TPM是Total-Productive-Maintenance-第一个字母的缩写-本意是
公司常用中英文对照缩写 (2)
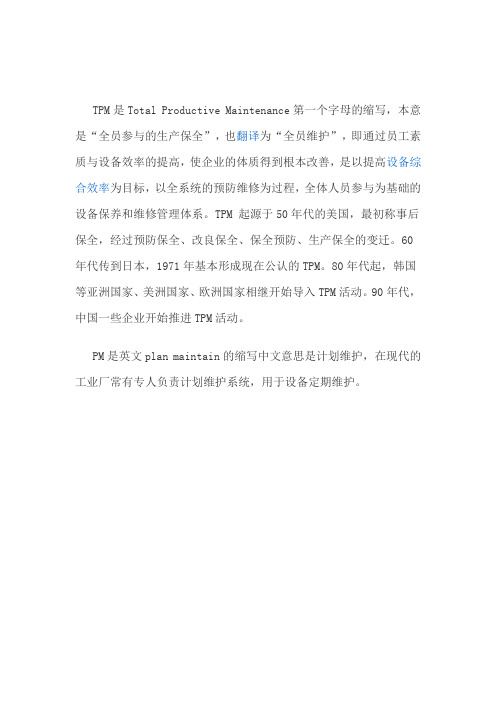
TPM是Total Productive Maintenance第一个字母的缩写,本意是“全员参与的生产保全”,也翻译为“全员维护”,即通过员工素质与设备效率的提高,使企业的体质得到根本改善,是以提高设备综合效率为目标,以全系统的预防维修为过程,全体人员参与为基础的设备保养和维修管理体系。
TPM 起源于50年代的美国,最初称事后保全,经过预防保全、改良保全、保全预防、生产保全的变迁。
60年代传到日本,1971年基本形成现在公认的TPM。
80年代起,韩国等亚洲国家、美洲国家、欧洲国家相继开始导入TPM活动。
90年代,中国一些企业开始推进TPM活动。
PM是英文plan maintain的缩写中文意思是计划维护,在现代的工业厂常有专人负责计划维护系统,用于设备定期维护。
ERP: (Enterprise Resource Planning)企业资源规划(ERP是什么?)CRM : (Customer Relationship Management)客户关系管理KM :(Knowledge Management)知识管理MRP : (Material Requirement Planning)物料需求规划MRPII : (Manufacturing Resource Planning) 制造资源计划SCM : (Supply Chain Management)供应链管理BOM Bill of Material 资材传票BPR Business Process Reengineering 业务程序在设计CE Concurrent Engineering 同时进行工程管理CIM Computer Integrated Manufacturing 计算机加工一体化CRP Capacity Requirement Planning 能力需求计划DSS Decision Support System 协助决裁系统DW/DM Data Warehouse/Data Marketing 数据库/市场EC Electronic Commerce 电子商业EDI Electronic Data Interchange 电子资料交流EDMS Electronic Document Management System 电子文件管理体系EHS Environment Health & Safety 环境卫生安全EI Enterprise Integration 企业一体化EIS Executive Information System 信息执行体系EMS Electricity Management System 电力管理体系ERP Enterprise Resource Planning 企业资源计划FMS Flexible Manufacturing System 灵活的生产体系FP Factory Planning 工厂计划GDMS Global Data management System 全球数据管理体系IDB Integrated Data Base 集成数据IMS Intelligent Manufacturing System 可微机控制的生产体系ISP Information Strategic Planning 信息战术计划KBS Knowledge Base System 知识管理体系KMS Knowledge Management System 文化管理体系MES Manufacturing Execution System 生产加工执行体系MIS Management Information System 信息管理体系MMS Maintenance Management System 维护管理体系MP Master Planning 主要计划MPS Master Production Schedule 主要生产安排MRP Material Requirement Planning 资材需求计划PDM Product Data Management 生产数据管理PI Process Innovation 工艺改进POP Point of Production 生产管理QFD Quality Functional Deployment 质量功能开发QMS Quality Management System 质量管理体系RCCP Rough Cut Capacity Planning 粗能力计划SCADA Supervisory Computer And Data Acquisition 计算机管理及数据的获取SCM Supply Chain Management 信息渠道管理SCOR Supply Chain Operations Reference 供应渠道管理SFC Shop Floor Control 车间地面控制SOP Sales & Operations Planning 销售及运行计划SPC Statistical Process Control 统计数据控制SQM Standard Quality Management 标准质量管理UMS Utility Management System 应用程序管理VPD Virtual Product Development 实质产品开发BOM : (Bill Of Material)物料清单DPS:详细生产排程(DPS)5S : 5S管理ABC : (Activity-Based Costing) 作业制成本制度ABB : (Activity-Based Budgeting) 实施作业制预算制度ABM : (Activity-Base Management)作业制成本管理(Activity-Base Management)APS : (Advanced Planning and Scheduling)先进规画与排程系统ASP :(Application Service Provider)应用程序服务供货商ATP : (Ava il ab le T o Pro mi se)可承诺量AVL : (Approved Vendor List)认可的供货商清单BPR : (Business Process Reengineering)企业流程再造BSC : (Balanced ScoreCard)平衡记分卡BTF : (Build To Forecast)计划生产BTO : (Build To Order)订单生产CPM : (Critical Path Method)要径法CRP : (Capacity