气缸体钻削加工组合机床总体及多轴箱设计
双缸柴油机气缸体钻削组合机床总体及夹具设计开题报告

毕业设计开题论证报告专业机械设计制造及其自动化学生姓名班级 B 机制054学号指导教师完成日期2009 年 3 月31 日的工作台的选择,按照其运动的方式,从液压、机械和气动传动等多种型式中选择一款。
(4)接着选择支承部件,这根据机床选择的配置来选择最好的支承部件。
通用部件的选择是组合机床设计的主要内容之一,遵循其基本的方法:根据所需的功率、进给力、进给速度等要求,选择动力部件及其配套部件。
3.选择好通用部件之后,就要对此钻削组合机床进行总体设计。
(1)首先要对该机床进行必要的工艺方案拟定。
要分析、研究本组合机床的加工要求和现场工艺以便定出切合实际的合理工艺方案。
确定选择基准和夹压部位。
确定影响工艺方案的主要因素,就加工的工序内容和加工精度,就被加工零件的特点,就零件的生产批量和使用厂后方车间的制造能力进行分析总结。
确定工序间余量。
确定刀具结构的选择,但尽量选择标准和简单刀具,要提高工序集中程度或保证加工精度。
(2)还要考虑组合机床的配置类型及结构方案对加工精度、排屑通畅使用条件等等诸多因素的考虑。
(3)课题需要设计的钻削组合机床的设计方案它的分析比较的主要指标很重要,要知道机床的加工精度和生产率,要考虑到机床的使用方便性和自动化程度,还要衡量它的经济性和可靠性。
(4)切削用量的确定也是很重要的,要选择合理的切削量,它对加工精度、生产率、刀具耐用度、结构型式及可靠性影响很大。
4.对机床的总体设计,需要绘制“三图一卡”,即被加工零件工序图、加工示意图、机床联系尺寸总图和编制生产率计算卡。
这是针对具体零件,在选定的工艺和结构方案的基础上,进行组合机床总体方案图样文件设计。
三、解决方案及预期效果该钻削组合机床根据工件加工需要,应是以大量通用部件为基础,配以少量专用部件组成的一种高效的专用机床。
1.机床是对工件的上下两面进行钻削加工,借鉴典型的其他类型的机床,它应该是夹具、中间底座和多轴箱要根据工件的具体尺寸和工艺要求来设计的专用部件,而其他的大部分零部件都可以是标准件和通用件。
气缸体双工位专用钻床总体及夹具设计摘要

气缸体双工位专用钻床总体及夹具设计摘要:本课题设计的是气缸体双工位专用钻床,用于钻削被加工零件左侧面上的12个∅30深110mm的挺柱孔,右侧扩12个∅41的孔、锪挺柱孔∅41端面,并钻削12个∅8和7个∅6的水孔。
本机床设计主要包括总体设计和夹具设计两个部分。
采用卧式双工位双面加工方案,左侧主轴箱用来加工这12个挺柱孔,右侧主轴箱用来完成剩下的31个孔的加工,两主轴箱的中间是夹具部分。
机床采用液压滑台实现刀具的进给,以保证进给速度的稳定可靠。
由于工件左侧12个∅30 mm的挺柱孔之间孔距较小,使得左主轴箱中主轴的排布受到了限制,为此采用双工位分两批加工。
工件选用“一面两孔”的定位方案,采用液压夹紧方式。
为保证工件上被加工孔的位置精度,采用了导向装置。
因工件批量较大,导向装置中的钻套容易磨损,所以采用了可换钻套。
夹具体材料采用HT200,并在夹具体上开设排屑槽以防止切屑在定位元件工作表面上或其他装置中堆积而影响工件的正确定位和夹具的正常工作。
关键词:气缸体;组合机床;总体设计;夹具Design of General and Fixture of Modular Machine Toolwith Double Stations Drilling for the Cylinder BodyAbstract:The modular machine tool is designed for double stations drilling of the cylinder body. It is used for machining these holes in the work piece: twelve holes with the diameter 30mm and depth 110mm on the left side, twelve diameter 41mm holes and their bottom surfaces on the right surface, twelve diameter 8mm and seven diameter 6mm holes. The topic includes two parts, the general design and fixture design of the machine tool.The modular machine tool uses the horizontal-type, double-station and two-side processing plan. The left spindle box is used formachining twelve tappet holes, the right spindle box is used for machining 31 holes, and a fixture is between two spindle boxes. To achieve stable and reliable feed, hydraulic pressure sliding tables are used in this machining tool. The small distance between two tappet holes on the left side of the cylinder body makes arrangement of main spindle in the headstock restricted. Therefore twelve holes on the left side are separated into two groups through double-station machining. The work piece is located at the fixture through "a face two holes", and clamped by hydraulic pressure devices. To ensure position precision, the guiding devices are used. Replaceable guiding sleeves are chosen, because they are easy wearing in large quantities of production. The material of clamp body is HT200. Chip troughs which are in the clamp body are free of chip falling onto the working surface of positioning components or accumulating on other devices, and ensure the work piece correct positioning and the fixture normal working.Key words:cylinder body; modular machine tool; general design; fixture。
R180柴油机气缸体三面钻削组合机床总体及左主轴箱设计说明书

目录1 前言 (1)2组合机床总体设计 (3)2.1总体方案论证 (3)2.1.1被加工零件特点 (3)2.1.2工艺路线的确定 (3)2.1.3机床配置型式的选择............... (3)2.1.4定位基准的选择 (4)2.1.5滑台型式的选择............... (4)2.2切削用量的确定及刀具选择 (4)2.2.1 切削用量选择 (4)2.2.2切削力、切削扭矩及切削功率计算 (5)2.3组合机床总体设计—三图一卡 (6)2.3.1被加工零件工序图 (6)2.3.2加工示意图 (7)2.3.3 机床尺寸联系总图 (9)2.3.4 机床生产率计算卡 (11)3 组合机床主轴箱设计 (14)3.1 主轴箱原始依据图的绘制 (14)3.2主轴结构型式的选择和动力计算 (15)3.3 主轴箱传动系统的设计与计算 (15)3.3.1 根据原始依据图对坐标尺寸的计算 (15)3.3.2 主轴箱传动路线的拟订 (15)3.3.3 传动轴位置及齿轮齿数的确定 (16)3.4 主轴箱坐标计算、坐标检查图的绘制 (19)3. 4.1传动轴的坐标的计算 (19)3.4.2坐标检查图的绘制 (20)3.5 轴、齿轮、轴承、键的校核 (20)3.5.1轴的校核 (20)3.5.2齿轮的校核 (21)3.5.3轴承的寿命校核 (23)3.5.4键的强度计算 (24)3.6主轴箱前、后盖及箱体设计 (24)3.7主轴箱上附件材料的设计 (25)4结论 (26)参考文献 (27)致谢 (28)附件清单 (29)1 前言本次毕业设计的课题来源于盐城市江动集团,课题是关于R180柴油机气缸体三面钻削组合机床的设计。
R180柴油机是该集团大批量生产的产品之一,为保证柴油机气缸体三面孔的加工和相应的位置精度,提高生产效率而设计的一台三面钻削的卧式组合机床。
为了加深在组合机床方面的认识,了解并收集相关设备的技术资料,以便完善我们对主轴箱的设计,学院组织我们去江动集团进行生产实习。
气缸体钻削加工组合机床总体及多轴箱设计
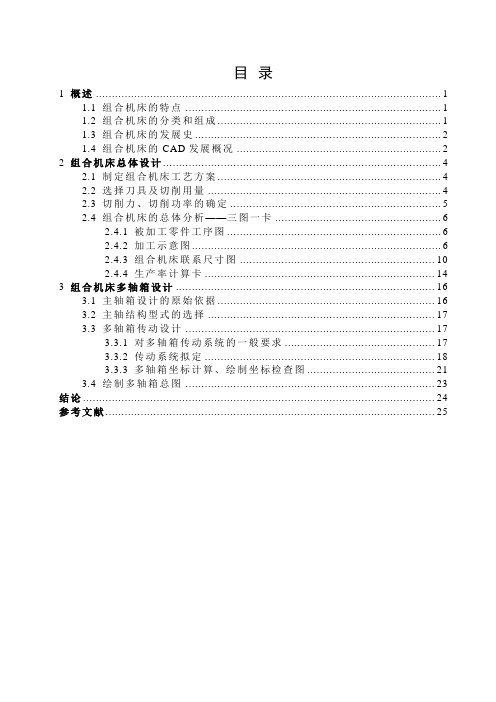
目录1 概述 (1)1.1 组合机床的特点 (1)1.2 组合机床的分类和组成 (1)1.3 组合机床的发展史 (2)1.4 组合机床的CAD发展概况 (2)2 组合机床总体设计 (4)2.1 制定组合机床工艺方案 (4)2.2 选择刀具及切削用量 (4)2.3 切削力、切削功率的确定 (5)2.4 组合机床的总体分析——三图一卡 (6)2.4.1 被加工零件工序图 (6)2.4.2 加工示意图 (6)2.4.3 组合机床联系尺寸图 (10)2.4.4 生产率计算卡 (14)3 组合机床多轴箱设计 (16)3.1 主轴箱设计的原始依据 (16)3.2 主轴结构型式的选择 (17)3.3 多轴箱传动设计 (17)3.3.1 对多轴箱传动系统的一般要求 (17)3.3.2 传动系统拟定 (18)3.3.3 多轴箱坐标计算、绘制坐标检查图 (21)3.4 绘制多轴箱总图 (23)结论 (24)参考文献 (25)1 概述1.1 组合机床的特点组合机床是由大量的通用部件和少量专用部件组成的工序集中的高效率专用机床。
