天然气制备合成气复习过程
合成气的生产培训资料

合成气的生产第五章合成气的生产5.2由天然气制合成气5.2.1概述1.水蒸气转化法在高温和催化剂存在下,烷烃与水蒸气反应生产合成气的方法称为水蒸气转化法。
当以天然气为原料时,又称甲烷蒸汽转化法,是目前工业生产应用最广泛的方法。
2.部分氧化法部分氧化法是指用氧气(或空气)将烷烃部分氧化制备合成气的方法。
反应式表示为, 部分氧化法多用于以石脑油或重油为原料的合成气生产。
3. 自热式催化转化部分氧化法(ATR工艺)CH4的部分氧化和蒸汽转化组合在一个反应器进行。
反应器上部为无催化剂的燃烧段,CH4的不完全燃烧,放出热量。
反应器下部为含催化剂的转化段,利用燃烧段反应放出的热量,进行吸热的水蒸气转化反应。
催化剂为:颗粒状镍催化剂,以含氧化锰和氧化铝的尖晶石为载体,具有很高的活性和耐高温性能,可采用较高空速进行反应。
4.甲烷-二氧化碳催化转化法(Sparg工艺)催化剂上易结炭:改进镍基转化催化剂、开发新型抗积炭催化剂和优化反应条件等。
调节原料混合气的CO2/CH4H2O/CH4之比,转化后合成气中H2/CO在1.8—2.7之间变动5.2.2天然气蒸汽转化的基本原理一、主要反应天然气中所含的多碳烃类与水蒸气发生类似反应在—定条件下,转化过程可能发生成碳反应二、催化剂和工艺条件:1.催化剂催化剂的基本条件:高活性、高强度、抗析碳。
活性组分:镍是目前天然气蒸汽转化催化剂的唯一活性组分。
在制备好的催化剂中,镍以NiO形式存在,含量一般为10%一30%(质量)。
助催化剂:抑制熔结过程,使催化剂有较稳定的高活性,延长使用寿命并提高抗硫抗析碳能力。
金属氧化物,如Cr2O3、A12O3、MgO、TiO等。
助催化剂用量一般为镍含量的10%(质量)以下。
载体:使镍的晶粒尽量分散,较大比表面。
催化剂的载体是熔点在2000℃以上的金属氧化物,它们能耐高温,且有很强的机械强度。
常用的载体有A12O3、MgO、CaO、K2O等。
2.工艺条件甲烷蒸汽转化过程中控制的主要工艺条件是温度、压力、水碳比、空气加入量等。
5 合成气的生产过程
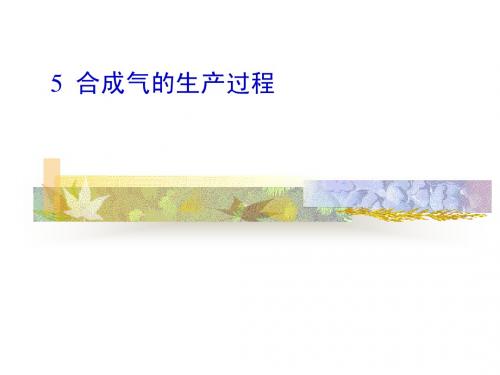
可将有机硫转化为无机H2S
低变催化剂
工业上应用的低变催化剂均以CuO为主体。还原 后具有活性的组分是细小的铜结晶——铜微晶。 常用的添加物有ZnO,Cr2O3, Al2O3
钴-钼耐硫催化剂
影响因素 温度、压力、汽/气比
5.4 渣油制合成气 P172
部分氧化法 美国德士古(Texaco)和荷兰谢尔(Shell) 蓄热炉深度裂解法
反应26
影响转化反应平衡主要因数 (1)、温度的影响
甲烷与水蒸气反应生成 CO和H2是吸热的可逆 反应,高温对平衡有利,即 H2 及 CO 的平衡产 率高, CH4 平衡含量低 ; 对一氧化碳变换反应 的平衡不利,可以少生成二氧化碳。是温度过 高,有利于甲烷裂解,会大量析出碳,并沉积 在催化剂和器壁上。
碳酸钾水溶液
碳酸钾水溶液具有强碱性,与CO2反应 生成的KHCO3在减压和受热时,解吸出 CO2,溶液重新再生为K HCO3, 吸收操作温度105一130℃
杂质
物理吸收法
加压(2~5MPa)和较低温度条件下吸收CO2,溶液的再 生靠减压解吸 冷甲醇法 聚乙二醇二甲醚法 碳酸丙烯酯法
反应物浓度在孔内分布
Ⅱ.转化催化剂的使用和失活
转化催化剂
使用前:氧化态;氧化镍还原成金属镍才 有活性 还原气:氢气、甲烷或一氧化碳。 老化、中毒、积炭
活性下降原因
xNi + H2S
NixS + H2
(5-43)
砷化物 永久性中毒
积炭因素
“架桥” 空间积炭 酸性太强,催化裂化结焦 深度脱氢析碳 一氧化碳歧化析碳 保持足够的水碳比
化学工艺学第5章 合成气的生产过程

工艺条件—反应压力
反应压力: 3.5~ 4.0MPa
采取加压原因 ① 节省动力消耗 ② 提高传热效率 ③ 提高过热蒸汽的余热利用价值
工艺条件—反应温度
反应温度
①一段转化炉出口温度
中型合成氨 1.8MPa,760℃
大型
3.2MPa,800℃
出口温度尽可能不要高。
②二段转化炉出口温度 平均温距增大 △ T=T-TP,
蒸汽转化法 Steam reforming
CH4 H2O CO 3H2 H(298K) 206 kJ / mol
