车架总成(半承载)设计规范
车架总成的包装规范
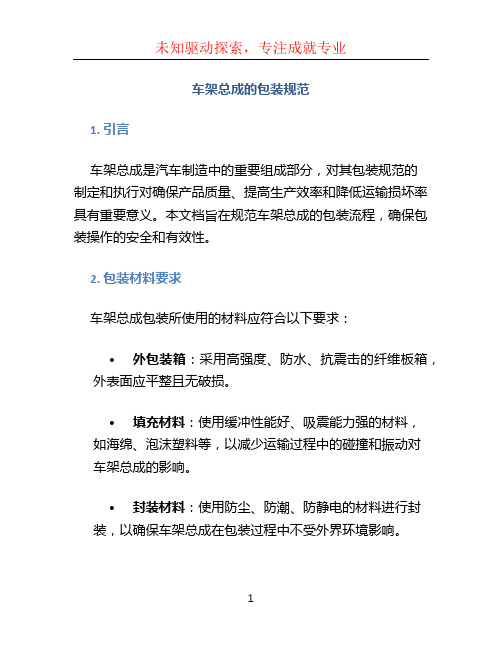
车架总成的包装规范1. 引言车架总成是汽车制造中的重要组成部分,对其包装规范的制定和执行对确保产品质量、提高生产效率和降低运输损坏率具有重要意义。
本文档旨在规范车架总成的包装流程,确保包装操作的安全和有效性。
2. 包装材料要求车架总成包装所使用的材料应符合以下要求:•外包装箱:采用高强度、防水、抗震击的纤维板箱,外表面应平整且无破损。
•填充材料:使用缓冲性能好、吸震能力强的材料,如海绵、泡沫塑料等,以减少运输过程中的碰撞和振动对车架总成的影响。
•封装材料:使用防尘、防潮、防静电的材料进行封装,以确保车架总成在包装过程中不受外界环境影响。
3. 包装操作流程3.1 准备工作在进行车架总成包装前,应进行以下准备工作:1.检查外包装箱的完整性和牢固性,确保其能够承受运输过程中的压力和震动。
2.准备填充材料和封装材料,确保其质量符合要求,并做好数量的统计。
3.检查包装设备的正常运行状态,如封箱机、缠绕机等。
3.2 包装流程车架总成的包装流程应按照以下步骤进行:1.将车架总成放置在外包装箱底部,注意放置位置的稳定性。
2.用填充材料将车架总成的周围空隙填满,确保车架总成不会在运输过程中发生移动或碰撞。
3.在填充材料上方放置一层封装材料,以防止尘土和湿气污染车架总成。
4.根据需要,重复上述步骤,增加外包装箱的高度,确保车架总成在箱内无法移动。
3.3 封装操作完成包装流程后,应进行封装操作,以确保车架总成在运输过程中不会受到外界环境的污染或损害。
1.用封装材料将外包装箱进行封闭,确保箱盖能够完全覆盖箱体并紧密封闭。
2.使用胶带、绳索或其他固定工具将箱盖牢固固定,防止在运输过程中意外打开。
3.在包装箱外部标注车架总成的型号、数量、重量等信息,以便于运输和仓库管理。
4. 包装质量检验为确保包装操作的质量和有效性,应进行包装质量检验,包括以下内容:1.外包装箱的完整性检查:检查箱体是否有破损、裂纹、折痕等。
2.填充材料的位置检查:检查填充材料是否均匀分布,车架总成是否能够牢固固定在箱内。
半挂车设计规范

半挂车架设计规范目录摘要 (3)关键词 (3)1 前言 (3)2 普通半挂车制动系统工作原理 (4)不带ABS防抱系统原理 (4)带ABS防抱系统原理 (4)3 ABS防抱系统的组成及工作原理 (5)ABS防抱系统的组成 (5)ABS防抱系统工作原理及性能特点 (6)4 ABS防抱系统的安装及故障检测 (9)ABS防抱系统的安装 (9)ABS防抱系统的测试 (10)5 ABS防抱系统常见故障的诊断 (12)6 结束语 (15)半挂车架设计规范摘要:本论文介绍了半挂车架在设计过程中应遵循的设计规范,分别从纵梁的选择、纵梁强度的计算、横梁的选择、纵梁和横梁的连接等几方面做了详细的阐述,对半挂车技术人员在设计半挂车时起很好的参考作用。
关键词:车架、纵梁、横梁、强度、规范。
1 前言:车架是车辆的骨架,是车辆的重要承载部件,连接着各个主要总成,承受着复杂空间力系的作用。
一般,车架应该具有足够的强度、合适的刚度,在保证刚度和强度的前提下重量最轻,以及结构应尽量简单等。
随着高速公路的发展,车速不断提高,因而要求车架要具有足够的抗弯曲变形和抗扭转变形的能力。
2 设计车架注意事项:车架的各个构件几乎都是冲压件,因此,各构件的形状要尽量符合冲压工艺的要求,拉伸量不能太大,余料也不能过多,以节省材料;由于在每个截面上的扭转应力总是在上、下翼面的翼缘处最大,因此在车架上、下翼面上应尽可能不要钻孔、开口或有其他工艺缺陷。
在前后轴之间车架纵梁的下翼面、后悬架部分纵梁的上翼面等都禁止钻孔。
在车架纵梁的腹板及横梁上钻孔时,孔间距和孔大小都应符合规定。
在车架上焊接零件时,应该采用与车架材料焊接性能相同的材料进行焊接,不能随意地在车架上进行焊接。
对于承受扭转应力的构件,应尽量采用抗扭刚度高的箱形和圆管等闭口截面来制造。
为了避免材料折弯时产生破裂,内圆角半径应比板材的厚度大一些,对于T700钢的材料,一般内圆角的半径应等于板材厚度的2-3倍。
车架总成(半承载)设计规范

Q/WCYG车架总成(全承载)设计规范扬州亚星客车股份有限公司发布前言本标准是根据国家有关客车方面的法规、标准等要求,结合我公司产品开发流程,并参考高等院校汽车专业教材相关章节制定而成,作为扬州亚星客车股份有限公司车架总成(半承载)设计的主要依据。
本标准由扬州亚星客车股份有限公司提出并归口。
本标准由扬州亚星客车股份有限公司汽车研究院起草。
本标准主要起草人:本标准由扬州亚星客车股份有限公司汽车研究院负责解释。
前言的内容可包括:(宋体,五号,段落1.5倍行距)a)任务来源;b)制定过程及征求意见情况;c)指明该标准采用国际标准、国外先进标准的程度;d)该标准导致废止或代替其他标准文件的全部或一部分的说明;e)实施该标准过渡期的要求;f)哪些附录是标准的附录,哪些附录是提示的附录的说明;g)附加说明:——本标准由汽车研究院提出。
——本标准由汽车研究院归口。
——本标准起草部门。
——本标准主要起草人。
——本标准首次发布、历次修改和复审确认年、月车架(半承载)总成设计规范1 范围本标准规定了半承载式车架总成的术语和定义、设计规范、车架的制造工艺及材料、车架防腐蚀要求、车辆VIN码和产品标牌在车架上的固定(位置)、车架总成的变动、设计评审要求、设计输出图样和文件的明细等基本设计准则。
本标准适用于半承载车架总成设计过程控制,外购底盘车架改制可参照执行。
本标准不适用于全承载车架总成设计过程控制。
2 规范性引用文件下列文件对于本文件的应用是必不可少的。
凡是注日期的引用文件,仅所注日期的版本适用于本文件。
凡是不注日期的引用文件,其最新版本(包括所有的修改单)适用于本文件。
GB 7258-2012 机动车运行安全技术条件GB1184-80 形状和位置公差GB3323-87 钢熔化焊对接接头射线照相焊缝质量分级Q/WCYG ZT C QY G 25-2012《外购零部件防腐蚀要求》3 术语和定义下列术语和定义适用本文件。
中重型载货汽车总布置设计规范
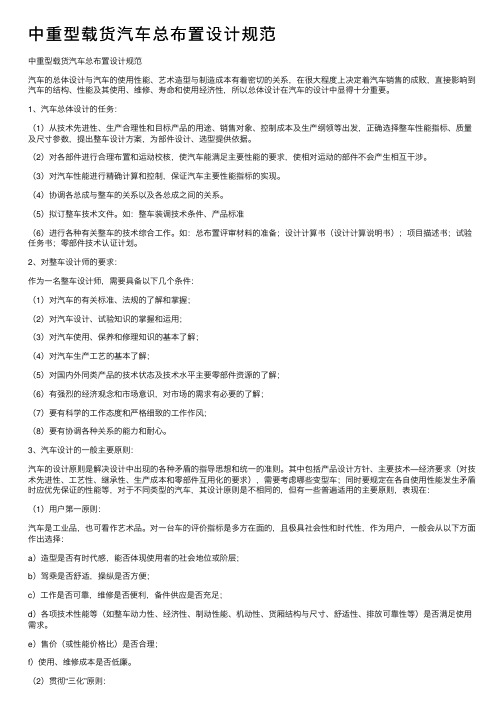
中重型载货汽车总布置设计规范中重型载货汽车总布置设计规范汽车的总体设计与汽车的使⽤性能、艺术造型与制造成本有着密切的关系,在很⼤程度上决定着汽车销售的成败,直接影响到汽车的结构、性能及其使⽤、维修、寿命和使⽤经济性,所以总体设计在汽车的设计中显得⼗分重要。
