作业准备验证及停工后验证程序(含表格)
作业准备验证表

生产线
产品名称
触发原因 □停机超过1周以上
类型
序 号1
验证项目
□新产品首次投入生产
验证方法
接收准备
人2
3
1
机2
3
1
料2
3
1
法2
3
1
环231测2 Nhomakorabea3
操作员确认
班组长确认
□材料更换 工序1
验证时间 □工程更改后重新恢复生产
工序2 工序3
处理记录
反应计划
1.验证过程中发生不符合,应立即反馈生产部经理,由生产经理组织检验员、工艺工程师实施改进,; 2.如需采用临时替代措施,应在措施实施前获得生产部经理批准,并按照临时更改流程执行。
1.当出现以下情况时,需由操作员和班组长共同实施作业准备验证,并将验证结果记录在此表单中,其中满足要求
打“√”,不符合打“×”,并将不符合的问题及纠正措施填写在处理记录栏中。
填写说明
1)停机超过1周以上; 2) 新产品首次投入生产;
3) 材料更换;
4)工程更改后重新恢复生产。
表单编号
程更改后重新恢复生产 工序4
工序5
艺工程师实施改进,; 改流程执行。
果记录在此表单中,其中满足要求
IATF16949作业准备验证程序(停工后验证)

按照4.2的内容,各项作业准备的验证项目均无异常后,开始正常生产。
5.相关文件
现场有产品的作业文件:包括工艺流程卡,图纸或者控制计划
挤压首、巡检记录表
检验员
15
做到5S
符合工5S管理程序的要求
不记录
检验员
16
选定检测所需的检具,计量器具,样件
符合检验指导书,图纸,控制计划上的要求
不记录
检验员
17
准备好生产产品的检验文件,例如图纸,控制计划
现场有检验文件:包括图纸或者控制计划
挤压首、巡检记录表
③自然灾害(比如火灾等)后造成生产停工
④公共设施中断(比如停电停水等)后造成生产停工
⑤劳动力短缺后造成生产停工
⑥基础设施的破坏后造成生产停工
4.工作流程及内容
4.1作业准备的内容
审核
批准
日期
-181-
编制部门:质量部
文件名称
作业准备验证程序(停工后验证)
编号:
版次:
版本号:
编制人:
第2页共5页
日期:
-180-
编制部门:质量部
文件名称
作业准备验证程序(停工后验证)
编号:
版次:
版本号:
编制人:
第1页共5页
日期:
1.目的
作业开始前,包括在计划或非计划生产停工期后的作业开始,通过对该作业工位上的人、机、料、法、环、测的检验或测验,来验证作业准备的精确性和准确性。确保作业开始后,能持续生产出合格的产品,避免产生批量的不合格品,预防产生不良的质量成本,确保生产作业的有效性。
检验员
3
转岗人员具备上岗资质
核查人员的培训记录,资质证书
31 作业准备验证程序
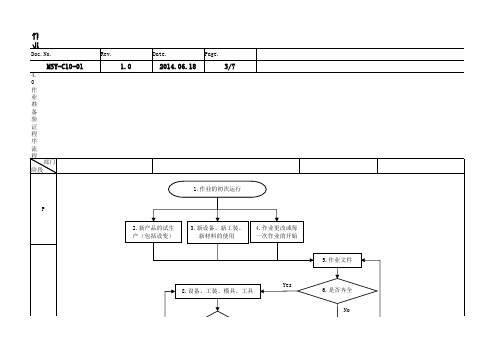
保管年限 2年 2年 2年 2年 2年 2年 2年 2年 2年
备注
关联文件
编号 MSY-R-C10-01-01 MSY-R-C10-01-02 MSY-R-C10-01-03 MSY-R-C10-01-04 MSY-R-C10-01-05 MSY-R-C10-01-06 MSY-R-C10-01-07 MSY-R-C10-01-08 MSY-R-C10-01-09
保管场所
No D/C 18.是否 到位并 有能力 Yes 20.工作环境 16.继续准备
No 19.培训
21.是否符 合5S要求
Yes
No 22.整改 23.调整设备参数,小 批试运行 C
B
C
作业准备验证程序
Doc.No. Rev. Date. Page.
MSY-C10-01
4.0 作业准备验证程序流程 部门 阶段 B
1.0
2014.06.18
5/7
Yes 24.是否合格 No
25.调整设备参数
C
26.作业准备完毕 No D/C 生产过程验证有效率 27.生产 28.首 件检验 Yes
29.生产过程验证
30.是否有效 Yes No 31.重新验证生产过程
A
32.正式开始生产
作业准备验证程序
Doc.No. Rev. Date. Page.
