Hannstar-HG171D-英文维修手册
三星1710打印机维修手册

故障排除
故障排除
7.1 图像损坏
7.1.1 竖直黑条和黑带
y 说明
1 打印时出现竖直细黑线 2 打印时出现竖直黑带
检查和原因
解决办法
1 显影器中的显影辊损坏或刮墨刀 1 如果显影器盒中出现原因 1 和原
或清理刀变形
因 2 应更换显影器并试一试打
印
2 显影器中出纸辊表面划伤
2 如果出现原因 3 应更换转印辊
7.1.10 重影 2
y 说明
在整个打印过程中 以 OPC 鼓的 75.5 mm 间隔出现重影 使用手动进纸器 在卡片或透明胶片上打印
检查和原因 当打印比普通纸厚的卡片或投影片等 透明胶片时 需要较高的转印电压
解决办法 从软件应用程序在纸张类型菜单上选 择 厚纸模式 建议使用后返回初 始模式
三星电子
解决办法 1 执行 OPC 鼓清理模式打印 2 或
3 次 执行自检 清除转印辊的 污物
2 如果污染严重 应更换转印辊
3 拆卸定影单元 并清理加热辊和 压力辊 检查加热辊和热敏电阻 之间的区域 如果有污染 应清 理该区域 不可弄变形
7.1.15 打印空白页 1
y 说明
打印空白页
检查和原因 OPC 和 或 显影器接地不良
维修手册 7-4
三星电子
故障排除
7.1.9 重影 1
y 说明
在整个打印过程中 以 OPC 鼓的 75.5 mm 间隔出现重影
检查和原因
解决办法
1 墨粉微粒造成污染 引起主机体 1 当 墨粉微 粒污染 时 应 清理 端
的高电压端子和显影器电极接触
子
不良
2 墨粉微粒造成污染 引起主机体 2 如在显影器盒中发生 应更换显
Parker Hannifin NX系列恒温拓展阀说明书
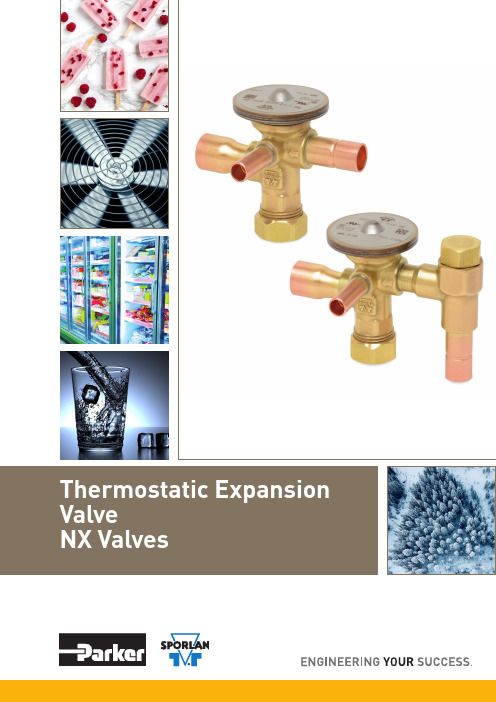
▲WARNING - USER RESPONSIBILITYFailure or improper selection or improper use of the products described herein or related items can cause death, personal injury and property damage.This document and other information from Parker Hannifin Corporation, its subsidiaries and authorized distributors provide product or system options for further investigation by users having technical expertise.The user, through its own analysis and testing, is solely responsible for making the final selection of the system and components and assuring that all performance, endurance, maintenance, safety and warning requirements of the application are met. The user must analyze all aspects of the application, follow applicable industry standards, and follow the information concerning the product in the current product catalog and in any other materials provided from Parker or its subsidiaries or authorized distributors.To the extent that Parker or its subsidiaries or authorized distributors provide component or system options based upon data or specifications provided by the user, the user is responsible for determining that such data and specifications are suitable and sufficient for all applications and reasonably foreseeable uses of the components or systems.For safety information see the Safety Guide at /safetyOFFER OF SALEPlease, contact your Paker representation for a detailed "Offer of Sale"FOR USE ON REFRIGERATION and/or AIR CONDITIONING SYSTEMS ONLYType NX Valves THERMOSTATIC EXPANSION VALVEType NXEType SNXE Sporlan built the Type NX valve with a stainless steel capillary tube laser welded to the sensing bulb and element housing to withstand the repeated bending during installation and improve endurance to vibrations while in service. The forged brass NX valve body is available with a straight-through flow configuration and ODF (sweat) copper connections. The valve can be supplied with either an internal or external equalizer and features a field adjustable superheat stem. Valves with fittings in metric sizes are available upon special request. Sporlan constructed the NX valve with a single, balance-ported pushrod which is specifically designed to help flush out any solid debris build-up. The bleed port feature allows the system refrigerant to bypass the pin and port. System designers can utilize this feature to alter system p erformance f or a v ariety o f r easons. B leed port options are available upon special request. SpecificationsThe Type NX valves offer a wide range of type W thermostatic charges with or without the MOP feature. You can use the thermostatic charges with the MOP (maximum operating pressure) feature to help protect the compressor from overloading at startup or under high load conditions. S ee the MOP temperature in the table below.The small and compact design of S porlan’s Type NX Thermostatic Expansion Valves makes this product ideal for foodservice and food retail applications such as display cases, ice machines, frozen drink dispensers and commercial kitchen refrigerators and freezers. The Type NX valves feature a laser-welded stainless steel element, capillary tube, and sensing bulb assembly optimized for reliability and long life. The single pushrod balanced port design ensures precise pin and port alignment, enabling the valve to maintain superior superheat control at all load conditions. Features and Benefits• Long-lasting and durable stainless steeldiaphragm and weld design• Single pushrod balanced port construction• Suitable for all common refrigerants includingR-290• Internal or external equalizer• Easily adjustable superheat setting• High strength silver soldered joints with solid copper connections.The design ensures enabling the valve to main-tain a superior superheat control from 15% to 100% load conditions therefore fully compat-ible to work with inverter driven compressors.MOP Temperature TableS tandard static superheat settings vary based on the system refrigerant selected, but the valves are set to approximately 4K static superheat based on the newer refrigerants such as R448A, etc. S pecial settings are available upon special request. The seal cap utilizes a mechanical knife-edge seal. The torque required for proper sealing is 10,8 to 14,9 Nm. S porlan offers 2 optional inlet strainers for use with NX valves; an insert strainer and an integral strainer. The insert type strainer is placed into the inlet fitting prior to brazing and can only be serviced by disconnecting the liquid line.Valve ModelsNXInternallyEqualizedNXEExternallyEqualizedValves, its item number completely defines thetype NX valve. The standard NX item number has 7 positions; however, item numbers can be up to 14 positions in length. Positions 8-14 are reserved for special OEM configurations.Refer to the following example of a standard NX item number and the position descriptions when ordering.Nomenclature and Item Numbering SystemLike other Sporlan Thermostatic Expansion Valves, the Type NX valves follow the nomenclature example and ordering instructions below.Item NumberPosition DescriptionsItem Number and PositionsPackagingAll valves are packaged in clear plastic bags for protection.Standard NX valves are individually boxed with a bulb strap kit and are packed 24 pieces per case. Egg crate style production packaging is available upon special request and valves come packed 36 pieces per case.AccessoriesIdentification and Markings Several valve identifications are laser marked onthe element, as shown. The 5 digit date code indicates the day and year. The first 3 digits repre-sent the day of the year. The last 2 digits are the year. The PTS Number is a Parker Sporlan serial number. Additional markings are on the forged brass body, including a flow direction arrow and the Sporlan trademark.DescriptionRefrigerantCompatibility Parker SporlanItem NumberDate CodePTS Number2D DataMatrix ElementThermostatic expansion valve capacity ratings are based on vapor free 38°C (100°F) liquid refrigerant entering the expansion valve; a maximum open-ing superheat of 7K (4°F); and a standard fac-tory air test superheat setting. A discussion of the relationship between valve capacity and super-heat setting (along with other important applica-tion information) can be found in Bulletin 10-9. The valves are tested in accordance with ANSI/ ASHRAE 17. The ratings in the capacity tables are in accordance with ANSI/AHRI Standard 750. It is possible to correct for both liquid temperature and pressure drop using the factors in the tables following the capacity tables. The liquid temperature correction factors are refrigerant dependent, and tables are pro-vided for each refrigerant. The pressure drop correc-tion factor is affected by the valve and is indepen-dent of the refrigerant. The correction calculation is shown below, followed by an example calculation.TEV Capacity = TEV Rating x CF Liquid Temperature x CF Pressure DropExample Calculation: The actual capacity of a Type NX valve with a C38 capacity code on R448A at 20°F evaporator temperature, 100 psi pressure drop across the TEV, and 90°F liquid temperature entering the TEV is:Actual Capacity = 2.07 (from rating chart) x 1.08 (CF liquid temperature) x 0.89 (CF pressure drop) = 1.99 tonskW ■ bar ■ °CkW ■ bar ■ °CkW ■ bar ■ °CCapacity Ratings and SelectionLiquid Temperature kW ■ bar ■ °CDimensions - Inches (mm)Type NX(E)Front ViewTop ViewExternal 1/4” ODF Equalizer FittingNotesParker Hannifin RACE Instrumentation GroupRefrigeration and Air Conditioning Europe Via Enrico Fermi,520060 Gessate - Milano - ItalyTel. +39 (0) 2 95125.1 - /raceEU.RE1.C.9T2.NX.EN.1.2021.04© 2021 Parker Hannifin Corporation. All rights reserved.Parker WorldwideUnited Arab Emirates Middle EastSarkis OHANNESSIAN Tel +961 3334622***********************Germany, Austria and German speaking part of Switzerland Francesco GALANTE Tel +49 (0)175 5756 032****************************Spain and Portugal Alberto PEÑATel +34 609 153 154***********************France, Belgium,French speaking part of Switzerland Goska WARNECKTel + 33 (0)6 73 89 36 08*******************Italy, Greece, Malta, Cyprus Italian speaking part of Switzerland Andrea BRAGATel +39 334 6944386 *****************Baltic Countries,Eastern and Central Europe, AfricaEliane EMERIT-BONNOT Tel +33 (0)6 73 89 36 01 ******************Turkey************************UK andNorthern Europe Kenny ADAMSON Tel +44 77853 71229*******************Customer Service: Parker Hannifin Ltd Instrumentation Group Refrigeration andAir Conditioning Europe Manvers House Office 21Pioneer CloseWath Upon Dearne Rotherham S63 7JZ United KingdomTel +44 (0) 1709 774600 Fax +44 (0) 1709 774601******************************/raceYour local authorized Parker distributor。
Onan Elite Generator维修引导书说明书
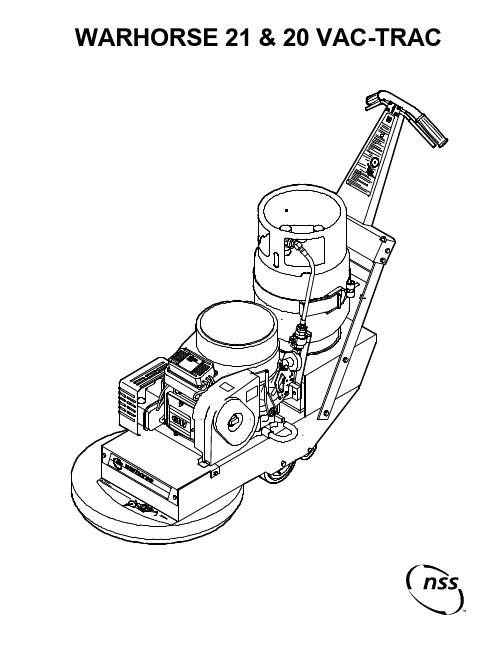
WARHORSE 21 & 20 VAC-TRACELITE WIRING DIAGRAM124 ELITE SERVICE PARTSNSS NO.ONAN NO.DESCRIPTION6590021308-385KEY SWITCH ONAN6593191515-0295KEY6591661155-2378GASKET6591741338-3646HARNESS - POWER SUPPLY6591801110-3591GASKET - CYLINDER6591811102-1462GASKET - CARBURETOR6591821123-1836BREATHER6591831541-0563-11OIL CAP KIT6591841123-2043TUBE - BREATHER6591851150-2548SPRING - GOVERNOR6591861110-3579VALVE - EXHAUST6591871110-3578VALVE - INTAKE6591931965-0764MANUAL - ELITE SERVICE6591941965-0174MANUAL - ELITE OPERATION6591951965-0200MANUAL - ELITE PARTS6592041965-0174-GR ONAN ELITE OPERATOR MANUAL - GERMAN 6592051965-0174-FR ONAN ELITE OPERATOR MANUAL - FRENCH 6592301502-0269SEAL - TUBE6592311123-1915-50TUBE - OIL FILL6592321155-3080-02BRACKET - MUFFLER GUARD6592351166-0832MAGNETO6593541541-0563-06OIL CAP KIT6592371357-0030RECTIFIER - SILICON6592381321-0162FUSE - 30 AMP6592951509-0289SEAL - INTAKE VALVE6593011152-0330LINK - THROTTLE6593021150-2338LEVER - GOVERNOR6593031152-0343CLIP - LINK6593041153-0650LINK - CHOKE6593051153-0621SPRING - CHOKE LINKAGE6593061821-2033M6 X 14mm. BOLT6593071815-0474HEX WASHER HEAD SCREW6593081503-1445-04CLAMP - HOSE6593091122-0770ADAPTOR - OIL FILTER6593101509-0142“O” RING6593111509-0304“O” RING65931210226-4815LEAD - RESISTOR6593131168-0220COMPLETE ENGINE GASKET SET6593141509-0330SEAL EXHAUST VALVE6593151503-2097M.A.P. HOSE (MANIFOLD ABSOLUTE PRESSURE) 6593161105-0693-02CAM SHAFT ASSEMBLY6593171115-0423TAPPET6593181541-0508KIT - GOVERNORONAN PROPANE ENGINE 124 ELITEITEM PART NO.ONAN NO.DESCRIPTION QTY. 1016590181FEMALE QUICK COUPLING1 10265913211/4 90 DEGREE STREET ELBOW - STEEL1 1036591091PROPANE - FUEL HOSE1 1046591751338-3651HARNESS - ENGINE1 1056591521122-0737FILTER - OIL1 659178170725-15OIL FILTER WRENCH1 1066591731309-0646-06SWITCH - OIL PRESSURE1 1076591711191-1906STARTER - 12 VOLT1 1086591571140-2825-01FILTER - PRECLEANER1 1096591011ONAN PROPANE ENGINE 124 1 1106591651148-1077CONTROL UNIT - LPG1 1116591721191-2207REGULATOR - VOLTAGE1 1126590791LABEL - “CAUTION SURFACES MAY BE HOT”1 1136591681155-3005-02GUARD - MUFFLER1 1146591771155-2429-01SPARK ARRESTOR1 1156591671155-3002MUFFLER - CATALYTIC1 1166590671LABEL SET - “CLEAN AIR FILTER”1 1176591701167-0263-02SPARK PLUG1 1186591691167-1621CAP - SPARK PLUG1 1196591641148-1076SENSOR - OXYGEN1 1206591551140-2676COVER - AIR CLEANER1 121912129010 mm. - 1.5 X 30 mm. FULL THREAD HEX HEAD BOLT - STEEL1 122912130010 mm. SPLIT LOCK WASHER1 12391221103/8 X 1 1/2 FENDER WASHER1 1246591031CENTRIFUGAL CLUTCH - SINGLE GROOVE1 12591213151/4 SQUARE X 1 1/2 LONG KEY1 1266591101COLLAR - ENGINE SHAFT1 1276590991140-2761KNOB - AIR CLEANER COVER 1/4-201 1286591761504-0186VALVE - OIL DRAIN1 1296591531140-2674-01COVER - ELEMENT1 1306591541140-2675KNOB - INNER COVER1 1316591561140-2748-01WRAPPER - ELEMENT1 1326591581140-3010ELEMENT - AIR CLEANER1 133********/16-18 X 5/8 HEX BOLT1 134********/16 SPLIT LOCK WASHER1 135912139011/32 I.D. X 11/16 O.D. X .051/.080 THICK SAE FLAT WASHER (5/16)1 1362395761CLAMP - TUBE1 137********/8-16 HEX NUT WITH NY-LOK INSERT1 1386591601148-1072SOLENOID - DUTY1 1396591631148-1075HOSE - FUEL1 1406591611148-1073REGULATOR - VAPOR1 1416591621148-1074FUEL SHUTDOWN SOLENOID WITH FILTER1 6591591148-1071SYSTEM ASSEMBLY - FUEL1 14291209309/32 I.D. X 5/8 O.D. X .051/.080 THICK SAE FLAT WASHER (1/4)1 14391212701/4-20 X 1 HEX BOLT1 144912218013/32 I.D. X 13/16 O.D. X .051/.080 THICK WROUGHT WASHER (3/8)1 14591223013/8-16 X 1 1/4 HEX BOLT1 1466591121BRACKET - FUEL SYSTEM1 14791209101/4-20 HEX NUT WITH STAR LOCK WASHER1 14891209309/32 I.D. X 5/8 O.D. X .051/.080 THICK SAE FLAT WASHER1 1496591181CLAMP - FUEL SYSTEM1 150********/4-20 X 1/2 HEX BOLT1 151********/4-20 HEX NUT WITH STAR LOCK WASHER1 152659017145 DEGREE STREET ELBOW 1/41ONAN PROPANE ENGINE 124 ELITEDECK ASSEMBLYITEM PART NO DESCRIPTION QTY. 2016592779BATTERY - 12 VOLT - INCLUDES:1 6592771BATTERY - 12 VOLT16592763BATTERY CLAMP - SHORT1 2026590041CABLE - POSITIVE BATTERY1 2036590071GASKET - BATTERY1 2046590081GASKET - PROPANE TANK1 2056590671LABEL SET - “CHECK OIL LEVEL”1 2062397361HOUR METER1 2076591141POSITIVE LEAD - HOUR METER1 6590451NEGATIVE LEAD - HOUR METER1 2086590391TANK LOCATOR - WARHORSE 20 ONLY1 20991208801/4 SPLIT LOCK WASHER - WARHORSE 20 ONLY2 21091212101/4-20 X 5/8 HEX BOLT - WARHORSE 20 ONLY2 2116592573DECK1 2126591163FRONT COVER1 2136590671LABEL SET - “MACHINE NAME AND LOGO”1 21491211701/4-20 X 1/2 HEX BOLT4 21591208801/4 SPLIT LOCK WASHER4 21691209309/32 I.D. X 5/8 O.D. X .051/.080 THICK SAE FLAT WASHER (1/4)4 2176591051AXLE - 6" MAIN WHEEL1 2185293151RETAINING RING2 21991231053/4 I.D. X 1 1/4 O.D. X .071 THICK WASHER2 22091231103/16 I.D. X 1 1/8 O.D. X .13 THICK 1 WAVE SPRING WASHER - WARHORSE 202 22165911116” X 1 1/2” WHEEL2 6591211DELRIN BEARING FOR 6” WHEEL - TWO REQUIRED PER WHEEL2 22249910913/4 I.D. X 1 1/2 O.D. X .031 THICK FLAT WASHER - PLASTIC4 2236591066AXLE - DOLLY WHEEL1 22427902813" BUMPER WHEEL2 2259122465.615 I.D. X .813 O.D. X .027/.030 THICK FLAT WASHER4 22691219807/16 I.D. X 1 O.D. X .075/.080 THICK SAE FLAT WASHER (3/8)2 22791221003/8 SPLIT LOCK WASHER2 22891222603/8-16 X 1 HEX BOLT2 22991215605/16-18 X 1/2 HEX BOLT2 23091215205/16 SPLIT LOCK WASHER2 231912139011/32 I.D. X 11/16 O.D. X .051/.080 THICK SAE FLAT WASHER (5/16)2 23291212501/4-20 X 3/4 HEX BOLT2 23391208801/4 SPLIT LOCK WASHER2 2344894461RUBBER STOP2 2356591241LABEL - “UL LISTED”1 23691216805/16-18 X 1 HEX BOLT4 23791215205/16 SPLIT LOCK WASHER4 238912139011/32 I.D. X 11/16 O.D. X .051/.080 THICK SAE FLAT WASHER (5/16)4 2396590531BELT ADJUSTMENT BRACKET1 24091223503/8-16 X 3 HEX BOLT1 24191219807/16 I.D. X 1 O.D. X .075/.080 THICK SAE FLAT WASHER (3/8)1 24291212101/4-20 X 5/8 HEX BOLT2 24391208801/4 SPLIT LOCK WASHER2 2446590051CABLE - NEGATIVE BATTERY1DECK ASSEMBLYHANDLE ASSEMBLYITEM PART NO.DESCRIPTION QTY. 3016590351THROTTLE LEVER GRIP2 302912045010-24 X 1 ROUND HEAD PHILLIPS MACHINE SCREW1 303912036010-24 HEX NUT WITH STAR LOCK WASHER1 3044490641EXTENSION SPRING1 305912078310-38 NYLON SCREW INSULATOR1 306912035010-24 HEX NUT WITH NY-LOK INSERT1 307912051010-24 X 1/2 TRUSS HEAD PHILLIPS MACHINE SCREW1 3086590461LIGHT1 30991224709/16 I.D. X 1 3/8 O.D. X .086/.132 THICK WROUGHT WASHER (1/2)1 3106590021KEY SWITCH - INCLUDES:1 3116593191KEY ONLY1 3126590671LABEL KIT - “PROPANE TANK FILL AND STORAGE”1 3136590101PROPANE FUEL TANK1 31499970501/2" SHRINK TUBE6" 3159997100 1 1/2" SHRINK TUBE4" 31691214003/8 I.D. X 7/8 O.D. X .064/.104 THICK WROUGHT WASHER (5/16)1 31791214505/16-18 HEX NUT WITH NY-LOK INSERT4 318912032010 SPLIT LOCK WASHER1 3196590081GASKET - PROPANE TANK1 32091230153/16 X 7 1/2 LONG #10 MOUNTING HOLE WIRE TIE1 321912041010-24 X 1/2 ROUND HEAD PHILLIPS MACHINE SCREW1 3226590133HANDLE BASE1 3236590497VELCRO LOOP - 34"1 3246590111CLAMP - TANK1 3256590671LABEL KIT - “CALL FOR SERVICE”1 3266592563DECK1 3276592801VAC TRAC DUST COLLECTION BAG - WARHORSE 20 ONLY1 3286591343SINGLE HOSE BRACKET - WARHORSE 20 ONLY1 32991215105/16 SPLIT LOCK WASHER4 33091216005/16-18 X 5/8 HEX BOLT4 33191209001/4-20 HEX NUT WITH NY-LOK INSERT - WARHORSE 20 ONLY4 33291209309/32 I.D. X 5/8 O.D. X .051/.080 THICK SAE FLAT WASHER (1/4) - WARHORSE 20 ONLY4 3336591881CLAMP - DOUBLE HOSE BRACKET - WARHORSE 20 ONLY2 3344894071CLAMP - .437 DIAMETER CABLE - HEYCO1 33591203707/32 I.D. X 1/2 O.D. X .032/.065 THICK SAE FLAT WASHER (#10)1 336912032010 SPLIT LOCK WASHER1 337912050010-24 X 3/8 TRUSS HEAD PHILLIPS MACHINE SCREW1 3386592883DOUBLE HOSE BRACKET - WARHORSE 20 ONLY1 