部分氧化法 Partial oxidation
CH4 1 / 2O2 CO 2H2 H (298K) 35.7 kJ / mol CH4 CO2 2CO 2H2 H (298K) 247 kJ / mol
T
2.0814103 T
1.8737 107 T2 11.894
陈五平 《无机化工工艺学》
lg
KP2
2.183 T
0.09361 lg
T
0.632103 T
1.08107 T2 2.298
平衡组成的计算
已知条件: m 原料气中的水碳比 (m H2O )
CH 4 p 系统压力;T 转化温度 假定:无炭黑析出
p=3.5MPa、T=800℃
反应压力影响
16
14
甲 12 烷 10 平 衡8 含6 量4 %
2
0
1.4
2.8
3.5
反应压力 MPa
水碳比=2、T=800℃
压力增加,甲烷平衡 含量也随之增大。
在烃类蒸汽转化方法 的发展过程中,压力 都在逐步提高,主要 原因是加压比常压转 化经济效果好。
天然气制备合成气

天然气制备合成气 天然气作为一种清洁、环境友好的能源,越来越受到广泛的重视.天然气作为一种清洁、环境友好的能源,越来越受到广泛的重视。
制合成气是间接利用天然气的重要步骤,也是天然气制氢的基础,充分了解天然气制合成气 的工艺与催化剂对于我们进一步研究天然气的利用将有很大帮助.天然气中甲烷含量一般大于90%,其余为小量的乙烷、丙烷等气态烷烃,有些还含有少量氮和硫化物。
其他含甲烷等气态烃的气体,如炼厂气、焦炉气、油田气和煤层气等均可用来制造合成气。
目前工业上有天然气制合成气的技术主要有蒸汽转化法和部分氧化法。
本文主要对蒸汽转化法进行具体的描述,并具体介绍此工艺的发展趋势. 蒸气转化法蒸气转化法是目前天然气制备合成气的主要途径。
蒸汽转化法是在催化剂存在及高温条件下,使甲烷等烃类与水蒸气反应,生成CO H 、2等混合气,其主反应为:2243H CO O H CH +=+,mol /206298KJ H =∆Θ该反应是强吸热的,需要外界供热。
因为天然气中甲烷含量在90%以上,而甲烷在烷烃中热力学最稳定,其他烃类较易反应,因此在讨论天然气转化过程时,只需考虑甲烷与水蒸气的反应。
甲烷水蒸气转化反应和化学平衡甲烷水蒸气转化过程的主要反应有: 2243H CO O H CH +⇔+,mol /206298KJ H =∆Θ222442H CO O H CH +⇔+,mol /165298KJ H =∆Θ222H CO O H CO +⇔+,mol /9.74298KJ H =∆Θ可能发生的副反应主要是析碳反应,它们是:242H C CH +⇔,mol /9.74298KJ H =∆Θ22CO C CO +⇔,mol /5.172-298KJ H =∆ΘO H C H CO 22+⇔+,mol /4.131-298KJ H =∆Θ甲烷水蒸气转化反应必须在催化剂存在下才有足够的反应速率.倘若操作条件不适当,析碳反应严重,生成的碳会覆盖在催化剂内外表面,致使催化剂活性降低,反应速率下降。
天然气制合成气
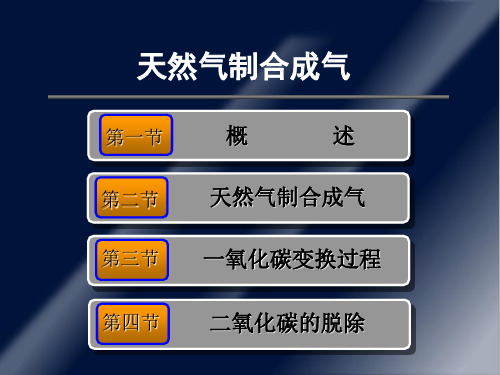
(3)合成醋酸
CH 3OH CO CH 3COOH
首先将合成气制成甲醇,再将甲醇与CO羰基化合成 醋酸. 1960年.德国的BASF公司将甲醇羰基化合成醋酸的 工艺工业化,此法比正丁烷氧化法和乙醛氧化法工 艺更经济。BASF公司的工艺需要70MPa高压.醋酸 收率90%。1970年,美国Monsanto公司推出了低压 法工艺,开发出一种新型催化剂(碘化物促进的铑络 合物)使甲醇羰基化反应能在180℃和3~4 MPa的温 和条件下进行,醋酸收率高于99%,现已成为生产 工业醋酸的主要方法。并且,带动了有关羰基过渡 金属络合物催化作用的基础研究,促进了合成气化 学和C1化工的发展。
0 1.4 2.8 3.5
16
反应压力影响
压力降低有利于甲烷转化, 但低压易使其分解析炭。 在蒸汽转化法的发展过程中 ,压力都在逐步提高,主要 原因是加压比常压转化经济 效果好。
反应压力 MPa 水碳比=2、T=800℃
低压,但实际高压。
甲烷蒸气转化催化剂
蒸汽转化活化能极大,T>1300℃才有工业应用 价值,但大量甲烷裂解析碳,反应选择性急剧降低 .
转化,最高温度800 ℃左右, 出口CH4约 10%(干基).
