轴类工件车削
轴的加工工艺包括什么
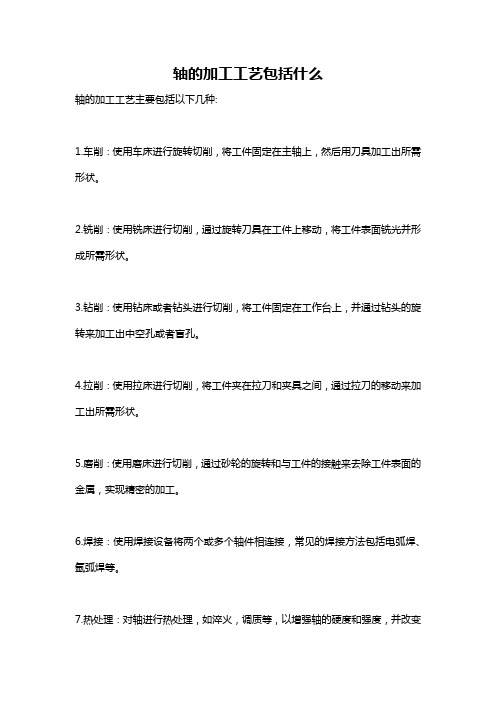
轴的加工工艺包括什么
轴的加工工艺主要包括以下几种:
1.车削:使用车床进行旋转切削,将工件固定在主轴上,然后用刀具加工出所需形状。
2.铣削:使用铣床进行切削,通过旋转刀具在工件上移动,将工件表面铣光并形成所需形状。
3.钻削:使用钻床或者钻头进行切削,将工件固定在工作台上,并通过钻头的旋转来加工出中空孔或者盲孔。
4.拉削:使用拉床进行切削,将工件夹在拉刀和夹具之间,通过拉刀的移动来加工出所需形状。
5.磨削:使用磨床进行切削,通过砂轮的旋转和与工件的接触来去除工件表面的金属,实现精密的加工。
6.焊接:使用焊接设备将两个或多个轴件相连接,常见的焊接方法包括电弧焊、氩弧焊等。
7.热处理:对轴进行热处理,如淬火,调质等,以增强轴的硬度和强度,并改变
其组织结构和性能。
8.抛光:对轴进行表面抛光处理,使其表面光滑,增加其美观性。
9.组装:将加工好的轴与其他配件一起进行组装,形成完整的机械设备。
第三讲典型轴类零件数控车削加工工艺及编程

B
准确定位
B
英制O米制OB:基本功能 0:选购功能 数控车设定—— A功能
2. 进给功能(F功能)
F 功能指令用于在程序中控制切削进给量,有两种指令模式: (1)每转进给模式(G99)
编程格式: G99 F ___; F后面的数字表示主轴每转一转刀具的进给量。 单位:mm/r。
说明:模态指令,一经指定直到被G98取代,一直有效。 系统默认状态,车床上一般常用此种进给量指令方式。
A’ 65,2
B’ 10.01,2
C‘ 18.01,-2
D’ 18.01,-20
E‘ 24,-25
F’ 28,-25 G‘ 48.016,-35 H’ 48.016,-51 I‘ 58.023,-51 J‘ 58.023,-58 K’ 62,-58
符号
含义
编程原点
零件外轮廓走刀路线
工序号 程序段号
工步号 加工内容
粗车左端外轮廓,X轴留0.4、 Z轴留0.1精加工余量
精加工左端面外轮廓,各加工 表面符图示要求
审核
产品名称或代号
零件名称
材料 零件图号
XXX
夹具名称
三爪卡盘
刀具号
刀具规格/ (mm)
主轴转速/ (r/min)
T01
25×25
粗600 精1000
螺纹轴
45钢
XXX
使用设备
车间
CK6132
数控车
进给速度/ 背吃刀量/ 备注 (mm/r) (mm)
恒转速控制 编程格式: S ~
S后面的数字表示主轴转速,单位: r/min。
注意:
在具有恒线速功能的机床上, S 功能指令可限制主轴最高转速
(1)主轴最高转速限制(G50)
2轴类零件车削(普车实训操作+图解)
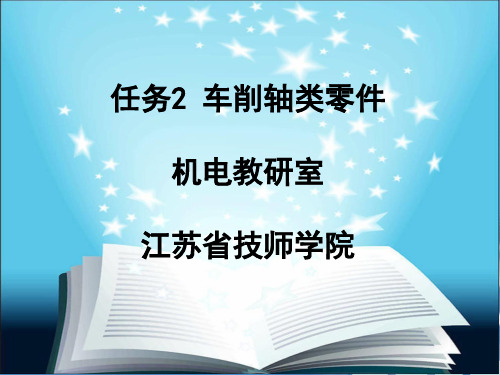
×
至所需位置30
2)机动进给转手动。当纵向车削将至所需
刻度时,应转为手动进给车削至尺寸,然
后退刀,停车检验。 3)横向二倍关系。半径和直径的关系。
10
4、主轴变速,必须先停车!
手柄变速:主轴转速s和进给量f。 参考:
主轴转速s=570r/min,
进给量f=0.05-0.11mm/r。
11
5.粗车和精车
a)开车对刀,使车刀 和工件表面轻微接触;
b) 向右退出车刀, 中滑板不变;
c)按要求横向进刀ap1;
d) 试切1~3毫米
e) 向右退出,停车,测量
f)调整切深至ap2后,机动进给车外圆
8
3. 注意事项 (1)消除机械间隙。
40 30 30
c)正确:反转 b) 错误: a)手柄摇过:要求 转至30,但转到40; 直接退至30; 约一周,再转
20
a)摇动床鞍、中滑板, 移动刀架;
b)使车刀距离工件端 面3mm左右处;
0
c)转动小滑板,使刀 尖轻微接触工件端面;
d)中滑板退刀(床鞍和 小滑板不动);
d)床鞍刻度盘调零 (注意消除机械间隙)。
2、质量分析
1)台阶长度不正确、不垂直。
2)表面粗糙度差。车刀不锋利,手动不
均匀或太快,切削用量不当。
3)倒角:防伤手;便于装配。
4
一、轴类零件:长度超过直径三倍以上。 1、组成:平面、外圆、倒角等。
5
一、轴类零件:长度超过直径三倍以上。 1、组成:平面、外圆、倒角等。
6
一、车外圆 1、车刀选择: 90°车刀、 45°弯头车 刀、尖刀(粗车外圆)。
a)90°车刀
