问题解决五原则表
问题解决5原则表的作成和运用指南

■不良现象的要因调查
・「什么时间、在哪个工序、发生了 什么?」
⇒锁定对象工程和对象批量 ・一般的记入内容
・工程的确认 ・每次确认的时候有无引起相关 不良的可能性 ・工程调查结果
工程履历、数据、作业记录 调查作业者的结果
5原则表的作成 (2)原因の究明
实施2种原因的究明!
別紙デ-タ10参照
○:マツダ様にて確認結果、 接点部導通しっぱなしなし
○:メカでの強制 O FF構造であ
接点溶着
り接点溶着なし
別紙デ-タ11参照
組み付け手順 間違い
○:マツダ様にて確認結果、 組付け手順に問題なし
スイッチ内部ズレ
バネ 不良
×:現象確認
別紙デ-タ3,4参照
下ケース
摺動体
接点
ランプ 接点組成
第2阶段 <对象扩大>
出荷
顾客
顾客索赔
必须! 第1阶段
5原则表的作成运用要点
①首先要优先于开始活动! 不要对策后才报告 ⇒中途经过也可以要向顾客迅速报告!
②不能只有QC担当者作成! 由主要因部门作成、QC协助、承认是基本的途径。 ⇒若是生产的要因那就是制造、设计的要因是技术… 当然要用CFT作成讨论
通过对问题进行4个合理的思考过程分析,从而得出正确的结论。
自然人的思考过程=从以下4个角度进行反复提问,对其结论进行持续考虑。 ①什么课题?(WHAT) ②为什么会那样?(WHY) ③怎样入手解决?(HOW) ④若什么的话会不会引起什么?(IF)
◎状况把握过程(略称SA=Situation Appraisal) 引起什么?→课题是什么?
要点:「目前的处置怎么办?」 首先要检讨不能扩大顾客困惑的处置方法。
五项原则报告解析2.7
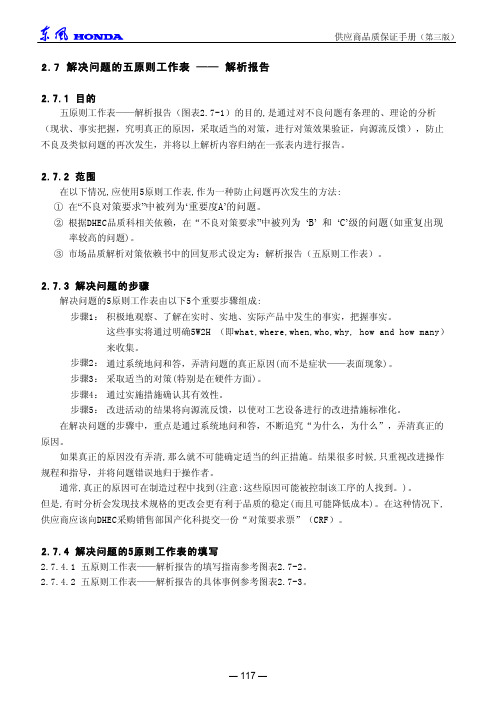
保存期限: 年
供应商品质保证手册(第三版) 图表2.7-3
— 120 —
主题 零件号 零件名
止瓦槽(切槽)位置反向加工
1112*-P**-O***
No.1主轴承盖
具体事例
五原则工作表〔解 析 报 告〕
管理NO: 20041129-001
编
***** 有限公司
2004年12月10日
【目标】 1.证明品质、成本、日程都是最合适的,以防止出现的情 况再次发生。
【填写内容】 1.引起问题零件/部位的硬件(设备、夹工具等)的恒久对策, 以及对策日程、责任人。 2.防止问题零件/部位流出的硬件(QA机、防止错误装置等)的 恒久对策,以及对策日程、责任人。 3.维持上述内容的FMEA、QA矩阵表、作业标准等的对策内容 和管理实施日程和责任人。 4.其它采取对策的机号和机型。 5.出货件的处理判断(预见性、发生的预测和条件、零件和
编制部门的名称
⑦由编制部门的相关人员签
【目的】 1.下次行动时锁定目标。 2.真实填写发生的原因和状况,以便使不良零部件、部位 更清晰