作业前的准备
5~26
作业准备
1 作业前各相关部门需要准备的工作: a ****检查本次生产所需的作业文件是否齐全,若不全,则需补充 和完善,全部作业文件齐全后,发至相关部门; b ****要检查本次生产所需的设备、工装、模具、工具是否齐全完好, 若有问题,则需继续准备,直至全部设备、工装、模具、工具齐全完好; c *****检查本次生产所需的材料是否备齐,若没有备齐,则需继续 准备,直至全部材料备齐; d ****检查本次生产所需的检测设备是否齐全并校准,若 没有齐全或没有校准,则需继续准备,直至全部检测设备齐全并校准; 作业前的准备 e ****检查本次生产所需的人员是否是否到位并有能力,若没有 到位,则需及时补充人员;若人员能力不足,则需对能力不足的 人员进行专门的培训,直至所有人员全部到位并具有相应的能力; f *****检查工作环境是否符合5S标准要求,若不符合5S标准要求, 则需及时进行整改,直至完全符合5S标准的要求; g 调整设备参数,*****试运行:*****首先要在正式作业前调整设 备参数,然后****试运行,检查产品是否符合规定要求,若不符合规 定的要求,则需继续调整设备参数,直至产品完全符合规定的要求,作业 准备完毕。 1 ****作业准备完毕后,开始首件生产,在生产过程中, ****要对生产过程中的检测项目和最终产品的检测项目 进行检验,若检测结果不符合规定的要求,则需调整, 或采取其它措施,直至全部检测项目完全符合规定的要求。
作业准备验证程序(含表格)

作业准备的验证程序
(IATF16949-2016)
1.目的
对公司生产前工序作业准备规定必要的验证手段,保证生产可以正常、有效进行。
2.范围
适用于本公司产品生产前的作业准备。
3.职责
3.1 品质部负责制定验证记录表的相关内容。
3.2 车间班组长负责填写《作业准备验证记录》。
4.程序及要求
4.1在作业的初步运行、材料的改变、作业更改、运行间过长的停顿、变换产品生产/加工等情况下,均须进行作业准备验证,并记录于“作业准备验证记录表”中。
如验证结果不符合生产所要求,则由相关生产车间进行处理。
4.2每个工作班,工装、设备调整后生产的首件产品,按《产品监视和测量控制程序》执行首件检验。
作业准备产生的不合格品,按《不合格品控制程序》执行。
4.3新产品、过程更改,进行试生产后进行PPAP及生产确认试验,按APQP、PPAP 要求执行。
4.4 每次进行作业准备验证,都必须由验证人员认真填写《作业准备验证记录》,由生产部保存。
5.相关文件
监测资源控制规范
产品和服务放行控制规范
不合格控制规范APQP、PPAP 6.相关记录
6.1《作业准备验证记录》
作业准备验证记录
表.xl s。
作业准备验证确认记录表
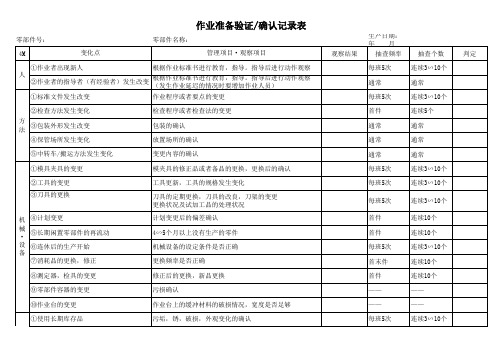
生产日期:
作业准备验证/确认记录表
零部件号:零部件名称:
料
每班5次连续3∽10个首件
连续3个通常
连续3∽10个作业人员管理人员
检验员
修正后进行再次检查④材质变更成形确认(要有初物标识,检查成绩表)1.每班次生产前,生产者和专职生产管理人员进行作业准备验证,确认变化点的状态;将其填入“观察结果”中。
2.当班检验员在首件生产前,对生产车间的作业准备验证工作进行监督,并作出判定。
②修正品的再利用材料实施流程
③让步接收品的流通
1.“观察结果”栏:如发生变化填写○,未发生该变化填写X ,不适用填写N/A 。
2.”判定“栏:确认生产车间对变化点的判定;如发生变化,确认是否采取管理措施及其实施效果的一下下。
符合OK ,不符合NG 。
3.检验员按规定的频次进行抽查,并作好产品检验记录;同时巡回检查影响产品质量的生产因素(4M1E )。
4.发现问题需立即进行改善,然后再次进行作业准备验证;记录留存质检部。
生产停线管理程序(含表格)

生产停线管理程序(IATF16949-2016/ISO9001-2015)1.0目的:为了有效维持公司正常的生产秩序,降低由于零部件缺件、质量问题、生产线设备故障以及工位装配质量等因素对生产的影响,特制订本生产停线管理办法。
2.0适用范围:本制度适用于全公司。
3.0引用文件和标准:《应急计划管理办法》《不合格品控制程序》4.0术语定义:4.1停工定义:a、停线几小时或几个月不等,包括计划性停工及非计划停工;b、停工及复工要求及措施,制造部必须填写复工或停工申请单,相关部门及人员组织评审和风险分析,确定具体对应措施;c、通常停工后的再次开工,必须进行作业准备验证及首末件确认;至于采取其他措施,则由相关部门人员进行风险分析、评审确定(考虑客户要求及法律法规要求)具体措施,记录在开工申请单中;无论如何,最终确保复工后的过程产品满足标准要求;d、设计过程变更及生产过程变更按照变更管理流程要求进行,突发异常按照应急计划管理办法要求进行;5.0职责:5.1制造部、制造部仓储组5.1.1负责正常生产秩序的维护;5.1.2负责整个生产停线的归口管理,以及生产停线指令的下达;5.1.3负责生产线物料配送;5.1.4负责风险物料预警;5.1.5负责对停线责任单位提出考核。
