压力容器通用工艺守则
压力容器原材料检验通用工艺守则样本

压力容器原材料检验通用工艺守则样本压力容器是一种经过特殊设计和制造的装置,用于储存和运输高压气体、液体或固体。
由于容器内部承受着高压力,因此其原材料的质量和性能至关重要。
以下是压力容器原材料检验的一般工艺守则样本。
1.原材料选择:选择适用的原材料,如碳钢、合金钢、不锈钢等,根据容器的使用环境和工作条件来确定原材料的类型和规格。
2.原材料验收:接收原材料时,应对其进行质量检验。
检查原材料的化学成分、机械性能、外观等指标是否符合技术要求。
可以使用化学成分分析仪、拉伸试验机等设备进行检测。
3.材料切割:根据设计要求和材料规格,将原材料进行切割。
切割时应确保切割面光滑平整,无裂纹、间隙等缺陷。
4.材料加工:对切割好的材料进行加工,如冷冲压、热冲压、焊接等工艺。
加工过程中应注意避免产生过大的热变形和残余应力。
5.焊接:焊接是压力容器制造中最重要的工艺之一、焊接工艺应符合相关的规范和标准。
在焊接前,应对焊接材料进行质量检验,并选用适当的焊接材料和焊接工艺。
6.焊缝检验:焊接完成后,应对焊缝进行检验。
常用的焊缝检验方法有X射线检测、超声波检测、磁粉检测等。
通过检验,判断焊缝的质量是否符合要求。
7.热处理:对焊接完成的容器进行热处理,以消除焊接产生的残余应力,并提高材料的强度和韧性。
8.表面处理:对容器的表面进行处理,以提高其耐腐蚀性和美观度。
常用的表面处理方法有喷砂、热浸镀锌、电镀等。
9.容器测试:对已制造完成的容器进行压力测试、泄漏测试等。
通过测试,验证容器的密封性和安全性。
10.质量检验:对制造好的容器进行质量检验,包括外观检查、储罐容量测试、材料性能测试等。
以上是压力容器原材料检验的一般工艺守则样本。
严格按照这些守则进行原材料的选择、切割、加工、焊接、热处理和测试,可以确保压力容器的质量和安全性。
SZ011检验通用工艺守则
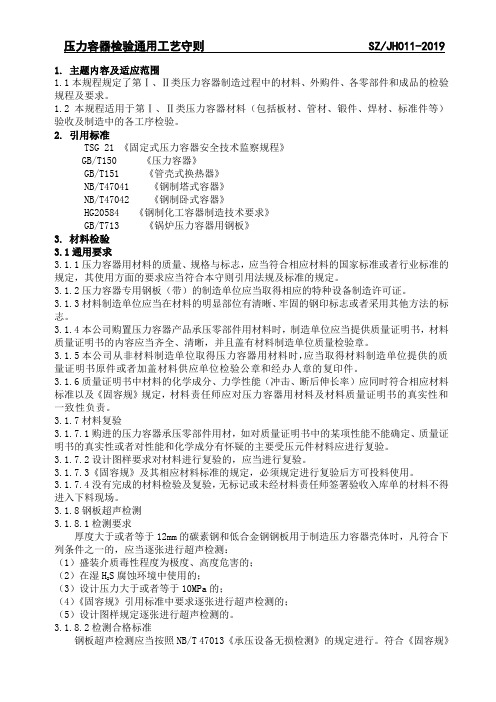
1. 主题内容及适应范围1.1本规程规定了第Ⅰ、Ⅱ类压力容器制造过程中的材料、外购件、各零部件和成品的检验规程及要求。
1.2 本规程适用于第Ⅰ、Ⅱ类压力容器材料(包括板材、管材、锻件、焊材、标准件等)验收及制造中的各工序检验。
2. 引用标准TSG 21 《固定式压力容器安全技术监察规程》GB/T150 《压力容器》GB/T151 《管壳式换热器》NB/T47041 《钢制塔式容器》NB/T47042 《钢制卧式容器》HG20584 《钢制化工容器制造技术要求》GB/T713 《锅炉压力容器用钢板》3. 材料检验3.1通用要求3.1.1压力容器用材料的质量、规格与标志,应当符合相应材料的国家标准或者行业标准的规定,其使用方面的要求应当符合本守则引用法规及标准的规定。
3.1.2压力容器专用钢板(带)的制造单位应当取得相应的特种设备制造许可证。
3.1.3材料制造单位应当在材料的明显部位有清晰、牢固的钢印标志或者采用其他方法的标志。
3.1.4本公司购置压力容器产品承压零部件用材料时,制造单位应当提供质量证明书,材料质量证明书的内容应当齐全、清晰,并且盖有材料制造单位质量检验章。
3.1.5本公司从非材料制造单位取得压力容器用材料时,应当取得材料制造单位提供的质量证明书原件或者加盖材料供应单位检验公章和经办人章的复印件。
3.1.6质量证明书中材料的化学成分、力学性能(冲击、断后伸长率)应同时符合相应材料标准以及《固容规》规定,材料责任师应对压力容器用材料及材料质量证明书的真实性和一致性负责。
3.1.7材料复验3.1.7.1购进的压力容器承压零部件用材,如对质量证明书中的某项性能不能确定、质量证明书的真实性或者对性能和化学成分有怀疑的主要受压元件材料应进行复验。
3.1.7.2设计图样要求对材料进行复验的,应当进行复验。
3.1.7.3《固容规》及其相应材料标准的规定,必须规定进行复验后方可投料使用。
3.1.7.4没有完成的材料检验及复验,无标记或未经材料责任师签署验收入库单的材料不得进入下料现场。
压力容器工艺守则(新)[1]
![压力容器工艺守则(新)[1]](https://img.taocdn.com/s3/m/0865a3926bec0975f465e22b.png)
第一章下料工艺守则1.总则(1) 本守则适用于碳素钢、低合金钢及不锈钢制压力容器的下料工序。
(2) 不锈钢压力容器下料除按本守则规定执行外,还应遵守《不锈钢制压力容器制造工艺守则》的规定。
(3) 本守则若与产品工艺文件有矛盾,应以产品工艺文件为准。
2.通用规定(1) 工艺文件(施工图、工艺卡、钢板排板图、产品零件清单等)齐全,有疑义时应及时向工艺员、材料员反映。
(2) 供应库房按产品零件清单提供符合相应标准的合格材料,下料前要进行复核并做好记录。
(3) 根据钢板排板图进行排板划线。
(4) 按照《标记移植管理制度》进行标记移植。
(5) 按施工图或压力容器焊接工艺文件确定坡口型式。
3.排板图(1) 排板时应根据施工图纸、到货材料规格及以下规定进行排板;a. 焊缝排板图、钢板排板图中下料尺寸、焊缝编号及件号应统一。
b. 筒节的最短长度:碳素钢和低合金钢不小于300mm,不锈钢不小于200mm。
c. 同一筒节纵缝应相互平行,相邻焊缝间的弧长距离:碳素钢和低合金钢不小于500mm,不锈钢不小于200mm。
d. 相邻筒节的纵焊缝中心线间外圆弧长以及封头A类焊缝中心线与相邻筒节A类焊缝中心线间外圆弧长应大于3倍筒节壁厚,且不小于100mm。
e. 容器内件和筒体焊接的焊缝,与其相邻焊缝边缘的距离应不小于筒体壁厚,且不小于50mm。
f. 对于卧式容器,纵焊缝应位于壳体下部140°范围之外。
支座包板角焊缝与筒体焊缝边缘的距离应不小于筒节壁厚,且不小于50mm。
g. 封头由两块或三块钢板拼接时,拼接缝应呈水平或垂直,不宜斜置。
h. 筒体下料尺寸一般按实际测量封头中径展开尺寸配尺。