它能够对一种(或几种)零件进行多刀、多轴、多面、多工位加工。
在组合机床上可以完成钻孔、扩孔、锪孔、铰孔、镗孔、铣削平面、切削内外螺纹以及加工外圆和端面等工序,生产效率比通用机床高几倍至几十倍,且加工精度十分稳定。
组合机床一般用于加工箱体类或特殊形状的零件。
加工时,工件一般不旋转,由刀具的旋转运动和刀具与工件的相对进给运动,来实现。
有的组合机床采用车削头夹持工件使之旋转,由刀具作进给运动,也可实现某些回转体类零件(如飞轮、汽车后桥半轴等)的外圆和端面加工。
组合机床与通用机床、其他专用机床比较,具有以下特点:1)组合机床上的通用部件和标准零件约占全部机床零、部件总量的70~80%,因此设计和制造的周期短,投资少,高效率,经济效果好。
2)由于组合机床采用多刀加工,并且自动化程度高,因此比通用机床生产效率高,产品质量稳定,劳动强度低。
组合机床总体及主轴箱的设计

1前言1.1研究的目的和意义主轴箱是选用通用零件,按专业要求进行设计的。
它通过按一定速比排布传动齿轮,把动力从动力部件——动力头、动力箱、电动机等传递给各工作主轴,使之获得所要求的转速和转向。
主轴箱主轴前端外伸部分和机床刀具装置连接,从而完成被加工零件。
目的是熟练利用CAD绘图软件进行绘图,掌握基本的设计方法和能力,为以后的学习和工作打下良好的基础。
研究汽缸盖钻铰组合机床不但有助于汽缸盖的加工水平提高,从而提高我国的汽车生产水平,而且对我国组合机床的发展也有重要意义。
1.2国内外研究现状我国的组合机床产业发展比较晚,原因之一是我国整体的工业发展就比较晚,其次我国的工业水平已经落后了一大截。
组合机床的发展是由汽车产业的带动,由专用机床发展而来的。
改革开放后,我国的组合机床产业得到了很大的发展,特别是民营企业对发展组合机床起到了很大的作用,他们的设计和改良使得组合机床的效率和加工水平得到了极大的提高。
我国的组合机床主要优势在于劳动力密集,缺点是精度不高,没有什么科技水平。
工业革命后,国外的工业发展很快,组合机床的发展更是如此。
由于他们的起步早,发展到现在,组合机床的种类繁多,可以满足用户和生产的各种需求。
国外的组合机床自动化程度高,广泛使用了数控技术,不仅提高了生产效率,而且对操作人员的安全有保障。
1.3研究内容和方法组合机床总体设计是针对具体的被加工零件,在选定工艺方案和结构方案的基础上,进行方案图纸设计,本设计要求完成机床联系尺寸图、被加工零件工序图、加工示意图。
主轴箱传动系统是多轴、多齿轮、多排次的复杂齿轮传动系统。
在完成组合机床总体设计之后,利用CAD绘图软件设计有四根主轴的主轴箱,主轴的转速分别为200r/min。
根据所提供的技术数据,选择主要通用部件,然后按照组合机床设计步骤进行:绘制机床总图、加工工序图、计算切削用量及绘制加工示意图、主轴箱传动系统设计(4轴n=200r/min),最后绘制主轴箱装配图和主要零件图,并写出设计说明书。
机械机床毕业设计7485柴油机缸体螺栓底孔加工组合机床设计(多轴箱)
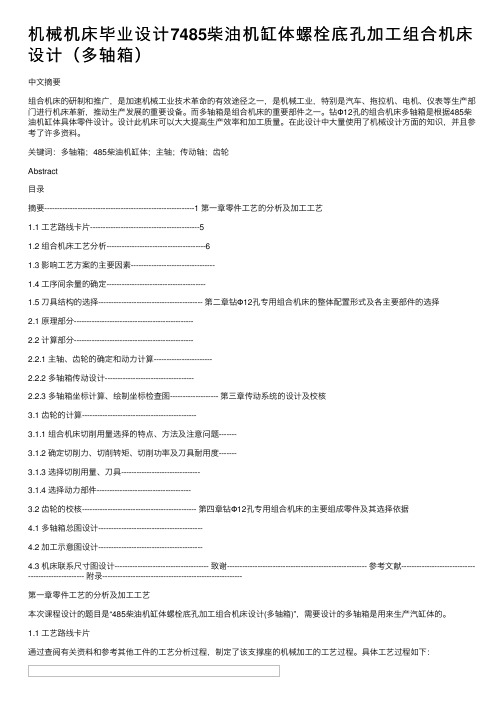
机械机床毕业设计7485柴油机缸体螺栓底孔加⼯组合机床设计(多轴箱)中⽂摘要组合机床的研制和推⼴,是加速机械⼯业技术⾰命的有效途径之⼀,是机械⼯业,特别是汽车、拖拉机、电机、仪表等⽣产部门进⾏机床⾰新,推动⽣产发展的重要设备。
⽽多轴箱是组合机床的重要部件之⼀。
钻Φ12孔的组合机床多轴箱是根据485柴油机缸体具体零件设计。
设计此机床可以⼤⼤提⾼⽣产效率和加⼯质量。
在此设计中⼤量使⽤了机械设计⽅⾯的知识,并且参考了许多资料。
关键词:多轴箱;485柴油机缸体;主轴;传动轴;齿轮Abstract⽬录摘要-----------------------------------------------------------1 第⼀章零件⼯艺的分析及加⼯⼯艺1.1 ⼯艺路线卡⽚-------------------------------------------51.2 组合机床⼯艺分析---------------------------------------61.3 影响⼯艺⽅案的主要因素---------------------------------1.4 ⼯序间余量的确定---------------------------------------1.5 ⼑具结构的选择----------------------------------------- 第⼆章钻Φ12孔专⽤组合机床的整体配置形式及各主要部件的选择2.1 原理部分-----------------------------------------------2.2 计算部分-----------------------------------------------2.2.1 主轴、齿轮的确定和动⼒计算-----------------------2.2.2 多轴箱传动设计-----------------------------------2.2.3 多轴箱坐标计算、绘制坐标检查图------------------- 第三章传动系统的设计及校核3.1 齿轮的计算---------------------------------------------3.1.1 组合机床切削⽤量选择的特点、⽅法及注意问题-------3.1.2 确定切削⼒、切削转矩、切削功率及⼑具耐⽤度-------3.1.3 选择切削⽤量、⼑具-------------------------------3.1.4 选择动⼒部件-------------------------------------3.2 齿轮的校核--------------------------------------------- 第四章钻Φ12孔专⽤组合机床的主要组成零件及其选择依据4.1 多轴箱总图设计-----------------------------------------4.2 加⼯⽰意图设计-----------------------------------------4.3 机床联系尺⼨图设计------------------------------------- 致谢------------------------------------------------------- 参考⽂献--------------------------------------------------- 附录-------------------------------------------------------第⼀章零件⼯艺的分析及加⼯⼯艺本次课程设计的题⽬是“485柴油机缸体螺栓底孔加⼯组合机床设计(多轴箱)”,需要设计的多轴箱是⽤来⽣产汽缸体的。
468Q发动机缸体双面卧式组合钻床总体设计及右主轴箱设计资料

468Q发动机缸体双面卧式组合钻床总体设计及右主轴箱设计资料对于发动机缸体双面卧式组合钻床总体设计及右主轴箱设计资料,需要一定的技术知识和详细的描述才能得到满足要求的1200字以上的文章。
发动机缸体双面卧式组合钻床是一种专门用于处理发动机缸体工件的机床。
它采用卧式结构,钻床的两侧设有工作台,可同时进行两面的加工操作。
这种设计能够提高生产效率和加工精度。
对于总体设计来说,首先需要考虑机床的功能需求和性能指标。
发动机缸体加工通常包括钻孔、铰孔和粗加工等多个过程。
机床需要满足这些加工要求,并具备可行性和经济性。
设计者还需要考虑到加工工艺的合理性和操作的便捷性。
在组合钻床的总体设计中,需要充分考虑机床的结构和布局。
机床结构需要具备稳定性、刚性和刚性。
特别是在钻孔加工过程中,需要保证机床的稳定性,避免加工误差和振动。
布局方面,需要合理安排工作台、主轴箱、刀具更换装置等部件的位置,以保证加工效率和操作便捷。
主轴箱是组合钻床的核心部件之一,对总体设计和性能有重要影响。
在右主轴箱的设计中,需要考虑主轴和刀具的固定和调整方式、切削液系统、冷却系统等。
设计者还需要充分考虑主轴的转速、功率和加工精度等参数,以保证加工质量和效果。
在设计资料方面,需要提供机床的总装图、分解图和零件图。
总装图应精确描述机床的各个部件的位置和安装方式。
分解图和零件图则详细说明每个部件的结构和尺寸。
此外,还需要提供有关机床性能参数和加工工艺的资料,例如加工速度,加工精度等。
综上所述,发动机缸体双面卧式组合钻床总体设计及右主轴箱设计资料需要充分考虑机床的功能需求、结构、布局和性能指标。
在设计资料中需要提供详细的机床图纸和加工工艺资料。
通过此类资料,可以为生产厂家提供准确和详细的设计参考,以满足发动机缸体加工的要求。
468Q发动机缸体双面卧式钻床总体设计及左主轴箱设计

前言毕业设计是按照教学计划的规定,必须进行的一个重要的综合性教学环节,使学生所学的知识在实践中得到具体应用。
通过这次设计,能使学生全面了解和掌握一些机械设备方面的知识,便于使自己形成一套设计的思维模式,而且使所学的知识系统化地由理论转向实践,以培养学生对知识的综合运用能力,为毕业后走上工作岗位打下一个良好的基础。
同时通过认真的设计,可以提高学生分析和解决问题的能力,以便更好的适应社会。
本设计的主要内容有:组合机床的概述、组合机床通用部件及其选用、组合机床总体设计、组合机床主轴箱设计、组合机床技术设计五个部分。
本设计以提高生产率和保证加工精度为目的,以较充足的专业课知识为基础,结合毕业设计任务书,在收集和参考大量资料的前提下独立完成。
设计基本上做到:图纸绘制基本符合国家标准,做到布局合理,图纸也基本能够正确、完整、清晰的表达出零件的形状及尺寸。
计算说明书的条理较清晰,语言通顺流畅,图表和公式的编辑也基本符合毕业论文撰写规范。
