连铸减少铸坯氧化铁皮方案
降低连铸钢铁料消耗.
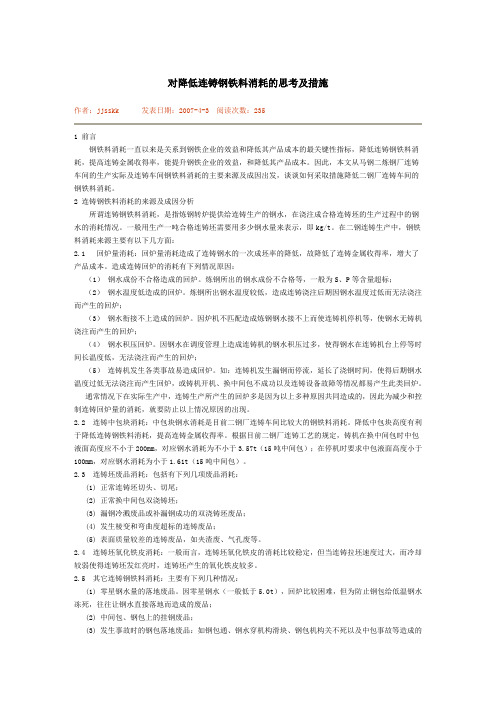
对降低连铸钢铁料消耗的思考及措施作者:jjsskk 发表日期:2007-4-3 阅读次数:2351 前言钢铁料消耗一直以来是关系到钢铁企业的效益和降低其产品成本的最关键性指标,降低连铸钢铁料消耗,提高连铸金属收得率,能提升钢铁企业的效益,和降低其产品成本。
因此,本文从马钢二炼钢厂连铸车间的生产实际及连铸车间钢铁料消耗的主要来源及成因出发,谈谈如何采取措施降低二钢厂连铸车间的钢铁料消耗。
2 连铸钢铁料消耗的来源及成因分析所谓连铸钢铁料消耗,是指炼钢转炉提供给连铸生产的钢水,在浇注成合格连铸坯的生产过程中的钢水的消耗情况。
一般用生产一吨合格连铸坯需要用多少钢水量来表示,即kg/t。
在二钢连铸生产中,钢铁料消耗来源主要有以下几方面:2.1 回炉量消耗:回炉量消耗造成了连铸钢水的一次成坯率的降低,故降低了连铸金属收得率,增大了产品成本。
造成连铸回炉的消耗有下列情况原因:(1)钢水成份不合格造成的回炉。
炼钢所出的钢水成份不合格等,一般为S、P等含量超标;(2)钢水温度低造成的回炉。
炼钢所出钢水温度较低,造成连铸浇注后期因钢水温度过低而无法浇注而产生的回炉;(3)钢水衔接不上造成的回炉。
因炉机不匹配造成炼钢钢水接不上而使连铸机停机等,使钢水无铸机浇注而产生的回炉;(4)钢水积压回炉。
因钢水在调度管理上造成连铸机的钢水积压过多,使得钢水在连铸机台上停等时间长温度低,无法浇注而产生的回炉;(5)连铸机发生各类事故易造成回炉。
如:连铸机发生漏钢而停流,延长了浇钢时间,使得后期钢水温度过低无法浇注而产生回炉,或铸机开机、换中间包不成功以及连铸设备故障等情况都易产生此类回炉。
通常情况下在实际生产中,连铸生产所产生的回炉多是因为以上多种原因共同造成的,因此为减少和控制连铸回炉量的消耗,就要防止以上情况原因的出现。
2.2 连铸中包块消耗:中包块钢水消耗是目前二钢厂连铸车间比较大的钢铁料消耗。
降低中包块高度有利于降低连铸钢铁料消耗,提高连铸金属收得率。
连铸坯缺陷的产生与防止措施 Microsoft Word 文档1

连铸坯裂纹的产生与防止措施连铸坯裂纹的分类 :铸坯表面裂纹包括表面纵裂纹、表面横裂纹、网状裂纹(星裂)、发裂、角部纵裂纹、角部横裂纹等;铸坯内部裂纹包括中间裂纹、角部裂纹、中心线裂纹、三角区裂纹、皮下裂纹、矫直裂纹等。
1.1 铸坯表面裂纹部纵裂纹等几种主要的缺陷形式。
铸坯表面裂纹主要有表面纵裂纹、表面横裂纹、网状裂纹、角部横裂纹、边铸坯表面裂纹是在结晶器内产生的,在二冷段得到扩展。
它会导致轧制板材表面的微细裂纹,影响最终产品的表面质量。