i.筒体排板时纵、环焊缝应避开开孔边缘1.5倍开孔直径。
(2) 绘制排板图时,以施工图为依据,从节约材料的原则出发,根据所到材料规格的实际情况,按3.(1)的规定,做到合理排板。
(3) 排板图上所标各开孔的轴向安装尺寸应以左封头或下封头与筒体对接焊缝为基准线标注;环向安装尺寸以0°线为基准线测量,以外弧长表示,且在小于180°侧标注。
压力容器工艺守则

压力容器工艺守则压力容器通用工艺守则汇编目录一、下料通用工艺守则 (1)二、筒体制造通用工艺守则 (7)三、封头、管板、换热器等制造通用工艺守则 (12)四、机械加工通用守则 (19)五、不锈钢产品制造通用工艺守则 (20)六、热处理通用工艺守则 (22)七、奥氏体不锈钢压力容器酸洗钝化工艺守则 (27)八、耐压试验和气密性试验通用工艺守则 (30)九、油漆通用工艺守则 (36)十、包装通用工艺守则 (40)十一、金属材料化学分析通用工艺守则 (42)十二、金属材料机械性能试验通用工艺守则 (45)十三、金相试验通用工艺守则 (47)十四、检验通用工艺守则 (49)十五、无损检测通用工艺手册 (68)一、下料通用工艺守则总则1.1压力容器下料通用工艺守则,以下简称《下料守则》,是压力容器制造中材料、总零部件下料等工序遵照的工艺技术文件。
1.2《下料守则》若与《容规》标准,图样各工艺文件的技术要求不相符时,应以《容规》、标准、图样要求及工艺文件为准。
1.3凡属受压元件的材料<板材、管材、棒材>应有标记。
当钢材需割开前、应按《材料标记移植制度》先进行移植。
1.4下料人员必须熟悉图纸:工艺文件、核对图纸要求的材料与投入使用的材料是否相符,需代用的材料手续是否齐全,严禁使用不合格的材料。
1.5下料人员应根据使用的板材,型材的规格和图纸尺寸,进行排料,并注意下列各项要求。
1.5.1避免支座和接管开孔碰上焊缝。
1.5.2钢管拼接的最短长度;碳素钢不小于300mm,不锈钢不小于400mm。
1.5.3下料时应取钢板的轧制方向与卷园平行。
1.6凡使用气割下料的钢材应垫平,要求切口光滑、平整、垂直,并将熔渣和飞溅必须清除干净。
表面不得有裂纹、分层、夹渣等缺陷。
1.7 奥氏体不锈钢下料划线时不得使用钢针和能引起表面刻痕的工具,应使用无氯无硫记号笔书写划线,标记移植时,不得打钢印,不得使用油漆、等有污染的物料书写。
压力容器原材料检验通用工艺守则样本

压力容器原材料检验通用工艺守则样本1.本工艺适用范围:本工艺适用于D 级压力容器产品所用的受压原材料的入厂检验。
2.原材料入厂验收的程序为:原材料报验T审核质量证书,确定检验标准T 外观检验T 给出检验编号,取样打标记T 试样加工及检验T 理化室按规定项目试验T 理化室作试验记录和试验报告T材料责任人审核试验报告并定结论T 办理入库手续。
3.材料员办理原材料报验手续:(1)采购员将受控原材料连同票证、质量证书一起移交材料库管员。
(2)库管员检查票证及质量证书,看其炉批号、钢号、规格、数量和实物是否相符,核对无误后填写《原材料报验单》,连同质量证书移交材料检验员。
然后将待验的原材料放在待验区。
4.审核质量证书,确定检验标准:(1)材料检验员收到《报验单》及质量证书后,按《压力容器安全技术监察规程》(以下简称“容规” )第10 条的规定审核质量证书的内容是否齐全、清晰,并符合相应标准。
如从非生产单位购料时,应取得材料质量正证明书原件或加盖供材单位检验公章和经办人章的有效复印件。
材料质量证明书无效或内容不全、不符合相关标准的一律不予验收。
( 2) 核对无误后,材料检验员应根据受压材料的品种确定验收标准。
5.外观检验:(1)材料检验员根据《容规》第10条、GB150第4章的规定,按受压原材料质量证书检查原材料上的炉批号、钢号及规格、数量、几何尺寸,检查其材料标记是否清晰、齐全。
(2)检验员根据《容规》、GB150和相应的材料标准的规定进行外观检验,并填写材料外观检验纪录。
检验员应按上述标准判定受检原材料是否合格。
6.给出检验编号,取样打标记:( 1 ) 检验员对原材料外观检验合格后,应由材料责任人按有关规定给出检验编号。
( 2) 除了《容规》第25 条规定须作材料复验的以外,即可按本《原材料检验通用工艺》第9 条的规定由材料责任人定结论,并办理材料入库手续。
(3)对第25 条规定必须作复验的材料 (即I 、II 类压力容器的受压原件、M36以上的设备主螺栓和直径大于等于250mm的接管和法兰等原件所用的材料,当设计图样或用户要求复验时,或制造单位对材料的性能和化学成分有怀疑时),材料责任人应做材料复验的决定,并通知材料检验员进行取样、材料复验。
压力容器制造工艺守则

1.下料工艺守则GS01-20101. 1总则1. 1. 1下料是产品制造的首道工序,直接影响到产品的制造质量和原材料的合理使用,特拟定本守则。
1. 1. 2下料人员必须做到:(a)主要受压元件及一般受压元件必须严格按照工艺或图纸要求进行划线下料,按照材料标记移植规定进行移植材料标记。
(b)非受压元件按工艺流程、材料消耗定额卡的下料规格和材质进行划线下料。
(c)凡图纸、工艺不全,材料不符合图纸要求,代料需代用而无“材料代用通知”时不准划线下料。
(d)划线经自检、专检无误后,方可进行下料。
(e)清除下料飞边、毛刺和飞溅物。
非机械加工表面的线性尺寸的极限偏差应符合GB/T1804中的C级规定。
1. 1. 3下料场地及切割划线工具的要求:(a)不锈钢、钛材、铝材下料均应铺有橡胶或其它软质材料,均不得与钢材混合。
(b)钛材、铝材的切割和坡口加工一般采用机械方法,厚度较大时也允许用火焰切割和等离子切割,此时应避免火花溅落在材料表面,且切割边缘和坡口应用机械方法加工和去除污染层,见金属光泽。
复合板在机械切割时应将基层朝下,注意防止分层。
加工后的坡口表面应平整、光滑、不应有裂纹、分层、毛刺和飞边等。
不锈钢用等离子机械切割方法。
用等离子下料或开孔的板材,如割后尚需焊接,则要去除割口处的氧化物至显露金属光泽。