在设计过程中,尽量采用通用部件,为组合机床的生产提供便利条件。
其中主轴箱的设计是重点,也是难点。
主轴箱设计应充分考虑被加工零件的形状及加工要求,合理布置传动及齿轮的位置。
尤其在齿轮设计上,更要反复验算转速,努力作出最合理的设计方案。
摘要组合机床使用系列化、标准化的通用部件和少量的专用部件组成的多轴、多刀、多工序、多面或多工位同时加工的高校专用机床,其生产率比通用机床高几倍至几十倍,可进行钻、镗、铰、攻丝、车削、铣削等切削加工。
组合机床的通用部件和标准件约占70-80%,这些部件是系列化的,可以进行成批生产.其余20-30%的专用部件是由被加工零件的形状,轮廓尺寸,工艺和工序来决定。
在批量生产中这了提高生产率,必须要缩短加工时间和辅助时间,而且尽可能使辅助时间和加工时间重合,使每个装夹多外工件同时进行多刀加工,实行工序高度集中,因而广泛采用组合机床及自动线。
关键词:组合机床,主轴箱,切削AbstractAggregate machine-tool use seriation , the standardized general part and the few special-purpose parts compose the university special purpose machine which multiple spindle, the multi-knives, the multi-working procedures, the multi-surface or the multi-locations simultaneously process, its productivity compared to general engine bed high several times to several dozens times, may carry on drills, the boring, the articulation, attacks machinings and so on the silk, turning, milling. The aggregate machine-tool general part and the standard letter approximately compose 70-80%, these parts are the seriation , may carry on the mass productions. Other 20-30% special-purpose part is by is processed the components the shape, the overall size, the craft and the working procedure decided.This enhanced the productivity in the volume production, must have to reduce the process period and the non-cutting time, moreover causes the non-cutting time and the process period superposition as far as possible, causes each attire to clamp many outside work pieces simultaneously to carry on the multi-knife processing, implements the working procedure high degree of concentration, thus widely uses the aggregate machine-tool and from generatrix .Key word: Aggregate machine-tool, headstock, cutting目录前言 (i)摘要 (ii)Abstract (iv)第一章概述 (1)第一节组合机床的组成 (1)第二节组合机床的类型 (2)一、具有固定夹具的单工位组合机床 (2)二、具有移动夹具的多工位组合机床 (3)三、转塔式组合机床 (4)第二章组合机床设计概述 (5)第一节组合机床及其特点 (5)第二节组合机床工艺范围及加工精度 (6)一、组合机床的工艺范围 (6)二、组合机床的加工精度 (6)第二节采用组合机床的经济分析 (7)第三节组合机床的发展趋势 (8)一、提高通用部件的水平 (8)二、发展适应中、小批生产的组合机床 (8)三、采用新刀具 (8)四、发展自动监测技术 (9)五、扩大工艺范围 (9)第三章组合机床通用部件及其选用 (9)第一节通用部件的类型 (10)一、通用部件的分类 (10)二、通用部件的型号、规格及配套关系 (10)第二节常用通用部件 (11)第三节通用部件的选用 (11)第四章组合机床总体设计 (12)第一节组合机床方案设计 (13)一、拟定方案阶段、 (13)二、技术设计阶段 (13)三、工作设计阶段 (13)第二节零件分析 (13)一、气缸体的功用和结构特点 (13)二、基准的选择 (14)三、加工阶段的划分 (14)第五章绘制“三图一卡” (15)第一节加工工序图 (16)一、被加工零件工序图的作用和要求 (16)二、被加工零件工序图的内容 (16)三、编制被加工零件工序图的注意事项 (16)第二节加工示意图 (17)一、被加工零件示意图的作用: (17)二、被加工零件示意图的内容: (17)三、选择刀具、导向及有关计算 (17)四、加工示意图简图 (20)第三节机床联系尺寸图 (21)一、被加工零件联系尺寸图的作用: (21)二、被加工零件联系尺寸图的内容: (21)三、动力部件的选择 (21)四、组合机床其它尺寸的确定 (22)五、机床联系尺寸图简图: (24)第六章多轴箱——右主轴箱设计 (24)第一节多轴箱的基本结构 (24)第一节通用多轴箱设计 (25)一、绘制多轴箱设计原始依据图 (25)二、主轴、齿轮的确定及动力运算 (28)三、多轴箱传动设计 (30)四、多轴箱坐标计算、绘制坐标检查图 (33)第三节多轴箱的传动设计方案 (36)一、传动设计方案分析 (36)二、传动系统的设计计算 (36)第四节绘制多轴箱总图及零件图 (40)外文资料 (41)中文译文 (50)致谢 ................................................ 错误!未定义书签。
柴油机气缸体钻削组合机床总体和后主轴箱设计

柴油机气缸体三面钻削组合机床总体及后主轴箱设计摘要:课题来源于江动集团,ZH1105W型柴油机是该集团大批量生产的产品之一。
本课题设计的是柴油机气缸体三面钻削组合机床,用于加工被加工零件左、右、后三个面上的31个光孔。
该机床设计的重点是总体设计和后主轴箱设计两部分。
总体设计包括机床配置型式的确定、结构方案的选择以及“三图一卡”的绘制。
后主轴箱设计包括绘制主轴箱设计原始依据图、确定主轴和齿轮、完成动力计算、设计传动系统、绘制多轴箱装配图和零件补充加工图。
在进行组合机床总体设计时,首先应根据柴油机气缸体后侧面上钻6个孔的位置精度、表面粗糙度及其他技术要求,拟订总体方案。
主轴箱是需要大量生产的零件。
在多轴箱设计中,设计的主要思路是把原有的多道工序的单孔加工改为多孔同时加工,这样设计主要是为了解决由多次装夹引起的定位误差问题,保证了孔的位置精度。
本组合机床效率高,成本低,加工精度高,操作使用方便,减轻了工人的劳动强度,提高了劳动生产率。
关键词:组合机床;总体设计;后主轴箱设计本设计来自:完美毕业设计网登陆网站联系客服远程截图或者远程控观看完整全套论文图纸设计客服QQ:8191040Design of General and Rear Headstock of Modular Machine Tool for Drilling Holes on Three-Side of CylinderBodyAbstract: This subject comes from Jianghuai power group, Model ZH1105W Diesel is the one of the products of mass production. This issue is the design of modular machine tool surface for drilling holes on three-side of cylinder diesel,The modular machine tool is used to drill 31 holes, which are on the left, right and rear surface.The important point of this topic is the system design and the rear headstockdesign. The system design includes the definite of the modular machine tool, the selecting of the structure plan and the drawing of “three pictures and one card”. The rear headstock design includes drawing the primitive basic chart for the headstock, determining the spindle and the gears, completing the power computation, designingthe transmission system, drawing the headstock assembly drawing and the part processing chart.Conducting modular machine to system design,first under-cylinder