造铜锍过程中锍与渣的分离
造铜锍过程中锍与渣的分离

造铜锍过程中锍与渣的分离在铜冶炼过程中,铜锍是一种含有高浓度铜和少量杂质的物质。
锍与渣的分离是铜冶炼过程中非常重要的一步,它的目的是将锍中的铜分离出来,以便进一步加工和提炼。
铜锍是由冶炼矿石经过熔炼和还原反应得到的产物。
在冶炼过程中,矿石被加热至高温,使其中的铜矿物质发生熔化,形成熔融的铜锍。
这个过程中还会产生大量的气体和杂质,它们会与铜锍中的铜形成固态的渣。
锍与渣的分离有多种方法,下面将介绍其中两种常用的方法。
第一种方法是重力分离法。
这种方法利用了锍和渣在密度上的差异。
由于铜的密度较大,锍的密度也相应较大;而渣中含有较多的非金属杂质,密度较小。
在分离过程中,可以利用重力使得锍沉淀在底部,而渣则浮在上方。
这种方法常用于较小规模的铜冶炼工艺中,通过调节渣锍比例、温度和时间等参数,可以获得较好的分离效果。
第二种方法是浮力分离法。
这种方法利用了锍和渣在浮力上的差异。
在冶炼过程中,可以通过向锍中注入气体或其他浮力助剂,使得锍中的铜形成气泡并上升,而渣则下沉。
这样,锍和渣会在冶炼炉中分离出来,便于进一步处理和提炼。
这种方法常用于较大规模的铜冶炼工艺中,具有分离效果好、速度快、自动化程度高等优点。
无论是重力分离法还是浮力分离法,为了提高分离效果,还需要进行一系列的处理操作。
首先,需要对锍进行冷却和固化,以便减少锍中固态杂质的含量。
其次,可以通过磁选、气浮、离心和过滤等方法,进一步去除锍和渣中的杂质。
最后,通过熔炼和铸造等工艺,可以将锍中的铜进一步提纯和加工,得到高纯度的铜材料。
总之,锍与渣的分离是铜冶炼过程中至关重要的一步。
通过合理选择和优化分离方法,可以将铜从锍中分离出来,为后续的加工和提炼提供了基础。
同时,为了提高分离效果,还需要进行一系列的处理操作,以去除锍和渣中的杂质。
这样才能得到高纯度的铜材料,满足不同领域的需求。
火法炼铜工艺讲解

------------------------------------------精品文档-------------------------------------1 概述铜是人类应用的最古老的金属之一,它有很长的、很光辉的历史。
考古学证明,早在一万年前,西亚人已用铜制作装饰品之类的物件。
铜和锡可制成韧性合金青铜,考古发现在公元前约3000年,历史已进入了青铜时代。
而今铜的化学、物理学和美学性质使它成为广泛应用于家庭、工业和高技术的重要材料。
铜具有优良可锻性、耐腐蚀性、韧性,适于加工;铜的导电性仅次于银,而其价格又较便宜,故而被广泛应用于电力;铜的导热性能也颇佳;铜和其他金属如锌、铝、锡、镍形成的合金,具有新的特性,有许多特殊的用途。
铜是所有金属中最易再生的金属之一,再生铜约占世界铜供应总量的40%。
铜以多种形态在自然环境中存在,它存在于硫化物矿床中(黄铜矿、辉铜矿、斑铜矿、蓝铜矿)、碳酸盐矿床中(蓝铜矿、孔雀石)和硅酸盐矿床中(硅孔雀石、透视石),也以纯铜即所谓“天然铜”的形态存在。
铜以硫化矿或氧化矿形式露天开采或地下开采,采出矿石经破碎后,再在球磨机或棒磨机中磨细。
矿石含铜一般低于1%。
1.1 国内外铜冶金的发展现状目前国内外的铜冶炼技术的发展主要还是以火法冶炼为主,湿法为辅。
铜的火法生产量占总产量的80%左右。
目前,全世界约有110座大型火法炼铜厂。
其中,传统工艺(包括反射炉、鼓风炉、电炉)约占1/3;闪速熔炼(以奥托昆普炉为主)约占1/3;熔池熔炼(包括特尼恩特炉、诺兰达炉、三菱炉、艾萨炉、中国的白银炉、水口山炉等)约占1/3。
另外,世界范围内铜冶金工业同样面临铜矿资源短缺的问题,国土资源部信息中心统计资料表明:在世界范围内,铜是仅次于黄金的第2个固体矿产勘查热点,全球固体矿产勘查支出中约20%是找铜的,并且这一比例还有增加的趋势。
相应地,铜也是各大势力集团争夺的焦点之一。
从全球角度看铜的保证年限只有约29年。
火法冶炼操作工竞赛初赛试题(C卷答案)

火法冶炼操作工竞赛初赛试题(C卷)一、填空题(每空0.5分,共20分)1、有色重金属是指铜、铅、锌、锡、汞、镉、铋等20多种金属,他们的共同点是比重都大于5.0。
2、铜矿石或铜精矿生产铜的方法概括起来有火法和湿法两大类。
3、耐火材料一般是指耐火度在1580 ℃以上的无机非金属材料。
4、冶金炉渣的主要作用是使矿石和熔剂中的脉石和燃料中的灰分集中,并在高温下与主要的冶炼产物金属、锍(冰铜)等分离。
5、铜是一种具有金属光泽的橙红色金属,组织致密、高导电性、导热性、及良好的延展性是铜最有价值的特性。