严禁在不锈钢材料垛直接切割下料。
这几种材料当采用机械切割时,下料前应将机械清理干净,为防止板材表面划伤,压脚上应包橡胶等软质材料。
(c)划线、标记确定要求:铝制容器:在原有确定标记被裁掉或材料分成几块,应有材料切割前完成标记移植。
划线时应注意避免磕碰、划伤,不应在表面用划针划辅助线,必要时用红蓝铅笔。
不应在铝材的耐腐蚀面采用硬印作为材料的确认标记。
钛制容器:在钛材划线应尽量采用金属铅笔,只有在以后加工工序中能除的部分才允许打冲眼,钛钢复合层的划线应在基层钢板上进行,不应在钛材和钛钢复合板的耐腐蚀面采用硬印作为材料的确认标记的表达方法,可采用不溶于水的不含金属颜料的无硫、无氯的墨水书写。
压力容器制造通用工艺守则

一、下料通用工艺1 范围本通用工艺规定了下料的工艺规则,适用于本公司的产品材料的下料。
2 下料前的准备2.1 看清下料单上的材质、规格、尺寸及数量等。
2.2核对材质、规格与下料单要求是否相符。
材料代用必须严格履行代用手续。
2.3 查看材料外观质量(疤痕、夹层、变形、锈蚀等)是否符合有关质量规定。
2.4 将不同工件所用相同材质、规格的料单集中,考虑能否套料。
2.5 号料2.5.1 端面不规则的型钢、钢板、管材等材料号料时必须将不规则部分让出。
钢材表面上如有不平、弯曲、扭曲、波浪等缺陷,在下料切割和成形加工之前,必须对有缺陷的钢材进行矫正。
2.5.2 号料时,应考虑下料方法,留出切口余量。
2.5.3 有下料定尺挡板的设备,下料前要按尺寸要求调准定尺挡板,并保证工作可靠,下料时材料靠实挡板。
3 下料3.1剪板下料3.1.1钢板、角钢、扁钢下料时,应优先使用剪切下料。
钢板、扁钢用龙门剪床剪切下料,角钢用冲剪机剪切下料。
3.1.4 下料时应先将不规则的端头切掉。
3.1.5 切口断面不得有撕裂、裂纹、棱边。
3.1.6 龙门剪床上的剪切工艺3.1.6.1 首先清理工件并划出剪切线,将钢板放至剪床的工作台面上,使钢板的一端放在剪床台面上以提高它的稳定性,然后调整钢板,使剪切线的两端对准下刀口,控制操作机构将剪床的压紧机构先将钢板压牢,接着进行剪切。
剪切狭料时,在压料架不能压住板料的情况下可加垫板和压板,选择厚度相同的板料作为垫板。
3.1.6.2 剪切尺寸相同而数量又较多的钢板、型材时,利用挡板(前挡、后挡板和角挡板)定位,免去划线工序。
3.1.6.3 利用挡板进行剪切时,必须先进行试剪,并检验被剪尺寸是否正确,然后才能成批剪切。
3.2 气割下料3.2.1 气割时,看清切割线条符号。
3.2.2切割前,将工件分段垫平(不能用砖和石块),将工件与地面留出一定的间隙利于氧化铁渣吹出。
3.2.3 将氧气调节到所需的压力。
压力容器守则
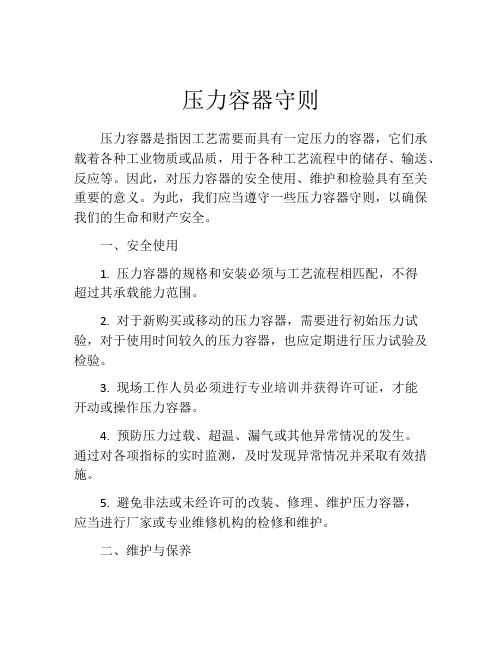
压力容器守则压力容器是指因工艺需要而具有一定压力的容器,它们承载着各种工业物质或品质,用于各种工艺流程中的储存、输送、反应等。
因此,对压力容器的安全使用、维护和检验具有至关重要的意义。
为此,我们应当遵守一些压力容器守则,以确保我们的生命和财产安全。
一、安全使用1. 压力容器的规格和安装必须与工艺流程相匹配,不得超过其承载能力范围。
2. 对于新购买或移动的压力容器,需要进行初始压力试验,对于使用时间较久的压力容器,也应定期进行压力试验及检验。
3. 现场工作人员必须进行专业培训并获得许可证,才能开动或操作压力容器。
4. 预防压力过载、超温、漏气或其他异常情况的发生。
通过对各项指标的实时监测,及时发现异常情况并采取有效措施。
5. 避免非法或未经许可的改装、修理、维护压力容器,应当进行厂家或专业维修机构的检修和维护。
二、维护与保养1. 压力容器应进行定期检查,依据可以分为定期检验和定期维护。
2. 定期检验:是指周期性地进行对压力容器内部、外部结构的检验、试验、测量,并在其安全使用期内,满足国务院、生产安全监督管理部门安全技术规程的要求,进行监督检验。
3. 定期维护:是指随着压力容器的使用,由于外表面的腐蚀变形或内部管道腐蚀、老化等原因引起的定期维修改造。
维修是指修复已经损害的部位或修补破损、变形、出现裂缝等缺陷,改造是指对压力容器的改造、加强,以延长其使用寿命。
4. 对压力容器的维护保养应该作出严格的计划,并进行每一项的记录与整理,避免忽视小的问题而带来安全隐患。
三、安全管理1. 压力容器必须经过许可和备案,实行安全生产许可制度,并组建专业的安全管理机构,全课必须接受安全管理培训。
2. 对于涉及到危险度较高的压力容器使用,应当在其周边设置防护区,并设置安全警示标志。
3. 严防未经许可、未得到授权的人员对压力容器进行操作、卸载、拆卸等行为。
如压力容器因应力过大、过时失效或由于其他原因导致严重问题时必须立即关闭相关设备,进行整改操作。
压力容器焊缝返修及补焊通用工艺守则

焊缝返修及补焊通用工艺守则1.适用范围1.1 本守则为通用工艺文件,仅适用于不锈钢制压力容器的筒体、封头、接管对接,法兰拼接焊缝焊接缺陷的返修。
1.2 本守则不足以保证特殊情况下缺陷返修的质量时,需另行制订专用的返修工艺文件。
2. 返修程序2.1 焊缝返修由探伤室开出返修通知单,确定缺陷性质,部位。
2.2 第一、二次返修需经焊接责任人批准,焊工按探伤人员在产品上所划出的缺陷部位进行返修、焊接检验员监督返修程序的进行。
2.3 第三次返修前由焊接责任人制订返修方案,得到技术负责人批准后方可进行,焊接责任人负责现场监督。
3.焊工3.1 返修部位的焊接工作,必须由考试合格,具有焊接相应项目资格的焊工担任。
3.2 第一、二次返修时,一般情况下可由原施焊的焊工进行,第三次返修时,由焊接责任人指定焊工进行返修。
4. 返修焊缝所用的焊接材料,原则上与该焊缝所采用的焊接材料相同,等离子弧自动焊除外。
5. 缺陷清除5.1 清除焊接缺陷可以用角向砂轮磨。
5.2 从筒体内侧或外侧清除缺陷,视探伤结果而定,原则上是返修量越少越好。