② 在较高温度下,耐火砖衬里的钢制圆筒,
可耐1000 ℃以上高温。加入氧气,利用反应 热继续甲烷转化反应。
CH4 ,H2O
500° C
650° C
CH4 >10% 800° 1100° C C O2
C 1000 °
3.6MPa 一段转化炉为变温反应器
耗氧气,投资和生产费 用较高,需廉价氧 。
新工艺
节能、灵活调节H2/CO比
ATR工艺
自热式催化转化部分氧化法 (ART工艺)
合成气的生产过程培训课件(PPT 46页)
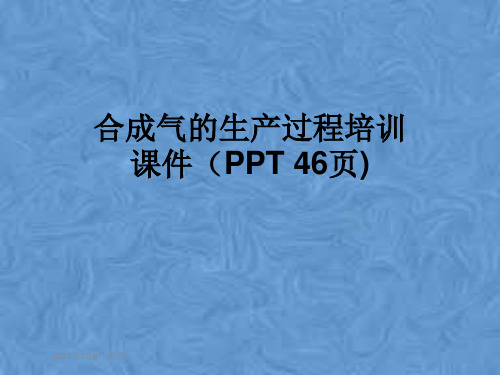
C + 2 H2O C + CO2
CO2 + 2 H2 2 CO
H29890.3 kj/mol H298172.6 kj/mol
C + 2 H2
CH4
H298-74.9 kj/mol
气化生成的混合气称为水煤气,以上均为可逆反应,
总过程为强吸热反应。 温度:1100℃
反应条件 压力:2.5~3.2 MPa
C + H2O
高温
H298 -131.4 kJ/mol
Kp4
p(CO2) P2 (CO)
Kp5
p(H 2O) P(H 2) • P(CO)
P164 表5-6
高温不利于CO歧化析碳 高温有利于CH4裂解析碳
判断是否有析碳发生
ΔG = -RTlnKp + RTlnJp = RTln(Jp/Kp)
Jp为反应体系中各组分的压力熵 (产物与反应物实际分压的关系) Jp/Kp < 1, ΔG < 0, 有析碳 Jp/Kp=1, ΔG=0, 热力学析碳的边界 Jp/Kp > 1, ΔG > 0, 不析碳
H298-35.7 kj/mol
天然气蒸汽转化过程工艺原理
主反应
CH4 + H2O CH4 + 2 H2O CO + H2O
CO + 3 H2 CO2 + 4 H2 CO2 + H2
H298 206 kJ/mol H298 165 kJ/mol H298 -41.2 kJ/mol
副反应 析碳反应 致使催化剂崩裂或粉化!!
水蒸汽和氧气比例
煤气化生产方法和主要设备 固定床间歇式气化
间歇式 连续式
化工工艺学__复习

化⼯⼯艺学__复习第⼆章制⽓# 热量的供给⽅式不同有两种制备粗原料⽓的⽅法:1外部供热的蒸汽转化法; 2内部蓄热的间歇操作法# ⽓态烃蒸汽转化反应在⾼温有催化剂存在的条件下可实现下述反应:CH4(g) + H2O(g) = CO(g) + 3H2(g) CO(g) + H2O(g) = CO2(g) + H2(g)但要完成这⼀⼯业过程,必须对可能发⽣的主要反应及副反应进⾏详细研究。
主要的副反应有CH4(g) = C (s) + 2H2(g) ;2CO(g) = CO2(g) + C(s) ; CO(g) + H2(g) = C(s) + H2O(g)# CH4转化反应热⼒学:甲烷蒸汽转化在⾼温、⾼⽔碳⽐和低压下进⾏为好# CH4转化反应的动⼒学分析:反应主要取决于在催化剂内表⾯的反应,所以该反应控制步骤为内表⾯控制。
因此减⼩粒度增加内表⾯积有利于扩散过程和提⾼反应速率。
#防⽌析炭的措施:A 配料时增⼤S/C,从热⼒学上去消除B选⽤适宜的催化剂C选择适宜的操作条件。
#析碳的处理析炭不严重,可减压、减原料⽓,提⾼S/C,甚⾄可停进天然⽓,利⽤析炭逆反应除碳析炭严重,可通⼊蒸汽为载体,加⼊少量空⽓燃烧碳,但空⽓量⼀定要严格控制,结束后对催化剂进⾏还原。
#转化过程描述;⼀段转化完成转化⼤部分任务;⼆段炉转化剩余甲烷和加⼊原料氮⽓空⽓加⼊量对⼆段炉出⼝⽓组成和温度有⽆影响,如何影响?P97#对转化催化剂的要求⾼活性、强度好、耐热性好、抗析炭能⼒强.(转化催化剂所处⼯况转化温度⾼、⽔蒸⽓和氢⽓分压⾼、流速⼤、可能析炭)#转化催化剂的基本组成NiO为最主要活性成份。
实际加速反应的活性成份是Ni,所以使⽤前必须进⾏还原反应,使氧化态变成还原态Ni NiO(s) +H2(g) = Ni(s) + H2O(g)#催化剂制备制备⽅法有三种:沉淀法、浸渍法、混合法,这三种⽅法最后都需要进⾏⾼温焙烧,从⽽使催化剂有⾜够的机械强度#转化分为⼆段的原因:A转化条件不允许;B补充合成所需要的氮⽓#为什么⽤⼆段转化⽅式?转化率⾼必须转化温度⾼,全部⽤很⾼温度,设备和过程控制都不利,设备费⽤和操作费⽤都⾼。
合成气的生产过程培训课件(ppt 129页)
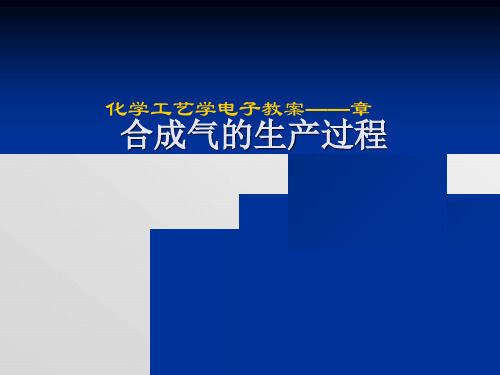
Ceramic Membrane Technology