diesel engine rear surface drilling 6 holes accuracy of the location, surface roughness, and other technical requirements,develop overall program.The headstock is a product which needs mass production. Headstock in the design, the design is the main ideas from the original multi-channel process to the processing of porous single hole while processing, this design is mainly to solve the fixture by the time the positioning error caused the problems to ensure the accuracy of the location of holes.This modular mechanical tool has some advantages such as high efficiency, low cost as high precessing precision, operating easily and reduceing the worker’s labor intensity, enhancing the productivity.Key word: Modular machine tool; The system design; The rear headstock design目录1 前言 (2)1.1 课题内容 (2)1.2 课题由来 (2)1.2.1 课题背景 (2)1.2.2 课题要求 (2)1.3 组合机床国内外发展概述 (2)1.4 本课题主要解决的问题和总体设计思路 (1)1.4.1 主要解决的问题 (1)1.4.2 总体设计思路.................................... 错误!未定义书签。
气缸体双工位专用钻床总体及左主轴箱设计说明书

目录1前言 (1)2 总体设计 (3)2.1总体方案论证 (3)2.1.1 加工对象工艺性的分析 (3)2.1.2 机床配置型式的选择 (3)2.1.3 定位基准的选择 (3)2.2确定切削用量及选择刀具 (4)2.2.1 选择切削用量 (4)2.2.2 计算切削力、切削扭矩及切削功率 (5)2.2.3 选择刀具结构 (5)2.3组合机床总体设计—“三图一卡” (6)2.3.1 被加工零件工序图 (6)2.3.2 加工示意图 (6)2.3.3 机床联系尺寸图 (7)2.3.4 机床生产率计算卡............................................................ 错误!未定义书签。
2.4夹具轮廓尺寸的确定........................................................... 错误!未定义书签。
3 组合机床左主轴箱设计.......................................................... 错误!未定义书签。
3.1绘制左主轴箱设计原始依据图........................................... 错误!未定义书签。
3.2主轴结构型式的选择及动力计算....................................... 错误!未定义书签。
3.2.1 主轴结构型式的选择........................................................ 错误!未定义书签。
3.2.2 主轴直径和齿轮模数的初步确定.................................... 错误!未定义书签。
3.2.3 主轴箱动力计算................................................................ 错误!未定义书签。
缸体钻孔组合机床设计

缸体钻孔组合机床设计摘要组合机床是根据工件加工需要,以大量通用部件为基础。
配以少量专用部件组成的一种高效率专用机床。
本次设计的是汽缸体双面钻孔组合机床,汽缸体是发动机的主要部件,属于大批大量生产的零件,从经济性上考虑,为适应生产需求采用组合机床较为合理。
根据组合机床的特点,设计步骤主要包括:调查研究、总体方案设计、技术设计、工作设计。
调查研究:根据被加工零件图样,研究其尺寸、形状、材料、硬度、重量、加工部位的结构及加工精度和表面粗糙度要求等内容。
同时深入调查了解生产现场状况。
总之,通过调查研究应为组合机床总体设计提供必要的大量的数据、资料,做好充分的、全面的技术准备。
总体方案设计:组要包括制定工艺方案、确定机床配置形式、制定影响机床总体布局和技术性能的主要部件的结构方案。
总体设计的具体工作是编制“三图一卡”,即绘制被加工零件工序图、加工示意图、机床尺寸联系图,编制生产效率计算卡。
技术设计:根据总体设计已经确定的“三图一卡”,设计机床个专用部件正式总图,如设计夹具、多轴箱等装配图以及根据运动部件有关参数和机床循环要求,设计液压和电气控制原理图。
工作设计:当技术设计通过审后即可展开工作设计,即绘制各个专用部件的施工图样、编制各个部件零件明细表。
通过以上设计步骤,本次设计的汽缸体双面钻孔组合机床充份满足了生产需求,达到了预期的设计目标。
关键词:组合机床,三图一卡,多轴箱,夹具Cylinder body Drilling Modular Machine Tools DesignABSTRACTMachine Tool is required under the workpiece, based on a large number of common components. Accompanied by a small amount of the composition of specific parts of a machine tool with high efficiency.The design of the cylinder body combination double drilling machine, cylinder body is the main engine components, is a large number of mass-produced components, from the economy be considered, to meet the production needs of combination machine tool is reasonable. Machine according to portfolio characteristics, the design steps include: research, overall program design, technical design, job design.Research: According to the parts to be machined patterns, to study the size, shape, material, hardness, weight, structure and machining parts machining accuracy and surface roughness requirements and so on. Also in-depth investigation to find out about on-site conditions. In short, through the research design should provide the necessary combination of machine tool large amounts of data, information, and make full and comprehensive technical preparation.Overall Design: Group program to include the development process to determine the tool configurations, the machine tool to develop the overall layout and technical performance of the main components of the structure of the program. Overall design of the concrete work is the preparation of the "three plans a card", drawn by processing parts that process map, process diagram, machine size contact map, the preparation of production efficiency calculation card.Technical design: According to the overall design has been identified "three map one card" design tool dedicated official general plan components, such as the design of fixtures, and other multi-axle box assembly diagram and the parameters under the moving parts and machine cycle requirements, design of