Requirements Planning)产能需求规划CTO : (Configuration To Order)客制化生产DBR : (Drum-Buffer-Rope)限制驱导式排程法DMT : (Design Maturing Testing)成熟度验证DVT : (Design Verification Testing)设计验证DRP : (Distribution Resource Planning)运销资源计划DSS : (Decision Support System)决策支持系统EC : (Engineer Change)设计变更/工程变更EC : (Electronic Commerce)电子商务ECRN : (Engineer Change Request Notice)原件规格更改通知EDI : (Electronic Data Interchange)电子数据交换EIS : (Executive Information System)主管决策系统EMC : (Electric Magnetic Capability)电磁相容EOQ : (Economic Order Quantity)基本经济订购量FAE : (Field Application Engineer)应用工程师FCST : (Forecast)预估FMS : (Flexible Manufacture System)弹性制造系统FQC : (Finish or Final Quality Control)成品质量管理IPQC: (In-Process Quality Control)制程质量管理IQC : (Incoming Quality Control)进料质量管理ISO : (International Organization for Standardization)国际标准组织ISAR: (Initial Sample Approval Request)首批样品认可JIT : (Just In Time)实时管理L4L : (Lot-for-Lot)逐批订购法LTC : (Least Total Cost)最小总成本法LUC : (Least Unit Cost)最小单位成本MES : (Manufacturing Execution System)制造执行系统MO : (Manufacture Order)制令MPS : (Master Production Schedule)主生产排程MRO : (Maintenance Repair Operation)请修(购)单NFCF : Notice for Changing Forecast更改预估量的通知OEM : (Original Equipment Manufacture)委托代工ODM : (Original Design & Manufacture)委托设计与制造OLAP :(On-Line Analytical Processing)在线分析处理OLTP :(On-Line Transaction Processing)在线交易处理OPT : (Optimized Production Technology)最佳生产技术OQC : (Out-going Quality Control)出货质量管理PDCA :(Plan-Do-Check-Action)PDCA管理循环PDM : (Product Data Management)产品数据管理系统PERT: (Program Evaluation and Review Technique)计划评核术PO : (Purchase Order)订单POH : (Product on Hand)预估在手量PR : Purchase Request采购申请QA : (Quality Assurance)品质保证QC : (Quality Control)质量管理QCC : (Quality Control Circle)品管圈QE : (Quality Engineering)品质工程RCCP : (Rough Cut Capacity Planning)粗略产能规划RMA : Returned Material Approval退货验收ROP :(Re-Order Point)再订购点SFC :(Shop Floor Control)现场控制SIS :(Strategic Information System)策略信息系统SO : (Sales Order)订单SOR :(Special Order Request) 特殊订单需求SPC :(Statistic Process Control)统计制程管制TOC : (Theory of Constraints)限制理论TPM : Total Production Management全面生产管理TQC : (Total Quality Control)全面质量管理TQM : (Total Quality Management)全面品质管理WIP :(Work In Process) 在制品客户Customer供应商Supplier仓库Stockroom库存Inventory货品Product型号Part Number销售Sell单据Bill成本Cost交货期Delivery Period采购Purchase采购申请Purchase Requisition采购报价Purchase Quote采购退货Purchase Return采购订单Purchase Order回复交期Purchase Response销售报价Sell Quote销售订单Sell Order销售退货Sell Return销售备货Sell Buffer未完成销售订单Outstanding Sell Order 出库单Stock Out入库单Stock In转仓Stock Transfer锁定Product Hold借货Product Lend收款Collection付款Payment退款Refundment发票Invoice应收帐Account Receivable应付账Account Payable应收帐冲销Account Receivable Write-off应付账冲销Account Payable Write-off冲销Write-off应收账款账龄分析表accounts receivable aging schedule 已转让应收账款accounts receivable assigned应收账款收款期accounts receivable collection period 已贴现应收账款accounts receivable discounted应收账款筹资,应收账款融资accounts receivable financing 