b)45°车刀
车工技术教程-车削简单轴类零件
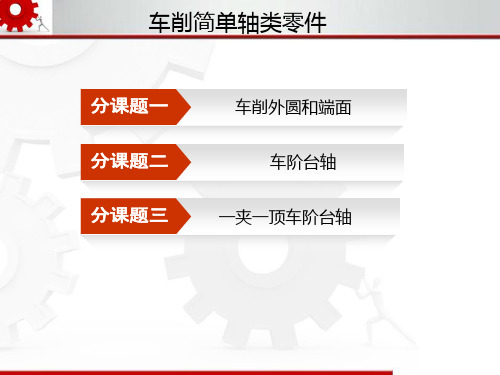
分课题三 一夹一顶车阶台轴
知识目标
•了解中心钻的规格、选择及应用; •掌握阶台轴的工艺制定方法,初步掌握工艺卡片的绘制。
技能目标
•掌握一夹一顶的安装工件技术;
•完成图2-12所示零件的加工(毛坯尺寸为Φ35 mm×113
mm,材料为45
分课题三 一夹一顶车阶台轴
车阶台轴
分课题三 一夹一顶车阶台轴
分课题一 车削外圆和端面
三、 45°端面车刀
45°端面车刀
45°端面车刀刀尖
45°端面车刀主、副偏角
分课题一 车削外圆和端面
二、 中滑板和小滑板刻度的认知
1.中滑板刻度
中滑板示Байду номын сангаас图
分课题一 车削外圆和端面
2.小滑板刻度
小滑板每小格为0.02 mm,一大格包含10个小 格,为0.2 mm。也就是 说每进一大格,车刀纵向 (轴向)前进0.2 mm, 车完后的工件长度尺寸减 小0.2 mm。
车削简单轴类零件
车削外圆和端面 车阶台轴
一夹一顶车阶台轴
分课题一 车削外圆和端面
知识目标
•掌握外圆车刀的安装方法; •掌握外圆车削的技术方法。
分课题一 车削外圆和端面
一、 45°、90°车刀的基本刃磨步骤
外圆车刀的刃磨
分课题一 车削外圆和端面
二、 外圆车刀的安装、对准中心和紧固方法
1. 以车床后顶尖为基准,车刀放在刀架定位位置上, 刀尖对准后顶尖尖头,将钢直尺放在车床导轨上,垂 直测量,观察出刀尖的尺寸读数,此读数就是刀具所 需安装的中心高。
手动匀速进 给车削端面,保 证表面粗糙度, 切削深度不超过 1 mm。
分课题二 车 阶 台 阶
知识目标
轴类零件外圆的加工方法
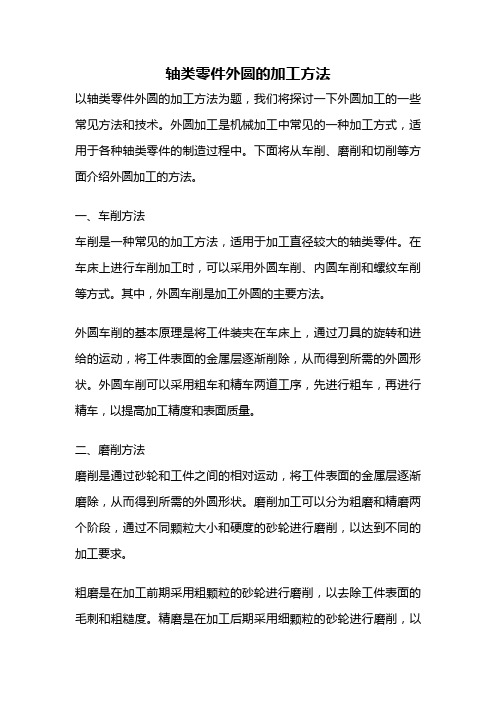
轴类零件外圆的加工方法以轴类零件外圆的加工方法为题,我们将探讨一下外圆加工的一些常见方法和技术。
外圆加工是机械加工中常见的一种加工方式,适用于各种轴类零件的制造过程中。
下面将从车削、磨削和切削等方面介绍外圆加工的方法。
一、车削方法车削是一种常见的加工方法,适用于加工直径较大的轴类零件。
在车床上进行车削加工时,可以采用外圆车削、内圆车削和螺纹车削等方式。
其中,外圆车削是加工外圆的主要方法。
外圆车削的基本原理是将工件装夹在车床上,通过刀具的旋转和进给的运动,将工件表面的金属层逐渐削除,从而得到所需的外圆形状。
外圆车削可以采用粗车和精车两道工序,先进行粗车,再进行精车,以提高加工精度和表面质量。
二、磨削方法磨削是通过砂轮和工件之间的相对运动,将工件表面的金属层逐渐磨除,从而得到所需的外圆形状。
磨削加工可以分为粗磨和精磨两个阶段,通过不同颗粒大小和硬度的砂轮进行磨削,以达到不同的加工要求。
粗磨是在加工前期采用粗颗粒的砂轮进行磨削,以去除工件表面的毛刺和粗糙度。
精磨是在加工后期采用细颗粒的砂轮进行磨削,以提高工件的尺寸精度和表面质量。
三、切削方法切削加工是通过刀具与工件之间的相对运动,将工件表面的金属层逐渐切削掉,从而得到所需的外圆形状。
切削加工可以采用车削切削、铣削切削和车铣复合切削等方式。
车削切削是通过车床上的刀具进行切削加工,根据工件的形状和加工要求选择合适的刀具进行切削。
铣削切削是通过铣床上的刀具进行切削加工,将刀具按照预定的路径进行旋转和进给运动,从而形成所需的外圆形状。
车铣复合切削是将车床和铣床的功能进行组合,通过车床上的主轴旋转和铣床上的进给运动,实现对外圆形状的加工。
总结:以上是轴类零件外圆的加工方法,包括车削、磨削和切削等多种方式。
在实际加工过程中,根据工件的形状、尺寸和加工要求选择合适的加工方法,以确保外圆加工的精度和质量。
此外,还需要注意刀具的选择、刀具的磨损与更换、加工参数的控制等方面的问题,以提高加工效率和质量。
《普通车床加工技术(第2版)》教学讲义 项目二 车削简单轴类工件 11、车削外圆的方法
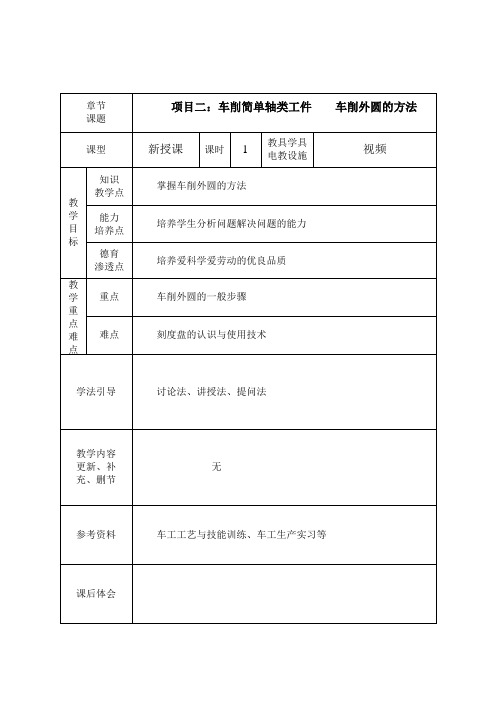
教师活动内容学生活动内容设计意图使用中、小滑板刻度盘时应注意的内容:
根据加工的需要把刻度盘转到所需的位置,如果不慎多
转了几格,不能直接退回多转的格数,必须向相反的方
向退回全部空行程,再将刻度盘转到正确的位置
四、讨论题:
1、请同学分析加工光轴的车削步骤?