5.2制造部生产车间装配组、热试组5.2.1负责如实记录生产过程中发生的停线;5.2.2负责本单位不能独立完成停线处理时的通知;5.2.3负责跟踪、落实质量问题的处理;5.3质量管理部5.3.1负责零部件到货质量和入库检验把关;5.3.2负责生产现场质量问题停线的责任判定;5.3.3负责提出质量停线临时或永久监控措施。
5.4产品研发部5.4.1负责技术文件的下达;5.4.2负责因零部件、装配等质量问题造成停线时的技术判定;5.4.3负责提出质量停线临时或永久的解决措施。
5.5供应商管理部5.5.1对工艺、设计更改并切换的外协件供给负责;5.5.2对因产能、质量、商务及合作意愿等问题造成供应商不能按时交付或影响生产的零件供给负责;5.5.3负责外协件让步接收归口管理,以及流程提起、跟踪与落实。
工程中途停工验收流程

工程中途停工验收流程一、停工前的准备。
咱工程要中途停工啦,那可得好好准备准备验收的事儿呢。
施工方得先把自己手头的工作捋一捋。
比如说,各种施工资料得整理好吧,像施工日志,这就像咱每天的小日记一样,记录了工程每天的进展、遇到的问题还有解决的办法,这可是很重要的哦。
还有那些工程材料的检验报告,就好比食材的健康证明一样,得保证材料都是合格的。
另外呢,已完成工程的工程量清单也得做出来呀,这就像我们去超市购物后的小票,清楚地写着我们买了啥、花了多少钱一样,让大家都能明白工程做到哪一步,干了多少活。
而且呀,施工场地也得打扫打扫。
不能乱糟糟的就等着验收,就像我们出门见客人之前得把屋子收拾干净一样。
把那些建筑垃圾清理一下,工具摆放整齐,这样验收人员一进来,看着就舒服,心情好了,验收说不定也能更顺利呢。
二、通知相关方。
这时候啊,施工方就要通知甲方啦,就像跟自己的合作伙伴说一声:“咱这工程要停工验收啦。
”通知得详细一点,告诉甲方什么时候停工,停工的原因是什么。
要是因为一些特殊情况,像天气不好或者资金暂时有困难之类的,也都坦诚地说出来。
除了甲方,监理方也得通知到呢。
监理方就像工程的小管家一样,监督着工程的每一个环节。
他们可是很重要的角色,所以得提前告诉他们验收的事儿,让他们也有时间准备准备,好来看看工程做得咋样。
三、验收流程。
1. 外观检查。
验收人员一到现场,首先映入眼帘的就是工程的外观啦。
比如说建筑工程,房子的外立面有没有裂缝啊,墙面是不是平整呀。
如果是道路工程,路面有没有坑洼之类的。
这就像我们看一个人,先看他的外表一样。
如果外观就有很多问题,那肯定会让人心里有点小担忧的。
2. 质量检查。
接下来就是重点的质量检查啦。
这可不能马虎,对于工程来说,质量就是生命啊。
比如建筑的结构是否稳固,混凝土的强度够不够,钢筋的布置符不符合标准。
要是质量不过关,那可就像建在沙子上的城堡,随时可能出问题呢。
验收人员会拿着各种专业的工具,像检测混凝土强度的回弹仪之类的,来检测工程的质量。
作业准备验证要求点检表(TS16949要求)
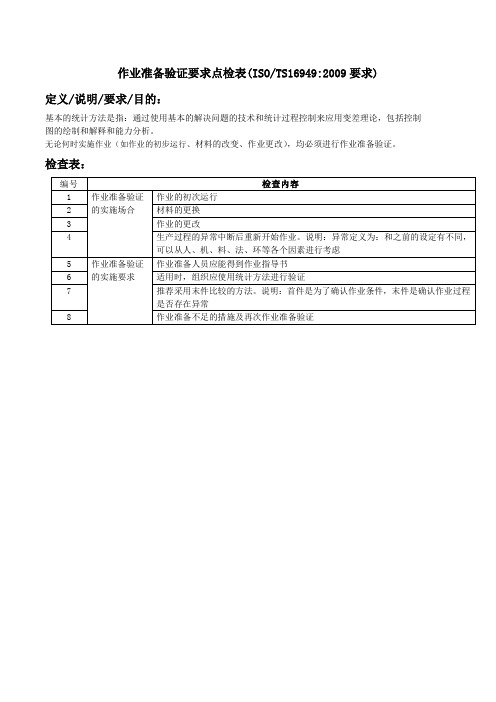
定义/说明/要求/目的:
基本的统计方法是指:通过使用基本的解决问题的技术和统计过程控制来应用变差理论,包括控制图的绘制和解释和能力分析。
无论何时实施作业(如作业的初步运行、材料的改变、作业更改),均必须进行作业准备验证。
检查表:
编号
检查内容
1
作业准备验证的实施场合
作业的初次运行
2
材料的更换
3
作业的更改
4
生产过程的异常中断后重新开始作业。说明:异常定义为:和之前的设定有不同,可以从人、机、料、法、环等各个因素进行考虑
5
作业准备验证的实施要求作业 Nhomakorabea备人员应能得到作业指导书
6
适用时,组织应使用统计方法进行验证
7
推荐采用末件比较的方法。说明:首件是为了确认作业条件,末件是确认作业过程是否存在异常
8
作业准备不足的措施及再次作业准备验证
作业准备停工后验证记录表

□OK □NO □是 □不是
7
检验标准/ 检验规程
检验标准/检验规程是否已准备OK? 并且在生产现场是否易于得到?
□OK □NO □是 □不是
8 作业指导书
作业指导书是否已准备OK? 并且在软骨头现场是否易于得到?
□OK □NO □是 □不是
9 控制计划
控制计划是否已准备OK? 并且在软骨头现场是否易于得到?
□OK □NO □是 □不是
10
原材料
原材料是否已全部到位?
□是 □不是
11 铺助材料
铺助材料是否已全部到位?
□是 □不是
12 首件检验
是否需做首件检验?
