产能计算方法
产能计算方法

产能核算方式一:工时换算1、各车间选取本车间一种近三年工艺、生产方式较为稳定的产品作为参照,设置其产能指数为1,其人均每小时产量为P0;2、各车间报上各类产品在不需要其他班组帮忙情况下一个工作日(8小时)的最大理想产量M i和对应班组人数N i(以近三月生产情况作为参考,数据仅用在不同产品产能指数换算,不作为生产能力依据);(此条目方法待定,如果能够区分过往月份产品由对应班组生产数和非对应班组生产数的话可尝试通过具体工时与产量换算)3、如一个班组生产一单位本职产品i的周期为H,车间其他班组生产产品i的周期为I,则需商定一个周期比例系数I/H(即非熟练工人工时损耗);(此条目方法待定,如果能够区分过往月份产品由对应班组生产数和非对应班组生产数的话可尝试通过具体工时与产量换算)4、产品的理论人均每小时产量P=日产量/(8*班组人数),产品i的产能指数为P i /P0;5、产能计算方式:以十一车间I段为例,设低压柜为参照产品,其产能指数为1,配电箱产能指数为0.4,配电箱工人生产低压柜周期比例系数为1.4,低压柜工人生产配电箱周期比例系数为1.3,七月共生产低压柜800台,配电箱100台,其中100台低压柜为配电箱工人生产,则产能总值为800*1+100*0.4,此外补偿产能(换班生产补偿)为100*1.4-100,七月份如全部生产低压柜的话可生产[800*1+(100*0.4)/1.4]/1台,全部生产配电箱的话可生产[700/(1.3*0.4)]+(100*1.4)/0.4+100 台;6、各车间每月上报生产任务完成情况时需注明各类产品由对应班组人员生产台数和非对应班组人员生产台数。
产能核算方式二:简化投入产出分析鉴于电气各分厂之间物资流整体较为明晰,可考虑在分厂间甚至车间间进行投入产出统计,减少造成产值虚高现象的可能性,便于进行分析。
产能怎么计算范文
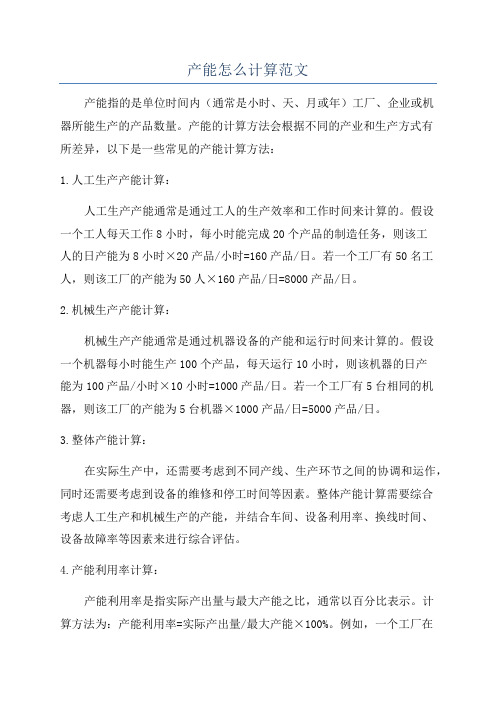
产能怎么计算范文产能指的是单位时间内(通常是小时、天、月或年)工厂、企业或机器所能生产的产品数量。
产能的计算方法会根据不同的产业和生产方式有所差异,以下是一些常见的产能计算方法:1.人工生产产能计算:人工生产产能通常是通过工人的生产效率和工作时间来计算的。
假设一个工人每天工作8小时,每小时能完成20个产品的制造任务,则该工人的日产能为8小时×20产品/小时=160产品/日。
若一个工厂有50名工人,则该工厂的产能为50人×160产品/日=8000产品/日。
2.机械生产产能计算:机械生产产能通常是通过机器设备的产能和运行时间来计算的。
假设一个机器每小时能生产100个产品,每天运行10小时,则该机器的日产能为100产品/小时×10小时=1000产品/日。
若一个工厂有5台相同的机器,则该工厂的产能为5台机器×1000产品/日=5000产品/日。
3.整体产能计算:在实际生产中,还需要考虑到不同产线、生产环节之间的协调和运作,同时还需要考虑到设备的维修和停工时间等因素。
整体产能计算需要综合考虑人工生产和机械生产的产能,并结合车间、设备利用率、换线时间、设备故障率等因素来进行综合评估。
4.产能利用率计算:产能利用率是指实际产出量与最大产能之比,通常以百分比表示。
计算方法为:产能利用率=实际产出量/最大产能×100%。
例如,一个工厂在一些月生产了3000个产品,而其最大产能为5000个产品,则该工厂的产能利用率为3000产品/5000产品×100%=60%。
5.各种因素的影响:除了工人和机器生产能力,还有一些其他因素也会影响产能,如设备故障率、员工培训和生产流程的优化等。
通过减少故障率、提高员工技能和改进生产流程,可以提高单位时间内的产能。
总结起来,产能计算是通过对工人和机械的生产能力、工作时间和产出数量进行综合计算得出的。
同时,还需要考虑到设备的维修和停工时间、换线时间以及产能利用率等因素。
产能计算方法
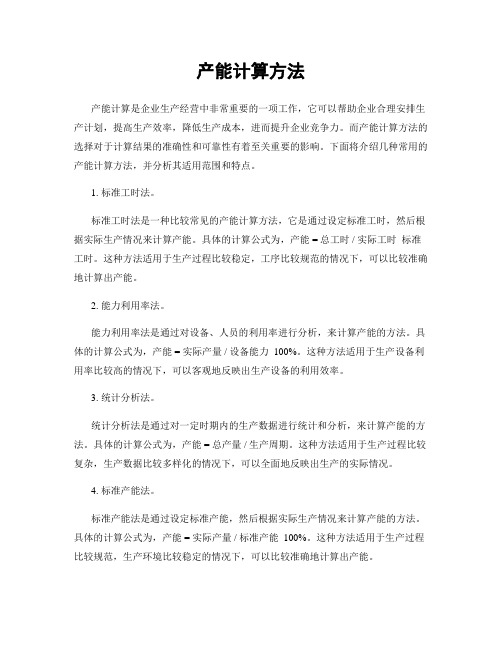
产能计算方法产能计算是企业生产经营中非常重要的一项工作,它可以帮助企业合理安排生产计划,提高生产效率,降低生产成本,进而提升企业竞争力。
而产能计算方法的选择对于计算结果的准确性和可靠性有着至关重要的影响。
下面将介绍几种常用的产能计算方法,并分析其适用范围和特点。
1. 标准工时法。
标准工时法是一种比较常见的产能计算方法,它是通过设定标准工时,然后根据实际生产情况来计算产能。
具体的计算公式为,产能 = 总工时 / 实际工时标准工时。
这种方法适用于生产过程比较稳定,工序比较规范的情况下,可以比较准确地计算出产能。
2. 能力利用率法。
能力利用率法是通过对设备、人员的利用率进行分析,来计算产能的方法。
具体的计算公式为,产能 = 实际产量 / 设备能力 100%。
这种方法适用于生产设备利用率比较高的情况下,可以客观地反映出生产设备的利用效率。
3. 统计分析法。
统计分析法是通过对一定时期内的生产数据进行统计和分析,来计算产能的方法。
具体的计算公式为,产能 = 总产量 / 生产周期。
这种方法适用于生产过程比较复杂,生产数据比较多样化的情况下,可以全面地反映出生产的实际情况。
4. 标准产能法。
标准产能法是通过设定标准产能,然后根据实际生产情况来计算产能的方法。
具体的计算公式为,产能 = 实际产量 / 标准产能 100%。
这种方法适用于生产过程比较规范,生产环境比较稳定的情况下,可以比较准确地计算出产能。
在实际生产中,以上几种方法可以根据企业的实际情况进行灵活选择和结合,以达到更加准确和可靠的产能计算结果。
同时,产能计算方法的选择也需要考虑到生产过程的特点、数据的获取难易程度、计算的复杂程度等因素,综合分析选择最适合的方法进行产能计算。
总之,产能计算是企业生产管理中的重要环节,选择合适的产能计算方法对于企业的生产经营至关重要。
希望企业能够根据自身情况,选择合适的方法进行产能计算,提高生产效率,降低生产成本,从而获得更好的经济效益。
产能怎么计算

产能怎么计算
按照设备的单位产量*标准生产时间=标准产能。
1、标准产能:将单位时间除以标准时间即得标准产能。
如1小时(3600秒)/46秒=78,即14”腰盘1小时的标准产能是78个;如8小时/46秒=620,即14”腰盘8小时的标准产能是620个。
2、产能是指在计划期内,企业参与生产的全部固定资产,在既定的组织技术条件下,所能生产的产品数量,或者能够处理的原材料数量。
3、产能的计算公式:产能=单位工作时间/周期时间,拉的周期时间是指该拉产出单位产品的时间间隔,它等于该拉的瓶颈时间,单位工作时间是指出勤时间减去相关活动产生的等待时间。
4、标准产能=总时间/(总工位数*瓶颈时间)。
扩展资料:
标准产能步骤确定:
在计算生产能力时,必须了解每条独立生产线的情况、每家独立工厂的生产水平以及整个生产系统的生产分配状况,一般可通过以下步骤来进行:
1)运用预测技术预测每条独立生产线的产品的销售情况;
2)计算为满足需求所需投入的设备和劳动力数量;
3)合理配置可获得的设备与劳动力数量。
企业常常还要考虑一个生产能力余量作为平衡设计生产能力与实际生产能力的缓冲。
生产能力余量是指超过预期需求的生产富余能力。
产能计算文档

产能计算介绍在生产和制造过程中,产能计算是一种重要的工具,用于评估生产线或工厂的生产能力和效率。
产能计算的目标是根据生产过程中的各项指标,如生产时间、资源利用率和单位时间产出量等,量化生产线的产能。
通过合理的产能计算,企业可以更好地规划生产计划、资源配置、工作流程和供应链管理,从而提高生产效率和降低成本。
产能计算公式产能计算的方法和公式多种多样,以下是一种常用的产能计算公式:总产能 = 单位时间产出量 × 产出时间单位时间产出量 = 总产出数量 ÷ 产出时间生产效率 = 单位时间产出量 ÷ 总资源消耗量其中,总产能是指在给定的产出时间内,生产线或工厂可以完成的总产出量。
单位时间产出量是指一段时间内单位时间内的产出量。
生产效率则是衡量单位时间内所消耗的资源,与产出量之间的比率。
产能计算的重要指标在产能计算中,有几个重要的指标需要考虑:1. 生产时间生产时间是指从开始生产到完成生产的时间。
它包括了准备时间、运输时间、制造时间、装配时间等各个环节的时间消耗。
生产时间的准确计算对于产能计算非常重要,它可以帮助企业了解生产过程中的时间瓶颈和瓶颈环节,从而优化生产流程。
2. 资源利用率资源利用率是指在生产过程中,各种资源的利用程度。
它包括了设备利用率、人力资源利用率等。
资源利用率的计算可以帮助企业评估资源配置是否合理,是否存在资源浪费和闲置的情况。
3. 单位时间产出量单位时间产出量是指在单位时间内的产出量。
它可以通过总产量与生产时间的比率来计算。
单位时间产出量是衡量产线效率的重要指标之一,它可以帮助企业评估生产线的效率和生产能力。
4. 生产效率生产效率是指在单位时间内所消耗的资源,与产出量之间的比率。
生产效率的计算可以帮助企业评估生产过程中的资源利用情况和效率水平,从而找出生产中的瓶颈和改进生产效率的方法。
产能计算的应用产能计算在企业的生产管理中具有广泛的应用,以下是几个典型的应用场景:1. 生产计划通过产能计算,企业可以根据生产线的产能,制定合理的生产计划。
产能的计算方式

产能的计算方式产能是指单位时间内生产的产品数量或提供的服务数量。
不同行业和企业具有不同种类的产能计算方式,以下是一些常见的产能计算方法。
1. 单位时间内产量计算法这是最基本的产能计算方法,即单位时间内生产的产品数量。
通常以小时、天、月或年为单位。
例如,某个工厂每月生产5000台电视机,那么该工厂的产能就是每月5000台电视机。
2. 单位时间内产值计算法产值是指生产的产品或提供的服务所产生的销售收入。
产值计算的单位可以是小时、天、月或年。
例如,某家餐饮公司每天的产值为10000元,那么该公司的单位时间产能就是每天的产值。
3. 机器设备利用率计算法对于生产过程中使用机器设备的企业,可以通过计算机器设备的利用率来评估产能。
设备利用率是指机器设备实际运转时间占总时间的比例。
例如,某家工厂的生产线每天运转16个小时,而设备实际运转时间为14个小时,那么该工厂的设备利用率为 14/16 = 87.5%。
较高的设备利用率通常表示较高的产能。
4. 人力资源计算法对于服务行业或以人力为主要生产要素的企业,产能的计算可以基于人力资源的数量和效率。
人力资源计算可以包括员工数量、人均产能和劳动生产率。
例如,某家客服中心一天有100名客服员工,每名客服员工每天平均处理100个来电,那么该客服中心的每天产能为10000个来电。
5. 标准工时计算法标准工时是指完成一项生产任务所需的时间。
通过计算标准工时和生产周期,可以得到单位时间内的产能。
例如,某个生产任务的标准工时为5小时,生产周期为一个月,那么该任务的单位时间产能为每月5小时。
总之,产能的计算方式取决于行业和企业的特点。
无论采用哪种计算方法,都需要根据实际情况确定有效的指标进行计算,以便准确评估和提高产能水平。
产能计算文档
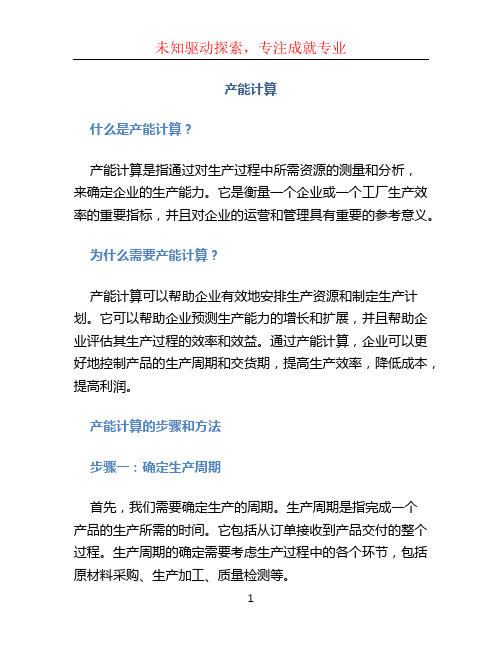
产能计算什么是产能计算?产能计算是指通过对生产过程中所需资源的测量和分析,来确定企业的生产能力。
它是衡量一个企业或一个工厂生产效率的重要指标,并且对企业的运营和管理具有重要的参考意义。
为什么需要产能计算?产能计算可以帮助企业有效地安排生产资源和制定生产计划。
它可以帮助企业预测生产能力的增长和扩展,并且帮助企业评估其生产过程的效率和效益。
通过产能计算,企业可以更好地控制产品的生产周期和交货期,提高生产效率,降低成本,提高利润。
产能计算的步骤和方法步骤一:确定生产周期首先,我们需要确定生产的周期。
生产周期是指完成一个产品的生产所需的时间。
它包括从订单接收到产品交付的整个过程。
生产周期的确定需要考虑生产过程中的各个环节,包括原材料采购、生产加工、质量检测等。
步骤二:确定生产能力在确定生产周期后,我们需要计算企业的生产能力。
生产能力是指在一定时间内企业能够完成生产的能力。
生产能力的计算需要考虑到生产设备的数量和性能、生产员工的数量和技能水平等因素。
步骤三:计算每小时产能通过将生产能力除以生产周期,我们可以计算出每小时的产能。
每小时产能是指企业在一个小时内能够完成的产品数量。
计算每小时产能可以帮助企业评估生产过程的效率,并进一步优化生产计划和资源配置。
步骤四:监控和调整产能一旦完成产能计算,企业需要对生产过程进行监控和调整。
通过与实际生产情况的对比,企业可以发现生产中的瓶颈和问题,并采取相应的措施进行改进。
监控和调整产能是一个持续的过程,可以帮助企业不断提高生产效率,提高产品质量,并满足市场需求。
产能计算的应用和意义产能计算在企业运营和管理中有着广泛的应用和重要的意义。
生产计划和资源分配通过产能计算,企业可以根据市场需求和生产能力来制定生产计划和资源分配。
它可以帮助企业避免产能过剩或不足的情况,提高资源利用率,优化生产效率。
评估生产效率和成本产能计算可以帮助企业评估生产过程的效率和成本。
通过比较实际产能和目标产能,企业可以找出生产过程中的瓶颈和问题,并采取相应的措施进行改进。
产能计算方法范文

产能计算方法范文产能计算是生产过程中的重要环节,它可以帮助企业合理规划生产能力,提高生产效率,降低生产成本。
产能计算方法有很多种,下面将详细介绍几种常用的方法。
一、单一产能计算方法单一产能指一些工段或设备在规定的时间内所能完成的生产任务量。
计算单一产能的方法很简单,只需要将生产任务量除以规定时间即可。
