钣金检验规范(标准文本)
钣金件检验标准5则范文

钣金件检验标准5则范文第一篇:钣金件检验标准3063钣金件检验标准一、适用范围: 公司产品306钣金件的尺寸、外观检验。
二、检验项目及验收标准: A.尺寸验收标准: 尺寸按图纸要求及钣金加工公差表执行,特殊情况以实际装配为准。
B.表面处理验收标准: 1.颜色、图案、光泽度与样板相符合,同批产品无色差(不得大于3度)。
2.附着检验:用百格刀划一面100方格到底材后,用3M胶布贴上,60度方向瞬间用力拉开,不得脱落40/100格。
3.溶剂检验:酒精擦拭后,不能有变色、掉色、无光泽等现象。
4.硬度检验:以H铅笔将笔芯前端切齐,铅笔与待测物成45度推出,表面无划伤。
C 外观判定标准, 1.表面不得有任何碰伤、开裂、刮伤等严重表面缺陷。
2.表面污点、颗粒、气泡检验: 2.1 A面: 整个表面内允许3点,每点直径1mm以下,点与点距离20mm以上。
2.2 B面: 整个表面内允许5点,每点直径1mm以下,点与点距离20mm以上。
2.3 C 面: 整个表面内允许7点,每点直径1mm以下,点与点距离20mm以上3.箱体内表面允许8点气泡或污点, 每点直径1mm以下,点与点距离20mm以上。
4.烤漆厚度30μm-60μm。
5、不得有纹印,粘有织物绒毛现象;6、不能有流挂:表面有液体流淌状的突起,顶端呈圆珠状;7、不能有颗粒:表面呈砂粒状,用手摸有阻滞感;8、不能有桔皮:外观呈现如桔皮般凹凸不平,不规则波纹; 5)不能有漏底:表面透青,露出底材颜色;6)不能有麻点:表面因收缩而呈现小孔(麻点),亦称针孔;7)不能有发花:表面颜色深浅不一,呈花纹状;8)不能起皱:局部堆积凸起,呈皱纹状(皱纹粉除外);9 不能有夹杂:涂层中夹有杂物;机械损伤:外力所致的划伤、刮花、磨损、碰伤。
备注:A面:使用时面对使用者的表面B面:与A面相邻的4个表面、C面:使用时背对使用者的表面第二篇:钣金件检验规范钣金件检验规范包装质量要求1、目的明确来料的包装要去,确保外包装能有效防护产品,避免在运输、搬运等过程造成损伤,同时确保来料产品易于识别和追溯。
钣金加工通用检验标准

b是否拉、压到位,有无带料 c方向正确
d拉压后螺纹
目测
通止规
铆钉型号符合图纸要求
拉、压牢固≥15kg;带料≤1mm
方向依据图纸
螺纹通规通,止规止
螺钉、螺柱、螺帽是否歪斜
目测
目测无歪斜
编 制
日 期
审 核
日 期
批 准
日 期
钣金加工通用检验标准
文件编号
Q/GC201702
版 本
A0
生效日期
钣金加工通用检验标准
钣金加工通用检验标准
文件编号
Q/GC201702
版 本
A0
生效日期
总 页 数
5
页 次
1/5
1、目的
统一公司内生产加工基本的质量标准,规范各工段加工过程检验的内容。
2、适用范围
适用于公司内钣金件的生产加工和质量检验;若本标准与客户特殊要求或工程图面要求相抵触时,以后者为主。若工程图面未详述时,以本规范为主。
可接受手感轻微,无割手感;
碰焊正面凸点
样品比对目测Biblioteka 正面用刀口尺靠齐后平整、无缝隙
管材下料尺寸
卷尺、卡尺
重点尺寸:符合图纸标注
0~120:;大于120:GB/T 1804-2000-m
管材下料角度
角度尺、直角尺
角度±°,无歪斜;(试)
焊接
焊接尺寸、
对角线
卡尺、卷尺
重点尺寸:符合图纸标注
未注公差:GB/T 1804-2000-m
b、视产品强度、重量、形状决定产品堆叠高度;以手摇不晃,最底部产品没有变形风险为标准;
c、能使用打包带时尽量使用打包带,使用缠绕膜时需要将产品与栈板整个缠绕在一起,缠绕牢固;以产品不能随意移动为标准;
钣金检验规范

. 目的:为了便于控制钣金产品质量以及给检验员提供检验时的准确依据。
检验要求3.1 工件形状、材料种类符合图纸设计要求。
3.2 工件尺寸应符合要求:3.2.1 基本尺寸、公差范围应符合图纸标注尺寸。
3.3对盛装液体的工件检验:向工件内加入水如不发生渗漏则为合格外观A. 焊缝平整光滑,无裂纹,凹凸等缺陷。
B. 工件成型后边角分明,切边无毛刺,表面无划伤,不锈钢保护膜无破损。
尺寸A.直线度:1000以内≤±1㎜,1000~3000≤±3㎜B.平行度:1000以内≤0.5㎜,1000~3000≤0.8㎜C.焊接符合图纸设计要求,图纸未标注要求的工件: 1.厚度1~2mm时,焊缝高度1~4mm,焊缝宽度2~4mm;2.厚度3~4mm时,焊缝高度3~5mm,焊缝宽度3~5mm;D.剪板符合图纸要求,图纸未标注要求的工件: 1.厚度≤1.2 mm,公称尺寸≤200 mm 时,允许偏差±0.5 mm2.厚度≤1.2~4 mm,公称尺寸≤200 mm时,允许偏差±1 mm。
3.厚度≤1.2~4 mm,公称尺寸200~1000 mm时,允许偏差±1.5 mm。
4. 厚度≤1.2~4 mm,公称尺寸1000~3000 mm时,允许偏差±2.0 mm.表面处理A.护罩类钣金件焊缝必须打磨抛光打磨面要求平整、光滑、相接边倒圆角;B.不锈钢件,不要有毛刺,焊缝打磨光滑。
C.焊缝打磨拉丝的宽带不允许15㎜,拉丝后的表面和原表面无明显差别,光泽纹理一致。