6、近年来湿法炼铜工艺有了更大的发展,现在世界上已有20 %的铜用湿法生产。
7、碱性耐火材料一般指以氧化镁和氧化钙为主要成分的耐火材料。
这类耐火材料的耐火度都很高,抵抗碱性渣的能力强。
8、造锍熔炼炉渣中的主要酸性氧化物是SiO2。
9、自然界已经发现的含铜矿物有200多种,但是重要的矿物只有20来种,除少量的自然铜外,主要有原生硫化铜矿物和次生氧化铜矿物。
铜矿中伴生的脉石矿物常见的石英、石灰石和方解石等。
10、诺兰达炉类似于铜锍吹炼的转炉,沿长度方间将炉内空间分为吹炼区和沉淀区。
11、耐火材料的主晶相是指构成耐火制品结构的主体且熔点较高的一种晶体。
12、铜锍与熔渣的密度差越大,熔渣的粘度越小,沉降速度就越快,锍和渣相分离越好,铜的夹带损失就越小。
13、三菱法连续炼铜包括一台熔炼炉(S炉)、一台贫化电炉(CL炉)和一台吹炼炉(C炉),这三台炉子用溜槽连接在一起连续生产14、在艾萨炉生产控制中,较理想的熔池控制温度为1180~1195℃。
燃煤、氧气和鼓风机的空气是温度控制的主要手段。
燃油使用的相对较少。
15、编制热平衡的目的,主要是为了验算热的指出和更深入地分析过程,以发现热量支出的主要原因和分析节省燃料的可能性。
16、氧化矿一般多为黑色或灰色;硫精矿一般多为纯绿色。
二、选择题(每题1.5分,共30分)1、从性质和成分来看,在配料中氧化矿与硫精矿相比,其性质(C )。
造铜锍过程中锍与渣的分离(三篇)

造铜锍过程中锍与渣的分离炉渣和铜锍相的分离1)在造锍熔炼中,炉渣的主要成分是FeO和SiO2,铜锍相Cu2S 和FeS。
所以当炉渣和铜锍共存时,最重要的关系是FeS―FeO―SiO2和Cu2S―FeS―FeO。
根据研究,无SiO2存在时,FeO和FeS完全互溶,但当加入SiO2时,均相溶液出现分层;SiO2足量时,两相几乎完全分离。
另外,当渣中存在CaO或Al2O3时,将对FeS―FeO―SiO2系的互溶性质产生很大影响,它们的存在均降低FeS在渣中的溶解度。
所以,高CaO和高Al2O3炉渣,炉渣和锍相的分离特性将进一步加强。
2)这就解释了在铜冶炼厂熔炼炉出现的排放过程中冰铜、炉渣明显分离,冰铜和炉渣流动性级差大的情况。
针对这一情况,为保证炉渣的正常排放,一是降低操作熔池面;二是在铜溜槽可承受范围内尽可能提高炉渣温度;三是通过配比计算和精良的操作,将炉渣组分严格控制在低熔点区域,提高炉渣流动性。
另外,适当增加搅动,也将会有一定帮助。
3)同时,由于炉渣溶解FeS的能力降低,使得反应:Fe3O4+SiO2+FeS===2FeOSiO2+SO2的反应不能在炉渣熔池中完成,使得很容易形成高磁性铁或高硅两个极端的高熔点炉渣。
除调整控制精矿配比外,应考虑通过进一步加强横向搅动,来促使精矿落入炉渣熔池后,能在渣层中即充分完成其分解和造渣反应,形成尽可能多的铁橄榄石炉渣。
4、炉渣成分对炉渣性质的影响SiO2FeOFe3O4Fe2O3CaOAl2O3MgO温度升高粘度电导率-密度表面粘力-造铜锍过程中锍与渣的分离(二)铜是一种重要的金属材料,在工业生产和日常生活中广泛应用。
然而,在铜的生产过程中,会产生一些杂质和非铜成分,这些杂质通常以残留物或渣滓的形式存在。
为了获得纯度高的铜材料,需要进行锍与渣的分离过程。
接下来,我将详细介绍铜锍与渣的分离过程。
铜锍是指富含铜的矿石熔化或冶炼后得到的液态金属。
真正的铜锍中除了铜还存在一些其他金属和非金属杂质,例如铁、硫和铅等。
造铜锍过程中锍与渣的分离范文(二篇)
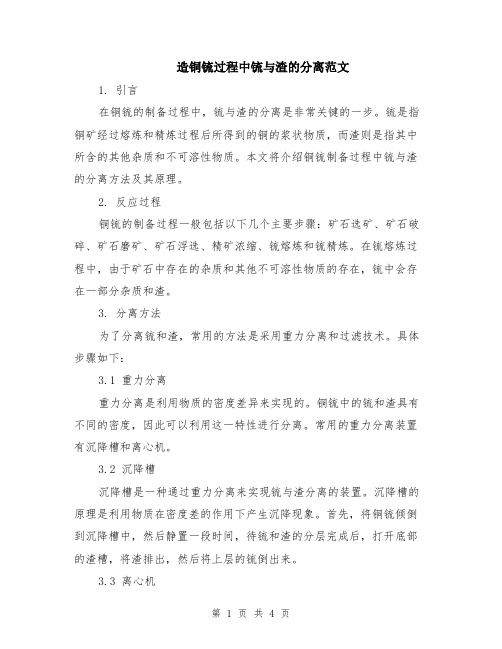
造铜锍过程中锍与渣的分离范文1. 引言在铜锍的制备过程中,锍与渣的分离是非常关键的一步。
锍是指铜矿经过熔炼和精炼过程后所得到的铜的浆状物质,而渣则是指其中所含的其他杂质和不可溶性物质。
本文将介绍铜锍制备过程中锍与渣的分离方法及其原理。
2. 反应过程铜锍的制备过程一般包括以下几个主要步骤:矿石选矿、矿石破碎、矿石磨矿、矿石浮选、精矿浓缩、锍熔炼和锍精炼。
在锍熔炼过程中,由于矿石中存在的杂质和其他不可溶性物质的存在,锍中会存在一部分杂质和渣。
3. 分离方法为了分离锍和渣,常用的方法是采用重力分离和过滤技术。
具体步骤如下:3.1 重力分离重力分离是利用物质的密度差异来实现的。
铜锍中的锍和渣具有不同的密度,因此可以利用这一特性进行分离。
常用的重力分离装置有沉降槽和离心机。
3.2 沉降槽沉降槽是一种通过重力分离来实现锍与渣分离的装置。
