镭雕PFMEA失效模式分析
pfmea过程潜在失效模式及后果分析案例(从原材料-加工-出货整套案例分析)

1、注射压力大 2、锁模力不够 3.模具分型面有异物
4 调节注射压力 作业准备验证,适当调
整,并进行工艺监控 清理模具分型面
产品不合格
2
C 4.塑料温度太高
调节 56
5
制品质量符合 要求
气泡
1.原料含水分、溶剂或 易挥发物
3
原料检验
2.塑料温度太高或受热 时间长,易降聚或分解
标签贴错 漏检 纸箱受潮变形 数量不准确
产品型号错
误,顾客不满 2
意
不良品混入, 影响客户使用
5
纸箱变形破损 3
顾客不满意
1
C 包装人员粗心 C 检验人员操作失误 C 纸箱堆积太高 C 仓库计数错误
3 检查、更正 3 检验、及时标记 3 检查、更正 3 检查、更正
2 42
1 21
3 18 4 60 3 27 26
3.注射压力太小
调节注射压力
4.注射柱塞退回太早 产品不合格 7 A
5.模具温度太低
调节注射温度
6.注射速度快
调节注射速度
2 42
7.在料筒加料端混入空 气
6
制品质量符合 要求
凹痕、缩水
产品不合格 7
1、流道浇口太小
4
2、塑料件太厚或厚薄 不均
3、浇口位置不当
4、注射保压时间太短 A 5、加料量不夠
过程潜在失效模式及后果分析 (PFMEA)
类型/部件: 车型年:
核心小组:
设计责任: 关键日期:
RPN DETECT
OCCUR CLASS SEV
项目
设计功能/要 求
潜在失效模式
潜在失效后果
1 原材料采购 原材料不合格
PFMEA过程失效模式及后果分析
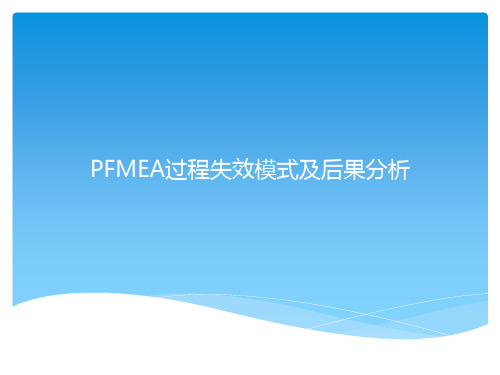
下列可以帮助确定是否将现有的PFMEA纳入最终范围: 新开发的产品和过程; 操作条件的变化; 要求变化(法律/法规,标准规范,客户,最新状态) 制造经验、场内问题,或现场问题/保修; 可能导致危险的过程失效; 人体工程学; 持续改进。
过程FMEA步骤一:规划和准备
PFMEA定义范围的目的---清晰定义过程范围: 识别项目----哪些过程需要分析; 项目计划----培训团队成员、创建项目时间; 定义分析界限---包括什么,不包括什么; 确定能使用的相关经验教训和决策,例如:最佳实践、标准、防错等。
示例:“磨削滑动油封”过程的功能结构
工作坊:步骤三-功能分析(绿色+蓝色笔)
1.过程项目、过程步骤、作业要素具有何种功能和要求? 填入结构树中各项功能和要求: 功能 +要求=绿色字体+蓝色字体 将各项功能填写 在过程项目、过程步骤及作业要素的下面。 备注:“发生什么?”如何从左到右实现产品/过程要求-(过程项目-过程步骤-作业
过程FMEA步骤二:结构分析
结构树按层次排列系统元素,并通过结构连接说明关联关系。这个形象化的结 构考虑了过程项目、过程步骤和过程工作要素之间的关系,在后面,将对他们 分别添加功能模块和失效模块。
对于过程来,查验的最基础层次—变差来源(Sources of Variation),是传统的 “4M(人Man、机Machine、料Material、环Milieu)”,即设备、工装、夹具、 刀/模具的硬件基本参数、动态的控制参数、辅助系统的参数、环境特性、影 响本序的前工序的加工余量、定位点的尺寸及形位公差等。
过程FMEA步骤四:失效分析
PFMEA失效分析的目的是: 1.为过程项目、过程步骤和作业要素的每个功能建立失效(一个或多个失效); 2.识别可能发生的失效/原因,并分配给作业要素和过程步骤; 3.失效关系的可视化(影响-模式-原因,基于功能网的失效网络); 4.通过链接失效链中的失效来创建失效结构; 5.是FMEA表格中记录的失效的基础; 6.失效分析对过程中的每个元素/过程步骤进行了失效描述(结构分析/步骤2和 功能分析/步骤3) 可能的失效从功能/任务推断出来,如设备特定目标状态的不合格、不能充分 完成工作任务、非预期或不必要的活动等; 对失效的描述必须要清晰。不符合、不OK、失效、中断及诸如此类的描述并不 不足以帮助我们去找到失效。 通常,某一功能可以有多种失效。
pfmea过程失效模式与后果分析报告

通过深入分析,我们确定了导致这些失效的潜在原因,包 括设备老化、操作规程不完善、员工培训不足、原材料质 量控制不严格以及工艺参数设置不合理等。
对未来工作的建议和展望
改进措施建议
持续改进计划
未来研究方向
基于PFMEA的结果,我们提出了一系 列改进措施,包括更新设备、优化操 作规程、加强员工培训、严格控制原 材料质量以及调整工艺参数等。这些 措施旨在减少失效发生的风险,提高 生产过程的可靠性和稳定性。
为了确保改进措施的有效实施,我们 制定了持续改进计划。该计划包括定 期评估改进效果、监测潜在问题的出 现以及调整改进措施等。通过持续改 进,我们期望能够不断优化生产过程 ,提高产品质量和客户满意度。