5.3 当清除深度已达厚度的三分之二,而缺陷尚未清除时,则不应再清除下去,而应将此侧先补焊完毕,再从另一侧将缺陷清除掉,然后补焊。
5.4 焊接缺陷必须彻底清除干净,缺陷清除后的返修表面要圆滑,不得有尖锐棱角。
6. 焊接6.1 焊接方法原则上与原来的方法相同,等离子弧自动焊除外。
6.2 第一层焊缝一般应用Φ3.2㎜的焊条焊接,焊接电流较一般施焊大10%左右,以保证焊透,且一般不用摆动焊法。
6.3 每条焊缝的起弧和收弧处应错开20㎜以上,并注重起弧与收弧的质量。
6.4 每焊一层都应仔细检查,确定无缺陷后再焊下一层,不允许采用单层,单道大规范及慢焊速进行补焊。
6.5 必须修磨返修部位的焊缝表面,使其外形与焊缝基本一致,经外观检查合格后,按原焊缝的无损检测要求进行探伤。
6.6 不锈钢焊缝返修时,应控制层间温度不得超过60℃,返修焊缝表面不得有咬边等缺陷。
压力试验通用工艺守则

压力试验通用工艺守则1.主题内容与适用范围本标准规定了压力容器耐压试验工艺技术要求。
本标准适用于我公司一、二类压力容器耐压试验、泄漏试验。
2.引用标准固定式压力容器安全技术监察规程GB150-98钢制压力容器3.耐压试验通用要求3.1耐压试验方法分为液压试验、气压试验和气液组合压力试验三种。
3.2耐压试验的压力应当符合设计图样要求,并且不小于下式计算值:P T[][]tPσση=式中:PT-耐压试验压力,MPa;η-耐压试验压力系数。
对于钢制压力容器液压试验时为1.25;气压试验和气液组合压力试验时为1.1。
P-压力容器的设计压力,MPa;[σ]-试验温度下材料的许用应力,MPa;[σ]t-设计温度下材料的许用应力,MPa。
压力容器各元件(圆筒、封头、接管、法兰等)所用材料不同时,计算耐压试验压力应当取各元件材料[σ]/[σ]t比值中最小者。
3.3耐压试验前的准备工作(1)耐压试验必须在容器经过全面检验合格后进行,耐压试验前,压力容器各连接部位的紧固螺栓必须装配齐全、紧固妥当;(2)耐压试验至少采用二个量程相同并且经过校验的压力表。
试验压力小于1.6MPa时使用的压力表的精度不应当低于2.5级,试验压力大于等于1.6MPa时使用的压力表的精度不应当低于1.6级。
压力表盘刻度极限值应当为试验压力的1.5~3.0倍,表盘直径不应当小于100mm。
试验用压力表应当安装在被试验压力容器顶部便于观察的位置。
(3)耐压试验时,压力容器上焊接的临时受压元件,应当采取适当的措施,保证其强度和安全性。
(4)容器的开孔补强圈应在压力试验前通入0.4~0.5MPa的压缩空气检查焊接接头质量。
(5)耐压试验场地应有可靠的安全防护措施,安全防护措施须经单位技术负责人和安全管理部门检查认可。
3.4保压期间不得采用连续加压来维持试验压力不变,耐压试验过程中不得带压紧固螺栓或者向受压元件施加外力。
3.5耐压试验过程中不得进行与试验无关的工作,无关人员不得在试验现场停留。
压力容器制造工艺守则

压力容器制造工艺守则针对压力容器制造工艺,制作出高质量的产品需要严格遵守守则。
本文将围绕这个主题,从以下几方面来阐述。
一、设计规范压力容器的制造过程必须严格遵守国家相关标准和规范,根据实际使用情况,进行设计和计算。
其中包括:建筑设计规范、压力容器制造工艺规范、压力管道技术规范等。
在设计过程中必须注意物料的选择、结构设计、底板设计等。
要保证容器结构稳定,避免在使用中产生安全隐患。
二、材料的选择压力容器的制造材料必须符合规范并具有高强度、高韧性、耐腐蚀性等优良的性能。
在选择材料时一定要注意材料的组织结构和化学成分,材料的开裂倾向等。
只有选对材料,才能使压力容器具有高强度和耐腐蚀性。
三、制造基本要求一是要完整记录和备份各种制造工艺的过程和检验记录。
二是要严格按照制造过程规范进行制造。
三是要遵循流程图或工艺路线图完成每个工序,用精细的设备进行组装或焊接。
四是要严格进行压力容器的检验,注意检查压力容器表面是否平整、无瑕疵和散焊,以及其它细节。
五是要按检验标准进行验收。
严格遵守这些制造基本要求是制造质量保障的重要措施。
四、生产过程的管理在生产过程中,需要对操作人员进行严格培训和管理,确保各生产环节遵照规范进行。
在质量管理中,对产品进行分类管理和过程控制,可以从根本上保证产品质量,减少错误和不良品率。
五、质量控制在生产过程中,通过对各工序进行严格的质量控制,防止有缺陷的产品投入市场。
同时,要对产品进行质量检验,保证产品符合国家标准和用户要求的各种性能指标。
要做好检验标准、校验和检定等工作,以确保产品性能监控和产品质量的稳定。
六、售后服务售后服务是一项重要的工作,也是压力容器企业竞争力的体现。
企业需要完善售后服务流程,为用户提供及时、周到的服务。
对于用户遇到的问题要及时回应并提供解决方案,对于有质量问题的产品,要快速处理,及时维修或更换产品,以维护客户的利益。
总之,严格遵守压力容器制造守则,保障制造质量和产品安全,同时在售后服务上与客户建立长期信任。
15压力容器充氮保护通用工艺守则
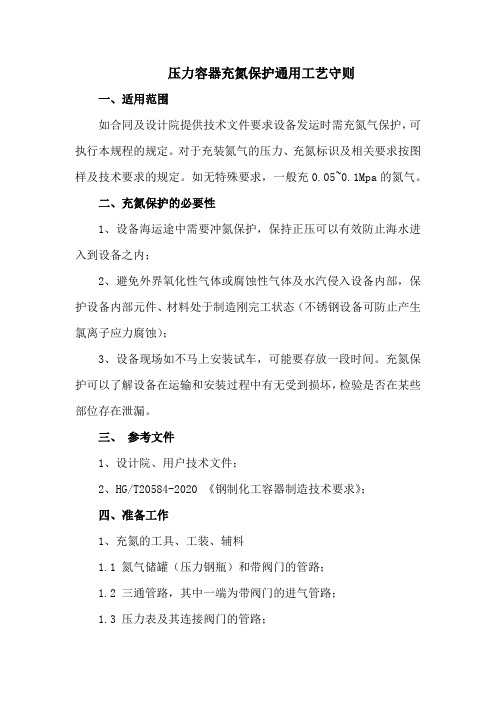
压力容器充氮保护通用工艺守则一、适用范围如合同及设计院提供技术文件要求设备发运时需充氮气保护,可执行本规程的规定。
对于充装氮气的压力、充氮标识及相关要求按图样及技术要求的规定。
如无特殊要求,一般充0.05~0.1Mpa的氮气。
二、充氮保护的必要性1、设备海运途中需要冲氮保护,保持正压可以有效防止海水进入到设备之内;2、避免外界氧化性气体或腐蚀性气体及水汽侵入设备内部,保护设备内部元件、材料处于制造刚完工状态(不锈钢设备可防止产生氯离子应力腐蚀);3、设备现场如不马上安装试车,可能要存放一段时间。
充氮保护可以了解设备在运输和安装过程中有无受到损坏,检验是否在某些部位存在泄漏。