沉降槽的原理是利用物质在密度差的作用下产生沉降现象。
首先,将铜锍倾倒到沉降槽中,然后静置一段时间,待锍和渣的分层完成后,打开底部的渣槽,将渣排出,然后将上层的锍倒出来。
3.3 离心机离心机是一种利用离心力来实现物质分离的装置。
在铜锍的制备过程中,可以使用离心机来进行锍与渣的分离。
首先,将铜锍倒入离心机中,然后以高速旋转离心机,通过离心力的作用,将锍和渣分离开来。
锍通常为液状,会成为离心机内部的上层液体,而渣则会成为下层固体。
然后,打开离心机的出口,分别将锍和渣倒出。
3.4 过滤技术过滤技术是常用的分离方法之一。
过滤技术利用滤纸或其他过滤介质来分离固体颗粒和液体。
在铜锍制备过程中,可以通过过滤技术来分离锍中的渣。
首先,将铜锍倒入过滤器中,然后通过压力或真空等方式使锍中的液体通过滤纸,而固体颗粒则被留在滤纸上。
将滤纸上的固体颗粒收集起来,即为锍中的渣。
4. 分离原理锍与渣的分离原理是基于物质的密度差异或固液分离原理。
铜锍中的锍和渣具有不同的密度,因此可以通过重力分离或过滤技术将其分离开来。
熔炼常识

熔炼常识1.造锍熔炼过程中物料的主要物理化学变化?(1)高价硫化物、氧化物及碳酸盐的分解(2)硫化物氧化(3)铁的氧化物及脉石造渣反应(4)造锍反应(5)燃料的燃烧反应2.冰铜的概念?冰铜(锍)是在熔炼过程中产生的重金属硫化物的共熔体,是以Cu2S-FeS系为主并溶解少量其他金属硫化物(如Ni3S2, PbS, Co3S2, ZnS等), 氧化铁(Fe3O4,FeO),铂族金属及微量脉石成分的多元系混合物. 造锍熔炼炉渣碱度是如何定义的? 3.碱度定义:碱性渣和酸性渣有什么区别,它们对炉渣粘度的影响是什么? M0=1的渣称为中性渣,M0>1的渣称为碱性渣,M0<1的渣称为酸性渣.在炉渣组成一定时,炉渣粘度随温度升高而降低.但温度对碱性炉渣和酸性炉渣粘度的影响有显著区别.4. 造锍熔炼过程对炉渣的基本要求如何?炉渣与冰铜不互溶,对Cu2S溶解度小;具有良好的流动性;具有相对低的密度;具有相对大的界面张力5. 渣含氧化硅对锍与炉渣平衡有何影响?SiO2为42-45%时,铜在渣中的损失最小,且随SiO2的升高,铜的溶解损失降低;SiO2低于42-44%时,机械夹带损失降低;SiO2超过42-45%时,机械夹带损失升高.6. 冰铜吹炼的目的是什么?锍吹炼的两个阶段是什么?冰铜的吹炼多在水平转炉中进行,其主要原料为熔炼产出的液态冰铜吹炼的目的是利用空气中的氧,将冰铜中的铁和硫几乎全部氧化除去,同时除去部分杂质,以得到粗铜转炉吹炼是一个周期性的作业,可分为两个阶段:第一阶段:造渣期,主要进行FeS的氧化和造渣反应;第二阶段:造铜期,主要进行Cu2S的氧化及Cu2S 和Cu2O的相互反应,最终获得粗铜。
造渣期根据情况加入冰铜和石英溶剂,并间断地排放炉渣。
造铜期无需加溶剂,不产出炉渣。
7.粗铜火法精炼过程包括哪些?火法精炼的目的如何?精炼过程: 每一精炼周期包括装料、熔化、氧化、还原和浇铸五个工段,其中氧化和还原工段是最关键工段火法精炼目的: 粗铜含有各种杂质和金银等贵金属,其含量为0.25~2%。
造铜锍过程中锍与渣的分离范本

造铜锍过程中锍与渣的分离范本铜锍是从铜矿石中提取出来的一种熔炼产物,通常含有铜、硫、铁、锌等金属元素。
在铜锍的制备过程中,锍与渣的分离是非常关键的一步。
本文将详细介绍铜锍制备过程中锍与渣的分离方法、原理及范本。
1. 锍与渣的分离方法1.1 重力分离重力分离是最常见的铜锍分离方法之一。
根据不同的密度,铜锍中的不同成分会出现不同的分层现象,通过重力作用分别收集锍和渣。
具体的分离方法可以是静置分离、沉淀分离和离心分离等。
1.2 浮选分离浮选分离是利用物理和化学性质的差异分离铜锍中的锍和渣。
在浮选过程中,将含有铜矿石研磨成粉末,与浮选药剂混合后通过气泡的附着和胶结作用,使锍浮于水面形成浮锍,而渣则沉入底部形成渣渣。
1.3 磁选分离磁选分离是根据铜锍中的铁成分具有磁性的特点进行分离。
通过磁选机的磁性作用,将铜锍中的铁分离出来,从而实现锍与渣的分离。
1.4 电渣法分离电渣法分离是通过电渣炉进行分离的方法。
将铜锍倒入电渣炉中,在高温条件下进行电解,将铜锍中的铜和其他金属元素分离出来,形成纯净的锍和渣。
2. 锍与渣的分离原理2.1 重力分离原理重力分离是根据不同物质之间的密度差异进行分离的原理。
在铜锍中,由于不同成分的密度不同,比如铜的密度较大,而渣的密度较小,因此可以通过重力作用使锍和渣分开。
2.2 浮选分离原理浮选分离是根据铜锍中的物理和化学性质的差异进行分离的原理。
