皮带胶接
皮带胶接
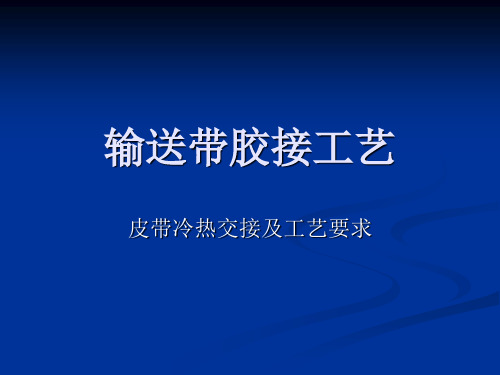
思 考 题
胶带胶接头制做的质量要求有哪些?
热硫化与冷硫化胶接在工艺上的主要区别 有哪些? 热硫化胶接三要素是什么? 对于天然橡胶制成的胶带,硫化三要素通 用标准是什么?
硫化三要素对胶带性能的影响
温度:硫化温度是硫化三要素之首,是橡胶进 行硫化反应(交联反应)的基本条件,直接影 响橡胶硫化速度和制品的质量。与所有化学反 应一样,硫化反应随着温度升高而加快,温度 每上升8~10℃,其反应速度约增加一倍,即反 应时间约减少一半。 硫化温度决定于橡胶的品种,如天然橡胶 的最佳硫化温度为145-148度,丁苯胶的最佳硫 化温度为148—153度。在实际操作时应考虑温 差,调节温度在这个基础一般加3-5 度左右。 从提高硫化效率来说,硫化温度越高越好, 但考虑到橡胶的耐热性和“硫化返原”现象, NR(天然橡胶) 最好在140-150℃,最高不超 过160℃。
输送带胶接工艺
皮带冷热交接及工艺要求
第一节 工艺流程
主要工序
将胶带接口或待更换部分转至适宜接口工作的 位置。 设备停电,做好防止转动措施。
用起吊工具将配置拉起或将张紧装置松开,提 升高度或松开量视皮带接头需要量而定,一般 标准为皮带胶接完成后,张紧装置行程量不小 于3/4拉紧额定行程。 皮带接头两侧用皮带卡子与皮带架固定,使接 头处皮带呈松弛状态。
过硫阶段:正硫阶段之后,继续硫化便进入过 硫阶段。这一阶段的前期属于硫化平坦期的一 部分。在平坦期中,硫化胶的各项物理机械性 能基本上保持稳定。当过平坦期之后,天然橡 胶和丁基橡胶由于断链多于交联出现“硫化返 原”现象而变软;合成橡胶则因交联继续占优 势和环化结构的增多而变硬,且伸长率也随之 降低,橡胶性能受到损害。
皮带胶接工艺培训资料
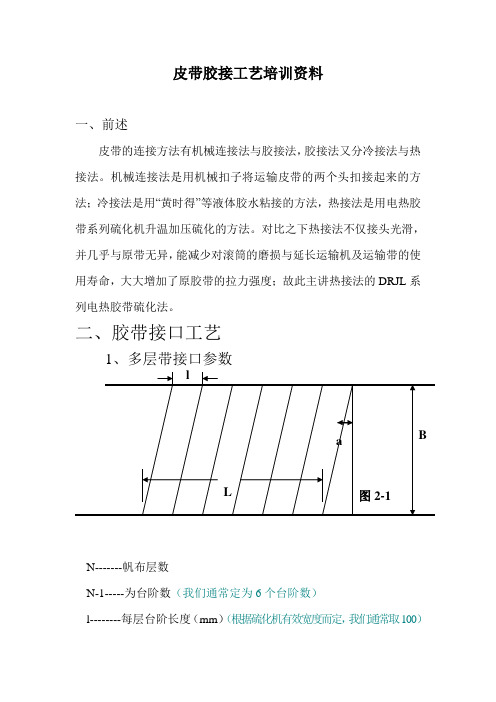
皮带胶接工艺培训资料一、前述皮带的连接方法有机械连接法与胶接法,胶接法又分冷接法与热接法。
机械连接法是用机械扣子将运输皮带的两个头扣接起来的方法;冷接法是用“黄时得”等液体胶水粘接的方法,热接法是用电热胶带系列硫化机升温加压硫化的方法。
对比之下热接法不仅接头光滑,并几乎与原带无异,能减少对滚筒的磨损与延长运输机及运输带的使用寿命,大大增加了原胶带的拉力强度;故此主讲热接法的DRJL系列电热胶带硫化法。
二、胶带接口工艺1、多层带接口参数N-------帆布层数N-1-----为台阶数(我们通常定为6个台阶数)l--------每层台阶长度(mm)(根据硫化机有效宽度而定,我们通常取100)在胶粘剂选定后,层间粘合强度一定,l长度要紧取决于单层带芯帆布的强度,强度越高l越长。
通常取在100-400mm之间(见表)B--------胶带宽度(mm)a--------斜角角度,通常tga=0.3-0.5大有利于应力分布均匀,但加工胶带损耗大。
据有关资料介绍,德国取tga=0.3(a=16°42′);英国取tga=0.5(a=26°)日本取a=22°;我国有取30°,经综合分析我们取硫化机隔热板两个相邻边的锐角。
2、接口加工步骤2.1下部接口台阶加工加工前准备胶带两端互相搭接时要使上部胶带与运行方向一致,并标出上部胶带与下部胶带的记号。
在胶带端部划垂直于运行方向的的直线,用硫化机隔热板划出与胶带边缘呈与硫化机隔热板相同的锐角的斜线。
加工要点:a、根据我矿硫化机(DRJL-1200)或者(DRJL-1000)的加热盘宽度,确定L=600mm(即6台阶,每台阶长l=100mm);b、根据胶带的帆布层数合理匀分每台阶帆布层数;c、剥层及修边,若是钢丝皮带剥层走向应与钢丝走向一致;2.2上部接口台阶加工胶带两端与边胶定位线为准互相叠放,下部胶带的最上层帆布承接上部胶带的斜块段,加工方法如下部胶带加工,其基本止标是始终准备地保证帆布层台阶的尺寸。
皮带胶接岗位安全技术规程(3篇)
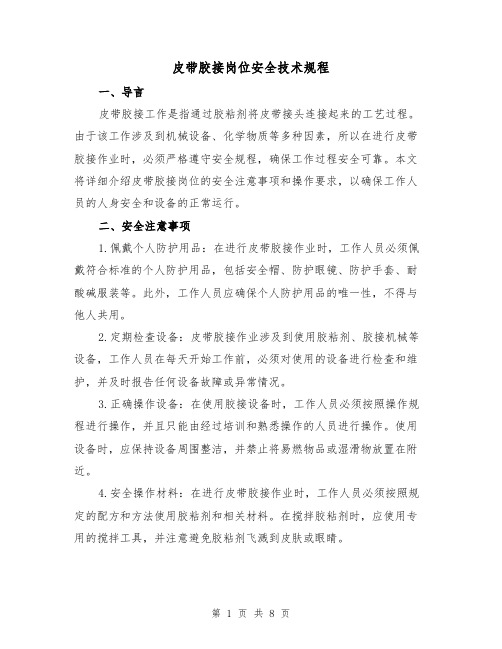
皮带胶接岗位安全技术规程一、导言皮带胶接工作是指通过胶粘剂将皮带接头连接起来的工艺过程。
由于该工作涉及到机械设备、化学物质等多种因素,所以在进行皮带胶接作业时,必须严格遵守安全规程,确保工作过程安全可靠。
本文将详细介绍皮带胶接岗位的安全注意事项和操作要求,以确保工作人员的人身安全和设备的正常运行。
二、安全注意事项1.佩戴个人防护用品:在进行皮带胶接作业时,工作人员必须佩戴符合标准的个人防护用品,包括安全帽、防护眼镜、防护手套、耐酸碱服装等。
此外,工作人员应确保个人防护用品的唯一性,不得与他人共用。
2.定期检查设备:皮带胶接作业涉及到使用胶粘剂、胶接机械等设备,工作人员在每天开始工作前,必须对使用的设备进行检查和维护,并及时报告任何设备故障或异常情况。
3.正确操作设备:在使用胶接设备时,工作人员必须按照操作规程进行操作,并且只能由经过培训和熟悉操作的人员进行操作。
使用设备时,应保持设备周围整洁,并禁止将易燃物品或湿滑物放置在附近。
4.安全操作材料:在进行皮带胶接作业时,工作人员必须按照规定的配方和方法使用胶粘剂和相关材料。
在搅拌胶粘剂时,应使用专用的搅拌工具,并注意避免胶粘剂飞溅到皮肤或眼睛。
5.防范火灾风险:由于胶粘剂具有易燃性,所以在搅拌胶粘剂、进行胶接作业时,禁止吸烟、使用明火,并确保工作场所通风良好。
6.注意工作环境安全:在进行皮带胶接作业时,工作人员必须注意四周环境的安全情况。
工作场所应保持干净整洁,地面上不得有滑倒物品,工具、材料等物品应放置在规定的位置上。
7.防止皮带危险:当进行皮带胶接作业时,工作人员必须确保皮带处于停止状态,并采取相应的锁定措施,以防止皮带突然启动造成事故。
