钢球斜轧机轧制钢球工艺技术
钢球生产工艺流程
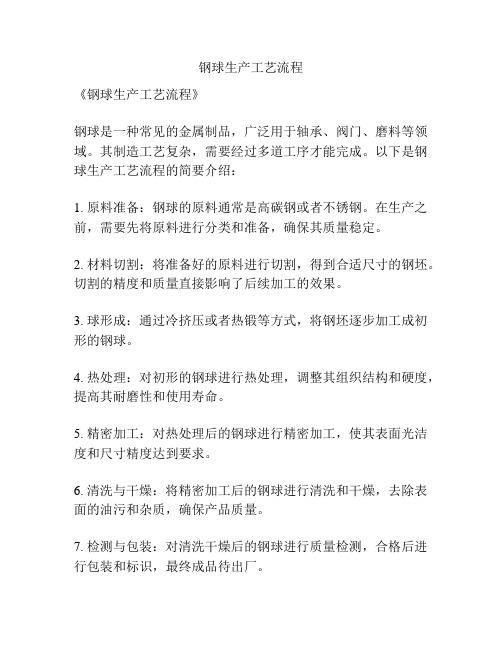
钢球生产工艺流程
《钢球生产工艺流程》
钢球是一种常见的金属制品,广泛用于轴承、阀门、磨料等领域。
其制造工艺复杂,需要经过多道工序才能完成。
以下是钢球生产工艺流程的简要介绍:
1. 原料准备:钢球的原料通常是高碳钢或者不锈钢。
在生产之前,需要先将原料进行分类和准备,确保其质量稳定。
2. 材料切割:将准备好的原料进行切割,得到合适尺寸的钢坯。
切割的精度和质量直接影响了后续加工的效果。
3. 球形成:通过冷挤压或者热锻等方式,将钢坯逐步加工成初形的钢球。
4. 热处理:对初形的钢球进行热处理,调整其组织结构和硬度,提高其耐磨性和使用寿命。
5. 精密加工:对热处理后的钢球进行精密加工,使其表面光洁度和尺寸精度达到要求。
6. 清洗与干燥:将精密加工后的钢球进行清洗和干燥,去除表面的油污和杂质,确保产品质量。
7. 检测与包装:对清洗干燥后的钢球进行质量检测,合格后进行包装和标识,最终成品待出厂。
钢球的生产工艺流程较为复杂,需要多道工序的精密加工和严格质量控制。
但正是这些精细的工艺流程,才确保了钢球在各种工业领域中的优异表现。
钢球生产设备旋切滚锻技术

钢球生产设备旋切滚锻技术
钢球生产设备旋切滚锻技术无需专业锻打人员,无需下料,无需空气锤锻打!该线从给料到出成品以及后续淬火等工艺全部采用微电脑自动化控制,提高了锻造钢球综合生产效率约20倍,节省劳动力,为企业提高产量同时节约大量生产成本。
钢球生产设备旋切滚锻技术基本原理:
将斜轧机的轧辊加工出螺旋状的沟槽或者突起,其断面可以是半圆形、梯形或其他形状。
从而使变形区形成螺旋状的孔型。
在轧制过程中,轧辊使轧件螺旋前进,金屑逐渐充满孔型,进而得到所需要形状的轧件。
该项技术可以用于钢球、麻花钻头和羽翎翅片管等产品的轧制生产中,也可以用来生产各种环件产品。
螺旋孔型轧制所使用的设备主要是二辊或三辊式斜轧机,利用辊型的变化来生产不同形式的产品,本生产线可以实现单机自动化生产,如翅片管轧机等,生产线的组成包括上料装置、加热用自动输送机构、自动推料人料装置、轧机和出料分选装置,还有淬火或冷却装置等。
我们生产的中频加热钢球轧制生产线、锻造钢球滚锻半自动生产线,只需空气锤粗打一锤毛坯料,然后进入自动滚锻。
操作简单,无需专业锻打,生产效率比传统应用要高很多。
轴承钢球斜轧机设计说明书1

轴承钢球斜轧机设计说明书与常用成型工艺铸造、锻造、切削相比,轴承钢球斜轧工艺具有如下优点: ○1单机生产效率高。
轧辊每旋转一圈就生产一个产品,轧辊转速以500 r/min 计,每分钟可生产500个产品(多头孔型则倍增),比锻造、切削的生产效率平均高5~20倍。
○2材料利用率高。
锻造之后进行机加工的轴承钢球,材料利用率一般只有60%左右,斜轧成型的轴承钢球,材料利用率一般可达80%,精密斜轧可达90%以上。
○3产品质量高。
轧制成型的轴承钢球金属纤维流线沿产品轴线保持连续,轧后晶粒细化。
○4劳动条件得到改善。
与锻造相比,无冲击噪声,劳动条件得到明显改善。
轴承钢球的成形、精整、切断在轧辊孔型中连续自动完成,若进出料亦采用自动操作,可极大减轻操作工人的劳动强度。
○5生产成本下降。
生产人员、辅助人员、设备台数及厂房面积等都可大幅度降低,生产成本大幅度下降。
以上优点在国内外相关轧制成型产品生产中均得到证实,斜轧成型的这些突出优点及社会生产对环保、节能、效率要求的提高,必将使轴承钢球斜轧技术得到广泛的应用。
1. 轧机要求为使轧机系统匹配合理,综合考虑规模、效益、节能与复杂性之间的关系,对轴承钢球轧机提出如下设计要求。
○1能轧制直径Ф20~40 mm 的轴承钢球,其中轧辊孔型以"811钢球为例进行设计;○2为保证适当的劳动生产率,轧辊需具有较适当的转速,"811钢球轧制时轧辊转速约为150r/min ;○3为保证在一台轧机上实现多种型号轴承钢球的轧制,轧辊采用分体式结构,并可进行轧辊倾角、相位角、轴向位置、径向距离、导板的调整;○4轧机有安全保障及急停机构。
2. 轧机总体配置从国内外的现有设计情况看,斜轧机总体结构配置上主要有三种类型:一是将电动机、传动装置及工作机座安装在地基基础上,从轧制无缝钢管的斜辊式穿孔机发展来的穿孔机式斜轧机;另一种是将电动机、传动装置、工作机座等配置在一起,从辊式无心磨床发展来的机床式斜轧机;第三种是机架可调整的钳式斜轧机。
钢球的生产工艺

钢球的生产工艺钢球的生产工艺主要包括原料准备、钢球制造、热处理和表面处理。
下面将分别介绍这些工艺的步骤和流程。
首先是原料准备。