剪板1.所剪板材必须满足技术要求;2.对角线必须准确,达到技术要求;3.剪料无毛刺,无弯曲,不变形,表面不得划伤。
型材切割1.所切割型材的长度尺寸必须满足要求;2. 2.所切割型材的角度满足技术要求;3. 3.切割断面必须垂直、平整、光洁,无变形现象。
数控冲孔1.计算、输入的数据必须准确无误;2.选择的冲模必须合理;3.加工后的零部件必须满足图纸及工艺要求。
钣金件检验标准

钣金件检验标准钣金件标准文档一、适用范围:公司产品钣金件的尺寸、外观检验。
二、检验项目及验收标准:A.尺寸验收标准:尺寸按图纸要求及钣金加工公差表执行,特殊情况以实际装配并提交研发部工程师协同解决。
附表:钣金加工公差表钣金加工公差表:a.剪断加工品之一般公差表板厚划分尺度区分1.5mm以下1.6mm~2.9mm3mm以上120以下121以上~315以下316以上±0.2±0.3±0.4±0.3±0.4±0.5±0.5±0.7±1.0b.折曲角度之一般公差折曲种类一般公差直角折曲0.5°其它角度折曲1.0°B.表面处理验收标准:a.表面烤漆检验标准:1.颜色及纹路:由承制方按要求制作样板,双方确认。
验收按样板,不得有明显色差(不得大于3度),纹路符合样板。
2.密着检验:用百格刀划一面100方格到底材后,用3M胶布贴上,60度方向瞬间用力拉开,不得脱落40/100格。
3.溶剂检验:酒精擦拭后,不能有变色、掉色、无光泽等现象。
4.硬度检验:以H铅笔将笔芯前端切齐,铅笔与待测物成45度推出,表面无划伤。
5.钣金件表面烤漆前须作前道电着处理,达到双重保护的目的。
根据实际的使用效果,允许厂商使用双面镀锌材质加工,以替代电着工艺。
钣金件标准文档6.厂商在每次送货时须提供材质报告,有表面处理要求的须提供表面处理检验合格报告7.外观判定标准,如下表:判定标准外观1.表面不得有任何碰伤、开裂、刮伤等严重表面缺陷。
如加工过程中有此缺陷,喷涂前须补腻子处理。
表面各边、角、焊接部位毛刺均须去除。
2.表面污点、颗粒、气泡检验:A面:整个表面内允许3点,每点直径1mm以下,点与点距离20mm以上。
B面:整个表面内允许5点,每点直径1mm以下,点与点距离20mm以上。
C 面:整个表面内允许7点,每点直径1mm以下,点与点距离20mm以上3.箱体内表面检验:各面允许8点气泡或污点,每点直径1mm以下,点与点距离20mm以上。
钣金通用检验标准
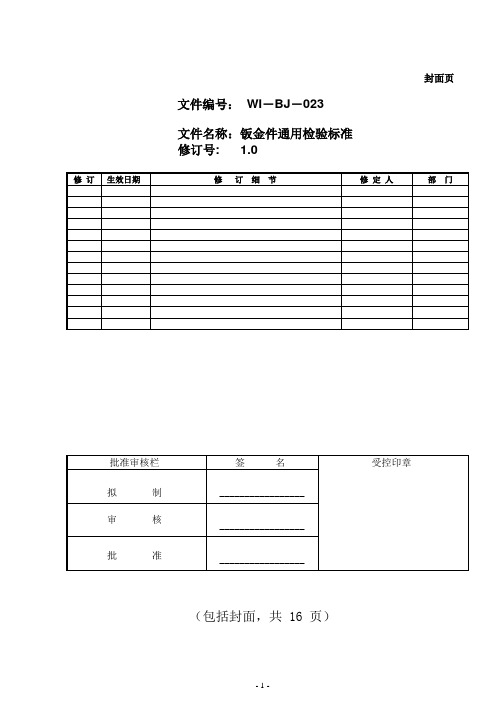
封面页文件编号: WI-BJ-023文件名称:钣金件通用检验标准修订号: 1.0(包括封面,共 16 页)1.0目的为保证我司钣金件产品的质量,又减少图纸对通用要求的描述,特制订本通用检验标准。
2.0范围本标准适用于我司标准以及非标准的钣金产品,本标准侧重范围,规定了钣金件在质量形成过程中各个工序的检验标准,主要从外观、尺寸控制、力度、组装要求作出规定;对钣金件产品的功能、结构特别性能不作规定,我司主要产品要求须参照相关检验标准,特别产品之特殊要求需另外说明。
3.0职责3.1工程部3.1.1设计时应支持本标准,对特别要求应特别说明。
3.1.2与本标准有关的不符合项之特纳。
3.2销售部3.2.1客户特别要求的收集3.2.2与本标准有关的不符合项之特纳3.3生产部按本标准做货及自检。
3.4品管部按本标准检验。
4.0作业内容4.1剪床开料4.1.1外观保证4.1.1.1剪床开料必须用经IQC检验合格之板材,大料平直度、外表面状态必须符合IQC检验标准。
4.1.1.2未经确认不得采用已生锈之SECC和SPCC板料,以及表面严重划伤之SUS板料。
4.1.1.3对胶沙不锈钢应注意开料之纹向要求,不可在不确定情况下作出纹向任意开料,并严格保护表面,以避免刮伤。
4.1.1.4剪床开料之批锋应小于料厚之3%,手摸应无明显刮手现象。
4.1.2尺寸控制4.1.2.1为保证钣金成形尺寸,减少过程累积误差对工件尺寸的影响,剪床开料尺寸允差按下表检验:4.1.2.2对一开几过多的开料件,如单一方向开料数量超过六件(一般应为偶数),应先将料对开,然后再开成单件,以减少误差累积。
4.1.2.3对长度超过1500-2500之开料切边直线度应小于0.3mm/m,宽度大小端误差小于0.5mm。
4.1.2.4开料件之长短边90。
角度允差±3´。
4.2 CNC冲孔4.2.1外观保证4.2.1.1 CNC冲孔应先检查板材是否有划伤,对经剪床放行而有少许划伤之板料,冲孔时应将划伤面尽量放于批锋面,以减少对外观的影响。
钣金件外观检验标准-00

凹坑接受原则,需不影响装配和功能;
漏底
不允许
不允许
碰伤
不允许
不允许
掉漆
不允许
不允许
掉漆指在附着力测试合格的前提下,因运输、周转等原因造成局部漆层脱落的状态
毛刺
冲裁后毛刺高度小于0.4mm
图纸标注的以图纸要求为准
脏污、灰尘
不允许
不允许
不允许
裂纹(拉裂)
ቤተ መጻሕፍቲ ባይዱ不允许
不允许
压痕
S<4.0mm2,H<1.5mm,在200mmx200mm范围内允许存在的缺陷个数为4,缺陷间距大于100mm;
S<4.0mm2,H<1.5mm,箱体单边允许存在的缺陷个数为6,缺陷间距大于100mm;
压痕仅限于存在底材表面;单个产品总缺陷数小于3
凹坑