□需要 □不需要
13 自主检验
是否需做自主检验?
□需要 □不需要
14 巡回检验
是否需做巡回检验?
□需要 □不需要
15 完工检验
是否需做完工检验?
□需要 □不需要
产品名称是否正确?
□正确 □不正确
2 产品编号
产品编号是否正确?
□正确 □不正确
3 产品规格/型号
产品规格/型号是否正确?
□正确 □不正确
4 生产作业人员
是否具备上岗资格?
□具备 □不具备
5 顾客名称
顾客名称是否正确?
□正确 □不正确
6 工艺文件
工艺文件是否已准备OK? 并且在生产现场是否易于得到?
是否需作X-R控制图? 是否需作过程能力分析?
□正常 □不正常 □有 □没有
□OK □NO □有 □没有 □正常 □不正常
□OK □NO □正常 □不正常
□OK □NO □正常 □不正常 □有 □没有
□需要 □不需要 □需要 □不需要
作业准备验证
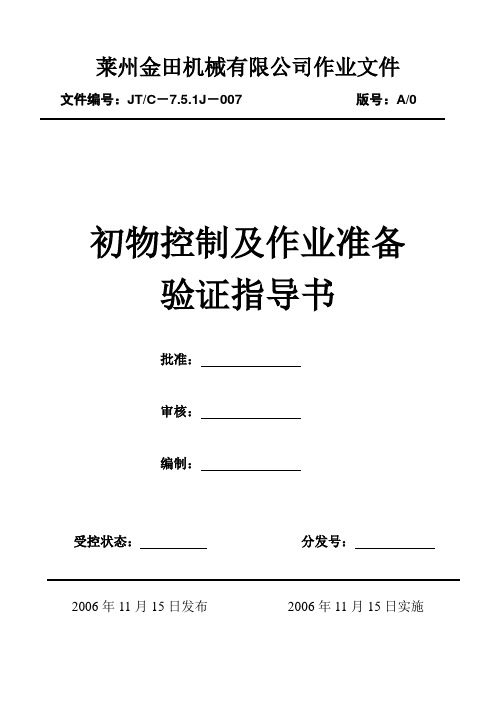
莱州金田机械有限公司作业文件文件编号:JT/C-7.5.1J-007 版号:A/0初物控制及作业准备验证指导书批准:审核:编制:受控状态:分发号:2006年11月15日发布2006年11月15日实施初物管理及作业准备验证指导书JT/C-7.5.1J-0071 目的进行初物管理和作业准备验证,维持适当的品质目标,保证生产可以正常、有效进行。
2 范围适用于本公司产品生产前初物管理和作业准备。
3 引用术语和定义4 职责4.1 生产科负责指导车间实施的初物管理和作业准备验证;负责初物品数量、包4.2 技术科负责组织设计变更初物样件(含小批阶段初物样件)、初物样件的后序加工及装配、可否转量产进行确认和判定;负责对组织自主管理初物《自主管理初物联络书》进行确认、回答、提示。
4.3 品管办(量产后)负责供方品质改善初物的提出和推进。
4.4 检验科负责初物样件的检验和外协初物的进货检验。
4.5 各车间负责对小批阶段初物进行后序加工及装配确认。
4.6 供方负责初物的验证、生产、管理、发放,并做好相应的记录。
负责自主管理初物样件的验证、确认及可否转量产判定。
5 初物控制工作流程5.1 设计变更流程初物管理流程见附录A;5.2 品质改善初物管理管理流程见附录B;5.3 自主管理初物管理流程见附录C。
5.4 转入量产后的工程品质管理5.4.1 供方对量产过渡后的工艺,原则上对品质的适合性进行一个月的重点监督,但供方的品质保证负责人可以根据判断调整监督时间。
5.4.2 对量产后的管理,供方如收到公司技术部门指定事项时,应实施其指定事项。
5.5 初物管理单编号方法5.5.1外协初物管理单编号方法:公司+厂家代码+初物发生日期。
例如:某供方代码为A1,提供初物品时间为2007年7月15日,则初物管理单编号应为:JT-A1-070115。
6 作业准备验证6.1 初物管理的适当时机,应进行作业准备验证:1)设计变更时――新设计变更时;――无互换设计变更时;――有呼唤设计变更时。
IATF16949作业准备验证及停工后验证规定
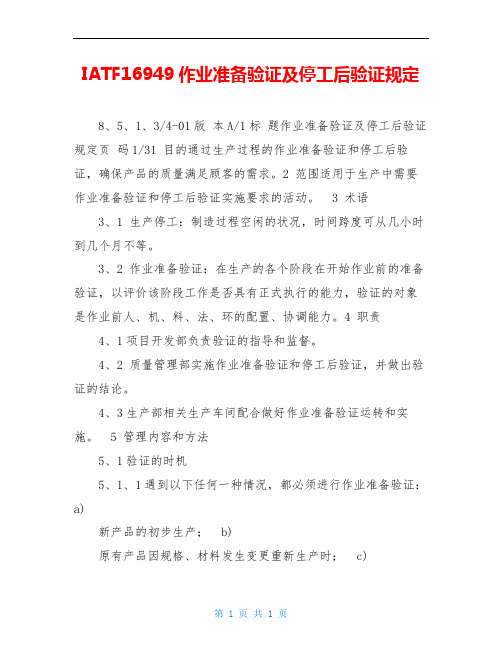
IATF16949作业准备验证及停工后验证规定8、5、1、3/4-01版本A/1标题作业准备验证及停工后验证规定页码1/31 目的通过生产过程的作业准备验证和停工后验证,确保产品的质量满足顾客的需求。
2 范围适用于生产中需要作业准备验证和停工后验证实施要求的活动。
3 术语3、1 生产停工:制造过程空闲的状况,时间跨度可从几小时到几个月不等。
3、2 作业准备验证:在生产的各个阶段在开始作业前的准备验证,以评价该阶段工作是否具有正式执行的能力,验证的对象是作业前人、机、料、法、环的配置、协调能力。
4 职责4、1项目开发部负责验证的指导和监督。
4、2 质量管理部实施作业准备验证和停工后验证,并做出验证的结论。
4、3生产部相关生产车间配合做好作业准备验证运转和实施。
5 管理内容和方法5、1验证的时机5、1、1遇到以下任何一种情况,都必须进行作业准备验证:a)新产品的初步生产;b)原有产品因规格、材料发生变更重新生产时;c)作业更改,如作业方式、设备、模具、工装等变更后,首次生产时;d)发生过程的临时变更时。
5、1、2 同一产品生产计划或非计划停工后,又重新恢复生产,必须进行验证后才能正式生产。
5、2 验证的方法5、2、1评审法按照规定的《作业准备/停工后验证记录》的检查项目,对作业准备进行评审,即是否使用了正确的作业指导书、控制计划、检验标准,以及机器设备参数设置是否按照作业指导书的要求设置。