钢球的主要原料是铬合金钢,其主要成分为碳(C)、铬(Cr)和锰(Mn)。
根据不同型号和规格的钢球需求,选择合适的原料进行准备。
原料一般采用炉料和粉料两种形式,经过称重、混合和筛选等工序进行准备。
第二步是钢球制造。
钢球制造主要包括热轧、冷镦、热镀、磨削和德比通风等工序。
其中,热轧是将预热的钢坯通过热轧设备进行压制和锻造,形成初始形状的钢球。
冷镦是将初始形状的钢球通过冷镦设备进行冷加工,使钢球的强度和硬度得到提高。
热镀是将经过冷镦处理的钢球通过热镀设备,进行淬火和回火处理,使钢球的表面硬度和抗磨性得到提升。
磨削是对热镀后的钢球进行研磨和抛光,使钢球的精度和表面光洁度达到要求。
德比通风是对磨削后的钢球进行分级和筛选,将符合规格和质量要求的钢球进行筛选和分装。
第三步是热处理。
热处理主要是通过加热和冷却的方式,改变钢球的组织结构和性能。
常用的热处理方法有淬火和回火。
淬火是将钢球快速加热到临界温度后进行急冷,使钢球的组织转变为马氏体,提高钢球的硬度和强度。
回火是将淬火后的钢球再次进行加热,然后进行缓冷,使钢球的组织转变为回火组织,提高钢球的韧性和抗冲击性。
最后是表面处理。
表面处理主要是为了提高钢球的抗腐蚀性和表面质量。
常用的表面处理方法有酸洗、电镀和喷丸。
酸洗是将钢球浸泡在酸性溶液中进行酸洗,去除钢球表面的氧化皮和污染物,以达到清洁的效果。
电镀是将酸洗过的钢球放入电镀溶液中,通过电流的作用使钢球表面形成一层金属电镀层,提高钢球的抗腐蚀性和光洁度。
喷丸是将钢球放入喷丸设备中,通过高速旋转的喷丸剂,喷射钢球表面,去除表面的氧化皮和污染物,提高钢球的表面质量和光洁度。
综上所述,钢球的生产工艺包括原料准备、钢球制造、热处理和表面处理等步骤。
每个步骤都需要严格的操作和控制,以确保钢球的质量和性能达到要求。
钢球轧制生产线独特创新

钢球轧制生产线独特创新
面对钢球轧制设备空前的发展机遇。
百川进行了独特的创新,通过整体布局设计,操作简易快捷。
我公司不但调整产品结构、提高开发能力,而且加强技术升级、产品换代、经营管理能力。
在钢球轧制设备方面,采用国际先进的标准与最新的计算机自动化技术,强化质量和设计结构,塑造高端的品牌形象,提升产品附加值,为我国钢球轧制行业打好基础。
进行生产改革、技术改革、设备改革等,走向了自主创新发展之路。
钢球轧制设备生产工艺流程:
轧制钢球时,先用感应加热炉把直径比轧出球的直径小4%左右的圆钢毛坯加热至850~1100℃,滚珠轴承钢取下限。
加热好的棒料送入斜轧机进行轧制。
(1)圆钢棒料经检验后,按定尺长度剪切成钢球坯料.
(2)钢球坯料在轧制前在连续感应加热炉中被加热到合适的温度。
(3)红热态的钢坯被送入钢球轧机后,在2个带有特殊螺旋形孔型的轧辊之间旋转前进,并被连续地轧制成钢球。
每台钢球轧机每分钟可轧成60-360个钢球。
(4)轧成后的红热态钢球立刻进入本厂特殊设计的在线热处理设备进行淬火-回火热处理,使钢球获得很高而且均匀的硬度。
(5)经检验合格的产品送往成品仓库,进行包装后发往客户。
百川通过密切合作和个性化服务,与客户共同分享对于事业的激情与关注。
我们不仅仅销售钢球轧制设备、钢球轧制生产线,更重要的是
为客户提供理想的解决方案。
我们优化您的布局,合理分配电能。
运用多年积累,经过不断优化的知识和经验,我们的客户将获得在市场上更加有效的竞争利器。
钢球轧机工作原理

钢球轧机工作原理
钢球轧机的工作原理如下:
1. 钢球输送:将待轧的钢球通过输送系统送入钢球轧机的工作区域。
2. 钢球定位:利用定位装置将钢球准确地放置在轧制辊道上,以确保每个钢球进入轧制环节时位置一致。
3. 轧制过程:钢球在轧制辊道上通过一系列的辊轧操作。
辊轧一般由一对或多对辊子组成,辊子通常是呈圆筒形状,通过旋转将钢球挤压成所需的形状和尺寸。
压力可以通过调整辊子之间的间隙来控制。
4. 冷却:经过轧制后,钢球通常会发热,因此需要进行冷却。
冷却可以通过水或其他冷却介质进行。
5. 检验和修整:冷却后的钢球可能存在一些缺陷,如尺寸不一致、表面不平整等。
因此,需要进行检验和修整,通常使用特殊设备检测钢球的尺寸、硬度、表面质量等,并通过修整设备对其进行修整和研磨。
6. 成品收集:经过检验和修整后,符合要求的钢球被收集起来,用作后续的应用,如制作轴承、汽车零部件等。
整个过程中,钢球轧机需要通过传动装置提供足够的力量和速度,以确保钢球在轧制过程中能够达到所需的形状和尺寸。
同
时,工作区域需要具备较好的冷却和排气条件,以确保钢球的质量和生产效率。
钢球轧制生产线

铸球的一半,冲击韧性高达12-35J/cm²,破碎率小于0.1%。 能耗低、无污染、劳动强度低、生产成本较低,从长远来看,铸球将不可避免地