在报告的最后,我们提出了一些未来 可能的研究方向。这些方向包括进一 步探索失效模式与潜在原因之间的关 系、研究新的失效分析方法以及开发 更加智能化的失效预测模型等。通过 深入研究,我们期望能够为企业的持 续改进提供更有力的支持。
失效模式
汽车发动机性能下降
后果
影响汽车动力性能,可能导致油耗增加、排放超标
潜在原因
制造过程中材料、工艺、设备等方面的问题
风险评估
高风险,需采取措施进行改进
案例二:电子产品制造过程的PFMEA分析
失效模式
电子元件短路
潜在原因
制造过程中元件组装、焊 接等环节出现问题
后果
产品功能失效,可能引发 安全事故
提前发现和预防问
题
PFMEA是一种预防性的质量工具 ,它通过提前发现和预防潜在的 问题,减少后期修改和返工的成 本。
优化设计和过程
PFMEA分析结果可以为设计和过 程的改进提供指导,帮助企业优 化产品和过程的性能、可靠性和 安全性。
PFMEA_失效模式分析

PFMEA_失效模式分析PFMEA(Process Failure Mode and Effects Analysis)是一种用于识别并评估过程中潜在失效模式及其影响的工具。
它是在设计阶段早期或产品推出前执行的一种质量工具,旨在识别和消除可能导致质量问题的潜在失效模式。
本文将详细介绍PFMEA的定义、目的、执行步骤以及其在改善和优化过程中的应用。
PFMEA在制造和生产领域被广泛使用,特别是在汽车、电子、航空等高风险行业。
它的目的是通过确定潜在失效模式和评估其潜在影响来减少生产过程中的错误。
它通过三个主要方面的分析来完成:失效模式(Failure Mode)、影响评估(Effect Analysis)和失效原因(Cause Analysis)。
首先,失效模式是指可能在过程中发生的失效或故障,例如零件破裂、接头松脱或设备停止工作等。
对于每个失效模式,需要确定其严重性、发生概率和检测性。
严重性是指失效对产品或过程的影响程度,包括安全风险、客户满意度和产品可靠性。
发生概率是指失效模式发生的频率,包括供应商质量、使用寿命和环境因素。
检测性是指在出现失效后,能够及时检测到并采取纠正措施的能力。
其次,影响评估是对每个失效模式的影响进行定量评估。
通过评估严重性、发生概率和检测性的分级来确定每个失效模式的风险优先级。
风险优先级可以帮助团队确定应该优先处理的失效模式,以便采取相应的预防和纠正措施。
最后,失效原因分析是为了确定导致各个失效模式的潜在原因。
这可以通过使用工程知识和经验、故障树分析、故障模式与影响分析等工具来实现。
确定失效原因有助于在改善和优化过程中提出有效的纠正和预防措施。
此外,执行PFMEA的步骤可以总结为以下六个步骤:1.确定分析对象:确定要进行PFMEA的流程或产品。
2.列出所有失效模式:与团队合作,列出所有可能的失效模式和潜在问题。
3.评估失效影响:评估每个失效模式的严重性、发生概率和检测性。
4.识别失效原因:确定每个失效模式可能的原因,并识别潜在风险。
PFMEA过程失效模式及后果分析

PFMEA过程失效模式及后果分析PFMEA(Process Failure Mode and Effects Analysis)过程失效模式及后果分析是一种常用的质量管理工具,用于评估和改进产品制造过程中的潜在问题和风险。
它旨在预测和预防可能导致产品失效的过程步骤。
1.确定过程步骤:首先,识别和定义产品制造过程中的每个关键步骤,包括原材料采购、加工、装配、测试等。
2.确定失效模式:对于每个过程步骤,识别可能导致失效的模式。
失效模式可以是设备故障、人为错误、材料质量问题等。
3.评估失效后果:对于每个失效模式,评估其可能导致的后果和影响。
后果可以涉及到产品质量问题、安全风险、客户满意度等。
4.定义风险优先级:根据失效模式的严重性、发生频率和检测能力,为每个失效模式分配一个风险优先级。
这可以帮助制定合理的风险控制策略。
5.制定改进计划:对于评估出的高优先级失效模式,制定相应的改进计划和控制措施。
这可能包括优化生产工艺、提供培训和教育、改进设备维护等。
6.实施和监控措施:执行改进计划,并监控其有效性。
定期对PFMEA进行更新,以反映过程改进和新的风险评估。
通过实施PFMEA,可以有效地识别和消除潜在的制造过程问题,并降低产品质量问题的风险。
下面以汽车制造业为例,具体分析PFMEA的应用。
在汽车制造过程中,每个制造步骤都可能存在潜在的失效模式。
例如,原材料采购环节可能存在材料质量问题的风险,加工环节可能存在操作错误或设备故障的风险,装配环节可能存在组装错误或安装不良的风险,测试环节可能存在测试不准确或设备故障的风险。
针对这些潜在问题,可以使用PFMEA来识别并评估其风险。
例如,在加工环节,识别可能的失效模式可能包括不正确的参数设置、设备故障、操作错误等。
然后,评估这些失效模式可能导致的后果和影响,如产品偏差、生产延误、设备故障等。
根据评估结果,确定失效模式的风险优先级,以便制定相应的改进计划和控制措施。
