机械制造技术基础第五章
机械制造技术基础第5章-1
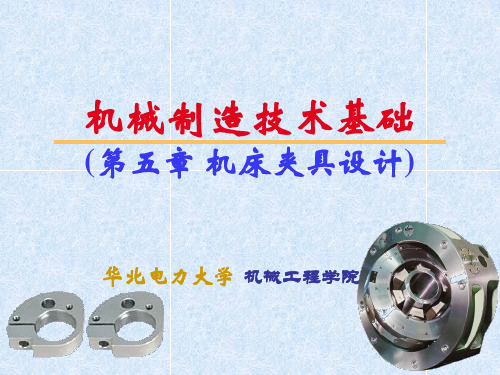
线,安装时首先按找正线找正工件位臵,夹紧工件。
特点:
•精度低;(0.1mm左右) •效率低; •多用于形状复杂、尺寸偏差大
找正线 加工线
的铸、锻件毛坯的粗加工;
•适于单件小批量生产; •不需其它专门设备,通用性好;
flash
毛坯孔
3.利用夹具定位
来实现定位。
联接
原理:通过工件上定位基准和夹具上定位元件接触或配合 特点:
5.2.3 典型的定位方式及定位元件的选择
(2)可调支承
是顶端位置可在一定高度范围内调整的支承。 多用于未加工平面的定位,以调节和补偿各批 毛坯尺寸的误差。一般每批毛坯调整一次。
返回第39页
5.2.3 典型的定位方式及定位元件的选择
(3)自位支承
支承本身的位置在定位过程中,能自动适应工件定位基准面位置变化 的一类支承。 自位支承能增加与工件定位面的接触点数目(但只限制一个自由 度) ,使单位面积压力减小,故多用于刚度不足的毛坯表面或不连续的 平面的定位。
3.过定位与欠定位
欠定位: 按工序的加工要求, 工件应该限制的自由度而未予限 制的定位, 称为欠定位。 绝对不允许出现 过定位: 工件的同一自由度被两个或两个以上的支承点重复 限制的定位, 称为过定位。
过定位一般不允许, 但是在精加工中,为提高定位稳定性和结构刚度,简 化夹具 可用过定位 ;粗加工不允许。
5.2.3 典型的定位方式及定位元件的选择
定位元件的设计应满足下列要求:
⑴要有与工件相适应的精度; ⑵要有足够的刚度,不允许受力后发生变形; ⑶要有耐磨性,以便在使用中保持精度。一般多采用 低碳钢渗碳淬火或中碳钢淬火,硬度为58∼62HRC
5.2.3 典型的定位方式及定位元件的选择
机械制造技术基础第5章-3
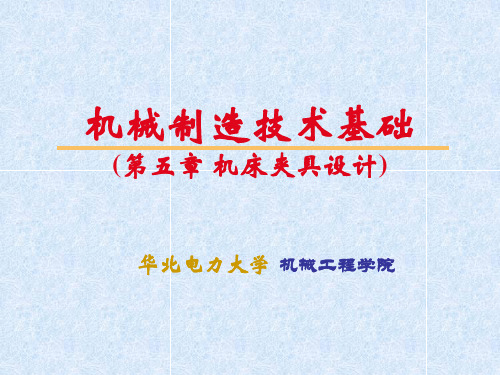
(2)钻模板
作用:用于安装钻套。 类型:固定式、铰链式、分离式和悬挂式等。
固定式钻模板:钻模板直接固定在夹具体上,结构简单, 分离式钻模板:装卸工件方便,精度比铰链式高。
精度较高,但装卸工件困难。
1—钻模板;2—钻套;3—夹紧元件;4—工件
图5-62 分离式钻模板
铰链式钻模板:装卸工件方便,但铰链处存在间隙,故精
1—线圈;2—吸盘;3—隔磁体;4—铁芯;5—导磁体;6—工件;7—夹具体;8—过渡盘 图5-78 电磁卡盘
2.车床夹具设计要点
(1)车床夹具总体结构
夹具的结构应尽量紧凑,重心应尽
量靠近主轴端,一般要求夹具悬伸 不大于夹具轮廓外径。对于弯板式
车床夹具和偏重的车床夹具,应很
好地进行平衡。通常可采用加平衡 块(配重)的方法进行平衡。
当工件定位面较复杂或有其他特殊要求时(例如为了获 得高的定位精度或在大批量生产时要求有较高的生产率), 应设计专用车床夹具。
如图所示为一弯板式车床夹具,用于加工壳体零件的孔和端面。
1—平衡块;2—防护罩;3—钩形压板
图5-76 弯板式车床夹具
返回第40页
如图所示为一种利用夹紧元件均匀变形实现自动定心夹紧 的心轴——液塑心轴。这种心轴有较好的定心精度,但由于 薄壁套扩张量有限,故要求工件定位孔精度在8级以上。
定位键与夹具体配合多采用H7/h6,为了提高夹具的安装精度,定 位键的下部(与工作台T形槽配合部分)可留有余量进行修配,或在 安装夹具时使定位键一侧与工作台T形槽靠紧,以消除间隙的影响。
夹具体
定位键
定位键
(2)对刀装置
对刀装置用以确定夹具相对于刀具的位置。铣床夹具的对刀 装置主要由对刀块和塞尺构成。
机械制造技术基础-第二版---吕明主编---习题答案

机械制造技术基础-第—版--- 吕明主编---习题答案第一章金属切削过程的基础知识一.单项选择1.进给运动通常是机床中()Oa)切削运动中消耗功率最多的:b)切削运动中速度最高的运动;c)不断地把切削层投入切削的运动;d)使工件或刀具进入1E确加工位置的运动。
2•在外圆磨床上磨削工件外圆表面,其上运动是()o a)砂轮的回转运动,b)工件的回转运动,c)砂轮的H线运动,d)工件的直线运动。
3.在立式钻床上钻孔,其上运动和进给运动()o町均山工件来完成:b)均由刀具来完成:c)分别由T•件和刀具來完成;d)分别由刀具和工件來完成。
4.背吃刀量作是指上刀刃与工件切削表面接触长度()。
a)在切削平面的法线方向上测届的值;b)止交平面的法线方向上测量的值;c)在基而上的投影值:d)在上运动及进给运动方向所组成的平面的法线方向上测届的值。
5.在背吃刀暈作和进给屋f 一定的条件卜,切削厚度与切削宽度的比值取决于()oa)刀具询角;b)刀具后角;c)刀具上偏角;d)刀具副偏角。
6.垂直于过渡表面度鼠的切削层尺寸称为()。
a)切削深度,b)切削氏度,c)切削厚度,d)切削宽度。
7.通过切削刃选定点,垂直于上运动方向的平而称为(九a)切削半面,b)进给平面,c)基面,d)主剖面。
&在正交平面内度量的基而与前刀而的夹角为()oa)前角,b)后角,c)主偏角,d)刃倾角.9.刃倾角是上切削刃与()之间的夹角。
a)切削平而,b)基面,c)上运动方向,d)进给方向11.用硬质合金刀具对碳素钢工件进行精加匸时,应选择刀具材料的牌号为()oa) YT30. b) YT5, c) YG3, d) YG8.三.分析1.图1所示为在车床上车孔示意图,试在图中标岀刀具前角、后角、上角、副偏角和刃倾角。
第二章金属切削过程的基本规律及其应用3.靠询刀面处的变形区域称为_______ 变形区,这个变形区上要集中在和前刀面接触的切M底面一薄层金属内。
