冷堆技术
高温气冷堆功率

高温气冷堆功率高温气冷堆(HTGR)是一种新型的核能技术,它采用氦气作为冷却剂,具有高温、高效率和安全可靠的特点。
高温气冷堆功率是评估该技术的重要指标之一。
本文将对高温气冷堆功率进行详细介绍。
高温气冷堆功率是指高温气冷堆在单位时间内产生的热能或电能的大小。
由于高温气冷堆的工作温度较高,可以达到700至1000摄氏度,因此其热效率和电效率都相对较高。
高温气冷堆可以通过核裂变将燃料中的核能转化为热能,然后利用热能驱动发电机产生电能。
根据燃料的不同,高温气冷堆可以使用铀、钍等元素作为燃料,并将其装入微孔球形燃料颗粒中。
高温气冷堆在核能技术领域具有许多优势。
首先,高温气冷堆具有较高的热效率,可以将燃料中的核能充分转化为热能,提高了能源利用率。
其次,高温气冷堆产生的热能可以用于工业和城市供热,实现热电联供,进一步提高能源利用效率。
此外,高温气冷堆还具有安全性好的特点。
由于采用氦气作为冷却剂,不需要高压循环和使冷却剂沸腾,从而降低了核能系统的复杂性,提高了安全性。
高温气冷堆功率的大小与多个因素有关。
首先,燃料的选择和寿命会对高温气冷堆的功率产生影响。
不同的燃料在衰变过程中会释放出不同数量的能量,因此会影响高温气冷堆的功率。
其次,高温气冷堆的设计和运行参数也会影响功率的大小。
比如,反应堆的尺寸和结构、冷却剂的流速和温度等都会对功率产生影响。
此外,燃料的循环方式和功率调整方式也会影响高温气冷堆的功率。
高温气冷堆的功率大小对于核能的开发和利用具有重要意义。
首先,高温气冷堆可以作为一种新型的核能技术,为国内能源结构调整提供了新的选择。
高温气冷堆可以实现多能联供,既可以产生电能,又可以提供热能,满足工业和城市的能源需求。
其次,高温气冷堆可以作为一种安全可靠的核能技术,为核能的发展提供了更可行的方案。
高温气冷堆通过采用氦气作为冷却剂,避免了核能系统中的复杂性,提高了核能的安全性。
总的来说,高温气冷堆功率是评估该技术的重要指标之一。
高温气冷堆技术特点包括

高温气冷堆技术特点包括高温气冷堆(High Temperature Gas-cooled Reactor,HTGR)是一种高效、安全、环保的新型核能技术,其技术特点包括以下几个方面。
首先,高温气冷堆具有高效能的特点。
传统的压水堆和沸水堆采用的是低温冷却剂,限制了核反应堆的热效率。
而高温气冷堆采用氦气作为冷却剂,使得工作温度可以达到800℃以上,相对于传统堆芯的温度提高了几倍。
高温气冷堆可以利用高温热能,提高热效率,提供更多的电力输出,实现核能的高效利用。
其次,高温气冷堆具有更高的安全性。
高温气冷堆采用了三次裂变转变概念,核反应堆芯与冷却循环系统之间的辐射屏蔽层完全隔离,有效避免了裂变产品的泄漏,降低了放射性污染的风险。
此外,高温气冷堆还采用了几何具有安全特性的芯块形状,使其具有良好的自稳定性和应对冲击负荷的能力。
同时,高温气冷堆采用了固体燃料,避免了液体燃料在高温下破裂的可能性,大大降低了核反应堆事故的风险。
另外,高温气冷堆还具有较强的灵活性和适应性。
高温气冷堆采用了球堆的设计形式,模块化程度高,堆芯单节点可拆卸,堆芯构件可根据实际需求进行灵活调整,方便维护和更新。
高温气冷堆还可以根据实际需求提供多种不同形式的热能输出,如发电、煤炭转化、水化制氢等,具有多功能的适用性。
此外,高温气冷堆具有较低的燃料消耗和核废料产生。
高温气冷堆采用了高浓缩程度的燃料球形颗粒,可实现燃料的长周期使用,燃料利用率高达90%以上。
同时,由于反应堆芯温度高于传统堆芯,核废料的销售期相对较长,对于核废料的处理和排放也相对较少,减少了对环境的负面影响。
最后,高温气冷堆具有经济性和可持续性。
高温气冷堆具有较长的寿命和高可靠性,核电经济性指标较高。
由于核反应堆芯温度高,可以与多种工业生产过程进行热耦合,实现齐氏动力系统。
同时,高温气冷堆还具有低碳排放的特点,与新能源和智能电网相结合,能够提供带有较少温室气体排放的能源需求。
综上所述,高温气冷堆具有高效能、高安全性、较强的灵活性和适应性、低燃料消耗和核废料产生、经济性和可持续性等一系列技术特点。
高温气冷堆技术发展历史

早期研究与实验
1940年代:美国橡树 岭国家实验室开始研 究高温气冷堆技术
1960年代:德国卡尔 斯鲁厄研究中心开始 研究高温气冷堆技术
1950年代:美国阿贡 国家实验室进行了高 温气冷堆实验
1970年代:日本开始 研究高温气冷堆技术, 并进行了实验
技术挑战:高温气冷堆技术仍面临一些技术难题,如 材料、安全性等方面的挑战
市场竞争:高温气冷堆技术面临与其他核电技术的竞争, 需要不断提高技术水平和降低成本以增强竞争力
4 高温气冷堆技术的未来展望
技术发展趋势
提高安全性:通过 改进设计、材料和 制造工艺,提高高 温气冷堆技术的安 全性能。
降低成本:通过优 化设计和制造工艺, 降低高温气冷堆技 术的建设和运行成 本。
03
02
清洁能源:高温 气冷堆技术在清 洁能源领域的应 用潜力巨大
04
国际合作:高温 气冷堆技术在国 际合作领域的潜 力与机遇
社会效益与影响
提高能源利用效率:高温气冷堆技术可以提高能源利用效率,减少能源消耗, 降低环境污染。
促进经济发展:高温气冷堆技术可以带动相关产业的发展,促进经发展, 增加就业机会。
03
03
高温气冷堆技术:20世纪60年代, 美国开始研究高温气冷堆技术
04
04
发展现状:高温气冷堆技术已成为 核能发电技术的重要发展方向之一
高温气冷堆技术的诞生
起源:20世纪40年代,美国橡树岭国家实验室开 始研究高温气冷堆技术
目的:开发一种安全、高效的核能发电技术
原理:利用高温气体作为冷却剂,直接冷却堆芯, 提高发电效率
高温气冷堆技术
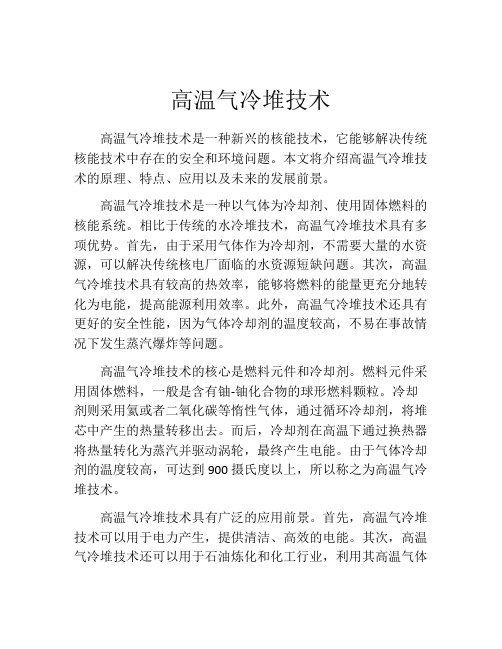