浮选药剂的作用会改变不同成分的表面性质,使铜锍中的锍颗粒上浮形成浮锍,而渣则沉入底部形成渣渣。
2.3 磁选分离原理磁选分离是根据铜锍中铁成分具有磁性的特点进行分离的原理。
通过磁选机的磁性作用,可以吸引铜锍中的铁成分,从而分离出锍和渣。
2.4 电渣法分离原理电渣法分离是根据电渣炉的电解原理进行分离的方法。
在高温条件下,通过电解作用,将铜锍中的铜和其他金属元素分离出来,形成纯净的锍和渣。
3. 锍与渣的分离范本以下是一个铜锍制备过程中锍与渣的分离范本,详细描述了每个步骤和过程:3.1 原料准备收集并选取铜矿石作为原料。
闪速炉铜锍熔炼车间设计

闪速炉铜锍熔炼车间设计闪速炉铜锍熔炼车间设计(design of flash furnace smelter of copper matte)以硫化铜精矿为原料,配入粉状石英石熔剂,在闪速炉内进行熔炼,产出吹炼用铜锍的铜冶炼厂车间设计。
闪速炉有奥托昆普(Outokumpu)型和国际镍公司(International Nickel Co.简称INCO)型两种。
闪速炉除生产铜锍外,对特殊的原料还可以生产粗铜。
闪速炉铜锍熔炼车间设计内容主要为:工艺流程选择、设备结构设计、车间配置和主要技术经济指标。
简史 1949年芬兰奥托昆普公司在哈里亚瓦尔塔(Harjavalta)厂建成世界上第一座闪速炉。
其反应塔内径为3.6m,日处理铜精矿360t。
1956年至1973年间,日本共建成7座闪速炉,对炉体结构和热风制备等方面都作了重大改进,同时还发展了能一次获得弃渣的自电闪速炉。
20世纪80年代,美国马格马铜公司(Magma Copper Corp)圣•曼纽埃尔(San Manuel)炼铜厂采用富氧自热熔炼技术建成单炉年产铜25万t的闪速炉。
波兰格沃古夫(Glogow)厂根据处理含硫铁低的高品位铜精矿的特点,设计建成直接获得含铜98%以上粗铜的闪速炉。
中国在80年代,设计建成第一台奥托昆普型闪速炉,并对炉渣的铁硅比、铜锍品位和铜锍温度三项参数实现计算机在线控制,1990年又完成了富氧熔炼技术改造工程。
1953年加拿大国际镍公司首先建成INCO型闪速炉,设计规模为日处理铜精矿1000t。
80年代初,美国熔炼与精炼公司(American Smeling & Refining Corp Asarco)海登(Hayden)厂和齐诺矿业公司(Chino Mines Co.)赫尔利(Hurley)厂各建成1座:INCO型闪速炉。
此外,苏联于1968年在阿尔马累克公司建成1座类似于INC()型闪速炉的氧焰炉。
90年代,全世界建成的铜闪速炉约有35座。
铜的加工冶炼工艺流程
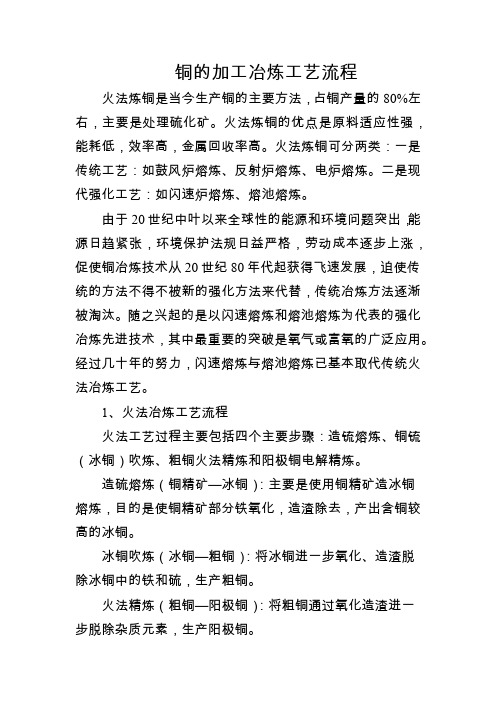
铜的加工冶炼工艺流程火法炼铜是当今生产铜的主要方法,占铜产量的80%左右,主要是处理硫化矿。
火法炼铜的优点是原料适应性强,能耗低,效率高,金属回收率高。
火法炼铜可分两类:一是传统工艺:如鼓风炉熔炼、反射炉熔炼、电炉熔炼。
二是现代强化工艺:如闪速炉熔炼、熔池熔炼。
由于20世纪中叶以来全球性的能源和环境问题突出,能源日趋紧张,环境保护法规日益严格,劳动成本逐步上涨,促使铜冶炼技术从20世纪80年代起获得飞速发展,迫使传统的方法不得不被新的强化方法来代替,传统冶炼方法逐渐被淘汰。
随之兴起的是以闪速熔炼和熔池熔炼为代表的强化冶炼先进技术,其中最重要的突破是氧气或富氧的广泛应用。
经过几十年的努力,闪速熔炼与熔池熔炼已基本取代传统火法冶炼工艺。
1、火法冶炼工艺流程火法工艺过程主要包括四个主要步骤:造锍熔炼、铜锍(冰铜)吹炼、粗铜火法精炼和阳极铜电解精炼。
造硫熔炼(铜精矿—冰铜):主要是使用铜精矿造冰铜熔炼,目的是使铜精矿部分铁氧化,造渣除去,产出含铜较高的冰铜。
冰铜吹炼(冰铜—粗铜):将冰铜进一步氧化、造渣脱除冰铜中的铁和硫,生产粗铜。
火法精炼(粗铜—阳极铜):将粗铜通过氧化造渣进一步脱除杂质元素,生产阳极铜。
电解精炼(阳极铜—阴极铜):通过引入直流电,阳极铜溶解,在阴极析出纯铜,杂质进入阳极泥或电解液,从而实现铜和杂质的分离,产出阴极铜。
火法炼铜一般流程图2、火法冶炼工艺分类(1)闪速熔炼闪速熔炼(flash smelting)包括国际镍公司因科(Inco)闪速炉、奥托昆普(Outokumpu)闪速炉和旋涡顶吹熔炼(ConTop)3种。
闪速熔炼是充分利用细磨物料巨大的活性表面,强化冶炼反应过程的熔炼方法。