1、汽车总体设计的任务:(1)从技术先进性、⽣产合理性和⽬标产品的⽤途、销售对象、控制成本及⽣产纲领等出发,正确选择整车性能指标、质量及尺⼨参数,提出整车设计⽅案,为部件设计、选型提供依据。
(2)对各部件进⾏合理布置和运动校核,使汽车能满⾜主要性能的要求,使相对运动的部件不会产⽣相互⼲涉。
(3)对汽车性能进⾏精确计算和控制,保证汽车主要性能指标的实现。
(4)协调各总成与整车的关系以及各总成之间的关系。
(5)拟订整车技术⽂件。
如:整车装调技术条件、产品标准(6)进⾏各种有关整车的技术综合⼯作。
如:总布置评审材料的准备;设计计算书(设计计算说明书);项⽬描述书;试验任务书;零部件技术认证计划。
2、对整车设计师的要求:作为⼀名整车设计师,需要具备以下⼏个条件:(1)对汽车的有关标准、法规的了解和掌握;(2)对汽车设计、试验知识的掌握和运⽤;(3)对汽车使⽤、保养和修理知识的基本了解;(4)对汽车⽣产⼯艺的基本了解;(5)对国内外同类产品的技术状态及技术⽔平主要零部件资源的了解;(6)有强烈的经济观念和市场意识,对市场的需求有必要的了解;(7)要有科学的⼯作态度和严格细致的⼯作作风;(8)要有协调各种关系的能⼒和耐⼼。
3、汽车设计的⼀般主要原则:汽车的设计原则是解决设计中出现的各种⽭盾的指导思想和统⼀的准则。
其中包括产品设计⽅针、主要技术—经济要求(对技术先进性、⼯艺性、继承性、⽣产成本和零部件互⽤化的要求),需要考虑哪些变型车;同时要规定在各⾃使⽤性能发⽣⽭盾时应优先保证的性能等,对于不同类型的汽车,其设计原则是不相同的,但有⼀些普遍适⽤的主要原则,表现在:(1)⽤户第⼀原则:汽车是⼯业品,也可看作艺术品。
大客车-车架-结构
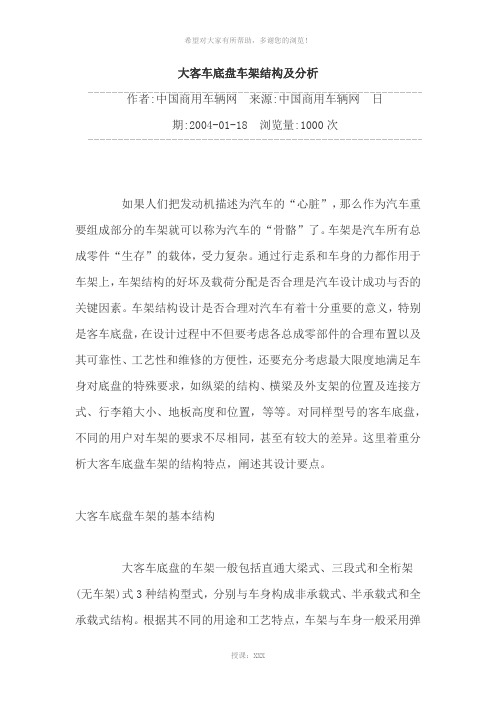
大客车底盘车架结构及分析作者:中国商用车辆网来源:中国商用车辆网日期:2004-01-18 浏览量:1000次如果人们把发动机描述为汽车的“心脏”,那么作为汽车重要组成部分的车架就可以称为汽车的“骨骼”了。
车架是汽车所有总成零件“生存”的载体,受力复杂。
通过行走系和车身的力都作用于车架上,车架结构的好坏及载荷分配是否合理是汽车设计成功与否的关键因素。
车架结构设计是否合理对汽车有着十分重要的意义,特别是客车底盘,在设计过程中不但要考虑各总成零部件的合理布置以及其可靠性、工艺性和维修的方便性,还要充分考虑最大限度地满足车身对底盘的特殊要求,如纵梁的结构、横梁及外支架的位置及连接方式、行李箱大小、地板高度和位置,等等。
对同样型号的客车底盘,不同的用户对车架的要求不尽相同,甚至有较大的差异。
这里着重分析大客车底盘车架的结构特点,阐述其设计要点。
大客车底盘车架的基本结构大客车底盘的车架一般包括直通大梁式、三段式和全桁架(无车架)式3种结构型式,分别与车身构成非承载式、半承载式和全承载式结构。
根据其不同的用途和工艺特点,车架与车身一般采用弹性或刚性连接。
现国内外大都采用刚性连接,以使车架与车身共同承载,受力趋于合理化,从而提高车辆的可靠性和安全性。
1.直通大梁式该结构是传统的结构型式,采用槽形或矩型截面纵梁,有些车型还有加强副纵梁。
根据不同的要求,纵梁设计可前后贯通,也可前、中和后搭接成不同高度或不同宽度的结构,有些车型受后桥和地板高度要求的限制而在该处设计成结构复杂的“Ω”型。
横梁结构一般采用“I型或双槽背对形成的“I”型,有时也采用“○”型横梁。
根据布置和总成的安装要求,同一车架可同时采用多种型式的组合和不同的横梁翼面,车架总成可设计成前后等宽或不等宽结构。
直通大梁式车架结构简单、工艺性好,但存在本身质量大、总成布置困难、受力不均匀和损坏后难以修复等缺点,主要用于城市公交和普通短途客运车辆。
2.三段式该结构前、后段为槽形大梁,中段为桁架结构(行李舱区)。
整车总布置设计规范

整车总布置设计规范一、 定义汽车总布置是指在汽车的总体方案确定后,要对总成和部件进行空间布置, 并校核初步选定的各个部件的结构尺寸与安装位置能否满足整车空间尺寸的 要求,使其在安全性、拆装便利性以及与人体的关系合理性等多个方面协调 可靠,达到最优结果。
二、整车布置基准线 工作步骤如下图I■■ ■■初步参数确定绘制总布置草图校核总布置方案整车布置基准线注:1.均应在汽车营群雄窸下进行之母图时应将汽耳前融荏左侧■1车库上平面线纵粱上翼面较长的一段平面或承载式车身中部地板或边粱的上缘面在侧(前) 视图上的投影线称为车架上平面,它作为垂直方自尺寸的基准线(面), z 坐标线,向上为“ +”、向下为“-”。
有些客车的车架上平面在满载静止位 置时,通常与地面倾斜 0.5 °〜1.5 ° ,使车架呈前低后高状,这样在汽车加 速时,客厢可接近水平。
为了画图方便,可将车架上平面线画成水平的,将 地面画成斜的。
| 22、前轮中心线通过左右前轮中心,并垂直于车架平面线的平面,在侧视图和俯视图上的投影线称为前轮中心线,它作为纵向方自尺寸的基准线(面),即 z 坐标线, 向前为“-”,向后为“ +”。
33、汽车中心线汽车纵向垂直对称平面在俯视图和前视图上曲投影线称为汽车中心线,用它 作为横自尺寸的基准线(面)。
即 y 坐标线,向左为“ +”、自右为“-”, 4 4、地面线地平面在侧视图和前视图上的投影线称为地面线,此线是标注汽车高度、接 近角、离去角、离地间隙和踏板高度等尺寸的基准线。
55、前轮垂直线通过左、右前轮中心,并垂直于地面的平面,在侧视图和俯视图上的投影线 称为前轮垂直线。
此线用来作为标注汽车轴距和前悬的基准线。
当车架与地 面平行时,前轮垂直线与前轮中心线重合(如轿车)。
形式发动机昼矍驱动形式载客量装或量基准线/面确定同图的零线确定整车方式方和标注 酬定正负要求和琴数的 整车工况 是再合 结构尺寸三、各部件的布置各部件的布置主要包括传动、转向、悬挂、制动等,下面来一一看看:11、传动系的布置由于电动机、无极变速器装成一体,所以在电动机位置确定后,包括电动机、无极变速器在内的动力总成位置也随之而定。
大中型客车车架总成设计规范
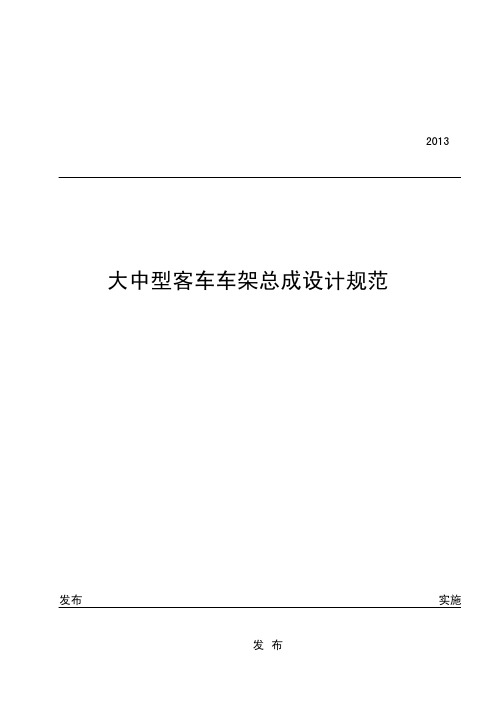
a) 纵向弯曲
b) 侧向弯曲
c) 纵向受力
d) 整体扭转
e) 纵向受力
图2 车架的受力和变形
由于车架所承受的动负荷无规律且不断变化,因此车架变形形式和状况是随机的。车架实际上是一 个承受空间力系的平面框架,而且车架纵梁与横梁的截面形状和连接接头又是各式各样的,更导致问题