例如,对于评估为高风险的加工失效模式,可以采取以下改进措施:加强对操作员的培训和教育,确保他们正确操作设备和设置参数;增加设备维护和保养频率,以减少设备故障的风险;实施过程监控和自动化控制,以确保稳定的生产环境。
PFMEA-失效模式分析

02
失效模式分析
失效模式定义
失效模式定义
01
失效模式是指产品或过程中可能出现的不满足设计意图、技术
要求或操作规范的状或现象。
失效模式分类
02
根据失效的性质和影响程度,失效模式可以分为功能失效、性
能失效、安全失效、适应性失效等类型。
失效模式分析方法
03
失效模式分析方法包括故障树分析、事件树分析、故障模式与
制定改进措施和预防措施
01
根据分析结果,制定针对性的改进措施,以提高产品或过程的 性能、安全性和可靠性。
02
制定预防措施,降低失效模式的发生风险,包括设计优化、工
艺改进、环境控制和使用指导等。
跟踪改进措施和预防措施的实施效果,持续改进,确保产品质
03
量和过程稳定。
04
PFMEA案例分析
案例一:汽车刹车系统PFMEA分析
识别关键特性,确定分析的重点,确 保分析的准确性和有效性。
列出潜在的失效模式
通过头脑风暴、历史数据分析和经验总结等方法,列出可能的失效模式,确保覆盖全面。
对失效模式进行分类和整理,以便后续分析。
分析失效模式的后果
分析失效模式对产品或过程性能、安 全性、可靠性和符合性等方面的影响 。
评估失效模式对客户满意度和生产成 本的影响,以便制定有效的改进措施 。
主观性
在评估失效模式的严重程度、发生频率和检测难度时,可能存在 主观性,导致结果的不一致。
静态性
PFMEA通常在产品开发阶段进行,而后期的更改和改进可能未 被考虑。
PFMEA未来发展方向
人工智能与机器学习应用
利用人工智能和机器学习技术辅助PFMEA分析,提高识别失效模式 的准确性和效率。
PFMEA制程潜在失效模式和影响分析(ppt 28页)

發生度 10 9 8 7 6 5 4 3 2 1
21
FMEA表格
16. 現行工序控制
• 現有的工序控制可以預防或驗證出該失效模式及/ 或失效原因
• 一般可分為下 2 種工序控制
1.
的控制 2.
的控制
預防該失效模式/效 可測試出失效原因/
應/原因/機制出現 機制或失效模式,並
或減低出現頻次
且引發改善行動
17
FMEA表格
14. 潛在的失效原因/機制
➢ 尋找原因 因果圖(Cause-Effect Diagram)/魚骨 圖(Fish Bone Diagram) 故障樹分析(Fault Tree Analysis FTA) 5 Why? – 問五次為什麼
18
FMEA表格
14. 潛在的失效原因/機制 (續)
製程潛在失效模式和影響分析 PFMEA
1
PFMEA
製程(工序)FMEA是一種分析技術 製造工程師/小組將此技術用作分析潛
在失效模式的原因和機制 用以評估整個系統、子系統、零件和組
件等 是工程師/小組對於工序的思想總會 可以在計劃製造過程時,將工程師的思
考正規化和文件化
2
PFMEA
➢ 一些常見的製程失效原因/機制
錯誤刀具
使用磨損刀具
19
FMEA表格
15. 發生頻度(O)
➢ 這是一個比較性的分數 ➢ 應根據公司過住的記錄,自行訂立指標 ➢ 設計小組對 評定準則和分級規則應意見一
致,即使因為個別產品分析作了修改也應 一致
20
發生度(O)的提議指標
失效發生的可能性 很高: 持續的失效 高: 反複發生的失效 中等: 偶然發生的失效
PFMEA_失效模式分析

22
7、发生频度(O)评估
发生频度(O)评估: 发生频度(O):Occurrence,是指具体的失效起因发 生的概率 频度的分级数值着重在其含义而不是数值,通常也 用1~10分来评估可能性的大小 分值越高,发生的机会越大 对于无历史资料参考的过程,根据小组的工程经验 判断来估计
23
Process FMEA
过程潜在失效模式及后果分析
Agenda
PFMEA的基本概念 PFMEA的做法 实际操作
2
What - 什么是PFMEA?
Process Potential Failure Mode and Effects Analysis,简称PFMEA 即过程潜在失效模式及后果分析
10
1、准备工作
过程流程图 – 示范
11
1、准备工作
过程特性矩阵表 – 示范
12
1、准备工作
PFMEA 表格 – 示范
子系 统 功能 要求
潜 在 失 效 模 式
潜 在 失 效 后 果
严 级 潜 重 别 在 度 失 S 效 起 因/ 机 理
频 现行控 探 度 制 测 O 预 探 度 防 测 D
R 建 P 议 N 措 施
初始PFMEA
必须在试生 产前,工装 准备前
更新PFMEA
各项未考虑的 失效模式发现 及讨论
更新PFMEA
各项未考虑的 失效模式发现 及讨论
时间
动态的PFMEA
8
How – 怎么做PFMEA?