被轧球所取代。
11
钢球轧制生产线案例
Click here to add your title
操作方便 节能环保
智能操作简单,适用于各种加热工艺。
全数字式高效快速谐振,节能环保优势突 出
16
钢球轧制生产线三大优势
加热快 效率高
智能化 自动化
环保节 能省电
钢球轧制生产线可达到环保部门的各项指标要求,同时树立公司 形象。生产速度快,表面氧化少。非常容易实现自动控制,省心 省力。感应加热时电加热炉中最节能的加热方式由室温加热到 1100℃的吨锻件耗电小于360度。
7J/cm²),破碎率高于3%。 3、能耗高、污染大、工人劳动强度大、劳动生产率低。 4、原材料成本高、工资成本高、特别是Ø 50mm以下的小球,成本更高。 相对于铸球来说,旋切滚锻钢球是一种全新的轧制工艺技术,是球磨球制造业的
工艺技术突破,正在逐渐替代铸造球,滚锻钢球具有以下特点: 1、滚锻钢球具有钢的一切优点,通过热处理后层位高质量的球磨球。 2、生产效率高、产量大、旋切滚锻球生产机械化、自动化程度极高,没有人工操
6
(2)轧制钢球的质量高
轧制钢球质量高的主要原因 有两个方面:第一是轧制成 型的产品,金属纤维为流线 形;第二是轧制后晶粒细化。 这两点也是咋呼钢球的冲击 韧性和抗拉强度较高的原因。
(3)轧制生产是劳动条件好
轧制钢球,如果采用感应加 热和自动化上,下料生产线, 劳动条件将得到极大的改善。 减轻了工人劳动强度,改善 了劳动环境。
钢球是如何制造的
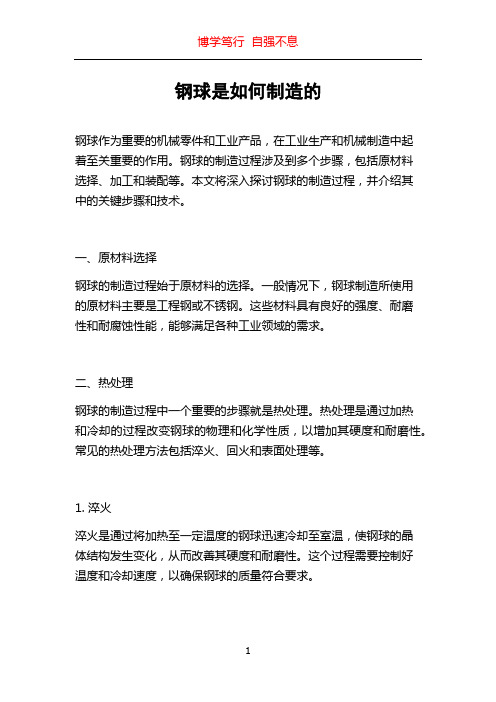
钢球是如何制造的钢球作为重要的机械零件和工业产品,在工业生产和机械制造中起着至关重要的作用。
钢球的制造过程涉及到多个步骤,包括原材料选择、加工和装配等。
本文将深入探讨钢球的制造过程,并介绍其中的关键步骤和技术。
一、原材料选择钢球的制造过程始于原材料的选择。
一般情况下,钢球制造所使用的原材料主要是工程钢或不锈钢。
这些材料具有良好的强度、耐磨性和耐腐蚀性能,能够满足各种工业领域的需求。
二、热处理钢球的制造过程中一个重要的步骤就是热处理。
热处理是通过加热和冷却的过程改变钢球的物理和化学性质,以增加其硬度和耐磨性。
常见的热处理方法包括淬火、回火和表面处理等。
1. 淬火淬火是通过将加热至一定温度的钢球迅速冷却至室温,使钢球的晶体结构发生变化,从而改善其硬度和耐磨性。
这个过程需要控制好温度和冷却速度,以确保钢球的质量符合要求。
2. 回火回火是在淬火后将钢球加热至较低的温度,然后保温一段时间,最后冷却至室温。
回火可以减轻淬火带来的内应力,并使钢球具有更好的韧性和强度。
3. 表面处理对于需要具备特殊功能和性能的钢球,如防腐蚀、耐磨、抗疲劳等,常会进行表面处理。
常见的表面处理方法包括镀锌、镀铬、磨削和抛光等。
三、加工和装配经过热处理后的钢球需要进行进一步的加工和装配。
这个阶段的主要工艺包括车削、磨削、抛光和洗涤等。
1. 车削车削是将热处理后的钢球放置在车床上,通过旋转和切削,使钢球达到所需的尺寸和形状。
车削时需要注意控制好车刀的质量和切削速度,以确保车削出的钢球达到要求。
2. 磨削磨削是通过研磨机将钢球加工至更高的精度和光洁度。
磨削时需要选择合适的磨削工具和工艺参数,以达到所需的表面质量和精度。
3. 抛光抛光是在磨削后对钢球进行光洁度提升的工艺。
抛光可以使钢球表面更加平滑,减少摩擦和磨损。
4. 洗涤在加工和装配后,钢球需要进行洗涤以去除可能附着在表面的污垢和杂质。
洗涤过程可以使用化学洗涤剂或高压水流等。
综上所述,钢球的制造过程包括原材料选择、热处理、加工和装配等多个步骤。
热轧钢球设备详解

热轧钢球设备工艺参数
? 轧机采用铸钢半闭式机架、机座刚性好;导板更换简便快速、效率高。为钢球轧制生产 线设备稳定、高效、高质量的运行提供保证。 φ60mm 以上轧机设有电动侧压调整装置, 其调整更省力、更换轧辊更方便。热处理淬火温度自动控制,轧辊自动快退功能,轧卡 时保证轧辊不受损伤;自动送料功能,提高成材率。
? 热轧钢球设备采用全自动生产流水线作业环保,节能高效。生产的钢球具有尺寸精确、 圆整的几何形状,高硬度和良好的机械性能并具有冲击韧性高,抗破碎能力强的特点。 钢球斜轧机经过创新设计具有如下特点:
8
热轧钢球设备轧辊简介
? 热轧钢球及孔型法向剖面尺寸
? 热轧钢球时,先用感应加热装置把直 径比轧出球的直径小 4%左右的圆钢 毛坯加热至 850 ~1100℃ ,滚珠轴承 钢取下限。加热好的棒料送入斜轧机 进行轧制。轧辊轴线与轧制线倾斜一 定角度。轧辊上有螺旋孔型。轧件螺 旋前进。在螺旋孔型作用下,圆钢逐 渐变成球形,球形间连接颈部分越来 越细,最后断开而获得钢球。