33991212501/4-20 X 3/4 HEX BOLT WITH NYLON PATCH - WARHORSE 20 ONLY4 34025903912” HOSE CUFF - WARHORSE 20 ONLY1 34165919712” DIAMETER HOSE - 54” LONG - WARHORSE 20 ONLY1 3426590541POSITIVE LEAD - LIGHT1 3436590551NEGATIVE LEAD - LIGHT1 34491216805/16-18 X 1 HEX BOLT4 34591214003/8 I.D. X 7/8 O.D. X .064/.104 THICK WROUGHT WASHER (5/16)4 346912050010-24 X 3/8 TRUSS HEAD PHILLIPS MACHINE SCREW1 3476590671LABEL SET - “MACHINE OPERATION AND STARTING”1 3486590151CABLE - THROTTLE1 3496590361CABLE CLIP1 350912035010-24 HEX NUT WITH NY-LOK INSERT1 3516590411HANDLE GRIP2 3526590123HANDLE - UPPER1 3536591217GASKET - THROTTLE LEVER PLATE2 3546590163THROTTLE LEVER PLATE1 355912032010 SPLIT LOCK WASHER4 356912061510-24 X 3/8 SOCKET HEAD CAP SCREW4 3576590141THROTTLE LEVER1HANDLE ASSEMBLYSKIRT ASSEMBLYITEM PART NO.DESCRIPTION QTY. 4016592573DECK1 4026593009SINGLE GROOVE SHEAVE KIT - INCLUDES:1 6592981SINGLE GROOVE SHEAVE1 40391212511/4-20 X 3/4 HEX BOLT2 4046592961SPLIT TAPER BUSHING1 4056590521 1 I.D. X 1.5 O.D. X .13 THICK FLAT WASHER - STEEL - 10 GAGE2 4066590271BEARING - LOWER DRIVEN1 4076590671LABEL SET - “PAD APPLICATION”1 4082691241BEARING - PILLOW BLOCK1 409912218013/32 I.D. X 13/16 O.D. X .051/.080 THICK WROUGHT WASHER (3/8)2 41091221003/8 SPLIT LOCK WASHER2 41191223003/8-16 X 1 1/4 HEX BOLT2 41291208801/4 SPLIT LOCK WASHER8 41391211701/4-20 X 1/2 HEX BOLT8 4146592591SHAFT - DRIVEN - WARHORSE 20 ONLY1 6590281SHAFT - DRIVEN - WARHORSE 21 ONLY1 41565903211” EXTERNAL RETAINING RING1 41665919712” DIAMETER HOSE - 54” LONG - WARHORSE 20 ONLY1 4174495441HOSE CLAMP - 1 9/16 TO 2 1/2 DIAMETER - WARHORSE 20 ONLY1 41891209501/4 X 1 1/4 FENDER WASHER - WARHORSE 20 ONLY3 41991208801/4 SPLIT LOCK WASHER - WARHORSE 20 ONLY3 42091212101/4-20 X 5/8 HEX BOLT - WARHORSE 20 ONLY3 4216592608FLEXIBLE PAD DRIVER ASSEMBLY - WARHORSE 20 ONLY1 6591028FLEXIBLE PAD DRIVER ASSEMBLY - WARHORSE 21 ONLY1 42291224001/2 I.D. X 1 3/32 O.D. X .074/.121 THICK SAE FLAT WASHER (7/16)1 42391222603/8-16 X 1 HEX BOLT1 424912079010 X 5/8 PAN HEAD PHILLIPS SHEET METAL SCREW3 4255990721SPRING CLIP PAD HOLDER SET1 426----------PAD - SEE ACCESSORIES PAGE FOR DIFFERENT TYPES1 42791221003/8 SPLIT LOCK WASHER1 4286490729FLEXIWALL SHIELD ASSEMBLY - WARHORSE 20 ONLY1 4296490191BUMPER BRUSH - WARHORSE 20 ONLY1 4306490732BUMPER STRAP - WARHORSE 20 ONLY1 431912045010-24 X 1 ROUND HEAD PHILLIPS MACHINE SCREW - WARHORSE 20 ONLY1 432912035010-24 HEX NUT WITH NY-LOK INSERT - WARHORSE 20 ONLY1 4336590521 1 I.D. X 1.5 O.D. X .13 THICK FLAT WASHER - STEEL - 10 GAGE1 43491208253/16 SQUARE X 7/8 LONG KEY - STEEL1 43591213151/4 SQUARE X 1 1/2 LONG KEY - STEEL1 4366590407BUMPER - 6" - WARHORSE 21 ONLY1 43791203091/8 X 1/2 DOME HEAD POP RIVET - WARHORSE 21 ONLY6 4386591969SKIRT - WARHORSE 20 - INCLUDES:1 6591963SKIRT - WARHORSE 201 43991220753/8-16 X 1 1/2 HEX BOLT2 4406592911REINFORCEMENT RING1 44191221403/8-16 HEX NUT WITH NY-LOK INSERT2 4386591009SKIRT - WARHORSE 21 - INCLUDES:1 6591003SKIRT - WARHORSE 211 43991220753/8-16 X 1 1/2 HEX BOLT2 4406592911REINFORCEMENT RING1 44191221403/8-16 HEX NUT WITH NY-LOK INSERT2 4426590251TAPPING PLATE - UPPER BEARING1 443912218013/32 I.D. X 13/16 O.D. X .051/.080 THICK WROUGHT WASHER (3/8)2 444912129010 mm. - 1.5 X 30 mm. FULL THREAD HEX HEAD BOLT - STEEL1 445912130010 mm. SPLIT LOCK WASHER1 44691221103/8 X 1 1/2 FENDER WASHER1 4476591031CENTRIFUGAL CLUTCH - SINGLE GROOVE1 44891213151/4 SQUARE X 1 1/2 LONG KEY - STEEL1 4496591101COLLAR - MOTOR SHAFT1 4506591081BELT - DRIVE1SKIRT ASSEMBLYNSS ® Enterprises, Inc.3115 Frenchmens Road, Toledo, Ohio 43607PHONE (419) 531-2121 FAX (419) 531-3761NSS ® Enterprises, Inc. European Distribution CentreUnit II, Pinfold Trading Estate * 55 Nottingham RoadSTAPLEFORD, NOTTINGHAM NG9 8AD ENGLAND U.K.PHONE: (44) 0115 939 1568 * FAX: (44) 0115 949 0615WARHORSE 20 & 21 VAC-TRAC ORIG. 08-02 9096515ACCESSORIES6594019SETTING FIXTURE - 20” VAC TRAC6594219SETTING FIXTURE - 21”1093621BAG SNAP - VAC TRAC ONLY1099801HANGER RING ONLY - WITHOUT SNAP - VAC TRAC ONLY 5990601BIG MOUTH PAD HOLDER SET 5990611BIG MOUTH - MALE THREAD PORTION799275127” LITE BLUE SOFT FINISH PAD 799276127" LITE HAIR BURNISH PAD 799278127" ULTRA HAIR HARD FINISH PAD 799279127” ULTIMATE HAIR PAD6590801L.P. TANK STORAGE CAGE。
欧洲汽车和重型卡车液氢系统维修指南说明书
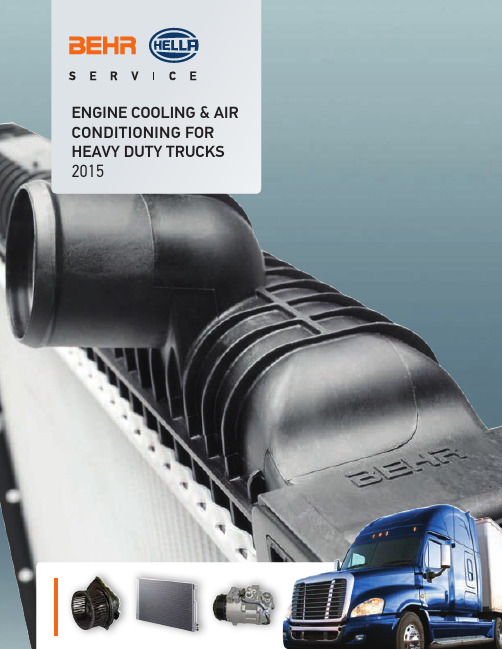
vehicles under extreme simulated conditions to see how well their
parts will perform. With more than 1000 quality parts available for
cooling and air conditioning products combined through one
source, Behr Hella Service. Both companies represent quality and
technical expertise in the automotive industry, so it’s only natural
This means, an ideal combination of products and service for your business. Hella’s Sales organization plus Behr’s extensive O E product knowledge form Behr Hella Service.
ENGINE COOLING & AIR CONDITIONING FOR HEAVY DUTY TRUCKS 2015
2014
Behr Hella Service -
Engine Cooling and Air Conditioning for Passenger Cars and Heavy Duty Trucks
684
915
51
Hannstar HG171A液晶显示器图纸

Model Name:HG171A Model No:HSG1033 17” Color TFT LCD DisplayCopyrightCopyright © 2006 by HannStar Corporation. All rights reserved. No part of this publication may be reproduced, transmitted, transcribed, stored in a retrieval system, or translated into anylanguage or computer language, in any form or by any means, electronic, mechanical, magnetic, optical, chemical, manual or otherwise, without the prior written permission of HannStar Corporation.DisclaimerHannStar makes no representations or warranties, either expressed or implied, with respect to the contents hereof and specifically disclaims any warranty of merchantability or fitness for any particular purpose. Further, HannStar reserves the right to revise this publication and to make changes from time to time in the contents hereof without obligation of HannStar to notify any person of such revision or changes.TrademarksOpt quest is a registered trademark of HannStar Corporation.HannStar is a registered trademark of HannStar Corporation.All other trademarks used within this document are the property of their respective owners.Revision HistoryRevision SM Editing Date ECR Number Description of Changes TPV Model A00 Sep.-10-08 First Version Release T7RHM5D8AWHZNCA01 Dec.-02-08 Add new BOM in item 16 T7RHM5DBAWZ3NNTABLE OF CONTENTS1. Dimensions 42. Precautions and Safety Notice 63.Monitor Specification 74.LCD Monitor Description 85.Operation Instruction 96. Input/output Specification 147. Mechanical Instructions 188. Block Diagram 219.Schematic 2710.PCB Layout 3541 11.Maintainability12 DDC Instruction 4713. White-Balance, Luminance adjustment 5314.Monitor Exploded View 5515. BOM List 5616.Different Parts List (65)1. Dimensions 1.1 Front View1.2 Back View1.3 Side View1.4 Bottom View2. Precautions and Safety NoticesProper service and repair is important to the safe, reliable operation of all AOC Company Equipment. The service procedures recommended by AOC and described in this service manual are effective methods of performing service operations. Some of these service operations require the use of tools specially designed for the purpose. The special tools should be used when and as recommended.It is important to note that this manual contains various CAUTIONS and NOTICES which should be carefully read in order to minimize the risk of personal injury to service personnel. The possibility exists that improper service methods may damage the equipment. It is also important to understand that these CAUTIONS and NOTICES ARE NOT EXHAUSTIVE. AOC could not possibly know, evaluate and advise the service trade of all conceivable ways in which service might be done or of the possible hazardous consequences of each way. Consequently, AOC has not undertaken any such broad evaluation. Accordingly, a servicer who uses a service procedure or tool which is not recommended by AOC must first satisfy himself thoroughly that neither his safety nor the safe operation of the equipment will be jeopardized by the service method selected.Hereafter throughout this manual, AOC Company will be referred to as AOC.WARNINGUse of substitute replacement parts, which do not have the same, specified safety characteristics may create shock, fire, or other hazards.Under no circumstances should the original design be modified or altered without written permission from AOC. AOC assumes no liability, express or implied, arising out of any unauthorized modification of design.Servicer assumes all liability.FOR PRODUCTS CONTAINING LASER:DANGER-Invisible laser radiation when open AVOID DIRECT EXPOSURE TO BEAM.CAUTION-Use of controls or adjustments or performance of procedures other than those specified herein may result in hazardous radiation exposure.CAUTION -The use of optical instruments with this product will increase eye hazard.TO ENSURE THE CONTINUED RELIABILITY OF THIS PRODUCT, USE ONLY ORIGINAL MANUFACTURER'S REPLACEMENT PARTS, WHICH ARE LISTED WITH THEIR PART NUMBERS IN THE PARTS LIST SECTION OF THIS SERVICE MANUAL.Take care during handling the LCD module with backlight unit.-Must mount the module using mounting holes arranged in four corners.-Do not press on the panel, edge of the frame strongly or electric shock as this will result in damage to the screen.-Do not scratch or press on the panel with any sharp objects, such as pencil or pen as this may result in damage to the panel.-Protect the module from the ESD as it may damage the electronic circuit (C-MOS).-Make certain that treatment person’s body is grounded through wristband.-Do not leave the module in high temperature and in areas of high humidity for a long time.-Avoid contact with water as it may a short circuit within the module.‐If the surface of panel becomes dirty, please wipe it off with a soft material. (Cleaning with a dirty or rough cloth may damage3. Monitor Specifications4. LCD Monitor DescriptionAssembly DescriptionThe LCD MONITOR will contain a main board, a power board, and a key board which house the flat panel control logic, brightness control logic and DDC.The power board will provide AC to DC Inverter voltage to drive the backlight of panel and the main board chips each voltage.5. Operating Instructions5.1 General InstructionsPress the power button to turn the monitor on or off. The control buttons are located in the front of the monitor.By changing these settings, the picture can be adjusted to your personal preferences.-The power cord should be connected.-Connect the video cable from the monitor to the video card.-Press the power button to turn on the monitor, the power indicator will light up.5.2 Control ButtonsFRONT PANEL CONTROL• Power Button:Press this button to switch ON/OFF of monitor’s power.• Power Indicator:Green — Power On mode.Orange — Power Saving mode.• MENU / ENTER:1. Turn the OSD menu on/off or return to the previous menu2. Exit OSD menu when in volume OSD status.• Adjust < >:1. Activates the volume control when the OSD is OFF.2. Navigate through adjustment icons when OSD is ON or adjust a function when function is activated.• A Button:• The OSD menu is used as ¡§confirmation¡¨ function during start-up. 2. Press and hold this button more than 3 seconds will start 「Auto Adjust」function when using VGA input only. (The auto adjustment function is used to optimize the 「horizontal position」, 「vertical position」,「clock」,and 「phase」.)NOTES:• Do not install the monitor in a location near heat sources such as radiators or air dusts, or in a place subject to direct sunlight, or excessive dust or mechanical vibration or shock.• Save the original shipping box and packing materials, as they will come in handy if you ever have to ship your monitor. • For maximum protection, repackage your monitor as it was originally packed at the factory.• To keep the monitor looking new, periodically clean it with a soft cloth. Stubborn stains may be removed with a cloth lightly dampened with a mild detergent solution. Never use strong solvents such as thinner, benzene, or abrasive cleaners, since these will damage the cabinet. As a safety precaution, always unplug the monitor before cleaning it. • Function Key Lock:Press the 「<」, 「>」 and the 「Menu」buttons simultaneously to enable the Function Key Lock. When the Function Key Lock is enabled, only the Power button is active. Press the 「<, 「>」 and the 「Menu」buttons simultaneously again to unlock the function keys.08/09/09 5.3 Adjusting the Picture08/09/0908/09/096. Input/output Specification 6.1 Input Signal Connector6.2 Factory Preset Display Modes6.3 Panel SpecificationHannStar Display model HSD170MGW1-B00 is a color active matrix thin film transistor(TFT) liquid crystal display (LCD) that uses amorphous silicon TFT as a switching device. This model is composed of a TFT LCD panel, a driving circuit and a back light system. This TFT LCD has a 17.0 inch diagonally measured active display area withXGA resolution (900 vertical by 1440 horizontal pixel array) and can display up to 16.2M (6-bit+FRC)colors.6.3.1 Features_ 17.0 WXGA+ for Monitor application_ High Resolution: 1440*900_ 2-ch LVDS interface system_ LCD Timing Controller_ Wide Viewing Angle_ RoHS compliance6.3.2 Display Characteristics6.3.3 Electrical Characteristics1. TFT LCD Module2. Backlight Unit6.3.4 Optical CharacteristicsMeasuring Condition_ Measuring surrounding: dark room_ Lamp current IBL: 7.5±0.1mA, lamp freq. FL=50 KHz, Inverter: TDK TBD315NR-1 _ VDD=5.0V, fV=60Hz_ Ambient temperature: 25±2oC_ 30min. Warm-up time.7. Mechanical Instructions08/09/0908/09/091) MCU initialize.2) Is the EPROM blank?3) Program the EPROM by default values.4) Get the PWM value of brightness from EPROM.5) Is the power key pressed?6) Clear all global flags.7) Are the AUTO and SELECT keys pressed?8) Enter factory mode.9) Save the power key status into EPROM.Turn on the LED and set it to green color.Scalar initializes.10) In standby mode?11) Update the lifetime of back light.12) Check the analog port, are there any signals coming?13) Does the scalar send out an interrupt request?14) Wake up the scalar.15) Are there any signals coming from analog port?16) Display "No connection Check Signal Cable" message. And go into standby mode after the message disappear.17) Program the scalar to be able to show the coming mode.18) Process the OSD display.19) Read the keyboard. Is the power key pressed?8.2 Electrical Block Diagram 8.2.1 Main Board8.2.2 Power/Inverter Board8.3 Mechanical Block Diagram 8.3.1 Assembly Block8.3.1 Disassembly Block08/09/09 9. Schematic9.1 Main BoardTSUM16FWR SCHEMATICXGA/SXGA LVDS OUTPUT08/09/095555555HG171A F B 47Monday , July 21, 2008715G2904-1D <称爹>02.InputG2904-1D-2-X -4-080728OEM MODEL Size Rev DateSheetofTPV MODEL PCB NAME 称爹T P V ( Top Victory Electronics Co . , Ltd. )Key Component絬 隔 瓜 絪 腹5555HG171A F B 77Monday , July 21, 2008715G2904-1D <称爹>05.PowerG2904-1D-2-X -4-080728OEM MODEL Size Rev DateSheetofTPV MODEL PCB NAME 称爹T P V ( Top Victory Electronics Co . , Ltd. )Key Component絬 隔 瓜 絪 腹4, 508/09/095HG171A F A 67Monday , July 21, 2008715G2904-1D <称爹>04.OutputG2904-1D-2-X-4-080728OEM MODEL Size Rev DateSheetofTPV MODEL PCB NAME 称爹T P V ( Top Victory Electronics Co . , Ltd. )Key Component絬 隔 瓜 絪 腹5PPWR_ON#508/09/09 9.2 Power Board08/09/0908/09/0908/09/09 10. PCB Layout10.1 Main Board08/09/0908/09/0908/09/0910.2 Power Board08/09/0908/09/09 10.3 key board11. Maintainability11.1 Equipments and Tools Requirement1. Voltmeter.2. Oscilloscope.3. Pattern Generator.4. DDC Tool with Compatible Computer.5. Alignment Tool.6. LCD Color Analyzer.7. Service Manual.8. User Manual.11.2 Trouble Shooting11.2.1 Main BoardNo powerNo picture (LED orange)08/09/09 White screen08/09/09 11.2.2 Power Board1) No power08/09/09 2.) No Backlight11.2.3 Key Board12. DDC InstructionGeneralDDC Data Re-programmingIn case the main EEPROM with Software DDC which store all factory settings were replaced because a defect, repaired monitor’ the serial numbers have to be re-programmed.It is advised to re- soldered the main EEPROM with Software DDC from the old board onto the new board if circuit board have been replaced, in this case the DDC data does not need to be re-programmed.Additional information about DDC (Display Data Channel) may be obtained from Video Electronics Standards Association (VESA). Extended Display Identification Data (EDID) information may be also obtained from VESA. 1. An i486 (or above) personal computer or compatible. 2. Microsoft operation system Windows 95/98/2000/XP . 3. “ PORT95NT.exe, WinDDC_ setup” program. 4. Software OSD SN Alignment kits The kit contents: a. OSD SN BOARD x1b.Printer cablex1c. VGA cable x1d. Digital cable x1e. 12V DC power source1. Install the “PORT95NT.EXE”, and restart the computer.2. Install the “WinDDC_ setup”3. Connect the DDC board as follow: (Take philips 190B8 for example)Note: Pin5 of the VGA cable which connects to the monitor should be cut off.08/09/09 4. Take analog DDC write for example, as followa. Double-click ,appear as follow Figs:b. Click .c. Key 14 numbers in the Serial Number blank, then click “OK”. Now analog DDC Write completes, as follow.Note: The way of digital DDC write is the same as analog DDC write.HG171A EDID128 bytes EDID Data (Hex):00 01 02 03 04 05 06 07 08 09 10 11 12 13 14 150: 00 FF FF FF FF FF FF 00 22 64 D1 1B sn sn sn sn16: ww yy 01 03 0A 25 17 78 EA B6 90 A6 54 51 91 2532: 17 50 54 BF EF 80 81 80 81 C0 81 40 71 4F 61 4648: 90 4F 95 0F 01 01 9A 29 A0 D0 51 84 22 30 50 9864: 36 00 72 E6 10 00 00 1E 00 00 00 FD 00 sn sn sn80: sn sn sn sn sn sn sn sn sn sn 00 00 00 FF 00 3296: 33 31 31 32 33 31 32 33 31 32 33 33 00 00 00 FC112: 00 48 61 6E 6E 73 2E 47 20 48 47 31 37 31 00 D2。