【填写内容】 1.机种、机型 2.车身号码、发动机号码、批号。 3.发生地点。 4.发生年月日。 5.(发生后在销售店)登记年月日。 6.行使路程/时间。 7.事象内容。 8.处置方法和结果。 ※注:上述以外如果有必要的信息请记录。
Ⅴ . 向 源 流 的 反 馈 (反映在体制・组织上的内容)
为什么 ·为什么分析
步骤
1
2
3
4
5
内 发生
容 流出
EQ F1701 M01 D02
保存期限: 年
供应商品质保证手册(第三版) 图表2.7-2
解决问题五原则表

作成部门
接收部门 日期 审批 确认
解决问题的5原则表
审批
确认
制作
1-A 问题定义--现象、投诉内容、发生件数、处置内容
1-B 问题定义(事实把握)--确认结果、分析原因、品质状况
2-A 找出根本原因(分析问题和回答)--根据特性要因图
问题① 为什麽② 显象(硬项目) 为什麽③ 为什麽④ 为什麽⑤
2-B 找出根本原因--问题和答案分析、问题产生过程、重复测试 根本原因的陈述
隐象(软项目)
3 纠正措施--内容、预期效果、潜在问题分析
4 确认措施--实际效果
5 反馈/下一步的行动
跟进日期:
广本5原则培训资料

☆集体创造性思考 ☆特性要因图
• 调查结果总结、变化点和推断原因总结
4、现在的対応状况(緊急処置後的)
• 用X-R管理图 、矩形图、CP值等
可以说问题一定源于变化点(人、物、设备等,4M1E)
1、老七种工具: 调查表 分层法 排列图 因果图 直方图 控制图 散布图 2、新七种工具 亲和图 树图 关联图 矩阵图 箭条图 PDPC法(过程决策程序图法) 矩阵数据分析法
・可用于解决开发、生产、销售、供应、管理等 所有领域发生的问题。
来自顾客的意见、投诉产品、服务不好 设备、机械、机器的问题 精确度与效率不高的工作
解决问题、防止再发
五原则工作表
重要度的决定及处置判断
• 重要度、麻烦度、重要保安部品判断
零件品质科
重要度
麻烦度
重要保安部品
A 不良时判断为危害人身安 A 已进行整车的检测、修理 HS
17 240±5 +7 +8 +9
P21
10 270 SET SET SET
(工序概要) No 工程名 1 来料仓库 2 端末加工 3 弯管加工 4 最終検査 5 出荷
加工機種名 起因 西岛端末加工机 T型弯管机 ★ -
*根据现品确认,弯管形状有同样倾向
■ 5原则工作表(解析报告)
是指从发生问题的初期对应到彻底解决问题,防止再发的问题解 决手法。是本田特有的问题解决手法。
目的:通过对不良问题进行有条理的、理论性的分析(三现主 义) ,查找真正的原因,采取适当的对策,防止问题再发。
・解析报告要将解决问题流程的结果用1张纸(A3)总结后进行报告。
■ 使用范围
集、整理)
• 工序中现正生产的零部件的品质状况、良品批次确认(根据X-R管理图、工程
五原则表五个步骤
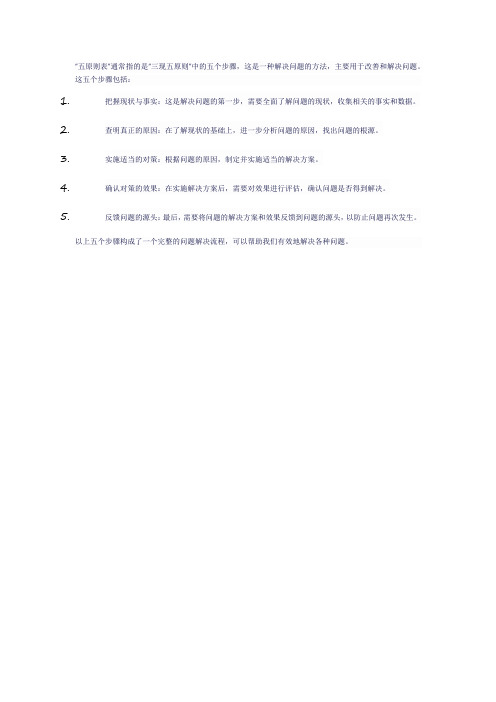
“五原则表”通常指的是“三现五原则”中的五个步骤,这是一种解决问题的方法,主要用于改善和解决问题。