完成PFMEA的13个步骤
1. 前期准备工作 2. 描述“过程功能/要求” 8. 现行的过程控制方法 9. 可检测度(D)评估 10. 计算当前的RPN值,确 定优先改善项目 11. 提出建议的措施,负责 人及时间 12. 描述“采取的措施” 13. 重新计算RPN值
PFMEA潜在失效模式及后果分析
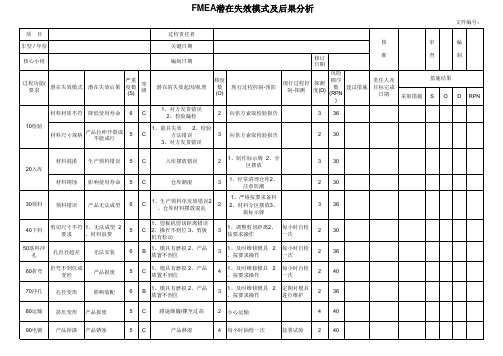
6C
1、搬运摆放混乱 2、标示牌丢失
2
1、贴标识牌 2、 每3天查看1次
出入库台账
3
36
备注:1.凡顾客指定特殊特性均按其特性符号标注,如◇表示配合/功能,○表示安全/符号,或顾客提出的其它符号要求。 2.顾客无特殊特性要求,本厂标准规定重要度控制标准符号要求如下:A —特殊特性 B—重要特性 C—一般特性
机有松动
3
1、调整剪切距离2、 按要求操作
每小时自检 一次
2
30
50落料冲 孔
孔直径超差
无法安装
6
B
1、模具有磨பைடு நூலகம் 2、产品 放置不到位
3
1、及时维修模具 2 、按要求操作
每小时自检 一次
2
36
60折弯
折弯不到位或 变形
产品报废
5
C
1、模具有磨损 2、产品 放置不到位
4
1、及时维修模具 2 、按要求操作
日期
材料材质不符 降低使用寿命 6 C
1、对方发货错误 2、检验漏检
2 向供方索取检验报告
3 36
10检验
材料尺寸规格
产品拉伸开裂或 不能成行
5
1、量具失效 2、检验
C
方法错误
3
3、对方发货错误
向供方索取检验报告
2 30
采取措施
审
编
查
制
措施结果 SOD
RPN
20入库
材料混淆 生产领料错误 5 C 材料锈蚀 影响使用寿命 5 C
入库摆放错误 仓库潮湿
2
1、制作标示牌 2、分 区摆放
3
1、经常清理仓库2、 注意防潮
3 30 2 30
PFMEA失效模式与效应分析
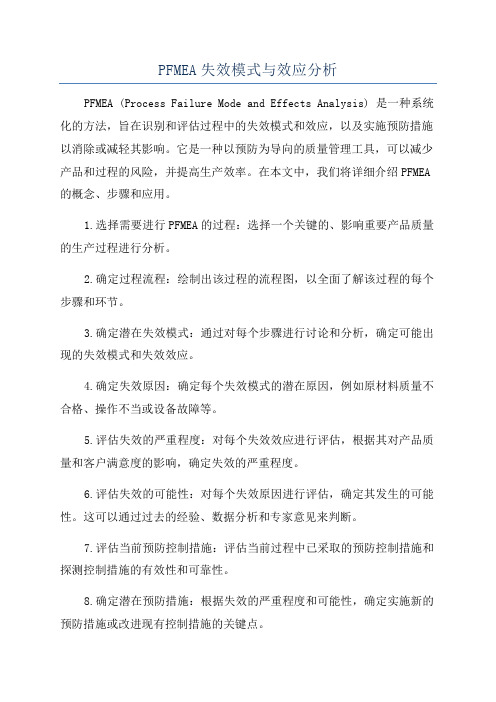
PFMEA失效模式与效应分析PFMEA (Process Failure Mode and Effects Analysis) 是一种系统化的方法,旨在识别和评估过程中的失效模式和效应,以及实施预防措施以消除或减轻其影响。
它是一种以预防为导向的质量管理工具,可以减少产品和过程的风险,并提高生产效率。
在本文中,我们将详细介绍PFMEA 的概念、步骤和应用。
1.选择需要进行PFMEA的过程:选择一个关键的、影响重要产品质量的生产过程进行分析。
2.确定过程流程:绘制出该过程的流程图,以全面了解该过程的每个步骤和环节。
3.确定潜在失效模式:通过对每个步骤进行讨论和分析,确定可能出现的失效模式和失效效应。
4.确定失效原因:确定每个失效模式的潜在原因,例如原材料质量不合格、操作不当或设备故障等。
5.评估失效的严重程度:对每个失效效应进行评估,根据其对产品质量和客户满意度的影响,确定失效的严重程度。
6.评估失效的可能性:对每个失效原因进行评估,确定其发生的可能性。
这可以通过过去的经验、数据分析和专家意见来判断。
7.评估当前预防控制措施:评估当前过程中已采取的预防控制措施和探测控制措施的有效性和可靠性。
8.确定潜在预防措施:根据失效的严重程度和可能性,确定实施新的预防措施或改进现有控制措施的关键点。
9.优先级排序和实施措施:根据失效的严重程度、可能性和控制可靠性,对预防措施进行优先级排序,并制定实施计划。
10.跟踪和监测措施的实施效果:实施预防措施后,跟踪和监测结果,确保措施的有效性和可持续性。
1.产品设计阶段:在产品设计和开发阶段使用PFMEA可以识别潜在的设计缺陷,提前采取措施来确保产品质量和可靠性。
2.工艺优化和改进:通过对生产过程进行PFMEA,可以发现可改进的环节和潜在的问题,从而优化生产效率和质量。
3.新生产线的引入:在引入新的生产线或设备时,使用PFMEA可以帮助识别潜在的问题和风险,确保新工艺的稳定性和可靠性。
镭雕PFMEA失效模式分析

6
原料放错位置
6
图案相象,图案用错
5
产品摆放未放到位置
5
镭射电流过大/过小
5
镭雕鼓调整精度不够
5
工人忘记填写
2
1定期修改更新控制计划; 2实行员工考核制度。
1定期修改更新控制计划;
2
3实行员工考核制度。
2 放入纸箱中保存
2 1 产品做定位摆放 2 样品图案进行控制 4 专用对位菲林对位控制 4 样品图案进行控制 4 样品图案进行控制 4 目测检查
目测100%控制
4
40 无
4
40 无