Parker Hannifin 自动化系列线性电机维护指南与零件清单说明书
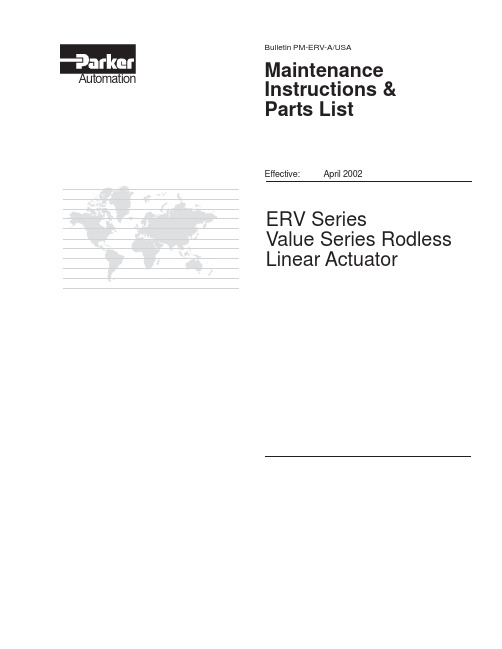
Effective:April 2002Bulletin PM-ERV-A/USAMaintenance Instructions &Parts ListERV SeriesValue Series Rodless Linear ActuatorAutomation2ERV SeriesMaintenance Instructions and Parts List PM-ERV-A/USAParker Hannifin Corporation Automation Actuator Division Wadsworth, OH 44281AutomationWho's WhoET125 Electric CylindersVoice (330)336-3511 - Fax (330)334-3335Karen Dutt Ext. 122Order entry, expeditingVictor Massolli Ext. 125Technical Information, Applications Mark Fisher Ext. 123Applications, spare parts Ben Furnish Ext. 128Programming, ApplicationsScott Frederick Ext. 124Electro-Mechanical Product Sales Manager Bill Service Ext. 107Marketing Manager Roger SherrardExt. 103General Manager© Copyright 1997, Parker Hannifin Corporation, All Rights ReservedThe items described in this document are hereby offered for sale by Parker Hannifin Corporation, its subsidiaries or its authorized distributors. This offer and its acceptance are governed by the provisions stated on the separate page of this document entitled "Offer of Sale".Offer of SaleFAILURE OR IMPROPER SELECTION OR IMPROPER USE OF THE PRODUCTS AND/OR SYSTEMS DESCRIBED HEREIN OR RELATED ITEMS CAN CAUSE DEATH, PERSONAL INJURY AND PROPERTY DAMAGE.This document and other information from Parker Hannifin Corporation, its subsidiaries and authorized distributors provide product and/or system options for further investigation by users having technical expertise. It is important that you analyze all aspects of your application and review the informa-tion concerning the product or system in the current product catalog. Due to the variety of operating conditions and applications for these products or systems, the user, through its own analysis and testing, is solely responsible for making the final selection of the products and systems and assuring that all performance, safety and warning requirements of the application are met.The products described herein, including without limitation, product features, specifications, designs, availability and pricing, are subject to change by Parker Hannifin Corporation and its subsidiaries at any time without notice.WARNINGERV SeriesMaintenance Instructions and Parts List PM-ERV-A/USADescriptionPage No.ERV Features .......................................................................................................4Carriage Preload Adjustment................................................................................4Carriage Removal/Assembly Procedure ...............................................................5Mounting...............................................................................................................6Parts List ..............................................................................................................7Wheel Wiper/Bumper ...........................................................................................8Torque Table ......................................................................................................10Offer of Sale . (11)This guide contains maintenance instructions, replacement parts information, and information onvarious options.Maintenance Instructions and Parts List PM-ERV-A/USAAutomation Actuator Division Wadsworth, OH 44281AutomationERV SeriesMaintenance Instructions and Parts List PM-ERV-A/USAThe carriage can be easily removed from the unit without disconnecting the belt or drive train.1.Remove the three bolts (8) from the top of the carriage.2.Then roll the carriage off the body in the direction of the idler end cap. The carriage and wheel assembly will slide over the idler end cap. T3.The wheel assemblies can be removed by holding the hex head on the wheel bolts (5) and removing the flat head set screw (6).Carriage Assembly ProcedureCarriage Removal or wheel Replacement1,Roll the carriage onto the housing body and adjust the eccentric wheels as described above and on page 4. The amount of pre-load on the wheels can be felt when the carriage wheels are rolled into the body rails.2.When the pre-load is satisfactory, roll the carriage over the carriage shuttle (9) and line up the holes.3.Assemble the bolts (8) into the carriage and torque to specification on page 10.Carriage Removal/AssemblyMaintenance Instructions and Parts List PM-ERV-A/USAAutomation Actuator Division Wadsworth, OH 44281AutomationERV SeriesMaintenance Instructions and Parts List PM-ERV-A/USAParts ListMaintenance Instructions and Parts List PM-ERV-A/USAAutomation Actuator Division Wadsworth, OH 44281AutomationERV SeriesMaintenance Instructions and Parts List PM-ERV-A/USA** nn= V5 to fit ERV5 or V8 to fit ERV8Hall Effect/Reed SwitchesHall effect and reed switches can be specified to sense the position of the carriage by detecting the magnet attached to the inside of the carriage. Magnets come as standard on all units. The switches are attached to the T-slot on the body and can be easily adjusted to the position. See the figure below for the bracket and hard-ware needed for the switches. The switch specifications are also listed below.Maintenance Instructions and Parts List PM-ERV-A/USAAutomation Actuator Division Wadsworth, OH 44281AutomationERV SeriesMaintenance Instructions and Parts List PM-ERV-A/USAOffer Of Sale1. Terms and Conditions of Sale: All descriptions, quotations, proposals,offers acknowledgments, acceptances and sales of Seller's products are subject to and shall be governed exclusively by the terms and conditions stated herein. Buyer's acceptance of any offer to sell is limited to these terms and conditions. Any terms or conditions in addition to, or inconsistent with those stated herein, proposed by Buyer in any acceptance of an offer by Seller, are hereby objected to. No such additional,different or inconsistent terms and conditions shall become part of the contract between, Buyer and Seller unless expressly accepted in writing by Seller. Seller's acceptance of any offer to purchase by Buyer is expressly conditional upon Buyer's assent to all the terms and conditions stated herein, including any terms in addition to,or inconsistent with those contained in Buyer's offer. Acceptance of Seller's products shall in all events constitute such assent.2. Payment: Payment shall be made by Buyer net 30 days from the date ofdelivery of the items purchased hereunder. Amounts not timely paid shall bear interest at the maximum rate permitted by law for each month or portion thereof that the Buyer is late in making payment. Any claims by Buyer for omissions or shortages in a shipment shall be waived unless Seller receives notice thereof within 30 days after Buyer's receipt of the shipment.3. Delivery: Unless otherwise provided on the face hereof, delivery shall bemade F.O.B. Seller's plant. Regardless of the method of delivery, however, risk of loss shall pass to Buyer upon Seller's delivery to a carrier. Any delivery dates shown are approximate only and Seller shall have no liability for any delays in delivery.4. Warranty: Seller warrants that the items sold hereunder shall be free fromdefects in material or workmanship for a period of 18 months from date of shipment from Parker Hannifin Corporation. THIS WARRANTY COMPRISES THE SOLE AND ENTIRE WARRANTY PERTAINING TO ITEMS PROVIDED HEREUN-DER. SELLER MAKES NO OTHER WARRANTY, GUARANTEE, OR REPRESENTATION OF ANY KIND WHATSOEVER. ALL OTHER WAR-RANTIES, INCLUDING BUT NOT LIMITED TO, MERCHANTABILITY AND FITNESS FOR PURPOSE, WHETHER EXPRESS, IMPLIED, OR ARISING BY OPERATION OF LAW, TRADE USAGE, OR COURSE OF DEALING ARE HEREBY DISCLAIMED.NOTWITHSTANDING THE FOREGOING, THERE ARE NOWARRANTIES WHATSOEVER ON ITEMS BUILT OR ACQUIRED WHOLLY OR PARTIALLY, TO BUYER'S DESIGNS OR SPECIFICATIONS.5. Limitation of Remedy: SELLER'S LIABILITY ARISING FROM ORIN ANY WAY CONNECTED WITH THE ITEMS SOLD OR THIS CONTRACT SHALL BE LIMITED EXCLUSIVELY TO REPAIR OR REPLACEMENT OF THE ITEMS SOLD OR REFUND OF THE PURCHASE PRICE PAID BYBUYER, AT SELLER'S SOLE OPTION. IN NO EVENT SHALL SELLER BE LIABLE FOR ANY INCIDENTAL, CONSEQUENTIAL OR SPECIALDAMAGES OF ANY KIND OR NATURE WHATSOEVER, INCLUDING BUT NOT LIMITED TO LOST PROFITS ARISING FROM OR IN ANY WAYCONNECTED WITH THIS AGREEMENT OR ITEMS SOLD HEREUNDER,WHETHER ALLEGED TO ARISE FORM BREACH OF CONTRACT,EXPRESS OR IMPLIED WARRANTY, OR IN TORT, INCLUDING WITHOUT LIMITATION, NEGLIGENCE, FAILURE TO WARN OR STRICT LIABILITY.6. Changes, Reschedules and Cancellations: Buyers may request to modifythe designs or specifications for the items sold hereunder as well as the quantities and delivery dates thereof, or may request to cancel all or part of this order, however, no such requested modification or cancellation shall become part of the contract between Buyer and Seller unless accepted by Seller in a written amendment to this Agreement.Acceptance of any such requested modification of cancellation shall be at Seller's discretion, and shall be upon such terms and conditions as Seller may require.7. Special Tooling: A tooling charge may be imposed for any special tooling,including without limitation, dies, fixtures, molds and patterns, acquired to manufacture items sold pursuant to this contract. Such special tooling shall be and remain Seller's property notwithstanding payment of any charges by Buyer. In no event will Buyer acquire any interest in apparatus belonging to Seller which is utilized in the manufacture of the items sold hereunder, even if such apparatus has been specially converted or adapted for such manufacture and notwithstanding any charges paid by Buyer. Unless otherwise agreed, Seller shall have the right to alter, discard or otherwise dispose of any special tooling or other property in its sole discretion at any time.8. Buyer's Property: Any designs, tools, patterns, materials, drawings confidential information or equipment furnished by Buyer, or any otheritems which become Buyer's property, may be considered obsolete and may be destroyed by Seller after two (2) consecutive years have elapsed without Buyer placing an order for the items which are manufactured using such property.Seller shall not be responsible for any loss or damage to such property while it is in Seller's possession or control.9. Taxes: Unless otherwise indicated on the face hereof, all prices andcharges are exclusive of excise, sales, use, property, occupational or like taxes which may be imposed by any taxing authority upon the manufacture, sale or delivery of the items sold hereunder. If any such taxes must be paid by Seller or if Seller is liable for the collection of such tax, the amount thereof shall be in addition to the amounts for the items sold. Buyer agrees to pay all such taxes or to reimburse Seller therefore upon receipt of its invoice. If Buyer claims exemption from any sales, use or other tax imposed by any taxing authority,Buyer shall save Seller harmless from and against any such tax, together with any interest or penalties thereon which may be assessed if the items are held to be taxable.10. Indemnity For Infringement of Intellectual Property Rights:Seller shall have no liability for infringement of any patents, trademarks,copyrights, trade dress, trade secrets or similar rights except as provided in this Part 10. Seller will defend and indemnify Buyer against allegations ofinfringement of U.S. patents, U.S. trademarks, copyrights, trade dress and trade secrets (hereinafter 'Intellectual Property Rights'). Seller will defend at itsexpense and will pay the cost of any settlement or damages awarded in an action brought against Buyer based on an allegation that an item sold pursuant to this contract infringes the Intellectual Property Rights of a third party. Seller'sobligation to defend and indemnify Buyer is contingent on Buyer notifying Seller within ten (10) days after Buyer becomes aware of such allegations ofinfringement, and Seller having sole control over the defense of any allegations or actions including all negotiations for settlement or compromise. If an item sold hereunder is subject to a claim that it infringes the Intellectual Property Rights of a third party, Seller may, at its sole expense and option, procure for Buyer the right to continue using said item, replace or modify said item so as to make it noninfringing, or offer to accept return of said item and return the purchase price less a reasonable allowance for depreciation. Notwithstanding the foregoing,Seller shall have no liability for claims of infringement based on informationprovided by Buyer, or directed to items delivered hereunder for which the designs are specified in whole or part by Buyer, or infringements resulting from the modification, combination or use in a system of any item sold hereunder. The foregoing provisions of this Part 10 shall constitute Seller's sole and exclusive liability and Buyer's sole and exclusive remedy for infringement of Intellectual Property Right.If a claim is based on information provided by Buyer or if the design foran item delivered hereunder is specified in whole or in part by Buyer, Buyer shall defend and indemnify Seller for all costs, expenses or judgements resulting from any claim that such item infringes any patent, trademark, copyright, trade dress,trade secret or any similar right.11. Force Majeure: Seller does not assume the risk of and shall not beliable for delay or failure to perform any of Seller's obligations by reason of circumstances beyond the reasonable control of Seller (hereinafter 'Events of Force Majeure'). Events of Force Majeure shall include without limitation,accidents, acts of God, strikes or labor disputes, acts, laws, rules or regulations of any government or government agency, fires, floods, delays or failures in delivery of carriers or suppliers, shortages of materials and any other cause beyond Seller's control.12. Entire Agreement/Governing Law: The terms and conditions setforth herein, together with any amendments, modifications and any different terms or conditions expressly accepted by Seller in writing, shall constitute the entire Agreement concerning the items sold, and there are no oral or other representations or agreements which pertain thereto. This Agreement shall be governed in all respects by the law of the State of Ohio. No actions arising out of the sale of the items sold hereunder of this Agreement may be brought by either party more than two (2) years after the cause of action accrues.The items described in this document and other documents or descriptions provided by Parker Hannifin Corporation, its subsidiaries and its authorized distributors arehereby offered for sale at prices to be established by Parker Hannifin Corporation, its subsidiaries and its authorized distributors. This offer and its acceptance by any customer ("Buyer") shall be governed by all of the following Terms and Conditions. Buyer's order for any such item, when communicated to Parker Hannifin Corporation, its subsidiary or an authorized distributor ("Seller") verbally or in writing, shall constitute acceptance of this offer.Parker Hannifin CorporationAutomation Actuator Division135 Quadral DriveWadsworth, Ohio 44281 USA AutomationTel: (330) 336-3511Fax: (330) 334-3335Web site: /automation。
Parker Hannifin HD Series 产品手册说明书
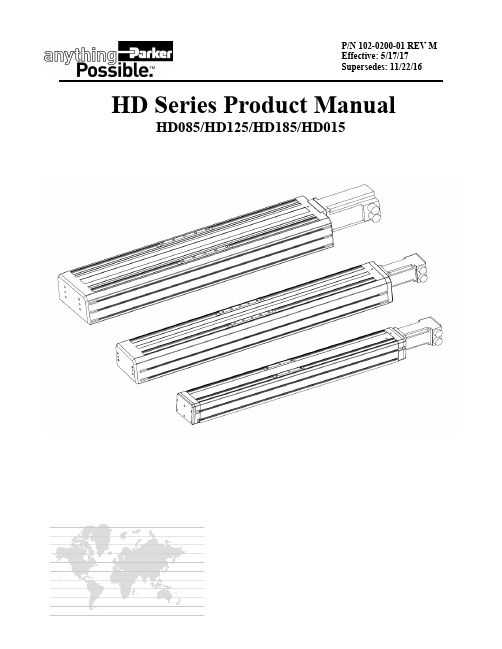