S<3.0mm2单面允许存在缺陷数为3,缺陷间距大于100mm;
单个产品总缺陷数不超过5;不计入S<0.50mm2的点
颗粒(渣子)
S<1.20mm2,在200mmx200mm范围内,允许存在的缺陷个数为3,缺陷间距大于100mm
S<1.20mm2,单边允许存在的缺陷个数为3,缺陷间距大于100mm
不计入S<0.30mm2的点;B壳嵌在前壳部分,B壳底部颗粒标准可适当放宽
以洁净布料擦拭为依据
遮喷区域
参照图纸要求
螺母柱需遮喷以避免影响使用;
定位压痕
参照图纸
定位压痕指粘贴标牌、铭牌、绝缘片定位用压痕
焊点
参照图纸
其它
参照图纸
范围
本标准规定了钣金件、焊接件外观质量验收准则。本标准适用于钣金件、焊接件外观质量的检验和判定。
钣金件检验规范标准
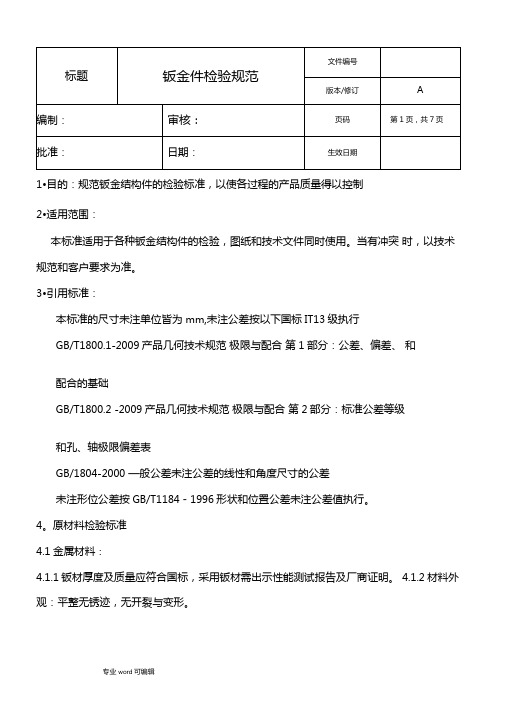
1•目的:规范钣金结构件的检验标准,以使各过程的产品质量得以控制2•适用范围:本标准适用于各种钣金结构件的检验,图纸和技术文件同时使用。
当有冲突时,以技术规范和客户要求为准。
3•引用标准:本标准的尺寸未注单位皆为mm,未注公差按以下国标IT13级执行GB/T1800.1-2009产品几何技术规范极限与配合第1部分:公差、偏差、和配合的基础GB/T1800.2 -2009产品几何技术规范极限与配合第2部分:标准公差等级和孔、轴极限偏差表GB/1804-2000 —般公差未注公差的线性和角度尺寸的公差未注形位公差按GB/T1184 - 1996形状和位置公差未注公差值执行。
4。
原材料检验标准4.1金属材料:4.1.1钣材厚度及质量应符合国标,采用钣材需出示性能测试报告及厂商证明。
4.1.2材料外观:平整无锈迹,无开裂与变形。
4.1.3尺寸:按图纸或技术要求执行,本司未有的按现行国标执行4.2通用五金件、紧固件4.2.1外观:表面无绣迹、无毛刺批锋,整批来料外观一致性良好4.2.2尺寸:按图纸与国标要求,重要尺寸零缺陷。
4.2.2性能:试装配与使用性能符合产品要求。
5、工序质量检验标准5.1冲裁检验标准5.1.1对有可能造成伤害的尖角、棱边、粗糙要做去除毛刺处理<5.1.2图纸中未明确标明之尖角(除特别注明外)均为R1.0。
5.1.3冲压加工所产生的毛刺,对于门板、面板等外露可见面应无明显凸起、凹陷、粗糙不平、划伤、锈蚀等缺陷。
5.1.4毛刺:冲裁后毛刺高L<5%t (t为板厚)。
5.1.5划伤、刀痕:以用手触摸不刮手为合格,应<0.1mm。
5.1.6平面度公差要求见表一。
附表一、未注平面度公差要求5.2折弯检验标准5.2.1毛刺:折弯后挤出毛刺高L<10%t(t为板厚)。
5.2.2压印:看得到有折痕,但用手触摸感觉不到。
(有特殊表面要求和镜面除外)523折弯变形标准按照表二》及表三》附表二:对角线公差要求】524折弯方向、尺寸与图纸一致5.2.5钢板在弯、折、卷制作过程中出现的锤击痕迹应予以修复,不得有明显锤窝现象。
钣金件加工检验标准

钣金件加工检验标准一、目的:明确钣金车间各工序所生产的零部件的检验方法和质量要求,确保每件产品合格流入下工序。
二、适用范围:钣金车间加工的各工序,是对钣金车间加工产品的质量的控制。
三、职责:1、钣金车间操作技术人员负责对钣金加工过程的产品的自检,互检。
2、综合质检部在钣金车间的质检员负责对钣金生产加工的过程中的产品质量进行抽验、监督、确认。
3、综合质检部负责对不合格品的发现,记录并做标识隔离,组织处理不合格品。
4、生产部钣金车间参与不合格品的处理。
5、采购部对进厂的钣金原料不合格品与供应商进行沟通。
四、检测工具:5mm 卷尺、200300 卡尺、角度尺、目测五、操作流程下料组1、内装:⑴先审图后施工,首先对工程项目的料厚,规格,领用数量进行审核后, 严格按图纸要求进行下料。
⑵标准件下料5件内的长w 2000mm、宽w 1200 mm尺寸公差控制在士0.5mm, 5件以上的产品下料尺寸要完全跟图纸一致,》2000mm 公差控制在± 0.8mm.⑶非标件下料5件以内的长w 2000mm、w 1200mm宽尺寸公差控制在士0.8mm, 5件以上的产品下料尺寸要完全跟图纸一致, >2000mm 公差控制在士 1 mm。
⑷标准件、非标件的下料毛刺公差控制在士0.3mm。
⑸标准件5件以内的产品对角线公差在士0.5mm。
5件以上的产品对角线要完全跟图纸一致,非标件 5 件以内的产品角线公差在士1mm,5件以上的产品对角线要完全跟图纸一致,长度》4000mm,宽度》1300mm 对角线公差士3mm。
⑹表面无划伤、凹凸点、水印、氧化、辊印、波浪、变形等。
戈U伤、凹凸点宽度〉1mm,深度〉0.3mm,板面是w 2000mm,划伤、凹凸点宽度> 1.5mm、深度〉0.5mm,板面是》2000mm。
⑺标准件每隔半小时对所下之料进行抽检, 非标件每隔3-5 件须进行抽检。
⑻每份订单编号的贴法由所生产的板的实际情况下贴在同一位置。
钣金件来料检验规范

钣金件来料检验规范一、目的:明确钣金件检验方法与标准,确保产品符合技术的要求,防止不良品流入下一道工序。
二、适用范围:适用于本公司的所有钣金件配件与产品。