5.3.1天然气蒸汽转化反应
烷烃
CnH2n2n21H2O3n41CH 4n41CO 2 CnH2n2nH 2OnCO(2n1)H2 CnH2n22nH 2OnC2O (3n1)H2
烯烃 CnH2n n2H2O34nCH4 n4CO2 CnH2n nH2OnCO2nH2 CnH2n 2nH2OnCO2 3nH2
蒸汽吹净:置换炉内和出口管中的吹风 气,以保证水煤气质量。
一次上吹制气:燃料层下部温度下降, 上部升高。
下吹制气:使燃料层温度均衡 二次上吹制气: 将炉底部下吹煤气排
净,为吸入空气做准备。 空气吹净:此部分吹风气可以回收。
工艺生产条件:
温度 吹风速度 蒸汽用量 燃料层高度 循环时间
间歇气化法优缺点:
化学工艺学电子教案——章
合成气的生产过程
5.1 合成气的应用及发展前景
5.1.1 应用
(1)合成气(synthesis gas or syngas)
CO和H2的混合物 原料:
煤 油 天然气 油页岩、石油砂 农林废料、城市垃圾
(2)氢能利用背景
化石类能源使用
过渡开采化石类能源的逐渐枯竭 石油价格不断攀升
铑络合物-HI催化剂
甲醇
3MPa,175℃
醋酸
铜、锌系催化剂
汽油、烯烃、芳烃
中低压、230-270℃
乙二醇
同系化
甲醇
乙醇
乙烯
合成气 + 丙烯醇
1,4-丁二醇
5.1.2发展背景 煤
石油、天然气
5.1.3 关键问题
(1)实现新工艺,降低成本,解决污染问 题
(2)合成气生产烯烃、含氧化合物技术中 高压、高温、贵金属催化剂的替代。
天然气制合成气分析解析精品PPT课件

注:水碳比为2
高温有利甲烷转化,还要控制副反应。 T>750℃,析碳严重,沉积。
一 合成气的应用实例
合成气 合成气
NH3
改进的费托合成催化剂
乙烯、丙烯
合成气
锌、铬系催化剂
铑络合物-HI催化剂
甲醇
醋酸
高压、380℃
3MPa,175℃
铜、锌系催化剂
汽油、烯烃、芳烃
乙二醇
中低压、230-270℃
甲醇同系化 乙醇
乙烯
合成气 + 丙烯醇
1,4-丁二醇
第二节 天然气制造合成气
天然气
优质、清洁、环境友好的能源。
一 以天然气为原料的生产方法
水蒸气转化法 Steam reforming
CH4 H2O CO 3H2 H (298K ) 206kJ / mol
特点:目前工艺多采用的方法,H2/CO=3, 以天然气为原料的大型合成氨厂广泛采用。
强吸热反应
非催化部分氧化法 Partial oxidation
(一)甲烷水蒸气转化反应和化学平衡
主反应
变换反应
CH 4 C 2H2
副反应 (析碳) 2CO C CO2
H
Hale Waihona Puke 29874.9kJ/
mol
H
298
172.5kJ
/
mol
CO H2 C H2O
H
298
131.4kJ
/
mol
析炭危害
炭黑覆盖在催化剂表面,堵塞微孔,降 低催化剂活性。 影响传热,使局部反应区产生过热而缩 短反应管使用寿命。 催化剂内表面炭与水蒸气反应,使催化 剂破碎,影响生产能力。
(3)合成醋酸
天然气制合成气分析解析

脱碳
变换
工艺流程充分合理地利用不同温位的余热,加热 各种物料和产生动力及工艺蒸汽。。
天然气蒸汽转化流程
天然气压缩到3.6MPa并配氢氮混合气,到一段炉的对流段3 预热至380~400℃,热源是辐射段4的高温烟道气。预热后 进钴钼催化脱硫器l,有机硫加氢成硫化氢,再到氧化锌脱 硫罐2脱除硫化氢,总含硫量降至0.5×10-6以下。脱硫后与 中压蒸汽混合,送至对流段加热到500~520℃,分流进入辐 射段4的转化管,自上而下经管内催化剂层转化反应,热量 由管外燃烧天然气提供。 反应管底部转化气温度为800~820℃,甲烷含量约9.5%,汇 合于集气管沿中心管上升,由炉顶送往二段转化炉5。二段 炉入口引入预热450℃的空气,与部分甲烷在炉顶燃烧,温 度升至1200℃,经催化剂层继续转化,二段炉出口转化气温 度约1000℃,压力3.0MPa,残余甲烷低于0.3%,(H2+CO)/ N2=3.1~3.2。二段炉出来高温转化气先后经二个废热锅炉 6,7,回收显热产生蒸汽.此蒸汽经对流段加热成高压过热蒸 汽,作为工厂动力和工艺蒸汽。转化气温度降至370℃,送 变换工段。
不同用途要求的合成气组成
用途 合成氨 合成甲醇 羰基合成高级醇 生产氢气 CO/ H2 1:3 1:2 1:1 H2>95%
一 合成气的应用实例 1. 已工业化的主要产品
(1)合成氨