三、参考文件1、设计院、用户技术文件;2、HG/T20584-2020 《钢制化工容器制造技术要求》;四、准备工作1、充氮的工具、工装、辅料1.1 氮气储罐(压力钢瓶)和带阀门的管路;1.2 三通管路,其中一端为带阀门的进气管路;1.3 压力表及其连接阀门的管路;1.4 纯净氮气(氮气纯度99.99%以上);1.5 便携式氧含量检测仪;1.6 肥皂水。
2、充氮前准备:2.1 设备、仪器、仪表等需经有关部门标定合格,且在有效期内。
必须用两个量程相同的并经校正的压力表。
压力表的量程为充氮压力的2倍为宜,但不应低于1.5倍和高于3倍的试验压力,压力表精度等级不得低于2.5级;2.2 操作者必须经过专业技术培训方可上岗操作。
遵守有关劳动保护及劳动安全法规、规定、制度,做到安全生产,设备及工具等操作遵守操作规程;2.3 检查各相应管路、接头、阀门及产品连接的可靠性;2.4 压力表安装在产品的顶部便于观察的位置。
五、充氮工序1、设备制作完毕并经检验合格后,充氮前必须用压缩空气把设备内部吹干,特别是刚做完水压试验的设备,干燥处理并检验合格;2、装焊各管口法兰盖(闷盖)、螺塞及人孔盖等,法兰盖(闷盖)需经校核强度合格。
各连接部位的紧固螺栓,必须装配齐全,紧固妥当;3、设备充氮口用连接管路应焊接(连接)牢固,防止设备在运输过程中由于颠簸而产生松动,避免充氮设备到安装工现场后,氮气压力表已经为零了,不能完全起到保护作用。
压力容器工艺守则

压力容器工艺守则压力容器是在许多行业中使用的重要设备,如化工、石油、天然气等。
为了确保压力容器的安全性能和可靠性,需要遵守严格的工艺守则。
下面就是关于“压力容器工艺守则”的一些详细介绍。
一、压力容器的设计标准根据不同的行业和用途,压力容器有着不同的设计标准和规范。
在设计压力容器时,必须遵守所采用的国家或行业标准,例如ASME(美国机械工程师协会)规范、JIS(日本工业标准)或GB(国家标准)等。
在进行设计的过程中,还要考虑到容器的适用环境和使用条件,并应遵循安全性、可靠性、经济性和节能减排等原则。
二、材料的选择在压力容器的设计中,材料的选择是至关重要的。
选择材料时,需要考虑其抗腐蚀性能、强度、塑性、热膨胀系数、裂纹敏感性等因素。
钢制品是最常用的压力容器材料,而不锈钢、镍合金、合金钢等也是常见的选择。
必须严格遵照标准要求,选择具有合适化学成分和相应耐蚀性的材料。
三、焊接工艺的要求焊接是压力容器制造的重要环节之一。
焊接质量的好坏直接影响着容器的结构安全和产生不良事故的概率。
焊接前需要进行充分的预备工作,如清洁焊接部位、选用适当的焊接工艺、应用合适的焊接辅材、保障佳的焊接温度、施加正确的焊接加压力等。
必须注意对焊接部位进行可靠性测试,进行X光或者超声波探伤等测试手段,以确保数据真实有效。
四、检测和检验在压力容器的制造中,将涉及很多不同的检测和检验程序和设备,以确保容器的质量和安全性。
例如,涉及到材料金相检测、焊接断面金相检测、压力试验、超声波探伤等等。
每一项检测和检验都必须符合国家或行业标准的要求,并由专业的检验人员进行操作。
在检测和检验过程中,如出现任何问题,都应及时进行排除和修复,确保容器构件可以满足标准要求和安全性能。
总的来说,压力容器工艺守则是非常重要的,必须遵循标准要求,确保容器的安全性和可靠性。
只有符合标准,压力容器才可以发挥其最大的作用,为我们的生产和生活提供更加稳定的保障。
在制造压力容器时,合理选材、科学自变量规、精选接径合和高质量检测是非常必要的。
容器组装通用工艺守则
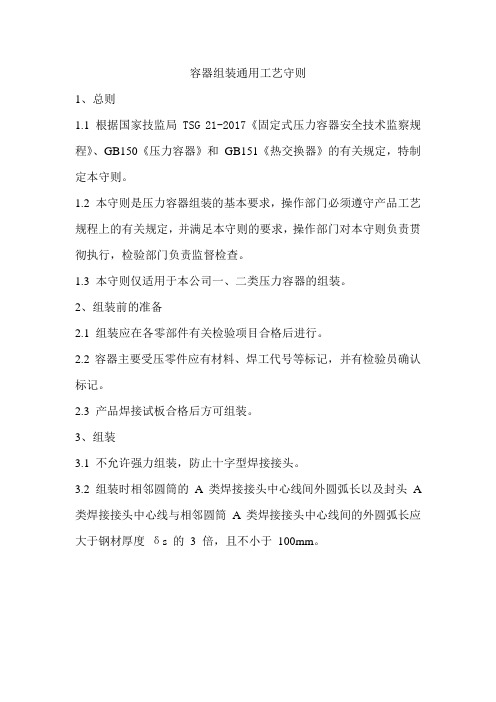
容器组装通用工艺守则1、总则1.1 根据国家技监局TSG 21-2017《固定式压力容器安全技术监察规程》、GB150《压力容器》和GB151《热交换器》的有关规定,特制定本守则。
1.2 本守则是压力容器组装的基本要求,操作部门必须遵守产品工艺规程上的有关规定,并满足本守则的要求,操作部门对本守则负责贯彻执行,检验部门负责监督检查。
1.3 本守则仅适用于本公司一、二类压力容器的组装。
2、组装前的准备2.1 组装应在各零部件有关检验项目合格后进行。
2.2容器主要受压零件应有材料、焊工代号等标记,并有检验员确认标记。
2.3 产品焊接试板合格后方可组装。
3、组装3.1 不允许强力组装,防止十字型焊接接头。
3.2 组装时相邻圆筒的A 类焊接接头中心线间外圆弧长以及封头A 类焊接接头中心线与相邻圆筒A类焊接接头中心线间的外圆弧长应大于钢材厚度δs 的3 倍,且不小于100mm。
3.3 A、B 类焊接接头以及圆筒与球形封头相连的A 类焊接接头,当两侧板厚不等时,若薄板厚度不大于10mm,两板厚度差超过3mm,若薄板厚度大于10mm,两板厚度差大于薄板厚度的30%,或超过5mm 时,均应按图一的要求单面或双面削薄厚板边缘或按图样要求采用堆焊方法将薄板边缘焊成斜面。
图一3.4 当两板厚度差小于上列数值时,则对口错边量 b 按《筒体制造通用工艺守则》中表一规定,且对口错边量 b 以较薄板厚度为基准确定。
在测量对口错边量b 时,不应计入两板厚度的差值。
3.5 由焊接接头轴向或环向形成的棱角度E,用长度不小于300mm的直尺或不小于300mm 的内样板(或外样板)检查,其值均为E≤(0.1δs+2)mm,且不大于5mm。
3.6 换热器园筒内直径允许偏差。
3.6.1 用钢板卷制时,内直径允许偏差可通过外园周长加以控制,其外园周长允许上偏差为10mm,下偏差为零。
3.6.2 用钢管作圆筒时,其尺寸允许偏差应符合GB/T8163、GB/T14976 的规定。
钢制压力容器焊接通用工艺守则
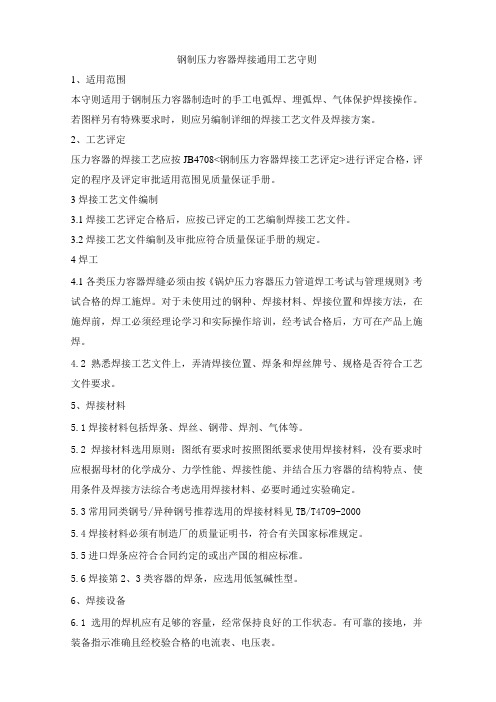
钢制压力容器焊接通用工艺守则1、适用范围本守则适用于钢制压力容器制造时的手工电弧焊、埋弧焊、气体保护焊接操作。
若图样另有特殊要求时,则应另编制详细的焊接工艺文件及焊接方案。
2、工艺评定压力容器的焊接工艺应按JB4708<钢制压力容器焊接工艺评定>进行评定合格,评定的程序及评定审批适用范围见质量保证手册。