图1为表面裂纹示意图图 1 铸坯表面裂纹示意图1-表面纵裂纹;2-表面横裂纹;3-网状裂纹;4-角部横裂纹;5-边部纵裂纹1.1.1 表面纵裂纹连铸坯表面纵裂纹是指沿着拉坯方向在铸坯表面上发生的裂纹。
它可由工艺因素或设备因素引起。
由工艺因素引起的纵裂,大多出现在铸坯宽面的中央部位,是表面裂纹中最常见的一种裂纹缺陷。
纵裂主要是由于初生坯壳在结晶器内冷却强度不均匀,造成应力的集中,在坯壳相对较薄的地方坯壳厚度不足以承受这种应力,致使坯壳裂开而产生裂纹,并在二冷区得到扩展,形成表面纵裂纹。
图2 图3 图4为表面纵裂纹示意图图2图3 图41.影响连铸坯表面纵裂纹因素:实际生产过程中,主要有以下因素影响连铸坯表面纵裂纹的产生:1) 成品成分及钢水质量(1) 成品钢中碳含量处在亚包晶和包晶反应区时,由于初生坯壳在结晶器弯月面内激冷时收缩较大,容易造成初生坯壳厚薄不均,从而使铸坯发生纵裂纹的倾向增加。
因此,在实际生产中各连铸厂家都尽量控制其成品钢中碳含量,使其避开亚包晶和包晶反应区,从而减少铸坯纵裂纹的发生机率。
(2) 成品钢中硫、磷含量也会影响铸坯纵裂纹的产生。
钢中硫、磷含量增加时,钢的高温强度和塑性明显降低,在应力作用下就容易产生裂纹,因此,在实际生产中各连铸厂家都尽量控制其成品钢中硫、磷含量,尽量控制在0.02%以内。
(3) 钢中微合金如铌、钒等对铸坯纵裂纹的产生也有重要影响,因为微合金而产生的铸坯纵裂纹在铸坯表面上分布不规则,缺陷较短、数量较多。
连铸氧化铁皮清理方案
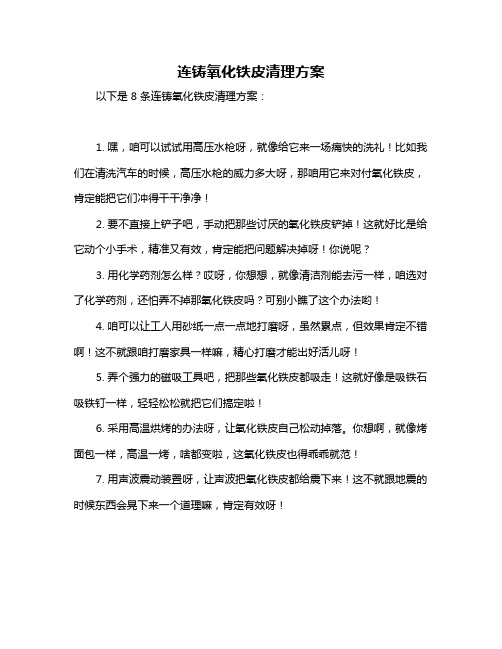
连铸氧化铁皮清理方案
以下是 8 条连铸氧化铁皮清理方案:
1. 嘿,咱可以试试用高压水枪呀,就像给它来一场痛快的洗礼!比如我们在清洗汽车的时候,高压水枪的威力多大呀,那咱用它来对付氧化铁皮,肯定能把它们冲得干干净净!
2. 要不直接上铲子吧,手动把那些讨厌的氧化铁皮铲掉!这就好比是给它动个小手术,精准又有效,肯定能把问题解决掉呀!你说呢?
3. 用化学药剂怎么样?哎呀,你想想,就像清洁剂能去污一样,咱选对了化学药剂,还怕弄不掉那氧化铁皮吗?可别小瞧了这个办法哟!
4. 咱可以让工人用砂纸一点一点地打磨呀,虽然累点,但效果肯定不错啊!这不就跟咱打磨家具一样嘛,精心打磨才能出好活儿呀!
5. 弄个强力的磁吸工具吧,把那些氧化铁皮都吸走!这就好像是吸铁石吸铁钉一样,轻轻松松就把它们搞定啦!
6. 采用高温烘烤的办法呀,让氧化铁皮自己松动掉落。
你想啊,就像烤面包一样,高温一烤,啥都变啦,这氧化铁皮也得乖乖就范!
7. 用声波震动装置呀,让声波把氧化铁皮都给震下来!这不就跟地震的时候东西会晃下来一个道理嘛,肯定有效呀!
8. 干脆来个全面的,各种方法都用上,高压水枪、铲子、化学药剂一起上,就不信搞不定这些氧化铁皮!就像全面进攻一样,全方位打击它们,胜利肯定属于我们呀!