三、检验条件:1、环境:450-1000流明正常光源或日光灯下,从45度角度观察,距离为30-35cm。
2、抽样方案:一般检验水平Ⅱ,正常抽样,AQL值为(Cr=0,Ma=0.65,Mi=2.5)。
3、抽检频率:针对可靠性试验,新供应商的第一批物料做,量产供应产的每三个月做一次可靠性测试。
四、异常定义:1、划伤:手指感觉不出的线条或凹凸痕。
2、点缺陷:具有点形状的缺陷,测量时以最大直径为尺寸。
3、凹凸点:受到外力撞击而导致表面上出现的高低不平。
4、裂缝:在材料部分断裂,常发生在折弯引伸加工之外侧,因内/外力或机械损伤而造成的裂纹和细小开裂。
5、披锋:剪切或冲压导致残留的不平整边缘。
6、氧化:材料与空气中的氧起化学变化,失去原有特性:如生锈。
7、油渍:在表面残留的油污。
8、变形:加工成型时因冲压拉伸或卸料造成的整体形变。
9、焊痕:焊接所留下的痕迹。
10、脱焊:焊点分离现象。
五、缺陷分类CRI(严重缺陷):违反相关安规标准,可能对使用者造成伤害或有安全隐患的缺陷。
MAJ(主要缺陷):属于功能性缺陷,影响使用与装配。
MIN(次要缺陷):属于外观、包装轻微缺陷,不影响使用或装配。
六、测量分类A面:在成品使用过程中,直接在近处观看且暴露在外的表面。
例如产品的前面与顶部。
B面:在不移动产品情况下,不直接观看但暴露在外的表面。
例如产品的侧面与背面。
C面:产品在移动与打开的情况下,很少见的表面。
如产品的底部。
钣金结构件外观检验规范
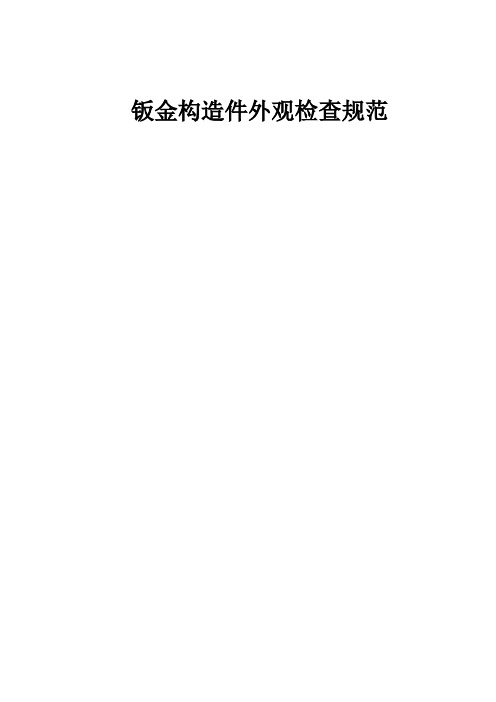
钣金构造件外观检查规范目录1 目旳 ......................................................................................................................... 错误!未定义书签。
2 合用范围 ................................................................................................................. 错误!未定义书签。
3 术语 ......................................................................................................................... 错误!未定义书签。
4外观表面等级定义.................................................................................................. 错误!未定义书签。
4.1 1级表面................................................................................................... 错误!未定义书签。
4.2 2级表面................................................................................................... 错误!未定义书签。
4.3 3级表面................................................................................................... 错误!未定义书签。
钣金件检验规范标准

#1.目的:规范钣金结构件的检验标准,以使各过程的产品质量得以控制。
2.适用范围:本标准适用于各种钣金结构件的检验,图纸和技术文件同时使用。
当有冲突时,以技术规范和客户要求为准。
3.引用标准:本标准的尺寸未注单位皆为mm,未注公差按以下国标IT13级执行GB/产品几何技术规范极限与配合第1部分:公差、偏差、和配合的基础GB/ -2009产品几何技术规范极限与配合第2部分:标准公差等级和孔、轴极限偏差表GB/1804-2000 一般公差未注公差的线性和角度尺寸的公差未注形位公差按GB/T1184 -1996 形状和位置公差未注公差值执行。
4。
原材料检验标准金属材料:钣材厚度及质量应符合国标,采用钣材需出示性能测试报告及厂商证明。
材料外观:平整无锈迹,无开裂与变形。
尺寸:按图纸或技术要求执行,本司未有的按现行国标执行。
通用五金件、紧固件外观:表面无绣迹、无毛刺批锋,整批来料外观一致性良好。
尺寸:按图纸与国标要求,重要尺寸零缺陷。
性能:试装配与使用性能符合产品要求。
5、工序质量检验标准冲裁检验标准对有可能造成伤害的尖角、棱边、粗糙要做去除毛刺处理。
图纸中未明确标明之尖角(除特别注明外)均为。
冲压加工所产生的毛刺,对于门板、面板等外露可见面应无明显凸起、凹陷、粗糙不平、划伤、锈蚀等缺陷。
毛刺:冲裁后毛刺高L≤5%t(t为板厚)。
划伤、刀痕:以用手触摸不刮手为合格,应≤。
平面度公差要求见表一。
附表一、未注平面度公差要求折弯检验标准毛刺:折弯后挤出毛刺高L≤10%t(t为板厚)。