8.组织安全培训:对于从事皮带胶接工作的人员,必须进行必要的安全培训,包括工作操作规程、安全事故案例分析等内容,并定期进行安全知识的更新培训。
三、操作要求1.准备工作:进行皮带胶接作业前,必须对工作场所进行安全检查,检查设备是否正常运行,确保胶粘剂的配方正确,并组织工作人员佩戴个人防护用品。
皮带胶接作业标准

皮带热硫化胶接作业标准1、适用范围本标准适用于检修公司范围对内织物芯分层皮带(棉帆布、尼龙、聚酯)热硫化胶接接头的制作。
2、施工准备2.1设备及材料要求:2.1.1主要材料:成份和性能与制造胶带采用相符的复盖胶、油皮胶、胶浆、封口胶以及120#溶剂汽油2.1.2辅助材料:卡板、铁丝2.2主要机具:硫化机、扒皮机、刀具、手钳、米尺、角尺、木工划线笔、手锤、扳手、刷子、电动钢丝刷、不锈钢桶、橡胶手套、倒链等2.3作业条件:接头的作业场所,要绝对干燥、干净、无粉尘、不能暴晒、对于潮湿处必须反复去除水汽,必要时可搭建简易帐篷。
2.4准备工作:2.4.1在作业前同岗位取得联系,填写检修联络票并会同岗位人员一齐进行安全确认,选择作业场地,断电挂好检修牌,确认锁紧拉绳。
2.4.2用倒链将配重小车或配重吊起到配重最高处。
2.4.3用卡板卡好所胶接的皮带两端。
2.4.4搭工作平台,便于工作,将皮带接口切断准备拨口。
3.作业程序3.1将胶带平整放臵在工作平台上,接头部位擦拭干净,划出接头中心线,3.2在胶带一端画出中心线,皮带搭头斜长为0.3*皮带宽度,画出切割线、边胶切割线,阶梯节距线。
图一布层解剖示意图3.3按需使用皮带长度切断皮带3.4裁剥按照尺寸线,裁断斜切,剥离,注意裁刀不能割伤下层帆布。
划线完毕后,进行剖切扒剥工作,剥离的顺序是:先第一层,再第二层,依次进行,即从后部开始,向端部推进。
剖切时,注意不要损伤下一层胶布。
一般是两次剖切,第一次切印,第二次是切断,俗称“两刀法”。
第二次剖切时,务必小心,并要用力,根据皮带线层数,确定搭头的台阶和每个台阶的宽度,搭头台阶为胶带层数减一。
3.5以切断处切口为基准,在里外两侧作出加工标记,按照阶梯式的拨线层,封口胶宽50mm,也就是,接缝口为45度切口,用钳子剥去接缝部分的覆盖胶。
3.6按阶梯线用刀切割第一层芯体,用起层器(螺丝刀)侧45°挑起芯体,注意用起层器(螺丝刀)时不得损伤下一层芯体。
皮带机胶接定额

皮带机胶接定额
皮带机胶接的过程并不复杂,但需要一定的专业知识和技术。
胶接的质量直接影响到皮带
机的运行效果和寿命。
为了保证胶接的质量,制定了一些胶接定额,以规范操作流程和质
量标准。
皮带机胶接定额主要包括以下内容:
1. 胶接的条件和要求:胶接的条件包括环境温度、湿度、清洁度等;要求包括胶接的质量
标准、接头的结构、尺寸等。
2. 胶接的工具和材料:胶接过程需要的工具包括胶接机、割胶钳、压胶器等;材料包括胶水、润滑剂、填充料等。
3. 胶接的步骤和流程:胶接的步骤包括准备工作、打磨、涂胶、压接、固化等;流程包括
操作顺序、时间控制、质量检查等。
4. 胶接的质量要求:胶接后要经过质量检查,合格后才能投入使用;不合格的接头需要重
新胶接。
5. 胶接的注意事项和常见问题:胶接过程中需要注意安全、操作规范等;常见问题包括胶
水过多、压力不均匀、固化不充分等。
通过制定胶接定额,可以规范胶接操作流程,提高胶接质量,延长皮带机的使用寿命,减
少故障率,确保生产运行的顺利进行。
同时,定额也为操作人员提供了指导和参考,帮助
他们更好地完成胶接工作。
在实际操作中,需要根据具体情况对胶接定额进行适当调整和修改,以适应不同的工艺要
求和实际情况。
同时,要加强对操作人员的培训和指导,提高他们的技术水平和操作能力,确保胶接作业的安全和质量。
总之,胶接定额是制定皮带机胶接工艺和质量标准的重要依据,对于确保皮带机运行的安
全和稳定具有重要意义。
只有严格按照定额要求进行胶接操作,才能保证胶接质量和效果
达到预期目标,为生产运行提供可靠的保障。
胶接皮带技术规范

胶接皮带技术规范一、检修前的准备:1、检修前要明确工作项目、性质、质量及工期进度要求,确认皮带规格型号与包装是否一致。
2、检修前到现场实地勘察,确定检修方案,需生产岗位配合拿带时,做到专人指挥;故障抢修时,检修记录中必须详细记录损伤部位和损伤程度。
3、核对皮带备件是否符合条件要求,更换一段时,新备件与原皮带线层数、厚度一致。
4、做好工具、材料的准备,如:夹板、倒链、粘合剂等,确定好停机位置,尽量避开粉尘、高温、潮湿地带,便于粘接,确保粘接质量。
5、皮带做口严禁使用壁纸刀,必须使用自制锋钢锯条刀。
6、与岗位操作人员取得联系,领取操作牌,切断电源,挂上检修牌。
一、冷粘操作:1、确认上下胶面,保证工作面为厚胶面,确认上下接口的方向,将皮带穿好夹牢,开始做口,条件允许可先做皮带口,以缩短检修工时。
2、皮带扒口:⑴皮带口的长度、斜口长度及带口宽度:B650mm皮带斜口长度为750mm带口宽150m m×线层数,B800mm皮带斜口长度为950mm带口宽150m m ×线层数,B1000mm皮带斜口长度为1150mm带口宽150m m×线层数;台阶数量:总线层数减1层线;⑵扒口操作:①、使用皮带刀割口时,必须控制好进刀深度,不可过深,最好是捅口时稍带点线毛为宜。
②、捅口时对面不得有人,螺丝刀刃不能太快,更不准立着刃口捅皮带,以免损伤线层。
③、皮带接口留有防烫台,宽度为30㎜,防烫台做成台阶状,防烫台整体厚度不超过皮带厚度的1.2倍,防止从防烫台处开胶。
⑶、扒完皮带后将预留的皮带边铲平,铲边时要逐渐过渡,凹凸不平会造成皮带边开胶。
⑷皮带打磨:①、打磨时应横向打磨,不得将台阶磨成毛状,不得用力过大,将胶打净即可。
②、打磨要均匀,不得打糊及有打不到的死角,打磨完毕用笤帚清扫干净。
