PFMEA示例
六步法pfmea案例
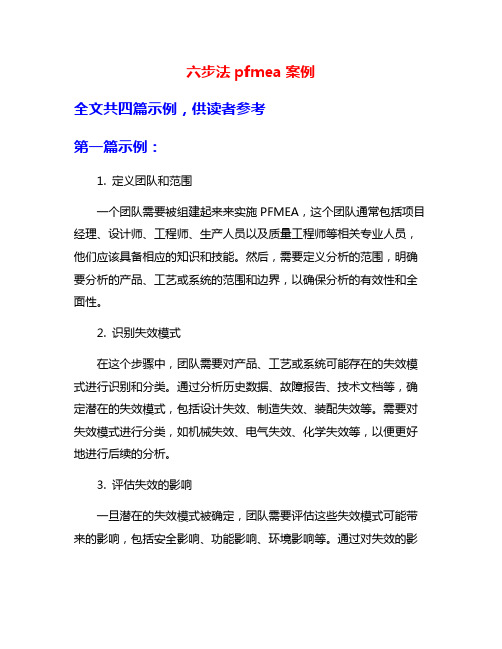
六步法pfmea案例全文共四篇示例,供读者参考第一篇示例:1. 定义团队和范围一个团队需要被组建起来来实施PFMEA,这个团队通常包括项目经理、设计师、工程师、生产人员以及质量工程师等相关专业人员,他们应该具备相应的知识和技能。
然后,需要定义分析的范围,明确要分析的产品、工艺或系统的范围和边界,以确保分析的有效性和全面性。
2. 识别失效模式在这个步骤中,团队需要对产品、工艺或系统可能存在的失效模式进行识别和分类。
通过分析历史数据、故障报告、技术文档等,确定潜在的失效模式,包括设计失效、制造失效、装配失效等。
需要对失效模式进行分类,如机械失效、电气失效、化学失效等,以便更好地进行后续的分析。
3. 评估失效的影响一旦潜在的失效模式被确定,团队需要评估这些失效模式可能带来的影响,包括安全影响、功能影响、环境影响等。
通过对失效的影响进行评估,可以确定关键的失效模式,并优先制定控制措施,以确保产品质量和可靠性。
4. 评估失效的频率和检测能力在这一步骤中,团队需要评估每个失效模式发生的频率和检测能力,即失效的可能性和检测的有效性。
通过对失效频率和检测能力的评估,可以确定高风险的失效模式,并制定相应的控制措施,以减少失效的发生和提高检测的有效性。
5. 制定和实施控制措施基于前面的分析,团队需要制定和实施相应的控制措施,以减少潜在的失效发生和影响。
这些控制措施可以包括设计改进、工艺优化、操作规程更新等,确保产品或系统在生产和使用过程中能够达到预期的性能和可靠性要求。
6. 监控和持续改进团队需要建立一个监控机制来跟踪控制措施的实施效果,并进行持续改进。
通过监控失效模式的发生和影响,可以及时调整和改进控制措施,以确保产品或系统的质量和可靠性得到持续改进。
通过六步法PFMEA的实施,可以帮助团队深入分析潜在失效模式,制定有效的控制措施,从而提高产品质量、减少生产成本和不良问题,提升企业的竞争力。
建议企业在产品设计和生产过程中广泛应用PFMEA方法,并不断优化和完善实施流程,以实现持续的质量改进和效率提升。
pfmea标准案例
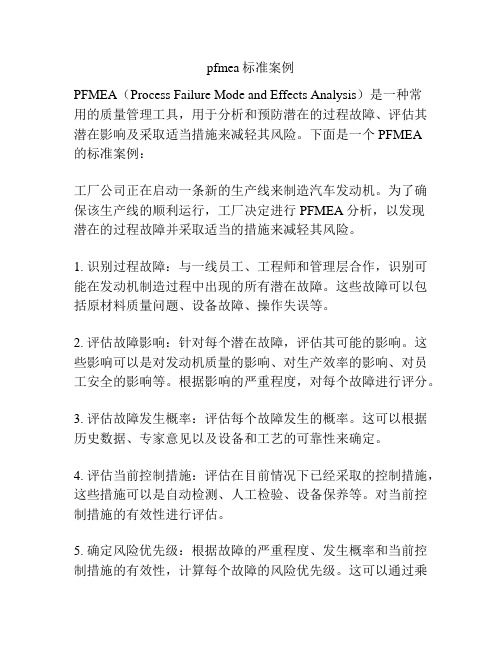
pfmea标准案例PFMEA(Process Failure Mode and Effects Analysis)是一种常用的质量管理工具,用于分析和预防潜在的过程故障、评估其潜在影响及采取适当措施来减轻其风险。
下面是一个PFMEA的标准案例:工厂公司正在启动一条新的生产线来制造汽车发动机。
为了确保该生产线的顺利运行,工厂决定进行PFMEA分析,以发现潜在的过程故障并采取适当的措施来减轻其风险。
1. 识别过程故障:与一线员工、工程师和管理层合作,识别可能在发动机制造过程中出现的所有潜在故障。
这些故障可以包括原材料质量问题、设备故障、操作失误等。
2. 评估故障影响:针对每个潜在故障,评估其可能的影响。
这些影响可以是对发动机质量的影响、对生产效率的影响、对员工安全的影响等。
根据影响的严重程度,对每个故障进行评分。
3. 评估故障发生概率:评估每个故障发生的概率。
这可以根据历史数据、专家意见以及设备和工艺的可靠性来确定。
4. 评估当前控制措施:评估在目前情况下已经采取的控制措施,这些措施可以是自动检测、人工检验、设备保养等。
对当前控制措施的有效性进行评估。
5. 确定风险优先级:根据故障的严重程度、发生概率和当前控制措施的有效性,计算每个故障的风险优先级。
这可以通过乘以这三个因素得到一个风险优先级数值。
6. 制定预防和纠正措施:根据风险优先级数值的高低,确定改进措施的紧急性。
高风险的故障可能需要立即采取纠正措施,而较低风险的故障可以在以后的时间里解决。
7. 实施措施:对确定的措施进行实施,并跟踪它们的有效性。
确保改进措施的有效性并记录结果。
通过这个PFMEA案例,工厂公司可以识别并降低生产线制造发动机过程中的潜在风险,提高发动机质量和生产效率,从而满足客户需求并实现更好的质量管理。
PFMEA实例分析
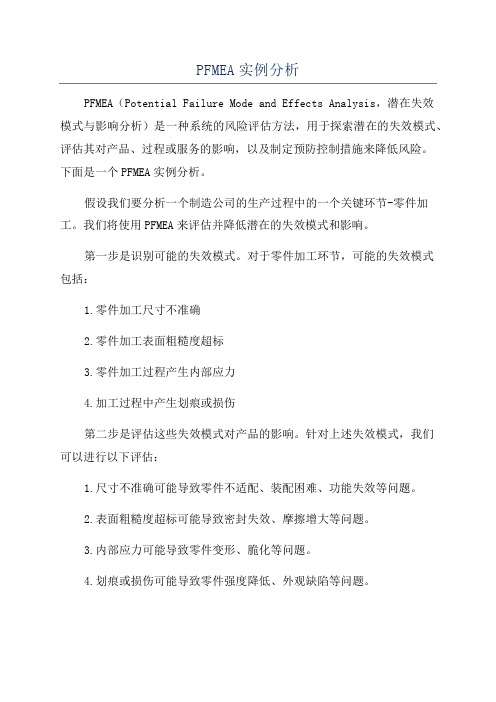
PFMEA实例分析PFMEA(Potential Failure Mode and Effects Analysis,潜在失效模式与影响分析)是一种系统的风险评估方法,用于探索潜在的失效模式、评估其对产品、过程或服务的影响,以及制定预防控制措施来降低风险。
下面是一个PFMEA实例分析。
假设我们要分析一个制造公司的生产过程中的一个关键环节-零件加工。
我们将使用PFMEA来评估并降低潜在的失效模式和影响。
第一步是识别可能的失效模式。
对于零件加工环节,可能的失效模式包括:1.零件加工尺寸不准确2.零件加工表面粗糙度超标3.零件加工过程产生内部应力4.加工过程中产生划痕或损伤第二步是评估这些失效模式对产品的影响。
针对上述失效模式,我们可以进行以下评估:1.尺寸不准确可能导致零件不适配、装配困难、功能失效等问题。
2.表面粗糙度超标可能导致密封失效、摩擦增大等问题。
3.内部应力可能导致零件变形、脆化等问题。
4.划痕或损伤可能导致零件强度降低、外观缺陷等问题。
第三步是评估当前的失效预防控制措施。