N2 3H2 2NH3
20世纪初,德国人哈伯发明了由氢气和氮气直接合 成氨,并于1913年与博茨创建了合成氨工艺,由含 碳原料与水蒸气、空气反应制成含H2和N2的粗原 料气,再经精细地脱除各种杂质,得到H2:N2=3:l( 体积比)的合成氨精原料气,使其在500~600℃、 17.5~20MPa及铁催化剂作用下合成为氨。近年来 ,该过程已可在400~450℃、8~15MPa下进行。 •氨的最大用途是制氮肥,这是目前世界上产量最 大的化工产品之一,氨还是重要的化工原料。
能源化工—第15章 天然气转化制合成气讲解

第15章 天然气转化制合成气
15.3.2 Uhde CAR工艺 15.3.3 Topsoe ATR工艺
图15.4 CAR反应器结构示意图
图15.5 ATR反应器结构示意图
将两种转化集于一个反应器内以降低投资和提高能源效率,ATR反应器更 简单而更具应用前景。
溶液无毒,设备无腐蚀,溶液有多种再生方案,用于合
成氨装置脱CO2时通常使用压力下闪蒸加蒸汽汽提的流程。
第15章 天然气转化制合成气
15.4.2 甲烷化
甲烷化是除去合成气中CO和CO2的最后工序,使其转化 为CH4。为了减少氢的消耗,有些大型装置在脱除CO2前增设 一选择催化氧化工序。将CO转化为CO2,CO浓度可降至1~ 2mL/m3。
以空气代替纯氧使天然气部分氧化制含氮合成气它可以节省空分装置 及相应费用、并有助于克服飞温问题。
第15章 天然气转化制合成气
15.3 联合转化工艺
天然气 脱硫
蒸汽 氧气或空气
一段转化 二段转化 合成气
图 天然气联合转化制合成气过程
第15章 天然气转化制合成气
15.3.1 Lurgi联合转化工艺
2)压力:由于CH4的蒸汽转化反应是分子数增加的反 应,所以压力的升高是不利的;但从总体安排考虑, 蒸汽转化还是要在适当压力下进行。
3)水碳比:较高的水碳比有助于CH4的转化。
第15章 天然气转化制合成气
15.1.2氮氢合成气生产工艺流程
用于合成氨的氮氢合成气需在天然气转化过程中导入 氮,通常采用两段转化工艺:在一段进行蒸汽转化,使出 口气中的CH4含量降至10%以下,二段导入空气,利用 CO及H2燃烧所产生的热量使CH4进一步转化降至0.3%左 右。转化的气体经变换工序使CO转化为CO2,在脱碳工 序脱除CO2,再经甲烷化工序除去微量碳氧化物,得到氮 气合成气去合成氨工序。
2.1 合成气制取
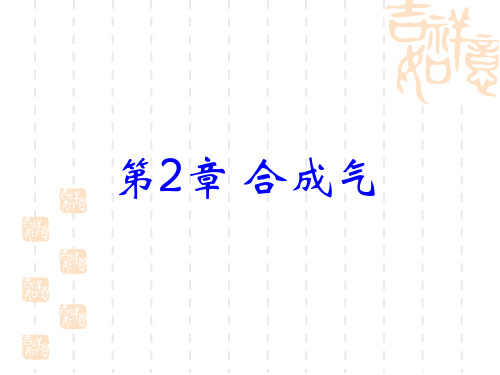
二、重油气化的工艺条件 反 应 温 度
重油气化的控制步骤: CH4+H2O=CO+3H2+206.29KJ/mol C+H2O=CO+H2+131.47KJ/mol 热力学分析:均为可逆吸热反应,提高温度 可提高甲烷与碳黑的平衡转化率。 动力学分析:提高温度有利于提高甲烷和碳 黑的转化反应速率。 ①保护炉衬和喷嘴 ②控制O2消耗指标(T提高,氧耗增加) T<1400 ℃
y 1+m+2x
预计转化气组成 已知温度 求平衡常数 求平衡组成 选择工艺条件 判断工况
影响甲烷蒸汽转化 反应平衡组成的因素
水碳比 反应温度 反应压力
P=3MPa、T=800℃
水 碳 比 的 影 响
水碳比 2
甲烷平衡含量(%) 18.0
4
6
7.9
3.9
水碳比越高,甲烷平衡含量越低。
反应温度的影响 (水碳比=2)
什么?
间歇法制气的特点是什么?
固定层煤气发生炉的燃料层如何分区?
间歇式气化的工艺流程? 间歇式气化工作循环的五个阶段?
主要设备及其结构?
思考题
• 蒸汽转化法制粗原料气应满足的条件是什么? • 天然气为原料的合成氨厂转化工序为何采用两段 • • • • • • •
转化?各段的转化条件分别是什么? 简述甲烷转化反应的基本原理? 二段转化的目的是什么? 如何防止析碳副反应的发生? 说出甲烷转化催化剂的主要组分和助催化剂。 简述蒸汽转化加压操作的优缺点。 简述温度、水碳比对转化反应的影响。 简述激冷流程与废热锅炉流程的特点及区别。
甲烷平衡含量% 压力 (MPa) 1 2 4 800 870 940 870 950 1020 5.0 2.0 1.0 温度 ℃ 910 1000 1080 950 1030 1130 1000 1100 1200 0.5 0.2
合成气的生产过程培训课件.pptx

5.三类气化炉的炉内温度分布比较
天然气
优质、相对稳定、价廉、清洁、环境友好的能源。 CH4含量>90%.