五、提问并作记录
六、布置作业
(一)课后作业
(二)预习作业:轴类工件如何测量?分组讨论
回答问题
预习下节课内
容
培养学生
团队合作
意思
培养学生
预习书本
的好习惯。
车削轴类零件
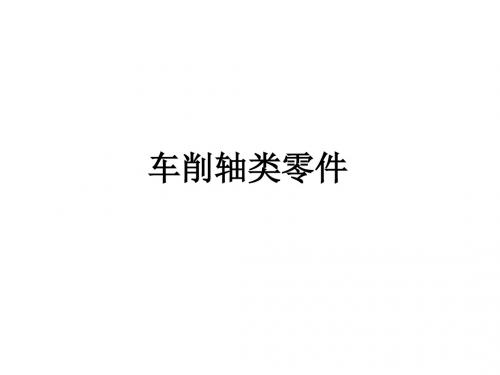
• (4)用一夹一顶装夹 用双顶尖装夹零件精度高,但刚性较差,故在车削 一般轴类零件时采用一端用卡盘夹住,另一端用顶 尖顶住的装夹方法,如图所示。为防止切削时产生 轴向位移,可采用限位支承或台阶限位。其中台阶 限位安全,刚性好,能承受较大切削力,故应用广 泛。
• 4.中心孔、顶尖、拨盘和夹头 (1)中心孔 国家标准 GB/T 145—2001 规定中心孔有A 型(不带护锥)、B 型(带护锥)、C 型带 螺孔)和 R 型(弧形)4 种,如图所示。
3.轴类零件的装夹要求
• 车削加工前,必须将零件放在机床夹 具中定位和夹紧,使零件在整个切削 过程中始终保持正确的位置。根据轴 类零件的形状、大小、精度、数量的 不同,可采用不同的装夹方法。
• (1)在四爪单动卡盘上 装夹 四爪单动卡盘(如图所 示)的卡爪是各自独立运 动的,因此在装夹零件时 必须找正后才可车削,但 找正比较费时。其夹紧力 较大,常用于装夹大型或 形状不规则的零件。四爪 单动卡盘的卡爪可装成正 爪或反爪,反爪用于装夹 较大的零件。
车削轴类零件
• 一、轴类零件的种类 轴类零件由圆柱表面、端面、沟槽、阶 台和倒角等组成, 它有光滑轴、阶台轴等几 种。
• 二、轴类零件的特点 轴是各种机器中最常见的零件之一。它的轴向尺寸一 般大于径向尺寸,如图所示。
• ① 圆柱表面:一般用于支承轴上传动零件。 ② 端面和台阶:常用来确定安装零件的轴 向位置。 ③ 沟槽:使磨削或车螺纹时退刀方便,并 使零件装配时有一个正确的轴向位置。 ④ 键槽:主要是周向固定轴上传动零件和 传递扭矩。 ⑤ 螺纹:固定轴上零件的相对位置。 ⑥ 倒角:去除锐边防止伤人,便于轴上零 件的安装。 ⑦ 圆弧:提高强度和减少应力集中,有效 防止热处理中裂纹的产生。
细长轴的车削加工要领

细长轴类零件的车削加工1. 中心架和跟刀架在细长轴零件加工中的应用车削细长轴工件,长度是直径10~12倍以上的长轴时,如车床光杠、丝杠等,由于这些轴本身的刚性差,加上切削力、切削热和震动等影响,车削时易产生弯曲、锥度、腰鼓度和竹节形等缺陷。
此外,在车削过程中还会引起震动,影响工件表面粗糙度。
为了防止这种现象产生,我们可以应用一种叫做中心架的特殊支承夹具。
中心架和跟刀架是车床附件之一,用卡盘顶针与中心架,或前后顶针与跟刀架装夹,可提高切削加工系统的刚性。
使用这些附加的装卡工具,可以增加工件的装卡刚度,减少震动,保证加工质量,避免零件产生鼓面,提高工件表面形状精度和表面粗糙度,并允许采用大切削用量加工,提高劳动生产率。
下面分别就中心架与跟刀架在细长轴零件中的应用加以说明。
一、中心架在细长轴零件加工中的应用1.中心架的结构中心架的结构组成如图5-1所示。
中心架一般固定在床面一定位置上,如图5-1(b)所示。
它的主体座l通过压板4和螺母5紧固在床面上。
盖子3与主体1用销作活落连接,盖子3可以打开或盖住,并用螺钉2固定。
三个爪的向心或离心位置,可以用螺钉6调节,以适应不同直径大小的工件,并用螺钉9紧固爪7和8,使爪在需要位置上固定不动。
2.中心架的使用(1)中心架的使用调整方法工件装上中心架之前,先在毛坯中间处车一条安装中心架卡爪的沟槽,槽的直径等于工件的直径,其宽度略比爪宽大些。
接着把中心架安装在床面适当位置上并加以固定,打开盖子3,把工件安装在两顶针中间(床尾要先调整好),用划针盘或百分表检查槽是否跳动,然后将盖子3盖好,并调整中心架3个爪,使他们与工件沟槽轻轻接触。
这时慢慢转动工件,看是否能转得动。
在爪与工件之间最好垫一层铜皮或平皮带,并加些润滑油,或者3个爪用夹布胶木制造,这样可防止擦伤工件表面。
在车削大型工件或工件转速较高时,就必须采用带滚动轴承的中心架,如图5-2所示。
(2)车削步骤车削时,先车一端,一直车到沟槽为止。
车削轴类零件

1)台阶长度不正确,不垂直,不清晰。 原因是操作粗心,测量失误,自动走刀控制不当,刀尖不锋利, 车刀刃磨或安装不正确。 2)表面粗糙度差。 原因是车刀不锋利,手动走刀不均匀或太快,自动走刀切削用 量选择不当。
一、车削轴类零件
四)、切断和车外沟槽
一、车削轴类零件
常见的各种沟槽
一、车削轴类零件
车工短期培训
车削轴类零件
一、车削轴类零件
装夹方法
车削方法
质量分析
一、车削轴类零件
• 1、什么叫轴类零件. • 答:长度尺寸超过直径在三倍以上的旋体零件。轴类零件可分: 光滑轴,阶台轴两种。此外还有比较复杂的空心轴(机床主轴) 等。 • 2、轴类零件的组成.