高温气冷堆技术高温气冷堆技术是一种新兴的核能技术,它能够解决传统核能技术中存在的安全和环境问题。
本文将介绍高温气冷堆技术的原理、特点、应用以及未来的发展前景。
高温气冷堆技术是一种以气体为冷却剂、使用固体燃料的核能系统。
相比于传统的水冷堆技术,高温气冷堆技术具有多项优势。
首先,由于采用气体作为冷却剂,不需要大量的水资源,可以解决传统核电厂面临的水资源短缺问题。
其次,高温气冷堆技术具有较高的热效率,能够将燃料的能量更充分地转化为电能,提高能源利用效率。
此外,高温气冷堆技术还具有更好的安全性能,因为气体冷却剂的温度较高,不易在事故情况下发生蒸汽爆炸等问题。
高温气冷堆技术的核心是燃料元件和冷却剂。
燃料元件采用固体燃料,一般是含有铀-铀化合物的球形燃料颗粒。
冷却剂则采用氦或者二氧化碳等惰性气体,通过循环冷却剂,将堆芯中产生的热量转移出去。
而后,冷却剂在高温下通过换热器将热量转化为蒸汽并驱动涡轮,最终产生电能。
由于气体冷却剂的温度较高,可达到900摄氏度以上,所以称之为高温气冷堆技术。
高温气冷堆技术具有广泛的应用前景。
首先,高温气冷堆技术可以用于电力产生,提供清洁、高效的电能。
其次,高温气冷堆技术还可以用于石油炼化和化工行业,利用其高温气体可以进行高效的反应过程。
此外,高温气冷堆技术还可以用于热力供暖等领域,提供可靠的高温热能。
高温气冷堆技术在全球范围内得到了广泛的关注和研究。
许多国家已经开始了高温气冷堆技术的研发和建设。
例如,中国的“华龙一号”核电技术就采用了高温气冷堆技术。
高温气冷堆技术还与其他新兴能源技术相结合,例如核聚变技术,可以实现更稳定、安全、高效的能源供应。
然而,高温气冷堆技术在实际应用中还存在一些挑战和问题。
首先,高温气冷堆技术的燃料元件和冷却剂的选择和研发,仍然需要进一步的研究。
其次,高温气冷堆技术的建设和运行成本相对较高,需要进一步降低成本,提高经济效益。
此外,高温气冷堆技术在废物处理和核安全等方面也需要进一步研究和完善。
高温气冷堆的特点与应用

高温气冷堆的特点与应用高温气冷堆(High Temperature Gas-cooled Reactor,HTGR)是一种新型的核能发电技术,具有许多独特的特点和广泛的应用前景。
本文将介绍高温气冷堆的特点以及其在能源领域的应用。
一、高温气冷堆的特点1. 高温工作温度:高温气冷堆的工作温度通常在700℃以上,甚至可以达到1000℃。
相比传统的水冷堆,高温气冷堆的工作温度更高,能够提供更高的热效率。
2. 气冷散热:高温气冷堆采用气体作为冷却剂,通过直接循环冷却剂与燃料颗粒之间的热交换,实现散热。
相比水冷堆的间接循环冷却方式,气冷堆的散热效果更好,能够更高效地将热能转化为电能。
3. 燃料颗粒堆芯:高温气冷堆的燃料采用微米级的球形燃料颗粒,这些颗粒由包裹燃料核心的多层包覆层组成。
这种设计可以有效地防止燃料核心的泄漏和扩散,提高燃料的利用率和安全性。
4. 高安全性:高温气冷堆采用固体燃料和气体冷却剂,不存在液体冷却剂的蒸汽压力和蒸汽爆炸的风险。
同时,燃料颗粒堆芯的设计也能够有效地防止燃料泄漏和核裂变产物的扩散,提高了堆芯的安全性。
5. 多种燃料适应性:高温气冷堆可以使用多种燃料,包括天然气、石油、煤炭等化石燃料,以及铀、钍等核燃料。
这种多种燃料适应性使得高温气冷堆在能源转型和资源利用方面具有广阔的应用前景。
二、高温气冷堆的应用1. 核能发电:高温气冷堆作为一种新型的核能发电技术,具有高效率、高安全性和多燃料适应性的特点,被广泛应用于核能发电领域。
高温气冷堆可以提供稳定可靠的电力供应,同时还可以与其他能源形式相结合,实现能源的多元化利用。
2. 工业热能供应:高温气冷堆的高温工作温度使其可以提供高温热能,广泛应用于工业领域的热能供应。
高温气冷堆可以为工业生产提供稳定的高温热源,满足工业生产过程中的热能需求,提高能源利用效率。
3. 氢能生产:高温气冷堆可以通过核热解水的方式产生氢气,为氢能产业的发展提供可靠的能源支持。
我国高温气冷堆的发展
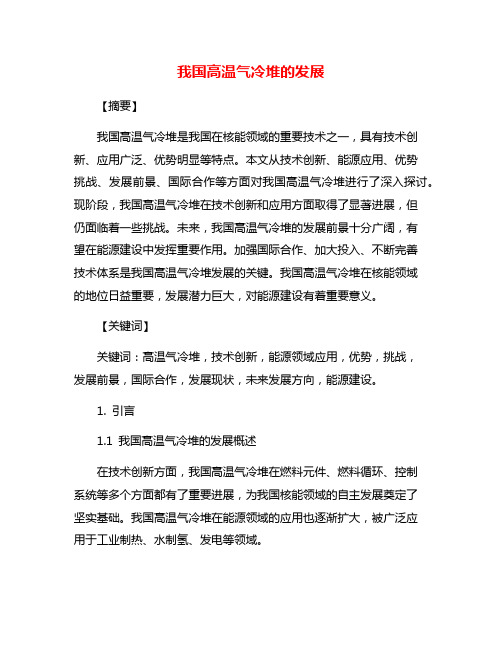
我国高温气冷堆的发展【摘要】我国高温气冷堆是我国在核能领域的重要技术之一,具有技术创新、应用广泛、优势明显等特点。
本文从技术创新、能源应用、优势挑战、发展前景、国际合作等方面对我国高温气冷堆进行了深入探讨。
现阶段,我国高温气冷堆在技术创新和应用方面取得了显著进展,但仍面临着一些挑战。
未来,我国高温气冷堆的发展前景十分广阔,有望在能源建设中发挥重要作用。
加强国际合作、加大投入、不断完善技术体系是我国高温气冷堆发展的关键。
我国高温气冷堆在核能领域的地位日益重要,发展潜力巨大,对能源建设有着重要意义。
【关键词】关键词:高温气冷堆,技术创新,能源领域应用,优势,挑战,发展前景,国际合作,发展现状,未来发展方向,能源建设。
1. 引言1.1 我国高温气冷堆的发展概述在技术创新方面,我国高温气冷堆在燃料元件、燃料循环、控制系统等多个方面都有了重要进展,为我国核能领域的自主发展奠定了坚实基础。
我国高温气冷堆在能源领域的应用也逐渐扩大,被广泛应用于工业制热、水制氢、发电等领域。
虽然我国高温气冷堆具有诸多优势,但也面临着挑战。
比如材料技术、安全问题、经济性等方面的挑战需要我们不断突破。
我国高温气冷堆的发展前景依然十分广阔,具有巨大的发展潜力。
在国际合作方面,我国高温气冷堆也积极开展与其他国家的合作,共同推动该技术的发展。
我国高温气冷堆的发展正处于蓬勃发展的阶段,具有重要的战略意义和广阔的市场前景。
2. 正文2.1 我国高温气冷堆技术创新我国高温气冷堆技术创新是我国核能领域的重要突破之一。
高温气冷堆是一种新型的核能技术,与传统的水冷堆相比具有更高的工作温度和热效率,适用于多种应用场景。