钢球轧机传动装置包括:电动机、皮带 减速装置、减速分动器、齿轮座及万向 节轴等。其主要作用是将电动机转速下 降到轧辊的转速(增大输出转矩),将 一个旋转运动转换成两个相同方向的旋 转运动,并实现轧辊相位的调整。
5
热轧钢球设备发展情况
随着科技的发展,传统空气锤锻打工艺逐渐淡出历史舞台,取而代之的是钢球轧机斜 轧工艺,用电炉将整根的圆钢加热,通过、输送装置送入轧辊,通过电机和减速机带 动轧辊旋转,轧辊就可、以利用其自身的球槽设计将高温的圆钢斜扎成球。旋转切割 技术取代传统的空气锤,大大提高钢球生产的产品效率。 斜轧工艺无需下料,无需空气锤锻打,大大提高了生产效率,工人劳动强度也大大、 降低,受到的噪音等危害也大大减少,钢球轧制技术使锻造钢球行业得到飞跃式的发 展。
球磨钢球轧机

10
钢球轧制生产线发展趋势
根据轧制球磨钢球的规格品种,钢球轧制生产线能生产φ20~150各规格的球 磨钢球以及各种钢段,满足不同用户的要求。
11
例
图 片
案
例
图 片
案
例
图 片
案
广
•通过密切合作和个性化服务,百川钢球设备与客户共同分享 他们对于事业的激情与关注。不仅仅销售球磨钢球轧机、钢
8
•球磨钢球轧机采用全新的轧制工艺技术,是球磨球制造业的工艺技术突破,热轧 钢球正在逐渐替代铸造钢球。 •本公司设计制造的球磨钢球生产线还具有以下功能: •1、热处理入淬温度自动控制,保证淬火质量; •2、轧辊自动快退功能,轧卡时保证轧辊不受损伤; •3、定点送料功能,提高成材率。本公司开发设计制造的热轧球磨钢球生产线为全 自动流水线生产,达到热轧钢球生产的最新水平。
球磨钢球轧机配有全自动加热设备和 传动设备形成钢球自动化生产线。
采用全自动生产流水线作业,无人工 干预,全自动生产,能够最大限度确 保钢球品质的稳定性。该生产线生产 工艺环保,节能高效。生产的钢球具 有尺寸精确、圆整的几何形状,高硬 度和良好的机械性能并具有冲击韧性 高,抗破碎能力强的特点。
3
球磨钢球轧机简介
6
球磨钢球轧机应用
•近十年,斜轧钢球成形技术和设备有 了突破型发展。一般来说,铸球可称 为耐“热”球,适合干磨,水泥厂用 铸球比较合适,轧球可称耐“腐蚀” 球,适合湿磨,铸球容易碎,轧球的 效果要优于铸球。 •钢球的轧制也称为钢球斜轧,是在球 磨钢球轧机上进行。轧制成型工艺有 几十年的历史,但在近十年才在钢质 磨球的生产中得到广泛的应用。 •在建材,冶金,矿山,陶瓷,电力等 行业使用的耐磨钢球分为铸造钢球和 锻轧钢球两大类。铸造钢球主要有低 铬钢球、高铬钢球、和铬铜钢球等。
钢管斜轧技术

钢管斜轧技术2006年第6期世界钢铁?2l?钢管斜轧技术(德)RolfKtimmerling摘要介绍了不同类型斜轧机的轧制原理和数学模型.通过变形分析,专门研究了轧辊和轧件接触面的速度状态,检验了不同结构的轧机在其使用范围的能力.检验结果表明,现有轧机设计并非都是最优.此外,还提出了各种使用条件下的改善方案.借助斜轧的通用表述形式,把变形行为转换为数学模型,可以使之更加完善.关键词钢管斜轧变形分析数学模型0前言斜轧方法是曼氏兄弟在I20年前的发明.两根轧辊倾斜于轧制方向,在同方向旋转,使轧辊之间的圆形钢坯产生螺旋前进运动,并通过一只固定在轧制线上并在出口侧用顶杆支撑的顶头将轧件穿孔.斜轧穿孔的发明使经济生产无缝钢管成为可能.从光轧过程开始观察,轧件在两根轧辊中进行螺旋前进运动,但没有内部工具.轧辊通过锉轧轧件表面,仅仅起到光整轧件的作用.若以螺旋运动为特征定义,那么,斜轧是一种非常独特的轧制方式.斜SLSL机具有同行星斜轧机一样的特性.从行星轴线角度观察轧件运动为螺旋运动.表I示出几种主要的斜轧设备形式,并给出他们的使用范围及各自螺旋运动方式(即进料方式)等信息.表I常用斜轧设备矫直机对圃棒或钢管矫直.无轰譬筹垂直线上倾无1工艺选择选择新的钢管轧机,需要确定其规格,材料,辅助工具以及生产能力等.有多种斜轧工艺和纵轧工艺可供选择.斜轧生产的钢管管壁厚度波动较小,但轧制过程中轧件经受的应力很大,而纵轧具有更高的生产能力和表面质量.这就需要研究斜轧时材料变形力,尺寸(直径,壁厚)变化以及轧制力和能耗等.-22-2006年第6期通常,可以用以下分析方法进行斜轧变形的分析计算.1.1变形技术研究到目前为止,要真正完整地描述斜轧过程是不太可能的,但至少可以通过如下方法对各种斜轧方法进行评价和比较.(1)变形区几何分析;(2)轧制速度研究;(3)轧制压力和功率计算.1.1.1几何参数分析表述由于轧辊是轴对称的,可以用轧辊自身坐标系w,Yw,zw来描述,z是轧辊轴线.