P/N 102-0200-01 REV MEffective: 5/17/17Supersedes: 11/22/16HD Series Product ManualHD085/HD125/HD185/HD015Important User InformationThe information in the product manual, including any apparatus, methods, techniques, and con-cepts described herein, are the proprietary property of Parker Hannifin Corporation or its licensors, and may not be copied, disclosed, or used for any purpose not expressly authorized by the owner thereof.Since Parker Hannifin Corporation constantly strives to improve all of its products, we reserve the right to change this product manual and equipment mentioned therein at any time without notice.For assistance contact:Parker Hannifin Corporation1140 Sandy Hill RoadIrwin, PA 15642Phone: 724/861-8200800/245-6903Fax: 724/861-3330E-mail:*****************Web site: Table of ContentsREVISION NOTES (5)SECTION 1 - INTRODUCTION (6)PRODUCT DESCRIPTION (6)U NPACKING (6)R ETURN I NFORMATION (7)R EPAIR I NFORMATION (7)W ARNINGS AND P RECAUTIONS (7)S PECIFICATION C ONDITIONS AND C ONVERSIONS (7)SECTION 2 - HD SERIES TABLE SPECIFICATIONS (8)O RDER N UMBER N OMENCLATURE .......................................................................................................................................................... 8-11D IMENSIONAL D RAWINGS ..................................................................................................................................................................... 12-21E XPLODED VIEW/PARTS LIST ................................................................................................................................................................. 22-29G ENERAL T ABLE S PECIFICATIONS……………………………………………………………………………………………………...30-31BALLSCREW/TABLE MAXIMUM SPEEDS (32)BEARING /LOADING ENGINEERING REFERENCE .................................................................................................................... 33-36 REFLECTED INERTIAS ENGINEERING REFERENCE................................................................................................................. 37-39 CARRIAGE STIFFENESS/BASE-RAIL MOMENT OF INERTIAS (40)SECTION 3 - COMPONENT SPECIFICATIONS/ MOUNTING (41)B RAKES ................................................................................................................................................................................................. 41-43L IMIT & H OME S ENSORS (44)C OUPLINGS (45)SECTION 4 - BASE MOUNTING PROCEDURES (46)M OUNTING S URFACE R EQUIREMENTS (46)B ASE M OUNTING M ETHODS (46)SECTION 5– WRAP AROUND INFORMATION (47)HD085 WRAP AROUND (47)HD125 WRAP AROUND (48)HD185 WRAP AROUND (49)SECTION 6 - MAINTENANCE AND LUBRICATION..................................................................................................................... -50-52B ELT S EALS INFORMATION.................................................................................................................................................................... 50-51S QUARE R AIL B EARING L UBRICATION (52)G ROUND B ALLSCREW L UBRICATION (52)SECTION 7 - MOTOR/TABLE PERFORMANCE CHARTS/TECHNICAL INFORMATION.................................................... 53-59 HD085 MOTOR/TABLE PERFORMANCE CHARTS . (53)HD125 MOTOR/TABLE PERFORMANCE CHARTS (54)HD185 MOTOR/TABLE PERFORMANCE CHARTS (55)H V232 MOTOR TECHNICAL INFORMATION (56)S M232/233 MOTOR TECHNICAL INFORMATION (57)C MP/MPP921 MOTOR TECHNICAL INFORMATION ................................................................................................................................... 58-59Revision Notes :REV-2 (3-28-06) :UPDATED CATALOG CONFIGURABLE OPTIONSUPDATED EXPLODED BOMS HD125/HD185HD125 ITEM# 9A/9B CARRIAGE WEAR BARSHD185 ITEM#9 CARRIAGE WEAR BARITM#18/28 QTY NOW 2(NEW BUMPER ASSEMBLY)NEW BRAKE ASSEMBLYS 002-2601/002-2611 PG 34/35REV-3 (10-08-07) :UPDATED IXX VALUES ON PAGE 30 FOR HD085 HD125 AND HD185UPDATED DIMS IN RED ON PAGES 12,13REV-4 (3-31-08) :CORRECTED TYPO ON PAGE 45 . MAINTENANCE FREE OPERATION UP TO 5 YEARS/2540KM OF LIFEREV-5 (8-01-08) :ADDITIONAL PAGES FOR THE INDUSTRIAL GRADE OPTION AND NEW WRAP ASSEMBLIESREV-6 (1-19-09) :PAGE 16 CORRECTED THE MOTOR OPTION F122-HD125 DIM “A” NOW 25.0 WAS 20.0 DIM B” WAS 28.0 NOW 33.0 PAGE 19 CORRECTED THE MOTOR OPTION F122-HD185 DIM “A” NOW 25.0 WAS 20.0 DIM “B” WAS 8.0 NOW 13.0 REV-7 (5-26-10) :PAGE 30 CORRECTED 1200MM TRAVEL HD185 MAX BREAKAWAY TORQUE NOW 0.38 WAS 0.25 N-MPAGE 31 CORRECTED 1200MM TRAVEL HD185 MAX BREAKAWAY TORQUE NOW 0.38 WAS 0.25 N-MREV-8 (4-25-12) :PAGE 31 CORRECTED 1200MM TRAVEL HD185 MAX BREAKAWAY TORQUE NOW 0.38 WAS 0.25 N-M(SAME AS REV 7 BUT ONLY PAGE 30 WAS UPDATED)REV-9 (5-12-12) :PAGE 52 Changed Alvania grease to GADUS S2 V100 2 (just a name change)REV-10 (10-23-12) :PAGE 12 Corrected the dowel pin size on carriage was 5mm now 6mmCorrected the dowel and thread call outs on base was 6mm and m6 x1.0 now 5mm and m5 x 0.8REV-11 (11-22-16) :PAGE 15 ADD NOTE - WHEN THE 40MM LEAD IS CHOSEN WITH THE HD125, TRAVEL IS RESTRICTED BY 50 MM ON TRAVELS 200-1000MMREV-M (12) (5/17/17) :PAGE 51– UPDATED PROCEDURE ON REPLACING THE BELT SEALChapter 1 - IntroductionProduct DescriptionHD series linear table line is a robust industrial positioner that is easy to apply, easy to install, and easy to maintain. The robust design begins with and extruded body and carriage that provide exceptional beam strength and carriage stiffness. The linear bearings and ballscrew are precision components selected for their long life at 100% duty operation, they both em-ploy lube seals which provide maintenance free operation in most applications. The HD series also includes IP30 rated belt seals that protect the interior components from debris.The HD series is very easy to apply. As part of the configurable number, users can select options such as screw lead, motors, brakes and limit/homes. With motors as part of standard table, system level performance is provided in the form of graphs to enable quick application without the need for a complex motor sizing exercise.HD series has three distinct sizes allowing for ease of applying to application.HD085 85mm wide x 70mm tallHD125 125mm wide x 85mm tallHD185 185mm wide x 95mm tallThe above sizes make the HD series ideal for applying to applications requiring Cartesian set-ups.HD series also offers a standard extruded idler/square rail HD015 60mm wide x 62mm tall for use in gantry style applica-tionsUnpackingUnpackingCarefully remove the positioner from the shipping crate and inspect the unit for any evidence of shipping damage. Report any damage imme-diately to your local authorized distributor. Please save the shipping crate for damage inspection or future transportation. Incorrect handling of the positioner may adversely affect the performance of the unit in its application. Please observe the following guide-lines for handling and mounting of your new positioner.DO NOT allow the positioner to drop onto the mounting surface. Dropping the positioner can generate impact loads that may re-sult in flat spots on bearing surfaces or misalignment of drive components.DO NOT drill holes into the positioner. Drilling holes into the positioner can generate particles and machining forces that may ef-fect the operation of the positioner. Parker Hannifin Corporation will drill holes if necessary; contact your local authorized distributor.DO NOT subject the unit to impact loads such as hammering, riveting, etc. Impacts loads generated by hammering or riveting may result in flat spots on bearing surfaces or misalignment of drive components.DO NOT push in belt seals when removing positioner from shipping crate. Damaging belt seals may create additional friction dur-ing travel and may jeopardize the ability of the beltseals to protect the interior of the positioner. If belt seals are pushed in run carriage by hand over entire travel and the belts will reset.DO NOT submerge the positioner in liquids.DO NOT disassemble positioner. Unauthorized adjustments may alter the positioner’s specifications and void the product warran-ty.Return InformationReturnsAll returns must reference a “R eturn M aterial A uthorization”, (RMA), number. Please call your local authorized distributor or Parker Hannifin Corporation Customer Service Department at 800-245-6903 to obtain a “RMA” number.Repair InformationOut-of-Warranty RepairOur Customer Service Department repairs Out-of-Warranty products. All returns must reference a “RMA” number. Please call your local authorized distributor or Parker Hannifin Corporation Customer Service Department at 800-245-6903 to obtain a “RMA” number. You will benotified of any cost prior to making the repair.Warnings and PrecautionsVertical OperationDepending upon your load and ballscrew selection the carriage and load may ‘backdrive’ in power loss situations potentially causing product damage or personal injury. An electro-mechanical brake, which will activate in response to a loss of power (option ‘B2’), can be used to pre-vent potential product damage or personal injury. Note: Actual maximum load for brake holding is dependent on screw lead.Strain Relieve Electrical ComponentsAll electrical components (such as brakes, encoders, and limit/home switches) must be strain relieved. Failure to strain relieve electrical wires or cables may result in component failure and/or possible personal injury.Specification Conditions and ConversionsSpecifications are Temperature DependentCatalog Specifications are obtained and measured at 20 Degrees C. Specifications at any other temperature may deviate from catalog spec-ifications. Minimum to Maximum continuous operating temperature range (with NO guarantee of any specification except motion) of a stand-ard unit before failure is 5 - 70 Degrees C. Certain components can be eliminated or substituted to improve operation at these temperatures.Positioners with low temperature or high temperature components will be handled as specials, contact your local distributor.Specifications are Mounting Surface DependentCatalog Specifications are obtained and measured when the positioner is fully supported, bolted down (to eliminate any extrusion deviation), and is mounted to a work surface that has a maximum flatness error of 0.013mm/300mm (0.0005”/ft).Specifications are Point of Measurement DependentCatalog Specifications and Specifications in this manual are measured in the center of the carriage, 37.5mm above the carriage surface. All measurements taken at any other location may deviate from these values.IndustrialNSEE PAGES #13,14 FOR ADDITIONAL MOTOR MOUNTS OFFERINGSIndustrial NSEE PAGES #16,17 FOR ADDITIONAL MOTOR MOUNTS OFFERINGSIndustrialNSEE PAGES #19,20 FOR ADDITIONAL MOTOR MOUNTS OFFERINGSHD SERIES PRODUCT MANUAL 11PARKER HANNIFIN CORPORATIONELECTROMECHANICAL AUTOMATION DIVISIONSECTION 2HD015 CONFIGURABLEHD085 DIMENSIONAL DRAWINGSPlease refer to for the latest, updated drawings DOWEL HOLESFOR 5MM PINS“D” HOLES1/2 “A” +4.5M5 x 0.8 Thd.ON PG 12STANDARD BELT TENSION SET @ 75NHD125 DIMENSIONAL DRAWINGSPlease refer to for the latest, updated drawings*WHEN THE 40MM LEAD IS CHOSEN WITH THE HD125, TRAVEL IS RESTRICTED BY 50 MM ON TRAVELS 200-1000MM*******ON PG 15 STANDARD BELT TENSION SET @ 120NHD185 DIMENSIONAL DRAWINGS Please refer to for the latest, updated drawings25.0BRAKE OPTIONQTY. 4 TAPPED HOLESM6 x 1.0 x 12.0dp.ENDVIEWON PG 18 STANDARD BELT TENSION SET @ 120NHD015 DIMENSIONAL DRAWINGS Please refer to BILL OF MATERIALSHD085 EXPLODED VIEWBILL OF MATERIALSHD125 EXPLODED VIEWBILL OF MATERIALSHD185 EXPLODED VIEWHD015 BILL OF MATERIALSHD015 EXPLODED VIEWGeneral Table Specifications Standard grade: note : see page #31 for Industrial grade STANDARD GRADESTANDARD GRADEGeneral Table Specifications Industrial grade: note : see page #30 for Standard gradeBALLSCREW INFORMATION *Note:When employing 20mm diameter 40mm lead ballscrew maximum rps=56Maximum Carriage Linear Speed (mm/s)Maximum Screw Speed (Revs/Sec)HD Series Engineering ReferenceThe following performance information is provided as a supplement to the product specifications pages. The following graphsand formulas are used to establish the table life relative to the applied loads. The useful life of a linear table at full catalog specifications is dependent on the forces acting upon it. These forces include both static components resulting from payload weight, and dynamic components due to acceleration/deceleration of the load. in multi -axes applications, the primary position-er at the bottom of the stack usually establishes the load limits for the combined axes. When determining life/load, it is criticalto include the weight of all positioning elements that contribute to the load supported by the primary axis.Table Life Load Chart : Compression (Normal Load)This graph provides a “rough cut” evaluation of the support bearing life/load characteristics. The curves show the life/load relationship when the applied load is centered on the carriage, normal (perpendicular) to the carriage mounting surface. For final evaluation of life vs. load,Table Life Load Chart : Thrust(Axial load)HD185105HD SERIESHD12577.0 Kgf ( TENSION) 65 mm70 mm57.5 mm107.5 mm(PAGE 28)-77.0Kgf ( COMPRESSION)125.0 Kgf -75 Kgf77.0 Kgf ( TENSION)125.0 Kgf SIDE LOAD163.5 Kgf(1603N) PAGE 27100 KgfLife @1603N =4500kmREFLECTED INERTIASPLEASE NOTE : ONE MUST ADD THE ADDITIONAL EFFECTS OF CUSTSOMER LOADREFLECTED INERTIAS CONTINUED:REFLECTED INERTIAS CONTINUED:CARRIAGE STIFFNESS:BASE/RAIL ASSEMBLY MONMENTS OF INERTIAS:EXTERNAL BRAKE INFORMATION :NOTE : OFFERED ON HD125/HD185 SERIES ONLYHD085 OFFERS ON MOTORNOTE :ANALYSIS OF REQUIRED BRAKING TORQUE SHOULD BE DONE.THE REQUIRED BRAKING TORQUE SHOULD BE MULTIPLIED BY A SERVICE FACTOR OF 1.5 TO 4.0 DEPENDING ON THE APPLICATIONCONSULT FACTORY FOR MORE DETAILED INFORMATIONHD125 BRAKE ASSY (002-2611-02) MOUNTING INSTRUCTIONSHD185 BRAKE ASSY (002-2601-02) MOUNTING INSTRUCTIONSLIMIT HOME SENSORSMOUNTING:INSERT INTO UPPER MOST T-SLOT AND POSITION WHERE REQUIRED. TIGHTEN SCREW TO FIX. POSITION.NOTE : MAGNET TRIPPER CENTERED INTERNALLY ON CARRIAGE (BOTH SIDES)COUPLINGS:Mounting Surface RequirementsProper mounting of the HD SERIES is essential to optimize product performance.All specifications are based on the following conditions:The positioner must be bolted down along its entire length.The positioner must be mounted to a flat, stable surface with a flatness error less than or equal 0.020mm/300mm.Catalog Specifications may deviate for positioners mounted to surfaces that do not meet the above conditions.If the surface does not meet these specifications the surface can be shimmed to comply with these requirements.If mounting conditions require that the table base is overhung, table specifications will not be met over that portion of the table. Additionally, in X-Y Systems the overhung portion of the Y-axis may not meet specifications due to the additional error caused by deflection and non-support of the base. Contact Parker Hannifin Corporation for guidelines on specifications ofoverhang applicationsBase Mounting MethodsThe HD series can mounted via two ways:1. Tapped holes in the base.Reference the dimensional drawings on pages 11-142. Toe ClampingHD085 WRAP AROUNDBELT TENSIONING:LOOSEN ITEM #15 ALLOWING MTR ADP TO SLIDE FREELY.USE ITEM #13 TO TIGHTEN/LOOSEN TENSION.MEASURE BELT TENSION WITH BELT TENSION METER.(FOR MORE INFORMATION CONTACT FACTORY)BELT TENSION SHOULD MEASURE 75N-95NHD125 WRAP AROUNDBELT TENSIONING:LOOSEN ITEM #17 ALLOWING ITEM 8 TO SLIDE FREELY. USE ITEM #20 TO TIGHTEN/LOOSEN TENSION.MEASURE BELT TENSION WITH BELT TENSION METER. (FOR MORE INFORMATION CONTACT FACTORY)BELT TENSION SHOULD MEASURE 110N-130NHD185 WRAP AROUNDBELT TENSIONING:LOOSEN ITEM #17 ALLOWING ITEM 8 TO SLIDE FREELY. USE ITEM #20 TO TIGHTEN/LOOSEN TENSION.MEASURE BELT TENSION WITH BELT TENSION METER.(FOR MORE INFORMATION CONTACT FACTORY)BELT TENSION SHOULD MEASURE 110N-130NBelt Seal Information : Qty 2 belt seals per table (except HD015)HD015 BELT SEALSPART#DESCRIPTION PART#DESCRIPTION 101-2966-01BELT SEAL HD015 SINGLE CARR 100MM 101-2966-101BELT SEAL HD015 DOUBLE CARR 100MM101-2966-02BELT SEAL HD015 SINGLE CARR 200MM 101-2966-102BELT SEAL HD015 DOUBLE CARR 200MM101-2966-03BELT SEAL HD015 SINGLE CARR 300MM 101-2966-103BELT SEAL HD015 DOUBLE CARR 300MM101-2966-04BELT SEAL HD015 SINGLE CARR 400MM 101-2966-104BELT SEAL HD015 DOUBLE CARR 400MM101-2966-05BELT SEAL HD015 SINGLE CARR 500MM 101-2966-105BELT SEAL HD015 DOUBLE CARR 500MM101-2966-06BELT SEAL HD015 SINGLE CARR 600MM 101-2966-106BELT SEAL HD015 DOUBLE CARR 600MM101-2966-07BELT SEAL HD015 SINGLE CARR 700MM 101-2966-107BELT SEAL HD015 DOUBLE CARR 700MM101-2966-08BELT SEAL HD015 SINGLE CARR 800MM 101-2966-108BELT SEAL HD015 DOUBLE CARR 800MM101-2966-09BELT SEAL HD015 SINGLE CARR 900MM 101-2966-109BELT SEAL HD015 DOUBLE CARR 900MM101-2966-10BELT SEAL HD015 SINGLE CARR 1000MM 101-2966-110BELT SEAL HD015 DOUBLE CARR 1000MM101-2966-11BELT SEAL HD015 SINGLE CARR 1100MM 101-2966-111BELT SEAL HD015 DOUBLE CARR 1100MM101-2966-12BELT SEAL HD015 SINGLE CARR 1200MM 101-2966-112BELT SEAL HD015 DOUBLE CARR 1200MM101-2966-13BELT SEAL HD015 SINGLE CARR 1300MM 101-2966-113BELT SEAL HD015 DOUBLE CARR 1300MM101-2966-14BELT SEAL HD015 SINGLE CARR 1400MM 101-2966-114BELT SEAL HD015 DOUBLE CARR 1400MM101-2966-15BELT SEAL HD015 SINGLE CARR 1500MM 101-2966-115BELT SEAL HD015 DOUBLE CARR 1500MM101-2966-16BELT SEAL HD015 SINGLE CARR 1600MM 101-2966-116BELT SEAL HD015 DOUBLE CARR 1600MM101-2966-17BELT SEAL HD015 SINGLE CARR 1700MM 101-2966-117BELT SEAL HD015 DOUBLE CARR 1700MM101-2966-18BELT SEAL HD015 SINGLE CARR 1800MM 101-2966-118BELT SEAL HD015 DOUBLE CARR 1800MM101-2966-19BELT SEAL HD015 SINGLE CARR 1900MM 101-2966-119BELT SEAL HD015 DOUBLE CARR 1900MM101-2966-20BELT SEAL HD015 SINGLE CARR 2000MM 101-2966-120BELT SEAL HD015 DOUBLE CARR 2000MM。
金王征途I机械体维修手册说明书
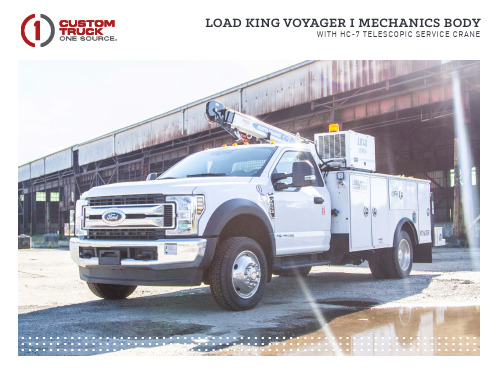
ELIMINATION CABLE BOOM MOUNTED 55 FT/MIN PLANETARY WINCH 20’ 4” BOOM LENGTH - ADJUSTABLE BOOM SUPPORT
CRANE HOOK AND SNATCH BLOCK ANTI-TWO-BLOCK DEVICE
ASK ABOUT THE CUSTOMIZED AND FLEXIBLE LEASING & FINANCING SOLUTIONS AVAILABLE FROM CUSTOM TRUCK CAPITAL
........... ........... ...........