我国在高温气冷堆技术上取得了许多创新成果。
我国在高温气冷堆燃料元件设计方面有了较大突破。
通过优化燃料元件结构和材料,提高了燃料利用率和安全性能,实现了燃料寿命的延长和燃料循环的有效性。
我国还开展了燃料后处理技术的研究,提高了燃料再处理工艺和设备的稳定性和效率。
高温气冷堆技术特点

高温气冷堆技术特点高温气冷堆技术特点引言:高温气冷堆技术是近年来在核能领域的重要研究方向之一。
与传统的水冷堆相比,高温气冷堆具有许多独特的技术特点。
本文将从四个方面分析高温气冷堆技术的特点:燃料和冷却剂,耐腐蚀材料,热工性能,以及安全和环保。
一、燃料和冷却剂:高温气冷堆使用的燃料是球形的微制球,一般是由含有铀和三核化铀的氧化物颗粒组成。
这种独特的燃料形式可以提高燃料的热导率,从而提高堆芯的热工性能。
高温气冷堆常用的冷却剂是氦气,氦气具有良好的热导率和化学稳定性,可以用于有效地冷却燃料颗粒和提取热能。
二、耐腐蚀材料:高温气冷堆的结构材料需要具备良好的耐腐蚀性能,能够在高温和辐射环境中长期稳定工作。
一般采用的耐腐蚀材料有石墨、石墨复合材料和陶瓷材料等。
石墨在高温环境下具有较高的强度和稳定性,并且对气体和液体的腐蚀性能很好。
石墨复合材料因其综合性能优良而成为高温气冷堆中常用的结构材料。
三、热工性能:高温气冷堆具有出色的热工性能,主要表现在以下几个方面:1. 高温:高温气冷堆的工作温度通常在700-950摄氏度之间,相比传统的水冷堆,具有更高的工作温度,可以充分利用核燃料的热能。
2. 高效:高温气冷堆的热效率比传统水冷堆高,能够更有效地将核燃料的热能转化为电能或有用的热能。
3. 多用途:高温气冷堆不仅可以产生电能,还可以利用余热进行工业生产或其他领域的应用,提高能源利用效率。
四、安全和环保:高温气冷堆具有较高的安全性和环保性,主要体现在以下几个方面:1. 相对于传统的水冷堆,高温气冷堆使用的冷却剂是氦气,不存在冷却剂泄漏导致的放射性物质释放的问题。
2. 高温气冷堆的燃料颗粒稳定性好,不易产生放射性物质泄露,有助于减少核废料的产生和处理。
3. 高温气冷堆采用气体冷却方式,可以减少对水资源的消耗,降低对环境的影响。
结论:高温气冷堆技术具有独特的技术特点,包括燃料和冷却剂的选择,耐腐蚀材料的应用,出色的热工性能以及安全和环保等方面的优势。
高温气冷堆的优点
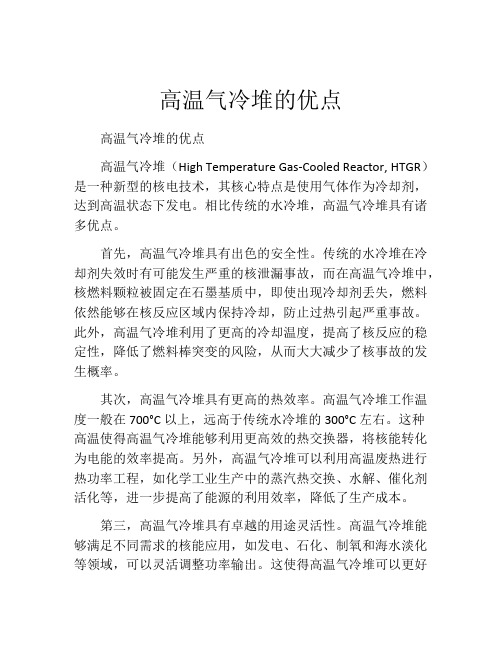
高温气冷堆的优点高温气冷堆的优点高温气冷堆(High Temperature Gas-Cooled Reactor, HTGR)是一种新型的核电技术,其核心特点是使用气体作为冷却剂,达到高温状态下发电。
相比传统的水冷堆,高温气冷堆具有诸多优点。
首先,高温气冷堆具有出色的安全性。
传统的水冷堆在冷却剂失效时有可能发生严重的核泄漏事故,而在高温气冷堆中,核燃料颗粒被固定在石墨基质中,即使出现冷却剂丢失,燃料依然能够在核反应区域内保持冷却,防止过热引起严重事故。
此外,高温气冷堆利用了更高的冷却温度,提高了核反应的稳定性,降低了燃料棒突变的风险,从而大大减少了核事故的发生概率。
其次,高温气冷堆具有更高的热效率。
高温气冷堆工作温度一般在700°C以上,远高于传统水冷堆的300°C左右。
这种高温使得高温气冷堆能够利用更高效的热交换器,将核能转化为电能的效率提高。
另外,高温气冷堆可以利用高温废热进行热功率工程,如化学工业生产中的蒸汽热交换、水解、催化剂活化等,进一步提高了能源的利用效率,降低了生产成本。
第三,高温气冷堆具有卓越的用途灵活性。
高温气冷堆能够满足不同需求的核能应用,如发电、石化、制氧和海水淡化等领域,可以灵活调整功率输出。
这使得高温气冷堆可以更好地适应不同地区的能源需求和经济发展水平,提高能源供应的可靠性和稳定性。
第四,高温气冷堆具有较小的用地需求。
传统的水冷堆需要大量的水源供冷,因此在选择建设地点时需要考虑水资源的充足性和污染控制。
而高温气冷堆无需大量水资源,只需利用大气作为冷却介质,因此在选址上更加灵活,并且减少了对水资源的污染风险,降低了核电站运营的环境风险。
第五,高温气冷堆具有较长的燃料寿命。
高温气冷堆使用的核燃料一般为球形或棒状的颗粒状燃料,具有很强的耐高温和抗辐照性能。
燃料颗粒在高温气冷堆中的停留时间较长,使得能源的利用效率更高、燃料更加充分利用,从而延长了燃料更换周期,降低了燃料管理的成本。
高温气冷堆技术研究

高温气冷堆技术研究一、综述高温气冷堆(High Temperature Gas-Cooled Reactor,HTGR)是一种基于氦气作为冷却剂,球形燃料颗粒构成燃料元件,使用含有放射性210Pb和226Ra的天然矿石球团体作为反应堆壳的中子反射层的一种核反应堆。
由于其独特的设计和系统性能,HTGR 已经成为当前核电技术研究的热点之一,具有开发和推广的潜力。
本文将在深入分析HTGR技术原理的基础上,对不同类型的HTGR技术进行研究论述和探讨。
二、技术原理1.堆芯设计HTGR堆芯设计一般采用球形燃料颗粒构成燃料元件,燃料颗粒由内而外分布不同结构,包括燃料核心、内降温层、内热输出层、外降温层和外热输出层五个部分。
燃料元件都串联在控制棒组、反应堆内壳、中子反射层和球壳之间,构成了HTGR的正常燃料链。
2.冷却剂拥堵特性HTGR使用氦气作为冷却剂,其特性是高热传导、惰性和透明,对于核燃料具有优异的散热性和防护性能,在HTGR的设计和控制中发挥了重要的作用。
HTGR 氦气冷却系统的主要功能是通过散热管式燃料元件的外壳和头部将热量传递到冷却剂中,而氦气冷却通过各种机制保证在一定范围内的温度水平来有效地控制燃料和减轻设备运行过程中的冷却剂拥堵。
3.安全特性HTGR对安全性的关注已经在其设计和应用阶段中进行了鉴定和评价。