3
的复杂化。车架的损坏主要是疲劳破坏,其主要形式是断裂,而疲劳裂纹则位于纵梁或横梁的边缘或应 力集中处。通过有限元计算法的应用,使车架的强度及结构设计更趋于合理。
a) 提高弯曲强度: 1) 选定较大的断面尺寸和合理的断面形状(槽形梁断面高宽比一般为 3:1); 2) 将上、下翼缘加厚或在其上贴加强板; 3) 将受拉力翼缘适当加宽。
b) 提高局部扭转强度: 1) 注意偏心载荷的布置,使相近的几个偏心载荷尽量接近纵梁断面的弯曲中心,并使合成量 较小; 2) 在偏心载荷较大处设置横梁,并根据载荷大小及分散情况确定连接强度和宽度; 3) 将悬置点布置在横梁的弯曲中心上; 4) 当偏心载荷较大且偏离横梁较远时,可采用 K 形梁,或将该段纵梁形成封闭断面; 5) 当偏心载荷较大且分散时,应采用封闭断面梁,横梁间距也应缩小; 6) 选用较大的断面; 7) 限制制造扭曲度,减小装配应力。
5
为了解决以上两个方案的不足,可以在槽形横梁的上下方各采用一个连接板,或仅在其下方采用一 个连接板。 6.4.2.2 鳄鱼式横梁
鳄鱼式横梁通常由帽形截面在其两端加接头构成,如图4所示:
a) 翼板连接
b)腹板连接
图4 鳄鱼式横梁
鳄鱼式横梁优点如下: a) 有较大的连接宽度,使主、副簧支架都可得到支撑; b) 截面高度较低,可以让开下部空间,使某些汽车的传动轴自由穿过; c) 可用矩形胚料直接压制; 鳄鱼式横梁的不足之处是:其弯曲刚度不如槽形横梁大,车架扭转时纵梁的应力偏大。因此,可将 将翼缘连接改为腹板连接。 鳄鱼式横梁也可由两个帽形截面组成封闭的箱形截面,其扭转刚度较大,弯曲刚度比其它两种大。
车架设计手册
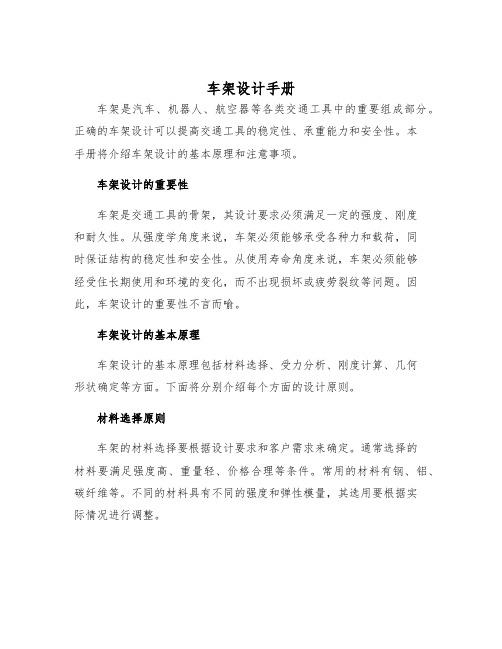
车架设计手册车架是汽车、机器人、航空器等各类交通工具中的重要组成部分。
正确的车架设计可以提高交通工具的稳定性、承重能力和安全性。
本手册将介绍车架设计的基本原理和注意事项。
车架设计的重要性车架是交通工具的骨架,其设计要求必须满足一定的强度、刚度和耐久性。
从强度学角度来说,车架必须能够承受各种力和载荷,同时保证结构的稳定性和安全性。
从使用寿命角度来说,车架必须能够经受住长期使用和环境的变化,而不出现损坏或疲劳裂纹等问题。
因此,车架设计的重要性不言而喻。
车架设计的基本原理车架设计的基本原理包括材料选择、受力分析、刚度计算、几何形状确定等方面。
下面将分别介绍每个方面的设计原则。
材料选择原则车架的材料选择要根据设计要求和客户需求来确定。
通常选择的材料要满足强度高、重量轻、价格合理等条件。
常用的材料有钢、铝、碳纤维等。
不同的材料具有不同的强度和弹性模量,其选用要根据实际情况进行调整。
受力分析原则车架需要承受各种载荷和力,因此设计时需要进行受力分析。
理论上,车架的受力分析应该采用有限元分析等数学模型进行计算。
但在实际设计中,可以采用近似方法,也可以通过经验公式等方法进行计算。
受力分析的结果应该用于判断车架的强度和刚度情况,以便对设计进行调整。
刚度计算原则车架的刚度是其稳定性的关键指标。
刚度的计算要根据车架的整体结构、材料、截面尺寸和安装方式等多个因素进行考虑。
通常情况下,车架的刚度可以通过直接拟合或计算得出。
同时,刚度的计算还要考虑其对车辆操控性和行驶舒适度的影响。
几何形状确定原则车架的几何形状对其强度、刚度和外观等方面的影响非常大。
常见的车架形状有方管式、圆管式、H型钢式等。
不同的形状具有不同的刚度和强度特点。
因此,在进行车架设计时,几何形状的选择要综合考虑材料的特性、受力分析结果和使用要求等因素,以确保车架的性能和稳定性。
车架设计的注意事项在进行车架设计时,还需注意以下事项:安全性车架的安全性是设计的首要考虑因素。
车架设计手册

重控制悬架系统引起的局部扭转。提高纵梁强度
常用的措施如下:
一、提高弯曲强度
1,选定较大的断面尺寸和合理的断面形
状(槽形梁断面高宽比一般为3:1);
2,将上、下翼缘加厚或在其上贴加强板;
3, 将受拉力翼缘适当加宽;
二、提高局部扭转强度
1,注意偏心载荷的布置,使相近的几个偏心载荷尽量接近纵梁断面的弯曲中心,并使合成量较小;
3) 由前、后悬架总成布置确定前、后悬钢板支架位置、减震器、缓冲块安装位置或空气弹簧支架安装位置、推力杆支架安装位置、稳定杆支架安装位置等;
4) 由转向系总成布置确定方向机安装位置、 中间垂臂支架安装位置或角转向器支架安装位置;
5) 由车身总布置确定车架各牛腿安装位置;
如上述几条中安装位置有干涉,则和相关设计人员勾通并协商统一解决。至此,车架基本框架就已完成,接下来就是车架各部分总成的细节设计2。
5,必要时可采用铰孔或冲压边缘修磨,以提高某些薄弱部位的疲劳强度;
五、减小失稳
1,在受压翼缘和厚度的比值不宜过大(常在12左右);
2,在容易失稳处加焊撑板;
3,在容易出现波纹处限制其平整度;
六、局部强度加强
1,采用较大的板厚;
2,在集中力较大处将纵、横梁局部贴加强板,必要时再将加强板压成肋或翻边;
3,加大支架紧固面尺寸,增多紧固件数量,并尽量使力作用点接近腹板的上、下侧。
GB1958-80 形状和位置公差检测规定
GB1184-80 形状和位置公差
GB3323-87 钢熔化焊对接接头射线照相焊缝质量分级
3 符号、代号、术语及其定义
车架:汽车承载的基体,支撑着发动机、离合器、变速器、转向器、非承载式(或半承载式)车身等所有簧上质量的有关机件,承受着传给它的各种力和力矩。
半挂车设计规范标准

车架的纵梁结构是根据货台形式要求,相应的有平板式、阶梯式、凹梁式三种,如
图 3.9 所示。 纵梁截面有工字形和槽形, 为防止上
平板式
下翼缘受拉伸和压缩作用而破裂,
阶梯式
按薄板理论进行校核,其弯曲应 力不应超过临界弯曲应力。翼缘
凹梁式
最大宽度一般不超过 16t(t 为钢
图 3.9 车架纵梁的形式
板的厚度),对于大吨位半挂车多采用工字形截面梁。
2.6 纵梁若要有加强板,由于纵梁在加强板处的扭转应力下降,但在离开加强板处的 扭转应力反而又增大,故应使加强板的形状向两端逐渐减小,从而得到缓和、过度的扭 转应力。
2.7 纵梁的扭转应力是按不同位置的横梁分段的,每段与横梁连接处扭转应力或为最 大或为最小,如果在两根横梁之间加装一根横梁,则车架的扭转应力提高、加装横梁处 的扭转应力增加,而纵梁在与原来两根横梁连接处的扭转应力反而下降,布置横梁时应 注意这个问题。
.