3焊接工艺文件编制3.1焊接工艺评定合格后,应按已评定的工艺编制焊接工艺文件。
3.2焊接工艺文件编制及审批应符合质量保证手册的规定。
4焊工4.1各类压力容器焊缝必须由按《锅炉压力容器压力管道焊工考试与管理规则》考试合格的焊工施焊。
对于未使用过的钢种、焊接材料、焊接位置和焊接方法,在施焊前,焊工必须经理论学习和实际操作培训,经考试合格后,方可在产品上施焊。
4.2熟悉焊接工艺文件上,弄清焊接位置、焊条和焊丝牌号、规格是否符合工艺文件要求。
5、焊接材料5.1焊接材料包括焊条、焊丝、钢带、焊剂、气体等。
5.2焊接材料选用原则:图纸有要求时按照图纸要求使用焊接材料,没有要求时应根据母材的化学成分、力学性能、焊接性能、并结合压力容器的结构特点、使用条件及焊接方法综合考虑选用焊接材料、必要时通过实验确定。
5.3常用同类钢号/异种钢号推荐选用的焊接材料见TB/T4709-20005.4焊接材料必须有制造厂的质量证明书,符合有关国家标准规定。
5.5进口焊条应符合合同约定的或出产国的相应标准。
5.6焊接第2、3类容器的焊条,应选用低氢碱性型。
6、焊接设备6.1选用的焊机应有足够的容量,经常保持良好的工作状态。
有可靠的接地,并装备指示准确且经校验合格的电流表、电压表。
7焊前准备7.1焊缝坡口形式、尺寸、容器开孔、接管、接头型式按设计图纸要求或工艺文件确定,制造厂也可以参照有关标准结合制造、施工经验自行设计,以工艺文件形式确定。
7.2坡口加工宜采用机械方法,也可采用等离子弧、气割等热加工方法,对于碳素钢和标准抗拉强度不大于540Mpa的碳锰低合金钢,两种方法均可选择,对于标准抗拉强度大于540Mpa的碳锰低合金钢、铬钼低合金钢和高使金钢宜采用机械加工,若采用热加工方法,在进行切割后,应消除表面淬硬层。
压力容器筒体制造通用工艺守则102

压力容器制造、检验通用工艺规程文件编号Q/PV-Q-3-102-2003第 1 版筒体制造通用工艺规程第0 次修改修改日期:第 1 页共8 页1总则1.1 本守则依据GB150—1998《钢制压力容器》和GB151—1999《管壳式换热器》标准,以及《压力容器安全技术监察规程》99版,结合我厂设备及技术力量,编制的压力容器筒体制造通用工艺守则。
1.2 由于压力容器种类较多,各种类型之间要求各不相同,因此,本守则若同产品设计或工艺文件有矛盾时,应以产品设计图样设计要求或工艺文件规定为准。
1.3 操作工人必须熟悉图样和工艺文件,对本岗位所使用的设备结构性能和操作规程必须了解。
1.4 筒体焊缝必须由持证合格焊工施焊。
2 材料2.1 制造筒体用的材料质量及规格应符合《容规》第10条国标、部标及相应的国家标准、行业标准有关的规定,并具有质量证明书,材料上明显部位有清晰、牢固的钢印标志或其他标志。
2.2 属下列之一的主要受压元件材料应复验2.2.1 设计图样要求复验的;2.2.2 用户要求复验的;2.2.3 制造单位不能确定材料真实性或材料的性能和化学成分有怀疑的;2.2.4 钢材质量证明书注明复印件无效或不等效的。
2.3 需要代用的材料,原则上应事先取得原设计单位出具的设计更改批准文件。
2.4 制造筒体的钢板表面不得有严重锈蚀或裂纹、斑疤、夹层等影响强度的缺陷。
2.5 严禁使用未经检验或检验不合格的材料。
3 筒体加工3.1 领料3.1.1 领料人员应根据领料单、图样、工艺过程卡,核对材料规格,材质标记,并在工艺过批准: 审核:编制: 2003.08.15实施压力容器制造、检验通用工艺规程文件编号Q/PV-Q-3-102-2003第 1 版筒体制造通用工艺规程第 0 次修改 修改日期: 第 2 页 共8 页程卡上作记录。
3.1.2 所领钢板平直度必须在允差范围内,其弧曲度与波浪度可根据具体产品图样要求确 定。
钢制压力容器下料通用工艺守则

钢制压力容器下料通用工艺守则(总13页)--本页仅作为文档封面,使用时请直接删除即可----内页可以根据需求调整合适字体及大小--1 适用范围本守则规定了压力容器受压元件下料的通用技术要求。
本工艺守则规定了下料工序的操作要点、质量要求和控制的主要内容。
本守则适用于压力容器制造零部件的下料工序。
2 引用标准《压力容器安全技术监察规程》GB150-98《钢制压力容器》(第1、2号修改单)GB151-99《管壳式换热器》(第1号修改单)公司《质量手册》及相关程序文件、管理制度3 材料压力容器用材料的质量及规格应符合《压力容器安全技术监察规程》、GB150-2011《钢制压力容器》、GB151-2012《管壳式换热器》及相应国家标准、行业标准的规定。
制造压力容器受压元件的材料必须具有材料生产单位按照相应标准规定提供的质量证明书(原件)。
质量证明书的内容必须齐全、完整,并应有材料生产单位质量检验部门盖章确认。
如质量证明书为材料生产单位出具的复印件,应由材料销售单位在质量证明书的复印件中加盖销售单位质量检验章和经办人章。
购进的压力容器受压元件用材,应有明显清晰的标志,且和质量证明书一致,图样及相关标准要求复验及对质量证明书中的某项性能有怀疑时均需复验,没有完成的材料检验,未经材料责任师签署验收入库单的材料不得进入下料现场。
投入下料现场的材料未种植本单位材料代号标识及检查员见证标识,不允许进行划线下料。
主要受压元件用材必须进行标记的种植,且应经材料检查员确认。
在使用中始终保留有标识,当制造中需要使用时,应进行标记的移植,并有材料检验员的确认标记。
主要受压元件包括:压力容器中筒体,封头(端盖),人孔盖、人孔法兰、人孔接管、膨涨节、开孔补强圈、设备法兰、换热器的管板和换热管、M36mm以上的设备主螺栓及直径大于等于250mm的接管和管法兰。
标记位置图1 筒节钢板拼接标记位置封头拼缝图2 封头钢板标记位置图3 圆形锻件标记位置图4管板、法兰标记位置4 划线划线工人必须熟悉图样和制造卡的要求,划线前应核对材料的品种、规格是否符合图样和工艺文件的要求。
压力容器通用守则