我的观点结论就是:这些方法都有各自的优势和可行性,根据实际情况选择合适的方法或者组合使用,肯定能把连铸氧化铁皮清理得好好的!。
降低热轧氧化铁皮的控制技术

( i i g a irn& S e S c o Ld Xn a y I j n B o t l t kC . t、 e o
Ab t a t S ae r n ft ei o tn co sa e t gHo l S r u fc 。 B n r a d p e e t g me s r s sr c : c sa e o e o l h mp ra t a tr f ci tRol t p s r e f n i a i r gf w r rv n i a u e o n vaa ay i a d lo igf r o migr a o s c mb nn ea t n o a i te 7 0 h t ol l i n l s n k n r n s n , o i i gt ci f y e l1 5 o l mi . s o o f e h o b s r 1 Ke r s y wo d :h t ol t p;c ls tmp r tr o l sr s ae ; r i e e au e
向外依次为 F O、e e 并且氧化膜变得越来 e F2 、 , 0 F0 越致 密 l l J 。
通 常氧化 铁皮 去 除采用 高压 水 除鳞 ,在高 压水 的喷射 之下 ,氧化 铁 皮表 面局 部急冷 ,产生很 大 收 缩 , 而使 氧 化铁 皮 裂 纹扩 大 , 有 部 分翘 曲 , 从 并 经高 压 水 的冲击 ,在裂 纹 中高压 水 的动压 力 变成流 体静 压 力而 侵入 氧化铁 皮底 部 ,通过 氧化 铁皮 下 面的水
图 1 一次氧化铁皮压入缺 陷
在 钢坯 出炉 及轧 机轧 制过 程 中钢坯上 下表 面 的
连铸减少铸坯氧化铁皮方案

连铸减少铸坯氧化铁皮方案一、减少氧化铁皮的意义目前铸造一车间连铸机主要生产20#、45#钢坯,生产过程中,铸坯表面产生大量的氧化铁皮,铸坯出拉矫机后,氧化铁皮大块大块的脱落,既影响铸坯质量及钢水收得率,同时也造成氧化铁皮清理量大,清理困难。
因而减少和防止连铸坯在冷却过程中的氧化,对提高成材率具有十分重要的意义。
解决这个问题,可有效的提高产量、减少单位成品的金属消耗、降低成本,得到显着的经济效益。
二、氧化铁皮形成机理高温钢水在连铸结晶器内凝固成型,形成一定厚度的坯壳,铸坯出结晶器后表面温度较高,暴露在空气中,与氧气及二冷室的水蒸汽发生反应,生成氧化铁。
具体反应式如下:⑴、钢与氧气的反应:2Fe+O2=2FeO3Fe+2O2=Fe3O42Fe3O4+1/2O2=3Fe2O3⑵、钢与水的反应:Fe+H2O=FeO+H23Fe+4H2O=Fe3O4+4H23FeO+H2O=Fe3O4+H2由以上反应可知,连铸坯表面的氧化铁在整个厚度上不仅仅是一种氧化铁,最多可能存在三种氧化铁,从外到内Fe2O3、Fe3O4、FeO同时存在。
而且形貌、成分、结构不同的氧化层与基体的结合力不同,FeO为面心立方、晶轴为,Fe3O4为立方晶体,晶轴为,面心立方的FeO 分解成立方晶体的Fe3O4,组织结构转变,体积产生膨胀,这就是高温铸坯表面产生氧化铁皮并容易脱落的原因。
三、铸坯氧化的影响因素1、钢水温度的影响钢水温度高,钢坯出结晶器后温度也相应增高,氧化铁皮的生成几率增大。
目前,我司连铸钢水受生产节奏及钢包、中间包保温效果差,散热快等因素的影响,上台温度普通偏高,这是造成铸坯氧化铁皮厚的一个主要原因。
2、钢中化学成份的影响钢中的一些合金元素对于连铸坯表面氧化铁皮的生成速度也有一定的影响,其中碳、硅、镍、铜、硫促进氧化铁皮形成,锰、铝、铬可以减缓氧化铁皮的形成。
因而在生产过程中,降低易产生氧化铁皮的合金元素含量,有利于减少铸坯氧化铁皮的生成。
连铸机热坯氧化铁皮清理装置的应用实践
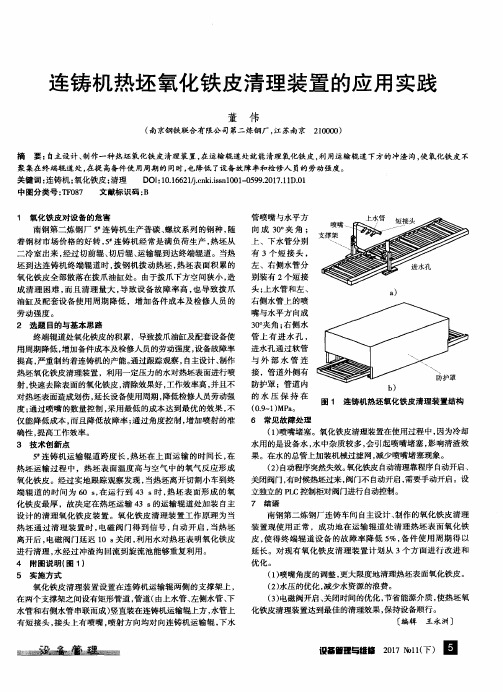
5 实 施 方 式
氧 化铁皮清理装 置设置在连铸 机运输辊两侧 的支撑 架上 ,
在两个 支撑架之 间设有矩形管道 , 管道( 由上水管 、 左侧水管 、 下
水 管和右侧水管 串联而成 ) 竖直装在连铸机运输辊上方 , 水管上 有短接头 , 接头上有 喷嘴 , 喷射方 向均对 向连铸 机运输辊 , 下水
化铁皮清理装置达到最佳 的清理效果 , 保持设备顺行 。 [ 编Fra bibliotek 王永洲 ]
i f t z I I l  ̄ ! g U 2 0 1 7 N o 1 1 ( T ' ) 日
南钢第 二炼钢 厂 5 连铸 机生产普碳 、 螺纹系列 的钢 种 , 随 着钢材 市场 价格 的好转 , 5 连铸 机经常 是满负荷 生产 , 热坯 从 二冷室 出来 , 经过切前辊 、 切后辊 、 运输辊 到达终端辊道 。当热 坯到达 连铸 机终端辊道 时 , 拨钢机 拨动 热坯 , 热坯 表面积 累的 氧化铁 皮全部散 落在 拨爪油缸处 。由于拨爪下 方空间狭小 , 造 成 清理 困难 , 而且清 理量 大 , 导 致设备 故 障率高 , 也导 致拨 爪 油缸及 配套设备 使用周 期 降低 ,增加 备件成 本及检 修人员 的
4 附图说明( 图1 )
皮, 使 得终 端辊道 设备 的故 障率 降低 5 %, 备 件使 用周 期得 以 延长 。对现有 氧化铁 皮清理 装置计划从 3个 方面进行 改进 和
优化 。 ( 1 ) 喷嘴角度 的调整 , 更大 限度地清理热坯表面氧化铁皮 。 ( 2 ) 水压 的优化 , 减少水资源 的浪费 。 ( 3 ) 电磁 阀开启 、 关 闭时间的优化 , 节省 能源介质 , 使热坯氧
提高 , 严重 制约着连铸机 的产能 。 通 过跟踪观察 , 自主设计 、 制作
减少板坯氧化烧损的措施_王丽云

总第201期2012年第9期HEBEI METALLURGYTotal No.2012012,Number 9收稿日期:2012-08-26作者简介:王丽云(1982-),女,助理工程师,2007年毕业于河北理工大学金属材料工程专业,现在河北钢铁集团唐钢中厚板公司工作,E -mail :lywang0801@sina.com.cn减少板坯氧化烧损的措施王丽云,刘翠花,金鑫鑫,马欣然,陈爱苗(河北钢铁集团唐钢中厚板材有限公司,河北唐山063016)摘要:氧化烧损是金属热加工中影响经济技术指标的重要因素。
轧钢加热炉在加热过程中钢的氧化烧损会造成一定的经济损失,同时氧化铁皮还会降低成品表面质量,延长钢在炉加热时间,增加停炉清渣次数等。