半挂车架 设计规
.页脚.
.
目录
摘要...............................................................3 关键词.............................................................3 1 前言.............................................................3 2 普通半挂车制动系统工作原理...................................4
纵梁截面高度根据吨位不同有较大的差异。可参考以下尺寸:
载质量 15t,主截面高 300mm 左右;载质量 20~30t,主截面高 350~450mm;载质量 40~50t,主截面高 450~550mm。
承载式车身与非承载式车身的区分

全承载式车身与半承载式车身的区分----- OOOO自从2005年底00客车已着手研发和全面推动全承载客车产品,目前00和0000全承载城市客车产品已经批量投放市场,OOOOo产品已经过几轮试制形成小批量订单,OO(X)O系列(8〜9米)全承载客车产品正在试制阶段。
但是全承载客车与目前公司批量生产的半承载客车在结构方面主要有哪些方面的区分?都有什么优缺点?许多员工还不是很清晰,下面简洁的给大家做个介绍:半承载式车身的汽车有一刚性底盘大梁车架。
在半承载式车身中发动机、传动系统的一部分、车身等总成部件都是用悬架装置固定在车架上,车架通过前后悬架装置与车轮联接。
半承载式车身比较笨重,质量大,高度高。
半承载式车身就是悬挂不是直接联在车身上,而是联在车架上,车架上面再扣上一个车身。
它的优点就是有独立的大梁,底盘强度较高,抗颠簸性能好,此外四个车轮受力再不匀称,也是由车架担当,而不会传递到车身上去。
缺点就是车身和车架是刚性联接的,在大路上行驶的时候,不是很平稳,会产生震惊。
此外遇到危急(如翻车)的时候,厚重的底盘,也会对相对薄弱的车身产生致命威逼。
全承载式车身的汽车没有刚性车架,发动机、前后悬架、传动系统的一部分等总成部件装配在车身上设计要求的位置,车身负载通过悬架装置传给车轮。
全承载式车身除了其固有的乘载功能外,还要直接承受各种负荷力的作用。
全承载式车身不论在平安性还是在稳定性方面都有很大的提高,它具有质量小、高度低、装配简洁等优点。
说白了,全承载式车身就是整个车身为一体悬挂直接联在车身上。
这样的车身优势是:大路行驶特别平稳,整个车身为一体, 固有频率震惊低,噪音小,整体式车身比较平安。
缺点就是底盘强度远不如大梁结构的车身,当四个车轮受力不匀称时,车身会发生变形此外,此外制造成本偏高。
综上所述,从使用的角度看,半承载式除了底盘牢固外,其他几乎全是缺点;而全承载式除了底盘不够牢固外,其他几乎全是优点,从创造以来汽车全部都是半承载式的。
汽车设计-车身前副车架安装点设计规范模板
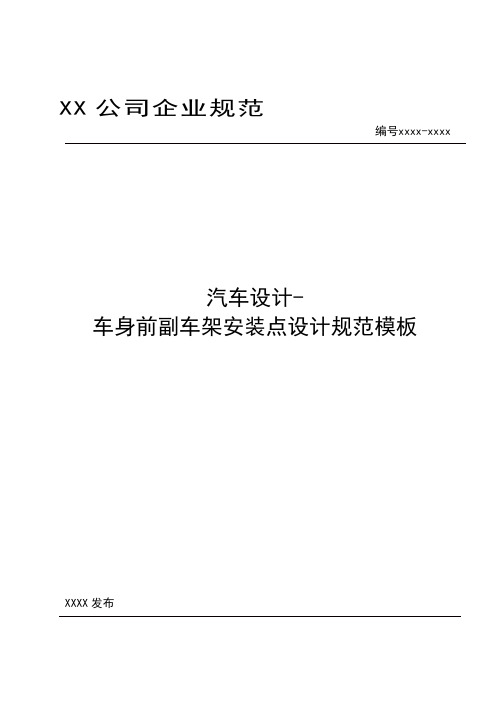
汽车设计-车身前副车架安装点设计规范模板XXXX发布1 范围本规范规定了车身前副车架安装点设计要点及其判断标准等。
本规范适用于新开发的M1类和N1类汽车车身前副车架安装点设计。
2 规范性引用文件下列文件对于本文件的应用是必不可少的,凡是注日期的引用文件,仅注日期的版本适用于本文件。
凡是不注日期的引用文件,其最新版本(包括所有的修改单)适用于本文件。
《GB 11566-2009 乘用车外部凸出物》《GB/T19234-2003 乘用车尺寸代码》《GB/T 709-2006 热轧钢板和钢带的尺寸、外形、重量及允许偏差》《GB/T 710-2008 优质碳素结构钢热轧薄钢板和钢带》《GB/T4780-2000 汽车车身术语》《整车车身设计公差与装配尺寸链分析》《螺栓连接的装配质量控制》3 术语和定义3.1 车身结构3.1.1车身结构是各个零件的安装载体。
3.2 副车架3.2.1副车架最早的应用原因是可以降低发动机舱传递到驾驶室的振动和噪音。
副车架与车身的连接点就如同发动机悬置一样。
通常一个副车架总成需要由四个悬置点与车身连接,这样既能保证其连接刚度,又能有很好的震动隔绝效果。
副车架能分5级减小震动的传入,对副车架来说,在性能上主要目的是减小路面震动的传入,以及提高悬挂系统的连接刚度,因此装有副车架的车驾驶起来会感觉底盘非常扎实,非常紧凑。
而副车架悬置软硬度的设定也面临着像悬挂调校一样的一个不可规避的矛盾。
所以工程师们在设计和匹配副车架时通常会针对车型的定位和用途选择合适刚度的橡胶衬垫。
由于来自发动机和悬挂的一部分震动会先到达副车架然后再传到车身,经过副车架的衰减后振动噪声会有明显改善。
副车架发展到今天,可以简化多车型的研发步骤。
这是因为悬挂、稳定杆、转向机等底盘零件都可以预先安装在一起,形成一个所谓的超级模块,然后再一起安装到车身上。
3.3前副车架安装点3.3.1前副车架安装点指安装在车身的安装孔中心线与安装面下平面交点的位置(XYZ 坐标)及装配孔公称尺寸。
半挂车设计规范

半挂车架设计规范目录摘要 (3)关键词 (3)1 前言 (3)2 普通半挂车制动系统工作原理 (4)2.1 不带ABS防抱系统原理 (4)2.2 带ABS防抱系统原理 (4)3 ABS防抱系统的组成及工作原理 (5)3.1 ABS防抱系统的组成 (5)3.2 ABS防抱系统工作原理及性能特点 (6)4 ABS防抱系统的安装及故障检测 (9)4.1 ABS防抱系统的安装 (9)4.2 ABS防抱系统的测试 (10)5 ABS防抱系统常见故障的诊断 (12)6 结束语 (15)半挂车架设计规范摘要:本论文介绍了半挂车架在设计过程中应遵循的设计规范,分别从纵梁的选择、纵梁强度的计算、横梁的选择、纵梁和横梁的连接等几方面做了详细的阐述,对半挂车技术人员在设计半挂车时起很好的参考作用。
关键词:车架、纵梁、横梁、强度、规范。
1 前言:车架是车辆的骨架,是车辆的重要承载部件,连接着各个主要总成,承受着复杂空间力系的作用。
一般,车架应该具有足够的强度、合适的刚度,在保证刚度和强度的前提下重量最轻,以及结构应尽量简单等。
随着高速公路的发展,车速不断提高,因而要求车架要具有足够的抗弯曲变形和抗扭转变形的能力。
2 设计车架注意事项:2.1车架的各个构件几乎都是冲压件,因此,各构件的形状要尽量符合冲压工艺的要求,拉伸量不能太大,余料也不能过多,以节省材料;2.2由于在每个截面上的扭转应力总是在上、下翼面的翼缘处最大,因此在车架上、下翼面上应尽可能不要钻孔、开口或有其他工艺缺陷。
在前后轴之间车架纵梁的下翼面、后悬架部分纵梁的上翼面等都禁止钻孔。
在车架纵梁的腹板及横梁上钻孔时,孔间距和孔大小都应符合规定。
2.3在车架上焊接零件时,应该采用与车架材料焊接性能相同的材料进行焊接,不能随意地在车架上进行焊接。
2.4对于承受扭转应力的构件,应尽量采用抗扭刚度高的箱形和圆管等闭口截面来制造。
2.5为了避免材料折弯时产生破裂,内圆角半径应比板材的厚度大一些,对于T700钢的材料,一般内圆角的半径应等于板材厚度的2-3倍。
中华人民共和国国家标准汽车车架修理技术条件
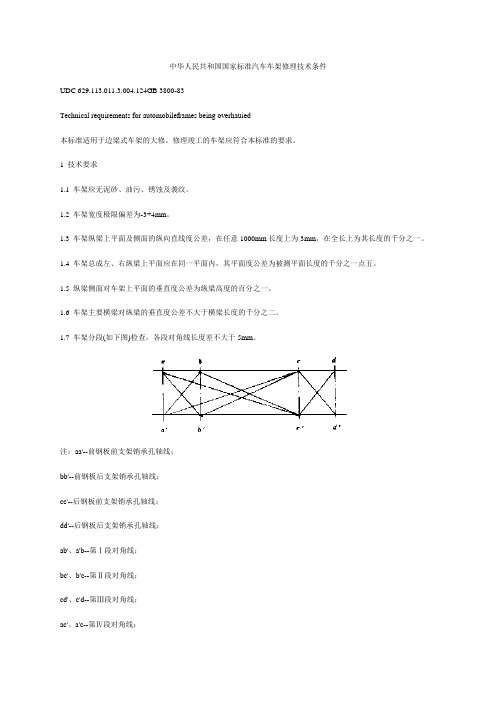
中华人民共和国国家标准汽车车架修理技术条件UDC 629.113.011.3.004.124GB 3800-83Technical requirements for automobileframes being overhauied本标准适用于边梁式车架的大修。
修理竣工的车架应符合本标准的要求。
1 技术要求1.1 车架应无泥砂、油污、锈蚀及袭纹。