一、压力容器筒体、封头、下料通用工艺一、下料人员根据图纸及铆造工艺文件的规定,及下料尺寸,持工艺卡去仓库找保管员领用筒体及封头的板材料。
二、所用材料应依据铆造工艺规定,在整板上划出所用材料的尺寸,下料应本着尽量节省主料,少出下脚料的原则,划线尺寸应考虑加工量的预留,封头尺寸按规定尺寸不动,筒体下料尺寸长度应考虑坡口加工量,宽度应考虑加工时变形量原则上内周长算尺寸减去一个板的厚度为宜。
同时也应考虑剩料能否再利用的原则,线划好后请质检员验证尺寸。
三、材料在切割前应将材料发料单与板材的炉批号、规格、对应复查无误进行材料标识移植。
移植部位按质保手册规定执行,对已移植的下料板材由质检员进行确认,验证合格后才能进行切割,根据不同的材料选用不同的切割方法,如气割、等离子及剪板机等方法。
四、下料后的板材应在加工不影响的部位用油漆或油性划号笔写上所制容器的制号及下料编号,以示区别及确认。
五、本守则下料未包括的事宜以质保手册规定为准则依据。
二、筒体卷圆纵缝组对通用工艺守则一、筒体卷圆时应对来料的尺寸及标识移植进行复核无误后才能加工。
二、加工时如用数控卷板机可一次成型,但对厚板〉12㎜的应予制两头的过渡圆弧,然后才能一次成型。
三、对已成型的圆筒节,应进行内径的尺寸复验,并对有椭圆度超标的应进行修正滚制,直到达到要求后才能进行组对焊缝点焊。
四、点焊组对焊缝时不能强力组对,应顺其自然组对减少组对应力及焊后变形,点焊组对后应请质检员对筒节的椭圆度,棱角度及错边量进行初检验,对达到要求的组对筒节才能转焊接工序,严禁超标的筒节转焊接工序。
五、对未能考虑到的因素,以质保手册规定为依据。
三、壳体环焊缝组对工艺规程一、壳体环焊缝组对是由筒节与筒节或与封头的组对焊缝构成。
二、筒节在组对时应先对每个筒节的外形尺寸,及排版图进行确认,防止组对后发生不直度错边量,棱角度超标及开孔开在焊缝上的不良后果影响产品质量。
三、组对时应对每个筒节直径误差最小的两个筒节组对在一起,同时要保证组对后筒体的不直度应符合要求,并对每个筒节、封头的制号、材质标记确认,以防错装配。
- 1、下载文档前请自行甄别文档内容的完整性,平台不提供额外的编辑、内容补充、找答案等附加服务。
- 2、"仅部分预览"的文档,不可在线预览部分如存在完整性等问题,可反馈申请退款(可完整预览的文档不适用该条件!)。
- 3、如文档侵犯您的权益,请联系客服反馈,我们会尽快为您处理(人工客服工作时间:9:00-18:30)。
6.14压力容器组装的操作接TYR1115-2012的有关要求进行。
6.15受压元(部)件涂敷与运输包装的操作按TYR1116-2012的有关要求进行。
7加工操作后的处理
7.1各加工工序完成后的工件经检验合格后方能转入下道工序。
4.2.4划线时按设计图样和工艺文件以1:1比例在钢材上进行,同时应根据不同的下料方法留出适当的切割余量。
4.2.5划线时,应首先划出基准线,再划其它的线;对于对称的工件,一般应先划出中心线,以此为基准再划弧线,最后再划各直线。划线时可用样冲打出划规的定位点。
4.2.6用石笔划出或粉线弹出的线条应清晰、准确。
TSG R0004 固定式压力容器安全技术监察规程
3 工艺技术准备
3.1根据所要加工的工件或产品图样及技术要求,按本守则的相应内容,编制工件或产品制造工艺文件,规定具体的工艺要求。
3.2按工艺要求设计或选用所需使用的工艺设备和工艺装备。
4操作前的准备
4.1操作人员接到加工任务后,应检查加工所需的产品图样、工艺文件和有关技术资料是否齐全、正确。
GB150.1-2011 第1部分:通用要求
GB150.2-2011 第2部分:材料
GB150.3-2011 第4部分:制造、检验和验收
JB/T 4308锅炉产品钢印及标记移植规定
JB/T 10045.3 热切割 气切割质量及尺寸偏差要求
3 操作人员要求
3.1操作人员应熟悉图样、技术要求及工艺文件的内容,并熟悉所用设备、工具的使用性能,严格遵守设备操作规程、工艺要求和设备维护保养规则。切割及设备操作人员应具备相应的操作证。
GB/T 21433 不锈钢压力容器晶间腐蚀敏感性检验
JB/T 4700 压力容器法兰分类与技术条件
JB/T 4701 甲型平焊法兰
JB/T 4702 乙型平焊法兰
JB/T 4703 长颈对焊法兰
JB/T 4704 非金属软垫片
JB/T 4705 缠绕垫片
JB/T 4706 金属包垫片
JB/T 4707 等长双头螺柱
5.2.4管材下料的一般规定
5.2.4.1管子下料可采用管子切断机、带锯、弓锯、圆盘锯或砂轮切割机等设备进行。
5.2.4.2薄壁管下料(如空气预热器用管)可用切断模在切断机上切断下料,但在切断模前后需加两套校正装置,以防管子切口有凹痕。
5.2.4.3在切断机上下料时,应使内切刀的刀尖比外切刀的刀尖在接触管子外壁时短0.3mm~0.5mm,并进行试切。在切断长度小于60mm的管接头时,应用接棒穿入被切断管子的一端,以接持管接头。
5.3气割下料
5.3.1一般要求
5.3.1.1被切材料表面应平整、光洁,表面无凹凸不平或严重油污、锈蚀。
5.3.1.2为减少气割后工件变形和利于气割时排渣,气割前工件应垫平并选放好支点,且工件下面留有一定高度的空间。
5.3.1.3切割工件时,应选择在余料较大部分处结束切割,防止工件受热变形而使工件移动,影响工件尺寸。在切割细长工件时,应采用断续切割或双边同时切割工艺。
压力容器制造通用工艺守则
下料
TYR1102-2012
1 范围
本守则规定了D级第一、二类类压力容器制造过程中钢材划线、下料及矫正等工艺的技术要求。
本守则适用于制造压力容器用板材、型材和管材的划线、下料及矫正。
2 规范性引用文件
下列文件中的条款通过本守则的引用而成为本守则的条款。凡是注日期的引用文件,其随后所有的修改单(不包括勘误的内容)或修订版均不适用于本守则,然而,鼓励根据本守则达成协议的各方研究是否可使用这些文件的最新版本。凡是不注日期的引用文件,其最新版本适用于本守则。