(1)对于碳与氧气的反应,一般认为先生成CO2,然后 CO2再与碳反应生成CO.
rC = kyO2
O2的一级反应
T < 775℃,动力学控制 T > 900℃ ,扩散控制
增加扩散反应速率措施: a 气速↑ b 颗粒直径 ↓
775℃ < T < 900℃ ,过渡区
(2)C与CO2的还原反应在2000℃ 以下, 属于动力学控制,反应速率大致为CO2 的一级反应。
5.2由煤制合成气
5.2.1煤气化的基本原理
5.2.1.1化学平衡 (1)以空气为气化剂时
C + O2 =CO2 C +1/2O2 =CO C + CO2 = 2CO CO + 1/2O2 =CO2
-393.777KJ/mol (5-1) -110.595KJ/mol (5-2) +172.284KJ/mol (5-3) -283.183KJ/mol (5-4)
实际生产时按以下6个步骤的顺序完成工作循环:
吹风阶段:吹入空气,提高燃料层温度, 吹风气放空,1200 ℃结束。
蒸汽吹净:置换炉内和出口管中的吹风 气,以保证水煤气质量。
一次上吹制气:燃料层下部温度下降, 上部升高。
下吹制气:使燃料层温度均衡 二次上吹制气: 将炉底部下吹煤气排
净,为吸入空气做准备。 空气吹净:此部分吹风气可以回收。
P = PH2 + PCH4 + PH2O + PCO + PCO2 ③ 根据水中氢与氧的物料平衡
PH2 + 2 PCH4 = PCO + 2PCO2
天然气为原料合成氨气的流程

天然气为原料合成氨气的流程一、原料准备。
1. 天然气预处理。
- 首先呢,天然气从气田开采出来后,里面可能会有一些杂质,像硫化物啊,水啊这些东西。
硫化物要是不除掉,会对后面的反应设备有损害,就像小虫子慢慢腐蚀大树一样。
所以要先把天然气通过脱硫装置,把硫化物去除掉。
一般常用的脱硫方法有湿法脱硫和干法脱硫。
- 湿法脱硫呢,就是让天然气和一种能和硫化物反应的液体接触,就像把脏衣服放到有洗衣液的水里洗一样,把硫化物洗出来。
干法脱硫就是让天然气通过一种能吸附硫化物的固体材料,像活性炭吸附异味那样把硫化物吸附掉。
- 除了硫化物,天然气里的水也得除掉。
这就用到脱水装置啦,可以用吸附法,让天然气通过有吸水能力的材料,比如分子筛,分子筛就像一个个小海绵,把水都吸走了。
2. 天然气转化剂准备。
- 为了让天然气能更好地进行后面的反应,我们还需要准备转化剂。
对于以天然气为原料合成氨气,常用的转化剂是镍催化剂。
这个镍催化剂要提前进行活化处理,就像给运动员做热身运动一样,让它在反应的时候能更好地发挥作用。
活化的过程一般是在一定的温度和气体氛围下处理镍催化剂,使它的活性位点暴露出来。
二、天然气的转化反应。
1. 一段转化。
- 经过预处理的天然气就进入到转化炉进行一段转化啦。
在转化炉里,天然气和水蒸气按照一定的比例混合,这个比例很重要哦,一般是1:3到1:4左右。
就像做饭的时候各种调料要按比例放一样。
- 然后在镍催化剂的作用下发生反应,主要反应是甲烷和水蒸气反应生成一氧化碳和氢气,化学方程式是CH_4 + H_2O→ CO+3H_2。
这个反应需要在高温下进行,温度大概在700 - 800℃左右。
转化炉里要不断地提供热量,就像小火炉一直烧着,保证反应持续进行。
2. 二段转化。
- 一段转化后的气体还不能直接用于合成氨气,还需要进一步转化。
一段转化气进入二段转化炉。
- 在二段转化炉里,会通入空气。
这里通入空气是有讲究的,要控制好空气的量。
- 1、下载文档前请自行甄别文档内容的完整性,平台不提供额外的编辑、内容补充、找答案等附加服务。
- 2、"仅部分预览"的文档,不可在线预览部分如存在完整性等问题,可反馈申请退款(可完整预览的文档不适用该条件!)。
- 3、如文档侵犯您的权益,请联系客服反馈,我们会尽快为您处理(人工客服工作时间:9:00-18:30)。
天然气制备合成气天然气制备合成气 天然气作为一种清洁、环境友好的能源,越来越受到广泛的重视。
天然气作为一种清洁、环境友好的能源,越来越受到广泛的重视。
制合成气是间接利用天然气的重要步骤,也是天然气制氢的基础,充分了解天然气制合成气 的工艺与催化剂对于我们进一步研究天然气的利用将有很大帮助。
天然气中甲烷含量一般大于90%,其余为小量的乙烷、丙烷等气态烷烃,有些还含有少量氮和硫化物。
其他含甲烷等气态烃的气体,如炼厂气、焦炉气、油田气和煤层气等均可用来制造合成气。
目前工业上有天然气制合成气的技术主要有蒸汽转化法和部分氧化法。
本文主要对蒸汽转化法进行具体的描述,并具体介绍此工艺的发展趋势。
蒸气转化法蒸气转化法是目前天然气制备合成气的主要途径。
蒸汽转化法是在催化剂存在及高温条件下,使甲烷等烃类与水蒸气反应,生成CO H 、2等混合气,其主反应为:2243H CO O H CH +=+,mol /206298KJ H =∆Θ该反应是强吸热的,需要外界供热。