1.2 车架宽度极限偏差为-3+4mm。
1.3 车架纵梁上平面及侧面的纵向直线度公差,在任意1000mm长度上为3mm,在全长上为其长度的千分之一。
1.4 车架总成左、右纵梁上平面应在同一平面内,其平面度公差为被测平面长度的千分之一点五。
1.5 纵梁侧面对车架上平面的垂直度公差为纵梁高度的百分之一。
1.6 车架主要横梁对纵梁的垂直度公差不大于横梁长度的千分之二。
1.7 车架分段(如下图)检查,各段对角线长度差不大于5mm。
注:aa'--前钢板前支架销承孔轴线;bb'--前钢板后支架销承孔轴线;cc'--后钢板前支架销承孔轴线;dd'--后钢板后支架销承孔轴线;ab'、a'b--第Ⅰ段对角线;bc'、b'c--第Ⅱ段对角线;cd'、c'd--第Ⅲ段对角线;ac'、a'c--第Ⅳ段对角线;1.8 左右钢板弹簧固定支架销孔应同轴,其同轴度公差为φ2.0mm(按GB 1958-80《形状和位置公差检测规定》检测方法5-1进行检测)。
前后固定支架销孔轴线间的距离左、右相差:轴距在4000mm及其以下的应不大于2mm,轴距在4000mm以上的应不大于3mm。
1.9 车架的焊接应符合焊接规范。
焊缝应平整、光滑、无焊瘤、弧坑,咬边深度不大于0.5mm,咬边长度不大于焊缝长度的百分之十五,并不得有气孔、夹渣等缺陷。
1.10 车架挖补或截修的焊缝方向,除特殊车架外,不允许与棱线垂直、重叠;焊缝及其周围基体金属上,不应有裂纹。
半承载车身结构设计
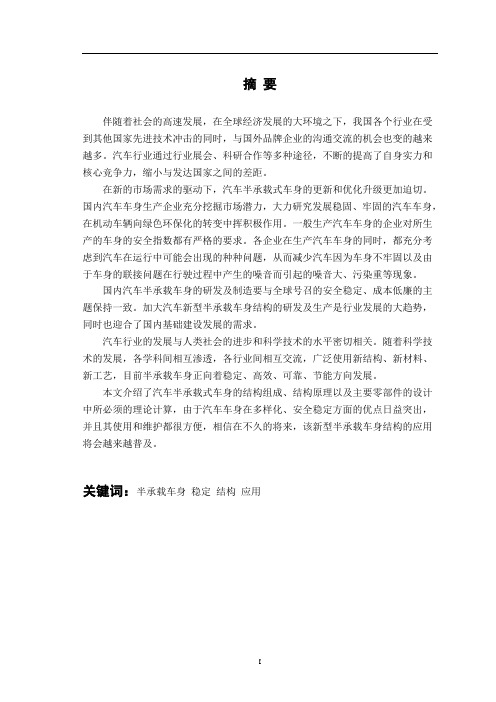
摘要伴随着社会的高速发展,在全球经济发展的大环境之下,我国各个行业在受到其他国家先进技术冲击的同时,与国外品牌企业的沟通交流的机会也变的越来越多。
汽车行业通过行业展会、科研合作等多种途径,不断的提高了自身实力和核心竞争力,缩小与发达国家之间的差距。
在新的市场需求的驱动下,汽车半承载式车身的更新和优化升级更加迫切。
国内汽车车身生产企业充分挖掘市场潜力,大力研究发展稳固、牢固的汽车车身,在机动车辆向绿色环保化的转变中挥积极作用。
一般生产汽车车身的企业对所生产的车身的安全指数都有严格的要求。
各企业在生产汽车车身的同时,都充分考虑到汽车在运行中可能会出现的种种问题,从而减少汽车因为车身不牢固以及由于车身的联接问题在行驶过程中产生的噪音而引起的噪音大、污染重等现象。
国内汽车半承载车身的研发及制造要与全球号召的安全稳定、成本低廉的主题保持一致。
加大汽车新型半承载车身结构的研发及生产是行业发展的大趋势,同时也迎合了国内基础建设发展的需求。
汽车行业的发展与人类社会的进步和科学技术的水平密切相关。
随着科学技术的发展,各学科间相互渗透,各行业间相互交流,广泛使用新结构、新材料、新工艺,目前半承载车身正向着稳定、高效、可靠、节能方向发展。
本文介绍了汽车半承载式车身的结构组成、结构原理以及主要零部件的设计中所必须的理论计算,由于汽车车身在多样化、安全稳定方面的优点日益突出,并且其使用和维护都很方便,相信在不久的将来,该新型半承载车身结构的应用将会越来越普及。
关键词:半承载车身稳定结构应用AbstractAlong with the rapid development of society, under the environment of global economic development. China's various industries in by the other countries the impact of advanced technology at the same time, opportunity to communicate with foreign brand enterprises has become more and more. Automobile industry through industry exhibitions, research cooperation and other ways, and constantly improve their own strength and core competitiveness, narrowing the gap between the developed countries.Driven by the new market demand, the automobile semi - load vehicle body is updated and optimized. Domestic automobile body production enterprises to fully tap the market potential, and vigorously research and development of a solid, strong car body, in a motor vehicle to the green environmental protection change in a positive role. General production of auto body enterprises on the production of the body's safety index has strict requirements. The enterprise in the production of car body, at the same time, give full consideration to the car may arise in the operation of all sorts of questions, so as to reduce the vehicle because the body is not strong and the body connection problem in running the noise generated in the process caused by noise, heavyThe development and manufacture of the domestic automobile semi bearing body should be consistent with the global call for security and stability, low cost and low cost. The development and production of the new type half bearing body structure is the major trend of the development of the industry, but also to meet the needs of the development of domestic infrastructure.The development of automobile industry is closely related to the progress of human society and the level of science and technology. With the development of science and technology, interdisciplinary mutual infiltration, mutual exchanges between the industry, widely used new structure, new materials, new technology, at