压印:看得到有折痕,但用手触摸感觉不到。
(有特殊表面要求和镜面除外)折弯变形标准按照《表二》及《表三》。
【附表二:对角线公差要求】折弯方向、尺寸与图纸一致。
钢板在弯、折、卷制作过程中出现的锤击痕迹应予以修复,不得有明显锤窝现象。
钣金加工件检验标准尺寸:尺寸按图纸要求检验,尺寸公差见表三。
【附表三:未注尺寸公差要求】焊接焊缝应牢固、均匀,不得有虚焊、裂纹、未焊透、焊穿、豁口、咬边等缺陷。
钣金结构件通用检验标准
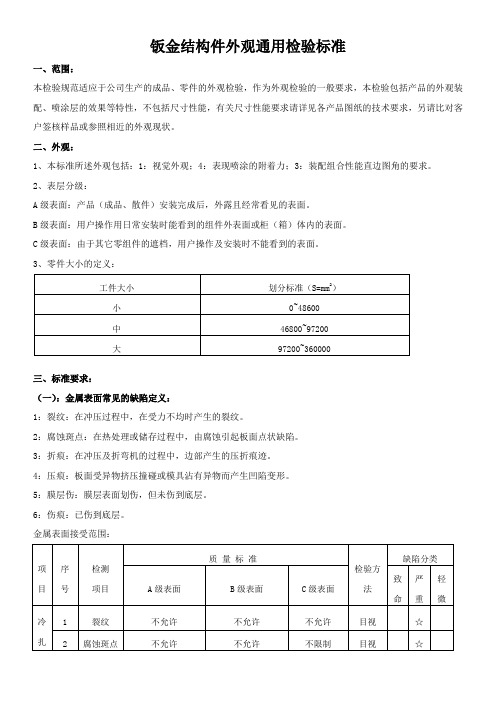
钣金结构件外观通用检验标准一、范围:本检验规范适应于公司生产的成品、零件的外观检验,作为外观检验的一般要求,本检验包括产品的外观装配、喷涂层的效果等特性,不包括尺寸性能,有关尺寸性能要求请详见各产品图纸的技术要求,另请比对客户签核样品或参照相近的外观现状。
二、外观:1、本标准所述外观包括:1:视觉外观;4:表现喷涂的附着力;3:装配组合性能直边图角的要求。
2、表层分级:A级表面:产品(成品、散件)安装完成后,外露且经常看见的表面。
B级表面:用户操作用日常安装时能看到的组件外表面或柜(箱)体内的表面。
C级表面:由于其它零组件的遮档,用户操作及安装时不能看到的表面。
3、零件大小的定义:三、标准要求:(一):金属表面常见的缺陷定义:1:裂纹:在冲压过程中,在受力不均时产生的裂纹。
2:腐蚀斑点:在热处理或储存过程中,由腐蚀引起板面点状缺陷。
3:折痕:在冲压及折弯机的过程中,边部产生的压折痕迹。
4:压痕:板面受异物挤压撞碰或模具沾有异物而产生凹陷变形。
5:膜层伤:膜层表面划伤,但未伤到底层。
6:伤痕:已伤到底层。
金属表面接受范围:附注:(1):表中L: 表示单个缺陷长度,单位:mm, S表示单个缺陷面积,单位mm2,P表示缺陷的数量,单位个。
(2):上表所列的缺陷个数当在每一表面上超过2个时,每二个缺陷之间的距离必须大于10mm,否则视为同一缺陷面积认其总和计算。
(二):电镀表面常见缺陷的定义:1:浅划伤:膜层表面划伤,但未伤至底层。
2:深划伤:表面膜层划伤,且以伤至底层。
3:水印:电镀因清洗水未及时干澡或干澡不彻底所形成的斑纹,印迹。
4:漏镀:电镀时,因堆积导致的工件部分表面无镀层现象。
5:雾状:镀层表面上的模湖,不清晰,不光泽的现象。
6:砂眼:镀层表面的疏松针孔现象。
7:颗粒:因材料杂质或外来物的影响在表面形成的颗状物与正常表面一致的凸起现象。
电镀件外观缺陷可按以下范围表:(三): 喷涂表面常见缺陷定义:1:附着力:色漆、清漆及有关产品的涂层从底材分离的抗性。
钣金外观检验标准
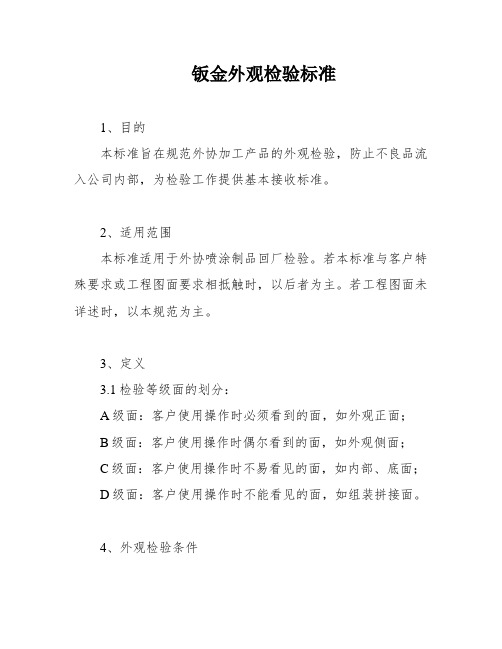
钣金外观检验标准1、目的本标准旨在规范外协加工产品的外观检验,防止不良品流入公司内部,为检验工作提供基本接收标准。
2、适用范围本标准适用于外协喷涂制品回厂检验。
若本标准与客户特殊要求或工程图面要求相抵触时,以后者为主。
若工程图面未详述时,以本规范为主。
3、定义3.1检验等级面的划分:A级面:客户使用操作时必须看到的面,如外观正面;B级面:客户使用操作时偶尔看到的面,如外观侧面;C级面:客户使用操作时不易看见的面,如内部、底面;D级面:客户使用操作时不能看见的面,如组装拼接面。
4、外观检验条件4.1光照强度:自然光或光照强度300-600lux的近似自然光下。
4.2目视检验距离:约60cm左右。
4.3目视检验时间:每面10-15秒。
5、喷涂质量标准及控制细则5.1色差比对标准色板,有仪器的情况下按ΔE≤1.0为标准。
亦可对比色板目视,要求:目视无明显差异。
有无明显差异若存在争议,可用如下方式判决:将判定者判定有明显差异的产品在反面或内部标记,并将此产品混入3个无明显颜色差异的产品当中,让判定者5秒内选出有标记的产品。
此实验可反复操作,若选择又快又准,说明色差明显。
5.2膜厚膜厚仪测量:70~150um。
表面目视无发青、针孔的现象。
5.3附着力百格测试无脱落。
测试位置应该在产品内部或反面不明显处,测试后补漆处理。
5.4外观常发生的缺陷与接收标准:序号现象检验接收标准缺陷严重度1没有手感的擦伤A面:每面≤2处,长度≤20mm;B面:每面≤2处,长度≤20mm;轻2有手感的划伤(不露底)A面:每面≤1处,长度≤10mm;B面:每面≤1处,长度≤10mm;一般3深划伤(露底)A面:不接受;B面:每面≤1处,长度≤10mm;重4凹坑、撞变形(未掉整块漆的情况)每面≤1处,直径≤Φ3,修复过后不明显的;重5色点、杂质每面≤5处,直径≤Φ0.5,目视10秒内难发现;轻6桔纹过小、过大全外观面参考限度样;一般7拐角处积粉无;轻8气孔、针孔每面≤5处,直径≤Φ0.5,目视10秒内难发现;轻9露底不接受;重10外观无;轻11表面不平整无;一般审核日期:2018.7.20 批准日期:2018.7.20编制人:___验收标准和质量控制细则接收标准:A-B面:不接受C面:如果不影响安装,可接受B-C面:不集中,不超过5个,目视10秒内难发现缺陷严重度:轻一般重前处理不良,有锈,橘皮,厚度明显不均匀的A-B面不接受。
钣金结构件检验通用标准