hydraulic and electrical control schematic.Work Design: When the technical design through post-trial to begin work as designed, or drawn construction drawings of various specific components, the preparation of the various components parts list.The above design steps, this design of cylinder body Drilling Modular Machine Tools fully meet the production needs to reach the desired design goals.KEY WORDS: machine tool, the three plans for a card, multi-axle box, fixture前言 (1)第1章组合机床总体设计 (3)1.1 工艺方案拟定 (3)1.1.1 确定组合机床工艺方案的基本原则及注意问题 (3)1.1.2 组合机床工艺方案的拟定 (3)1.1.3 确定组合机床配置型式及结构方案应考虑的问题 (5)1.2 切削用量的确定 (5)1.2.1 组合机床切削用量选择的特点、方法及注意问题 (5)1.2.2 确定切削力、切削转矩、切削功率及刀具耐用度 (5)1.3 组合机床总体设计—“三图一卡” (6)1.3.1 被加工零件工序图...................... 错误!未定义书签。
机械机床毕业设计120基于三维的柴油机气缸盖组合钻床总体及夹具设计

机械机床毕业设计120基于三维的柴油机气缸盖组合钻床总体及夹具设计柴油机气缸盖是柴油机中重要的部件之一,其组合钻床是用于加工气缸盖的关键设备之一、本文将就基于三维的柴油机气缸盖组合钻床总体及夹具设计进行详细介绍。
首先,柴油机气缸盖组合钻床的总体设计。
根据柴油机气缸盖的特点和加工要求,设计了一台三轴数控钻床。
该钻床由机床主体、主轴系统、进给系统、控制系统和润滑系统等组成。
机床主体采用钢铁结构,具有良好的刚性和稳定性。
主轴系统采用高精度主轴轴承和主轴驱动装置,可以实现稳定的高速运转。
进给系统采用伺服驱动,具有高精度和稳定性。
控制系统采用数控控制,可以实现多个坐标轴的精确控制和编程操作。
润滑系统采用分区润滑,可以实现对机床各个部位的润滑和冷却。
其次,柴油机气缸盖组合钻床的夹具设计。
夹具是用于固定工件并实现其加工的装置。
针对柴油机气缸盖的形状和尺寸特点,设计了适应性强、稳定性好的夹具。
夹具采用可调节的夹持方式,可以适应不同尺寸和形状的气缸盖。
夹具的夹持力可以通过调节螺栓的紧固程度来实现。
夹具采用特殊材料和表面处理,具有良好的摩擦性和耐磨性,可以有效防止工件的位移和变形。
最后,根据柴油机气缸盖的加工工艺要求,对柴油机气缸盖组合钻床进行了性能测试。
测试结果表明,钻床具有较高的加工精度和稳定性,满足了柴油机气缸盖的加工需要。
综上所述,基于三维的柴油机气缸盖组合钻床总体及夹具设计,可以实现对柴油机气缸盖的高效加工。
该设计具有一定的创新性和实用性,对于提高柴油机气缸盖的加工质量和生产效率具有重要意义。
希望本文的设计思路和方法对相关领域的研究者和工程师有所启发。
组合机床多轴箱设计 毕业设计讲解
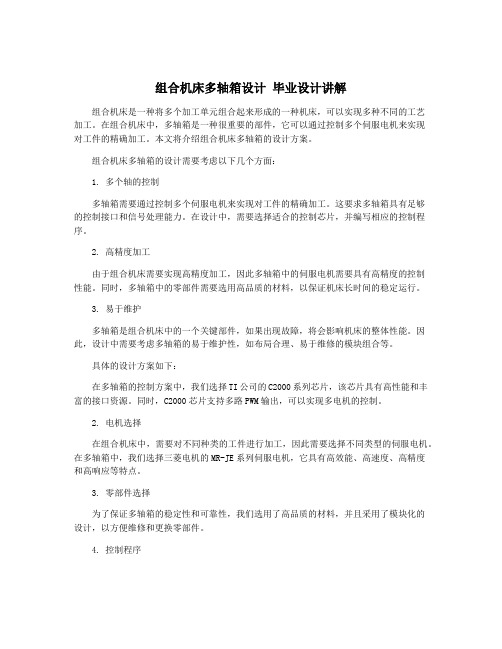
组合机床多轴箱设计毕业设计讲解组合机床是一种将多个加工单元组合起来形成的一种机床,可以实现多种不同的工艺加工。
在组合机床中,多轴箱是一种很重要的部件,它可以通过控制多个伺服电机来实现对工件的精确加工。
本文将介绍组合机床多轴箱的设计方案。
组合机床多轴箱的设计需要考虑以下几个方面:1. 多个轴的控制多轴箱需要通过控制多个伺服电机来实现对工件的精确加工。
这要求多轴箱具有足够的控制接口和信号处理能力。
在设计中,需要选择适合的控制芯片,并编写相应的控制程序。
2. 高精度加工由于组合机床需要实现高精度加工,因此多轴箱中的伺服电机需要具有高精度的控制性能。
同时,多轴箱中的零部件需要选用高品质的材料,以保证机床长时间的稳定运行。
3. 易于维护多轴箱是组合机床中的一个关键部件,如果出现故障,将会影响机床的整体性能。
因此,设计中需要考虑多轴箱的易于维护性,如布局合理、易于维修的模块组合等。
具体的设计方案如下:在多轴箱的控制方案中,我们选择TI公司的C2000系列芯片,该芯片具有高性能和丰富的接口资源。
同时,C2000芯片支持多路PWM输出,可以实现多电机的控制。
2. 电机选择在组合机床中,需要对不同种类的工件进行加工,因此需要选择不同类型的伺服电机。
在多轴箱中,我们选择三菱电机的MR-JE系列伺服电机,它具有高效能、高速度、高精度和高响应等特点。
3. 零部件选择为了保证多轴箱的稳定性和可靠性,我们选用了高品质的材料,并且采用了模块化的设计,以方便维修和更换零部件。
4. 控制程序在多轴箱的控制程序中,我们采用PID算法对电机进行控制,并且增加了伺服电机的保护机制,以避免损坏电机和其他设备。
通过以上的设计方案,我们可以实现一个高性能、高精度、易维护的组合机床多轴箱。
该方案在实际应用中已得到验证,具有较好的稳定性和加工精度。
气缸体双工位专用钻床总体及左主轴箱设计
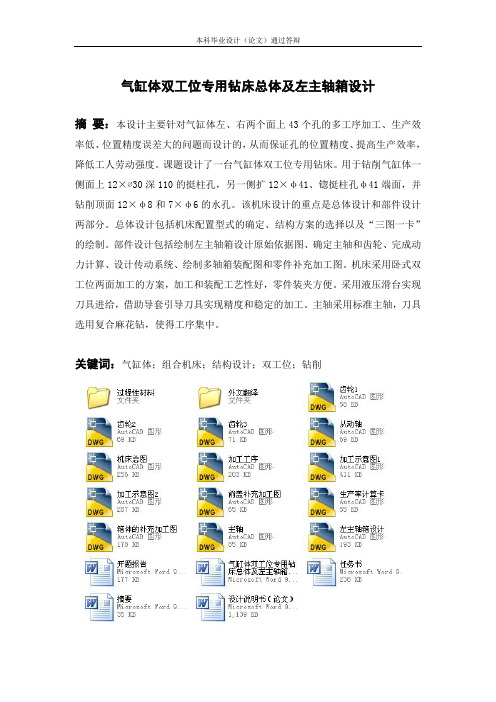
Design of General and left spindle Box ofModularMachine Tool for Cylinder Body
Abstract:This design is mainly directed at problems which are the lowproduction efficiencyand thebigerrorsontheirposition precisionwhenthemachining of43 holesontheright and left sides of the cylinder bodyare doneseparatelyinmulti-working procedures. In order to guaranteetheirposition precision oftheholes, enhance production efficiency and reduce the labor intensity of workers, amodularmachine tool for drilling the cylinder body is designed. Themachinetoolisused fordrillingtwelvetappet holeswith thediameter30mmand depth110mmon one side of the cylinderbody, expanding themandtheir bottomsurfacesto thediameter40mmon the other side,and drillingtwelvediameter8mmand sevendiameter6mmwaterholes.Thistopicisaboutthe general design and theleft spindle boxdesignof the machine tool.Thegeneraldesign includesthe arrangingofthe modular machine tool, thechoosingof the structure plan and the completing of“threedrawings and one card”(theworking proceduredrawing of the partmachined, the general drawing of modular machine tool,thedrawing of cutter display and thecalculationcard ofproductivity).Theleft spindle boxdesign includesdrawing the primitive basic chart for the gear box,determiningthe spindle and the gears, completing the power computation, designing the transmission system, drawing assembly drawingofthe gear box and thesupplementaryprocessing charts ofitsparts. Machine tool takes the horizontal-type with doublestationsand both sides processing plan with the good technologic capability of processing and assemble. And it is convenient for parts to put into theclamp. The designusesthe hydraulic pressure sliding table to realize the replenishment of cutting tool,andbythe guide sleeves insuresthe processing precision and the stablemachining. In order to the working procedure to be centralized, the mainspindlesusethe standardonesand the cutting toolsarethe compound twist drills.