例如,一些设备在8小时内能完成500个产品的生产任务量,那么该设备的单一产能就是500/8=62.5个产品每小时。
二、综合产能计算方法综合产能指各个工段或设备相互配合下,整个生产过程能完成的生产任务量。
这种方法需要考虑到各个工段之间的协调能力及相互的制约关系。
计算综合产能需要进行多个工序之间的数据对比和分析,从而确定整个生产过程的产能。
例如,一些产品的生产过程包括原材料准备、加工、组装三个工序。
在准备原材料工序中,每小时能准备100个产品的原材料;在加工工序中,每小时能处理80个产品;在组装工序中,每小时能完成60个产品的组装。
那么整个生产过程的综合产能=100×80×60=480,000个产品每小时。
三、加权平均法四、瓶颈法瓶颈法是一种根据生产过程中的瓶颈工序来确定产能的方法。
瓶颈工序是指生产过程中生产速度最慢的工序,它决定整个生产过程的产能。
计算方法是将瓶颈工序的产能作为整个生产过程的产能。
例如,一些生产过程由三个工序组成,第一工序的产能为100个每小时,第二工序的产能为120个每小时,第三工序的产能为80个每小时。
那么整个生产过程的产能为80个每小时。
五、效益系数法效益系数法是考虑到设备利用率和设备运转稳定性对产能的影响,进行产能计算的方法。
计算方法是将设备的实际生产时间与规定生产时间之比,再乘以单一产能。
例如,一些设备规定每天工作8小时,但实际只能连续运转6小时,那么效益系数为6/8=0.75、设备的单一产能为500个产品每小时,那么该设备的产能=0.75×500=375个产品每小时。
啤酒生产线最大产能计算表

啤酒生产线最大产能计算表摘要:一、引言二、啤酒生产线最大产能计算方法1.产能计算公式2.产能影响因素3.产能优化策略三、实例分析1.某啤酒生产线的具体情况2.按照公式计算最大产能3.分析影响产能的因素4.提出优化方案并验证效果四、结论正文:一、引言随着啤酒市场的不断壮大,提高生产线的产能成为了各大啤酒厂商关注的焦点。
本文旨在介绍如何计算啤酒生产线的最大产能,以及如何优化生产线以提高产能。
二、啤酒生产线最大产能计算方法1.产能计算公式啤酒生产线的产能可以用以下公式表示:产能(吨/小时)= 生产线速度(吨/小时)× 工作时间× 生产效率其中,生产线速度指的是啤酒生产线每小时的产量;工作时间为生产线每天的工作时间;生产效率指的是生产线在单位时间内的工作效率。
2.产能影响因素(1)生产线速度:生产线速度是影响产能的关键因素,提高生产线速度可以提高产能。
(2)工作时间为:工作时间越长,产能越高。
(3)生产效率:提高生产效率可以提高产能。
3.产能优化策略(1)提高生产线速度:通过技术改造或设备升级,提高生产线速度。
(2)延长工作时间:在保证员工休息时间的前提下,适当延长工作时间。
(3)提高生产效率:优化生产流程,减少浪费;提高员工操作技能,提高生产效率。
三、实例分析1.某啤酒生产线的具体情况某啤酒生产线每小时可以生产10吨啤酒,每天工作8小时,生产线设备完好,员工操作熟练。
2.按照公式计算最大产能最大产能= 10吨/小时× 8小时× 100% = 800吨/天3.分析影响产能的因素(1)生产线速度:目前生产线速度为10吨/小时,可以考虑提高速度以提高产能。
(2)工作时间:每天工作8小时,可以考虑适当延长工作时间。
(3)生产效率:员工操作熟练,生产效率较高,但还可以通过提高团队合作、优化生产流程等方式进一步提高生产效率。
4.提出优化方案并验证效果(1)提高生产线速度:通过设备升级,将生产线速度提高至12吨/小时。
产能详细计算方法

产能详细计算方法一、绿油工序产能计算公式:1、绿油磨板机(火山灰2台及精磨机1台):参数:D——每月工作时间:29天板之返工率:2%(是否为磨板返工,)T——每天有效工作时间:24-2小时(清洁保养时间,每班1-2小时)- 2小时(维修保养时间,每班1小时)= 20hrs机器故障率:2%V——行板速度: 2.0m/minB——板的宽度:16.0″×0.0254=0.4046m2 S——板面积:2.0 ftQ——产能X——板间间距:0.05mN——机器数量:3(有一台仅能生产闪金板)月产能计算方法:Q = D×T×[V×60?(B+X)] ×S×(1-2%)×(1-2%)×N =29×20×[2×60?(0.4046+0.05)] ×2×(1-2%)×(1-2%)×3=882232ft22、丝印机参数:D——每月工作时间: 29天板之返工率:3%(,,)T——每天有效工作时间:24hrs-2hrs (用膳时间)-2hr (清洁保养时间) –0.5hr(维修保养时间) -2.5hrs (调校和对网时间)=17hrsN——机器数量:18V——单机每小时印板面数:75(平均约60面,包括塞孔不算)2 S——板面积: 2.0 ftQ——产能产能计算方法:Q = D×T×[V?2]×S×(1-3%)×N= 29×17×[75?2]×2×(1-3%)×18=645583ft3、预焗:3.1、六仓隧道炉:参数:D——每月工作时间:29天2 S——板面积: 2.0 ftT——每天有效工作时间: 24-2小时(清洁保养时间)-1小时(维修保养时间)= 21.0hrsV——出板速度: 208panels/hr(周期时间450S,每仓2架*13pnl)板之返工率:3%N——机器数量:2月产能计算方法:Q1 = D×T×V×S×(1-3%)×N= 29×21×208×2×(1-3%)×2=506688ft23.2、单门柜式炉:参数:D——每月工作时间:29天2S——板面积:2.0ftT——每天有效工作时间: 24-4小时(进出板和升温时间)-1小时(清洁保养时间)-1小时(维修保养时间)= 18.0hrsV1——出板速度:117panels/hr(单面20分钟,每次3架*13pnl,比例70%),V2——出板速度:78panels/hr(双面30分钟,每次3架*13pnl, 比例30%)板之返工率:3%N——机器数量:3Q——产能 2月产能计算方法:Q2 = [D×(T×*50%)*V1×S×(1-3%)×3/2]+ [D×(T×*50%)*V2×S×(1-3%)×3]= [29×18×*70%*117×2×(1-3%)×3/2]+ [29×18×*30%*78×2×(1-3%)×3] =195498ft23.3、总月产能:Q = Q1+Q2=506688+195498=702186ft24、曝光机:参数:D——每月有效工作时间: 29天N——机器数量T——每天有效工作时间:24-2小时(做首板)-2小时(维修保养时间)=20.0hrs(应该按每小时曝光的面积算)V——曝光速度:2.4panel/min(每次曝光间隔时间为50s,每次曝光2pnl)2 S——板面积:2.0 ft板返工率: 3%Q——产能月产能计算方法:Q = D×T×V×60(min/hr)×S×(1-3%)×N=29×20×2.4×60(min/hr)×2×(1-3%)×4=648115ft25显影机:参数:D——每月有效工作时间:29天2 S——板面积:2.0 ft板返工率: 3%T——每天有效工作时间:24-2小时(清洁保养时间)-1小时(维修保养时间)= 21.0hrs(没有那么长的时间)V——冲板速度:2.3m/minB——板之宽度:16.0″×0.0254=0.4064mN——机器数量:2X——板之间距离:0.05m月产能计算方法:Q = D×T×[V×60?