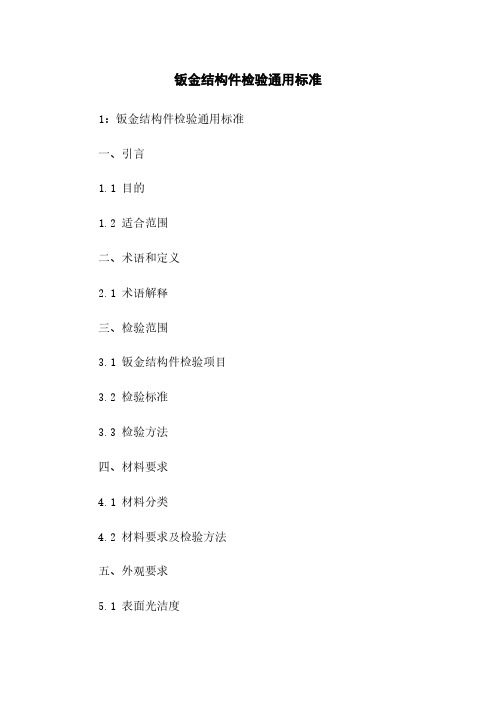
钣金结构件检验通用标准1:钣金结构件检验通用标准一、引言1.1 目的1.2 适合范围二、术语和定义2.1 术语解释三、检验范围3.1 钣金结构件检验项目3.2 检验标准3.3 检验方法四、材料要求4.1 材料分类4.2 材料要求及检验方法五、外观要求5.1 表面光洁度5.2 表面涂层5.3 表面缺陷检验六、尺寸要求6.1 尺寸测量工具6.2 尺寸容许偏差6.3 表面平整度要求七、性能要求7.1 强度要求7.2 刚度要求7.3 密封性要求八、特殊测试要求8.1 耐腐蚀性测试8.2 防震性能测试8.3 焊缝质量检验九、检验记录及报告9.1 检验记录要求9.2 检验报告要求十、附件罗列出本所涉及附件如下:1. 技术图纸2. 检验记录表3. 检验设备清单十一、法律名词及注释罗列出本所涉及的法律名词及注释:1. 质量管理体系:指组织在组织内实施并维护的,为持续改进和提供一致性,以满足客户要求的质量管理活动。
2. GB/T 19001-2022:质量管理体系-要求。
2:钣金结构件检验通用标准一、引言1.1 此的目的在于确立钣金结构件检验的通用标准,以确保产品满足质量要求。
1.2 适合范围为所有钣金结构件的生产和验收阶段。
二、术语和定义2.1 术语解释:详细解释了本中所使用的术语及其定义,为正确理解内容提供依据。
三、检验范围3.1 钣金结构件检验项目:罗列了常见的钣金结构件检验项目,如外观检验、尺寸测量等。
3.2 检验标准:根据国家标准和行业规范制定了相应的检验标准,并列出了相关标准的名称和编号。
3.3 检验方法:详细描述了每一个检验项目的具体检验方法和步骤,包括检验工具、操作要点等。
四、材料要求4.1 材料分类:根据材料的种类和性质进行分类,并说明了不同材料的特点和使用要求。
4.2 材料要求及检验方法:了不同材料的要求,包括化学成份、力学性能等,并给出了相应的检验方法。
五、外观要求5.1 表面光洁度:定义了不同等级的表面光洁度要求,并说明了检验方法和评定标准。
钣金检验规范(标准文本)

Q/SK钣金件及不锈钢件检验规范(依据GB-19001-2008质量管理体要求标准制定)一:钣金外观部分1.目的及适及范围:1.1本检验规范为了进一步提高钣金制品的质量,为外协加工提供检验根据,为外观检验提供科学、客观的方法。
对某些无法用定量表明的缺陷,用供需双方制订的检验标准和封样的办法加以解决。
1.2本检验规范适用于金属钣金件制成的产品及其相关加工组成品。
2. 参照文件2.1本文件根据浙江斯克瑞德安全技术有限分司质量管理体系GB-19001-2008质量管理体要求标准制定2.2本检验规范参照金属冷冲压件通用技术条件2.3本规范若与零件图/规格相抵触, 则以零件图/规格为优先2.4本规范若与参考文件相抵触, 则以本规范为优先3.内容:术语部分钣金件外观术语解释:3.2 检验方法3.2.1外观缺陷的检验方法及要求:将待验品置于以下条件,作检验判定:A、目测距离: 距离产品25cmB、检验角度: 成45度目视检测。
C、检验光源: 正常日光灯,室内无日光时用40W日光灯或60W普通灯泡的照度为标准。
D 、观察时间:<10秒 (每个可见平面需要3秒)。
E 、检查半成品、成品之前应核对相关检验资料。
3.2.2 外观尺寸及尺寸的配合的检验方法 使用普通长度测量仪或各种量规进行测量。
3.3 不合格类别划分:根据本行业客户的具体实际要求,金属钣金件制品的外观不合格类别有亮度差、边缘不良、变形、污渍(不清洁)、麻点、压痕、粗砂、磨花等。
结合以上不合格类别的客户要求等级,可将钣金件制品共分6级和特殊级,以作轻重不良的区分(见表1)。
3.4 检验项目及标准 3.4.1冲压件判定标准(表2)标题:产品外观检验标准版本: A 页次: 3 of 3N=数量,L=长度,W=宽度,D=直径,A=区域,J=距离,H=深度,S=面积,1批鋒在五金件周围多出的五金料废边 1.影响外观为轻缺陷.目测L 为長 H 為寬L ≤0.1mm.H ≤0.1mm 2.影响功能或装配为重缺陷.2 五金件手印 以反光面检查为条件不允許超过标准为得不良. 目测3 帖紙粘性 与实物粘贴实验 以测试结果已定1.脱落为严重不良.2.与样品相差为轻缺陷.目测4 混料 混有不同规格的物料 不允许 重缺陷 游标卡尺/针规5 规格不符 与标准不符不允许 重缺陷 目测 6 生锈 产品表面生成黄黑色异物 不允许 重缺陷 目测 7 少數 少于标准数量 不允许 重缺陷 目测 8破裂物料破裂不允许重缺陷目测披LH3.4.2 成型钣金件的检验项目及标准(表3)3.4.3 检验时注意事项:1.本规范如与客户要求不同时,原则上以客户之检验标准,如客户提供之检验规范或备注在客户注意事项内。
- 1、下载文档前请自行甄别文档内容的完整性,平台不提供额外的编辑、内容补充、找答案等附加服务。
- 2、"仅部分预览"的文档,不可在线预览部分如存在完整性等问题,可反馈申请退款(可完整预览的文档不适用该条件!)。
- 3、如文档侵犯您的权益,请联系客服反馈,我们会尽快为您处理(人工客服工作时间:9:00-18:30)。