• 答:轴类工件一般由圆柱表面、阶台、端面、退刀槽、倒角、圆 弧等部分组成。
二)、车端面
一、车削轴类零件
3、车端面时应注意以下几点
• 1)车刀的刀尖应对准工件中心,以免车出的端面中心留有凸 台。 • 2)偏刀车端面,当背吃刀量较大时,容易扎刀。背吃刀量ap 的选择:粗车时ap=0.2mm~1mm,精车时ap=0.05 mm~0.2mm。 • 3)端面的直径从外到中心是变化的,切削速度也在改变,在 计算切削速度时必须按端面的最大直径计算。 • 4)车直径较大的端面,若出现凹心或凸肚时,应检查车刀和 方刀架,以及大拖板是否锁紧。
3)外径有锥度:
•原因是吃刀深度过大,刀具磨损;刀具或拖板松动;用小拖板车削时转盘下基
准线不对准“0”线;两顶尖车削时床尾“0”线不在轴心线上;精车时加工余量不
足造成的。
一、车削轴类零件
减小工件表面粗糙度值的方法
减小残留面积高度
避免工件表面产生毛刺 避免磨损亮斑 防止切屑拉毛已加工表面 防止和减小振纹 合理选用切削液
中职教育-《车工工艺与技能实训》项目二 车削轴类工件.ppt

1.直进法 2.左右借刀法 3.反切法
图2-13 切削方法
任务刀与切槽刀的区别
1.切刀的角度 2.切刀的刃磨 先粗磨侧面,再磨前刀面;然后精磨侧面和前刀面。 3.切断刀与切槽刀的区别 切断刀与切槽刀的刀刃几何角度基本一样,只是切断刀要比切槽刀 的刀刃长。
图2-1 轴的种类
项目导读 轴类零件简介
图2-2 双向台阶轴
任务一 车端面、外圆和倒角
❖ 一、外圆车刀的种类及用途
1.种类 常用外圆车刀有90°、75°、45°外圆偏刀。
图2-3 3种常用车刀外形
2.用途 90°外圆偏刀根据进给方向不同分为左偏刀(又称正偏刀)和右偏 刀。左偏刀常用车削外圆和左向台阶,也可以车削粗而短的工件端面。 右偏刀用于加工外圆和右台阶。
在切削加工过程中,一般分粗车和精车。
❖ 四、常用的测量工具
常用的测量工具有游标卡尺和外径千分尺。其中游标卡尺在学校实 习车间更为常用。
❖ 五、用手动进给车端面、外圆和倒角
1.车端面 2.车外圆 车削外圆时,分划线、试切和试测量、加工三个阶段。 3.车倒角
任务一 车端面、外圆和倒角
图2-7 车端面
任务一 车端面、外圆和倒角
任务一 车端面、外圆和倒角
图2-4 90°车刀
任务一 车端面、外圆和倒角
图2-5 75°车刀
任务一 车端面、外圆和倒角
图2-6 45°车刀
任务一 车端面、外圆和倒角
❖ 二、定位基准的选择原则
定位基准选择的是否合理,对保证工件加工后尺寸精度和形位精度 起着决定性的作用。它分为粗基准和精基准。
❖ 三、粗车和精车的概念
任务二 切槽和切断
图2-14 切刀的角度
细长轴车削加工问题浅析

细长轴车削加工问题浅析
细长轴车削加工是制造业中非常常见的一种加工方式,它主要适用于制造特殊类型的
轴类工件。
在细长轴车削加工过程中,常常会面临一些问题,比如加工难度大、工艺复杂、加工精度要求高等。
本文将对细长轴车削加工的问题进行浅析,并提出一些解决方案。
细长轴车削加工的问题主要包括以下几个方面:
1. 加工难度大:由于轴类工件的细长特点,使得其在车削过程中容易产生较大的振
动和变形,因此加工难度较大。
长时间的振动会导致切削力不稳定,严重时还会影响加工
精度和表面质量。
解决方案:针对加工难度大的问题,可以采取以下措施:选择较高刚性的车床和工具,控制切削速度和进给速度,用适当的切削液进行冷却和润滑,合理设计刀具的放置位置,
减小振动和变形。
2. 工艺复杂:在细长轴车削加工中,由于工件的长、细和特殊形状,使得工艺过程
较为复杂。
加工过程需要经过多个环节,包括车削、切割、定位、研磨等。
解决方案:为了简化工艺流程,可以考虑采用特殊的夹具和定位装置,提高工件的加
工精度和稳定性;合理安排每个工艺环节的顺序和方法,确保加工过程的稳定性和一致
性。
3. 加工精度要求高:细长轴车削加工中,由于工件的细长特点,其加工精度要求较高。
包括直径的精度、圆度的精度、轴心的精度等。
解决方案:对于加工精度要求高的轴类工件,可以采取以下措施:选择高精度的车床
和工具;采用刚性好的定位装置,确保工件的稳定性和一致性;控制切削参数,包括切削
速度、切削深度和进给速度等;加工过程中定期测量和调整,确保加工精度的达标。
轴类零件的车削步骤
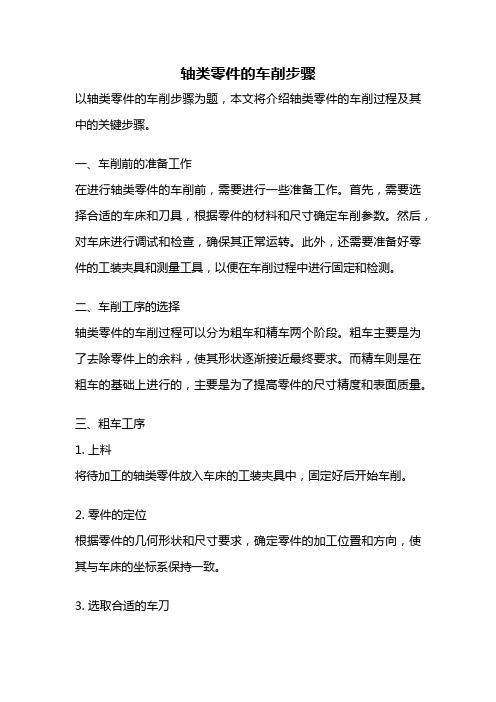
轴类零件的车削步骤以轴类零件的车削步骤为题,本文将介绍轴类零件的车削过程及其中的关键步骤。
一、车削前的准备工作在进行轴类零件的车削前,需要进行一些准备工作。
首先,需要选择合适的车床和刀具,根据零件的材料和尺寸确定车削参数。
然后,对车床进行调试和检查,确保其正常运转。
此外,还需要准备好零件的工装夹具和测量工具,以便在车削过程中进行固定和检测。
二、车削工序的选择轴类零件的车削过程可以分为粗车和精车两个阶段。
粗车主要是为了去除零件上的余料,使其形状逐渐接近最终要求。
而精车则是在粗车的基础上进行的,主要是为了提高零件的尺寸精度和表面质量。
三、粗车工序1. 上料将待加工的轴类零件放入车床的工装夹具中,固定好后开始车削。
2. 零件的定位根据零件的几何形状和尺寸要求,确定零件的加工位置和方向,使其与车床的坐标系保持一致。
3. 选取合适的车刀根据零件的材料和形状,选择合适的车刀,并进行安装和调整。
4. 确定车削参数根据零件的材料和要求,确定车削的进给量、切削速度和主轴转速等参数。
5. 粗车加工按照预定的车刀路径,进行轴类零件的粗车加工。
在车削过程中,要保证工件与车刀之间的切削速度和进给量的匹配,以避免零件表面出现过大的切削力和热量积聚。