机械制造技术基础(第2版)第五章课后习题答案

《机械制造技术基础》部分习题参考解答第五章工艺规程设计5-1 什么是工艺过程?什么是工艺规程?答:工艺过程——零件进行加工的过程叫工艺过程;工艺规程——记录合理工艺过程有关内容的文件叫工艺规程,工艺规程是依据科学理论、总结技术人员的实践经验制定出来的。
5-2 试简述工艺规程的设计原则、设计内容及设计步骤。
5-3 拟定工艺路线需完成哪些工作?5-4试简述粗、精基准的选择原则,为什么同一尺长方向上粗基准通常只允许用一次?答:粗、精基准的选择原则详见教材P212-214。
粗基准通常只允许用一次的原因是:粗基准一般是毛面,第一次作为基准加工的表面,第二次再作基准势必会产生不必要的误差。
5-5加工习题5-5图所示零件,其粗、精基准应如何选择(标有 符号的为加工面,其余为非加工面)?习题5-5图a)、b)、c)所示零件要求内外圆同轴,端面与孔轴线垂直,非加工面与加工面间尽可能保持壁厚均匀;习题5-5图d)所示零件毛坯孔已铸出,要求孔加工余量尽可能均匀。
习题5-5图解:按题目要求,粗、精基准选择如下图所示。
5-6为什么机械加工过程一般都要划分为若干阶段进行?答:机械加工过程一般要划分为粗加工阶段、半精加工阶段、精加工阶段和光整加工阶段。
其目的是保证零件加工质量,有利于及早发现毛坯缺陷并得到及时处理,有利于合理使用机床设备。
5-7 试简述按工序集中原则、工序分散原则组织工艺过程的工艺特征,各用于什么场合?5-8什么是加工余量、工序余量和总余量?答:加工余量——毛坯上留作加工用的材料层;工序余量——上道工序和本工序尺寸的差值;总余量——某一表面毛坯与零件设计尺寸之间的差值。
5-9 试分析影响工序余量的因素,为什么在计算本工序加工余量时必须考虑本工序装夹误差和上工序制造公差的影响?5-10习题5-10图所示尺寸链中(图中A0、B0、C0、D0是封闭环),哪些组成环是增环?那些组成环是减环?习题5-10图解:如图a),A0是封闭环,A1, A2, A4, A5, A7, A8是增环,其余均为减环。
机械制造技术基础_重点
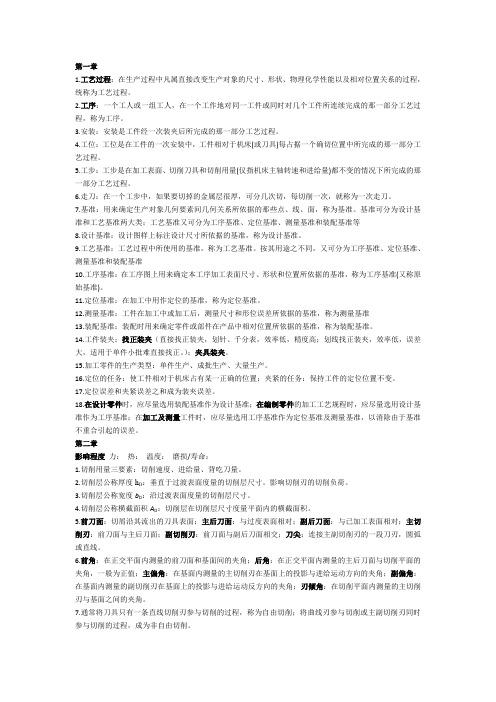
第一章1.工艺过程:在生产过程中凡属直接改变生产对象的尺寸、形状、物理化学性能以及相对位置关系的过程,统称为工艺过程。
2.工序:一个工人或一组工人,在一个工作地对同一工件或同时对几个工件所连续完成的那一部分工艺过程,称为工序。
3.安装:安装是工件经一次装夹后所完成的那一部分工艺过程。
4.工位:工位是在工件的一次安装中,工件相对于机床(或刀具)每占据一个确切位置中所完成的那一部分工艺过程。
5.工步:工步是在加工表面、切削刀具和切削用量(仅指机床主轴转速和进给量)都不变的情况下所完成的那一部分工艺过程。
6.走刀:在一个工步中,如果要切掉的金属层很厚,可分几次切,每切削一次,就称为一次走刀。
7.基准:用来确定生产对象几何要素间几何关系所依据的那些点、线、面,称为基准。
基准可分为设计基准和工艺基准两大类;工艺基准又可分为工序基准、定位基准、测量基准和装配基准等8.设计基准:设计图样上标注设计尺寸所依据的基准,称为设计基准。
9.工艺基准:工艺过程中所使用的基准,称为工艺基准。
按其用途之不同,又可分为工序基准、定位基准、测量基准和装配基准10.工序基准:在工序图上用来确定本工序加工表面尺寸、形状和位置所依据的基准,称为工序基准(又称原始基准)。
11.定位基准:在加工中用作定位的基准,称为定位基准。
12.测量基准:工件在加工中或加工后,测量尺寸和形位误差所依据的基准,称为测量基准13.装配基准:装配时用来确定零件或部件在产品中相对位置所依据的基准,称为装配基准。
14.工件装夹:找正装夹(直接找正装夹,划针、千分表,效率低,精度高;划线找正装夹,效率低,误差大,适用于单件小批难直接找正。
);夹具装夹。
15.加工零件的生产类型:单件生产、成批生产、大量生产。
16.定位的任务:使工件相对于机床占有某一正确的位置;夹紧的任务:保持工件的定位位置不变。
17.定位误差和夹紧误差之和成为装夹误差。
18.在设计零件时,应尽量选用装配基准作为设计基准;在编制零件的加工工艺规程时,应尽量选用设计基准作为工序基准;在加工及测量工件时,应尽量选用工序基准作为定位基准及测量基准,以消除由于基准不重合引起的误差。
机械制造技术基础(第2版)前五章课后习题答案

《机械制造技术基础》部分习题参考解答第一章绪论1-1 什么是生产过程、工艺过程和工艺规程?答:生产过程——从原材料(或半成品)进厂,一直到把成品制造出来的各有关劳动过程的总称为该工厂的过程。
工艺过程——在生产过程中,凡属直接改变生产对象的尺寸、形状、物理化学性能以及相对位置关系的过程。
工艺规程——记录在给定条件下最合理的工艺过程的相关内容、并用来指导生产的文件。
1-2 什么是工序、工位、工步和走刀?试举例说明。
答:工序——一个工人或一组工人,在一个工作地对同一工件或同时对几个工件所连续完成的那一部分工艺过程。
工位——在工件的一次安装中,工件相对于机床(或刀具)每占据一个确切位置中所完成的那一部分工艺过程。
工步——在加工表面、切削刀具和切削用量(仅指机床主轴转速和进给量)都不变的情况下所完成的那一部分工艺过程。
走刀——在一个工步中,如果要切掉的金属层很厚,可分几次切,每切削一次,就称为一次走刀。
比如车削一阶梯轴,在车床上完成的车外圆、端面等为一个工序,其中,n, f, a p不变的为一工步,切削小直径外圆表面因余量较大要分为几次走刀。
1-3 什么是安装?什么是装夹?它们有什么区别?答:安装——工件经一次装夹后所完成的那一部分工艺过程。