这五个步骤包括:
1.把握现状与事实:这是解决问题的第一步,需要全面了解问题的现状,收集相关的事实和数据。
2.查明真正的原因:在了解现状的基础上,进一步分析问题的原因,找出问题的根源。
3.实施适当的对策:根据问题的原因,制定并实施适当的解决方案。
4.确认对策的效果:在实施解决方案后,需要对效果进行评估,确认问题是否得到解决。
5.反馈问题的源头:最后,需要将问题的解决方案和效果反馈到问题的源头,以防止问题再次发生。
以上五个步骤构成了一个完整的问题解决流程,可以帮助我们有效地解决各种问题。
解决问题的五原则
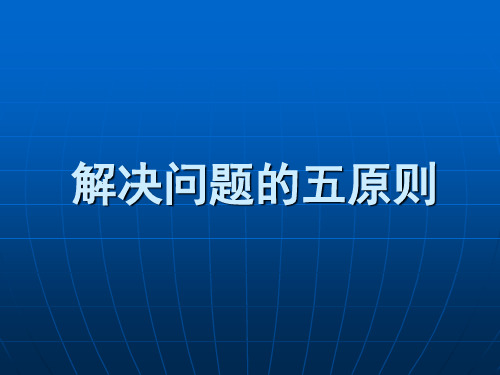
写好五原则表的关键:运用五原则手法分析、解决问题
五原则表的表达要求
要用简单、具体、准确的表述语言填写事实,不要 使用抽象性、否定性(确实、正确、避免、不要、 可能等)的语言。 要求插入示意图、照片、路线图、表格等,这样, 在传递过程时,就可以使你表达的意思和阅读的人 理解内容的一致。 ①.尽量使用短句写 ②.用小学六年的孩子能理解的话写
解决问题的五原则
五原则的定义
“五原则”是指从“三现主义”出发,分五个步骤解决问题
充分把握事实 查明的真正原因 实施切实的对策 确认对策的有效性 反馈到问题的源头
1
五 个 步 骤
2
3 4 5
三现主义
不但适用于制 造现场,也适 用于广泛的其 它工作。
亲自接触实物
亲自到现场
(现物)
总是以事 实为基础 而行动
异常对应难以预测的现象: 临时调休 突发的产品质量问题 突发的设备故障 到货材料、零件异常 停电、地震、洪灾、台风等
工厂是避免不了变化 点的,问题是对变化 点有没有制定正确的 对应方法
三、充分把握事实—2
<要因变化点的确定>
4M变化点
人 变化点的具体事例
(批次追踪及变化点调查)
对预测的变化点,没有进行 正确的管控时也会发生问题
③.用小学六年之前学过的汉字写
④.尽量不要使用专业性很强的文字和西洋文字 (英 、日文)写
五原则表填写要领
01.标题
发生状况 现状把握
02.发生状况
1-1 不良品确认 结果
合适 的 对 策
1-2 批次跟踪 变化点调查
1-3 原因分析
查 明的原 因
检查对 策 的效 果
2-1.查明的原因 发生机理 再现试验
5原则表填写说明

作业要领书的修改
□要 □否
条件表的修改 其他
□要 □否 □要 □否
18/23
19/23
通过对标准类(QC工程图、检查基准书、作业指示书)的 完善,明确再发防止策、对策实施效果的继续・维持方法。 ①判断需要对哪些文书进行修改。
作业标准类:PQC、检查基准书、作业指导书、包装 类指导书、作业要领书,条件表等
①取得正确的事实. ②针对发生及流出原因,用分析图明确表示 ③明确不具合发生基本原因. ④反复为什么为什么找到真正发生的原因. (更进一步使用春风分析图分析原因) ⑤进行适当对策并实施. ⑥反映到标准类、体系中. ⑦确认效果及数值.