应收账款管理accounts receivable management应收账款周转率,应收账款周转次数accountsreceivableturnover 利润Profit会计循环Accounting Procedure/Cycle会计信息系统Accounting information System账户Ledger会计科目Account会计分录Journal entry原始凭证Source Document日记账Journal总分类账General Ledger明细分类账Subsidiary Ledger试算平衡Trial Balance现金收款日记账Cash receipt journal现金付款日记账Cash disbursements journal 销售日记账Sales Journal购货日记账Purchase Journal普通日记账General Journal分批认定法Specific identification加权平均法Weighted average先进先出法First-in, first-out or FIFO后进先出法Lost-in, first-out or LIFO移动平均法Moving average上限Upper limit下限Lower limit订单Order在途On Order在库On Hand审批Approve取消审批Cancel Approved ARI 应收发票ARC 应收贷项通知单ARR 应收账款ARF 应收形式发票API 应付发票APC 应付贷项通知单APP 应付账款CMB 现金管理之银行对账单CMC 现金管理之现金日记账C M A现金管理之分配MMS 物料发货MMR 物料收货MMI 物料库存MMM 物料移库MMP 物料生产MXI 匹配发票MXP 匹配采购订单GLJ 总账日记账POO 采购订单SOO 销售订单PJI 项目投放POR 采购申购。
TPM(TotalProductiveMaintenance)简介

TPM(TotalProductiveMaintenance)简介TotalProductiveMaintenance (全员参与的生产保全 ) 之缩写,TPM简称“全员生产保全”,也有称为“全员生产维护”。
T —— Total 为由经营层至第一线作业者全员参加之 T otal;设备总合效率之 T otal;生产系统全体之寿命周期之 T otal。
PM—— ProductiveMaintenance (生产保全)则为最经济的保养,亦即生产上最经济的保养方法。
按照日本工程师学会(JIPE),TPM有如下的定义:(1)以最高的设备综合效率为目标;(2)确立以设备一生为目标的全系统的预防保全;(3)设备的计划、使用、保全等所有部门都要参加;(4)从企业的最高管理层到第一线职工全体参加;(5)通过开展小组的自主活动来推进生产保全。
TPM的原理TPM的原理TPM的管理特征日本的全员生产保全与原来的生产保全相比,主要突出一个“全”字,“全”有三个含义,即全效率、全系统和全员参加。
所谓的全效率,是指设备寿命周期费用评价和设备综合效率。
全系统即指生产维修的各个侧面均包括在内,如预防维修、维修预防、必要的事后维修和改善维修。
全员参加即指这一维修体制的群众性特征,从公司经理到相关科室,直到全体操作工人都要参加,尤其是操作工人的自主小组活动。
1、目标性:人类的每一项活动都是为了取得一定的效果,达到一定的目标。
TPM管理也不例外,它的目标就是要不断追求企业生产效率的最大化,全面提升企业的综合素质。
具体来讲,TPM管理是通过对设备的六大损失(故障损失、工艺调整损失、突停和空转损失、速度损失、废次品损失、开工损失)和生产现场的一切不良因素实施持续的改善,努力实现“5Z”(零事故、零故障、零缺陷、零库存、零差错)的目标,从而达到最佳的设备综合效率和企业经营效益,提高企业的市场竞争能力和应变能力,最终达成“3S”(员工满意、顾客满意、社会满意)的可持续发展的企业,其目标是明确的。
第1章 TPM概述
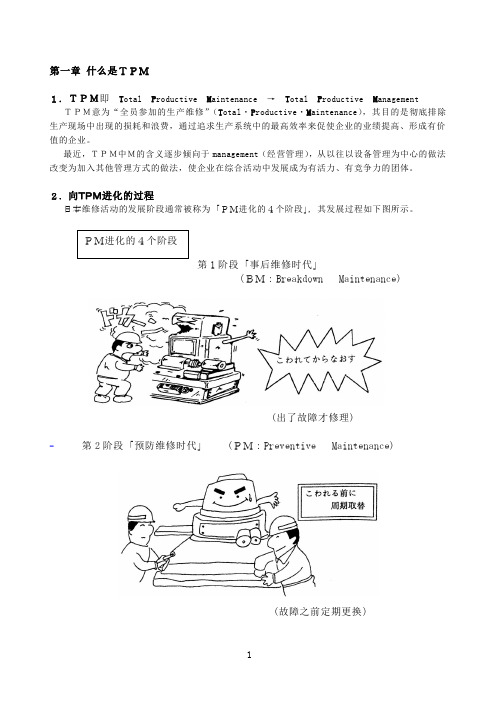
第一章 什么是TPM1.TPM即 T otal P roductive M aintenance → T otal P roductive M anagement TPM意为“全员参加的生产维修”(T otal ・P roductive ・M aintenance ),其目的是彻底排除生产现场中出现的损耗和浪费,通过追求生产系统中的最高效率来促使企业的业绩提高、形成有价值的企业。
最近,TPM中M的含义逐步倾向于management (经营管理),从以往以设备管理为中心的做法改变为加入其他管理方式的做法,使企业在综合活动中发展成为有活力、有竞争力的团体。
2.向TPM进化的过程日本维修活动的发展阶段通常被称为「PM进化的4个阶段」,其发展过程如下图所示。
第1阶段「事后维修时代」(BM:Breakdown Maintenance)(出了故障才修理)- 第2阶段「预防维修时代」 (PM:Preventive Maintenance)(故障之前定期更换)第3阶段「生产维修时代」(PM:Productive Maintenance)(在维持高信赖性、维修性的同时还要争取更多的利润)第4阶段「TPM时代」(TPM:Total Productive Maintenance)详细说明(1)预防维修(PM:Preventive Maintenance)……即设备的健康管理,也可以说是设备的预防医学。
预防医学的发达使人类的疾病得到了有效预防,延长了寿命。
同样,预防维修也是以通过预防设备可能出现的故障(疾病)而最终达到延长其使用寿命的活动。
(2)改良维修(CM:Corrective Maintenance)……对于机器故障防患于未然的想法得到进一步的发展,改良维修就是以不发生故障(提高信赖性)或易于维修(提高维修性)为目的,对设备进行改良的做法。
(3)维修予防(MP:Maintenance Prevention)……新设备在计划阶段即采取不需要维修(maintenance free)的设计方法。
什么是TPM

什么是TPM?全面生产维护(TPM)是一个维护程序的概念。