当评审结果符合规定要求时,得到项目开发部批准后,才能正式开始生产。
5、2、2首、末件比较法用本批生产的首件和前一批生产的末件进行比较,当本批首件的质量达到或超出前一批末件的质量水平时,才能正式开始生产。
本批生产的首件和末件进行比较,当本批末件的质淅川县林吉特精密科技有限公司文件编号LJT-GL/8、5、1、3/4-01版本A/1标题作业准备验证及停工后验证规定页码2/3量达到或超出首件,才能进行下一班的生产。
5、2、3 适当时,也使用统计方法进行验证。
生产作业准备验证记录表
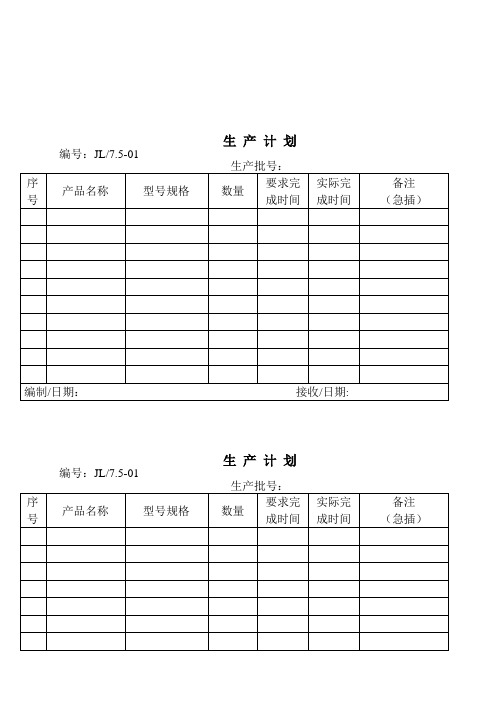
生产计划编号:JL/7.5-01
生产计划编号:JL/7.5-01
JL/7.5.1-11 生产计划更改单
JL/7.5.1-11 生产计划更改单
年月日
JL/7.5.1-02 生产作业准备验证记录№:
L/7.5.1-02 生产作业准备验证记录№:
□初次鉴定 □周期鉴定
□工艺变更鉴定
过程确认记录
编号: JL/7.5.1-03序号:
注:确认合格用“√”表示;确认不合格用“×”表示;具体情况要详细记录右栏内。
JL/7.5.1-04 应急计划实施情况记录№:
记录:审核:
JL/7.5.1-04 应急计划实施情况记录№:
记录:审核:
JL/7.5.1-05 发货单(参考)
JL/7.5.1-05 发货单(参考)
JL/7.5.1-06 工艺参数监控记录()
JL/7.5.1-07 工序流转卡
发料/日期: 批准/日期:
JL/7.5.1-07 工序流转卡
产品名称: 图号: 投产批量: 投产日期:
发料/日期: 批准/日期:
\JL/7.5.1-08 车间生产统计表(日)
\JL/7.5.1-08 车间生产统计表(日)
\JL/7.5.1-08 车间生产统计表(日)
JL/7.5.1-09 产成品统计表( 月)
JL/7.5.1-09 产成品统计表( 月)。
IATF16949作业准备验证程序(停工后验证)

审核
批准
日期
-182-
编制部门:质量部
文件名称
作业准备验证程序(停工后验证)
编号:
版次:
版本号:
编制人:
第3页共5页
日期:
4.2作业准备的验证
序号
作业准备的验证项目
验证方法
验证记录
验证人员
1
人员配备齐全
符合工艺操作规程规定的人数
不记录
检验员
2
新进人员具备上岗资质
核查人员的培训记录,资质证书
不记录
检验员
3
转岗人员具备上岗资质
核查人员的培训记录,资质证书
不记录
检验员
4
人员佩戴好劳防用品
符合工艺操作规程上规定的劳防用品
不记录
检验员
5
选定生产的设备
符合工艺操作规程或控制计划上规定的设备
不记录
检验员
6
开机后设定设备上的工艺运行参数
核查设备上的工艺运行参数
挤压首、巡检记录表
检验员
7
对设备进行点检
核查有无设备点检记录
现场有产品的作业文件:包括工艺流程卡,图纸或者控制计划
挤压首、巡检记录表
检验员
15
做到5S
符合工5S管理程序的要求
不记录
检验员
16
选定检测所需的检具,计量器具,样件
符合检验指导书,图纸,控制计划上的要求
不记录
检验员
17
准备好生产产品的检验文件,例如图纸,控制计划
现场有检验文件:包括图纸或者控制计划
挤压首、巡检记录表
序号
作业准备的项目
作业准备的要求
责任人
1
生产作业准备验证记录表

生产作业准备验证记录表1. 编写目的本文档旨在记录生产作业准备过程中的验证步骤和相关数据,以确保产品质量和生产过程的合规性。
2. 适用范围本文档适用于所有需要进行生产作业准备的工作环境和操作人员。
3. 定义3.1 生产作业准备生产作业准备是指在生产过程开始之前,进行必要的前期准备工作,包括设备检查、物料准备、清洁操作区域等。
3.2 验证验证是指通过一系列的测试和确认,确保所进行的工作和行动符合特定的要求,如产品质量标准、工艺流程等。
3.3 记录表记录表是记录和汇总相关信息的表格或文件,常用于收集、报告和审查工作过程和结果。
4. 验证步骤4.1 设备验证•检查生产设备是否完好,并确保设备符合使用要求。
•检查设备的日常维护记录,确认设备已按要求进行维护。
•运行设备,通过观察和检测,确认设备运行正常。
4.2 物料验证•核对物料清单,确保所有需要使用的物料齐全。
•检查物料的产地和供应商,确保物料来源和质量可靠。
•进行物料验收,包括外观检查、数量确认等。
•进行物料抽样,将样品送至质量控制部门进行测试。
•记录物料验收和抽样的结果,包括物料编号、批次号、生产日期等。