1 3
6/23
2
5 4
6
1.发生状况(现实)
7/23
①.现象·投诉内容
□要 □否
担当
纳期
检查基准书的修改
□要 □否
作业指导书的修改 手顺书的修改
□要 □否 □要 □否
PIR记录项目变更
□要 □否
日常/定期点检项目变更
□要 □否
保养项目变更 异常处理方法变更
□要 □否 □要 □否
图面(治工具/金型/制品)的修改 □要 □否
FMEA的修改 包装类指导书的修改
□要 □否 □要 □否
发 生
内
容
流 出
探明原因[采用系统图法进行分析。] 从各个角度反复重复为什么为什么,抓住根本性真 正原因明确填写认为是最受影响的项目。
现象
为何发生
为什么
为什么
为何流出
为什么
为什么 为什么
为什么 为什么 为什么 为什么
为什么 为什么 为什么 为什么 为什么 为什么 为什么 为什么
解决问题的五原则分析

解决问题的五原则
五 原 则 的 定 义
“五原则”是指从“三现主义”(现场、现物、现 实)出发,分五个步骤解决问题。
2
1
充分掌握事实情况
2 查明真正的原因
五个步骤是:
4
3 实施切实的对策 确认所采取的对策是否有效
5 反馈到发生问题的源流
三现主义的定义
不但适用于制造现场,也适用 于广泛的其它工作 。
五原则的填写说明-Байду номын сангаас
8
事 实 的 把 握(部品的确认结果、原因分析、生产品的品质状况)
目标 1、为探明部品、部位的原因; 2、变化(工序与用户的使用方法)产生不良, 为了一针见血找到变化和限定批次。 见下页
五原则的填写说明-
填入内容:
9
事 实 的 把 握(部品的确认结果、原因分析、生产品的品质状况)
◆等待生产现场的联系或生产现场对于技术、品质、资材等部门服务、指导、指示、供应的等待。等待下级 的汇报,任务虽已布置,但是没有检查,没有监督。不主动去深入实际调查研究,掌握第一手资料,只是被动 地听下级的汇报,没有核实,然后作决定或向上级汇报,瞒天过海没有可信度,出了问题,责任往下级身上 一推。“三现主义”的缺乏是等待中的最致命原因之一,严重影响生产现场工作的及时解决。
三现主义在中国用得很早:远点,“捉贼捉脏, 捉奸捉双”;近点,毛主席的“没有调查研究 就没有发言权”;再近点,;新闻工作者不也是 天天在掌握第一手材料么?谁和谁有拍拖之 嫌呀,哪个和哪个出现在某酒店啊,这都是三 现主义的运用,可是中国的三现主义只用于 政治或只用于整人,很少用于品质管理。
三现主义的定义
①不良品 制造工序条件 ②不良品 制造年月日 ③不良品 发生个数、概率 …等,用工序系列、时间系列整理。
3w2h原则表格

3w2h原则表格3W2H原则是一种问题解决方法,它包括以下七个要素:What(什么),Why (为什么),Who(谁),When(何时),Where(何地),How(如何)和How much (多少)。
通过回答这七个问题,可以全面了解和分析一个问题或任务。
下面是一个示例表格,展示了如何使用3W2H原则来解决问题:使用3W2H原则可以帮助我们更系统地思考和解决问题,确保每个方面都得到充分考虑。
以下是一些使用该原则的步骤:1. What(什么):明确问题或任务的具体内容和目标。
例如,“我需要完成一篇关于气候变化的论文。
”2. Why(为什么):分析问题的原因、目的和意义。
例如,“我想了解气候变化对地球的影响,并提出解决方案。
”3. Who(谁):确定参与问题解决的人员和责任分工。
例如,“我将与我的导师合作,并邀请其他专家提供意见。
”4. When(何时):确定问题解决的时间范围和截止日期。