TPM的全称为Total Productive Maintenance以最大限度提高生产效率为目标以“5S活动”为基础从总经理到一线员工的全体成员为主体以相互连接的小组活动形式以设备及物流为切入点进行思考创造整合有机的生产体系TPM的发展历史:1 事后维修(BM :Breakdown Maintenance)故障后再维护;1950年以前2 改良维修(CM : Corrective Maintenance )查找薄弱部位对其进行改良1950年以后3 预防维修(PM reventive Maintenance)对周期性故障提出的维护1955年前后6 全面生产维护(TPM: Total Productive Maintenance)全员参加型的保养1980年以后5 生产维修(PM: Productive Maintenance)综合上述维护方法,系统的维护方案1960年前后4 维修预防(MP: Maintenance Prevention)设计不发生故障的设备,设备FMEA1960年前后TPM与TQM的关系:TPM是TQM演变而来的.TQM是W.Edwards Deming博士在影响日本工业的直接效果下发展得来.Deming博士是在二战结束不久后在日本开始工作的,作为一个统计学家,他首次向日本人展示了如何在制造过程中使用统计分析和如何在制造过程中使用效果数据来控制质量。
由日本工作理论建立的早期统计程序和效果质量控制概念很快成为日本工业的—种生存方式,这种新的制造概念最终被命名为全面质量管理(TQM)。
当工厂维护的问题作为TQM程序部分被检查出来,一些通用概念看起来在维护环境中就不太适合或不能发挥作用。
原始的TQM概念做了一些修正。
这些调整将维护提升至全面质量管理程序的一个重要部分TPM是一个以制造业领先的创新,强调人的重要性。
一个“能做”和“持续改进”理论、生产的重要性和维护员工共同协作。
tpm是什么

tpm是什么
TPM是Total Productive Maintenance的缩写,意为全面生产维护。
它是一种全面参与员工的生产管理方式,旨在最大化产品生产率、品质和工作效率。
TPM追求全员参与,通过识别和消除造成设备故障、停机和质量问题的根本原因,实现其生产目标。
下面是TPM的几个重要方面:
1. 设备可靠性维护
TPM强调设备可靠性的提高,以预防定期维护之外的故障,保证设备持续运转,最大限度地减少停机时间。
2. 设备效率提高
TPM通过工程控制、生产操作技能和设备管理等方式来实现设备效率的提高,提高其产量和效益,并保证产品质量。
3. 计划性维护
TPM注重对设备的计划性和预防性维护,以减少突发性的问题和需要紧急维修的情况。
4. 全员参与
TPM通过全员参与,以实现彻底的质量管理和效率提高。
所有员工都可以参与到设备的维护、改善、生产和管理中。
5. 标准化工作
TPM强调标准化工作,并通过不断的改进与学习,提高工作效率和质量,从而减少浪费和成本。
总之,TPM是一种重视员工参与、维护设备可靠性和提高效率、通过计划性维护实现生产目标、强调标准化工作、全员参与的生产管理方式。
它可以帮助企业提高生产效率,降低成本,提高产品质量,并提高员工的工作满意度和认同感。
TPM含义
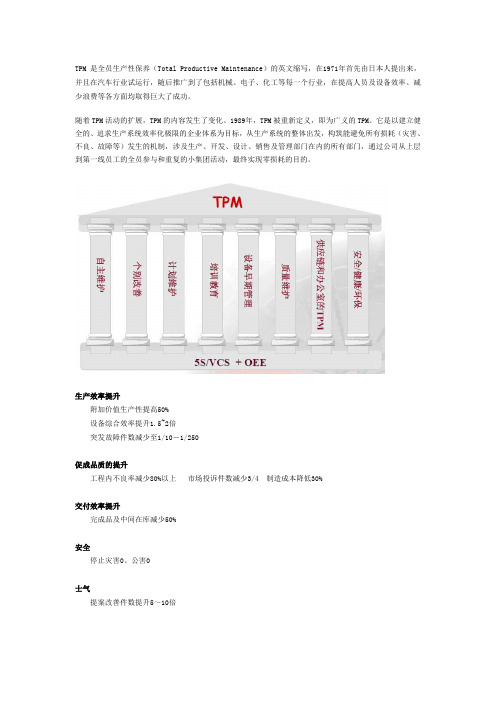
TPM是全员生产性保养(Total Productive Maintenance)的英文缩写,在1971年首先由日本人提出来,并且在汽车行业试运行,随后推广到了包括机械、电子、化工等每一个行业,在提高人员及设备效率、减少浪费等各方面均取得巨大了成功。
随着TPM活动的扩展,TPM的内容发生了变化。
1989年,TPM被重新定义,即为广义的TPM。
它是以建立健全的、追求生产系统效率化极限的企业体系为目标,从生产系统的整体出发,构筑能避免所有损耗(灾害、不良、故障等)发生的机制,涉及生产、开发、设计、销售及管理部门在内的所有部门,通过公司从上层到第一线员工的全员参与和重复的小集团活动,最终实现零损耗的目的。
生产效率提升
附加价值生产性提高50%
设备综合效率提升1.5~2倍
突发故障件数减少至1/10-1/250
促成品质的提升
工程内不良率减少80%以上市场投诉件数减少3/4 制造成本降低30%
交付效率提升
完成品及中间在库减少50%
安全
停止灾害0、公害0
士气
提案改善件数提升5~10倍。
TPM—全员生产保养
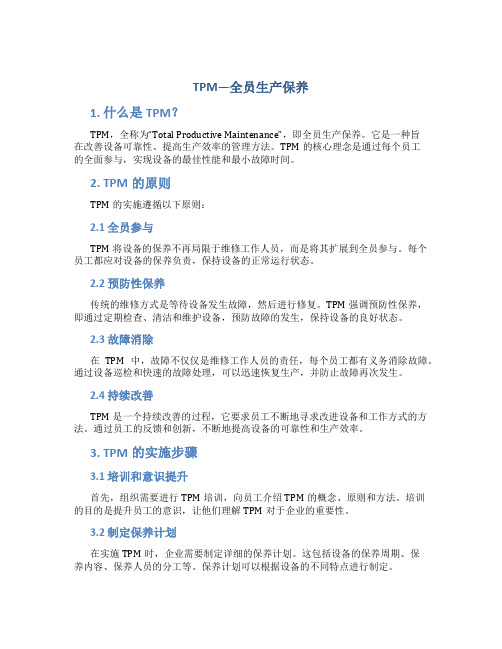
TPM—全员生产保养1. 什么是TPM?TPM,全称为“Total Productive Maintenance”,即全员生产保养。
它是一种旨在改善设备可靠性、提高生产效率的管理方法。
TPM的核心理念是通过每个员工的全面参与,实现设备的最佳性能和最小故障时间。
2. TPM的原则TPM的实施遵循以下原则:2.1 全员参与TPM将设备的保养不再局限于维修工作人员,而是将其扩展到全员参与。
每个员工都应对设备的保养负责,保持设备的正常运行状态。
2.2 预防性保养传统的维修方式是等待设备发生故障,然后进行修复。
TPM强调预防性保养,即通过定期检查、清洁和维护设备,预防故障的发生,保持设备的良好状态。
2.3 故障消除在TPM中,故障不仅仅是维修工作人员的责任,每个员工都有义务消除故障。
通过设备巡检和快速的故障处理,可以迅速恢复生产,并防止故障再次发生。
2.4 持续改善TPM是一个持续改善的过程,它要求员工不断地寻求改进设备和工作方式的方法。
通过员工的反馈和创新,不断地提高设备的可靠性和生产效率。
3. TPM的实施步骤3.1 培训和意识提升首先,组织需要进行TPM培训,向员工介绍TPM的概念、原则和方法。
培训的目的是提升员工的意识,让他们理解TPM对于企业的重要性。
3.2 制定保养计划在实施TPM时,企业需要制定详细的保养计划。
这包括设备的保养周期、保养内容、保养人员的分工等。
保养计划可以根据设备的不同特点进行制定。
3.3 设备巡检和保养根据保养计划,员工需要定期对设备进行巡检和保养。
巡检的目的是发现潜在故障,并及时进行修复。
保养的内容包括清洁设备、更换易损件等。
3.4 故障处理和改善当设备发生故障时,员工需要迅速进行故障处理。
故障处理的目标是恢复生产,并找出故障的原因,避免类似故障再次发生。
此外,员工还应积极提出改善设备的建议。
4. TPM的好处4.1 提高设备可靠性通过TPM的实施,设备的故障率可以明显下降。
TPM基础知识

·每日的对策 ·定期保全 ·预知保全 ·延长寿命的改善 ·备件的管理 ·故障分析和 防止再发 ·润滑管理
·保全基础过程 ·螺钉螺母的安装 ·对齐销子的作业 ·轴承的保全 ·电动零部件的保全 ·防止泄漏作业 ·油压空压机器的 保全 ·电气控制机器的 保全
·开发设计目标的 反 设定 映 ·易于生产 在 ·QA易实现性 设 ·保全性 计 ·可靠性 上 ·LCC的探讨 ·設計:出图 试生产:生产试运行
4。扎扎实实地分步展开 5。系统化与专门技术促进制造业改革 6。通过样本制造标杆
总经理
TPM
副总经理 ①本部会议 ⑥专 技术技能 营业技能 规划管理技能 生产技能
·5S · · 生产 · · ·业务 化
会
·技术 I
总公司
专家 ②推进会议 第一生产事业部 第
第二生产事业部
·专
第 二 制 造 部 部 造 制