2
20 无
2
24 无
3
18
2
24 无
2
40 无
2
40
2
40 无
2
40 无
外形图案不合格 检验错误、漏检 限制性物质
客户困难,造成停线
7
1、错判,不合格品流入客户,引起顾客抱怨; 2、误报,成本浪费
7
影响用户的健康
9
图案相象,图案用错
1、检验作业指导书不详细,不能起指导作用; 2、检验员技能不足。
项目名称 核心小组: 过程责任部门 工艺项目
1 原素材进料检验
2储存 3领料 4 产品镭雕
5批号
6成品检验
7包装和贴标识 8入库 9发运 10出货检
潜在失效模式
潜在失效后果
潜在失效模式及后果分析 ( PFMEA )
品管部
严重度 Class级
S
别
潜在失效起因/机理
Version/版本号
频度 O
预防
现行过程控制
1、随时抽检报告和实物; 2、操作者加工前自检。
PFMEA过程失效模式及后果分析
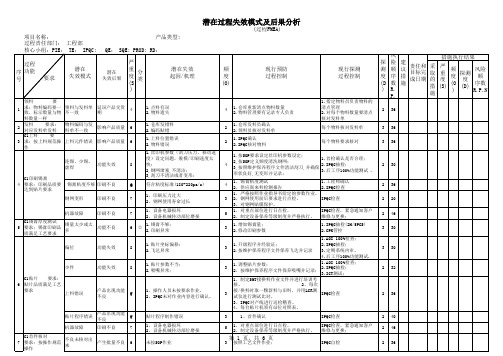
第 1 页,共 6 页
3 按照工艺文件作业;
IPQC检查,紧急通知客户 维修与更换;
IPQC自检
风
措施执行结果
探 测 度 (D )
险 顺 序 数 R. P.
建 议 措 施
责任和 采 目标完 取 成日期 的
措 施
严 重 度 (S)
频 度 (O )
探测 度 (D)
风险 顺 序数 R.P.N
2 36
3 36 3 36
领料
要
1
求:物料编码要一 领料与发料单 致,标示数量与物 不一致
延误产品交货 期
4
料数量一样
2
发料 要求: 对应发料单发料
物料编码与发 料单不一致
影响产品质量
6
C1上料 要
3 求:按上料规范操 上料元件错误 影响产品质量 6
作
连锡、少锡、 虚焊
功能失效
8
C1印刷锡膏
4 要求:印刷品质要 锡膏粘度不够 印刷不良
钢网变形
印刷不良
7
使用前未点检
1.接插件未防护; 2.作业操作失误;
1.摆放不按要求 2.重叠
1.上料位置错误 2.物料错误 1.丝印机参数(刮刀压力,移动速 度)设定问题,脱模/印刷速度太 快; 2,钢网堵塞,不清洁; 3,刮刀不清洁或者变形; 符合粘度标准(180-220pa/s)
1、印刷压力过大 2、钢网使用寿命过长
炉温设定错误
板未放到位 1、板与板叠放产生撞件 2、取放板时板跌落地面引起 3、PCB摆放错误 现场管理不到位 1、现场“5S”未做好 2.物品未标示 未执行工艺要求。 不良位置没有标识。
现场管理不到位 修理技术欠孰练 不按作业规范操作
PFMEA过程失效模式及后果分析
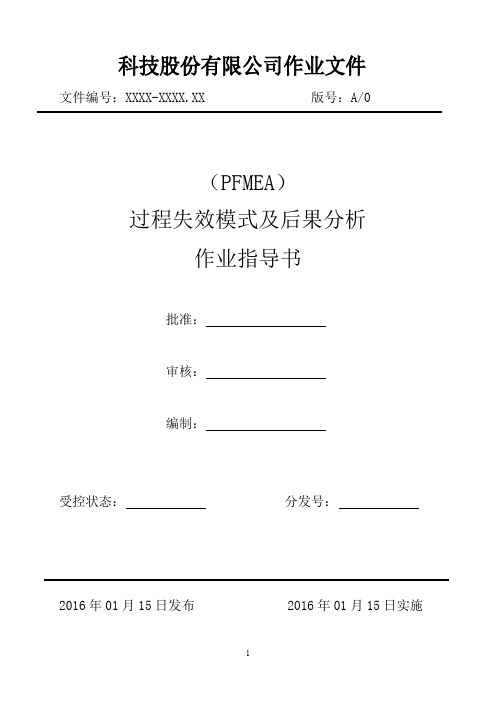
科技股份有限公司作业文件文件编号:XXXX-XXXX.XX 版号:A/0(PFMEA)过程失效模式及后果分析作业指导书批准:审核:编制:受控状态:分发号:2016年01月15日发布2016年01月15日实施过程潜在失效模式及后果分析作业指导书(PFMEA)XXXX-XXXX.XX1目的过程潜在失效模式及后果分析,简称PFMEA。
是一种信赖度分析的工具,可以描述为一组系统化的活动,是对确定产品/过程必须做哪些事情才能使顾客满意这一过程的补充。
其目的是:(a)并评价产品/过程中的潜在失效以及该失效的后果;(b)确定能够消除或减少潜在失效发生机会的措施;(c)将全部过程形成文件。
2范围:适用于公司用于零组件的所有新产品/过程的样品试制和批量生产。
适用于过程设计的风险性及后果的分析;适用于过程重复,周期性永不间断的改进分析。
3术语和定义:1)PFMEA:指Process Failure Mode and Effects Analysis(过程失效模式及后果分析)的英文简称。
由负责制造/装配的工程师/小组主要采用的一种分析技术,用以最大限度地保证各种潜在的失效模式及其相关的起因/机理已得到充分的考虑和论述。
2)失效:在规定条件下(环境、操作、时间),不能完成既定功能或产品参数值和不能维持在规定的上下限之间,以及在工作范围内导致零组件的破裂卡死等损坏现象。
3)严重度(S):指一给定失效模式最严重的影响后果的级别,是单一的PFMEA范围内的相对定级结果。
严重度数值的降低只有通过设计更改或重新设计才能够实现。
4)频度(O):指某一特定的起因/机理发生的可能发生,描述出现的可能性的级别数具有相对意义,但不是绝对的。
5)探测度(D):指在零部件离开制造工序或装配之前,利用第二种现行过程控制方法找出失效起因/机理过程缺陷或后序发生的失效模式的可能性的评价指标;或者用第三种过程控制方法找出后序发生的失效模式的可能性的评价指标。
