钻孔灌注桩施工质量进行验证与评估的过程。
通过验收,可以确保施工符合设计要求,从而保证工程的安全性和稳定性。
本次验收的目的是评估首桩的技术参数与工程质量,为后续施工提供参考依据。
三、验收内容1. 钻孔质量评估:对钻孔形状、坚实程度、垂直度等进行检查,并进行定量评估。
2. 灌注质量评估:对灌注过程控制情况进行评估,包括水泥浆或混凝土的配比、搅拌均匀度、注浆速度等指标。
3. 强度检测:采取取样方式进行强度试验,评估桩体的抗压强度。
4. 其他要求:如检测桩身的沉降情况、表面平整度等。
四、验收结果1. 钻孔质量评估:首桩钻孔形状整齐,直径和深度符合设计要求。
钻孔坚实程度良好,无明显松动情况。
垂直度满足施工要求。
2. 灌注质量评估:灌注过程中,水泥浆和混凝土的配比准确,搅拌均匀度良好,无分层现象。
注浆速度适量,未出现漏浆或渗漏现象。
3. 强度检测:取样试验结果显示,首桩桩体强度满足设计要求,抗压强度达到预期数值。
4. 其他要求:首桩桩身未发现沉降情况,表面平整度良好,无明显缺陷。
五、验收结论通过对旋挖钻孔灌注桩首桩的验收评估,结合相关数据与检测结果,得到如下结论:。
- 1、下载文档前请自行甄别文档内容的完整性,平台不提供额外的编辑、内容补充、找答案等附加服务。
- 2、"仅部分预览"的文档,不可在线预览部分如存在完整性等问题,可反馈申请退款(可完整预览的文档不适用该条件!)。
- 3、如文档侵犯您的权益,请联系客服反馈,我们会尽快为您处理(人工客服工作时间:9:00-18:30)。
旋挖钻钻孔灌注桩施工总结我项目桩基施工主要采用旋挖钻机施工,旋挖钻机施工是钻孔灌注桩施工中一种较先进的施工方法,该施工方法的主要特点是施工效率高。
旋挖钻机因其具有程控速度快,移动灵活方便,产生废浆少,低噪音,环境污染小、适应地层较广泛等特点,在桥梁桩基施工中得到广泛应用,适用于工期要求紧的工程项目,在特大桥施工发挥着重要作用。
一、工程概况我项目基础大多采用钻孔桩基础,桩基直径多为1.25m,少量1.5 m,根据不同跨度和地质条件,单个承台的桩基数量多采用6根,部分采用8根。
桩长为8m~18m,比较适用旋挖钻机施工。
二、施工流程1、旋挖钻成孔桩基施工工艺旋挖钻成孔桩基施工工艺详见以下“旋挖钻施工工艺流程图”:2、旋挖钻成孔施工步骤(1)桩位放样合理布置施工场地,先平整场地、清除杂物、换除软土、夯打密实。
在进行场地整平后,组织有资格的测量放样人员,将所有桩位放出,钉好十字保护桩,做好测量复核。
(2)埋设钢护筒桩基定位后,根据桩定位点拉十字线钉放四个控制桩,以四个控制桩为基准埋设钢护筒,为了保护孔口防止坍塌,形成孔内水头和定位导向,护筒的埋设是旋挖作业中的关键。
护筒选用5㎜~10mm厚钢板卷制而成,护筒内径为设计桩径+20~+40cm,高度2.0m,护筒埋设时顶端高出地面0.3m。
上部开设2个吊装孔,护筒埋设时,由人工、机械配合完成,主要利用钻机旋挖斗将其静力压入土中,其顶端应高出地面20cm,并保持水平,埋设深度1.8 m,护筒中心竖直线应与桩中心线重合,平面位置允许偏差为10cm,倾斜度的偏差不大于1%。
(3)钻机定位在桩位复核正确,护筒埋设符合要求,护筒、地坪标高已测定后钻机就位;钻机定位要准确、水平、垂直、稳固,钻机导杆中心线、回旋盘中心线、护筒中心线应保持在同一直线。
旋挖钻机就位后,利用自动控制系统调整其垂直度,钻机安放定位时,要机座平整,机塔垂直,转盘(钻头)中心与护筒十字线中心对正后,进行钻孔。
(4)钻进成孔钻孔过程中根据地质情况控制进尺速度,钻孔施工中要常检查钻杆的垂直度、钻头直径、钻头磨损情况及钻机作业平台的稳定,保证钻机平整、稳固,严防桩孔倾斜及塌孔等事故的发生。
成孔后需通知驻地监理工程师认可,方可经行下道工序。
3、钢筋笼制作及安装(1)钢筋骨架的吊放①钢筋的种类、型号及直径应经检查须符合设计要求,钢筋骨架制作完毕应进行检查。
②长桩骨架宜根据吊装条件分段进行制作。