装夹——特指工件在机床夹具上的定位和夹紧的过程。
安装包括一次装夹和装夹之后所完成的切削加工的工艺过程;装夹仅指定位和夹紧。
1-4 单件生产、成批生产、大量生产各有哪些工艺特征?答:单件生产零件互换性较差、毛坯制造精度低、加工余量大;采用通用机床、通用夹具和刀具,找正装夹,对工人技术水平要求较高;生产效率低。
大量生产零件互换性好、毛坯精度高、加工余量小;采用高效专用机床、专用夹具和刀具,夹具定位装夹,操作工人技术水平要求不高,生产效率高。
成批生产的毛坯精度、互换性、所以夹具和刀具等介于上述两者之间,机床采用通用机床或者数控机床,生产效率介于两者之间。
1-5 试为某车床厂丝杠生产线确定生产类型,生产条件如下:加工零件:卧式车床丝杠(长为1617mm ,直径为40mm ,丝杠精度等级为8级,材料为Y40Mn );年产量:5000台车床;备品率:5%;废品率:0.5%。
机械制造技术基础第五章习题及答案(机械制造质量分析与控制)

机械制造技术基础第五章习题及答案(机械制造质量分析与控制)《机械制造质量分析与控制》习题⼀.单项选择题1.机床和⼑具达到热平衡前的热变形所引起的加⼯误差属于:()a、常值系统误差b、形位误差c、随机误差d、变值系统误差2. 某⼯序的加⼯尺⼨为正态分布,但分布中⼼与公差中点不重合,则可以认为:()a、⽆随机误差b、⽆常值系统误差c、变值系统误差很⼤d、同时存在常值系统误差和随机误差3. 夹具在机床上的安装误差所引起的加⼯误差属于:()a、常值系统误差b、变值系统误差c、随机误差d、形位误差4. ⼀次性调整误差所引起的加⼯误差属于:()a、随机误差b、常值系统误差c、变值系统误差d、形位误差5. 误差复映所引起的加⼯误差属于:()a、变值系统误差b、常值系统误差c、随机误差d、形位误差6. ⼑具磨损所引起的加⼯误差属于:()a、常值系统误差b、变值系统误差c、随机误差d、形位误差7. 内应⼒引起的变形误差属于:()a、常值系统误差b、形位误差c、变值系统误差d、随机误差8. 定位误差所引起的加⼯误差属于:()a、常值系统误差b、随机误差c、变值系统误差d、形位误差9. 对滚动轴承进⾏适当的预紧,是提⾼主轴系统()的重要措施。
()a、精度b、强度c、刚度d、柔度10.通常⽤()系数表⽰某种加⼯⽅法和加⼯设备胜任零件所要求加⼯精度的程度()a、⼯艺能⼒b、误差复映c、误差传递d、误差敏感11.原理误差所引起的加⼯误差属于:()a、常值系统误差b、随机误差c、形位误差d、变值系统误差12.误差的敏感⽅向指产⽣加⼯误差的⼯艺系统的原始误差处于加⼯表⾯的:()a、切线⽅向b、轴线⽅向c、法线⽅向d、倾斜⽅向13. 受迫振动系统在共振区消振最有效的措施是()。
a、增⼤系统刚度b、增⼤系统阻尼c、增⼤系统质量14. 在车床上进⾏削扁镗杆⾃激振动的切削实验时,若切削条件相同 , 试指出下列各种情况下切削最稳定的场合()a、弱刚度主轴与加⼯表⾯法向的夹⾓450b、弱刚度主轴与加⼯表⾯法向的夹⾓1350c、采⽤直径相同的圆镗杆d、增⼤阻尼15. 削扁镗杆的抗振性⽐圆镗杆好是由于:()a、刚度⾼b、阻尼⼤、消耗振动能量⼤c、系统刚度的组合特性合适⼆.多项选择题1.⽤调整法在车床三⽖卡盘上精镗⼀批薄壁铜套的内孔,各种因素引起的加⼯误差是属于常值系统误差的是:()a、三⽖卡盘的制造和安装误差b、车床主轴的径向跳动c、薄壁铜套的夹紧变形d、机床导轨的⼏何误差e、镗⼑的磨损2.指出下列哪些情况产⽣的误差属于加⼯原理误差:()a、加⼯丝杠时机床丝杠螺距有误差b、⽤模数铣⼑加⼯渐开线齿轮c、⼯件残余应⼒引起的变形d、⽤阿基⽶德滚⼑加⼯渐开线齿轮e、夹具在机床上的安装误差3.机械加⼯中达到尺⼨精度的⽅法有:()a、试切法b、定尺⼨⼑具法c、调整法d、选配法e、⾃动控制法4.⽤调整法在车床三⽖卡盘上精镗⼀批薄壁铜套的内孔,各种因素引起的加⼯误差是属于随机误差的是:()a、镗⼑的磨损b、薄壁铜套的夹紧变形c、三⽖卡盘的制造和安装误差d、机床导轨的⼏何误差e、⼯件外圆形状误差引起的安装误差5. 指出下列哪些⼑具的制造误差会直接影响加⼯精度:()a、外圆车⼑b、齿轮滚⼑c、端⾯车⼑d、铰⼑e、键槽铣⼑6.主轴的纯轴向窜动对哪些加⼯有影响: ()a、车削螺纹b、车削外圆c、车削端⾯d、车削内孔7.影响加⼯精度的主要误差因素可归纳为以下⽅⾯:()a、⼯艺系统的⼏何误差b、⽑坯的制造误差c、⼯艺系统⼒效应产⽣的误差d、⼯艺系统热变形产⽣的误差e、加⼯原理误差8.机械加⼯中获得⼯件形状精度的⽅法有:()a、试切法b、轨迹法c、调整法d、成形法e、展成法三.判断题1.零件表⾯层的加⼯硬化能减⼩表⾯的弹塑性变形,从⽽提⾼了耐磨性,所以表⾯硬化程度越⾼越耐磨。
机械制造技术基础(第2版)课后习题答案

《机械制造技术基础》部分习题参考解答第五章工艺规程设计5-1 什么是工艺过程?什么是工艺规程?答:工艺过程——零件进行加工的过程叫工艺过程;工艺规程——记录合理工艺过程有关内容的文件叫工艺规程,工艺规程是依据科学理论、总结技术人员的实践经验制定出来的。
5-2 试简述工艺规程的设计原则、设计内容及设计步骤。
5-3 拟定工艺路线需完成哪些工作?5-4试简述粗、精基准的选择原则,为什么同一尺长方向上粗基准通常只允许用一次?答:粗、精基准的选择原则详见教材P212-214。
粗基准通常只允许用一次的原因是:粗基准一般是毛面,第一次作为基准加工的表面,第二次再作基准势必会产生不必要的误差。