创建不需要工人的工作场所
工厂管理与TPM活动的关系
Input Output 人 (Man) 4 Factors for Plant Control (4M Control) 人与设备的体质改善 设 备 (Machine) 原材料 (Material)
管理手法 (Method)
P 产量
(Production)
管 贯 理 计 改 ~ 生 产 个 ~ 运 转 的 ~ 保 全 涯 生 善 整 设 备 穿 设
日 程 进 度 管 理 (Production Planning & Scheduling) 质 量 管 (Quality Control) 成 本 管 (Cost Control) 理
Q C
质量 (Quality) 成本 (Cost) ( eli ery)
1.TPM简介

TPM设备管理什么是TPMTPM含义T otal P roductive M aintenance (全员参与的生产保全 ) 之缩写,TPM简称“全员生产保全”,也有称为“全员生产维护”。
T —— Total 为由经营层至第一线作业者全员参加之 Total;设备总合效率之 Total;生产系统全体之寿命周期之 Total。
PM—— Productive Maintenance (生产保全)则为最经济的保养,亦即生产上最经济的保养方法。
按照日本工程师学会(JIPE),TPM有如下的定义:(1)以最高的设备综合效率为目标;(2)确立以设备一生为目标的全系统的预防保全;(3)设备的计划、使用、保全等所有部门都要参加;(4)从企业的最高管理层到第一线职工全体参加;(5)通过开展小组的自主活动来推进生产保全。
TPM的产生和演变设备管理体制演变TPM起源于1950年代的美国,最初称事后保全,经过预防保全、改良保全、保全预防、生产保全的变迁。
20世纪50年代,美国的制造工业对机械装备的依赖性越来越突出,伴随而来的设备故障率也与日俱增,严重影响着产品品质和生产效率的进一步提高。
为了解决这些问题,美国借助欧洲工业革命的成果把维护设备的经验进行了总结和优化。
将装备出现故障以后采取应急措施的事后处置方法称为“事后保全(Breakdown Maintenance ,BM)”,将装备在出现故障以前就采取对策的事先处置方法称为“预防保全(Preventive Maintenance,PM)”,将为延长装备寿命的改善活动称为“改良保全(Corrective Maintenance ,CM)”,把为了制造不出故障不出不良的装备的活动叫做“保全预防(Maintenance Prevention ,MP)”,最后将以上BM、PM、CM、MP四种活动结合起来称之为“生产保全(Productive Maintenance ,PM)”,从此找到了设备管理的科学方法。
全员生产维修(TPM)
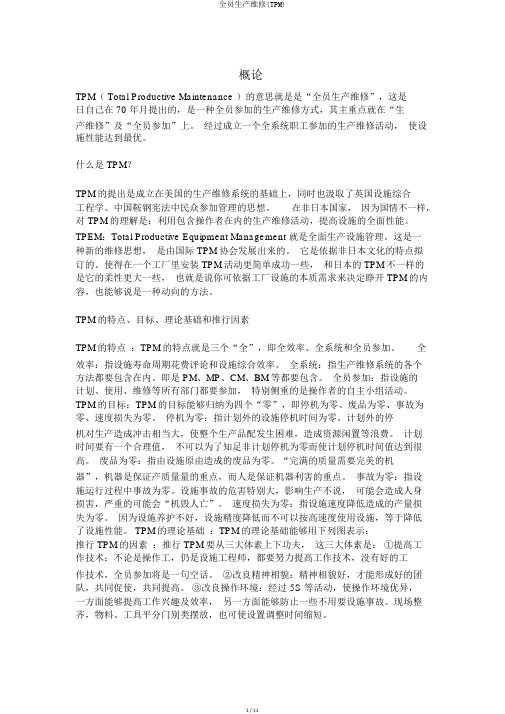
概论TPM( Total Productive Maintenance )的意思就是是“全员生产维修”,这是日自己在 70 年月提出的,是一种全员参加的生产维修方式,其主重点就在“生产维修”及“全员参加”上。
经过成立一个全系统职工参加的生产维修活动,使设施性能达到最优。
什么是 TPM?TPM的提出是成立在美国的生产维修系统的基础上,同时也汲取了英国设施综合工程学、中国鞍钢宪法中民众参加管理的思想。
在非日本国家,因为国情不一样,对 TPM的理解是:利用包含操作者在内的生产维修活动,提高设施的全面性能。
TPEM:Total Productive Equipment Management 就是全面生产设施管理。
这是一种新的维修思想,是由国际 TPM协会发展出来的。
它是依据非日本文化的特点拟订的。
使得在一个工厂里安装 TPM活动更简单成功一些,和日本的 TPM不一样的是它的柔性更大一些,也就是说你可依据工厂设施的本质需求来决定睁开 TPM的内容,也能够说是一种动向的方法。
TPM的特点、目标、理论基础和推行因素TPM的特点:TPM的特点就是三个“全”,即全效率、全系统和全员参加。
全效率:指设施寿命周期花费评论和设施综合效率。
全系统:指生产维修系统的各个方法都要包含在内。
即是 PM、MP、CM、BM等都要包含。
全员参加:指设施的计划、使用、维修等所有部门都要参加,特别侧重的是操作者的自主小组活动。
TPM的目标:TPM的目标能够归纳为四个“零”,即停机为零、废品为零、事故为零、速度损失为零。
停机为零:指计划外的设施停机时间为零。
计划外的停机对生产造成冲击相当大,使整个生产品配发生困难,造成资源闲置等浪费。
计划时间要有一个合理值,不可以为了知足非计划停机为零而使计划停机时间值达到很高。
废品为零:指由设施原由造成的废品为零。
“完满的质量需要完美的机器”,机器是保证产质量量的重点,而人是保证机器利害的重点。
事故为零:指设施运行过程中事故为零。
关于TPM管理

关于TPM管理一、什么就是TPM管理TPM就是Total Productive Maintenance 第一个字母的缩写,本意就是“全员参与的生产保全”,也翻译为“全员维护”,即通过员工素质与设备效率的提高,使公司的体质得到根本改善。
TPM 起源于50年代的美国,最初称事后保全,经过预防保全、改良保全、保全预防、生产保全的变迁。
60年代传到日本,1971年基本形成现在公认的TPM。
80年代起,韩国等亚洲国家、美洲国家、欧洲国家相继开始导入TPM咨询活动。
90年代,中国一些公司开始推进TPM咨询活动。
至今在全球得到了广泛的应用与推广并取得了巨大的成功,包括日本、欧洲、北美以及韩国等地的公司。
目前,TPM管理还在持续的发展,它作为公司降低生产成本,提高生产效率,改善公司经营管理,强化公司竞争力的有效工具发挥着积极的作用。
TPM管理已成为设备管理与维修的先进模式与当代公司管理的重要组成部分。
二、为什么要导入TPM管理辅导公司及推行效果TPM就是一项以预防或预知对策型为主的不断向上的改善活动。
一方面,TPM与TQC、ISO没有任何冲突,三者可以有效地结合,相互促进,共同提高。
另一方面,由于TPM就是一项公司内部的变革,因此,它既不至于出现TQC推动力不足的问题,又可以避免ISO外部认证过程中过多地追求对证书的获得,而忽视对公司品质持续改善的问题。
随着中国经济与世界的接轨,公司所面临的竞争与挑战就是前所未有的。
为了使公司能够在激烈的市场竞争中站稳脚根,并谋求新的发展,就必须对那些制约企业提高经济效益与管理水平的关键环节进行全面变革。
目前,我国未实施TPM管理辅导的公司不同程度地存在着以下问题:1、生产成本或管理费用过高2、生产过程控制不严3、生产现场脏乱不堪4、产品质量或成品率低下5、员工缺乏参与公司管理的热情,工作积极性与主动性不强等问题这不但严重影响了公司效率与公司形象,而且极易诱发各类人身与设备事故。