轧辊表面任一点Pw的坐标可用方程1表示:+yw2=r(zw)(1)因轧件采用笛卡儿坐标系,Y,z表示,轧辊上点Pw=Pw(w,Yw,zw),通过公式(2)将坐标变换成轧件坐标系坐标.Pw=Pw((w,Yw,w),Y(w,Yw,w),z(w,Yw,zw))(2)取z轴表示轧件轴线,取轧辊间距最小点(辊面最高点)所在面与z轴的交点为原点,建立—Y—z坐标系.图1示出该坐标系的主视图,俯视图和侧视图,并在图中标明,,c以及前进角JB和咬入角等5个参数.相应的变换方程式如下:w:[(—)cosd+(Y一—)sind]cosE一(z—C)sinE图1斜轧过程一般几何示意图Yw=一(—A)sing+(Y—B)cosw=[(—A)cos+(Y—B)sina]sinE+(z—C)cosE(3a)或=(XWcosE+ZWsinE)cos—Ywsina+AY(XWcosE+ZWsine)sina+YwCOS+B=一XWsine+zWcosE+C(3b)这些轧机形式的特征参数用,,C以及前进角JB和辗轧角d值表示,如表2所示.表2不同斜轧机特征参数参数带转向轴的桶/锥斜轧机带偏心的锥式斜轧机带扭转机架的桶/锥形斜轧机行星轧机AⅡaD./2丑Ob00CZHP0ZHPZHl,~CCO$(co.cosy)O一w/2口alY:CO$(sin6/v,l—COS.ycos占)占6叮rarcc0s(sin占c0s',/~/1一CO$',c08占)0一w/20o=轧辊轴线沿送进角回转轴到轧机中a=在孑L喉面上轧制Dl=出口处支架环直径a=轧辊轴线沿送心线的距离中心线到轧辊中6=辗车L角进角回转轴到=送进角心线的距离L=机架间距轧机中心线的6=辗轧角b=偏心值口=机架扭转角距离6=辗车L角..Dl—Docos0=转向角丽一6=辗车L角..…~/L一DoDl(1一cos0)/2z=轧辊圆点面……£十(Dl—Do).到孔吼面的D0=人口处支架环直径距离Do=D一2L't∞6zHP=人F1支架到孑L吼处的距离世界钢铁?23?1.1.2轧件轴至轧辊的距离为确定内部工具形状,需要计算从轧件轴线上某一点到轧辊表面的距离.利用计算机很容易计算这个距离,只要在径向引一条线与轧辊相交即可.该交点确实存在,并恰好与最短距离的点重合.对于给定的空间曲线,往往需要计算轧辊的辊型.下面是一个矫直辊辊型的例子.轧件的计算公式如下(轧件坐标系,Y,ZM):F=2+y一r(z)(4)通过坐标转换成工具坐标系,y,Z有:M=M(w,Yw,Zw)YM=YM(w,Yw,Zw)ZMZM(w,Yw,Zw)rM=rM(ZM(w,Yw,Zw))(5)求解以下方程组可得到w和YwM(M,YM,ZM);0(6).一.:0Yw(7)一OYM'XW【)轧辊外形半径可以通过下式计算:rw(zw)=√+y(8)1.2速度参数计算为了分析材料的变形行为,了解轧件和轧制工具在接触面上的速度分布是非常重要的.假设轧辊在逆时针方向旋转,根据公式(9)可以得到各个方向上的速度分量:w.—d—tWYw'''w.—d—tYw一W''dfdzw=w=0(9)把变换方程式(3b)对时间微分,代人公式(9),则:=([(Y—B)cosfl一(Z—C)sin/3sinc~]=[一(-A)cos/3一(Z—C)sinflcosO/]z=([(—A)sintx一(Y—B)COSO/]sin]3(10)若想研究延伸变形,就要考察沿轧辊与轧件轴线距离最短线上的速度.这条线限制了理想轧制表面.比较该边界线的平行线上的速度,检查其速度分量,则可判断其与期望的变形过程是否吻合.材料沿z轴的延伸和流动可以通过纵向和轧件圆周方向的分量比,也可通过接触面流动的送进角来研究.在随后具体轧机的变形行为分析中可以发现,本方法和实际结果有良好的符合性.1.3轧制压力及功率计算穿孑L机,延伸机以及斜轧扩管机等斜轧设备的扭矩和功率可以通过下式来计算:N=A?V^?v?Kw,(11)式中,表示轧件出口处的横断面面积;VA表示轧件出口速度;表示总变形率;Kw表示变形抗力.通过测量或对类似轧机数据的回归可以得到变形抗力.例如,穿孔轧机中变形抗力约300N/ram.但计算轧机的轧制力采用比较简单的方法,如轧制力=变形抗力X受压面积,计算精度难以如愿.根据对工具的分析描述,工具的速度和经验系数可以准确计算辊管接触而积.通过局部应力平衡,对表面应力求和,即可得到轧制力.由于已知空间位置,也可以计算轧机机架和轴承的受力情况.2斜轧机变形研究2.1桶形/锥形穿孔机桶形/锥形穿孔机是斜轧机的主要代表,用于生产各种无缝钢管半成品.桶形斜轧机配导板的叫施蒂费尔斜轧机,配狄塞尔导盘的叫狄塞尔斜轧机.目前常用的狄塞尔斜轧机是一种具有高变形效率的钢管斜轧机,轧后长度可以达到10m, 轧制节奏可达到4.5根/min.