(B+X)] ×S×(1-3%)×N=29×21×[2.3×60?(0.4064+0.05)] ×2×(1-3%)×2=714467ft2二、字符工序产能计算公式:1、丝印机参数:D——月工作时间:29天板之返工率:3%T——每天有效工作时间: 24hrs-0.5hr (清洁保养时间) –0.5hr(维修保养时间) -3hrs (调校和对网时间)(时间太短,应该按换网频率)=20hrs N——机器数量 :16V——印板速度:60面/hr2S——板面积:2.0 ft 单面白字比例30%,双面白字比例70%Q——产能月产能计算方法:Q = [D×T×V×(60/2)×S×(1-3%)×N]*(1+30%) =[29×20×(60/2)×2×(1-3%)×16]*1.3=702124ft22 、后烤:2.1、八仓隧道炉参数:D——每月工作时间:29天2 S——板面积: 2.0 ftT——每天有效工作时间: 24-1小时(清洁保养时间)-1小时(维修保养时间)= 22.0hrsV——出板速度: 97.5panels/hr(周期时间1440S,每仓3架*13pnl) (按塞孔板算烤板)板之返工率:3%, 单面烤板比例20%,双面烤板比例80%N——机器数量:1月产能计算方法:Q1 = [D×T×V×S×(1-3%)×N]*(1-20%/2)= 29×22×97.5×2×(1-2%)×1*0.9=109730ft2 2.2、十仓隧道炉参数:D——每月工作时间:29天2 S——板面积: 2.0 ftT——每天有效工作时间: 24-1小时(清洁保养时间)-1小时(维修保养时间)= 22.0hrsV——出板速度: 156panels/hr(周期时间900S,每仓3架*13pnl)板之返工率:3%, 单面烤板比例20%,双面烤板比例80%N——机器数量:1月产能计算方法:Q2 = [D×T×V×S×(1-3%)×N]*(1-20%/2)= 29×22×156×2×(1-3%)×1*0.9=175568ft22.3、双门柜式炉:参数:D——每月工作时间:29天2S——板面积:2.0ftT——每天有效工作时间: 24-4小时(进出板和升温时间)-1小时(清洁保养时间)-1小时(维修保养时间)= 18.0hrsV1——出板速度:130panels/hr(每炉烤板时间30分钟,每次5架*13pnl) 板之返工率:3%,单面烤板比例20%,双面烤板比例80%N——机器数量:3月产能计算方法:Q3 = [D×T×V×S×(1-3%)×N]*(1-20%/2) = 29×18×130×2×(1-3%)×3*0.9=355450ft2 2.4、单门柜式炉:参数:D——每月工作时间:29天2S——板面积:2.0ftT——每天有效工作时间: 24-4小时(进出板和升温时间)-1小时(清洁保养时间)-1小时(维修保养时间)= 18.0hrsV1——出板速度:78panels/hr(每炉烤板时间30分钟,每次3架*13pnl)板之返工率:3%,单面烤板比例20%,双面烤板比例80%N——机器数量:4月产能计算方法:Q4 = [D×T×V×S×(1-3%)×N]*(1-20%/2) = 29×18×78×2×(1-3%)×4*0.9=284360ft22.5、月总产能:Q = Q1+Q2+ Q3+Q4=109730+175568+355450+284360=925108ft2 3、碳油丝印参数:D——月工作时间:29天板之返工率:3%T——每天有效工作时间: 24hrs-0.5hr (清洁保养时间) –0.5hr(维修保养时间) -3hrs (调校和对网时间)=20hrsN——机器数量 :5V——印板速度:60面/hr2S——板面积:2.0 ft 单面白字比例30%,双面白字比例70%Q——产能月产能计算方法:Q = [D×T×V×(60/2)×S×(1-3%)×N]*(1+30%) =[29×20×(60/2)×2×(1-3%)×16]*1.3=702124ft2三、表面处理工序产能计算公式1、喷锡1.1、前处理机:参数:D——每月有效工作时间:29天2 S——板面积:2.0 ft板返工率: 1%T——每天有效工作时间:24-2小时(清洁保养时间)-1小时(维修保养时间)= 21.0hrsV——速度:3.0m/minB——板之宽度:16.0″×0.0254=0.4064mN——机器数量:1X——板之间距离:0.05m月产能计算方法:Q = D×T×[V×60?(B+X)] ×S×(1-1%)×N= 29×21×[3×60?(0.4064+0.05)] ×2×(1-1%)×1=475564ft21.2、喷锡机:参数:D——每月有效工作时间:29天2 S——板面积:2.0 ft板返工率: 1%T——每天有效工作时间:24-4小时(清洁保养时间)-1小时(维修保养时间)=19.0hrsV——喷板速度:3.5pnl/minN——机器数量:1月产能计算方法:Q = D×T×[V×60)] ×S×(1-1%)×N= 29×19×[3.5×60] ×2×(1-1%)×1=229106ft2 1.3、后处理机:参数:D——每月有效工作时间:29天2 S——板面积:2.0 ft板返工率: 1%T——每天有效工作时间:24-2小时(清洁保养时间)-1小时(维修保养时间)= 21.0hrsV——速度:3.0m/minB——板之宽度:16.0″×0.0254=0.4064mN——机器数量:1X——板之间距离:0.05m月产能计算方法:Q = D×T×[V×60?(B+X)] ×S×(1-1%)×N= 29×21×[3×60?(0.4064+0.05)] ×2×(1-1%)×1=475564ft2 2、抗氧化:参数:D——每月有效工作时间:29天T——每天有效工作时间:24-2小时(清洁保养时间)-1小时(维修保养时间)= 21.0hrsV——速度:2.6m/minW——有效宽度:24″×0.0254mN——机器数量:1X1——宽度利用率:85%Y1——长度度利用率:85% 板返工率: 1%2210.74—— m和kft之间换算常数月产能计算方法:Q = D×T×W×V×60×X1×Y1×(1-1%)×N×10.74=29×21×0.6096×2.6×60×85%×85%×(1-1%)×1×10.74=444901ft23、沉镍金:3.1、前处理线参数:D——每月有效工作时间:29天2 S——板面积:2.0 ft板返工率: 3%T——每天有效工作时间:24-2小时(清洁保养时间)-1小时(维修保养时间)= 21.0hrsV——速度:2.0m/minB——板之宽度:16.0″×0.0254=0.4064mN——机器数量:1X——板之间距离:0.05m月产能计算方法:Q = D×T×[V×60?