HTGR通过基础防线和二次防线两种符合原则和目的的安全机制来保证其安全性能。
基础防线工作原理是在堆芯内部设计足够的容量来保证对堆芯内部故障的快速响应和封堵,而二次防线的目的是在基础防线封闭之前保证超额保护能力。
三、技术类型1.复合型复合型气冷堆用于煤制气合成,采用下列动力学模拟方法,在反应器水平开堆模式下,达到化学品的高度稳定的水平:1) 分层模拟:通过解决运动方程和固定基本参数来进行模拟。
2) 长程热效应模拟:通过区分化学反应机理,通过 MATLAB 来进行模拟。
3) 质量传递模拟:通过分析气固反应的动力学过程,来达到气体的质量传递。
高温气冷堆 中核能源

高温气冷堆中核能源高温气冷堆是一种新型的核能源技术,其提供了一种可持续、高效且环保的能源解决方案。
中核能源是中国领先的核能公司,他们在高温气冷堆技术方面取得了显著的成就。
本文将探讨高温气冷堆技术的原理、特点以及中核能源在该领域的贡献。
高温气冷堆(High-Temperature Gas-cooled Reactor,简称HTGR)利用了高温下的核燃料燃烧来产生能源。
该技术使用固体燃料(通常是球形的小型燃料颗粒)和气体冷却剂,如氦气。
核燃料在高温下燃烧,产生的热能被转化为蒸汽,然后驱动涡轮机发电。
与传统的核电技术相比,高温气冷堆具有许多优势。
首先,高温气冷堆具有更高的热效率。
由于工作温度更高,其发电效率可达到50%以上,而传统核电技术大约只有30%。
这使得高温气冷堆在能源利用率方面更具竞争力。
其次,高温气冷堆可以产生高品质的热能。
由于工作温度高,其产生的热能可以直接应用于工业生产和供暖领域,而无需转换为电力。
传统核电通常需要通过蒸汽循环来转换热能,这导致一定的能量损失。
第三,高温气冷堆具有更高的安全性。
由于使用固体燃料和气体冷却剂,HTGR在设计上更加稳定,不易发生核燃料泄漏或冷却剂事故。
此外,高温气冷堆具有自动关闭和自冷却的特性,在危险情况下能够自动停止核反应,从而避免了可能的事故情况。
与其他核能公司相比,中核能源在高温气冷堆技术领域的研发和应用取得了重要进展。
中核能源在桃花江高温气冷堆核电站的建设和运营中起到了关键作用。
中核能源的高温气冷堆采用了自主研发的核燃料和冷却剂技术,使其在效率和可靠性方面优于其他类似技术。
此外,中核能源还致力于高温气冷堆技术的应用与推广。
他们与工业和供暖领域的合作伙伴合作,利用高温气冷堆的热能直接供应给工业设备和供暖系统,提高能源利用效率。
这不仅提供了可持续而高效的能源解决方案,同时也减少了对传统化石燃料的依赖,降低了环境污染的风险。
总结起来,高温气冷堆是一种具有巨大潜力的技术,能够提供可持续、高效和环保的能源。
高温气冷堆的原理

高温气冷堆的原理高温气冷堆是一种先进的核能发电技术,它能够通过气体冷却来驱动和冷却核反应中的燃料。
相比于传统的水冷堆,高温气冷堆具有更高的工作温度,更高的热效率以及更强的安全性能。
本文将详细介绍高温气冷堆的原理。
首先,高温气冷堆的核心部分是核燃料。
核燃料一般选择铀或钍等放射性元素,通过核反应产生的热能来驱动发电机组发电。
而与传统的水冷堆不同,高温气冷堆采用气体冷却介质,例如气体冷却堆可以使用氦气,氦气作为冷却介质能够在高温下具有很好的热导性能,并且不易发生化学反应。
其次,高温气冷堆的核反应基于核裂变原理。
核裂变是指将重核(例如铀、钍)撞击中子后裂变成两个或多个轻核的过程。
核反应发生时,会释放出大量的能量。
在高温气冷堆中,裂变产生的热能被传递给气体冷却剂,通过气体冷却剂暖气器传递给热交换器或直接用于发电。
第三,高温气冷堆中的热交换器是实现热能转换的关键。
热交换器一般由管子组成,通过管道内的气体冷却剂与裂变燃料之间的热传递,将高温气体中的热能通过换热传递给工作介质,例如用于蒸汽发电的水。
通过这种方式,可以将核反应释放的热能高效地转化为电能。
此外,高温气冷堆的安全性能也值得关注。
高温气冷堆采用气体冷却剂,相比水冷堆而言,气体冷却剂更不易发生蒸汽爆炸等事故,避免了放射性物质的泄漏和生态环境的影响。
而且,高温气冷堆通过设计安全堆芯结构和控制系统,能够自动响应异常情况,使堆芯安全地关闭。
最后,高温气冷堆的优势不仅体现在高效能转换和安全性上,还可以用于热利用,使核能发电进一步提高经济效益。
高温气冷堆的高温热能可以用于工业生产过程中的蒸汽供应、海水淡化、油砂开采等,进一步满足社会需求。
总的来说,高温气冷堆是一种既高效又安全的核能发电技术。
通过核裂变原理和气体冷却介质的选择,高温气冷堆能够实现核能的高效转化,并且具有更好的安全性能。
随着科技的不断进步,高温气冷堆必将在未来的核能发电领域发挥重要作用。
高温气冷堆技术采用

高温气冷堆技术采用高温气冷堆技术采用引言高温气冷堆技术是一种新型的核能利用技术,它采用了气体作为热传输介质,将核能转化为电能或热能。
与传统的水冷堆技术相比,高温气冷堆技术具有诸多优势,包括安全性、高效性、环境友好等。
本文将详细介绍高温气冷堆技术的原理、应用及前景。
一、高温气冷堆技术的原理高温气冷堆技术是通过将核燃料(如铀、钚等)放置在燃料元件中,并在控制条件下进行核反应,产生大量热能。
燃料元件通常由燃料棒和包围燃料棒的燃料壳组成。
燃料元件中的热能通过与工质气体(通常是氦气)的热交换来实现转化,将热能转化为电能或热能。
高温气冷堆技术与传统的水冷堆技术相比,最大的区别在于热传输介质的差异。
传统的水冷堆技术使用水作为冷却剂,通过循环水来从反应堆中带走热量。
而高温气冷堆技术则使用气体(通常是氦气)作为热传输介质,利用气体的高热导性能,直接将热能传递给燃料元件外的供热系统。
二、高温气冷堆技术的应用1. 电力生成高温气冷堆技术可以转化核能为电能,并将其供给电网。
高温气冷堆可以提供高温高压的工质气体,这些气体可以直接驱动汽轮机或发电机,实现电力的生成。