⑸皮带预热:①、皮带预热必须用烤灯盘加热,确保加热均匀,皮带温度达到50℃。
⑹皮带刷胶:①、刷胶前要清除好杂物,接口表面用草根刷子朝一个方向刷杂物,严禁烟火,避免震动,防止粉尘落在粘接胶面上。
皮带胶接工艺培训资料
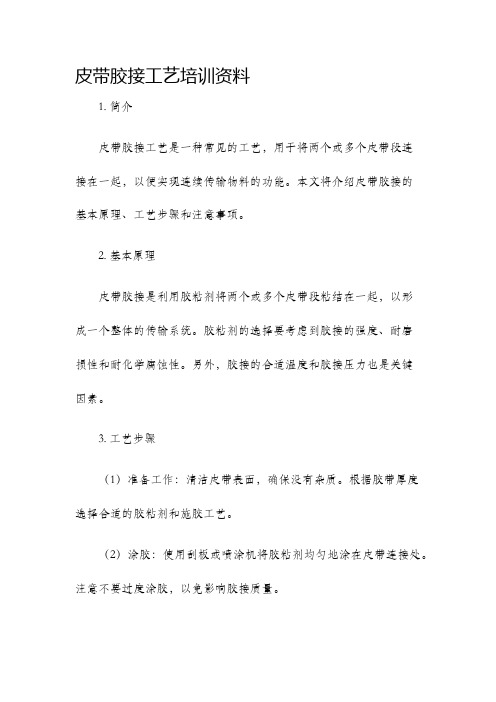
皮带胶接工艺培训资料1. 简介皮带胶接工艺是一种常见的工艺,用于将两个或多个皮带段连接在一起,以便实现连续传输物料的功能。
本文将介绍皮带胶接的基本原理、工艺步骤和注意事项。
2. 基本原理皮带胶接是利用胶粘剂将两个或多个皮带段粘结在一起,以形成一个整体的传输系统。
胶粘剂的选择要考虑到胶接的强度、耐磨损性和耐化学腐蚀性。
另外,胶接的合适温度和胶接压力也是关键因素。
3. 工艺步骤(1)准备工作:清洁皮带表面,确保没有杂质。
根据胶带厚度选择合适的胶粘剂和施胶工艺。
(2)涂胶:使用刮板或喷涂机将胶粘剂均匀地涂在皮带连接处。
注意不要过度涂胶,以免影响胶接质量。
(3)对齐:将两个或多个皮带段粘结在一起前,确保它们的位置和轴线对齐。
可以使用导向板或模具辅助对齐。
(4)压接:使用胶接机或其他压接设备将两个或多个皮带段加压在一起。
根据胶粘剂特性和胶接厚度,确定胶接的合适温度和压力。
(5)固化:将压接完成的皮带放置在恒温室中,等待胶粘剂固化。
在此期间,压接施加的合适温度和压力将有助于胶粘剂的固化。
(6)修整:待胶粘剂固化后,使用切割工具修整胶接处边缘,使其平整。
4. 注意事项(1)选择合适的胶粘剂:根据胶接的需求,选择具有良好粘接性能的胶粘剂。
考虑胶粘剂的粘接强度、耐磨性和耐化学腐蚀性等特性。
(2)注意涂胶均匀:胶粘剂涂布要均匀,不要过度涂胶,以免影响胶接质量。
(3)确保对齐:在进行胶接之前,确保要连接的皮带段的位置和轴线对齐。
使用导向板或模具辅助对齐。
(4)控制压接温度和压力:根据胶粘剂特性和胶接厚度,确定合适的压接温度和压力。
过高的温度或压力可能导致胶粘剂固化不良或胶接强度不够。
(5)胶粘剂固化时间:为了确保胶粘剂能够充分固化,胶接完成后要将皮带放置在恒温室中等待一定时间。
固化时间根据胶粘剂的要求确定。
(6)修整胶接处:在胶粘剂固化后,使用切割工具修整胶接处边缘,使其平整。
这将有助于提高胶接的整体效果。
5. 总结皮带胶接工艺是一种常见的工艺,用于将两个或多个皮带段连接在一起。
皮带胶接工艺培训资料
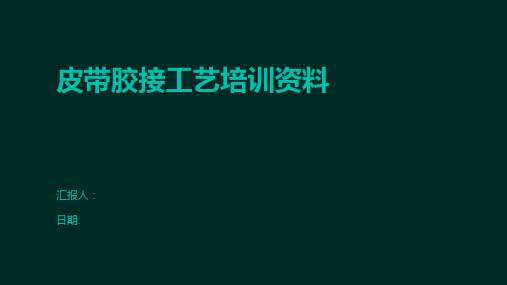
选择合适的胶粘剂和工艺参 数,确保皮带之间的粘合强
度和稳定性。
01
02
03
在涂胶和贴合过程中要保持 清洁,避免杂质和灰尘影响
胶接质量。
在加压和固化过程中要保持 适当的压力和时间,以确保
胶粘剂充分固化。
04
05
在冷却过程中要注意观察皮 带的变形情况,如有异常应
及时处理。
03
皮带胶接工艺设备与工具
皮带胶接工艺设备介绍
在皮带胶接过程中,需要选择 合适的胶粘剂和工艺参数,以 确保皮带之间的粘合强度和稳 定性。
皮带胶接工艺操作流程
准备工作
检查皮带的表面质量,确 保无油污、灰尘等杂质。 根据需要选择合适的胶粘 剂和工具。
表面处理
对皮带表面进行打磨、清 洁等处理,以提高胶粘剂 的粘附力。
涂胶
将胶粘剂均匀地涂抹在皮 带表面上,确保涂层均匀 、无气泡。
胶接质量。
加强质量检测
03
增加质量检测频次,对不合格产品进行返工或报废,避免问题
产品流入市场。
05皮带Βιβλιοθήκη 接工艺安全操作规范及 应急处理措施
皮带胶接工艺安全操作规范
操作前检查
对皮带、胶接机、工具 等进行检查,确保设备
完好无损。
防护措施
操作人员应佩戴防护眼 镜、手套等个人防护用
品,避免受伤。
胶接操作
皮带胶接工艺操作流程
贴合
固化
将两条皮带贴合在一起,确保位置准 确、平整。
保持加压状态一定时间,使胶粘剂充 分固化。
加压
通过加压设备对皮带进行加压,以确 保胶粘剂充分固化。
皮带胶接工艺操作流程
冷却
释放加压设备,让皮带自然冷却 。
皮带现场接头胶接硫化操作规程副本

皮带现场接头胶接硫化操作规程副本Document serial number【NL89WT-NY98YT-NC8CB-NNUUT-NUT108】EP-300阻燃耐寒输送带接头现场胶接热硫化操作规程一、胶接前的准备工作:1、将皮带接头牵引到方便硫化的位置;2、胶接场地要清扫干净,宽敞干燥、明亮。
3、在胶接作业处,拆除输送机4组以上的上托辊架子。
4、将预先做好的工作台平放于输送机架上。
5、将硫化机底座及下热板平放于工作台上。
6、将制作好的两个皮带工装限位支架(图)放于工作台两侧。
7、将胶带两端带头放入硫化机下热板上,然后开始作业。
二、胶接作业程序及要点:1、皮带牵引到位后,皮带打夹子,用两个2T葫芦固定住皮带,根据实际所需长度用刀割断备用;2、摆好硫化机加热夹板做平台;3、剥出皮带接头共三梯:1.用裁纸刀沿加热板斜面对皮带头外斜面进行修整;2.沿加热板内斜面对皮带接头内斜面划出标记线;3.用裁纸刀沿标记线小心的划开皮带第一层胶层,不破坏布层;4.用钳子横向撕开胶层,每次撕开50mm,直至全部撕开;5.第一层遗留50mm宽度梯层,用加热板斜边角度划第二梯层斜边记号线;6.采用裁纸刀沿记号线小心花开皮带层,不破坏下一层布层;7.用钳子横向撕开划开的皮带层,每次撕开50mm,直至全部撕开;8.第二梯层遗留300mm,用加热板斜边角度划第三梯斜边记号线;9.用裁纸刀沿记号线小心划开皮带层,不破坏下一层布层;10.用钳子横向撕开划开的皮带层,每次撕开50mm,直至全部撕开;11.用磨光机对撕开的皮带层分层进行打磨;12.使用清洗剂对两个接头撕开的皮带层进行清洗;13.上胶,在皮带剥层处均匀涂抹胶浆;14.在撕开的帆布层上铺满油皮胶4、在硫化机两端放好皮带校正工装,工装长度为4米,共两个,在两端皮带中间找出三个中心点,划上长度为3~4米白色记号;5、将涂好胶的皮带两端放到加热板上后,铺上油皮胶,用约9米长细钢丝对齐白色记号线将皮带找正。