例如,“我计划在一个月内完成论文。
”5. Where(何地):确定问题解决的地点和环境条件。
例如,“我将在我的图书馆里进行研究和写作。
”6. How(如何):制定解决问题的具体步骤和方法。
例如,“我将收集相关文献,进行数据分析,并撰写论文的各个部分。
”7. How much(多少):确定问题解决所需的资源和成本。
例如,“我需要购买一些参考书籍和订阅相关的学术期刊。
”通过回答这些问题,我们可以更好地规划和管理学习任务,提高学习效率和成果。
同时,3W2H原则也适用于团队合作和项目管理中,帮助团队成员明确任务目标、分工和时间安排。
解决问题的5原则

试验温度
☆向其它部门提供信息 ①空军 46/02~ ②海军 46/02~ ③警察 48/03~
题目 零件号 零件名
分析记录[解决问题5原则表] 运用渠道1.要求对策时:编制部门 (报告单位) 2.其它、编制部门(编制-保管)
编 制 部 门
部室名或供货方名 年 月 日
—对策要求时→
要求报告不良对 策时,应付上不 良对策
解决问题的5原则
1. 把 2. 究 握 明 事 原 实 因
See Think Plan→Do Check Action
3. 合 适 的 对 策 4. 确 认 效 果
5.向 源 头 的 反 馈
六种教训
其一 不论什么报告也不一定 传达的完全准确、 其中可能隐蔽着 重要的事实。 其二 适切数据的收集和分析、 以此把因当事人的经验和观察力 所隐藏的重要的事实挑出
-25
o o o o o o o o o o
-30
o o o o o o o o o o
-35
x x o o o o o o o o
-40
向源头反馈(反映体制、计划内容) 1.硬件对策要继续保持 反映项目计划(基准、标准类) 2.成为原因的项目排除掉 反映机制计划(向横向波及 向横向水平展开 )(规程、基准、 )(规程、 技术积累等 基准、技术积累等 ) )
2
大的分支 流 采用特性要因图查出问题的特性 出
中分支
小分支
真正的原因
送弹部被破坏 勃朗宁机关枪的 破坏(中弹)
由于压力上升发生 爆炸 陆军的规格、只有 -20℃
颗粒呈切断固体状火 药的粘结剂在低温下 变脆、受到振动
陆军是根据冬季战场 经验设定为-20℃的
下降到-30℃后、 火药的粘结剂变脆 (根据再现测试)
五原则图的使用手册

解决问题5原则图的序言5原则图手法的特征可以总结为“系统地考虑问题”。
也就是说,在5个步骤中,需要做的事情已经非常明确地做了规定,按照这样的步骤来解决问题的话,就可以正确地解决哪怕是很复杂的问题,并且解决过程不会出现浪费的行为和举措,还能够有效地防止问题的复发。
这个手法的另一个特征就是虽然它以质量管理手法为基础,但是能够适用于各种业务,不仅仅是质量问题,而且对于生产、安全等问题的解决也是有帮助的。
所以,希望这个5原则图在包括事务性部门在内的全公司各部门中得到广泛应用。
解决问题5原则图的使用手册1. 使用5原则图的目的:·问题发生后,依据现场、现物、现实情况,调查事实,对事实进行把握和分析,从中找出真正的原因,然后及时采取对策,防止同样的问题再次发生。
2.使用5原则图的好处-1、把对策的过程及结果写在一张纸上,便于从整体进行审查。
例如:·由于是按照逻辑进行分解的,所以可以正确地去实施各个步骤应做的事情,另外,如果有遗漏,还可以很容易地检查出来;·可以查证整个的推进方法是否合适、有没有问题等。
从上述2点来看,把它当作一种报告对待的话,接受报告的人也较容易对检查报告内容。