present carrying body towards a stable, efficient, reliable, energy-saving direction.This paper introduces the semi auto bearing type body structure composition, structure principle and main parts design must have the theoretical calculation, because of the increasingly prominent advantages of car body in diverse, safe and stable, and the operation and maintenance are very convenient, I believe in not long future, the new semi bearing body structure will be applied more and more popular.Key words: semi bearing body stability structure application目录1 绪论 (1)1.1课题的来源与研究的目的和意义 (1)1.2课题的内容 (2)1.3车身结构 (4)1.4客车车身的分类 (6)2 车身总布置设计 (7)2.1发动机与车门的布置 (9)2.2外廊尺寸和有关总布置尺寸 (10)2.3车箱布置及横截面尺寸 (11)2.4座椅尺寸及操纵机构的布置 (13)2.5备胎、油箱和蓄电池的布置 (15)3 车架及车身骨架设计 (17)3.1车架设计 (19)3.2车身骨架设计 (20)4 半承载车身主要零部件的有限元分析 (21)4.1大梁的有限元强度分析 (22)结论 (23)参考文献 (24)致谢 (25)1 绪论1.1 课题的来源与研究的目的和意义目前,我国生产的半承载式车身结构简陋,稳定性始终不高,虽然经过几十年的发展,近期产品的质量较早期有所提高。
浅析客车六大总成骨架合装工艺
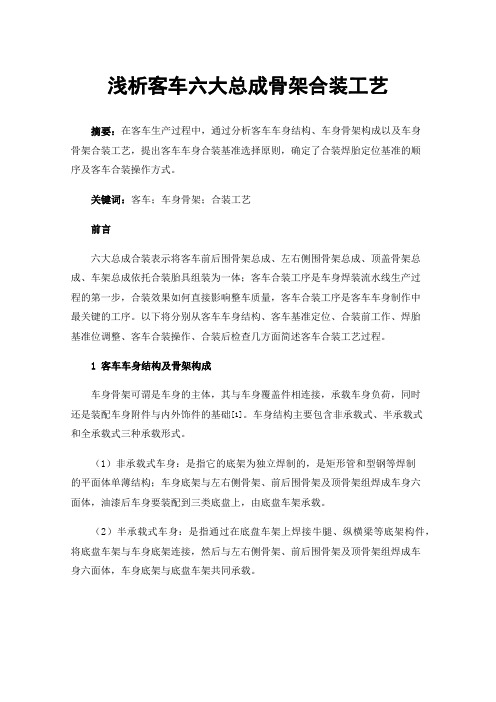
浅析客车六大总成骨架合装工艺摘要:在客车生产过程中,通过分析客车车身结构、车身骨架构成以及车身骨架合装工艺,提出客车车身合装基准选择原则,确定了合装焊胎定位基准的顺序及客车合装操作方式。
关键词:客车;车身骨架;合装工艺前言六大总成合装表示将客车前后围骨架总成、左右侧围骨架总成、顶盖骨架总成、车架总成依托合装胎具组装为一体;客车合装工序是车身焊装流水线生产过程的第一步,合装效果如何直接影响整车质量,客车合装工序是客车车身制作中最关键的工序。
以下将分别从客车车身结构、客车基准定位、合装前工作、焊胎基准位调整、客车合装操作、合装后检查几方面简述客车合装工艺过程。
1客车车身结构及骨架构成车身骨架可谓是车身的主体,其与车身覆盖件相连接,承载车身负荷,同时还是装配车身附件与内外饰件的基础[1]。
车身结构主要包含非承载式、半承载式和全承载式三种承载形式。
(1)非承载式车身:是指它的底架为独立焊制的,是矩形管和型钢等焊制的平面体单薄结构;车身底架与左右侧骨架、前后围骨架及顶骨架组焊成车身六面体,油漆后车身要装配到三类底盘上,由底盘车架承载。
(2)半承载式车身:是指通过在底盘车架上焊接牛腿、纵横梁等底架构件,将底盘车架与车身底架连接,然后与左右侧骨架、前后围骨架及顶骨架组焊成车身六面体,车身底架与底盘车架共同承载。
(3)全承载式车身:是由矩形管和型钢焊制桁架结构而成,底架与左右侧围骨架、前后围骨架及顶骨架共同组焊成车身六面体。
在车架上装配发动机、前后桥、传动系等底盘部件,车身车架全部承载。
(4)通过以上三种车身承受载荷不同的车身结构[2],我们了解到车身骨架与底盘车架间连接的方式并关系到客车合拢工艺中合装焊胎上车架总成定位的方式。
2客车车身骨架合装工艺客车车身合装就是依托合装设备,通过对客车车架、前后围骨架、左右侧围骨架及顶围骨架等总成的定位组焊成型,符合设计要求车身六面体结构[2]。
2.1合装设备合装设备属于大型专用工艺设备,主要负责组合车身六大总成成为车身六面体。
汽车各大总成的设计规范

汽车是一个多学科、社会化的产品,汽车的发展水平与社会的发展是同步的,只有好的社会背景作为载体。
汽车行业才能得到正常有序的发展。
因而国家已出台了包括汽车政策与产品发展重点、产品认证、产业组织政策、产品技术政策、投资金融政策、外资政策、进出口管理政策、国产化及相关工业和社会保障政策等。
从汽车设计本身而言,汽车是一个集机电、人机工程、美学、制造工艺为一体的多学科的产品。
同时汽车本身又因地域、功能的不同而多样化。
因而汽车技术是一个“丰富多彩”的技术。
1、整车方案设计整车的方案设计直接影响到整个项目的成败,因而作为整车方案设计的前期准备工作是非常重要的。
作为整车方案,首先必须了解所开发的车型是一个什么用途的车型。
该类车型的技术要求及规模成本。
不同用途的车辆的技术要求及规模大小直接影响到产品的设计思想。
整车方案设计主要从汽车的动力性、经济性、制动性、操纵稳定性、通过性、舒适性、维修成本及方便性来考虑。
当然。
汽车的各项性能是不能同时满足的,不同车辆追求的性能不同。
经济型轿车追求的是成本价格及使用费用。
其更多地追求经济性,不会追求动力性.因而其对应的发动机要求较小,排量不大于2 L,功率在5 0 kW左右,其动力性不会好,随之的传动系统也就比较经济,其主要用于家庭、出租车,其最高车速不大于130 km/h。
对于豪华轿车。
由于其更多地追求动力性、制动性能、安全性能、舒适性能,因而其采用大功率的发动机,排量不小于3 L,功率为100 kW左右。
其最高车速不小于180 km/h,因而随之而来的其他系统能力也将相应的加强,其各项技术性能指标进一步地提高。
同时不同地区标准也不同。
例如:欧洲其高速公路上的车辆的车速大于200 km/h。
其市内轿车的速度也不小于140 km/h,其豪华程度也不同。
.对于客车也不同,城市公交客车其最高车速为80 km/h,其行驶车速为60 km/h,其追求经济性及一挡、二挡的加速性,其比功率为12 kW/t;而旅游客车最高车速为12 0 km/h,其行驶车速为100 km/h。
副车架总成技术条件

车架总成基本技术条件1 范围本标准规定了汽车车架的技术要求、试验方法、检验规则、标志、包装、运输及贮存。
本标准适用于非承载车身的轻型汽车车架。
2 规范性引用标准本文件引用一下标准。
GB/T 1730 漆膜硬度测定法摆杆阻尼试验GB/T 1731 漆膜柔性测定法GB/T 1732 漆膜耐冲击测定法GB/T 3323 金属熔化焊焊接接头射线照相GB/T 9286 色漆和清漆漆膜的划格试验QC/T 518 汽车用螺纹紧固件紧固力矩GB/T 13452.2 — 2008 色漆和清漆漆膜厚度的测定QC/T 484-1999 汽车油漆涂层3 技术要求3.1 一般要求3.1.1 车架应符合本标准的要求,并按经规定程序批准的产品图样和设计文件制造。
3.1.2 组成车架总成的各零件应为检验合格的零件。
3.2 外观要求3.2.1 车架表面不应有影响外观的裂纹和使用性能、尖角和毛刺等缺陷。
3.2.2 冲压件不应有影响外观裂纹和使用性能的皱褶等缺陷。
3.2.3 焊缝平整光滑,不允许有裂纹、气孔、夹渣、咬边等缺陷。
3.2.4 漆膜应平整光滑,不允许有漏底、起皱、划碰伤等缺陷。
3.3 装配要求3.3.1 各零部件应装配完整 , 无错装、漏装现象。