相比传统的水冷堆技术,高温气冷堆技术的电力转化效率更高,能够更充分地利用核能资源。
2. 工业供热高温气冷堆技术的另一个应用是工业供热。
高温气冷堆可以提供高温的工质气体,这些气体可以直接供给工业生产中的加热炉、锅炉等设备,满足工业生产中对高温热能的需求。
相比传统的水冷堆技术,高温气冷堆技术的供热效率更高,能够更好地满足工业生产的需求。
3. 燃料制氢高温气冷堆技术还可以用于燃料制氢。
高温气冷堆中的工质气体(氦气)可以与水反应,产生氢气。
氢气被认为是一种清洁能源,可以用于替代传统的化石燃料。
利用高温气冷堆技术制氢,可以实现核能和可再生能源的结合,提高能源的可持续性和环境友好性。
三、高温气冷堆技术的前景目前,高温气冷堆技术仍处于发展初期,但已经在一些国家得到了重视和推广。
高温气冷堆 制氢

高温气冷堆制氢高温气冷堆制氢技术引言:随着能源需求的不断增长和环境污染的日益严重,人们对清洁能源的需求与日俱增。
氢能作为一种无污染、高能量密度的清洁能源,被广泛认为是未来的主要能源之一。
而高温气冷堆制氢技术正是一种可以实现高效、低成本生产氢能的新兴技术。
一、高温气冷堆的基本原理高温气冷堆是一种核能反应堆,通过核聚变或核裂变的方式产生高温,而后经由热交换器将热量转化为电能或热能。
其工作原理是通过将氢气从水中释放出来,从而实现制氢的目的。
高温气冷堆的工作温度通常在700°C至950°C之间,这使得气冷堆可以充分利用高温热能,以提高氢气的产量和能量转化效率。
二、高温气冷堆制氢的特点1. 高效能:高温气冷堆能够充分利用高温热能,将水分解为氢气和氧气。
相较于传统的制氢技术,高温气冷堆能够提供更高的制氢效率。
2. 低成本:与传统的电解水法相比,高温气冷堆制氢技术的成本更低,仅需很少的电能来驱动反应堆,降低了制氢过程的能源消耗。
3. 清洁环保:高温气冷堆制氢技术无二氧化碳等污染物的排放,没有二次污染的问题,对环境友好。
4. 应用广泛:高温气冷堆制氢技术不仅可以用于能源生产,还可以应用于工业、交通等领域,推动氢能在多个领域的应用。
三、高温气冷堆制氢的关键技术1. 材料技术:高温气冷堆所面临的高温和辐射环境对核燃料、热交换器和结构材料等提出了更高的要求,需要研发耐高温、辐射性能良好的材料。
2. 燃料循环技术:高温气冷堆一般使用氦气作为冷却剂,因此需要研发高温下的氦气循环系统,以提供足够的冷却能力。
3. 氢气提纯技术:高温气冷堆制氢产生的氢气中通常还包含着其他杂质,比如氮气、水蒸气等,需要通过合适的氢气提纯技术将这些杂质去除,以得到高纯度的氢气。
4. 安全技术:由于高温气冷堆使用核能,需要采取一系列严格的安全措施来确保堆的正常运行和人员的安全防护。
四、高温气冷堆制氢的应用前景高温气冷堆制氢技术在能源产业和其他行业中有着广泛的应用前景。
高温气冷堆特点

高温气冷堆特点高温气冷堆(High-temperature gas-cooled reactor, HTGR)是一种与传统核反应堆设计截然不同的核能技术。
其独特的特点使其在许多领域具有广阔的应用前景。
本文将重点介绍高温气冷堆的特点以及其在能源、环境和工业领域的潜在应用。
1. 高温运行:高温气冷堆具有非常高的工作温度,通常在700度以上。
相比之下,传统的液体冷却堆的工作温度一般在300度左右。
高温操作有助于提高热效率,并且可以为其他工业过程提供高温热能。
例如,高温气冷堆可以用于发电、水热解制氢和其他高温化学过程,进一步推动绿色能源和可持续发展。
2. 安全性:高温气冷堆具有优良的核安全特性。
由于其独特的设计,HTGR可以以天然的方式实现负反馈,即在异常情况下,反应堆的功率会自动降低。
此外,高温气冷堆使用了固体燃料球,这种设计可以防止核燃料的泄漏和融化,并且使堆芯更加稳定和耐用。
3. 资源利用:高温气冷堆可以利用多种燃料形式,包括天然铀、钚等。
同时,它还可以利用废弃核燃料和核废料作为燃料源。
这种资源利用的特点使得高温气冷堆成为核能领域的重要技术,有助于解决核废料处理和核燃料供应的问题。
4. 环境友好:相比传统的液体冷却堆,高温气冷堆具有更低的环境风险。
高温气冷堆使用气体作为冷却介质,不涉及与水相关的安全隐患,减少了核能发电对水资源的依赖。
另外,高温气冷堆的燃料球是固体的,可以防止核燃料的泄漏和废核燃料的再处理。
5. 应用领域的多样性:高温气冷堆具有广泛的应用前景。
其中一个重要领域是发电。
高温气冷堆可以通过直接或间接的方式产生高温蒸汽,驱动涡轮发电机发电。
此外,高温气冷堆还可以为工业过程提供高温热能,如水热解制氢、合成氨和化学工业的过程。
此外,高温气冷堆还可以应用于石油精炼、有色金属冶炼和化工等领域,提供高温热能。
6. 市场潜力:随着对清洁能源的需求逐渐增加,高温气冷堆作为一种可持续发展和环境友好的能源选择,具有广阔的市场潜力。
棉梭织冷堆工艺

棉梭织冷堆工艺全文共四篇示例,供读者参考第一篇示例:棉梭织冷堆工艺是一种传统的手工艺技术,主要用于制作棉织品。
这种工艺在中国已有数千年的历史,至今仍然被许多工匠传承并继续发展。
在这个快速发展的时代,很多传统工艺正在濒临失传,但是棉梭织冷堆工艺因其独特的韵味和文化价值,依然得到了重视和保护。
棉梭织冷堆工艺中最重要的工具就是冷堆梭和织布机。
冷堆梭是一种手工织布工具,形状和大小都与普通梭子不同,它使用起来更加方便和灵活。
在织布的过程中,工匠首先要将纱线穿过冷堆梭,并将其插入织布机的线孔中。
然后,经过精细的操作,工匠就可以开始织布了。
由于冷堆梭的特殊设计,使得织出来的布料更加细腻,质地更加柔软。
棉梭织冷堆工艺的工作流程非常繁琐,需要工匠经过长时间的练习和训练才能掌握。
棉花要经过多道工序进行处理,包括去籽、梳理、纺纱等,最终才能得到织布所需的纱线。