-2、通过5个步骤总结出来的资料,可以当作积累专有技术的手段。
·具体来说,就是可以把它当作一种过往(已经发生过的问题)缺陷(的资料)做参考。
-3、可以当作水平展开问题的工具使用·在类似问题上应用、向类似工序、类似设备等方面的反馈·还可以向新工序、新产品方面进行反馈-4、利用这个总结性的资料,可以向后进行技术传承3.在什么情况下使用5原则图呢?·对于简单问题,可以仅在脑海里过一边就可以了,那么如果遇到以下情况,就劝大家一定要考虑采用这个手法,按步骤切实推进,进行总结。
-1、不清楚问题的真因的时候※-2、发生重要问题的时候-3、要迫切解决问题的时候-4、问题复发的时候※那么所谓重要问题,究竟是指什么样的问题呢?举例说明:⑴关系公司信用的问题⑵事关人身安全的安全问题⑶关系火灾、公共灾害的问题⑷因问题所引起的损失较大时⑸停产时(因品质不良/缺品等)⑹发生与安全有关的产品缺陷时⑺由于产品的功能、外观不良造成报废或者修理工时过大时⑻问题多发时⑼因品质问题在客户处进行检查时⑽发生市场投诉时⑾发生交货延迟和数量不够时4.各步骤的目的和推进方法·步骤1-A------发生状况(问题的概要)在此处进行的是对问题整体的了解性调查。
解决问题的五原则
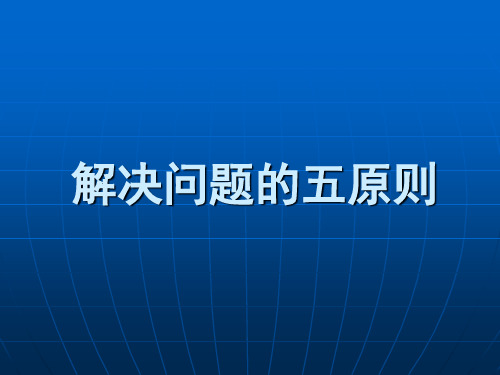
发
临时调休
点有没有制定正确的
的 变 化 点
突发的产品质量问题 突发的设备故障 到货材料、零件异常 停电、地震、洪灾、台风等
对应方法
三、充分把握事实—2 (批次追踪及变化点调查)
<要因变化点的确定>
对预测的变化点,没有进行 正确的管控时也会发生问题
4、发生数量:明确不良数量、不良率 车架/发动机号、购买日期、行驶里程(如果是市场发生时)
从反馈 部门得 到正确 的信息
5、发生现象:在什么情况下发生的? ●外观、装配问题可简单描述 ●动态问题要详尽描述:离合器手柄作动不顺畅!详尽:哪种角度还是全角度?
6、处理情况 发生问题的车(机)型及零件的处理内容 ●怎样处置:换装、挑选、调整、返修等
变化点 固定、反复的作业
通常这个能持续的话就 不会发生问题
可
非固定、非定期的作业
预
机种准备
测
夹具、刀具、设备、模具维修
由于有这样的事情出现导 致问题发生时就被定义 为要因变化点(见下页)
的
工艺变化、加工方法变更
变
零件更换
化
避免不了变化
突
异常对应难以预测的现象: 点的,问题是对变化
2日
3日
100
100
100
100
300
问题对象批次
4日
5日
100
/
100
100
变人
化 设备
☆设备变更了
点 方法 基于4M进行变化点的调查
材料
<批次追踪及变化点调查结果>
1)问题批次是×月×日~ ×月×日生产的××台
2)对象批次的变化点是什么?
<要点> 问题的发生总是 由变化点引起
品质管理的三现五原则

5、变化点分析不清楚
疑 问 点:以前为何不会发生不良,现在才发生? 一定是哪里有变更,变化点在哪里? 思 考:不良隐藏於变化点中。
分析方法:4M1D里寻找真因 人[Man]:人员有否更换,有否依标准作业、人员之 士气等。 机[Machine]:机器设备、镆、治、检、工具有否调 整、变更等。 料[Material]:材料有否改变、前工程流入件不良事 等。 方法[Method]: 标准有否规定?标准是否明确? 设计[Design]: 是否设计变更等。
疑 问 点:常发生的直觉判断 ~ 焊接强度不足对策:焊道加长2mm.正确吗? ~ 模温不足变形对策:模温提高10℃.没问题吗? 思 考:加长2mm、提高10℃如何得到的?