通过分析、讨论影响板坯氧化烧损的因素,提出了降低板坯出炉目标温度、减少板坯在炉时间、合理控制炉内气氛等优化措施,板坯氧化烧损得到有效控制,创造了良好的经济效益和社会效益。
关键词:板坯;氧化烧损;均热温度;在炉时间;炉膛气氛;优化中图分类号:TG333.2文献标识码:B文章编号:1006-5008(2012)09-0038-03MEASURES TO REDUCEOXIDATION BURNING LOSS OF SLABWang Liyun ,Liu Cuihua ,Jin Xinxin ,Ma Xinran ,Chen Aimiao(Plate Co.Ltd.of Tang Steel ,Hebei Iron and Steel Group ,Tangshan ,Hebei ,063016)Abstract :Oxidation burning loss is an important factor to affect economic and technical indexes in metal hot -working.Steel oxidation burning loss in heating furnace would make a certain economical loss ,the scale would affect the surface quality of products ,prolong the heating time and increase times of stopping and slag -clear-ing.Based on analysis and discussion about the factors to affect slab oxidation burning loss ,it is proposed the measures to effectively control the loss :lowering furnace exit temperature of slab ,shortening heating time ,and reasonably controlling furnace atmosphere ,excellent economic and social profit got.Key Words :slab ;oxidation burning loss ;even heating temperature ;time in furnace ;furnace chamber atmos-phere ;optimization1前言随着中厚板产品市场竞争的日益激烈,唐钢中厚板公司从改善技术经济指标入手来提高板材效益。
连铸坯表面氧化铁皮除不尽原因及对策_丁波

情况,并对嵌入钢基体的氧化铁皮进行 EDS分析。
2 试验结果分析及对策研究
2.1 氧 化 铁 皮 除 鳞 除 不 尽 的 原 因 分 析 图2 是 Q235B、Q345B、SPA-H 连 铸 坯 内 层 氧
化铁皮与钢基体 结 合 情 况 的 SEM 照 片。 图 3 是 图 2中 A、B、C 3点处 嵌 入 钢 基 体 氧 化 铁 皮 的 EDS 测 量结果。从图 2 可 以 看 出,3 种 试 验 连 铸 坯 内 层 部 分氧 化 铁 皮 呈 楔 形 嵌 入 钢 基 体 中,主 要 表 现 在 图 2 中的 A 点、B 点和 C 点 处;在 (a)、(b)和 (c)中 未 脱 落的氧化铁皮与基体之间因体积效应产生的内应力
· 51 ·
Si 0.14 0.24 0.36
表 1ition of continuous casting slab
%
Mn 0.30 1.28 0.41
P 0.01 0.01 0.08
S 0.01 0.01 0.01
作 者 简 介 :丁 波 (1986— ),男 ,硕 士 ,助 理 研 究 员 ; E-mail:www024151@163.com; 收 稿 日 期 :2013-01-07
第6期
钢种 Q235B Q345B SPA-H
C 0.13 0.15 0.08
丁 波 等 :连 铸 坯 表 面 氧 化 铁 皮 除 不 尽 原 因 及 对 策
热卷板由连铸 坯 热 轧 而 成,连 铸 坯 在 热 轧 前 需 经高温 加 热,在 连 铸 坯 表 面 就 会 生 成 一 层 氧 化 铁 皮[1-4],连 铸 坯 内 层 氧 化 铁 皮 基 本 以 FeO 为 主 , [5] FeO 在高温条件下具 有 一 定 的 致 密 性 和 黏 度,与 钢 基体结合相对较 为 紧 密。 在 工 业 生 产 中,热 轧 前 需 对高温连铸坯表面进 行 高 压 水 除 鳞 处 理 。 [6-10] 若 氧 化皮在除鳞处理中 得 不 到 彻 底 清 除,后 续 轧 制 时 氧 化铁皮就会被压 入 钢 板 而 造 成 表 面 缺 陷。 因 此,研 究连铸坯氧化铁皮除鳞除不尽的原因及对策是非常 重要的。
连铸钢坯氧化铁皮产生的原因及降低措施

( X i n l i n I r o n& S t e e l G r o u p C o . , L t d . , Y i c h u n He i l o n g j i a n g , 1 5 3 0 2 5 C h i n a )
效果。
~
皮 的主要 因素有连铸 二次冷 却 配水量 , 连铸 过程 的 铸坯温度 , 连铸二 次冷却水 的温度 、 钢水 成分等 。
2 . 1 连铸二次冷却 配水 量对铸坯 氧化铁 皮的影响
3 、 4 连铸 机结 晶器 的配 水量 一般 控 制 在 1 2 0 1 4 0 t / h , 钢水 在 结 晶器 内与 铜 管壁 接 触 后 , 受 到 强 制冷 却 , 凝 结成 细小 等 轴 晶的 坯壳 , 初 生 坯壳 的 厚 度大 于 1 0 m m, 由结 晶器 拉 出的铸 坯 进入 二 次冷
Ab s t r a c t : T h r o u g h a n a l y z i n g t h e r e a s o n s f o r o x i d i z e d s c a l e o n c o n t i n u o u s c a s t i n g b i l l e t ,t h e me a s u r e s we r e f o r mu l a t e d t o r e d u c e t h e c o n t i n u o u s c a s t i n g b i l l e t o x i d a t i o n o f i r o n a n d s o me r e s u l t s h a d b e e n a .