将精矿经过深度干燥后,与熔剂经干燥一起用富氧空气喷入反应塔内,精矿粒子在空间悬浮1-3s时间,与高温氧化性气流迅速发生硫化矿物的氧化反应,并放出大量的热,完成熔炼反应即造锍的过程。
反应的产物落入闪速炉的沉淀池中进行沉降,使铜锍和渣得到进一步的分离。
一种从低铁铜鋶中分离铜的方法

说明书摘要本发明公开了一种从低铁铜锍中选择性提取铜的工艺,属于有色金属冶金湿法领域。
一种从低铁铜锍中选择性提取铜的方法,本发明是以低铁铜锍为原料,将破碎研磨过筛后的低铁铜锍粉末与硫酸(或电积废液)、调整剂A以及添加剂B按一定的配比调浆后倒入高压釜中,往高压釜中通入富氧并控制釜内氧气的压力进行氧化浸出,控制技术条件:硫酸浓度80~120g/L,液固比8~12∶1,温度130~160 ℃,釜内压力1.0~1.4MPa搅拌速度500~700 r/min,反应时间2~4 h。
在氧化浸出过程中,铅铜锍中的硫被氧化成单质硫转移到渣中;Cu则以Cu2+形式进入溶液,Pb、Ag分别以PbSO4、Ag2SO4的形式和金、铂等贵金属留在渣中;在高温高压(pH<2)的条件下,大部分As则被加入的添加剂B固化进入渣中,由此实现了铜的选择性浸出。
浸出过程完成后,进行液固分离,从而实现铜与其他有价元素的初步分离;浸出液经调酸后直接进行旋流电解提取其中的铜,可获得符合国家标准的阴极铜产品;浸出渣送至火法炼铅系统综合回收Pb、Ag、Au等有价元素。
权利要求书1、一种从低铁铜锍中选择性提取铜的工艺。
铅铜锍经破碎、磨粉、调浆后在高压釜内进行氧化浸出,浸出过程中不断通入富氧并控制适宜的技术指标。
浸出完成后进行液固分离,浸出液经调酸后直接进行旋流电解,得符合国标的阴极铜产品,浸出渣送至火法炼铅系统综合回收Pb、Ag、Au等有价元素,电积废液返回高压釜作为浸出溶剂循环使用。
2、根据权利要求1所述的从低铁铜锍中选择性提取铜的工艺,其特征在于:低铁铅铜锍的成分为:Pb:15~45%;Cu:35~60%;S:2~18%;Ag:0.2~0.8%;As:5~20%;Fe:0.05~0.6%。
3、根据权利要求1所述的从低铁铜锍中选择性提取铜的工艺,其特征在于:低铁铜锍经磨粉后粒度在0.147mm以下。
4、根据权利要求1所述的从低铁铜锍中选择性提取铜的工艺,其特征在于:低铁铜锍在高压釜氧化浸出时采用富氧为氧化介质,其氧含量60%以上。
7 造锍熔炼和熔锍吹炼技术 - gxxdnetcn1002

7.1.3
Cu-Fe-S 三元系状态图
熔炼硫化矿所得各种金属的锍是复杂的硫化物共熔体,基本上是由金属的低价硫化 物所组成,其中富集了所要提取的金属及贵金属。例如铜锍中主要是 Cu2S 和 FeS,它 们两者所含铜、铁和硫的总和常占铜锍总量的 80%~95%,所以 Cu、Fe、S 三种元素可 以说是铜锍的基本成分,即 Cu-Fe-S 三元系实际上可以代表铜锍的组成。通过对该三元 系状态图的研究,对铜锍的性质、理论成分、熔点等性质可有较详细的了解。
Cu(固 P1P 线——为二元包晶液相线,该)两个四相平衡不变点: E 点——为三元共晶点,共晶温度为 1188K(靠近 FeS-Cu2S 连线的 E3 处) ,
Cu2S(固溶体)+FeS(固溶体)+Fe(固溶体) LE 。
7.1.2
造锍熔炼过程的主要化学反应
2FeS(l)+3O2 = 2FeO(l)+ SO2 (1)
造锍熔炼主要包括两个过程,即造渣和造锍过程。其主要反应如下:
150
2 FeO(l)+ SiO2(S)= 2FeO·SiO2(l) xFeS(l)+yMeS(l) = [ yMeS·xFeS](l)
(2) (3)
表 7―1 锍的类型 铜锍(冰铜) 高铜锍(白冰铜) 镍锍(冰镍) 高镍锍(高冰镍、镍高锍) 铜镍锍 高铜镍锍 0.8~2.5 7~8 24~30 各种熔锍主要成分 Cu 36~65 70~80 12~20 78~79.5 13~15 40~48 Ni Fe 10~40 <1 56~69 0.2~0.3 47~49 2~14 S 20~25 18~19 17~23 17~19 24~25 21~23
P 点 —— 为三元包晶点,析出温度为 1358K (靠近 Cu 角处) , Lp+Fe( 固溶体 )
2023年造铜锍过程中锍与渣的分离
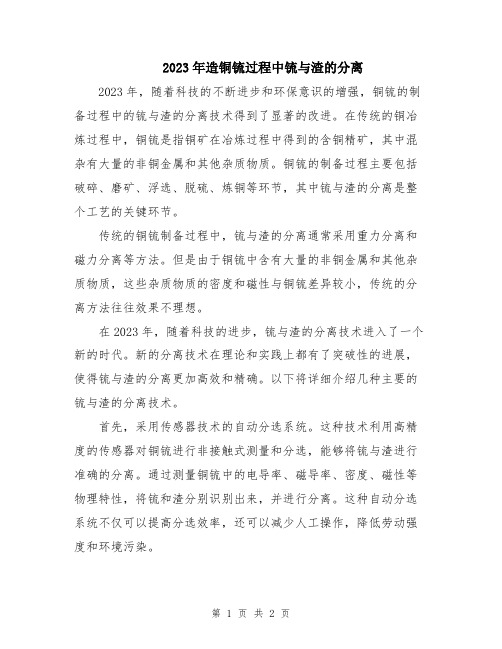
2023年造铜锍过程中锍与渣的分离2023年,随着科技的不断进步和环保意识的增强,铜锍的制备过程中的锍与渣的分离技术得到了显著的改进。
在传统的铜冶炼过程中,铜锍是指铜矿在冶炼过程中得到的含铜精矿,其中混杂有大量的非铜金属和其他杂质物质。