(B+X)] ×S×(1-1%)×N=29×21×[2.0×60?(0.4064+0.05)] ×2×(1-3%)×1=310638ft23.2、沉镍金线参数:D——每月有效工作时间:29天2 S——板面积:2.0 ftT——每天有效工作时间:24-3小时(清洁保养时间)-1小时(维修保养时间)= 20.0hrsV——出板速度:120pnl/hr(周期时间10分钟,每次1架*20pnl)N——机器数量:1月产能计算方法:Q = D×T×V ×S×N= 29×21×120 ×2×1=146160ft23.3、洗板线参数:D——每月有效工作时间:29天2 S——板面积:2.0 ft板返工率: 3%T——每天有效工作时间:24-2小时(清洁保养时间)-1小时(维修保养时间)= 21.0hrsV——速度:2.0m/minB——板之宽度:16.0″×0.0254=0.4064mN——机器数量:1X——板之间距离:0.20m月产能计算方法:Q = D×T×[V×60?(B+X)] ×S×(1-1%)×N=29×21×[2.0×60?(0.4064+0.20)] ×2×(1-3%)×1=233798ft24、沉银线:参数:D——每月有效工作时间:29天T——每天有效工作时间:24-2小时(清洁保养时间)-1小时(维修保养时间)= 21.0hrsV——速度:2.0m/minW——有效宽度:24″×0.0254mN——机器数量:1X1——宽度利用率:85%Y1——长度度利用率:85% 板返工率: 1%2210.74—— m和kft之间换算常数月产能计算方法:Q = D×T×W×V×60×X1×Y1×(1-1%)×N×10.74=29×21×0.6096×2.0×60×85%×85%×(1-1%)×1×10.74=342232ft2四、成型工序产能计算公式:1.、锣板:参数:D——每月有效工作时间:29天2 S——板面积:2.0 ftT——每天有效工作时间:24-1小时(清洁保养时间)-2小时(做Fixture及测首板时间)= 21.0hrsT——平均每首板cycle time:0.45hr CP——平均每叠块数:3N——机器数量:1n——单机锣头数量:4月产能计算公式:Q = D×T×P×S×N×n?T= 29×21×3×2×11×4?0.45=357280 C2、啤板:D——每月有效工作时间:29天T——每天有效工作时间:24-1小时(清洁保养时间)-2小时(上下啤模及测首板时间)= 21.0hrs, T——每小时啤板次数:300p S——每啤一次面积:0.3ft2, 20%需啤板两次N——机器数量:10月产能计算公式:Q = D×T×T×S×[1-(20%?2)]×N= 29×21×300×0.4×0.9×10=493290ft2 p3、洗板机参数:D——每月有效工作时间:29天T——每天有效工作时间:24-2小时(清洁保养时间)-1小时(维修保养时间)= 21.0hrsV——速度:2.0m/minW——有效宽度:23″×0.0254mN——机器数量:1X1——宽度利用率:85%Y1——长度度利用率:85% 板返工率: 1%2210.74—— m和kft之间换算常数月产能计算方法:Q = D×T×W×V×60×X1×Y1×(1-1%)×N×10.74=29×21×0.5842×3.0×60×85%×85%×(1-1%)×1×10.74=491958ft2。
生产能力计算公式

生产能力计算公式
生产能力的计算公式
生产能力是指在一定时间内,通过一定的设备和生产条件,以一定的技术水平和劳动条件,以满足某种生产要求的产品数量的一种能力。
它是衡量一个企业发展水平和生产能力的重要标志。
生产能力的计算公式一般有三种:
1、机器投入式计算公式:机器投入式生产能力=机器数量×机器产能;
2、劳动投入式计算公式:劳动投入式生产能力=劳动力数量×单位劳动产能;
3、资金投入式计算公式:资金投入式生产能力=资金投入金额×资金投入比率。
生产能力的计算公式是衡量企业生产效率的重要指标,它是依据实际生产情况,综合考虑机器、劳动力和资金投入等多种要素,根据一定的科学原理,分析和推算出来的。
因此,企业在了解生产能力的计算公式时,一定要深入分析,全面考虑各种因素和相关因素,才能更好地提高生产能力。
此外,企业还要不断加强技术的更新,提高劳动力的素质,做好资
金的安排,提高生产能力,这样才能保证生产能力的计算公式的准确性,最终实现企业的可持续发展。
产能等计算公式范文

产能等计算公式范文产能是指单位时间内生产所能完成的产品数量或提供的服务量。
对于不同的行业和企业,产能的计算方法也有所不同。
本文将介绍几种常用的产能计算公式,并对其应用进行详细说明。
1.产能计算公式一:产能=单位时间内生产的产品数量这是最简单直接的计算公式,适用于生产同种产品的企业。
例如,一个工厂每小时能够生产1000台手机,那么其产能为1000台手机/小时。
2.产能计算公式二:产能=单位时间内能够完成的产品的加工工序数量×单位时间内每个加工工序的平均处理时间这个计算公式适用于产品生产过程包含多个工序的情况,且每个工序的处理时间相对固定。
例如,一个工厂生产自行车,每辆自行车包含3个工序:组装、喷漆和包装。
如果单位时间内可以完成10个组装、10个喷漆和10个包装工序,且每个工序的平均处理时间分别为1小时、0.5小时和0.2小时,那么该工厂的产能为10个组装工序×1小时/组装+10个喷漆工序×0.5小时/喷漆+10个包装工序×0.2小时/包装=14小时/单位时间。
3.产能计算公式三:产能=单位时间内的工作时间×平均每小时生产率这是一种常用的计算公式,适用于大部分企业,包括制造业和服务业。
工作时间指的是单位时间内实际用于生产或提供服务的时间,例如,每天8小时工作时间、一周5天工作时间等。
平均每小时生产率指的是单位时间内单位劳动力或资源所能完成的工作量,例如,每人每小时产能、每台机器每小时产能等。
4.产能计算公式四:产能=单位时间内可利用的生产设备数量×单位时间内每台设备的平均运行时间×单位时间内每台设备的平均生产效率这个计算公式适用于需要大量生产设备的企业,如制造业的车间。
可利用的生产设备数量指的是单位时间内可用于生产的设备数量,例如,每天有10台机床可用于生产。
每台设备的平均运行时间指的是单位时间内每台设备的实际工作时间,例如,每台机床每小时工作45分钟。
如何计算标准工时和产能?