Q/SK钣金件及不锈钢件检验规范(依据GB-19001-2008质量管理体要求标准制定)一:钣金外观部分1.目的及适及范围:1.1本检验规范为了进一步提高钣金制品的质量,为外协加工提供检验根据,为外观检验提供科学、客观的方法。
对某些无法用定量表明的缺陷,用供需双方制订的检验标准和封样的办法加以解决。
1.2本检验规范适用于金属钣金件制成的产品及其相关加工组成品。
2. 参照文件2.1本文件根据浙江斯克瑞德安全技术有限分司质量管理体系GB-19001-2008质量管理体要求标准制定2.2本检验规范参照金属冷冲压件通用技术条件2.3本规范若与零件图/规格相抵触, 则以零件图/规格为优先2.4本规范若与参考文件相抵触, 则以本规范为优先3.内容:术语部分钣金件外观术语解释:3.2 检验方法3.2.1外观缺陷的检验方法及要求:将待验品置于以下条件,作检验判定:A、目测距离: 距离产品25cmB、检验角度: 成45度目视检测。
C、检验光源: 正常日光灯,室内无日光时用40W日光灯或60W普通灯泡的照度为标准。
D、观察时间:<10秒(每个可见平面需要3秒)。
E、检查半成品、成品之前应核对相关检验资料。
3.2.2 外观尺寸及尺寸的配合的检验方法使用普通长度测量仪或各种量规进行测量。
3.3 不合格类别划分:根据本行业客户的具体实际要求,金属钣金件制品的外观不合格类别有亮度差、边缘不良、变形、污渍(不清洁)、麻点、压痕、粗砂、磨花等。
结合以上不合格类别的客户要求等级,可将钣金件制品共分6级和特殊级,以作轻重不良的区分(见表1)。
3.4 检验项目及标准3.4.1冲压件判定标准(表2)标题:产品外观检验标准版本: A页次: 3 of 3N=数量,L=长度,W=宽度,D=直径,A=区域,J=距离,H=深度,S=面积,1 批鋒在五金件周围多出的 1.影响外观为轻缺陷. 目测披3.4.2 成型钣金件的检验项目及标准(表3)3.4.3 检验时注意事项:1.本规范如与客户要求不同时,原则上以客户之检验标准,如客户提供之检验规范或备注在客户注意事项内。
2.对模棱两可的缺失,虽经检验员初次误判为允收,但第二次检验发现属缺失时,可判为定为不合格。
3.如各项品质标准所列为缺点时,后制程加工(如点焊,压超声波等),完工后品质缺点降低者,该缺点项目列为允收。
4.关于五金件的外观A、 B、 C面检验的方法:外观面板/铝合金饰板/电解铝底座/马口铁遮磁板/不锈钢面板/马达固定片/CIS支架等五金件都应分为外观的A、B、C面4.1 目的本标准定义冲压件产品外观品质的基本要求,并确立允收/拒收之准则。
4.2 适用范围本标准适用于生产的所有冲压件产品。
4.3 相关文件《产品外观检验标准》。
4.4 定义A级面:客户经常看到的面,外观面板,出给客户的外表面。
B级面:不移动的情况下,客户偶尔能看到的面。
C级面:产品在移动或被打开时才能看到的面。
5 检测条件5.1 所有检验均应在正常照明,并模拟最终使用条件下进行。
检测过程中不使用放大镜,所检验表面和人眼呈45°角。
A级面在检测时应转动,以获得最大反光效果。
B级面和C级面在检测期间不必转动。
光源=40W荧光灯零件表面人眼距离250毫米5.2 A级面停留10秒,B级面停留5秒,C级面停留3秒。
6 薄板金属件外观检验标准6.1 允收总则6.1.1 可接受的缺陷不能影响该零件的装配和功能,否则,将被拒收。
6.1.2 缺陷允收定义了1250平方毫米的区域内各类缺陷的最大允收数量。
对于较大的零件表面,可允收数量和该表面所含1250平方毫米区域数量成正比,但是,两个或两个以上缺陷不能相连。
6.2 缺陷定义6.2.1彩虹效应:镀锌有可能造成变色或“彩虹”效应。
6.2.2生锈/氧化:暴露在空气中的金属表面发生的化学反应。
6.2.3变色:底色或预期的颜色发生改变,或零件表面的颜色不一致。
轻微晕状条纹可接受.直径75mm的任何圆形内的6个包括白色氧化所造成斑点,如果不超过长50mm 宽2.00mm或直径6.00mm可接受。
6.2.4刮伤:零件表面的呈条状的浅沟。
刮痕或磨损以致裸露出金属者, 不接受. 若直径150mm之范围内, 只有一个未裸露出金属之刮痕或磨损,未改变表面颜色, 且直径小于3.00mm者, 则可接受. 任何肉眼可见破坏花纹之条纹或撕痕, 均不接受6.2.5压痕:由尖锐物件在零件表面造成的沟痕,指甲能够感受到。
直径大于2.00mm 者,(深度大于0.125mm者, )皆不予接受. 任何直径600mm之范围内不得超过一个凹痕或压痕.6.2.6镀痕/流痕:由于镀层厚度不均匀造成零件表面上波纹状或条状异常的区域直径大于20mm之凹痕及压痕不予接受.任何600mm直径之圆内不得有超过三个凹痕或压痕6.2.7痕迹:指基体材料的小坑、折弯痕或其他痕迹,涂装后仍无法消除。
6.2.8灰尘或油脂:在制造过程中产生并留在零件表面上的赃污(未清洗)零件应无灰尘, 污垢, 润滑油, 机油, 残胶或任何其它表面沾染物. 如果是在搬运材料时, 可吹掉或擦拭的灰尘则可接受. 零件应无任何可能陷在硬件, 裂缝或弯折处或其它凹陷处的沾染物.6.2.9斑点/沙粒/绒线:涂装面或零件表面任何非预期的异物,直径大于1.50mm之杂质不予接受.在任何600mm之圆圈内不得有6个以上或任二个距离小于50.00mm之杂质.6.2.10凹坑:零件表面弹坑状的缺陷,直径大于12.5mm之凹痕及压痕不予接受.任何600mm直径之圆内不得有超过三个凹痕或条纹6.2.11模压痕:因成形模具在零件表面造成的工艺痕,所有零件的模压痕的位置和大小都一样,均匀分布于成形/折弯区域。