直觉+经验≠事实
100个直觉或经验不如1个数据
分析方法:科学的根据=实验数据 ~ 有实验的数据才能决定新的标准。 ~ 要去试验出焊道加长2mm及模温提高10℃是作 业最好的条件。
9、制造面、流出面未检讨
疑 问 点:1.为何会流出?为何会制造出?为何设备检不出? 2.流出面之解析对策经常被疏忽。 思 考:顾客所反应之问题必定制造面、流出面共同发生, 仅对策制造或流出面并未能彻底解决问题。 分析方法:1.制造面→分析4M之变化点→真因对策。 2.流出面→a.分析制程中之流程→作业环境、作 业检验工程标准。 b.分析检验之流出→出货检验标准、 限度样品、自动检测、防呆装置。 检验: 为何会检测不出来。
发生问题 零件号 零件名称
提出部门
日期 批准 审核 编制
日期
编制部门
批准 审核 编制
1-A 发生状况(现象、申诉内容、发生次数、5W2H处置内容)
1-B 把握事实(对零部件的确认结果、原因分析、现在正在生产的零件的品质状况)
处理问题的标准五原则

当一个企业发展到一定的阶段,不能完全依靠“人治”,而是应该逐步向“法治”转化,必须做到“有法可依”。
1、当出现问题的时候管理者首先应先检查在做这件事时有没标准,如果因为没有标准,那么在我的理解是管理者自身出了问题。
2、如果有标准,那么标准是否对员工进行了培训,如果标准只是存在于管理者的书柜里和电脑里,形同虚设,没有对员工进行培训,那么这也是管理者的问题。
3、如果已对员工进行过培训,员工也清楚这件事应该如何去做,那么应检查员工在做的时候有没有遵守标准。
4、如果员工按标准去做了出问题,那么我们应该检查标准本身是否存在不合理的地方。
5、如果标准不存在问题,那么管理者应该反思下在日常标准的执行上有没有进行定期的检查监督。
要知道,只要是人都有惰性,员工只会做领导关心的事情。
综上所述,我想,作为一名管理人员在处理问题上只要能把握“
标准五原则”,在最大程度上将大大减少甚至杜绝一些异常问题的反复发生。
在公司员工队伍的稳定上也将起到积极的促进作用。
本田五原则报告的作成

五原则的填写说明-
13
对 策 效 果 的 确 认(效果实绩)
填写目标: 为定量证明防止再发 见下页
五原则的填写说明-
14
对 策 效 果 的 确 认(效果实绩)
在工序上或客户处对对策实施效果进行跟踪(注明确认人及 确认日期,效果可以通过品质数据/测量对策前后的变化来确认, 充分活用统计手法) 1、用品质数据对对策效果进行前后比较; 2、偶发不良品时,制造条件的比较数据; 3、制品无法体现变化时,制造条件的比较数据; 在数值上无法对 4、适用方面包括到客户处确认。 比的对策不是真 正的对策 说明 定量进行效果的检证和结果的检查。 这些效果检证属: · 在客户条件下的确认 · 限度值的确认 · 试验等的确认 · 依照质量情况监视 要点: 1、确认数据的取样数量,最终确 认需要的时间也很重要 2、确认所实施对策对正常作业程 序有无不良影响 (确认工程熟练度) 3、确认人的熟练程度(确认对人有 无风险)
例:为什么机器停了?
真正的原因
课题是 构筑购买设备的体系
没有制定购买 设备时的 规则 · 渠道 在购买设备时 没有进行 充分的确认
20
最初的问题 (表象的)
为什么 机器停了
为什么-1
是因为过载造成 保险丝 断开
<防患于未然> ~管理水平~
购买了不带 过滤器的设备
为什么-2
轴承部位的 润滑 不充分
为什么-3
——依工序流程与时序,以变化为中心进行填写 3、不良发生要因调查(尽量使用图、表等来表达) ﹡ QC手法在发生要因分析中有效,利用特性要因图、FMEA进 行分析
﹡对发生要因、流出要因和事实的验证,不产生问题的条件的
特征与变化的比较,相对于集中找准的工序的不良点要因分析与 其结果 4、调查结果总结、变化点和推断原因总结 ——一针见血!变化与原因?