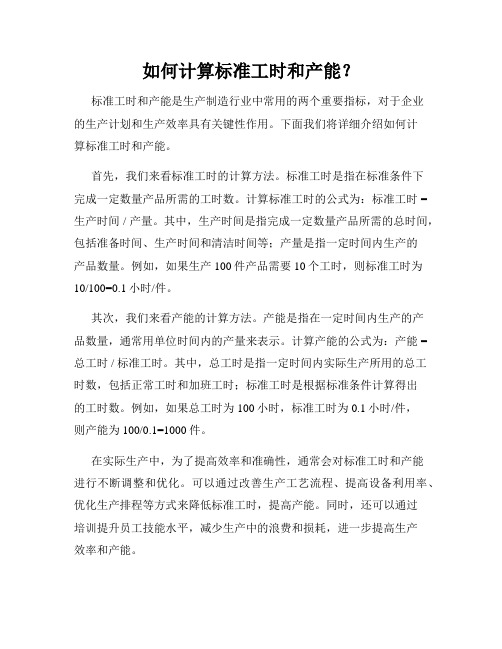
如何计算标准工时和产能?标准工时和产能是生产制造行业中常用的两个重要指标,对于企业的生产计划和生产效率具有关键性作用。
下面我们将详细介绍如何计算标准工时和产能。
首先,我们来看标准工时的计算方法。
标准工时是指在标准条件下完成一定数量产品所需的工时数。
计算标准工时的公式为:标准工时 = 生产时间 / 产量。
其中,生产时间是指完成一定数量产品所需的总时间,包括准备时间、生产时间和清洁时间等;产量是指一定时间内生产的产品数量。
例如,如果生产100件产品需要10个工时,则标准工时为10/100=0.1小时/件。
其次,我们来看产能的计算方法。
产能是指在一定时间内生产的产品数量,通常用单位时间内的产量来表示。
计算产能的公式为:产能 = 总工时 / 标准工时。
其中,总工时是指一定时间内实际生产所用的总工时数,包括正常工时和加班工时;标准工时是根据标准条件计算得出的工时数。
例如,如果总工时为100小时,标准工时为0.1小时/件,则产能为100/0.1=1000件。
在实际生产中,为了提高效率和准确性,通常会对标准工时和产能进行不断调整和优化。
可以通过改善生产工艺流程、提高设备利用率、优化生产排程等方式来降低标准工时,提高产能。
同时,还可以通过培训提升员工技能水平,减少生产中的浪费和损耗,进一步提高生产效率和产能。
总之,计算标准工时和产能是企业管理中至关重要的一环,它直接影响到生产效率和盈利能力。
只有通过科学合理地计算和分析标准工时和产能,企业才能更好地制定生产计划、合理安排生产资源,提高生产效率,降低成本,实现经济效益最大化。
希望以上内容对您有所帮助。
标准产能计算公式
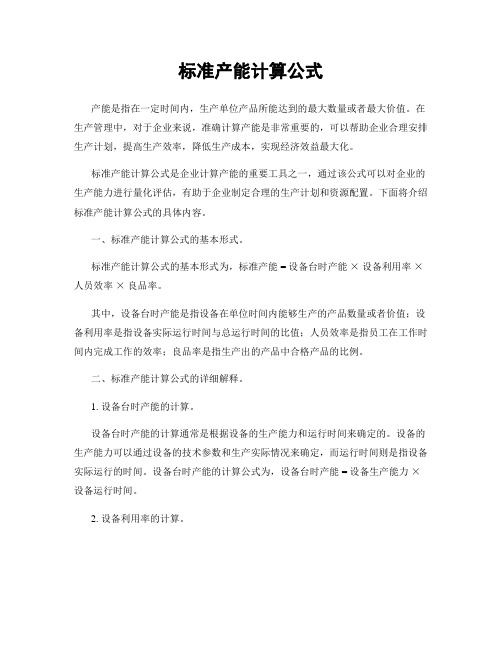
标准产能计算公式产能是指在一定时间内,生产单位产品所能达到的最大数量或者最大价值。
在生产管理中,对于企业来说,准确计算产能是非常重要的,可以帮助企业合理安排生产计划,提高生产效率,降低生产成本,实现经济效益最大化。
标准产能计算公式是企业计算产能的重要工具之一,通过该公式可以对企业的生产能力进行量化评估,有助于企业制定合理的生产计划和资源配置。
下面将介绍标准产能计算公式的具体内容。
一、标准产能计算公式的基本形式。
标准产能计算公式的基本形式为,标准产能 = 设备台时产能×设备利用率×人员效率×良品率。
其中,设备台时产能是指设备在单位时间内能够生产的产品数量或者价值;设备利用率是指设备实际运行时间与总运行时间的比值;人员效率是指员工在工作时间内完成工作的效率;良品率是指生产出的产品中合格产品的比例。
二、标准产能计算公式的详细解释。
1. 设备台时产能的计算。
设备台时产能的计算通常是根据设备的生产能力和运行时间来确定的。
设备的生产能力可以通过设备的技术参数和生产实际情况来确定,而运行时间则是指设备实际运行的时间。
设备台时产能的计算公式为,设备台时产能 = 设备生产能力×设备运行时间。
2. 设备利用率的计算。
设备利用率是指设备实际运行时间与总运行时间的比值,通常通过设备的运行记录来确定。
设备利用率的计算公式为,设备利用率 = 设备实际运行时间 / 总运行时间。
3. 人员效率的计算。
人员效率是指员工在工作时间内完成工作的效率,通常可以通过工作时间和完成工作的数量或者价值来确定。
人员效率的计算公式为,人员效率 = 完成工作的数量或者价值 / 工作时间。
4. 良品率的计算。
良品率是指生产出的产品中合格产品的比例,通常可以通过抽样检验或者全面检验来确定。
良品率的计算公式为,良品率 = 合格产品数量 / 总产品数量。
三、标准产能计算公式的应用。
标准产能计算公式可以应用于各种生产领域,例如制造业、加工业、服务业等。
产能计算方法

产能计算方法产能是指在一定时间内单位设备或单位工人所能生产的产品数量。
产能计算是企业生产管理中非常重要的一环,它可以帮助企业合理安排生产计划,提高生产效率,降低生产成本,从而提升企业竞争力。
下面将介绍几种常用的产能计算方法。
1. 时间效率法。
时间效率法是最常用的产能计算方法之一。
它是通过统计生产过程中的实际生产时间和计划生产时间,来计算设备或工人的产能。
具体计算公式为:时间效率 = (实际生产时间 / 计划生产时间) 100%。
例如,某设备计划生产时间为8小时,实际生产时间为7小时30分钟,则时间效率为(7.5 / 8) 100% = 93.75%。
通过时间效率法可以直观地了解设备或工人的生产效率,有助于发现生产过程中的浪费和瓶颈,进而进行优化调整。
2. 能力利用率法。
能力利用率法是另一种常用的产能计算方法。
它是通过统计设备或工人的实际生产量和理论生产量,来计算产能。
具体计算公式为:能力利用率 = (实际生产量 / 理论生产量) 100%。
例如,某设备在一天内理论上可以生产1000个产品,实际生产了920个产品,则能力利用率为(920 / 1000) 100% = 92%。
通过能力利用率法可以评估设备或工人的生产能力是否得到充分利用,有助于发现生产过程中的资源浪费和效率低下的环节。
3. 综合效率法。
综合效率法是将时间效率和能力利用率结合起来进行产能计算的方法。
具体计算公式为:综合效率 = 时间效率能力利用率。