连铸连轧生产:无氧化保护浇注

4.3.1钢包到中间包注流的保护
另外,敞开浇注时,在注流的冲击作用下,容易将中间包渣卷入钢液内部。 钢包到中间包的注流保护浇注通常采用长水口保护浇注。长水口上部与钢包 下水口连接,下部插入中间包内钢液面下方100mm左右,可以有效减少卷渣现 象。 在实际生产过程中务必做好长水口与钢包下水口的连接密封,首先上水口的 内径尺寸要与钢包下水口尺寸相互配合,其次采用石棉垫+氩气气幕方式进行密 封。在连接部位形成正压氩气气幕,可以有效防止空气被吸入。
1—钢包;2—滑动水口;3—长水口; 4—氩气;5—中间包;
6—浸式水口;7—结晶器;8—保护渣
4.3.1钢包到中间包注流的保护
如果注流没有保护浇注,钢液从水口流出,在具有一定速度的注流周围形 成一个负压区,从而将注流周围空气卷入钢液中,造成钢液二次氧化。二次氧 化程度与注流比表面积和注流形态有关。
4.3.2中间包到结晶器注流的保护
中间包到结晶器的注流保护采用浸入式水口,使注流与空气完全隔绝,防止 二次氧化。浸入式水口与中间包水口的接缝,与钢包的长水口一样必须密封。用 铝碳质、镁碳质、锆碳质等材料制作的密封环密封,并吹入氩气和涂抹耐火泥, 注流保护效果会更好。采用氩气密封,氩气流量不能过大,否则结晶器内液面容 易出现翻腾现象。
4.3无氧化保护浇注
如图所示,钢包浇注时,对钢液表面加 覆盖剂+钢包盖;从钢包到中间包注流采用长 水口+氩气密封;中间包浇注时,对钢液面加 覆盖剂+保温稻壳,有的吹入氩气进行保护浇 注;中间包到结晶器注流采用浸入式水口+氩 气密封;结晶器内采用保护渣覆盖。其中最 为关键,也是最容易发生吸氧污染的两个环 节是钢包到中间包注流的保护浇注和中间包 到结晶器内注流的保护浇注。
5、氧化的防控措施
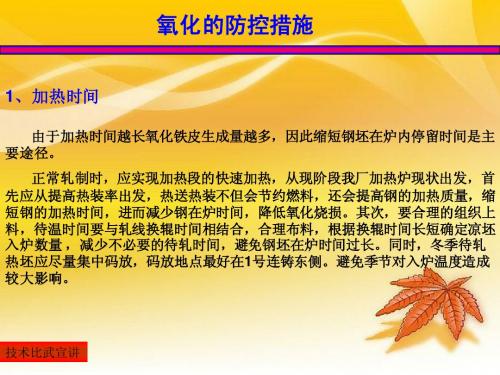
技术比武宣讲
氧化的防控措施
3、钢的化学成分
不同钢种的化学成分,对同等条件下氧化程度的反应是不同的。这里重点介 绍一下我们车间除普碳钢以外的钢种。
硅钢,含有硅的钢在加热过程中会形成特殊的氧化层2FeO.SiO2(铁橄榄 石),铁橄榄石由于熔点较低(1170℃),形成熔融状态后便会以楔形侵入鳞与铁
质中,这样不但会使氧化层附着力强,难以去除,同时,极易造成表面氧化铁皮粘结, 形成轻度粘钢。
锰钢,氧化铁皮加入锰元素后,也会使其熔点降低,如控制不好也极易造成氧化加 重,同时易造成轻度粘钢。
技术比武宣讲
氧化的防控措施
4、炉内气氛
炉内气氛是控制氧化铁皮生成量的关键,在检修加热炉时,冬季炉内的氧化 铁皮堆积量明显增加,查阅氧化铁皮运输车辆检斤记录,冬季量也明显增大,所 风机入口 以我重点介绍一下冬季炉内气氛控制要点。
技术比武宣讲
氧化的防控措施
2、加热温度
合理确定加热温度,也是降低钢坯氧化烧损的重要途径,在满足轧制要求情 况下,加热温度应取下限控制。
从下表氧化烧损与温度对比关系可以看出,在粗轧换辊期间,加热炉在保 证可以有1----2小时提温时间的前提下,最理想降温区间是预热段降至900℃以下,
加热段、均热段降至1000 ℃-----1050 ℃,如提温时间充足,停炉时间较长情况下,整体 炉温应降至900 ℃以下,以防止氧化烧损加重。 此外,在轧制不同规格的钢坯和不同的钢种情况下,加热炉的钢温应作出明显调整 以降低氧化烧损的量。
氧化的防控措施
1、加热时间
由于加热时间越长氧化铁皮生成量越多,因此缩短钢坯在炉内停留时间是主 要途径。 正常轧制时,应实现加热段的快速加热,从现阶段我厂加热炉现状出发,首 先应从提高热装率出发,热送热装不但会节约燃料,还会提高钢的加热质量,缩 短钢的加热时间,进而减少钢在炉时间,降低氧化烧损。其次,要合理的组织上 料,待温时间要与轧线换辊时间相结合,合理布料,根据换辊时间长短确定凉坯 入炉数量 ,减少不必要的待轧时间,避免钢坯在炉时间过长。同时,冬季待轧 热坯应尽量集中码放,码放地点最好在1号连铸东侧。避免季节对入炉温度造成 较大影响。
降低氧化铁皮方案
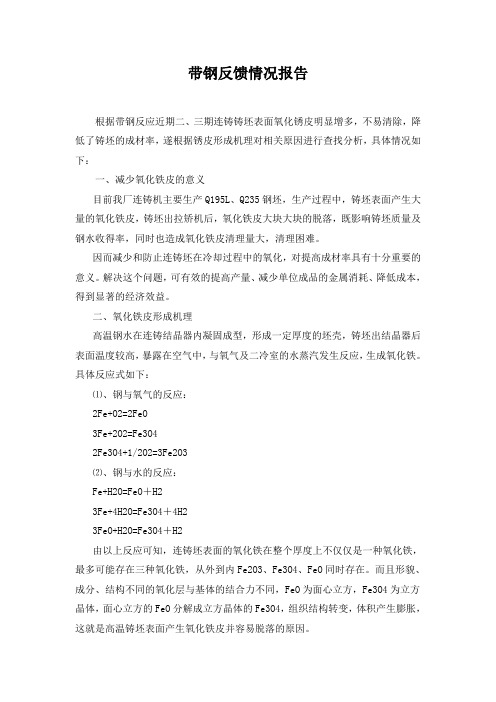