3.3.2 下臂轴套与车架压装配合要求:轴套凸缘与车架下臂套管 X 向间隙 3/4 圆周≤0.1 , 1/4 圆周≤ 0.5 。
3.3.3 下臂轴套与车架之间的拉拖力≥ 15kN( 暂定 ) 。
3.3.4 螺纹紧固件紧固力矩符合 QC/T 518 的规定。
3.4 尺寸的要求3.4.1 各安装点尺寸符合设计要求,其中前悬架各安装点尺寸、车身悬置各安装点尺寸、后悬架各安装点尺寸及动力总成各安装点尺寸的重要度应为 B 级。
3.4.2长度≤5m 的车架总成对角线之差≤3mm ,长度 > 5m 的车架总成对角线之差≤5mm 。
长度≤5m 的车架车架总成扭曲变形≤5mm ,长度 > 5m 的车架总成扭曲变形≤7mm 。
车架总成工艺技术标准

28LSA74
第3页
下料尺寸
幅面板厚
板料宽度
主要设备及工装夹具
7×6610×382(外)
5×6610×362(内)
250/7+5
翼面80mm
1200(外)
1150(内)
ቤተ መጻሕፍቲ ባይዱ型号
名称
规格
数量
工艺技术作业指导—装夹成型
1、内、外片梁夹层刷防锈油漆;2、内、外片梁用∅13定位销定位,工装夹具见图A;
3、焊装工艺孔,工艺孔焊点不能高于大梁平面,在0~-1mm范围内;
3、斜尾封板焊缝均匀,封板焊接后不能高于大梁上翼面。
图A
图B
设计
校对
审核
批准
标记
处数
文件号
签字
日期
标记
处数
文件号
签字
日期
****汽车部件有限公司
28LSA74车架总成工艺技术标准
产品名称或产品型号
共5页
28LSA74
第3页
下料尺寸
幅面板厚
板料宽度
主要设备及工装夹具
7×6610×382(外)
5×6610×362(内)
幅面板厚
板料宽度
主要设备及工装夹具
7×6610×382(外)
5×6610×362(内)
250/7+5
翼面80mm
1200(外)
1150(内)
型号
名称
规格
数量
工艺技术作业指导—打磨
1、纵梁外表面“禁磨”:在纵梁外表面禁止使用磨光机打磨,对毛刺的位置只能用铲刀铲掉(铲刀口必须锋利);
2、外表面大孔飞边毛刺无法铲除的,用磨光机(带百叶片)打磨,磨痕距孔边缘不能超过5mm,切不得有较深磨痕;
车架设计手册
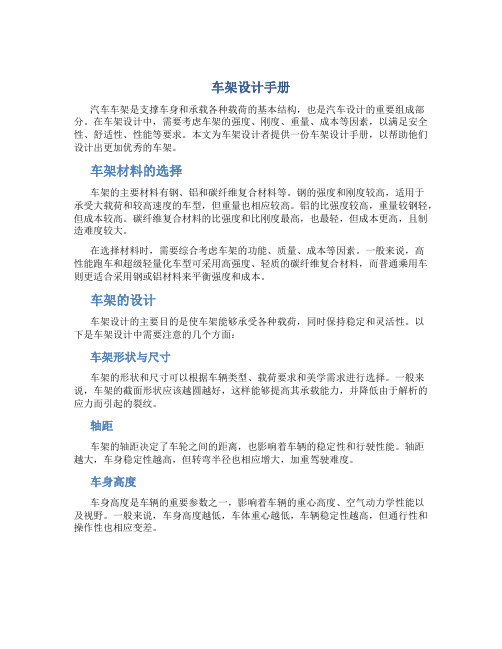
车架设计手册汽车车架是支撑车身和承载各种载荷的基本结构,也是汽车设计的重要组成部分。
在车架设计中,需要考虑车架的强度、刚度、重量、成本等因素,以满足安全性、舒适性、性能等要求。
本文为车架设计者提供一份车架设计手册,以帮助他们设计出更加优秀的车架。
车架材料的选择车架的主要材料有钢、铝和碳纤维复合材料等。
钢的强度和刚度较高,适用于承受大载荷和较高速度的车型,但重量也相应较高。
铝的比强度较高,重量较钢轻,但成本较高。
碳纤维复合材料的比强度和比刚度最高,也最轻,但成本更高,且制造难度较大。
在选择材料时,需要综合考虑车架的功能、质量、成本等因素。
一般来说,高性能跑车和超级轻量化车型可采用高强度、轻质的碳纤维复合材料,而普通乘用车则更适合采用钢或铝材料来平衡强度和成本。
车架的设计车架设计的主要目的是使车架能够承受各种载荷,同时保持稳定和灵活性。
以下是车架设计中需要注意的几个方面:车架形状与尺寸车架的形状和尺寸可以根据车辆类型、载荷要求和美学需求进行选择。
一般来说,车架的截面形状应该越圆越好,这样能够提高其承载能力,并降低由于解析的应力而引起的裂纹。
轴距车架的轴距决定了车轮之间的距离,也影响着车辆的稳定性和行驶性能。
轴距越大,车身稳定性越高,但转弯半径也相应增大,加重驾驶难度。
车身高度车身高度是车辆的重要参数之一,影响着车辆的重心高度、空气动力学性能以及视野。
一般来说,车身高度越低,车体重心越低,车辆稳定性越高,但通行性和操作性也相应变差。
骨架结构车架的骨架结构应该平衡强度和轻量化。
对于大型车辆,骨架结构的设计应该较为复杂,以保持其稳定性和承载能力。
车架的生产车架的生产需要采用精确的工艺和设备以满足各种质量标准。
以下是车架生产相关的几个要点:焊接车架中的焊接点对于车辆的稳定性和耐久性至关重要。
焊接质量影响到车架的强度和刚度,因此需要采用高质量的焊接方法,避免焊接缺陷和裂缝。
附属零部件车架包含许多附属零部件,如车轮、传动系统、刹车系统等,这些配件也需要精细加工以确保车架的稳定性和耐久性。
- 1、下载文档前请自行甄别文档内容的完整性,平台不提供额外的编辑、内容补充、找答案等附加服务。
- 2、"仅部分预览"的文档,不可在线预览部分如存在完整性等问题,可反馈申请退款(可完整预览的文档不适用该条件!)。
- 3、如文档侵犯您的权益,请联系客服反馈,我们会尽快为您处理(人工客服工作时间:9:00-18:30)。
Q/WCYG车架总成(全承载)设计规范扬州亚星客车股份有限公司发布前言本标准是根据国家有关客车方面的法规、标准等要求,结合我公司产品开发流程,并参考高等院校汽车专业教材相关章节制定而成,作为扬州亚星客车股份有限公司车架总成(半承载)设计的主要依据。
本标准由扬州亚星客车股份有限公司提出并归口。
本标准由扬州亚星客车股份有限公司汽车研究院起草。
本标准主要起草人:本标准由扬州亚星客车股份有限公司汽车研究院负责解释。
前言的内容可包括:(宋体,五号,段落1.5倍行距)a)任务来源;b)制定过程及征求意见情况;c)指明该标准采用国际标准、国外先进标准的程度;d)该标准导致废止或代替其他标准文件的全部或一部分的说明;e)实施该标准过渡期的要求;f)哪些附录是标准的附录,哪些附录是提示的附录的说明;g)附加说明:——本标准由汽车研究院提出。
——本标准由汽车研究院归口。
——本标准起草部门。
——本标准主要起草人。
——本标准首次发布、历次修改和复审确认年、月车架(半承载)总成设计规范1 范围本标准规定了半承载式车架总成的术语和定义、设计规范、车架的制造工艺及材料、车架防腐蚀要求、车辆VIN码和产品标牌在车架上的固定(位置)、车架总成的变动、设计评审要求、设计输出图样和文件的明细等基本设计准则。
本标准适用于半承载车架总成设计过程控制,外购底盘车架改制可参照执行。
本标准不适用于全承载车架总成设计过程控制。
2 规范性引用文件下列文件对于本文件的应用是必不可少的。
凡是注日期的引用文件,仅所注日期的版本适用于本文件。
凡是不注日期的引用文件,其最新版本(包括所有的修改单)适用于本文件。
GB 7258-2012 机动车运行安全技术条件GB1184-80 形状和位置公差GB3323-87 钢熔化焊对接接头射线照相焊缝质量分级Q/WCYG ZT C QY G 25-2012《外购零部件防腐蚀要求》3 术语和定义下列术语和定义适用本文件。
车架:汽车承载的基体,支撑着发动机、离合器、变速器、转向器、非承载式(或半承载式)车身等所有簧上质量的有关机件,承受着传给它的各种力和力矩。
纵梁:车架总成中主要承载元件,也是车架中最大的加工件,其形状应力求简单。
纵梁沿全长方向多取平直且断面不变或少变,以简化工艺。
有时也采取中间断面高、两边较低来保证纵梁各断面应力接近横梁:横梁将左右纵梁连在一起,构成完整的车架总成,保证车架有足够的扭转刚度,限制其变形和降低某些部位的应力。
有的横梁还作为发动机、散热器、传动轴以及悬架系统的紧固点。
4 设计规范4.1 车架的结构型式半承载式汽车,其前后悬架装置,发动机及变速器等传动系部件施加的作用力均由车架承受,所以,车架总成的刚性、强度及振动特性等几乎完全决定了车辆整体的强度、刚性和振动特性。
设计时在确保车架总成性能的同时,还应对车辆性能和匹配性进行认真的研究。
根据纵梁的特点,半承载客车车架主要可分为以下几种型式(见图4.1)。