4.3 清洁操作区域验证•检查操作区域的卫生情况,确保表面和设备干净无尘。
•检查操作区域的温度和湿度,确保符合生产要求。
•检查操作区域的消毒记录,确认操作区域已按要求进行消毒。
•进行微生物测试,确认操作区域的卫生状况。
5. 验证结果记录以下是本次生产作业准备验证的相关记录:验证步骤验证内容验证结果设备验证设备检查符合要求设备验证设备维护记录齐全设备验证设备运行测试正常运行物料验证物料清单核对齐全物料验证物料来源确认可靠物料验证物料验收无异常物料验证物料抽样抽样结果符合要求清洁操作区域验证卫生情况检查干净无尘清洁操作区域验证温度和湿度检查符合要求清洁操作区域验证消毒记录检查按要求消毒清洁操作区域验证微生物测试合格6. 验证结论本次生产作业准备验证完成后,通过各项验证步骤,确认生产设备完好,物料齐全且质量可靠,操作区域清洁无尘,并且符合卫生要求。
IATF16949作业准备验证及停工后验证程序(含表格)

IATF16949作业准备验证及停工后验证1.0目的通过生产过程的作业准备验证和停工后验证,确保产品的质量满足顾客的需求。
2.0范围适用于生产中需要作业准备验证和停工后验证实施要求的活动。
3.0术语3.1 生产停工:制造过程空闲的状况,时间跨度可从几小时到几个月不等。
3.2 作业准备验证:在生产的各个阶段在开始作业前的准备验证,以评价该阶段工作是否具有正式执行的能力,验证的对象是作业前人、机、料、法、环的配置、协调能力。
4.0职责4.1项目开发部负责验证的指导和监督。
4.2 质量管理部实施作业准备验证和停工后验证,并做出验证的结论。
4.3生产部相关生产车间配合做好作业准备验证运转和实施。
5.0管理内容和方法5.1验证的时机5.1.1遇到以下任何一种情况,都必须进行作业准备验证:a) 新产品的初步生产;b) 原有产品因规格、材料发生变更重新生产时;c) 作业更改,如作业方式、设备、模具、工装等变更后,首次生产时;d) 发生过程的临时变更时。
5.1.2 同一产品生产计划或非计划停工后,又重新恢复生产,必须进行验证后才能正式生产。
5.2 验证的方法5.2.1评审法按照规定的《作业准备/停工后验证记录》的检查项目,对作业准备进行评审,即是否使用了正确的作业指导书、控制计划、检验标准,以及机器设备参数设置是否按照作业指导书的要求设置。
当评审结果符合规定要求时,得到项目开发部批准后,才能正式开始生产。
5.2.2首、末件比较法用本批生产的首件和前一批生产的末件进行比较,当本批首件的质量达到或超出前一批末件的质量水平时,才能正式开始生产。
本批生产的首件和末件进行比较,当本批末件的质量达到或超出首件,才能进行下一班的生产。
5.2.3 适当时,也使用统计方法进行验证。
生产足够的产品以构成SPC所用容量的子组,对产品进行测量,并将结果绘制成控制图表。
如果这些测量结果落在控制限区域的中间1/3范围内,则作业准备可获批准。
作业准备验证规范(含表格)

作业准备验证规范(含表格)
作业准备验证规范
(ISO9001-2015)
1.目的:
进行必要的作业准备验证,以确保生产过程的稳定。
2.适用范围:
适用于生产过程对作业的初步运行、运行间过长的停顿的作业准备验证的有效控制。
3.定义:
3.1作业的初步运行——每天/每班批量生产、材料或生产品种更换后、工艺更改后、或设备故障排除后的第一次作业运行。
4.职责:
4.1生产部是作业准备验证的归口部门。
4.2其他部门是配合部门。
5.工作程序:
5.1生产部对作业的初步运行,以及运行时间过长的停顿(12个月以上),均应进行作业准备验证。
5.2相关作业人员均需要通过培训合格后才能上岗操作。
5.3作业准备验证的内容:
5.3.1凡是用作试模、校模的生产件一律做好标识,或用规定的容器,或放于
指定的区域,防止不合格品流入生产件中;只有通过检验员验证认可以后,才能作为合格的生产件流入下一道工序。
5.4由生产部、质保部相关人员进行作业准备验证,并做好相关验证记录,只有全部项目达到要求后才能进行正常生产。
6.相关文件
生产管理程序
人力资源管理程序
检验和试验控制程序7.所属记录
设备点检记录卡
设备点检表.d oc
产品首件确认单
产品首检记录表.d
oc 首件确认表.d oc首件检查确认单.d oc
作业准备验证表
作业准备验证记录
表.d oc 作业准备验证记录
表.xl s。
作业准备验证记录表