铜锍的制备过程主要包括破碎、磨矿、浮选、脱硫、炼铜等环节,其中锍与渣的分离是整个工艺的关键环节。
传统的铜锍制备过程中,锍与渣的分离通常采用重力分离和磁力分离等方法。
但是由于铜锍中含有大量的非铜金属和其他杂质物质,这些杂质物质的密度和磁性与铜锍差异较小,传统的分离方法往往效果不理想。
在2023年,随着科技的进步,锍与渣的分离技术进入了一个新的时代。
新的分离技术在理论和实践上都有了突破性的进展,使得锍与渣的分离更加高效和精确。
以下将详细介绍几种主要的锍与渣的分离技术。
首先,采用传感器技术的自动分选系统。
这种技术利用高精度的传感器对铜锍进行非接触式测量和分选,能够将锍与渣进行准确的分离。
通过测量铜锍中的电导率、磁导率、密度、磁性等物理特性,将锍和渣分别识别出来,并进行分离。
这种自动分选系统不仅可以提高分选效率,还可以减少人工操作,降低劳动强度和环境污染。
其次,采用化学分离技术。
化学分离技术是指利用化学反应的原理和方法,将锍和渣进行有效分离。
例如,利用锍和渣中不同金属的化学性质差异,可以通过溶解、沉淀、过滤等过程,将锍和渣分离。
这种化学分离技术具有分离效果好、操作简便等优点,但需要对铜锍进行较为复杂的前处理和后处理,成本较高。
再次,采用机械分离技术。
机械分离技术是指利用不同的物理性质,通过机械设备将锍和渣进行有效分离。
例如,利用锍和渣的颗粒大小、形状、密度等差异,可以通过震动筛、离心机、气流分类机等设备,将锍和渣分离。
这种机械分离技术具有操作简便、成本低等优点,但需要对铜锍进行较为细致的物料分析和设备调试。
除了上述几种分离技术,还有许多其他的新兴技术在锍与渣的分离领域得到了应用。
造锍熔炼的基本原理(一)

造锍熔炼的基本原理(一)造锍熔炼的基本原理什么是造锍熔炼?造锍熔炼是一种将金属矿石转化为金属锍的冶金过程。
锍是金属矿石在高温下部分熔化的产物,其中含有金属和非金属成分。
通过进一步处理,金属锍可以被提纯并用于制造各种金属制品。
造锍熔炼的基本步骤1.矿石破碎:首先,将金属矿石进行破碎,以增加其表面积和接触面,便于后续处理。
2.矿石浮选:将破碎后的矿石放入浮选机中,通过气泡吸附的方式分离金属矿石和非金属矿物。
在浮选过程中,利用矿石表面的物化性质,使金属矿石浮起来,而非金属矿物沉入底部。
3.锍矿化:经过浮选的金属矿石被送入熔炼炉,并与熔剂(通常是氧化剂和还原剂的混合物)一起加热。
在高温下,金属矿石开始熔化,并与熔剂中的其他化学物质发生反应。
4.分离:在熔炼过程中,金属和非金属成分会发生相互作用,生成金属锍和熔渣。
通过浮力和密度的差异,可以将金属锍与熔渣分离。
5.精炼:分离得到的金属锍可能含有杂质,需要进行精炼。
精炼过程中,通过加入化学剂或调节温度、压力等参数,可以进一步纯化金属锍。
6.冷却和固化:经过精炼的金属锍被冷却成块状,并固化为有固定形状的金属。
造锍熔炼的原理解析1.浮选原理:浮选是根据矿物表面与气泡的相互作用来实现分离的。
通过给矿浆注入含有诸如气体或化学药品的液体,使气泡产生并吸附在目标矿物表面,从而改变其浮力或附着特性。
2.熔渣分离原理:熔渣分离是利用熔渣与金属锍的密度和浮力差异来实现的。
通过控制熔渣的成分和温度,可以调节其物理性质,使得熔渣具有更高的密度,从而下沉或被分离出来。
3.精炼原理:精炼是通过控制反应条件和添加特定的化学剂来消除金属锍中的杂质。
常用的精炼方法包括化学精炼、电解精炼、熔盐精炼等。
造锍熔炼的应用领域造锍熔炼广泛应用于金属冶金工业,包括以下领域:•铁矿石冶金:将铁矿石熔炼成熔铁,用于生产钢材或其他铁制品。
•铜冶金:将铜矿石熔炼成熔铜,用于制造电线、管道等。
•铝冶金:将铝矿石熔炼成熔铝,用于汽车制造、建筑等行业。
重金属冶金学作业答案
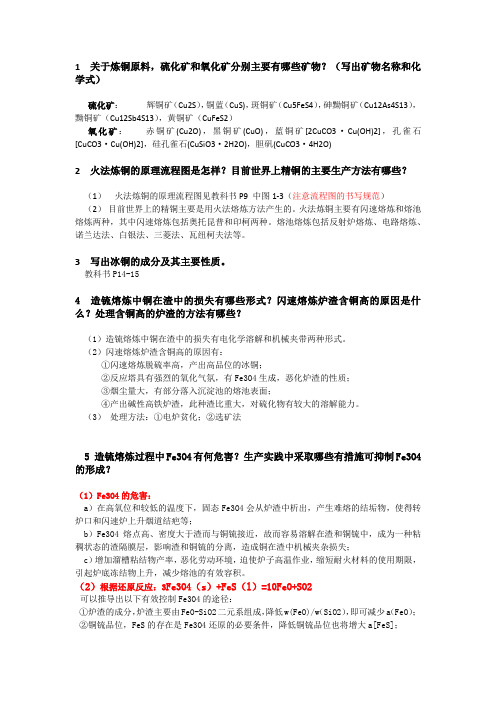
1 关于炼铜原料,硫化矿和氧化矿分别主要有哪些矿物?(写出矿物名称和化学式)硫化矿:辉铜矿(Cu2S),铜蓝(CuS),斑铜矿(Cu5FeS4),砷黝铜矿(Cu12As4S13),黝铜矿(Cu12Sb4S13),黄铜矿(CuFeS2)氧化矿:赤铜矿(Cu2O),黑铜矿(CuO),蓝铜矿[2CuCO3·Cu(OH)2],孔雀石[CuCO3·Cu(OH)2],硅孔雀石(CuSiO3·2H2O),胆矾(CuCO3·4H2O)2 火法炼铜的原理流程图是怎样?目前世界上精铜的主要生产方法有哪些?(1)火法炼铜的原理流程图见教科书P9 中图1-3(注意流程图的书写规范)(2)目前世界上的精铜主要是用火法熔炼方法产生的。