注塑喷油丝印镭雕装配PFMEA分析

8
≤
高
7
≤1/100 (经常性)
6 5 4
≤ ≤ ≤
中等 (偶然性)
8 微小 只通过目视检查
7
很小
只通过双重目视 检查
6
小
制图,统计过程控制
×
×
××
5 中等 量具控制
×
× × 4
中上
后工程探测.作业前确认
3
≤
2≤
1≤
低(相对 很少发
几乎不会发生
3
高
× × 工程中探测,后工程探测
2
高
× × 工程中探测(自动测量并
3 虽机能无影响,但顾客(50%)有发见的可能性
2 虽机能无影响,但顾客(25%)有发见的可能性
1 对机能.规格完全不会造成影响
过程 编号 /proc ess No
过程process
功能 function
潜在失 效模式potential failure
mode
潜在失 效后果potential
effects of failure
e度
prevention 模具改良,注
塑调机改善
detection 目视全检外观出
货
c 3
54
建议措施 recomend
actions
责任及目 标完成日期 reponsibility and target completion
date
措施结果action results
采取的 措施actions
taken
注塑
按键电 镀件
尺寸大
装配困难
6
供应商原料不良/配料 不当
3
供应商明确材 IQC依据SGS报
PFMEA制程潜在失效模式及后果分析

分析项目名称:D型胶塞产品编号:203002 制作部门:技术部PFMEA编号:PFMEA203002-01核心小组成员:钟道平、管巧智、丁佩文、朱华星、刘照伦、罗熠、鲜其辉、安斌强、江功志功能要求潜在失效模式潜在失效后果严重度S级别潜在失效原因/机理频度O现行控制措施现行控制探测探测度DRPN需要采取预防措施责任人及目标完成日期措施结果采取措施S O DRPN原材料采购(按照产品需求购入各产品的生产原料)型号/规格错误影响产品性能2供应商送料错误1每批送货供应商提供材质证明书收料员检查送货单与采购单是否一致3 6IQC检验(利用设备,量具、各材料检验标准等检验来料)材料物性不稳定影响产品性能2供应商生产制程不稳定1采购订单中明确标注材料之各项需求,供应商送货时需添付与要求相符之材质证明书及相关报告按照来料检验标准进行来料检验2 4 环保要求不合格影响产品使用2 1 2 4 外观差异影响产品外观5 2 1 10 包装破损影响原材料品质、性能4包装材料强度不足2 1 8包装方式设计不合理2 1 8仓储(检验合格材料移动至仓库放置、贮存的过程)标识混乱领错材料,影响后工序生产5放置区域划分不明,无隔离区域标识3材料分区域放置,各材料上方明确标识牌号、批号、供应商等信息管理人员定期巡检确认3 45标识单填写错误3岗前培训,技能培训实施3 45分析项目名称:D型胶塞产品编号:203002 制作部门:技术部PFMEA编号:PFMEA203002-01核心小组成员:钟道平、管巧智、丁佩文、朱华星、刘照伦、罗熠、鲜其辉、安斌强、江功志功能要求潜在失效模式潜在失效后果严重度S级别潜在失效原因/机理频度O现行控制措施现行控制探测探测度DRPN需要采取预防措施责任人及目标完成日期措施结果采取措施S O DRPN 变质影响产品性能2仓库贮存条件与产品要求不符1仓库的温湿度管理设定温湿度记录表填写,1次/天3 6超过原材料贮存有效期1 材料定期盘点材料盘点,1次/月2 4领料(按照生产计划从仓库领取后工序用材料)领错材料影响产品性能5材料标识错误3入库前材料上贴来料管理票管理人员定期巡检确认3 45配料(将领取材料按一定配方比例称重、分类的过程)配料时各组分比例错误影响产品性能5称量器具失准2量具的定期点检定期点检:1次/天,定期校正:1次/半年3 30员工配错重量3员工岗前培训,技能培训实施管理人员监控实施3 45炼胶(将配好粉状材料通过设备,工艺转化为一定尺寸的块状体)色差影响产品外观3材料配比错误3按照《配方表》作业每批次对比标准样板2 18材料混合不均匀3按照《混炼操作工艺卡》作业2 18 硬度不稳定影响产品性能5材料配比错误3按照《配方表》作业每批次进行硬度测试2 30分析项目名称:D型胶塞产品编号:203002 制作部门:技术部PFMEA编号:PFMEA203002-01核心小组成员:钟道平、管巧智、丁佩文、朱华星、刘照伦、罗熠、鲜其辉、安斌强、江功志功能要求潜在失效模式潜在失效后果严重度S级别潜在失效原因/机理频度O现行控制措施现行控制探测探测度DRPN需要采取预防措施责任人及目标完成日期措施结果采取措施S O DRPN 胶料存放时间过长硫化成型不良增加4放置时间记录错误3员工岗前培训,技能培训实施管理人员监控实施3 36分散不均影响产品性能5搅拌时间不足或薄通次数不够3按照.