因为天然气中甲烷含量在90%以上,而甲烷在烷烃中热力学最稳定,其他烃类较易反应,因此在讨论天然气转化过程时,只需考虑甲烷与水蒸气的反应。
甲烷水蒸气转化反应和化学平衡甲烷水蒸气转化过程的主要反应有: 2243H CO O H CH +⇔+,mol /206298KJ H =∆Θ222442H CO O H CH +⇔+,mol /165298KJ H =∆Θ222H CO O H CO +⇔+,mol /9.74298KJ H =∆Θ可能发生的副反应主要是析碳反应,它们是:242H C CH +⇔,mol /9.74298KJ H =∆Θ22CO C CO +⇔,mol /5.172-298KJ H =∆ΘO H C H CO 22+⇔+,mol /4.131-298KJ H =∆Θ甲烷水蒸气转化反应必须在催化剂存在下才有足够的反应速率。
倘若操作条件不适当,析碳反应严重,生成的碳会覆盖在催化剂内外表面,致使催化剂活性降低,反应速率下降。
析碳更严重,床层堵塞,阻力增加,催化剂毛细孔内的碳遇水蒸汽会剧烈汽化,致使催化剂崩裂或粉化,迫使停工,经济损失巨大。
所以对于烃类蒸汽转化过程要特别主要防止析碳,而高温有利于甲烷裂解析碳,不利于一氧化碳歧化析碳,也不利于还原析碳,却有利于碳被水蒸气所气化,温度越高,水蒸气比例越大,则越有利于消碳;如果气相中22CO H 、分压很大时,均有利于抑制析碳。
由此可见,影响甲烷水蒸气转化反应平衡的主要因素有温度、水碳比和压力。
温度的影响甲烷与水蒸气反应生成2H CO 和吸热的可逆反应,高温对平衡有利,即2H CO 和的平衡产率高,4CH 平衡含量低。
一般情况下,当温度提高10℃,甲烷的平衡含量可降低1%-1.3%,高温对一氧化碳变换反应的平衡不利,可以少生成二氧化碳,而且高温也会抑制一氧化碳歧化和还原析碳的副反应。
但是,温度过高,会有利于甲烷裂解,当温度高于700℃时,甲烷均相裂解速率很快,会大量析出碳,并沉淀在催化剂和器壁上。
水碳比的影响水碳比对于甲烷转化影响重大,高的水碳比有利于甲烷的蒸气重整反应,在800℃、2Mpa 条件下,水碳比由3提高到4时,甲烷平衡含量由8%将至5%,可见水碳比对甲烷平衡含量影响是很大的。
同时,高水碳比也有利于抑制析碳副反应。
压力的影响甲烷蒸汽转化反应是体积增大的反应,低压有利于平衡,当温度800℃、水碳比4时,压力由2Mpa 降低到1Mpa 时,甲烷平衡含量由5%降至2.5%。
低压也可抑制一氧化碳的两个析碳反应,但是低压对甲烷裂解析碳反应平衡有利,适当加压可抑制甲烷裂解。
压力对一氧化碳变换反应平衡无影响。
总之,从反应平衡考虑,甲烷水蒸气转化过程应该用适当的高温、稍低的压力和高水碳比。
甲烷水蒸气转化催化剂甲烷水蒸气转化,在没有催化剂的情况下反应速率很慢,然而在高温下甲烷会裂解,这样会导致没有工业生产价值,所以必须使用催化剂。
催化剂的组成和结构决定了其催化性能,而对其使用是否得当会影响其性能的发挥。
甲烷水蒸气转化对催化剂的基本要求是高强度、高活性、抗析碳、热稳定性好。
工业装置使用的催化剂均以Ni 为活性组分。
载体通常都用硅铝酸钙、铝酸钙以及难熔的耐火氧化物,如32O Al 、MgO 、CaO 、ZIo2、2TiO 等。
随着工业条件的改变.对载体的耐压、强度也有不同要求。
近年来一般使用32O Al a 作为载体。
目前国内外开发的低Ni 型天然气蒸汽转化催化剂含NiO 12%,而ICI 公司近年来研制的PALL 环负载NiO 量只有2.7%,其活性与工业转化催化剂相同,可见降低Ni 用量还大有潜力。
甲烷水蒸气转化反应动力学 当有催化剂时,反应活性能降低,转化速率显著增大,在700-800℃时已具有工业生产价值。
催化剂的活性越高,反应速率越快。
对于一定的催化剂而言,影响反应速率的主要因素有温度、压力和组成。
温度温度升高,反应速率常数k 增大,反应速率也增大。
压力总压增高,会使各组分的分压也增高,对反应初期的速率提高很有利。
此外,加压尚可使反应体积减少。
组分原料的组成由水碳比决定,42/CH O H 过高时,虽然水蒸气分压高,但甲烷分压过低,反应速率不一定高;反之,42/CH O H 过低时,反应速率也不会高。
所以水碳比要适当。
在反应初期,反应物O H CH 24和的浓度高,反应速率高。
到反应后期,反应物浓度下降,产物浓度增高,反应速率降低,需要提高温度来补偿。
转化反应是气固相催化过程,包括内外扩散和催化剂表面上吸附、反应、产物脱附和扩散等多个步骤,每个步骤对整个过程的总速率都有影响,最慢的一步控制了总速率。
上述动力学方程式是本征动力学方程式。
在工业生产中,反应器内气流速度较快,外扩散影响可以忽略。
但为了减少床层阻力,所用催化剂颗粒较大(>2mn),故内扩散阻力较大,催化剂内表面利用率较低。