然后,工匠需要根据设计的花样和色彩选择合适的纱线,并将其穿过冷堆梭。
接下来,工匠就要开始在织布机上进行织布,这个过程需要非常耐心和细致的操作,一丝不苟。
在织布的过程中,工匠需要不断调整织布机的速度和张力,确保织出来的布料质地均匀和色彩明亮。
工匠还要不断检查纱线是否有杂质或者断裂,并及时进行处理。
只有通过认真细致的工作,才能织出一方完美的布料。
棉梭织冷堆工艺所制作的布料非常适合用来制作衣服、帷幔、床单等家居用品。
由于其细腻的质地和独特的花样,深受消费者的喜爱。
而且,这种手工织布的工艺也更加环保和健康,不含有任何化学添加剂,对人体没有任何危害。
虽然棉梭织冷堆工艺在现代社会已经被机械化的生产工艺所替代,但是依然有一些工匠坚守传统,坚持手工织布的技艺。
他们认为,传统的手工艺技术不仅仅是一种工作方式,更是一种文化传承和生活方式。
而且,只有通过手工织布,才能真正感受到布料的质地和纹理,更加珍惜身边的物品。
在保护和传承棉梭织冷堆工艺的过程中,我们可以采取一些措施。
应该加强对这种传统手工艺的宣传和推广,让更多人了解并感受到其独特魅力。
高温气冷堆发展前景

高温气冷堆发展前景高温气冷堆发展前景引言:随着社会科技的不断进步和人们对环境问题的关注,清洁能源的需求越来越迫切。
目前,核能作为一种清洁、高效且可靠的能源,备受关注。
高温气冷堆作为核能发电的一种新型技术,具有较好的发展前景。
本文将从发展现状、优势、挑战和前景四个方面进行论述和分析。
一、发展现状:高温气冷堆技术起源于上世纪五十年代,一直在不断完善和发展。
目前,全球多个国家的科研机构和企业都在积极推动高温气冷堆技术的研发。
其中,我国是高温气冷堆技术的重要推动者和参与者,已经取得了丰硕成果。
我国的两个高温气冷堆实验堆平安启动并运行良好,为我国高温气冷堆工程化建设奠定了坚实的基础。
二、优势:1.安全可靠: 高温气冷堆采用固体燃料,燃料偶变系数低,一旦堆芯温度升高,会自动减小功率输出,避免堆芯失控。
2.高效节能: 高温气冷堆在发电过程中,利用高温燃气直接驱动燃气轮机发电,提高了能源利用效率。
3.灵活性: 高温气冷堆可以制备多种燃料形式,如硒铜砷铵燃料、铍烯烷燃料等,适应性强。
4.多功能: 高温气冷堆除了发电,还可以利用高温热能进行水裂解、制氢等其他产业应用。
三、挑战:1.技术问题: 高温气冷堆技术相对于传统核能技术相对较新,存在着一系列的技术问题,如材料选型、燃料循环等,需要持续进行研发和改进。
2.经济问题: 高温气冷堆的建设和运行成本相对较高,需要充分考虑经济可行性和市场竞争力。
3.安全问题: 高温气冷堆涉及到核能,核安全一向是重中之重,高温气冷堆安全技术的研发和应用需要更加重视。
四、前景:高温气冷堆发展前景广阔。
首先,高温气冷堆技术可以在解决能源问题的同时,减少温室气体的排放,对于缓解气候变化和保护环境具有重要意义。
其次,高温气冷堆具有极高的供热温度,可以广泛应用于热解、合成氨、制氢等领域,为产业升级和能源转型提供支撑。
再次,高温气冷堆技术在我国得到了政府的大力支持和投入,将成为我国核能发展和能源战略的重要组成部分。
高温气冷堆技术的研发与应用
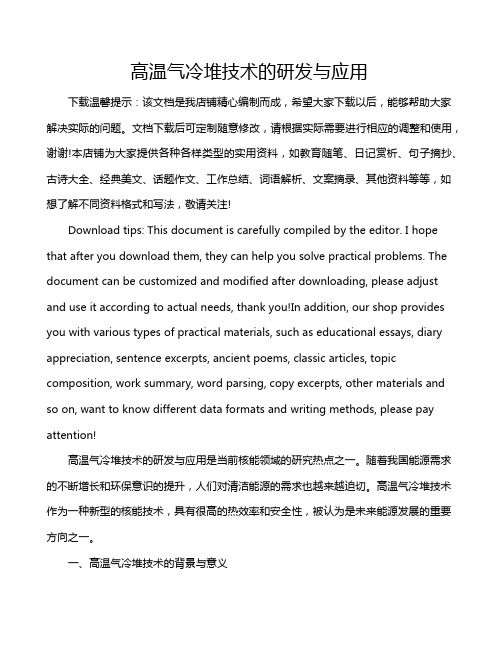
高温气冷堆技术的研发与应用下载温馨提示:该文档是我店铺精心编制而成,希望大家下载以后,能够帮助大家解决实际的问题。
文档下载后可定制随意修改,请根据实际需要进行相应的调整和使用,谢谢!本店铺为大家提供各种各样类型的实用资料,如教育随笔、日记赏析、句子摘抄、古诗大全、经典美文、话题作文、工作总结、词语解析、文案摘录、其他资料等等,如想了解不同资料格式和写法,敬请关注!Download tips: This document is carefully compiled by the editor. I hope that after you download them, they can help you solve practical problems. The document can be customized and modified after downloading, please adjust and use it according to actual needs, thank you!In addition, our shop provides you with various types of practical materials, such as educational essays, diary appreciation, sentence excerpts, ancient poems, classic articles, topic composition, work summary, word parsing, copy excerpts, other materials and so on, want to know different data formats and writing methods, please pay attention!高温气冷堆技术的研发与应用是当前核能领域的研究热点之一。
高温气冷堆优缺点
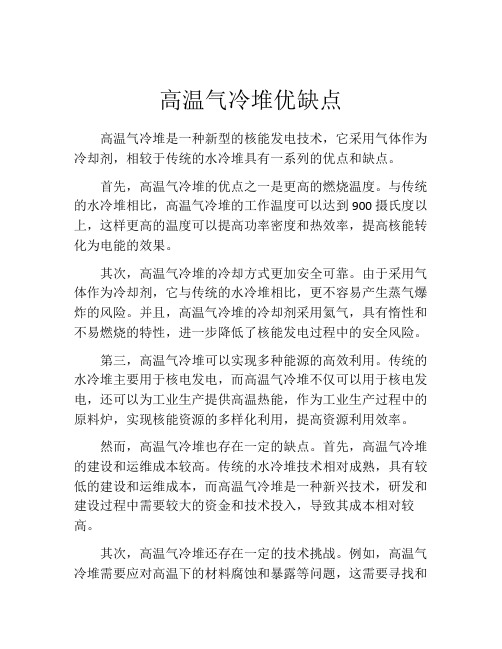
高温气冷堆优缺点高温气冷堆是一种新型的核能发电技术,它采用气体作为冷却剂,相较于传统的水冷堆具有一系列的优点和缺点。
首先,高温气冷堆的优点之一是更高的燃烧温度。
与传统的水冷堆相比,高温气冷堆的工作温度可以达到900摄氏度以上,这样更高的温度可以提高功率密度和热效率,提高核能转化为电能的效果。
其次,高温气冷堆的冷却方式更加安全可靠。
由于采用气体作为冷却剂,它与传统的水冷堆相比,更不容易产生蒸气爆炸的风险。