6.2.12零件应无灰尘, 污垢, 润滑油, 机油, 残胶或任何其它表面沾染物. 如果是在搬运材料时, 可吹掉或擦拭的灰尘则可接受. 零件应无任何可能陷在硬件, 裂缝或弯折处或其它凹陷处的沾染物..脏污改变表面颜色且直径大于0.60mm者, 不予接受. 如直径小于0.25mm之脏污, 视为看不见. 任两个脏污之最小距离为5.0mmC:杂质: 直径大于1.0mm者,(高度大于0.125mm者,) 皆不予接受. 在任何直径300mm之范围内不得有四个以上或任两个距离小于50mm之杂质.6.2.13烤漆面刮痕或磨损: 刮痕或磨损以致裸露出金属者, 不接受. 若直径150mm之范围内, 只有两个未裸露出金属之刮痕或磨损,未改变表面颜色, 且直径小于12.5mm者, 则可接受. 任何肉眼可见破坏花纹之条纹或撕痕, 均不接受.6.2.14电镀表面:A.刮痕:刮痕如超过200mm X 宽1.25mm不接受.磨损直径大于25mm者不予接受.在直径150mm的圆形内,不得超过6个刮伤或4个磨损.B. 凹痕及压痕: 直径大于20mm之凹痕及压痕不予接受.任何600mm直径之圆内不得有超过三个凹痕或压痕.C.颜色均一性: 轻微晕状条纹可接受.包括白色氧化所造成斑点可接受.D.水渍: 水渍大于3/4 总表面积者不予接受.二:表面喷涂检验规范1、目的规范检验操作,发现、控制不良品,防止批不良品输入下道工序。
同时给检验工作提供引导及接收标准。
2、范围适用于进料、外协制品回厂、成品的检验接收及顾客退货的挑选检验。
3、定义喷塑、喷漆件检验过程的参照标准(电泳漆件检验参照喷漆件检验标准)。
4、职责4.1 品质部负责不合格的发现、记录、标识及隔离,组织处理不合格品。
4.2 制造部参与不合格品的处理。
4.3 采购部负责进料中不合格品与供应商的联络。
4.4 管理者代表负责不合格品处理的批准。
5、工作程序外观(目测)5.1 喷涂种类(如:塑粉或漆)、颜色与图纸要求及客户、我司、供应商三方确认的色板是否一致。
5.2 一般情况下,产品喷涂表面外观在使用时要求100%进行检验(员工自检),检验方式依据本标准。
进料、外协回厂或过程验收则采用抽检,抽检操作方式依据《抽检规范》。
特殊产品根据产品的具体要求检验。
5.3 外观缺陷:有缩孔、针孔、杂质点、漏底、涂层厚度明显不均、流泪、预处理不良有锈、表面有污斑、不光滑、不平整、桔皮、花斑、凹坑等。
5.4 外观和颜色检验的环境:5.4.1 色板采用客户样件或经客户认可的签样。
5.4.2 应在标准光源对色灯箱CAC-600箱内(无设备条件时则要求在天然散射光线或光照度不低于2×40w光源环境下),以目视方法进行。
光照度通常在D65(特殊情况下用5.4.3 检查距离:被测品与眼睛的距离为500mm,检验时在±15°范围内旋转。
涂膜附着力(划格实验)5.5涂膜附着力检验(基体金属为铁、钢、铝及铝合金):5.5.1 采用划格—胶带粘贴法测定漆膜附着力,每批次以一件或两件检验则可。
不合格时可用加严检验。
5.5.2 检验方法:使用锋利刃口的刀片(刃口宽要求0.05mm,刃口达到0.1mm时必须重新磨刃口),沿能确保得到直线切口的导向器,刃口在相对涂面35-45度角,均速划线。
划线位置距产品边缘最近距离不应小于2mm,切口要保证切到基体,在涂膜上,切出每个方向是6至11条切口的格子图形,切口以1mm间隔隔开,长度约20mm。
对于涂膜厚度大于50μm,小于125μm(喷塑要求厚度80--150μm,喷漆要求厚度20--26μm),切口以2mm的间隔隔开。
在将格子区切屑用软刷或软纸清除后,撕下一段粘附力在2.9N/10mm (300GF/10mm) 以上的胶带,将格子区全部覆盖,用手磨擦胶带,确保已完全粘牢后,拿住胶带的一端,沿着与其原位置尽可能接近180º的方向迅速(不要猛烈)将胶带撕下,然后用放大镜或肉眼观察。
如果沿切口的边和方格部分有涂层脱落,损伤的区域为格子的5%以上,再重复上述方法检验。
如果两次结果不同,换不同的检验人员,将在同样的条件下获得的涂膜,按同样的方式进行该检验。
若仍出现上述结果或更差的情况,则有权怀疑该批涂层质量不合格,可以做出拒收决定。
损伤的区域小于格子的区域5%为合格(参考下图)。
涂层的密封性(盐雾试验检验)5.6盐雾试验检验(如无盐雾试验专用设备则可采用溶液浸泡的方式代替检验)5.6.1 装置:A)恒温箱试验温度在40±1℃;B)烧杯:化学分析用的玻璃器具,容量为500ml。
5.6.2 溶液配制:A)试剂:氯化钠试剂; B)水:蒸馏水; C)溶液浓度:0.43~0.6mol/l,(2.5%~3.5%)5.6.3 试样:按照《GB/T 2828。
1-2003/ISO 259-1:1999 计数抽样检验程序第一部分》进行涂层检验,确定合格质量水平AQL=1.5。
如发现有不允许的缺陷或不合格数大于接收要求则拒收此批产品。