皮带胶接工艺培训资料
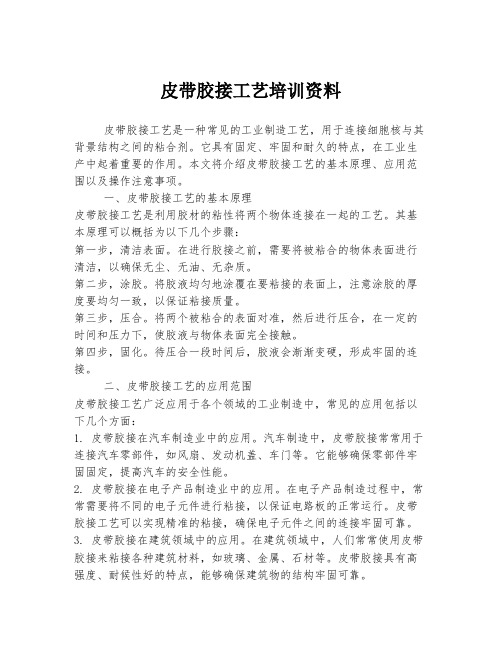
皮带胶接工艺培训资料皮带胶接工艺是一种常见的工业制造工艺,用于连接细胞核与其背景结构之间的粘合剂。
它具有固定、牢固和耐久的特点,在工业生产中起着重要的作用。
本文将介绍皮带胶接工艺的基本原理、应用范围以及操作注意事项。
一、皮带胶接工艺的基本原理皮带胶接工艺是利用胶材的粘性将两个物体连接在一起的工艺。
其基本原理可以概括为以下几个步骤:第一步,清洁表面。
在进行胶接之前,需要将被粘合的物体表面进行清洁,以确保无尘、无油、无杂质。
第二步,涂胶。
将胶液均匀地涂覆在要粘接的表面上,注意涂胶的厚度要均匀一致,以保证粘接质量。
第三步,压合。
将两个被粘合的表面对准,然后进行压合,在一定的时间和压力下,使胶液与物体表面完全接触。
第四步,固化。
待压合一段时间后,胶液会渐渐变硬,形成牢固的连接。
二、皮带胶接工艺的应用范围皮带胶接工艺广泛应用于各个领域的工业制造中,常见的应用包括以下几个方面:1. 皮带胶接在汽车制造业中的应用。
汽车制造中,皮带胶接常常用于连接汽车零部件,如风扇、发动机盖、车门等。
它能够确保零部件牢固固定,提高汽车的安全性能。
2. 皮带胶接在电子产品制造业中的应用。
在电子产品制造过程中,常常需要将不同的电子元件进行粘接,以保证电路板的正常运行。
皮带胶接工艺可以实现精准的粘接,确保电子元件之间的连接牢固可靠。
3. 皮带胶接在建筑领域中的应用。
在建筑领域中,人们常常使用皮带胶接来粘接各种建筑材料,如玻璃、金属、石材等。
皮带胶接具有高强度、耐候性好的特点,能够确保建筑物的结构牢固可靠。
4. 皮带胶接在纺织行业中的应用。
在纺织行业中,常常需要将不同的织物进行粘合,以制作服装、鞋帽等产品。
皮带胶接工艺可以实现高效粘合,提高产品的质量和耐用度。
三、皮带胶接工艺的操作注意事项在进行皮带胶接工艺时,需要注意以下几点:1. 选择合适的胶液。
不同的材料需要选择不同的胶液,以确保胶接效果的最佳。
2. 清洁表面。
在进行胶接之前,需要彻底清洁被粘合的表面,以去除灰尘、油污等杂质。
输送皮带胶水粘接方法

输送皮带胶水粘接方法
1. 准备工作:将输送皮带两端的接口清洗干净,确保表面干燥、无油污、灰尘等杂质。
2. 涂胶:将胶水涂在输送皮带接口的两端,涂抹均匀,厚度一般为2-3毫米。
3. 接合:将两端的输送皮带对接,用力压紧,确保胶水充分贴合。
4. 固化:将接合处用夹具夹紧,待胶水固化后,夹具可拆卸。
5. 整理:将接口处的多余胶水刮掉,用砂纸打磨平整。
6. 检查:检查接口处是否牢固,无松动、开裂等情况。
注意事项:
1. 胶水应选用适合输送皮带材质的胶水。
2. 涂胶时应注意胶水的均匀涂抹,避免出现厚薄不均的情况。
3. 接合时应用力均匀,确保胶水充分贴合。
4. 固化时间应根据胶水的说明进行控制。
5. 检查时应仔细检查接口处是否牢固,避免出现安全隐患。
皮带胶接工艺简介PPT课件

三、皮带接头的阶梯形式
接头的阶梯剖切口角度,是胶带接头型式的另一个重要 因数。一般,接头阶梯型式,可以分为四种,如图2所示。
直角形(或称直角),剖切口与胶带中心线成直角,如图2a。 斜角形或称斜口,剖切口与胶带中心线成斜角,如图2b。 人字形或对斜口,剖切口与胶带中心线成对称形双斜角,如图2c
。
三、皮带接头的阶梯形式
25―40分钟。 7、帆布及尼龙皮带的接头形式可以分为:对接和搭接,如图1所示,为
帆布皮带接头型式。
一、皮带接头的方法
图中:(a)对接(b)搭接 1、上复盖胶2、下复盖胶 3、胶布层4、粘合面 a、对接:是使胶带接头两端相 应的芯层(胶布层),处在同 一级阶梯上对口相接。如图1a。 b、搭接:是使胶带接头两端相应的芯层,分别处在差一级的阶梯上对 口相接,如图1b。 一般来说,帆布胶带的硫化胶接,常采用对接。但是这种接头形式只能 满足粘接强度的不高的胶带。搭接适用于要粘接强度高的皮带粘接,如 尼龙布芯层胶带等。
二、接头强度计算
所谓接头强度的计算,是胶带硫化胶接后,接头抗张强力与胶带 本 体抗张强力之比。一般,胶带接头的抗张强力是由试验测来的;而本身 抗张强力是胶带厂或资料提供的。
目前较常用的计算公式为:1/织物层数*(皮带层数-1)。例如: 三 层的皮带两个台阶,1/3*(3-1)=67%;六层的皮带五个台阶,1/6*( 6-1)=80%;从而证明了,皮带层数越高,阶梯的强度越大。
四、皮带接头长度计算
接头长度或称粘合长度,决定着接头的粘合面积的大小,又决定着接 头 的强度。接头长度过短,即结合面积小,可能保持不了接头强度。接头过 长,粘合面积增大,强度增大并不明显,意义不大、反而造成接头加工困 难和浪费。
经验证明,对于强度要求不高的帆布芯层胶带,其接头长度等于胶带 的 宽度即可。胶带接头的阶梯层数,随着脚的芯层的不同而等,因为这样会 使接头强度损失太大。一般,接头是每个阶梯的最小长度e按表1选取。实 践证明,表中e值有些偏大,最好通过试验,然后计算来确定其接头长度。
皮带胶接工艺培训资料

皮带胶接工艺培训资料
一、引言
近年来,随着工业的发展和需求的增加,皮带胶接工艺在传输
材料和产品的行业中扮演着重要的角色。
皮带胶接工艺是一种将两
个或更多皮带连接在一起的方法,以形成连续传输材料的过程。
本
文将介绍皮带胶接的基本原理、工艺步骤以及常见的故障及其解决
方法。
二、皮带胶接的基本原理