并且,高温气冷堆的冷却剂采用氦气,具有惰性和不易燃烧的特性,进一步降低了核能发电过程中的安全风险。
第三,高温气冷堆可以实现多种能源的高效利用。
传统的水冷堆主要用于核电发电,而高温气冷堆不仅可以用于核电发电,还可以为工业生产提供高温热能,作为工业生产过程中的原料炉,实现核能资源的多样化利用,提高资源利用效率。
然而,高温气冷堆也存在一定的缺点。
首先,高温气冷堆的建设和运维成本较高。
传统的水冷堆技术相对成熟,具有较低的建设和运维成本,而高温气冷堆是一种新兴技术,研发和建设过程中需要较大的资金和技术投入,导致其成本相对较高。
其次,高温气冷堆还存在一定的技术挑战。
例如,高温气冷堆需要应对高温下的材料腐蚀和暴露等问题,这需要寻找和研发能够在高温环境下长期稳定运行的新材料,提高核电站的寿命和安全性。
此外,高温气冷堆的处理废物的问题也是一个挑战。
由于采用气体冷却,高温气冷堆产生的废物较少,但其中包含的核废品必须进行安全处理和储存,以防止对环境造成污染和危害。
综上所述,高温气冷堆作为一种新型的核能发电技术,具有更高的燃烧温度、更安全可靠的冷却方式和多种能源的高效利用等一系列优点,但其建设和运维成本较高,存在技术挑战和处理废物的问题。
随着科技的发展和不断的研发投入,相信高温气冷堆技术将不断完善,为人类提供更多高效、安全、可持续发展的能源选择。
高温气冷堆项目核准

高温气冷堆项目核准高温气冷堆项目核准引言高温气冷堆技术是一种新兴的核能发电技术,具有高效率、安全性高、低碳排放等优势。
在当今全球能源转型的背景下,高温气冷堆技术被认为是未来核能行业的重要发展方向。
本文将对高温气冷堆项目核准进行详细探讨。
一、高温气冷堆技术概述高温气冷堆技术是指利用核燃料进行热核反应,在高温下产生热能,将热能转化为电能的一种技术。
与传统的核能发电技术相比,高温气冷堆技术具有更高的发电效率,可以达到50%以上,同时还可以利用余热进行热能供应。
此外,高温气冷堆技术不需要水冷却,可以实现气冷运行,减少水资源的消耗,对环境影响更小。
二、高温气冷堆项目的意义1.节能环保高温气冷堆技术采用气冷方式运行,不需要使用大量的水资源进行冷却,减少了对水资源的消耗。
与传统的水冷却堆相比,高温气冷堆可以显著减少对水资源的需求,从而节约水资源。
此外,高温气冷堆技术还能通过余热回收利用,提供热能供应,实现能源的高效利用。
2.增强电力供应能力高温气冷堆技术具有较高的发电效率,可以实现50%以上的高效率发电。
采用高温气冷堆技术建设核电项目,能够提高发电效率,增强电力供应能力,满足日益增长的能源需求。
3.促进能源结构优化升级高温气冷堆技术具有清洁、低碳的特点,是实现能源结构优化升级的一种重要方向。
通过发展高温气冷堆项目,可以减少对传统化石能源的依赖,降低碳排放,推进能源结构向清洁能源和新能源的转型,促进可持续发展。
三、高温气冷堆项目核准的必要性1.发展新能源随着全球能源消耗的不断增长,传统能源的储量逐渐减少,新能源的开发和利用变得尤为重要。
高温气冷堆技术作为一种新兴的能源技术,具有广阔的发展前景。
核准高温气冷堆项目有利于推动新能源的发展,减少对传统能源的依赖,推动能源转型。
2.提高能源供应安全性能源供应安全性是国家经济发展的重要保障。
通过核准高温气冷堆项目,能够增加国家的能源供应能力,提高能源供应的稳定性和可靠性,为国家经济发展提供坚实的能源保障。
- 1、下载文档前请自行甄别文档内容的完整性,平台不提供额外的编辑、内容补充、找答案等附加服务。
- 2、"仅部分预览"的文档,不可在线预览部分如存在完整性等问题,可反馈申请退款(可完整预览的文档不适用该条件!)。
- 3、如文档侵犯您的权益,请联系客服反馈,我们会尽快为您处理(人工客服工作时间:9:00-18:30)。
核心提示:对棉织物冷轧堆染色时染料用染、碱剂用量、被染半成品的温度、导布张力、浸轧染液用水、堆置时间等工艺条件进行了分析,并对H型活性染料冷轧堆染色工艺进行了实验,分析了M型活性染料冷轧堆染色碱剂浓度、食盐浓度、堆置时间、堆置温度等工艺条件对织物固色率的影响。
控制好冷轧堆染色的工艺,对于纯棉织物,固色率可达90%左右。
随着世界能源日趋紧张,冷轧堆染色技术正逐步推行。
冷轧堆染色工艺介于浸染工艺和连续轧染工艺之间,是一种半连续化轧染工艺。
冷轧堆染色是一种低能耗,对环境污染小、高效率、短流程的工艺,具有生产效率高、准备周期短、重演性好、固色率高及染料渗透性极佳等优点。
近年来国内外越来越多的企业应用冷轧堆染色工艺进行纺织印染生产,取得了较好的经济效益。
然而,在实施冷轧堆工艺的过程中仍存在一些问题。
1冷轧堆染色工艺条件
1.1冷轧堆染色对染料的要求
冷轧堆的染色机理分吸附、扩散、固着三个阶段。
冷轧堆是在不加热的情况下,通过浸轧染液使纤维素膨胀,从而使染料分子转移到纤维内部,所以要求染料的扩散性良好、对纤维的亲和力以及直接性要低,保证织物的匀染,有利于克服头梢色差现象。
乙烯砜型活性染料具有比较适中的反应性。
在染色过程中,控制乙烯砜的形成,使染料有充分的时间扩散到纤维内部,以获得较好的匀染、透染效果。
所以乙烯砜染料很适合冷轧堆染色。
1.2冷轧堆染色对碱剂的要求
染料与纤维的反应速率不仅取决于染料的反应性大小,也取决于碱剂的强度,不同种类的染料所选用的碱剂也不同。
冷轧堆染色固色方法有纯烧碱法、烧碱一纯烧碱法、烧碱一磷酸三钠法、烧碱一水玻璃法四种。
采用硅酸钠与烧碱的混合液为冷轧堆染色工艺的碱液,这种碱液可得到最佳得色量。
烧碱保证了冷轧堆的碱性而硅酸钠则可作为缓冲剂。
1.3冷轧堆染色对被染半成品的温度要求
前处理加工的半制品,温度不均是产生头尾色差和左、中、右色差的原因之一。
在冷轧堆染色工艺中,布身温度过高染料水解加剧;布身含湿不均,浸轧后导致带液浓度不均,形成色差。