5-5加工习题5-5图所示零件,其粗、精基准应如何选择(标有 符号的为加工面,其余为非加工面)?习题5-5图a)、b)、c)所示零件要求内外圆同轴,端面与孔轴线垂直,非加工面与加工面间尽可能保持壁厚均匀;习题5-5图d)所示零件毛坯孔已铸出,要求孔加工余量尽可能均匀。
习题5-5图解:按题目要求,粗、精基准选择如下图所示。
5-6为什么机械加工过程一般都要划分为若干阶段进行?答:机械加工过程一般要划分为粗加工阶段、半精加工阶段、精加工阶段和光整加工阶段。
其目的是保证零件加工质量,有利于及早发现毛坯缺陷并得到及时处理,有利于合理使用机床设备。
5-7 试简述按工序集中原则、工序分散原则组织工艺过程的工艺特征,各用于什么场合?5-8什么是加工余量、工序余量和总余量?答:加工余量——毛坯上留作加工用的材料层;工序余量——上道工序和本工序尺寸的差值;总余量——某一表面毛坯与零件设计尺寸之间的差值。
5-9 试分析影响工序余量的因素,为什么在计算本工序加工余量时必须考虑本工序装夹误差和上工序制造公差的影响?5-10习题5-10图所示尺寸链中(图中A0、B0、C0、D0是封闭环),哪些组成环是增环?那些组成环是减环?习题5-10图解:如图a),A0是封闭环,A1, A2, A4, A5, A7, A8是增环,其余均为减环。
《机械制造基础》第5章 机械加工工艺规程的制定

河南科技大学教案首页课程名称机械制造基础任课教师邓效忠第五章机械加工工艺规程的制定计划学时14教学的目的和要求:要求学生掌握定位基准和表面加工方法的选择原则,能够拟定工艺路线,会运用工艺尺寸链确定工序尺寸及其公差,使学生具有编制中等复杂零件加工工艺规程的能力。
重点:工件定位基准的选择;工序顺序的确定;工艺尺寸链及其应用。
难点:工艺尺寸链及其应用。
思考题:1.什么叫基准?基准分哪儿种?2.精、粗定位基准的选择原则各有哪些?如何分析这些原则之间出现的矛盾?3.零件表面加工方法的选择原则是什么?4.制定机械加工工艺规程时,为什么要划分加工阶段?5.切削加工顺序安排的原则是什么?6.什么叫工序集中?什么叫工序分散?各用于什么场合?7.什么叫工序余量?影响工序余量的因素是什么?8.什么叫尺寸链?它具有哪些特征?9.什么叫工艺规程?它有什么作用?10.如何确定尺寸链中的增环、减环和封闭环?第5章机械加工工艺规程设计5.1 概述一、机械加工工艺规程及其作用将产品或零部件的制造工艺过程的所有内容用图、表、文字的形式规定下来的工艺文件汇编称为工艺规程。
二、工艺规程设计所需的原始资料⑴零件图和产品整套装配图;⑵产品的生产纲领和生产类型;⑶产品的质量验收标准;⑷毛坯情况;⑸本厂的生产条件和技术水平;⑹国内外生产技术发展情况。
三、工艺规程设计的步骤⑴零件的工艺性分析。
⑵确定毛坯。
⑶拟定工艺路线,选择定位基准。
⑷确定各工序的设备和工装。
⑸确定主要工序的生产技术要求和质量验收标准。
⑹确定各工序的余量,计算工序尺寸和公差。
⑺确定各工序的切削用量。
⑻确定工时定额。
⑼填写工艺卡。
5.2 机械加工工艺规程设计一、零件的结构工艺性分析结构工艺性是指产品的结构是否满足优质、高产、低成本制造的一种性质。
零件结构工艺性举见教材表5-4。
二、确定毛坯三、定位基准的选择粗基准是指未经机械加工的定位基准,而精基准则是经过机械加工的定位基准。
1.粗基准的选择原则粗基准选择的主要目的是:保证非加工面与加工面的位置关系;保证各加工表面余量的合理分配。
《机械制造技术基础》 教学大纲 及 教案全套

《机械制造技术基础》教学大纲及教案全套第一章:机械制造概述教学目标:1. 了解机械制造的基本概念、分类和特点。
2. 掌握机械制造过程的基本步骤。
3. 熟悉机械制造中的常见问题和解决方案。
教学内容:1. 机械制造的基本概念和分类。
2. 机械制造过程的基本步骤。
3. 机械制造中的常见问题和解决方案。
教学方法:1. 讲授法:讲解机械制造的基本概念、分类和特点。
2. 案例分析法:分析机械制造过程中的实际案例,讨论常见问题和解决方案。
教学资源:1. 教材:《机械制造技术基础》。
2. 课件:机械制造过程的图片和视频。
教学评估:1. 课堂讨论:评估学生对机械制造过程的理解和分析能力。
2. 课后作业:评估学生对机械制造基本概念和步骤的掌握程度。
第二章:金属切削原理教学目标:1. 了解金属切削的基本概念和原理。
2. 掌握金属切削过程中刀具与工件的相互作用。
3. 熟悉金属切削过程中切削力、切削热和切削变形的基本规律。
教学内容:1. 金属切削的基本概念和原理。
2. 刀具与工件的相互作用。
3. 切削力、切削热和切削变形的规律。
教学方法:1. 讲授法:讲解金属切削的基本概念和原理。
2. 实验法:观察和分析刀具与工件的相互作用。
3. 数值分析法:计算切削力、切削热和切削变形。
教学资源:1. 教材:《机械制造技术基础》。
2. 实验设备:刀具、工件和切削实验机。
3. 课件:金属切削过程的动画和图表。
教学评估:1. 课堂讨论:评估学生对金属切削原理的理解。
2. 实验报告:评估学生对刀具与工件相互作用实验的分析能力。
第三章:金属切削机床及刀具教学目标:1. 了解金属切削机床的分类和结构。
2. 掌握金属切削机床的工作原理和操作方法。
3. 熟悉刀具的类型、结构和选用原则。
教学内容:1. 金属切削机床的分类和结构。
2. 金属切削机床的工作原理和操作方法。
3. 刀具的类型、结构和选用原则。
教学方法:1. 讲授法:讲解金属切削机床的分类和结构。
机械制造技术基础5

组织、 管理和 指导生 产
各项生 产准备 工作的 技术依 据
技术的 储备和 交流
工艺规程的设计原则
⑴ 必须可靠地保证零件图纸上所有技术 要求的实现。