皮带胶接是通过使用特殊的胶水将两个或多个皮带连接在一起。
此工艺的基本原理在于将胶水涂布在皮带的连接部分上,并将其加热,使其固化。
固化后的胶水将两个皮带牢固地连接在一起,以实
现传输材料的连续运输。
三、皮带胶接的工艺步骤
1. 准备工作
在进行皮带胶接之前,首先需要准备好以下工具和材料:
- 皮带胶
- 清洁剂
- 刮刀和刷子
- 加热装置
2. 清洁皮带表面
使用清洁剂将待胶接的皮带表面清洁干净,以确保胶水可以牢固地附着在皮带上。
清洁时要注意避免使用含有溶剂的清洁剂,以免造成皮带损坏。
3. 涂布胶水
使用刮刀或刷子将胶水均匀地涂布在待胶接的皮带表面上。
涂布时要确保胶水的厚度和面积适中,以免影响胶接强度。
4. 加热胶接部分
使用加热装置,对已涂布胶水的皮带进行加热。
加热的温度和时间要根据所使用的胶水类型和厂家的建议进行控制。
加热过程中要注意保持适当的温度和时间,避免过度加热导致胶接效果不佳。
5. 胶接。
皮带胶接岗位安全技术规程(3篇范文)
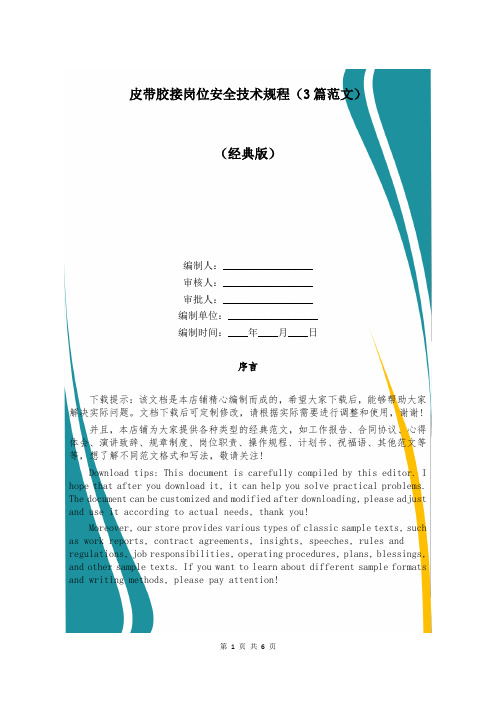
皮带胶接岗位安全技术规程(3篇范文)(经典版)编制人:__________________审核人:__________________审批人:__________________编制单位:__________________编制时间:____年____月____日序言下载提示:该文档是本店铺精心编制而成的,希望大家下载后,能够帮助大家解决实际问题。
文档下载后可定制修改,请根据实际需要进行调整和使用,谢谢!并且,本店铺为大家提供各种类型的经典范文,如工作报告、合同协议、心得体会、演讲致辞、规章制度、岗位职责、操作规程、计划书、祝福语、其他范文等等,想了解不同范文格式和写法,敬请关注!Download tips: This document is carefully compiled by this editor. I hope that after you download it, it can help you solve practical problems. The document can be customized and modified after downloading, please adjust and use it according to actual needs, thank you!Moreover, our store provides various types of classic sample texts, such as work reports, contract agreements, insights, speeches, rules and regulations, job responsibilities, operating procedures, plans, blessings, and other sample texts. If you want to learn about different sample formats and writing methods, please pay attention!皮带胶接岗位安全技术规程(3篇范文)【第1篇】皮带胶接岗位安全技术规程1、检查所使用的工具是否完好,不得勉强使用。
皮带胶接工艺培训资料

皮带胶接工艺培训资料一、前述皮带的连接方法有机械连接法和胶接法,胶接法又分冷接法和热接法。
机械连接法是用机械扣子将运输皮带的两个头扣接起来的方法;冷接法是用“黄时得”等液体胶水粘接的方法,热接法是用电热胶带系列硫化机升温加压硫化的方法。
对比之下热接法不仅接头光滑,并几乎与原带无异,能减少对滚筒的磨损和延长运输机及运输带的使用寿命,大大增加了原胶带的拉力强度;故此主讲热接法的DRJL系列电热胶带硫化法。
二、胶带接口工艺1、多层带接口参数lBN-------帆布层数N-1-----为台阶数(我们通常定为6个台阶数)l--------每层台阶长度(mm)(根据硫化机有效宽度而定,我们通常取100)在胶粘剂选定后,层间粘合强度一定,l长度主要取决于单层带芯帆布的强度,强度越高l越长。
通常取在100-400mm之间(见表)B--------胶带宽度(mm)a--------斜角角度,一般tga=0.3-0.5大有利于应力分布均匀,但加工胶带损耗大。
据有关资料介绍,德国取tga=0.3(a=16°42′);英国取tga=0.5(a=26°)日本取a=22°;我国有取30°,经综合分析我们取硫化机隔热板两个相邻边的锐角。
2、接口加工步骤2.1下部接口台阶加工加工前准备胶带两端互相搭接时要使上部胶带与运行方向一致,并标出上部胶带和下部胶带的记号。
在胶带端部划垂直于运行方向的的直线,用硫化机隔热板划出与胶带边缘呈与硫化机隔热板相同的锐角的斜线。
加工要点:a、根据我矿硫化机(DRJL-1200)或(DRJL-1000)的加热盘宽度,确定L=600mm(即6台阶,每台阶长l=100mm);b、根据胶带的帆布层数合理匀分每台阶帆布层数;c、剥层及修边,若是钢丝皮带剥层走向应与钢丝走向一致;上部接口台阶加工2.2胶带两端与边胶定位线为准互相叠放,下部胶带的最上层帆布承接上部胶带的斜块段,加工方法如下部胶带加工,其基本止标是始终准备地保证帆布层台阶的尺寸。
皮带胶接(硫化)作业指导书.doc

皮带胶接(硫化)作业指导书1目的1.1规范检修行为,确保输煤胶带接头在胶接后符合规定要求1. 2本作业指导书为所有参加本项目的工作人员所必须遵循的质量保证程序2适用范围木作业指导书适用于EP-300 1200 /1400/1600X5层输煤胶带接头在生产现场的热硫化胶接,其他胶带可参照执行。