例如,某设备的时间效率为95%,能力利用率为90%,则综合效率为95% 90% = 85.5%。
综合效率法可以综合考虑生产时间和生产量两个因素,对设备或工人的产能进行全面评估,有助于找出生产过程中的瓶颈和提升空间。
总结。
产能计算是企业生产管理中的重要工作,选择合适的产能计算方法可以帮助企业更好地了解生产状况,发现问题并加以解决,提高生产效率,降低成本,增强竞争力。
以上介绍的时间效率法、能力利用率法和综合效率法是常用的产能计算方法,企业可以根据自身的实际情况选择合适的方法进行产能计算,以实现持续稳定的生产和经营。
产能计算方法

产能核算方式一:工时换算1、各车间选取本车间一种近三年工艺、生产方式较为稳定的产品作为参照,设置其产能指数为1,其人均每小时产量为P0;2、各车间报上各类产品在不需要其他班组帮忙情况下一个工作日(8小时)的最大理想产量M i和对应班组人数N i (以近三月生产情况作为参考,数据仅用在不同产品产能指数换算,不作为生产能力依据);(此条目方法待定,如果能够区分过往月份产品由对应班组生产数和非对应班组生产数的话可尝试通过具体工时与产量换算)3、如一个班组生产一单位本职产品i的周期为H,车间其他班组生产产品i的周期为I,则需商定一个周期比例系数I/H (即非熟练工人工时损耗);(此条目方法待定,如果能够区分过往月份产品由对应班组生产数和非对应班组生产数的话可尝试通过具体工时与产量换算)4、产品的理论人均每小时产量P=日产量/ (8*班组人数),产品i的产能指数为P i /P。
;5、产能计算方式:以十一车间I段为例,设低压柜为参照产品,其产能指数为1,配电箱产能指数为0.4,配电箱工人生产低压柜周期比例系数为1.4,低压柜工人生产配电箱周期比例系数为 1.3,七月共生产低压柜800台,配电箱100台,其中100台低压柜为配电箱工人生产,则产能总值为800*1 + 100*0.4,此外补偿产能(换班生产补偿)为100*1.4-100,七月份如全部生产低压柜的话可生;.产[800*1+ (100*0.4) /1.4]/1台,全部生产配电箱的话可生产[700/(1.3*0.4) ]+ (100*1.4) /0.4+100 台;6、各车间每月上报生产任务完成情况时需注明各类产品由对应班组人员生产台数和非对应班组人员生产台数。
产能核算方式二:简化投入产出分析鉴于电气各分厂之间物资流整体较为明晰,可考虑在分厂间甚至车间间进行投入产出统计,减少造成产值虚高现象的可能性,便于进行分析。
产能计算方法
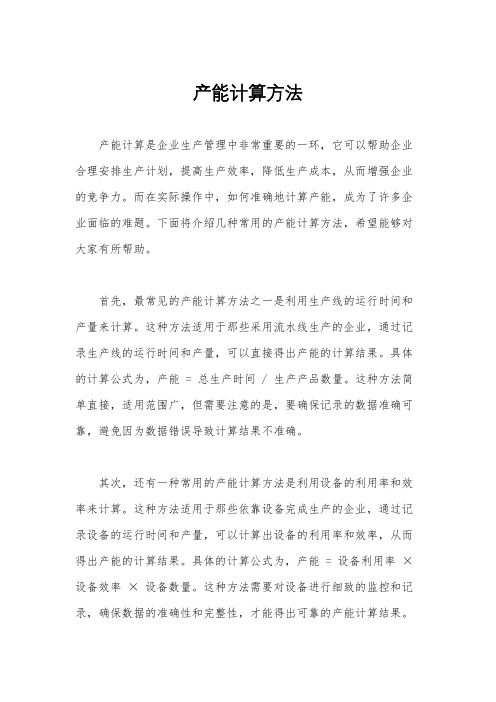
产能计算方法产能计算是企业生产管理中非常重要的一环,它可以帮助企业合理安排生产计划,提高生产效率,降低生产成本,从而增强企业的竞争力。
而在实际操作中,如何准确地计算产能,成为了许多企业面临的难题。
下面将介绍几种常用的产能计算方法,希望能够对大家有所帮助。
首先,最常见的产能计算方法之一是利用生产线的运行时间和产量来计算。
这种方法适用于那些采用流水线生产的企业,通过记录生产线的运行时间和产量,可以直接得出产能的计算结果。
具体的计算公式为,产能 = 总生产时间 / 生产产品数量。
这种方法简单直接,适用范围广,但需要注意的是,要确保记录的数据准确可靠,避免因为数据错误导致计算结果不准确。
其次,还有一种常用的产能计算方法是利用设备的利用率和效率来计算。
这种方法适用于那些依靠设备完成生产的企业,通过记录设备的运行时间和产量,可以计算出设备的利用率和效率,从而得出产能的计算结果。
具体的计算公式为,产能 = 设备利用率× 设备效率× 设备数量。
这种方法需要对设备进行细致的监控和记录,确保数据的准确性和完整性,才能得出可靠的产能计算结果。
另外,还有一种常用的产能计算方法是利用劳动力的利用率和效率来计算。
这种方法适用于那些依靠人工完成生产的企业,通过记录劳动力的工作时间和产量,可以计算出劳动力的利用率和效率,从而得出产能的计算结果。
具体的计算公式为,产能 = 劳动力利用率× 劳动力效率× 劳动力数量。
这种方法需要对劳动力进行合理的分配和管理,提高劳动力的利用率和效率,才能提高产能。
综上所述,产能计算是企业生产管理中非常重要的一环,而产能计算方法的选择取决于企业的实际情况。
无论是利用生产线的运行时间和产量、设备的利用率和效率,还是劳动力的利用率和效率,都需要对数据进行准确记录和分析,确保计算结果的准确性和可靠性。
希望以上介绍的产能计算方法能够对大家有所帮助,帮助企业合理安排生产计划,提高生产效率,降低生产成本,从而增强企业的竞争力。
- 1、下载文档前请自行甄别文档内容的完整性,平台不提供额外的编辑、内容补充、找答案等附加服务。
- 2、"仅部分预览"的文档,不可在线预览部分如存在完整性等问题,可反馈申请退款(可完整预览的文档不适用该条件!)。
- 3、如文档侵犯您的权益,请联系客服反馈,我们会尽快为您处理(人工客服工作时间:9:00-18:30)。
计算生产能力
生产能力(产能)对于所有企业以及企业所有层级来说,都是一个重要的问题。
生产能力是指一个作业单元满负荷生产所能处理的最大限度。
这里的作业单元可以是一个工厂、部门、机器或单个工人。
在计算生产能力时要把握以下内容:1.确定生产能力的计算单位