5.2.2.4剪切批量较大时,应尽量采用后挡料装置,并检查后挡板与剪床下刀刃之间的平行度,其平行度在1000mm测量长度上不应大于0.5mm。
5.2.2.5剪切最后剩下的料头,应保证剪床的压板能压牢。
5.2.2.6振动剪切时,应调整好刀刃间隙,通常为待剪板厚的四分之一。在刃口两侧可安装托架或夹具。
5.2.2.7振动剪剪切时,剪切直径较大的圆板可采用定心装置,工件作旋转运动。剪切内孔前,需将上、下刀刃分开,工件放入后再对合上下刀刃;剪切时,应先剪出一个缺口再沿线剪切。
4.2操作人员应看懂、看清产品图样、工艺文件和有关资料,了解相应的工艺要求。如有疑问向有关人员反映,待消除疑问后方可进行加工。
4.3按工件或产品图样、工艺文件等复核需加工的原材料、工件毛坯或半成品是否符合有关要求,发现问题应及时向有关人员反映,待问题解决后方可进行加工。
4.4按工艺文件要求,准备好加工所需的全部工艺装备,发现问题应及时处理;对初次使用的夹具、模具等,应先熟悉其使用要求和操作方法。
6.9焊接接头表面质量检查细则的操作按TYR11010-2012的有关要求进行。
6.10耐压试验和泄漏试验的操作按TYR1111-2012的有关要求进行。
6.11承压设备产品试件力学性能试验的操作按TYR1112-2012的有关规定进行。
6.12不锈钢压力容器的加工和组装的操作按TYR1113-2012的有关规定进行。
5.3.1.4气割板厚不大于8mm的薄板时,应对钢板进行有效的夹持,以防止钢板在切割受热时变形而产生位移,从而影响切割质量。
5.3.1.5数控切割下料(包括喷粉划线)前应根据工件图样采用相应的排版软件进行排版或编制气割控制程序并输入数控切割机。
5.3.1.6数控切割下料时应对首件进行检验,合格后方可进行批量切割下料。
3.2操作前,操作人员应准备好作业必备的工具、量具,并仔细检查、调试所用的设备、仪表、量检具、模具、刀具,使其处于良好状态。使用的仪表、量具、检具应在有效检定期内。
3.3操作人员应按有关文件的规定,认真做好现场管理工作。对工件和工具应备有相应的工位器具,整齐地放置在指定地点,防止碰损、锈蚀。
3.4需要有材质钢印(或标记)的钢材,下料前(数控切割可在下料后)操作人员参照JB/T 4308的规定在坯料和余料上进行钢印(或标记)移植。有耐腐蚀要求的不锈钢,不得在耐腐蚀面采用硬印标记。记号标记用油彩色(非碳素)。移植后的材质钢印(或标记)需经检验人员确认后方可流入下道工序,需要标记移植而无标记移植的材料不应流入下道工序。
5.2.3型材下料的一般规定
5.2.3.1锯切下料前,要根据材料选好锯带、锯条或锯片并在相应锯床上精心调试后进行下料;亦可采用联合冲剪机、压力机或冲床下料。
5.2.3.2锯切下料前,坯料装夹时,其轴线方向应与弓架锯切平面垂直,其长度超过锯床台面宽度时,应用料架支撑。
5.2.3.3锯切不锈钢等韧性大、强度高的材料时,应采用乳化液、硫化油等润滑剂进行润滑散热。
6.4压力容器机械加工的操作按TYR1105-2012的有关要求进行。
6.5压力容器焊接时的操作按TYR1106-2012的有关要求进行。
6.6碳弧气刨的操作按TYR1107-2012的有关要求进行。
6.7受压元(部)件焊后热处理的操作按TYR1108-2012的有关要求进行。
6.8焊接接头返修的操作按TYR1109-2012的有关要求进行。
5.2.2.2剪切下料时,剪刀应锋利,剪切间隙(刀刃间隙)按表1的规定进行调整。
表1单位为毫米
钢板厚度
4
6
8
10
12
14
16
剪切间隙
0.15
0.25
0.35
0.45
0.55
0.65
0.75
5.2.2.3不允许重叠剪切或冲剪,剪切较大钢板时,应有相应的辅助设备将钢板吊起或托起,且托持高度略低于下剪口。
4.4.1钢材坯料划线的尺寸偏差值应不大于尺寸公差值的三分之一;如果下料后为方形或矩形板料时,则划线时对角线长度偏差应不大于图样规定的对角线长度偏差的三分之一。
4.4.2筒体、封头等重要工件的划线应进行100%检验。其它工件则应做好首检、抽检工作,抽检的数量可根据工件的情况由制造厂自行决定。
5 下料
压力容器制造通用工艺守则
总 则
TYR1101-2012
1 范 围
本守则规定了压力容器产品加工制造过程中主要专业工种应遵守的基本操作规则。
本守则适用于D级第一、二类压力容器的零部件或产品的加工。
2 规范性引用文件
下列文件对于本文件的应用是必不可少的。凡是注日期的引用文件,仅注日期的版本适用于本文件。凡是不注日期的引用文件,其最新版本(所括所有的修改单)适用于本文件。
7.2凡经检验合格的原材料、半成品、成品均应挂(或贴)合格标记,需做标记移值或打焊工钢印的均应按要求进行。
7.3加工过程及加工后所涉及的原材料、半成品、成品应按定置管理要求摆放在规定的位置或区域内。
7.4加工完毕,所用设备及工艺装备应按企业相关管理制度进行处理。
7.5产品图样、工艺文件及所用的其它技术资料,应注意保持整洁、妥善保管、严禁涂改。
GB150-2011 压力容器
GB/T 196 普通螺纹 基本尺寸
GB/T 197 普通螺纹 公差
GB/T 228 金属材料 室温拉伸试验方法
GB/T 229 夏比摆锤冲击试验方法
GB/T 232 金属材料 弯曲试验方法
GB/T 1804 一般公差 未注公差的线性和角度尺寸的公差
GB/,应按照工件从小到大的顺序依次进行切割。
4 划线
4.1一般规定
4.1.1钢材存在影响划线的弯曲、凹凸不平时,应先进行矫正。
4.1.2划线前,钢材表面应清理干净,去除锈蚀、油污等,如发现钢材有裂纹、严重锈蚀等缺陷,应经检验部门作出处理后,方可划线。
4.1.3自行制作的划线样板、样杆,应经检验部门认可。
4.2技术要求
4.2.1对于断面不规则的板材、型材及管材,应在规则部分进行划线,并注意个别工件对材料轧制纹络的要求。需要剪切的工件,在划线时应考虑剪切线是否合理和便于操作。