带钢反馈情况报告根据带钢反应近期二、三期连铸铸坯表面氧化锈皮明显增多,不易清除,降低了铸坯的成材率,遂根据锈皮形成机理对相关原因进行查找分析,具体情况如下:一、减少氧化铁皮的意义目前我厂连铸机主要生产Q195L、Q235钢坯,生产过程中,铸坯表面产生大量的氧化铁皮,铸坯出拉矫机后,氧化铁皮大块大块的脱落,既影响铸坯质量及钢水收得率,同时也造成氧化铁皮清理量大,清理困难。
因而减少和防止连铸坯在冷却过程中的氧化,对提高成材率具有十分重要的意义。
解决这个问题,可有效的提高产量、减少单位成品的金属消耗、降低成本,得到显著的经济效益。
二、氧化铁皮形成机理高温钢水在连铸结晶器内凝固成型,形成一定厚度的坯壳,铸坯出结晶器后表面温度较高,暴露在空气中,与氧气及二冷室的水蒸汽发生反应,生成氧化铁。
具体反应式如下:⑴、钢与氧气的反应:2Fe+O2=2FeO3Fe+2O2=Fe3O42Fe3O4+1/2O2=3Fe2O3⑵、钢与水的反应:Fe+H2O=FeO+H23Fe+4H2O=Fe3O4+4H23FeO+H2O=Fe3O4+H2由以上反应可知,连铸坯表面的氧化铁在整个厚度上不仅仅是一种氧化铁,最多可能存在三种氧化铁,从外到内Fe2O3、Fe3O4、FeO同时存在。
而且形貌、成分、结构不同的氧化层与基体的结合力不同,FeO为面心立方,Fe3O4为立方晶体,面心立方的FeO分解成立方晶体的Fe3O4,组织结构转变,体积产生膨胀,这就是高温铸坯表面产生氧化铁皮并容易脱落的原因。
三、铸坯氧化的影响因素1、钢水温度的影响★钢水温度高,钢坯出结晶器后温度也相应增高,氧化铁皮的生成几率增大。
目前,我司连铸钢水受生产节奏及中间包保温效果差,散热快等因素的影响,上台温度普通偏高,这是造成铸坯氧化铁皮厚的一个主要原因。
2、钢中化学成份的影响钢中的一些合金元素对于连铸坯表面氧化铁皮的生成速度也有一定的影响,其中碳、硅、镍、铜、硫促进氧化铁皮形成,锰、铝、铬可以减缓氧化铁皮的形成。
减少氧化物夹杂提高连铸坯质量_王维

收稿日期:2005-05-28; 修订日期:2005-06-19基金项目:河南科技大学青年基金项目(2003QY003)作者简介:王 维(1971- ),河南南阳人,硕士,讲师.研究方向:连铸温度场模拟.V ol.26N o.9Sep.2005铸造技术F O UN D RY T ECH NO LOG Y减少氧化物夹杂提高连铸坯质量王 维1,赵红瑞2(1.河南科技大学,洛阳471003;2.安龙钢铁有限责任公司,洛阳455004)摘要:本文结合安龙的实际生产,通过在炼钢和连铸过程的各个阶段加入不同的示踪剂及其成分含量的变化情况,分析了连铸坯中的氧化物夹杂的来源和影响因素,氧化物夹杂主要来源于二次氧化产物、夹渣、耐火材料侵蚀产物。
就安龙的现状进行了设备技术改造,炼钢工艺改进。
严格控制外来夹杂物,降低钢液二次氧化机会,达到了减少氧化物夹杂,提高连铸坯质量的目的。
关键词:夹杂物;连铸;质量中图分类号:TG249.7 文献标识码:A 文章编号:1000-8365(2005)09-0793-02Decreasing Inclusion and Improving the Quality of Continuous Cast SlabW AN G Wei 1,Z HA O Ho ng -rui 2(1.U niversity of Science and Technology Henan ,Luoyang 471003,China ;2.Anlong Iron &Steel G roup Co.,Ltd ,Luoyang 455004,China )A bstract :This paper analy ses the inclusions so urce and affecting facto rs by adding different trace elements into slag and ladle and trundishing The main source of o