⑵ 在规定的生产纲领和生产批量下,一 般要求工艺成本最低。
⑶ 充分利用现有生产条件,少花钱,多 办事。
⑷ 尽量减轻工人的劳动强度,保障生产 安全,创造良好、文明的劳动条件。
2、精基准的选择原则
(1)基准重合的原则
采用设计基准作为定位基准称为基准重 合。它可以避免产生基准不重合误差, 从而利于保证加工精度。
车床主轴箱的加工:
注意
基准不重合误差不仅产生于定位基准与 设计基准不重合,同样产生于其它基准 不重合的场合。定位过程中,基准不重 合误差是在用夹具装夹、调整法加工一 批工件时产生的;若用试切法加工,每 个尺寸均可直接测量保证,故不存在基 准不重合误差。
外圆面:2Zb=da–db 内圆面:2Zb=db–da 总加工余量与工序余 量的关系为: n
Z0= Z i i1
由于工序尺寸在加工时有偏差,实际切除的余 量值也必然是变化的。故加工余量有基本(或公称) 余量Z、最大余量Zmax和最小余量Zmin之分。
Z=La–Lb; Zmin=Lamin–Lbmax; Zmax=Lamax–Lbmin。
多刀同时加工的集中称为工艺集中。
多刀或多面依次加工的集中称为组织集中。
目前,机械加工的发展方向是工序集中。
工序集中的优点: ⑴ 可减少装夹次数; ⑵ 便于保证各加工表面之间的位置精度; ⑶ 便于采用高生产率的机床; ⑷ 有利于生产组织和管理; ⑸ 减少了机床和工人,占用生产面积小。
工序集中存在的问题:
5.2.1 零件的结构工艺性分析 5. 定位
《机械制造技术基础》第五章钻、镗、刨、插、拉削加工的知识

2.粗精加工一起完成,影响了工件的加工质量;
3.排屑困难,易产生阻塞,导致刀齿损坏。
§5-1 钻削与孔加工刀具 孔加工复合刀具种类较多,按工艺类型分有: 1.同类工艺复合刀具
2.不同类工艺复合刀具
§5-1 钻削与孔加工刀具 二、麻花钻的构造与主要几何参数
是常见的孔加工刀具。一般用于实体材料上的粗 加工。钻孔的尺寸精度为IT11--IT12,Ra为5012.5μm。加工范围为0.1--80mm,以φ30mm以下时最
(3)通常只能单刀加工,不能用多刀同时切削。 所以与铣加工比较,牛头刨床的生产率比较低。 牛头刨床主要用于单件、小批量生产或修理车间。
二、龙门刨床
主要用来加工大平 面,尤其是长而窄的 平面,也可加工沟槽 或同时加工几个中小 型零件的平面。生产
率不如铣削高,主要
用于中小批生产及修 理车间。
§5-4 刨床、插床及其加工范围 三、单臂刨床
§5-1 钻削与孔加工刀具
1.从实体材料上加工出孔的刀具 用于加工精度要求不高,或为精度要求较高的 孔作预加工。 (1)扁钻 (2)中心钻 中心钻用来加工各种轴类工件的中心孔。
§5-1 钻削与孔加工刀具
3、麻花钻
是常见的孔加工刀具。一般用于实体材料上的粗 加工。钻孔的尺寸精度为IT11--IT13,Ra为5012.5μm。加工范围为0.1--80mm,以φ30mm以下时最 常用。
适用于加工宽度较大,而又不需要在整个宽度上加工的零件。
四、插床
插床的生产效率较低,通常只用于单件、小批量生产中插削槽、 平面及成型表面等。
§5-4 刨床、插床及其加工范围
插刀上下运动为主运动,工件 可作纵横两个方向的移动,
工作台还可作分度运动。加工 与安装面垂直的面、沟槽
机械制造基础第五章习题及答案

第5章习题及答案5-1机床的运动按功用分为哪几种?答:分为表面成形运动和辅助运动两大类。
直接参与切削过程,使之在工件上形成一定几何形状表面的刀具和工件间的相对运动称为表面成形运动。
机床上除表面成形运动外的所有运动都是辅助运动。
5-2如何衡量切削加工的质量?答:零件切削加工的质量主要由加工精度和表面质量来衡量。
加工精度就是指零件加工后零件的尺寸、形状和表面间的相互位置等方面的几何参数与理想几何参数的相符合程度,两者的差距愈小,加工精度愈高。
零件的表面质量对零件的耐磨性、疲劳强度、抗腐蚀性、密封程度、接触刚度等都有一定的影响。
5-3切削用量要素包括哪几项?切削用量的选择原则是什么?答:切削用量是切削过程中最基本的操作参数,包括切削速度v c、进给量f和背吃刀量a p,其分别表示切削刃与过渡表面之间的相对运动速度、待加工表面转化为已加工表面的速度、已加工表面与待加工表面之间的垂直距离。
合理地选择切削用量,对于保证加工质量、提高生产效率和降低成本有着重要的影响。
切削加工时应当根据具体的加工条件,确定切削用量三要素的合理组合。
背吃刀量要尽可能取得大些,最好一次走刀能把该工序的加工余量切完。
进给量的选择主要受机床、刀具和工件所能承受的切削力的限制。
精加工时,一般背吃刀量不大,切削力也不大,限制进给量的主要因素是工件表面粗糙度。
选定背吃刀量和进给量以后,根据合理的刀具耐用度,用计算法或查表法选择切削速度。
5-4切削层尺寸平面要素包括哪几项?答:切削层尺寸平面要素包括切削层的公称厚度h D、公称宽度b D和公称横截面积A D。
5-5试述刀具的结构和刀具的角度。
答:刀具基本组成部分包括夹持部分和切削部分。
夹持部分俗称刀柄或刀体,主要用于刀具安装与标注的部分。
切削部分俗称刀头,是刀具的工作部分,由刀面、切削刃(又称刀刃)组成。
其组成要素包括:1)前面。
又称前刀面,切削过程中切屑流出所经过的刀具表面。
2)主后面。
又称主后刀面,是切削过程中与过渡表面相对的刀具表面。
第五章 机械加工工艺规程制定
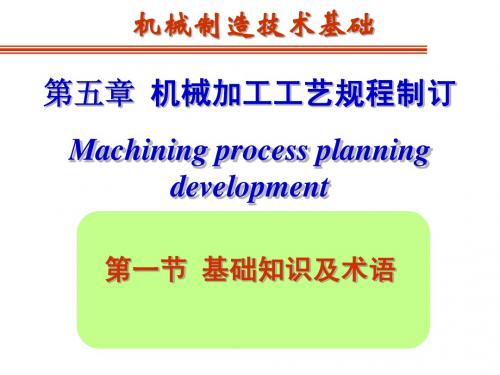
第一节 基础知识及术语
一、生产过程和工艺过程 生产过程 在机械产品制造中,将 原材料(或半成品)转变为成 品的全过程。
第一节 基础知识及术语