888-925-0858
维修提醒器217 - 主要内容说明书
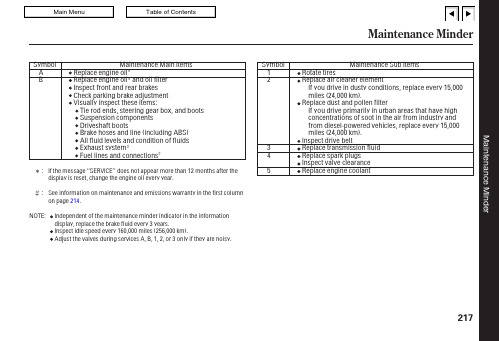
Maintenance Minder217:See information on maintenance and emissions warranty in the first column on page .Independent of the maintenance minder indicator in the information display,replace the brake fluid every 3years.Adjust the valves during services A,B,1,2,or 3only if they are noisy.Inspect idle speed every 160,000miles (256,000km).NOTE:214MaintenanceMinderMaintenance Record218mi mi mi mi mi mi mi mi mi mi mi mi mi mi Maintenance PerformedAB12345A B 12345A B 12345A B 12345A B 12345A B 12345A B 12345Signature DateMaintenance PerformedAB12345AB12345AB12345AB12345AB12345AB12345AB12345Signature DateMileagekm km km km km km kmMileagekm km km km km km kmYou or the servicing dealer can record all completed maintenance here.When maintenance is performed,record the mileage,circle the coded item(s)completed,and write in any other non-coded items (such as brake fluid replacement)below the codes.Keep the receipts for all work done on your vehicle.Maintenance can also be recorded in your Honda service historybooklet.Maintenance RecordMaintenance219mi mi mi mi mi mi mi mi mi mi mi mi mi mi Maintenance PerformedAB12345A B 12345A B 12345A B 12345A B 12345A B 12345A B 12345Signature DateMaintenance PerformedAB12345AB12345AB12345AB12345A B 12345A B 12345A B 12345Signature DateMileagekm km km km km km kmMileagekm km km km km kmkmFluid LocationsDX,Canadian DX-G,LX,and EX models220Fluid LocationsSi modelMaintenance221Oil is a major contributor to your engine’s performance and longevity.Always use a premium-grade detergent oil displaying the APICertification Seal.This seal indicates the oil is energy conserving,and that it meets the American Petroleum Institute’s latest requirements.It is highly recommended that you use Honda Motor Oil in your vehicle for optimum engine protection.Unscrew and remove the engine oil fill cap on the valve cover.Pour in the oil slowly and carefully so you do not spill any.Clean up any spills immediately.Spilled oil coulddamage components in the engine compartment.Recommended Engine Oil Adding Engine Oil222。
浩瀚电器重型电锅替换零部件手册说明书

VTMB22VB2S VB21VTMB2VB SERIES1 THRU45 - 678 - 9101112 - 13 - 14ELECTRICAL COMPONENTSVB SERIESELECTRICAL COMPONENTSILLUS.PART OF PART AMT.1417934-G1Block Assy. - Porcelain (208-240 V. Machine)(Incls.items 2, 3 & 4)..........................................AR 2SC-117-3Mach. Screw 10-24 x 11⁄4 Rd. Hd................................................................................................AR 3WS-23-20Washer.......................................................................................................................................AR 4NS-44-9Nut Assy 10-24 Hex “KEPS”......................................................................................................AR 5411497-B1Contactor (208-240 V. Machines)..............................................................................................AR 6417856-1Ground Lug (VB21, VB221) (1)7406708-G1Door - Breaker Panel (1)8412578-1Closure - Breaker (208-240 V.)(Shown) (1)9412578-2Closure - Breaker (480 V.) (1)10411501-14Circuit Breaker (50 Amp.)(208-240 V. Machines)......................................................................AR 11412577-1Box - Breaker. (1)12410472-9Block - Terminal (208/240 V.) (1)13410472-11Terminal Block (208-240 V.) (1)14410472-8Terminal Block (480 V.) (1)VB SERIESVB SERIES 5VB SERIESDOOR MECHANISM — OVENPL-40408-11011 THRU141516171821 - 2219 - 20VB SERIESDOOR MECHANISM - OVENILLUS.PART OF PART AMT.1410110-1Anchor - Spring (1)2417865-1Turnbuckle (36") (1)3405618-1Hook - Oven Door (1)4SC-90-1Bolt - Shoulder 1⁄2-13 x 2 Hex Hd (1)5408895-G1Crank Support Assy (1)6409240-2Spacer - 3⁄4 Pipe x 7⁄16 Lg (1)7404629-1Bearing - Hinge Pin (1)8408896-1Support - Crank (2)9410111-1Crank - Bell (1)10406363-1Spring - Door (Long) (1)11408895-G1Crank Support Assy (1)12409240-1Spacer - 3⁄4 x 5⁄16 Lg (1)13404629-1Bearing - Hinge Pin (1)14408896-1Support - Crank (1)15410090-G1Radius Bar Assy (1)16410089-1Arm - Door Control (1)17SC-90-1Bolt - Shoulder 1⁄2-13 x 2 Hex Hd (1)18PC-3-36Cotter Pin 3⁄32 x 1 Lg (1)19417860-1Bolt - Shoulder 3⁄8-16 x 3⁄4 Hex Hd (1)20417862-1Pin - Door Hinge (1)21410114-1Cover - Bottom Terminal (1)22410113-1Cover - Terminals (Top Oven Heat Elements) (1)412887-G1Door Frame Assy (1)VB SERIESBROILER GRID & DRIP SHIELDNAME OF PARTGrid Assy (1)Handle (1)Retainer - Drip Shield (1)Mach. Screw 10-24 x 1 Truss Hd (2)Spacer (2)Lock Nut 10-24 Light Flexloc (2)Post - Door (R.H.) (1)Post - Door (L.H.) (1)Drip Shield (1)Ball Bearing (Grid Carriage).........................................................................................................VB SERIESPL-40410-1915 - 16 CARRIAGE & LIFT UNIT (BROILER)PART OF PART406966-G1Carriage & Lift Mechanism (Incls.items 2 thru 7)......................................................................... 417866Spring - Carriage.. (1)405655-1Ball Bearing (Grid Carriage)......................................................................................................... 407488-1Pin - Bearing (2)417869-1Spacer (2)WS-3-3Washer (4)PC-3-36Cotter Pin 3⁄32 x 1 Lg (2)407619-1Ratchet Stop (1)406046-1Sleeve - Handle (1)414819-1Red Plastic Ball Handle................................................................................................................ 406056-2Adapter - Ball Handle. (1)407636-G1Push Rod Assy (1)417810-2Spring - Compression (1)NS-13-22Full Nut 3⁄8-16 Hex (2)406990-G1Grease Collector (1)407006-1Handle - Grease Collector (1)VB SERIESPL-40411-1ELECTRIC HEAT ELEMENTS(BROILER)PARTNAME OF PART407012-4Electric Heat Element 208 V........................................................................................................407012-5Electric Heat Element 240 V........................................................................................................407012-6Electric Heat Element 480 V........................................................................................................410465-1Retainer - Heating Element (3)407930-G1Heat Shield Assy (1)VB SERIES9 THRU141715 - 16PL-40412-1ELECTRIC HEAT ELEMENTS (OVEN)NAME OF PARTFrame Assy. - Top Elements (1)Frame Assy. - Bottom Elements................................................................................................... Element Assy. - Outer Top (208 V.)............................................................................................. Element Assy. - Outer Top (240 V.)............................................................................................. Element Assy. - Outer Top (480 V.)............................................................................................. Element - Outer Bottom (208 V.).. (1)Element - Outer Bottom (240 V.) (1)Element - Outer Bottom (480 V.) (1)VB SERIES2PL-40413-1MISCELLANEOUSNAME OF PARTFlue Riser (1)Strap - Back Attaching................................................................................................................Leg (SST) (4)Caster W/O Brake (2)Caster W/Brake (2)。
Hanna Instruments产品维修保修说明书
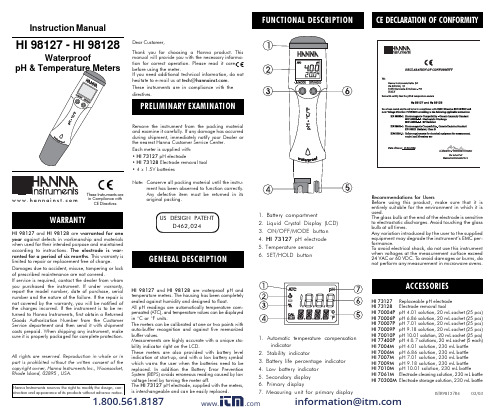
w w w.h a n n a i n s t.c o mWARRANTYHI 98127 and HI 98128 are warranted for one year against defects in workmanship and materials when used for their intended purpose and maintained according to instructions. The elect rode is war-ranted for a period of six months . This warranty is limited to repair or replacement free of charge.Damages due to accident, misuse, tampering or lack of prescribed maintenance are not covered.If service is required, contact the dealer from whom you purchased the instrument. If under warranty,report the model number, date of purchase, serial number and the nature of the failure. If the repair is not covered by the warranty, you will be notified of the charges incurred. If the instrument is to be re-turned to Hanna Instruments, first obtain a Returned Goods Authorization Number from the Customer Service department and then send it with shipment costs prepaid. When shipping any instrument, make sure it is properly packaged for complete protection.All rights are reserved. Repro ductio n in who le o r in part is pro hibited witho ut the written co nsent o f the copyright owner, Hanna Instruments Inc., Woonsocket,Rhode Island, 02895 , USA.Instruction ManualHI 98127 - HI 98128WaterproofRemove the instrument from the packing material and examine it carefully. If any damage has occurred during shipment, immediately notify your Dealer or the nearest Hanna Customer Service Center.Each meter is supplied with:• HI 73127 pH electrode• HI 73128 Electrode removal tool • 4 x 1.5V batteriesNote:Conserve all packing material until the instru-ment has been observed to function correctly.Any defective item must be returned in its original packing.HI 98127 and HI 98128 are waterproof pH and temperature meters. The housing has been completely sealed against humidity and designed to float.All pH readings are automatically temperature com-pensated (ATC), and temperature values can be displayed in °C or °F units.The meters can be calibrated at one or two points with auto-buffer recognition and against five memorized buffer values.Measurements are highly accurate with a unique sta-bility indicator right on the LCD.These meters are also provided with battery level indication at start-up, and with a low battery symbolwhich warns the user when the batteries need to bereplaced. In addition the Battery Error Prevention System (BEPS) avoids erroneous reading caused by low1. Battery compartment2. Liquid Crystal Display (LCD)3. ON/OFF/MODE button4. HI 73127 pH electrode5. Temperature sensor6. SET/HOLD buttonThese Instruments are in Compliance with CE DirectivesRecommendations for UsersBefore using this p roduct, make sure that it is entirely suitable for the environment in which it is used.The glass bulb at the end of the electrode is sensitive to electrostatic discharges. Avoid touching the glass bulb at all times.Any variation introduced by the user to the supplied equipment may degrade the instrument’s EMC per-formance.T o avoid electrical shock, do not use this instrument when voltages at the measurement surface exceed 24 VAC or 60 VDC. T o avoid damages or burns, do not perform any measurement in microwave ovens.HI 73127Replaceable pH electrode HI 73128Electrode removal toolHI 70004P pH 4.01 solution, 20 mL sachet (25 pcs)HI 70006P pH 6.86 solution, 20 mL sachet (25 pcs)HI 70007P pH 7.01 solution, 20 mL sachet (25 pcs)HI 70009P pH 9.18 solution, 20 mL sachet (25 pcs)HI 70010P pH 10.01 solution, 20 mL sachet (25 pcs)HI 77400P pH 4 & 7 solutions, 20 mL sachet (5 each)HI 7004M pH 4.01 solution, 230 mL bottle HI 7006M pH 6.86 solution, 230 mL bottle HI 7007M pH 7.01 solution, 230 mL bottle HI 7009M pH 9.18 solution, 230 mL bottle HI 7010M pH 10.01 solution, 230 mL bottleHI 7061M Electrode cleaning solution, 230 mL bottle 1. Automatic temperature compensation indicator 2. Stability indicator 3. Battery lif e percentage indicator 4. Low battery indicator 5. Secondary display ISTR98127R4 03/03US DESIGN PATENTD462,024Dear Customer,Thank you for choosing a Hanna product. This manual will provide you with the necessary informa-tion for correct operation. Please read it carefully before using the meter.If you need additional technical information, do not hesitate to e-mail us at ******************.These instruments are in compliance with the directives.Notes :• Before taking any measurements make sure the meter has been calibrated (CAL tag present on the LCD).• If measurements are taken in different samples successively, rinse the probe thoroughly to eliminate cross-contamination; and after cleaning, rinse the probe with some of the sample to be measured.For better accuracy, frequent calibration of the instru-ment is recommended. In addition, the instrument must be recalibrated whenever:a)The pH electrode is replaced.b)After testing aggressive chemicals.c)Where high accuracy is required.d)At least once a month.Calibration procedurethe calibration mode displaying “pH 7.01 USE” (or “pH 6.86 USE” if the NIST buffer set was selected).After 1 second the meter activates the automatic buffer recognition feature. If a valid buffer is detected then its value is shown on the primary display and REC appears on the secondary LCD. If no valid buffer is detected, the meter keeps the USE indication active for 12 seconds, and then it replaces it with WRNG,indicating the sample being measured is not a valid buffer.• For a single-point calibration with buffers pH 4.01,9.18 or 10.01, the meter automatically accepts the calibration when the reading is stable; the meter displays the accepted buffer, with the message “OK 1”. After 1 second the meter automatically returns to the normal measuring mode.If a single-point calibration with buffer pH 7.01 (or pH 6.86) is desired, then after the calibration point has been accepted the button is pressed, the meter shows “7.01” (or “6.86”)- “OK 1” and, after 1 second, it automatically returns to the normal measuring mode.Note : It is always recommended to carry out a two-point calibration for better accuracy.• For a two-point calibration, place the electrode in pH 7.01 (or pH 6.86) buffer. After the first calibration point has been accepted, the “pH 4.01 USE” message appears. The message is held for 12 seconds, unless a valid buffer is recognized. If no valid buffer is recog-nized, then the WRNG message is shown. If a valid buffer (pH 4.01, pH 10.01, or pH 9.18) is detected,then the meter completes the calibration procedure.When the buffer is accepted, the LCD shows the accepted value with the “OK 2” message, and then the meter returns to the normal measuring mode.Note : When the calibration procedure is completed,the CAL tag is turned on.To quit calibration and to reset to the default values• After entering the calibration mode and before the first point is accepted, it is possible to quit the procedure and return to the last calibration data by pressing the the normal measuring mode.• To reset to the default values and clear a previous calibration, press the SET/HOLD button after entering the calibration mode and before the first point is accepted. The secondary LCD displays “CLR” for 1second, the meter resets to the default calibration andthe CAL tag on the LCD disappears.The meter displays the remaining battery percentage every time it is switched on. When the battery level is below 5%, the - + symbol on the bottom left of the LCD lights up to indicate a low battery condition. The batter-ies should be replaced soon. If the battery level is low enough to cause erroneous readings, the meter shows “0%” and the Battery Error Prevention System (BEPS) will automatically turn the meter off.To change the batteries, remove the 4 screws located on the top of the meter.Once the top has been removed, carefully replace the 4batteries located in the compartment while paying atten-tion to their polarity.Replace the top, making sure that the gasket is properlyseated in place, and tighten the screws to ensure a watertight seal.• The pH electrode can be easily replaced by using the supplied tool (HI 73128). Insert the tool into the elec-trode cavity as shown below.Rotate the electrode counterclockwise.Pull the electrode out by using the other side of the tool.Insert a new pH electrode following the above instruc-tions in reverse order.• When not in use, rinse the electrode with water to minimize contamination and store it with a few drops of HI 70300 storage solution in the protective cap.DO NOT USE DISTILLED OR DEIONIZED WATER FOR STORAGE PURPOSES.• If the electrode has been left dry, soak in storage solution for at least one hour to reactivate it.• To prolong the life of the pH electrode, it is recommended to clean it monthly by immersing it in the HI 7061 cleaning solution for half an hour.Afterwards, rinse it thoroughly with tap water and recalibrate the meter.RangeResolutionAccuracy(@20°C/68°F)Typical E MC DeviationTemp. Compensation Environment CalibrationElectrode Battery Type/Life Auto-off Dimensions WeightTo turn the meter on and check the battery status Press and hold the visible for 1 second (or as long as the button is pressed), followed by the percent indication of the remaining battery life (E.g. % 100 BATT).Taking measurementsSubmerge the electrode in the solution to be tested while stirring it gently. The measurements should be taken when the stability symbol on the top left of the LCD disappears.The pH value automatically com-pensated for temperature is shown on the primary LCD while the secondary LCD shows the temperature of the sample.To freeze the displayWhile in measurement mode,press the SET/HOLD button.HOLD appears on the second-ary display and the reading will be frozen on the LCD (E.g.pH 5.78 HOLD).Press any button to return to normal mode.To turn the meter offWhile in normal mode, press the the button.Setup mode allows the selection of temperature unit and pH buffer set.To enter the Setup mode, press the TEMP and the current temperature unit (E.g. TEMP °C). Then:• fo r °C/°F selectio n : Use the SET/HOLD button.After the temperature unit has been selected, press the mode; press the • to change the calibratio n buffer set : After setting the temperature unit, the meter will show the current buffer set: “pH 7.01 BUFF” (for 4.01/7.01/10.01) or “pH 6.86 BUFF” (for NIST 4.01/6.86/9.18).Change the set with the SET/HOLD button, then press -2.0 to 16.0 pH (HI 98127)-2.00 to 16.00 pH (HI 98128)-5.0 to 60.0°C / 23.0 to 140.0°F0.1 pH (HI 98127)0.01 pH (HI 98128)0.1°C / 0.1°F ±0.1 pH (HI 98127)±0.05 pH (HI 98128)±0.5°C / ±1°F ±0.1 pH (HI 98127)±0.02 pH (HI 98128)±0.3°C / ±0.6°FAutomatic-5 to 50°C (23 to 122°F); RH 100%1 or2 points with 2 sets of memorized buffers (pH 4.01/7.01/10.01 or4.01/6.86/9.18)HI 73127 pH electrode (included )4 x 1.5V with BEPS/typical 300 hoursAfter 8 minutes163 x 40 x 26 mm (6.4 x 1.6 x 1.0”)85 g (3.0 oz)pH:Temp:pH:Temp:pH:Temp:pH:Temp:*******************1.800.561.8187。
海尔赛思泰液压器维修指南说明书
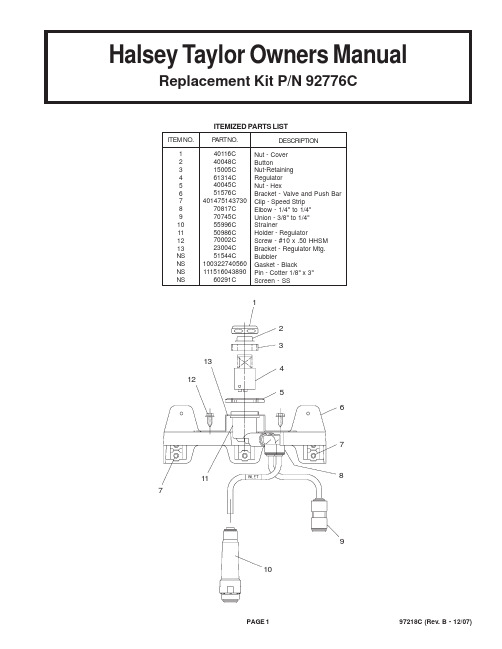