xidation inclusio n is that secondary o xidation ,slag enclosure and mo no lithic m aterial action.Futherm ore ,We do equipments technical improvement and im pro ve steelingpro cess.Controling the outer inclusio n strictly ,decreasing the o ppor tunity of secondary oxidatio n ,so w e achieve the anticipated g oal.Key words :Inclusion ;Continuous casting ;Q uality 1 利用试验确定夹杂物的来源采用示踪剂跟踪夹杂物的来源,在电炉出钢过程中,在钢包中配入渣量9%的CeO 2,在中间包覆盖剂中配入渣量7%的Pr 6O 11,在钢包耐火材料中配入5%的La 2O 3,在中间包涂料中配入7%的ZrO 2[1]。
氧化铁皮生成分析及消除措施

学术·超薄热带氧化铁皮生成分析及消除措施转载自《金属世界》1 前言唐钢超薄热带生产线汇集了世界一流的设备和技术,自2003年1月29日热试以来,已经利用半无头轧制工艺成功轧制了0.8mm的超薄带钢,并于2005年年产300余万t,突破设计产量,创出了世界瞩目的成绩。
FTSC连铸机是意大利DANIELI公司的;辊底式均热炉是美国BRICMONT公司的.车L机采用2RM+5FM 布置,粗轧机DANIELI设计,精轧机由三菱一日立设计;卷取区采用了石川岛播磨的高速飞剪、双地下卷取机。
其工艺流程如图1所示。
该设备组成和工艺在国内都属于首次使用,没有成熟的经验可借鉴。
由于品种钢、薄规格钢板具有较大的利润空间,增加品种钢、薄规格钢板产量的压力,使得带钢质量面临极大的考验。
从而使影响带钢表面质量的氧化铁皮缺陷问题愈加突出。
2 氧化铁皮生成原因分析钢的氧化反应一般为: 02与钢的反应:2Fe+O2=2FeO 3Fe+202= Fe3O4 2Fe304+1/2O2=3Fe203 H20与钢的反应:Fe+H2O=FeO+H2 3Fe+4H20= Fe3O4+4H2 3FeO+H20= Fe3O4+H2 由上述反应可知:薄板表面的氧化铁在整个厚度上不仅仅是一种氧化铁,最多可有三种氧化铁,Fe203、Fe304、FeO从外到内同时存在。
并且形貌、成分、结构不同的氧化层与基体的结合力不同。
由于面心立方、晶轴为4.307的FeO,分解成立方晶体、晶轴为8.3967的Fe304,组织结构转变,产生了体积膨胀,组织结构转变应力造成了原层中的细小裂纹,使成品表面二次氧化铁皮容易剥离。
上部薄层呈黑色(Fe203),容易腐蚀,接下来是红色氧化铁皮层(Fe3O4),金属表面为黑色薄层(FeO)。
2.1连铸坯在连铸机出口、加热炉入口板坯温度较高,暴露在空气中,与氧气发生反应;在蒸汽中与水发生反应生产氧化铁皮。
2.2粗轧机轧制造成一次氧化铁皮压入由于铸坯自重、尾部剪切弓形以及炉辊的严重粘铁、损坏、变形、啃伤等,造成一次氧化铁皮压入板坯下表面。
- 1、下载文档前请自行甄别文档内容的完整性,平台不提供额外的编辑、内容补充、找答案等附加服务。
- 2、"仅部分预览"的文档,不可在线预览部分如存在完整性等问题,可反馈申请退款(可完整预览的文档不适用该条件!)。
- 3、如文档侵犯您的权益,请联系客服反馈,我们会尽快为您处理(人工客服工作时间:9:00-18:30)。
连铸减少铸坯氧化铁皮
方案
-CAL-FENGHAI-(2020YEAR-YICAI)_JINGBIAN
连铸减少铸坯氧化铁皮方案
一、减少氧化铁皮的意义
目前铸造一车间连铸机主要生产20#、45#钢坯,生产过程中,铸坯表面产生大量的氧化铁皮,铸坯出拉矫机后,氧化铁皮大块大块的脱落,既影响铸坯质量及钢水收得率,同时也造成氧化铁皮清理量大,清理困难。
因而减少和防止连铸坯在冷却过程中的氧化,对提高成材率具有十分重要的意义。