3引用文件本程序引用《燃燃运检修规程C版》、《燃料设备运行与检修技术问答》、《胶带硫化机使用说明书》、《电力生产安全规程》。
4定义硫化粘接工艺5设备概述输煤胶带的接头是将胶带的布层和胶层,按一定形式和角度剖切成对称差级,涂以胶浆使其粘连,然后在一定压力、温度条件下加热一定时间,经过硫化反应后,生橡胶变成硫化橡胶,从而获得接头部位较高的粘着强度。
此种方法所得接头强度可达原胶带的85、90%。
5层胶带接头的阶梯形式采用直角形式,接头长度为,每阶梯长度及斜角接头角度如下表:6修前准备6. 1检修计划工期天人员要求6.2.1工作人员应是从事燃料检修人员,并且通过安规考试及技能资格审查。
6.2.2工作负责人组织得当、分工明确,对安全和质量负责。
6.2.3指定专人做好记录,确保记录真实、准确、工整。
6. 3安全措施6.3. 1. 1办理工作票6.3. 1.2进入现场穿工作服,戴好安全帽,高空作业系好安全带。
6.3. 1.3开工前,工作负责人要向工作人员详细交待安全措施及注意事项,明确工作范围。
6. 3. 1.4工作人员禁止接触运行中的设备。
6. 3. 1. 5使用手提电动钢丝轮时应戴防护眼睛。
6.3. 1.6工作现场严禁动火作业。
6.4 质量控制点汇总6. 5备品备件*材料6. 6工器具电热硫化机一套、常用扳手、皮带刀、胡桃钳、手提电动钢丝轮机、手锤、皮带起子、钢直尺、皮尺(100米)、专用平台2台、5吨链条葫芦2 只、2吨链条葫芦2只、钢丝绳、皮带夹板、胶皮锤、胶盆、毛刷、碘鹄灯。
6. 7 设置【检修场地6. 7.1清理接头附近的场地,以便于胶带放置和电源接线方便,若在露天作业还应搭一临时防雨棚;施工地点温度控制在20〜40°C,和对湿度不超过80%,施工地点不应有灰尘。
皮带胶接工艺培训
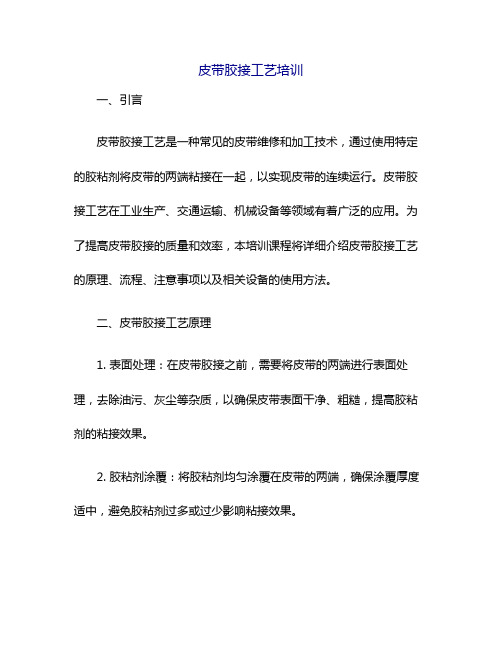
皮带胶接工艺培训一、引言皮带胶接工艺是一种常见的皮带维修和加工技术,通过使用特定的胶粘剂将皮带的两端粘接在一起,以实现皮带的连续运行。
皮带胶接工艺在工业生产、交通运输、机械设备等领域有着广泛的应用。
为了提高皮带胶接的质量和效率,本培训课程将详细介绍皮带胶接工艺的原理、流程、注意事项以及相关设备的使用方法。
二、皮带胶接工艺原理1. 表面处理:在皮带胶接之前,需要将皮带的两端进行表面处理,去除油污、灰尘等杂质,以确保皮带表面干净、粗糙,提高胶粘剂的粘接效果。
2. 胶粘剂涂覆:将胶粘剂均匀涂覆在皮带的两端,确保涂覆厚度适中,避免胶粘剂过多或过少影响粘接效果。
3. 粘接:将涂覆胶粘剂的两端对接在一起,施加适当的压力,使胶粘剂充分渗透到皮带纤维中,形成牢固的粘接。
4. 固化:将粘接好的皮带放置在适当的温度和湿度条件下进行固化,使胶粘剂完全固化,提高皮带胶接的耐久性和稳定性。
三、皮带胶接工艺流程1. 表面处理:使用清洗剂或砂纸等工具对皮带的两端进行清洗和打磨,去除油污、灰尘等杂质,确保皮带表面干净、粗糙。
2. 胶粘剂选择:根据皮带的材质和工作环境选择合适的胶粘剂,并按照说明书进行调配。
3. 胶粘剂涂覆:将调配好的胶粘剂均匀涂覆在皮带的两端,确保涂覆厚度适中,避免胶粘剂过多或过少影响粘接效果。
4. 粘接:将涂覆胶粘剂的两端对接在一起,施加适当的压力,使胶粘剂充分渗透到皮带纤维中,形成牢固的粘接。
5. 固化:将粘接好的皮带放置在适当的温度和湿度条件下进行固化,使胶粘剂完全固化,提高皮带胶接的耐久性和稳定性。
6. 检查:固化完成后,对皮带胶接部位进行检查,确保粘接牢固、无气泡、无裂纹等缺陷。
四、注意事项1. 表面处理要彻底,确保皮带表面干净、粗糙,以提高胶粘剂的粘接效果。
2. 选择合适的胶粘剂,并按照说明书进行调配,确保胶粘剂的性能符合要求。
3. 涂覆胶粘剂要均匀,避免胶粘剂过多或过少影响粘接效果。
4. 粘接时要施加适当的压力,使胶粘剂充分渗透到皮带纤维中,形成牢固的粘接。
皮带胶接工艺培训资料
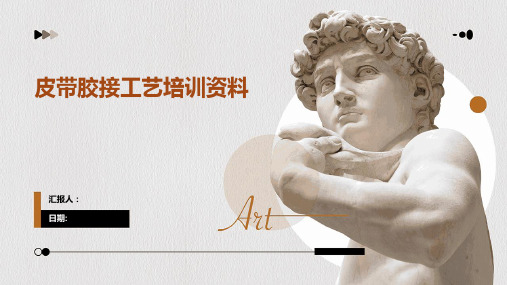
高效快速
由于胶粘剂的粘接强度高,因此皮带胶接工艺可以提供可靠的连接效果,确保皮带的正常运行。
连接可靠
皮带胶接工艺适用于各种类型的皮带,可以适应不同的使用环境和工况条件。
准备个人防护
加压粘合
将晾干的皮带放置在胶接设备中,加压加热一定时间,直至皮带完全粘合。
晾干
将涂抹好胶液的皮带放置在通风处晾干,避免阳光直射。
上胶
将胶液均匀涂抹在皮带表面,确保涂抹均匀、无气泡。
清洁表面
使用清洁剂擦拭皮带表面,去除灰尘和污垢。
配胶
按照胶接设备的说明书调配胶液。
检查皮带粘合部位是否平整、牢固,如有缺陷应及时处理。
01
02
03
04
原因可能是胶粘剂选择不当、胶接工艺执行不严格、胶接面清洁度不足等。
原因可能包括皮带材料缺陷、过载使用、长时间疲劳等。
原因可能是皮带轮不对中、轴承损坏、传动系统不平衡等。
原因可能是摩擦系数过大、接触面不平整、运行速度不稳定等。
包括皮带和胶粘剂等原材料的质量,确保符合工艺要求和产品质量标准。
遵守法律法规
03
工具使用不当
容易造成工伤,应选用合适的工具,避免使用不合适的工具。
01
电源开关未及时关闭
容易造成电击事故,应定期检查电源开关是否处于关闭状态。
02
操作过程中注意力不集中
容易造成设备损坏或人身伤害,应保持专注,避免分心。
企业应定期对员工进行皮带胶接工艺的安全操作规程培训,确保员工掌握安全操作规程。
定期对设备进行润滑保养,延长其使用寿命。
若设备出现故障,应立即停机并联系维修人员检查维修。
皮带胶接作业标准程序