6. 进行必要的修整粗车完成后,需要对零件进行必要的修整,包括切削面的清理和表面的修整,以便为后续的精车工序做好准备。
四、精车工序1. 选取合适的车刀根据零件的要求,选择合适的车刀,并进行安装和调整。
2. 确定车削参数根据零件的材料和要求,确定车削的进给量、切削速度和主轴转速等参数。
在精车过程中,要更加注重表面质量和尺寸精度的控制。
3. 精车加工按照预定的车刀路径,进行轴类零件的精车加工。
在车削过程中,要注意切削速度、进给量和切削深度的控制,以确保零件的表面质量和尺寸精度满足要求。
4. 检测与修整精车完成后,需要对零件进行检测和修整。
使用合适的测量工具对零件的尺寸和表面质量进行检测,如有需要,则进行必要的修整,以保证零件的质量和精度。
轴类零件加工工艺的过程
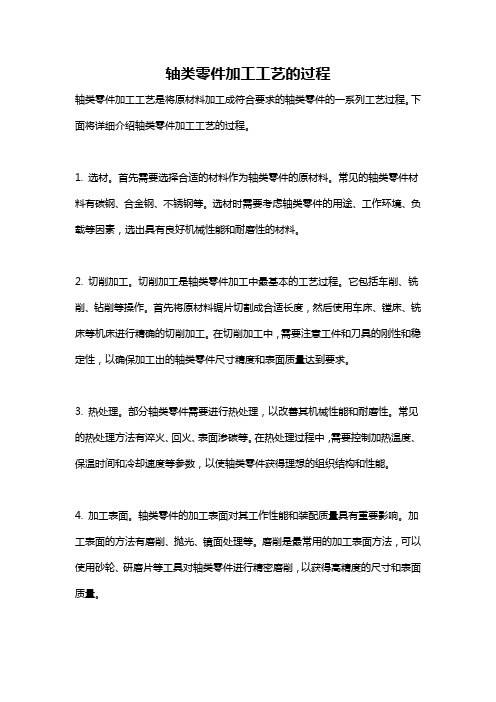
轴类零件加工工艺的过程轴类零件加工工艺是将原材料加工成符合要求的轴类零件的一系列工艺过程。
下面将详细介绍轴类零件加工工艺的过程。
1. 选材。
首先需要选择合适的材料作为轴类零件的原材料。
常见的轴类零件材料有碳钢、合金钢、不锈钢等。
选材时需要考虑轴类零件的用途、工作环境、负载等因素,选出具有良好机械性能和耐磨性的材料。
2. 切削加工。
切削加工是轴类零件加工中最基本的工艺过程。
它包括车削、铣削、钻削等操作。
首先将原材料锯片切割成合适长度,然后使用车床、镗床、铣床等机床进行精确的切削加工。
在切削加工中,需要注意工件和刀具的刚性和稳定性,以确保加工出的轴类零件尺寸精度和表面质量达到要求。
3. 热处理。
部分轴类零件需要进行热处理,以改善其机械性能和耐磨性。
常见的热处理方法有淬火、回火、表面渗碳等。
在热处理过程中,需要控制加热温度、保温时间和冷却速度等参数,以使轴类零件获得理想的组织结构和性能。
4. 加工表面。
轴类零件的加工表面对其工作性能和装配质量具有重要影响。
加工表面的方法有磨削、抛光、镜面处理等。
磨削是最常用的加工表面方法,可以使用砂轮、研磨片等工具对轴类零件进行精密磨削,以获得高精度的尺寸和表面质量。
5. 组装。
在零件加工完成后,需要进行零件的组装。
轴类零件的组装通常需要与其他零件配合使用,如轴套、轴承、齿轮等。
在组装过程中,需要注意零件的配合间隙和装配顺序,以确保零件的配合精度和工作可靠性。
6. 检测。
最后,对加工完成的轴类零件进行检测。
常见的检测方法有尺寸测量、硬度测量、外观检查等。
通过检测,可以判断轴类零件是否达到要求,并进行必要的修正和改进。
综上所述,轴类零件加工工艺的过程包括选材、切削加工、热处理、加工表面、组装和检测等环节。
每个环节都需要严格控制,以确保加工出的轴类零件具有良好的机械性能、尺寸精度和表面质量,能够满足工程需求。
车削轴类工件时常见的加工误差与控制

好, 必 须更 换齿 轮 。使 齿轮 啮合状态 良好 , 消 除齿 轮 传动 时产 生 的冲击 , 减轻 产 生振 动给 车 削 带 来 的 振
纹。
1 . 3 套类 工件伸 出太长
控 制 方法 : 安装 工件要 牢 固 , 加工 套类 工件 不 能 伸 出过 长 , 车 刀要 刃磨锋 利 , 这 样可避 免 工件表 面 出
可使刀刃强度和散热性降低, 同时增加刀刃 的锋利
第 3期
性, 使 摩擦 减 小 。
宗春 英 : 车削 轴类 工件 时常 见 的加工 误 差与控 制
l 7
出方 向 、 刀 尖 强度 和 散 热 ; 影 响 切入 的平 稳 性 、 切 削
后 角 的选 择 原 则 : 粗加工 、 承 受 冲 击 载 荷 的 刀
拧 紧。有条 件 时 , 更换 带有 橡胶 垫 圈的 调整垫 块 。 1 . 2 车床 主轴承 松动 或不 圆 。 主 轴上 的齿 轮啮 合 不
好。 主轴后 轴承 松动 或不 圆
度, 应选择较小 的前 角, 反之精加工选择 较 大的前
角; 成 形刀 具 为防 止 刀 刃 畸变 , 常 取 较 小 的前 角 ; 刀 具 材料 的强 度低 、 韧性差时, 应 取 较 小 的前 角 ; 工 艺
不得犬 宗春英
( 宁夏职业技术学 院, 宁夏 银川 7 5 0 0 0 2 )
摘
要: 主要 阐述 了车削轴类 工件过程中工件产生振纹、 表面拉毛 、 粗糙 度高 、 精轴类工 件 ; 误差 ; 控制
中 图分 类 号 : T G 8 3
现代机械制造业 中, 不论是数控车床还是普通 卧式 车床 上车 削轴 类 工 件是 最 基 本 、 最 常见 的一种 加工过程 。无论操作者是采取手动操作或 自动进给 方法 , 都必须严格保持加工工件与车刀之 间的运动 关系: 主轴 每转 一 转 , 刀 具 应均 匀 移 动 一 个 进 给量 。
轴类零件加工工艺过程
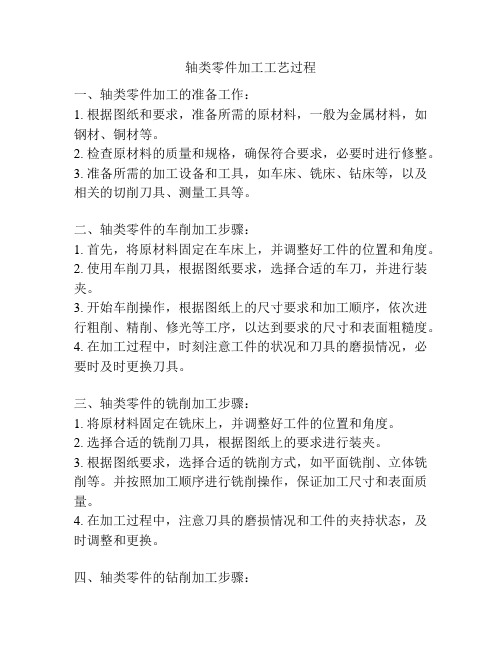
轴类零件加工工艺过程一、轴类零件加工的准备工作:1. 根据图纸和要求,准备所需的原材料,一般为金属材料,如钢材、铜材等。
2. 检查原材料的质量和规格,确保符合要求,必要时进行修整。
3. 准备所需的加工设备和工具,如车床、铣床、钻床等,以及相关的切削刀具、测量工具等。
二、轴类零件的车削加工步骤:1. 首先,将原材料固定在车床上,并调整好工件的位置和角度。
2. 使用车削刀具,根据图纸要求,选择合适的车刀,并进行装夹。
3. 开始车削操作,根据图纸上的尺寸要求和加工顺序,依次进行粗削、精削、修光等工序,以达到要求的尺寸和表面粗糙度。
4. 在加工过程中,时刻注意工件的状况和刀具的磨损情况,必要时及时更换刀具。
三、轴类零件的铣削加工步骤:1. 将原材料固定在铣床上,并调整好工件的位置和角度。
2. 选择合适的铣削刀具,根据图纸上的要求进行装夹。
3. 根据图纸要求,选择合适的铣削方式,如平面铣削、立体铣削等。