关于穿孑L机目前还有很多问题有待解决,如: 结构是选用桶形还是锥形结构,锥形结构选用多大的辗轧角,导向工具选用导板,还是狄塞尔导盘,能否达到外径壁厚要求等等.下文详述各种轧机的优缺点.假定斜轧机轧辊表面速度状态的评价,这类轧机常规参数为:孔喉处的轧辊直径为1100mm,轧辊间距为150mm,入口角与水平线的角度为一3.5.,出口角与水平方向的角度为+3.5.,送进角为l0..图2~4示出孑L喉面及其前150mm和后300mm面的纵向速度分量,角速度,送进角随辗轧角(范围为一30.至+30.)的变化.图中0线表示轧辊轴线到辊管接触面的最小距离.3o线表示在轧辊轴向上与0线距离为30mm的平行线. 就评价而言,这已经足够了.为了简化起见,假设轧件在轧辊下相对纵轴只作横向运动.-24-2006年第6期ll一一L囊1l;O柚-自t'皿面一,,一_一'一孔喉面I孔喉I后I310OnI的I平I面J一一/一/—/—一30-20~100102O30辗轧角/(.)一一0线——30线图2纵向速度随辗轧角的变化(轧辊角速度:1/s) 孔嚷l口11;01?白£皿孔喉i叫孔嚷言3()01?自乞.皿-30-20-100102030辗轧角/(.)一一0线一30线图3角速度随辗轧角的变化(轧辊角速度:1/s) 令人惊讶的是,通常的穿孔轧机,从桶形(碾轧角为O.)到具有+30.碾轧角的锥形结构,都没有因轧辊引起的附加纵向金属流动,原因是轧辊下变形区的送进角变小,只有在碾轧角为负值时才有所增加.穿管中由径向金属造成的延伸主要是材料内部协调的结果.14121086.12l0e614121086孔喉前】50m的西●/lJll/ll,J一l——LJ_:十1IlIlllfL峨脚—L—Ll.王.fL峨/ⅢHU-T_:一30—20辗轧角()一一线——30线图4送进角随辗轧角的变化(轧辊角速度:)业已确认的结论是,锥形穿孔机比桶形穿孔机的送进效率高,因为锥形穿孔机送进角和纵向速度都高一些.从实际生产中得知,锥形穿孔机延伸能力较好,因为其送进角大.每道次轧制中, 孔喉前的压下较大,材料内部协调更好,流向纵向的金属更多.孔喉后区域中,壁厚的减少几乎都变成了直径的增加.穿孔过程中轧件因沿长度上的速度变化造成的长度金属纤维的转动也有必要进行研究.桶形穿孔在孔喉前金属稍稍正向方向(转动方向)转动,在孔喉后为剧烈的反向转动,最终造成管坯上反向扭转.对于锥形穿孔,在孔喉之前,根据碾轧角从稍稍有点正向扭转到强烈的扭转,在孔喉之后,只有一点点反向扭转直至完全没有扭转.这样根据辊形和碾轧角不同,最终可能是正向,也可能是反向扭转.由于考察材料应变必须考虑变形历史,仅仅根据管坯上的扭转确定材料应变是不合适的.像具有大碾轧角的锥形穿孔机造成的纯粹正向扭转不比桶形穿孔机造成的先正向然后反向的扭转差.实际生产中,由于机型和辊形不同,可能会造成轧件强烈正向至再到剧烈反向扭转.这里没有涉及到内部或外部缺陷.大的送进角和高的送进效率轧制对材料总是有利的,也就是说,在这方面锥形穿孔优于桶形穿孔.关于是否可以选择负碾轧角的锥形穿孔机,从两个方面考虑答案都是否定的.一方面,这类轧机不能扩径,另一方面,若是(下转第45页) mm∞∞∞mm∞∞∞啪mm∞∞∞一I-s.-I)\越厘器975397639763\越瓒嘏世界钢铁?45?:I臣,/…一5O250255O75--50—250255075单向AN0~A:C5对c1液面波Jv均值标准偏燕前l861,5.1221.68后915.74ll1.9l均标准偏差=19.O4图13UCN3000的统计效果5结语用于消除不稳定鼓肚和表面波的控制模块被集成在UCN3000分级控制器中,大大改进了浦项GYCC21连铸机的结晶器液面周期性波动问题,这种方法似乎非常有前景,2006年在欧洲的两台板坯铸机上对液面控制的改善情况进行过评估.这种包括过程分析,控制设计,工厂试验,工业实施在内的全方位解决方法对CC2—1连铸机是非常有效的.而且,对于在投资一个新的液面控制系统或对现有液面控制系统改造前计算其收益的高要求用户来说,分析阶段在预测改进效果时的高精确性为用户提供了强大的工具.参考文献(略)职建军译自((AISTech2006}.995~1003李晟校.-t--.+.+"'_卜"'_卜".+l?'+L"—+"+"+"十,,-t--'?—+'?—+??-4-??-4-,?-t--?-+?-+--+-?+?-+--+-?-4-??-t--"+?-+--+"+"+一一+-?十一?+??+,?+?+-+?-+--+,?+?-+-,+"+"+(上接第24页)希望减径和产生大的延伸,这类轧机会在矫正区,即孔喉后产生极大的速度差(详见后面行星斜轧机).