Halsey Taylor Owners ManualReplacement Kit P/N 92776C ITEMIZED PARTS LIST ITEM NO.P ART NO.DESCRIPTION40116C 40048C 15005C 61314C 40045C 51576C 40147514373070817C 70745C 55996C 50986C 70002C 23004C 51544C 10032274056011151604389060291C 12345678910111213NS NS NS NS Nut - CoverButtonNut-RetainingRegulatorNut - HexBracket - Valve and Push BarClip - Speed StripElbow - 1/4" to 1/4"Union - 3/8" to 1/4"StrainerHolder - RegulatorScrew - #10 x .50 HHSMBracket - Regulator Mtg.BubblerGasket - BlackPin - Cotter 1/8" x 3"Screen - SS711761213543211089FRONT PANEL SCREWSRECEPTORSMALLSIDEPANELS COOLERWASTELINE TRAPBUMPER SCREWS Remove two (2) bumper screws and two (2)screws mounting front panel at bottom using a5/16" and 1/4" socket or nut driver or a regularslotted screwdriver. Loosen the (2) screws hold-ing the front panel at the top. Remove the frontpanel and set asideLoosen (2) screws on upper front panel using a 5/16" socket or nut driver. Remove upper front panel. Unplug the water cooler from electricaloutlet. Shut off water supply.Removal of Existing ValveRECEPTORFLEXCOPPERTUBEFor additional access to water valve connections.Remove the eight (8) receptor mounting screws,disconnect the waste line from P-trap and unscrewthe projector. Lift the receptor. NOTE: Extreme caremust be taken not to kink the flexible copper linewhich supplies the projector.Remove (5) screws holding the black plastic regulator bracketusing a 5/16" socket or nut driver.Disconnect water inlet and outlet lines from existing water valve.Remove regulator with bracket from the water cooler. Removecotter pins from bracket and remove front push bar.If the water lines on the unit were connected to the valve with blackcompression fittings:-Remove and discard the "o"-ring and black plastic spacer-DO NOT ATTEMPT to remove the grab ring and connection nut.Attempting to remove the grab ring can damage, nick or scratch,the sealing area on the tube end.If the water lines on the unit were connected to the valve with brassflare fittings:-Cut the tubing as close to the flare as possible with a tubecutter. NOTE: Only use a tube cutter to cut the tubing so the endis square. Other tools, for example a hacksaw, could leave anexcessive burr.-Discard the cutoff end and flare nut.-De-burr the tube ends before assembling to the new valveassembly.Top view of cooler w/basin removedTop view of coolerw/basin removedConnect water inlet line, from building supply tostrainer on replacement valve assembly.Connect chiller line to super speed fitting.Installation Of New Valve AssemblyFOR PARTS, CONTACT YOUR LOCAL DISTRIBUTOR OR CALL 1.800.323.0620PRINTED IN U.S.A.2222 CAMDEN COURTOAK BROOK, IL 60523630.574.3500NOTE: WATER FLOWDIRECTION BUILDING WATER INLETSERVICE STOP(NOT FURNISHED)1/4" O.D. TUBEWATER INLETTO COOLER 3/8" O.D. UNPLATED COPPER TUBE CONNECT COLD WATER SUPPLY1. Push tubing into fitting until it reaches positivestop (approximately 3/4 inches). DO NOT SOLDERTUBES INSERTED INTO THE STRAINER ASDAMAGE TO THE O-RINGS MAY RESULT .2. To remove tubing from fitting, relieve waterpressure, push in on gray collar while pullingout on tubing.Turn on water supply and check for leaks. Install new projector and reposition receptor and drain tube to "P"-trap.Adjust water flow. Flow is adjusted by removing cover and button on valve bracket, a clockwise adjustment toscrewdriver slot increases the stream height. Reassemble cover and button. NOTE: Flow must be adjusted before push bar is installed. Install push bar on to new valve bracket. Add speed clip strip to valve bracket assembly,(row of 4 - (1) each side). Install valve bracket into unit. Reattach receptor and reconnect wate tube to "P"-trap.Connect power cord to electrical outlet. Reassemble panels and kickplate to unit.。
海尔电器维修技术手册说明书

FOR SERVICE TECHNICIAN’S USE ONL YFOR SERVICE TECHNICIAN’S USE ONL YFOR SERVICE TECHNICIAN’S USE ONL Y324FOR SERVICE TECHNICIAN’S USE ONL YT ech SheetDo not discardFOR SERVICE TECHNICIAN’S USE ONLYPRECAUTIONS TO BE OBSERVED BEFORE AND DURING SERVICING TO AVOID POSSIBLE EXPOSURE TO EXCESSIVE MICROWAVE ENERGYa. Do not operate or allow the oven to be operated with the dooropen.b. Make the following safety checks on all ovens to be servicedbefore activating the magnetron or other microwave source, and make repairs as necessary:1. Interlock Operation 2. Proper Door Closing3. Seal and Sealing Surfaces (Arcing, Wear and Other Damage)4. Damage to or Loosening of Hinges and Latches5. Evidence of Dropping or Abusec. Before turning on microwave power for any service test orinspection within the microwave generating compartments, check the magnetron, wave guide or transmission line, and cavity for proper alignment, integrity and connections.d. Any defective or misadjusted components in the interlock,monitor, door seal, and microwave generation and transmission systems shall be repaired, replaced, or adjusted by procedures described in this manual before the oven is released to the owner.e. A microwave leakage check to verify compliance with the FederalPerformance Standard should be performed on each oven prior to release to the owner.f. Do not attempt to operate the oven if the door glass is broken.FAILURE CODE INDICATIONSNOTE: Many of the problems listed in the chart below may be solved by power cycling: Unplug microwave oven or disconnect power. After 1 minute, plug in microwave oven or reconnect power.Display Likely Failure Condition Recommended Repair Procedure“Enter clock”Power failureAfter a power failure, “Enter clock” will be flashing. Press CANCEL to end this indication. The colon (:) will appear when in Standby mode.F1E4Microwave ACU failure 1. Unplug microwave oven or disconnect power.2. Replace ACU.3. Replace all parts and panels before operating.4. Plug in microwave oven or reconnect power.F2E1Stuck key failure1. Unplug microwave oven or disconnect power.2. Replace touch panel.3. Replace all parts and panels before operating.4. Plug in microwave oven or reconnect power.F4E4Humidity sensor error 1. Enter the Diagnostics mode (press CANCEL - CANCEL- START), and then press COOK TIME to display the humidity sensor reading. If display does not show “3789,” continue to Step 2. Press COOK POWER to display the RH sensor NTC reading. If display does not show “026,” continue to Step 2.2. Unplug microwave oven or disconnect power.3. Connect a new humidity sensor ACU to cable.4. Replace all parts and panels before operating.5. Plug in microwave oven or reconnect power.6. Enter the Diagnostics mode (press CANCEL - CANCEL - START), then press COOKTIME, and then press COOK POWER to see if failure code reappears.NOTE: There may be a delay (approximately 1 minute, 20 seconds) before the F4E4 failure code is displayed.7. If the F4E4 failure code reappears, unplug microwaveoven or disconnect power.8. Replace ACU.9. Replace all parts and panels before operating.10. Plug in microwave oven or reconnect power.F8E5Exhaust air templatedetection failure1. Enter the Diagnostics mode (pressCANCEL - CANCEL - START), and then press OPTIONS/CLOCK to display the exhaust air temperature sensor reading. Verify the sensor temperature reading is at room temperature (typically 50ºF to 90ºF [10ºC to 32ºC]) and verify failure code. If failure code matches complaint, continue to Step 2.2. Unplug microwave oven or disconnect power.3. Disconnect sensor from ACU.4. Measure sensor resistance between connector pinsand confirm reading is between 9.5 kΩ and 10.5 kΩ at room temperature. If measurement is not correct, or if a short or open circuit is found, replace sensor.5. Replace all parts and panels before operating.6. Plug in microwave oven or reconnect power.7. Enter the Diagnostics mode (pressCANCEL - CANCEL - START), and then pressOPTIONS/CLOCK to display the cavity temperature sensor reading. Verify the sensor temperature reading. If it is still not correct, replace ACU.8. If failure does not reappear, stop.PRIMARY , MONITOR, SECONDARY , AND DOOR INTERLOCK SWITCH CHECKOUT PROCEDURESIMPORTANT: Before checking the interlock switches, unplug microwave oven or disconnect power. Be sure to disconnect all of the wires at the switch being tested before making any continuity readings.NOTE: The Primary Interlock switch, Monitor Interlock switch, Secondary Interlock Switch, and Door Interlock Switch are mounted in the door lockswitch cradle. All the Interlock Switches can be identified by the wire colors that are connected to the terminals of the switches. See the chart below for wire color designation.SwitchCheck ByDoor OpenDoor ClosedPrimary Interlock1. Unplug microwave oven or disconnect power.2. Disconnect the wires at the Primary Interlock Switch.3. Check from the common terminal (black/brown wires) to the normally open terminal(black/white wires).4. Reconnect wires to switch.-+Monitor Interlock 1. Unplug microwave oven or disconnect power.2. Disconnect the wires at the Monitor Interlock Switch.3. Check from the common terminal (white wire) to the normally closed terminal(blue/white wires).4. Reconnect wires to switch.+-Secondary Interlock 1. Unplug microwave oven or disconnect power.2. Disconnect the wires at the Secondary Interlock Switch.3. Check from the common terminal (white/blue wires) to the normally open terminal(blue/blue wires).4. Reconnect wires to switch-+Door Interlock 1. Unplug microwave oven or disconnect power.2. Disconnect the wires at the Door Interlock Switch.3. Check from the common terminal (blue wire) to the normally closed terminal(orange wire).4. Reconnect wires to switch.+-(+) Continuity (-) No ContinuityM W O v e n R u n n i n g —A C V R e a d i n g sP i n N a m eW i r e C o l o rP o w e r O n , D o o rC l o s e dP o w e r O n , D o o r O p e nH o o d F a n M o t o r —H i g hH o o d F a n M o t o r —H i g h , D o o r O p e nH o o d F a n M o t o r —M e d -H i g hH o o d F a n M o t o r —M e d -H i g h , D o o r O p e nH o o d F a n M o t o r —M e d i u mH o o d F a n M o t o r —M e d i u m , D o o r O p e nH o o d F a nM o t o r —L o wH o o d F a n M o t o r —L o w , D o o r O p e nH o o d L i g h t —H ig hH o od L i g h t —H i g h , D o o r O pe nH o o d L i g h t —L o wH o o d L i g h t —L o w , D o o r O p e nM W O v e n S t a r t P1-1 (L)Brown 120120120120120120120120120120120120120120120P1-3 (N)White 00 0000000000000P2-3 (NFS)White 0120012001200120012001200120 3.6P2-2 (Door)Orange 012001200120012001200120012049P2-1 (N)Green 000000000000000P4-4 (HF)White 01200120012001200120012000120P4-5 (TTM)Red 0120012001200120012001200120120P4-1 (HL)Yellow 00000000001201206767 2.4P4-2 (HF-R)Gray 00120120120120585877770000 3.6P4-3 (HF-Hi)Black001201206868585839390000 3.7P4-6 (CL)Green151151120120555577773.7CONNECTORS ON ACUTOUCH P ANELT ouch Panel and ACU T estThe microwave hood combination is provided with a self-diagnostic routine that can be accessed through the touch keypad.T o initiate this routine:1. Plug in microwave oven or reconnect power, and press CANCEL tostandby (“:”).2. Close door, then press CANCEL - CANCEL - START within3 seconds.3. All display segments will be lit to indicate the Test mode has beenentered.NOTE: If CANCEL is pressed during this diagnostic routine, you will exit the Test mode.ACU21P41 2 3 4 5 6Relay 4903P11 3L N.P91 2P111 2 3 4P6 3 2 1P21 2 3P3 14 13 12 11 10 9 8 7 6 5 4 3 2 1P71234567891011Relay 490321NOTE: There are purposely emptyterminals between each of the numbered terminals on P1 connector.W11268419ANOTE: These diagrams are not intended to show a complete circuit; they represent the position of switches during “DOOR OPEN” or “DOOR CLOSED” (continuity checks only).NOTE: Interlock, Monitor switches and Door interlock switch cannot be adjusted and all these switches should be replaced if any one of them is found to be defective. After replacing interlock/monitor switches, reconnect wires to switch and check for continuity. Safety interlocks and monitor switches will actuate within 2 mm.Door ClosedDoor OpenNOT HEATING TROUBLESHOOTING INSTRUCTIONIMPORTANT: High-voltage is present at the magnetron and high-voltage capacitor terminals. Avoid direct contact when power is connected to these components to avoid serious injury or possible death. Always be sure that the high-voltage capacitor is discharged before accessing any of these components.For a no-heat condition, refer to the following step-by-step instructions:1. Unplug microwave oven or disconnect power.2. Discharge the high-voltage capacitor.3. Disconnect the high-voltage transformer primary windings.4. Attach the voltmeter leads to the high-voltage transformer primaryinput wires.5. Plug in microwave oven or reconnect power.6. Close door and program the microwave oven to operate for30 seconds.7. Press START.8. Check the input voltage at the high-voltage transformer primary inputwires. If the voltage is not close to the rating voltage 120 +/-15 VAC, unplug microwave oven or disconnect power. Check the circuitry as follows:■Measure resistance of the fuse, microswitches and thermostats. Replace any failed components. (Refer to the wiring diagram.)■Check for loose terminals. (Refer to the wiring diagram.) Check all of the terminals on the main route from the power supply to the high-voltage transformer.■Check for loose or failed connectors on the ACU (P1, P2, P4). Ifthese check out OK, plug in microwave oven or reconnect power. ■Check for ACU failure. Refer to the “ACU Pin Voltage Matrix” section.9. If the input voltage at the high-voltage transformer primary inputwires is close to the rating voltage 120 +/-15 VAC, unplug microwave oven or disconnect power.10. Check the power supply components. Refer to the “ComponentTests” section.■High-voltage transformer ■High-voltage capacitor■High-voltage diode11. If the power supply components check out OK, check the connectionbetween the magnetron and the high-voltage transformer.12. If all of the components check out OK, replace the magnetron.13. Reconnect the high-voltage transformer primary windings.ACU PIN VOLTAGE MATRIXCheck for proper voltage by completing the following steps:1. Unplug microwave oven or disconnect power.2. Connect voltage measurement equipment to the terminals listedbelow. (P1-3 and P2-3 are neutral.) 3. Plug in microwave oven or reconnect power, and confirm voltagereading.4. Unplug microwave oven or disconnect power.NOTE: For 50 V and over, the tolerance is +/-15 V . For 0 V , the tolerance is +/-3 V .AbbreviationsHL – Hood LightN – NeutralCL – Cavity LightHF – Hood FanL – Line VoltageTT – Turntable MotorNFS – Neutral for SwitchNOTE: When checking voltage readings on ACU, connect the grounding test lead of voltmeter to P1-3, P2-1. Use the positive test lead to probe connectors designated below.Door Interlock SwitchSecondary Interlock Switch(NO)Interlock SwitchDoor Interlock SwitchMW Oven Plugged In—Sitting Idle—ACV ReadingsFOR SERVICE TECHNICIAN’S USE ONL Y FOR SERVICE TECHNICIAN’S USE ONL YFOR SERVICE TECHNICIAN’S USE ONL Y FOR SERVICE TECHNICIAN’S USE ONL Y 57608/18FOR SERVICE TECHNICIAN’S USE ONLYW11268419A©2018 All rights reserved.Components Test/ResultsH.V. Transformer 1. Unplug microwave oven or disconnect power.2. Remove wire leads.3. Measure resistance:■Primary winding: Less than 0.5 ohm (approximate)■Secondary winding: 120 ohms (approximate)■Filament winding: 0 ohms■Primary winding to grounding: Normal: Infinite■Filament winding to grounding: Normal: InfiniteMagnetron 1. Unplug microwave oven or disconnect power.2. Remove wire leads.3. Measure resistance:■Filament terminal: Normal: Less than 1 ohm■Filament to chassis: Normal: InfiniteH.V. Capacitor 1. Unplug microwave oven or disconnect power.2. Remove wire leads.3. Measure resistance:■Terminal to terminal: Normal: Momentarily indicates several ohms and then gradually returns toinfinite.■Terminal to case: Normal: InfiniteH.V. Diode NOTE: Some inexpensive meters may indicate infinite resistance in both directions.1. Unplug microwave oven or disconnect power.2. Measure resistance:■Forward: Normal: Continuity■Reverse: Normal: InfiniteTurntable Motor 1. Unplug microwave oven or disconnect power.2. Remove wire leads.3. Measure resistance:■Normal: 2.4k to 3.2k ohms (approximate)Motor Capacitor 1. Unplug microwave oven or disconnect power.2. Remove wire leads.3. Measure motor capacitor:■Normal: Momentarily 0 ohms, then goes to infinite1. Unplug microwave oven or disconnect power.2. Remove the 4-pin connector from the cable.3. Measure resistance across pins 1 and 2.■Normal: 10k ohms +/-5% at 77°F (25°C)4. Measure capacity value across pins 3 and 4.■Normal: 180pF +/-5% at 55% RHHood Exhaust Fan Motor 1. Unplug microwave oven or disconnect power.2. Remove wire leads.3. Measure resistance:■High Speed—Normal: Red (RD) and Blue (BU) wires: 70 to 100 ohms (approximate); Blue (BU) andBlack (BK) wires: 30 to 60 ohms (approximate)■Low Speed—Normal: Red (RD) and Blue (BU) wires: 70 to 100 ohms (approximate); Blue (BU) andWhite (WH) wires: 50 to 80 ohms (approximate)HF NTC Thermistor 1. If “NTC SHORT, CALL FOR SERVICE” or “NTC OPEN, CALL FOR SERVICE” scrolls on display, unplugmicrowave oven or disconnect power.2. Measure resistance:■Normal: 10k ohms +/-5% at 77ºF (25ºC)Power Resistor 1. Unplug microwave oven or disconnect power.2. Remove wire leads.3. Measure resistance:■Normal: 65 ohms/65 WPrimaryFilament(orange/red wires)Secondary (whitewire - ground totransformer case)23Components Test/ResultsCooling Fan Motor 1. Unplug microwave oven or disconnect power.2. Remove wire leads.3. Measure resistance:■Normal: 40 to 60 ohms (approximate)AC Line Filter Board 1. Unplug microwave oven or disconnect power.2. Remove wire leads.3. Measure resistance:■Normal: L-IN to L-OUT (coil): Less than 1 ohm; N-IN to N-OUT (coil): Less than 1 ohmThermostats NOTE: Refer to “Parts Layout” for opening and closing temperatures.1. Unplug microwave oven or disconnect power.2. Remove wire leads.3. Measure continuity:■Normal: ContinuitySCHEMATIC DIAGRAMCavity ThermostatMagnetron ThermostatCavityzH6V521/V21CAKey T ables for T est ModeKey Name Function Display BuzzerPopcorn-key 30 1 beepPotato orBaked Potato-key 31 1 beepVegetable-key 2E 1 beepFrozen Entrée-key 33 1 beepSteam Simmeror Steam Cook-key 2D 1 beepWarm Hold-key 06 1 beepReheat-key 24 1 beepDefrost-key 25 1 beepSoften/Melt-key 29 1 beepCook Time Humidity sensorcheckValue between2000 and 60001 beepCook Power RH NTC sensorcheckValue between10 and 401 beepCook key 07 1 beepTimer Set/Off-key 05 1 beepOptions/Clock HF NTC Thermistor XXX 1 beepStart or Software/Geeversion check*xx.xx.xx 1 beepAdd 30 Sec or +30Sec key 20 1 beepDinner Plate-key 32 1 beepBeverage-key 34 1 beepPizza-key 35 1 beep* Continuously pressing START or will respectively display SW Versionand Gee Version for each press.Key Name Function Display Buzzer1Cavity Light andCooling Fan OnCL 1 beep2Cavity Light, CoolingFan and Turntable OnCL TT 1 beep3-key 36 1 beep4-key 14 1 beep5-key 15 1 beep6Hood (Cooktop) LightOn (High)HL HIGH 1 beep7Hood (Cooktop) LightOn (Low)HL LOW 1 beep8Vent Fan On (HighSpeed)HF HIGH 1 beep9Vent Fan On (LowSpeed)HF LOW 1 beep0Microwave Oven(1000 W), CL, TT andCF On for 10 SecondsMW 1 beepLight or -key 03 1 beepTurntable -key 09 1 beepPOWER OUTPUT MEASUREMENTThe power output of the magnetron can be measured using the following“Voltage Measurement” and “Output Test” sections. Before you performthe test:■Make sure that the oven cavity is cool and clean.■Check the line voltage at the wall outlet while microwave oven isoperating. See the “Voltage Measurement at Power Source” section.T ools Needed■2-cup measuring cup■Thermometer■Voltmeter/ohmmeterVoltage Measurement at Power Source1. Fill the measuring cup with 2 cups (500 mL) of tap water.2. Place in the center of the microwave oven cavity.3. Operate the microwave oven on High speed for 1 minute.4. While the microwave oven is operating, measure the line voltage atthe power source. See “Measure Voltage” illustration.5. Verify the voltage is constant during microwave oven operation. Ifvoltage drops below 108V, contact a qualified electrician to checkyour electrical supply.6. Make note of the voltage while the microwave oven is running andproceed to the output test.Measure VoltageOutput T est1. Fill the measuring cup with 2 cups (500 mL) of 70ºF (21ºC) tap water.2. Stir the water with the thermometer to ensure uniform temperature.Add warm or cool water to bring the water to the correct temperature.3. Place the measuring cup in the center of the microwave oven cavity.4. Operate the microwave oven on High speed for 1 minute.5. Remove the measuring cup and stir the water with the thermometerfor about 20 seconds.6. Record the temperature of the water.7. Refer to the model serial tag on the microwave oven to acquirewattage output rating of the microwave oven.8. Using the following chart, determine if the output of the microwaveoven is within the range listed based on the line voltage and wattagerating of the microwave oven.Water Temperature for Line Voltage and Wattage RatingVoltage700 W1000 W1200 W120 V96ºF to 102ºF(36ºC to 39ºC)110ºF to 116ºF(43ºC to 47ºC)124ºF to 130ºF(51ºC to 54ºC)108 V91ºF to 97ºF(33ºC to 36ºC)101ºF to 107ºF(38ºC to 42ºC)111ºF to 117ºF(44ºC to 47ºC)COMPONENT TESTSAA. House power supply wall outletB. Voltmeter/Ohmmeter test leadsC. Microwave oven plugP ARTS LA YOUT (NOT TO SCALE)A. Line fuse (20 amp)B. AC line filter boardC. Hood fan motor assemblyD. Cavity lightE. Cavity light holderF. MagnetronG. Magnetron thermostat—opens at 257ºF (125ºC), closesat 185ºF (85ºC)H. Power resistorI. H.V. capacitorJ. H.V. diodeK. H.V. transformerL. Motor capacitorM. Cooling fan motorN. HF NTC thermistorO. ACUP. Touch panelQ. Secondary interlock switchR. Door interlock switchS. Monitor interlock switchT. Primary interlock switchU. Turntable motorV. Hood (cooktop) lightW. Hood (cooktop) light holderX. Cavity thermostat—opens at 257°F (125°C), non-resettableY. Humidity sensor ACUIMPORTANT:■Unplug microwave oven or disconnect power.■Discharge the high-voltage capacitor and remove thelead wires from the primary winding of the high-voltagetransformer before conducting any of the following tests.■Remove the lead wires from the related component beforeconducting any of the following tests.■All operational checks using microwave energy must be donewith the microwave oven loaded with a minimum of 8 oz(250 mL) of water in a microwave-safe container.■Conduct a microwave energy test after performing any testsor repairs to the microwave oven.■Check that all wire leads are in the correct positions beforeoperating the microwave oven.■Grasp wire connectors when removing the wire leads frommicrowave oven parts.■All testing must be done with an ohmmeter having asensitivity of 20,000 ohms per volt DC or greater andpowered by at least a 9 V battery.。