工艺过程 在生产过程中,毛坯的制造、零件的机械加工与热处理、 产品的装配等工作将直接改变生产对象的采用形状、尺寸、 相对位置和性质等,使其成为成品和半成品的过程。 主要内容 毛坯和零件成形——铸造、锻压、冲压、 毛坯和零件成形——铸造、锻压、冲压、焊接 、压制、烧结、 压制、烧结、 注塑、 注塑、压塑 … 机械加工——切削、磨削、 机械加工——切削、磨削、特种加工 材料改性与处理——热处理、电镀、转化膜、涂装、 材料改性与处理——热处理、电镀、转化膜、涂装、热喷涂 … 机械装配——把零件按一定的关系和要求连接在一起, 机械装配——把零件按一定的关系和要求连接在一起,组合成 部件和整台机械产品, 包括零件的固定、 连接、 调整、 平衡、 部件和整台机械产品 ,包括零件的固定、 连接、 调整、 平衡 、 检 验和试验等工作
第一节 基础知识及术语
获得尺寸精度的方法 试切法 试切—测量—调整—再试切,反复进行直到被加工 尺寸(工序尺寸)达到要求精度为止的加工方法。 调整法 在机床上先调整好刀具和工件在工序尺寸方向上的 相对位置,并在一批工件的加工过程中保持这个位置不变,以 保证工件工序尺寸精度的方法。 定尺寸刀具法 用刀具的相对尺寸来保证工件被加工部位工 序尺寸的方法。 主动测量法 在加工过程中,利用自动测量装置边加工边测 量加工尺寸,并将测量结果与要保证的工序尺寸比较后,或使 机床继续工作,或使机床停止工作的方法。 自动控制法 在加工过程中,利用测量装置或数控装置等自 动控制加工过程的加工方法。
机械制造基础部分课后习题答案
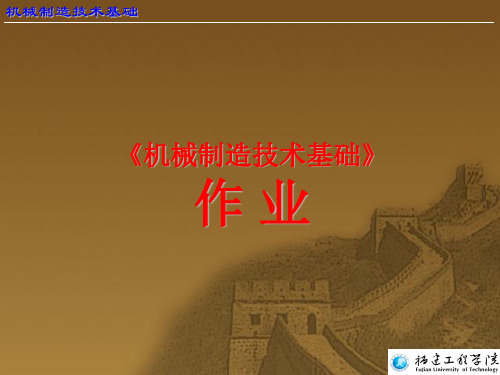
X 45
0.05 0.15
44.9 0.05
机械制造技术基础
3.16 轴套零件如图所示,其内外圆及端面A、B、D均已
加工。现后续加工工艺如下: ①以A面定位,钻¢8孔,求工序尺寸及其偏差。 ②以A面定位,铣缺口C,求工序尺寸及其偏差。
X Y
机械制造技术基础
解: 工序2
①画尺寸链 ②判断:封闭环 20 0.12 增环 减环 ③计算:
0.012 14 0.004 , H
减环 14.25 ③计算:
0 0.05
, 0 0.02
H=4.25 ESH=0.078 EIH=0.016
0.062 0
4=14+H-14.25-0
0.16=0.012+ ESH –(-0.05-0.02) 0=0.004+EIH-0-0.02
H 4.25
0.078 0.016
4.266
机械制造技术基础
0 某零件规定的外圆直径为 32 0 ,渗碳深度为 .05 mm 3.19 0.5~0.8mm。现为使此零件能和其它零件同炉渗碳,限定其 工艺渗碳层深度为0.8~1.0 mm。试计算渗碳前车削工序的直 径尺寸及其偏差。
机械制造技术基础
Y
44.9 0.05
Y=64.9 ESY=-0.07 EIX=-0.07
0 0.14
20=Y-44.9 0.12=ESY –(-0.05) -0.12=EIY-0.05
Y 64.9 0.07 64.97
机械制造技术基础
3.17
铣削加工一轴类零件的键槽时,如图所示,要求保证 键槽深度为 40.16 mm ,其工艺过程为:
机械制造技术基础
机械制造基础(第二版)第5章 z铣削与刨插削加工

5-2.6 数控加工中心
卧式加工中心
指主轴轴线为水平状态设置的加工中心(见图5-18)。通常都 带有可进行分度回转运动的正方形分度工作台。
与立式加工中 心相比,卧式 加工中心的结 构复杂,占地 面积大,重量 大,价格也较 高。
-2.6 数控加工中心
万能加工中心 又称复合加工中心,具有立式和卧式加工中心的功能,工 件一次装夹后能完成除安装面外所有侧面和顶面的加工, 也叫五面加工中心,常见的五面加工中心有两种形式,一 种是主轴可实现立、卧转换;另一种是主轴不改变方向, 工作台带着工件旋转90完成对工件五个面的加工。
5-1.1铣削加工的应用和特点
5-1.1铣削加工的应用和特点
5-1.1铣削加工的应用和特点
5-1.1铣削加工的应用和特点
5-1.1铣削加工的应用和特点
铣削加工的特点 ➢工艺范围广 通过合理地选用铣刀和铣床附件,铣削不仅 可以加工平面、沟槽、成形面、台阶,还可以进行切断和刻 度加工。 ➢铣削加工生产率高 由于多个刀齿参与切削,切削刃的作 用总长度长,每个刀齿的切削载荷相同时,总的金属切除率 就会明显高于单刃刀具切削的效率。
1)每齿进给量af 是铣刀每转一个刀齿时,工件与铣刀沿进 给方向的相对位移量,单位为mm/z。 2)每转进给量f 是铣刀每转一转时,工件与铣刀沿进给方 向的相对位移,单位为mm/r。
3)进给速度f 是单位时间内工件与铣刀沿进给方向的相对
位移,单位为mm/min。
f fnaf zn
5-1.2 铣削要素
5-2.5 数控铣床
5-2.6 数控加工中心
立式加工中心
指主轴轴心线为垂直 状态设置的加工中心 (见图5—17)。其结构 形式多为固定立柱式, 工作台为长方形,无 分度回转功能,适合 加工盘类零件。在工 作台上安装一个水平 轴的数控回转台,可 用于加工螺旋线类零 件。立式加工中心的 结构简单、占地面积 小、价格低。
机械工艺制造基础

➢ 刀具简朴:制造,刃磨,安装均以便.适应性广。
➢ 应用广泛:
细长轴外圆旳车削加工
常将长径比(L/D≥5~10)轴称为细长轴,其刚度很差,车 削时轻易弯曲和振动,产生腰鼓形或竹节形误差而不能确保 加工质量。所以,必须采用有效措施来处理车削时旳变形、 振动等问题。
★磨削旳径向磨削力Fy大:
★磨削温度高:切削速度高,且多为负前角切削, 挤压和摩擦大,加上砂轮导热性很差,在磨削区产 生很高旳瞬时高温,所以磨削时应采用大量切削液 已降低温度。