解决这个问题,可有效的提高产量、减少单位成品的金属消耗、降低成本,得到显著的经济效益。
二、氧化铁皮形成机理
高温钢水在连铸结晶器内凝固成型,形成一定厚度的坯壳,铸坯出结晶器后表面温度较高,暴露在空气中,与氧气及二冷室的水蒸汽发生反应,生成氧化铁。
具体反应式如下:
⑴、钢与氧气的反应:
2Fe+O2=2FeO
3Fe+2O2=Fe3O4
2Fe3O4+1/2O2=3Fe2O3
⑵、钢与水的反应:
Fe+H2O=FeO+H2
3Fe+4H2O=Fe3O4+4H2
3FeO+H2O=Fe3O4+H2
由以上反应可知,连铸坯表面的氧化铁在整个厚度上不仅仅是一种氧化铁,最多可能存在三种氧化铁,从外到内Fe2O3、Fe3O4、FeO 同时存在。
而且形貌、成分、结构不同的氧化层与基体的结合力不同,FeO为面心立方、晶轴为,Fe3O4为立方晶体,晶轴为,面心立方的FeO分解成立方晶体的Fe3O4,组织结构转变,体积产生膨胀,这就是高温铸坯表面产生氧化铁皮并容易脱落的原因。
三、铸坯氧化的影响因素
1、钢水温度的影响
钢水温度高,钢坯出结晶器后温度也相应增高,氧化铁皮的生成几率增大。
目前,我司连铸钢水受生产节奏及钢包、中间包保温效果差,散热快等因素的影响,上台温度普通偏高,这是造成铸坯氧化铁皮厚的一个主要原因。
2、钢中化学成份的影响
钢中的一些合金元素对于连铸坯表面氧化铁皮的生成速度也有一定的影响,其中碳、硅、镍、铜、硫促进氧化铁皮形成,锰、铝、铬可以减缓氧化铁皮的形成。
因而在生产过程中,降低易产生氧化铁皮的合金元素含量,有利于减少铸坯氧化铁皮的生成。
目前我司主要生产普通碳素结构钢,钢中铝含量比较低,这也是铸坯氧化铁皮厚的原因之一。
3、冷却制度的影响
二次冷却制度,对钢坯的氧化影响较大,连铸机二冷全部采用气雾水冷却,如果冷却均匀,钢坯得到良好的冷却,可以减轻表面的氧化,目前我司连铸机二冷室的气雾冷却效果不是很好,冷却水的雾化效果较差,同时二冷室内漏水严重,大量的水直接喷到铸坯表面,造成铸坯冷却不均,因而很容易产生大量的氧化铁皮。
4、拉速的影响
理论上分析,拉速越快,铸坯在二冷室与水气接触的时间短,铸坯的氧化程度也会减弱,目前由于受生产节奏的限制,拉速都偏低,因而铸坯表面氧化都比较严重。
四、减少铸坯氧化铁皮的措施
针对以上分析,为控制铸坯氧化,减少氧化铁皮的生成量,特制订以下控制措施:
1、适当提高钢中锰、铝含量。
目前,为防止连铸絮水口,钢水中铝含量控制较低,在连铸采用大水口开浇,塞棒自动控制投入使用后,建议适当提高钢中铝含量。
2、稳定中间包钢水过热度,避免高温吊包。
中间包钢水过热度最佳控制范围为20~30℃,但由于目前生产节奏不稳定,钢包、中间包保温效果差,连铸钢水温度控制时高时低。
因而稳定生产节奏,尽可能降低连铸钢水温度,控制合适的中间包钢水过热度,是减少铸坯氧化铁皮量的一个重要措施。
3、优化二次冷却制度
目前需要解决的主要问题有:
⑴、二冷段支承辊全部采用开路冷却,开路冷却水从管路喷出时,有不少直接淋到铸坯表面,造成铸坯局部发黑。
因而要对开路冷却水出水口进行改进,防止冷却水直接喷到铸坯表面。
⑵、二冷室喷淋环及喷嘴连接管路漏现象较多,要想办法解决。
⑶、合理调节气水雾化比,保证二冷水的雾化效果,目前根据现场多次调整,二冷压缩空气的二次调节合适压力为~,各班在启铸生产过程中,要及时到二冷室压缩空气压力调节阀站观察二冷压缩空气的压力情况,调整到合适范围。
⑷、调整各区冷却强度,避免铸坯在冷却过程中回温过大。
小断面各区水量分配比调整为:45:40:15
大断面各区水量分配比调整为:50:40:10
⑸、保证二冷密封效果。
前期在设备安装过程中,二冷室开了不少的孔洞,密封效果差,建议进行彻底的封闭。
4、提高拉速,在过热度稳定的情况下尽可能保持恒速拉坯,不要频繁变动拉坯速度,以免造成铸坯回温过大。
5、铸坯出二冷室后,建议设计制作铸坯二冷段保温罩,一是保证生产高碳钢、高合金钢铸坯的内部质量,同时也可减缓铸坯表面氧化铁皮的生成。
编制:铸锻技术中心朱庆桂
2014年4月5日。