产品名称:产品图号:工序编号:_ 月__日_ 月__日_ 月__日_ 月__日_ 月__日_ 月__日_ 月__日_ 月__日_ 月__日_ 月__日_ 月__日_ 月__日_ 月__日_ 月__日类别点检方法接受标准__点__分__点__分__点__分__点__分__点__分__点__分__点__分__点__分__点__分__点__分__点__分__点__分__点__分__点__分PPE 1劳保用品佩戴目视符合本工位《PPE规范》人2是否经过培训并具备能力目视对照技能矩阵表(U或O)3检查光电保护有效性目视见点检指导书4检查机器背门是否关闭目视见点检指导书5检查转台是否有异响耳听见点检指导书6检查设备电流目视见工艺参数表7检查设备电压目视见工艺参数表8检查保护气体流量目视见工艺参数表9检查工装目视、手调安装正确、无松动10检查法兰夹紧面目视、手摸定位面洁净、无飞溅11检查挠性节保护罩目视见点检指导书12检查气密堵头目视见点检指导书13导电嘴有无损坏/是否松动目视导电嘴无损坏、无松动料14零件齐全、零件编号目视符合该工序过程检验记录表内的零件明细表法15文件及记录表单是否齐全目视文件及表单明细表16现场5S 目视零件材料整齐现场干净 17现场光线是否充足目视灯光打开、无损坏18检具是否在有效日期内目视合格证在有效期内19各仪表计量器具是否在有效日期内目视合格证在有效期内版本号开班 □换型 □停机 □开班 □换型 □停机 □开班 □换型 □停机 □开班 □换型 □停机 □开班 □换型 □停机 □反应计划处理记录开班 □换型 □停机 □开班 □换型 □停机 □开班 □换型 □停机 □开班 □换型 □停机 □开班 □换型 □停机 □开班 □换型 □停机 □操作者确认机(设备、工装)环测反应计划说明点检时如发现不合格项,应立即通知班长,由班长通知生产主管,生产主管通知相应的负责人改正或临时改正,并在处理记录和反应计划中记录处理情况。
- 1、下载文档前请自行甄别文档内容的完整性,平台不提供额外的编辑、内容补充、找答案等附加服务。
- 2、"仅部分预览"的文档,不可在线预览部分如存在完整性等问题,可反馈申请退款(可完整预览的文档不适用该条件!)。
- 3、如文档侵犯您的权益,请联系客服反馈,我们会尽快为您处理(人工客服工作时间:9:00-18:30)。
作业准备验证及停工后验证程序
(ISO9001-2015/IATF16949-2016)
1.0目的
通过生产过程的作业准备验证和停工后验证,确保产品的质量满足顾客的需求。
2.0范围
适用于生产中需要作业准备验证和停工后验证实施要求的活动。
3.0术语
3.1生产停工:制造过程空闲的状况,时间跨度可从几小时到几个月不等。
3.2作业准备验证:在生产的各个阶段在开始作业前的准备验证,以评价该阶段工作是否具有正式执行的能力,验证的对象是作业前人、机、料、法、环的配置、协调能力。
4.0职责
4.1技术部负责验证的指导和监督。
4.2质量部实施作业准备验证和停工后验证,并做出验证的结论。
4.3生产车间配合做好作业准备验证运转和实施。
5.0管理内容和方法
5.1验证的时机
5.1.1遇到以下任何一种情况,都必须进行作业准备验证:
a) 新产品的初步生产;
b) 原有产品因规格、材料发生变更重新生产时;
c) 作业更改,如作业方式、设备、模具、工装等变更后,首次生产时;
d) 发生过程的临时变更时。
5.1.2同一产品生产计划或非计划停工后,又重新恢复生产,必须进行验证后才能正式生产。
5.2验证的方法
5.2.1评审法
按照规定的《作业准备/停工后验证记录》的检查项目,对作业准备进行评审,即是否使用了正确的作业指导书、控制计划、检验标准,以及机器设备参数设置是否按照作业指导书的要求设置。
当评审结果符合规定要求时,得到技术部批准后,才能正式开始生产。
5.2.2首、末件比较法
用本批生产的首件和前一批生产的末件进行比较,当本批首件的质量达到或超出前一批末件的质量水平时,才能正式开始生产。
本批生产的首件和末件进行比较,当本批末件的质量达到或超出首件,才能进行下一班的生产。
5.2.3适当时,也使用统计方法进行验证。
生产足够的产品以构成SPC所用容量的子组,对产品进行测量,并将结果绘制成控制图表。
如果这些测量结果落在控制限区域的中间1/3范围内,则作业准备可获批准。
5.3验证的实施步骤:
5.3.1技术部在确认上述时机中的任何一项时,必须以书面的形式通知制造部门进行作业准备验证或停工后验证。
5.3.1.1当产品的加工尺寸发生重大变化、加工工艺发生更改时,由技术部发出《工艺文件更改通知单》,通知制造部,操作人员在接到通知后才能生产。
5.3.1.3当产品生产停工后重新恢复生产,由技术部通知车间做好作业准备验证,须重新通过工艺确认。