外圆表面磨削措施
1)中心磨削法:在外圆磨床上以工件旳两顶尖孔 定位进行外圆磨削。 ★纵向进给磨削法
★横向进给磨削法 ★综合磨削法
★ 切削:磨削深度、磨削 点温度和应力到达一定数 值,形成磨屑,沿磨粒前 刀面流出
➢ 详细到每个磨粒,不一 定三个阶段都有
磨屑形成过程
a)平面示意图 b)截面示意图
磨削工艺特点
★精度高、表面粗糙度小:多刃,刃口圆弧半径r小 ,切削层很薄,切削厚度小到微米,磨床精度高, 刚性好,微量进给。
★砂轮有自锐作用:生产率高。
=0°
=0° a =8°
a =0°
切削部分后角
修光部分后角
5.2.3 镗孔
对于直径较大旳孔(D>80~100mm)、内成形面或孔内 环槽等,镗削是唯一合适旳加工措施。一般镗孔精度达 IT8~IT7,表面粗糙度Ra值为0.8~1.6μm;精细镗时, 精度可达IT7~IT6,表面粗糙度Ra值为0.2~0.8μm。
➢精细车:精度可达IT6~IT7,表面粗糙度为 Ra0.2~0.8μm。对于小型有色金属零件,高速精细车 是主要加工措施 (Ra0.4~0.1μm)。
- 1、下载文档前请自行甄别文档内容的完整性,平台不提供额外的编辑、内容补充、找答案等附加服务。
- 2、"仅部分预览"的文档,不可在线预览部分如存在完整性等问题,可反馈申请退款(可完整预览的文档不适用该条件!)。
- 3、如文档侵犯您的权益,请联系客服反馈,我们会尽快为您处理(人工客服工作时间:9:00-18:30)。
(3)由于夹紧变形引起的误差
(4)其他作用力的影响 除上述因素外,重力、惯性力、传动力等也 会使工艺系统的变形发生变化,引起加工误差。
图5-21 夹紧力引起的加工误差 a)夹紧后 b)镗孔后 c)放松后 d)加过渡环后夹紧
6.减小工艺系统受力变形的途径
(1)提高工艺系统刚度 1)提高工件和刀具的刚度 2)提高机床刚度 3)采用合理的装夹方式和加工方式 (2)减小切削力及其变化 合理地选择刀具材料、增大前角和主偏角、对 工件材料进行合理的热处理以改善材料的加工性能 等,都可使切削力减小。
2.机械制造中常见的误差分布规律
(1)实际分布曲线符合正态分布,6σ≤T且分 散中心与公差带中心重合 (2)实际分布曲线符合正态分布,6σ≤T,但 分散中心与公差带中心不重合 (3)实际分布曲线符合正态分布,6σ>T,且 分散中心与公差带中心不重合 (4)实际分布曲线不符合正态分布,而呈平顶 分布 (5)实际分布曲线不符合正态分布,而呈偏态 分布 (6)双峰或多峰分布
4.误差敏感方向的概念
原始误差所引起的 切削刃与工件间的相对 位移,如果产生在加工 表面的法线方向,则对 加工误差有直接的影响; 如果产生在加工表面的 切线方向上,就可以忽 略不计。我们把加工表 面的法向称之为误差的 敏感方向。
图5-3 由δz引起的加工误差
5.研究机械加工精度的方法
分析计算法是在掌握各原始误差对加工精度影 响规律的基础上,分析工件加工中所出现的误差可 能是哪一个或哪几个主要原始误差所引起的,并找 出原始误差与加工误差之间的影响关系,进而通过 估算来确定工件的加工误差的大小,再通过试验测 试来加以验证。 统计分析法是对具体加工条件下加工得到的几 何参数进行实际测量,然后运用数理统计学方法对 这些测试数据进行分析处理,找出工件加工误差的 规律和性质,进而控制加工质量。分析计算法主要 是在对单项原始误差进行分析计算的基础上进行的, 统计分析法则是对有关的原始误差进行综合分析的 基础上进行的。
3.刀具热变形对加工精度的影响 刀具热变形的热源主要是切削热。
图5-25 车刀的热变形曲线
4.机床热变形对加工精度的影响
由于机床热源分布的不均匀、机床结构的复 杂性以及机床工作条件的变化很大等原因,机床 各个部件的温升是不相同的,甚至同一个零件的 各个部分的温升也有差异,这就破坏了机床原有 的相互位置关系。
(3)微进给误差
2.按定程机构调整 在大批大量生产中广泛应用行程挡 块、靠模、凸轮等机构保证加工精度。 这时候,这些机构的制造精度和调整, 以及与它们配合使用的离合器、电气开 关、控制阀等的灵敏度就成了影响误差 的主要因素。
3.按样件或样板调整
在大批大量生产中用多刀加工时,常用专门 样件来调整切削刃间的相对位置。如活塞环槽半 精车和精车时就是如此。 当工件形状复杂,尺寸和重量都比较大的时 候,利用样件进行调整就太笨重,且不经济,这 时可以采用样板对刀。
3.夹具的几何误差
夹具的作用是使工件相 对于刀具和机床具有正确的 位置,因此夹具的制造误差 对工件的加工精度 (特别是 位置精度) 有很大影响。
图5-10 工件在夹具中装夹示意
三、调整误差 1.试切法调整
试切法调整广泛用在单件、小批生产中。这 种调整方式产生调整误差的来源有3个方面:
(1)度量误差 (2)加工余量的影响
五、工艺系统受热变形引起的误差
1.工艺系统的热源
(1)内部热源 内部热源来自工艺系统内部, 其热量主要是以热传导的形式传递的。 1)切削热 切削热对工件加工精度的影响最 为直接。 2)摩擦热和能量损耗 工艺系统因运动副 (如齿轮副、轴承副、导轨副、螺母丝杠副、离合 器等) 相对运动所生摩擦热和因动力源 (如电动 机、液压系统等) 工作时的能量损耗而发热。 3)派生热源 工艺系统内部的部分热量通过 切屑、切削液、润滑液等带到机床其它部位,使 系统产生热变形。
2.内应力的产生 (1)热加工中内应力的产生
在铸、锻、焊、 热处理等工序中由于 工件壁厚不均、冷却 不均、金相组织的转 变等原因,使工件产 生内应力。
图5-32 铸件因内应力而引起的变形