分段焊接时,钢筋焊接接头应错开,达到设计及规范。
为尽量缩短焊接时间,规定可采用几台焊接机同时进行,焊接质量(应经监理检查)必须满足规范要求。
③钢筋骨架在运输和吊放过程中要采取措施防止变形。
如果刚度不足,可在骨架内每隔4m设置一个可拆卸的十字形临时加劲架。
④在钢筋骨架外侧四周设置控制保护层厚度的垫块,竖向间隔2m,横向周围不少于4个。
在吊放过程中发现保护层垫块掉落,在下放前要及时补上。
⑤骨架顶端可焊四个吊环(吊环钢筋采用未经冷拉的Ⅰ级钢筋),保证钢筋骨架上下标高符合设计要求。
⑥骨架入孔采用吊车,按骨架长度的编号入孔。
下放时,要确保位置正确,缓慢平稳地进行,防止扭曲变形和碰撞孔壁。
4、灌注桩基混凝土灌注桩基砼是钻孔桩施工的重要工序,在灌注混凝土前应对孔径、孔深、孔型、渗水量全部检查并报监理工程师,经检验合格后方可灌注混凝土,连续灌注的时间控制在初凝时间内。
干孔桩桩砼灌注工艺如下:⑴混凝土由拌和站集中拌制,灌注时要提前向拌和站提供混凝土用量、混凝土标号、准确的时间、施工地点及使用部位。
搅拌站应根据项目经理部中心试验室提供的混凝土配合比严格控制。
混凝土拌和物应具有良好的和易性,在运输和灌注过程中应无明显离析、泌水现象,灌注时应保持足够的流动性。
混凝土拌和物运至灌注地点时,应检查其均匀性和测定坍落度(坍落度宜为180~220mm),并及时做好记录。
如不符合要求时,应进行二次拌和,二次拌和后仍不符合要求时,不得使用。
⑵灌注支架采用移动式的,事先拼装好,用时移至孔口,以悬挂串筒,漏斗底口。
从高处直接倾卸时,其自由倾落高度一般不宜超过2米以不发生离析为度。
当倾落高度超过2米时,应通过串筒、溜管或震动溜管等设施下落;倾落高度超过10米时,并应设置减速装置。
⑶混凝土分层浇筑,分层厚度控制在30~45cm。
振捣采用50插入式振动器,振动器的振动深度一般不超过棒长度2/3~3/4倍,振动时要快插慢拔,不断上下移动振动棒,以便捣实均匀,减少混凝土表面气泡。
振动棒插入下层混凝土中5~10cm,移动间距不超过40cm,对每一个振动部位,振动到该部位混凝土密实为止,即混凝土不再冒出气泡。
⑷对于渗水量过大或桩身较长,混凝土振捣操作有困难时,可采用水下混凝土方法灌注。
水下混凝土浇灌方法如下:(1)混凝土由拌和站集中拌制,灌注时要提前向拌和站提供混凝土用量、混凝土标号、准确的时间、施工地点及使用部位。
搅拌站应根据项目经理部中心试验室提供的混凝土配合比严格控制。
混凝土拌和物应具有良好的和易性,在运输和灌注过程中应无明显离析、泌水现象,灌注时应保持足够的流动性。
混凝土拌和物运至灌注地点时,应检查其均匀性和测定坍落度(坍落度宜为180~220mm),并及时做好记录。
如不符合要求时,应进行二次拌和,二次拌和后仍不符合要求时,不得使用。
(2)首批灌注混凝土的数量应能满足导管首次埋置深度(≥1.0m且<3m)和填充导管底部的需要。
首批混凝土拌和物下落后,应连续快速地进行灌注,中途不应停顿,要尽量缩短灌注时间。
(3)在灌注过程中,应经常用标有尺度的测绳挂圆锥形测深锤,测探混凝土面上升高度(应派二人进行测探,取平均值),及时提拔导管,调整导管的埋置深度控制在2~6m范围内。
任何时候,都应确保埋管不小于2m的要求。
(4)当砼面升到钢筋骨架下端时,为防止钢筋骨架上浮,可采取以下措施:可采取在钢筋骨架上口四周用钢管套上,顶在钻架上固定等措施来阻止其上浮。
尽量缩短砼总的灌注时间,防止顶层砼进入钢筋骨架时,砼的流动性过小。
当孔内砼面进入钢筋骨架底口4m以上时,适当提高导管,减少导管埋置深度(不得小于2m),以保证骨架在导管底口以下的埋置深度,从而增加砼对钢筋骨架的握裹力。
导管提升到高于骨架底部2m以上,即可恢复灌注速度。
(5)在灌注过程中,应经常注意观察管内混凝土下降和孔内水位升降情况,并注意保持孔内排水。
(6)导管提升过程中要注意尽量居中缓慢提升,防止挂卡钢筋骨架。