由于企业种类的广泛性,不同企业的产品和生产过程差别很大,在计算生产能力以前,必须确定本企业的生产能力计量单位。
(1)投入和产出量
生产能力同投入量和产出量密切相关,不同的企业可以根据自身的性质和其他情况选择投入量或产出量作为生产能力的计量单位。
当企业以产出量作为计量单位时,则需考虑企业生产的产品种类有多少,如果只有一种主要产品,则可以以该产品作为计量单位;如果生产多种产品,则很难以其中某一种产品的产出量作为整体的计量单位,这时可采用代表产品计量法。
选择出代表企业专业方向、产量与工时定额乘积最大的产品作为代表产品,其他的产品可利用换算系数换算到代表产品。
换算系统Ki的计算公式如下:
Ki=ti/to
式中:Ki——i产品的换算系数;
ti——i产品的时间定额;
to——代表产品的时间定额。
有时企业用产出量计算生产能力准确度不高,不能很好的反映生产能力,则可以用投入量作为计量单位,如总设备数、装机容量等。
(2)以原材料处理量为计量单位
有的企业使用单一固定的原材料生产多种产品,这时以年处理原材料的数量作为生产能力的计量单位是比较适量的。
这类企业的生产特征往往是分解型的,即使用一种主要原料,分解制造出多种产品。
2.确定影响生产能力的因素
(1)产品因素
产品设计对生产能力有巨大的影响。
如果生产相似产品,作业系统生产这类产品的能力要比后续产品不同的生产能力大。
一般来说,产出越相近,其生产方式和材料就越有可能实现标准化,从而能达到更大的生产能力。
此外设计的特定产品组合也必须加以考虑,因为不同产品有不同的产量。
(2)人员因素
组成一项工作的任务、涉及活动的各类人员以及履行一项任务需要的培训、技能和经验对潜在和实际产出有重要的影响。
另外,相关人员的动机、缺勤和滚动与生产能力也有着直接的联系。
(3)设施因素
生产设施的设计,包括厂房大小以及为扩大规模留有的空间也是一个关键的影响因素。
厂址因素,包括运输成本、与市场的距离、劳动供应、能源和扩张空间,也是很重要的因素。
同样,工作区的布局也决定着生产作业是否能够平稳执行。
(4)工艺因素
产品工艺设计是决定生产能力的一个明显因素,工艺设计是否合理影响产品质量。
如果产品质量不能达到标准,就会增加产品检验和返工工作,从而导致产量下降。
(5)运作因素
一个组织由于存在不同设备生产能力的矛盾或工作要求的矛盾而产生的排程问题、存货储备的决策、发货的推迟、所采购的原材料部件的合意性,以及质量检验与制程控制,都对有效生产能力具有影响。
(6)其他因素
产品标准,特别是产品最低质量标准,能够限制管理人员增加和使用生产能力的选择余地,比如企业为了达到产品和设备的污染标准,经常会减少有效生产能力。
3.计算成批加工企业的生产能力
这种类型的企业,生产部门的组织采用工艺专业化原则,产品的投料与产出有较长的间隔期及明显的周期性。
它们的生产能力计算与工艺专业化原则划分车间和班组有密切关系。
(1)计算单台设备产能
由于加工的零件不是单一品种,数量可达上百上千种。
所有零件的形状大小不同,加工的工艺步骤也不同,而且加工的时间长短不一,这时不能用产出量计算,而只能采用设备能提供的有效加工时间来计算,称为机时。
计算公式如下:
He=Ho×η=Ho(1-θ)=Fo-S
其中:Ho——年制度工作时间;
η——设备制度工作时间计划利用率;
θ——设备计划修理停工率;
S——设备计划修理停工时间。
(2)计算班组产能
车间班组是最小生产单位,每个班组配备一定数量的加工工艺相同的设备,但它们的性能与能力不一定相同。
所以计算班组生产能力是从单台设备开始,再将这些设备的生产能力整合计算。
如果班组内全部设备的加工技术参数差异不大,则全部设备的时间之和就是班组的生产能力。
如果技术参数相差很大,这时要分别统计不同参数设备的机时,着重查看某些大工件的设备加工能力能否满足生产要求。
(3)确定车间产能
由于班组的加工对象是零件,它们的能力应该以机时计量,而对于车间它的生产对象往往是产品或零部件配套数,所以它的生产能力应该以产量计量。
工时与产量之间的换算是比较简单的。
(4)确定工厂产能
工厂生产能力可以根据主要生产车间的能力来确定,能力不足的车间,可以用调整措施解决。
4.计算流水线企业的生产能力
(1)计算流水线生产能力
流水线的生产能力取决于每道工序设备的生产能力,所以从单台设备开始计算。
计算公式如下:
M单=He/ti
式中:M单——单台设备生产能力;
He——单台设备计划期(年)有效工作时间(小时);
ti——单件产品在该设备上加工的时间定额(小时/件)。
如果工序由一台设备承担时,单台设备的生产能力即为该工序能力。
当工序由N 台设备承担时,工序生产能力为M单×N。
(2)确定车间的生产能力
如果是制造车间,它既有零件加工流水线,又有部件装配流水线,这时它的生产能力应该由装配流水线的能力决定。
即使有个别的零件加工能力低于装配流水线能力,也应该按照这个原则确定。
如果是零件加工车间,每个零件有一条专用生产线,而所有零件又都是为本企业的产品配套,那么该车间的生产能力应该取决于生产能力最小的那条生产线的能力。
(3)确定企业的生产能力
由于各车间之间加工对象和加工工艺差别较大,选用的设备性能差别很大,生产能力不一致,因此,基本生产车间的生产能力通常按主导生产环节来确定。
而当基本生产车间和辅助生产部门的生产能力不一致时,企业应由基本生产车间的生产能力决定。