5.3.2制造部在安排生产计划中注明需要进行作业准备验证的需求。
5.3.3制造部应根据安排的生产时间,提前采用评审法进行自我检查,生产过程的生产条件是否已完全具备,填写《作业准备验证记录表》。
5.3.4进行生产作业准备验证时,生产车间操作人员按照《生产控制计划》工艺参数要求,调试设备和工装,并开始试产首件产品。
5.3.5操作人员按照《生产控制计划》和《作业指导书》要求自检,将认为合格的产品作为首件产品报质量部检验员检验。
5.3.6检验员将本次生产的首件产品与上班生产的末件产品在主要尺寸、外观质量和其它需要测量的项目上进行比较,对产品进行逐项检验,并填写《首件检验记录》。
当确认不合格后操作员应检查设备、工装模具的情况,并重新生产首件,再重复上述过程,不合格品按《不合格品控制程序》执行。
5.3.7经检验合格的首件应放在指定位置,待本班生产任务完成后,操作人员应将认为合格的末件产品报质量部检验员检验。
5.3.7检验员将本次生产的末件产品与当班生产的首件产品在主要尺寸、外观质量和其它需要测量的项目上进行比较,对产品进行逐项检验,并填写《末件检验记录》。
5.3.8末件检验合格,则可以放行该批产品。
如不合格,应对该批产品按不合格品控制程序进行标识。
隔离,并按追溯要求进行挑选。
5.3.8首件随产品流入下道工序。
末件产品应放在指定位置,作为下一班验证的依据。
5.3.9对于量产产品停工后的验证,除按上述5.3.1~5.3.7进行评审检查和首件检验外,还需试生产小批量,进行过程能力分析,确定过程处于受控状态且能力充分时(Cpk≥1.33),方可进行正常量产。
5.4作业准备验证和停工后验证的记录应由质量部保存,并按《记录控制程序》的保存要求执行。
5.5当产品停止生产一年以上重新生产,当顾客有要求时,必须重新提交PPAP,得到顾客认可后方可重新正式生产。
5.6当材料发生变化或需用其他材料代用时,应执行《APQP产品先期质量策划控制程序》中的设计更改流程,并重新通过试生产确认,重新提交PPAP,得到顾客批准后方可正式生产。
6.0引用文件
不合格品控制程序
纠正措施控制程序
APQP产品先期质量策划控制程序
工程变更控制程序
7.0记录表单
作业准备/停工后验证记录
首件检验记录
首件检验记录表
(2).xls
末件检验记录
首末件检验记录表.
xls
作业准备/停工后验证记录
对象:车间班
生产依据
产品名称产品规格/型号生产数量
验证的起因
□新产品的首次量产□换模/换线□开班□材料变更□作业方式/工艺更改□停工№验证项目验证内容验证结果备注
1 产品名称产品名称是否正确?□正确□不正确
2 产品编号产品编号是否正确?□正确□不正确
3 产品规格/型
号
产品规格/型号是否正确?□正确□不正确
4 生产作业人员是否具备上岗资格?□具备□不具备
5 顾客名称顾客名称是否正确?□正确□不正确
6 工艺文件工艺文件是否已准备OK?
并且在生产现场是否易于得到?
□OK□NO
□是□不是
7 检验标准/
检验规程
检验标准/检验规程是否已准备
OK?
并且在生产现场是否易于得到?
□OK□NO
□是□不是
8 作业指导书作业指导书是否已准备OK?
并且在生产现场是否易于得到?
□OK□NO
□是□不是
9 控制计划控制计划是否已准备OK?
并且在生产现场是否易于得到?
□OK□NO
□是□不是
10 原材料原材料是否已全部到位?□是□不是
11 辅助材料辅助材料是否已全部到位?□是□不是
12 首件检验是否需做首件检验?□需要□不需要
13 自主检验是否需做自主检验?□需要□不需要
14 巡回检验是否需做巡回检验?□需要□不需要
15 完工检验是否需做完工检验?□需要□不需要
16 机器设备机器设备是否正常?
是否有作日常预防保养记录?
□正常□不正常
□有□没有
17 检测仪器检测仪器是否到位?
检测仪器是否正常?
是否有作日常预防保养记录?
□OK□NO
□正常□不正常
□有□没有
18 工装夹具工装夹具是否到位?
工装夹具是否正常?□OK□NO
□正常□不正常
19 包装材料包装材料是否到位?
包装材料数量是否正确?
□OK□NO
□正确□不正确
顾客对包装材料是否有特殊要
求?
□有□没有
20 过程能力是否需作Xbar-R控制图?
是否需作过程能力分析?
□需要□不需要
□需要□不需要
验证方法验证结果是否具备条件生产:
□是□否
□首末件对比□控制图
□其它□合格
□不合格,需改进
验证
时机
过程所有者:制造部/车间主任/班组长:作业员:检验员:验证日期:年月日。