tpm意思详细明确介绍
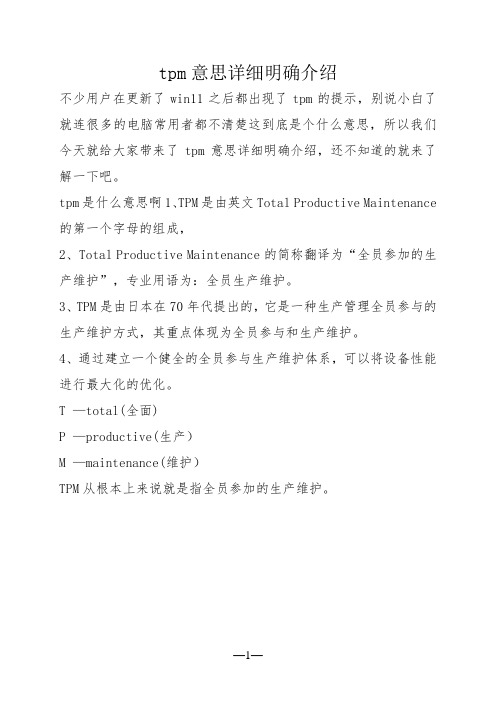
tpm意思详细明确介绍
不少用户在更新了win11之后都出现了tpm的提示,别说小白了就连很多的电脑常用者都不清楚这到底是个什么意思,所以我们今天就给大家带来了tpm意思详细明确介绍,还不知道的就来了解一下吧。
tpm是什么意思啊1、TPM是由英文Total Productive Maintenance 的第一个字母的组成,
2、Total Productive Maintenance的简称翻译为“全员参加的生产维护”,专业用语为:全员生产维护。
3、TPM是由日本在70年代提出的,它是一种生产管理全员参与的生产维护方式,其重点体现为全员参与和生产维护。
4、通过建立一个健全的全员参与生产维护体系,可以将设备性能进行最大化的优化。
T —total(全面)
P —productive(生产)
M —maintenance(维护)
TPM从根本上来说就是指全员参加的生产维护。
你可能还想看:the pc must support tpm2.0解决方法。
TPM试题

TPM试题第一篇:TPM试题“设备管理与TPM”知识竞赛复习试题1、TPM是英文全称:Total ProductiveMaintenance2、TPM的中文意义:全员生产维修(或全面生产维护、全面生产保全)3、TPM的定义:TPM是(Total ProductiveMaintenance)全员生产维修的英文缩写,其本质是全面生产维护;TPM倡导全员参与、引导自主的工作,追求最高的生产效率,努力实现零故障、零事故、零缺陷,加强对设备的维护和保养,减少故障,缩短生产周期,强调零缺和小集团活动(改善活动)。
4、TPM的三“全”:全员、全系统、全效率。
全员是基础,全系统是载体,全效率是目标。
5、TPM包含哪五个方面的基本要素:⑴TPM以最大限度的发挥设备功能,以零故障、零事故、零缺陷为总目标。
⑵TPM以重叠式的小组活动方式,在等级制度的组织之下加以推动的,力争从上到下的政策和自下而上的意见得到贯彻和沟通。
⑶TPM以5S为基础,开展自主维修活动。
⑷TPM以降低六大损失来提高设备的综合效率;⑸TPM的推动不仅局限于生产部门和维修部门,设计开发等其他业务、行政部门都要纳入其中。
6、TPM活动的五大支柱:自主维修(或自主保全)、教育与培训、计划维修体制、以PM 为主旨的前期动态管理、难点攻关即个例的改善。
7、全员的三种方式:纵向的全员、横向的全员及小组活动三种方式。
⑴纵向的全员:TPM强调从企业最高领导到一线职工全员参与设备生产维护,我们称之为纵向的全员。
只有最高领导身体力行的参与和支持TPM活动,才能使这项工程得到有力的贯彻实施。
⑵横向的全员:TPM强调设备不仅是设备维修部门的事,而且也是生产、工艺、安全、质量、设计、供应、后勤等部门的事,这是横向的全员;⑶小组活动:生产计划和工艺流程的执行离不开设备,质量的保障离不开设备,安全环保也和设备密切相关;反过来,良好运行的设备又是企业赖以生存的基础,是企业以新设计产品、高质量产品满足市场需求的保障,因此说维护好设备人人有责。
TPM-全员设备管理与维护

TPM-全员设备管理与维护引言TPM(全员设备管理)是一种旨在改善设备管理和维护效率的方法。
它要求每个员工都有责任保护和维护公司的设备,以确保设备的正常运行和寿命。
本文将介绍TPM的基本概念和原则,以及如何实施TPM来提高设备管理和维护效率。
什么是TPM?TPM是Total Productive Maintenance(全员生产维护)的缩写,是一种由日本引入的管理方法。
它的目标是通过全员参与设备管理和维护,最大限度地减少设备故障和停机时间,提高设备的生产效率。
TPM强调的是预防性维护和日常保养,每个员工都有责任保持设备的运行状态良好。
通过养成良好的维护习惯,可以有效地减少设备故障和停机时间,提高设备的效率和寿命。
TPM的原则TPM基于以下几个基本原则:1.全员参与:TPM要求每个员工都参与设备管理和维护,包括机器操作员、维修人员、管理人员等。
每个员工都应该对设备的正常运行负责,并且能够及时发现和解决设备故障。
2.预防性维护:TPM注重预防设备故障而不是修复故障。
通过进行定期的保养和检查,可以提前发现设备问题并采取相应的措施,以减少故障和停机时间。
3.持续改进:TPM强调持续改进,通过不断地优化设备管理和维护流程,提高设备的效率和可靠性。
每个员工都应该提出改进建议,并参与改善活动。
4.操作员的自主性:TPM鼓励机器操作员参与设备管理和维护,使他们能够及时识别和解决设备故障。
操作员应该接受培训,具备一定的维修和故障排除能力。
TPM的实施步骤要实施TPM,可以按照以下步骤进行:1.培训和意识提高:为所有员工提供TPM培训,使他们了解TPM的概念和原则,以及他们在设备管理和维护中的角色和责任。
同时,提高员工对设备管理和维护的重要性的意识。
2.制定设备管理计划:与设备管理团队合作,制定设备管理计划,包括设备的保养计划、检查标准、操作规程等。
确保计划能够实施,并进行定期的检查和评估。
3.建立设备管理团队:成立设备管理团队,包括设备操作员、维修人员和管理人员等。
TPM是什么意思?TPM理论

TPM是什么意思? TPM由英语全面生产维护的首字母组成。
它是Total Productive Maintenance的缩写,表示所有员工的平均生产维护。
专业术语是:全员工生产维护。
TPM理论是生产管理充分参与活动的生产和维护方法,其重点体现在充分参与和生产维护上。
通过建立一个涉及所有员工的完善的生产和维护系统,最终将优化设备性能。
TPM设备管理
它是一种设备维护和维修管理系统,其基础是提高设备的整体效率,将整个系统的预防性维
护作为过程,并由全体人员参与。
T-总计(完整含义)
P-生产性(生产的含义)
M —维护(维护的含义)
一般来说,TPM是指所有员工的生产和维护。
TPM是通过提高人员和设备的质量来提高企业质量的。
(天行健咨询的家庭专注于精益生产管理,六西格码管理培训咨询和项目咨询管理咨询公司)人员素质的提高是指对必要人员的培训以适应自动化生产,并且通过提高人员素质和整体水平来提高设备的质量实现设备的效率-即提高生产率。
相关阅读:
•三步法帮助模具厂促进TPM管理
•[企业基准测试]海尔TPM管理成功案例分享
•我国石油工厂使用TPM设备管理的案例
•精益生产TPM管理开始率和可动率
•TPM管理在涂装设备的智能升级中得到了优化和探索
•企业为何实施TPM管理
•如何在化工行业中管理TPM设备?
•TPM管理,是实施TPM所需的主要活动
•TQC和TPM有什么区别,主要区别是。
OEE的定义