皮带胶接作业标准程序设备名称#4B皮带机作业名称皮带撕裂修复序号作业步骤作业内容技术标准1 准备工作◆皮带上的余煤处理干净;◆备品备件材料及工器量具准备齐全;◆计量器具是否准确;◆检查起重设备是否完好、可靠;◆将皮带接头部分转到上面;◆安全措施完善;◆工作票已签证;2 粘接前的准备◆将配重吊起,放松皮带;◆将皮带接头处托辊架拆卸下来,有序放置;◆接头处将工作平台准备好;◆根据截去皮带的长度加上余量4米,下25米阻燃耐寒新皮带;◆在要截取皮带的两侧打皮带卡子固定皮带;◆截去皮带接头及破损皮带;◆吊运并铺设皮带;3 皮带的粘接◆划线:◆将胶带平整放置在工作台上,接头部位擦拭干净,划出两接头中心线、基准线、切断线、切割线、边胶切割线及芯胶切口线、阶梯节距线。
◆注意:接头的上下搭接方向◆工作面的接口应与胶带的运行方向相反◆斜切角度20º;◆共五层台阶,每个台阶长度为300mm;◆边胶宽度为20mm;◆裁剥:◆按照尺寸线裁断、斜切、剥离,注意裁刀不能割伤下层帆布。
◆裁剥时先将边胶留下,待裁剥完后将边胶按照台阶高度修出;◆盖胶要修出45º坡度◆打毛:◆用钨钢打磨碟或电动钢丝轮清除帆布带接头阶梯面的残留胶,注意避免发生擦亮、打光或产生烧焦现象。
◆决不允许伤到布层;◆凡是要粘结的部位都要打毛,不允许有光面;◆接头阶梯配合:◆将两头相叠,检查其接头分层是否相互精确配合,若不准确进行修正。
◆接头分层相互精确配合,且中心线重合;◆涂胶:◆将粘接剂SC2000与UT-R20硬化剂按照100:4的比例混合并充分搅拌均匀(混合后两小时内必须用完,否则硬化失效)。
◆先用毛刷清干净剥离层,然后涂胶两遍。
第一次要干透后,才能涂下一次胶。
◆第一层须完全干透,并达到不再粘附手指背的程度,第二层干到尚有略微粘性时(用手指背试)即可进行表面的最后粘接;◆不允许用水或化学溶剂进行清洗;◆未混合的粘接剂及硬化剂硬密封完好,置于阴凉干燥处保存;◆贴合:◆胶粘手时,将两头贴合,应使胶带两边松紧程度一致,各接头阶梯对齐,中心线对准,从皮带中间向两边贴合,以利于空气从两边逸出。
- 1、下载文档前请自行甄别文档内容的完整性,平台不提供额外的编辑、内容补充、找答案等附加服务。
- 2、"仅部分预览"的文档,不可在线预览部分如存在完整性等问题,可反馈申请退款(可完整预览的文档不适用该条件!)。
- 3、如文档侵犯您的权益,请联系客服反馈,我们会尽快为您处理(人工客服工作时间:9:00-18:30)。
接头质量应保证使用一年以上,其间不发生空 洞、翘边等不良现象
热硫化胶接注意事项
胶浆浓度不易过大,以便渗透布层。 胶浆为汽油泡制,远离火源,注意安全。
胶片在放卷过程中,应尽量轻拉放卷以避免胶 片变薄,硫化时填充量不足,影响粘接质量。
胶片和胶浆生产后应尽快用于胶带的粘接,以 取得最佳效果。胶片的存放有效期为三个月, 最佳粘合期为一个月,存放温度25℃以下;胶 浆的存放期为15天,一般存放温度以10~20℃ 为宜。
调整胶带两边的松紧程度,按中心线贴合接头, 并以覆盖胶填充封口处。 加热硫化:压力不小于0.5MPa,温度135℃- 145℃,恒温时间25―40分钟。
冷硫化胶接法
冷硫化胶接工艺与热硫化胶接类似,不同之 处在于采用专门的胶黏剂(天然胶、氯丁胶)在 常温、常压下硫化,现场施工比较方便。 冷硫化胶接与热硫化胶接在工艺要求上的主 要区别有以下几点: 接头角度:多采用直角。 打磨:必须将残余橡胶打磨干净。 贴合:贴合处必须严密,缝隙小于1mm,否则 影响外观和质量。 施工环境:温度20℃―40℃,相对湿度小于80%, 现场无飞尘。
输送带胶接工艺
皮带冷热交接及工艺要求
第一节 工艺流程
主要工序
将胶带接口或待更换部分转至适宜接口工作的 位置。 设备停电,做好防止转动措施。
用起吊工具将配置拉起或将张紧装置松开,提 升高度或松开量视皮带接头需要量而定,一般 标准为皮带胶接完成后,张紧装置行程量不小 于3/4拉紧额定行程。 皮带接头两侧用皮带卡子与皮带架固定,使接 头处皮带呈松弛状态。
按照胶接头制做工艺完成胶接头(第二节详细 阐述)。 拆除卡子,张紧装置拉紧。 清理现场,设备交付使用。
第二节 皮带胶接头的制做方法
机械连接法
一般采用钩卡(搭扣)连接。搭扣为多爪状, 用锤楔入皮带两端,穿入柱销后即成;
这种方法对胶带强度削弱很大,只能达到胶带 本身强度的35% — 40%;
总结
要求高强度、较低的定伸应力和硬度时,硫化 温度可选择较低一些,反之硫化温度宜采用高 一些。
橡胶属于热的不良导体,受热升温较慢。采用 高温硫化很难使内外层胶料同时达到平坦范围, 从而内部出现欠硫化,或者内部恰好出现正硫 化时,而外部已过硫化。为了保证硫化均匀, 在选择硫化温度时,可考虑硫化温度低一些或 采用逐步升温的操作方法。 天然橡胶胶带硫化温度一般控制在145±2℃, 恒温时间30分钟,压力不低于0.5MPa。调整硫 化温度应对应调整恒温时间。
过硫阶段:正硫阶段之后,继续硫化便进入过 硫阶段。这一阶段的前期属于硫化平坦期的一 部分。在平坦期中,硫化胶的各项物理机械性 能基本上保持稳定。当过平坦期之后,天然橡 胶和丁基橡胶由于断链多于交联出现“硫化返 原”现象而变软;合成橡胶则因交联继续占优 势和环化结构的增多而变硬,且伸长率也随之 降低,橡胶性能受到损害。
硫化过程的四个阶段
硫化起步阶段(又称焦烧期或硫化诱导期): 硫化起步的意思是指硫化时间胶料开始变硬而 后不能进行热塑性流动那一点的时间。在这一 阶段内,交联尚未开始,胶料有良好的流动性。 胶料硫化起步的快慢,直接影响胶料的焦烧和 操作安全性。这一阶段的长短取决于所用配合 剂,特别是促进剂的种类。用有超速促进剂的 胶料,其焦烧比较短,此时胶料较易发生焦烧, 操作安全性差;在使用迟效性促进剂时,可取 得较长的焦烧期和良好的操作安全性。在大多 数情况下,希望有较长的焦烧时间以保证操作 的安全性。
思 考 题
胶带胶接头制做的质量要求有哪些?