基于三维的柴油机气缸盖组合钻床总体及左主轴箱设计-任务书

毕业设计任务书课题:基于三维的柴油机气缸盖组合钻床总体及左主轴箱设计专业学生姓名班级学号指导教师专业系主任发放日期设计一台柴油机气缸盖三面组合钻床,具体设计任务是进行总体设计及左主轴箱计。
主要设计内容如下:1、总体设计1)制定工艺方案,确定机床配置型式及结构方案。
2)三图一卡设计,包括:(a) 被加工零件工序图, (b) 加工示意图,(c) 机床联系尺寸图,(d) 生产率计算卡,(e) 有关设计计算、校核。
2、左主轴箱设计(a) 左主轴箱三维造型设计及装配图的绘制(b) 左主轴箱零件图(c) 有关计算、校核等。
二、设计依据1.课题来源:盐城市江动集团2.产品名称:ZH1105WA柴油机B3.被加工零件:气缸盖(附零件图)4.工件材料:HT250,硬度190~240HBS5.加工内容:钻排气道面上2×M10—7H螺纹底孔至φ8.376,深19mm,Ra6.3,各孔位置度公差为φ0.20mm;钻井气道上4×M10-7H螺纹底孔至φ8.376,深19mm,Ra 6.3,各孔位置度公差为φ0.30mm;钻G3/8"放置螺塞底孔至φ15.2mm通孔,Ra 6.3,以上倒角均C1,Ra 12.5。
6. 生产纲领:4万件/年,两班制。
7. 批量:本机床设计、制造一台。
1、机床应能满足加工要求,保证加工精度;2、机床应运转平稳,工作可靠,结构简单,装卸方便,便于维修、调整;3、机床尽量采用标准件和通用件,以便降低制造成本;4、设计图样总量:折合成A0幅面在3张以上;工具要求:应用计算机软件绘图。
过程要求:装配图需提供手工草图。
5、毕业设计说明书应满足相关要求。
6、毕业设计说明书按照学校规定的格式规范统一编排、打印,字数不少于1万字。
7、到相关单位进行毕业实习,撰写不少于3000字实习报告;8、撰写开题报告。
四、毕业设计物化成果的具体内容及要求1、设计成果要求1)毕业设计说明书 1 份2)被加工零件工序图 1 张3)加工示意图 1 张4)机床联系尺寸图 1 张5)生产率计算卡 1 张6)左主轴箱总装配图 1 张7)左主轴箱零件图不少于7张2、外文资料翻译(英译中)要求1)外文翻译材料中文字不少于3000字;2)内容必须与毕业设计课题相关;3)所选外文资料应是近10年的文章,并标明文章出处。
基于三维的柴油机气缸体三面钻削组合机床总体及夹具设计

目录1 前言 (1)2 组合机床总体设计 (3)2.1 总体方案论证 (3)2.1.1 加工对象工艺性的分析 (3)2.1.2 机床配置型式的选择 (3)2.1.3 定位基准的选择 (4)2.1.4 选用滑台传动型式 (4)2.2 确定切削用量及选择刀具 (4)2.2.1 选择切削用量 (4)2.2.2 计算切削力、切削扭矩及切削功率 (7)2.2.3刀具耐用度的计算................................. 错误!未定义书签。
2.2.4 选择刀具结构 .................................... 错误!未定义书签。
2.3三图一卡设计....................................... 错误!未定义书签。
2.3.1 被加工零件工序图 ................................ 错误!未定义书签。
2.3.2 加工示意图 ...................................... 错误!未定义书签。
2.3.3 机床联系尺寸图 .................................. 错误!未定义书签。
2.3.4机床生产率计算卡................................. 错误!未定义书签。
3 组合机床夹具设计 .................................... 错误!未定义书签。
3.1夹具总体分析....................................... 错误!未定义书签。
3.1.1 零件的工艺性分析 ................................ 错误!未定义书签。
3.1.2 夹具设计的基本原则和要求 ........................ 错误!未定义书签。
3.1.3 夹具总体结构构思 ................................ 错误!未定义书签。
468Q发动机缸体双面卧式组合钻床总体设计及右主轴箱设计资料

太原理工大学阳泉学院毕业设计说明书毕业生姓名:董飞专业:机械设计制造及自动化学号:110511007指导教师张立仁所属系(部):机电系二〇一五年六月太原理工大学阳泉学院毕业设计评阅书题目:468Q发动机缸体双面卧式组合钻床总体设计及右主轴箱设计机电系机械设计制造及其自动化专业姓名董飞设计时间:2015年4月13日~2015年6月8日评阅意见:成绩:指导教师:(签字)职务:2015年月日太原理工大学阳泉学院毕业设计答辩记录卡机电系机械设计制造及其自动化专业姓名董飞答辩内容记录员:(签名)成绩评定专业答辩组组长:(签名)2015年月日前言制造业是一个国家或地区经济发展的重要支柱,其发展水平标志着一个国家或地区的经济实力,科技水平,生活水平和国防实力。
国际市场的竞争归根结底是个过制造生产能力的竞争,机械制造业是制造业的核心。
随着科技和生活水平的不断提高,机械制造业生产模式发生了巨大的演变。
从20世纪20年代的不计成本发展,到20世纪50年代一福特为代表的“规模效益”,再到20世纪70年代丰田为代表的“精益生产”模式,80年代以后靠制造技术的改进和管理方法的创新,以单项的先进制造技术来缩短生产周期,提高产品质量,降低产品成本和改善服务质量,90年代至今许多新的生产模式产生,并加以应用,而且还将继续发展。
我国机械制造装备水平还比较落后,基本上属于国外50年代“传统产业”的范畴,我过机械制造装备产业仅仅是整个制造业的缩影,而机械制造装备产业的萎靡不振又严重影响了机械制造业乃至整个制造业的振兴。
故振兴我国机械制造装备产业,提高我国机械制造装备产品的技术水平和市场竞争力是当前国内企业改革,改组,改造的当务之急。
汽车工业是一个国家制造业的集中代表,随着这几年我过经济的强劲发展,汽车工业蓬勃发展,汽车工业成为我国经济发展的发动机,所以人们讨论现代汽车发展的同时,对已有的发动机或装备进行改造设计,以满足人们的各种需求,这也是我们这次毕业设计研究加工468Q的意义。
气缸体钻头组合机床后主轴箱设计参考文献
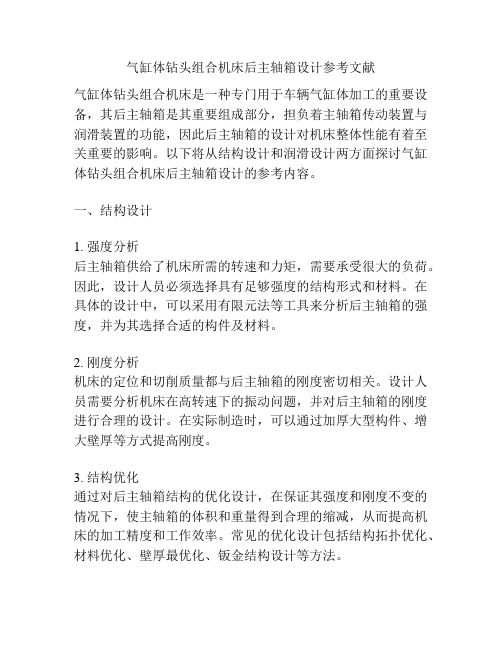
气缸体钻头组合机床后主轴箱设计参考文献气缸体钻头组合机床是一种专门用于车辆气缸体加工的重要设备,其后主轴箱是其重要组成部分,担负着主轴箱传动装置与润滑装置的功能,因此后主轴箱的设计对机床整体性能有着至关重要的影响。
以下将从结构设计和润滑设计两方面探讨气缸体钻头组合机床后主轴箱设计的参考内容。
一、结构设计1. 强度分析后主轴箱供给了机床所需的转速和力矩,需要承受很大的负荷。
因此,设计人员必须选择具有足够强度的结构形式和材料。
在具体的设计中,可以采用有限元法等工具来分析后主轴箱的强度,并为其选择合适的构件及材料。
2. 刚度分析机床的定位和切削质量都与后主轴箱的刚度密切相关。
设计人员需要分析机床在高转速下的振动问题,并对后主轴箱的刚度进行合理的设计。
在实际制造时,可以通过加厚大型构件、增大壁厚等方式提高刚度。