穿孔机选择桶形还是锥形,导向工具选择导板还是狄塞尔导盘取决于需要,这里应该考虑以下因素:①带狄塞尔导盘的锥形穿孔机比带导板的桶形穿孔机昂贵;②带狄塞尔导盘的锥形穿孔机比带导板的桶形穿孔机轧制速度快;③顶杆应力,顶头应力取决于接触时间,与轧制速度一同评价;④狄塞尔导盘的寿命比导板更长;⑤导板的磨损会导致轧后毛管产生外部缺陷;⑥哪个可以轧制高合金材质的钢管,而且进料效率更高;⑦对于不同材质的坯料(包括高合金坯料),导板和导盘哪个更好.轧辊直径大小与变形关系不大,主要取决于框架大小和磨削量.2.2桶形斜轧延伸机桶形斜轧延伸机原理上和配有导板或狄塞尔导盘的桶形穿孔机一样,但并不是穿孔机,而是将穿孔后的厚壁毛管延伸,但几乎不改变钢管的外径.管内工具是芯棒,其作用和穿孔顶杆一样,放在出口端并有止推小车进行支撑.延伸机用在自动轧管机组中压力穿孔机之后,在传统设计中,它位于穿孔机后作为二次斜轧机.其结构与孔型设计和桶形穿孔机相似,其速度随辗轧角的变化见图2~4.由于入口毛管的壁厚较厚且变形区相对较短,使得材料在轧制切线方向的流动比较困难,因此一般认为该机只能作延伸机用.3结语通过对几何学和速度的研究可以设训.车L辊及其配套工具的形状,可以研究轧件的变形行为. 根据介绍的方法,可以较高精度地计算斜轧变形力并进行能力评价.综合两种方法成功地进行了测试.相对速度和变形力相互依存,可以通过叠代来确定.这样也可能预测轧件在自由面的几何尺寸.通过斜SLSL$0一般示意图,将所需的变形参数进行坐标变换,计算未知的五个几何参数,研究轧制过程的几何变化和速度变化.这种方法可以用来优化现有的轧制设备.参考文献(略)洪杰摘译自《StahlundEisen》,1989,(9/l0),181~189焦四海校;},}}.。
百川钢球设备讲述钢球轧制

百川钢球设备讲述钢球轧制用孔型斜轧生产钢球的轧制工艺。
钢球主要有轴承钢球和球磨钢球等。
过去,钢球生产多半采用锻造、冷镦和铸造等方法制造,生产率低,劳动条件差,成本高。
现多采用螺旋孔型斜轧工艺生产。
既可采用单头孔型轧制,也可采用多头孔型轧制。
单头螺旋孔型是指轧辊上只258有一条螺旋孔型,而多头螺旋孑L型则指轧辊上有两条或两条以上的螺旋孔型。
生产上多采用两头、三头或四头螺旋孔型轧制,轧辊每转一转可以生产出两件、三件或四件产品,生产率成倍增长。
钢球轧制多采用热轧,小直径的钢球可以冷轧。
<BR>热轧钢球时,先用感应加热装置把直径比轧出球的直径小4%左右的圆钢毛坯加热至850~1100℃,滚珠轴承钢取下限。
加热好的棒料送入斜轧机进行轧制。
</P><P>轧辊轴线与轧制线倾斜一定角度。
轧辊上有螺旋孔型。
轧件螺旋前进。
在螺旋孔型作用下,圆钢逐渐变成球形,球形间连接颈部分越来越细,最后断开而获得钢球。
轧后的钢球经过进一步处理后即得到成品钢球。
斜轧钢球轧辊及其孔型展开示意图如图a所示。
图b是棒料被咬入孔型后轧件沿孔型沟槽在滚动中前进时受到压缩成形、精整,最后成圆球脱离孔型的全过程的示意图。
<BR>轧辊孔型由成形段和精整段两部分组成。
成形段孔型完成咬入毛坯,并把圆棒轧成球形。
精整段中轧件受到精整并同毛坯分离。
孔型总长度在1170~~1350’,之间。
轴承钢球一般取精整部分为一圈左右。
成形段为一圈半至两圈。
成形段过长会使棒料在孔型中旋转次数增多,易造成钢球中心疏松和孔腔。
<BR>球磨钢球孔型t原则与轴承钢球的基本相同。
但球磨钢球斜轧孔型精整凸棱升高至(或略高于)轧件轴线,以将轧件尾巴切净。
精整段孔型的凸棱是平直的,不需开储料槽。
球磨钢球孔型精整段比轴承钢球孔型加长较多。
其孔型总长度一般取1260~~1350o。
对小尺寸的锥面圆柱滚子常采用单腔轧制即一个轧辊带螺旋孔型,另一个轧辊是不带孔型的光辊。
钢球制造工艺流程

钢球制造工艺流程一、原材料准备。
钢球制造嘛,那原材料肯定得先准备好呀。
咱一般用的就是钢材啦。
这钢材可不是随便选的,得根据钢球的用途来挑呢。
要是做那种比较耐磨的钢球,就得选硬度高一点的钢材。
就像给钢球选衣服一样,得合适才行。
钢材选好了,还得检查检查,看看有没有什么瑕疵啊,裂缝之类的。
要是有问题的钢材做成了钢球,那钢球的质量可就没保证啦。
二、下料。
接下来就是下料啦。
这个过程就像是把一大块布料剪成小块一样。
不过咱这可是钢材,用专门的设备把钢材按照预定的尺寸切成一小块一小块的。
这个尺寸可重要啦,要是切大了或者切小了,后面的工序可就麻烦咯。
而且切割的时候得小心点,要保证切出来的钢材块形状规则,就像咱们剪纸的时候想要剪出一个漂亮的形状一样,得慢慢的,稳稳的。
三、锻造。
然后就到锻造这个环节啦。