5原则解析报告培训资料全

内容提要
• 1、定义及目的 • 2、说明及案例 • 3、目前存在的问题点 • 4、考试
零件品质科
五原则表培训
零件品质科
5原则工作表(解析报告)定义
■ 5原则工作表(解析报告)
是指从发生问题的初期对应到彻底解决问题,防止再发的
问题解决手法。是本田特有的问题解决手法。
目的:
通过对不良问题进行有条理的、理论性的分析,查找
• 重要度、麻烦度、重要保安部品判断
零件品质科
重要度
麻烦度
重要保安部品
A 不良时判断为危害人身安 A 已进行整车的检测、修理 HS
全的重大危害 操纵、行走、制动
火灾、感电、公害、安全 不能保护
除A外,产品机能和商品
已进行零件的检测、修理
性受到损害
B
B
HA
不良时,重要机能丧 失,可能引发重大事 故
不良时,重要机能丧 失,可能引发重大事 故,但可预知并进行 安全处置
麻烦度 C BC
零件品质科
五原则表培训
零件品质科
解析报告(5原则表)适用范围
• “重要度A”的问题
• “重要度B或C”的问题,但发生频率较高
• 基本上以PIR发行的项目为全部对象
五原则表培训
零件品质科
展开解析报告的5个步骤
1-A发生状况(现象・所述内容・发生件数・处理内容) 1-B把握事实(零件确认结果・要因分析・生产件的品质状况)
技术科 11/23
·在设备调整的作业标准中增加测量辅助滚轮锁紧后所在位置的规定 技术科 11/23
始业及每加工500件用卡尺测量并记录数据。
品质科 11/23
·在设备上明确标示辅助滚轮所在正确位置的尺寸。
- 1、下载文档前请自行甄别文档内容的完整性,平台不提供额外的编辑、内容补充、找答案等附加服务。
- 2、"仅部分预览"的文档,不可在线预览部分如存在完整性等问题,可反馈申请退款(可完整预览的文档不适用该条件!)。
- 3、如文档侵犯您的权益,请联系客服反馈,我们会尽快为您处理(人工客服工作时间:9:00-18:30)。
接 受 报 告 人
年 确认
月 批准
日
现状把握(零件的检查結果、分析原因・产品的质量状况) 零件的检查結果: 生产400件,其中不合格3件。不合格率为0.75%
原因分析: 我司的弯管机上面的弯管轮压力过大。 管材的厚度不够。 管材自身存在不良或有裂缝。 操作者和检验关注度不够。
对策效果的确认
查明原因(发生机理.再现实验.为什么.为什么分析) 合适的对策(对策内容・预测效果・PPA) 弯管机上面的弯管轮松弛造成产品应力集中。 对我厂在制品加大检验力度。对库存品再次进行检验。 再现不良:由于弯此产品的工序作业人员,实新进人员对弯 编写此工序的后果分析图。 型机的掌握熟练程度不够,擅自加大自检频率。未及时关注 对机器设备、工装夹具、校具进行维护和检验。 设备本身的状态。 加强管材入厂检验数量和项目。
在此工序设立专检。 加强我司供应商管理力度。 增强员工技能培训,要求员工严格按作业指导书作业。
加强对机器状况和管材材质的监控后,经制作 50件产品的测试,未发现管子出现裂纹和管子断 裂的现象。经验证以上处理措施可行。
源流反映(反映到体制、体系) 完善作业指导书、QC表。 加强人员技能熟练化得要求。 在此工序 电镀 设立工序 作业标专检员 准化。 。
产品检验时抽样比例偏 少。 出货前检验未检验产品 强度
原紙保存期限: 2010 2012年9月3日 年8月
作成:222 机械制造有限公司 本田摩托有限公司
阶段
发 内 生 容 流 出
1 弯型作业人员未 及时关注设备状 况。 作业人员质量意 识不强,没有及 时的把不良品区 分开。
2
3
4
5
加强入厂检验的抽样比例。
之前未出现过此种类似 机器上面的弯形轮松 产品的检测项目上 事件,人员关注度不够 弛,未及时调整。 面未检测此项。 。 检验人员进行了抽检作 检验作业指导书的 产品出货前仅抽检一 业(我司现已修改为全 箱产品 检验项目不完善 检) ZS110-26 110-60后货架断裂 部品号 部件名 ZS110-26 110-60货架 发生状况(现象·投诉内容·发生内容·处置内容)
1.机种型号: ZS110-26 KRF 110-60后货架 2.发生时间: 2012年3月29日 05年8月9日 3.症状:轮圈表面打痕 货架断裂 4.发生件数:530件,占44% 5.发生工序:客户厂家装配工 序 6.发生场所:4号机床 客户厂家处 7.生产厂家:上海万丰 机械制造有限公司 8.不合格发生生产日期:05年8月 2012年8月 9.故障处置:之前未引起重 之前未发生。 视,未处理。 部门或厂家 年 2012 年 8月 制 做 制做制作 确认 机械制造有限公司 部 门 29日 审核