因此,半制品在浸轧前一定要将湿度调均匀,将温度降到30℃以下。
对温度的控制是冷轧堆染色成功的关键。
一般冷轧堆染色工艺温度控制在20~30℃之间。
1.4冷轧堆染色对导布张力的要求
浸轧织物的张力变化导致织物渗透带液不均,形成织物色泽的波动。
因此在染色过程中应避免发生“压布”,大卷恒张力退布,使进布张力发生较小波动。
1.5冷轧堆染色对浸轧染液的用水要求
轧液一定要用软水,因为硬水会使硅酸钠形成不溶物,粘在辊筒上,辊筒表面在烘干后不可避免地会形成一层硅酸钠薄膜,所以辊筒表面常常用冷水冲洗。
1.6冷轧堆染色对堆置时间的要求
堆置的时间视染料的性能和堆置的温度来决定,少则24h,多则24h以上。
布卷堆置保持4~6r/min的速度不停地转动,以防布卷久置不动,染液下沉,导致布卷深浅不均。
1.7恒线速度恒张力收卷
冷轧堆染色工艺过程中较长时间是进行堆置渗透、上染、固色反应。
因此,合理、可靠的控制恒线速度、恒张力收卷极为重要,以确保织物带液均匀,防止缝头瑕疵。
2M型活性染料冷轧堆染色工艺实例
M型活性染料是由乙烯砜和一氯均三嗪构成的双活性基染料,可以克服活性基染料固色率低和染深色时易产生色差等缺点。
由于两活性基团具有可补性,使该染料既耐酸又耐碱,给色深度可以达到直接染料水平而牢度明显优于直接染料。
2.1M型活性染料冷轧堆染色工艺流程
2.1.1织物规格
29.5texX29.5tex236根/10cm×236根/10cm棉平布
19.5tex×19.5tex236根/10cm×251根/10cm人造棉平布
46.1texX35.4tex251.4根/10cm×503.2根/10cm棉灯芯绒
28texX20tex200.5根/10cm×228根/10cm苎麻/棉(50,50)平布
36tex29.5rex173根/10cm×527根/10cm人造棉/棉(50/50)灯芯绒
2.1.2主要药品
染料活性黄M一3RE活性红M一3BE活性深
蓝M一2GE
工业NaOH(30波美度)
工业硅酸钠(40波美度)
2.1.3工艺处方
染料5~40g/L
NaOH(100%)5~10g/L
水玻璃(40波美度)50—70geL
食盐40—5OL
尿素50g/L
TX一10+松油(1:1)1mL/L
2.1.4工艺流程和条件
浸轧染液(带液率70%一80%)一堆置(30℃,10一12小时)一冷水洗皂煮(肥皂5g/L,95℃,1分钟)一热水洗冷水洗一烘干
2.2实验结果与讨论
2.2.1冷轧堆染色织物的色牢度
活性深蓝M一2GE(owf)0.3%、活性红M一3BE(ow1)0.3%、活性黄M一3RE(oWf)O.4%。
M型活性染料既耐酸又耐碱,染料与纤维共价键结合后,具有很高的耐洗色牢度。
由表1可以看出M型活性染料红黄蓝拼成的染液上染织物的耐洗色牢度都在3~4级及以上,耐摩擦牢度能达3级以上,满足一般染色产品的色牢度要求。
2.2.2碱剂浓度对织物固色率的影响
活性红M一3BE(owf)2.oo%
由表2可知采用烧碱与水玻璃混合碱剂,一方面保证染液有足够高pH值,使活性染料固色反应有足够快的速率;另一方面,由于水玻璃的缓冲作用,使染液pH相对稳定,提高了匀染效果。
水玻璃用量大,缓冲能力大,固色率也增大。
但水玻璃浓度过大,会增大染液粘度反而会降低固色率。
因此,混合碱剂的用量一般可确定为烧碱5~]0g/L,水玻璃50~70g/L。
2.2..3食盐浓度对织物固色率的影响
从表3中可以看出,织物固色率随食盐浓度增大而提高,但达到50g/L后,固色率反而有所下降。
电解质加入可提高纤维内相的pH值,有利于固色反应。
但食盐浓度过高,会使染料发生聚集或沉淀,对上染和固色反应都不利。
因此,食盐用量一般确定为50g/L左右。
2.2.4堆置时间对织物固色率的影响
活性染料与纤维在碱剂作用下发生固色反应的同时,在织物毛细管内染料和在纤维内的染料还会发生一定程度的水解,固色反应基本完成后,如继续延长时间,起固色的染料越来越少,这时,纤维上已结合的染料发生水解。
因此,不适当地延长固色时间,反而使织物的固色率下降。
表4是堆置时间对织物固色率的影响,从表中可以看出,在30℃时用烧碱与硅酸钠混合,固色时间控制在l0小时左右为宜。
2.2.5堆置温度对织物固色率的影响
活性深蓝M一2GE(owf)2.0%从表5中可以看出在相同条件下,30℃、40℃温度的固色率明显高于20℃。
在20℃时,染料的扩散速率相对较慢,固色水解反应的速率也慢,所以要达到较高的固色率,必须延长固色反应时间。
提高温度,固色反应速率加快,但染料水解反应速率也加快而且比固色反应速率提高的更快。
3结语
3.1研究表明,冷轧堆染色时,一般选用反应性适中的乙烯砜型活性染料染色,以获得较好的匀染、透染效果;用硅酸钠与烧碱的混合液为染色工艺的碱液,可以得到最佳得色量;为了防止产生色差,要将被染半成品的温度降到30℃以下;控制好导布的张力,减小色泽的波动;浸轧过程中,轧液要使用软水;根据染料的性能和堆置的温度来制定适宜的堆置时间,防止布卷深浅不均;控制好轧液率、选用小容量的浸轧槽,以避免产生头尾色差。
3.2实验证明,活性染料能适用于各种纤维素纤维织物的冷轧堆染色。
通过以上实验可知,控制好冷轧堆染色的工艺,对于纯棉织物,固色率可达90%左右;对于棉、麻棉混纺织物,固色率达70%左右。
织物耐洗色牢度达3~4级,摩擦牢度也可达到3级以上。
参考文献
1.陈立秋.冷轧堆染色清洁生产的工艺条件.[J].印染,2004(13)
2.王水武.活性染料冷轧堆染色工艺[J].印染,2006(7):33~35.
3.赵爱国,宫成民,李付杰,刘成林,孙玉莲,纯棉织物新型高效活性染料冷轧堆染色工艺探讨.2007立信全国印染行业节能环保年会,常州:中国印染行业协会,2007.10:361363.。