火法炼铜主要有闪速熔炼和熔池熔炼两种,其中闪速熔炼包括奥托昆普和印柯两种。
熔池熔炼包括反射炉熔炼、电路熔炼、诺兰达法、白银法、三菱法、瓦纽柯夫法等。
3 写出冰铜的成分及其主要性质。
教科书P14-154 造锍熔炼中铜在渣中的损失有哪些形式?闪速熔炼炉渣含铜高的原因是什么?处理含铜高的炉渣的方法有哪些?(1)造锍熔炼中铜在渣中的损失有电化学溶解和机械夹带两种形式。
(2)闪速熔炼炉渣含铜高的原因有:①闪速熔炼脱硫率高,产出高品位的冰铜;②反应塔具有强烈的氧化气氛,有Fe3O4生成,恶化炉渣的性质;③烟尘量大,有部分落入沉淀池的熔池表面;④产出碱性高铁炉渣,此种渣比重大,对硫化物有较大的溶解能力。
(3)处理方法:①电炉贫化;②选矿法5 造锍熔炼过程中Fe3O4有何危害?生产实践中采取哪些有措施可抑制Fe3O4的形成?(1)Fe3O4的危害:a)在高氧位和较低的温度下,固态Fe3O4会从炉渣中析出,产生难熔的结垢物,使得转炉口和闪速炉上升烟道结疤等;b)Fe3O4熔点高、密度大于渣而与铜锍接近,故而容易溶解在渣和铜锍中,成为一种粘稠状态的渣隔膜层,影响渣和铜锍的分离,造成铜在渣中机械夹杂损失;c)增加溜槽粘结物产率,恶化劳动环境,迫使炉子高温作业,缩短耐火材料的使用期限,引起炉底冻结物上升,减少熔池的有效容积。
铜硫分离技术

铜硫分离技术一、石灰法石灰是抑制黄铁矿的常用抑制剂;采用石灰法进行铜硫分离时,矿浆pH值或矿浆中的游离的CaO含量能明显地影响分离效果;一般规律是,处理含黄铁矿量多的致密铁矿;对含黄铁矿少的浸染矿,pH值在9左右就能浮铜抑硫;二、石灰+氰化物法对于浮游活性大的黄铁矿,用石灰加氰化物法抑制是有效的;但由于氰化物有剧毒,会污染环境,因此人们力图用别的方法如石灰加亚硫酸法取代之;三、石灰+亚硫酸法这种方法是广泛使用的无氰抑制黄铁矿的方法;对于原矿含硫、含泥高或黄铁矿浮游活性较大不易被石灰抑制的铜硫矿石,可采用石灰加亚硫酸或SO2抑制黄铁矿进行铜硫分离;此法的关键是要根据矿石性质控制合适的矿浆pH值及亚硫酸SO2的用量,并注意适当的加强充气搅拌;有实验研究指出,在pH=~7的弱酸性介质中,采用石灰加亚硫酸法抑制黄铁矿较有效;此法与石灰法比较具有操作稳定,铜指标好,硫酸等活化剂用量低等特点;四、加温氧化法对于比较难处理的铜硫混合精矿可用此法;此法可分为加石灰或不加石灰的蒸汽加温法,都可以加速黄铁矿表面的氧化,使黄铁矿受到抑制;如某公司加石灰调整pH=11,再用蒸汽加温到60~70℃,获得了良好分选效果;在铜硫分离浮选中,有人还做过石灰加腐殖酸钠的研究,也取得了显著的分选效果;另外,采用选择性好的捕收剂或捕收剂的混合用药,不仅可以减少抑制剂和活化剂用量,而且操作稳定;如某选矿厂用丁基黄药加丁胺黑药或丁基黄药加OSN-43的混合用药,其结果大大提高了铜精矿品位和回收率;被抑制的黄铁矿活化时,为了节省硫酸、硫酸铜、碳酸钠或二氧化碳气体等活化剂的用量,浮铜尾矿可先用水力旋流器浓缩,脱除一部分高碱度泥浆水,然后再加新鲜水稀释;浮选技术---观察泡沫判断浮选效果浮选技术中最主要的一种办法就是观察浮选机中的泡沫,并根据泡沫变化情况来判断浮选效果的好坏;有经验的浮选机操作工人从观察泡沫的表观现象的各种变化,就能判断出引起变化的原因,从而及时调整,以保证浮选过程在最优条件下进行;浮选工能否正确地调节浮选药剂添加量、精矿刮出量和中矿循环量,首先取决于他对浮选泡沫外观好坏判断的正确程度,而观察、判断的能力主要是从不断的、认真的总结操作实践经验中获得;浮选泡沫的外观包括泡沫的虚实、大小、颜色、光泽、形状、厚薄、强度、流动性、音响等现象,这些现象主要是由泡沫表面附着的矿物种类、数量、粒度、颜色、光泽、密度、起泡剂用量多少等决定的;1、泡沫的虚和实:气泡表面附着的矿粒多而密,泡沫则实;气泡表面附着的矿粒少而稀,泡沫则虚,原矿品位高,药剂用量适当,泡沫则实,黄药少而2油多泡沫就会变虚;2、泡沫的大与小:泡沫层表面气泡的大小,常随矿石性质,药剂制度和浮选的区域而变;3、颜色:扫选区浮游矿物的颜色越发白,金属损失越小, 粗精选区浮游矿物的颜色越发黑,则精矿质量越好;4、光泽:浮选黄铁矿的粗选,精选区泡沫矿化好,则其金属光泽强,扫选区泡沫矿化差,呈现水膜的玻璃光泽;如果扫选泡沫出现半金属光泽,说明金属损失大;铜硫分离阶段,矿浆搅拌罐PH值超过12,铜硫分离粗选,泡沫发粘,并且泡沫不易碎,铜精矿品位不高;适宜的PH 