并按照加工顺序进行铣削操作,保证加工尺寸和表面质量。
4. 在加工过程中,注意刀具的磨损情况和工件的夹持状态,及时调整和更换。
四、轴类零件的钻削加工步骤:1. 将原材料固定在钻床上,并调整好工件的位置和角度。
2. 选择合适的钻孔刀具,根据图纸要求进行装夹。
3. 根据图纸上的孔径要求,选择合适的钻头,并进行设定,调整钻头的速度和进给量。
4. 开始钻削操作,根据图纸上的孔径位置进行钻孔,保证加工尺寸和孔壁的质量。
5. 在加工过程中,注意刀具的磨损情况和冷却液的使用,及时调整和更换。
五、轴类零件加工的后续工序:1. 进行工件的检验,包括尺寸测量、表面质量等,确保符合要求。
2. 进行必要的热处理、表面处理等工艺,以提高工件的性能和耐用度。
3. 进行最后的整理和打磨工作,使工件达到最终的要求。
4. 进行产品的包装和出库。
以上就是轴类零件加工的基本工艺过程,通过严格按照要求进行加工操作,可以确保加工出高质量的轴类零件。
加工过程中需要密切关注工件的状况和刀具的磨损情况,及时调整和更换,以保证加工质量和工艺效率。
轴类零件的加工方法

轴类零件的加工方法
轴类零件的加工方法包括以下几种:
1. 车削加工:通过旋转的刀具将工件的材料逐渐削除,形成所需的轴状结构。
车削加工可以分为外圆车削和内圆车削两种形式。
2. 镗削加工:利用旋转刀具进行波纹状运动,将工件内孔的材料逐渐削除,形成所需的内轴孔。
3. 铣削加工:通过刀具在工件表面上进行旋转和直线运动,将工件表面的材料逐渐削除,形成所需的轴状结构。
铣削加工可以分为平铣和立式铣两种形式。
4. 磨削加工:利用磨削工具对工件进行高速磨削,精确地去除工件表面的材料,以达到精密加工的目的。
磨削加工可以分为平面磨削和外圆磨削两种形式。
5. 钻削加工:通过旋转刀具对工件进行钻孔,形成所需的孔状结构。
钻削加工可以使用钻头进行,也可以使用钻床进行。
6. 切削加工:通过使用切削刀具对工件进行切削,将工件材料一部分削除,形成所需的轴形结构。
切削加工可以包括切削、切削、切割等操作。
此外,还可以使用其他加工方法如冲压、锻造、热处理等进行轴类零件的加工。
具体的加工方法选择取决于轴类零件的材料、尺寸、形状等要求。
车工工艺与技能训练6[1]
![车工工艺与技能训练6[1]](https://img.taocdn.com/s3/m/a520aff5998fcc22bcd10d24.png)
项目二 车削轴类零件
2.3 轴类工件各部分的车削与测量
一、车削外圆 车削轴类工件一般分粗车和精车两个阶段,粗车时,为了提高劳动生产率,应 尽快地将毛坯上的多余金属车去。精车时余量小,必须使工件达到图样上规定的尺 寸精度、形位精度和表面粗糙度。 1.外圆车刀 (1)粗车刀 粗车刀必须适应粗车时切削深、进给快的特 点,要求车刀有足够的强度,能在一次进给中车去较多的余量。 选择粗车刀几何参数的一般原则是: ① 为了增加刀头强度,前角 和后角 应取小些。 但前角过小会使切削力增大。 ② 主偏角 不宜太小,太小容易引起振动。当工 件形状许可时,最好选用75°左右,因为这时刀尖角 较大,不仅能承受较大的切削力,而且还有利于刀尖散 热。
项目二 车削轴类零件
2.3 轴类工件各部分的车削与测量
一、车削外圆 (2)刻度盘的原理和应用 车外圆时,背吃刀量可利用中滑板的刻度盘来控制。 中滑板刻度盘安装在中滑板丝杠上。当中滑板的摇动手柄带动刻度盘转一周 时,中滑板丝杠也转一周。这时固定在中滑板上与丝杠配合的螺母沿丝杠轴线 方向移动了一个螺距,因此安装在中滑板上的刀架也移动了一个螺距。如果中 滑板丝杠螺距为5 mm,当手柄转一周时,刀架就移动了5 mm。若把刻度盘 圆周等分100格,当刻度盘转过一格时,中滑板则移动了5 mm/100= 0.05 mm。所以,中滑板刻度盘转过一格,车刀横向移动的距离可按下式计算:
度。
项目二 车削轴类零件
2.3 轴类工件各部分的车削与测量
一、车削外圆 (2)车刀垫铁要平整,数量要少,垫铁 应与刀架对齐。车刀至少要用两个螺钉压紧在 刀架上,并逐个轮流拧紧。 (3)车刀刀尖一般应与工件轴线等高 (图2-11a),否则会因基面和切削平面的位 置发生变化,而改变车刀工作时的前角和后角 的数值。当车刀刀尖高于工件轴线时(图2- 11b),会使后角减小,增大车刀后刀面与工件 间的摩擦;当车刀刀尖低于工件轴线时(图2-
轴类零件加工方法
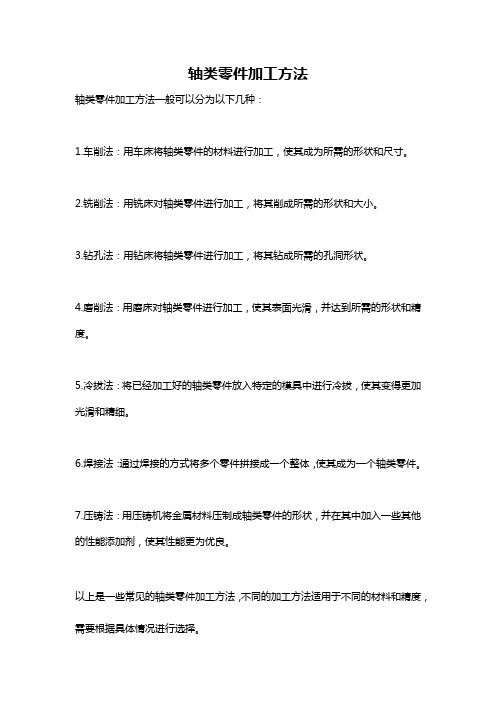
轴类零件加工方法
轴类零件加工方法一般可以分为以下几种:
1.车削法:用车床将轴类零件的材料进行加工,使其成为所需的形状和尺寸。
2.铣削法:用铣床对轴类零件进行加工,将其削成所需的形状和大小。
3.钻孔法:用钻床将轴类零件进行加工,将其钻成所需的孔洞形状。
4.磨削法:用磨床对轴类零件进行加工,使其表面光滑,并达到所需的形状和精度。
5.冷拔法:将已经加工好的轴类零件放入特定的模具中进行冷拔,使其变得更加光滑和精细。
6.焊接法:通过焊接的方式将多个零件拼接成一个整体,使其成为一个轴类零件。
7.压铸法:用压铸机将金属材料压制成轴类零件的形状,并在其中加入一些其他的性能添加剂,使其性能更为优良。
以上是一些常见的轴类零件加工方法,不同的加工方法适用于不同的材料和精度,需要根据具体情况进行选择。
车削加工基本工艺【车削加工基础篇 】

车削加工在机械生产中具有良好的适应性,其切削过程较为平稳,而且是连续进行,而且切削力的变化较小。
对被加工零件个表面位置精度有一定的保证,适合对有色金属零件进行精加工。
本文就来具体介绍一下车削加工的基本工艺。