Parker Hannifin Canada电子控制设备分部硬件用户手册说明书

PHK User Manual Hardware ManualEffective: November 2021units=mm4X R7.3107.5OFFER OF SALEThe items described in this document are hereby offered for sale by Parker-Hannifin Corporation, its subsidiaries or its authorized distributors. This offer and its acceptance aregoverned by the provisions stated in the detailed “Offer of Sale” elsewhere in this document or available at .Parker Hannifin Corporation Electronic Motion and Controls Division 850 Arthur Ave Elk Grove Village, IL 60007phone 800 221 /emcCopyright 2022 © Parker Hannifin Corporation. All rights reserved. No part of this work may be reproduced, published, or distributed in any form or by any means (electronically, mechanically, photocopying, recording, or otherwise), or stored in a database retrieval system, without prior written permission of Parker Hannifin Corporation in each instance.Rev. 003Inserting additional CAN messagesSafetyDo not perform the procedures in this manual unless you are experienced in the handling of electronic equipment. Contact the manufacturer if there is anything you are not sure about or if you have any questions regarding the product and its handling or maintenance. The term "manufacturer" refers to Parker Hannifin Corporation.The following symbols are used in this document to indicate potentially hazardous situations:Danger! Risk of death or injury.Warning! Risk of damage to equipment or degradation of signal.When you see these symbols, follow the instructions carefully and proceed with caution.Work on the hydraulics control electronics may only be carried out by trained personnel who are well- acquainted with the control system, the machine, and its safety regulations.Follow the manufacturer's regulations when mounting, modifying, repairing, and maintaining equipment. The manufacturer assumes no responsibility for any accidents caused by incorrectly mounted or incorrectly maintained equipment. The manufacturer assumes no responsibility for the system being incorrectly applied, or the system being programmed in a manner that jeopardizes safety.Do not use the product if electronic modules, cabling, or connectors are damaged or if the control system shows error functions.Electronic control systems in an inappropriate installation and in combination with strong electromagnetic interference fields can, in extreme cases, cause an unintentional change of speed of the output functionThis product can expose you to chemicals known to the State of California to cause birth defects or other reproductive harm. For more information go to If welding is required for installation, complete as much as possible of the welding work before the installation of the system. If welding must be done afterwards, proceed as follows:Do not place the welding unit cables near the electrical wires of the controlsystemIf sensor has been installed and additional welding is required, remove the 4-pin connector from the sensor to avoid possible electrical damage to sensor1.Disconnect the electrical connections between the system and externalequipment2.Disconnect the negative cable from the battery3.Disconnect the positive cable from the battery4.Connect the welder's ground wire as close as possible to the place of the weldingSafety SymbolsGeneral Safety RegulationsWelding After InstallationSafety continuedThe vehicle must be equipped with an emergency stop which disconnects the supply voltage to the control system's electrical units. The emergency stop must be easily accessible to the operator. If possible, the machine must be built so that the supply voltage to the control system's electrical units is disconnected when the operator leaves the operator’s station.Incorrectly positioned or mounted cabling can be influenced by radio signals, which can interfere with the functions of the system.Danger! Risk of death or injury. Do not start the machine’s engine before the control system is mounted and its electrical functions have been verified.Do not start the machine if anyone is near the machine.Before performing any work on the hydraulics control electronics, ensure thatThe machine cannot start movingFunctions are positioned safelyThe machine is turned offThe hydraulic system is relieved from any pressureSupply voltage to the control electronics is disconnectedConstruction RegulationsSafety During InstallationSafety During Start-UpSafety During Maintenance and Fault DiagnosisThe PHK Keypads come in three sizes: 2x3, 2x4 and 3x4 buttons, with CAN interface and indicator LEDs.2X3 Keypad2X4 Keypad3X4 KeypadConnectors and PinoutsSpecificationsCAN Keypad SpecificationsThe connector on the rear panel for the PHK Keypads are Deutsch DT06 Series ConnectorsThe pins in the Deutsch DT06 connectors connect to power and CAN. The following tables show the pinouts for each connector:CommunicationAuxiliary Input/Output - Status #1PGN: 65241 hex: 0FED9DescriptionThis message is broadcast periodically or on change of state to indicate the statusThe connector The PHK keypads support CAN bus communication. The default protocol is SAE J1939 format. The PHK have 1 CAN port.The default PHK CAN messages are shown belowS o u r c e A d d r e s s P H K 12: 0x C 0 P H K 6: 0x C 1 P H K 8:0x C 2Auxiliary Input/Output - Status #2 PGN: 42752 hex: 0A700Blacklight IntensityModel StatusThe Keypad module uses the J1939 Cab Illumination message to control the keypad icon backlighting. The message Data Field contains the desired intensity.The Keypad module uses a Proprietary J1939 message to broadcast system health.Module ConfigurationAll module configuration is performed using the Proprietary-A CAN message, PGN 61184 (0xFE00). The message Data Field will contain the configuration command function, action to be taken and any parameter data. All configuration commands must be sent from Service Tool Source Address 249 (0xF9).Upon receiving a Configuration Message, the module will attempt to execute the operation and then will return the Configuration Message with the Function Extension configured to convey the status of the operation. The service tool must wait for this message to be returned before the module will be ready to accept another Configuration Message.Appendix 1: Suspect Parameter Numbers (SPN)SPN 520192 – Function Byte Data Field position: Byte 1, 8 bits Used to define the configuration function is to performNotes:1. Must be a valid PGN 2. Valid range is 10-60000 milliseconds. Use 0xFFFF for no change. Use 0 to disable periodic transmissions.3. Valid range is 0-3000 milliseconds. This value will delay the initial transmission. Used to stagger messages having the same transmit rate.SPN 520193 Action ByteData Field position: Byte 2, 8 bitsUsed to define the action the function is to performSPN 520202 Module StatusData Field position: Byte 1, 16 bitsUsed to report module supply voltageRange: 0x0000-0x8CA0 (0-36000) expressed as 0.0-36000 mV 1 mV / bit Data Field position: Byte 3, 16 bitsUsed to report Module core temperatureRange: 0x0000-0x03E8 (0-1000) expressed as millivolts 0.1 °C / bitSPN 520207 16-bit Output CAN Timeout ParametersData Field position: Byte 5, 16 bitsUsed to set the output timeout in the event of lost CAN command messages.Range: 0x0001-0xFFDC (1-65500) expressed as 0.01-655 Sec 10 mS / bit Range: 0x0000 Timeout Feature DisabledRange: 0xFFFF Leaves value unchangedData Field position: Byte 7, 16 bitsUsed to set the output state in the event of a timeout0x00 = Turn OFF output, 0x01 = Turn ON output, 0xFF = UnchangedSPN 520208 16-bit CAN Transmission ParametersData Field position: Byte 3, 16 bitsUsed to identify the PGN of the messageRange: 0xFF40-0xFF62 (PGN 65344-65378)Data Field position: Byte 5, 16 bitsUsed to set the transmission interval of the messageRange: 0x000A-0xEA60 (10-60000) 1 mS / bittransmissionRange:0x0000 DisablesRange: 0xFFFF Leaves value unchangedData Field position: Byte 7, 16 bitsUsed to set the offset or stagger for many messages with same interval.Range: 0x0000-0x0BBF (0-3000) 1 mS / bitRange: 0xFFFF Leaves value unchangedAppendix 2: Typical Configuration Sequence* EXTENDED CAN ID - Assumes message priority = 0, module address = 0xC0. Command source address must be 0xF9. Tx = message sent from service tool to module, Rx = reply sent from module back to service tool. Tx: Command to Enter Configuration ModeExt ID *DLC Byte 1Byte 2Byte 3Byte 4Byte 5Byte 6Byte 7Byte 8 0xEFC0F980x100xFF0xF90xC00x440x550x660x77 Byte 1: 0x10 = Function (Enter Configuration Mode)Byte 2: 0xFF = Sub-command (none)Byte 3: 0xF9 = Service tool AddressByte 4: 0xC0 = Module AddressByte 5-8 0x77665544 = security key (low byte first)RX Reply:Ext ID *DLC Byte 1Byte 2Byte 3Byte 4Byte 5Byte 6Byte 7Byte 8 0xEFF9C080x100x120xF90xC0n/a n/a n/a n/a Byte 1: FunctionByte 2: Success = 0x12 (Three LEDs above Key 1 will light, center LED flashing)Tx: Command to Change Module Source AddressExt ID *DLC Byte 1Byte 2Byte 3Byte 4Byte 5Byte 6Byte 7Byte 8 0xEFC01980x200x110xFF0xC10xFF0xFF0xFF0xFF Byte 1: 0x20 = Function (J1939 Source Address)Byte 2: 0x11 = Sub-command (Write)Byte 3: 0xFFByte 4: 0xC1 = New Address (Desired Address)RX Reply:Ext ID *DLC Byte 1Byte 2Byte 3Byte 4Byte 5Byte 6Byte 7Byte 8 0xEFF9C080x200x120xFF0xC10xFF0xFF0xFF0xFF Byte 1: FunctionByte 2: Success = 0x12 (NOTE: New Address will not take effect until you save and exit configuration)O O OTx: Additional configuration commandsRx: ReplyO O OTx: Command to Save Configuration and Exit to Run ModeExt ID *DLC Byte 1Byte 2Byte 3Byte 4Byte 5Byte 6Byte 7Byte 8 0xEFC0F980x110xFF0xF90xC00x440x550x660x77 Byte 1: 0x11 = Function (Exit Configuration Mode)Byte 2: 0xFF = Sub-command (none)Byte 3: 0xF9 = Service tool AddressByte 4: 0xC0 = Current Module AddressByte 5-8 0x77665544 = security key (low byte first)Manual PHK 11/2022 © 2022 Parker Hannifin CorporationParker Hannifin CorporationElectronic Motion and Controls Division850 Arthur AveElk Grove Village, IL 60007phone 800 221 9257/emc。
Minuteman X17 ECO EXTRACTOR 零件手册说明书

For Safety When Servicing or Maintaining Machine• Stop on level surface.• Disconnect the power to the machine.• Avoid moving parts. Do not wear loose jackets, shirts, or sleeves when working on machine.• When working around machine use protective clothing and safety glasses. Remove metal jewelry.• Do not clean machine with a pressure washer.• Authorized personnel must perform repairs and maintenance. Use Minuteman supplied replacement parts.Table of ContentsX17 ECO Extractor Main Assembly I Rear View (1)X17 ECO Extractor Main Assembly BOM (2)Solution Tank Assembly Front View (3)Solution Tank Assembly Rear View (4)Solution Tank Assembly BOM (5)Recovery Tank Assembly (6)Recovery Tank Assembly BOM (7)Recovery Dome Lid Assembly (8)Spray Bar Assembly, X17 (9)X17 ECO Handle Assembly (10)X17 ECO Handle Assembly BOM (11)X17 ECO Handle Assembly Breakout (12)Back Panel Assembly (13)Chassis Sub-Assembly X17-ECO (14)Chassis Sub-Assembly X17-ECO BOM (15)Brush Head Assembly ECO (16)Brush Head Assembly ECO BOM (17)Valve-Filter Assembly, X17 (18)Wiring Schematic 115V, Handle Assembly X17-ECO (19)Wiring Schematic 115V, Wire Harness X17-ECO (20)X17-ECO 115V Electrical Schematic Reference Numbers (21)Wiring Schematic 230V, Handle Assembly X17-ECO (22)Wiring Schematic 230V, Wire Harness X17-ECO (23)X17-ECO 230V Electrical Schematic Reference Numbers (24)X17 ECO Extractor Main Assembly I Rear ViewX17 ECO Extractor Main Assembly BOMRecovery Tank AssemblyRecovery Tank Assembly BOMRecovery Dome Lid AssemblyX17 ECO Handle AssemblyX17 ECO Handle Assembly BOMBack Panel AssemblyChassis Sub-Assembly X17-ECOBrush Head Assembly ECOBrush Head Assembly ECO BOMX17-ECO 115V Electrical Schematic Reference NumbersX17-ECO 230V Electrical Schematic Reference NumbersMinuteman International, Inc. warrants to the original purchaser/user that the product is free from defects in workmanship and materials under normal use. Minuteman will, at its option, repair or replace without charge, parts that fail under normal use and service when operated and maintained in accordance with the applicable operation and instruction manuals. All warranty claims must be submitted through and approved by factory authorized repair stations.This warranty does not apply to normal wear, or to items whose life is dependent on their use and care, such as belts, cords, switches, hoses, rubber parts, electrical motor components or adjustments. Parts manufactured by Minuteman are covered by and subject to the warranties and/or guarantees of their manufacturers. Please contact Minuteman for procedures in warranty claims against these manufacturers.Special warning to purchaser — Use of replacement filters and/or prefilters not manufactured by Minuteman or its designated licensees, will void all warranties expressed or implied. A potential health hazard exists without original equipment replacement.All warranted items become the sole property of Minuteman or its original manufacturer, whichever the case may be.Minuteman disclaims any implied warranty, including the warranty of merchantability and the warranty of fitness for a particular purpose. Minuteman assumes no responsibility for any special, incidental or consequential damages.This limited warranty is applicable only in the U.S.A. and Canada, and is extended only to the original user/purchaser of this product. Customers outside the U.S.A. and Canada should contact their local distributor for export warranty policies. Minuteman is not responsible for costs or repairs performed by persons other than those specifically authorized by Minuteman. This warranty does not apply to damage from transportation, alterations by unauthorized persons, misuse or abuse of the equipment, use of non-compatible chemicals, or damage to property, or loss of income due to malfunctions of the product.If a difficulty develops with this machine, you should contact the dealer from whom it was purchased.This warranty gives you specific legal rights, and you may have other rights which vary from state to state. Some states do not allow the exclusion or limitation of special, incidental or consequential damages, or limitations on how long an implied warranty lasts, so the above exclusions and limitations may not apply to you.Cord Electric Group: Three years parts, two years labor, ninety days travel (Not to exceed two hours)Exceptions……….Model Parts Labor Poly TravelPort A Scrub1yr6months10yrs0MPV 131yr000MPV 14 & 182yrs1yr00V Series Upright Vacuums1yr1yr00Rapid Air Blower1yr1yr10yrs0Explosion Proof Vacuum1yr1yr00X12, X12H & TRS 141yr1yr10yrs0E17 & E20 Electric Scrubbers1yr6month10yrs0Pneumatic Vacuums3yr1yr00Description Parts Labor Poly TravelBattery Operated Group 3yrs 2yrs 10 90 daysSweepers 1yr 1yr 10 90 daysInternal Combustion Group 1yr 1yr 10 90 daysNot to exceed two hoursException: PAS 14B 1yr 1yr 10yr 0Battery Chargers: One year replacementReplacement Parts: Ninety daysBatteries: 0-3 months replacement, 4-12 months pro-ratePolyethylene Plastic Tanks: Tanks have 10yr warranty, no additional labor。
威斯汀顿水暖电器维修手册说明书
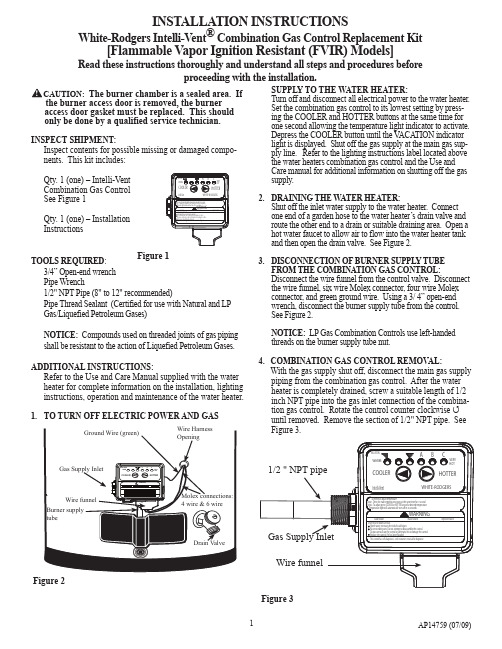
The burner chamber is a sealed area. Ifaccess door gasket must be replaced. This should only be done by a qualified service technician.INSPECT SHIPMENT:Inspect contents for possible missing or damaged compo-nents. This kit includes:Qty. 1 (one) – Intelli-Vent Combination Gas Control See Figure 1Q ty. 1 (one) – Installation InstructionsTOOLS REQUIRED : 3/4” Open-end wrench Pipe Wrench1/2" NPT Pipe (8" to 12" recommended)Pipe Thread Sealant (Certified for use with Natural and LP Gas/Liquefied Petroleum Gases)NOTICE: Compounds used on threaded joints of gas piping shall be resistant to the action of Liquefied Petroleum Gases.ADDITIONAL INSTRUCTIONS:Refer to the Use and Care Manual supplied with the water heater for complete information on the installation, lighting instructions, operation and maintenance of the water heater.1. TO TURN OFF ELECTRIC POWER AND GASSUPPLY TO THE WATER HEATER:Turn off and disconnect all electrical power to the water heater. Set the combination gas control to its lowest setting by press-ing the COOLER and HOTTER buttons at the same time for one second allowing the temperature light indicator to activate. Depress the COOLER button until the V ACA TION indicator light is displayed. Shut off the gas supply at the main gas sup-ply line. Refer to the lighting instructions label located above the water heaters combination gas control and the Use and Care manual for additional information on shutting off the gas supply.2. DRAINING THE W ATER HEATER:Shut off the inlet water supply to the water heater. Connect one end of a garden hose to the water heater’s drain valve and route the other end to a drain or suitable draining area. Open a hot water faucet to allow air to flow into the water heater tank and then open the drain valve. See Figure 2.3. DISCONNECTION OF BURNER SUPPLY TUBE FROM THE COMBINATION GAS CONTROL:Disconnect the wire funnel from the control valve. Disconnect the wire funnel, six wire Molex connector, four wire Molex connector, and green ground wire. Using a 3/ 4” open-end wrench, disconnect the burner supply tube from the control. See Figure 2.NOTICE: LP Gas Combination Controls use left-handed threads on the burner supply tube nut.4. COMBINATION GAS CONTROL REMOV AL:With the gas supply shut off, disconnect the main gas supply piping from the combination gas control. After the water heater is completely drained, screw a suitable length of 1/2 inch NPT pipe into the gas inlet connection of the combina-tion gas control. Rotate the control counter clockwise 4 until removed. Remove the section of 1/2" NPT pipe. See Figure 3.INSTALLATION INSTRUCTIONSWhite-Rodgers Intelli-Vent ® Combination Gas Control Replacement Kit[Flammable Vapor Ignition Resistant (FVIR) Models]Read these instructions thoroughly and understand all steps and procedures beforeproceeding with the installation.1AP14759 (07/09)Figure 1Figure 35. INTELLI-VENT® COMBINATION GAS CONTROLINSTALLATION:Ensure the replacement combination gas control is correct for the gas usage of the water heater. Hand start threading the control into the water heater. Install the suitable length of 1/2 inch NPT pipe previously used to the gas inlet of new control. Rotate the control by turning clockwise 3 until the control is tight and in the upright position.6. CONNECTION OF BURNER SUPPLY TUBE, MOLEXCONNECTORS AND GROUND WIRES:Install the inverted flare end of the burner supply tube into the combination gas control. Hand thread the hex nut fittingon the burner supply tube into the control. Ensure that the fitting is properly aligned with the control, otherwise cross threading of the connection will occur. Tighten the fitting using a ¾” open-end wrench. Thread the Molex connectors through the wire funnel. Connect the four (4) wire Molex connector to the four (4) pin connector on the bottom of the control. Connect the six (6) wire Molex connector to the six(6) pin connector on the bottom of the control. Connect thewire funnel to the control valve. Connect the green ground wire to the electricial connector on the side of the control.See Figure 2.7. CONNECTION OF THE MAIN GAS SUPPLY TO THECOMBINATION GAS CONTROL:Reconnect the main gas supply piping to the combinationgas control. Use pipe thread sealant certified for use withNatural and LP Gas/Liquefied Petroleum Gases.NOTICE:Compounds used on threaded joints of gas pip-ing shall be resistant to the action of liquefied petroleumgases.8. REFILLING THE WATER HEATER:Disconnect the garden hose from the water heater’s drainvalve. Close the drain valve and turn on the inlet watersupply to the water heater. Open all hot water faucets toallow all trapped air to escape. Let the water heater fill untila steady stream of water is observed coming from all hotwater faucets then close all faucets.9. TURN ON ELECTRIC POWER AND GAS SUPPLYTO THE WATER HEATER:Reconnect the electrical power to the water heater. Turn on the main electrical power and gas supply to the water heater.Check for leaks on the inlet supply piping using a soap and water solution.NOTICE: If the soap and water solution bubbles up, there is a leak and the inlet gas supply piping must be tightened and checked again.10. LIGHTING AND OPERATION INSTRUCTIONS:Follow the “FOR YOUR SAFETY READ BEFOREOPERATING” and “LIGHTING INSTRUCTIONS” on the label(s) affixed above the combination gas control.With the main burner in operation, use a soap and watersolution to check for gas leaks at the burner supply tubeconnections.NOTICE: If the soap and water solution bubbles up, thereis a leak and the fittings must be tightened and checkedagain.IMPORTANT: If the leak(s) cannot be eliminated, turn off the electrical power and gas supply to the water heater, andcontact the water heater manufacturer at 1-800-432-8373.:ANGER: Hotter water increases the potential for HotA temperature setting of 120° F (49°C) or less is recom-mended as a useable water temperature.Set the combination gas control to its lowest setting bypressing the COOLER or HOTTER buttons at the sametime for one second allowing a temperature light indicatorto activate. Depress the COOLER or HOTTER button until the 120°F ternperature indicator light is displayed.The illustration in Figure 4 shows the recommended tem-perature setting.2Figure 4VACATIONWARNINGVERYHOTWARMA B CCOOLER HOTTER。