在500℃左右时,内表面利用率越30%;温度升到800℃时,内表面利用率仅有1%,这是因为温度升高,表面反应速率加快,孔口侧的反应物消耗快,细孔内反应物浓度因内扩散阻力大而随孔长下降迅速,更多内表面没有被利用。
所以,在工业生产中的反应速率r '低于本征动力学速率r ,两者关系为r r η='。
r '考虑了传质过程的影响,减少催化剂的成型颗粒尺寸和制成环形或车轮形或多孔球形,可以提高内表面利用率,从而提高表观反应速率。
甲烷水蒸气转化过程的工艺条件 在选择工艺条件时,理论依据是热力学和动力学分析以及化学工程原理,此外,还需要结合技术经济、生产安全等进行综合优化。
转化过程主要工艺条件有压力、温度、水碳比和空速,这几个条件之间互有关系,要适当匹配。
压力从热力学特征看,低压有利转化反应。
从动力学看,在反应初期,增加系统压力,相当于增加了反应物分压,反应速率加快。
但到反应后期,反应接近平衡,反应物浓度高,加压反而会降低反应速率,所以从化学角度看,压力不宜过高。
但从工程角度考虑,适当提高压力对传热有利,因为甲烷转化过程需要外部供热,大的给热系数是强化传热的前提。
床层给热系数9.0b e a R ∝,提高压力,即提高了介质密度,是提高雷诺数Re 的有效措施。
为了增大传热面积,采用多管并联的反应器,这就带来了如何将气体均匀地分布的问题,提高系统压力可增大床层压降,使气流均布于各反应管。
虽然提高压力会增加能耗,但若合成气是作为高压合成过程(例如合成氨、甲醇等)的原料时,在制造合成气时将压力提高到一定水平,就能降低后序工段的气体压缩功,使全厂总能耗降低。
加压还可以减少设备、管道的体积,提高设备生产强度,占地面积也小。
综上所述,甲烷水蒸气转化过程一般是加压的,大约3Mpa 左右。
温度从热力学角度看,高温下甲烷平衡浓度低,从动力学看,高温使反应速率加快,所以出口残余甲烷含量低。
因加压对平衡的不利影响,更要提高温度来弥补。
在3Mpa 的压力下,为使残余甲烷含量降至0.3%(干基),必须使温度达到1000℃。
但是,在此高温下,反应管的材质经受不了,以耐高温的HK-40合金钢为例,在3Mpa 压力下,要使反应炉管寿命达10年,管壁温度不得超过920℃,其管内介质温度相应为800-820℃。
因此,为满足残余甲烷%3.0≤的要求,需要将转化过程分为两段进行。
第一段转化在多管反应器中进行,管间供热,反应器称为一段转化炉,最高温度(出口处)控制在800℃左右,出口残余甲烷10%(干基)左右。
第二段转化反应器为大直径的钢制圆筒,内衬耐火材料,可耐1000℃以上高温。
对于此结构的反应器,不能再用外加热方法供热。
温度在800℃左右的一段转化气绝热进入二段炉,同时补入氧气,氧与转化气中甲烷燃烧放热,温度升至1000℃,转化反应继续进行,使二段出口甲烷降至0.3%。
若补入空气则有氮气带入,这对于合成氨是必要的,对于合成甲醇或其他产品则不应有氮。
一段转化炉温度沿炉管轴向的分布很重要,在入口端,甲烷含量最高,应着重降低裂解速率,故温度应低些,一般不超过500℃,因有催化剂,转化反应速率不会太低,析出的少量碳也及时气化,不会积碳。
在离入口端1/3处,温度应严格控制不超过650℃,只要催化剂活性好,大部分甲烷都能转化。
1/3处以后,温度高于650℃,此时氢气已增多,同时水碳比相对变大,可抑制裂解,温度又高,消碳速率大增,因此不可能积碳了,之后温度继续升高,直到出口处达到800℃左右,以保证低的甲烷残余量。
因而,一段转化炉是变温反应器。
二段转化炉中温度虽高,但甲烷含量低,又有氧存在,不会积碳。
水碳比水碳比是诸操作变量中最便于调节的一个条件,又对一段转化过程影响较大。
水碳比高,有利于防止积碳,残余甲烷含量也低。
实验指出,当原料气中无不饱和烃时,水碳比若小于2,温度到400℃时会析碳,而当水碳比大于2时,温度要高达1000℃才有碳析出;但若有较多不饱和烃存在时,即使水碳比℃时就会析碳。
为了防止积碳,操作中一般控制水碳比在大于2,当温度4003.5左右。
近年来,为了节能,要降低水碳比,防止积碳可采取的措施有三个,其一是研制、开发新型的高活性、高抗碳性的低水碳比催化剂;其二是开发新的耐高温炉管材料,提高一段炉出口温度;其三是提高进二段炉的空气量,可以保证降低水碳比后,一段出口气中较高残余甲烷能在二段炉中耗尽。
目前,水碳比已可降至3.0,最低者可降至2.75。
气流速度反应炉管内气体流速高有利于传热,降低炉管外壁温度,延长炉管寿命。
当催化剂活性足够时,高流速也能强化生产,提高生产能力。
但流速不宜过高,否则床层阻力过大,能耗增加。
天然气蒸汽转化流程和主要设备天然气蒸汽转化制备合成气的基本步骤如下图所示。
图1 天然气蒸汽转化制合成气过程一段转化炉由辐射段和对流段组成,外壁用钢板制成,炉内壁衬耐火层。