我们可以询问工艺工程师、操作员和质量控制人员等,以了解当前生产过程中已经采取的措施。
例如,我们可能已经实施了以下措施:1.使用精确的加工设备和工具,确保尺寸准确性。
2.控制切削速度和刀具磨损情况,以确保表面粗糙度控制在合理范围内。
3.热处理和退火等工艺控制,以减少内部应力的产生。
4.使用防护设备和定期维护保养,以减少划痕或损伤的发生。
第四步是根据评估结果识别潜在的失效模式和影响的优先级。
考虑到产品的重要性、客户需求以及上述评估结果,我们可以确定尺寸不准确和表面粗糙度超标对产品影响最大。
因此,这两个失效模式将被认为是优先级较高的失效模式。
第五步是制定预防控制措施,以降低这些优先级较高的失效模式和影响。
基于上述失效模式和影响的分析,在此应用中我们可能会采取以下预防控制措施:1.实施更严格的尺寸测量和控制,以确保尺寸准确性。
PFMEA分析范例
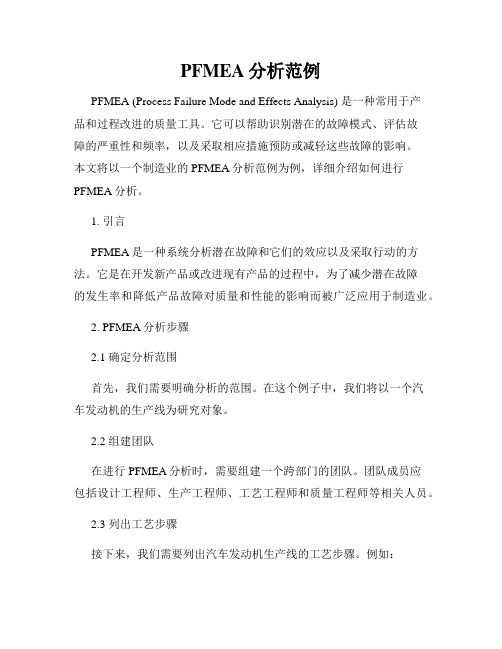
PFMEA分析范例PFMEA (Process Failure Mode and Effects Analysis) 是一种常用于产品和过程改进的质量工具。
它可以帮助识别潜在的故障模式、评估故障的严重性和频率,以及采取相应措施预防或减轻这些故障的影响。
本文将以一个制造业的PFMEA分析范例为例,详细介绍如何进行PFMEA分析。
1. 引言PFMEA是一种系统分析潜在故障和它们的效应以及采取行动的方法。
它是在开发新产品或改进现有产品的过程中,为了减少潜在故障的发生率和降低产品故障对质量和性能的影响而被广泛应用于制造业。
2. PFMEA分析步骤2.1 确定分析范围首先,我们需要明确分析的范围。
在这个例子中,我们将以一个汽车发动机的生产线为研究对象。
2.2 组建团队在进行PFMEA分析时,需要组建一个跨部门的团队。
团队成员应包括设计工程师、生产工程师、工艺工程师和质量工程师等相关人员。
2.3 列出工艺步骤接下来,我们需要列出汽车发动机生产线的工艺步骤。
例如:- 工艺步骤1:原材料采购和检验- 工艺步骤2:加工零部件- 工艺步骤3:组装零部件- 工艺步骤4:测试与质检- 工艺步骤5:包装和出厂2.4 识别潜在故障模式对于每个工艺步骤,团队成员需要一起识别潜在故障模式。
例如,在工艺步骤1中,可能存在以下潜在故障模式:- 检验不准确导致不合格原材料被误用于生产- 供应商延迟交付原材料,导致生产停滞2.5 评估故障严重性和频率在确定潜在故障模式后,团队成员需要评估每个故障的严重性和发生频率。
例如,在工艺步骤1中,检验不准确可能导致以下严重性和频率评估:- 严重性:高,因为不合格原材料可能导致发动机故障,导致安全隐患和质量问题- 频率:低,因为QC检验通常能准确发现不合格原材料2.6 识别潜在故障效应接下来,团队成员需要识别潜在故障对产品和过程的效应。
例如,在工艺步骤1中,检验不准确的潜在故障可能导致以下效应:- 效应1:生产线停滞,影响生产计划和交货时间- 效应2:不合格原材料出现在最终产品中,影响产品质量和客户满意度2.7 采取预防和纠正措施在识别潜在故障效应后,团队成员需要采取相应的预防和纠正措施来减轻故障的影响或防止故障发生。
PFMEA案例
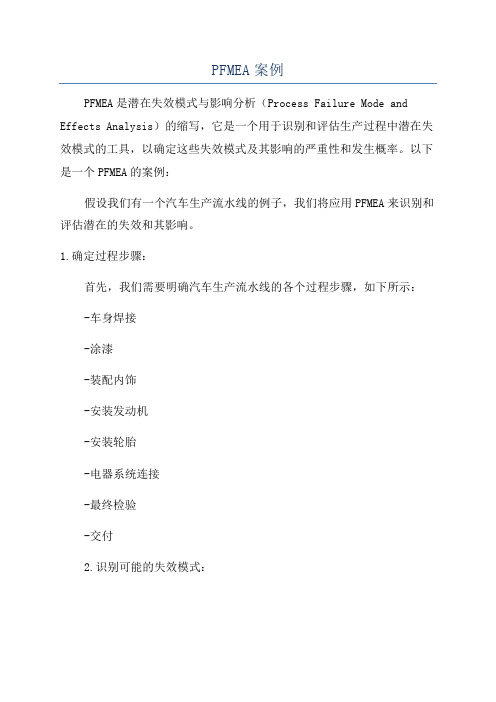
PFMEA案例PFMEA是潜在失效模式与影响分析(Process Failure Mode and Effects Analysis)的缩写,它是一个用于识别和评估生产过程中潜在失效模式的工具,以确定这些失效模式及其影响的严重性和发生概率。
以下是一个PFMEA的案例:假设我们有一个汽车生产流水线的例子,我们将应用PFMEA来识别和评估潜在的失效和其影响。
1.确定过程步骤:首先,我们需要明确汽车生产流水线的各个过程步骤,如下所示:-车身焊接-涂漆-装配内饰-安装发动机-安装轮胎-电器系统连接-最终检验-交付2.识别可能的失效模式:接下来,我们需要识别每个过程步骤中可能出现的失效模式。
例如,在车身焊接过程中,可能出现焊接点不牢固,焊接废弧,焊接接缝不均匀等问题。
相似地,其他过程步骤中也会有各种潜在的失效模式。
3.评估失效模式的严重性:对于每个失效模式,我们需要评估其对整个生产过程和最终产品的严重性。
例如,焊接点不牢固可能导致车身在使用过程中出现裂开的风险,这将对整个汽车的安全性产生严重的影响。
4.评估失效模式的发生概率:除了严重性,我们还需要评估每个失效模式发生的概率。
例如,在对焊接点进行质量控制的流程中,如果该过程的质量控制措施不严密,那么焊接点不牢固的问题就有更大的发生概率。
5.计算并确定潜在失效模式的优先级:最后,我们使用一个数学计算来确定每个失效模式的优先级。
该计算通常是通过将严重性和发生概率乘以一个探测度,来确定每种失效模式的优先级。
通过这种方法,我们可以明确识别并处理那些对整个生产过程和最终产品有重大影响的失效模式。
综上所述,PFMEA是一个重要的工具,可以用于识别和评估生产过程中的潜在失效模式。
通过识别这些模式及其严重性和发生概率,企业可以采取预防措施来降低失效风险,并提高产品和流程的质量。
PFMEA第五版实例

Item (Part #):Process Responsi bilityModelYear(s)/Program(s)Core Team:FAMILY OF PARTS: P1市场部/开发部/制造部/采购部/物流部/质保部POTENTIALFAILURE MODE AND EFFECTS ANALYSIS(PROCESS FMEA)APQP TEAM外购件领取(1);buyer:无影响(1)位料(2);存储在不开箱数量差异(6);buyer:无影响(1)视检查不足(3);操作员和不对成品产生损伤对成品产生损伤supplier:部分(小于100%)外购件需要报废(6);Coustomer:不合格产品流入客户(6);buyer:无影响(1)6检验员技能不合格4技能评定/培训培训记录/技能矩阵更新61442装车方法正确装车方法不正确supplier:产品变形或损坏(6);Coustomer:不合格产品流入客户(6);buyer:无影响(1)6仓管员技能不合格4技能评定/培训培训记录/技能矩阵更新71682产品防护正确产品防护不正确supplier:产品变形或损坏(6);Coustomer:不合格产品流入客户(6);buyer:无影响(1)6仓管员技能不合格4技能评定/培训培训记录/技能矩阵更新71682出货检验240发运Preparedby:FMEADate (Orig.)FMEADate (Rev.)。
PFMEA范本简版范文

PFMEA范本PFMEA范本引言PFMEA(Process Flure Mode and Effects Analysis)是一种风险评估工具,用于识别并消除或减轻制造过程中的潜在失效模式及其可能带来的影响。
本文档提供了一个标准的PFMEA范本,以帮助企业进行风险评估和改进制造过程。
范本结构PFMEA范本包含以下几个主要部分:1. 范本信息:包括范本名称、日期、版本、范围等基本信息。
2. 过程描述:对要评估的过程进行详细描述,包括输入、输出、所涉及的设备和资源等。
3. 团队成员:列出参与评估过程的团队成员及其角色。
4. 风险评估:对每个失效模式进行评估,包括潜在的失效模式、发生频率、严重程度和可检测性。
5. 改进措施:基于风险评估结果,提出相应的改进措施,并列出责任人和计划完成日期。
6. 验证:对改进措施的有效性进行验证,并记录验证结果。
范本信息范本名称:PFMEA范本版本:[填写版本号]范围:[填写评估的过程范围]过程描述[在此处写下要评估的过程的详细描述,包括输入、输出、所涉及的设备和资源等]团队成员角色姓名 --责任人 [填写责任人姓名] -评估员 [填写评估员姓名] -专家 [填写专家姓名] -风险评估对每个失效模式进行评估,评估结果可用高、中、低三个等级表示潜在风险。
以下是一个示例:失效模式发生频率严重程度可检测性风险等级--[失效模式1] [频率等级] [严重程度等级] [可检测性等级] [风险等级] -[失效模式2] [频率等级] [严重程度等级] [可检测性等级] [风险等级] -[失效模式3] [频率等级] [严重程度等级] [可检测性等级] [风险等级] -改进措施基于风险评估结果,制定相应的改进措施并指定责任人和计划完成日期。
以下是一个示例:失效模式改进措施责任人计划完成日期 --[失效模式1] [改进措施] [责任人姓名] [计划完成日期] -[失效模式2] [改进措施] [责任人姓名] [计划完成日期] -[失效模式3] [改进措施] [责任人姓名] [计划完成日期] --验证对改进措施的有效性进行验证,并记录验证结果。
PFMEA分析例子

PFMEA分析例子PFMEA是指过程故障模式和影响分析(Process Failure Mode and Effects Analysis)的缩写,是一种用于识别、评估和控制过程故障的方法。
它通过梳理过程的每一个环节,识别潜在的错误模式,并评估这些错误对产品质量、生产效率和安全性等方面的影响。
本文将通过一个虚构的例子,详细介绍PFMEA的分析过程。
假设汽车制造公司的条生产线负责生产汽车轮胎,下面将针对该生产线进行PFMEA分析。
首先,需要明确所要分析的过程。
这里是汽车轮胎生产线的整个过程,包括原材料采购、橡胶混合、轮胎成型、胶囊生产、硫化等环节。
接下来,需要确定每个环节的输入、输出及其特征。
比如,原材料采购环节的输入为橡胶等轮胎原材料,输出为符合质量要求的原材料,其特征包括橡胶硬度、厚度等。
同理,其他环节也需要明确输入、输出及其特征。
然后,根据以下几个方面,对每个环节的潜在故障模式进行识别和评估。
1.故障模式识别:对每个环节进行详细分析,找出可能出现的故障模式。
比如,在橡胶混合环节,故障模式可能包括橡胶混合不均匀、橡胶粘度异常等。
2.故障原因识别:确定导致每个故障模式出现的原因。
比如,在橡胶混合不均匀的故障模式中,可能原因包括橡胶配方错误、混合时间不足等。
3.故障后果评估:对每个故障模式的后果进行评估,包括对产品质量、生产效率和安全性等方面的影响。
比如,在橡胶混合不均匀的故障模式中,后果可能包括轮胎硬度不均匀、轮胎质量不符合要求等。
4.现有预防控制措施评估:评估目前已有的预防控制措施的有效性。
比如,在橡胶混合不均匀的故障模式中,可能已有的控制措施包括严格控制配方、定期维护混合设备等。
5.现有检测控制措施评估:评估目前已有的检测控制措施的有效性,以避免不合格品进入下一环节。
比如,在橡胶混合不均匀的故障模式中,可能已有的控制措施包括定期抽检混合橡胶的质量。
最后,根据以上分析结果,制定改进措施,包括:1.优化现有预防控制措施。
PFMEA第五版实例全篇

PFMEA第五版实例Item (Part #):Process Responsi bilityModelYear(s)/Program(s)Core Team:FAMILY OF PARTS: P1市场部/开发部/制造部/采购部/物流部/质保部POTENTIALFAILURE MODE AND EFFECTS ANALYSIS (PROCESS FMEA)APQP TEAM外购件领取(1);buyer:⽆影响(1)位料(2);存储在不开箱数量差异(6);buyer:⽆影响(1)视检查不⾜(3);操作员和不对成品产⽣损伤对成品产⽣损伤supplier:部分(⼩于100%)外购件需要报废(6);Coustomer:不合格产品流⼊客户(6);buyer:⽆影响(1)6检验员技能不合格4技能评定/培训培训记录/技能矩阵更新61442装车⽅法正确装车⽅法不正确supplier:产品变形或损坏(6);Coustomer:不合格产品流⼊客户(6);buyer:⽆影响(1)6仓管员技能不合格4技能评定/培训培训记录/技能矩阵更新71682产品防护正确产品防护不正确supplier:产品变形或损坏(6);Coustomer:不合格产品流⼊客户(6);buyer:⽆影响(1)6仓管员技能不合格4技能评定/培训培训记录/技能矩阵更新71682出货检验240发运Preparedby:FMEADate (Orig.)FMEADate (Rev.)。
PFMEA分析范例
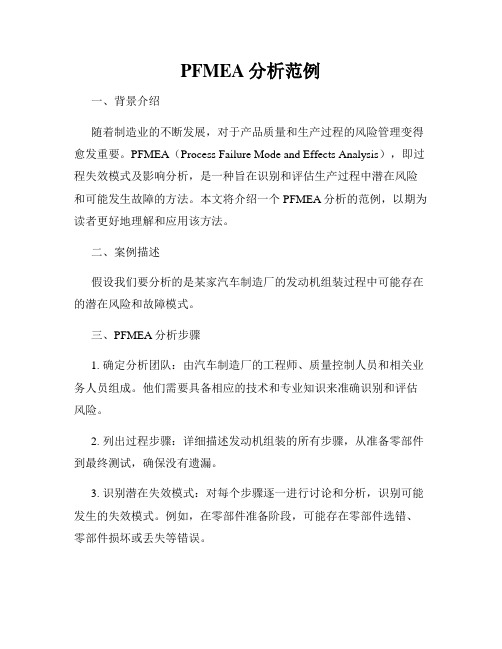
PFMEA分析范例一、背景介绍随着制造业的不断发展,对于产品质量和生产过程的风险管理变得愈发重要。
PFMEA(Process Failure Mode and Effects Analysis),即过程失效模式及影响分析,是一种旨在识别和评估生产过程中潜在风险和可能发生故障的方法。
本文将介绍一个PFMEA分析的范例,以期为读者更好地理解和应用该方法。
二、案例描述假设我们要分析的是某家汽车制造厂的发动机组装过程中可能存在的潜在风险和故障模式。
三、PFMEA分析步骤1. 确定分析团队:由汽车制造厂的工程师、质量控制人员和相关业务人员组成。
他们需要具备相应的技术和专业知识来准确识别和评估风险。
2. 列出过程步骤:详细描述发动机组装的所有步骤,从准备零部件到最终测试,确保没有遗漏。
3. 识别潜在失效模式:对每个步骤逐一进行讨论和分析,识别可能发生的失效模式。
例如,在零部件准备阶段,可能存在零部件选错、零部件损坏或丢失等错误。
4. 评估失效后果:对于每个失效模式,评估其对整个发动机性能和安全性的影响。
例如,零部件选错可能导致发动机无法正常工作或者存在严重的安全隐患。
5. 评估失效发生概率:考虑各种因素,如操作人员技能水平、设备可靠性、材料质量等,评估失效的发生概率。
例如,操作人员技能水平较低可能增加零部件选错的概率。
6. 计算风险优先级数值(RPN):根据失效的后果和发生概率,计算风险优先级数值。
RPN的计算公式为:RPN = 后果严重性 ×发生概率 ×检测能力。
例如,如果某个失效模式的后果严重性评分为10,发生概率为8,检测能力为9,则该失效模式的RPN为720。
7. 制定改进措施:对于RPN值较高的失效模式,制定相应的改进措施来降低风险。
例如,针对零部件选错,可以加强操作人员的培训和审查流程,以减少错误发生的概率。
8. 实施改进措施:将制定的改进措施纳入发动机组装过程,并确保实施有效。
pfmea优秀案例
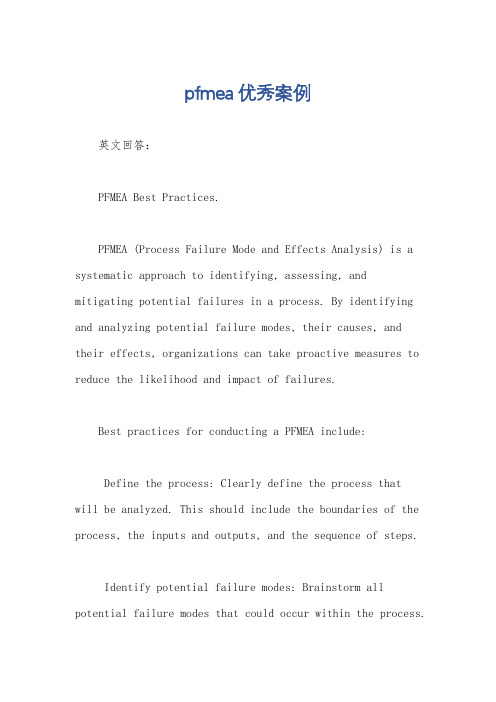
pfmea优秀案例英文回答:PFMEA Best Practices.PFMEA (Process Failure Mode and Effects Analysis) is a systematic approach to identifying, assessing, andmitigating potential failures in a process. By identifying and analyzing potential failure modes, their causes, and their effects, organizations can take proactive measures to reduce the likelihood and impact of failures.Best practices for conducting a PFMEA include:Define the process: Clearly define the process thatwill be analyzed. This should include the boundaries of the process, the inputs and outputs, and the sequence of steps.Identify potential failure modes: Brainstorm all potential failure modes that could occur within the process.This should be done by considering all aspects of the process, including equipment, materials, people, and procedures.Analyze the causes of failure modes: For each failure mode, identify the potential causes. These causes should be specific and actionable.Assess the effects of failure modes: Determine the potential effects of each failure mode. This should include both the immediate effects on the process and the ultimate effects on the customer or end user.Assign risk priority numbers (RPNs): Assign an RPN to each failure mode based on its severity, occurrence, and detectability. The RPN helps prioritize failure modes for mitigation.Develop mitigation strategies: For each failure mode with a high RPN, develop mitigation strategies to reduce the likelihood and impact of the failure. These strategies should be specific and actionable.Implement mitigation strategies: Implement the mitigation strategies that have been developed. This may involve making changes to the process, equipment, materials, people, or procedures.Monitor and evaluate the effectiveness of mitigation strategies: Monitor the effectiveness of the mitigation strategies that have been implemented. This may involve tracking the occurrence of failure modes and assessing the impact of the mitigation strategies.By following these best practices, organizations can improve the effectiveness of their PFMEA process and reduce the likelihood and impact of failures.中文回答:PFMEA优秀案例。
PFMEA分析范例
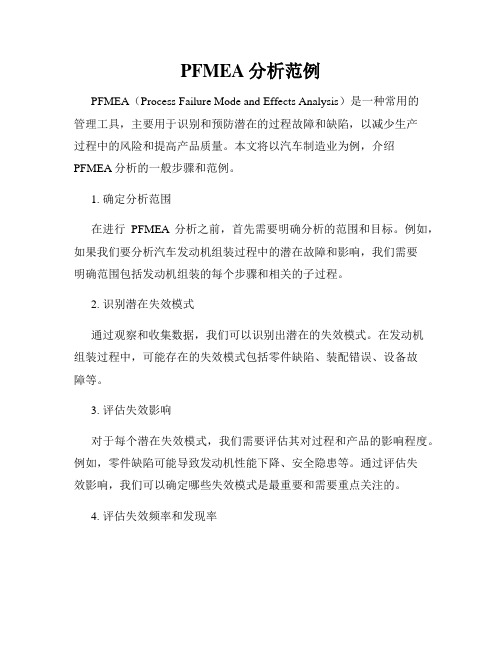
PFMEA分析范例PFMEA(Process Failure Mode and Effects Analysis)是一种常用的管理工具,主要用于识别和预防潜在的过程故障和缺陷,以减少生产过程中的风险和提高产品质量。
本文将以汽车制造业为例,介绍PFMEA分析的一般步骤和范例。
1. 确定分析范围在进行PFMEA分析之前,首先需要明确分析的范围和目标。
例如,如果我们要分析汽车发动机组装过程中的潜在故障和影响,我们需要明确范围包括发动机组装的每个步骤和相关的子过程。
2. 识别潜在失效模式通过观察和收集数据,我们可以识别出潜在的失效模式。
在发动机组装过程中,可能存在的失效模式包括零件缺陷、装配错误、设备故障等。
3. 评估失效影响对于每个潜在失效模式,我们需要评估其对过程和产品的影响程度。
例如,零件缺陷可能导致发动机性能下降、安全隐患等。
通过评估失效影响,我们可以确定哪些失效模式是最重要和需要重点关注的。
4. 评估失效频率和发现率在这一步骤中,我们需要评估潜在失效的频率和发现率。
频率指的是该失效模式在特定时间段内发生的次数,发现率指的是我们能在生产过程中或产品出厂之前检测到该失效模式的概率。
5. 确定风险优先级通过综合考虑失效影响、频率和发现率,我们可以确定每个失效模式的风险优先级。
通常采用风险优先数(RPN)计算方法,RPN = 失效影响 ×频率 ×发现率。
风险优先级高的失效模式意味着需要优先采取预防和纠正措施。
6. 制定预防和纠正措施根据风险优先级,我们可以制定相应的预防和纠正措施来降低潜在失效的风险。
例如,对于零件缺陷,我们可以建立更严格的质量控制流程,提高零件的检验和筛选标准。
7. 实施和监控措施制定好措施后,需要将其实施到实际生产过程中,并进行监控和评估。
通过不断追踪和更新PFMEA表格,我们可以及时发现并纠正新的失效模式,不断提升生产过程的稳定性和产品质量。
总结:本文以汽车制造业为例,介绍了PFMEA分析的一般步骤和范例。
PFMEA范本案例
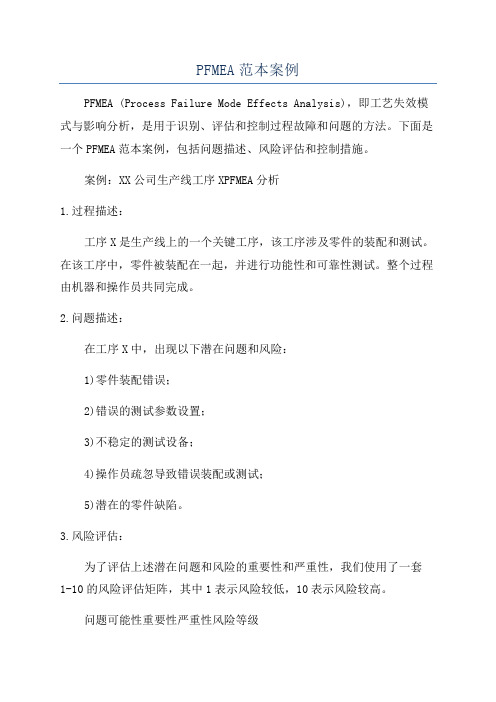
PFMEA范本案例PFMEA (Process Failure Mode Effects Analysis),即工艺失效模式与影响分析,是用于识别、评估和控制过程故障和问题的方法。
下面是一个PFMEA范本案例,包括问题描述、风险评估和控制措施。
案例:XX公司生产线工序XPFMEA分析1.过程描述:工序X是生产线上的一个关键工序,该工序涉及零件的装配和测试。
在该工序中,零件被装配在一起,并进行功能性和可靠性测试。
整个过程由机器和操作员共同完成。
2.问题描述:在工序X中,出现以下潜在问题和风险:1)零件装配错误;2)错误的测试参数设置;3)不稳定的测试设备;4)操作员疏忽导致错误装配或测试;5)潜在的零件缺陷。
3.风险评估:为了评估上述潜在问题和风险的重要性和严重性,我们使用了一套1-10的风险评估矩阵,其中1表示风险较低,10表示风险较高。
问题可能性重要性严重性风险等级零件装配错误87956错误的测试参数设置79856不稳定的测试设备58640操作员疏忽导致错误装配或测试66954潜在的零件缺陷310721注意:风险等级=可能性*重要性*严重性4.控制措施:基于上述评估结果,我们必须采取适当的控制措施来减少或消除潜在问题和风险。
问题控制措施零件装配错误1)提供装配指导书和流程图;2)定期进行员工培训,确保操作员技能;3)引入自动化装配设备,减少人为错误。
错误的测试参数设置1)设定可编程的测试参数,并进行封装;2)详细记录正确的测试参数;3)定期进行设备校准和维护。
不稳定的测试设备1)定期进行设备维护和保养;2)评估设备的可靠性,进行适当的维护。
操作员疏忽导致错误装配或测试1)强调操作员的责任和重要性;2)建立良好的质量管理文化;3)使用自动化检测设备进行装配和测试。
潜在的零件缺陷1)加强供应商质量管理;2)引入100%检验,筛选出潜在问题。
注意:控制措施要具体、可行,并由有效的检验和监控机制支持。
PFMEA分析范例
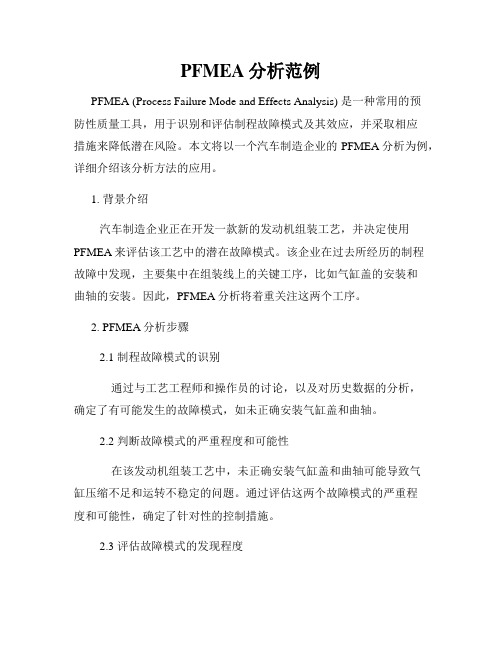
PFMEA分析范例PFMEA (Process Failure Mode and Effects Analysis) 是一种常用的预防性质量工具,用于识别和评估制程故障模式及其效应,并采取相应措施来降低潜在风险。
本文将以一个汽车制造企业的PFMEA分析为例,详细介绍该分析方法的应用。
1. 背景介绍汽车制造企业正在开发一款新的发动机组装工艺,并决定使用PFMEA来评估该工艺中的潜在故障模式。
该企业在过去所经历的制程故障中发现,主要集中在组装线上的关键工序,比如气缸盖的安装和曲轴的安装。
因此,PFMEA分析将着重关注这两个工序。
2. PFMEA分析步骤2.1 制程故障模式的识别通过与工艺工程师和操作员的讨论,以及对历史数据的分析,确定了有可能发生的故障模式,如未正确安装气缸盖和曲轴。
2.2 判断故障模式的严重程度和可能性在该发动机组装工艺中,未正确安装气缸盖和曲轴可能导致气缸压缩不足和运转不稳定的问题。
通过评估这两个故障模式的严重程度和可能性,确定了针对性的控制措施。
2.3 评估故障模式的发现程度考虑到设备和操作员的现有检测手段,确定了对未正确安装气缸盖和曲轴的发现程度。
如采用视觉检测和质量控制人员的检验。
2.4 计算RPN值通过将故障模式的严重程度、可能性和发现程度相乘,得到Risk Priority Number (RPN) 值,用于确定哪些故障模式需要优先处理。
2.5 制定预防和改善措施针对具有较高RPN值的故障模式,制定预防和改善措施,如提供培训、改进工艺规程、增加检测设备等。
2.6 实施和验证措施的有效性实施制定的措施,并通过监控和验证来确保其有效性。
比如设立关键工序的抽样检验,并对不合格品进行追踪分析。
3. 结果与总结通过PFMEA分析,汽车制造企业识别出了发动机组装工艺中的关键故障模式,并相应制定了有效的控制措施。
这些措施将有助于降低潜在的质量风险,提高发动机组装的可靠性和稳定性。
4. 心得体会通过本次PFMEA分析,我们深刻认识到了预防性质量工具的重要性。
PFMEA分析范例
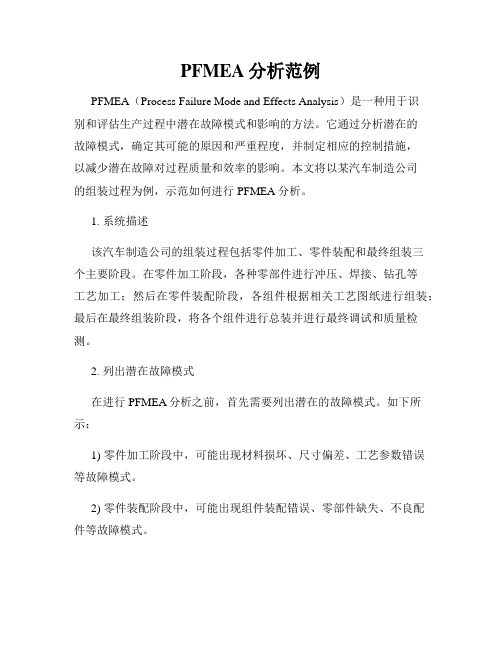
PFMEA分析范例PFMEA(Process Failure Mode and Effects Analysis)是一种用于识别和评估生产过程中潜在故障模式和影响的方法。
它通过分析潜在的故障模式,确定其可能的原因和严重程度,并制定相应的控制措施,以减少潜在故障对过程质量和效率的影响。
本文将以某汽车制造公司的组装过程为例,示范如何进行PFMEA分析。
1. 系统描述该汽车制造公司的组装过程包括零件加工、零件装配和最终组装三个主要阶段。
在零件加工阶段,各种零部件进行冲压、焊接、钻孔等工艺加工;然后在零件装配阶段,各组件根据相关工艺图纸进行组装;最后在最终组装阶段,将各个组件进行总装并进行最终调试和质量检测。
2. 列出潜在故障模式在进行PFMEA分析之前,首先需要列出潜在的故障模式。
如下所示:1) 零件加工阶段中,可能出现材料损坏、尺寸偏差、工艺参数错误等故障模式。
2) 零件装配阶段中,可能出现组件装配错误、零部件缺失、不良配件等故障模式。
3) 最终组装阶段中,可能出现组装错误、传动系统故障、电子系统故障等故障模式。
3. 评估故障原因在列出潜在故障模式之后,需评估每种故障模式的可能原因。
具体评估过程如下:1) 零件加工阶段中,材料损坏的原因可能是供应商提供的原材料质量不合格,尺寸偏差的原因可能是机床设备调整不当,工艺参数错误的原因可能是人工操作失误。
2) 零件装配阶段中,组件装配错误的原因可能是工人操作不规范,零部件缺失的原因可能是供应链管理不善,不良配件的原因可能是供应商提供的配件质量不合格。
3) 最终组装阶段中,组装错误的原因可能是工人操作失误,传动系统故障的原因可能是组装过程中零部件配合不良,电子系统故障的原因可能是控制芯片质量问题。
4. 评估故障严重程度在评估故障原因后,需要评估每种故障模式的严重程度,即故障发生时可能造成的影响程度。
具体评估过程如下:1) 零件加工阶段中,材料损坏可能导致后续组装工序无法进行,尺寸偏差可能导致产品性能下降,工艺参数错误可能导致产品质量问题。
pfmea分析范例

pfmea分析范例PFMEA(Process Failure Mode and Effects Analysis)是一种用于识别和评估过程中潜在故障模式和效应的方法。
下面是一个PFMEA分析的范例:1. 识别过程步骤:确定要分析的具体过程,列出该过程中的所有步骤。
例如,制造汽车发动机的过程可以包括设计、原材料采购、零部件制造、组装等。
2. 确定故障模式:对每个过程步骤,识别可能发生的故障模式。
例如,在零部件制造步骤中,故障模式可能包括材料不合格、尺寸偏差、缺陷等。
3. 评估故障严重性:根据故障的影响程度,为每个故障模式分配一个严重性评分。
评估因素可以包括安全影响、质量问题、工时损失等。
4. 确定故障原因:对每个故障模式,确定可能的原因。
例如,材料不合格的原因可能是供应商质量控制不良,尺寸偏差的原因可能是机器设备故障。
5. 评估故障概率:为每个故障原因分配一个概率评分,表示该故障发生的可能性。
评估因素可以包括供应商绩效、设备维护记录、操作人员技能等。
6. 评估故障检测能力:对每个故障模式,评估现有的检测方法是否能够及时发现故障。
评估因素可以包括检测设备的灵敏度、操作员培训、检测频率等。
7. 计算风险优先级数(RPN):根据故障严重性、故障概率和故障检测能力,计算每个故障模式的RPN值。
RPN值越大,表示风险越高,需要优先处理。
8. 制定改进措施:根据RPN值,确定需要采取的改进措施。
例如,对高RPN值的故障模式,可以考虑优化供应链,改进设备维护计划,提高检测灵敏度等。
9. 跟踪改进效果:实施改进措施后,对其效果进行跟踪和评估。
比较改进前后的RPN 值和其他指标,评估改进是否有效。
以上是一个PFMEA分析的简单范例,具体的分析步骤和评估标准可以根据具体的业务和行业需求进行调整。
PFMEA分析范例

PFMEA分析范例PFMEA(Potential Failure Mode and Effects Analysis)是一种常用于产品设计和生产过程中的风险评估工具。
它通过系统地识别潜在的失效模式,并评估这些失效对产品性能、生产效率和客户满意度的影响,从而帮助企业采取相应的措施来预防和降低潜在失效的风险。
本文将以汽车制造业为例,介绍PFMEA分析的具体步骤和相关应用。
1. 背景介绍汽车制造业面临着严格的质量要求和市场竞争压力。
在生产过程中,如果存在失效模式而未能及时发现或纠正,将会导致产品质量问题、客户投诉以及生产效率下降等严重后果。
因此,采用PFMEA分析方法能够帮助企业降低失效风险,提高产品质量和生产效率。
2. PFMEA分析步骤2.1 制定团队PFMEA分析需要跨职能团队共同参与,包括设计工程师、生产工程师、供应商等相关人员。
团队成员应根据其专业知识和经验来确定潜在失效模式及其影响因素。
2.2 识别失效模式团队成员根据产品设计和制造过程,逐一识别可能存在的失效模式。
例如,在汽车制造过程中,可能存在供应商提供零部件质量不合标准、零部件装配不准确等失效模式。
2.3 评估失效影响针对每个失效模式,团队成员评估其对产品性能、生产效率和客户满意度的影响程度。
评估指标可以根据实际情况进行确定,如利用5W1H法(What、When、Where、Why、How)来进行细致拆解。
2.4 评估失效原因团队成员分析导致每种失效模式的潜在原因,可以运用鱼骨图(也称因果图)或5W1H法来帮助识别。
例如,失效模式为零部件装配不准确,潜在原因可能包括操作员技能不足、装配工具磨损等。
2.5 制定控制措施团队成员针对每个失效模式及其原因,制定相应的控制措施,以预防或降低失效风险。
控制措施可以包括提高操作员培训、更换装配工具等。
2.6 评估控制效果实施控制措施后,团队成员应不定期进行监控和评估,以确定措施的有效性。
如果控制措施无效,需要重新进行评估并采取其他措施。
PFMEA分析范例
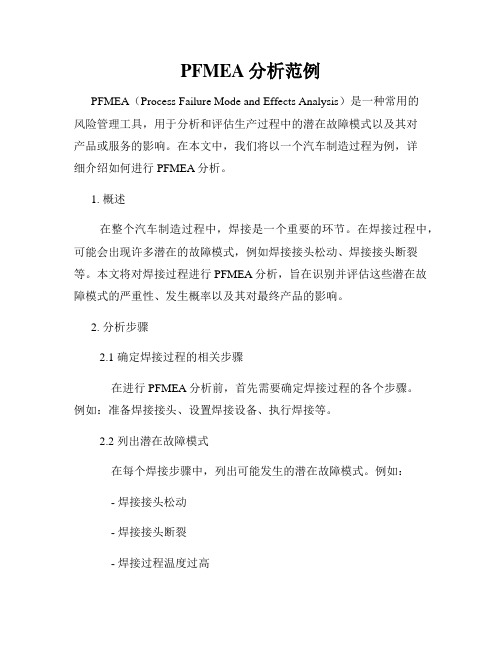
PFMEA分析范例PFMEA(Process Failure Mode and Effects Analysis)是一种常用的风险管理工具,用于分析和评估生产过程中的潜在故障模式以及其对产品或服务的影响。
在本文中,我们将以一个汽车制造过程为例,详细介绍如何进行PFMEA分析。
1. 概述在整个汽车制造过程中,焊接是一个重要的环节。
在焊接过程中,可能会出现许多潜在的故障模式,例如焊接接头松动、焊接接头断裂等。
本文将对焊接过程进行PFMEA分析,旨在识别并评估这些潜在故障模式的严重性、发生概率以及其对最终产品的影响。
2. 分析步骤2.1 确定焊接过程的相关步骤在进行PFMEA分析前,首先需要确定焊接过程的各个步骤。
例如:准备焊接接头、设置焊接设备、执行焊接等。
2.2 列出潜在故障模式在每个焊接步骤中,列出可能发生的潜在故障模式。
例如: - 焊接接头松动- 焊接接头断裂- 焊接过程温度过高2.3 评估潜在故障的严重性对每个潜在故障模式,评估其对产品的严重性影响。
例如: - 焊接接头松动可能导致车身结构不牢固,严重影响安全性。
2.4 评估潜在故障的发生概率对每个潜在故障模式,评估其发生的概率。
例如: - 焊接接头松动的发生概率较低,因为焊接质量控制较好。
2.5 评估潜在故障的发现难度对每个潜在故障模式,评估其在生产过程中被发现的难度。
例如:- 焊接接头松动的发现比较困难,需要进行仔细的检查。
2.6 计算风险优先级数(RPN)风险优先级数是根据潜在故障的严重性、发生概率和发现难度计算得出的。
例如:- 焊接接头松动的RPN = 严重性 ×发生概率 ×发现难度。
2.7 制定预防措施根据风险优先级数的计算结果,制定相应的预防措施来降低故障发生的可能性或对产品的影响。
例如:- 加强焊接接头的检查,确保其牢固性。
2.8 制定控制措施除了预防措施外,制定相应的控制措施来监控焊接过程并及时发现故障。
例如:- 定期对焊接设备进行维护,确保其正常运行。
六步法pfmea案例
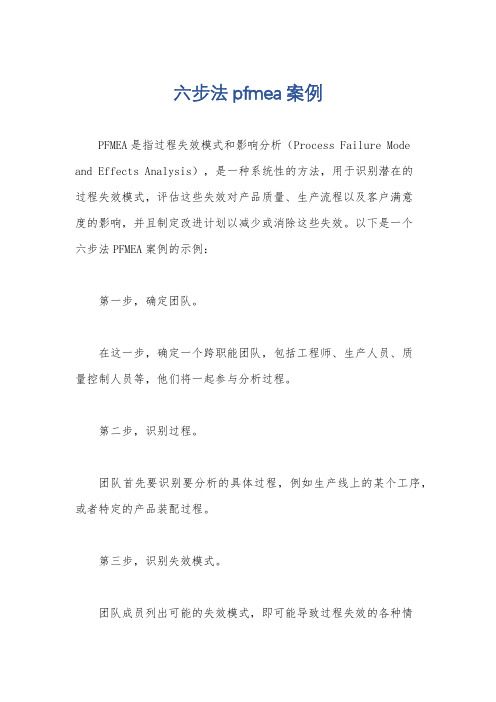
六步法pfmea案例
PFMEA是指过程失效模式和影响分析(Process Failure Mode and Effects Analysis),是一种系统性的方法,用于识别潜在的
过程失效模式,评估这些失效对产品质量、生产流程以及客户满意
度的影响,并且制定改进计划以减少或消除这些失效。
以下是一个
六步法PFMEA案例的示例:
第一步,确定团队。
在这一步,确定一个跨职能团队,包括工程师、生产人员、质
量控制人员等,他们将一起参与分析过程。
第二步,识别过程。
团队首先要识别要分析的具体过程,例如生产线上的某个工序,或者特定的产品装配过程。
第三步,识别失效模式。
团队成员列出可能的失效模式,即可能导致过程失效的各种情
况,例如机器故障、操作失误、材料缺陷等。
第四步,确定失效影响。
团队评估每种失效模式对产品质量、生产流程以及客户满意度的影响程度,确定其严重性。
第五步,确定改进措施。
针对每种失效模式,团队制定相应的改进措施,例如改进工艺流程、提高操作技能、加强设备维护等。
第六步,实施改进并监控。
团队将改进措施付诸实施,并持续监控过程,确保改进效果符合预期,必要时对改进措施进行调整。
通过这六个步骤,团队可以全面地分析潜在的失效模式,并采取相应的措施来提高产品质量和生产效率。
PFMEA案例的实施可以帮助企业减少质量问题和生产故障,提高客户满意度,从而提升竞争力。
- 1、下载文档前请自行甄别文档内容的完整性,平台不提供额外的编辑、内容补充、找答案等附加服务。
- 2、"仅部分预览"的文档,不可在线预览部分如存在完整性等问题,可反馈申请退款(可完整预览的文档不适用该条件!)。
- 3、如文档侵犯您的权益,请联系客服反馈,我们会尽快为您处理(人工客服工作时间:9:00-18:30)。
页码:第1页共8页关键日期:06.10.18 FMEA日期(编制): 06.10.16 编制者:王俊伟
主要参加人:李宝玉、王妙英、许博
页码:第2页共8页关键日期:06.10.18 FMEA日期(编制):06.10.16 编制者:王俊伟
主要参加人:李宝玉、王妙英、许博
页码:第3页共8页关键日期:06.10.18 FMEA日期(编制): 06.10.16 编制者:王俊伟
主要参加人:李宝玉、王妙英、许博
页码:第4页共8页关键日期:06.10.18 FMEA日期(编制): 06.10.16 编制者:王俊伟
主要参加人:李宝玉、王妙英、许博
页码:第5页共8页关键日期:06.10.18 FMEA日期(编制): 06.10.16 编制者:王俊伟
主要参加人:李宝玉、王妙英、许博
页码:第6页共8页关键日期:06.10.18 FMEA日期(编制): 06.10.16 编制者:王俊伟
主要参加人:李宝玉、王妙英、许博
页码:第7页共8页关键日期:06.10.18 FMEA日期(编制): 06.10.16 编制者:王俊伟
主要参加人:李宝玉、王妙英、许博
页码:第8页共8页关键日期:06.10.18 FMEA日期(编制): 06.10.16 编制者:王俊伟
主要参加人:李宝玉、王妙英、许博。