一、车轴类工件轴类工件时机器中经常遇到典型零件之一,车床车削也是比较常用、比较普遍的加工方法。
轴类工件是旋转体零件,长度大于直径,由外圆柱面、断面和台阶组成。
1、外圆车刀:常用的外圆车刀有直头外圆车刀、90°偏刀和45°偏刀。
2、车外圆:直头外圆车刀强度较好;常用于粗车外圆,90°偏刀主偏角大,适合车外圆、断面和台阶;45°弯头车刀适用于车削不带台阶的光滑轴。
二、车端面和台阶圆柱体两端的平面叫做端面。
由直径不同的两个圆柱体相连的部分叫做台阶。
1、车端面的方法:右偏刀车端面,是由外向里进刀,容易扎入工件而形成凹面;用右偏刀由中心向外车削端面,车削顺利,不容易产生凹面。
用左偏刀由外向中心车端面,利用主切削刃切削,切削条件有所改善。
弯头车刀车削端面以主切削刃进行,很顺利。
它不仅可用于车端面,还可以车外圆和倒角。
2、车台阶方法:车削低于5mm台阶工件,可以让偏刀在车外圆一次完成。
车削高于5mm 台阶的工件,因为肩部过款,车削会引起震动。
因此,高台阶工件可先用外圆车刀把台阶车程大致形状,然后由偏刀分层切削完成。
三、车槽与切断1、车槽:在工件表面上车沟槽的方法叫做切槽,槽的形状有外槽、内槽和端面槽。
(1)切槽刀:常选用高速钢切槽刀。
(2)切槽方法·对于精度不高和宽度较窄的矩形沟槽,可以用刀宽等于槽宽的切槽刀,采用直进法一次车出。
·车削宽槽,可以多次直进法切削,并在槽两侧留一定精车余量。
·车削较小圆弧形槽,可以用成形车刀车削。
·较大圆弧槽,可以使用双手联动车削,用样板检查修整。
2、切断:切断刀的形状与切槽刀相似,常用切断方法有直进法和左右借刀法,直进法用于铸铁等脆性材料;左右借刀法用于钢等塑性材料。
- 1、下载文档前请自行甄别文档内容的完整性,平台不提供额外的编辑、内容补充、找答案等附加服务。
- 2、"仅部分预览"的文档,不可在线预览部分如存在完整性等问题,可反馈申请退款(可完整预览的文档不适用该条件!)。
- 3、如文档侵犯您的权益,请联系客服反馈,我们会尽快为您处理(人工客服工作时间:9:00-18:30)。
本章学习目标
☆ 掌握车削轴类零件常用的车刀 ☆ 掌握车削轴类零件时工件的装夹 ☆ 掌握钻中心孔的一般原理和技巧 ☆ 掌握车外圆、平面和阶台的操作要点和技巧
本
第一节 第二节 第三节
章
大
纲
车削轴类零件用的车刀 工件的装夹 轴类零件的车削
什么是轴类零件?
基础知识
我们通常把长度大于直径三倍以上的工件称为轴类零件, 它们通常由圆柱面和端面组成,按用途可分为等直径轴、台 阶轴、偏心轴和空心轴等。
硬质合金(YT类)
第一节 车削轴类零件用的车刀
硬质合金刀头
第一节 车削轴类零件用的车刀
常用陶瓷刀具
第一节 车削轴类零件用的车刀
基础知识
2.车刀的种类和用途 (1)外圆与端面车刀,具体又可分为偏刀以及弯刀等类型 (2)车断刀 (3)内孔车刀 (4)圆头刀 (5)螺纹车刀
偏刀 弯刀
切断刀
内孔车刀
圆头刀
第一节 车削轴类零件用的车刀
④装车刀用的垫片要平整,尽可能地用厚垫片以 减少片数,一般只用2-3片。如垫刀片的片数太多 或不平整,会使车刀产生振动,影响切削。并使 各垫片在刀杆正下方,前端与刀座边缘齐
⑤车刀装上后,要紧固刀架螺钉,一般要紧固两 个螺钉。紧固时,应轮换逐个拧紧。同时要注意, 一定要使用专用扳手,不允许再加套管等,以免 使螺钉受力过大而损伤
第二节 工件的装夹
两顶尖间装夹工件:
第二节 工件的装夹
第二节 工件的装夹
两顶尖车削轴类零件视频
第二节 工件的装夹
基础知识
四、一夹一顶装夹工件 用两顶尖装夹工件虽然精度很高,但刚性较差,因此 ,车削一般轴类零件,尤其是较重的工件,不能用两顶 尖装夹,而是采用一端夹住(用三爪自定心卡盘或四爪 单动卡盘),另一端用后顶尖顶住的装夹方法。这种装 夹方法比较安全,能承受较大的进给力,因此应用很广 泛。
第二节 工件的装夹
四爪卡盘:
第二节 工件的装夹
基础知识
三、在两顶尖间装夹工件 对于较长的或必须经过多次装夹才能加工好的工件, 如长轴、长丝杠等的车削,或工序较多,在车削后还要 铣削和磨削的工件。为了保证每次装夹是的装夹精度( 如同轴度要求),可用两顶尖来装夹。两顶尖装夹工件 方便,不需要找正,装夹精度高。
第一节 车削轴类零件用的车刀
刀尖高于中心,后角α 0减小,摩擦加剧,表 面粗糙度增大;同时γ 0增大,振动加剧。 车端面时有凸头; 实际尺寸会增大;
第一节 车削轴类零件用的车刀
低于中心,前角γ 0减小,切削力集中于刀刃,容易崩刃。 车端面时有凸头; 实际外径增大;
第一节 车削轴类零件用的车刀
③车刀刀杆应与车床主轴轴线垂直
基础知识
4.车刀的主要切削角度
N 1 - N1 切削表面 已加工表面 副后角
o
N-N
后角 N1
o
前角 楔角 切削角 副偏角 K r N K 刃倾角
s o o
o
副前角
o
待加工表面 N K 主偏角K r N1 刀尖圆弧半径 r 刀尖角
r
第一节 车削轴类零件用的车刀
基础知识
5.对车刀的要求:
轴类零件的车削一般可分为粗车和精车两个阶段。 粗车时留有一定的精车余量外,不要求工件达到图纸要 求的尺寸精度和表面粗糙度,因此应尽快地将毛坯上的加 工余量车去,以提高劳动生产率。 精车时必须使工件达到图样或工艺上规定的尺寸精度和 表面粗糙度。 于粗车和精车的目的不同,因此对所使用的车刀要求也 不一样。
第二节 工件的装夹
基础知识
工件的装夹就是将工件在机床上或夹具中定位、夹紧的 过程。 由于工件的形状、大小和加工数量不同,因此可采用的 夹紧方法也不同,一下是常用的几种装夹方法:
第二节 工件的装夹
基础知识
一、在三爪自定心卡盘上装夹工件
