塑胶行业PFMEA案例
塑胶件PFMEA

5
组装
偏位 顾客抱怨 6
素材未卡緊
4
治具松动 作業環境易與產品發 生碰撞 刮伤 外观不良, 造成客訴 4 人員操作不标准
3
5
6
泰德兴精密电子(昆山)有限公司
潛在失效模式及效果分析-过程FMEA
组装站 2014.2.25 版 日 次 期
1.0
2014.2.17
ห้องสมุดไป่ตู้
审核 作版
现行过程控制-预防
現行过程控制-探测
4
48
1.机台点检
4
100
1.对作业人员进行教育训练.
4
100
治具做防呆
96 4 72
治具點檢 對流水臺與作業臺表面加防 護,降低碰刮傷機率
80 4 96
1.作業人員目視全檢 加强对作业人员教育,改正作 2.檢驗人員2H/次/4PCS 业手法,SOP中定義輕拿輕 放,堆放不可超過5pcs,且堆 放時需以包裝袋作依托
袁桃丽
改善結果 严 探 R 频 重 测 P 度 度 度 N
泰德兴精密电子(昆山)有
專案名称: MC32 机种 57-110158-02/57-110158-02/57110158-02/57-110158-02/57零件名称: 110158-02 小組成员: 袁桃丽.骆小峰.陆华龙.刘明进. 陈华.董淑涛. 过程责任: 组装站 关键日期: 2014.2.25
潛在失效模式及效果分析-过
严 过程功能 潜在失效 重 潜在失效模式 要求 后果 度 S
分 發 類 潜在失效原因/机 生 等 度 理 级 O
1.产线线速过快,人 員來不及 2.作业员手法不熟练
漏件
影响组装功 能
4
3
PFMEA(汽车产品塑胶件分析案例)
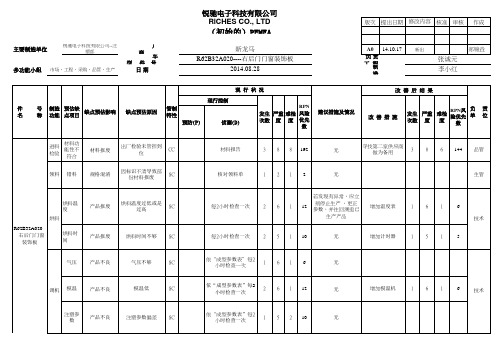
材料报废
出厂检验未管控到 位
CC
领料 错料
规格混淆
因标识不清导致部 份材料报废
SC
材料报告
3 8 8 192
核对领料单
1 21 2
无
寻找第二家供应商 做为备用
3
8
6 144
品管
无
生管
烘料温 度
烘料
R62B32A020---右后门门窗
装饰板
烘料时 间
产品报废
烘料温度过低或是 过高
SC
产品报废
烘料时间不够 SC
主要制造单位
锐驰电子科技有限公司--注 塑部
多功能小组 市场、工程、采购、品管、生产
厂 商车 型 件号 日期
锐驰电子科技有限公司 RiCHES CO., LTD
(初始的)PFMEA
新龙马 R62B32A020----右后门门窗装饰板
2014.08.28
版次 提出日期 修改内容 核准 审核 作成
A0 14.10.17 新出
发生
严重
难检
RPN风 险优先
负 单
责 位
次数 度 度 数
尺寸
报废
1.注塑工艺参数 (模温、压力、射 速)调试不当。
3
8
2
48
由专门人员进行调 试,必要时进行培训 。
由专职技术员调试 并记录到成型参数 表,首未件对比测
量
2
8
1
16
2.读数错误
SC
首未件检 测
依“成型参数表” 每2小时检查一次
2 8 5 80
3 7 4 84 由专门人员负责保养 第一个岗位人员需 2
7
3
42
要对每个产品外观
塑胶件PFMEA 样例
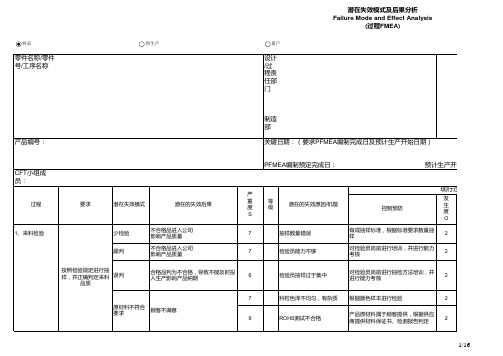
设计/过程责任部门 制造部 关键日期:(要求PFMEA编制完成日及预计生产开始日期) PFMEA编制预定完成日: 预计生产开始日:
严 重 度 S 6
现行过程
等 级 潜在的失效原因/机理 控制预防 发 生 度 O 7
包装箱规格使 造成产品擦伤,导致顾客投诉 用错误
未依据《作业指导书》的包 装要求执行
依据《作业指导书》实施
现行过程
等 级 潜在的失效原因/机理 控制预防 发 生 度 O 2
Байду номын сангаас过程
要求
潜在失效模式
潜在的失效后果
少检验 根据出货检验标准正 漏判 确判定是否可以出货 误判
不合格品进入公司 影响产品质量 不合格品流出公司 顾客投诉 合格品判为不合格, 影响纳期 顾客抱怨
7
抽样数量错误 检验员能力不够
做成抽样标准,根据标准要求数量抽 样 对检验员岗前进行培训,并进行能力 考核 对检验员岗前进行抽检方法培训,并 进行能力考核
现行过程
等 级 潜在的失效原因/机理 控制预防 发 生 度 O 3 模温监控、 成型工艺监控、 3 3 做成生产工艺卡, 根据工艺卡调机 4 3 3 根据生产工艺卡, 模温监控、 成型工艺监控 4 7 3 根据生产工艺卡, 成型工艺监控 根据生产工艺卡, 成型工艺监控 模具定期保养、维护 开机前清洗模具 按照产品《作业指导书》作业 3 3 4 4 3 7
样品 预生产 量产
零件名称/零件号/工序名称 产品编号: CFT小组成员:
严 重 度 S 6 6
设计/过程责任部门 制造部 关键日期:(要求PFMEA编制完成日及预计生产开始日期) PFMEA编制预定完成日: 预计生产开始日:
现行过程
等 级 潜在的失效原因/机理 控制预防 发 生 度 O 7 7
完整实用的过程PFMEA实例(注塑企业)
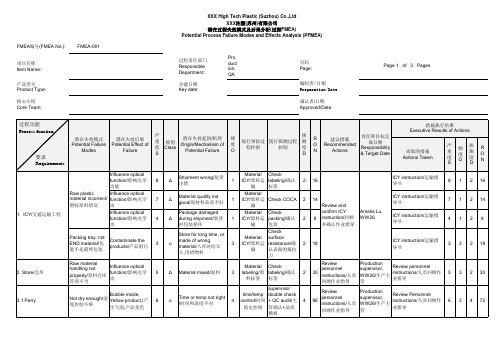
过程责任部门 Responsible Department:
Pro duct ion, QA
关键日期 Key date:
页码 Page:
编制者/日期 Preparation/Date
确认者/日期 Approved/Date
Page 1 of 3 Pages
பைடு நூலகம்
过程功能
Process function 要求
Imaging lens Dia.,
Dim 1: 5.78±0.03 Influence out of spec./镜头 assembly/影响装配
3
直径尺寸超规
Review PM mould
Order start
Production personnel instruction,
o
Wrong insert/嵌入错误
Contaminate the products/产品脏污
3
2. Store/仓库
Raw material handling not properly/原料仓库 管理不当
Influence optical function/影响光学 功
5
3.1 Perry
Not dry enough/湿 度控制不够
1
release
Dim check/尺
plan/订单开 寸确认
2
6
PM mould /点检 磨具
supervisor, incoming inspection WW26/生产主 optical inserts/人员回顾
时包装损坏
输
包装
并确认作业指导
ICY instruction/运输指 导书
ICY instruction/运输指 导书
塑胶产品易开裂物料 PFMEA 模板-(1

清理完成后技术员对清理工 作确认,用无尘布擦拭,无 脏污即可(详见换料作业指
导书进行作业) 技术员开机前对材料进行核 对确认是否按照规范做业。
技术员对加料人员设定的干 燥温度及时间进行确认,选
用设备进行确认.
材料在炮筒停留时间适 当,生产出外观、功能 合格的产品
成型机台与实际零件重量不匹 配,导致材料降解
7 材料在炮筒停留时间过长
成型周期设置不合理,导致生产 7 材料在炮筒停留时间过长 周期过长,导致材料降解
生产设备性能稳定可 靠,产品一致性好,支 持批量生产
螺杆磨损造成储料不稳定或驱动 曲臂磨损造成锁模不稳定,机台 稳定性差,产品一致性不好,可 能出现小概率的不良品
8
注塑机台维护不到位
模温符合理、正确,生 实测多点模温偏低,导致熔接线 8 实测模具温度不够高,致零件内
产出外观、功能合格的 位置强度下降、开裂
应力偏大
产品
注塑压力合理、正确, 注塑压力过大,使产品内应力大 8 注塑压力过大
生产出外观、功能合格
的产品
速度过快会导致材料温度上升而 8 小浇口情况下,注塑速度过快
5
设备维护不到位
生产前5模样品需废弃, 生产前10模内注塑机参数还不稳 5 生产过程控制不完善
10模后注塑趋于稳定, 定,产品一致性不好,不良率高
产品一致性好
8 零件清洗工艺缺失、或不彻底 金属镶件有油污,跟塑胶材料不
兼容
清洗外观、油污的溶剂跟塑胶材 8 清洗剂选择错误 料不兼容
8 模具上模前保养不规范 顶针油、润滑油等模具用油接触
过大,导致材料降解;背压过 小,导致熔胶内气体量过大,材 料易局部降解,产品易产生气 泡,开裂。
新版PFMEA案例-朱春佳老师
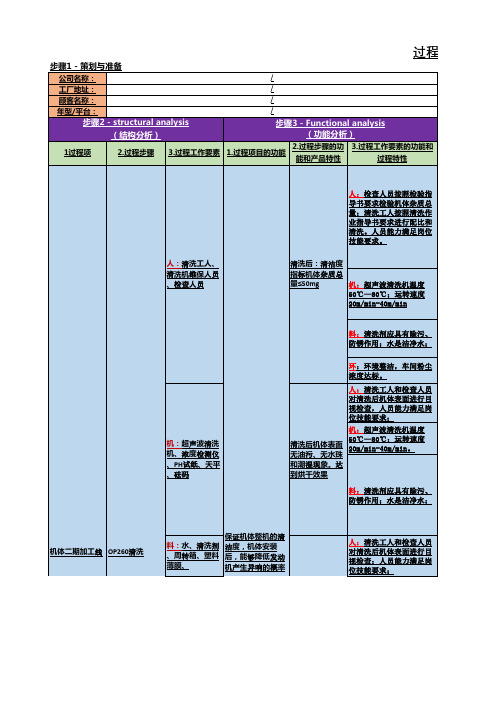
洗后,机体表面无锈蚀、磕碰、划痕过程失
线清洗
证机体整机的清洁度,机体安装后,能够降低发动机产生异响的概率
价进行确认。
2.每季度对维护保养计划的执行情况进行检查确认。
3.每月度对清洗剂的更换频次进行检查确认。
间使用,存在磕碰点;
料:清洗剂不能满足除污、防锈要求,清洗剂过期,未得到监控法:超声波清洗机内的液体未及时更换,液体变质:
计划,对传输带进行维护保养;3.确定清洗剂液体更换周期,并明确在作业标准中。
影响组装或装机后质量异常;
对最终用户影响:无
过程失效模式及后果分析(PFMEA)
对机体表面100%检查针对失效起因:
1.每半年对人员的能力评人员取放工件时与传输带表面碰撞;
机:传输带长时训,提高质量意识。
2.制定维护保养洗过后,机体表面存在锈斑、有磕碰点和划痕影响交付或交付后顾客投诉;
对主机厂影响:
进一步采取措施。
Standard-PFMEA连接器 ) - 实例

模温设备损坏(模具 标准化作业指
温度过低&过高)
导书
3
车间灰尘过多,有异 标准化作业指
物
导书
3
过程参数:气体流量,注 塑速度,注塑温度, 注塑 压力。
标准化作业指
导书
气体流量
(4~7MPa),
气体流量,注塑速 注塑速度(射
度,注塑温度, 注
胶段 55%~65%,注
3
塑压力设定不合理
塑温度
(300~320),
注塑压力(射
胶段
30~35%),
cess FMEA) 过程失效模式及影响分析(过程FMEA)
PFMEA Risk Analysis (Step 5) 过程 FMEA 风险分析 (步骤五)
PFMEA ID Number PFMEA ID 编号
Process Responsibility 过程责任人
Confidentiality Level: 保密级别
胶段
3
塑压力设定不合理 55%~65%,注
塑温度
(300~320),
注塑压力(射
胶段
设备运行不正常
标准化作业指 导书
3
模夹具损坏,未到位
标准化作业指 导书
3
5,调取注塑程序,空运 行,检查设备注塑程序
调取设备程序不正确
标准化作业指 导书
3
6,调试样件,试注塑, 自检确认样品,首件确 认,OK后生产
首件未完全确认OK
标准化作业指 导书
3
5,调取注塑程序,空运 行,检查设备注塑程序
调取设备程序不正确
标准化作业指 导书
3
6,调试样件,试注塑, 自检确认样品,首件确 认,OK后生产
PFMEA参考2010

潜在失效模式及后果分析(P-FMEA)
号/要求模式果度
S 别因/机理
度
O
:
世冠金属塑料制品有
潜在失效模式及后果分析(P-FMEA)
理不干净锌层,导致产
品返工返修
潜在失效模式及后果分析(P-FMEA)严
潜在失效模式及后果分析(P-FMEA)
品返工返修
时/客户拒收
潜在失效模式及后果分析(P-FMEA)
12阳极电解
化皮膜处顾客对外观不满意/镀不上5☆
潜在失效模式及后果分析(P-FMEA)
潜在失效模式及后果分析(P-FMEA)
潜在失效模式及后果分析(P-FMEA)
世冠金属塑料制品有
潜在失效模式及后果分析(P-FMEA)
度D
数
RPN
建议纠正
措施
标完
成日
期
及后果分析(P-FMEA)
品有限公司
及后果分析(P-FMEA)
及后果分析(P-FMEA)探风险
及后果分析(P-FMEA)
及后果分析(P-FMEA)
及后果分析(P-FMEA)
及后果分析(P-FMEA)
及后果分析(P-FMEA)
品有限公司
及后果分析(P-FMEA)。
PFMEA失效模式分析教学案例

26
9、可检测度(D)评估
可检测度(D)评估表
检测类别:A.防错 B.量具 C.人工检验
27
10、计算RPN值
风险顺序数(RPN): ➢ 风险顺序数(RPN):Risk Priority Number,是严
➢ PFMEA 是一个组织的经验积累,为以后的制程改善提供 了宝贵的参考
➢ PFMEA 的结果能为制订质量控制计划提供正确的、恰当 的根据
➢ PFMEA能引导资源去解决需良品 不生产不良品 不流出不良品
顾客
6
Who – 谁来做PFMEA?
➢ 以工艺工程师为主导,集合跨 部门相关人员,将可能发生的 问题挖掘出来 -- 制造、装配 -- 设计、工程、可靠性 -- 质量管理 -- 采购、设备及其他必要人员
processfmeaprocesspotentialfailuremodeeffectsanalysispfmeapfmea顾客设计生产出货不设计不良品不生产不良品不流出不良品pfmea有助于对制造过程中问题的早期发现从而避免和减少晚期失效带来的损失pfmea是一个组织的经验积累为以后的制程改善提供了宝贵的参考pfmea的结果能为制订质量控制计划提供正确的恰当的根据pfmea以工艺工程师为主导集合跨部门相关人员将可能发生的问题挖掘出来pfmeapfmea是一个事前的行为而不是事后的行为pfmea是一个动态文件初始pfmea必须在试生产前工装准备前各项未考虑的失效模式发现及讨论更新pfmea时间各项未考虑的失效模式发现及讨论动态的pfmea更新pfmea发生频度o评估完成pfmea的13个步骤可检测度d评估10
注塑产品_PFMEA案例

共 4页 编制
最初编 制日期
FMEA 编号
201
FMEA 版本号
A
电话号码
FMEA 最新 更改日期
过程
要求
潜在失效模式 潜在的失效后果
严
重 等 潜在的失效原因/
度级
机理
S
控制预防
产品表面缩水
产品外观不合格 顾客抱怨
产品尺寸偏大 与相关零件不匹配,
或偏小
使顾客不满意
4、注塑成型
通过注塑机和模 产品表面烧焦 具成型生产出颜 色、外观、尺寸 、性能合格的产
2
《成型条件表》每班 次点检
4
48
2/16
编号: 总成
零件名称/零件号/工 序名称
产品编号:
CFT小组成 员:
分总成
潜在的失效模式及后果分析-PFMEA
零件
设 计/ 过 程 责 任 部 门
制 造 部
关键日期:(要求PFMEA编制完成日及预计生产开始日期)
Hale Waihona Puke PFMEA编制预定完成日:
预计生产开始日:8
9/16
2013-01
A/0
措施结果 R
ODP N
10/16
2013-01
A/0
措施结果 R
ODP N
11/16
2013-01
A/0
措施结果 R
ODP N
12/16
2013-01
A/0
措施结果 R
ODP N
13/16
2013-01
A/0
措施结果 R
ODP N
14/16
2013-01
A/0
不正确
作业
7
注塑产品 PFMEA案例

零件名称/零件号/工序名称设计/过程责任部门编制电话号码制造部产品编号:最初编制日期FMEA 最新更改日期CFT小组成员:控制预防发生度O控制探测探测度D采取的措施S1、来料检验少检验不合格品进入公司影响产品质量7抽样数量错误做成抽样标准,根据标准要求数量抽样2检验记录表班长确认456漏判不合格品进入公司影响产品质量7检验员能力不够对检验员岗前进行培训,并进行能力考核2456误判合格品判为不合格,导致不能及时投入生产影响产品纳期6检验员抽样过于集中对检验员岗前进行抽检方法培训,并进行能力考核2448 7料粒色泽不均匀,有杂质根据颜色样本进行检验2投料前确认、记录456 9ROHS测试不合格该产品原材料属于顾客提供,根据供应商提供材料保证书、检测报告判定261082、生产领料根据出料单正确出料原材料出库错误产品特性不能满足顾客要求,顾客投诉8领料员未依据生产任务通知单进行实物确认对领料员、仓库管理员进行岗前教育2投料前确认、记录232要求按照检验规定进行抽样,并正确判定来料品质潜在的失效原因/机理关键日期:(要求PFMEA编制完成日及预计生产开始日期)PFMEA编制预定完成日: 预计生产开始日:8FMEA 编号FMEA 版本号RPN2等级措施结果共 4 页现行过程责任目标/完成日期建议措施过程潜在失效模式潜在的失效后果严重度S原材料不符合要求顾客不满意总成分总成零件零件名称/零件号/工序名称设计/过程责任部门编制电话号码制造部产品编号:最初编制日期FMEA 最新更改日期CFT小组成员:控制预防发生度O控制探测探测度D采取的措施S要求潜在的失效原因/机理关键日期:(要求PFMEA编制完成日及预计生产开始日期)PFMEA编制预定完成日: 预计生产开始日:8FMEA 编号FMEA 版本号RPN2等级措施结果共 4 页现行过程责任目标/完成日期建议措施过程潜在失效模式潜在的失效后果严重度S总成分总成零件零件名称/零件号/工序名称设计/过程责任部门编制电话号码制造部产品编号:最初编制日期FMEA 最新更改日期CFT小组成员:控制预防发生度O控制探测探测度D采取的措施S要求潜在的失效原因/机理关键日期:(要求PFMEA编制完成日及预计生产开始日期)PFMEA编制预定完成日: 预计生产开始日:8FMEA 编号FMEA 版本号RPN2等级措施结果共 4 页现行过程责任目标/完成日期建议措施过程潜在失效模式潜在的失效后果严重度S总成分总成零件零件名称/零件号/工序名称设计/过程责任部门编制电话号码制造部产品编号:最初编制日期FMEA 最新更改日期CFT小组成员:控制预防发生度O 控制探测探测度D 采取的措施S要求潜在的失效原因/机理关键日期:(要求PFMEA编制完成日及预计生产开始日期)PFMEA编制预定完成日: 预计生产开始日:8FMEA 编号FMEA 版本号R P N2等级措施结果共 4 页现行过程责任目标/完成日期建议措施过程潜在失效模式潜在的失效后果严重度S 总成分总成零件首件检查、PQC巡检、自检影响顾客装配顾客抱怨根据生产工艺卡,成型工艺监控8具成型生产出颜色、外观、尺寸、性能合格的产品产品缺胶零件名称/零件号/工序名称设计/过程责任部门编制电话号码制造部产品编号:最初编制日期FMEA 最新更改日期CFT小组成员:控制预防发生度O控制探测探测度D采取的措施S要求潜在的失效原因/机理关键日期:(要求PFMEA编制完成日及预计生产开始日期)PFMEA编制预定完成日: 预计生产开始日:8FMEA 编号FMEA 版本号RPN2等级措施结果共 4 页现行过程责任目标/完成日期建议措施过程潜在失效模式潜在的失效后果严重度S总成分总成零件零件名称/零件号/工序名称设计/过程责任部门编制电话号码制造部产品编号:最初编制日期FMEA 最新更改日期CFT小组成员:控制预防发生度O控制探测探测度D采取的措施S要求潜在的失效原因/机理关键日期:(要求PFMEA编制完成日及预计生产开始日期)PFMEA编制预定完成日: 预计生产开始日:8FMEA 编号FMEA 版本号RPN2等级措施结果共 4 页现行过程责任目标/完成日期建议措施过程潜在失效模式潜在的失效后果严重度S总成分总成零件零件名称/零件号/工序名称设计/过程责任部门编制电话号码制造部产品编号:最初编制日期FMEA 最新更改日期CFT小组成员:控制预防发生度O控制探测探测度D采取的措施S要求潜在的失效原因/机理关键日期:(要求PFMEA编制完成日及预计生产开始日期)PFMEA编制预定完成日: 预计生产开始日:8FMEA 编号FMEA 版本号RPN2等级措施结果共 4 页现行过程责任目标/完成日期建议措施过程潜在失效模式潜在的失效后果严重度S总成分总成零件不合格品进入公司做成抽样标准,根据标准零件名称/零件号/工序名称设计/过程责任部门编制电话号码制造部产品编号:最初编制日期FMEA 最新更改日期CFT小组成员:控制预防发生度O控制探测探测度D采取的措施S要求潜在的失效原因/机理关键日期:(要求PFMEA编制完成日及预计生产开始日期)PFMEA编制预定完成日: 预计生产开始日:8FMEA 编号FMEA 版本号RPN2等级措施结果共 4 页现行过程责任目标/完成日期建议措施过程潜在失效模式潜在的失效后果严重度S总成分总成零件。
2019第五版新版PFMEA 注塑实例

STRUCTURE ANALYSIS
FUNCTION ANALYSIS
FAILURE ANALYSIS
RISK ANALYSIS
OPTIMIZATION
问 题 号
历史/变更授权(适 用时)这一类是可选
栏目
2.1. 过程项 系统、子系统 、零件要素或
过程名称
2.2.过程步 骤
工位编号和 关注要素名
称
2.3.过程工作要 素4M
失效起因/失 效模式的频
度(O)
5.2当前的失效 起因/失效模式
的探测措施 (DC)
失效起 因/失效 模式的 探测度 (D)
5.3PFM EA措施 优先级
5.4特殊 特性
筛选器 代码 (可 选)
6.1预防 措施
6.2探测 措施
6.3责任 人姓名
6.4目标 完成日期
6.5状态
6.6采取 基于证据
的措施
3.1. 过程功能 系统、子系统、 零件要素或过程
的功能
3.2. 过程步骤的功 能和产品特性
(量值为可选项)
3.3. 过程工作要 素的功能和过程
特性
4.1对于上一较高级 别要素和/或最终用
户的影响(FE)
失效影响 的严重度
(S)
4.2关注要素的失 效模式(FM)
4.3工作要素的 失效原因 (FC)
5.1当前的对失 效起因的预防 措施(PC)
确保取件产品无划 伤
使用保护膜贴产品 将珍珠棉气泡袋包 装
产品报废,需要重新 制作,延误交货
5
产品表面划伤
产品未贴保护膜
产品注塑后表 面贴保护膜
3
操作员检查表 面是否划伤
5
L
工艺品生产PFMEA分析范例

注塑过程
① 操作员对作业 生疏产生恐惧心
理 ② 操作员带病上
岗 ③ 精神状态欠佳
机械伤害。 物体打击。
触电 产品损毁/损坏
报废。
4
—操作员对操作指引 不熟;
—操作员带病上岗 生理 —操作员感知延迟、
辨识错误、其他辨识 功能缺陷
①作业指引培训
2
②机器操作培训 ③拒绝员工带病上岗
目测
目视 目视 目视 目视 监督检查
电源测试 外观检查
标准电压下用电源 进行测试
2
30
无
试装
2
40
加强对检验员培训,主管定 期检查
已按计划内实 施,符合要求
4
3
2
24
误导安全库存数 材料错误使用, 量/材料无法识别 顾客投诉
7
材料型号规格标识不 清
2
仓库人员上岗培训
材料型号规格标识错 误
1
进料检验 过程检验
3
42
定期对标示进行检查,加强 对仓管培训
式
Potential Effect(s) of Failure 潜在失效
后果
Sev 严重 度
Class 级别/ 因素
Potential Cause(s) / Mechanism(s) of Failure
潜在失效起因/机理
Current Design or Current Design or
Occ 频度
Component部件
设计或过程责任:
样板部/品管部/生产部
编号: 编制:
页码: 电话:
共3页
Part Number零件编号: Core
日期:2018.6
编制日期:2018.06.20
吹塑成型pfmea分析范例
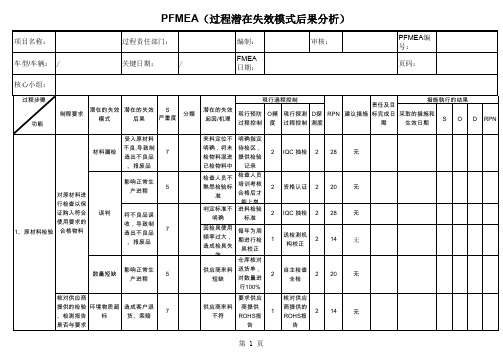
起因/机理
SOD
过程控制 度 过程控制 測度
期
生效日期
RPN
色差
影响产品外 观
8
说明书切口 影响产品外 切坏 观客户投诉
5
毛边过大
影响产品外 观
5
色母与胶料 配料作业 混料不均 指导书
3
自检
2 48
无
每批来料实施
色母母粒颜 打样时比 色差异 对色板
4
IQC 抽检 4
128
增加色板 比对频率
IQC 2018-9-
不清晰
观
4
字体偏移
影响产品外 观
4
用丝印机将
6、丝印
油墨印到产 品LOGO上
漏油
影响产品外 观
4
丝印网板被 定期清理 堵塞 丝印网板
3
自检
2 24
无
丝印定位装 置不稳定,
晃动
固定定位 装置
2
自检
2 16
无
丝印网板破 损
定期检查 、更换网
板
2
自检
2 16
无
颜色错误
无法出货、 客户投诉
7
造成客户使
数量短缺 用过程中数 4 量不够,客
标示
仓库 2018-9-1
用物料标示卡 对每板物料进
行明确标示 2018-9-1
8
1
1
8
穿孔
7
粘胶
模头尺寸过 大
首检/自检
2
3 42
无
/巡检
料胚温度设 定过高
首检/自检
2
3 42
无
/巡检
根据试模
料胚合模后 报告制作 气压过低 成型条件
塑胶行业PFMEA案例
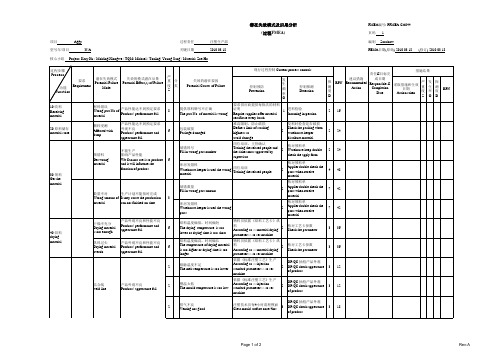
Aggy
过程责任
注塑生产部
型号年/项目
N/A
关键日期
2010.03.18
核心小组 Project: Kary Xu / Molding:Xiongwe / TQM: Michael / Tooling: Young Jiang / Material: Zoe Hu
潜在失效模式及后果分析 (过程FMEA)
Incoming inspection
certificate every batch
2 16
包装破损 Package damaged
堆高限制,防止破损 Define a limit of stacking highness to avoid damage
发料时检查是否破损
2
Check the packing when warehouse keeper
can not finished on time
干燥不充分 Drying material is not enough
产品外观不良和性能不良 Products' performance and appearance fail
6
烘料过头
产品外观不良和性能不良
Drying material Products' performance and 6
□ 注塑工艺原因 8 ◇ Caused by moulding parameter
setting
influence assembly
□ 原料变化原因 8 ◇ Caused by raw material
试模人员试模时发现问题,解 IPQC每4小时检查1shot
决问题 Solve problem on time once
IATF16949第五版AIAG-VDA PFMEA案例分析

维护 严重度为9-10级的缺陷产品流出? 是 OP 40 作业指导书【零件更换】
测试实验室 导致高昂失效成本缺陷产品流出? 是 硬度仪 配置程序
规划和准备:装配线层面
电机组装流水线
OP 70
OP 80
OP 30 OP 20
二、PFMEA概念---规划准备【表头】
结构分析【步骤二】
1.过程项目 系统/子系统/组件 或过程名称
2.过程步骤 关注要素名称
3.作业要素 4M【人机料环】
操作工
机器
材料
轴承加工线
精磨外圈内径
环境
工装
检测设备
切削液
三、PFMEA步骤二---结构分析【随堂练习】
进货检验
1 0
笔帽注塑
20
圆珠笔 装配
50
包装
60
笔筒注塑
30
入库检验
70
笔筒喷涂
结构树:按层次排列过 程要素,并通过结构化 连接展示依赖关系。 这种图形结构可帮助理 解不同过程项过程步骤 和过程工作要素之间的 关系。每个元素都是一 个构建块,随后会增添 相应的功能和失效。
要素名称:名词+行为 动词
过程项
电机 装配线
过程步骤
OP10:涂润 滑【轴承】 OP20:涂润 滑【齿轮】
OP30:烧结 轴承压装
OP40:齿轮罩装 配
OP……:……
如图:电机装配工序
三、PFMEA步骤二---结构分析【结构树-过程作业要素】
过程作业要素:
是过程流程图、结构树及PFMEA分析对象中的最低层级;
是影响过程步骤的主要潜在原因的类别;
分析维度:4M1E;
注塑成型PFMEA范例
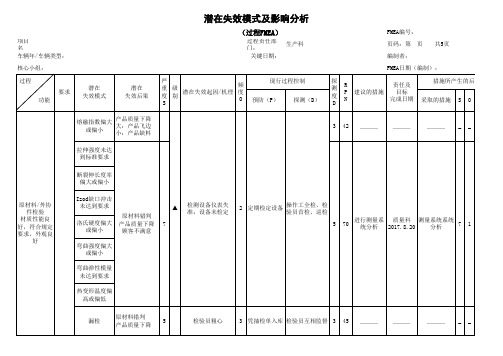
包装
6
产品变形、表 面擦毛
产品性能、外观 质量下降,顾客
不满意
6
纸箱偏大或偏小
4
纸箱进货检验
操作工自检,检 验员巡检
2
48
___
产品无内包装
3
作业指导书规 操作工自检,检
定
验员巡检
2
36
___
___ ___
___ _ _ ___ _ _
半成品入库贮 存
打孔 孔位准确到位
打孔 孔位准确到位
产品变形
产品性能下降, 顾客不满意
注塑成型
产品表面无不 良缺陷,注塑
尺寸精确
产品质量下降:
●表面油漆附着 5
力下降,漆面经
过长时间后脱
产品表面银丝
落,使顾客对外 观不满意
●涂装后产品表 面容易产生裂
5
纹,外观质量使
顾客不满意
时间计电器失准, 导致材料干燥时间 不够
3
计电器定期校 操作工自检,检
准
验员首检、巡检
3
45
___
___
温度表失准,导致 干燥温度过高或过 低
2
24
___
___
___ _ _
涂装工艺不对
3
制定涂装工艺 操作工自检,检
卡
验员巡检
4
48
___
___
___ _ _
涂装
产品表面无划 伤、颗粒、发 花等不良现象 油漆附着力符 合海南马自达
6
孔位偏移 四周飞边
产品装配不良, 使顾客不满意
5
外观质量下降, 使顾客对外观不 4
满意
堆放层数过高 夹具松动 电钻迟钝
注塑PFMEA实例

XXX High Tech Plastic(Suzhou)Co.,LtdXXX注塑(苏州)有限公司潜在过程失效模式及后果分析(过程FMEA)Potential Process Failure Modes and Effects Analysis(PFMEA)FMEA编号(FMEA No.): 项目名称Item Name:产品型号Product Type:核心小组Core Team: FMEA-001过程责任部门ResponsibleDepartment:关键日期Key date:Production, QA编制者/日期Prepartion/Date确认者/日期Approved/DatePage 1 of 3 Pages过程功能Process function要求Requirements1. IQC潜在失效模式PotentialFailureModes潜在失效后果Potential EffectofFailure严重度S级别Class(★,Δ,o)潜在失效起因/机理Origin/MechanismofPotential Failure频度O现行预防过程控制现行探测过程控制探测度D22222RPN1614818建议措施RecommendedActionsReview andconfirm IQCinstruction责任和目标完成日期Responsibility& TargetDate措施执行结果Excutive Results ofActions探测度D222RPN1614采取的措施 ActionsTakenIQC instructionIQC instructionIQC instruction严重度S874频度O111Amela Lu,WW26页码Page:2. Store3.1 Predry 3.2 Moulding Raw plasticmaterialincorrectPacking tray:not ESDmaterialRaw materialhandling notproperlyNot dryenoughImaging lensDia.,Dim 1: 5.78±0.03 out ofspec.Influence opticalfunctionInfluence opticalfunctionInfluence opticalfunctionContaminate theproductsInfluence opticalfunctionBuble inside,Yellow product,Influence assy8743563ΔΔΔoΔooShipment wrongMaterial quality notgoodPackage damagedduring shipmentStore for long time,or made of wrongmaterialMaterial mixedTime or temp not rightWrong insert1113341MaterialIQCMaterialIQCMaterialIQCMaterialIQCMateriallabellingtime/tempcontrolOrderstartreleaseplanChecklablingCheckCOCCheckpackingChecksurfaceresistanceChecklablingsupervisordoublecheck +QC auditDim check423966ReviewpersonnelinstructionsReviewpersonnelinstructionsPM mouldProductionsupervisor,WW26Productionsupervisor,WW26Productionsupervisor,WW26IQC instructionReview personnelinstructionsReview PersonnelinstructionsReview PM mouldpersonnelinstruction,incominginspection opticalinserts3563333122428183726过程功能Process function要求Requirements3.2 Moulding潜在失效模式PotentialFailureModesImaging lensthickness,Dim 2: 1.93±0.03 mm outof spec.Total heightDim.4: 5.05±0.05, out ofspec.Distance, Dim5: 14.54± 0.03out of spec.Distance,Dim.6: 7.86±0.03 out ofspec.Distance,Dim.9: 1.60±0.05 out ofspec.Overall width,Dim 12: 39.5±0.1 out ofspec.Diameter,Dim13: 42±0.1mm out ofspecThickness,Dim 16: 6±0.1mm out ofspec.潜在失效后果Potential EffectofFailurePoor imagequality,Influence TOPInfluenceimagingfunctionImpactillumination,spot positionImpactillumination,spot positionImpact TOPInfluenceproductassembly严重度S766676级别Class(★,Δ,o)★★ΔΔ★潜在失效起因/机理Origin/MechanismofPotential FailureIncorrect stackheight after PMmouldMolding processor mold dim. Ormould temp.Molding processor mold dim. Ormould temp.Molding processor mold dim. Ormould temp.Molding processor mold dim. Ormould temp.Mould dimensionwrongMould dimensionwrongMould dimensionwrong频度O155511现行预防过程控制Orderstartreleaseplan+IPQCIPQCOrderstartreleaseplanOrderstartreleaseplanIPQC现行探测过程控制Dim checkDim checkDim checkDim checkDim 2, 3, 4arecontrolledduringprocessDim check探测度D322232RPN2166621建议措施RecommendedActionsPM mouldPM mould,checkmouldingparameterregularlyPM mould,checkmouldingparameterregularlyPM mould,QC checkmouldingparameterregularlyPM mould,checkmouldingparameterregularlyPM mouldPM mould责任和目标完成日期Responsibility& TargetDateXu ZhenglinXu Zhenglin/AmelaXu Zhenglin/AmelaXu Zhenglin/AmelaXu Zhenglin/Amela措施执行结果Excutive Results ofActions采取的措施 ActionsTakenReview PMmouldpersonnelinstructionReview PM mouldpersonnelinstruction, checkmouldingparameterregularlyReview PM mouldpersonnelinstruction, checkmouldingparameterregularlyReview PM mouldpersonnelinstruction, checkmouldingparameterregularlyReview PM mouldpersonnelinstruction, checkmouldingparameterregularlyReview PMmouldpersonnelinstructionReview PM严重度S766676频度O155511探测度D322232RPN2166621Thickness, Dim 17: 10.36± 0.1 out of spec. Distance, Dim18:3.51±0.03mm out of spec. Thickness,Dim 19:1.3±0.1 out of spec. InfluenceproductassemblyInfluenceproductassemblyConflict with clipon productImpactillumination,spot position66666★★★★Δ★Mould dimensionwrongMould dimensionwrongMould dimensionwrong11151OrderstartreleaseplanOrderstartreleaseplanOrderstartreleaseplanOrderstartreleaseplanOrderstartreleaseplanOrderstartreleaseplanDim checkDim checkDim checkDim checkDim check2222212121212612PM mouldPM mouldPM mouldPM mouldXu ZhenglinXu ZhenglinXu ZhenglinXu ZhenglinXu ZhenglinFangGuozhu /XuZhenglinmouldpersonnelinstructionReview PMmouldpersonnelinstructionReview PMmouldpersonnelinstructionReview PMmouldpersonnelinstruction66661115612222212121212612过程功能Process function要求Requirements3.2 Moulding潜在失效模式PotentialFailureModesImaging lensshape changeImaging lenstransmittancetoo lowImaging lensoptical axisshift versusmech. AxisBiginclusions inlensFlowlines,defects etc.Warpage ofproductTOPContamination潜在失效后果Potential EffectofFailurePoor imagequality, TOP outof spec.Reduced imagequalityPoor imagequalityReduced imagequalityReduced imagequalityInfluenceimagingfunctionInfluenceimagingfunctionReduced image严重度S5555566级别Class(★,Δ,o)ΔooΔΔ★★潜在失效起因/机理Origin/MechanismofPotential FailureMouldingprocessparameter,ormould designmarginallyCavity cleanlinessWrong mouldImpurities orburned materialduringmouldingMoulding processparameterMouldingprocessparameter, orwrong mold dimMouldingprocessparameter, orwrong mold dimParticle generationduring packing频度O11134652现行预防过程控制IPQCIPQCIPQCIPQCIPQCIPQC现行探测过程控制TOPmeasurementMeasureimageresolutionVisualinspection100%Visualinspection100%WapagemeasurementTOPmeasurementVisual探测度D3322233RPN1515134189建议措施RecommendedActionsCheckmouldingparameterregularlyPM mouldPM mouldMouldingprocessoptimizationMouldingprocessoptimizationMouldingprocessoptimizationPM mould,MouldingprocessoptimizationHandling withfinger cots,ionized aircleaning,ESD packingmaterial责任和目标完成日期Responsibility& TargetDateAmela LuXu ZhenglinXu ZhenglinFangGuozhu /XuZhenglinFangGuozhu /XuZhenglinFangGuozhu /XuZhenglinFangGuozhu /Xu措施执行结果Excutive Results ofActions采取的措施Actions TakenCheck mouldingparameter regularlyPM mouldpersonnelinstructionPM mouldpersonnelinstructionPM mouldpersonnelinstruction, setprocess window严重度S5555566频度O1113465探测度D3322233RPN15151341894 Packing quality 5ΔIPQCinspection100%22ZhenglinProductionsupervisorPersonnel instruction 52 22Sheet-2002-0Kept by: DCC Keep period: production requirement + 1 year。
PFMEA案例

30
检查与评估现有的操纵方法
生产部
7﹑
装扣钩
漏装扣钩/扣钩装的位置不正确
线束装入车辆时困难或者安装失败
6
操作员未依规定操作
3
培训操作人员并重点标注图面要求
依照图面规定操作/100%外观检验
2
54
检查与评估现有的操纵方法
生产部
6
扣钩插入的深度不充分
2
培训操作人员并重点标注图面要求
依照图面规定操作/100%外观检验
装线盆入线不正确
3
用正确的装线盆/架
操作员检验
3
36
绝缘破皮,导线断线
端子铆线困难/导通测试不良
4
*裁线机故障/刀片设置太低/刀片用旧;*短路或者开路
5
保护保养/点检
100%检查
2
40
2﹑
压端子
端子变形
铆线端子插入壳仔困难
6
送料爪的变化导致端子经导流板时不正确
2
加大清洁/润滑端子机活动部门的频次
PQC每小时巡检/操作员自检
3
பைடு நூலகம்36
检查与评估现有的操纵方法
工程部
铆线端子插入壳仔后不合格
6
端子在导流板卡住而被硬拉出铆线
2
加大清洁/润滑端子机活动部位的频次
PQC每小时巡检/操作员自检
3
36
检查与评估现有的操纵方法
工程部/品管部/生产部
拉力不够
端子铆线不正确
8
▲
模座/刀座松动
2
保护保养/操纵正确的C/H
每小时拉力测试;巡检
3
48
灯炮装配线束时困难
5
检查图面脏污或者褪色未及时更换
- 1、下载文档前请自行甄别文档内容的完整性,平台不提供额外的编辑、内容补充、找答案等附加服务。
- 2、"仅部分预览"的文档,不可在线预览部分如存在完整性等问题,可反馈申请退款(可完整预览的文档不适用该条件!)。
- 3、如文档侵犯您的权益,请联系客服反馈,我们会尽快为您处理(人工客服工作时间:9:00-18:30)。
要求 Requirement
潜在失效模式 Potential Failure
Mode
失效的模式潜在后果 Potential Effect(s) of Failure
严 重分 度类 S
失效的潜在要因 Potential Causes of Failure
现行过程控制 Current process controls
材料错误 Wrong part No.of material
产品性能达不到预定要求 Products' performance fail
8
颗粒受潮
产品性能达不到预定要求 外观不良
Affected with Products' performance and
6
damp
appearance fail
领错料 Get wrong material
54
Clear mould surface once/4hrs
of product
6
模具设计不合理Mould design not
模具设计时考虑 Need consider this issue when
suitable
design the mould
OP/QC 抽检产品外观 3 OP/QC check appearance 2
36
of product
4
注塑速度偏快 The speed of injection is too fast
依据《标准注塑工艺》生产 According to <<injection standard parameter>> to set
OP/QC 抽检产品外观 2 OP/QC check appearance 2
项目
Aggy
过程责任
注塑生产部
型号年/项目
N/A
关键日期
2010.03.18
核心小组 Project: Kary Xu / Molding:Xiongwe / TQM: Michael / Tooling: Young Jiang / Material: Zoe Hu
潜在失效模式及后果分析 (过程FMEA)
Responsible & Completion Date
采取措施和生效 日期
Action taken
严 重 度
S
发 生 率
O
探 测 度
D
RPN
10 收料 Receiving material 20 原料储存 material store
30 领料 Get the material
40 烘料 drying material
控制预防 Prevention
发
生 频
控制探测
率
Detection
O
措施结果
责任&目标完
建议措施
成日期
探 测 度 D
RPN
Recommended Action
Responsible & Completion Date
采取措施和生效 日期
Action taken
严 重 度
S
发 生 率
O
探 测 度
D
RPN
warehouse keeper distribute material
填错料号 Fill in wrong part number
岗位培训,主管确认
核对领料单
Training the related people and the ticket must approved by supervisor
2
Warehouse keep double check the apply form
2
24
库房发错料
岗位培训
Warehouse keeper issued the wrong material
Training the related people
核对领料单 2 Applier double check the 4 48
can not finished on time
干燥不充分 Drying material is not enough
产品外观不良和性能不良 Products' performance and appearance fail
6
烘料过头
产品外观不良和性能不良
Drying material Products' performance and
OP/QC 抽检产品外观 2 OP/QC check appearance 2
16
machine
of product
8
□ 模具尺寸NG ◇ The dimension of mould is NG
产品功能不良,影响装配,
尺寸不良
客户抱怨
Products' performance and
dimension defect appearance fail and it
12
machine
of product
排气不良
2
Venting not good
注塑技术员每4小时清理模面 Clear mould surface once/4hrs
3
OP/QC 抽检产品外观 OP/QC check appearance of product
3
18
Page 1 of 2
Rev:A
过程步骤 Process
12
machine
of product
模温太低 The mould temperature is too low
依据《标准注塑工艺》生产 According to <<injection standard parameter>> to set
OP/QC 抽检产品外观 2 OP/QC check appearance 3
parts when receive material
填错数量 Fill in wrong part amount
核对领料单
2
Applier double check the parts when receive
7
42
material
库房发错料 Warehouse keeper issued the wrong parts
不能生产 影响产品性能 We Can not use it to produce 6 and it will influence the function of product
数量不对
生产计划不能按时完成
Wrong amount of It may cause the production 3
material
3
产品变形 product deformed
产品外观不良和性能不良 6 Products' performance and appearance fail
客户抱怨 Customer complain
3
清点错误
Make a mistake when count
依据包装作业指导书作业
3 FQC抽检
Follow the packing instruction
FQC sampling check
3 27
标识错误
客户抱怨
Mark incorrectly Customer complain
核对工艺卡参数 Check the parameter
3 36
熔融温度不足 The melt temperature is too lower
依据《标准注塑工艺》生产 According to <<injection standard parameter>> to set
OP/QC 抽检产品外观 2 OP/QC check appearance 3
2 尺寸 X-R
3 48
IPQC measure dimension
machine
once/4H by X-R
检查原材料 Check the raw material
IPQC每4小时检查1shot
1 尺寸 X-R
3 24
IPQC measure dimension
once/4H by X-R
数量有误 The quantity is incorrect
核对工艺卡参数 Check the parameter
3 36
烘料温度偏高,时间偏长 The temperature of drying material is too higher or drying time is too longer
物料员依据《烘料工艺卡》烘 料 According to <<material drying 2 parameter>> to set machine
6
overdo
appearance fail
2
结合线 weld line
产品外观不良
2
Products' appearance fail
提供原料牌号不正确 The part No. of material is wrong
要求供应商提供每批次的材料
证明
1 进料检验
Require supplier offer material
OP/QC 抽检产品外观 2 OP/QC check appearance 2
of product
16
4
注塑压力偏高 The pressure of moulding is too high
依据《标准注塑工艺》生产 According to <<injection standard parameter>> to set