美国机器与工具公司产品维修部件手册.pdf_1719188513.1075773说明书
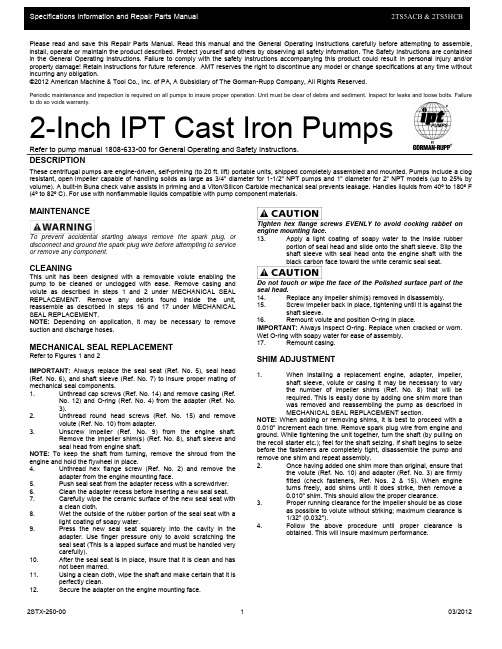
2STX-250-00103/2012Please read and save this Repair Parts Manual. Read this manual and the General Operating Instructions carefully before attempting to assemble, install, operate or maintain the product described. Protect yourself and others by observing all safety information. The Safety Instructions are contained in the General Operating Instructions. Failure to comply with the safety instructions accompanying this product could result in personal injury and/or property damage! Retain instructions for future reference . AMT reserves the right to discontinue any model or change specifications at any time without incurring any obligation.©2012 American Machine & Tool Co., Inc. of PA, A Subsidiary of The Gorman-Rupp Company, All Rights Reserved.Periodic maintenance and inspection is required on all pumps to insure proper operation. Unit must be clear of debris and sediment. Inspect for leaks and loose bolts. Failure to do so voids warranty.2-Inch IPT Cast Iron PumpsRefer to pump manual 1808-633-00 for General Operating and Safety Instructions.DESCRIPTIONThese centrifugal pumps are engine-driven, self-priming (to 20 ft. lift) portable units, shipped completely assembled and mounted. Pumps include a clog resistant, open impeller capable of handling solids as large as 3/4" diameter for 1-1/2" NPT pumps and 1" diameter for 2" NPT models (up to 25% by volume). A built-in Buna check valve assists in priming and a Viton/Silicon Carbide mechanical seal prevents leakage. Handles liquids from 40º to 180º F (4º to 82º C). For use with nonflammable liquids compatible with pump component materials.MAINTENANCETo prevent accidental starting always remove the spark plug, or disconnect and ground the spark plug wire before attempting to service or remove any component. CLEANING This unit has been designed with a removable volute enabling the pump to be cleaned or unclogged with ease. Remove casing and volute as described in steps 1 and 2 under MECHANICAL SEAL REPLACEMENT. Remove any debris found inside the unit, reassemble as described in steps 16 and 17 under MECHANICAL SEAL REPLACEMENT. NOTE: Depending on application, it may be necessary to removesuction and discharge hoses.MECHANICAL SEAL REPLACEMENTRefer to Figures 1 and 2IMPORTANT: Always replace the seal seat (Ref. No. 5), seal head (Ref. No. 6), and shaft sleeve (Ref. No. 7) to insure proper mating of mechanical seal components. 1. Unthread cap screws (Ref. No. 14) and remove casing (Ref.No. 12) and O-ring (Ref. No. 4) from the adapter (Ref. No. 3).2. Unthread round head screws (Ref. No. 15) and removevolute (Ref. No. 10) from adapter.3. Unscrew impeller (Ref. No. 9) from the engine shaft.Remove the impeller shim(s) (Ref. No. 8), shaft sleeve and seal head from engine shaft.NOTE: To keep the shaft from turning, remove the shroud from the engine and hold the flywheel in place. 4. Unthread hex flange screw (Ref. No. 2) and remove theadapter from the engine mounting face.5. Push seal seat from the adapter recess with a screwdriver.6. Clean the adapter recess before inserting a new seal seat.7. Carefully wipe the ceramic surface of the new seal seat witha clean cloth.8. Wet the outside of the rubber portion of the seal seat with alight coating of soapy water.9. Press the new seal seat squarelyinto the cavity in theadapter. Use finger pressure only to avoid scratching the seal seat (This is a lapped surface and must be handled very carefully).10. After the seal seat is in place, insure that it is clean and hasnot been marred.11. Using a clean cloth, wipe the shaft and make certain that it isperfectly clean.12. Secure the adapter on the engine mounting face.Tighten hex flange screws EVENLY to avoid cocking rabbet on engine mounting face.13. Apply a light coating of soapy water to the inside rubberportion of seal head and slide onto the shaft sleeve. Slip the shaft sleeve with seal head onto the engine shaft with the black carbon face toward the white ceramic seal seat.Do not touch or wipe the face of the Polished surface part of the seal head. 14. Replace any impeller shim(s) removed in disassembly. 15. Screw impeller back in place, tightening until it is against theshaft sleeve.16. Remount volute and position O-ring in place.IMPORTANT: Always inspect O-ring. Replace when cracked or worn. Wet O-ring with soapy water for ease of assembly. 17. Remount casing.SHIM ADJUSTMENT1.When installing a replacement engine, adapter, impeller, shaft sleeve, volute or casing it may be necessary to vary the number of impeller shims (Ref. No. 8) that will be required. This is easily done by adding one shim more than was removed and reassembling the pump as described in MECHANICAL SEAL REPLACEMENT section.NOTE: When adding or removing shims, it is best to proceed with a 0.010" increment each time. Remove spark plug wire from engine and ground. While tightening the unit together, turn the shaft (by pulling on the recoil starter etc.); feel for the shaft seizing. If shaft begins to seize before the fasteners are completely tight, disassemble the pump and remove one shim and repeat assembly. 2. Once having added one shim more than original, ensure thatthe volute (Ref. No. 10) and adapter (Ref. No. 3) are firmly fitted (check fasteners, Ref. Nos. 2 & 15). When engine turns freely,add shims until it does strike, then remove a 0.010" shim. This should allow the proper clearance.3. Proper running clearance for the impeller should be as closeas possible to volute without striking; maximum clearance is 1/32" (0.032").4. Follow the above procedure until proper clearance isobtained. This will insure maximum performance.2STX-250-00203/20122-Inch IPT Cast Iron PumpsRepair Parts ListPart Number for Models:Ref. 2TS5ACBNo. Description 2TS5HCB Qty.1 Engine B&S (2TS5ACB) 1639-034-00 1Engine Honda GX160 (2TS5HCB) 1639-036-00 12 Hex Head Cap Screw * 43 Adapter 2182-010-01 14 O-Ring 2186-000-00 14 O-Ring - Viton (optional) 2186-001-00 15 &6 ⑤Shaft Seal Assembly - Silicon Carbide/Viton 1641-166-91 17 Shaft Sleeve 1483-140-09 18 Impeller Shim Package 1658-000-90 19 Impeller 3935-012-01 110 Volute 2182-002-01 111 Flapper Valve 1609-002-00 111 Flapper Valve - Viton (optional) 1695-011-90 112 Casing 2112-001-02 113 1/2" NPT Plug * 214 Hex Head Cap Screw * 415 Socket Head Screw SS 1705-000-00 216 Nut * 417 Hex Head Cap Screw * 418 Hex Nut * 419 Flat Washer * 420 Lock Washer SS 1787-000-00 221 Roll Cage Frame Assembly 3120-105-K0 1❒ Raising Block 3120-119-90 2❒ NPT Pipe Nipple Kit C366-90 1❒ NPT Suction Strainer C362-90 1❒ 2” NPT Street Elbow1695-070-00 1❒ Wheel Kit (optional) A374-90 1(*) Standard Hardware Item, Available Locally(⑤) Seal assembly available as set only (includes seal head and seat).(❒) Not Shown2STX-250-00 3 03/2012。
Henny Penny商品机维修指南说明书

3-1. INTRODUCTIONThis section identifies and lists the replaceable parts of the Henny Penny merchandiser.3-2. GENUINE PARTSUse only genuine Henny Penny parts in your cabinet. Using a part of lesser quality or substitute design may result in cabinet damage or personal injury.3-3. HOW TO ORDEROnce the part you want to order has been found in the Parts List, write down the following information:1.From the Parts List (Sample)Item Number 3Part Number 40645Description Relay 2.From the data plate (Sample)Product Number HEC104.0Serial Number AY001JJ V oltage 102/208V3-4. PRICESYour independent Henny Penny distributor has a price parts list and will be glad to inform you of the cost of your parts order.3-5. DELIVERYCommonly replaced items are stocked by your independent Henny Penny distributor and will be sent out when your order is received.Other parts will be ordered by the distributor from Henny Penny Corporation. Normally, these will be sent to your distributor within three working days.3-6. WARRANTYAll replacement parts (except lamps and fuses) are coveredunder warranty for 90 days against manufacturing defects and work manship. If damage occurs during shipping, notify the carrier at once so that a claim may be properly filed. Refer to warranty on the front o f this section for other rights and limitations.Recommended replacement parts, stocked by your distributor, are indicated with √ in the parts lists. Please use care when ordering recommended parts, because all voltages and variations are marked. Distributors should order parts based upon common voltages and equipment sold in their territory.2063-13-7. RECOMMENDEDSPARE PARTS FOR DISTRIBUTORSItem Part Quantity No.No.Description103104123124165645-001Glass - Clear - LH Side - 10X 11--168158-001Glass - Clear - LH Side - 12X--11269230Assy - Molded Cord Lamp Plug - 103/123 3 or 4-2-267893Assy - Molded Cord Lamp Plug - 104/124- 3 or 4-2265995Receptacle - Molded Harness Lamp - 103/123/104/124 3 or 4 3 or 422365495Cap- HEC-103/123 - Top 1-1-365497Cap- HEC-104/124 - Top-1-1466344Panel - HEC-103 - Four Shelf Removable 1---466019Panel - HEC-104 - Four Shelf Removable -1--466361Panel - HEC-103 - Three Shelf Removable 1---466021Panel - HEC-104 - Three Shelf Removable -1--469639Panel - HEC-123 - Two Shelf Removable --1-468549Panel - HEC-124 - Two Shelf Removable ---1565645-002Glass - Clear - RH Side - 10X 11--568158-002Glass - Clear - RH Side - 12X --11665614Panel - Bottom Insert - HEC-10X34347Assy - Shelf - See chart on Next 2 Pages3 or4 3 or 422866500Assy - Cord Heater Plug3 or4 3 or 422865992Receptacle - Molded Harness Heat - 103/123/104/124 3 or 4 3 or 422966274Stud Assy - HEC-103 - Product Stop 3 or 4-2-966249Stud Assy - HEC-104 - Product Stop - 3 or 4-21081699Caster - 3” - Swivel w/Brake222211Assy - Front Panel - See Chart on Next Page11111266011-001Bumper - Snap-On - HEC-103/1231-1-1266011-002Bumper - Snap-On - HEC-104/124-1-11354649Snap-On End Cap (specify color)222214*MS01-384Strike - Latch -Male 1012101215*41356Leg Assembly (Optional)444416*81700Caster - 3” - Swivel 2222 *not shown 3-221158312461211791310705 3-3Item Part No.Description Language Array3-4 7057053-512453Item Part Quantity No.No.Description103104123124166014Panel - LH Rear - HEC-10X 11--168556Panel - LH Rear - HEC-12X --11265530Panel - RH Side1111366432Panel - Lower Rear - HEC-103/1231-1-365659Panel - Lower Rear - HEC-104/124-1-1466086Assy - 1PH-20A-12Ga - Power Cord 1111466128Assy - 1PH-30A-12Ga - Power Cord -1--466140Assy - 3PH-15A-12Ga - Power Cord 11--566030Panel - LH Side1111666300Panel -HEC-103 - RH Rear 1---666015Panel -HEC-104 - RH Rear -1--669641Panel -HEC-123 - RH Rear --1-668557Panel -HEC-124 - RH Rear ---1766022Stud Assy. - LH-HEC-10X Trim 11--768554Stud Assy. - LH-HEC-12X Trim --11866025Stud Assy. - RH-HEC-10X Trim 11--868555Stud Assy. - RH-HEC-12X Trim --119MS01-509Trimlock 1/4 Black Edge Guard 12ft 12ft 9.25ft 9.25ft 10PL01-0331-1/8 Plug Button - NI PL TD 333311*69208Insulation - Rear Panel - 103/12334--11*69744Insulation - Rear Panel - 104/124--34*not shown678910Item Part Quantity No.No.Description103104123124√166659-001Heater - HEC-103/123 - 1100W-208V - Well 1-1-√166659-002Heater - HEC-103/123 - 1100W-240V - Well 1-1-√165566-001Heater - HEC-104/124 - 825W-208V - Well -2-2√165566-002Heater - HEC-104/124 - 825W-240V - Well -2-2265951-001Holder - Price Label - HEC-104 (Optional)- 3 or 4-2265951-002Holder - Price Label - HEC-103 (Optional) 3 or 4-2-366121Gasket - Price Label (Optional)6 or 8 6 or 844√ recommended parts3-6206123Item Part Quantity No.No.Description103104123124165785Decal - HEC-10X - 4 Shelf 11--166038Decal - HEC-10X - 3 Shelf 11--168579Decal - HEC-12X - 2 Shelf--112MS01-383Latch (Plastic) - Female - Front Panel 10121012√3EF02-006Fuse Holder - 15 Amp (See SN Chart)2222√3EF02-007Fuse - 15 Amp (See SN Chart)2222√3EF02-125Breaker-Push Button Reset (See SN Chart)2222√3EF02-104Fuse Holder - 20 Amp - CE 2222√3EF02-105Fuse - 15 Amp - CE2222466411Panel - HEC-103 Lower - Removable 1-1-466020Panel - HEC-104 Lower - Removable -1-1√ recommended parts7073-71432Fuse, Fuse Holder and Breaker SN ChartItem Part Quantity No.No.Description103104123124√166095Control - HEC Duty Cycle1111√271036Ballast - Fluorescent Light - 120 - 277V 4 or 54 or 533√266811Ballast - CE - 220-240V - 14/21/28/35W 4 or 54 or 533365769Assy - Terminal Block - Power1111366815Assy - Terminal Block - CE - Power1111366848Assy - Terminal Block - Non-CE - Int’l. - Power 1111√428979Transformer - 208/240V-Pri. - 12V-Sec.1111√540645Relay - Solid State - 25 Amp - 48-280V AC 4 or 54 or 533666658Assy - Terminal Block - Lights1111666820Assy - Terminal Block - CE - Lights 1111√719405Contactor - 208-240V AC 1111√8*51057EMC Filter - CE1111√ recommended parts*not shown3-87071765432Item Part Quantity No.No.Description103104123124√172277Power switch2222266063Decal - Power Switch 1111366106Retainer - Ceiling Lamp 8 or 108 or 1066√4BL01-026Light - Fourescent - F14T5 4 or 5-3-√4BL01-025Light - Fourescent - F21T5- 4 or 5-3√570157Assy - Lampholder - T5 Lamp - Bi Pin 8 or 108 or 1066√ recommended parts7073-914253。
【海上小咖】船舶发电机(HyundaiHimsenH17)大修保养Part2

20,船舶集控室空调机组故障排除
21,船舶主机曲轴拐档差测量详解
22,双燃料主机工作原理
23,船舶辅机燃油喷射泵大修(YANMAR 系列)
24,船舶海水冷却系统详解
25,船舶淡水冷却系统详解
26,船舶FURUNO X-BAND雷达天线故障查找及排除
27,船体保护系统详解-外加电流的阴极保护ICCP
11,船舶主机性能测试 - 超实用版
12,船舶主机喷油器拆装完整视频
13,船舶发电机透平废气出口温度传感器故障排除
14,船舶机舱警报系统故障排除
15,船用电梯故障查找及排除
16,ETO 必须知道的VFD(变频驱动)完整指南
17,某船主机电子调速器信号中断故障分析与排除
18,某船交流发电机母线绝缘层脱落导致的发电机停车故障实例
5,还不知道如何更换ME-C主机MPC板吗?安排
6,一声巨响,三菱分油机损坏,什么原因?
7,船用FURUNO雷达(X-BAND)故障检查及排除
8,【轮机】发电机吊缸大修(overhaul)视频全过程(一)
9,【轮机】发电机吊缸大修(overhaul)视频全过程(二)
10,10分钟教会你船舶造水机的启停以及注意事项
28,还不了解ALPHA 注油器系统的看过来-实用版29,船舶源自电机优先脱扣故障排查以及逆功率脱口测试
原海上小咖船舶发电机hyundaihimsenh17大修保养part2
【海上小咖】船舶发电机(HyundaiHimsenH17)大修保养Part2
1,船舶ME电喷主机完整指南
2,史上最全船舶ME电喷主机MPC图文分析
3,轮机员必须知道的PID知识大全
- 1、下载文档前请自行甄别文档内容的完整性,平台不提供额外的编辑、内容补充、找答案等附加服务。
- 2、"仅部分预览"的文档,不可在线预览部分如存在完整性等问题,可反馈申请退款(可完整预览的文档不适用该条件!)。
- 3、如文档侵犯您的权益,请联系客服反馈,我们会尽快为您处理(人工客服工作时间:9:00-18:30)。
C on
fid
en
tia
l
C on
fid
en
tia
l
HannStarDisplayCorp. Document Title Document No.
HG171D_XY _HSM
Page No. Revision
32 32 / 79
07/08/03
The information contained in this document is the exclusive property of HanStar Display Corporation. It shall not be disclosed,distributed or reproduced in whole or in part without written permission of HannStar Display Corporation.
C on
fid
en
tia
l
HannStarDisplayCorp. Document Title Document No.
HG171D_XY _HSM
Page No. Revision
36 36 / 79
07/08/03
The information contained in this document is the exclusive property of HanStar Display Corporation. It shall not be disclosed,distributed or reproduced in whole or in part without written permission of HannStar Display Corporation.
C on
fid
en
tia
lபைடு நூலகம்
HannStarDisplayCorp. Document Title Document No.
HG171D_XY _HSM
Page No. Revision
33 33 / 79
07/08/03
The information contained in this document is the exclusive property of HanStar Display Corporation. It shall not be disclosed,distributed or reproduced in whole or in part without written permission of HannStar Display Corporation.
C on
fid
en
tia
l
HannStarDisplayCorp. Document Title Document No.
HG171D_XY _HSM
Page No. Revision
34 34 / 79
07/08/03
5
4
3
2
1
D
CN703 LVB0M LVB1M LVB2 RXO2LVBCK RXOCLVB3M LVA0M LVA1M LVA2M LVACK RXECLVA3M RXO0RXO1RXO3RXE0RXE1RXE2RXE3-
VLCD
B
C on
PB0 PB1 PB LVBCKP PB LVBCKM PB4 PB5 PB6 PB7 PB LVB0P PB LVB0M
LVB3P LVB3M LVB2P LVB2M LVB1P LVB1M
fid
4 PB[0..9]
PB[0..9]
C712 22uF/16V
R714 150R 1/4W
B
A
A
C
of
1
Wednesday, April 11, 2007
5
4
3
The information contained in this document is the exclusive property of HanStar Display Corporation. It shall not be disclosed,distributed or reproduced in whole or in part without written permission of HannStar Display Corporation.
2
LVACKP LVACKM
l
C
PA[0..9]
1 3 5 7 9 11 13 15 17 19 21 23
2 4 6 8 10 12 14 16 18 20 22 24
RXO0 RXO1 RXO2 RXOC RXO3 RXE0 RXE1 RXE2 RXEC RXE3
LVB0P LVB1P LVB2P LVBCKP LVB3P LVA0P LVA1P LVA2P LVACKP LVA3P
D
4 PA[0..9]
C
en
CONN
PA0 PA1 PA LVA2P PA3 PA4 PA5 PA6 PA7 PA LVA3P PA LVA3M
LVA2M LVA1P LVA1M LVA0P LVA0M
tia
VLC 2 R713 150R 1/4W Title SizDocument Numbe A Date Sheet Rev
HannStarDisplayCorp. Document Title Document No.
HG171D_XY _HSM
Page No. Revision
31 31 / 79
07/08/03
The information contained in this document is the exclusive property of HanStar Display Corporation. It shall not be disclosed,distributed or reproduced in whole or in part without written permission of HannStar Display Corporation.
C on
fid
en
tia
l
HannStarDisplayCorp. Document Title Document No.
HG171D_XY _HSM
Page No. Revision
37 37 / 79
07/08/03
The information contained in this document is the exclusive property of HanStar Display Corporation. It shall not be disclosed,distributed or reproduced in whole or in part without written permission of HannStar Display Corporation.
HannStarDisplayCorp. Document Title Document No.
HG171D_XY _HSM
Page No. Revision
35 35 / 79
07/08/03
9.2 Power Board
The information contained in this document is the exclusive property of HanStar Display Corporation. It shall not be disclosed,distributed or reproduced in whole or in part without written permission of HannStar Display Corporation.