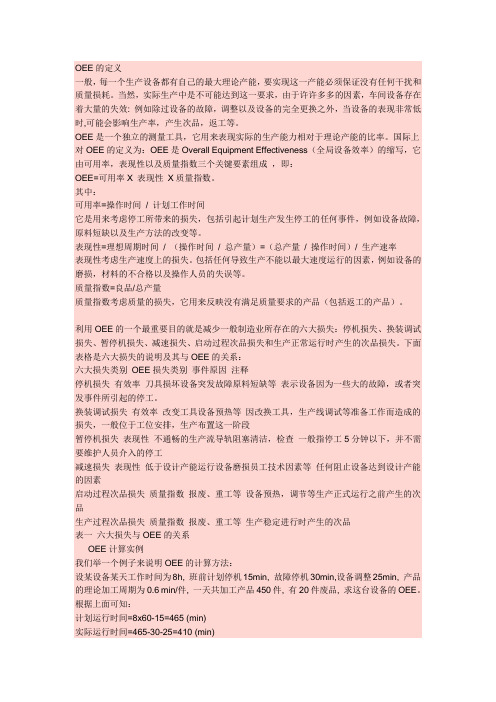
OEE的定义一般,每一个生产设备都有自己的最大理论产能,要实现这一产能必须保证没有任何干扰和质量损耗。
当然,实际生产中是不可能达到这一要求,由于许许多多的因素,车间设备存在着大量的失效: 例如除过设备的故障,调整以及设备的完全更换之外,当设备的表现非常低时,可能会影响生产率,产生次品,返工等。
OEE是一个独立的测量工具,它用来表现实际的生产能力相对于理论产能的比率。
国际上对OEE的定义为:OEE是Overall Equipment Effectiveness(全局设备效率)的缩写,它由可用率,表现性以及质量指数三个关键要素组成,即:OEE=可用率X 表现性X质量指数。
其中:可用率=操作时间/ 计划工作时间它是用来考虑停工所带来的损失,包括引起计划生产发生停工的任何事件,例如设备故障,原料短缺以及生产方法的改变等。
表现性=理想周期时间/ (操作时间/ 总产量)=(总产量/ 操作时间)/ 生产速率表现性考虑生产速度上的损失。
包括任何导致生产不能以最大速度运行的因素,例如设备的磨损,材料的不合格以及操作人员的失误等。
质量指数=良品/总产量质量指数考虑质量的损失,它用来反映没有满足质量要求的产品(包括返工的产品)。
利用OEE的一个最重要目的就是减少一般制造业所存在的六大损失:停机损失、换装调试损失、暂停机损失、减速损失、启动过程次品损失和生产正常运行时产生的次品损失。
下面表格是六大损失的说明及其与OEE的关系:六大损失类别OEE损失类别事件原因注释停机损失有效率刀具损坏设备突发故障原料短缺等表示设备因为一些大的故障,或者突发事件所引起的停工。
换装调试损失有效率改变工具设备预热等因改换工具,生产线调试等准备工作而造成的损失,一般位于工位安排,生产布置这一阶段暂停机损失表现性不通畅的生产流导轨阻塞清洁,检查一般指停工5分钟以下,并不需要维护人员介入的停工减速损失表现性低于设计产能运行设备磨损员工技术因素等任何阻止设备达到设计产能的因素启动过程次品损失质量指数报废、重工等设备预热,调节等生产正式运行之前产生的次品生产过程次品损失质量指数报废、重工等生产稳定进行时产生的次品表一六大损失与OEE的关系OEE计算实例我们举一个例子来说明OEE的计算方法:设某设备某天工作时间为8h, 班前计划停机15min, 故障停机30min,设备调整25min, 产品的理论加工周期为0.6 min/件, 一天共加工产品450件, 有20件废品, 求这台设备的OEE。
TPM是什么意思
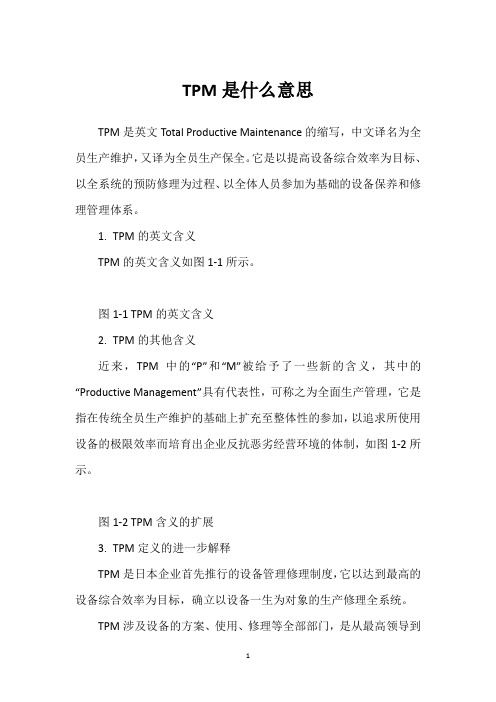
TPM是什么意思TPM是英文Total Productive Maintenance的缩写,中文译名为全员生产维护,又译为全员生产保全。
它是以提高设备综合效率为目标、以全系统的预防修理为过程、以全体人员参加为基础的设备保养和修理管理体系。
1.TPM的英文含义TPM的英文含义如图1-1所示。
图1-1 TPM的英文含义2.TPM的其他含义近来,TPM中的“P”和“M”被给予了一些新的含义,其中的“Productive Management”具有代表性,可称之为全面生产管理,它是指在传统全员生产维护的基础上扩充至整体性的参加,以追求所使用设备的极限效率而培育出企业反抗恶劣经营环境的体制,如图1-2所示。
图1-2 TPM含义的扩展3.TPM定义的进一步解释TPM是日本企业首先推行的设备管理修理制度,它以达到最高的设备综合效率为目标,确立以设备一生为对象的生产修理全系统。
TPM涉及设备的方案、使用、修理等全部部门,是从最高领导到第一线工人全员参与,依靠开展小组自主活动来推行的生产修理活动。
T——全员、全系统、全效率。
PM——生产修理,包括事后修理、预防修理、改善修理、修理预防。
4.TPM毕竟是什么下面以一个典型事例来说明TPM毕竟是什么。
TPM事例说明TPM的详细含义有下面4个方面:(1)以追求生产系统效率(综合效率)的极限为目标,实现设备的综合管理效率即OEE的持续改进;(2)从转变意识到使用各种有效的手段,构筑能防止全部灾难、不良、铺张发生的体系,最终构成“零灾难、零不良、零铺张”的体系;(3)从生产部门开头实施,渐渐进展到开发、管理等全部部门;(4)从最高领导到一线操作人员,全员参加。
TPM活动由“设备保全”“质量保全”“个别改进”“事务改进”“环境保全”“人才培育”6个方面组成,对企业进行全方位的改进。
相关链接TPM与TnPMTnPM是在TPM基础上进展起来的,其目标性更强、更加精确,是规范化下TPM的实际应用,具有更加详细的操作要求。
- 1、下载文档前请自行甄别文档内容的完整性,平台不提供额外的编辑、内容补充、找答案等附加服务。
- 2、"仅部分预览"的文档,不可在线预览部分如存在完整性等问题,可反馈申请退款(可完整预览的文档不适用该条件!)。
- 3、如文档侵犯您的权益,请联系客服反馈,我们会尽快为您处理(人工客服工作时间:9:00-18:30)。
TPM是T otal Productive Maintenance 第一个字母的缩写,本意是"全员参与的生产保全",也翻译为"全员维护",即通过员工素质与设备效率的提高,使企业的体质得到根本改善。
TPM 起源于50年代的美国,最初称事后保全,经过预防保全、改良保全、保全预防、生产保全的变迁。
60年代传到日本,1971年基本形成现在公认的TPM。
80年代起,韩国等亚洲国家、美洲国家、欧洲国家相继开始导入TPM活动。
90年代,中国一些企业开始推进TPM 活动。
TPM是英文T otal Productive Maintenance的缩略语,中文译名叫全面生产维修,又译为全员生产保全。
是以提高设备综合效率为目标,以全系统的预防维修为过程,全体人员参与为基础的设备保养和维修管理体系。
TPM强调五大要素,即:
——TPM致力于设备综合效率最大化的目标;
——TPM在设备一生建立彻底的预防维修体制;
——TPM由各个部门共同推行;
——TPM涉及每个雇员,从最高管理者到现场工人;
——TPM通过动机管理,即自主的小组活动来推进。
(PM)
其具体含义有下面4个方面:
1.以追求生产系统效率(综合效率)的极限为目标;
2.从意识改变到使用各种有效的手段,构筑能防止所有灾害、不良、浪费的体系,最终构成“零”灾害、“零”不良、“零”浪费的体系;
3.从生产部门开始实施,逐渐发展到开发、管理等所有部门;
4.从最高领导到第一线作业者全员参与。
TPM活动由“设备保全”、“质量保全”、“个别改进”、“事务改进”、“环境保全”、“人才培养”这6个方面组成,对企业进行全方位的改进。
1.TPM概念
从理论上讲,TPM是一种维修程序。