三爪自定心卡盘能自动定心,不需花很多时间去找正工件,安 装效率高,但夹紧力没有四抓卡盘大。所以适用于装夹大批量的 中小型规格的零件。 三爪自定心卡盘一般有正反两副卡爪、或一副正反都能使用的 卡爪,各卡爪都有编号,在装卡爪时应按顺序安装。还有一种装 配式卡爪,只要拆下卡爪上的螺钉,即可调向或换装软爪。必须 注意用正爪装夹工件时,工件直径不能太大,卡爪伸出卡盘圆周 一般不超过卡爪长度的 1/3 ,否则卡爪与平面螺纹啮合很少,受 力时容易使卡爪上的螺纹碎裂而产生事故。所以装夹大直径工件 时,应尽量用反爪。
第一节 车削轴类零件用的车刀
第一节 车削轴类零件用的车刀
技能训练
• • • • • • • • 【训练内容】 车刀的刃磨。 【预备知识】 1.砂轮的选择 2.磨刀前的准备 3.磨刀时的注意事项 4.车刀的磨削顺序 5.车刀角度的检测
第一节 车削轴类零件用的车刀
技能训练
• 【操作步骤】 • (1)粗磨主后刀面和副后刀面,同时磨出后角、主偏角和 副偏角。 • (2)粗精磨前刀面,并磨出前角。 • (3)精磨主、副刀面。 • (4)修磨刀尖角。
第二节 工件的装夹
基础知识
(2)中心钻的中心与工件的中心有偏差。 这个原因主要是车床尾座中心与主轴中心不一致造成的。 在进行钻中心孔加工工序时,首先要确定一下尾座与主轴的 中心位置是不是准确,如是左右的偏差,可直接调整尾座。调 整方法是:尾座两边各有一个调整螺丝,用板手旋转调整螺丝 ,直至尾座中心与主轴中心重合。如果是尾座偏低,就需要将 尾座拆开,在尾座中间层内垫入厚薄不同的薄片;如果是尾座 偏高,就要铲刮尾座。(最好不要去动车头箱)。
第一节 车削轴类零件用的车刀
基础知识
• 1.车刀材料及其应用 • 目前常用刀具材料有碳素工具钢、合金工具钢、高速钢、硬 质合金以及陶瓷材料等。 • 生产上应用最多的是高速钢(W18Cr4V)、硬质合金(YT 类)以及陶瓷材料。
第一节 车削轴类零件用的车刀
高速钢(W18Cr4V)
第一节 车削轴类零件用的车刀
第二节 工件的装夹
卡盘内装轴向限位支承
使用阶台作为限位支承
第二节 工件的装夹
第ห้องสมุดไป่ตู้节 工件的装夹
常用顶尖:
顶尖分为前顶尖和后顶尖2种,在车削加工过程中,顶尖 用于确定零件的中心,并承受工件的重量及切削力。 ① 固定顶尖。 固定顶尖定心准确,刚性好,切削时不易产生振动。但是 加工时,中心孔与工件之间的滑动摩擦易产生高热,烧坏中 心孔和顶尖,通常适合于低速车削 。 ② 回转顶尖 回转顶尖在加工时跟随工件一起转动。可以用于较高转速 的加工环境下,摩擦小,但是与固定顶尖相比,其定心精度 和刚度都较差 。
第二节 工件的装夹
第二节 工件的装夹
基础知识
第二节 工件的装夹
基础知识
二、在四爪单动卡盘上装夹工件 在四爪卡盘上装夹工件必须将加工部分的旋转中心找正到与 车床主轴旋转中心重合才能车削,在找正时必须注意一下几点: 1. 当工件的外圆或平面不需要加工时,为了保证外形正确, 必须找正不加工部位,对加工部位,只要保证有一定加工余量即 可。 2. 当工件的各部位加工余量不均匀时,应着重找正余量少的 部位。 3.一般情况下,为了找正方便,在卡爪与工件之间垫铜片。 4. 找正前必须做好安全防护措施,在车床导轨上方一木板, 并用尾座活顶尖通过辅助工具顶住工件,防止工件找正时掉落。
第二节 工件的装夹
基础知识
(1)A型中心孔。 A型中心孔又称不带护锥中心孔,只包含60°锥孔 。这种 中心孔仅在粗加工或不要求保留中心孔的工件上采用,其直 径尺寸d和D主要根据轴类工件的直径和质量来确定。 A型中心孔的主要缺点是孔口容易碰坏,致使中心孔与顶 尖锥面接触不良,从而引起工件的跳动,影响工件的精度。
基础知识
2.中心钻折断的原因及预防方法
在车床上加工轴类零件,往往需要在轴的两端面钻中心孔。中 心钻一般都是高速钢材料制成,钻头部位直径比较小,在实际 加工过程中,一不小心中心钻就会折断。 中心钻折断的原因主要有一下几点: (1)工件端面留有凸头。 由于在加工端面时,车刀中心没有对准,或高或低,造成端 面中心留有少许凸头。中心钻进入端面时,钻芯尖顶在凸头上 ,稍有偏斜,中心钻头就会折断。在加工端面时,车刀的安装 高度一定要与工件的旋转中心一致,车削端面时,决不能在工 件中心留下一点点的凸面,如果用的是45°刀,还可在工件中 心处车上一个小坑,就更利于中心钻的定位。
螺纹车刀
第一节 车削轴类零件用的车刀
基础知识
各种车刀的具体用途如图所示。
各种车刀的用途
第一节 车削轴类零件用的车刀
基础知识
3.外圆和端面车刀的种类和用途 外圆和端面车刀用于车削工件外圆、阶台和端面,主要有 以下3种类型。 (1)90°外圆车刀。 90°外圆车刀俗称偏刀,其主偏角Kr=90°,如书中图3-1 所示。这种车刀主偏角大,切削工件时,作用于工件的径向 切削力小,工件不易顶弯,适合于车削细长轴。 按照加工时进刀方向不同可分为右偏刀和左偏刀2种类型。
第一节 车削轴类零件用的车刀
基础知识
(1)对粗车刀的要求:
粗车刀应能适应切削深、进给快的特点,主要要求车刀 有足够的强度,能一次车去较多的余量。具体几何参数书 中P57。
第一节 车削轴类零件用的车刀
基础知识
(2)对精车刀的要求:
精车时要求达到工件的尺度精度和较细的表面粗造度, 并且切去的金属较少,因此要求车刀锋利,刀刃平直光洁, 刀尖处必要时还可磨出修光刃。切削时,必须使切削排向 工件待加工表面方向。具体几何参数书中P58。
第一节 车削轴类零件用的车刀
基础知识
(2)75°外圆车刀。 75°外圆车刀的刀尖角εr>90°,刀头强度高,耐用,如书 中图3-4所示。这种车刀适合于粗加工外圆或强力切削铸件 、锻件等余量较大的工件。 75°外圆车刀也有右偏刀和左偏刀之分。左偏刀还可以用来 切削铸件、锻件等上的大平面。
第一节 车削轴类零件用的车刀