锻造就像是给钢材块做运动,让它变得更结实呢。
把下料后的钢材块放到锻造设备里,通过高温和压力,让钢材块发生变形。
这个过程中啊,钢材的内部结构会变得更加紧密,就像我们人锻炼后肌肉更紧实一样。
锻造的时候温度要控制好,要是温度太高了,钢材可能就烧坏啦,温度太低呢,又锻造不好。
就像烤蛋糕一样,温度不对,蛋糕就做失败咯。
而且锻造的力度也得掌握好,力度太大,钢材可能就变形过度啦,力度小了,又达不到咱们想要的效果。
四、球化。
锻造完了就开始球化啦。
这个可是让钢块变成钢球的关键步骤哦。
通过一些特殊的工艺设备,把锻造后的钢材慢慢加工成接近球形的样子。
这个过程就像是捏橡皮泥一样,一点点的把钢材捏成圆滚滚的钢球。
不过这可比捏橡皮泥难多啦,要不断地调整形状,保证每个地方都能均匀地变成球形。
而且在球化的过程中,还得注意钢球的表面质量,不能有坑坑洼洼的地方,就像我们的脸蛋一样,要光滑平整才行呢。
五、热处理。
球化后的钢球还得经过热处理。
这就像是给钢球做个SPA,让它的性能更好。
热处理可以改变钢球的硬度、韧性等性能。
根据不同的需求,会有不同的热处理方式。
比如说有的钢球需要高硬度,那就采用能增加硬度的热处理方法。
国外钢球制造技术简介_一_

国外钢球制造技术简介 (一)洛阳轴承研究所 (471039 河南洛阳) 王保振以超高速旋转开式轧制的工艺方法, 将轧制成型 的钢球毛坯一个一个地断开, 最后球坯为不带小 尾巴的理想球形。
美国生产的M C 5 F 型冷轧成型机, 轧制 1 钢球毛坯的制造国外钢球毛坯的制造方法一般根据球径大小 可分为: 钢球直径小于 <25. 4 mm 时, 采用冷热镦压成型法; 钢球直径大于 <25. 4 mm 时, 采用热锻 成型法或冷热轧制成型法; 特大型钢球球坯则采 用车削加工法。
而当今普遍采用的是冷热镦压成 型方法。
日本 N TN 公司对钢球直径在 <0. 6~ 28. 575mm 的球坯采用冷镦成型法; 直径大于 <30. 1 625 mm 的球采用热镦 成 型 法; 直 径 在 <30. 1 625~ 50. 8 mm 的 球 坯 采 用 亚 热 锻 ( 温 度 为 700~ 720℃) 成型法; 直径大于 <53. 975 mm 的球坯采用热锻压 (温度为 1 000~ 1 500 ℃) 成型法。
冷镦设备 采用美国国民机械公司生产的高速冷镦机。
<3. 175 mm 的碳钢球球坯, 其生产效率为 4 000 粒ƒm i n , 轧辊转速可达 800 r ƒm i n 以上。
俄罗斯的倾斜螺旋轧辊钢球轧制机, 按钢球 尺寸分为: 1 英寸 ( 24. 5 mm )、3 英寸和 5 英寸的 小中、大三种, 生产效率为 40~ 180 粒ƒm i n , 其中 热轧 <25~ 45 mm 的钢球毛坯尺寸偏差为 0. 2~0. 4 mm 。
每一对轧辊的使用寿命, 依产品重量计算: 1 英寸球坯为 100~ 220 t , 5 英寸球坯可达600 ~ 1 400 t 。
日本藤崎制作所制造的M D 型轧机, 分大、中、小三种型号。
小型M D 100K 3 可轧制 <20~ 43mm 罗马尼亚对钢球直径小于 <30 mm 的球坯, 钢球; 中型M D 200K 2 可轧制 <31~ 62mm 钢球;采用冷镦成型; 钢球直径在 <30~ 50 mm 采用高速热镦锻成型法, 其设备为 AM P 速镦锻机。
- 1、下载文档前请自行甄别文档内容的完整性,平台不提供额外的编辑、内容补充、找答案等附加服务。
- 2、"仅部分预览"的文档,不可在线预览部分如存在完整性等问题,可反馈申请退款(可完整预览的文档不适用该条件!)。
- 3、如文档侵犯您的权益,请联系客服反馈,我们会尽快为您处理(人工客服工作时间:9:00-18:30)。
钢球斜轧机轧制钢球工艺技术
热轧钢球是一种全新的轧制工艺技术,是球磨球制造业的工艺技术突破,正在逐渐替代铸造球。
热轧钢球具有以下特点:
1、热轧钢球具有钢的一切优点,通过热处理后成为高质量的球磨球。
2、生产效率高、产量大、轧球生产机械化、自动化程度极高,没有人工操作的生产环节,用人少,人为因素干扰小。
3、质量稳定、硬度高、淬透性好、金相组织致密、晶粒细小、不变形,钢球由始至终不会变形、不失圆,耐磨性能好,冲击韧性高达12-35J/cm2,破碎率小于1%;
4、能耗低、无污染、劳动强度低、生产成本较低
5、成形好,几何公差小,质量稳定。
6、磨损率低,使用寿命长,是现有铸造铁球、锻造钢球的2~5倍,且价格相当。
7、钢球硬度可达60~67HRC,内外硬度均衡,硬度差<5HRC。
8、冲击韧性高达12~35J/cm3。
9、比重大(7.8~7.85J/cm3)。