它与TQM(全员质量管理)有以下几点相似之处:(1)要求将包括高级管理层在内的公司全体人员纳入TPM;(2)要求必须授权公司员工可以自主进行校正作业;(3)要求有一个较长的作业期限,这是因为TPM自身有一个发展过程,贯彻TPM需要约一年甚至更多的时间,而且使公司员工从思想上转变也需要时间。
TPM将维修变成了企业中必不可少的和极其重要的组成部分,维修停机时间也成了工作日计划表中不可缺少的一项,而维修也不再是一项没有效益的作业。
在某些情况下可将维修视为整个制造过程的组成部分,而不是简单地在流水线出现故障后进行,其目的是将应急的和计划外的维修最小化。
2.TPM的起源
TPM起源于“全员质量管理(TQM)”。
TQM是W·爱德华·德明博士对日本工业产生影响的直接结果。
德明博士在二战后不久就到日本开展他的工作。
作为一名统计学家,他最初只是负责教授日本人如何在其制造业中运用统计分析。
进而如何利用其数据结果,在制造过程中控制产品质量。
最初的统计过程及其产生的质量控制原理不久受到日本人职业道德的影响,形成了具有日本特色的工业生存之道,这种新型的制造概念最终形成了众所周知TQM。
当TQM要求将设备维修作为其中一项检验要素时,发现TQM本身似乎并不适合维修环境。
这是由于在相当一段时间内,人们重视的是预防性维修(PM)措施,多数工厂也都采用PM,而且,通过采用PM技术制定维修计划以保持设备正常运转的技术业已成熟。
然而在需要提高或改进产量时,这种技术时常导致对设备的过度保养。
它的指导思想是:“如果有一滴油能好一点,那么有较多的油应该会更好”。
这样一来,要提高设备运转速度必然会导致维修作业的增加。
而在通常的维修过程中,很少或根本就不考虑操作人员的作用,维修人员也只是就常用的并不完善的维修手册规定的内容进行培训,并不涉及额外的知识。
通过采用TPM,许多公司很快意识到要想仅仅通过对维修进行规划来满足制造需求是远远不够的。
要在遵循TQM原则前提下解决这一问题,需要对最初的TPM技术进行改进,以便将维修纳入到整个质量过程的组成部分之中。
现在,TPM的出处已经明确。
TPM最早是在40年前由一位美国制造人员提出的。
但最早将TPM技术引入维修领域的是日本的一位汽车电子元件制造商——Nippondenso在20世纪60年代后期实现的。
后来,日本工业维修协会干事Seiichi Naka jima对TPM作了界定并目睹了TPM在数百家日本公司中的应用。
3.TPM的应用
在开始应用TPM之前,应首先使全体员工确信公司高级管理层也将参与TPM作业。
实施TPM的第一步则是聘请或任命一位TPM协调员,由他负责培训公司全体员工TPM知识,并通过教育和说服工作,使公司员工们笃信TPM不是一个短期作业,不是只需几个月就能完成的事情,而是要在几年甚至更长时间内进行的作业。
一旦TPM协调员认为公司员工已经掌握有关知识并坚信TPM能够带来利益,就可以认为第一批TPM的研究和行动团队已经形成。
这些团队通常由那些能对生产中存在问题部位有直接影响的人员组成,包括操作人员、维修人员、值班主管、调度员乃至高层管理员。
团队中的每个人都是这一过程的中坚力量,应鼓励它们尽其最大努力以确保每个团队成功地完成任务。
通常这些团队的领导一开始应由TPM协调员担当,直到团队的其他成员对TPM过程完全熟悉为止。
行动团队的职责是对问题进行准确定位,细化并启动修复作业程序。
对一些团队成员来说,发现问题并启动解决方案一开始可能并不容易,这需要一个过程。
尽管在其他车间工作可能有机会了解到不同的工作方法,但团队成员并不需要这样的经验。
TPM作业进行的顺利与否,在于团队成员能否经常到其他合作车间,以观察对比采用TPM的方法、技术以及TPM
工作。
这种对比过程也是进行整体检测技术(称为水准基点)的组成部分,是TPM过程最宝贵的成果之一。
在TPM中,鼓励这些团队从简单问题开始,并保存其工作过程的详细记录。
这是因为团队开始工作时的成功通常会加强管理层对团队的认可。
而工作程序及其结果的推广是整个TPM过程成功的要决之一。
一旦团队成员完全熟悉了TPM过程,并有了一定的解决问题的经验后,就可以尝试解决一些重要的和复杂的问题。
4.案例分析
在一家采用TPM技术的制造公司中,TPM团队在一开始选择了一个冲床作为分析对象,对它进行了深入细致的研究和评估,经过一段较长时间的生产,建立了冲床生产使用和非生产时间的对比记录。
一些团队成员发现冲床在几种十分相似状态下的工作效率却相差悬殊。
这个发现使他们开始考虑如何才能提高其工作状态。
随后不久他们就设计出一套先进的冲床操作程序,它包括为冲床上耗损的零部件清洁、涂漆、调整和更换等维护作业,从而使冲床处于具有世界级水平的制造状态。
作为其中的一部分,他们对设备使用和维修人员的培训工作也进行了重新设计,开发了一个由操作人员负责检查的按日维护作业清单,并由工厂代理人协助完成某些阶段的工作。
在对一台设备成功进行TPM后,其案例记录会表明TPM确能大幅提高产品质量,厂方会因而更加支持对下一台设备采用TPM技术,如此下去,就可以把整个生产线的状态提高到世界级水平,公司的生产率也会显著提高。
由上述案例可知:TPM要求将设备的操作人员也当作设备维修中的一项要素,这就是TPM 的一种创新。
那种“我只负责操作”的观念在这里不再适用了。
而例行的日常维修核查、少量的调整作业、润滑以及个别部件的更换工作都成了操作人员的责任。
在操作人员的协助下,专业维修人员则主要负责控制设备的过度耗损和主要停机问题。
甚至是在不得不聘请外部或工厂内部维修专家的情况下,操作人员也应在维修过程中扮演显著角色。
TPM协调员有几种培训方式。
多数与制造业相结合的大型专业组织与私人咨询部、培训组织一样均可提供有关TPM实施的信息。
制造工程协会(SME)和生产率报业就是两个例子,他们都提供介绍TPM的磁带、书籍和其它相关教学资料。
生产率报业还在美国境内各大城市长期举办有关TPM研讨会,同时也提供工业水准基点的指导和培训工作。
5.TPM效果
成功实施TPM的公司很多,其中包括许多世界驰名公司,如:福特汽车公司、柯达公司、戴纳公司和艾雷·布雷德利公司等。
这些公司有关TPM的报告都说明了公司实施TPM后,生产率有显著提高。
尤其是柯达公司,它声称自公司采用TPM技术后,获得了500万比1600万的投入产出比。
另一家制造公司则称其冲模更换时间从原来的几小时下降到了20分钟。
这相当于无需购买就能使用两台甚至更多的、价值上百万美元的设备。
德克萨斯州立大学声称通过研究发现,在某些领域采用TPM可以提高其生产率达80%左右。
而且这些公司均声称通过TPM可以减少50%甚至更多的设备停机时间,降低备件存货量,提高按时交货率。
在许多案例中它还可以大幅减少对外部采办部件、甚至整个生产线的需求.
TPM是全员劳动生产率保持,目的是在各个环节上持续不断地进行改善。