a) b)c)图4.1 半承载客车车架主要型式a)直通纵梁式车架结构;b)中段桁架式车架结构;c)分段式车架结构;4.1.1 直通纵梁式车架结构见图4.1 a)该型式车架纵梁可为槽型或Z字型的直通大梁,横梁一般为槽型,有时也可采用其它特殊形状,如帽形或管形等等,纵梁与横梁之间联接一般采用过渡板铆、焊结构。
与车身联接的外横梁(也称牛腿)有槽型和异型钢管式。
4.1.2 中段桁架式车架结构见图4.1 b)该型式车架中段一般为矩形管的格栅式结构,前后段车架纵梁、横梁的形状一般为槽型,中段与前、后段之间联接一般采用过渡板铆、焊结构。
4.1.3组合式车架结构见图4.1 c)该型式车架纵梁为分段式,纵梁、横梁的形状一般为槽型、矩形管等形状不一,一般根据车辆用途、安装不同总成的需要来进行自然分段铆、焊接。
4.1.4 三种结构特点分析对比见表14.2 车架受力及其应力分析车架受力状态极为复杂。
汽车静止时,它在悬架系统的支撑下,承受着汽车各部件及载荷的重力,引起纵梁的弯曲和偏心扭转(局部扭转)。
如汽车所处的路面不平,车架还将呈现整体扭转。
汽车行驶时,载荷和汽车各部件的自身质量及其工作载荷(如驱动力、制动力和转向力等)将使车架各部位承受着不同方向、不同程度和随机变化的动载荷,车架的弯曲、偏心扭转和整体扭转将更严重,同时还会出现侧弯、菱形倾向以及扭转振动及噪声。
有时,某些专用汽车的装置件还可能使车架产生较大的装置载荷。
因此,车架应有足够的弯曲刚度,以使装在其上的有关机构之间的相对位置在汽车行驶过程中保持不变并使车身的变形最小;车架也应有足够的强度,以保证其有足够的可靠性与寿命,纵梁等主要零件在使用期内不应有开裂和严重变形。
车架的受力变形见图4.2图4.2 车架的受力和变形a)纵向弯曲;b)侧向弯曲;c)纵向受力;d)整体扭转;e)局部扭转在以上图示载荷作用下,纵梁将产生以下几种应力。
1) 弯曲应力。
设计时常假定纵梁在某些集中载荷作用下只产生弯曲,可按材料力学的原理采用弯矩差法和力多边形法进行分析。
2) 局部扭转应力。
开口断面纵梁在偏心载荷作用下往往出现较大的局部扭转,在载荷作用处及其邻近的翘曲约束处往往双力矩(B )较大,如图4.3a)和图4.3c)所示,可用薄壁杆件理论加以分析。
3) 整体扭转应力。
车架处于整体扭转时,开口断面梁一般在其翘曲约束较强处出现较大的扇性应力。
最好是在产品开发阶段,对车架静应力、刚度、振动模态以至动应力和碰撞安全等进行有限元分析,对其轻量化、使用寿命,以及振动和噪声特性做出初步判断,为缩短产品开发周期创造有利条件。
图4.3 车架扭转应力a)翘曲约束梁偏心扭转时的双力矩图;b)槽形断面的扇形应力图;c)车架整体扭转时纵梁翼缘应力;4.3 车架的刚度根据载荷特征和变形特征,可以定义出多种车架刚度。
车架模态分析时常注意其垂直弯曲刚度、整体扭转刚度及整车扭转刚度。
有时还要分析纵梁的局部扭转刚度(时常和横梁弯曲刚度结合)及车架水平弯曲刚度。
车架的各种刚度,因结构不同,有的相差极大。
例如常见的由开口断面梁组成的梯形车架,一般其整体扭转刚度极小,而弯曲刚度较大,纵梁局部扭转刚度在横梁处较大,而在横梁之间的部分则较小。
至于整车扭转刚度,往往比车架大好几倍。
车架刚度不足会引起振动和噪声,也使汽车的乘座舒适性、操纵稳定性及可靠性下降(车架的最大弯曲挠度通常小于10mm ),车架刚度又不宜过大,否则将使车架和悬架系统的载荷增大并使汽车轮胎的接地性变差,使通过性变坏。
车架整体扭转时,在车架扭转刚度计算中通常以前、后轴的相对扭角为准。
汽车行驶时,车架将出现整体扭转状态。
如汽车以低速通过路面凸包时,车架的轴间扭角.b a =)/(11s j c c +式中:b —道路不平度(以轴间扭角表示);Cj-车架(整体)扭转刚度; Cs-悬架系统(含车轮)角刚度。
当s j c c /=1时,α=0.5b,即车架和悬架系统的扭角各为道路扭角的一半。
提高车架扭转刚度可相应提高其自振频率。
同时也可增大整车的扭转刚度,使α有所减小。
其不利影响是,在某些使用条件下,汽车的通过性将下降,车架及悬架系统的载荷也会增大。
刚度及悬置跨度较大的装置件如发动机,通常采用四点或三点悬置,通过软垫与车架连接,以减小车架扭转变形的不利影响。
改变悬置方式及刚度,往往可以消除某些共振问题。
例如:将悬置点设于车架振动模态节点处,可显著减轻振动的传递;将悬置点接近梁的弯曲中心,或在该处设置横梁,则可有效地限制纵梁的局部扭转。
设计时应注意加强板、车架纵梁等零件的端部形状和连接方式,以避免刚度突变,导致损坏。
如图4。
4所示。
4.4 纵梁4.4.1 纵梁型式概述纵梁是车架中主要的承载元件,通常采用低合金钢板冲压而成,其长度大致接近整车长度,其形状应力求简单,一般为槽形,也有的做成Z 字形或箱形断面,沿长度方向的变化应小或不变,以简化工艺, 图4.5纵梁的形状及其断面 根据客车型式的不同和结构布置的要求,纵梁也可以在水平面内或纵向平面内做成弯曲的。
为了使材料得到合理利用,可将纵梁设计成等强度的简支梁,其中部截面高度较大, 两端逐渐减小。
4.4.2 纵梁类别及形状 :各种纵梁的形状及其断面 见图4.5。
梯形车架纵梁的上表面应尽可能做成平直的,中部断面一般较大、两端较小,与所受弯矩相适应。
也有全长或仅中部及后部为等断面的。
根据整车布置要求,有时采用前端或后端或前后端均弯曲的纵梁。
槽形断面梁抗弯强度大,工艺性好,零件安装、紧固方便,广泛应用于货车及客车。
根据需要也可用Z 形断面,多品种生产时,不同轴距、不同装载质量的系列车型采用内高相同的槽形断面纵梁,通过变化钣料厚度或翼缘宽度获得不同强度。
为保证通用化优先采用槽形结构,且其截面尺寸、长度应尽可能选用现有模具规格。
我公司常用模具规格如下:160X65(mm)、180X65(mm)、200X65(mm)、225x70(mm)、(240X75(mm)、(250X75(mm)等。
4.4.3纵梁的强度纵梁受力极为复杂,设计时不仅应注意降低各种应力,改善其分布情况,还应注意使各种应力峰值不出现在同一部位上。
例如,纵梁中部弯曲应力较大,则应注意降低其扭转应力,减小应力集中并避免失稳。
而在其前、后端,则应着重控制悬架系统引起的局部扭转。
提高纵梁强度常用的措施如下:4.4.3.1 提高弯曲强度1)、选定较大的断面尺寸和合理的断面形状(槽形梁断面高宽比一般为3:1左右);2)、在应力较大部位加加强板;图示4。
63)、将受拉翼缘适当加宽。
4.4.3.2 提高局部扭转刚度1)、注意偏心载荷的布置,使相近偏心载荷尽量接近纵梁断面的弯曲中心,使合成量小;2)、在偏心载荷较大处设置横梁,并根据载荷大小及分散情况确定连接强度和宽度;3)、将载荷点尽可能布置在纵梁断面的弯曲中心上;4)、当偏心载荷较大并偏离纵梁较远时,横梁可采用K形横梁或其他加强结构,或将该段纵梁形成封闭断面;5)、偏心载荷较大且较分散时,应采用封闭断面纵梁,横梁间距也应缩小;6)、选用较大的断面;4.4.3.3 提高整体扭转刚度1)、不使纵梁断面过大,在纵梁大断面处纵、横梁采用立板连接;2)、翼缘连接的横梁不宜相距太远。
4.4.4.4 减小应力集中及疲劳敏感1)、尽可能减小翼缘上的孔(特别是高应力区),严禁在翼缘上布置大孔;2)、对于弯曲纵梁,弯曲部位的圆弧半径不宜过小,以避免变形区出现波纹或严重变薄;3)、注意加强端部的形状和连接,避免刚度突变;4)、杜绝在槽形纵梁的翼缘边缘处施焊;4.4.4.5 减小失稳1)、在受压翼缘宽度和厚度的比值不宜过大(常在12左右);2)、在容易失稳处加焊撑板;4.4.4.6 局部强度加强1)、采用较大的板厚;2)、在集中力较大处将纵梁局部贴加强板,必要时再将加强板压肋或折边;3)、加大支架紧固面尺寸,增多紧固件数量,并尽量使力作用点接近纵梁立板的上、下侧。