《混炼操作工艺卡》作业每批次按快检标准检测3 45裁切(通过设备,在一定的工艺参数条件下转化为各规格的胶条)长、宽、厚度不符合要求影响硫化成型生产3裁切刻度未调试精准2按照胶料裁切标准作业按照裁切标准QC检验记录2 12硫化成型(将备好的胶料,通过设备、摸具,在一定的工艺参数条件下转化为各形状的产品)尺寸不合格影响产品装配使用5成型压力、温度过高或不足3按照《成型操作工艺卡》工艺参数生产1.QC首件检验实施2.生产过程中自检实施3 45模具老化,模腔受损2生产前模具自检生产前模具自检3 30材料收缩率不稳定3收缩率检测/每手料收缩率检测/每手料3 45 外观缺陷影响产品外观5生产工艺条件设定错误3按照《成型操作工艺卡》工艺参数生产1.QC首件检验2.生产过程中自检实施2 30分析项目名称:D型胶塞产品编号:203002 制作部门:技术部PFMEA编号:PFMEA203002-01核心小组成员:钟道平、管巧智、丁佩文、朱华星、刘照伦、罗熠、鲜其辉、安斌强、江功志功能要求潜在失效模式潜在失效后果严重度S级别潜在失效原因/机理频度O现行控制措施现行控制探测探测度DRPN需要采取预防措施责任人及目标完成日期措施结果采取措施S O DRPN 生产操作不规范3岗前培训,技能培训实施管理人员监控实施2 30模具老化,模腔受损2生产前模具自检生产前模具自检2 20机器动作异常3机器设备的定期点检,保养及测评1.机器点检:1次/天2.QC定期监察机器设备点检、保养及维护记录2 30生产环境不符合要求产品有污染或交叉污染5非指定机器,场所生产21.生产计划指定FCM车间生产生产计划,管理人员监控实施3 30现场5S管理不足32.严格按照《GMP操作规范》实施2 30IPQC检验(利用量具,检验标准等误判导致不合格品流出4质量判定标准不明确31.按《QC工程表》作业2.签发标准生QC抽样检验 3 36分析项目名称:D型胶塞产品编号:203002 制作部门:技术部PFMEA编号:PFMEA203002-01核心小组成员:钟道平、管巧智、丁佩文、朱华星、刘照伦、罗熠、鲜其辉、安斌强、江功志功能要求潜在失效模式潜在失效后果严重度S级别潜在失效原因/机理频度O现行控制措施现行控制探测探测度DRPN需要采取预防措施责任人及目标完成日期措施结果采取措施S O DRPN检验产品)测量误差 3 产样板和限度样板参照比对3.检测设备的定期鉴定/校准/维护/保养4 48修边(将成型后产品飞边清理干净的过程)外观缺陷影响产品外观3冲切治具刀口损伤31.按《后加工作业指导书》作业2.岗前培训,技能培训实施3.参照标准样本自检QC,管理人员巡查指导2 18 漏修 2人为作业失误4 3 24二次硫化(通过设备,在一定工艺条件下烘烤产品的过程)硫化不足不能满足环保和食品安全要求。
PFMEA过程失效模式及后果分析

PFMEA过程失效模式及后果分析PFMEA(Process Failure Mode and Effects Analysis)是一种通过系统地识别和评估潜在的失效模式及其后果来预防产品和过程问题的方法。
它有助于组织在设计和开发阶段就发现并解决潜在的问题,从而提高产品质量和生产效率。
在这篇文章中,我们将重点讨论PFMEA过程中的失效模式及其后果分析。
失效模式是指导致产品或过程失效的特定原因或机制。
它可以是由于设计缺陷、材料问题、加工误差、操作失误等引起的。
失效模式常常以不同的方式出现,在不同的环境下可能会有不同的后果。
在进行PFMEA过程中,首先需要识别潜在的失效模式。
这可能涉及到对产品、过程和相关文档的仔细研究,以了解可能存在的问题。
接下来,需要对每个失效模式的影响进行评估,这也就是后果分析。
后果分析可以帮助确定失效对产品质量、生产效率和安全性等方面造成的影响,从而决定需要采取的预防措施。