2.内应力的产生 (2)冷校直产生的内应力
图5-33 校直引起的内应力
3.减小内应力变形误差的途径
(1)改进零件结构 在设计零件时,尽量做到 壁厚均匀,结构对称,以减少内应力的产生。 (2)增设消除内应力的热处理工序 铸件、锻 件、焊接件在进入机械加工之前,应进行退火、 回火等热处理,加速内应力变形的进程;对箱体、 床身、主轴等重要零件,在机械加工工艺中尚需 适当按排时效处理工序。 (3)合理安排工艺过程 粗加工和精加工宜 分阶段进行,使工件在粗加工后有一定的时间来 松弛内应力。
2.工件热变形对加工精度的影响
工件在机械加工中所产生的热变形,主要是 由切削热引起的。 (1)工件均匀受热 在加工像轴类等一些形状 简单的工件时,如果工件处在相对比较稳定的温 度场中,此时就认为工件是均匀受热。 (2)工件不均匀受热 在铣、刨、磨平面时, 工件单面受切削热作用,上下表面之间形成温差 △θ,导致工件向上凸起,凸起部分被工具切去, 加工完毕冷却后,加工表面就产生了中凹,造成 了几何形状误差。
2.加工经济精度
图5-2 加工成本与加工误差之间的关系
3.原始误差
由机床、夹具、刀具和工件组成的机械加工工艺 系统 (简称工艺系统) 会有各种各样的误差产生,这 些误差在各种不同的具体工作条件下都会以各种不同 的方式 (或扩大、或缩小) 反映为工件的加工误差。 工艺系统的误差是“因”,是根源;工件的加工误差 是 “果”,是表现;因此,我们把工艺系统的误差 称为原始误差。
图5-18 车削外圆时工艺 系统受力变形对加工精度 的影响
5.工艺系统刚度及其对加工精度的影响 (2)由于切削力变化引起的误差
在加工过程中,由于工件的加工余量发生变 化、工件材质不均等因素引起的切削力变化,使 工艺系统变形发生变化,从而产生加工误差。
图5-19 毛坯形状误差的复映
5.工艺系统刚度及其对加工精度的影响
四、工艺系统受力变形引起的误差 1.基本概念
机械加工工艺系统在切削力、夹紧力、惯性 力、重力、传动力等的作用下,会产生相应的变 形,从而破坏了刀具和工件之间的正确的相对位 置,使工件的加工精度下降。
图5-12 受力变形对工件精度的影响 a)车长轴 b)磨内孔
2.工件刚度
工艺系统中如果工件刚度相对于机床、刀 具、夹具来说比较低,在切削力的作用下,工 件由于刚性不足而引起的变形对加工精度的影 响就比较大,其最大变形量可按材料力学有关 公式估算。
(3)工件尺寸在某区间内的概率
生产上感兴趣的问题往往不是工件为某一尺寸 的概率是多大,而是加工工件尺寸落在某一个区间 (x ≤x≤x ) 内的概率是多大。
1 2
图5-38 工件尺寸概率分布
2.机械制造中常见的误差分布规律
图5-40 机械加工误差分布规律 a)正态分布 b)平顶图的基本形式
点图的基本形式是由小样本均值x 的点图和 小样本极差R的点图联合组成的x 、R点图,如图 所示。
图5-43 x、R点图 a)x点图 b)R点图
3.x、R点图上、下控制限的确定
x ~N(μ,σ2/n) 也就是说,样本均值x 的分散范围为 (μ±3σ√n)。 数理统计学已经证明,样本极差R近似服从 正态分布,即有: (R ~N(R,σR2) 这就是说,样本极差R的分散范围为 (R±3σR)。到此,x-R点图上的上、下控制限 的位置就可以确定了。
3.刀具刚度
外圆车刀在加工表面法线(y)方向上的 刚度很大,其变形可以忽略不计。镗直径较小 的内孔,刀杆刚度很差,刀杆受力变形对孔加 工精度就有很大影响。
4.机床部件刚度 (1)机床部件刚度
图5-15 车床刀架部件的刚度曲线 1—加载曲线 2—卸载曲线
图5-14 车床部件静刚度的测定 1—心轴 2、3、6—千分表 4—测力环 5—螺旋加力器
4.机床部件刚度 (2)影响机床部件刚度的因素
1)结合面接触变形的影响 由于零件表面存在宏观几何形状误差和微观几 何形状误差,结合面的实际接触面积只是名义接触 面积的一小部分 (图所示),在外力作用下,实际 接触区的接触应力很大,产生了较大的接触变形。
图5-16 两零件结合面间的接触情况
4.机床部件刚度
图5-26 车床的热变形
5.减小工艺系统热变形的途径 (1)减少发热和隔热 (2)改善散热条件 (3)均衡温度场 (4)改进机床结构 (5)加快温度场的平衡 (6)控制环境温度
六、内应力重新分布引起的误差 1.基本概念
没有外力作用而存在于零件内部的应力,称 为内应力。 工件上一旦产生内应力之后,就会使工件金 属处于一种高能位的不稳定状态,它本能地要向 低能位的稳定状态转化,并伴随有变形发生,从 而使工件丧失原有的加工精度。
2)摩擦力的影响
图5-17 摩擦力对机床部件刚度的影响
4.机床部件刚度
3)低刚度零件的影响 在机床部件中,个别薄弱零件对刚度 的影响很大。
4)间隙的影响 机床部件在受力作用时,首先消除零 件间在受力作用方向上的间隙,这会使机 床部件产生相应的位移。
5.工艺系统刚度及其对加工精度的影响 (1)由于工艺系统刚度变化引起的误差
(2)外部热源 外部热源来自工艺系统外 部。
1)环境温度 以对流传热为主要传递形式的环 境温度的变化 (如气温的变化,人造冷、热风,地 基温度的变化等)影响工艺系统的受热均匀性,从 而影响工件的加工精度。 2)辐射热 以辐射传热为传递形式的辐射热 (如阳光、灯光照明、取暖设备、人体温度等)因其 对工艺系统辐射的单面性或局部性而使工艺系统的 热变形发生变化,从而影响工件的加工精度。
3.工艺过程的分布图分析 (1)样本容量的确定 (2)样本数据的测量 (3)异常数据的剔除 (4)实际分布图的绘制 (5)理论分布图的绘制 (6)工艺过程的分析