并尽可能缩短导管的拆除时间。
当导管提升到法兰接头露出孔口以上有一定高度,可拆除1节和2节导管,(视每节导管和工作平台距孔口高度而定)。
此时,暂停灌注,先取走漏斗,重新卡牢井口的导管,然后松开导管的接头螺栓,同时将起吊导管用的钓钩挂到待拆的导管上端的吊环,待螺栓全部拆除后,吊起待拆的导管,徐徐放在地上,然后将漏斗重新插入井口导管内,校好位置,继续灌注。
拆除导管动作要快,时间一般不宜超过15分钟,要防止螺栓.橡胶垫和工具等掉入孔中,并注意安全。
已拆下的管节要立即冲洗干净,堆放整齐。
在灌注过程中,当导管内砼不满含有空气时,后续砼要徐徐灌入,不可整斗地灌入漏斗和导管,以免在导管内形成高压气囊,挤出管节间的橡皮垫,而使导管漏水。
在灌注过程中,应防止污染环境和河流。
(7)灌注的桩顶标高应比设计高0.8-1m,以保证混凝土强度,多余部分接桩前必须凿除,保证桩头无松散层。
在灌注将近结束时,由于导管内砼柱高度减小,压力降低,而导管处的泥浆及所含渣土稠度增加,比重增大,如出现砼顶升困难时,可在孔内加水稀释泥浆,并掏出部分沉淀物,使灌注顺利进行。
在拔出最后一段长导管时,拔管速度要慢且上下移动,以防止桩顶沉淀的泥浆挤入导管,形成泥心。
(8)当灌注完的混凝土开始初凝时即可割断挂环,避免钢筋和混凝土的粘结力受损失。
地面以下部分的护筒在灌注混凝土后拔除。
(9)灌注混凝土的同时,每根桩应按规定制作2~4组混凝土试块,标准养护28天后,及时提交混凝土抗压强度报告。
(10)有关砼灌注情况,灌注时间,砼面的深度变化,导管埋深,导管拆除及发生的异常现象应由专人现场进行记录。
灌注砼时应做好应急预案措施,灌注过程中不得中断,尽量用最短的时间结束灌注。
(11)破桩头:由人工采用风镐进行,要破至设计高程,要保持钢筋的完整,桩顶基本平整、干净。
5、质量检验标准钻孔完成后,用检孔器进行检孔。
检孔器用ф20的钢筋加工制作,其外径等于设计桩径,长度为6m。
检测时,将检孔器吊起,把测绳的零点系于检孔器的顶端,使检孔器的中心、孔的中心与起吊钢丝绳的中心处于同一铅垂线上,慢慢放入孔内,通过测绳的刻度加上检孔器6米的长度判断其下放位置。
如上下畅通无阻直到孔底,表明钻孔桩成孔质量合格,如中途遇阻则表明在遇阻部位有缩径或孔倾斜现象,则需重新下钻头处理。
表5-1钻孔桩钻孔允许偏差和检验方法表5-2钻孔桩钢筋骨架允许偏差三、施工中的突发事件如何解决1、漏浆这种情况碎石或者流砂中常见,特别是在有地下水流动的地层中钻进时,稀泥浆向孔壁外漏失。
遇到漏浆情况及时往孔里加膨润土,使稠度增加,用钻杆来回搅动,直到不漏浆为止,同时赶紧安排人员向泥浆池内造浆。
2、塌孔若遇到塌孔现象,塌孔严重的护筒都下不去,可尝试用挖掘机掏出三到四米再回填弃土,凉3-4天,再钻,边钻边下护筒,若护筒孔边塌可用挖掘机填实夯实,钻孔要尽量做到慢进尺,尽量不破坏护壁泥皮同时应减少钻头内钻渣掉入孔内破坏泥浆的配比;灌注时若遇严重塌孔则要回填自然沉实再钻。
3、浮笼在灌注过程中发现钢筋笼上浮时,应及时减缓灌注速度,在保证导管有足够埋深的情况下,快速提升导管,待钢筋笼回到设计标高的位置再拆除导管,如果导管埋深不够拆除导管时则将导管快速提升,然后再缓慢放下导管,如此反复直到钢筋笼回到设计标高位置。
4、缩孔易出现缩孔或者塌孔的地区,钻进过程中应每进尺控制在30厘米左右,缓慢的提升钻头,能有效控制缩孔。
5、堵管在混凝土灌注过程中,混凝土在导管中下不去,首先应借用吊车上下抖动导管,若不行将导管拔出清理导管内堵塞的混凝土后重新安装导管,重新灌注。
6、导管进水由于首盘混凝土封底失败或者灌注过程中导管接头不密封导致导管进水,或者灌注过程中将导管拔脱,当封底失败时应及时将导管,钢筋笼拔出,用钻机将孔底混凝土掏出重新安装,钢筋笼导管,清空合格后重新灌注,若没灌注多少堵管也可以利用此方法。
避免措施:灌注前应检查好导管的密封性非常好,首盘封底方量,准确测量导管埋深。