在进行PFMEA过程失效模式及后果分析时,以下是一些常见的失效模式和其可能的后果:1.设计缺陷:-可能的后果:产品性能不达标、产品寿命缩短、安全隐患、产品被召回等-预防措施:加强设计评审、使用可靠的设计工具、进行模拟测试等2.材料问题:-可能的后果:产品强度不足、耐腐蚀性差、产品寿命缩短等-预防措施:严格选择、测试和审查材料供应商、加强入库检查等3.加工误差:-可能的后果:产品尺寸偏差、表面质量不良、装配困难等-预防措施:加强生产工艺控制、使用先进的制造设备、严格执行质量标准等4.操作失误:-可能的后果:生产过程中出现错误、设备损坏、人员伤亡等-预防措施:提供员工培训、实施作业规程、设立安全警示标志等除了上述提到的失效模式和后果,还有许多其他可能的情况需要被考虑和分析。
在进行PFMEA过程中,团队成员需要全面了解产品和过程,积极参与讨论和决策,以确保有效识别和评估潜在的问题。
此外,通过对失效模式及后果进行分析,团队还可以确定应对措施的优先级和实施计划。
- 1、下载文档前请自行甄别文档内容的完整性,平台不提供额外的编辑、内容补充、找答案等附加服务。
- 2、"仅部分预览"的文档,不可在线预览部分如存在完整性等问题,可反馈申请退款(可完整预览的文档不适用该条件!)。
- 3、如文档侵犯您的权益,请联系客服反馈,我们会尽快为您处理(人工客服工作时间:9:00-18:30)。
FMEA
编号:页数:项目名称编制/日期: 核心小组:审核/日期过程责任部门
修订日期
变形
产生不良品,造成制造成本浪费
5
1、进货控制计划不详细,有漏项目;
2、检验员粗心漏检项目。
2
1定期修改更新控制计划;2实行员工考核制度。
1、随时抽检报告和实物;2、操作者加工前自检。
4
40无
错检
产生不良品,造成成本浪费
51、进货控制计划没及时更新;2、检验员检验错误。
21定期修改更新控制计划;3实行员工考核制度。
1、随时抽检报告和实物;
2、操作者加工前自检。
4
40无
材料上有灰尘
影响产品外观5产品暴露在空气中2放入纸箱中保存目测100%控制220无尺寸不良
影响后续加工6供应商加工控制错误2来料检查
224无3领料
领错料造成产品性能降低
6原料放错位置1产品做定位摆放3
18雕错图案产品批量不良,造成成本浪费6图案相象,图案用错2样品图案进行控制1、随时抽检报告和实物;2、操作者加工前自检。
224无图案偏位
产品组装后灯光照射会偏暗5产品摆放未放到位置4专用对位菲林对位控制1、随时抽检报告和实物;2、操作者加工前自检。
240无烧焦/未雕干净影响外观
5镭射电流过大/过小4样品图案进行控制1、随时抽检报告和实物;3、操作者加工前自检。
240锯齿
产品图案不流畅,影响外观5镭雕鼓调整精度不够4样品图案进行控制1、随时抽检报告和实物;2、操作者加工前自检。
240无5批号
批号不清楚或没有
不清楚产品的生产日期
5
工人忘记填写
4
目测检查
目测100%控制
2
40无
外形图案不合格客户困难,造成停线
7
图案相象,图案用错
2
NA
目测100%控制
2
28无
检验错误、漏检
1、错判,不合格品流入客户,引起顾客抱怨;
2、误报,成本浪费7
1、检验作业指导书不详细,不能起指导作用;
2、检验员技能不足。
2
1定期修改检验作业指导书;2对检验员现场培训;
3每天不合格零件进行评审。
质量工程师巡检或抽检
4
56无
限制性物质
影响用户的健康
9CC
材料中含有有害物质
1设计选择符合要求的材料
3
27无
包装不符合要求
客户拒收或顾客抱怨
6
操作者未按照包装要求执行
2
包装规范发放到现场并培训操作者100%检验4
48无
标识不正确
发运错误,顾客抱怨
6
料箱上旧标识没有取出;操作者疏忽
2操作者100%检验;检验员成品抽验
4
48无
8入库产品数量不正确影响后续发货6生产装箱多装或少装,取货无登记2培训操作者,做好库存记录操作者100%检验,定期盘点448无9发运
产品数量不正确
客户抱怨
6
装货的时候数量不足或多装
2
实行出货检再加以控制发货前清点数量
4
48无
10出货检错检、漏检
1、错判,不合格品流入客户,引起顾客抱怨;
2、误报,成本浪费
71、检验作业指导书不详细,不能起指导作用;2、检验员技能不足。
2
1定期修改检验作业指导书;2对检验员现场培训
质量工程师巡检或抽检
4
56无
品管部
Version/版本号
A
措施后果
探测
责任和目标完成日期
R.P.N .
日期
修改人
变更号
修改内容
1 原素材进料检验
6成品检验2储存
预防
4 产品镭雕
建议措施 采取的措施严重度探测度频度
修改编号
7包装和贴标识
现行过程控制
探测度D
C lass 级别
工艺项目 潜在失效模式潜在失效后果
严重度S R.
P.
N.
潜在失效起因/机理
潜在失效模式及后果分析( PFMEA )
频度 O。