值为10-11,现象泡沫不发粘,并且铜扫二浮选机中的泡沫呈现黑白相间;如果出现黑黄相间,说明铜硫未分离,石灰补加量不足,矿浆PH值不够10-11;5、轮廓:被中等疏水性矿粒矿化的泡沫在矿浆表面则形成时,水分充足,每个气泡的轮廓都较为鲜明,泡沫在矿浆面上停留时间长,矿物疏水性大,泡壁干涸残缺后,则气泡轮廓模糊;6、厚与薄:泡沫层的厚薄主要与起泡剂的用量、气泡矿化的程度有关系,起泡剂多,原矿品位高,浓度大,矿化程度好,泡沫层一般较厚,反之就比较薄,浮游矿矿粒过粗,也难以形成厚泡沫层,精选区矿浆面低,泡沫层厚,精矿品位高,扫选区保持矿浆面高,被浮矿物能及时刮出,泡沫层较薄,回收率则高;7、脆性和粘性:泡沫的脆性太大,稳定性差,容易破裂,有时刮不出来,反之,泡沫粘性越大,越不易破,会使浮选机“跑槽”,破坏正常浮选过程,造成精2精矿槽自流困难通常加大冲洗水;造成的原因:起泡剂过量、掉入机油或矿石中有大量的矿泥和硫酸铅等可溶盐类;8、音响:泡沫被刮板刮入泡沫槽时发出“沙沙”的音响,常常是泡沫中含有大量比重较大、粒度较粗的矿物;以上八点就是判断浮选效果的浮选技术;泡沫的外观现象随浮选区域不同而不同,但特定的区域常有特定的现象;观察泡沫情况应抓住对精矿品位和回收率有主要影响的浮选槽包括:最终精矿浮选槽、粗选首部浮选槽和扫选尾部浮选槽;培训内容反浮选要点:稳定,必须保证铜硫精选的稳定,操作:硫反浮选浮选机,贴浆面刮矿;泡沫层厚度控制在10cm到20cm之间,铜硫精选刮黑泡,并且精选泡沫槽里的冲洗水必须固定量,保证下到工序的稳定;黄药和2油,勤检查,如果发现断药,及时补加;反浮选风量,如果液面出现泡沫少时,1.把风阀关掉,再重新开;2.检查2油;反浮选液面,及时根据矿量调整,液面,必须保证刮板贴浆面刮矿; 铜硫分离要点:PH值、柴油、KM109PH值:勤检查石灰补加,发现中断,及时补加;PH值控制在11-12,如果发现铜硫精选泡沫发粘,肯定是石灰量大,要把石灰量调整一下;检测扫选二矿浆PH值,PH值在10时,为最好;柴油:由于铜硫分离流程较长,补加柴油后,浮选机泡沫反应时间较长,调整柴油后,需等待20分钟左右,再进行调整;KM109:在铜硫分离搅拌罐补加,用量为2秒钟1滴左右;全部操作的要点为:稳定,调整稳定,控制刮泡稳定;。
- 1、下载文档前请自行甄别文档内容的完整性,平台不提供额外的编辑、内容补充、找答案等附加服务。
- 2、"仅部分预览"的文档,不可在线预览部分如存在完整性等问题,可反馈申请退款(可完整预览的文档不适用该条件!)。
- 3、如文档侵犯您的权益,请联系客服反馈,我们会尽快为您处理(人工客服工作时间:9:00-18:30)。
仅供参考[整理] 安全管理文书
造铜锍过程中锍与渣的分离
日期:__________________
单位:__________________
第1 页共4 页
造铜锍过程中锍与渣的分离
炉渣和铜锍相的分离
1)在造锍熔炼中,炉渣的主要成分是FeO和SiO2,铜锍相Cu2S
和FeS。
所以当炉渣和铜锍共存时,最重要的关系是FeS―FeO―SiO2
和Cu2S―FeS―FeO。
根据研究,无SiO2存在时,FeO和FeS完全互溶,但当加入SiO2时,均相溶液出现分层;SiO2足量时,两相几乎完全分离。
另外,当渣中存在CaO或Al2O3时,将对FeS―FeO―SiO2系的互溶性质产生很大影响,它们的存在均降低FeS在渣中的溶解度。
所以,高CaO和高Al2O3炉渣,炉渣和锍相的分离特性将进一步加强。
2)这就解释了在铜冶炼厂熔炼炉出现的排放过程中冰铜、炉渣明显分离,冰铜和炉渣流动性级差大的情况。
针对这一情况,为保证炉渣的正常排放,一是降低操作熔池面;二是在铜溜槽可承受范围内尽可能提高炉渣温度;三是通过配比计算和精良的操作,将炉渣组分严格控制在低熔点区域,提高炉渣流动性。
另外,适当增加搅动,也将会有一定帮助。
3)同时,由于炉渣溶解FeS的能力降低,使得反应:
Fe3O4+SiO2+FeS===2FeOSiO2+SO2的反应不能在炉渣熔池中完成,使得很容易形成高磁性铁或高硅两个极端的高熔点炉渣。
除调整控制精矿配比外,应考虑通过进一步加强横向搅动,来促使精矿落入炉渣熔池后,能在渣层中即充分完成其分解和造渣反应,形成尽可能多的铁橄榄石炉渣。
4、炉渣成分对炉渣性质的影响
SiO2FeOFe3O4Fe2O3CaOAl2O3MgO温度升高
第 2 页共 4 页
粘度
电导率-
密度
表面粘力-
第 3 页共 4 页
仅供参考[整理] 安全管理文书
整理范文,仅供参考!
日期:__________________
单位:__________________
第4 页共4 页。