3. 结构优化通过对后主轴箱结构的优化设计,在保证其强度和刚度不变的情况下,使主轴箱的体积和重量得到合理的缩减,从而提高机床的加工精度和工作效率。
常见的优化设计包括结构拓扑优化、材料优化、壁厚最优化、钣金结构设计等方法。
二、润滑设计1. 润滑方式后主轴箱润滑方式的选择对机床的寿命、加工质量和能耗等有着重要的影响。
目前,市场上常见的润滑方式包括干式润滑和油膜润滑两种。
在实际设计时,需要考虑机床的应用场景、加工需求和使用成本等方面,选择合适的润滑方式。
2. 润滑计量后主轴箱内部需要保证足够的润滑量,从而消除机床在高速运转时的热量和摩擦。
为了减少耗能和成本,设计人员需要对后主轴箱的润滑量进行合理的计量。
常见的计量方式包括液位计量、重量计量、流量计量等方法。
3. 润滑系统设计后主轴箱的润滑系统设计包括油品选择、油路布置、油泵设计等方面。
在油品选择时,应根据机床所需的摩擦和磨损等特点选择合适的润滑油品。
在油路布置和油泵设计时,需要考虑后主轴箱内的流量和压力等参数,从而设计出合理的润滑系统结构。
综上所述,气缸体钻头组合机床后主轴箱设计需要兼顾结构设计和润滑设计两方面,既要保证其强度和刚度,又要保证其良好的润滑状态和稳定的工作效率。
基于三维的柴油机气缸盖组合钻床总体及左主轴箱设计-开题报告

毕业设计开题论证报告专业学生姓名班级学号指导教师完成日期课题名称: 基于三维的柴油机气缸盖组合钻床总体及左主轴箱设计一、课题来源、课题研究的主要内容及国内外现状综述课题来源:课题来源于盐城市江动集团ZH1100WA柴油机,为了提高产品质量及生产效率,因此需要设计一些高效率的专用组合机床,来改善目前柴油机汽缸盖的生产状况。
主要内容:1) 设计绘制被加工零件工序图、加工示意图、机床联系尺寸总图和编制生产率计算卡等。
2) 根据三图一卡,设计组合机床的主轴箱。
3)绘制主轴箱设计原始依据图,绘制各轴的干涉检查图;绘制多轴箱装配图,零件图及编制组件明细表。
国内外现状综述:化技术(机床)是本世纪以来发展极迅速和影响极大的科学技术之一。
现代自动化技术是一全新型的生产力,是直接创造社会财富的主要手段之一,对人类的生产活动和物质文明起着极大动作用。
因此,自动化技术受到世界各国的广泛重视和越来越多的应用。
机械自动化(机床),主要指在机械制造业中应用自动化技术,实现加工对象的连续自动生产现优化有效的自动生产过程,加快生产投入物的加工变换和流动速度。
机械自动化技术的应用与,是机械制造业技术改造、技术进步的主要手段和技术发展的主要方向。
机械自动化的技术水准仅影响整个机械制造业的发展,而且对国民经济各部门的技术进步有很大的直接影响。
因此,发国的机械制造业自动化技术,符合我国社会主义的基本原则,符合我国现代生产的发展规律。
如何发展我国的机械自动化技术(机床),这里有个技术政策问题,应实事求是,一切从我国体国情出发,做好各项基础工作,走中国的机械自动化技术发展之路。
国内外的工业发展史告诉我们,实现机械自动化是一个由低级到高级、由简单到复杂、由不完完善的发展过程。
当机器的操作采用自动控制器后,生产方式才从机械化逐步过渡到机械控制()自动化、数字控制自动化、计算机控制自动化。
只有建立了自动化工厂后,生产过程才能全盘化,才能使生产率全面提高,达到自动化的高级理想阶段。
- 1、下载文档前请自行甄别文档内容的完整性,平台不提供额外的编辑、内容补充、找答案等附加服务。
- 2、"仅部分预览"的文档,不可在线预览部分如存在完整性等问题,可反馈申请退款(可完整预览的文档不适用该条件!)。
- 3、如文档侵犯您的权益,请联系客服反馈,我们会尽快为您处理(人工客服工作时间:9:00-18:30)。
目录1 概述 (1)1.1 组合机床的特点 (1)1.2 组合机床的分类和组成 (1)1.3 组合机床的发展史 (2)1.4 组合机床的CAD发展概况 (2)2 组合机床总体设计 (4)2.1 制定组合机床工艺方案 (4)2.2 选择刀具及切削用量 (4)2.3 切削力、切削功率的确定 (5)2.4 组合机床的总体分析——三图一卡 (6)2.4.1 被加工零件工序图 (6)2.4.2 加工示意图 (6)2.4.3 组合机床联系尺寸图 (10)2.4.4 生产率计算卡 (14)3 组合机床多轴箱设计 (16)3.1 主轴箱设计的原始依据 (16)3.2 主轴结构型式的选择 (17)3.3 多轴箱传动设计 (17)3.3.1 对多轴箱传动系统的一般要求 (17)3.3.2 传动系统拟定 (18)3.3.3 多轴箱坐标计算、绘制坐标检查图 (21)3.4 绘制多轴箱总图 (23)结论 (24)参考文献 (25)1 概述1.1 组合机床的特点组合机床是由大量的通用部件和少量专用部件组成的工序集中的高效率专用机床。
它能够对一种(或几种)零件进行多刀、多轴、多面、多工位加工。
在组合机床上可以完成钻孔、扩孔、锪孔、铰孔、镗孔、铣削平面、切削内外螺纹以及加工外圆和端面等工序,生产效率比通用机床高几倍至几十倍,且加工精度十分稳定。
组合机床一般用于加工箱体类或特殊形状的零件。
加工时,工件一般不旋转,由刀具的旋转运动和刀具与工件的相对进给运动,来实现。
有的组合机床采用车削头夹持工件使之旋转,由刀具作进给运动,也可实现某些回转体类零件(如飞轮、汽车后桥半轴等)的外圆和端面加工。
组合机床与通用机床、其他专用机床比较,具有以下特点:1)组合机床上的通用部件和标准零件约占全部机床零、部件总量的70~80%,因此设计和制造的周期短,投资少,高效率,经济效果好。
2)由于组合机床采用多刀加工,并且自动化程度高,因此比通用机床生产效率高,产品质量稳定,劳动强度低。
3)组合机床的通用部件是经过周密设计和长期生产实践考验的,又有厂成批制造,因此结构稳定、工作可靠,使用和维修方便。
4)在组合机床上加工零件时,由于采用专用夹具、刀具和导向装置等,加工质量靠工艺装备保证,对操作工人水平要求不高。
5)当被加工产品更新时,采用其他类型的专用机床时,其大部分件要报废。
用组合机床时,其通用部件和标准零件可以重复利用,不必另行设计和制造。
6)组合机床易于联成组合机床自动线,以适应大规模的生产需要。
组合机床常用的通用部件有:机身、底座、立柱、动力箱、动力滑台,各种工艺切削头等。
对于一些按循序加工的多工位组合机床,还具有移动工作台或回转工作台。
动力箱、各种工艺切削头和动力滑台是组合机床完成切削主运动或进给运动的动力部件。
其中还有能同时完成切削主运动和进给运动的动力头。
机身、立柱、中间底座等是组合机床的支承部件,起着机床的基础骨架作用。
组合机床的刚度和部件之间的精度保持性,主要是由这些部件保证。
1.2 组合机床的分类和组成组合机床的通用部件分大型和小型两大类。
大型通用部件是指电机功率为1.5-30千瓦的动力部件及其配套部件。
这类动力部件多为箱体移动的结构形式。
小型通用部件是指电机功率为1.1-2.2千瓦的动力部件及其配套部件。
这类动力部件多为套筒移动的结构形式。
用大型通用部件组成的机床称为大型组合机床。
用小型通用部件组成的机床称为小型组合机床。
按设计的要求本次设计的机床为大型通用机床。
组合机床除分为大型和小型外,按配置形式又分为单工为和多工位机床两大类。
单工位机床又有单面、双面、三面和四面几种,多工位机床则有移动工作台式、回转工作台式、中央立柱式和回转鼓轮式等配置形式。
本次设计的机床为单工位双面钻床。
组合机床部件分类通用部件按功能可分为动力部件、支承部件、输送部件、控制部件和辅助部件五类。
动力部件是为组合机床提供主运动和进给运动的部件。
主要有动力箱、切削头和动力滑台。
支承部件是用以安装动力滑台、带有进给机构的切削头或夹具等的部件,有侧底座、中间底座、支架、可调支架、立柱和立柱底座等。