热硫化与冷硫化胶接在工艺上的主要区别 有哪些? 热硫化胶接三要素是什么? 对于天然橡胶制成的胶带,硫化三要素通 用标准是什么?
在胶带裁剥之前,划出待接胶带两端的宽度中心线, 以便对齐找正。 对于1200-1400mm宽的胶带,裁剥台阶个数一般为胶 带层数-1,长度150-200mm,接头长度为带宽的50% -100%,角度一般为23o、63.5o、71.5o、90o。
裁剥后的打磨:清扫裁剥处残余胶屑,毛糙带 芯表面,需控制力度,不要损伤带芯。胶带接 头两侧边和覆盖胶接头斜面也要打磨粗糙。 涂胶:涂1-2遍稀胶浆(每遍需待前次胶浆 干),待胶浆干至不沾手时铺一层芯胶片。
正硫阶段:大多数情况下,制品在硫化时都必须使之 达到适当的交联度,达到适当的交联度的阶段叫做正 硫化阶段,即正硫阶段。在此阶段,硫化胶的各项物 理机械性能并非在同一时都达到最高值,而是分别达 到或接近最佳值,其综合性能最好。此阶段所取的温 度和时间称为正硫化温度和正硫化时间。 正硫化时间 须视制品所要求的性能和制品断面的厚薄而定。要求 抗撕裂性好的制品,应考虑抗撕强度最高或接近最高 值的硫化时间定为正硫化时间;要求耐磨性高的制品, 则可考虑磨耗量小的硫化时间定为正硫化时间。 在选择正硫时间时,尚需将“后硫化”考虑进去。 所谓“后硫化”,即是当正硫化完成以后,由于橡胶 导热性差,传热时间长,制品因散热而降温也就较慢, 所以它还可以继续进行硫化,特将它称为“后硫化”。 “后硫化”导致的抗张强度和硬度进一步增加,弹性 和其它机械性能降低。所以,制品越厚就越应将“后 硫化”的影响考虑进去。
抗张强度:抗张强度与定伸强度和硬度不同, 它不随交联键数目的增加而不断地上升,当交 联度达到适当值后,如若继续交联,其抗张强 度反会下降。 伸长率和永久变形:橡胶的伸长率随交联度的 增加而降低,永久变形也有同样的规律。有硫 化返原性的橡胶如天然橡胶和丁基橡胶,在过 硫化以后由于交联度不断降低,其伸长率和永 久变形又会逐渐增大。 弹性:橡胶硫化后,交联使分子或链段固定, 形变受到网络的约束,外力作用消除后,分子 或链段力图回复原来构象和位置,所以硫化后 橡胶表现出很大的弹性。交联度的适当增加, 这种可逆的弹性回复表现得更为显著。
第三节 热硫化质量控制
关于橡胶的几个基本概念
定伸强度:通过硫化,橡胶单个分子间产生交 联,且随交联密度的增加,产生一定变形(如 拉伸至原长度的200%或300%)所需的外力就随 之增加,硫化胶也就越硬。 这说明交联度大, 定伸强度也就越高。
硬度:与定伸强度一样,随交联度的增加,橡 胶的硬度也逐渐增加,有关定伸强度的概念基 本适用于硬度。
从实践来看,由于冷硫化胶接工艺条件 比较难掌握,另外粘合剂的质量对接头的 影响非常大,所以不是很稳定。
胶带冷胶接的质量标准
胶带各台阶等分的不均匀度小于1mm 裁剥时对下层带芯的误割深度不得大于带芯厚 度的50%,每个台阶误损长度不超过全长10%
打磨对带芯的毛糙或误损不超过带芯厚度的 25% 接头处胶带边缘应为直线,直线度小于0.3%
欠硫阶段(又称预硫阶段):硫化起步与正硫 化之间的阶段称为欠硫阶段。在此阶段,由于 交联度低,橡胶制品应具备的性能大多还不明 显。尤其是此阶段初期,胶料的交联度很低, 其性能变化甚微,制品没有实用意义。但是到 了此阶段的后期,制品轻微欠硫时,尽管制品 的抗张强度、弹性、伸长率等尚未达到预想的 水平,但其抗撕裂性耐磨性和抗动态裂口性等 则优于正硫化胶料。因此,如果着重要求后几 种性能时,制品可以轻微欠硫。
压力:促使胶料流动,防止胶料气泡的产生, 提高胶料的致密性 ,提高附着力,改善硫化胶 物理性能 。压力越高,胶带拉伸强度越高,扯 断伸长率降低,抗撕裂强度降低。
拉伸强度与压力的关系图 扯断伸长率与压力的关系图
时间:硫化时间的设定是根据胶带的厚度及操 作要求来设定的。因为橡胶的导热性是很差的, 胶带越厚硫化时间越长。薄制品硫化时间太长 是对生产力及能源的浪费,还可能造成过硫; 厚制品硫化时间太短,外焦里不熟,影响产品 质量。 为了提高硫化速度一般有两种方法:首先 是加温,再一种是增加促进剂用量或改用超速 促进剂。加温物性要求不高的情况下是可以考 滤的,但很难控制。按理论计算每提高10度硫 化时间约缩短一半时间,提高温度也应该按这 样推算应提高多少温度。
硫化三要素对胶带性能的影响
温度:硫化温度是硫化三要素之首,是橡胶进 行硫化反应(交联反应)的基本条件,直接影 响橡胶硫化速度和制品的质量。与所有化学反 应一样,硫化反应随着温度升高而加快,温度 每上升8~10℃,其反应速度约增加一倍,即反 应时间约减少一半。 硫化温度决定于橡胶的品种,如天然橡胶 的最佳硫化温度为145-148度,丁苯胶的最佳硫 化温度为148—153度。在实际操作时应考虑温 差,调节温度在这个基础一般加3-5 度左右。 从提高硫化效率来说,硫化温度越高越好, 但考虑到橡胶的耐热性和“硫化返原”现象, NR(天然橡胶) 最好在140-150℃,最高不超 过160℃。
因其作业速度快,一般作为应急措施,或者作 为硫化胶接前的准备工作。
热硫化胶接法
将胶带接头一部分的带芯和胶层,按一定形 式和角度剖切成对称差级,通过胶浆、胶片粘连, 然后在一定的温度、压力条件下加热一段时间, 使得胶片、胶浆发生硫化反应获得较高的连接强 度。这种方法获得的胶接头强度可达原胶带强度 的85% — 90%。 工艺流程如下: