焦炉煤气发电厂成功案例
安徽铜陵新亚星焦化有限公司焦炉煤气热电联产项目 _1_

安徽铜陵新亚星焦化有限公司焦炉煤气热电联产项目
铜陵新亚星焦化有限公司(以下简称“铜陵新亚星“)成立于2008年4月,是中国中信集团旗下中信泰富有限公司全资控股公司,也是中信泰富特钢集团沿长江流域布局的两大原料基地之一。
铜陵新亚星秉持“用一流技术、一流设备、一流团队,建设一流企业”的理念,建成了两座4.3米捣固焦炉、两座7米顶装焦炉和干熄焦、煤气净化、化产回收等完备的焦化生产装置,配套有4个5000吨级兼顾1万吨级泊位的码头和煤气综合利用项目,形成了220万吨炼焦化工、800万吨港口物流、75兆瓦热电能源等三大业务板块,主要产品有:冶金焦炭、煤焦油、粗苯、硫铵、硫氰酸钠,以及洁净煤气、蒸汽、电力等。
其中75MW热电能源业务为铜陵新亚星燃气轮机焦炉煤气热电联产项目,是铜陵新亚星积极发展循环经济探索出的一条重要道路,旨在实现能源的梯级利用,促进经济和环境的双重发展。
安徽铜陵新亚星与美国索拉透平国际公司于2013年6月签订了四台大力神130型(单台ISO出力15000KW)焦炉煤气燃气轮机发电机组合同,四台
燃气轮机发电机组于2014年7月16日已全部投产运行,蒸汽轮机于8月10日并网发电。
该项目主要由四台美国索拉国际透平公司大力神130型燃气轮机发电机组、四台余热锅炉、三台煤气压缩机及一台蒸汽轮机(额定功率:15000KW)组成,项目总装机容量为75MW,蒸汽(中温中压)产出为76T/hr,所发电力全部上网,蒸汽分成三部分:一部分供15MW汽机发电,其余为厂区自用及外供,年上网电量5亿度,外供蒸汽48万吨。
项目在为企业创造巨大的经济效益,改善了周边环境的同时,树立了对社会负责任的公司形象。
改烧焦炉煤气的燃气-蒸汽联合循环发电工程

时所得到的可燃气体 , 是伴随煤炭炼焦过 程产生 的
副 产 品 。焦 炉煤 气 的主要 成份 为 H ( 5 5 % ~5 9 %) 、 C H ( 2 4 %~ 2 8 %) 、 C O ( 5 % 一8 %) 以及 少 量其 它 成
3 0 %一 4 0 %) , 用水 量很 少 , 但 设备 输 出功 率较 小 ( 目 前国内有 5 0 0 k w机组投运 , 更大功率的焦炉煤气
内燃 发 电机组 在设 计开 发 中 ) , 一 般适 用 于焦 炉煤 气
份的气体物质 , 其净 比能约为 1 6 7 0 0 —1 8 0 0 0 k J / m
( 标 准状 况 下 , 下同) , 是 一 种 很 好 的气 体 燃 料 。我 国是焦 炭生 产大 国 , 据不 完全 统计 , 每 年可利 用 的焦 炉煤 气 资源 约有 3 5 0亿 m , 其 中大部分 经 燃 烧后 直 接排空 , 不 仅 浪 费 了能 源 , 而 且 造 成 环 境 污 染 。 因
1 5 0 0 0小时验 证 , 企业取 得 良好经 济效 益 的情况 下 ,
我国因经济发展需要 , 在上世纪 9 0年代初装备 了一 批引进技术 的中小功率( 2 0 M W~ 4 0 M W) 燃气轮机
收 稿 日期 : 2 0 1 2—1 2— 2 9 改稿 日期 : 2 0 1 3 —0 1 — 2 5
作者简介 : 严 军伟 ( 1 9 6 3一 ) , 男, 主要 从 事 燃 气轮 机 产 品 的 系统 设 计 、 改造 及 安装 维 护 工 作 , Eபைடு நூலகம்- m a i l :y a n j w@n a n g a n g —
环发 电机组在钢铁企业 和焦化企业 富余焦 炉煤气 能源利 用项 目中 的优 势 , 以及 国内 目前老 旧退役燃 气轮 机 发 电设备改造后再 利用的广阔前 景 。
煤炭行业的最佳实践成功案例解析与经验分享

煤炭行业的最佳实践成功案例解析与经验分享近年来,随着环境保护意识的增强和能源结构的调整,全球煤炭行业面临着重大的转型挑战。
在这个关键时刻,一些行业领军企业通过创新技术和管理方式取得了显著的成功。
本文将通过对几个煤炭行业的最佳实践成功案例进行深入解析,并分享他们的经验。
案例一:山西神华清洁能源有限公司山西神华清洁能源有限公司是国内首家大型煤制天然气企业。
他们通过煤炭气化技术将煤转化为天然气,实现了煤炭资源的高效利用,并有效降低了煤炭的污染排放。
该公司注重科技创新,不断提升产业链的自主研发能力。
他们与国内外优秀科研机构合作,不断改进技术,提高产能和产品质量。
神华清洁能源公司的成功经验在于将环保和经济效益相结合。
他们在环保设施建设上投入了大量资金,并严格执行国家环保标准。
同时,他们也采用了先进的生产工艺,提高了产品的附加值,并成功打入国内外市场。
此外,该公司还注重员工培训和激励机制的建设,确保员工的专业素质和创新能力。
案例二:中国煤炭集团有限公司中国煤炭集团有限公司是中国规模最大的煤炭企业之一,也是世界上最重要的煤炭供应商之一。
他们通过加强科技创新和资源整合,实现了煤炭生产的高效率和低排放。
该公司注重技术研发,不断引进和消化吸收国际先进技术,通过改进工艺和设备,提高煤炭的采掘和利用效率。
中国煤炭集团公司的成功经验在于战略规划和国际合作。
他们在全球范围内积极拓展市场,与不同国家的企业建立了合作伙伴关系。
他们在海外投资,开拓煤炭资源,并积极参与国际煤炭贸易。
此外,该公司还注重企业文化的建设,树立了良好的企业形象,并实施了社会责任计划,回馈社会。
案例三:美国联合煤炭公司美国联合煤炭公司是美国最大的煤炭生产企业之一,他们通过创新技术和管理模式取得了显著的成功。
该公司注重可持续发展,致力于能源转型和环境保护。
他们将更多的资源投入到煤炭洗选和煤炭利用的研究中,提高了煤炭的利用率和附加值。
美国联合煤炭公司的成功经验在于与政府和社区的良好合作关系。
浅谈焦炉煤气在冶金企业自备电厂的作用

浅谈焦炉煤气在冶金企业自备电厂的作用作者:郑英权来源:《科协论坛·下半月》2013年第12期摘要:焦炉煤气作为冶金企业在炼焦过程中产生的副产品,具有热值高、着火点低等特点,得到了诸多冶金企业的广泛利用。
宁波钢铁有限公司作为冶金行业中的一员,在资源再利用的行动中将焦炉煤气利用到余能发电厂,做到废气利用,为资源再利用开辟了一条新思路,这将对宁波钢铁有限公司的节能减排、降本增效、安全运行、环保效应等方面发挥积极重要地作用。
关键词:焦炉煤气节能减排降本增效安全运行中图分类号:TM621 文献标识码:A 文章编号:1007-3973(2013)012-043-021 前言随着国家节能减排工作的推进、随着企业间竞争的日益加剧、随着人们环保意识的逐步增强、随着一次能源的越来越匮乏,企业要想完成政府的节能减排任务、要想增强自身在同行业间的竞争能力、要想增强社会责任意识,企业必须要充分利用好各种能源,走可持续发展的道路。
焦炉煤气作为冶金企业在炼焦过程中产生的副产品,有如下特性:(1)组成成分中约含93%的可燃气体(CO:7.5%;H2:52-56%;CH4:27-31%;CnHm:3%;CO2:2%;N2:5%);(2)热值高(约18820KJ/Nm3);(3)着火温度低(约 450-500℃)。
2 焦炉煤气的现状目前宁波钢铁有限公司有二座焦炉,小时发生量为53995Nm3,除开焦炉、高炉、烧结等用户的小时使用量为50234Nm3,每小时仍旧有3761Nm3的富裕量(焦炉煤气供需平衡表详见表1)。
在余能发电厂未投产之前,这3761Nm3的富裕量分别分配给各用户而转换为放散高炉煤气的方式在利用。
余能发电厂投产后,焦炉煤气、高炉煤气、转炉煤气均得到了全部回收再利用。
3 焦炉煤气的作用3.1 从社会责任角度出发,起到节能减排的作用(1)近年来随着电力供应越来越紧张,虽然供电企业和政府部门也在采取各种措施来平衡电力的供应,但这其中少不了对一些高耗能的企业进行拉闸限电。
焦化厂降本增效的例子

焦化厂降本增效的例子焦化厂是煤炭加工行业中的重要环节,其主要作用是将煤炭加热至高温,使其发生热解反应,从而产生焦炭、煤气和焦油等副产品。
然而,由于焦化过程中存在能源浪费、环境污染等问题,导致生产成本高昂,效益低下。
为了降低成本,提高效益,焦化厂采取了一系列措施进行降本增效。
以下是其中的十个例子:1. 优化煤种选择:选择合适的煤种可以提高焦化厂的生产效率和焦炭质量,降低生产成本。
例如,选用低灰分、低硫分的煤炭可以减少焦炉结焦现象,提高焦炭收得率。
2. 引进先进的技术设备:焦化厂引进先进的技术设备,如高效的焦炉炉墙冷却技术、高效的煤气净化技术等,可以提高生产效率,减少能源消耗,并降低环境污染。
3. 实施能源回收利用:焦化厂通过采用余热回收技术,将焦炉炉顶、煤气等余热用于发电或供热,实现能源的回收利用,降低能源消耗。
4. 优化生产工艺:焦化厂通过对生产工艺的优化,如调整炉温、焦炉操作参数等,可以改善炭化效果,提高焦炭质量,减少副产品的产生,降低生产成本。
5. 加强煤气净化处理:焦化厂加强煤气净化处理,减少煤气中的硫化物、氮化物等有害物质的含量,提高煤气的利用率,减少环境污染。
6. 完善生产管理制度:焦化厂建立科学、规范的生产管理制度,加强对生产过程的监控和控制,提高生产效率,减少生产事故和质量问题,降低生产成本。
7. 强化能耗监测与节能措施:焦化厂建立完善的能耗监测系统,对能源消耗进行实时监测和分析,并采取相应的节能措施,如优化炉温控制、增加余热回收等,降低能源消耗。
8. 优化原料配比:焦化厂通过优化原料配比,合理控制煤炭、焦炭、煤气等原料的比例,可以提高焦炭收得率,降低生产成本。
9. 资源综合利用:焦化厂实施资源综合利用,将副产品如焦油、粗苯等进行回收利用或销售,降低废弃物处理成本,增加收入。
10. 加强环境监测与治理:焦化厂加强对环境的监测与治理,严格控制废气、废水、固体废物等的排放,减少环境污染,遵守环保法规,降低环保罚款的风险。
干熄焦焦炉煤气发电

一.干熄焦发电:干熄焦发电分为纯凝发电、抽汽发电、背压发电等类型。
锅炉分高温高压和中温中压。
不同方式发电的单位发电量不同。
一般的余热发电采用抽汽凝气式汽轮机较多,能量梯级利用,一般干熄焦锅炉采用中温中压。
1.根据百度百科:干熄焦可回收83%的红焦显热,采用干法熄焦,每处理1t 红热焦炭,可以回收约为1.35GJ的热量,每干熄1t焦炭可以产生压力为3.82MPa,450℃的中温中压蒸汽0.54~0.56t。
1t干熄焦——【0.54,0.56】t的3.82MPa,450℃蒸汽2.根据济钢集团2006投产的干熄焦发电装置的运行数据,检索到三种不同的统计结果:(1)第一种,如下图所示,采用背压式发电,吨焦发电38度左右,采用全凝式发电,吨焦发电约150度,平均每吨干熄焦产生0.575吨蒸汽。
1t干熄焦——0.575t的9.5MPa,540℃蒸汽——150度电(全凝式)(2)第二种,150t/h的干熄焦发电装置,年发电17600万Kw.h.,每小时产生蒸汽86.3t,按照每年350天计算,每小时每吨干熄焦发电139.7Kw.h:1t干熄焦——0.575t的3.82MPa,450℃蒸汽——139.7度电(3)第三种,150t/h干熄焦系统实现了均衡稳定生产,发电机组日平均发电量提高到46万kWh,得每小时每吨干熄焦发电127.8Kw.h,蒸汽的利用效率提高到0.533t/t。
1t干熄焦——0.533t的3.82MPa,450℃蒸汽——127.8度电对以上三种结果取并集,可得济钢集团焦化厂干熄焦发电效率:1t干熄焦—【0.533,0.575】t的3.82MPa,450℃/9.5MPa,540℃蒸汽—【127.8,150】度电3.根据中日联公司设计建造的干熄焦装置近年的统计数字显示,高温高压蒸汽产率≥0.56t/t焦,中温中压蒸汽产率≥0.59t/t焦,高温高压参数≥153kWh/t 焦,中温中压参数≥143kWh/t焦,取中温中压数字最小值,得1t干熄焦——0.59t的3.82MPa,450℃蒸汽——143度电对三种不同统计渠道取并集,可得干熄焦一般发电效率为:1t干熄焦—【0.533,0.59】t的3.82MPa,450℃/9.5MPa,540℃蒸汽—【127.8-150】度电二.焦炉煤气发电焦炉煤气是制取焦炭时产生的副产品,简称焦炉气,是煤焦化过程得到的可燃气体。
燃气轮机热电联产发电案例介绍-焦炉煤气应用1案例背景焦化厂在

燃气轮机热电联产(发电)案例介绍-焦炉煤气应用1 案例背景焦化厂在炼焦过程中伴生大量的焦炉煤气,除生产工艺消耗大约一半之外,还富余大量焦炉煤气。
随着焦化行业的竞争越来越激烈,企业的利润空间不断被压缩,甚至面临关停和破产的危险,因此焦炉煤气的利用成为企业的关注重点。
目前焦炉煤气的利用方式主要有直接卖气,制甲醇,制天然气以及发电等。
焦化厂化产工艺需要蒸汽,利用焦炉煤气作为燃料,采用燃气轮机热电联产(发电)方式,满足企业用电和蒸汽需求,降低企业能耗并改善当地环境,从而提升企业的竞争力。
相比其他方式,这种方式受外界的影响最小,技术也非常成熟,同时也可避免企业因限电而影响正常生产。
美国索拉燃机是全球中小型工业燃机的行业领导者,一直致力于应用中低热值燃料燃气轮机的研发,并已成功研制开发出可应用焦炉煤气的燃气轮机,并在中国已销售33台,其中16台已建成投产,最早的一台于2006年4月投产,目前运行良好。
相比其他发电方式,焦炉煤气燃气轮机热电联产(发电)的系统效率更高,简单可靠,应用灵活,节能环保,部分地区可享受国家政策鼓励,以下是以年产110万吨冶金焦的焦化企业应用燃气轮机热电联产(发电)的典型案例介绍。
1.1 现场条件(以河南为例)海拔高度220m设计大气温度14℃设计大气压力101.3Kpa设计大气相对湿度60%1.2 燃料以焦炉煤气为燃料燃气热值:4170 KCal/Nm3燃气压力:0.005Mpa(假设)1.3 热电负荷及运行时数最大蒸汽流量:50t/hr蒸汽压力: 1.0 Mpa蒸汽温度:185.5℃年供热时间:8200小时年运行时数:8200小时/年2 方案燃气轮机热电联产系统一般根据以热定电的原则进行设计和设备选择,该项目选用2台索拉公司大力神130(TITAN 130)燃气轮机,配2台余热锅炉,三台燃气压缩机(2用1备),一台抽凝式汽轮机发电机组,整个系统可布置在简易厂房内,总占地面积约7200平方米。
高效利用焦炉煤气发电

高效利用焦炉煤气发电--提升发电效率并减少CO2排放作者:本网编辑文章来源:POWER《电力》点击数:381发布时间:2010-07-05新浪微博QQ空间人人网开心网更多焦炭厂在使用原煤生产焦炭的同时,也生产出焦炉煤气(COG)。
采用燃气轮机,让焦炉煤气在燃气轮机中发电,并使燃气轮机的排气在余热锅炉中生产蒸汽,再利用汽轮机组发电,就构成了燃气-蒸汽联合循环发电方式。
这一发电方式具有很大的发展潜力,不仅能够节约一次能源的消耗,而且也大大减少了CO2的排放。
背景概述利源焦化有限公司成立于1997年,位于河南省安阳市铜冶镇北部,是一家集洗煤、炼焦、化工及发电于一体的现代化股份制焦化企业。
公司现年产优质冶金焦70万t、精洗煤240万t、焦油2.4万t、粗笨7000t、硫铵6000t,并拥有3000kW和6000kW汽轮发电机组各两台,年发电1.2亿kWh。
为了满足市场对优质冶金焦、煤焦油及粗笨不断增长的需求,提升企业竞争力,利源焦化公司进行了二期扩建。
二期扩建工程要建设200万t的焦化项目,并相应建设焦炉气净化、水处理,以及甲醇生产等配套工程。
利源焦化公司从工程建设伊始就提出了高标准的要求,不仅要使工程实现产能目标,更要创造综合社会效益,使其成为改善当地环境的榜样。
焦化厂生产流程焦化厂将精洗煤在焦炉中加热,使原煤中的挥发分等分解出来,从而生产出焦炭。
焦炭生产过程中会产生大量焦炉煤气(COG)。
每生产1t冶金焦,大约需要消耗1.33t焦煤,同时产生出大约350~400m3、热值在3700~4200kcal/m3的焦炉煤气。
由于焦炉加热的需要,只有约170~200m3的剩余焦炉煤气被排出,用于其他用途。
一座年产60万t焦炭的焦炉,每年可供使用的焦炉煤气大约为1.2亿m3,即每小时焦炉煤气产量为1.37万m3。
同时,还可以提取2万t的煤焦油和6900t的粗苯等,煤焦油和粗笨都是具有很高附加值的化工产品。
焦炉煤气可以卖给居民或附近的金属冶炼企业用做燃料,也可以用焦炉煤气来发电,还可以用焦炉煤气生产甲醇。
发展焦化煤气发电推进节能优先

发展焦化煤气发电推进节能优先发展焦化煤气发电推进节能优先摘要:中国是世界焦炭产量最大的国家,但每年在炼焦过程之中浪费了大量的焦化煤气,如果能够积极利用这一资源,每年可以节约数千万吨标准煤。
焦化煤气发电是一种比较便捷的综合利用方式,本文主要研究相应的技术设备应用,以及应该采取的配套政策。
关键字:焦化煤气利用煤气发电热电联产中国是全世界最大的焦炭生产国,每年估计有2亿吨左右的优质煤炭用于生产焦炭,仅山西一省的不完全统计,每年炼焦消耗煤炭就超过9,000万吨。
尽管今年中国限制了焦炭出口,但全年预计出口总量仍然将超过1,300万吨,中国焦炭的出口量直接影响着世界市场。
根据炼焦炉型和煤质不同的条件,每吨原煤转化为焦炭时可以产生300~400立方米,热值当量1,500~4,500大卡/立方米的焦化煤气,全国每年在炼焦中伴生600-800亿立方米的焦化煤气,粗略估算折合约250-350亿立方米的天然气,超过西气东输工程的热值总量,相当3,000~4,000万吨标准煤。
在目前生产焦炭的工艺流程中,绝大多数的项目没有回收利用焦化煤气,不是采取火炬头排空燃烧,就是直接放散。
不仅造成了资源的严重浪费,对环境也产生的巨大污染。
在山西、陕西和内蒙的一些产焦地区,大气污染已经达到了触目惊心、无法忍受的程度,空气中弥漫着呛人的烟雾和硫化氢的臭味,造成当地呼吸道疾病的蔓延,肺癌发病率持续走高,严重危害到当地人民群众的身体健康,对社会稳定和经济持续发展都构成了极大的威胁。
如何能够有效利用炼焦伴生煤气资源,对于中国的可持续发展是一个非常重要的课题,它不仅仅是治理环境污染,更主要的是节约资源,提高能源利用效率,解决目前的电力、煤炭供应紧张局面,维持国家社会和经济的持续发展。
中国煤炭资源按目前技术经济条件下开采,在生态环境容量所允许的范围内,达到有效供给的满负载开采能力的净有效量仅1,037亿吨,只占探明储量一万亿吨的10%。
中国煤炭资源供给的基本态势是总量丰富,但有效供给能力明显不足。
我国焦炉煤气制LNG技术不断突破 达到国际领先地位

我国焦炉煤气制LNG技术不断突破达到国际领先地位甲烷化技术是焦炉煤气制LNG项目的核心技术,此技术一直垄断在丹麦托普索、英国戴维及德国鲁奇等公司手中,国内许多企业主要采用技术引进的方式进行焦炉煤气制LNG项目生产。
可喜的是,2011年我国焦炉煤气制天然气关键技术取得重大突破,攻克了合成气体的深度净化、转化和合成技术难题,高活性催化剂及甲烷合成反应器相继研发成功。
2013年1月10日世界上第一套大型炼焦煤气制LNG项目在内蒙古恒刊化工公司成功投产。
截至到2014年第一季度,我国投产的焦炉煤气制LNG项目11个,拟建或正在建设的焦炉煤气制LNG项目达20个。
焦炉煤气制LNG技术也不再完全依赖国际先进技术,目前市面上的技术主要来源有新奥新地能源工程技术公司、西南化工设计院、英国戴维和丹麦托普索。
国内至少有5家设计单位掌握此技术,打破国外企业垄断核心技术的局面。
焦炉煤气制天然气工艺流程
近几年,新奥新地能源陆续设计、承建了河南京宝、唐山古冶、黑龙江鹤岗、云南曲靖盛凯、唐钢气体等多套焦炉煤气制LNG装置。
西南化工设计院的焦炉煤气制LNG技术备受焦化企业青睐,先后与九江煤炭储运有限公司、山西阳光焦化、山西国新正泰等10多家企业合作焦炉煤气制LNG项目。
上海华西化工科技有限公司开发的等温甲烷化反应器工艺,流程短、能耗低、投资小,采用该工艺的LNG工厂已顺利投产,为解决日后国内焦炉煤气制LNG提供了一条新工艺。
焦化厂节能
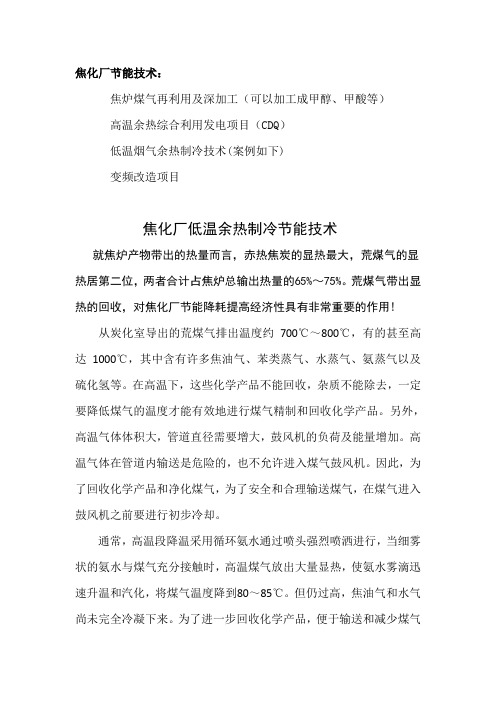
焦化厂节能技术:焦炉煤气再利用及深加工(可以加工成甲醇、甲酸等)高温余热综合利用发电项目(CDQ)低温烟气余热制冷技术(案例如下)变频改造项目焦化厂低温余热制冷节能技术就焦炉产物带出的热量而言,赤热焦炭的显热最大,荒煤气的显热居第二位,两者合计占焦炉总输出热量的65%~75%。
荒煤气带出显热的回收,对焦化厂节能降耗提高经济性具有非常重要的作用!从炭化室导出的荒煤气排出温度约700℃~800℃,有的甚至高达1000℃,其中含有许多焦油气、苯类蒸气、水蒸气、氨蒸气以及硫化氢等。
在高温下,这些化学产品不能回收,杂质不能除去,一定要降低煤气的温度才能有效地进行煤气精制和回收化学产品。
另外,高温气体体积大,管道直径需要增大,鼓风机的负荷及能量增加。
高温气体在管道内输送是危险的,也不允许进入煤气鼓风机。
因此,为了回收化学产品和净化煤气,为了安全和合理输送煤气,在煤气进入鼓风机之前要进行初步冷却。
通常,高温段降温采用循环氨水通过喷头强烈喷洒进行,当细雾状的氨水与煤气充分接触时,高温煤气放出大量显热,使氨水雾滴迅速升温和汽化,将煤气温度降到80~85℃。
但仍过高,焦油气和水气尚未完全冷凝下来。
为了进一步回收化学产品,便于输送和减少煤气风机的动力消耗,在鼓风机前将煤气通过初冷器进一步冷却。
中温段通常采用冷却塔循环水降温。
末段通常采用制冷机提供16℃冷水再次降温,最终使荒煤气温度降至21℃左右,此时,轻质焦油和氨水就冷凝下来。
然后再进入化产车间,再次对萘、焦油、粗苯等进行分离。
案例包钢焦化厂低温余热制冷系统节能技术改造包钢焦化厂是我国西北地区最大的焦炭生产企业,1958年建厂的老煤化工生产企业,经过多年的快速发展,目前企业焦炭产能达到360万吨。
近几年,该厂致力于打造绿色形象,建设环境友好型企业。
该企业对所有废水都进行无害化处理,并回收利用,实现了清洁生产。
回收利用粗煤气冷却采暖段的废热代替原工艺蒸汽型制冷机提供冷冻水每年可以节省蒸汽8.64万吨/年每年可以节约标煤8962吨/年产生经济效益518.4万元/年1、计算依据由于原系统蒸汽型溴化锂机组已使用十多年,机组制冷效率下降,蒸汽耗量增加。
焦化厂降本增效的例子

焦化厂降本增效的例子焦化厂是煤炭加工的重要环节,其主要产品焦炭是冶金、化工等行业的重要原料。
然而,由于煤炭资源的有限性和环境保护压力的增大,焦化厂面临着降本增效的重要任务。
下面将列举10个焦化厂降本增效的例子。
1. 优化煤炭选择:焦炭质量对焦化过程的效率和成本有着重要影响。
通过对不同煤种的研究和实验,选择适合焦化生产的高质量煤炭,能够提高焦炭产率和质量,降低生产成本。
2. 提高炼焦炉热效率:炼焦炉是焦化过程中能耗最大的设备之一。
通过改进炉膛结构、优化燃料燃烧方式,提高炉内温度分布均匀性,可以提高炉膛的热效率,减少能源消耗。
3. 引入先进的炼焦技术:采用先进的炼焦技术,如高炉煤气干法炼焦、胶结煤气干法炼焦等,能够提高焦化效率,减少煤气和焦炭的损失,降低生产成本。
4. 精细管理和控制:通过建立完善的生产管理和控制系统,实时监测和调整焦炉的运行参数,提高生产的稳定性和效率,降低能耗和废品率。
5. 节约用水:焦化过程中需要大量的水进行冷却和洗涤。
通过改进冷却系统、回收和循环利用废水,可以减少用水量,降低水资源消耗和处理成本。
6. 能源回收利用:焦化过程中产生大量的煤气、余热和废热。
通过引入煤气发电、余热利用等技术,将这些能源进行回收和利用,可以降低能源消耗和生产成本。
7. 优化原料储存和运输:合理规划原料储存仓库,采用先进的原料输送和供料系统,能够减少原料的堆积和流失,提高物料利用率,降低运输成本。
8. 推广节能设备:引入节能设备,如高效煤气净化设备、低能耗风机等,能够降低能源消耗和生产成本。
9. 加强煤气净化和废气治理:焦化过程中产生的煤气和废气对环境造成严重污染。
通过引入先进的煤气净化和废气治理技术,减少有害物质的排放,提高环境保护水平。
10. 加强人员培训和技术创新:加强员工培训,提高操作技能和安全意识,推动技术创新,不断提升焦化工艺和设备的性能,能够提高生产效率和品质,降低生产成本。
通过上述10个例子,焦化厂可以通过优化煤炭选择、提高炼焦炉热效率、引入先进的炼焦技术、精细管理和控制、节约用水、能源回收利用、优化原料储存和运输、推广节能设备、加强煤气净化和废气治理、加强人员培训和技术创新等方式,实现降本增效的目标,提高生产效率、降低生产成本,同时减少对环境的影响。
高炉煤气锅炉改烧焦炉煤气的实践应用
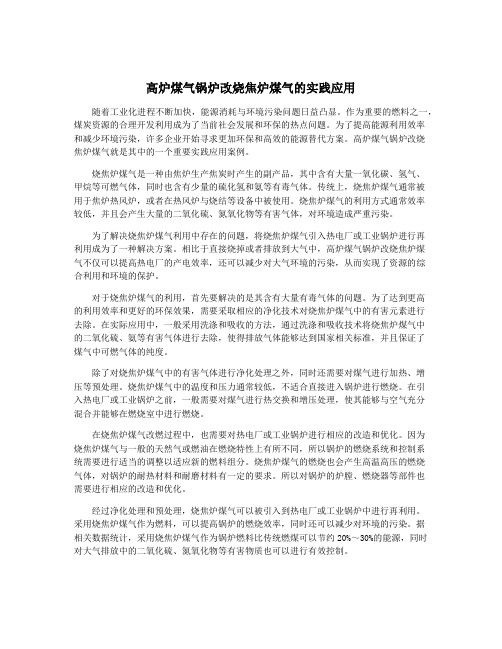
高炉煤气锅炉改烧焦炉煤气的实践应用随着工业化进程不断加快,能源消耗与环境污染问题日益凸显。
作为重要的燃料之一,煤炭资源的合理开发利用成为了当前社会发展和环保的热点问题。
为了提高能源利用效率和减少环境污染,许多企业开始寻求更加环保和高效的能源替代方案。
高炉煤气锅炉改烧焦炉煤气就是其中的一个重要实践应用案例。
烧焦炉煤气是一种由焦炉生产焦炭时产生的副产品,其中含有大量一氧化碳、氢气、甲烷等可燃气体,同时也含有少量的硫化氢和氨等有毒气体。
传统上,烧焦炉煤气通常被用于焦炉热风炉,或者在热风炉与烧结等设备中被使用。
烧焦炉煤气的利用方式通常效率较低,并且会产生大量的二氧化硫、氮氧化物等有害气体,对环境造成严重污染。
为了解决烧焦炉煤气利用中存在的问题,将烧焦炉煤气引入热电厂或工业锅炉进行再利用成为了一种解决方案。
相比于直接烧掉或者排放到大气中,高炉煤气锅炉改烧焦炉煤气不仅可以提高热电厂的产电效率,还可以减少对大气环境的污染,从而实现了资源的综合利用和环境的保护。
对于烧焦炉煤气的利用,首先要解决的是其含有大量有毒气体的问题。
为了达到更高的利用效率和更好的环保效果,需要采取相应的净化技术对烧焦炉煤气中的有害元素进行去除。
在实际应用中,一般采用洗涤和吸收的方法,通过洗涤和吸收技术将烧焦炉煤气中的二氧化硫、氨等有害气体进行去除,使得排放气体能够达到国家相关标准,并且保证了煤气中可燃气体的纯度。
除了对烧焦炉煤气中的有害气体进行净化处理之外,同时还需要对煤气进行加热、增压等预处理。
烧焦炉煤气中的温度和压力通常较低,不适合直接进入锅炉进行燃烧。
在引入热电厂或工业锅炉之前,一般需要对煤气进行热交换和增压处理,使其能够与空气充分混合并能够在燃烧室中进行燃烧。
在烧焦炉煤气改燃过程中,也需要对热电厂或工业锅炉进行相应的改造和优化。
因为烧焦炉煤气与一般的天然气或燃油在燃烧特性上有所不同,所以锅炉的燃烧系统和控制系统需要进行适当的调整以适应新的燃料组分。
富余高焦炉煤气联合循环发电在马钢的应用

文 献 标 识 码 : B 文 章编 号 :09— 89 20 ) 10 2 8 (070 4—00 —0 06 5
中 图分 类 号 :M 1 .1 T 6 13
钢铁 企业 是 国 民经 济 中能 源 消 耗 的最 大 用 户 , 我 国钢 铁工 业 的能耗 约 占全 国总 能耗 的 1 % 。 0 因此 钢铁 工业 的节能 降耗 是一项 极其 繁重 的任务 。 高 炉煤 气 、 炉 煤 气是 钢 铁 咨询 有 限公 司, 北京 102 ) 00 7
摘 要: 高炉 煤 气 、 炉 煤 气 是 钢 铁 生 产 过 程 中 的 副 产 品 , 中 高 炉 煤 气 气 量 大 , 焦 炉 煤 气 的 热 值 较 高 。 随 焦 其 而
着 钢 铁 工 业 的发 展 , 铁 过 程 中 产生 的 高炉 煤 气 量 逐 年 增 加 。 炼
焦炉 煤 气为燃 料 的 联 合循 环 发 电技 术方 兴 未 艾 , 开
* 收 稿 日期 :0 70 0 改 稿 日期 :0 7 8 0 2 0 8 1 2 0 —0 —2
气约 1 . O 8万 m / 。扣 除 本 身 消 耗 的气 量 以 及 轧 3h 钢、 烧结 、 石灰 窑 等用 户 的用 量 , 区 尚余 高 炉煤 气 新 2 3 5~ O万 m / 。 炉煤气 2 5~ 3h 焦 . 3万 m / 。 同时 , 3h 马
河南利源焦炉煤气联合循环发电工程
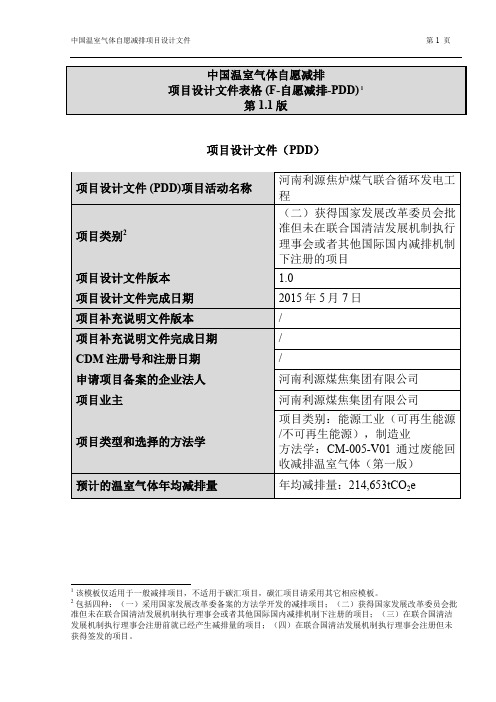
第1 页
中国温室气体自愿减排 项目设计文件表格 (F-自愿减排-PDD) 1 第 1.1 版
项目设计文件(PDD) 项目设计文件 (PDD)项目活动名称 河南利源焦炉煤气联合循环发电工 程 (二)获得国家发展改革委员会批 准但未在联合国清洁发展机制执行 理事会或者其他国际国内减排机制 下注册的项目 1.0 2015 年 5 月 7 日 / / / 河南利源煤焦集团有限公司 河南利源煤焦集团有限公司 项目类别:能源工业(可再生能源 /不可再生能源),制造业 方法学: CM-005-V01 通过废能回 收减排温室气体(第一版) 年均减排量:214,653tCO2e
本项目不属于余压项目
与 本 项 目 无关 焦化项目投产时,没有法律法规要 适用 求回收项目废能。 本项目仅包括已有的年产 110 万吨 适用 的焦炉。焦炉没有扩产计划,因此 没有扩产容量作为新建设施。 遇到故障,废能会进入火炬点燃排 适用 到大气中,记录故障时间,这些不 计入减排量。 项目没有多种废气流 与 本 项 目 无关
3 4
项目情况
/zylist.aspx?clmId=162 http://cdm.unfccc.int/methodologies/PAmethodologies/tools/am-tool-01-v7.0.0.pdf 5 http://cdm.unfccc.int/methodologies/PAmethodologies/tools/am-tool-07-v4.0.pdf 6 http://cdm.unfccc.int/methodologies/PAmethodologies/tools/am-tool-10-v1.pdf 7 http://cdm.unfccc.int/methodologies/PAmethodologies/tools/am-tool-05-v1.pdf 8 http://cdm.unfccc.int/methodologies/PAmethodologies/tools/am-tool-03-v2.pdf
GE能源集团第一例利用焦炉煤气发电项目

GE能源集团第一例利用焦炉煤气发电项目
佚名
【期刊名称】《流程工业》
【年(卷),期】2009(000)021
【摘要】2009年10月12日,GE能源集团宣布,随着与河南利源焦化有限公司签署的协议,其航改型燃气轮机正式进入中国低热值气体市场。
该燃气轮机可100%燃烧炼焦过程中产生的焦炉煤气,帮助利源焦化厂减少排放,并将低热值气体转化成高效能源。
【总页数】1页(P8)
【正文语种】中文
【中图分类】TQ546.5
【相关文献】
1.二次能源利用项目投资决策的影响因素分析——以华菱湘钢高炉煤气发电项目为例 [J], 刘爱东;朱恒孚
2.低热值煤综合利用发电节能技术的应用研究——以永陇矿区低热值煤发电项目为例 [J], 王小玲
3.利用GeoGebra辅助物理教学
——以高三第一轮"电势"的复习为例 [J], 肖丽芙
4.华电与GE能源集团合作沼气发电项目 [J],
5.华电工程与GE能源集团合作进军沼气发电项目 [J],
因版权原因,仅展示原文概要,查看原文内容请购买。
- 1、下载文档前请自行甄别文档内容的完整性,平台不提供额外的编辑、内容补充、找答案等附加服务。
- 2、"仅部分预览"的文档,不可在线预览部分如存在完整性等问题,可反馈申请退款(可完整预览的文档不适用该条件!)。
- 3、如文档侵犯您的权益,请联系客服反馈,我们会尽快为您处理(人工客服工作时间:9:00-18:30)。
焦炉煤气发电厂成功案例一、项目提出的背景山西焦化有限责任公司有年产60万吨、100万吨焦炉各一座,每小时产煤气32407 Nm3,该煤气除供锅炉和职工生活用外,每日有焦炉煤气直接排放约为48万Nm3,煤气的排放对大气和环境也造成了较严重的污染。
如何更好的利用这部份煤气,减少由于焦碳生产带来的环境污染问题,因此,拓宽煤气的利用领域已变得非常紧迫。
山西焦化有限责任公司严格遵循环保、高效、可行的原则,就如何利用好这部份煤气多次组织技术经济考察团对全国各大型焦化厂进行了深入细致考察和论证。
决定建设一座焦炉煤气综合利用电厂,充分利用能源,降低生产成本,创造经济效益。
二、装机容量及设备选型电站设备选型以立足于国内和国内配套为原则,根据目前日排放焦炉煤气量(48万Nm3、热值不低于15.07MJ/ Nm3)和外供蒸汽量(45~60T/h)来确定新建电站规模。
并在此基础上进行装机方案的比较。
经市场调查和研究,相适应的方案有如下三种。
方案一:燃气锅炉+蒸汽轮机发电:装机容量:12000kw,外供蒸汽34t/h这是一个非常传统的技术,也是大家比较熟悉的工艺方式。
它是采用锅炉来直接燃烧焦化煤气,将煤气的热能通过锅炉内的管束把水转换为蒸汽,利用蒸汽推动蒸汽轮机再驱动发电机发电。
系统的主要设备是燃气燃烧器、锅炉本体、化学水系统、给水系统、蒸汽轮机、冷凝器、冷却塔、发动机、变压器和控制系统,工艺流程比较复杂。
根据国内煤气锅炉对燃料的要求:当锅炉燃料的发热量≥12.56MJ/Nm3时,即可使锅炉稳定燃烧。
根据山西焦化有限责任公司提供的煤气资料,完全可以满足锅炉稳燃的要求。
根据煤气气量、热值计算得出,可产生84/h蒸汽。
可选一台双压燃气锅炉,可产生:50t/h、415℃、3.5Mpa和34t/h、190℃、1.25Mpa蒸汽。
可选配一台N12-3.43-V型凝汽式汽轮机,该型号机组最大功率可达12000kW,锅炉还可外供蒸汽:压力为1.27MPa、190℃、34T/h蒸汽。
组成热电联供电站。
过去这一技术是中国利用焦化煤气的主要技术方式,它可以与燃煤电厂结合,在燃煤锅炉中安装燃气燃烧器,将焦化厂的焦化气直接喷入锅炉燃烧,这种方式最大的优点是可以适应焦化厂间歇性生产的特性,有气少燃煤,无气多燃煤,不会影响电力供应的品质和能力。
该技术最大的限制是水,中国水资源极度缺乏,特别是山西、陕西、内蒙等焦炭生产大省,连人畜饮水都有困难,消耗大量的水资源来保障焦化煤气的利用几乎是不可能的,所以要解决焦炉煤气资源综合利用,必须考虑其他更加可行的技术解决方案。
●优点:对于燃料气体要求比较低,只要燃气燃烧器能够承受的气体,一般都可以适应,煤气只需要有限的压力,因而煤气处理系统投资比较简单;该方案是国内常规电站设计模式。
电站的运行、维修、管理等国内都有一套可参考的成熟经验。
●缺点:⑴工艺复杂,建设周期比较长,难以再移动;⑵装机容量仅达12000KW, 热效率为45.7%(含外供蒸汽);⑶机组占地面积大,投资相对较大。
⑷水消耗量大,机组需要的冷却水循环量约2020t/h(消耗量约为80t/h、大气温度25~40℃);⑸厂房结构、设备复杂,施工周期较长;⑹机组启动较慢,约需4小时以上,且低负荷运行对机组效率影响大。
方案二、采用燃气内燃机发电装机容量:20800kw,外供蒸汽:无燃气内燃机的工作原理基本与汽车发动机无异,需要火花塞点火,由于内燃机气缸内的核心区域工作温度可以达到1400℃,使其效率大大超过了蒸汽轮机,甚至燃气轮机。
燃气内燃机的发电效率通常在30%-40%之间,比较常见的机型一般可以达到35%。
在使用焦炉煤气时,由于煤气的热值不太稳定,含氢量较大,杂质含量较大,实际使用条件与设计值偏差较大,其发电效率一般在25%左右甚至更低。
目前我国已经有几家厂家可以提供相应的机组,例如500KW级燃气内燃机,并在中小型焦化厂得到大量应用。
但因其发电功率小仅500KW,发电电压低仅380V,因此只能作为厂用电,无法并网外输,无法大规模利用焦化煤气。
优点:●设备集成度高,安装快捷。
●对气体中的粉尘要求不高,●基本不需要水。
缺点:●综合热效率低:虽然发电效率可达25%,但蒸汽产量非常低,无法同时满足用户用电和蒸汽的要求。
●机组可用性和可靠性较低:从目前其它焦化厂使用的燃气内燃发电机组的运行情况来看,机组的稳定性不高,运行100~200小时就停机检修,有时不得不采取增加发电机组台数的办法,来消除利用率低的影响。
●燃料的不同,对机组出力影响较大:一台500kW燃气内燃发电机组当燃用焦化煤气时(4000Kcal/m3),其出力仅为燃用天然气时的55%左右(280~320kW)。
●单机容量小:目前国内生产的机组最大机组为1000kw,燃用焦炉煤气其出力仅为600kw 左右。
●气缸、进排气阀、火花塞更换频繁。
●需要频繁更换机油,消耗材料比较大。
●内燃机设备对焦化煤气中的水分子含量和硫化氢比较敏感,可能导致硫化氢和水形成硫酸腐蚀问题,需要采取一些必要措施加以克服。
根据焦化公司提供的焦炉煤气资料,采用国产燃气内燃机的情况如下:(生产厂家提供)根据目前日焦炉煤气量(48万Nm3/d、热值为15.07MJ/ Nm3)该型号机组每KW耗气量为:0.96Nm3/kWh(14.65MJ/Kwh)每小时可发电量:48万Nm3/24h/0.96Nm3/kWh =20833kWh建站容量:20833kWh选用燃气机组:20833kW÷320kW/台=65台采用燃气发电机组需要65台建立发电站:采用国产燃气内燃机发电主要是单机容量偏小,组成的台数也多,500kW级燃气内燃机只能在380V等级并网,因此只能作为厂用电电源,还无法实现大规模利用焦化煤气,同时也不能满足大型设备的启动和运行,机组对煤气热值要求高(热值需稳定,而焦化厂很难保证煤气热值不变化),因此机组适应范围小,稍有波动,即影响机组的稳定运行。
根据实地考察,煤气发电机组实际运行情况长期限运行时最大出力为320KW。
发电功率仅能达到额定功率的64%(500KW机组在320KW下运行),机组不能做到满发满供。
还不能满足供蒸汽的要求。
方案三:采用燃气轮机:从工作原理上看,燃气轮机无疑是最适合焦化煤气利用的工艺技术之一。
燃气轮机是从飞机喷气式发动机的技术演变而来的,它通过轴流压气机将空气压缩,高压空气在燃烧室与燃料混合燃烧,燃气急速膨胀推动动力涡轮旋转做功驱动发电机发电,因为是旋转持续做功,可以利用热值比较低的燃料气体。
国内已经有了不少成功的经验,燃气轮机比较适用于高含氢低热值和气体含杂质较多的劣质燃料,燃气轮机自身的发电效率不算很高,一般在30%~35%之间,但是产生的废热烟气温度高达450~550℃,可以通过余热锅炉再次回收热能转换蒸汽,驱动蒸汽轮机再发一次电,形成燃气轮机--蒸汽轮机联合循环发电,发电效率可以达到45%~50%,一些大型机组甚至可以超过55%。
如果采用燃气轮机热电联供机组的效率可达到75%以上。
因此采用燃气轮机的优势相对比较多,首先是设备的可用性和可靠性都比较高,综合利用率一般可以保持在90%;其次,对于燃料的适应性比较强,含硫、含尘高一点问题都不大;再有就是发电出力一般不会减少,甚至因为燃料进气量增加而有所增加;此外,燃气轮机功率密度大体积小,比较适合再移动,便于转移运行现场,这对于存在一些不确定性的焦化厂项目的焦化煤气利用非常有利。
但是,燃气轮机燃料进气压力比较大,越是发电效率高的机组燃料进气压力越高,因为焦化煤气本身没有什么压力,这就需要使用煤气压缩机,压缩煤气需要消耗大量的能量,影响到设备的实际输出功率,一些项目甚至需要消耗燃气轮机12%~14%的功率,对于联合循环项目达到影响可能是10%~15%的输出功率;采用联合循环系统存在与蒸汽轮机相同的水资源条件要求,系统比较复杂,投资也比较大,同时搬迁也比较困难。
燃气轮机在我国焦炉煤气利用上已经有不少成功的尝试,焦炉煤气在国际上主要规类为高氢燃料,国外公司在燃气轮机利用高氢燃料上都具有较多的经验,但是具体到焦炉煤气上的经验都不太多,主要原因是国外炼焦工业一直处于不断萎缩,中小型焦化厂已经很少,而大多数焦炭来自大型联合化工企业,产生的焦炉煤气多用于化工产品的制造,所以焦炉煤气发电项目不多。
根据焦化公司提供的焦炉煤气资料,采用国产燃气轮机的情况如下:装机容量:20000Kw,外供蒸汽55~65t/h。
根据煤气气量、热值,可选用十台2000Kw燃气轮机热电联供机组,并配置十台6.5t/h (1.25Mpa、194℃)的余热锅炉,该方案可满足焦化公司用电和用汽的要求。
●优点:⑴装机容量达20000KW, 热效率为74.7~83.9%(含外供蒸汽)⑵项目投资少、电站建设周期短、投资回收周期短。
⑶机组结构简单、启动迅速、运行稳定、故障率低、维修工作量小、灵活方便、自动化程度高。
⑷占地面积小⑸水消耗量小,机组需要的冷却水循环量约600t/h。
(消耗量约为24t/h、大气温度25~40℃)⑹该方案选用的燃气轮机热电联供机组是国家“九五、十五、十一五”期间重点推荐的节能、环保、高新技术项目,特别适合冶金、焦化、石化、油田、煤矿等剩余焦炉煤气、石油伴生气、炼油厂排放瓦斯气、煤矿排放的煤层气的开发利用。
●缺点:热电联供机组需按制造厂家要求进行定期的维护检查工作,燃气轮机大修需返制造厂修理,燃料进气压力要求高,需增设煤气升压装置。
方案比较表:项目方案一方案二方案三装机型式蒸汽轮机燃气内燃机燃气轮机装机容量12000KW32500KW(20800KW)20000KW机组自耗电12%6%12%外供电能力10560KW19552KW17600KW装机台数1台套65台套10台套外供蒸汽34T/h不能供蒸汽只能供热水55~65T/h 机组综合效率45.7%24.5%74.7~83.9%结论:通过以上三个方案的比较,推荐方案三,选用十套燃气轮机热电联供机组建设电站为最佳方案。
三、发电机组工艺流程在燃气轮机发电机机组中,燃气轮机是原动机,它将燃料中的热能转换成机械能,然后再通过其拖动的发电机转换成电能。
燃气轮机在启动时,先由与主机相联的励磁起动电机拖动机组运转。
待燃气轮机达到一定转速后,其燃气轮机上的压气机能将外部的空气吸入并增压,再送至燃烧室中。
当燃气轮机转速达到点火转速时,煤气经升压后进入燃气轮机燃料调节器,经调节的燃料进入燃气轮机燃烧室,与燃气轮机压气机吸入的空气混合并点火燃烧,产生高温高压的燃气以驱动燃气轮机涡轮作功。
当机组达到平衡转速后,发电机就可独立或并网发电了。
在额定状态下,从燃气轮机涡轮排出流量约20kg/s、温度约为400℃的尾气,通过排气管道引入余热锅炉。