输送部件是用以输送工件或主轴箱至加工工位的部件,主要有分度回转工作台、环形分度回转工作台、分度鼓轮和往复移动工作台等。
控制部件是用以控制机床的自动工作循环的部件,有液压站、电气柜和操纵台等。
辅助部件有润滑装置、冷却装置和排屑装置等。
1.3 组合机床的发展史组合机床是随着汽车工业的兴起而发展起来的。
在专用机床中某些部件因重复使用,逐步发展成为通用部件,因而产生了组合机床。
最早的组合机床是1911年在美国制成的,用于加工汽车零件。
初期,各机床制造厂都有各自的通用部件标准。
为了提高不同制造厂的通用部件的互换性,便于用户使用和维修,1953年美国福特汽车公司和通用汽车公司与美国机床制造厂协商,确定了组合机床通用部件标准化的原则,即严格规定各部件间的联系尺寸,但对部件结构未作规定。
二十世纪70年代以来,随着可转位刀具、密齿铣刀、镗孔尺寸自动检测和刀具自动补偿技术的发展,组合机床的加工精度也有所提高。
铣削平面的平面度可达0.05毫米/1000毫米,表面粗糙度可低达2.5~0.63微米;镗孔精度可达IT7~6级,孔距精度可达0.03~0.02微米。
组合机床未来的发展将更多的采用调速电动机和滚珠丝杠等传动,以简化结构、缩短生产节拍;采用数字控制系统和主轴箱、夹具自动更换系统,以提高工艺可调性;以及纳入柔性制造系统等。
1.4 组合机床的CAD发展概况计算机辅助设计简称CAD,即利用电子计算机及其外部设备进行工程设计计算。
国外组合机床CAD技术研究开始比较早。
70年代初,一些工业发达国家首先多轴箱CAD方面开始研究。
尤其是进入90年代以来,计算机技术发展,交互式绘图和数据库管理系统等发展和应用,使组合机床CAD技术日益实用且使用范围不断扩大,发达国家组合机床设计中已普遍采用了CAD技术。
目前,正向CAD/CAM集成系统发展。
近年来,美国几个主要机床厂家(BURGMAST、KINGSBURY、INGERSOLL LAMB、CINCINNATI、MILACRON、CROSS等公司),其CAD技术已到普遍应用。
其中最引人注目是INGERSOLL公司具有50个交互式CAD工作站组成软、硬件环境,使其实现了几乎百分之百CAD化。
国内对组合机床设计采用CAD认识也比较早。
70年代初,大连组合机床研究所就开始了这方面研究工作。
1978年国家把组合机床CAD列为机械工业重点项目,并责成上海交通大学、大连组合机床研究所、机械部自动化研究所负责,大连理工大学、清华大学、北京工业大学、上海机电产品研究院等单位参加,对钻孔组合机床CAD进行了研究,从此揭开了我国组合机床CAD技术序幕。
2 组合机床总体设计2.1 制定组合机床工艺方案1.被加工零件特点被加工零件是一气缸体。
该零件外形复杂,尺寸较大。
本工序所要加工孔的数量较多,而且是不同位置处的不同形状的孔。
同时,各孔又有一定的位置度要求。
但各孔没有尺寸精度要求,孔内表面粗糙度要求为Ra6.3、Rz50。
因此,直接钻孔即可满足次精度要求。
该零件材料为铜铬钼合金铸铁25-47,其硬度为212~285HBS ,其质量为15kg ,其生产类型为中型零件大量生产(生产纲领:70000件/年)。
2.确定工件的定位基准加工时,工件以底面(限制三个自由度)、H 面(限制二个自由度)和L 面(限制一个自由度)定位;并以顶面上的四点夹压(见工序图)。
3.本工序内容从工序图中可以看出:在顶面上钻6个φ 8.7mm 孔(图上编号为12-17),在底面上钻2个φ 6.7mm 孔(图上编号为1-2)、钻2个φ 8.2mm 通孔(图上编号为3-4)、钻3个φ 5mm 孔(图上编号为5-7)和钻4个φ 5mm 通孔(图上编号为8-11)。
各孔没有尺寸精度要求,但相对2个基准面有一定的位置度要求。
根据以上工艺特点,若选用普通机床加工,难以保证各孔的位置度,同时效率也不高。
因此,选用单工位的双面卧式组合钻床进行加工。
这样不仅提高了加工效率,而且多个孔一次走刀即加工成形,能够较好的保证其位置精度。
此外,在组合机床上加工零件时,由于采用专用夹具、刀具和导向装置等,加工质量靠工艺装备保证,对操作工人水平要求也不高。
2.2 选择刀具及切削用量本工序加工所需刀具为钻头。
选择刀具首先是选择刀具材料,对于钻头来说,常见材料有高速钢和硬质合金两种。
高速钢钻头主要用于切削硬度在250-280HBS 的部分结构钢和铸铁;硬质合金钻头则主要用于加工硬度较高的钢件。
被加工零件的材料为铸铁,硬度为212-285HBS 。
所以,选用高速钢钻头。
查《机械加工工艺手册》(GB/T6135.3-1996) 选择刀具类型为锥柄麻花钻,同时查《组合机床设计简明手册》表6-11选择切削用量并计算主轴转速进给速度,汇总于表2-1。
min /450min /7.83.121000r r d 1000n 1=⨯⨯==ππνmin /480min /7.61.101000r r d 1000n 2=⨯⨯==ππνmin /450min /2.86.111000r r d 1000n 3=⨯⨯==ππνmin /600min /542.91000r r d 1000n 4=⨯⨯==ππνmin /48min /100.048044332211mm mm f n f n f n f n v =⨯=====表2-12.3 切削力、切削功率的确定根据选定的切削用量(组要指切削速度v 及进给量f ),确定切削力,作为选择动力部件(滑台)及夹具设计的依据;确定切削扭矩,用以确定主轴及其他传动件(齿轮、传动轴等)的尺寸;确定切削功率,用以选择主传动电机功率。
查《组合机床设计简明手册》表6-20,得:切削力(N ):74.1065260.60.1078.72626D F 0.60.86.08.01=⨯⨯⨯==HB f50.777260.60.17.62626D F 0.60.86.08.02=⨯⨯⨯==HB f49.0041260.60.1078.22626D F 0.60.86.08.03=⨯⨯⨯==HB f36.854260.60.0852626D F 0.60.86.08.04=⨯⨯⨯==HB f式中,()()7.26021228531285HB HB 31HB HB min max max =--=--=。
切削扭矩(N.mm ):2872.4260.60.1078.71010D T 0.60.81.96.00.81.91=⨯⨯⨯==HB f656.511260.60.16.71010D T 0.60.81.96.00.81.92=⨯⨯⨯==HB f 2566.88260.60.1078.21010D T 0.60.81.96.00.81.93=⨯⨯⨯==HB f794.63260.60.0851010D T 0.60.81.96.00.81.94=⨯⨯⨯==HB f切削功率(kw ):133.07.897403.124.28729740Tv P 1=⨯⨯⨯==ππD082.07.697401.1051.16569740Tv P 2=⨯⨯⨯==ππD119.02.897406.1188.25669740Tv P 3=⨯⨯⨯==ππD049.05974042.963.7949740Tv P 4=⨯⨯⨯==ππD 2.4 组合机床的总体分析——三图一卡2.4.1 被加工零件工序图被加工零件工序图是根据制定的工艺方案,表示设计的组合机床所完成的工艺内容,加工部位的尺寸、精度、表面粗糙度及技术要求,加工用的定位基准、夹压部位以及被加工零件的材料、硬度和在机床加工前加工余量、毛坯或半成品情况的图样。